check engine LAND ROVER DEFENDER 1996 Owner's Guide
[x] Cancel search | Manufacturer: LAND ROVER, Model Year: 1996, Model line: DEFENDER, Model: LAND ROVER DEFENDER 1996Pages: 455, PDF Size: 6.44 MB
Page 143 of 455
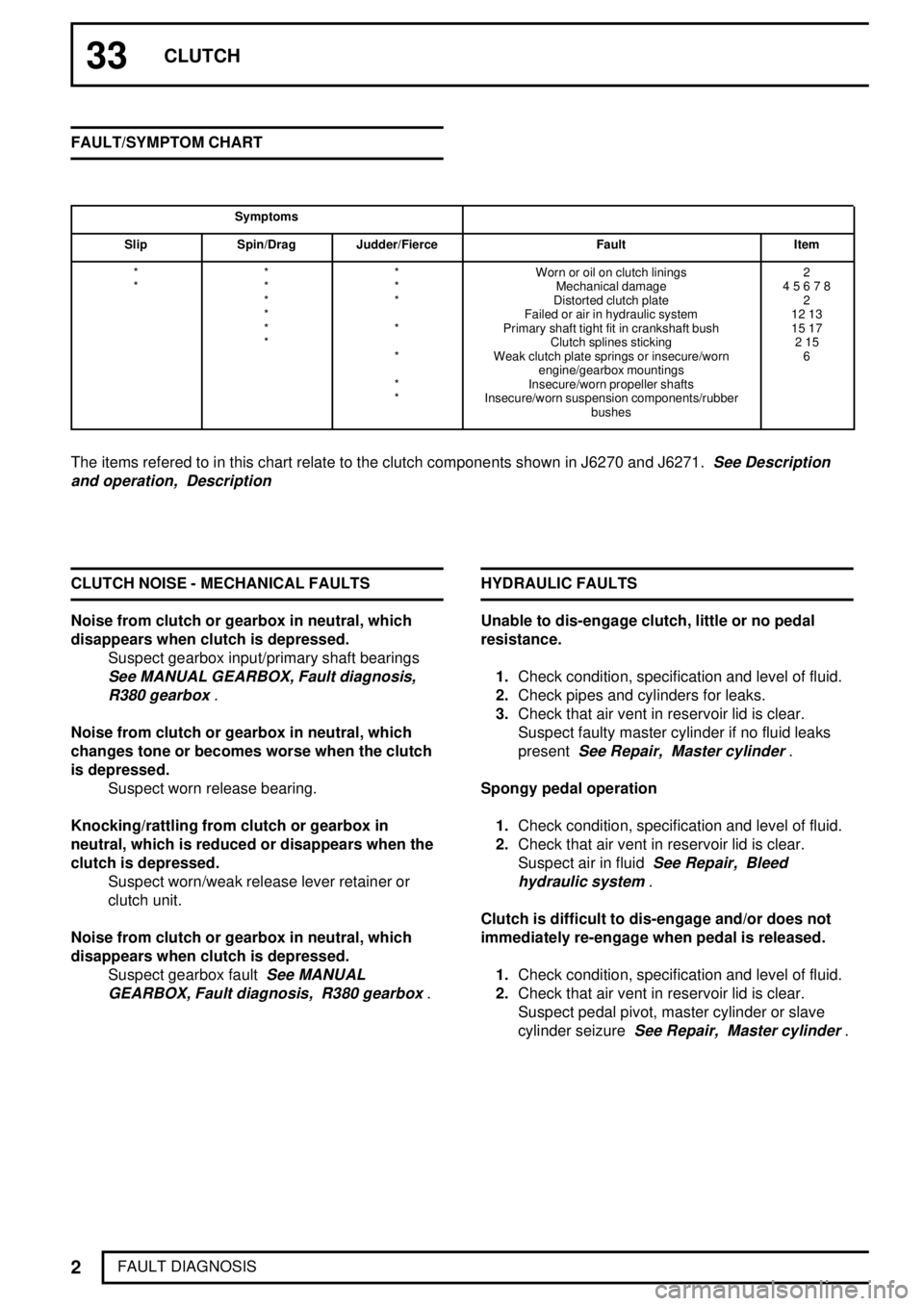
33CLUTCH
2
FAULT DIAGNOSIS FAULT/SYMPTOM CHART
Symptoms
Slip Spin/Drag Judder/Fierce Fault Item
* * * Worn or oil on clutch linings 2
* * * Mechanical damage45678
* * Distorted clutch plate 2
* Failed or air in hydraulic system 12 13
* * Primary shaft tight fit in crankshaft bush 15 17
* Clutch splines sticking 2 15
* Weak clutch plate springs or insecure/worn
engine/gearbox mountings6
* Insecure/worn propeller shafts
* Insecure/worn suspension components/rubber
bushes
The items refered to in this chart relate to the clutch components shown in J6270 and J6271.See Description
and operation, Description
CLUTCH NOISE - MECHANICAL FAULTS
Noise from clutch or gearbox in neutral, which
disappears when clutch is depressed.
Suspect gearbox input/primary shaft bearings
See MANUAL GEARBOX, Fault diagnosis,
R380 gearbox
.
Noise from clutch or gearbox in neutral, which
changes tone or becomes worse when the clutch
is depressed.
Suspect worn release bearing.
Knocking/rattling from clutch or gearbox in
neutral, which is reduced or disappears when the
clutch is depressed.
Suspect worn/weak release lever retainer or
clutch unit.
Noise from clutch or gearbox in neutral, which
disappears when clutch is depressed.
Suspect gearbox fault
See MANUAL
GEARBOX, Fault diagnosis, R380 gearbox
.HYDRAULIC FAULTS
Unable to dis-engage clutch, little or no pedal
resistance.
1.Check condition, specification and level of fluid.
2.Check pipes and cylinders for leaks.
3.Check that air vent in reservoir lid is clear.
Suspect faulty master cylinder if no fluid leaks
present
See Repair, Master cylinder.
Spongy pedal operation
1.Check condition, specification and level of fluid.
2.Check that air vent in reservoir lid is clear.
Suspect air in fluid
See Repair, Bleed
hydraulic system
.
Clutch is difficult to dis-engage and/or does not
immediately re-engage when pedal is released.
1.Check condition, specification and level of fluid.
2.Check that air vent in reservoir lid is clear.
Suspect pedal pivot, master cylinder or slave
cylinder seizure
See Repair, Master cylinder.
Page 146 of 455
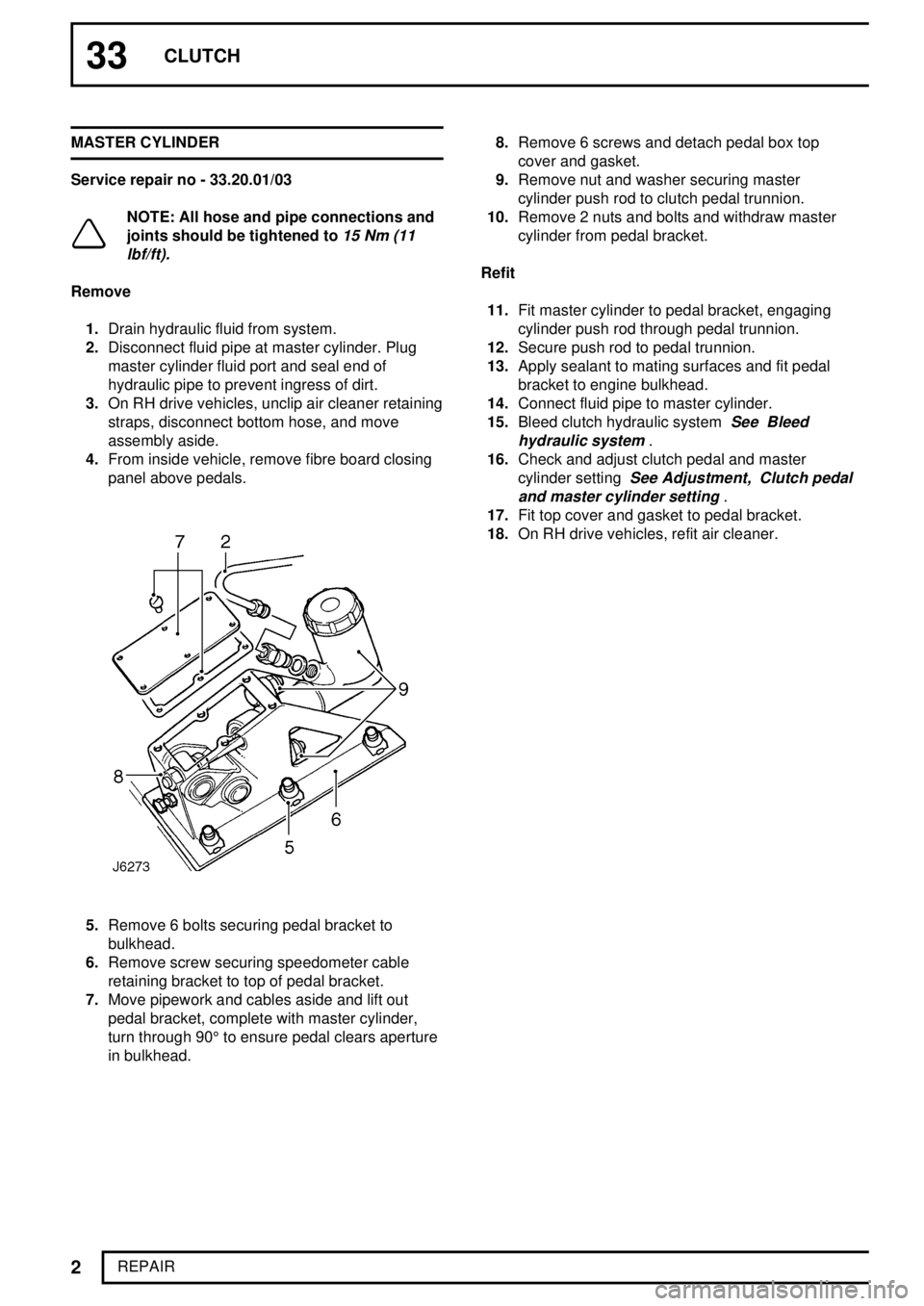
33CLUTCH
2
REPAIR MASTER CYLINDER
Service repair no - 33.20.01/03
NOTE: All hose and pipe connections and
joints should be tightened to
15 Nm (11
lbf/ft).
Remove
1.Drain hydraulic fluid from system.
2.Disconnect fluid pipe at master cylinder. Plug
master cylinder fluid port and seal end of
hydraulic pipe to prevent ingress of dirt.
3.On RH drive vehicles, unclip air cleaner retaining
straps, disconnect bottom hose, and move
assembly aside.
4.From inside vehicle, remove fibre board closing
panel above pedals.
5.Remove 6 bolts securing pedal bracket to
bulkhead.
6.Remove screw securing speedometer cable
retaining bracket to top of pedal bracket.
7.Move pipework and cables aside and lift out
pedal bracket, complete with master cylinder,
turn through 90°to ensure pedal clears aperture
in bulkhead.8.Remove 6 screws and detach pedal box top
cover and gasket.
9.Remove nut and washer securing master
cylinder push rod to clutch pedal trunnion.
10.Remove 2 nuts and bolts and withdraw master
cylinder from pedal bracket.
Refit
11.Fit master cylinder to pedal bracket, engaging
cylinder push rod through pedal trunnion.
12.Secure push rod to pedal trunnion.
13.Apply sealant to mating surfaces and fit pedal
bracket to engine bulkhead.
14.Connect fluid pipe to master cylinder.
15.Bleed clutch hydraulic system
See Bleed
hydraulic system
.
16.Check and adjust clutch pedal and master
cylinder setting
See Adjustment, Clutch pedal
and master cylinder setting
.
17.Fit top cover and gasket to pedal bracket.
18.On RH drive vehicles, refit air cleaner.
Page 153 of 455
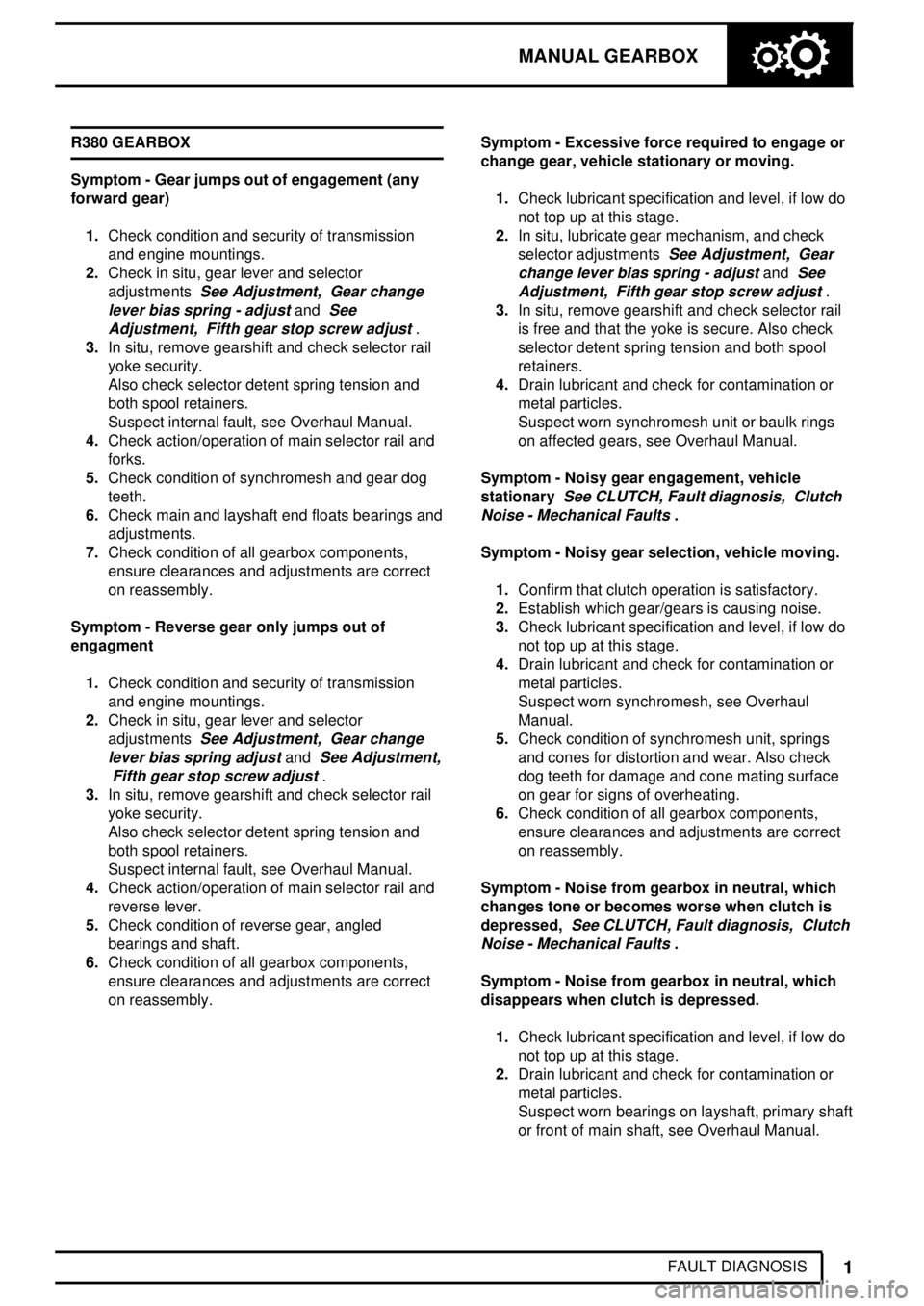
MANUAL GEARBOX
1
FAULT DIAGNOSIS R380 GEARBOX
Symptom - Gear jumps out of engagement (any
forward gear)
1.Check condition and security of transmission
and engine mountings.
2.Check in situ, gear lever and selector
adjustments
See Adjustment, Gear change
lever bias spring - adjust
andSee
Adjustment, Fifth gear stop screw adjust
.
3.In situ, remove gearshift and check selector rail
yoke security.
Also check selector detent spring tension and
both spool retainers.
Suspect internal fault, see Overhaul Manual.
4.Check action/operation of main selector rail and
forks.
5.Check condition of synchromesh and gear dog
teeth.
6.Check main and layshaft end floats bearings and
adjustments.
7.Check condition of all gearbox components,
ensure clearances and adjustments are correct
on reassembly.
Symptom - Reverse gear only jumps out of
engagment
1.Check condition and security of transmission
and engine mountings.
2.Check in situ, gear lever and selector
adjustments
See Adjustment, Gear change
lever bias spring adjust
andSee Adjustment,
Fifth gear stop screw adjust
.
3.In situ, remove gearshift and check selector rail
yoke security.
Also check selector detent spring tension and
both spool retainers.
Suspect internal fault, see Overhaul Manual.
4.Check action/operation of main selector rail and
reverse lever.
5.Check condition of reverse gear, angled
bearings and shaft.
6.Check condition of all gearbox components,
ensure clearances and adjustments are correct
on reassembly.Symptom - Excessive force required to engage or
change gear, vehicle stationary or moving.
1.Check lubricant specification and level, if low do
not top up at this stage.
2.In situ, lubricate gear mechanism, and check
selector adjustments
See Adjustment, Gear
change lever bias spring - adjust
andSee
Adjustment, Fifth gear stop screw adjust
.
3.In situ, remove gearshift and check selector rail
is free and that the yoke is secure. Also check
selector detent spring tension and both spool
retainers.
4.Drain lubricant and check for contamination or
metal particles.
Suspect worn synchromesh unit or baulk rings
on affected gears, see Overhaul Manual.
Symptom - Noisy gear engagement, vehicle
stationary
See CLUTCH, Fault diagnosis, Clutch
Noise - Mechanical Faults
.
Symptom - Noisy gear selection, vehicle moving.
1.Confirm that clutch operation is satisfactory.
2.Establish which gear/gears is causing noise.
3.Check lubricant specification and level, if low do
not top up at this stage.
4.Drain lubricant and check for contamination or
metal particles.
Suspect worn synchromesh, see Overhaul
Manual.
5.Check condition of synchromesh unit, springs
and cones for distortion and wear. Also check
dog teeth for damage and cone mating surface
on gear for signs of overheating.
6.Check condition of all gearbox components,
ensure clearances and adjustments are correct
on reassembly.
Symptom - Noise from gearbox in neutral, which
changes tone or becomes worse when clutch is
depressed,
See CLUTCH, Fault diagnosis, Clutch
Noise - Mechanical Faults
.
Symptom - Noise from gearbox in neutral, which
disappears when clutch is depressed.
1.Check lubricant specification and level, if low do
not top up at this stage.
2.Drain lubricant and check for contamination or
metal particles.
Suspect worn bearings on layshaft, primary shaft
or front of main shaft, see Overhaul Manual.
Page 163 of 455
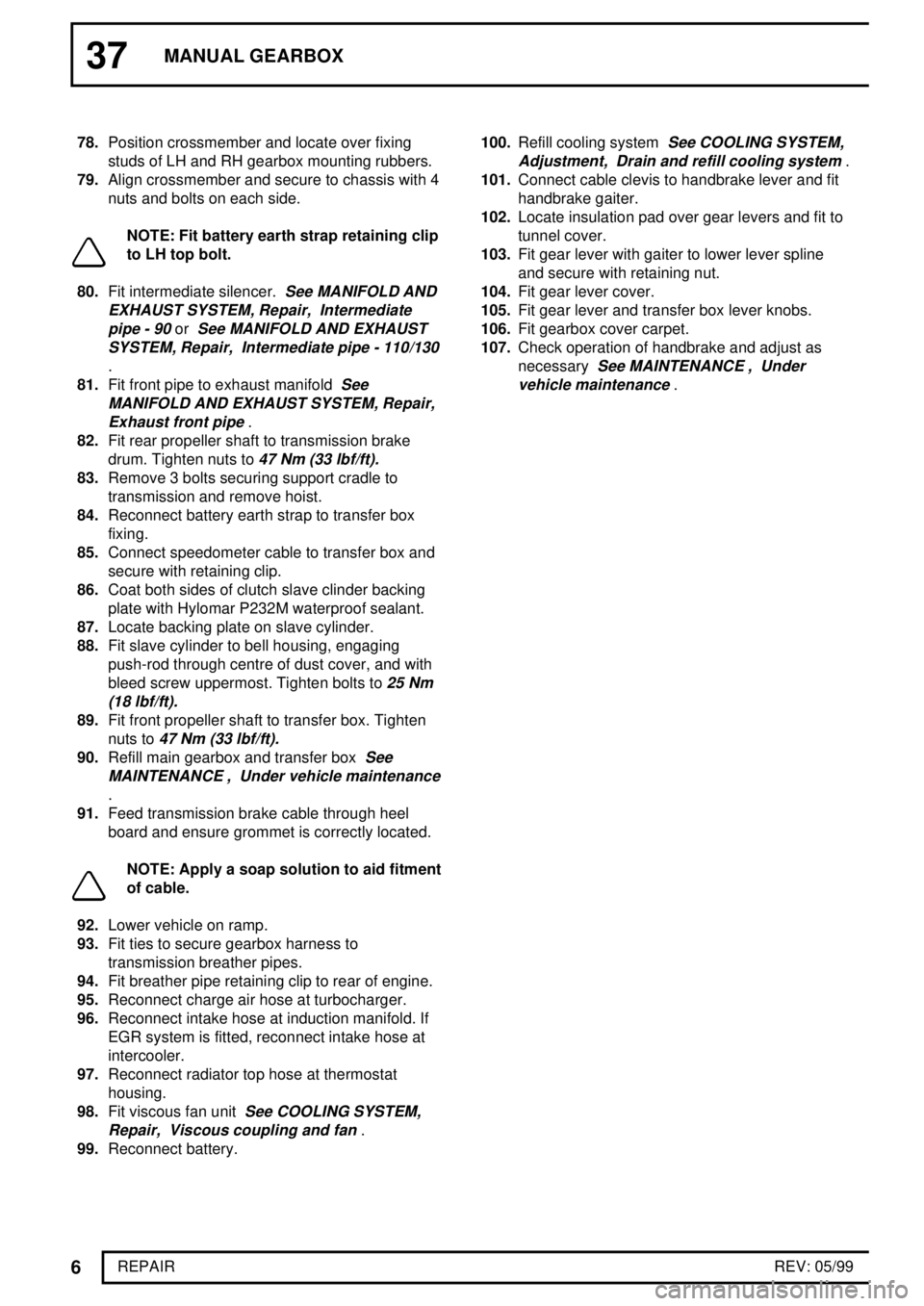
37MANUAL GEARBOX
6
REPAIRREV: 05/99 78.Position crossmember and locate over fixing
studs of LH and RH gearbox mounting rubbers.
79.Align crossmember and secure to chassis with 4
nuts and bolts on each side.
NOTE: Fit battery earth strap retaining clip
to LH top bolt.
80.Fit intermediate silencer.
See MANIFOLD AND
EXHAUST SYSTEM, Repair, Intermediate
pipe - 90
orSee MANIFOLD AND EXHAUST
SYSTEM, Repair, Intermediate pipe - 110/130
.
81.Fit front pipe to exhaust manifold
See
MANIFOLD AND EXHAUST SYSTEM, Repair,
Exhaust front pipe
.
82.Fit rear propeller shaft to transmission brake
drum. Tighten nuts to
47 Nm (33 lbf/ft).
83.Remove 3 bolts securing support cradle to
transmission and remove hoist.
84.Reconnect battery earth strap to transfer box
fixing.
85.Connect speedometer cable to transfer box and
secure with retaining clip.
86.Coat both sides of clutch slave clinder backing
plate with Hylomar P232M waterproof sealant.
87.Locate backing plate on slave cylinder.
88.Fit slave cylinder to bell housing, engaging
push-rod through centre of dust cover, and with
bleed screw uppermost. Tighten bolts to
25 Nm
(18 lbf/ft).
89.Fit front propeller shaft to transfer box. Tighten
nuts to
47 Nm (33 lbf/ft).
90.Refill main gearbox and transfer boxSee
MAINTENANCE , Under vehicle maintenance
.
91.Feed transmission brake cable through heel
board and ensure grommet is correctly located.
NOTE: Apply a soap solution to aid fitment
of cable.
92.Lower vehicle on ramp.
93.Fit ties to secure gearbox harness to
transmission breather pipes.
94.Fit breather pipe retaining clip to rear of engine.
95.Reconnect charge air hose at turbocharger.
96.Reconnect intake hose at induction manifold. If
EGR system is fitted, reconnect intake hose at
intercooler.
97.Reconnect radiator top hose at thermostat
housing.
98.Fit viscous fan unit
See COOLING SYSTEM,
Repair, Viscous coupling and fan
.
99.Reconnect battery.100.Refill cooling system
See COOLING SYSTEM,
Adjustment, Drain and refill cooling system
.
101.Connect cable clevis to handbrake lever and fit
handbrake gaiter.
102.Locate insulation pad over gear levers and fit to
tunnel cover.
103.Fit gear lever with gaiter to lower lever spline
and secure with retaining nut.
104.Fit gear lever cover.
105.Fit gear lever and transfer box lever knobs.
106.Fit gearbox cover carpet.
107.Check operation of handbrake and adjust as
necessary
See MAINTENANCE , Under
vehicle maintenance
.
Page 167 of 455
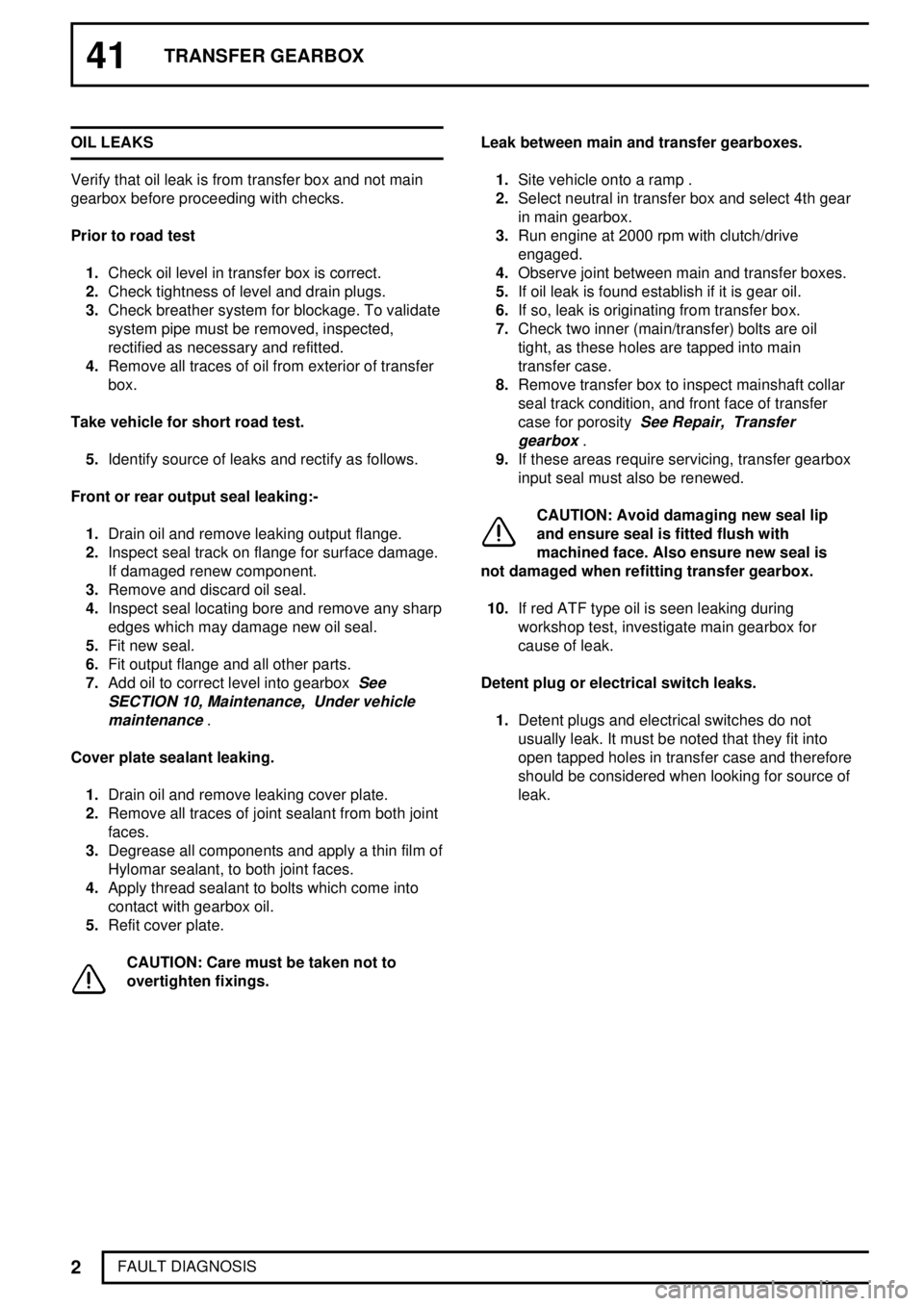
41TRANSFER GEARBOX
2
FAULT DIAGNOSIS OIL LEAKS
Verify that oil leak is from transfer box and not main
gearbox before proceeding with checks.
Prior to road test
1.Check oil level in transfer box is correct.
2.Check tightness of level and drain plugs.
3.Check breather system for blockage. To validate
system pipe must be removed, inspected,
rectified as necessary and refitted.
4.Remove all traces of oil from exterior of transfer
box.
Take vehicle for short road test.
5.Identify source of leaks and rectify as follows.
Front or rear output seal leaking:-
1.Drain oil and remove leaking output flange.
2.Inspect seal track on flange for surface damage.
If damaged renew component.
3.Remove and discard oil seal.
4.Inspect seal locating bore and remove any sharp
edges which may damage new oil seal.
5.Fit new seal.
6.Fit output flange and all other parts.
7.Add oil to correct level into gearbox
See
SECTION 10, Maintenance, Under vehicle
maintenance
.
Cover plate sealant leaking.
1.Drain oil and remove leaking cover plate.
2.Remove all traces of joint sealant from both joint
faces.
3.Degrease all components and apply a thin film of
Hylomar sealant, to both joint faces.
4.Apply thread sealant to bolts which come into
contact with gearbox oil.
5.Refit cover plate.
CAUTION: Care must be taken not to
overtighten fixings.Leak between main and transfer gearboxes.
1.Site vehicle onto a ramp .
2.Select neutral in transfer box and select 4th gear
in main gearbox.
3.Run engine at 2000 rpm with clutch/drive
engaged.
4.Observe joint between main and transfer boxes.
5.If oil leak is found establish if it is gear oil.
6.If so, leak is originating from transfer box.
7.Check two inner (main/transfer) bolts are oil
tight, as these holes are tapped into main
transfer case.
8.Remove transfer box to inspect mainshaft collar
seal track condition, and front face of transfer
case for porosity
See Repair, Transfer
gearbox
.
9.If these areas require servicing, transfer gearbox
input seal must also be renewed.
CAUTION: Avoid damaging new seal lip
and ensure seal is fitted flush with
machined face. Also ensure new seal is
not damaged when refitting transfer gearbox.
10.If red ATF type oil is seen leaking during
workshop test, investigate main gearbox for
cause of leak.
Detent plug or electrical switch leaks.
1.Detent plugs and electrical switches do not
usually leak. It must be noted that they fit into
open tapped holes in transfer case and therefore
should be considered when looking for source of
leak.
Page 224 of 455
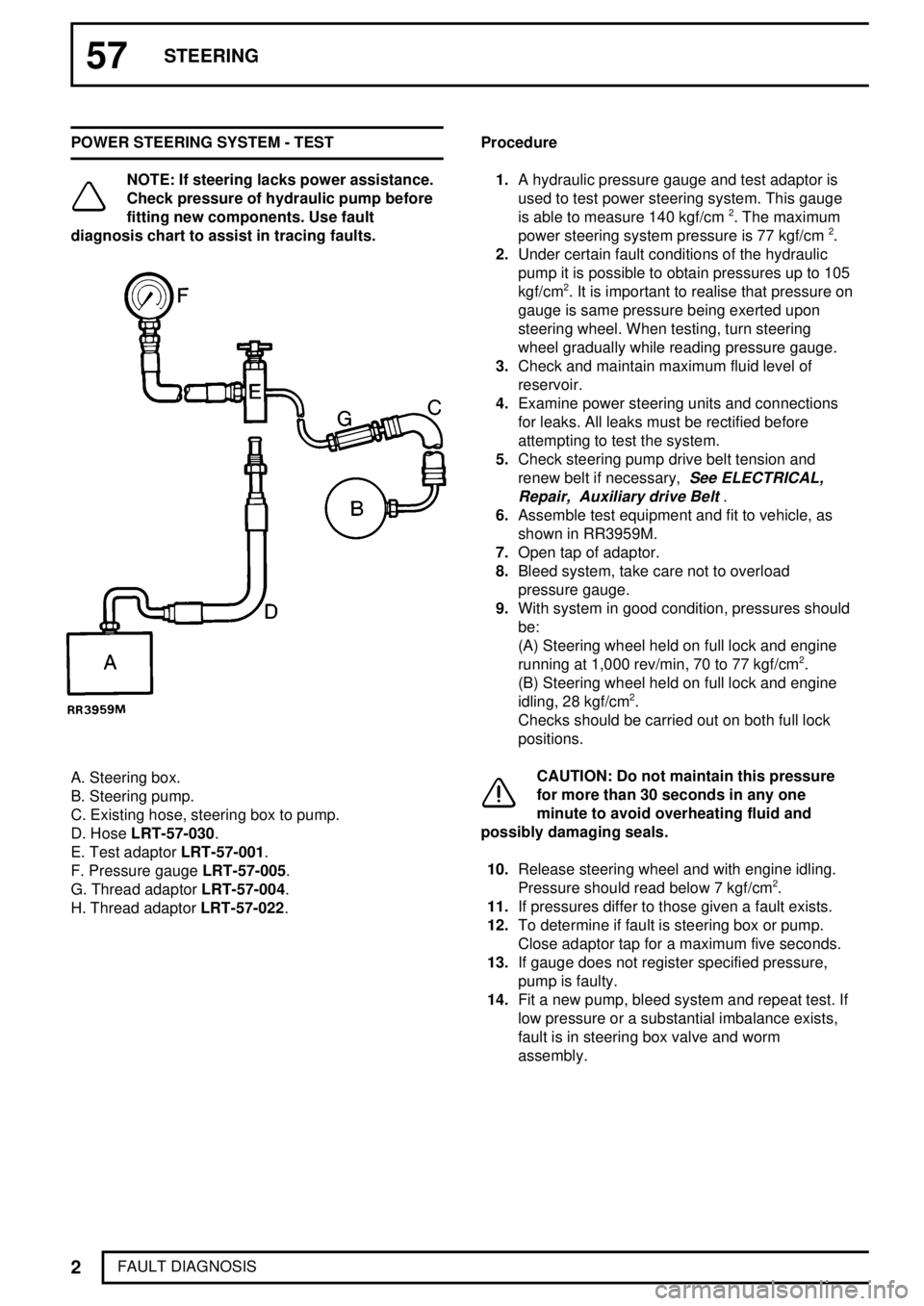
57STEERING
2
FAULT DIAGNOSIS POWER STEERING SYSTEM - TEST
NOTE: If steering lacks power assistance.
Check pressure of hydraulic pump before
fitting new components. Use fault
diagnosis chart to assist in tracing faults.
A. Steering box.
B. Steering pump.
C. Existing hose, steering box to pump.
D. HoseLRT-57-030.
E. Test adaptorLRT-57-001.
F. Pressure gaugeLRT-57-005.
G. Thread adaptorLRT-57-004.
H. Thread adaptorLRT-57-022.Procedure
1.A hydraulic pressure gauge and test adaptor is
used to test power steering system. This gauge
is able to measure 140 kgf/cm
2. The maximum
power steering system pressure is 77 kgf/cm2.
2.Under certain fault conditions of the hydraulic
pump it is possible to obtain pressures up to 105
kgf/cm
2. It is important to realise that pressure on
gauge is same pressure being exerted upon
steering wheel. When testing, turn steering
wheel gradually while reading pressure gauge.
3.Check and maintain maximum fluid level of
reservoir.
4.Examine power steering units and connections
for leaks. All leaks must be rectified before
attempting to test the system.
5.Check steering pump drive belt tension and
renew belt if necessary,
See ELECTRICAL,
Repair, Auxiliary drive Belt
.
6.Assemble test equipment and fit to vehicle, as
shown in RR3959M.
7.Open tap of adaptor.
8.Bleed system, take care not to overload
pressure gauge.
9.With system in good condition, pressures should
be:
(A) Steering wheel held on full lock and engine
running at 1,000 rev/min, 70 to 77 kgf/cm
2.
(B) Steering wheel held on full lock and engine
idling, 28 kgf/cm
2.
Checks should be carried out on both full lock
positions.
CAUTION: Do not maintain this pressure
for more than 30 seconds in any one
minute to avoid overheating fluid and
possibly damaging seals.
10.Release steering wheel and with engine idling.
Pressure should read below 7 kgf/cm
2.
11.If pressures differ to those given a fault exists.
12.To determine if fault is steering box or pump.
Close adaptor tap for a maximum five seconds.
13.If gauge does not register specified pressure,
pump is faulty.
14.Fit a new pump, bleed system and repeat test. If
low pressure or a substantial imbalance exists,
fault is in steering box valve and worm
assembly.
Page 230 of 455
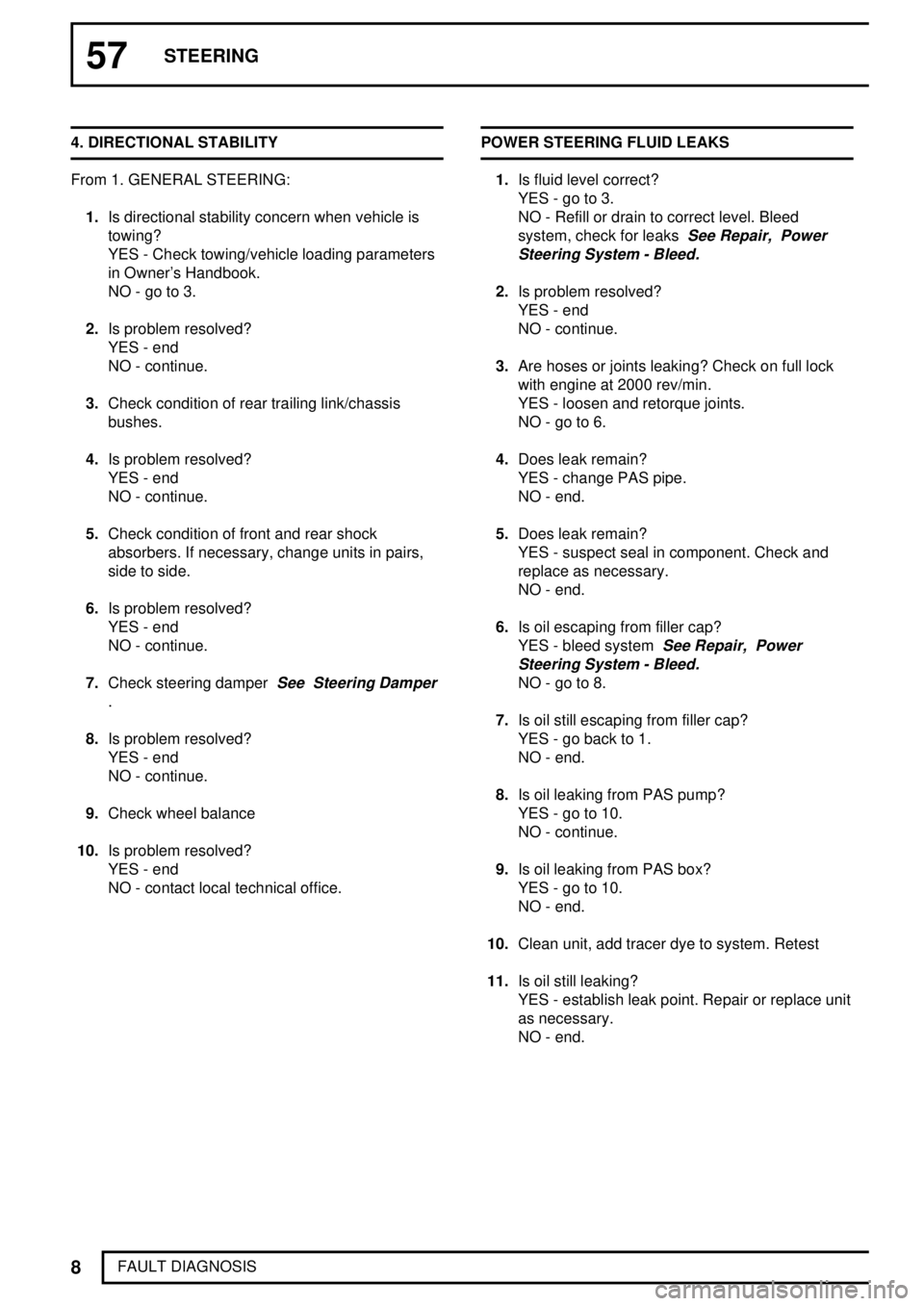
57STEERING
8
FAULT DIAGNOSIS 4. DIRECTIONAL STABILITY
From 1. GENERAL STEERING:
1.Is directional stability concern when vehicle is
towing?
YES - Check towing/vehicle loading parameters
in Owner's Handbook.
NO - go to 3.
2.Is problem resolved?
YES - end
NO - continue.
3.Check condition of rear trailing link/chassis
bushes.
4.Is problem resolved?
YES - end
NO - continue.
5.Check condition of front and rear shock
absorbers. If necessary, change units in pairs,
side to side.
6.Is problem resolved?
YES - end
NO - continue.
7.Check steering damper
See Steering Damper
.
8.Is problem resolved?
YES - end
NO - continue.
9.Check wheel balance
10.Is problem resolved?
YES - end
NO - contact local technical office.POWER STEERING FLUID LEAKS
1.Is fluid level correct?
YES - go to 3.
NO - Refill or drain to correct level. Bleed
system, check for leaks
See Repair, Power
Steering System - Bleed.
2.Is problem resolved?
YES - end
NO - continue.
3.Are hoses or joints leaking? Check on full lock
with engine at 2000 rev/min.
YES - loosen and retorque joints.
NO - go to 6.
4.Does leak remain?
YES - change PAS pipe.
NO - end.
5.Does leak remain?
YES - suspect seal in component. Check and
replace as necessary.
NO - end.
6.Is oil escaping from filler cap?
YES - bleed system
See Repair, Power
Steering System - Bleed.
NO - go to 8.
7.Is oil still escaping from filler cap?
YES - go back to 1.
NO - end.
8.Is oil leaking from PAS pump?
YES - go to 10.
NO - continue.
9.Is oil leaking from PAS box?
YES - go to 10.
NO - end.
10.Clean unit, add tracer dye to system. Retest
11.Is oil still leaking?
YES - establish leak point. Repair or replace unit
as necessary.
NO - end.
Page 233 of 455
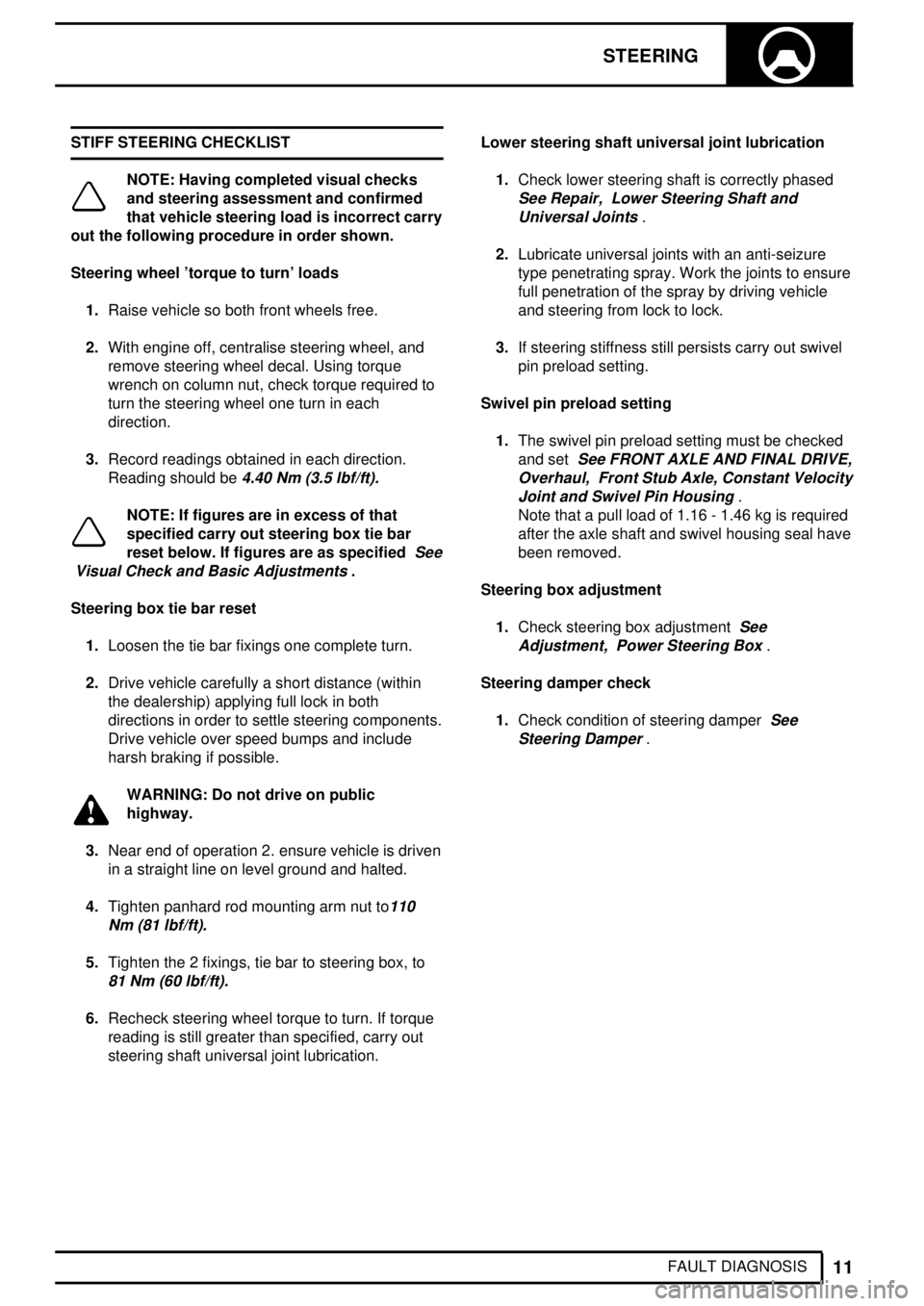
STEERING
11
FAULT DIAGNOSIS STIFF STEERING CHECKLIST
NOTE: Having completed visual checks
and steering assessment and confirmed
that vehicle steering load is incorrect carry
out the following procedure in order shown.
Steering wheel 'torque to turn' loads
1.Raise vehicle so both front wheels free.
2.With engine off, centralise steering wheel, and
remove steering wheel decal. Using torque
wrench on column nut, check torque required to
turn the steering wheel one turn in each
direction.
3.Record readings obtained in each direction.
Reading should be
4.40 Nm (3.5 lbf/ft).
NOTE: If figures are in excess of that
specified carry out steering box tie bar
reset below. If figures are as specified
See
Visual Check and Basic Adjustments
.
Steering box tie bar reset
1.Loosen the tie bar fixings one complete turn.
2.Drive vehicle carefully a short distance (within
the dealership) applying full lock in both
directions in order to settle steering components.
Drive vehicle over speed bumps and include
harsh braking if possible.
WARNING: Do not drive on public
highway.
3.Near end of operation 2. ensure vehicle is driven
in a straight line on level ground and halted.
4.Tighten panhard rod mounting arm nut to
110
Nm (81 lbf/ft).
5.Tighten the 2 fixings, tie bar to steering box, to
81 Nm (60 lbf/ft).
6.Recheck steering wheel torque to turn. If torque
reading is still greater than specified, carry out
steering shaft universal joint lubrication.Lower steering shaft universal joint lubrication
1.Check lower steering shaft is correctly phased
See Repair, Lower Steering Shaft and
Universal Joints
.
2.Lubricate universal joints with an anti-seizure
type penetrating spray. Work the joints to ensure
full penetration of the spray by driving vehicle
and steering from lock to lock.
3.If steering stiffness still persists carry out swivel
pin preload setting.
Swivel pin preload setting
1.The swivel pin preload setting must be checked
and set
See FRONT AXLE AND FINAL DRIVE,
Overhaul, Front Stub Axle, Constant Velocity
Joint and Swivel Pin Housing
.
Note that a pull load of 1.16 - 1.46 kg is required
after the axle shaft and swivel housing seal have
been removed.
Steering box adjustment
1.Check steering box adjustment
See
Adjustment, Power Steering Box
.
Steering damper check
1.Check condition of steering damper
See
Steering Damper
.
Page 241 of 455
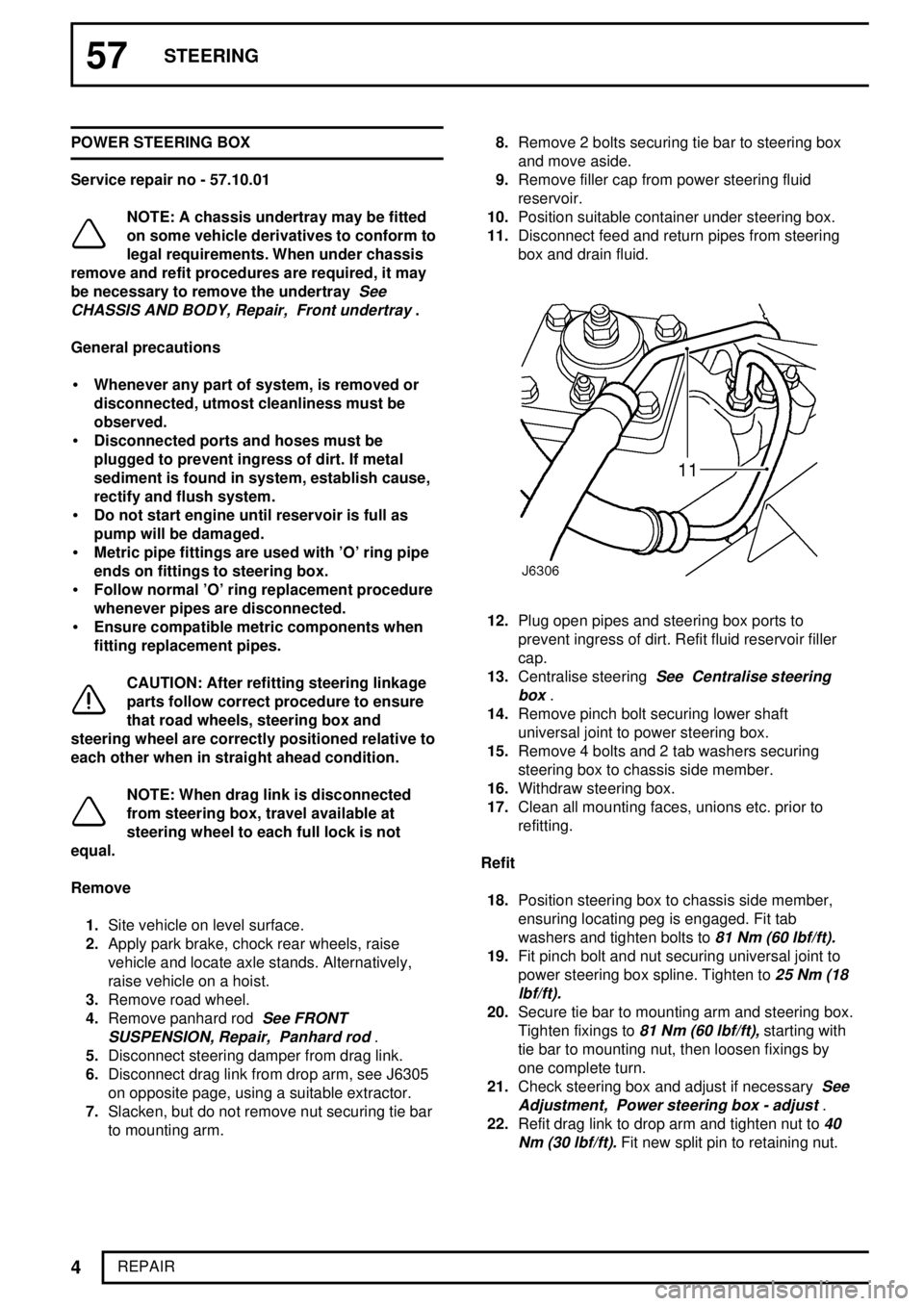
57STEERING
4
REPAIR POWER STEERING BOX
Service repair no - 57.10.01
NOTE: A chassis undertray may be fitted
on some vehicle derivatives to conform to
legal requirements. When under chassis
remove and refit procedures are required, it may
be necessary to remove the undertray
See
CHASSIS AND BODY, Repair, Front undertray
.
General precautions
·Whenever any part of system, is removed or
disconnected, utmost cleanliness must be
observed.
·Disconnected ports and hoses must be
plugged to prevent ingress of dirt. If metal
sediment is found in system, establish cause,
rectify and flush system.
·Do not start engine until reservoir is full as
pump will be damaged.
·Metric pipe fittings are used with 'O' ring pipe
ends on fittings to steering box.
·Follow normal 'O' ring replacement procedure
whenever pipes are disconnected.
·Ensure compatible metric components when
fitting replacement pipes.
CAUTION: After refitting steering linkage
parts follow correct procedure to ensure
that road wheels, steering box and
steering wheel are correctly positioned relative to
each other when in straight ahead condition.
NOTE: When drag link is disconnected
from steering box, travel available at
steering wheel to each full lock is not
equal.
Remove
1.Site vehicle on level surface.
2.Apply park brake, chock rear wheels, raise
vehicle and locate axle stands. Alternatively,
raise vehicle on a hoist.
3.Remove road wheel.
4.Remove panhard rod
See FRONT
SUSPENSION, Repair, Panhard rod
.
5.Disconnect steering damper from drag link.
6.Disconnect drag link from drop arm, see J6305
on opposite page, using a suitable extractor.
7.Slacken, but do not remove nut securing tie bar
to mounting arm.8.Remove 2 bolts securing tie bar to steering box
and move aside.
9.Remove filler cap from power steering fluid
reservoir.
10.Position suitable container under steering box.
11.Disconnect feed and return pipes from steering
box and drain fluid.
12.Plug open pipes and steering box ports to
prevent ingress of dirt. Refit fluid reservoir filler
cap.
13.Centralise steering
See Centralise steering
box
.
14.Remove pinch bolt securing lower shaft
universal joint to power steering box.
15.Remove 4 bolts and 2 tab washers securing
steering box to chassis side member.
16.Withdraw steering box.
17.Clean all mounting faces, unions etc. prior to
refitting.
Refit
18.Position steering box to chassis side member,
ensuring locating peg is engaged. Fit tab
washers and tighten bolts to
81 Nm (60 lbf/ft).
19.Fit pinch bolt and nut securing universal joint to
power steering box spline. Tighten to
25 Nm (18
lbf/ft).
20.Secure tie bar to mounting arm and steering box.
Tighten fixings to
81 Nm (60 lbf/ft),starting with
tie bar to mounting nut, then loosen fixings by
one complete turn.
21.Check steering box and adjust if necessary
See
Adjustment, Power steering box - adjust
.
22.Refit drag link to drop arm and tighten nut to
40
Nm (30 lbf/ft).
Fit new split pin to retaining nut.
Page 242 of 455
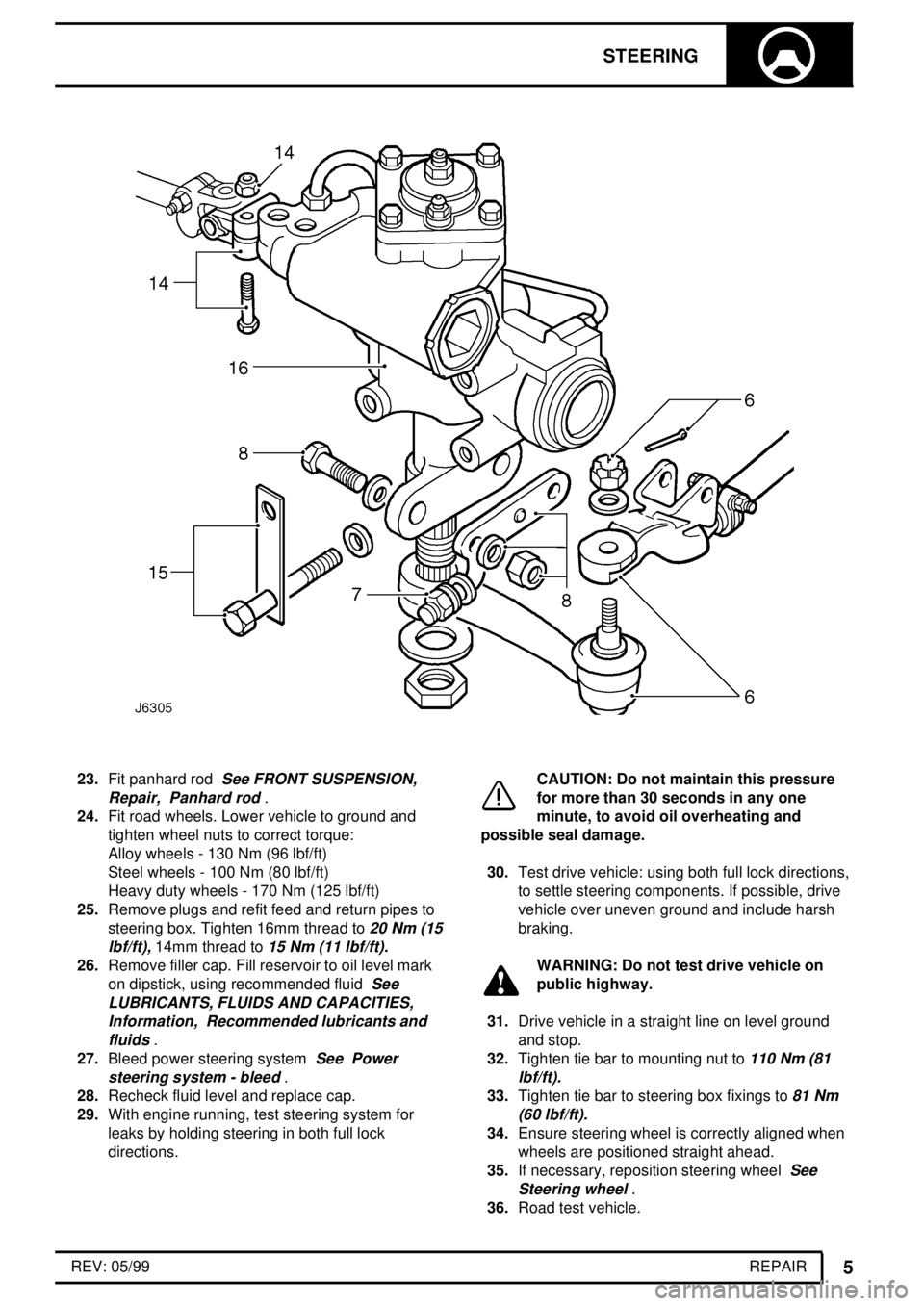
STEERING
5
REPAIR REV: 05/99
23.Fit panhard rodSee FRONT SUSPENSION,
Repair, Panhard rod
.
24.Fit road wheels. Lower vehicle to ground and
tighten wheel nuts to correct torque:
Alloy wheels - 130 Nm (96 lbf/ft)
Steel wheels - 100 Nm (80 lbf/ft)
Heavy duty wheels - 170 Nm (125 lbf/ft)
25.Remove plugs and refit feed and return pipes to
steering box. Tighten 16mm thread to
20 Nm (15
lbf/ft),
14mm thread to15 Nm (11 lbf/ft).
26.Remove filler cap. Fill reservoir to oil level mark
on dipstick, using recommended fluid
See
LUBRICANTS, FLUIDS AND CAPACITIES,
Information, Recommended lubricants and
fluids
.
27.Bleed power steering system
See Power
steering system - bleed
.
28.Recheck fluid level and replace cap.
29.With engine running, test steering system for
leaks by holding steering in both full lock
directions.
CAUTION: Do not maintain this pressure
for more than 30 seconds in any one
minute, to avoid oil overheating and
possible seal damage.
30.Test drive vehicle: using both full lock directions,
to settle steering components. If possible, drive
vehicle over uneven ground and include harsh
braking.
WARNING: Do not test drive vehicle on
public highway.
31.Drive vehicle in a straight line on level ground
and stop.
32.Tighten tie bar to mounting nut to
110 Nm (81
lbf/ft).
33.Tighten tie bar to steering box fixings to81 Nm
(60 lbf/ft).
34.Ensure steering wheel is correctly aligned when
wheels are positioned straight ahead.
35.If necessary, reposition steering wheel
See
Steering wheel
.
36.Road test vehicle.