check engine LAND ROVER DEFENDER 1996 Service Manual
[x] Cancel search | Manufacturer: LAND ROVER, Model Year: 1996, Model line: DEFENDER, Model: LAND ROVER DEFENDER 1996Pages: 455, PDF Size: 6.44 MB
Page 243 of 455
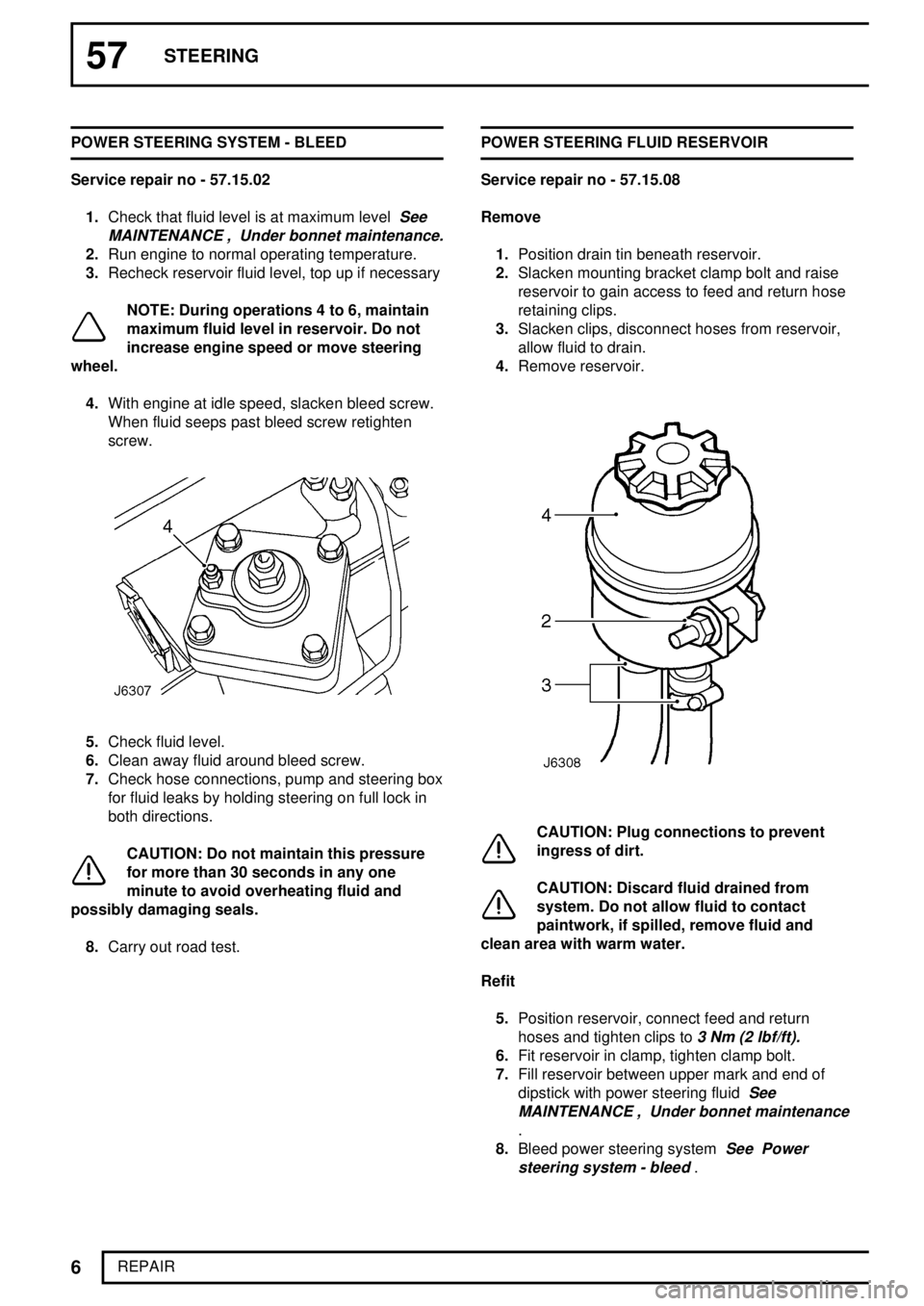
57STEERING
6
REPAIR POWER STEERING SYSTEM - BLEED
Service repair no - 57.15.02
1.Check that fluid level is at maximum level
See
MAINTENANCE , Under bonnet maintenance.
2.Run engine to normal operating temperature.
3.Recheck reservoir fluid level, top up if necessary
NOTE: During operations 4 to 6, maintain
maximum fluid level in reservoir. Do not
increase engine speed or move steering
wheel.
4.With engine at idle speed, slacken bleed screw.
When fluid seeps past bleed screw retighten
screw.
5.Check fluid level.
6.Clean away fluid around bleed screw.
7.Check hose connections, pump and steering box
for fluid leaks by holding steering on full lock in
both directions.
CAUTION: Do not maintain this pressure
for more than 30 seconds in any one
minute to avoid overheating fluid and
possibly damaging seals.
8.Carry out road test.POWER STEERING FLUID RESERVOIR
Service repair no - 57.15.08
Remove
1.Position drain tin beneath reservoir.
2.Slacken mounting bracket clamp bolt and raise
reservoir to gain access to feed and return hose
retaining clips.
3.Slacken clips, disconnect hoses from reservoir,
allow fluid to drain.
4.Remove reservoir.
CAUTION: Plug connections to prevent
ingress of dirt.
CAUTION: Discard fluid drained from
system. Do not allow fluid to contact
paintwork, if spilled, remove fluid and
clean area with warm water.
Refit
5.Position reservoir, connect feed and return
hoses and tighten clips to
3 Nm (2 lbf/ft).
6.Fit reservoir in clamp, tighten clamp bolt.
7.Fill reservoir between upper mark and end of
dipstick with power steering fluid
See
MAINTENANCE , Under bonnet maintenance
.
8.Bleed power steering system
See Power
steering system - bleed
.
Page 280 of 455
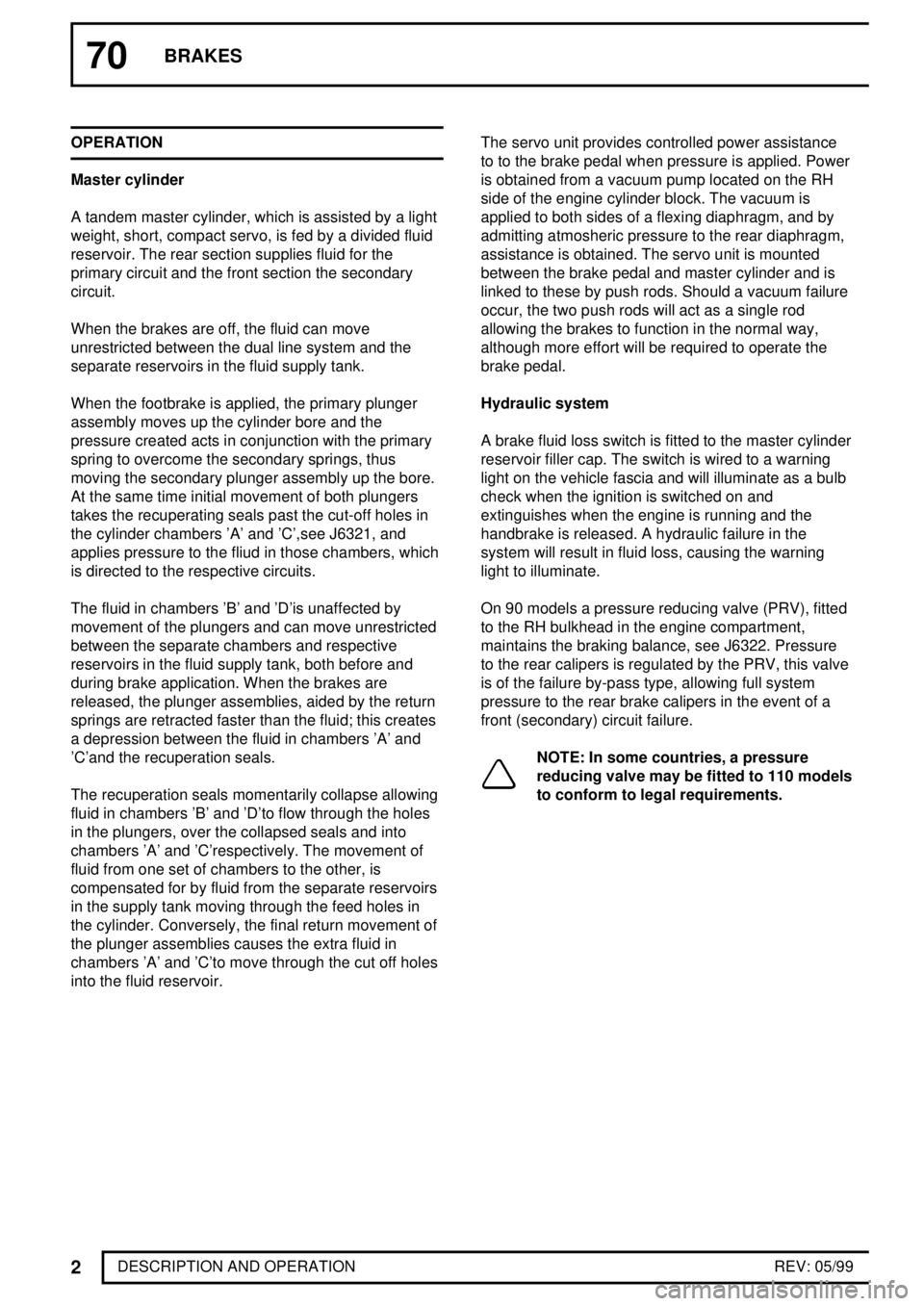
70BRAKES
2
DESCRIPTION AND OPERATION REV: 05/99 OPERATION
Master cylinder
A tandem master cylinder, which is assisted by a light
weight, short, compact servo, is fed by a divided fluid
reservoir. The rear section supplies fluid for the
primary circuit and the front section the secondary
circuit.
When the brakes are off, the fluid can move
unrestricted between the dual line system and the
separate reservoirs in the fluid supply tank.
When the footbrake is applied, the primary plunger
assembly moves up the cylinder bore and the
pressure created acts in conjunction with the primary
spring to overcome the secondary springs, thus
moving the secondary plunger assembly up the bore.
At the same time initial movement of both plungers
takes the recuperating seals past the cut-off holes in
the cylinder chambers 'A' and 'C',see J6321, and
applies pressure to the fliud in those chambers, which
is directed to the respective circuits.
The fluid in chambers 'B' and 'D'is unaffected by
movement of the plungers and can move unrestricted
between the separate chambers and respective
reservoirs in the fluid supply tank, both before and
during brake application. When the brakes are
released, the plunger assemblies, aided by the return
springs are retracted faster than the fluid; this creates
a depression between the fluid in chambers 'A' and
'C'and the recuperation seals.
The recuperation seals momentarily collapse allowing
fluid in chambers 'B' and 'D'to flow through the holes
in the plungers, over the collapsed seals and into
chambers 'A' and 'C'respectively. The movement of
fluid from one set of chambers to the other, is
compensated for by fluid from the separate reservoirs
in the supply tank moving through the feed holes in
the cylinder. Conversely, the final return movement of
the plunger assemblies causes the extra fluid in
chambers 'A' and 'C'to move through the cut off holes
into the fluid reservoir.The servo unit provides controlled power assistance
to to the brake pedal when pressure is applied. Power
is obtained from a vacuum pump located on the RH
side of the engine cylinder block. The vacuum is
applied to both sides of a flexing diaphragm, and by
admitting atmosheric pressure to the rear diaphragm,
assistance is obtained. The servo unit is mounted
between the brake pedal and master cylinder and is
linked to these by push rods. Should a vacuum failure
occur, the two push rods will act as a single rod
allowing the brakes to function in the normal way,
although more effort will be required to operate the
brake pedal.
Hydraulic system
A brake fluid loss switch is fitted to the master cylinder
reservoir filler cap. The switch is wired to a warning
light on the vehicle fascia and will illuminate as a bulb
check when the ignition is switched on and
extinguishes when the engine is running and the
handbrake is released. A hydraulic failure in the
system will result in fluid loss, causing the warning
light to illuminate.
On 90 models a pressure reducing valve (PRV), fitted
to the RH bulkhead in the engine compartment,
maintains the braking balance, see J6322. Pressure
to the rear calipers is regulated by the PRV, this valve
is of the failure by-pass type, allowing full system
pressure to the rear brake calipers in the event of a
front (secondary) circuit failure.
NOTE: In some countries, a pressure
reducing valve may be fitted to 110 models
to conform to legal requirements.
Page 282 of 455
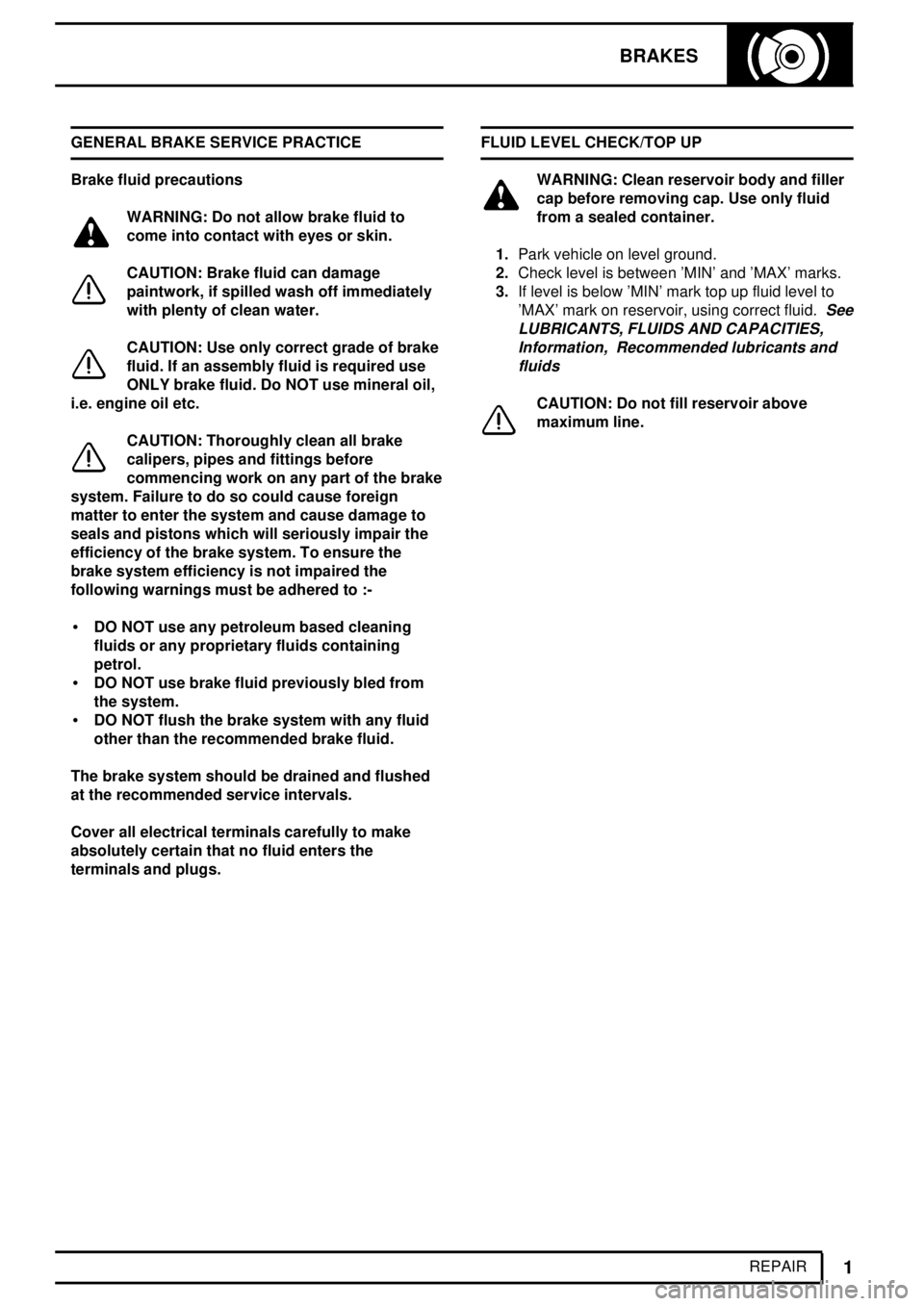
BRAKES
1
REPAIR GENERAL BRAKE SERVICE PRACTICE
Brake fluid precautions
WARNING: Do not allow brake fluid to
come into contact with eyes or skin.
CAUTION: Brake fluid can damage
paintwork, if spilled wash off immediately
with plenty of clean water.
CAUTION: Use only correct grade of brake
fluid. If an assembly fluid is required use
ONLY brake fluid. Do NOT use mineral oil,
i.e. engine oil etc.
CAUTION: Thoroughly clean all brake
calipers, pipes and fittings before
commencing work on any part of the brake
system. Failure to do so could cause foreign
matter to enter the system and cause damage to
seals and pistons which will seriously impair the
efficiency of the brake system. To ensure the
brake system efficiency is not impaired the
following warnings must be adhered to :-
·DO NOT use any petroleum based cleaning
fluids or any proprietary fluids containing
petrol.
·DO NOT use brake fluid previously bled from
the system.
·DO NOT flush the brake system with any fluid
other than the recommended brake fluid.
The brake system should be drained and flushed
at the recommended service intervals.
Cover all electrical terminals carefully to make
absolutely certain that no fluid enters the
terminals and plugs.FLUID LEVEL CHECK/TOP UP
WARNING: Clean reservoir body and filler
cap before removing cap. Use only fluid
from a sealed container.
1.Park vehicle on level ground.
2.Check level is between 'MIN' and 'MAX' marks.
3.If level is below 'MIN' mark top up fluid level to
'MAX' mark on reservoir, using correct fluid.
See
LUBRICANTS, FLUIDS AND CAPACITIES,
Information, Recommended lubricants and
fluids
CAUTION: Do not fill reservoir above
maximum line.
Page 285 of 455
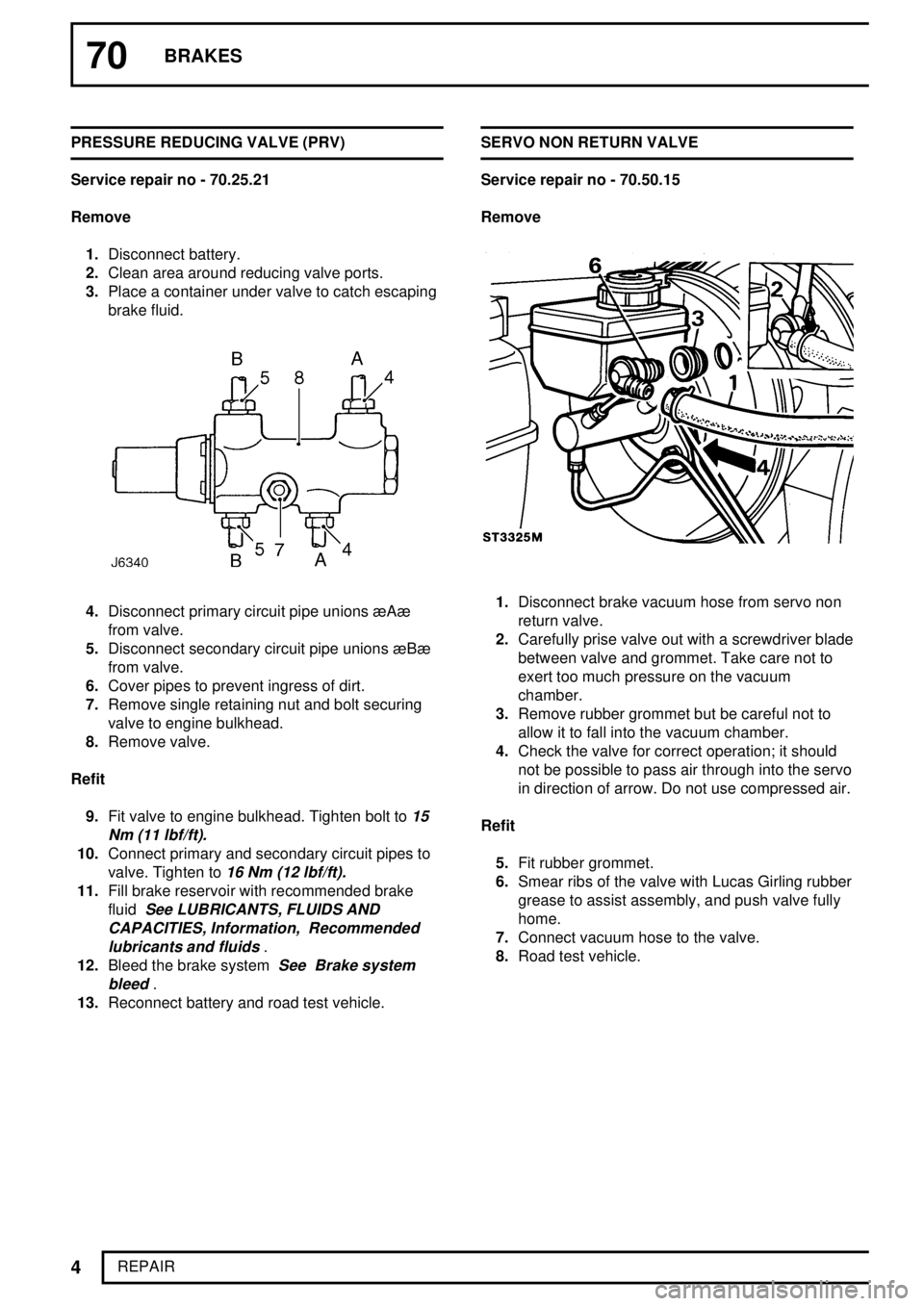
70BRAKES
4
REPAIR PRESSURE REDUCING VALVE (PRV)
Service repair no - 70.25.21
Remove
1.Disconnect battery.
2.Clean area around reducing valve ports.
3.Place a container under valve to catch escaping
brake fluid.
4.Disconnect primary circuit pipe unions ñAñ
from valve.
5.Disconnect secondary circuit pipe unions ñBñ
from valve.
6.Cover pipes to prevent ingress of dirt.
7.Remove single retaining nut and bolt securing
valve to engine bulkhead.
8.Remove valve.
Refit
9.Fit valve to engine bulkhead. Tighten bolt to
15
Nm (11 lbf/ft).
10.Connect primary and secondary circuit pipes to
valve. Tighten to
16 Nm (12 lbf/ft).
11.Fill brake reservoir with recommended brake
fluid
See LUBRICANTS, FLUIDS AND
CAPACITIES, Information, Recommended
lubricants and fluids
.
12.Bleed the brake system
See Brake system
bleed
.
13.Reconnect battery and road test vehicle.SERVO NON RETURN VALVE
Service repair no - 70.50.15
Remove
1.Disconnect brake vacuum hose from servo non
return valve.
2.Carefully prise valve out with a screwdriver blade
between valve and grommet. Take care not to
exert too much pressure on the vacuum
chamber.
3.Remove rubber grommet but be careful not to
allow it to fall into the vacuum chamber.
4.Check the valve for correct operation; it should
not be possible to pass air through into the servo
in direction of arrow. Do not use compressed air.
Refit
5.Fit rubber grommet.
6.Smear ribs of the valve with Lucas Girling rubber
grease to assist assembly, and push valve fully
home.
7.Connect vacuum hose to the valve.
8.Road test vehicle.
Page 379 of 455
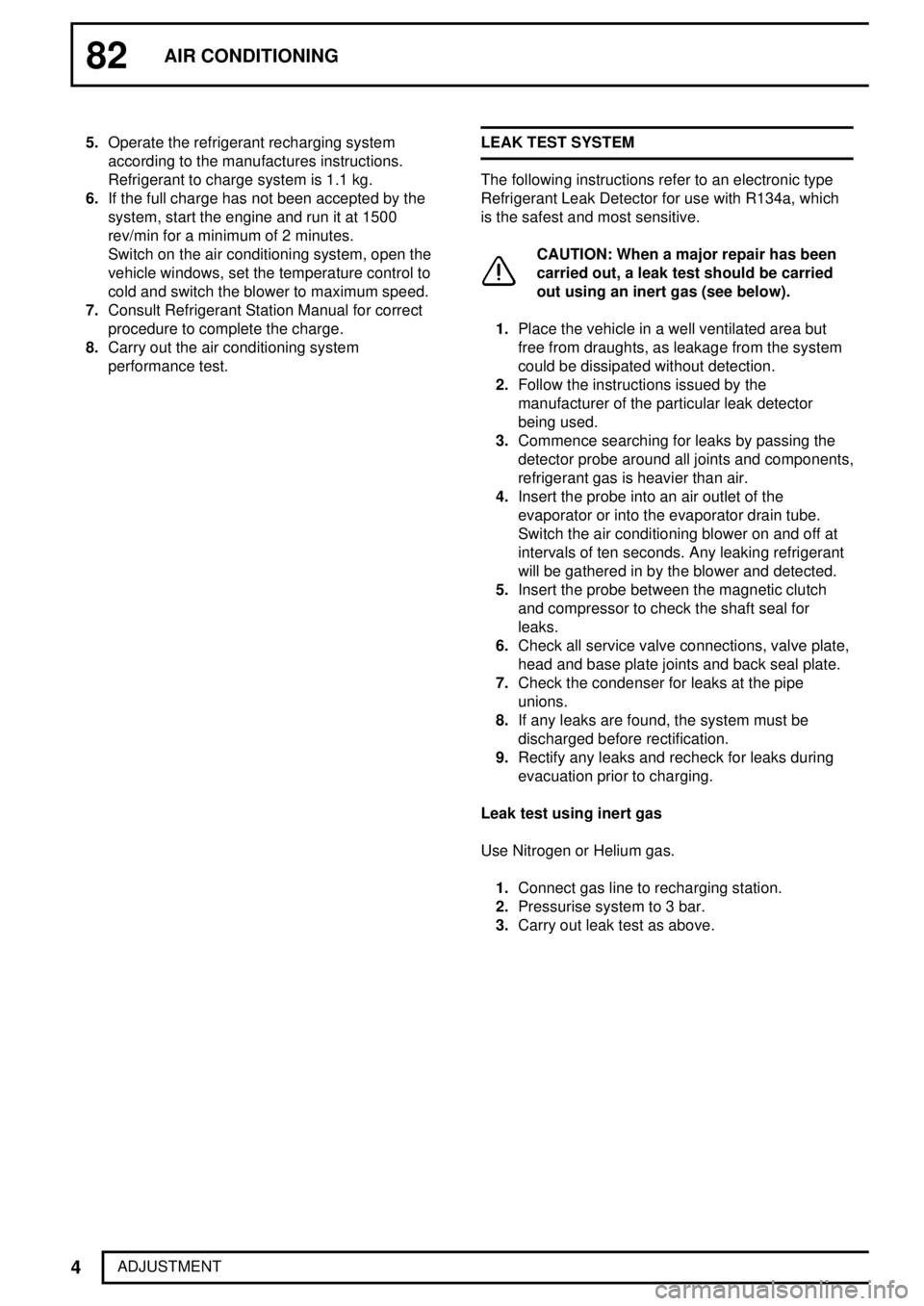
82AIR CONDITIONING
4
ADJUSTMENT 5.Operate the refrigerant recharging system
according to the manufactures instructions.
Refrigerant to charge system is 1.1 kg.
6.If the full charge has not been accepted by the
system, start the engine and run it at 1500
rev/min for a minimum of 2 minutes.
Switch on the air conditioning system, open the
vehicle windows, set the temperature control to
cold and switch the blower to maximum speed.
7.Consult Refrigerant Station Manual for correct
procedure to complete the charge.
8.Carry out the air conditioning system
performance test.LEAK TEST SYSTEM
The following instructions refer to an electronic type
Refrigerant Leak Detector for use with R134a, which
is the safest and most sensitive.
CAUTION: When a major repair has been
carried out, a leak test should be carried
out using an inert gas (see below).
1.Place the vehicle in a well ventilated area but
free from draughts, as leakage from the system
could be dissipated without detection.
2.Follow the instructions issued by the
manufacturer of the particular leak detector
being used.
3.Commence searching for leaks by passing the
detector probe around all joints and components,
refrigerant gas is heavier than air.
4.Insert the probe into an air outlet of the
evaporator or into the evaporator drain tube.
Switch the air conditioning blower on and off at
intervals of ten seconds. Any leaking refrigerant
will be gathered in by the blower and detected.
5.Insert the probe between the magnetic clutch
and compressor to check the shaft seal for
leaks.
6.Check all service valve connections, valve plate,
head and base plate joints and back seal plate.
7.Check the condenser for leaks at the pipe
unions.
8.If any leaks are found, the system must be
discharged before rectification.
9.Rectify any leaks and recheck for leaks during
evacuation prior to charging.
Leak test using inert gas
Use Nitrogen or Helium gas.
1.Connect gas line to recharging station.
2.Pressurise system to 3 bar.
3.Carry out leak test as above.
Page 380 of 455
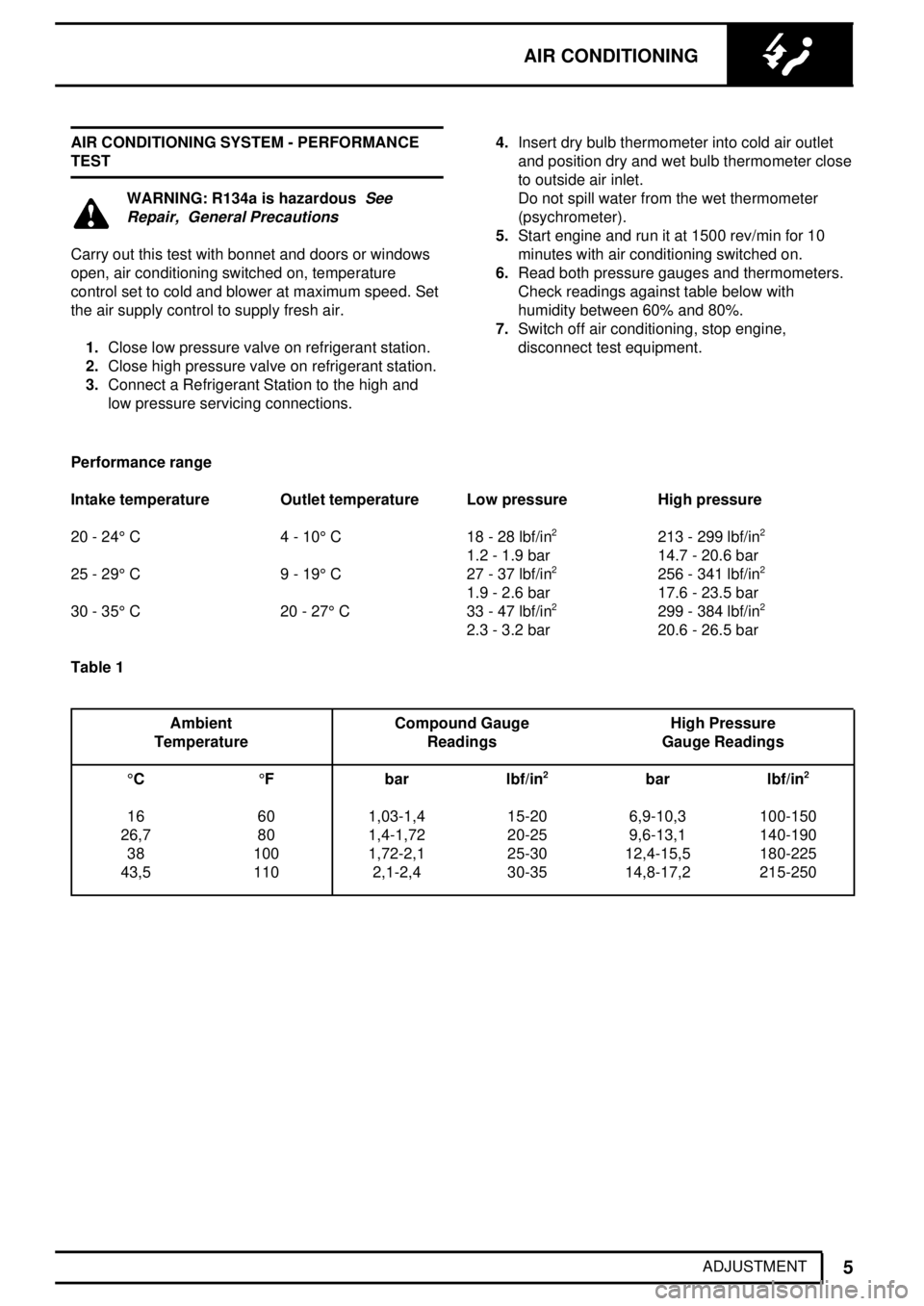
AIR CONDITIONING
5
ADJUSTMENT AIR CONDITIONING SYSTEM - PERFORMANCE
TEST
WARNING: R134a is hazardousSee
Repair, General Precautions
Carry out this test with bonnet and doors or windows
open, air conditioning switched on, temperature
control set to cold and blower at maximum speed. Set
the air supply control to supply fresh air.
1.Close low pressure valve on refrigerant station.
2.Close high pressure valve on refrigerant station.
3.Connect a Refrigerant Station to the high and
low pressure servicing connections.4.Insert dry bulb thermometer into cold air outlet
and position dry and wet bulb thermometer close
to outside air inlet.
Do not spill water from the wet thermometer
(psychrometer).
5.Start engine and run it at 1500 rev/min for 10
minutes with air conditioning switched on.
6.Read both pressure gauges and thermometers.
Check readings against table below with
humidity between 60% and 80%.
7.Switch off air conditioning, stop engine,
disconnect test equipment.
Performance range
Intake temperature Outlet temperature Low pressure High pressure
20 - 24°C4-10°C 18 - 28 lbf/in
2213 - 299 lbf/in2
1.2 - 1.9 bar 14.7 - 20.6 bar
25 - 29°C9-19°C 27 - 37 lbf/in2256 - 341 lbf/in2
1.9 - 2.6 bar 17.6 - 23.5 bar
30 - 35°C20-27°C 33 - 47 lbf/in2299 - 384 lbf/in2
2.3 - 3.2 bar 20.6 - 26.5 bar
Table 1
Ambient Compound Gauge High Pressure
Temperature Readings Gauge Readings
°C°F bar lbf/in
2bar lbf/in2
16 60 1,03-1,4 15-20 6,9-10,3 100-150
26,7 80 1,4-1,72 20-25 9,6-13,1 140-190
38 100 1,72-2,1 25-30 12,4-15,5 180-225
43,5 110 2,1-2,4 30-35 14,8-17,2 215-250
Page 381 of 455
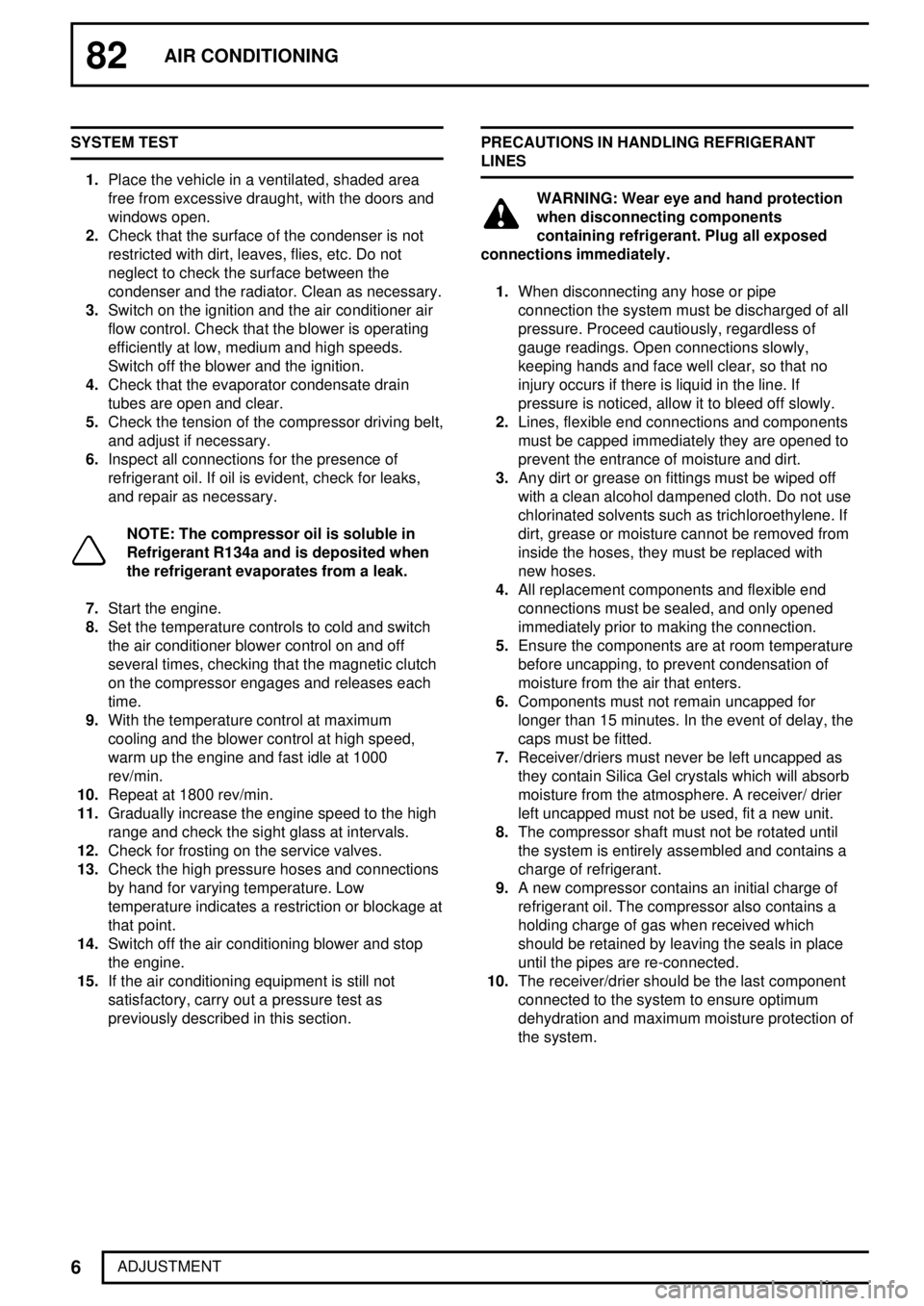
82AIR CONDITIONING
6
ADJUSTMENT SYSTEM TEST
1.Place the vehicle in a ventilated, shaded area
free from excessive draught, with the doors and
windows open.
2.Check that the surface of the condenser is not
restricted with dirt, leaves, flies, etc. Do not
neglect to check the surface between the
condenser and the radiator. Clean as necessary.
3.Switch on the ignition and the air conditioner air
flow control. Check that the blower is operating
efficiently at low, medium and high speeds.
Switch off the blower and the ignition.
4.Check that the evaporator condensate drain
tubes are open and clear.
5.Check the tension of the compressor driving belt,
and adjust if necessary.
6.Inspect all connections for the presence of
refrigerant oil. If oil is evident, check for leaks,
and repair as necessary.
NOTE: The compressor oil is soluble in
Refrigerant R134a and is deposited when
the refrigerant evaporates from a leak.
7.Start the engine.
8.Set the temperature controls to cold and switch
the air conditioner blower control on and off
several times, checking that the magnetic clutch
on the compressor engages and releases each
time.
9.With the temperature control at maximum
cooling and the blower control at high speed,
warm up the engine and fast idle at 1000
rev/min.
10.Repeat at 1800 rev/min.
11.Gradually increase the engine speed to the high
range and check the sight glass at intervals.
12.Check for frosting on the service valves.
13.Check the high pressure hoses and connections
by hand for varying temperature. Low
temperature indicates a restriction or blockage at
that point.
14.Switch off the air conditioning blower and stop
the engine.
15.If the air conditioning equipment is still not
satisfactory, carry out a pressure test as
previously described in this section.PRECAUTIONS IN HANDLING REFRIGERANT
LINES
WARNING: Wear eye and hand protection
when disconnecting components
containing refrigerant. Plug all exposed
connections immediately.
1.When disconnecting any hose or pipe
connection the system must be discharged of all
pressure. Proceed cautiously, regardless of
gauge readings. Open connections slowly,
keeping hands and face well clear, so that no
injury occurs if there is liquid in the line. If
pressure is noticed, allow it to bleed off slowly.
2.Lines, flexible end connections and components
must be capped immediately they are opened to
prevent the entrance of moisture and dirt.
3.Any dirt or grease on fittings must be wiped off
with a clean alcohol dampened cloth. Do not use
chlorinated solvents such as trichloroethylene. If
dirt, grease or moisture cannot be removed from
inside the hoses, they must be replaced with
new hoses.
4.All replacement components and flexible end
connections must be sealed, and only opened
immediately prior to making the connection.
5.Ensure the components are at room temperature
before uncapping, to prevent condensation of
moisture from the air that enters.
6.Components must not remain uncapped for
longer than 15 minutes. In the event of delay, the
caps must be fitted.
7.Receiver/driers must never be left uncapped as
they contain Silica Gel crystals which will absorb
moisture from the atmosphere. A receiver/ drier
left uncapped must not be used, fit a new unit.
8.The compressor shaft must not be rotated until
the system is entirely assembled and contains a
charge of refrigerant.
9.A new compressor contains an initial charge of
refrigerant oil. The compressor also contains a
holding charge of gas when received which
should be retained by leaving the seals in place
until the pipes are re-connected.
10.The receiver/drier should be the last component
connected to the system to ensure optimum
dehydration and maximum moisture protection of
the system.
Page 413 of 455
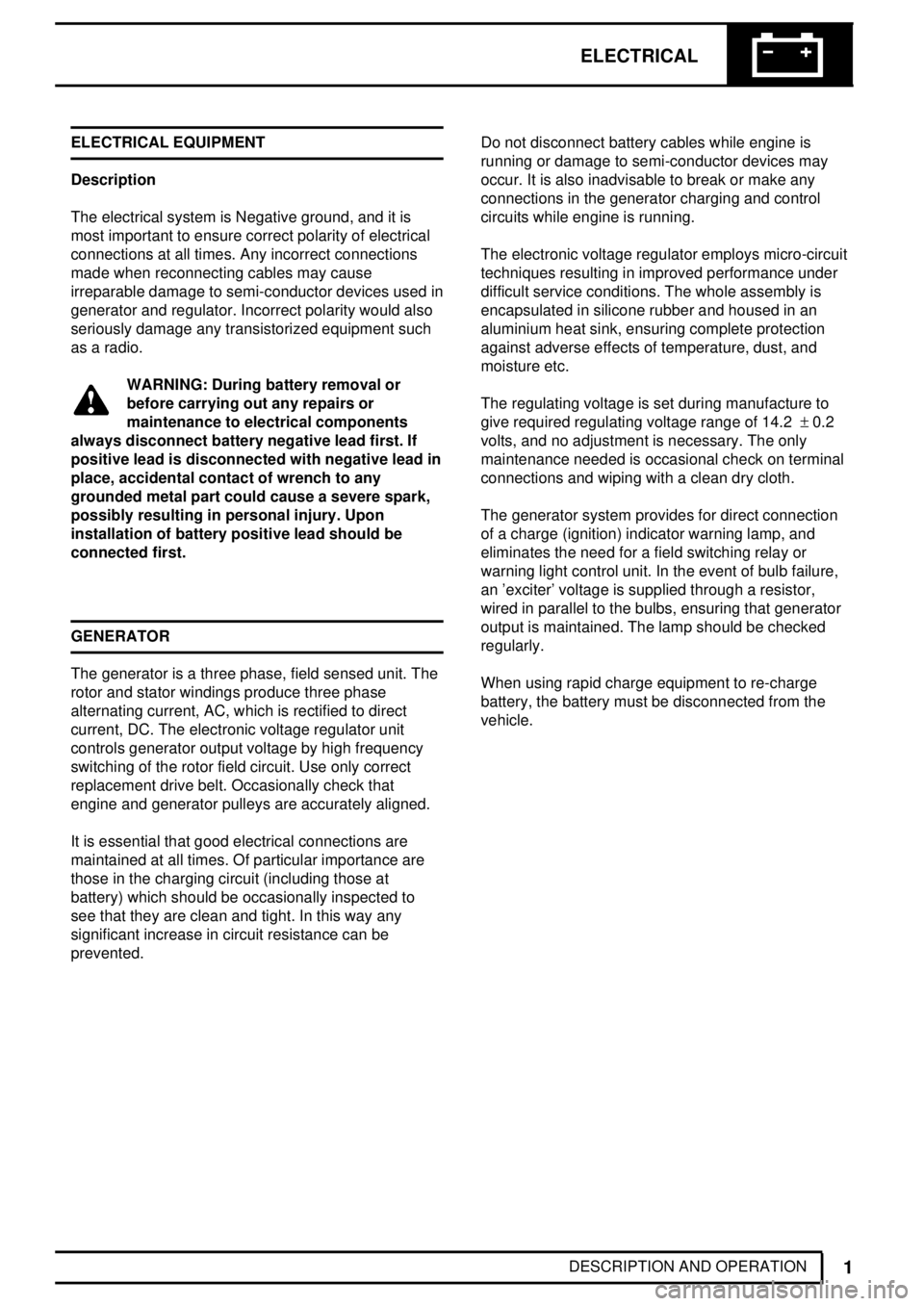
ELECTRICAL
1
DESCRIPTION AND OPERATION ELECTRICAL EQUIPMENT
Description
The electrical system is Negative ground, and it is
most important to ensure correct polarity of electrical
connections at all times. Any incorrect connections
made when reconnecting cables may cause
irreparable damage to semi-conductor devices used in
generator and regulator. Incorrect polarity would also
seriously damage any transistorized equipment such
as a radio.
WARNING: During battery removal or
before carrying out any repairs or
maintenance to electrical components
always disconnect battery negative lead first. If
positive lead is disconnected with negative lead in
place, accidental contact of wrench to any
grounded metal part could cause a severe spark,
possibly resulting in personal injury. Upon
installation of battery positive lead should be
connected first.
GENERATOR
The generator is a three phase, field sensed unit. The
rotor and stator windings produce three phase
alternating current, AC, which is rectified to direct
current, DC. The electronic voltage regulator unit
controls generator output voltage by high frequency
switching of the rotor field circuit. Use only correct
replacement drive belt. Occasionally check that
engine and generator pulleys are accurately aligned.
It is essential that good electrical connections are
maintained at all times. Of particular importance are
those in the charging circuit (including those at
battery) which should be occasionally inspected to
see that they are clean and tight. In this way any
significant increase in circuit resistance can be
prevented.Do not disconnect battery cables while engine is
running or damage to semi-conductor devices may
occur. It is also inadvisable to break or make any
connections in the generator charging and control
circuits while engine is running.
The electronic voltage regulator employs micro-circuit
techniques resulting in improved performance under
difficult service conditions. The whole assembly is
encapsulated in silicone rubber and housed in an
aluminium heat sink, ensuring complete protection
against adverse effects of temperature, dust, and
moisture etc.
The regulating voltage is set during manufacture to
give required regulating voltage range of 14.2±0.2
volts, and no adjustment is necessary. The only
maintenance needed is occasional check on terminal
connections and wiping with a clean dry cloth.
The generator system provides for direct connection
of a charge (ignition) indicator warning lamp, and
eliminates the need for a field switching relay or
warning light control unit. In the event of bulb failure,
an 'exciter' voltage is supplied through a resistor,
wired in parallel to the bulbs, ensuring that generator
output is maintained. The lamp should be checked
regularly.
When using rapid charge equipment to re-charge
battery, the battery must be disconnected from the
vehicle.
Page 425 of 455
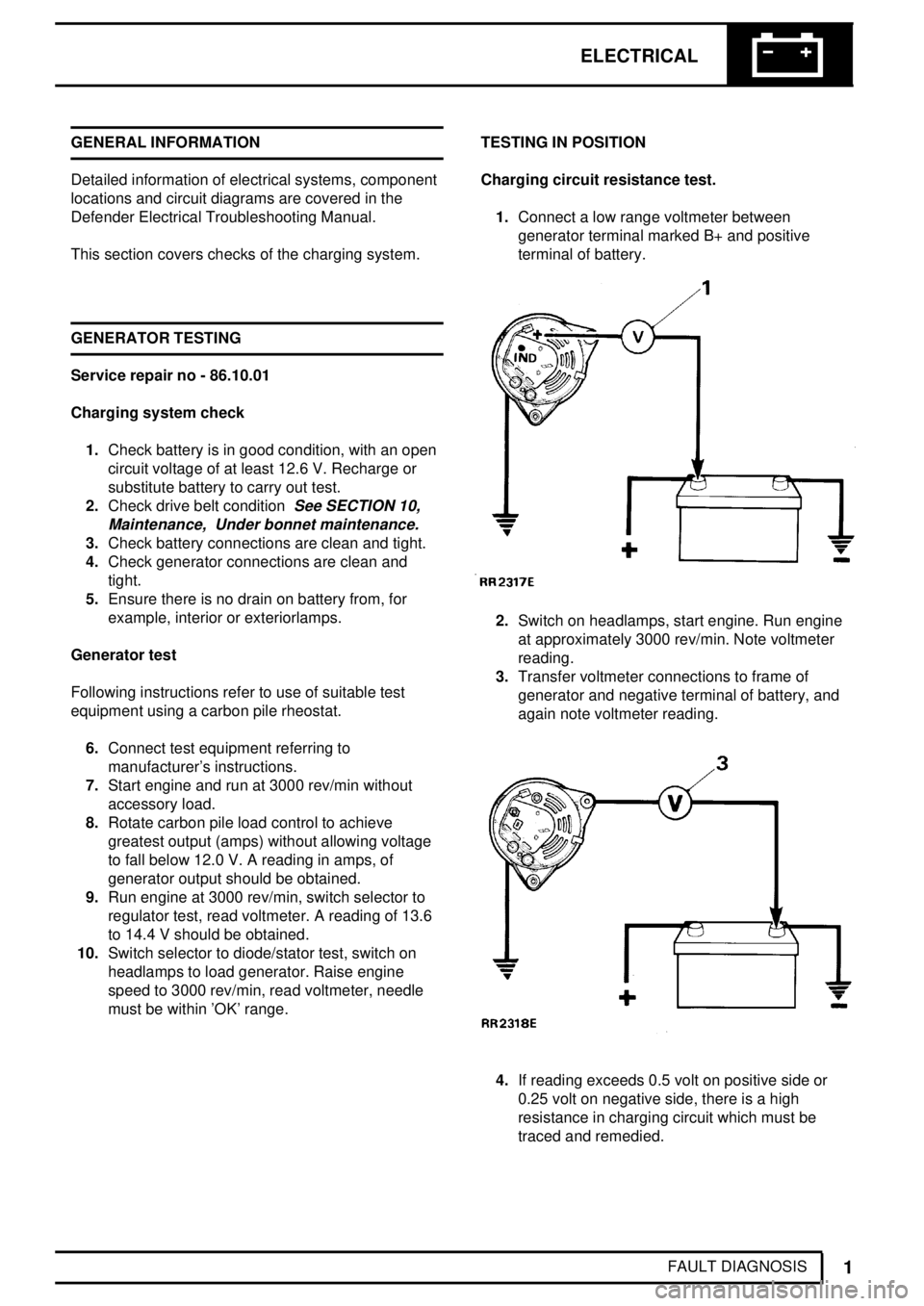
ELECTRICAL
1
FAULT DIAGNOSIS GENERAL INFORMATION
Detailed information of electrical systems, component
locations and circuit diagrams are covered in the
Defender Electrical Troubleshooting Manual.
This section covers checks of the charging system.
GENERATOR TESTING
Service repair no - 86.10.01
Charging system check
1.Check battery is in good condition, with an open
circuit voltage of at least 12.6 V. Recharge or
substitute battery to carry out test.
2.Check drive belt condition
See SECTION 10,
Maintenance, Under bonnet maintenance.
3.Check battery connections are clean and tight.
4.Check generator connections are clean and
tight.
5.Ensure there is no drain on battery from, for
example, interior or exteriorlamps.
Generator test
Following instructions refer to use of suitable test
equipment using a carbon pile rheostat.
6.Connect test equipment referring to
manufacturer's instructions.
7.Start engine and run at 3000 rev/min without
accessory load.
8.Rotate carbon pile load control to achieve
greatest output (amps) without allowing voltage
to fall below 12.0 V. A reading in amps, of
generator output should be obtained.
9.Run engine at 3000 rev/min, switch selector to
regulator test, read voltmeter. A reading of 13.6
to 14.4 V should be obtained.
10.Switch selector to diode/stator test, switch on
headlamps to load generator. Raise engine
speed to 3000 rev/min, read voltmeter, needle
must be within 'OK' range.TESTING IN POSITION
Charging circuit resistance test.
1.Connect a low range voltmeter between
generator terminal marked B+ and positive
terminal of battery.
2.Switch on headlamps, start engine. Run engine
at approximately 3000 rev/min. Note voltmeter
reading.
3.Transfer voltmeter connections to frame of
generator and negative terminal of battery, and
again note voltmeter reading.
4.If reading exceeds 0.5 volt on positive side or
0.25 volt on negative side, there is a high
resistance in charging circuit which must be
traced and remedied.
Page 429 of 455
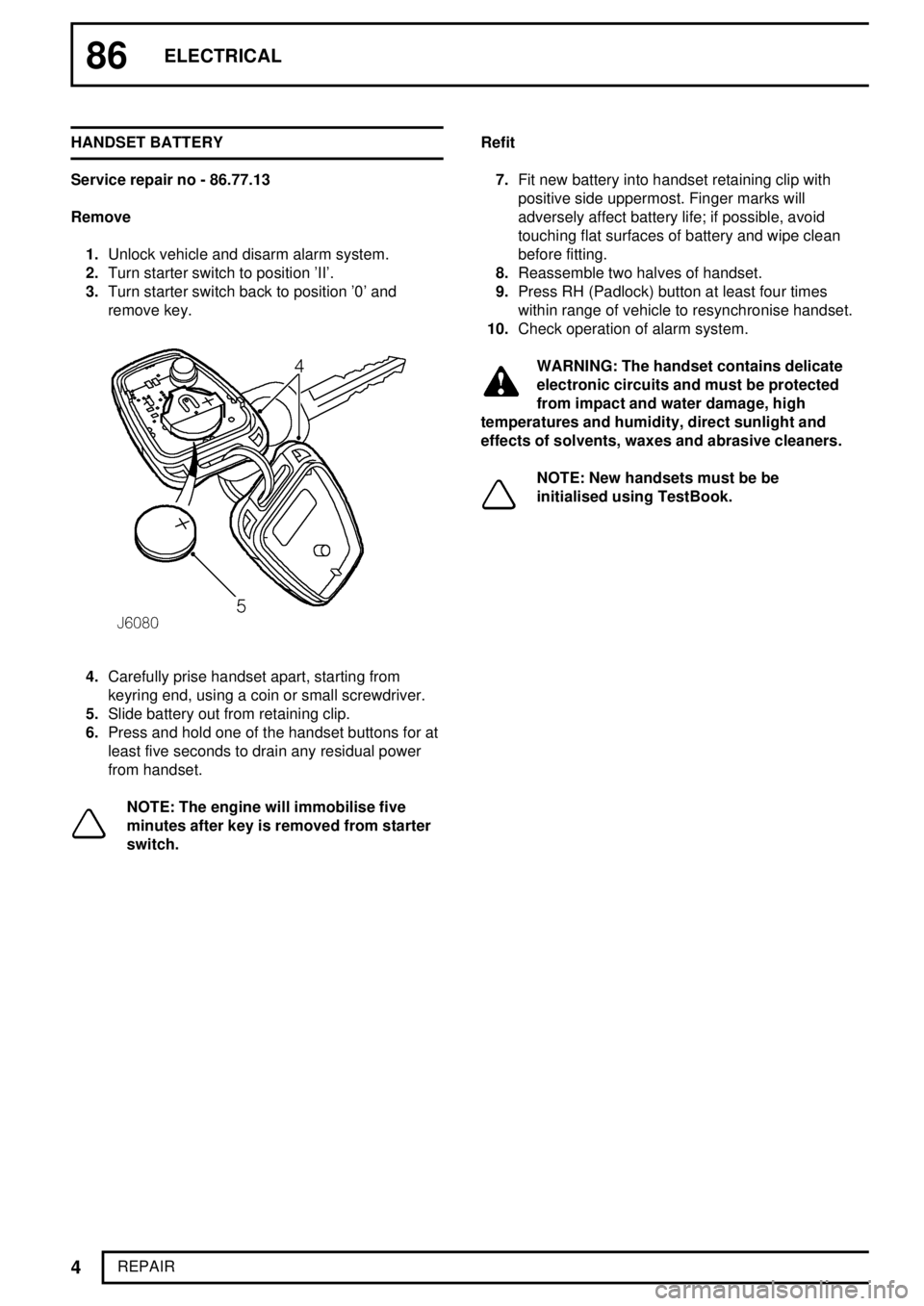
86ELECTRICAL
4
REPAIR HANDSET BATTERY
Service repair no - 86.77.13
Remove
1.Unlock vehicle and disarm alarm system.
2.Turn starter switch to position 'II'.
3.Turn starter switch back to position '0' and
remove key.
4.Carefully prise handset apart, starting from
keyring end, using a coin or small screwdriver.
5.Slide battery out from retaining clip.
6.Press and hold one of the handset buttons for at
least five seconds to drain any residual power
from handset.
NOTE: The engine will immobilise five
minutes after key is removed from starter
switch.Refit
7.Fit new battery into handset retaining clip with
positive side uppermost. Finger marks will
adversely affect battery life; if possible, avoid
touching flat surfaces of battery and wipe clean
before fitting.
8.Reassemble two halves of handset.
9.Press RH (Padlock) button at least four times
within range of vehicle to resynchronise handset.
10.Check operation of alarm system.
WARNING: The handset contains delicate
electronic circuits and must be protected
from impact and water damage, high
temperatures and humidity, direct sunlight and
effects of solvents, waxes and abrasive cleaners.
NOTE: New handsets must be be
initialised using TestBook.