check engine KIA CARNIVAL 2007 Service Manual
[x] Cancel search | Manufacturer: KIA, Model Year: 2007, Model line: CARNIVAL, Model: KIA CARNIVAL 2007Pages: 1575, PDF Size: 44.86 MB
Page 328 of 1575
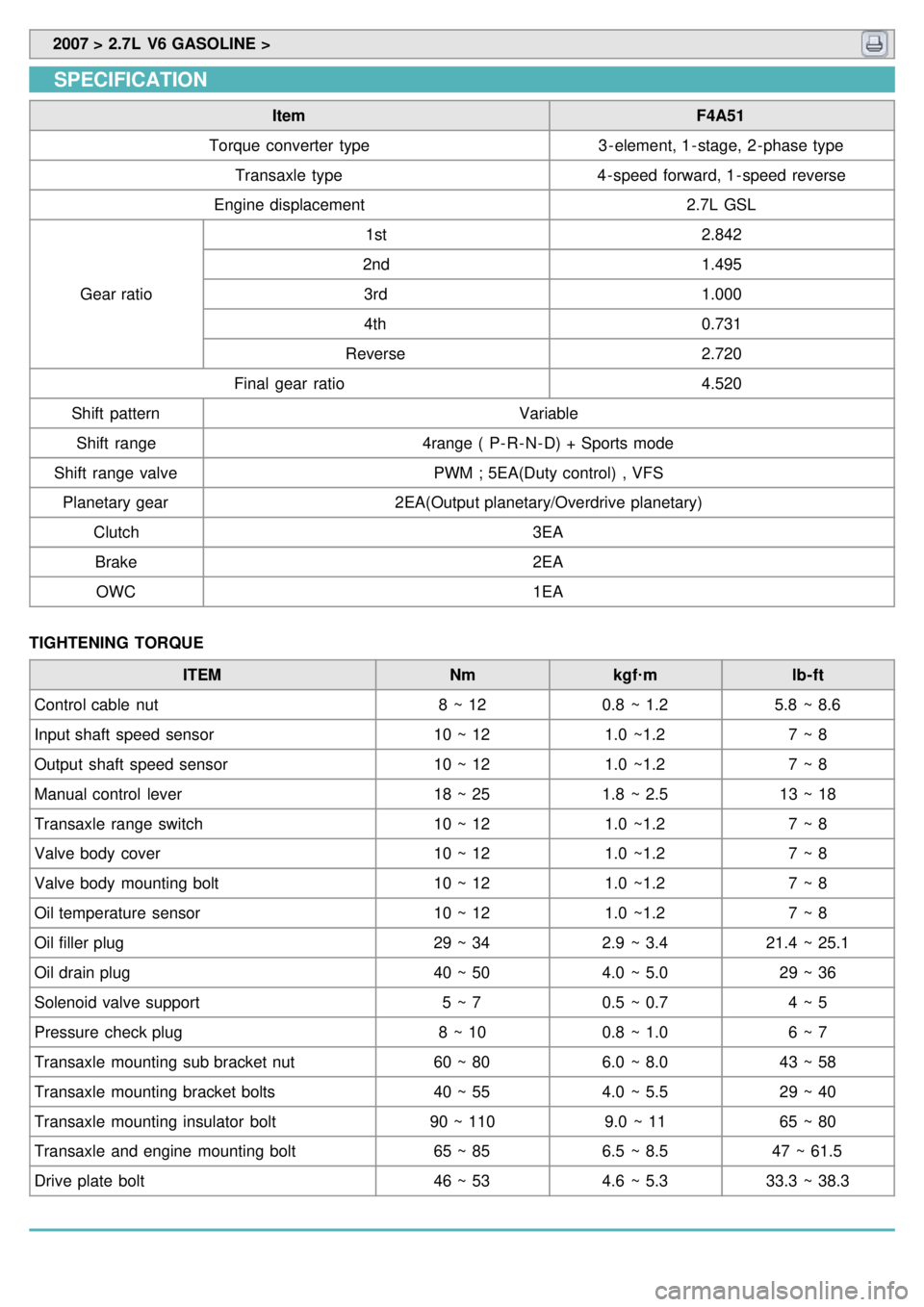
2007 > 2.7L V6 GASOLINE >
SPECIFICATION
Item F4A51
Torque converter type 3 - element, 1 - stage, 2 - phase type
Transaxle type 4 - speed forward, 1 - speed reverse
Engine displacement 2.7L GSL
Gear ratio 1st
2.842
2nd 1.495
3rd 1.000
4th 0.731
Reverse 2.720
Final gear ratio 4.520
Shift pattern Variable
Shift range 4range ( P- R- N- D) + Sports mode
Shift range valve PWM ; 5EA(Duty control) , VFS
Planetary gear 2EA(Output planetary/Overdrive planetary)
Clutch 3EA
Brake 2EA
OWC 1EA
TIGHTENING TORQUE ITEM Nmkgf·m lb- ft
Control cable nut 8 ~ 120.8 ~ 1.2 5.8 ~ 8.6
Input shaft speed sensor 10 ~ 121.0 ~1.2 7 ~ 8
Output shaft speed sensor 10 ~ 121.0 ~1.2 7 ~ 8
Manual control lever 18 ~ 251.8 ~ 2.5 13 ~ 18
Transaxle range switch 10 ~ 121.0 ~1.2 7 ~ 8
Valve body cover 10 ~ 121.0 ~1.2 7 ~ 8
Valve body mounting bolt 10 ~ 121.0 ~1.2 7 ~ 8
Oil temperature sensor 10 ~ 121.0 ~1.2 7 ~ 8
Oil filler plug 29 ~ 342.9 ~ 3.421.4 ~ 25.1
Oil drain plug 40 ~ 504.0 ~ 5.0 29 ~ 36
Solenoid valve support 5 ~ 70.5 ~ 0.7 4 ~ 5
Pressure check plug 8 ~ 100.8 ~ 1.0 6 ~ 7
Transaxle mounting sub bracket nut 60 ~ 806.0 ~ 8.0 43 ~ 58
Transaxle mounting bracket bolts 40 ~ 554.0 ~ 5.5 29 ~ 40
Transaxle mounting insulator bolt 90 ~ 1109.0 ~ 1165 ~ 80
Transaxle and engine mounting bolt 65 ~ 856.5 ~ 8.5 47 ~ 61.5
Drive plate bolt 46 ~ 534.6 ~ 5.333.3 ~ 38.3
Page 334 of 1575
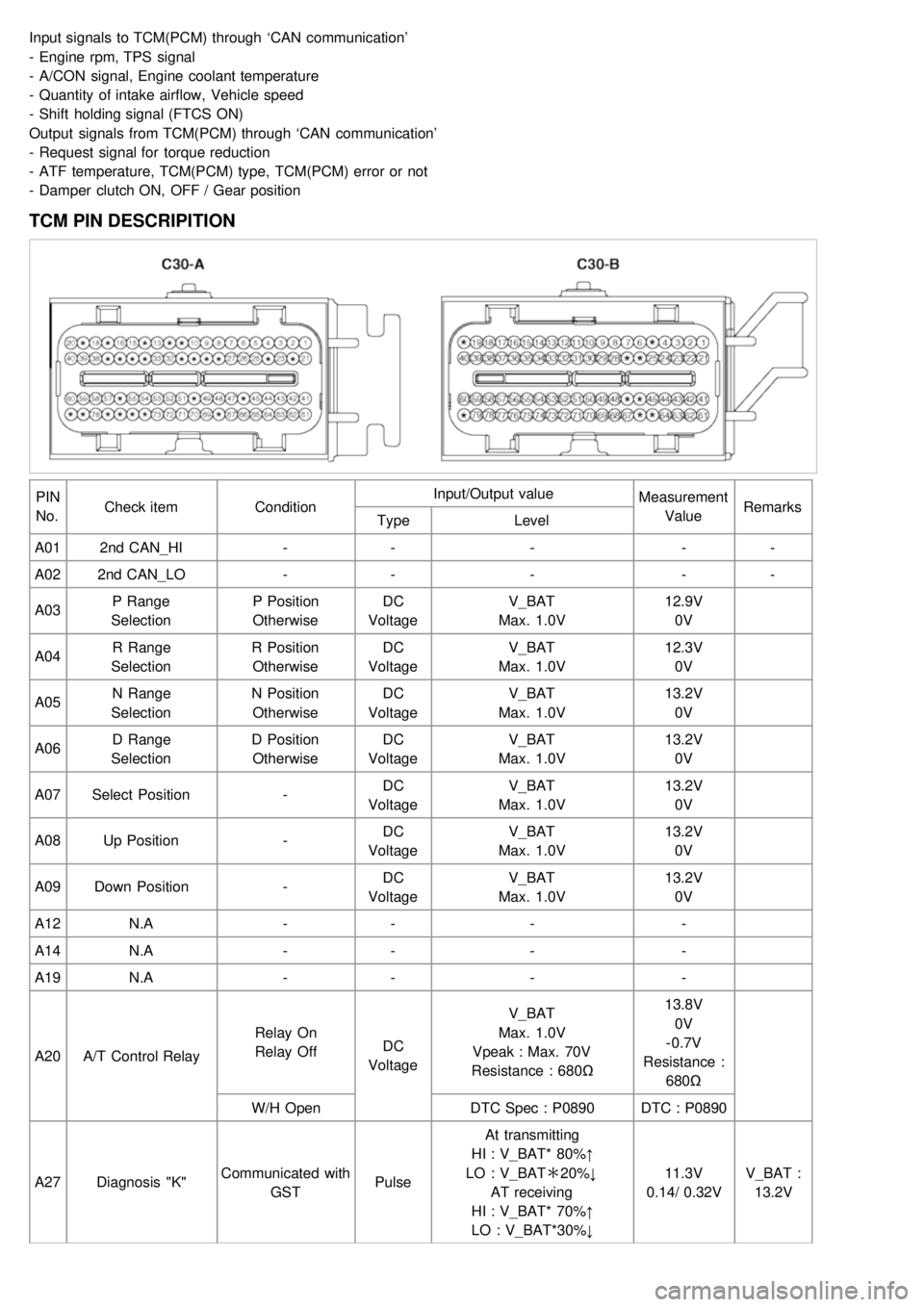
Input signals to TCM(PCM) through ‘CAN communication’
- Engine rpm, TPS signal
- A/CON signal, Engine coolant temperature
- Quantity of intake airflow, Vehicle speed
- Shift holding signal (FTCS ON)
Output signals from TCM(PCM) through ‘CAN communication’
- Request signal for torque reduction
- ATF temperature, TCM(PCM) type, TCM(PCM) error or not
- Damper clutch ON, OFF / Gear position
TCM PIN DESCRIPITION
PIN
No.Check item
Condition Input/Output value
Measurement
Value Remarks
Type Level
A01 2nd CAN_HI -- - --
A02 2nd CAN_LO -- - --
A03 P Range
Selection P Position
OtherwiseDC
Voltage V_BAT
Max. 1.0V 12.9V
0V
A04 R Range
Selection R Position
Otherwise DC
Voltage V_BAT
Max. 1.0V 12.3V
0V
A05 N Range
Selection N Position
Otherwise DC
Voltage V_BAT
Max. 1.0V 13.2V
0V
A06 D Range
Selection D Position
Otherwise DC
Voltage V_BAT
Max. 1.0V 13.2V
0V
A07 Select Position -DC
Voltage V_BAT
Max. 1.0V 13.2V
0V
A08 Up Position -DC
Voltage V_BAT
Max. 1.0V 13.2V
0V
A09 Down Position -DC
Voltage V_BAT
Max. 1.0V 13.2V
0V
A12 N.A -- - -
A14 N.A -- - -
A19 N.A -- - -
A20 A/T Control Relay Relay On
Relay Off
DC
Voltage V_BAT
Max. 1.0V
Vpeak : Max. 70V
Resistance : 680Ω 13.8V
0V
- 0.7V
Resistance : 680Ω
W/H Open DTC Spec : P0890DTC : P0890
A27 Diagnosis "K" Communicated with
GST Pulse At transmitting
HI : V_BAT* 80%↑
LO : V_BATÎ20%↓ AT receiving
HI : V_BAT* 70%↑
LO : V_BAT*30%↓ 11.3V
0.14/ 0.32V V_BAT :
13.2V
Page 340 of 1575
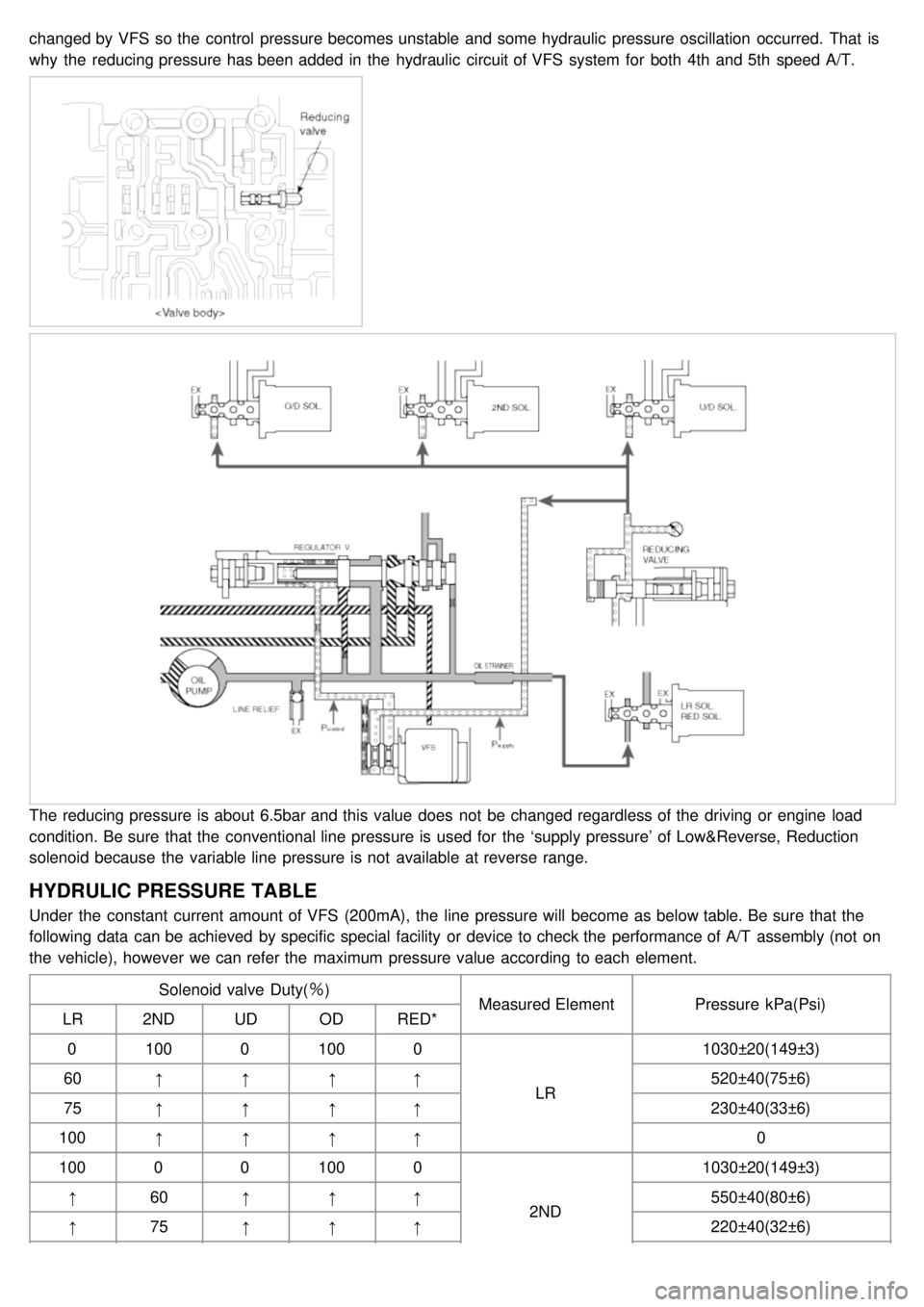
changed by VFS so the control pressure becomes unstable and some hydraulic pressure oscillation occurred. That is
why the reducing pressure has been added in the hydraulic circuit of VFS system for both 4th and 5th speed A/T.
The reducing pressure is about 6.5bar and this value does not be changed regardless of the driving or engine load
condition. Be sure that the conventional line pressure is used for the ‘supply pressure’ of Low&Reverse, Reduction
solenoid because the variable line pressure is not available at reverse range.
HYDRULIC PRESSURE TABLE
Under the constant current amount of VFS (200mA), the line pressure will become as below table. Be sure that the
following data can be achieved by specific special facility or device to check the performance of A/T assembly (not on
the vehicle), however we can refer the maximum pressure value according to each element.Solenoid valve Duty( Ë)
Measured Element Pressure kPa(Psi)
LR 2ND UDODRED*
0 100 0100 0
LR 1030±20(149±3)
60 ↑↑↑↑ 520±40(75±6)
75 ↑↑↑↑ 230±40(33±6)
100 ↑↑↑↑ 0
100 00100 0
2ND 1030±20(149±3)
↑ 60 ↑↑↑ 550±40(80±6)
↑ 75 ↑↑↑ 220±40(32±6)
Page 351 of 1575
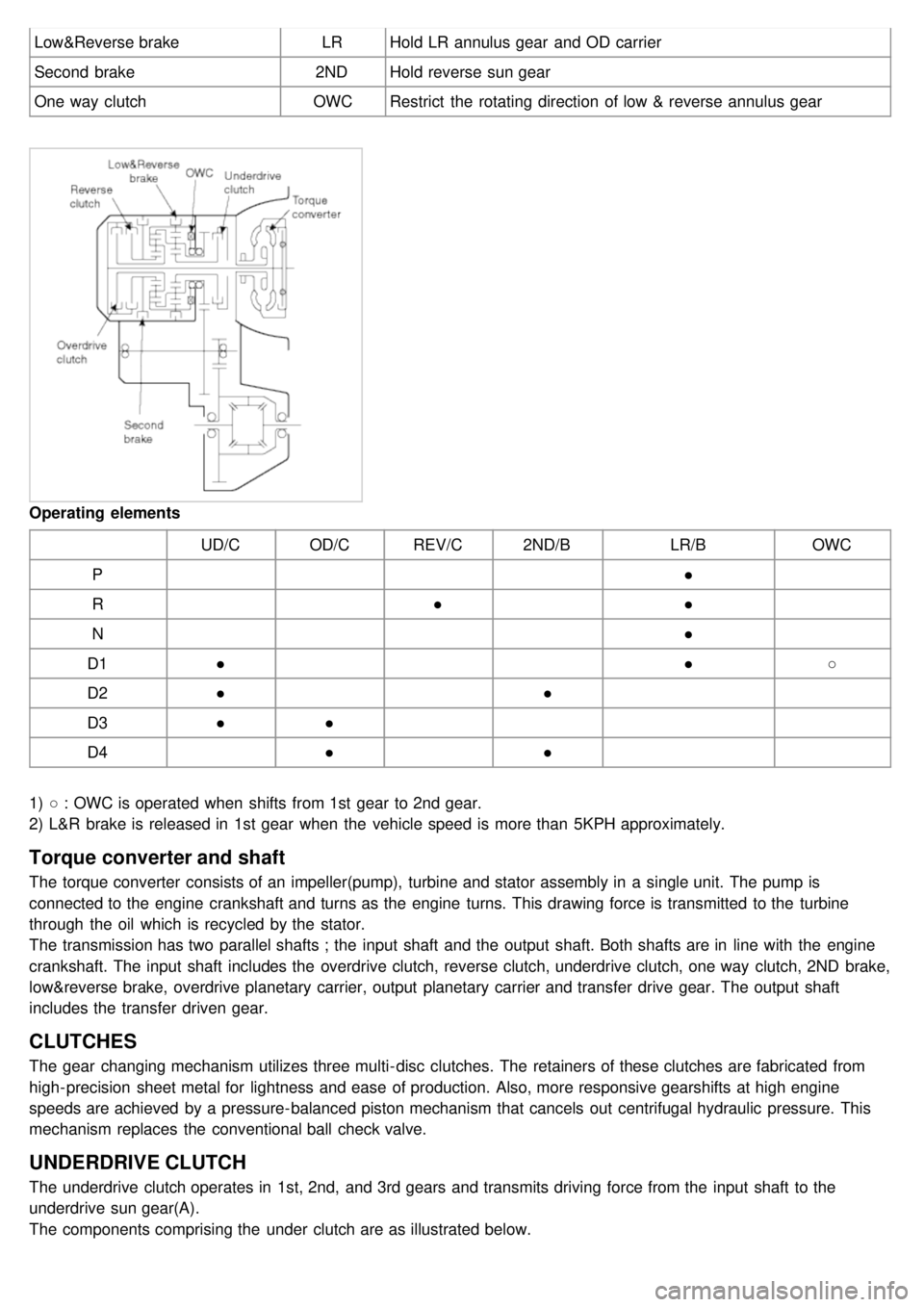
Low&Reverse brakeLRHold LR annulus gear and OD carrier
Second brake 2NDHold reverse sun gear
One way clutch OWCRestrict the rotating direction of low & reverse annulus gear
Operating elements
UD/COD/CREV/C 2ND/B LR/BOWC
P ●
R ●●
N ●
D1 ● ●○
D2 ● ●
D3 ●●
D4 ●●
1) ○ : OWC is operated when shifts from 1st gear to 2nd gear.
2) L&R brake is released in 1st gear when the vehicle speed is more than 5KPH approximately.
Torque converter and shaft
The torque converter consists of an impeller(pump), turbine and stator assembly in a single unit. The pump is
connected to the engine crankshaft and turns as the engine turns. This drawing force is transmitted to the turbine
through the oil which is recycled by the stator.
The transmission has two parallel shafts ; the input shaft and the output shaft. Both shafts are in line with the engine
crankshaft. The input shaft includes the overdrive clutch, reverse clutch, underdrive clutch, one way clutch, 2ND brake,
low&reverse brake, overdrive planetary carrier, output planetary carrier and transfer drive gear. The output shaft
includes the transfer driven gear.
CLUTCHES
The gear changing mechanism utilizes three multi- disc clutches. The retainers of these clutches are fabricated from
high- precision sheet metal for lightness and ease of production. Also, more responsive gearshifts at high engine
speeds are achieved by a pressure- balanced piston mechanism that cancels out centrifugal hydraulic pressure. This
mechanism replaces the conventional ball check valve.
UNDERDRIVE CLUTCH
The underdrive clutch operates in 1st, 2nd, and 3rd gears and transmits driving force from the input shaft to the
underdrive sun gear(A).
The components comprising the under clutch are as illustrated below.
Page 366 of 1575
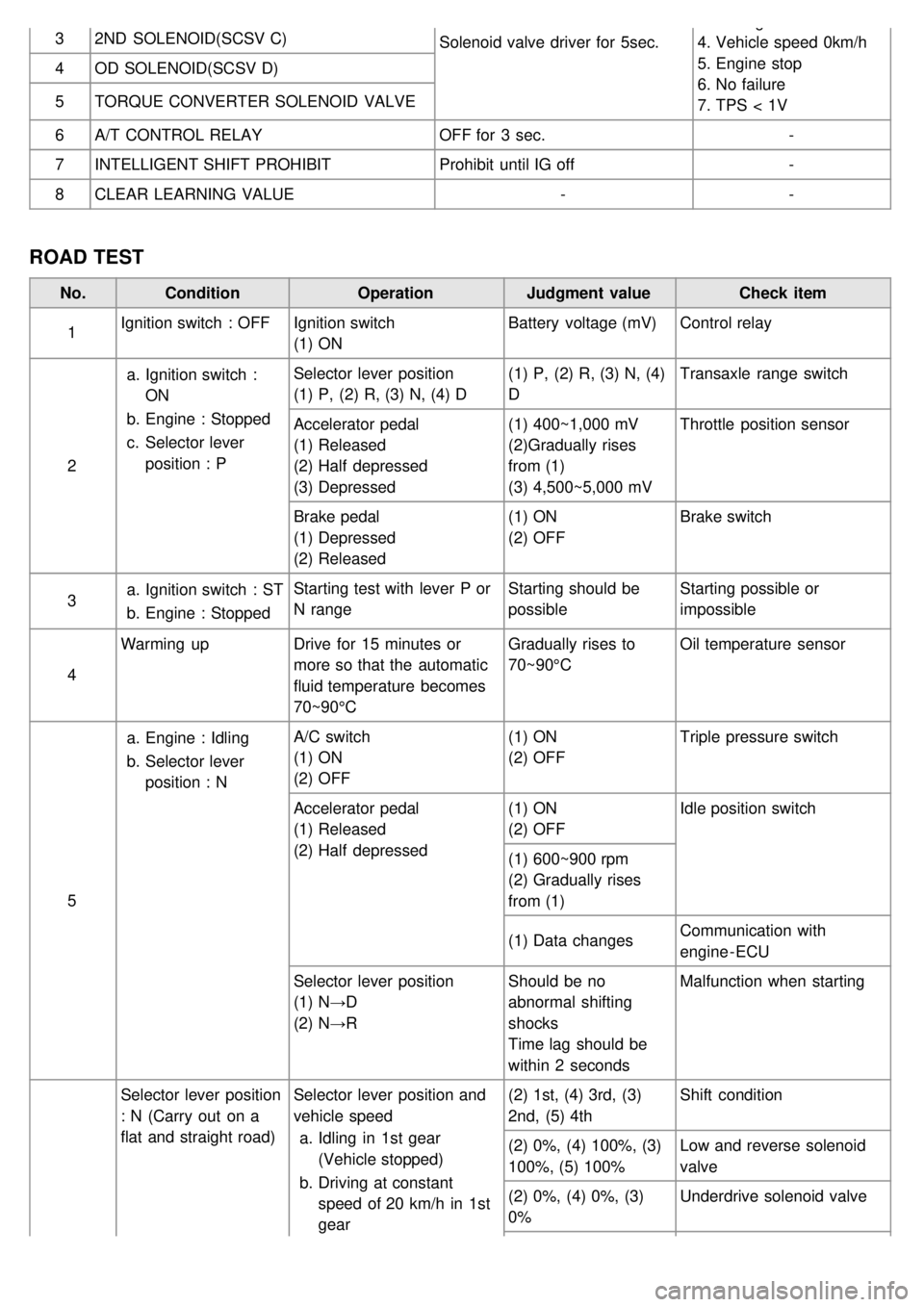
32ND SOLENOID(SCSV C)
Solenoid valve driver for 5sec.3. P range
4. Vehicle speed 0km/h
5. Engine stop
6. No failure
7. TPS < 1V
4
OD SOLENOID(SCSV D)
5 TORQUE CONVERTER SOLENOID VALVE
6 A/T CONTROL RELAY OFF for 3 sec. -
7 INTELLIGENT SHIFT PROHIBIT Prohibit until IG off -
8 CLEAR LEARNING VALUE --
ROAD TEST
No.Condition OperationJudgment value Check item
1 Ignition switch : OFF
Ignition switch
(1) ON Battery voltage (mV)
Control relay
2 a.
Ignition switch :
ON
b. Engine : Stopped
c. Selector lever
position : P Selector lever position
(1) P, (2) R, (3) N, (4) D
(1) P, (2) R, (3) N, (4)
DTransaxle range switch
Accelerator pedal
(1) Released
(2) Half depressed
(3) Depressed (1) 400~1,000 mV
(2)Gradually rises
from (1)
(3) 4,500~5,000 mVThrottle position sensor
Brake pedal
(1) Depressed
(2) Released (1) ON
(2) OFF
Brake switch
3 a.
Ignition switch : ST
b. Engine : Stopped Starting test with lever P or
N range
Starting should be
possibleStarting possible or
impossible
4 Warming up
Drive for 15 minutes or
more so that the automatic
fluid temperature becomes
70~90°C Gradually rises to
70~90°C
Oil temperature sensor
5 a.
Engine : Idling
b. Selector lever
position : N A/C switch
(1) ON
(2) OFF
(1) ON
(2) OFF
Triple pressure switch
Accelerator pedal
(1) Released
(2) Half depressed (1) ON
(2) OFF
Idle position switch
(1) 600~900 rpm
(2) Gradually rises
from (1)
(1) Data changes Communication with
engine - ECU
Selector lever position
(1) N→D
(2) N→R Should be no
abnormal shifting
shocks
Time lag should be
within 2 secondsMalfunction when starting
Selector lever position
: N (Carry out on a
flat and straight road) Selector lever position and
vehicle speed
a. Idling in 1st gear
(Vehicle stopped)
b. Driving at constant
speed of 20 km/h in 1st
gear (2) 1st, (4) 3rd, (3)
2nd, (5) 4th
Shift condition
(2) 0%, (4) 100%, (3)
100%, (5) 100% Low and reverse solenoid
valve
(2) 0%, (4) 0%, (3)
0% Underdrive solenoid valve
Page 367 of 1575
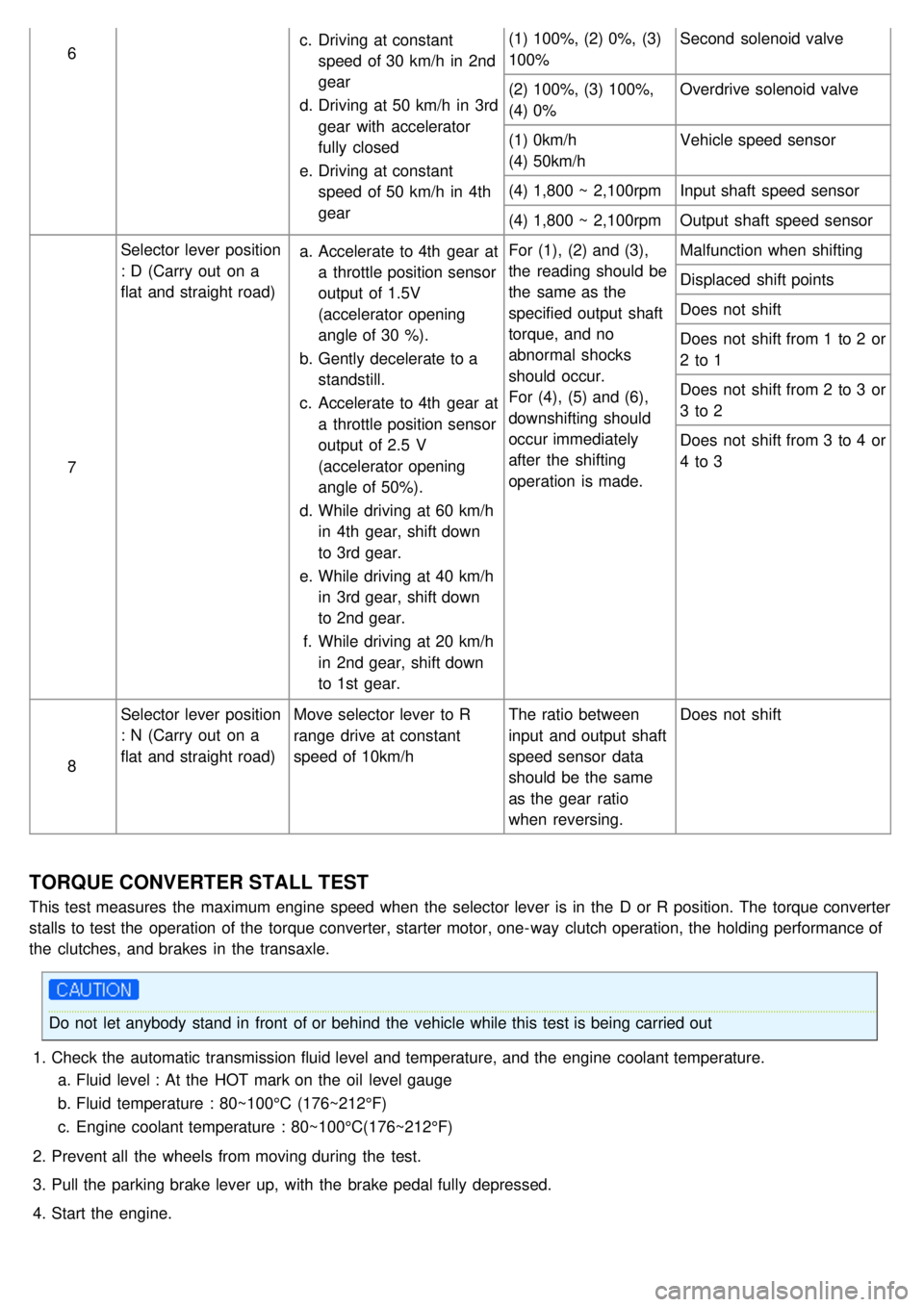
6c.
Driving at constant
speed of 30 km/h in 2nd
gear
d. Driving at 50 km/h in 3rd
gear with accelerator
fully closed
e. Driving at constant
speed of 50 km/h in 4th
gear (1) 100%, (2) 0%, (3)
100%
Second solenoid valve
(2) 100%, (3) 100%,
(4) 0% Overdrive solenoid valve
(1) 0km/h
(4) 50km/h Vehicle speed sensor
(4) 1,800 ~ 2,100rpm Input shaft speed sensor
(4) 1,800 ~ 2,100rpm Output shaft speed sensor
7 Selector lever position
: D (Carry out on a
flat and straight road)
a.
Accelerate to 4th gear at
a throttle position sensor
output of 1.5V
(accelerator opening
angle of 30 %).
b. Gently decelerate to a
standstill.
c. Accelerate to 4th gear at
a throttle position sensor
output of 2.5 V
(accelerator opening
angle of 50%).
d. While driving at 60 km/h
in 4th gear, shift down
to 3rd gear.
e. While driving at 40 km/h
in 3rd gear, shift down
to 2nd gear.
f. While driving at 20 km/h
in 2nd gear, shift down
to 1st gear. For (1), (2) and (3),
the reading should be
the same as the
specified output shaft
torque, and no
abnormal shocks
should occur.
For (4), (5) and (6),
downshifting should
occur immediately
after the shifting
operation is made.
Malfunction when shifting
Displaced shift points
Does not shift
Does not shift from 1 to 2 or
2 to 1
Does not shift from 2 to 3 or
3 to 2
Does not shift from 3 to 4 or
4 to 3
8 Selector lever position
: N (Carry out on a
flat and straight road)
Move selector lever to R
range drive at constant
speed of 10km/h The ratio between
input and output shaft
speed sensor data
should be the same
as the gear ratio
when reversing.Does not shift
TORQUE CONVERTER STALL TEST
This test measures the maximum engine speed when the selector lever is in the D or R position. The torque converter
stalls to test the operation of the torque converter, starter motor, one- way clutch operation, the holding performance of
the clutches, and brakes in the transaxle.
Do not let anybody stand in front of or behind the vehicle while this test is being carried out
1. Check the automatic transmission fluid level and temperature, and the engine coolant temperature.
a. Fluid level : At the HOT mark on the oil level gauge
b. Fluid temperature : 80~100°C (176~212°F)
c. Engine coolant temperature : 80~100°C(176~212°F)
2. Prevent all the wheels from moving during the test.
3. Pull the parking brake lever up, with the brake pedal fully depressed.
4. Start the engine.
Page 368 of 1575
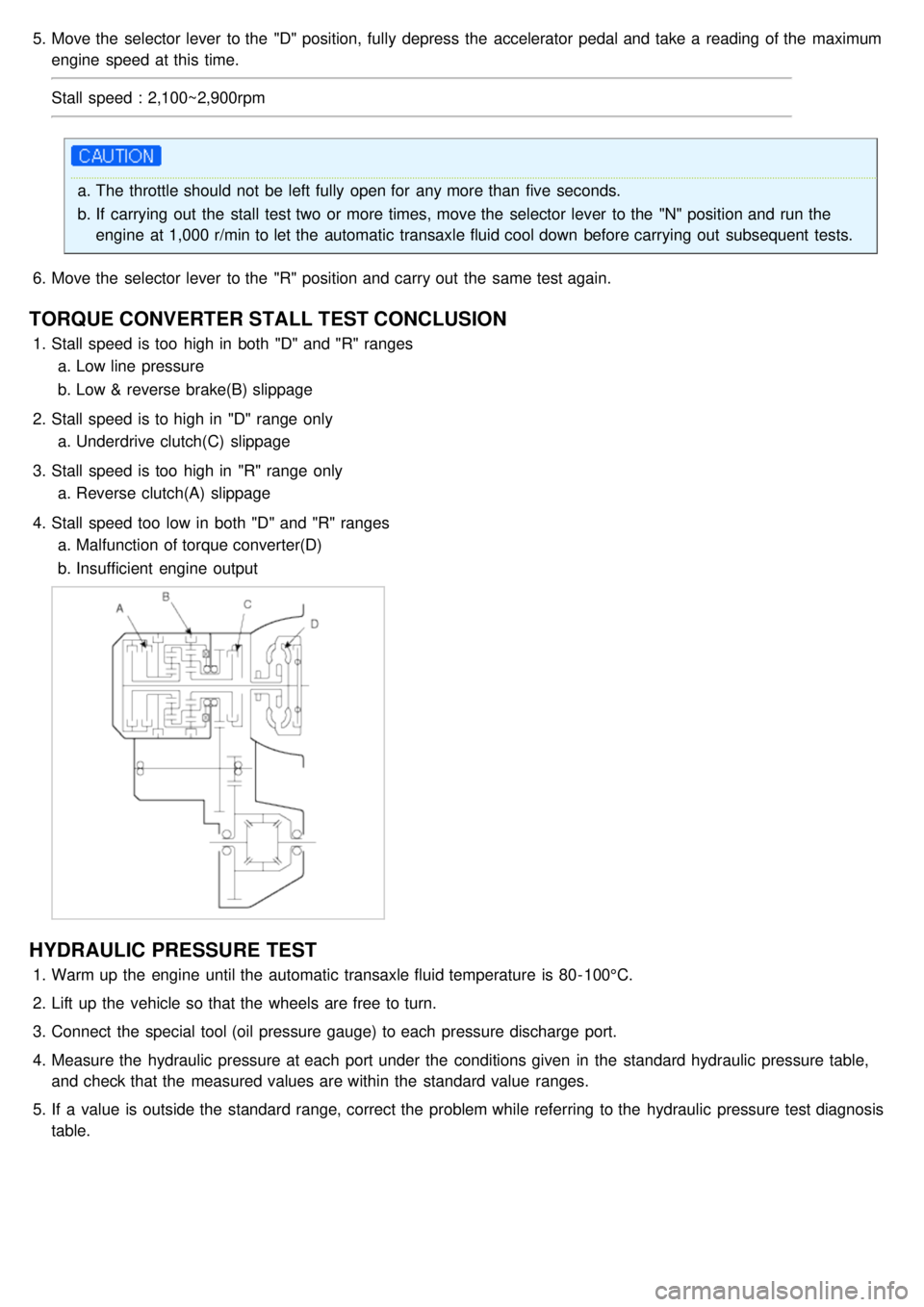
5.Move the selector lever to the "D" position, fully depress the accelerator pedal and take a reading of the maximum
engine speed at this time.
Stall speed : 2,100~2,900rpm
a.The throttle should not be left fully open for any more than five seconds.
b. If carrying out the stall test two or more times, move the selector lever to the "N" position and run the
engine at 1,000 r/min to let the automatic transaxle fluid cool down before carrying out subsequent tests.
6. Move the selector lever to the "R" position and carry out the same test again.
TORQUE CONVERTER STALL TEST CONCLUSION
1.Stall speed is too high in both "D" and "R" ranges
a. Low line pressure
b. Low & reverse brake(B) slippage
2. Stall speed is to high in "D" range only
a. Underdrive clutch(C) slippage
3. Stall speed is too high in "R" range only
a. Reverse clutch(A) slippage
4. Stall speed too low in both "D" and "R" ranges
a. Malfunction of torque converter(D)
b. Insufficient engine output
HYDRAULIC PRESSURE TEST
1.Warm up the engine until the automatic transaxle fluid temperature is 80- 100°C.
2. Lift up the vehicle so that the wheels are free to turn.
3. Connect the special tool (oil pressure gauge) to each pressure discharge port.
4. Measure the hydraulic pressure at each port under the conditions given in the standard hydraulic pressure table,
and check that the measured values are within the standard value ranges.
5. If a value is outside the standard range, correct the problem while referring to the hydraulic pressure test diagnosis
table.
Page 371 of 1575
![KIA CARNIVAL 2007 Service Manual 2007 > 2.7L V6 GASOLINE >
SERVICE ADJUSTMENT PROCEDURE
Automatic transaxle fluid
INSPECTION 1. Drive the vehicle until the fluid reaches normal operating temperature [70~80°C].
2. Place the KIA CARNIVAL 2007 Service Manual 2007 > 2.7L V6 GASOLINE >
SERVICE ADJUSTMENT PROCEDURE
Automatic transaxle fluid
INSPECTION 1. Drive the vehicle until the fluid reaches normal operating temperature [70~80°C].
2. Place the](/img/2/57045/w960_57045-370.png)
2007 > 2.7L V6 GASOLINE >
SERVICE ADJUSTMENT PROCEDURE
Automatic transaxle fluid
INSPECTION 1. Drive the vehicle until the fluid reaches normal operating temperature [70~80°C].
2. Place the vehicle on a level surface.
3. Move the selector lever through all gear positions. This will fill the torque converter and the hudraulic system with
fluid and move the selector lever to the "N" (Neutral) or "P"(Park) position.
4. Before removing the oil level gauge, wipe all contaminants from around the oil level gauge. Then take out the oil
level gauge and check the condition of the fluid.
If the fluid smells as if it is burning, it means that the fluid has been contaminated by fine particles from the
bushes and friction materials, a transaxle overhaul may be necessary.
5. Check that the fluid level is at the HOT mark on the oil level gauge. If the fluid level is low, add automatic transaxle
fluid until the level reaches the "HOT" mark.
Auto transaxle fluid:
DIAMOND ATF SP - III, SK ATF SP - III
Quantity : 8.5ℓ (9.0 US qt, 7.5 lmp.qt)
Low fluid level can cause a variety of a abnormal conditions because it allows the pump to take in air along
with fluid. Air trapped in the hydraulic system forms bubbles, which are compressable. Therefore, pressures
will be erratic, causing delayed shifting ,slipping clutches and brakes, etc. Improper filling can also raise fluid
level too high. When the transaxle has too much fluid, gears churn up foam and acuise the same conditions
which occur with low fluid level, resulting in accelerated deterioration of automatic transaxle fluid. In either
case, air bubbles can cause overheating, and fluid oxidation, which can interfere with normal valve, clutch, and
brake operation. Foaming can also result in fluid escaping from the transaxle vent where it may be mistaken
for a leak.
6. Insert the oil level gauge(A) securely.
When new, automatic transmission fluid should be red. The red dye is added so the assembly plant can
identify it as transmission fluid and distinguish it from engine oil or antifreeze. The red dye, which is not an
indicator of fluid quality, is not permanent. As the vehicle is driven the transmission fluid will begin to look
darker. The color may eventually appear light brown.
Page 372 of 1575
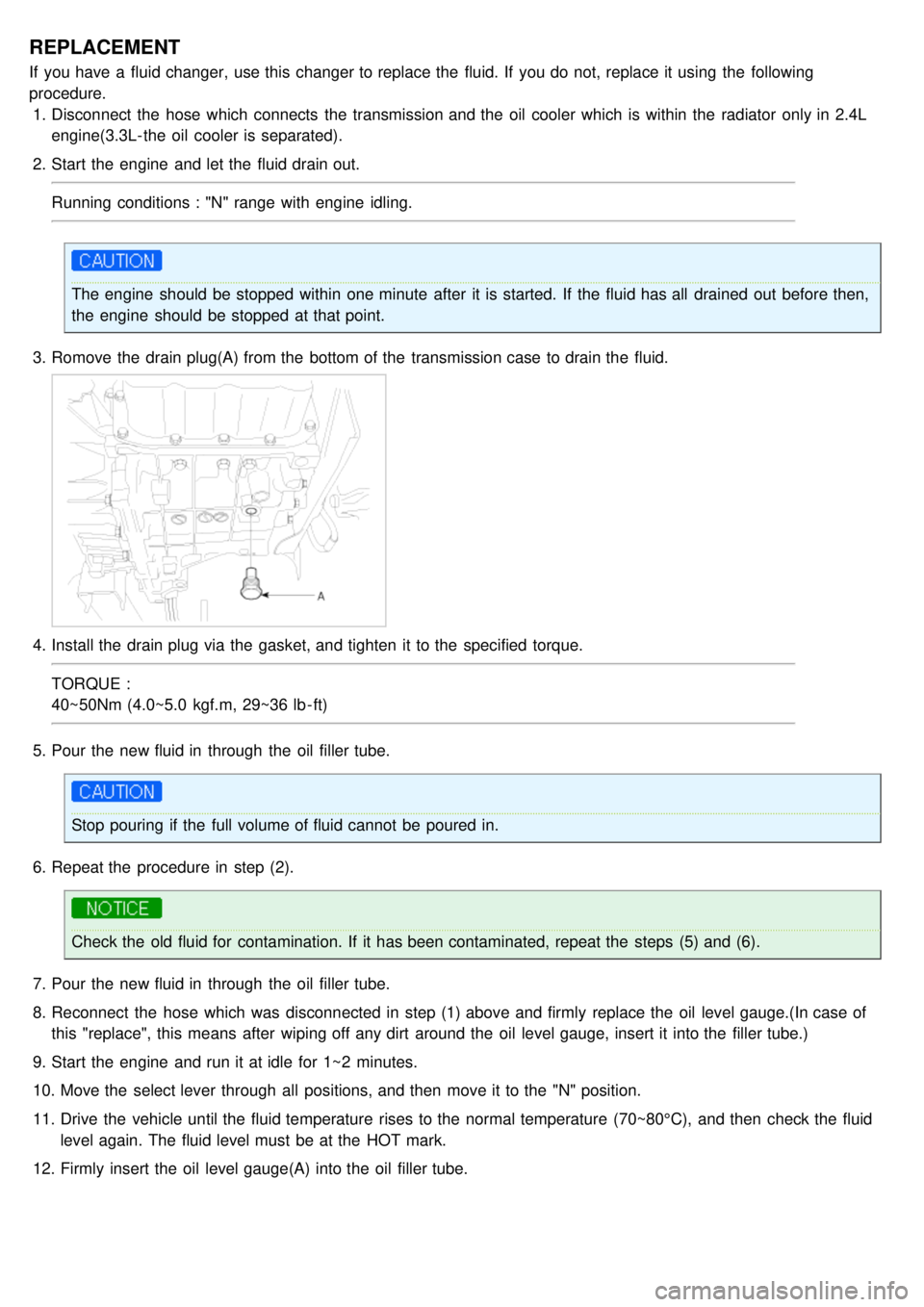
REPLACEMENT
If you have a fluid changer, use this changer to replace the fluid. If you do not, replace it using the following
procedure.1. Disconnect the hose which connects the transmission and the oil cooler which is within the radiator only in 2.4L
engine(3.3L- the oil cooler is separated).
2. Start the engine and let the fluid drain out.
Running conditions : "N" range with engine idling.
The engine should be stopped within one minute after it is started. If the fluid has all drained out before then,
the engine should be stopped at that point.
3. Romove the drain plug(A) from the bottom of the transmission case to drain the fluid.
4.Install the drain plug via the gasket, and tighten it to the specified torque.
TORQUE :
40~50Nm (4.0~5.0 kgf.m, 29~36 lb - ft)
5. Pour the new fluid in through the oil filler tube.
Stop pouring if the full volume of fluid cannot be poured in.
6. Repeat the procedure in step (2).
Check the old fluid for contamination. If it has been contaminated, repeat the steps (5) and (6).
7. Pour the new fluid in through the oil filler tube.
8. Reconnect the hose which was disconnected in step (1) above and firmly replace the oil level gauge.(In case of
this "replace", this means after wiping off any dirt around the oil level gauge, insert it into the filler tube.)
9. Start the engine and run it at idle for 1~2 minutes.
10. Move the select lever through all positions, and then move it to the "N" position.
11. Drive the vehicle until the fluid temperature rises to the normal temperature (70~80°C), and then check the fluid
level again. The fluid level must be at the HOT mark.
12. Firmly insert the oil level gauge(A) into the oil filler tube.
Page 421 of 1575
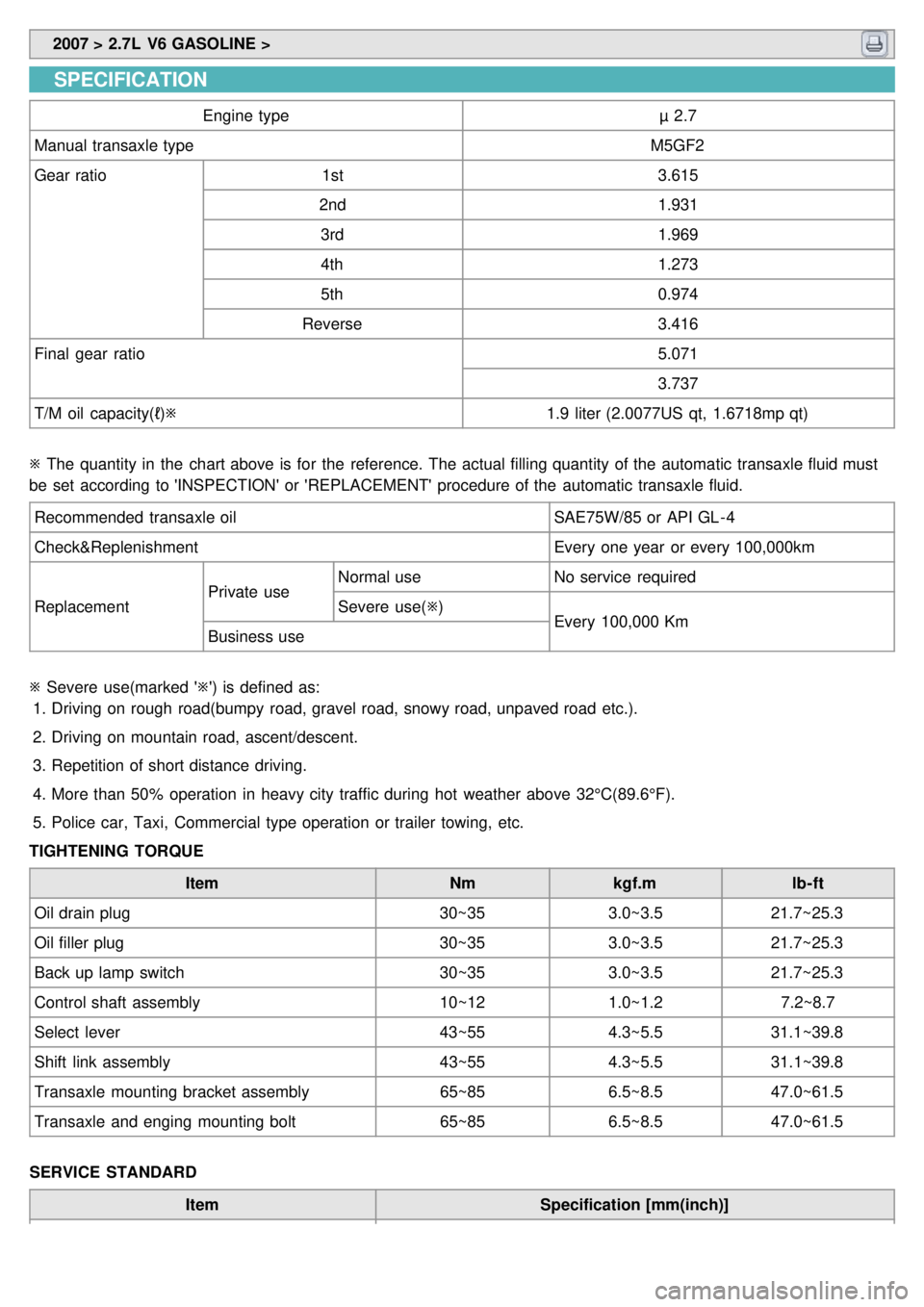
2007 > 2.7L V6 GASOLINE >
SPECIFICATION
Engine type µ 2.7
Manual transaxle type M5GF2
Gear ratio 1st 3.615
2nd 1.931
3rd 1.969
4th 1.273
5th 0.974
Reverse 3.416
Final gear ratio 5.071
3.737
T/M oil capacity(ℓ) ※ 1.9 liter (2.0077US qt, 1.6718mp qt)
※ The quantity in the chart above is for the reference. The actual filling quantity of the automatic transaxle fluid must
be set according to 'INSPECTION' or 'REPLACEMENT' procedure of the automatic transaxle fluid.
Recommended transaxle oil SAE75W/85 or API GL - 4
Check&Replenishment Every one year or every 100,000km
Replacement Private useNormal use
No service required
Severe use( ※)
Every 100,000 Km
Business use
※ Severe use(marked '※') is defined as:
1. Driving on rough road(bumpy road, gravel road, snowy road, unpaved road etc.).
2. Driving on mountain road, ascent/descent.
3. Repetition of short distance driving.
4. More than 50% operation in heavy city traffic during hot weather above 32°C(89.6°F).
5. Police car, Taxi, Commercial type operation or trailer towing, etc.
TIGHTENING TORQUE
Item Nmkgf.m lb- ft
Oil drain plug 30~353.0~3.521.7~25.3
Oil filler plug 30~353.0~3.521.7~25.3
Back up lamp switch 30~353.0~3.521.7~25.3
Control shaft assembly 10~121.0~1.2 7.2~8.7
Select lever 43~554.3~5.531.1~39.8
Shift link assembly 43~554.3~5.531.1~39.8
Transaxle mounting bracket assembly 65~856.5~8.547.0~61.5
Transaxle and enging mounting bolt 65~856.5~8.547.0~61.5
SERVICE STANDARD Item Specification [mm(inch)]