low oil pressure KIA CARNIVAL 2007 Workshop Manual
[x] Cancel search | Manufacturer: KIA, Model Year: 2007, Model line: CARNIVAL, Model: KIA CARNIVAL 2007Pages: 1575, PDF Size: 44.86 MB
Page 9 of 1575
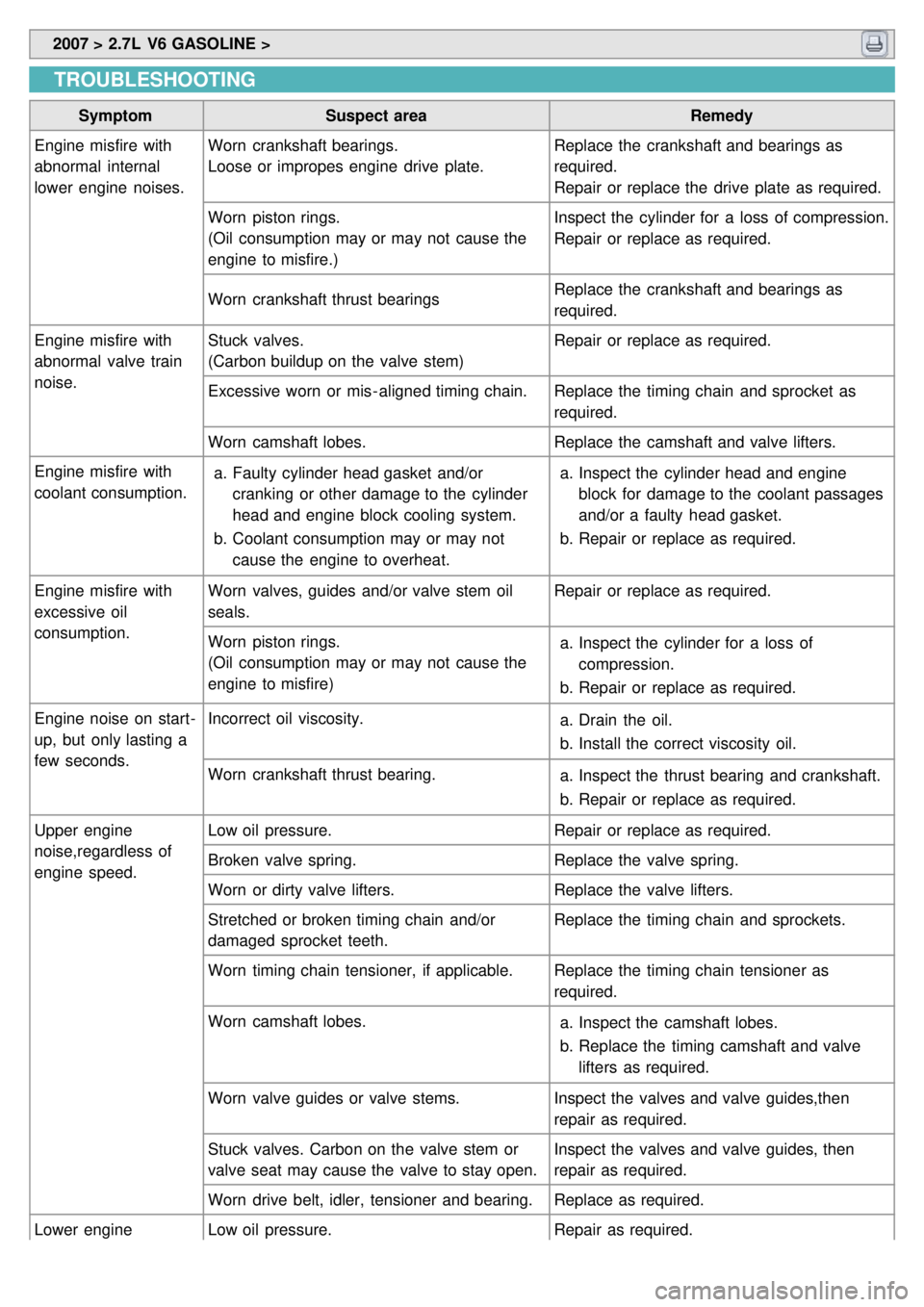
2007 > 2.7L V6 GASOLINE >
TROUBLESHOOTING
Symptom Suspect area Remedy
Engine misfire with
abnormal internal
lower engine noises. Worn crankshaft bearings.
Loose or impropes engine drive plate.
Replace the crankshaft and bearings as
required.
Repair or replace the drive plate as required.
Worn piston rings.
(Oil consumption may or may not cause the
engine to misfire.) Inspect the cylinder for a loss of compression.
Repair or replace as required.
Worn crankshaft thrust bearings Replace the crankshaft and bearings as
required.
Engine misfire with
abnormal valve train
noise. Stuck valves.
(Carbon buildup on the valve stem)
Repair or replace as required.
Excessive worn or mis - aligned timing chain. Replace the timing chain and sprocket as
required.
Worn camshaft lobes. Replace the camshaft and valve lifters.
Engine misfire with
coolant consumption. a.
Faulty cylinder head gasket and/or
cranking or other damage to the cylinder
head and engine block cooling system.
b. Coolant consumption may or may not
cause the engine to overheat. a.
Inspect the cylinder head and engine
block for damage to the coolant passages
and/or a faulty head gasket.
b. Repair or replace as required.
Engine misfire with
excessive oil
consumption. Worn valves, guides and/or valve stem oil
seals.
Repair or replace as required.
Worn piston rings.
(Oil consumption may or may not cause the
engine to misfire) a.
Inspect the cylinder for a loss of
compression.
b. Repair or replace as required.
Engine noise on start -
up, but only lasting a
few seconds. Incorrect oil viscosity.
a.Drain the oil.
b. Install the correct viscosity oil.
Worn crankshaft thrust bearing. a.Inspect the thrust bearing and crankshaft.
b. Repair or replace as required.
Upper engine
noise,regardless of
engine speed. Low oil pressure.
Repair or replace as required.
Broken valve spring. Replace the valve spring.
Worn or dirty valve lifters. Replace the valve lifters.
Stretched or broken timing chain and/or
damaged sprocket teeth. Replace the timing chain and sprockets.
Worn timing chain tensioner, if applicable. Replace the timing chain tensioner as
required.
Worn camshaft lobes. a.Inspect the camshaft lobes.
b. Replace the timing camshaft and valve
lifters as required.
Worn valve guides or valve stems. Inspect the valves and valve guides,then
repair as required.
Stuck valves. Carbon on the valve stem or
valve seat may cause the valve to stay open. Inspect the valves and valve guides, then
repair as required.
Worn drive belt, idler, tensioner and bearing. Replace as required.
Lower engine
noise,regardless of Low oil pressure.
Repair as required.
Page 10 of 1575
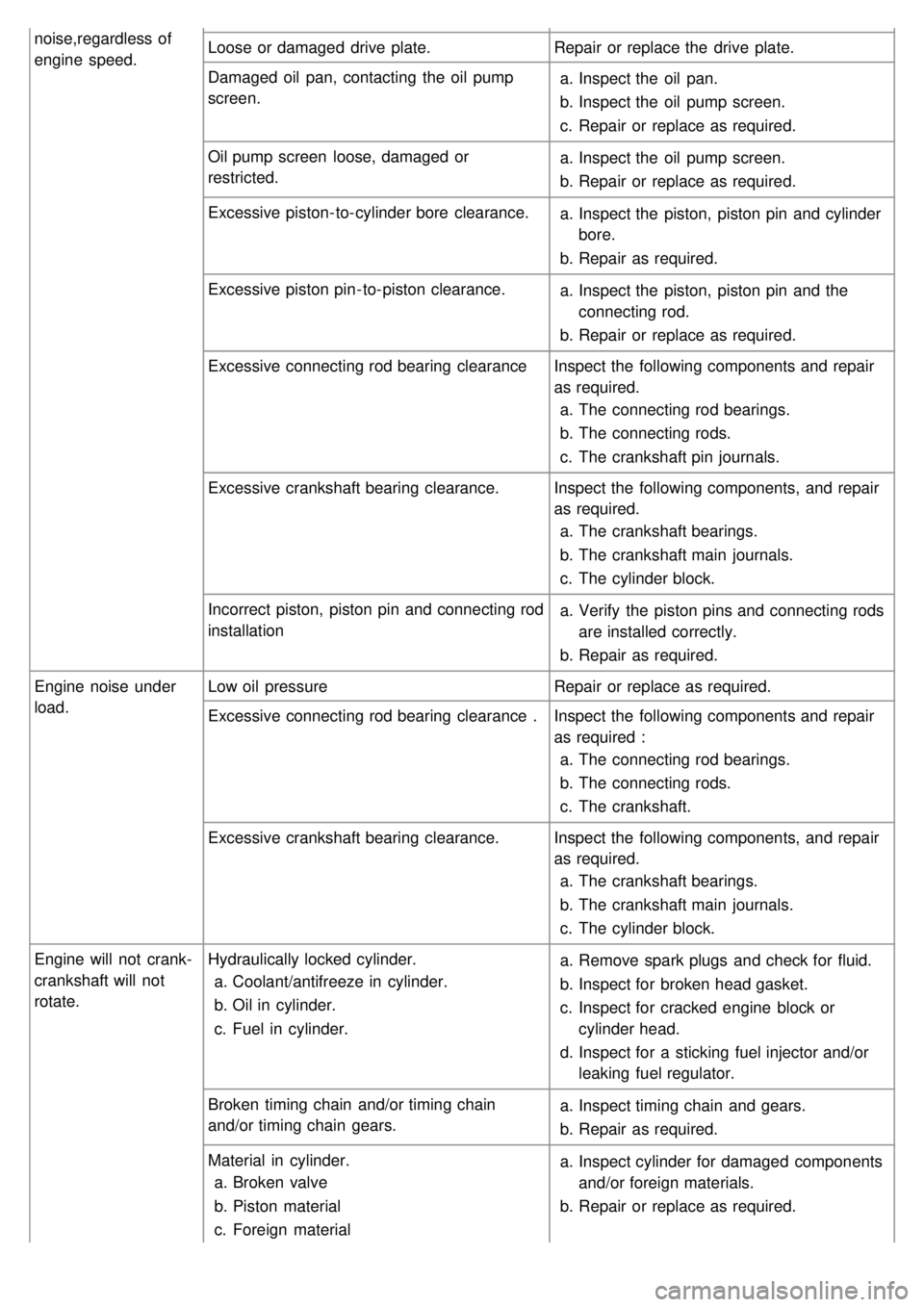
noise,regardless of
engine speed.Loose or damaged drive plate.
Repair or replace the drive plate.
Damaged oil pan, contacting the oil pump
screen. a.
Inspect the oil pan.
b. Inspect the oil pump screen.
c. Repair or replace as required.
Oil pump screen loose, damaged or
restricted. a.
Inspect the oil pump screen.
b. Repair or replace as required.
Excessive piston- to- cylinder bore clearance. a.Inspect the piston, piston pin and cylinder
bore.
b. Repair as required.
Excessive piston pin- to- piston clearance. a.Inspect the piston, piston pin and the
connecting rod.
b. Repair or replace as required.
Excessive connecting rod bearing clearance Inspect the following components and repair
as required.
a. The connecting rod bearings.
b. The connecting rods.
c. The crankshaft pin journals.
Excessive crankshaft bearing clearance. Inspect the following components, and repair
as required.
a. The crankshaft bearings.
b. The crankshaft main journals.
c. The cylinder block.
Incorrect piston, piston pin and connecting rod
installation a.
Verify the piston pins and connecting rods
are installed correctly.
b. Repair as required.
Engine noise under
load. Low oil pressure
Repair or replace as required.
Excessive connecting rod bearing clearance . Inspect the following components and repair
as required :
a. The connecting rod bearings.
b. The connecting rods.
c. The crankshaft.
Excessive crankshaft bearing clearance. Inspect the following components, and repair
as required.
a. The crankshaft bearings.
b. The crankshaft main journals.
c. The cylinder block.
Engine will not crank-
crankshaft will not
rotate. Hydraulically locked cylinder.
a. Coolant/antifreeze in cylinder.
b. Oil in cylinder.
c. Fuel in cylinder. a.
Remove spark plugs and check for fluid.
b. Inspect for broken head gasket.
c. Inspect for cracked engine block or
cylinder head.
d. Inspect for a sticking fuel injector and/or
leaking fuel regulator.
Broken timing chain and/or timing chain
and/or timing chain gears. a.
Inspect timing chain and gears.
b. Repair as required.
Material in cylinder. a. Broken valve
b. Piston material
c. Foreign material a.
Inspect cylinder for damaged components
and/or foreign materials.
b. Repair or replace as required.
Page 12 of 1575
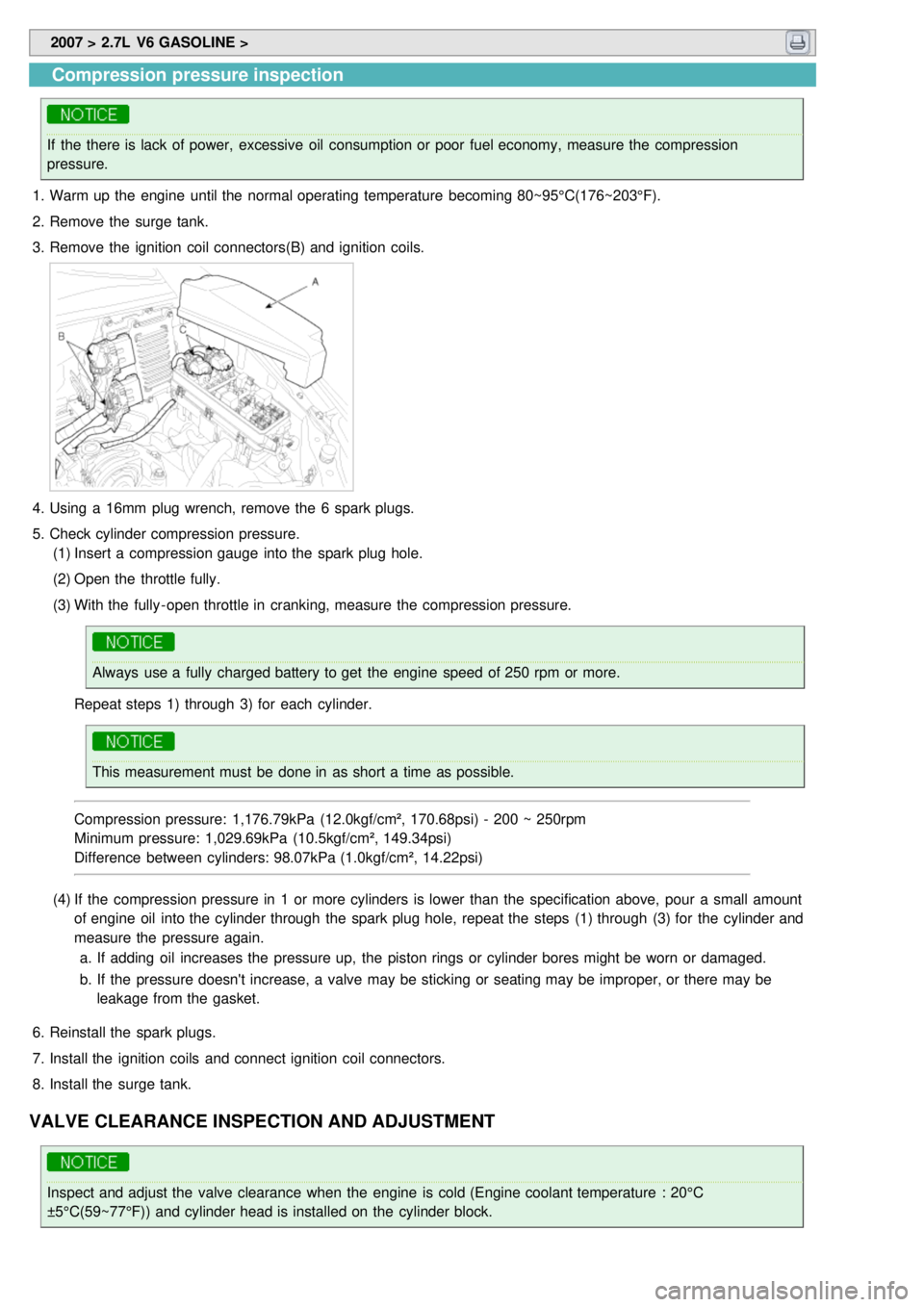
2007 > 2.7L V6 GASOLINE >
Compression pressure inspection
If the there is lack of power, excessive oil consumption or poor fuel economy, measure the compression
pressure.
1. Warm up the engine until the normal operating temperature becoming 80~95°C(176~203°F).
2. Remove the surge tank.
3. Remove the ignition coil connectors(B) and ignition coils.
4.Using a 16mm plug wrench, remove the 6 spark plugs.
5. Check cylinder compression pressure.
(1) Insert a compression gauge into the spark plug hole.
(2) Open the throttle fully.
(3) With the fully - open throttle in cranking, measure the compression pressure.
Always use a fully charged battery to get the engine speed of 250 rpm or more.
Repeat steps 1) through 3) for each cylinder.
This measurement must be done in as short a time as possible.
Compression pressure: 1,176.79kPa (12.0kgf/cm², 170.68psi) - 200 ~ 250rpm
Minimum pressure: 1,029.69kPa (10.5kgf/cm², 149.34psi)
Difference between cylinders: 98.07kPa (1.0kgf/cm², 14.22psi)
(4) If the compression pressure in 1 or more cylinders is lower than the specification above, pour a small amount
of engine oil into the cylinder through the spark plug hole, repeat the steps (1) through (3) for the cylinder and
measure the pressure again.
a. If adding oil increases the pressure up, the piston rings or cylinder bores might be worn or damaged.
b. If the pressure doesn't increase, a valve may be sticking or seating may be improper, or there may be
leakage from the gasket.
6. Reinstall the spark plugs.
7. Install the ignition coils and connect ignition coil connectors.
8. Install the surge tank.
VALVE CLEARANCE INSPECTION AND ADJUSTMENT
Inspect and adjust the valve clearance when the engine is cold (Engine coolant temperature : 20°C
±5°C(59~77°F)) and cylinder head is installed on the cylinder block.
Page 19 of 1575
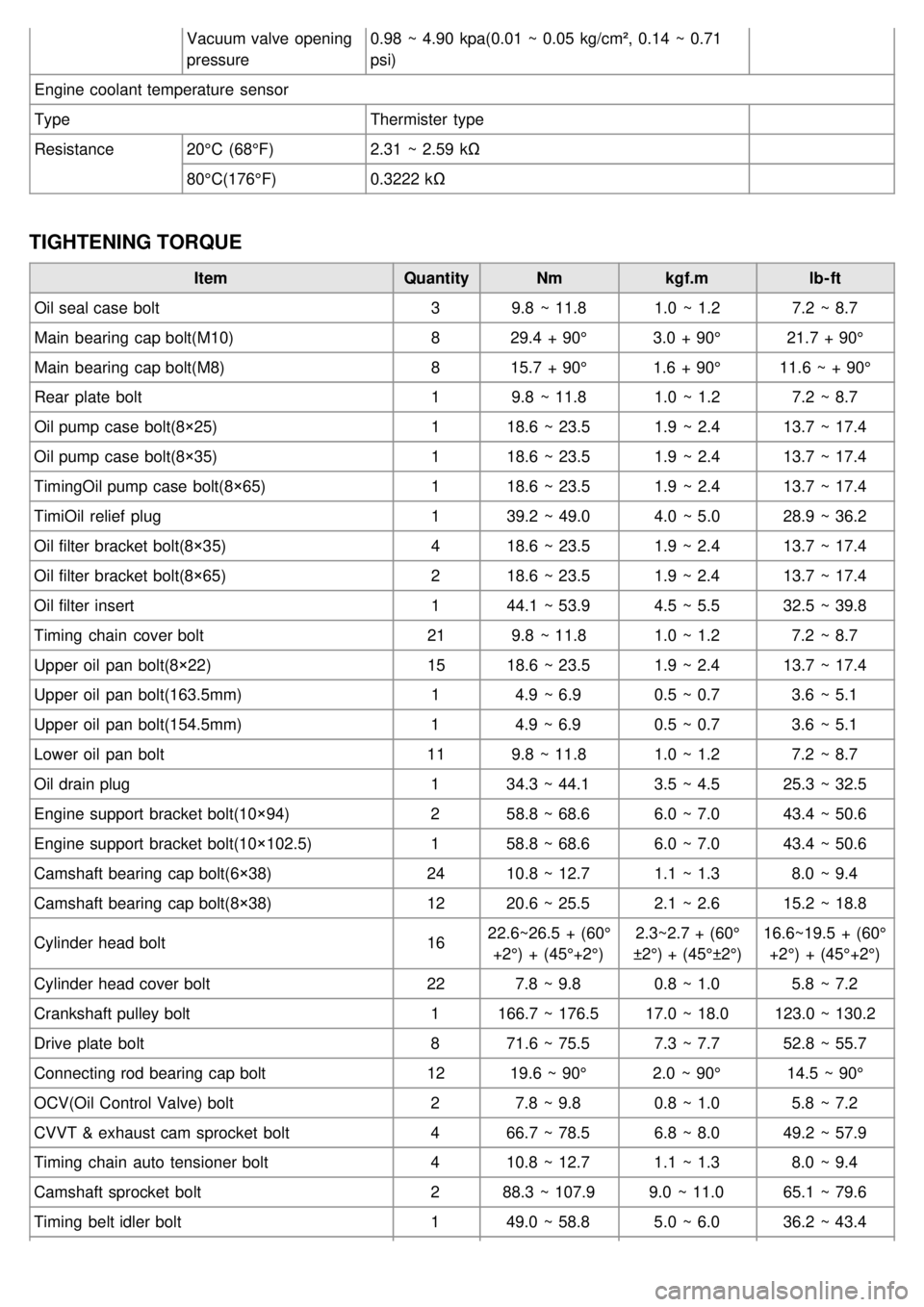
Vacuum valve opening
pressure0.98 ~ 4.90 kpa(0.01 ~ 0.05 kg/cm², 0.14 ~ 0.71
psi)
Engine coolant temperature sensor
Type Thermister type
Resistance 20°C (68°F) 2.31 ~ 2.59 kΩ
80°C(176°F) 0.3222 kΩ
TIGHTENING TORQUE
Item QuantityNmkgf.m lb- ft
Oil seal case bolt 39.8 ~ 11.8 1.0 ~ 1.27.2 ~ 8.7
Main bearing cap bolt(M10) 829.4 + 90° 3.0 + 90°21.7 + 90°
Main bearing cap bolt(M8) 815.7 + 90° 1.6 + 90°11.6 ~ + 90°
Rear plate bolt 19.8 ~ 11.8 1.0 ~ 1.27.2 ~ 8.7
Oil pump case bolt(8×25) 118.6 ~ 23.5 1.9 ~ 2.413.7 ~ 17.4
Oil pump case bolt(8×35) 118.6 ~ 23.5 1.9 ~ 2.413.7 ~ 17.4
TimingOil pump case bolt(8×65) 118.6 ~ 23.5 1.9 ~ 2.413.7 ~ 17.4
TimiOil relief plug 139.2 ~ 49.0 4.0 ~ 5.028.9 ~ 36.2
Oil filter bracket bolt(8×35) 418.6 ~ 23.5 1.9 ~ 2.413.7 ~ 17.4
Oil filter bracket bolt(8×65) 218.6 ~ 23.5 1.9 ~ 2.413.7 ~ 17.4
Oil filter insert 144.1 ~ 53.9 4.5 ~ 5.532.5 ~ 39.8
Timing chain cover bolt 219.8 ~ 11.8 1.0 ~ 1.27.2 ~ 8.7
Upper oil pan bolt(8×22) 1518.6 ~ 23.5 1.9 ~ 2.413.7 ~ 17.4
Upper oil pan bolt(163.5mm) 14.9 ~ 6.9 0.5 ~ 0.73.6 ~ 5.1
Upper oil pan bolt(154.5mm) 14.9 ~ 6.9 0.5 ~ 0.73.6 ~ 5.1
Lower oil pan bolt 119.8 ~ 11.8 1.0 ~ 1.27.2 ~ 8.7
Oil drain plug 134.3 ~ 44.1 3.5 ~ 4.525.3 ~ 32.5
Engine support bracket bolt(10×94) 258.8 ~ 68.6 6.0 ~ 7.043.4 ~ 50.6
Engine support bracket bolt(10×102.5) 158.8 ~ 68.6 6.0 ~ 7.043.4 ~ 50.6
Camshaft bearing cap bolt(6×38) 2410.8 ~ 12.7 1.1 ~ 1.38.0 ~ 9.4
Camshaft bearing cap bolt(8×38) 1220.6 ~ 25.5 2.1 ~ 2.615.2 ~ 18.8
Cylinder head bolt 1622.6~26.5 + (60°
+2°) + (45°+2°) 2.3~2.7 + (60°
±2°) + (45°±2°) 16.6~19.5 + (60°
+2°) + (45°+2°)
Cylinder head cover bolt 227.8 ~ 9.8 0.8 ~ 1.05.8 ~ 7.2
Crankshaft pulley bolt 1166.7 ~ 176.5 17.0 ~ 18.0123.0 ~ 130.2
Drive plate bolt 871.6 ~ 75.5 7.3 ~ 7.752.8 ~ 55.7
Connecting rod bearing cap bolt 1219.6 ~ 90° 2.0 ~ 90°14.5 ~ 90°
OCV(Oil Control Valve) bolt 27.8 ~ 9.8 0.8 ~ 1.05.8 ~ 7.2
CVVT & exhaust cam sprocket bolt 466.7 ~ 78.5 6.8 ~ 8.049.2 ~ 57.9
Timing chain auto tensioner bolt 410.8 ~ 12.7 1.1 ~ 1.38.0 ~ 9.4
Camshaft sprocket bolt 288.3 ~ 107.9 9.0 ~ 11.065.1 ~ 79.6
Timing belt idler bolt 149.0 ~ 58.8 5.0 ~ 6.036.2 ~ 43.4
Page 51 of 1575
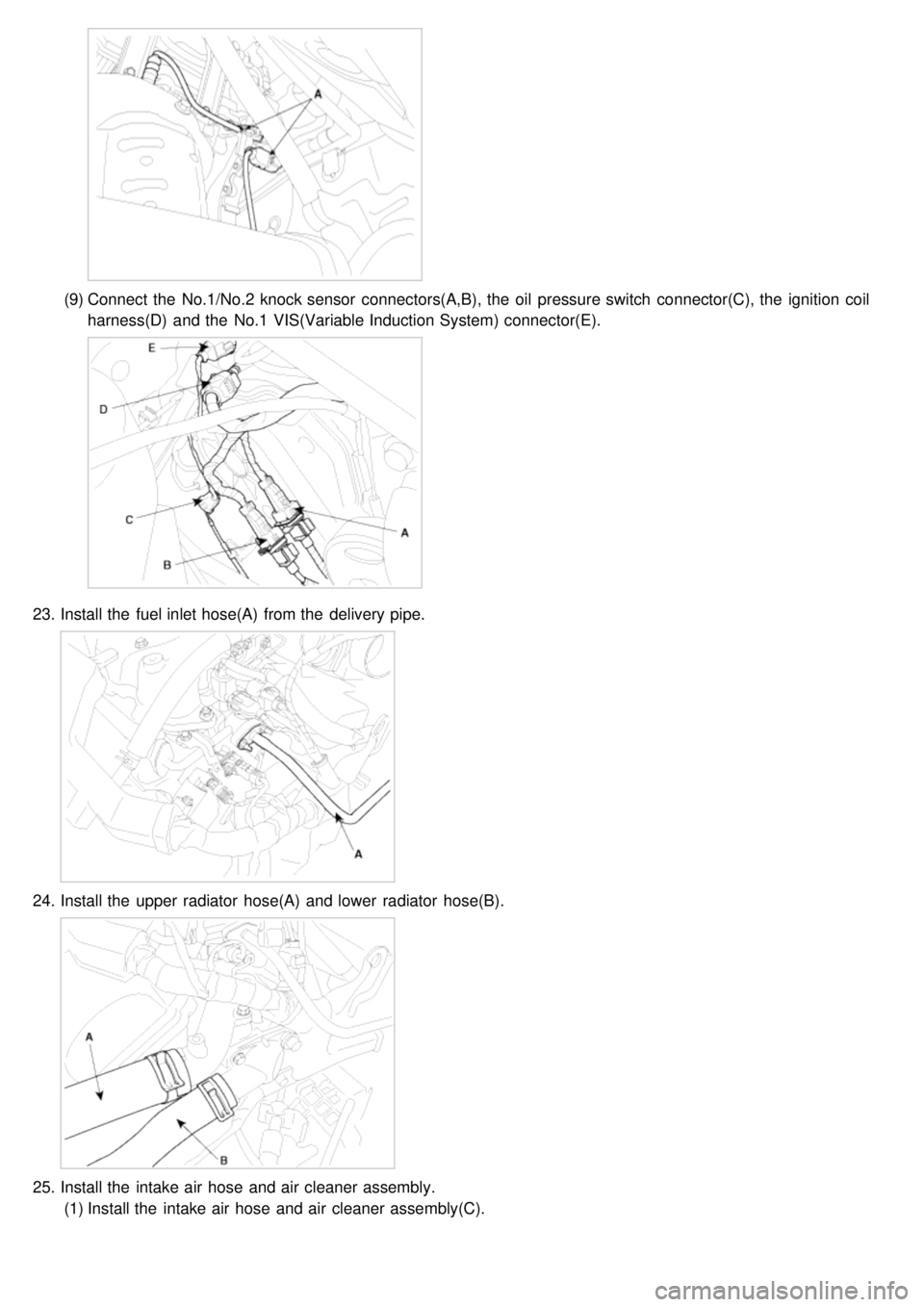
(9)Connect the No.1/No.2 knock sensor connectors(A,B), the oil pressure switch connector(C), the ignition coil
harness(D) and the No.1 VIS(Variable Induction System) connector(E).
23. Install the fuel inlet hose(A) from the delivery pipe.
24.Install the upper radiator hose(A) and lower radiator hose(B).
25.Install the intake air hose and air cleaner assembly.
(1) Install the intake air hose and air cleaner assembly(C).
Page 217 of 1575
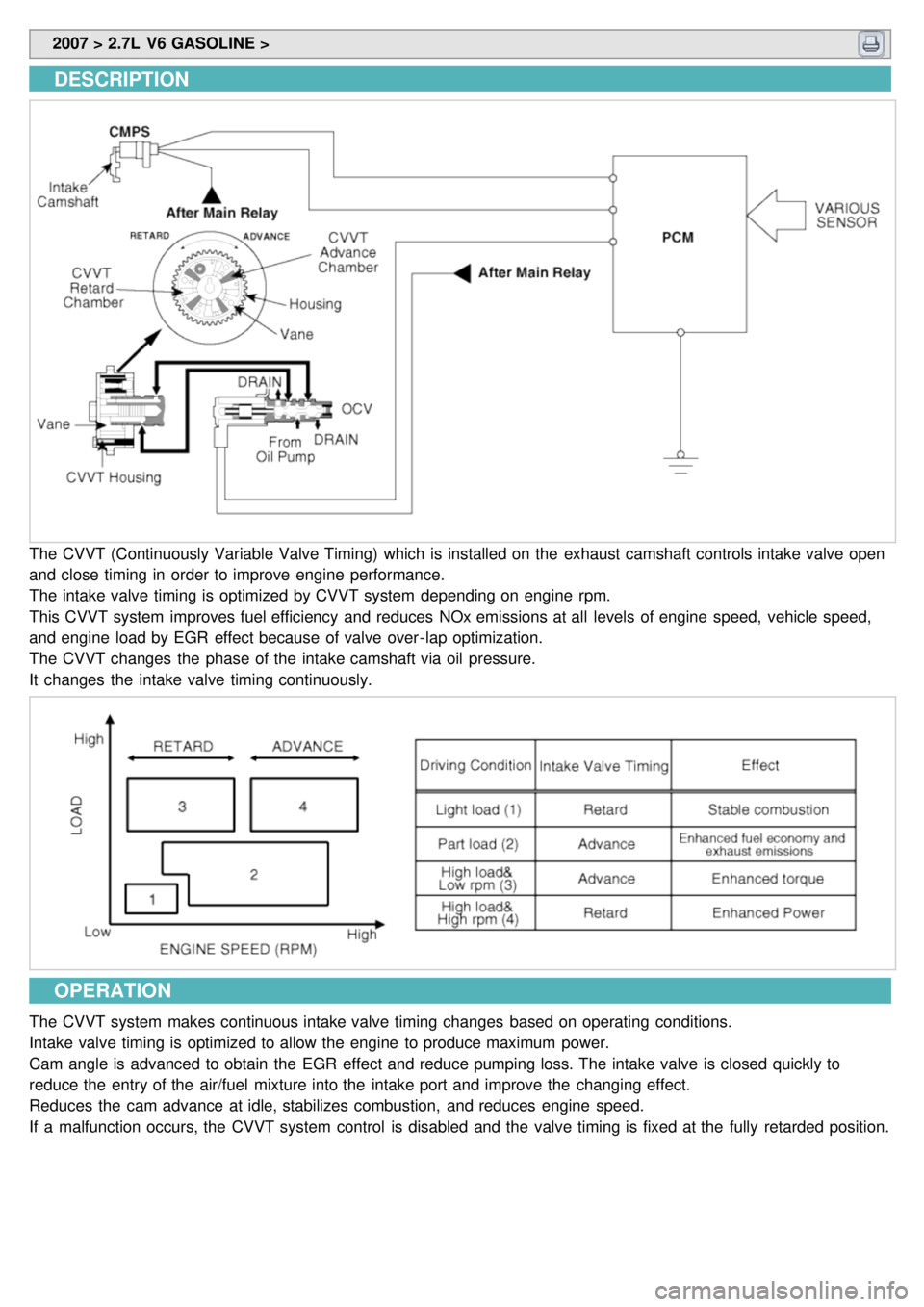
2007 > 2.7L V6 GASOLINE >
DESCRIPTION
The CVVT (Continuously Variable Valve Timing) which is installed on the exhaust camshaft controls intake valve open
and close timing in order to improve engine performance.
The intake valve timing is optimized by CVVT system depending on engine rpm.
This CVVT system improves fuel efficiency and reduces NOx emissions at all levels of engine speed, vehicle speed,
and engine load by EGR effect because of valve over - lap optimization.
The CVVT changes the phase of the intake camshaft via oil pressure.
It changes the intake valve timing continuously.
OPERATION
The CVVT system makes continuous intake valve timing changes based on operating conditions.
Intake valve timing is optimized to allow the engine to produce maximum power.
Cam angle is advanced to obtain the EGR effect and reduce pumping loss. The intake valve is closed quickly to
reduce the entry of the air/fuel mixture into the intake port and improve the changing effect.
Reduces the cam advance at idle, stabilizes combustion, and reduces engine speed.
If a malfunction occurs, the CVVT system control is disabled and the valve timing is fixed at the fully retarded position.
Page 218 of 1575
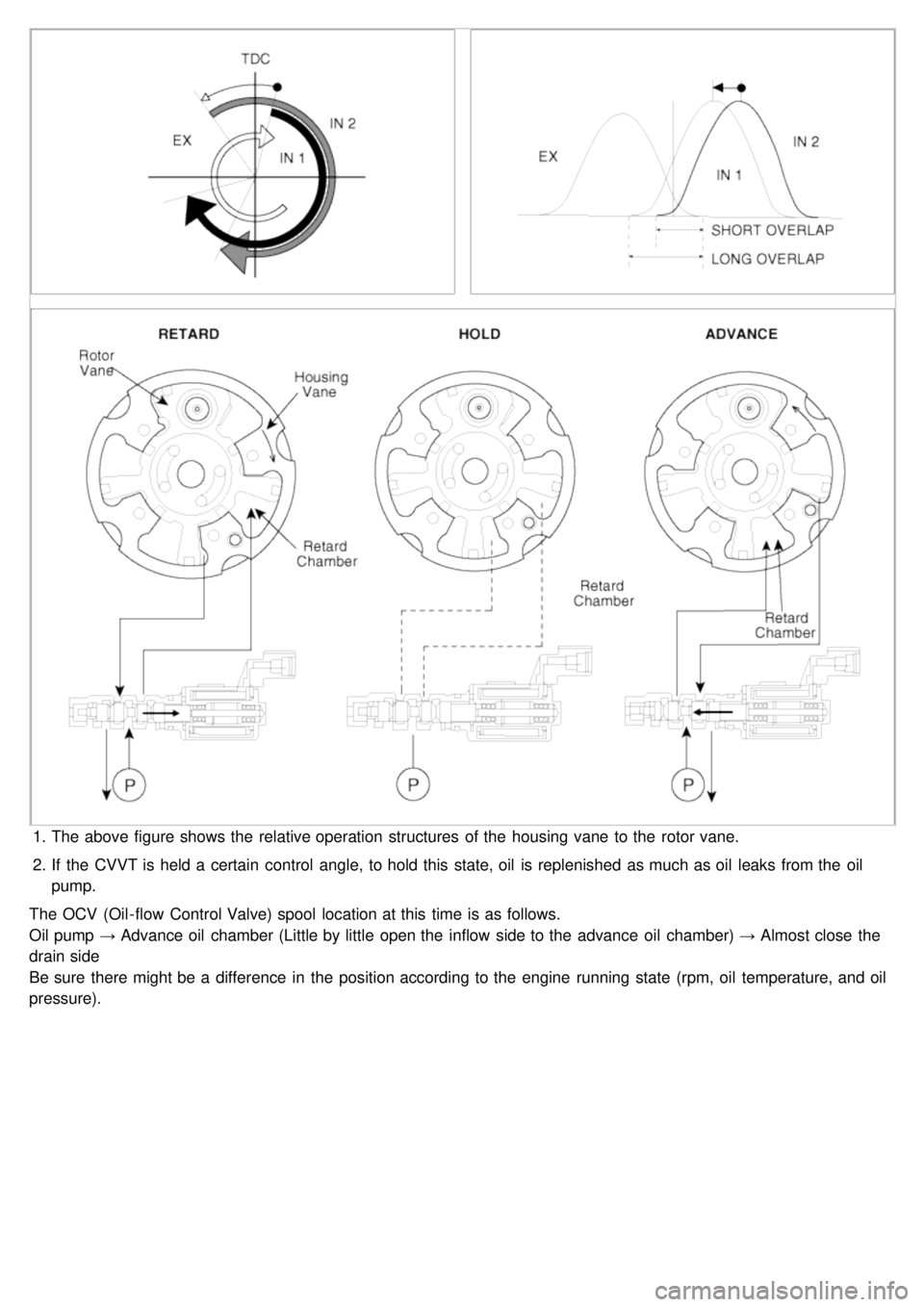
1.The above figure shows the relative operation structures of the housing vane to the rotor vane.
2. If the CVVT is held a certain control angle, to hold this state, oil is replenished as much as oil leaks from the oil
pump.
The OCV (Oil - flow Control Valve) spool location at this time is as follows.
Oil pump → Advance oil chamber (Little by little open the inflow side to the advance oil chamber) → Almost close the
drain side
Be sure there might be a difference in the position according to the engine running state (rpm, oil temperature, and oil
pressure).
Page 255 of 1575
![KIA CARNIVAL 2007 Workshop Manual 67Variable Intake Solenoid Valve #2 control output
Manifold Side]
68 Throttle Position Sensor signal (PWM) output ABS/ESP Control Module
69 Cruise "MAIN" lamp control output Cruise "MAIN" Lamp
KIA CARNIVAL 2007 Workshop Manual 67Variable Intake Solenoid Valve #2 control output
Manifold Side]
68 Throttle Position Sensor signal (PWM) output ABS/ESP Control Module
69 Cruise "MAIN" lamp control output Cruise "MAIN" Lamp](/img/2/57045/w960_57045-254.png)
67Variable Intake Solenoid Valve #2 control output
Manifold Side]
68 Throttle Position Sensor signal (PWM) output ABS/ESP Control Module
69 Cruise "MAIN" lamp control output Cruise "MAIN" Lamp
70 Fuel Pump Relay control output Fuel Pump Relay
71 Variable Intake Solenoid Valve #1 control output Variable Intake Solenoid (VIS) Valve #1 Surge
Tank Side]
72 Immobilizer lamp control output Immobilizer Lamp
73 -y
74 -y
75 -y
76 -y
77 -y
78 Purge Control Solenoid Valve control output Purge Control Solenoid Valve (PCSV)
79 Wheel Speed Sensor [Low] signal input Wheel Speed Sensor (WSS)(Without ABS/ESP
[Euro -
Ⅲ/Ⅳ])
80 Wheel Speed Sensor [High] signal input Wheel Speed Sensor (WSS)(Without ABS/ESP
[Euro -
Ⅲ/Ⅳ])
CONNECTOR [C151- 2] Pin
No. Description
Connected to
1 ETC Motor [- ] control output ETC Motor (in ETC Module)
2 ETC Motor [+] control output ETC Motor (in ETC Module)
3 -y
4 CVVT Oil Temperature Sensor signal input CVVT Oil Temperature Sensor (OTS)
5 -y
6 -y
7 Engine Coolant Temperature Sensor signal input Engine Coolant Temperature Sensor (ECTS)
8 Manifold Absolute Pressure Sensor signal input Manifold Absolute Pressure Sensor (MAPS)
9 -y
10 -y
11 Reference voltage (+5V) Manifold Absolute Pressure Sensor (MAPS)
12 Battery voltage supply after ignition switch Ignition Switch
13 Reference voltage (+5V) Throttle Position Sensor (TPS) #2
14 Sensor ground Throttle Position Sensor (TPS) #1
15 Reference voltage (+5V) Camshaft Position Sensor (CMPS) [Bank 2]
16 Reference voltage (+5V) Throttle Position Sensor (TPS) #1
17 Sensor ground Camshaft Position Sensor (CMPS) [Bank 2]
18 Sensor ground Camshaft Position Sensor (CMPS) [Bank 1]
19 Ignition Coil (Cylinder #6) control output Ignition Coil (Cylinder #6)
20 -y
21 Crankshaft Position Sensor [High] signal input Crankshaft Position Sensor (CKPS)
22 -y
Knock Sensor (KS) [Bank 1], Knock Sensor (KS)
Page 256 of 1575
![KIA CARNIVAL 2007 Workshop Manual 23Sensor Shield Knock Sensor (KS) [Bank 1], Knock Sensor (KS)
[Bank 2]
24 Camshaft Position Sensor [Bank 2] signal input Camshaft Position Sensor (CMPS) [Bank 2]
25 Camshaft Position Se KIA CARNIVAL 2007 Workshop Manual 23Sensor Shield Knock Sensor (KS) [Bank 1], Knock Sensor (KS)
[Bank 2]
24 Camshaft Position Sensor [Bank 2] signal input Camshaft Position Sensor (CMPS) [Bank 2]
25 Camshaft Position Se](/img/2/57045/w960_57045-255.png)
23Sensor Shield Knock Sensor (KS) [Bank 1], Knock Sensor (KS)
[Bank 2]
24 Camshaft Position Sensor [Bank 2] signal input Camshaft Position Sensor (CMPS) [Bank 2]
25 Camshaft Position Sensor [Bank 1] signal input Camshaft Position Sensor (CMPS) [Bank 1]
26 -y
27 -y
28 Sensor ground HO2S [B2 / S1] [Except for LEADED]
29 Sensor ground HO2S [B2 / S2] [Euro -Ⅲ/Ⅳ]
30 Sensor ground HO2S [B1 / S1] [Except for LEADED]
31 Sensor ground HO2S [B1 / S2] [Euro -Ⅲ/Ⅳ]
32 Reference voltage (+5V) Camshaft Position Sensor (CMPS) [Bank 1]
33 Sensor ground Engine Coolant Temperature Sensor (ECTS)
34 Sensor ground Manifold Absolute Pressure Sensor (MAPS),
CVVT Oil Temperature Sensor (OTS)
35 Power ground Chassis Ground
36 Power ground Chassis Ground
37 Power ground Chassis Ground
38 Power ground Chassis Ground
39 Power ground Chassis Ground
40 Ignition Coil (Cylinder #4) control output Ignition Coil (Cylinder #4)
41 Crankshaft Position Sensor [Low] signal input Crankshaft Position Sensor (CKPS)
42 -y
43 -y
44 -y
45 -y
46 -y
47 -y
48 Throttle Position Sensor #1 signal input Throttle Position Sensor (TPS) #1
49 Heated Oxygen Sensor [Bank 1 / Sensor 1] signal
input HO2S (B1/S1) [Except for LEADED]
50 Heated Oxygen Sensor [Bank 1 / Sensor 2] signal
input HO2S (B1/S2) [Euro -
Ⅲ/Ⅳ]
51 Heated Oxygen Sensor [Bank 2 / Sensor 1] signal
input HO2S (B2/S1) [Except for LEADED]
52 Heated Oxygen Sensor [Bank 2 / Sensor 2] signal
input HO2S (B2/S2) [Euro -
Ⅲ/Ⅳ]
53 Knock Sensor (KS) [Bank 2] [High] signal input Knock Sensor (KS) [Bank 2]
54 Knock Sensor (KS) [Bank 2] [Low] signal input Knock Sensor (KS) [Bank 2]
55 Knock Sensor (KS) [Bank 1] [Low] signal input Knock Sensor (KS) [Bank 1]
56 Knock Sensor (KS) [Bank 1] [High] signal input Knock Sensor (KS) [Bank 1]
57 Throttle Position Sensor #2 signal input Throttle Position Sensor (TPS) #2
58 Sensor ground Throttle Position Sensor (TPS) #2
59 -y
60 Ignition Coil (Cylinder #2) control output Ignition Coil (Cylinder #2)
Page 351 of 1575
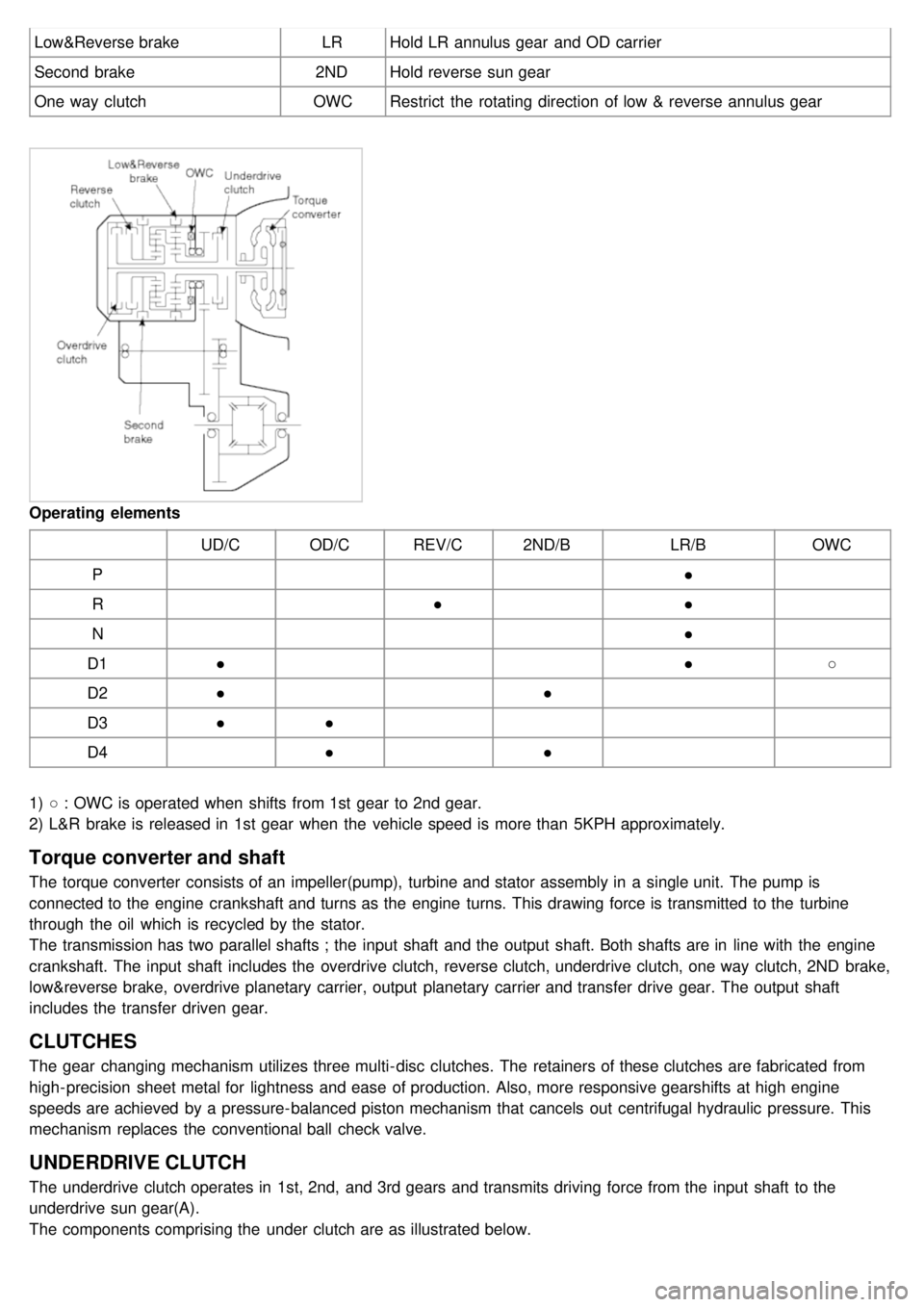
Low&Reverse brakeLRHold LR annulus gear and OD carrier
Second brake 2NDHold reverse sun gear
One way clutch OWCRestrict the rotating direction of low & reverse annulus gear
Operating elements
UD/COD/CREV/C 2ND/B LR/BOWC
P ●
R ●●
N ●
D1 ● ●○
D2 ● ●
D3 ●●
D4 ●●
1) ○ : OWC is operated when shifts from 1st gear to 2nd gear.
2) L&R brake is released in 1st gear when the vehicle speed is more than 5KPH approximately.
Torque converter and shaft
The torque converter consists of an impeller(pump), turbine and stator assembly in a single unit. The pump is
connected to the engine crankshaft and turns as the engine turns. This drawing force is transmitted to the turbine
through the oil which is recycled by the stator.
The transmission has two parallel shafts ; the input shaft and the output shaft. Both shafts are in line with the engine
crankshaft. The input shaft includes the overdrive clutch, reverse clutch, underdrive clutch, one way clutch, 2ND brake,
low&reverse brake, overdrive planetary carrier, output planetary carrier and transfer drive gear. The output shaft
includes the transfer driven gear.
CLUTCHES
The gear changing mechanism utilizes three multi- disc clutches. The retainers of these clutches are fabricated from
high- precision sheet metal for lightness and ease of production. Also, more responsive gearshifts at high engine
speeds are achieved by a pressure- balanced piston mechanism that cancels out centrifugal hydraulic pressure. This
mechanism replaces the conventional ball check valve.
UNDERDRIVE CLUTCH
The underdrive clutch operates in 1st, 2nd, and 3rd gears and transmits driving force from the input shaft to the
underdrive sun gear(A).
The components comprising the under clutch are as illustrated below.