check engine LAND ROVER DEFENDER 1996 Workshop Manual
[x] Cancel search | Manufacturer: LAND ROVER, Model Year: 1996, Model line: DEFENDER, Model: LAND ROVER DEFENDER 1996Pages: 455, PDF Size: 6.44 MB
Page 11 of 455
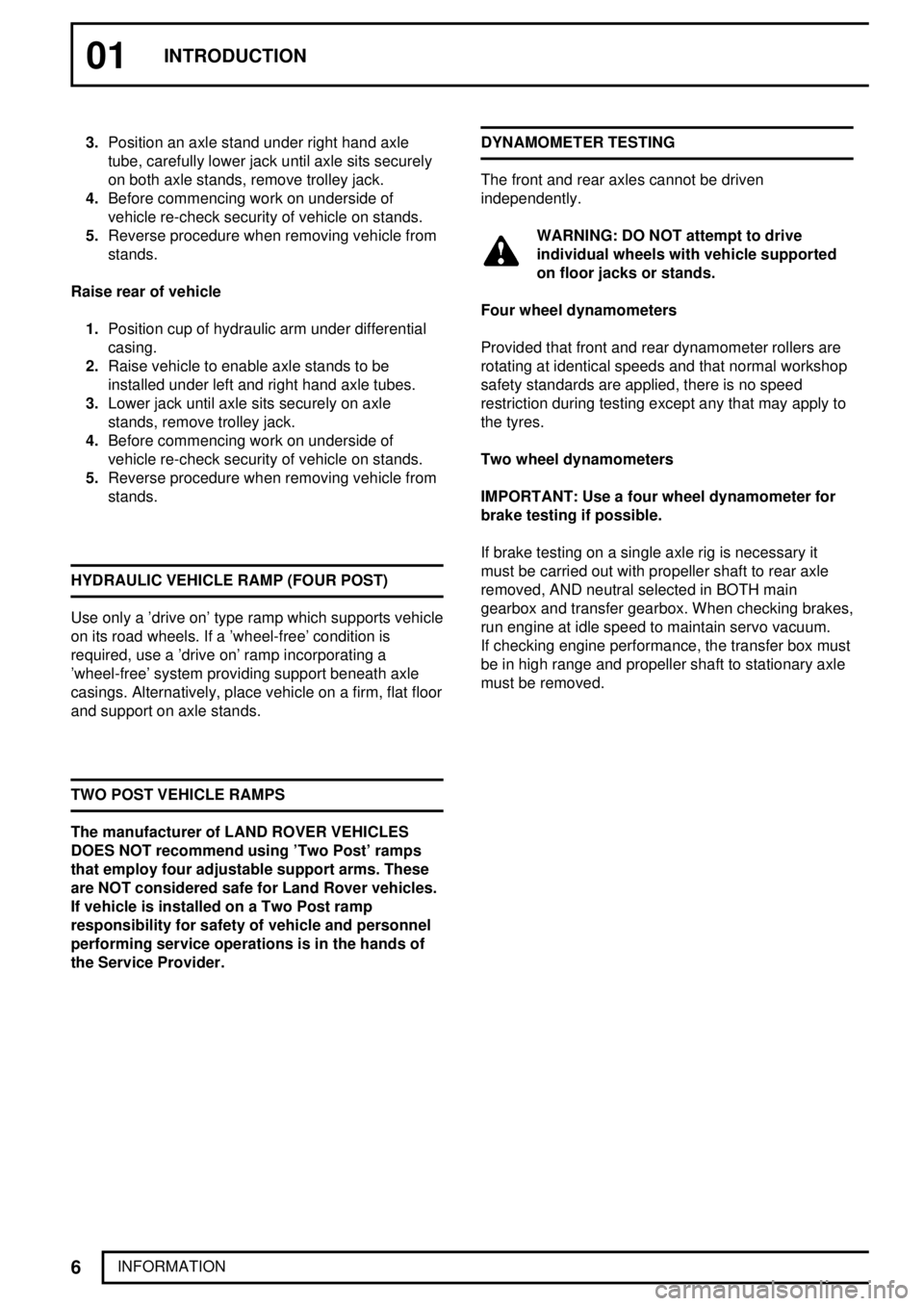
01INTRODUCTION
6
INFORMATION 3.Position an axle stand under right hand axle
tube, carefully lower jack until axle sits securely
on both axle stands, remove trolley jack.
4.Before commencing work on underside of
vehicle re-check security of vehicle on stands.
5.Reverse procedure when removing vehicle from
stands.
Raise rear of vehicle
1.Position cup of hydraulic arm under differential
casing.
2.Raise vehicle to enable axle stands to be
installed under left and right hand axle tubes.
3.Lower jack until axle sits securely on axle
stands, remove trolley jack.
4.Before commencing work on underside of
vehicle re-check security of vehicle on stands.
5.Reverse procedure when removing vehicle from
stands.
HYDRAULIC VEHICLE RAMP (FOUR POST)
Use only a 'drive on' type ramp which supports vehicle
on its road wheels. If a 'wheel-free' condition is
required, use a 'drive on' ramp incorporating a
'wheel-free' system providing support beneath axle
casings. Alternatively, place vehicle on a firm, flat floor
and support on axle stands.
TWO POST VEHICLE RAMPS
The manufacturer of LAND ROVER VEHICLES
DOES NOT recommend using 'Two Post' ramps
that employ four adjustable support arms. These
are NOT considered safe for Land Rover vehicles.
If vehicle is installed on a Two Post ramp
responsibility for safety of vehicle and personnel
performing service operations is in the hands of
the Service Provider.DYNAMOMETER TESTING
The front and rear axles cannot be driven
independently.
WARNING: DO NOT attempt to drive
individual wheels with vehicle supported
on floor jacks or stands.
Four wheel dynamometers
Provided that front and rear dynamometer rollers are
rotating at identical speeds and that normal workshop
safety standards are applied, there is no speed
restriction during testing except any that may apply to
the tyres.
Two wheel dynamometers
IMPORTANT: Use a four wheel dynamometer for
brake testing if possible.
If brake testing on a single axle rig is necessary it
must be carried out with propeller shaft to rear axle
removed, AND neutral selected in BOTH main
gearbox and transfer gearbox. When checking brakes,
run engine at idle speed to maintain servo vacuum.
If checking engine performance, the transfer box must
be in high range and propeller shaft to stationary axle
must be removed.
Page 18 of 455
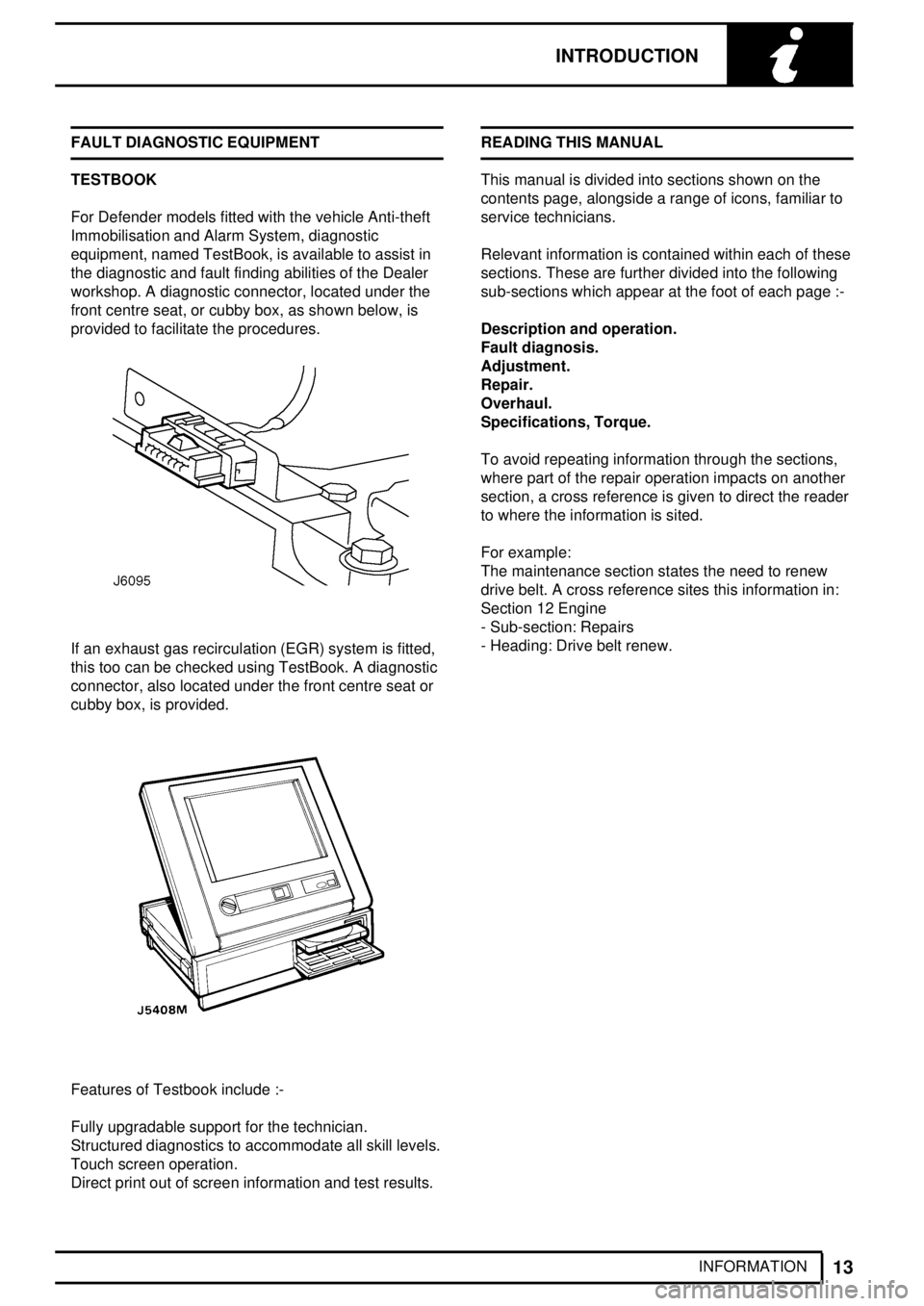
INTRODUCTION
13
INFORMATION FAULT DIAGNOSTIC EQUIPMENT
TESTBOOK
For Defender models fitted with the vehicle Anti-theft
Immobilisation and Alarm System, diagnostic
equipment, named TestBook, is available to assist in
the diagnostic and fault finding abilities of the Dealer
workshop. A diagnostic connector, located under the
front centre seat, or cubby box, as shown below, is
provided to facilitate the procedures.
If an exhaust gas recirculation (EGR) system is fitted,
this too can be checked using TestBook. A diagnostic
connector, also located under the front centre seat or
cubby box, is provided.
Features of Testbook include :-
Fully upgradable support for the technician.
Structured diagnostics to accommodate all skill levels.
Touch screen operation.
Direct print out of screen information and test results.READING THIS MANUAL
This manual is divided into sections shown on the
contents page, alongside a range of icons, familiar to
service technicians.
Relevant information is contained within each of these
sections. These are further divided into the following
sub-sections which appear at the foot of each page :-
Description and operation.
Fault diagnosis.
Adjustment.
Repair.
Overhaul.
Specifications, Torque.
To avoid repeating information through the sections,
where part of the repair operation impacts on another
section, a cross reference is given to direct the reader
to where the information is sited.
For example:
The maintenance section states the need to renew
drive belt. A cross reference sites this information in:
Section 12 Engine
- Sub-section: Repairs
- Heading: Drive belt renew.
Page 33 of 455
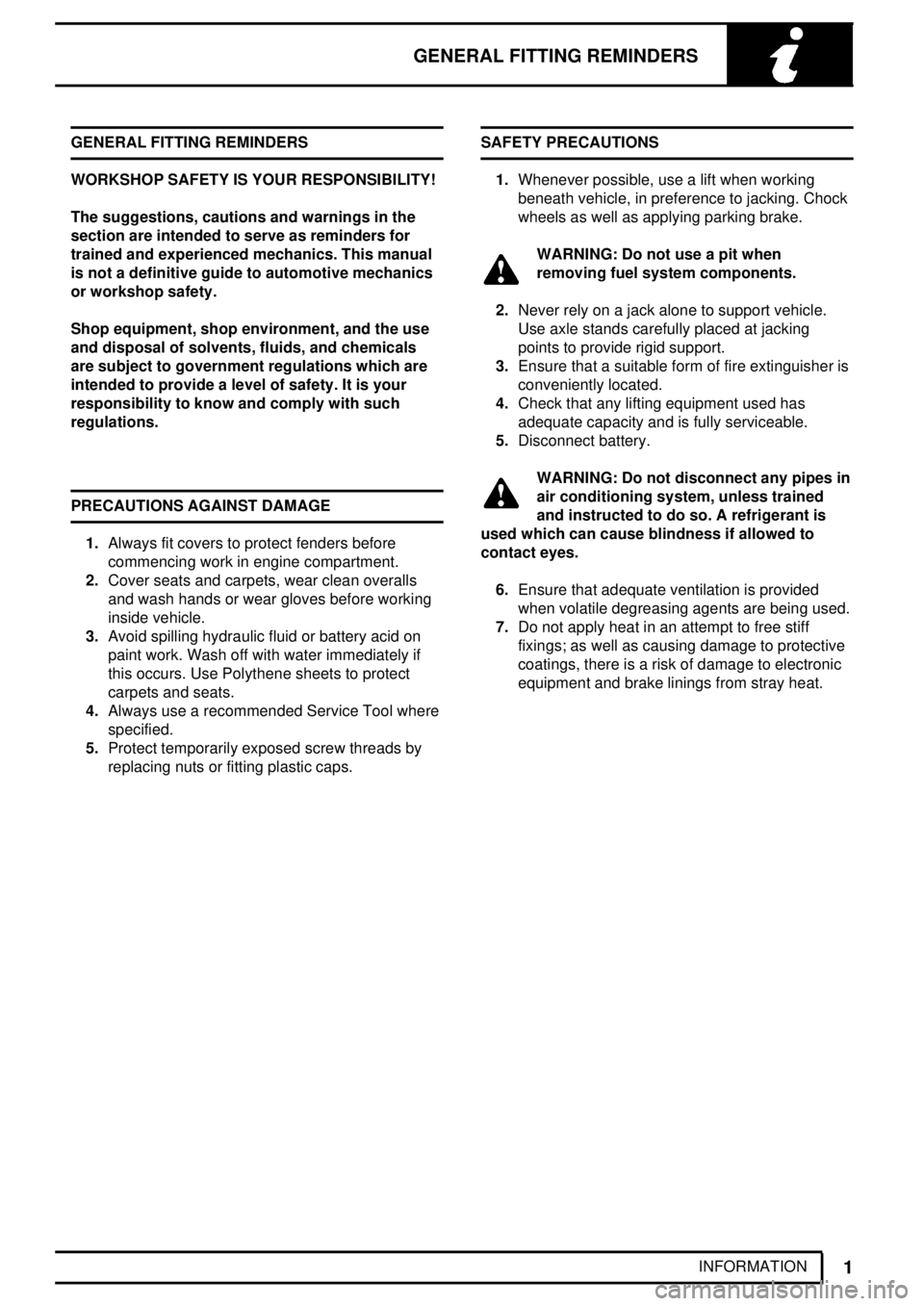
GENERAL FITTING REMINDERS
1
INFORMATION GENERAL FITTING REMINDERS
WORKSHOP SAFETY IS YOUR RESPONSIBILITY!
The suggestions, cautions and warnings in the
section are intended to serve as reminders for
trained and experienced mechanics. This manual
is not a definitive guide to automotive mechanics
or workshop safety.
Shop equipment, shop environment, and the use
and disposal of solvents, fluids, and chemicals
are subject to government regulations which are
intended to provide a level of safety. It is your
responsibility to know and comply with such
regulations.
PRECAUTIONS AGAINST DAMAGE
1.Always fit covers to protect fenders before
commencing work in engine compartment.
2.Cover seats and carpets, wear clean overalls
and wash hands or wear gloves before working
inside vehicle.
3.Avoid spilling hydraulic fluid or battery acid on
paint work. Wash off with water immediately if
this occurs. Use Polythene sheets to protect
carpets and seats.
4.Always use a recommended Service Tool where
specified.
5.Protect temporarily exposed screw threads by
replacing nuts or fitting plastic caps.SAFETY PRECAUTIONS
1.Whenever possible, use a lift when working
beneath vehicle, in preference to jacking. Chock
wheels as well as applying parking brake.
WARNING: Do not use a pit when
removing fuel system components.
2.Never rely on a jack alone to support vehicle.
Use axle stands carefully placed at jacking
points to provide rigid support.
3.Ensure that a suitable form of fire extinguisher is
conveniently located.
4.Check that any lifting equipment used has
adequate capacity and is fully serviceable.
5.Disconnect battery.
WARNING: Do not disconnect any pipes in
air conditioning system, unless trained
and instructed to do so. A refrigerant is
used which can cause blindness if allowed to
contact eyes.
6.Ensure that adequate ventilation is provided
when volatile degreasing agents are being used.
7.Do not apply heat in an attempt to free stiff
fixings; as well as causing damage to protective
coatings, there is a risk of damage to electronic
equipment and brake linings from stray heat.
Page 42 of 455
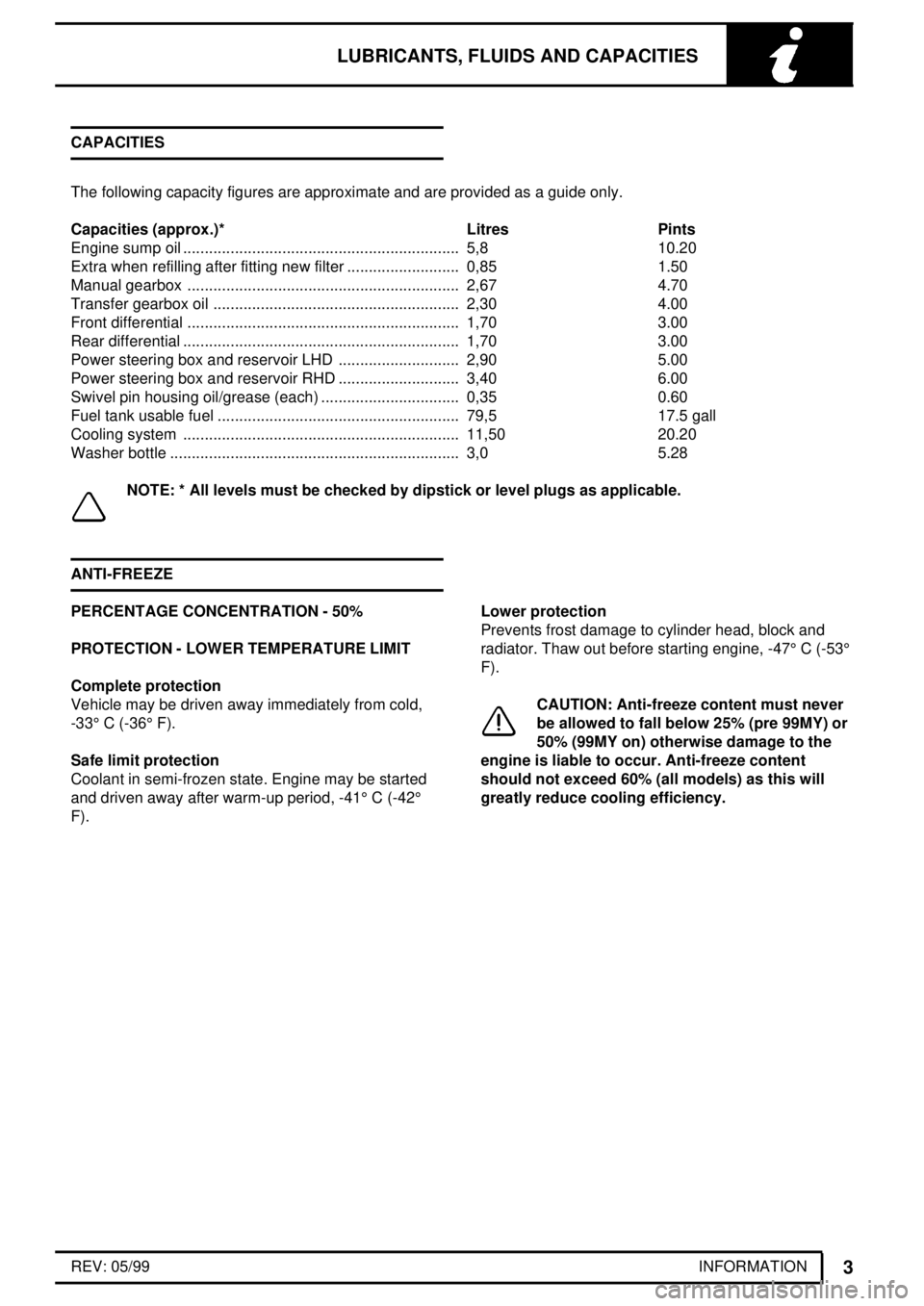
LUBRICANTS, FLUIDS AND CAPACITIES
3
INFORMATION REV: 05/99 CAPACITIES
The following capacity figures are approximate and are provided as a guide only.
Capacities (approx.)* Litres Pints
Engine sump oil 5,8................................................................ 10.20
Extra when refilling after fitting new filter 0,85.......................... 1.50
Manual gearbox 2,67............................................................... 4.70
Transfer gearbox oil 2,30......................................................... 4.00
Front differential 1,70............................................................... 3.00
Rear differential 1,70................................................................ 3.00
Power steering box and reservoir LHD 2,90............................ 5.00
Power steering box and reservoir RHD 3,40............................ 6.00
Swivel pin housing oil/grease (each) 0,35................................ 0.60
Fuel tank usable fuel 79,5........................................................ 17.5 gall
Cooling system 11,50................................................................ 20.20
Washer bottle 3,0................................................................... 5.28
NOTE: * All levels must be checked by dipstick or level plugs as applicable.
ANTI-FREEZE
PERCENTAGE CONCENTRATION - 50%
PROTECTION - LOWER TEMPERATURE LIMIT
Complete protection
Vehicle may be driven away immediately from cold,
-33°C (-36°F).
Safe limit protection
Coolant in semi-frozen state. Engine may be started
and driven away after warm-up period, -41°C (-42°
F).Lower protection
Prevents frost damage to cylinder head, block and
radiator. Thaw out before starting engine, -47°C (-53°
F).
CAUTION: Anti-freeze content must never
be allowed to fall below 25% (pre 99MY) or
50% (99MY on) otherwise damage to the
engine is liable to occur. Anti-freeze content
should not exceed 60% (all models) as this will
greatly reduce cooling efficiency.
Page 48 of 455
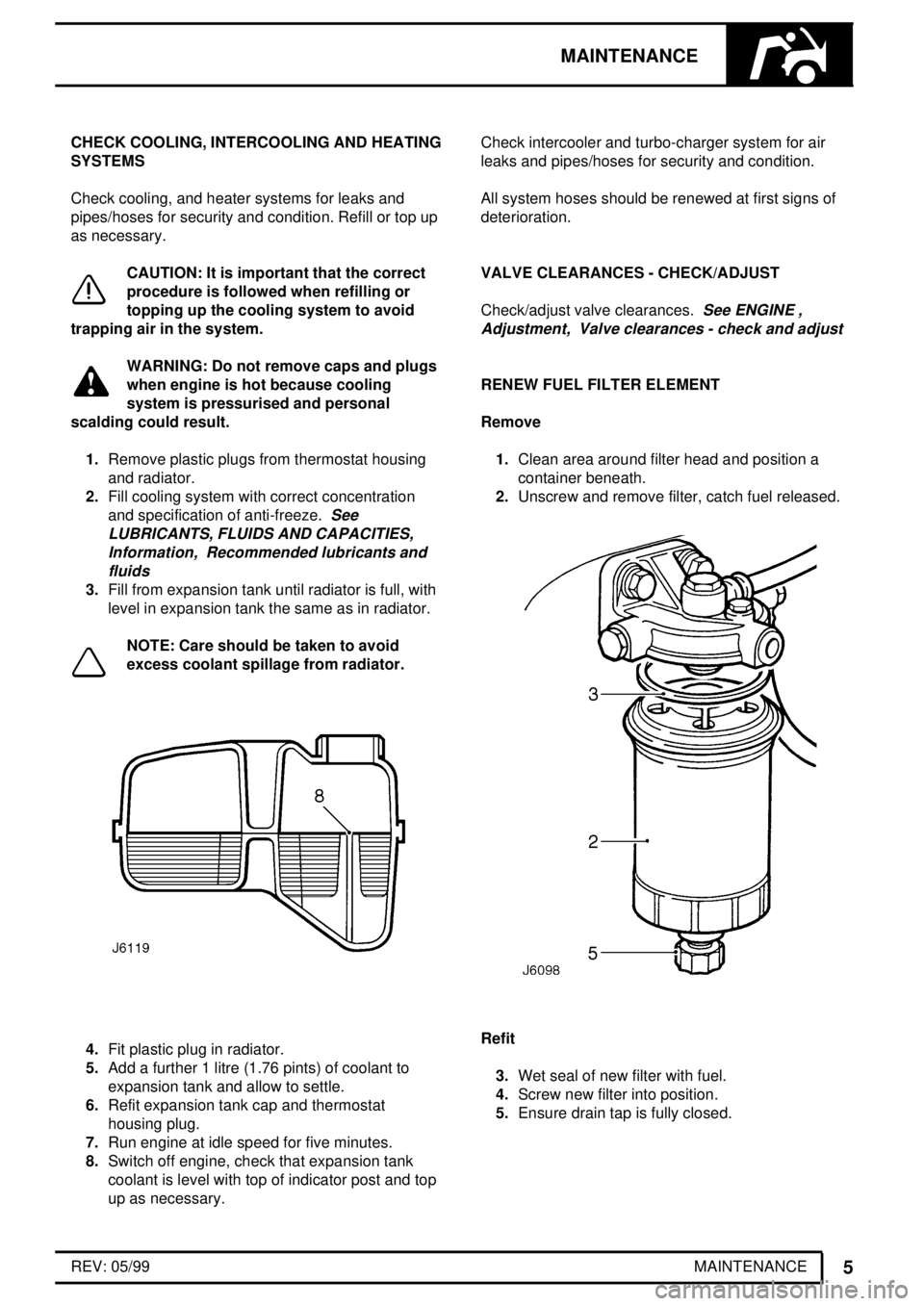
MAINTENANCE
5
MAINTENANCE REV: 05/99 CHECK COOLING, INTERCOOLING AND HEATING
SYSTEMS
Check cooling, and heater systems for leaks and
pipes/hoses for security and condition. Refill or top up
as necessary.
CAUTION: It is important that the correct
procedure is followed when refilling or
topping up the cooling system to avoid
trapping air in the system.
WARNING: Do not remove caps and plugs
when engine is hot because cooling
system is pressurised and personal
scalding could result.
1.Remove plastic plugs from thermostat housing
and radiator.
2.Fill cooling system with correct concentration
and specification of anti-freeze.
See
LUBRICANTS, FLUIDS AND CAPACITIES,
Information, Recommended lubricants and
fluids
3.Fill from expansion tank until radiator is full, with
level in expansion tank the same as in radiator.
NOTE: Care should be taken to avoid
excess coolant spillage from radiator.
4.Fit plastic plug in radiator.
5.Add a further 1 litre (1.76 pints) of coolant to
expansion tank and allow to settle.
6.Refit expansion tank cap and thermostat
housing plug.
7.Run engine at idle speed for five minutes.
8.Switch off engine, check that expansion tank
coolant is level with top of indicator post and top
up as necessary.Check intercooler and turbo-charger system for air
leaks and pipes/hoses for security and condition.
All system hoses should be renewed at first signs of
deterioration.
VALVE CLEARANCES - CHECK/ADJUST
Check/adjust valve clearances.
See ENGINE ,
Adjustment, Valve clearances - check and adjust
RENEW FUEL FILTER ELEMENT
Remove
1.Clean area around filter head and position a
container beneath.
2.Unscrew and remove filter, catch fuel released.
Refit
3.Wet seal of new filter with fuel.
4.Screw new filter into position.
5.Ensure drain tap is fully closed.
Page 49 of 455
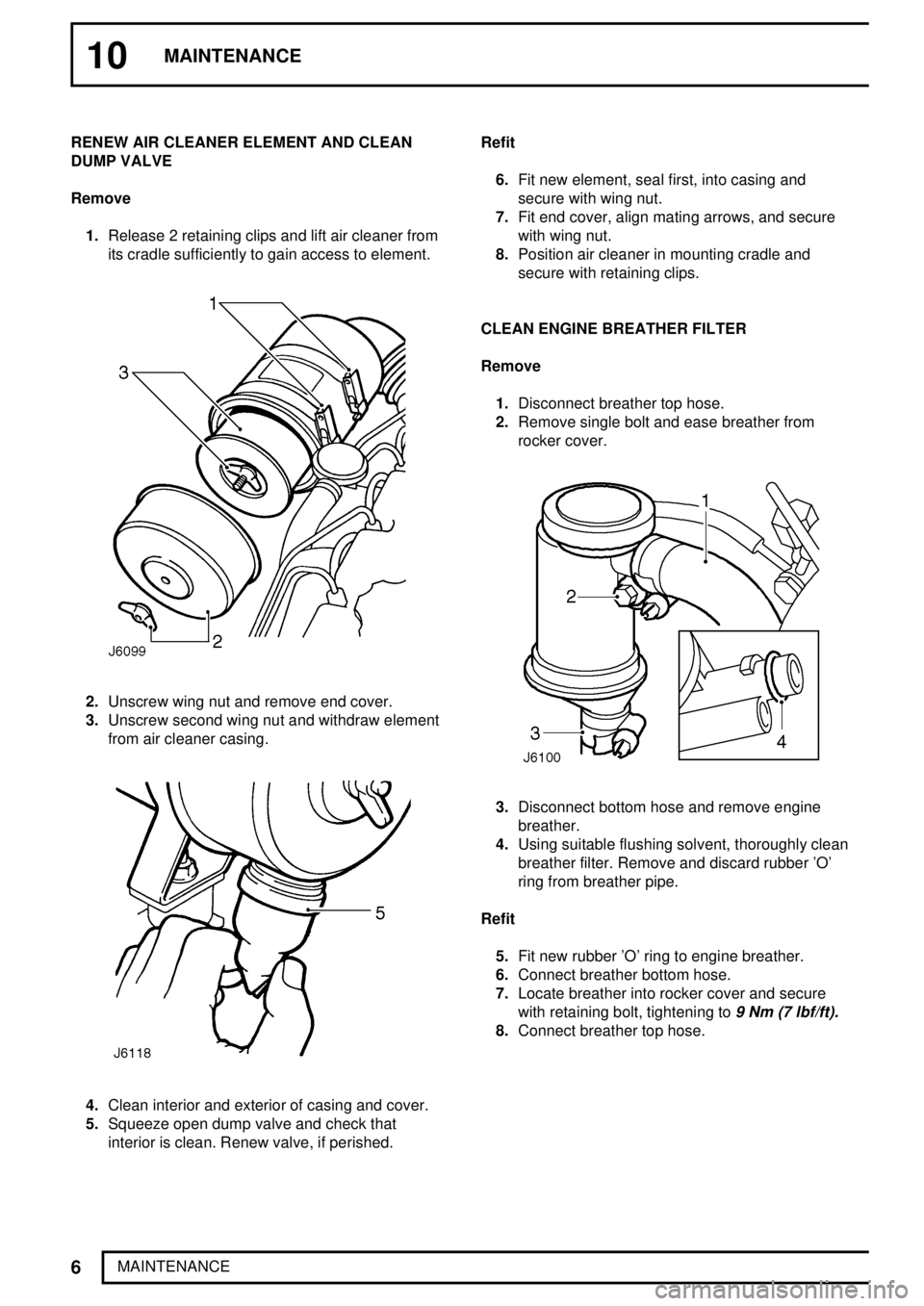
10MAINTENANCE
6
MAINTENANCE RENEW AIR CLEANER ELEMENT AND CLEAN
DUMP VALVE
Remove
1.Release 2 retaining clips and lift air cleaner from
its cradle sufficiently to gain access to element.
2.Unscrew wing nut and remove end cover.
3.Unscrew second wing nut and withdraw element
from air cleaner casing.
4.Clean interior and exterior of casing and cover.
5.Squeeze open dump valve and check that
interior is clean. Renew valve, if perished.Refit
6.Fit new element, seal first, into casing and
secure with wing nut.
7.Fit end cover, align mating arrows, and secure
with wing nut.
8.Position air cleaner in mounting cradle and
secure with retaining clips.
CLEAN ENGINE BREATHER FILTER
Remove
1.Disconnect breather top hose.
2.Remove single bolt and ease breather from
rocker cover.
3.Disconnect bottom hose and remove engine
breather.
4.Using suitable flushing solvent, thoroughly clean
breather filter. Remove and discard rubber 'O'
ring from breather pipe.
Refit
5.Fit new rubber 'O' ring to engine breather.
6.Connect breather bottom hose.
7.Locate breather into rocker cover and secure
with retaining bolt, tightening to
9 Nm (7 lbf/ft).
8.Connect breather top hose.
Page 50 of 455
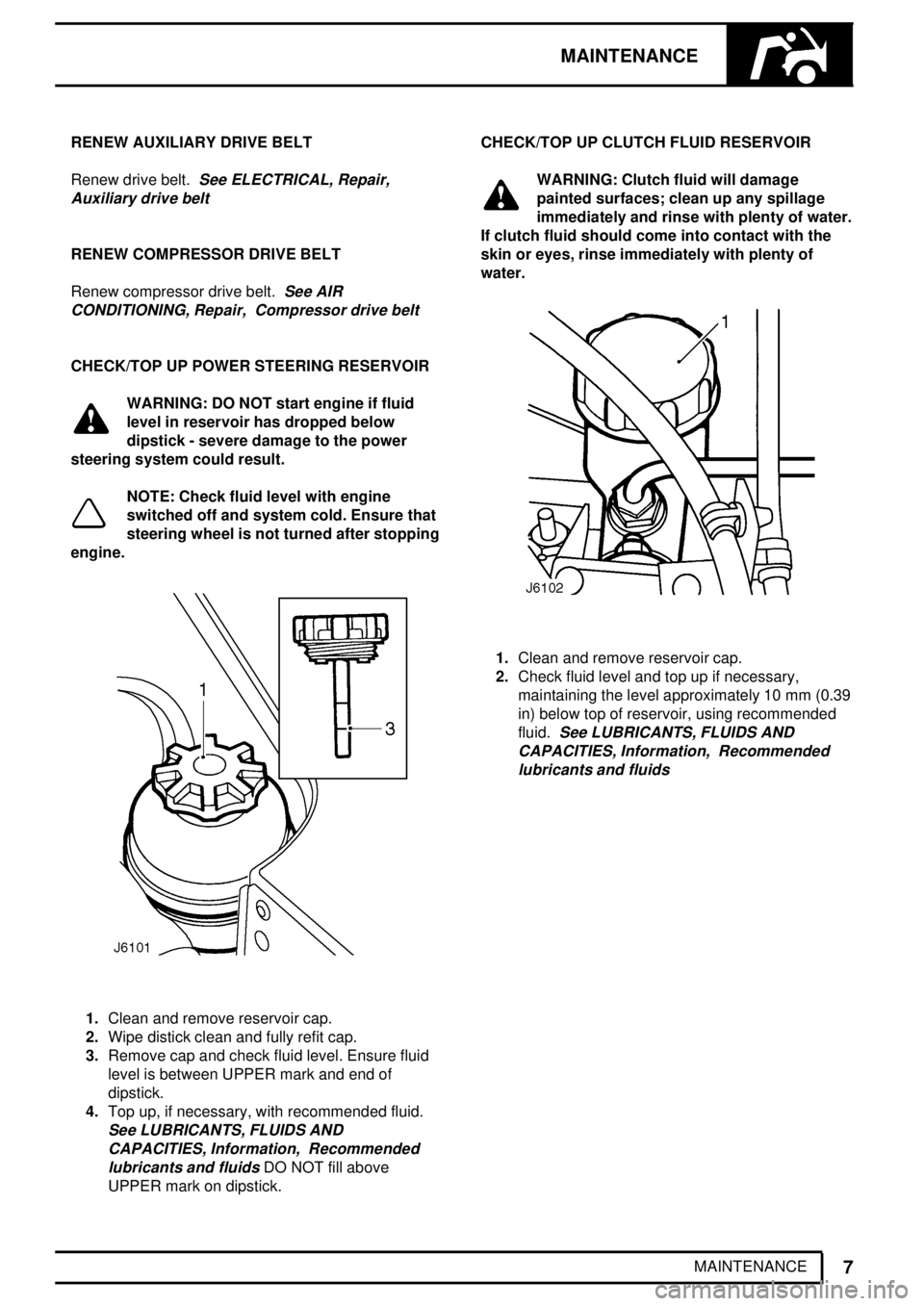
MAINTENANCE
7
MAINTENANCE RENEW AUXILIARY DRIVE BELT
Renew drive belt.
See ELECTRICAL, Repair,
Auxiliary drive belt
RENEW COMPRESSOR DRIVE BELT
Renew compressor drive belt.
See AIR
CONDITIONING, Repair, Compressor drive belt
CHECK/TOP UP POWER STEERING RESERVOIR
WARNING: DO NOT start engine if fluid
level in reservoir has dropped below
dipstick - severe damage to the power
steering system could result.
NOTE: Check fluid level with engine
switched off and system cold. Ensure that
steering wheel is not turned after stopping
engine.
1.Clean and remove reservoir cap.
2.Wipe distick clean and fully refit cap.
3.Remove cap and check fluid level. Ensure fluid
level is between UPPER mark and end of
dipstick.
4.Top up, if necessary, with recommended fluid.
See LUBRICANTS, FLUIDS AND
CAPACITIES, Information, Recommended
lubricants and fluids
DO NOT fill above
UPPER mark on dipstick.CHECK/TOP UP CLUTCH FLUID RESERVOIR
WARNING: Clutch fluid will damage
painted surfaces; clean up any spillage
immediately and rinse with plenty of water.
If clutch fluid should come into contact with the
skin or eyes, rinse immediately with plenty of
water.
1.Clean and remove reservoir cap.
2.Check fluid level and top up if necessary,
maintaining the level approximately 10 mm (0.39
in) below top of reservoir, using recommended
fluid.
See LUBRICANTS, FLUIDS AND
CAPACITIES, Information, Recommended
lubricants and fluids
Page 51 of 455
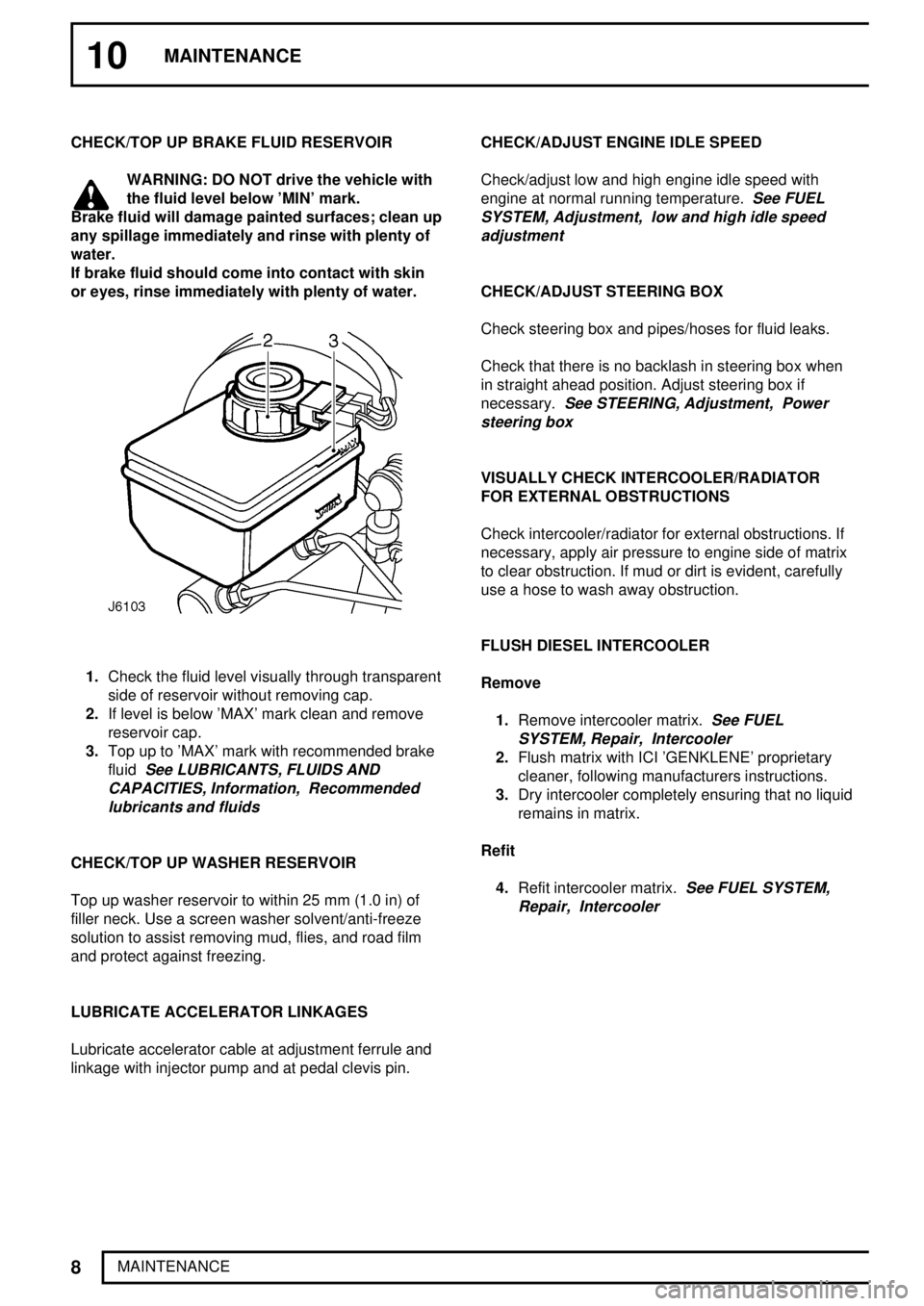
10MAINTENANCE
8
MAINTENANCE CHECK/TOP UP BRAKE FLUID RESERVOIR
WARNING: DO NOT drive the vehicle with
the fluid level below 'MIN' mark.
Brake fluid will damage painted surfaces; clean up
any spillage immediately and rinse with plenty of
water.
If brake fluid should come into contact with skin
or eyes, rinse immediately with plenty of water.
1.Check the fluid level visually through transparent
side of reservoir without removing cap.
2.If level is below 'MAX' mark clean and remove
reservoir cap.
3.Top up to 'MAX' mark with recommended brake
fluid
See LUBRICANTS, FLUIDS AND
CAPACITIES, Information, Recommended
lubricants and fluids
CHECK/TOP UP WASHER RESERVOIR
Top up washer reservoir to within 25 mm (1.0 in) of
filler neck. Use a screen washer solvent/anti-freeze
solution to assist removing mud, flies, and road film
and protect against freezing.
LUBRICATE ACCELERATOR LINKAGES
Lubricate accelerator cable at adjustment ferrule and
linkage with injector pump and at pedal clevis pin.CHECK/ADJUST ENGINE IDLE SPEED
Check/adjust low and high engine idle speed with
engine at normal running temperature.
See FUEL
SYSTEM, Adjustment, low and high idle speed
adjustment
CHECK/ADJUST STEERING BOX
Check steering box and pipes/hoses for fluid leaks.
Check that there is no backlash in steering box when
in straight ahead position. Adjust steering box if
necessary.
See STEERING, Adjustment, Power
steering box
VISUALLY CHECK INTERCOOLER/RADIATOR
FOR EXTERNAL OBSTRUCTIONS
Check intercooler/radiator for external obstructions. If
necessary, apply air pressure to engine side of matrix
to clear obstruction. If mud or dirt is evident, carefully
use a hose to wash away obstruction.
FLUSH DIESEL INTERCOOLER
Remove
1.Remove intercooler matrix.
See FUEL
SYSTEM, Repair, Intercooler
2.Flush matrix with ICI 'GENKLENE' proprietary
cleaner, following manufacturers instructions.
3.Dry intercooler completely ensuring that no liquid
remains in matrix.
Refit
4.Refit intercooler matrix.
See FUEL SYSTEM,
Repair, Intercooler
Page 52 of 455
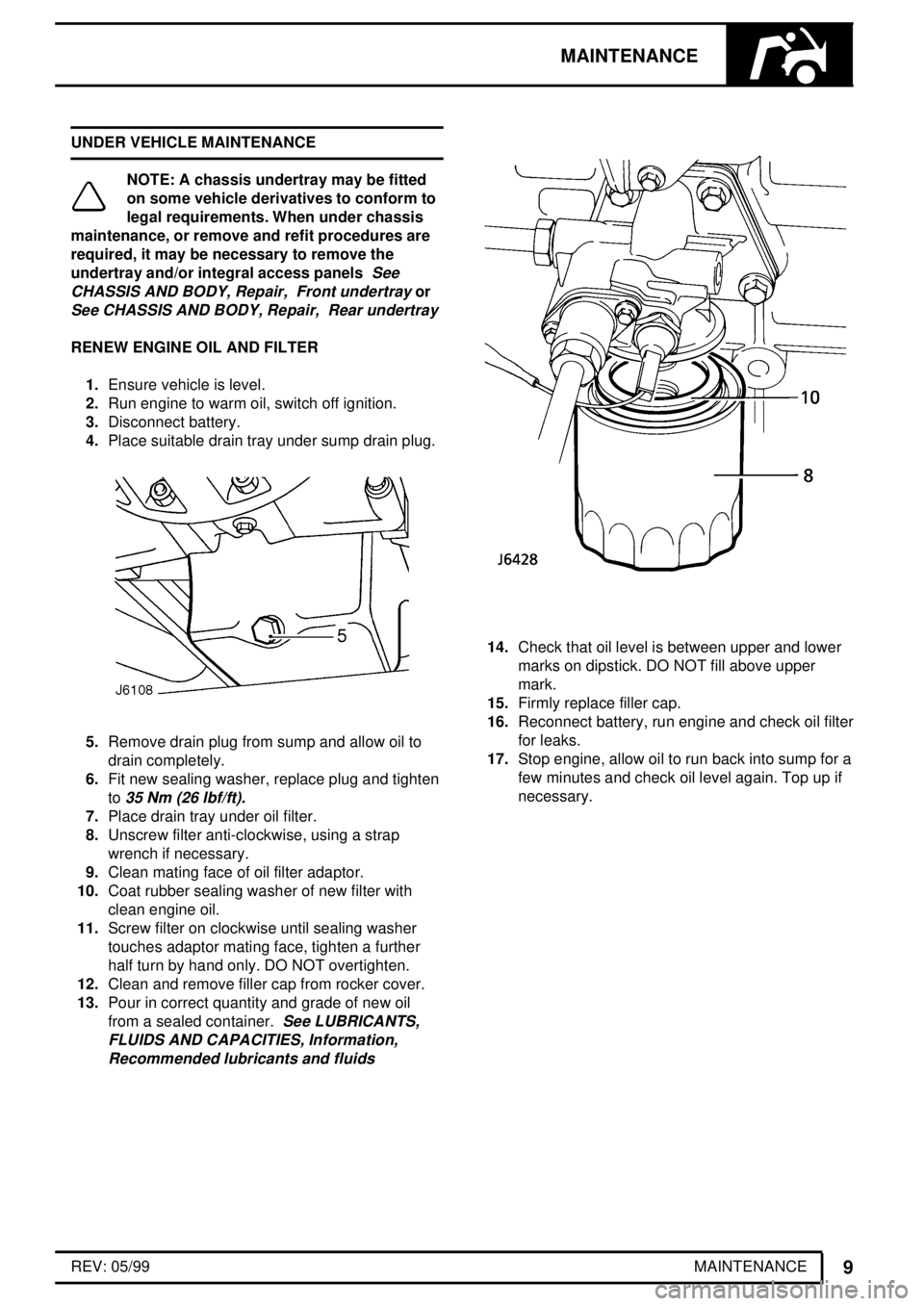
MAINTENANCE
9
MAINTENANCE REV: 05/99 UNDER VEHICLE MAINTENANCE
NOTE: A chassis undertray may be fitted
on some vehicle derivatives to conform to
legal requirements. When under chassis
maintenance, or remove and refit procedures are
required, it may be necessary to remove the
undertray and/or integral access panels
See
CHASSIS AND BODY, Repair, Front undertray
or
See CHASSIS AND BODY, Repair, Rear undertray
RENEW ENGINE OIL AND FILTER
1.Ensure vehicle is level.
2.Run engine to warm oil, switch off ignition.
3.Disconnect battery.
4.Place suitable drain tray under sump drain plug.
5.Remove drain plug from sump and allow oil to
drain completely.
6.Fit new sealing washer, replace plug and tighten
to
35 Nm (26 lbf/ft).
7.Place drain tray under oil filter.
8.Unscrew filter anti-clockwise, using a strap
wrench if necessary.
9.Clean mating face of oil filter adaptor.
10.Coat rubber sealing washer of new filter with
clean engine oil.
11.Screw filter on clockwise until sealing washer
touches adaptor mating face, tighten a further
half turn by hand only. DO NOT overtighten.
12.Clean and remove filler cap from rocker cover.
13.Pour in correct quantity and grade of new oil
from a sealed container.
See LUBRICANTS,
FLUIDS AND CAPACITIES, Information,
Recommended lubricants and fluids
14.Check that oil level is between upper and lower
marks on dipstick. DO NOT fill above upper
mark.
15.Firmly replace filler cap.
16.Reconnect battery, run engine and check oil filter
for leaks.
17.Stop engine, allow oil to run back into sump for a
few minutes and check oil level again. Top up if
necessary.
Page 56 of 455
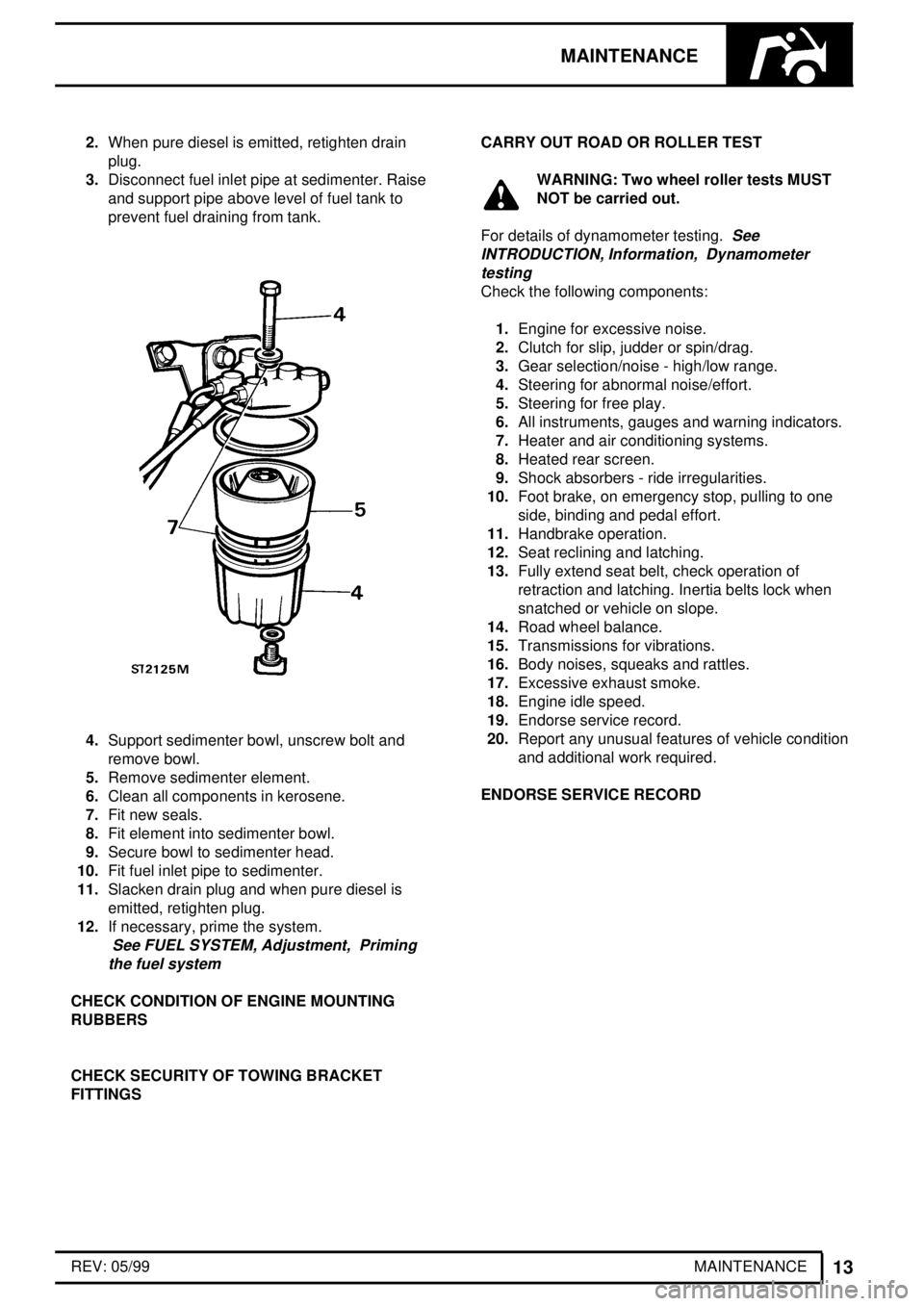
MAINTENANCE
13
MAINTENANCE REV: 05/992.When pure diesel is emitted, retighten drain
plug.
3.Disconnect fuel inlet pipe at sedimenter. Raise
and support pipe above level of fuel tank to
prevent fuel draining from tank.
4.Support sedimenter bowl, unscrew bolt and
remove bowl.
5.Remove sedimenter element.
6.Clean all components in kerosene.
7.Fit new seals.
8.Fit element into sedimenter bowl.
9.Secure bowl to sedimenter head.
10.Fit fuel inlet pipe to sedimenter.
11.Slacken drain plug and when pure diesel is
emitted, retighten plug.
12.If necessary, prime the system.
See FUEL SYSTEM, Adjustment, Priming
the fuel system
CHECK CONDITION OF ENGINE MOUNTING
RUBBERS
CHECK SECURITY OF TOWING BRACKET
FITTINGSCARRY OUT ROAD OR ROLLER TEST
WARNING: Two wheel roller tests MUST
NOT be carried out.
For details of dynamometer testing.
See
INTRODUCTION, Information, Dynamometer
testing
Check the following components:
1.Engine for excessive noise.
2.Clutch for slip, judder or spin/drag.
3.Gear selection/noise - high/low range.
4.Steering for abnormal noise/effort.
5.Steering for free play.
6.All instruments, gauges and warning indicators.
7.Heater and air conditioning systems.
8.Heated rear screen.
9.Shock absorbers - ride irregularities.
10.Foot brake, on emergency stop, pulling to one
side, binding and pedal effort.
11.Handbrake operation.
12.Seat reclining and latching.
13.Fully extend seat belt, check operation of
retraction and latching. Inertia belts lock when
snatched or vehicle on slope.
14.Road wheel balance.
15.Transmissions for vibrations.
16.Body noises, squeaks and rattles.
17.Excessive exhaust smoke.
18.Engine idle speed.
19.Endorse service record.
20.Report any unusual features of vehicle condition
and additional work required.
ENDORSE SERVICE RECORD