check engine KIA CARNIVAL 2007 Owner's Manual
[x] Cancel search | Manufacturer: KIA, Model Year: 2007, Model line: CARNIVAL, Model: KIA CARNIVAL 2007Pages: 1575, PDF Size: 44.86 MB
Page 125 of 1575
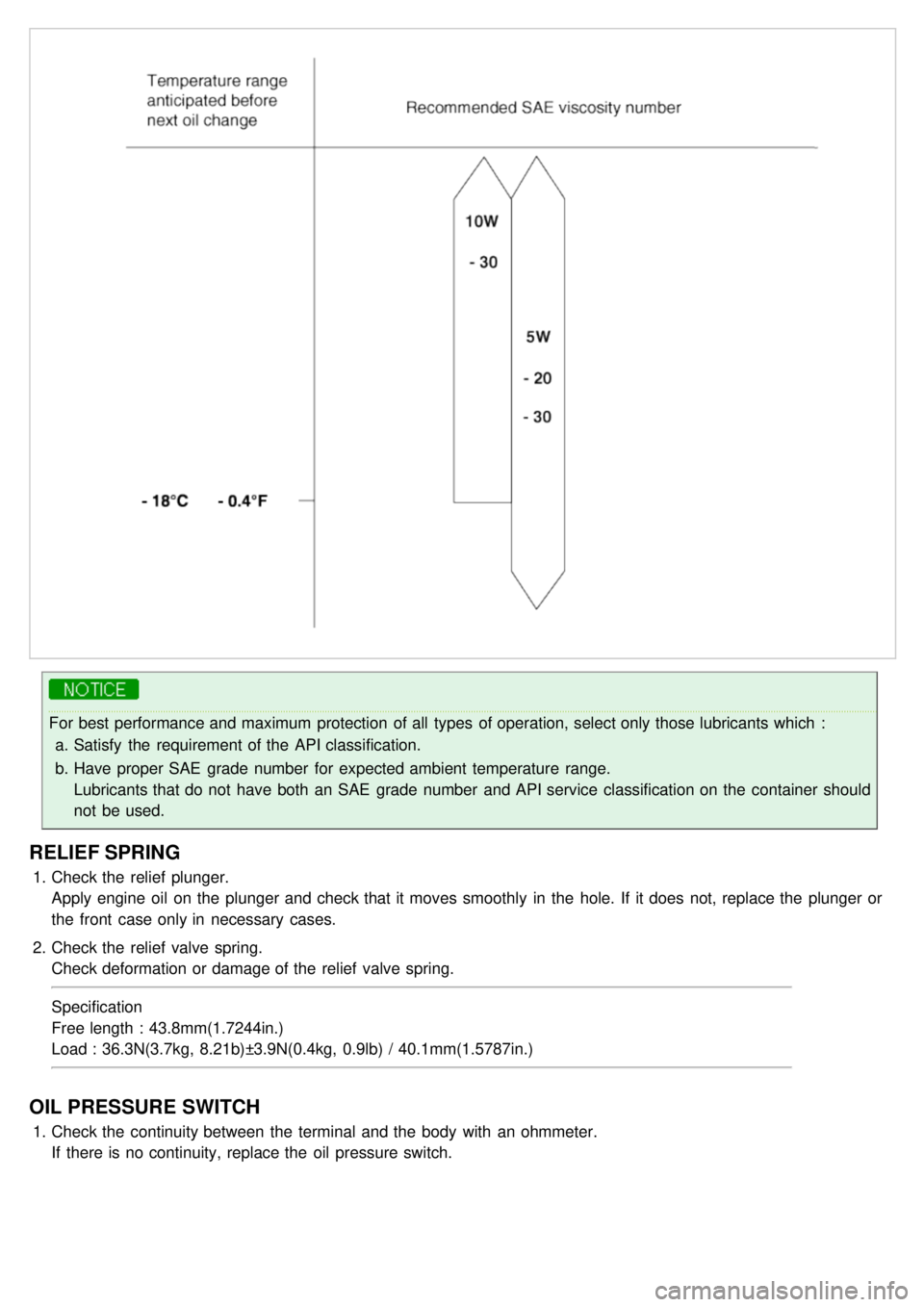
For best performance and maximum protection of all types of operation, select only those lubricants which :a. Satisfy the requirement of the API classification.
b. Have proper SAE grade number for expected ambient temperature range.
Lubricants that do not have both an SAE grade number and API service classification on the container should
not be used.
RELIEF SPRING
1.Check the relief plunger.
Apply engine oil on the plunger and check that it moves smoothly in the hole. If it does not, replace the plunger or
the front case only in necessary cases.
2. Check the relief valve spring.
Check deformation or damage of the relief valve spring.
Specification
Free length : 43.8mm(1.7244in.)
Load : 36.3N(3.7kg, 8.21b)±3.9N(0.4kg, 0.9lb) / 40.1mm(1.5787in.)
OIL PRESSURE SWITCH
1.Check the continuity between the terminal and the body with an ohmmeter.
If there is no continuity, replace the oil pressure switch.
Page 137 of 1575
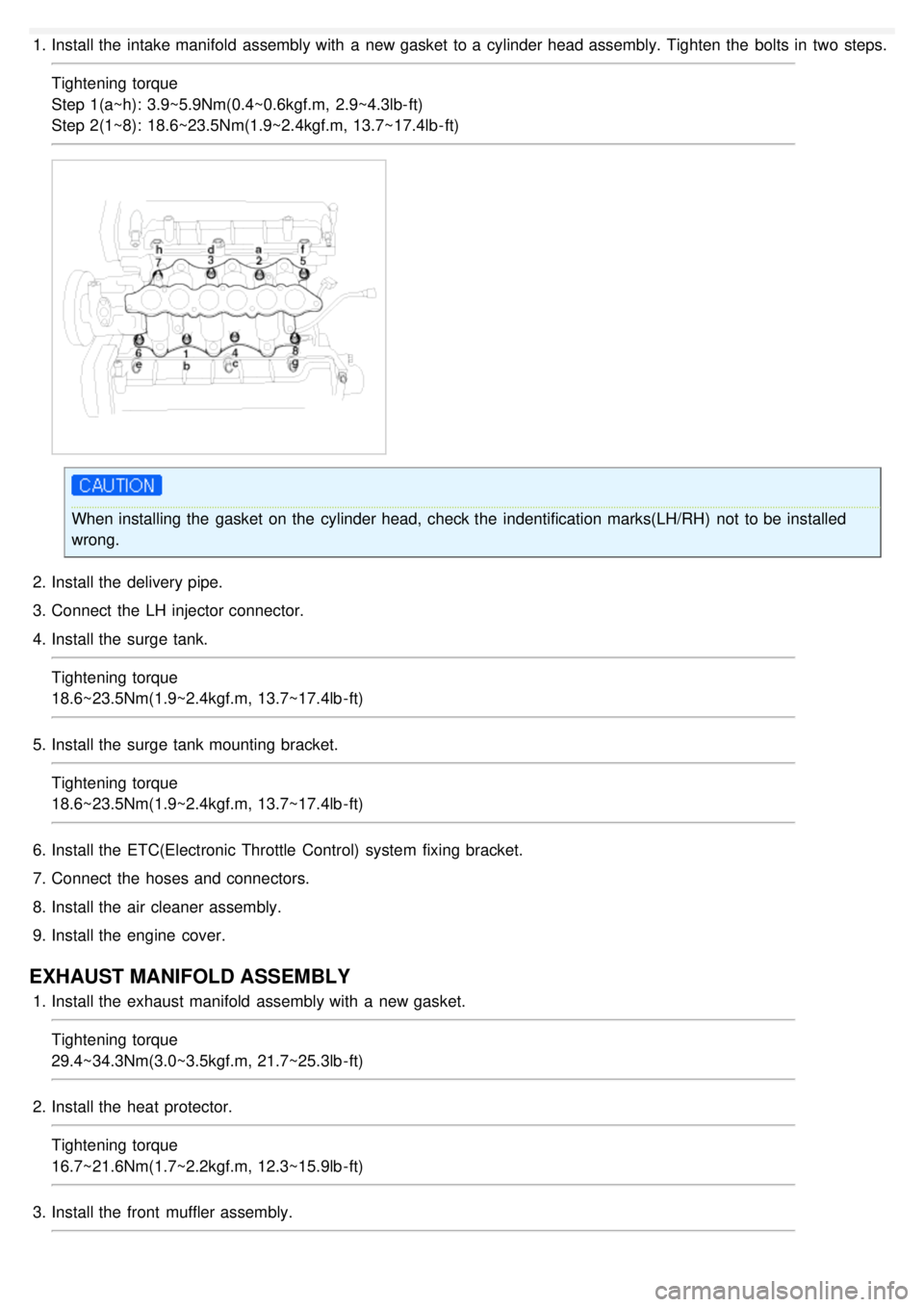
1.Install the intake manifold assembly with a new gasket to a cylinder head assembly. Tighten the bolts in two steps.
Tightening torque
Step 1(a~h): 3.9~5.9Nm(0.4~0.6kgf.m, 2.9~4.3lb- ft)
Step 2(1~8): 18.6~23.5Nm(1.9~2.4kgf.m, 13.7~17.4lb - ft)
When installing the gasket on the cylinder head, check the indentification marks(LH/RH) not to be installed
wrong.
2. Install the delivery pipe.
3. Connect the LH injector connector.
4. Install the surge tank.
Tightening torque
18.6~23.5Nm(1.9~2.4kgf.m, 13.7~17.4lb - ft)
5. Install the surge tank mounting bracket.
Tightening torque
18.6~23.5Nm(1.9~2.4kgf.m, 13.7~17.4lb - ft)
6. Install the ETC(Electronic Throttle Control) system fixing bracket.
7. Connect the hoses and connectors.
8. Install the air cleaner assembly.
9. Install the engine cover.
EXHAUST MANIFOLD ASSEMBLY
1.Install the exhaust manifold assembly with a new gasket.
Tightening torque
29.4~34.3Nm(3.0~3.5kgf.m, 21.7~25.3lb - ft)
2. Install the heat protector.
Tightening torque
16.7~21.6Nm(1.7~2.2kgf.m, 12.3~15.9lb - ft)
3. Install the front muffler assembly.
Page 144 of 1575
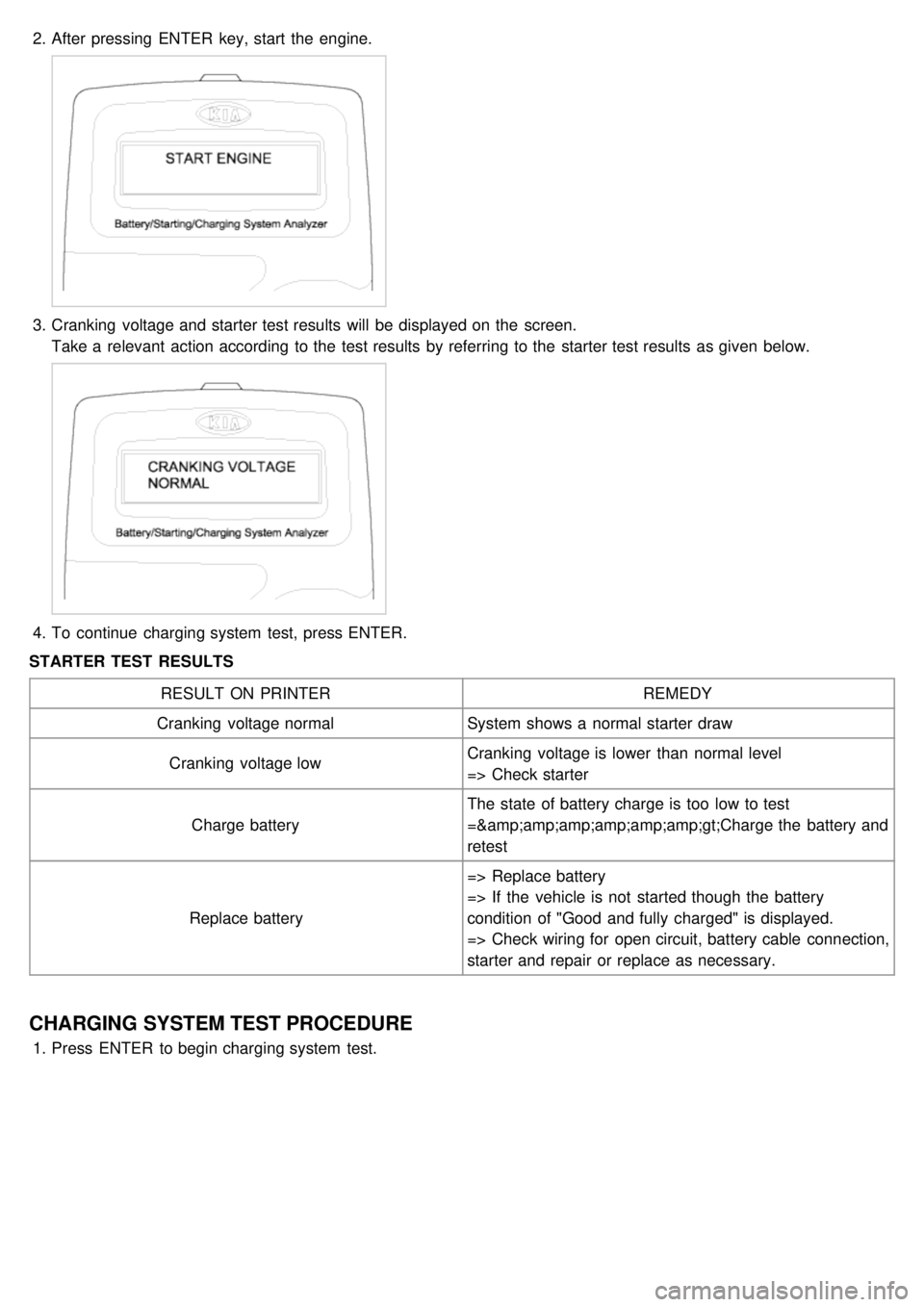
2.After pressing ENTER key, start the engine.
3.Cranking voltage and starter test results will be displayed on the screen.
Take a relevant action according to the test results by referring to the starter test results as given below.
4.To continue charging system test, press ENTER.
STARTER TEST RESULTS
RESULT ON PRINTER REMEDY
Cranking voltage normal System shows a normal starter draw
Cranking voltage low Cranking voltage is lower than normal level
=> Check starter
Charge battery The state of battery charge is too low to test
=>Charge the battery and
retest
Replace battery => Replace battery
=> If the vehicle is not started though the battery
condition of "Good and fully charged" is displayed.
=> Check wiring for open circuit, battery cable connection,
starter and repair or replace as necessary.
CHARGING SYSTEM TEST PROCEDURE
1.
Press ENTER to begin charging system test.
Page 149 of 1575
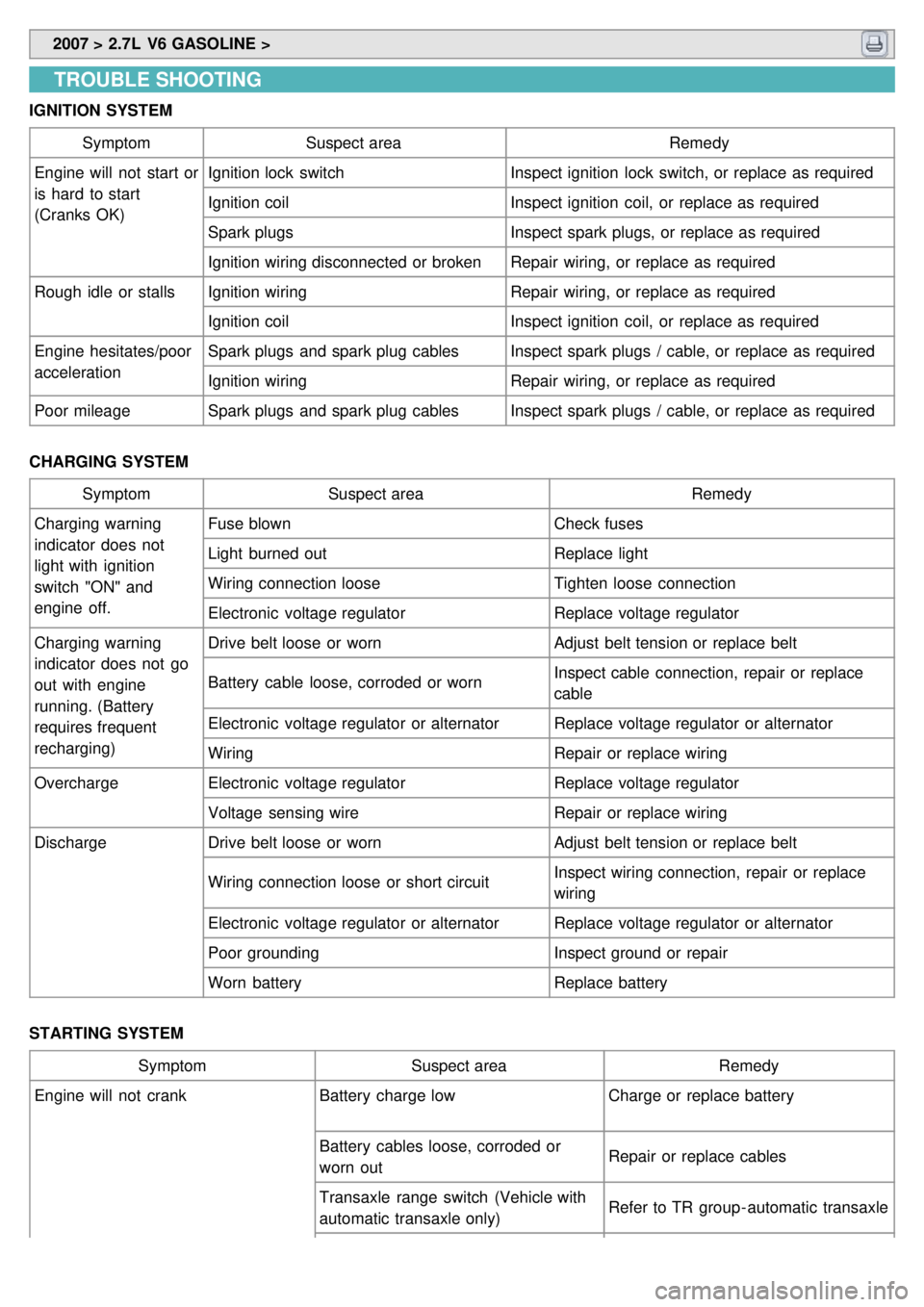
2007 > 2.7L V6 GASOLINE >
TROUBLE SHOOTING
IGNITION SYSTEM
Symptom Suspect area Remedy
Engine will not start or
is hard to start
(Cranks OK) Ignition lock switch
Inspect ignition lock switch, or replace as required
Ignition coil Inspect ignition coil, or replace as required
Spark plugs Inspect spark plugs, or replace as required
Ignition wiring disconnected or broken Repair wiring, or replace as required
Rough idle or stalls Ignition wiring Repair wiring, or replace as required
Ignition coil Inspect ignition coil, or replace as required
Engine hesitates/poor
acceleration Spark plugs and spark plug cables
Inspect spark plugs / cable, or replace as required
Ignition wiring Repair wiring, or replace as required
Poor mileage Spark plugs and spark plug cables Inspect spark plugs / cable, or replace as required
CHARGING SYSTEM Symptom Suspect area Remedy
Charging warning
indicator does not
light with ignition
switch "ON" and
engine off. Fuse blown
Check fuses
Light burned out Replace light
Wiring connection loose Tighten loose connection
Electronic voltage regulator Replace voltage regulator
Charging warning
indicator does not go
out with engine
running. (Battery
requires frequent
recharging) Drive belt loose or worn
Adjust belt tension or replace belt
Battery cable loose, corroded or worn Inspect cable connection, repair or replace
cable
Electronic voltage regulator or alternator Replace voltage regulator or alternator
Wiring Repair or replace wiring
Overcharge Electronic voltage regulator Replace voltage regulator
Voltage sensing wire Repair or replace wiring
Discharge Drive belt loose or worn Adjust belt tension or replace belt
Wiring connection loose or short circuit Inspect wiring connection, repair or replace
wiring
Electronic voltage regulator or alternator Replace voltage regulator or alternator
Poor grounding Inspect ground or repair
Worn battery Replace battery
STARTING SYSTEM Symptom Suspect area Remedy
Engine will not crank Battery charge low Charge or replace battery
Battery cables loose, corroded or
worn out Repair or replace cables
Transaxle range switch (Vehicle with
automatic transaxle only) Refer to TR group - automatic transaxle
Page 155 of 1575
![KIA CARNIVAL 2007 Owners Manual a.[U2.7]
L nleaded : ILFR5B11
Leaded : LFR5A
ON-VEHICLE INSPECTION
SPARK TEST
1. Remove the ignition coil connector(A).
Disconnect the iguition coil connector while pulling up tre connector KIA CARNIVAL 2007 Owners Manual a.[U2.7]
L nleaded : ILFR5B11
Leaded : LFR5A
ON-VEHICLE INSPECTION
SPARK TEST
1. Remove the ignition coil connector(A).
Disconnect the iguition coil connector while pulling up tre connector](/img/2/57045/w960_57045-154.png)
a.[U2.7]
L nleaded : ILFR5B11
Leaded : LFR5A
ON-VEHICLE INSPECTION
SPARK TEST
1. Remove the ignition coil connector(A).
Disconnect the iguition coil connector while pulling up tre connector lock.
2. Remove the ignition coil.
3. Using a spark plug socket, remove the spark plug.
4. Install the spark plug to the ignition coil.
5. Ground the spark plug to the engine.
6.Check is spark occurs while engine is being cranked.
To prevent fuel being injected from injectors while the engine is being cranked, remove the fuel pump(A) relay
from the fuse box.
Crank the engine for no more than 5 ~ 10 seconds.
7. Inspect all the spark plugs.
8. Using a spark plug socket, install the spark plug.
9. Install the ignition coil.
10. Reconnect the ignition coil connector.
Page 160 of 1575
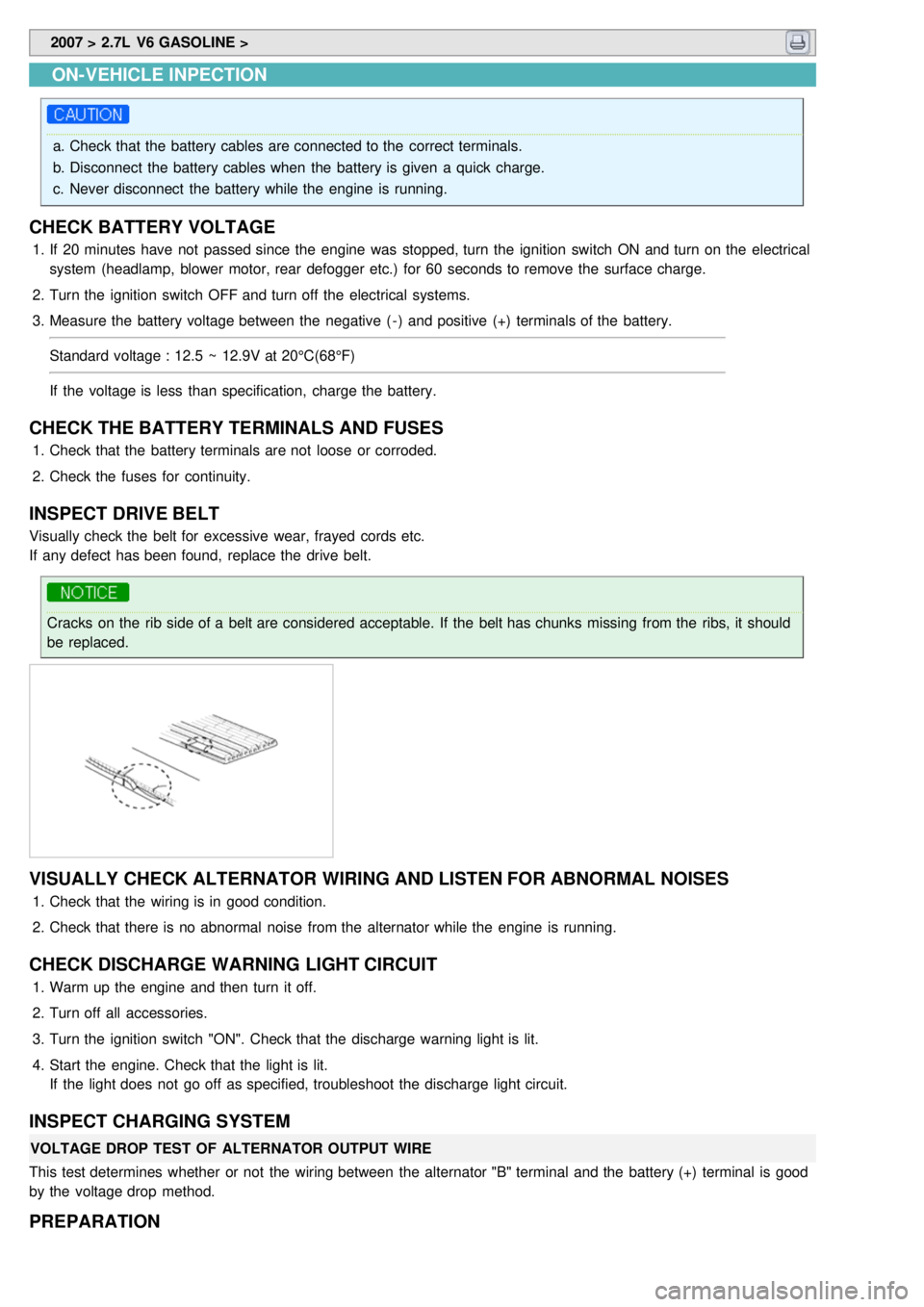
2007 > 2.7L V6 GASOLINE >
ON-VEHICLE INPECTION
a.Check that the battery cables are connected to the correct terminals.
b. Disconnect the battery cables when the battery is given a quick charge.
c. Never disconnect the battery while the engine is running.
CHECK BATTERY VOLTAGE
1.If 20 minutes have not passed since the engine was stopped, turn the ignition switch ON and turn on the electrical
system (headlamp, blower motor, rear defogger etc.) for 60 seconds to remove the surface charge.
2. Turn the ignition switch OFF and turn off the electrical systems.
3. Measure the battery voltage between the negative ( - ) and positive (+) terminals of the battery.
Standard voltage : 12.5 ~ 12.9V at 20°C(68°F)
If the voltage is less than specification, charge the battery.
CHECK THE BATTERY TERMINALS AND FUSES
1.Check that the battery terminals are not loose or corroded.
2. Check the fuses for continuity.
INSPECT DRIVE BELT
Visually check the belt for excessive wear, frayed cords etc.
If any defect has been found, replace the drive belt.
Cracks on the rib side of a belt are considered acceptable. If the belt has chunks missing from the ribs, it should
be replaced.
VISUALLY CHECK ALTERNATOR WIRING AND LISTEN FOR ABNORMAL NOISES
1.Check that the wiring is in good condition.
2. Check that there is no abnormal noise from the alternator while the engine is running.
CHECK DISCHARGE WARNING LIGHT CIRCUIT
1.Warm up the engine and then turn it off.
2. Turn off all accessories.
3. Turn the ignition switch "ON". Check that the discharge warning light is lit.
4. Start the engine. Check that the light is lit.
If the light does not go off as specified, troubleshoot the discharge light circuit.
INSPECT CHARGING SYSTEM
VOLTAGE DROP TEST OF ALTERNATOR OUTPUT WIRE
This test determines whether or not the wiring between the alternator "B" terminal and the battery (+) terminal is good
by the voltage drop method.
PREPARATION
Page 161 of 1575
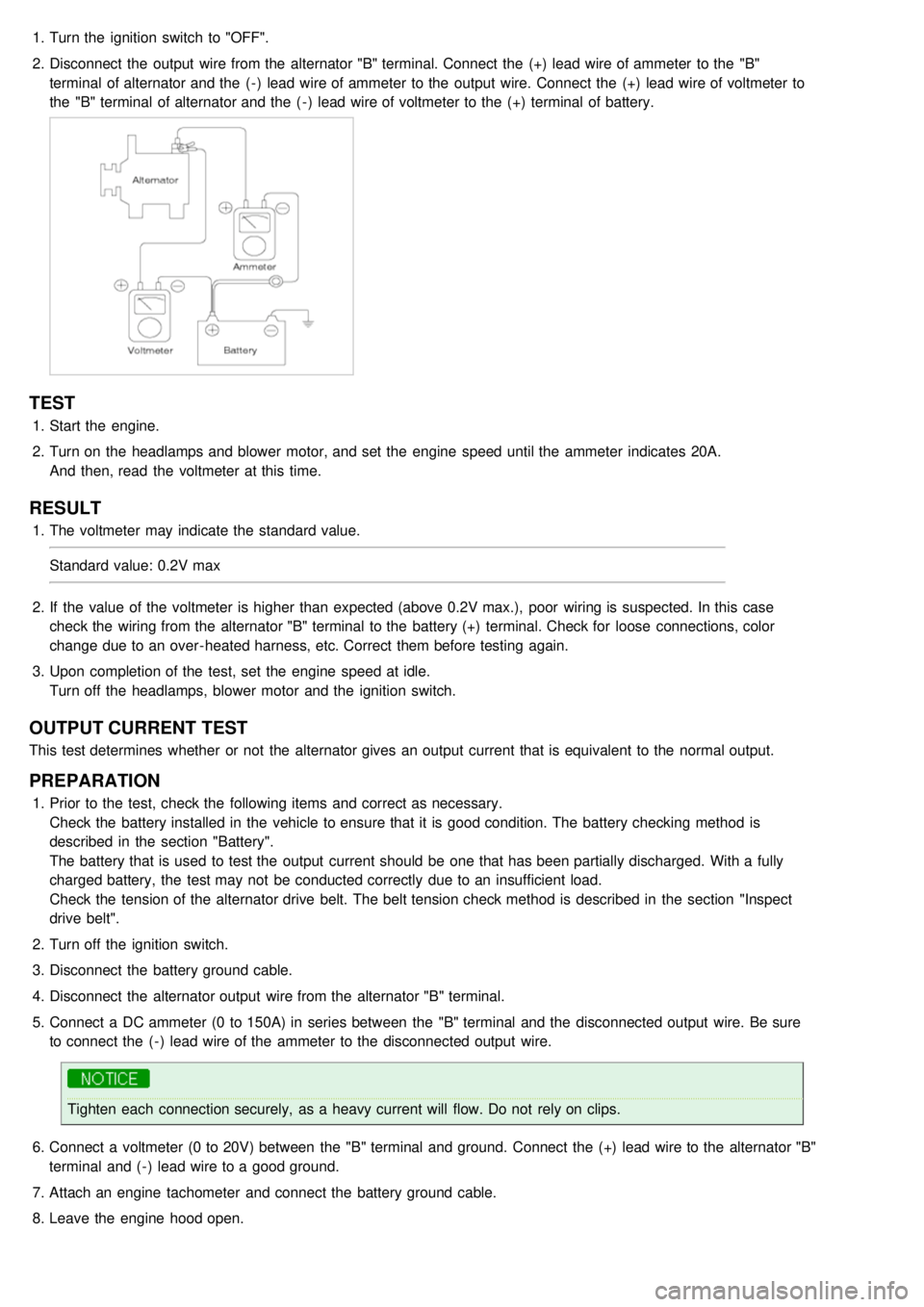
1.Turn the ignition switch to "OFF".
2. Disconnect the output wire from the alternator "B" terminal. Connect the (+) lead wire of ammeter to the "B"
terminal of alternator and the ( - ) lead wire of ammeter to the output wire. Connect the (+) lead wire of voltmeter to
the "B" terminal of alternator and the ( - ) lead wire of voltmeter to the (+) terminal of battery.
TEST
1.Start the engine.
2. Turn on the headlamps and blower motor, and set the engine speed until the ammeter indicates 20A.
And then, read the voltmeter at this time.
RESULT
1.The voltmeter may indicate the standard value.
Standard value: 0.2V max
2. If the value of the voltmeter is higher than expected (above 0.2V max.), poor wiring is suspected. In this case
check the wiring from the alternator "B" terminal to the battery (+) terminal. Check for loose connections, color
change due to an over - heated harness, etc. Correct them before testing again.
3. Upon completion of the test, set the engine speed at idle.
Turn off the headlamps, blower motor and the ignition switch.
OUTPUT CURRENT TEST
This test determines whether or not the alternator gives an output current that is equivalent to the normal output.
PREPARATION
1.Prior to the test, check the following items and correct as necessary.
Check the battery installed in the vehicle to ensure that it is good condition. The battery checking method is
described in the section "Battery".
The battery that is used to test the output current should be one that has been partially discharged. With a fully
charged battery, the test may not be conducted correctly due to an insufficient load.
Check the tension of the alternator drive belt. The belt tension check method is described in the section "Inspect
drive belt".
2. Turn off the ignition switch.
3. Disconnect the battery ground cable.
4. Disconnect the alternator output wire from the alternator "B" terminal.
5. Connect a DC ammeter (0 to 150A) in series between the "B" terminal and the disconnected output wire. Be sure
to connect the ( - ) lead wire of the ammeter to the disconnected output wire.
Tighten each connection securely, as a heavy current will flow. Do not rely on clips.
6. Connect a voltmeter (0 to 20V) between the "B" terminal and ground. Connect the (+) lead wire to the alternator "B"
terminal and ( - ) lead wire to a good ground.
7. Attach an engine tachometer and connect the battery ground cable.
8. Leave the engine hood open.
Page 162 of 1575
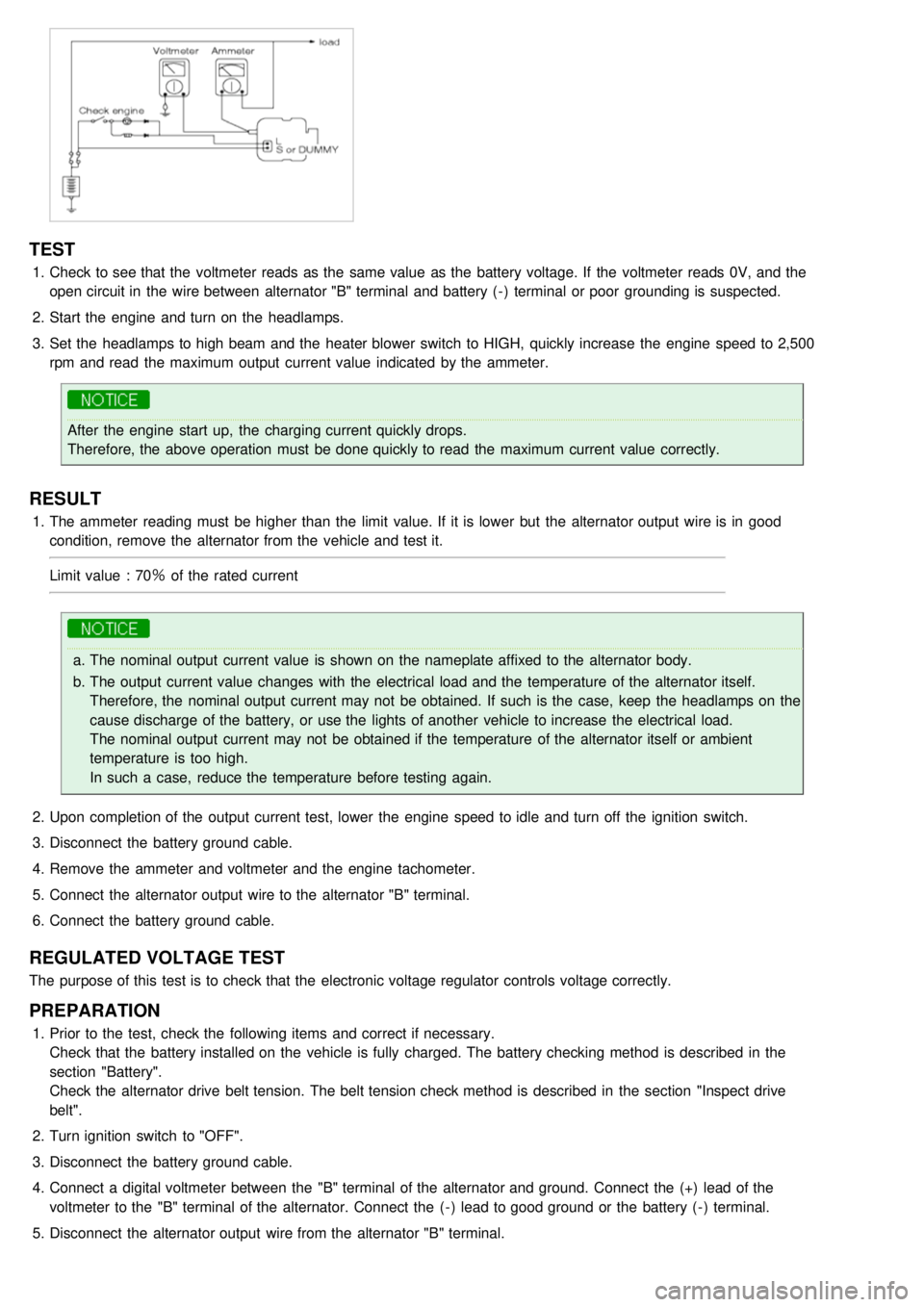
TEST
1.Check to see that the voltmeter reads as the same value as the battery voltage. If the voltmeter reads 0V, and the
open circuit in the wire between alternator "B" terminal and battery ( - ) terminal or poor grounding is suspected.
2. Start the engine and turn on the headlamps.
3. Set the headlamps to high beam and the heater blower switch to HIGH, quickly increase the engine speed to 2,500
rpm and read the maximum output current value indicated by the ammeter.
After the engine start up, the charging current quickly drops.
Therefore, the above operation must be done quickly to read the maximum current value correctly.
RESULT
1.The ammeter reading must be higher than the limit value. If it is lower but the alternator output wire is in good
condition, remove the alternator from the vehicle and test it.
Limit value : 70Ë of the rated current
a.The nominal output current value is shown on the nameplate affixed to the alternator body.
b. The output current value changes with the electrical load and the temperature of the alternator itself.
Therefore, the nominal output current may not be obtained. If such is the case, keep the headlamps on the
cause discharge of the battery, or use the lights of another vehicle to increase the electrical load.
The nominal output current may not be obtained if the temperature of the alternator itself or ambient
temperature is too high.
In such a case, reduce the temperature before testing again.
2. Upon completion of the output current test, lower the engine speed to idle and turn off the ignition switch.
3. Disconnect the battery ground cable.
4. Remove the ammeter and voltmeter and the engine tachometer.
5. Connect the alternator output wire to the alternator "B" terminal.
6. Connect the battery ground cable.
REGULATED VOLTAGE TEST
The purpose of this test is to check that the electronic voltage regulator controls voltage correctly.
PREPARATION
1.Prior to the test, check the following items and correct if necessary.
Check that the battery installed on the vehicle is fully charged. The battery checking method is described in the
section "Battery".
Check the alternator drive belt tension. The belt tension check method is described in the section "Inspect drive
belt".
2. Turn ignition switch to "OFF".
3. Disconnect the battery ground cable.
4. Connect a digital voltmeter between the "B" terminal of the alternator and ground. Connect the (+) lead of the
voltmeter to the "B" terminal of the alternator. Connect the ( - ) lead to good ground or the battery ( - ) terminal.
5. Disconnect the alternator output wire from the alternator "B" terminal.
Page 163 of 1575
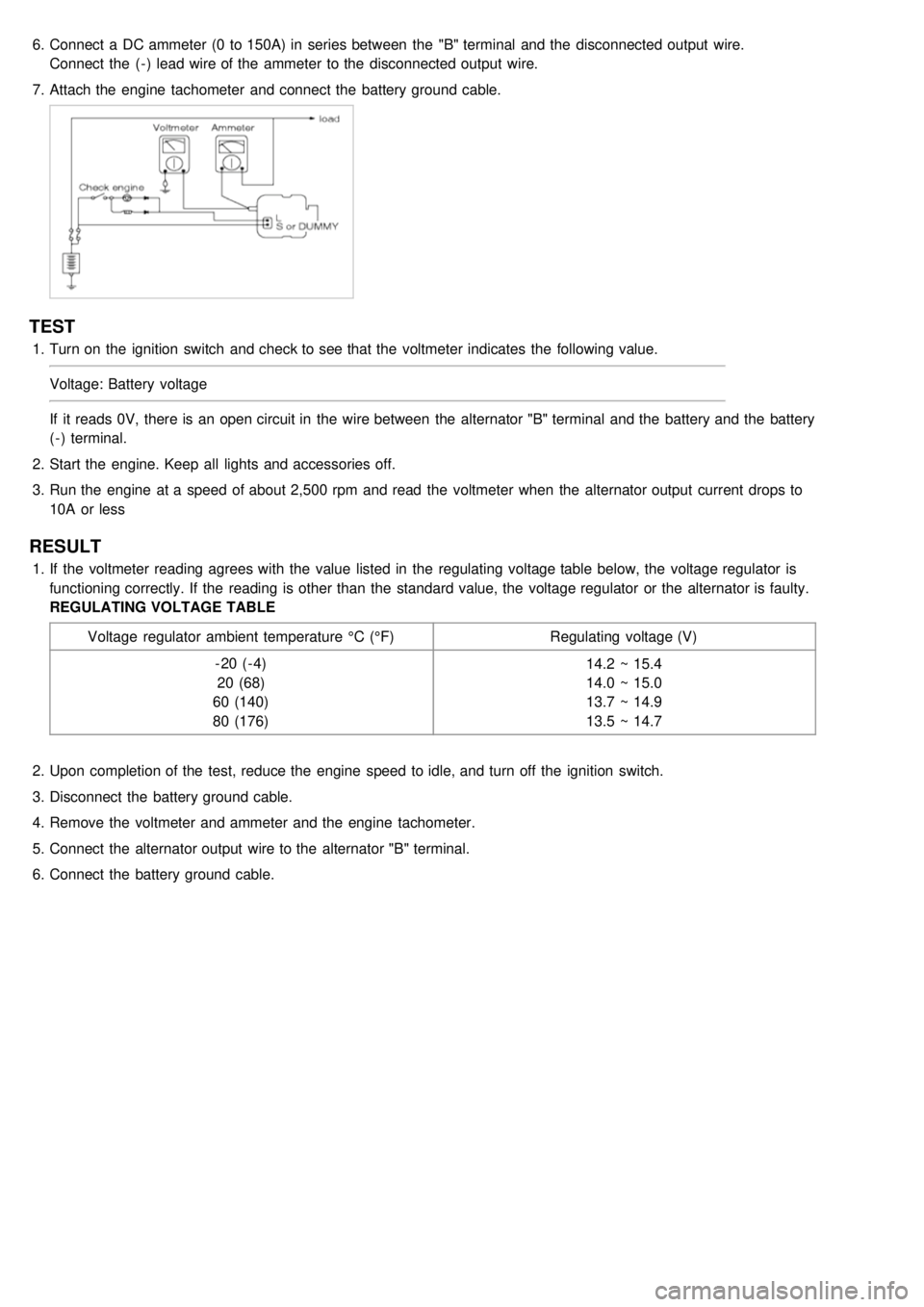
6.Connect a DC ammeter (0 to 150A) in series between the "B" terminal and the disconnected output wire.
Connect the ( - ) lead wire of the ammeter to the disconnected output wire.
7. Attach the engine tachometer and connect the battery ground cable.
TEST
1.Turn on the ignition switch and check to see that the voltmeter indicates the following value.
Voltage: Battery voltage
If it reads 0V, there is an open circuit in the wire between the alternator "B" terminal and the battery and the battery
( - ) terminal.
2. Start the engine. Keep all lights and accessories off.
3. Run the engine at a speed of about 2,500 rpm and read the voltmeter when the alternator output current drops to
10A or less
RESULT
1.If the voltmeter reading agrees with the value listed in the regulating voltage table below, the voltage regulator is
functioning correctly. If the reading is other than the standard value, the voltage regulator or the alternator is faulty.
REGULATING VOLTAGE TABLE
Voltage regulator ambient temperature °C (°F) Regulating voltage (V)
- 20 ( - 4) 20 (68)
60 (140)
80 (176) 14.2 ~ 15.4
14.0 ~ 15.0
13.7 ~ 14.9
13.5 ~ 14.7
2. Upon completion of the test, reduce the engine speed to idle, and turn off the ignition switch.
3. Disconnect the battery ground cable.
4. Remove the voltmeter and ammeter and the engine tachometer.
5. Connect the alternator output wire to the alternator "B" terminal.
6. Connect the battery ground cable.
Page 176 of 1575
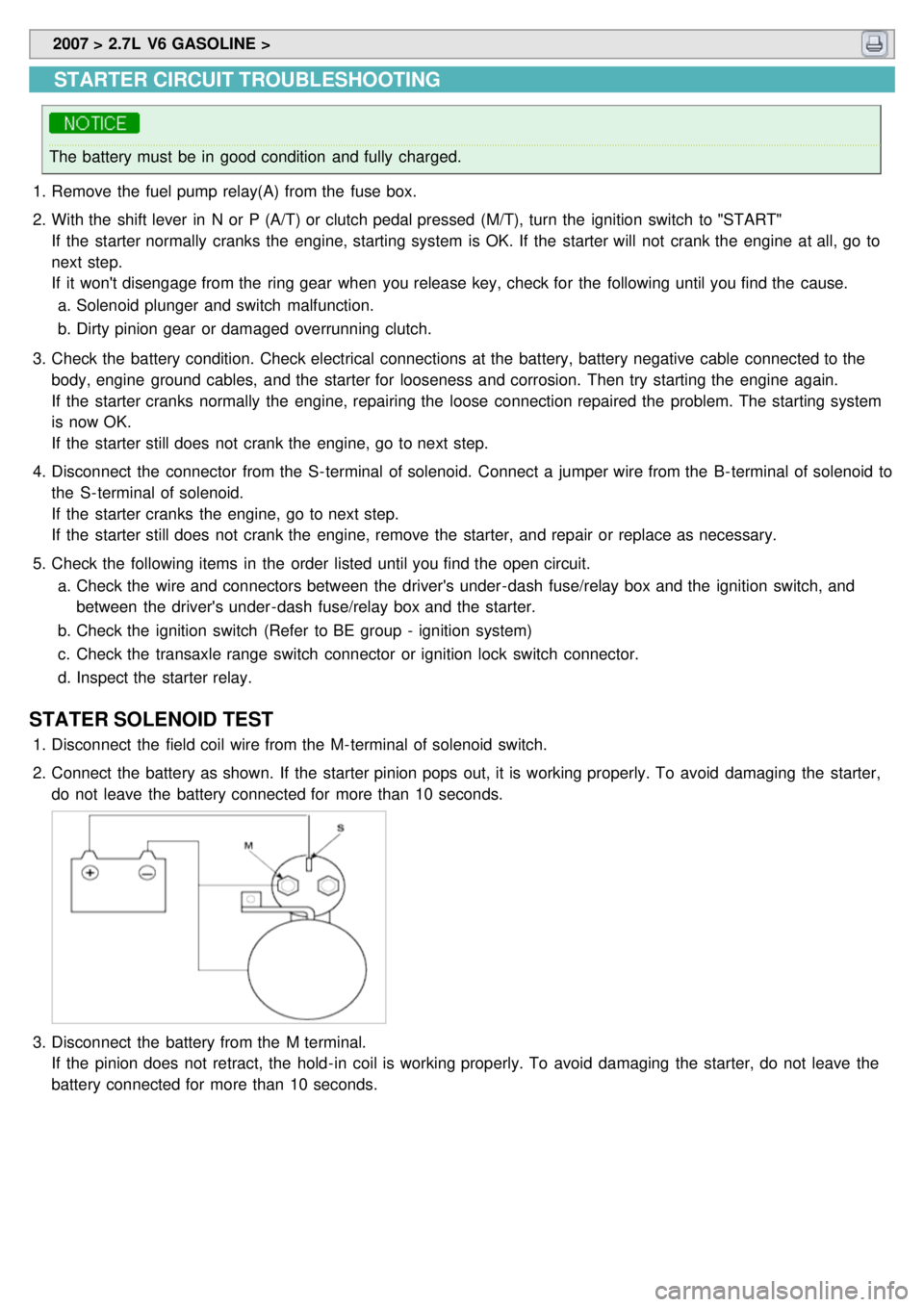
2007 > 2.7L V6 GASOLINE >
STARTER CIRCUIT TROUBLESHOOTING
The battery must be in good condition and fully charged.
1. Remove the fuel pump relay(A) from the fuse box.
2. With the shift lever in N or P (A/T) or clutch pedal pressed (M/T), turn the ignition switch to "START"
If the starter normally cranks the engine, starting system is OK. If the starter will not crank the engine at all, go to
next step.
If it won't disengage from the ring gear when you release key, check for the following until you find the cause.
a. Solenoid plunger and switch malfunction.
b. Dirty pinion gear or damaged overrunning clutch.
3. Check the battery condition. Check electrical connections at the battery, battery negative cable connected to the
body, engine ground cables, and the starter for looseness and corrosion. Then try starting the engine again.
If the starter cranks normally the engine, repairing the loose connection repaired the problem. The starting system
is now OK.
If the starter still does not crank the engine, go to next step.
4. Disconnect the connector from the S- terminal of solenoid. Connect a jumper wire from the B- terminal of solenoid to
the S- terminal of solenoid.
If the starter cranks the engine, go to next step.
If the starter still does not crank the engine, remove the starter, and repair or replace as necessary.
5. Check the following items in the order listed until you find the open circuit.
a. Check the wire and connectors between the driver's under - dash fuse/relay box and the ignition switch, and
between the driver's under - dash fuse/relay box and the starter.
b. Check the ignition switch (Refer to BE group - ignition system)
c. Check the transaxle range switch connector or ignition lock switch connector.
d. Inspect the starter relay.
STATER SOLENOID TEST
1.Disconnect the field coil wire from the M- terminal of solenoid switch.
2. Connect the battery as shown. If the starter pinion pops out, it is working properly. To avoid damaging the starter,
do not leave the battery connected for more than 10 seconds.
3.Disconnect the battery from the M terminal.
If the pinion does not retract, the hold- in coil is working properly. To avoid damaging the starter, do not leave the
battery connected for more than 10 seconds.