check engine LAND ROVER DEFENDER 1996 Owner's Manual
[x] Cancel search | Manufacturer: LAND ROVER, Model Year: 1996, Model line: DEFENDER, Model: LAND ROVER DEFENDER 1996Pages: 455, PDF Size: 6.44 MB
Page 99 of 455
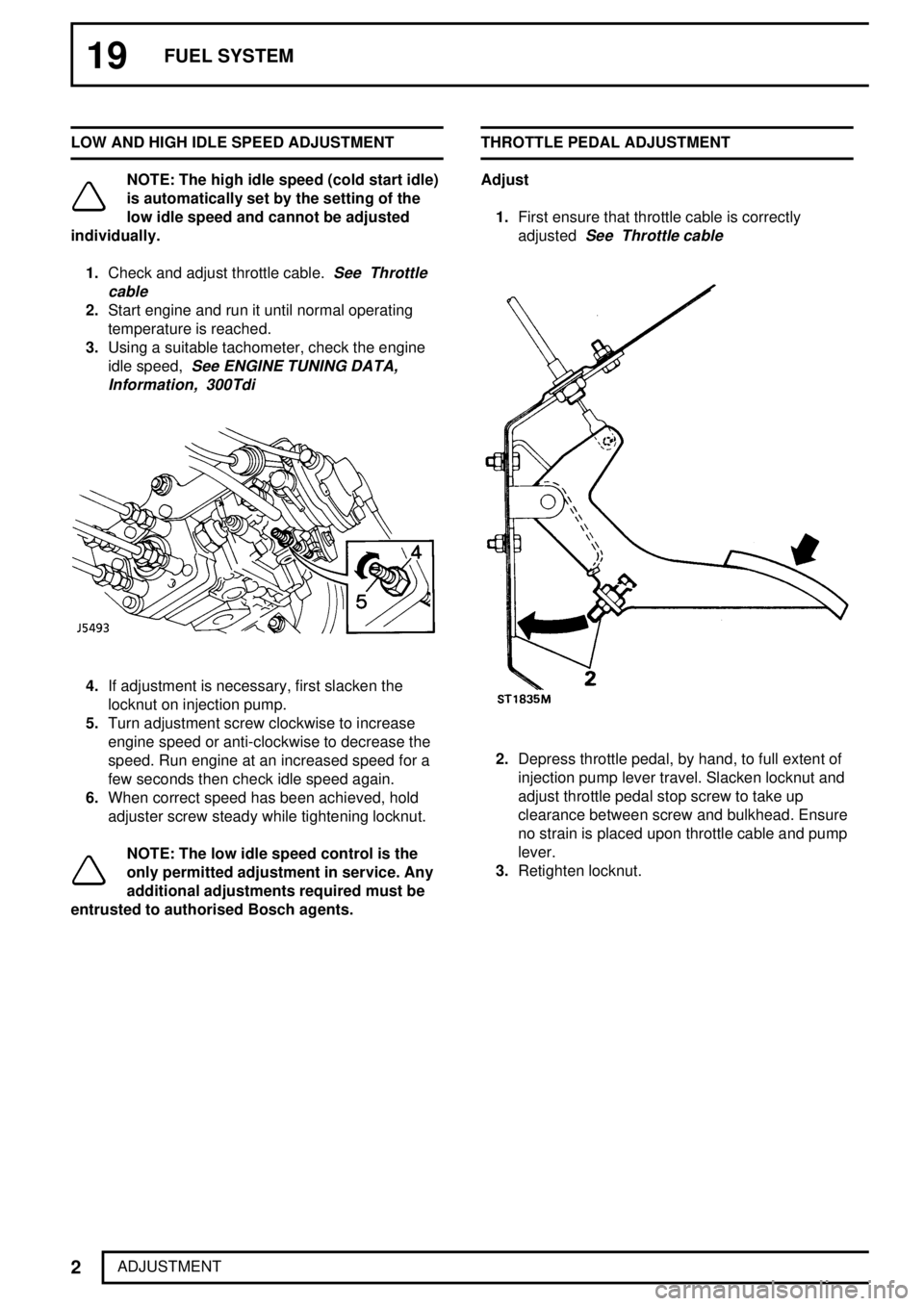
19FUEL SYSTEM
2
ADJUSTMENT LOW AND HIGH IDLE SPEED ADJUSTMENT
NOTE: The high idle speed (cold start idle)
is automatically set by the setting of the
low idle speed and cannot be adjusted
individually.
1.Check and adjust throttle cable.
See Throttle
cable
2.Start engine and run it until normal operating
temperature is reached.
3.Using a suitable tachometer, check the engine
idle speed,
See ENGINE TUNING DATA,
Information, 300Tdi
4.If adjustment is necessary, first slacken the
locknut on injection pump.
5.Turn adjustment screw clockwise to increase
engine speed or anti-clockwise to decrease the
speed. Run engine at an increased speed for a
few seconds then check idle speed again.
6.When correct speed has been achieved, hold
adjuster screw steady while tightening locknut.
NOTE: The low idle speed control is the
only permitted adjustment in service. Any
additional adjustments required must be
entrusted to authorised Bosch agents.THROTTLE PEDAL ADJUSTMENT
Adjust
1.First ensure that throttle cable is correctly
adjusted
See Throttle cable
2.Depress throttle pedal, by hand, to full extent of
injection pump lever travel. Slacken locknut and
adjust throttle pedal stop screw to take up
clearance between screw and bulkhead. Ensure
no strain is placed upon throttle cable and pump
lever.
3.Retighten locknut.
Page 100 of 455
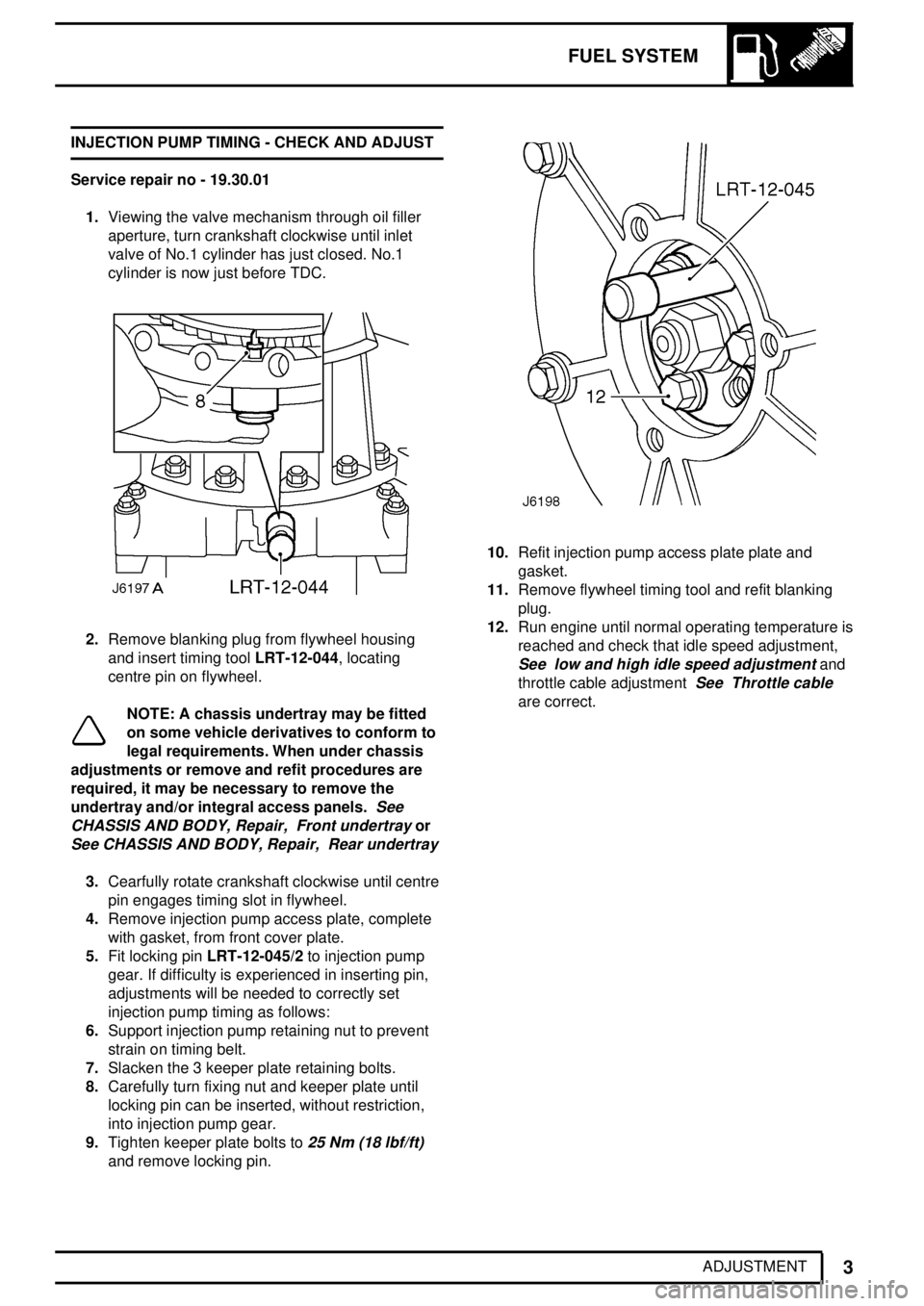
FUEL SYSTEM
3
ADJUSTMENT INJECTION PUMP TIMING - CHECK AND ADJUST
Service repair no - 19.30.01
1.Viewing the valve mechanism through oil filler
aperture, turn crankshaft clockwise until inlet
valve of No.1 cylinder has just closed. No.1
cylinder is now just before TDC.
2.Remove blanking plug from flywheel housing
and insert timing toolLRT-12-044, locating
centre pin on flywheel.
NOTE: A chassis undertray may be fitted
on some vehicle derivatives to conform to
legal requirements. When under chassis
adjustments or remove and refit procedures are
required, it may be necessary to remove the
undertray and/or integral access panels.
See
CHASSIS AND BODY, Repair, Front undertray
or
See CHASSIS AND BODY, Repair, Rear undertray
3.Cearfully rotate crankshaft clockwise until centre
pin engages timing slot in flywheel.
4.Remove injection pump access plate, complete
with gasket, from front cover plate.
5.Fit locking pinLRT-12-045/2to injection pump
gear. If difficulty is experienced in inserting pin,
adjustments will be needed to correctly set
injection pump timing as follows:
6.Support injection pump retaining nut to prevent
strain on timing belt.
7.Slacken the 3 keeper plate retaining bolts.
8.Carefully turn fixing nut and keeper plate until
locking pin can be inserted, without restriction,
into injection pump gear.
9.Tighten keeper plate bolts to
25 Nm (18 lbf/ft)
and remove locking pin.
10.Refit injection pump access plate plate and
gasket.
11.Remove flywheel timing tool and refit blanking
plug.
12.Run engine until normal operating temperature is
reached and check that idle speed adjustment,
See low and high idle speed adjustmentand
throttle cable adjustment
See Throttle cable
are correct.
Page 101 of 455
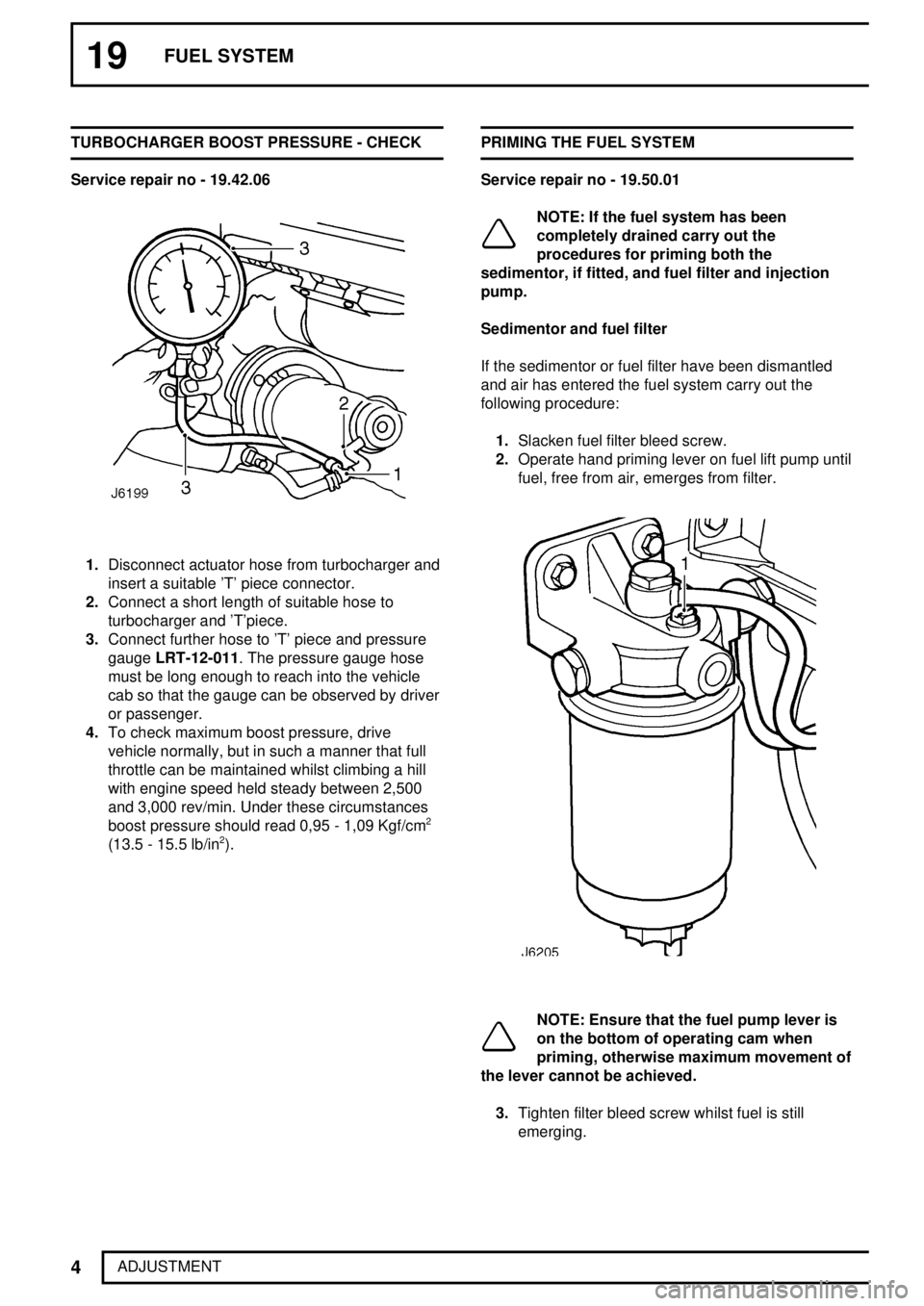
19FUEL SYSTEM
4
ADJUSTMENT TURBOCHARGER BOOST PRESSURE - CHECK
Service repair no - 19.42.06
1.Disconnect actuator hose from turbocharger and
insert a suitable 'T' piece connector.
2.Connect a short length of suitable hose to
turbocharger and 'T'piece.
3.Connect further hose to 'T' piece and pressure
gaugeLRT-12-011. The pressure gauge hose
must be long enough to reach into the vehicle
cab so that the gauge can be observed by driver
or passenger.
4.To check maximum boost pressure, drive
vehicle normally, but in such a manner that full
throttle can be maintained whilst climbing a hill
with engine speed held steady between 2,500
and 3,000 rev/min. Under these circumstances
boost pressure should read 0,95 - 1,09 Kgf/cm
2
(13.5 - 15.5 lb/in2).PRIMING THE FUEL SYSTEM
Service repair no - 19.50.01
NOTE: If the fuel system has been
completely drained carry out the
procedures for priming both the
sedimentor, if fitted, and fuel filter and injection
pump.
Sedimentor and fuel filter
If the sedimentor or fuel filter have been dismantled
and air has entered the fuel system carry out the
following procedure:
1.Slacken fuel filter bleed screw.
2.Operate hand priming lever on fuel lift pump until
fuel, free from air, emerges from filter.
NOTE: Ensure that the fuel pump lever is
on the bottom of operating cam when
priming, otherwise maximum movement of
the lever cannot be achieved.
3.Tighten filter bleed screw whilst fuel is still
emerging.
Page 102 of 455
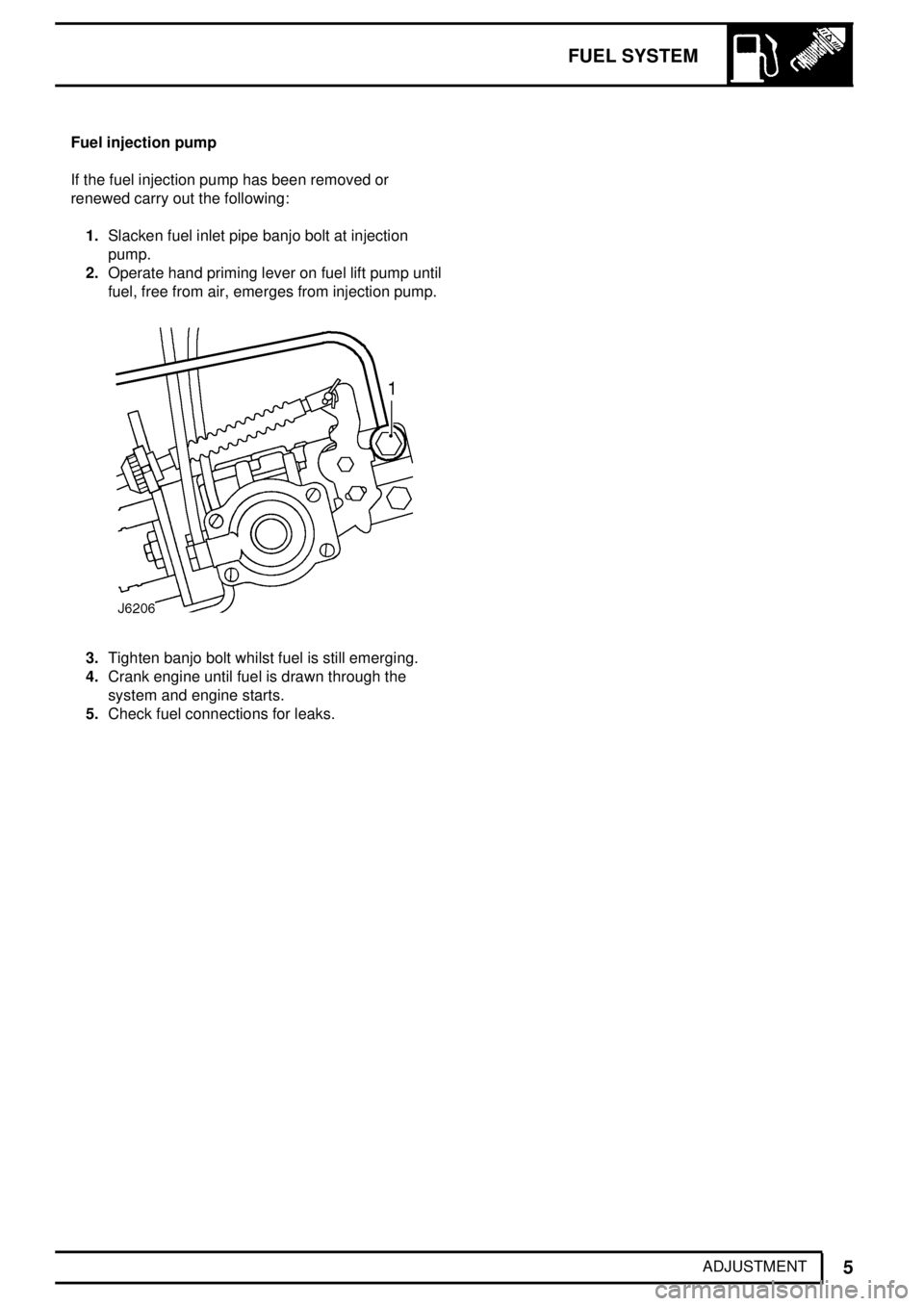
FUEL SYSTEM
5
ADJUSTMENT Fuel injection pump
If the fuel injection pump has been removed or
renewed carry out the following:
1.Slacken fuel inlet pipe banjo bolt at injection
pump.
2.Operate hand priming lever on fuel lift pump until
fuel, free from air, emerges from injection pump.
3.Tighten banjo bolt whilst fuel is still emerging.
4.Crank engine until fuel is drawn through the
system and engine starts.
5.Check fuel connections for leaks.
Page 109 of 455
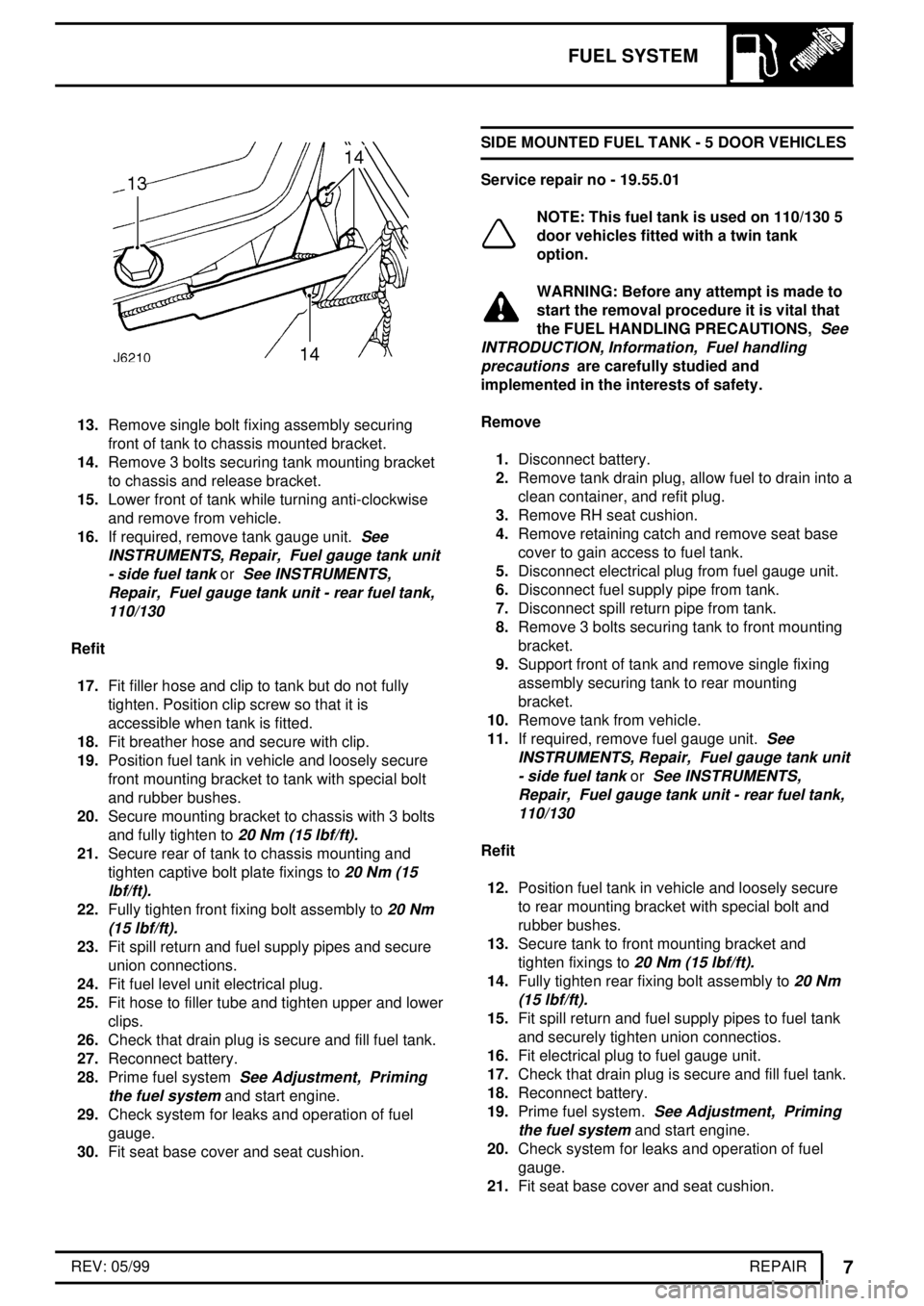
FUEL SYSTEM
7
REPAIR REV: 05/99
13.Remove single bolt fixing assembly securing
front of tank to chassis mounted bracket.
14.Remove 3 bolts securing tank mounting bracket
to chassis and release bracket.
15.Lower front of tank while turning anti-clockwise
and remove from vehicle.
16.If required, remove tank gauge unit.
See
INSTRUMENTS, Repair, Fuel gauge tank unit
- side fuel tank
orSee INSTRUMENTS,
Repair, Fuel gauge tank unit - rear fuel tank,
110/130
Refit
17.Fit filler hose and clip to tank but do not fully
tighten. Position clip screw so that it is
accessible when tank is fitted.
18.Fit breather hose and secure with clip.
19.Position fuel tank in vehicle and loosely secure
front mounting bracket to tank with special bolt
and rubber bushes.
20.Secure mounting bracket to chassis with 3 bolts
and fully tighten to
20 Nm (15 lbf/ft).
21.Secure rear of tank to chassis mounting and
tighten captive bolt plate fixings to
20 Nm (15
lbf/ft).
22.Fully tighten front fixing bolt assembly to20 Nm
(15 lbf/ft).
23.Fit spill return and fuel supply pipes and secure
union connections.
24.Fit fuel level unit electrical plug.
25.Fit hose to filler tube and tighten upper and lower
clips.
26.Check that drain plug is secure and fill fuel tank.
27.Reconnect battery.
28.Prime fuel system
See Adjustment, Priming
the fuel system
and start engine.
29.Check system for leaks and operation of fuel
gauge.
30.Fit seat base cover and seat cushion.SIDE MOUNTED FUEL TANK - 5 DOOR VEHICLES
Service repair no - 19.55.01
NOTE: This fuel tank is used on 110/130 5
door vehicles fitted with a twin tank
option.
WARNING: Before any attempt is made to
start the removal procedure it is vital that
the FUEL HANDLING PRECAUTIONS,
See
INTRODUCTION, Information, Fuel handling
precautions
are carefully studied and
implemented in the interests of safety.
Remove
1.Disconnect battery.
2.Remove tank drain plug, allow fuel to drain into a
clean container, and refit plug.
3.Remove RH seat cushion.
4.Remove retaining catch and remove seat base
cover to gain access to fuel tank.
5.Disconnect electrical plug from fuel gauge unit.
6.Disconnect fuel supply pipe from tank.
7.Disconnect spill return pipe from tank.
8.Remove 3 bolts securing tank to front mounting
bracket.
9.Support front of tank and remove single fixing
assembly securing tank to rear mounting
bracket.
10.Remove tank from vehicle.
11.If required, remove fuel gauge unit.
See
INSTRUMENTS, Repair, Fuel gauge tank unit
- side fuel tank
orSee INSTRUMENTS,
Repair, Fuel gauge tank unit - rear fuel tank,
110/130
Refit
12.Position fuel tank in vehicle and loosely secure
to rear mounting bracket with special bolt and
rubber bushes.
13.Secure tank to front mounting bracket and
tighten fixings to
20 Nm (15 lbf/ft).
14.Fully tighten rear fixing bolt assembly to20 Nm
(15 lbf/ft).
15.Fit spill return and fuel supply pipes to fuel tank
and securely tighten union connectios.
16.Fit electrical plug to fuel gauge unit.
17.Check that drain plug is secure and fill fuel tank.
18.Reconnect battery.
19.Prime fuel system.
See Adjustment, Priming
the fuel system
and start engine.
20.Check system for leaks and operation of fuel
gauge.
21.Fit seat base cover and seat cushion.
Page 111 of 455
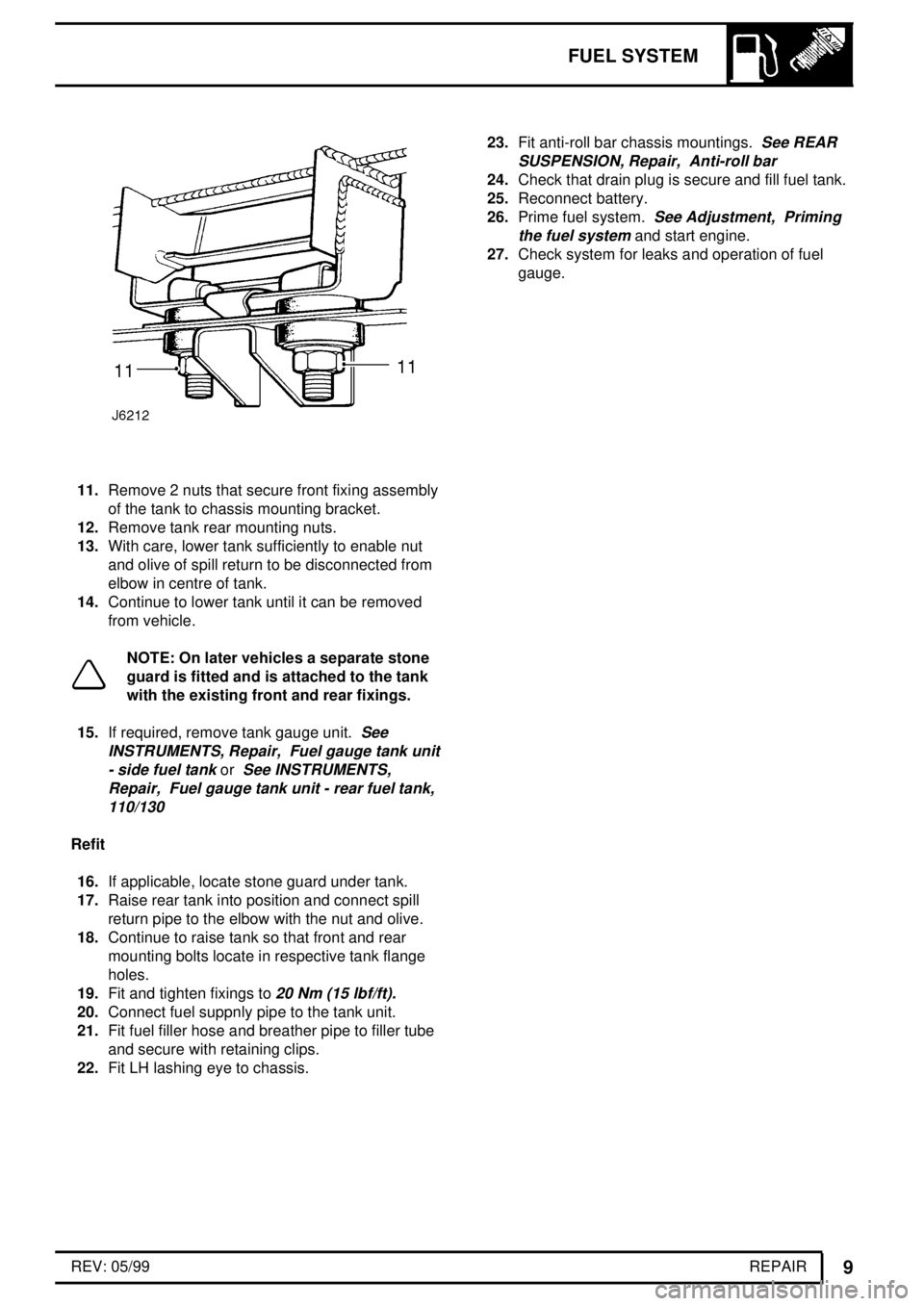
FUEL SYSTEM
9
REPAIR REV: 05/99
11.Remove 2 nuts that secure front fixing assembly
of the tank to chassis mounting bracket.
12.Remove tank rear mounting nuts.
13.With care, lower tank sufficiently to enable nut
and olive of spill return to be disconnected from
elbow in centre of tank.
14.Continue to lower tank until it can be removed
from vehicle.
NOTE: On later vehicles a separate stone
guard is fitted and is attached to the tank
with the existing front and rear fixings.
15.If required, remove tank gauge unit.
See
INSTRUMENTS, Repair, Fuel gauge tank unit
- side fuel tank
orSee INSTRUMENTS,
Repair, Fuel gauge tank unit - rear fuel tank,
110/130
Refit
16.If applicable, locate stone guard under tank.
17.Raise rear tank into position and connect spill
return pipe to the elbow with the nut and olive.
18.Continue to raise tank so that front and rear
mounting bolts locate in respective tank flange
holes.
19.Fit and tighten fixings to
20 Nm (15 lbf/ft).
20.Connect fuel suppnly pipe to the tank unit.
21.Fit fuel filler hose and breather pipe to filler tube
and secure with retaining clips.
22.Fit LH lashing eye to chassis.23.Fit anti-roll bar chassis mountings.
See REAR
SUSPENSION, Repair, Anti-roll bar
24.Check that drain plug is secure and fill fuel tank.
25.Reconnect battery.
26.Prime fuel system.
See Adjustment, Priming
the fuel system
and start engine.
27.Check system for leaks and operation of fuel
gauge.
Page 116 of 455
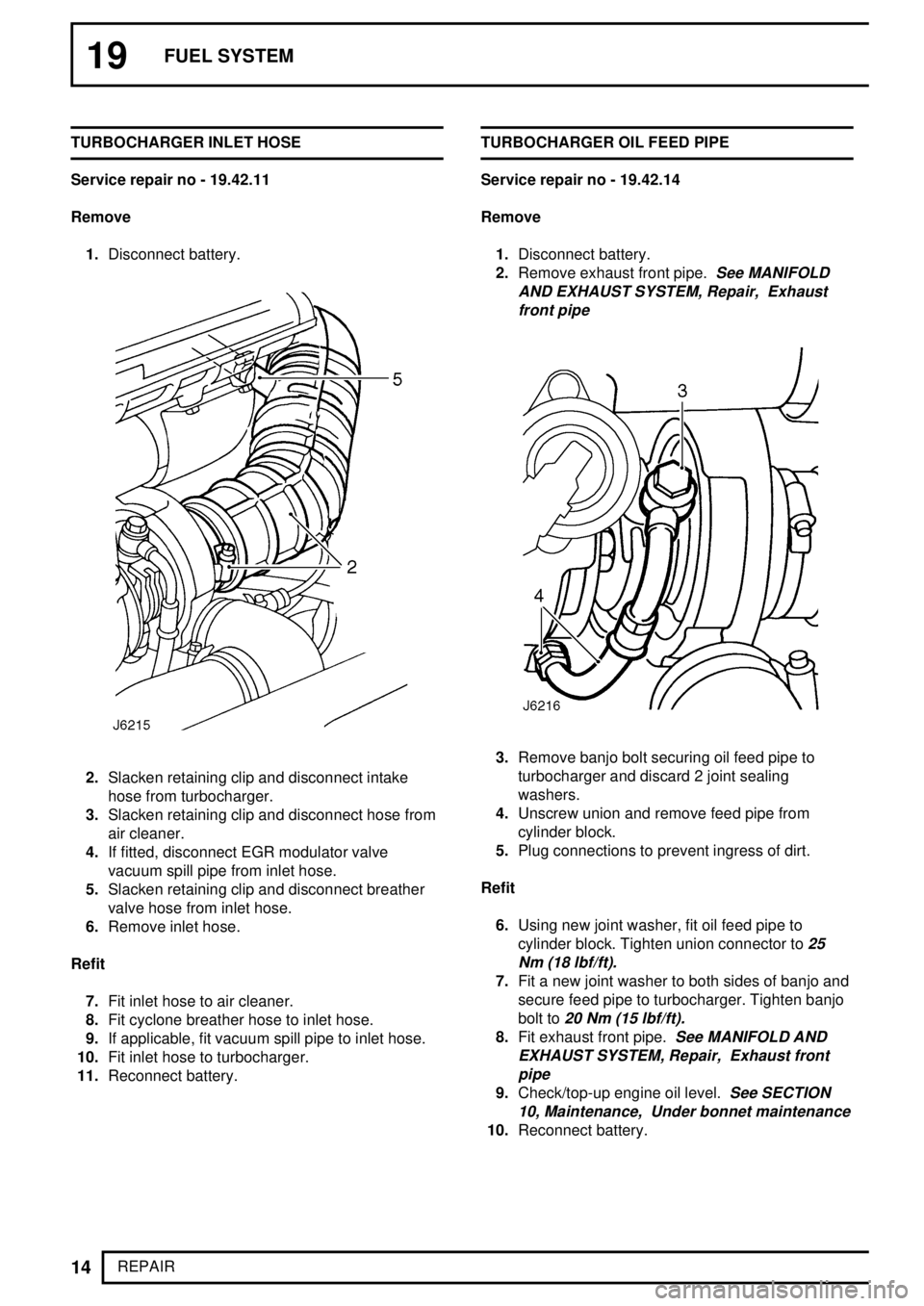
19FUEL SYSTEM
14
REPAIR TURBOCHARGER INLET HOSE
Service repair no - 19.42.11
Remove
1.Disconnect battery.
2.Slacken retaining clip and disconnect intake
hose from turbocharger.
3.Slacken retaining clip and disconnect hose from
air cleaner.
4.If fitted, disconnect EGR modulator valve
vacuum spill pipe from inlet hose.
5.Slacken retaining clip and disconnect breather
valve hose from inlet hose.
6.Remove inlet hose.
Refit
7.Fit inlet hose to air cleaner.
8.Fit cyclone breather hose to inlet hose.
9.If applicable, fit vacuum spill pipe to inlet hose.
10.Fit inlet hose to turbocharger.
11.Reconnect battery.TURBOCHARGER OIL FEED PIPE
Service repair no - 19.42.14
Remove
1.Disconnect battery.
2.Remove exhaust front pipe.
See MANIFOLD
AND EXHAUST SYSTEM, Repair, Exhaust
front pipe
3.Remove banjo bolt securing oil feed pipe to
turbocharger and discard 2 joint sealing
washers.
4.Unscrew union and remove feed pipe from
cylinder block.
5.Plug connections to prevent ingress of dirt.
Refit
6.Using new joint washer, fit oil feed pipe to
cylinder block. Tighten union connector to
25
Nm (18 lbf/ft).
7.Fit a new joint washer to both sides of banjo and
secure feed pipe to turbocharger. Tighten banjo
bolt to
20 Nm (15 lbf/ft).
8.Fit exhaust front pipe.See MANIFOLD AND
EXHAUST SYSTEM, Repair, Exhaust front
pipe
9.Check/top-up engine oil level.See SECTION
10, Maintenance, Under bonnet maintenance
10.Reconnect battery.
Page 117 of 455
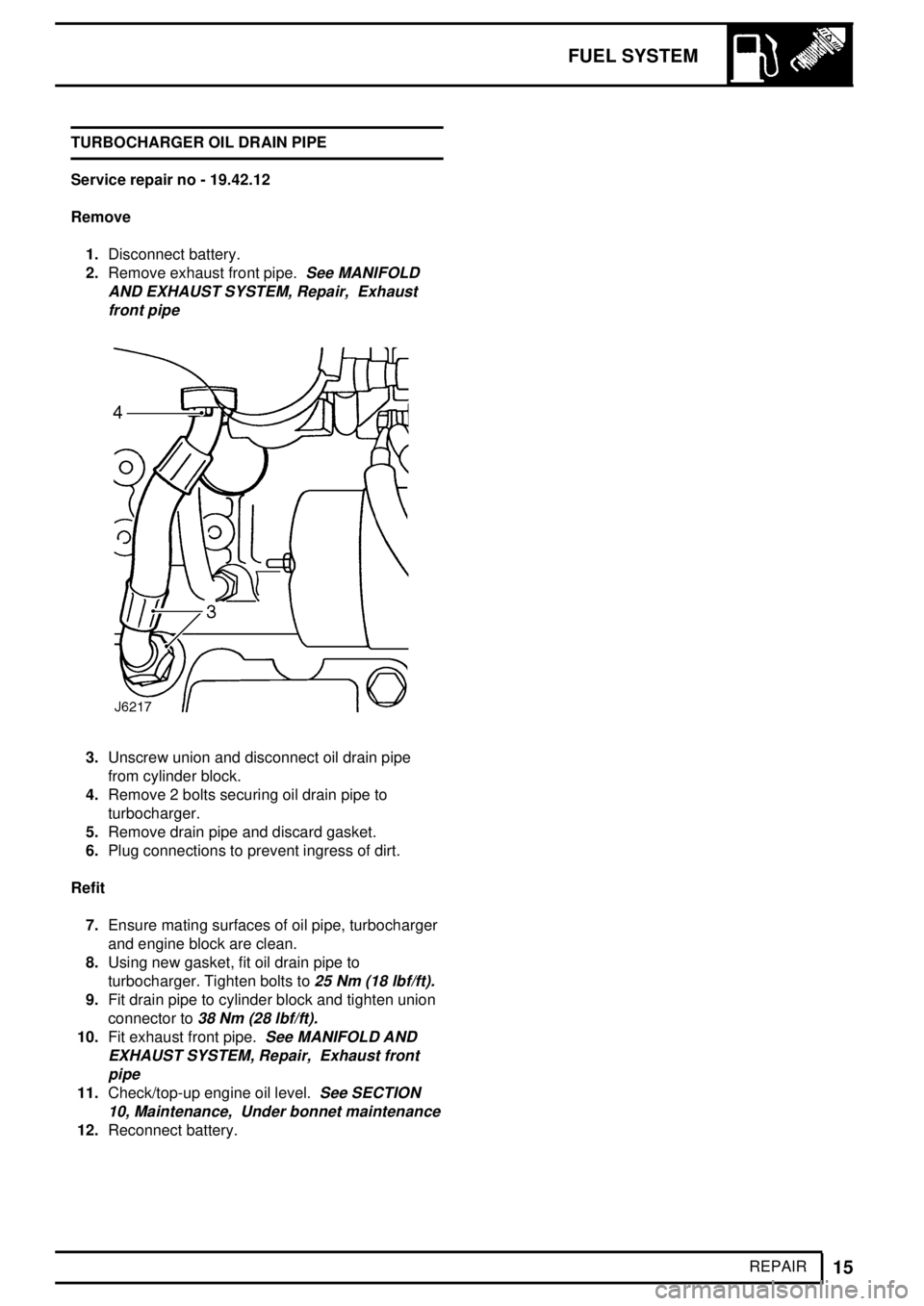
FUEL SYSTEM
15
REPAIR TURBOCHARGER OIL DRAIN PIPE
Service repair no - 19.42.12
Remove
1.Disconnect battery.
2.Remove exhaust front pipe.
See MANIFOLD
AND EXHAUST SYSTEM, Repair, Exhaust
front pipe
3.Unscrew union and disconnect oil drain pipe
from cylinder block.
4.Remove 2 bolts securing oil drain pipe to
turbocharger.
5.Remove drain pipe and discard gasket.
6.Plug connections to prevent ingress of dirt.
Refit
7.Ensure mating surfaces of oil pipe, turbocharger
and engine block are clean.
8.Using new gasket, fit oil drain pipe to
turbocharger. Tighten bolts to
25 Nm (18 lbf/ft).
9.Fit drain pipe to cylinder block and tighten union
connector to
38 Nm (28 lbf/ft).
10.Fit exhaust front pipe.See MANIFOLD AND
EXHAUST SYSTEM, Repair, Exhaust front
pipe
11.Check/top-up engine oil level.See SECTION
10, Maintenance, Under bonnet maintenance
12.Reconnect battery.
Page 125 of 455
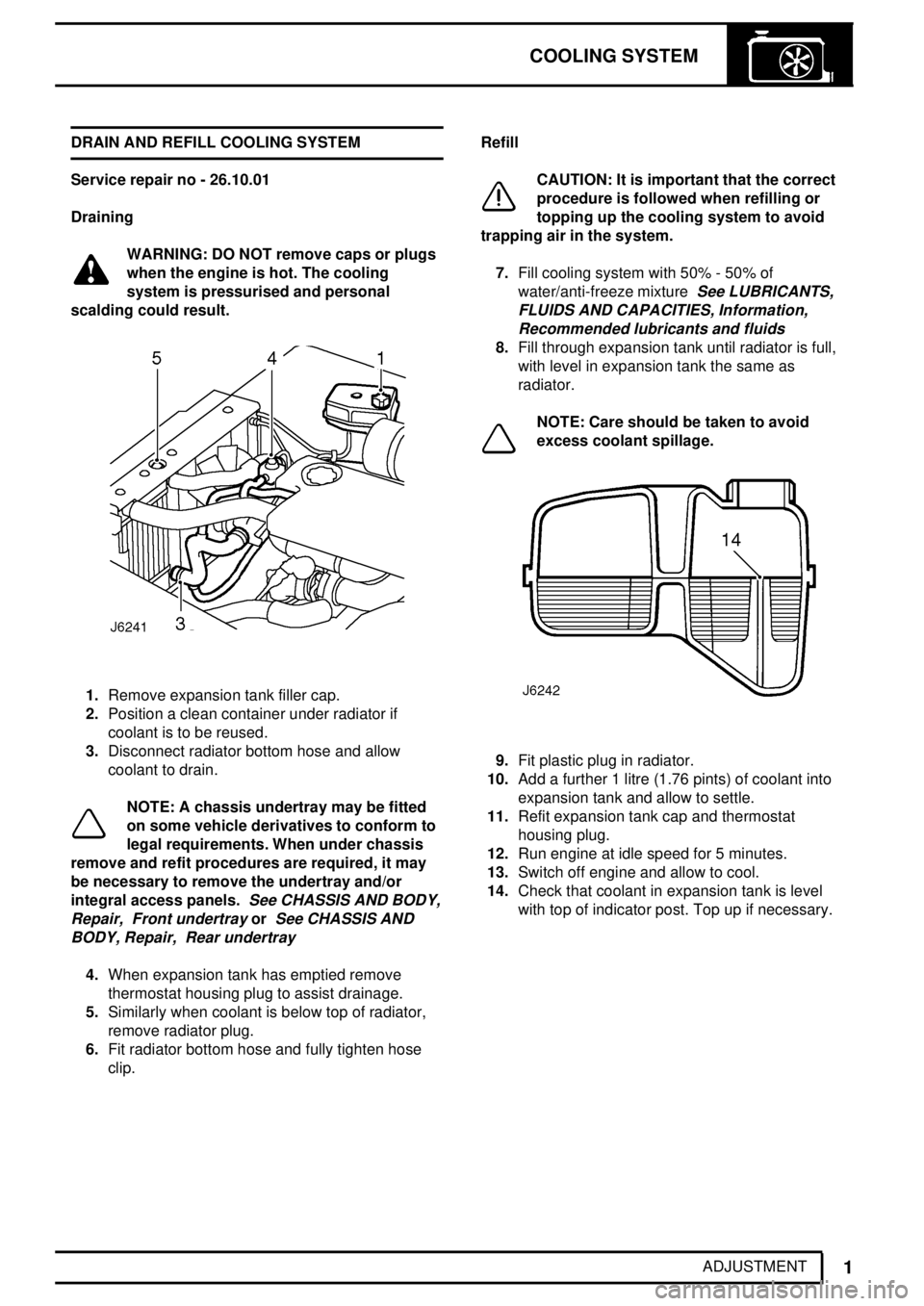
COOLING SYSTEM
1
ADJUSTMENT DRAIN AND REFILL COOLING SYSTEM
Service repair no - 26.10.01
Draining
WARNING: DO NOT remove caps or plugs
when the engine is hot. The cooling
system is pressurised and personal
scalding could result.
1.Remove expansion tank filler cap.
2.Position a clean container under radiator if
coolant is to be reused.
3.Disconnect radiator bottom hose and allow
coolant to drain.
NOTE: A chassis undertray may be fitted
on some vehicle derivatives to conform to
legal requirements. When under chassis
remove and refit procedures are required, it may
be necessary to remove the undertray and/or
integral access panels.
See CHASSIS AND BODY,
Repair, Front undertray
orSee CHASSIS AND
BODY, Repair, Rear undertray
4.When expansion tank has emptied remove
thermostat housing plug to assist drainage.
5.Similarly when coolant is below top of radiator,
remove radiator plug.
6.Fit radiator bottom hose and fully tighten hose
clip.Refill
CAUTION: It is important that the correct
procedure is followed when refilling or
topping up the cooling system to avoid
trapping air in the system.
7.Fill cooling system with 50% - 50% of
water/anti-freeze mixture
See LUBRICANTS,
FLUIDS AND CAPACITIES, Information,
Recommended lubricants and fluids
8.Fill through expansion tank until radiator is full,
with level in expansion tank the same as
radiator.
NOTE: Care should be taken to avoid
excess coolant spillage.
9.Fit plastic plug in radiator.
10.Add a further 1 litre (1.76 pints) of coolant into
expansion tank and allow to settle.
11.Refit expansion tank cap and thermostat
housing plug.
12.Run engine at idle speed for 5 minutes.
13.Switch off engine and allow to cool.
14.Check that coolant in expansion tank is level
with top of indicator post. Top up if necessary.
Page 135 of 455
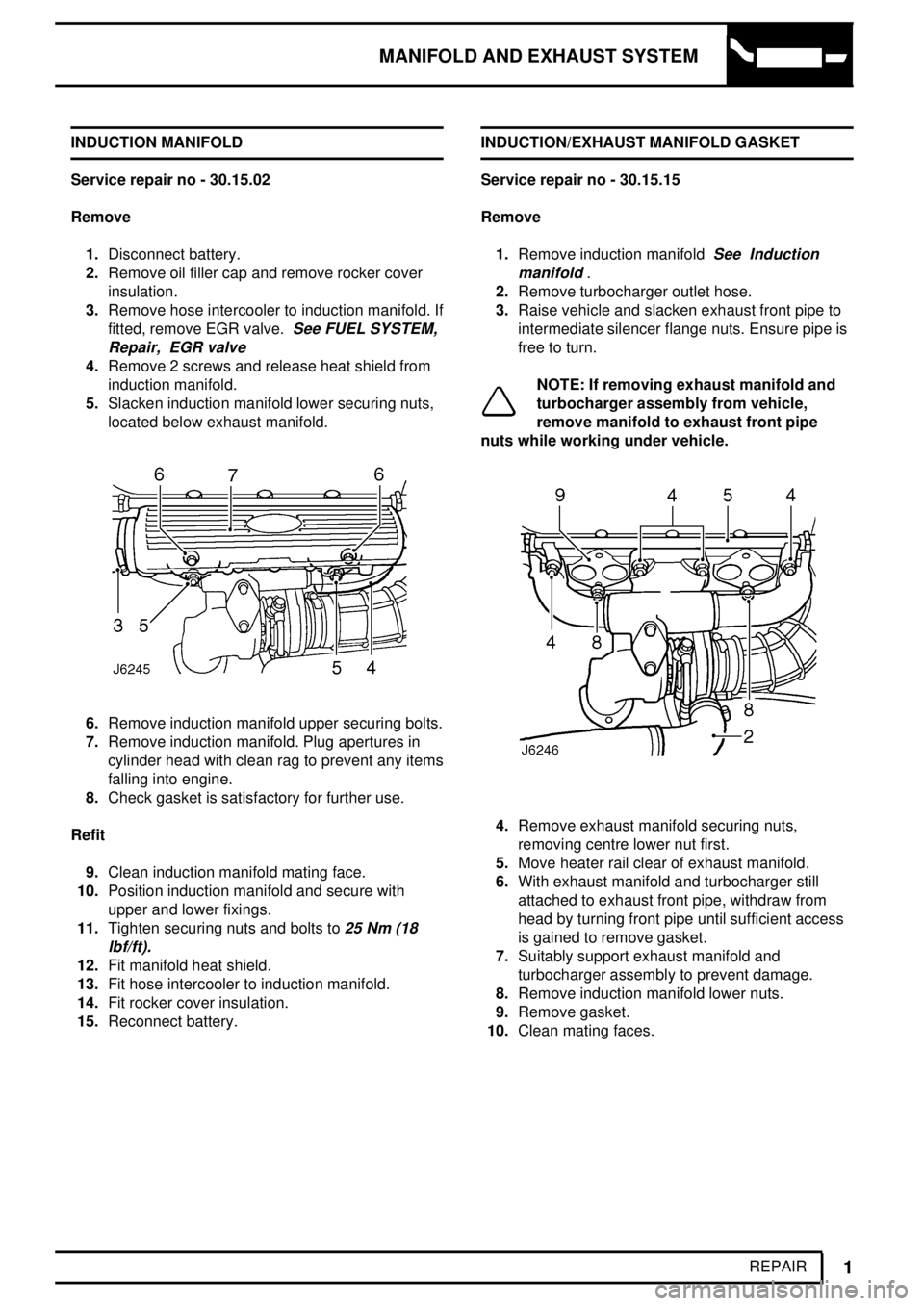
MANIFOLD AND EXHAUST SYSTEM
1
REPAIR INDUCTION MANIFOLD
Service repair no - 30.15.02
Remove
1.Disconnect battery.
2.Remove oil filler cap and remove rocker cover
insulation.
3.Remove hose intercooler to induction manifold. If
fitted, remove EGR valve.
See FUEL SYSTEM,
Repair, EGR valve
4.Remove 2 screws and release heat shield from
induction manifold.
5.Slacken induction manifold lower securing nuts,
located below exhaust manifold.
6.Remove induction manifold upper securing bolts.
7.Remove induction manifold. Plug apertures in
cylinder head with clean rag to prevent any items
falling into engine.
8.Check gasket is satisfactory for further use.
Refit
9.Clean induction manifold mating face.
10.Position induction manifold and secure with
upper and lower fixings.
11.Tighten securing nuts and bolts to
25 Nm (18
lbf/ft).
12.Fit manifold heat shield.
13.Fit hose intercooler to induction manifold.
14.Fit rocker cover insulation.
15.Reconnect battery.INDUCTION/EXHAUST MANIFOLD GASKET
Service repair no - 30.15.15
Remove
1.Remove induction manifold
See Induction
manifold
.
2.Remove turbocharger outlet hose.
3.Raise vehicle and slacken exhaust front pipe to
intermediate silencer flange nuts. Ensure pipe is
free to turn.
NOTE: If removing exhaust manifold and
turbocharger assembly from vehicle,
remove manifold to exhaust front pipe
nuts while working under vehicle.
4.Remove exhaust manifold securing nuts,
removing centre lower nut first.
5.Move heater rail clear of exhaust manifold.
6.With exhaust manifold and turbocharger still
attached to exhaust front pipe, withdraw from
head by turning front pipe until sufficient access
is gained to remove gasket.
7.Suitably support exhaust manifold and
turbocharger assembly to prevent damage.
8.Remove induction manifold lower nuts.
9.Remove gasket.
10.Clean mating faces.