ESP LAND ROVER DEFENDER 1996 Workshop Manual
[x] Cancel search | Manufacturer: LAND ROVER, Model Year: 1996, Model line: DEFENDER, Model: LAND ROVER DEFENDER 1996Pages: 455, PDF Size: 6.44 MB
Page 2 of 455
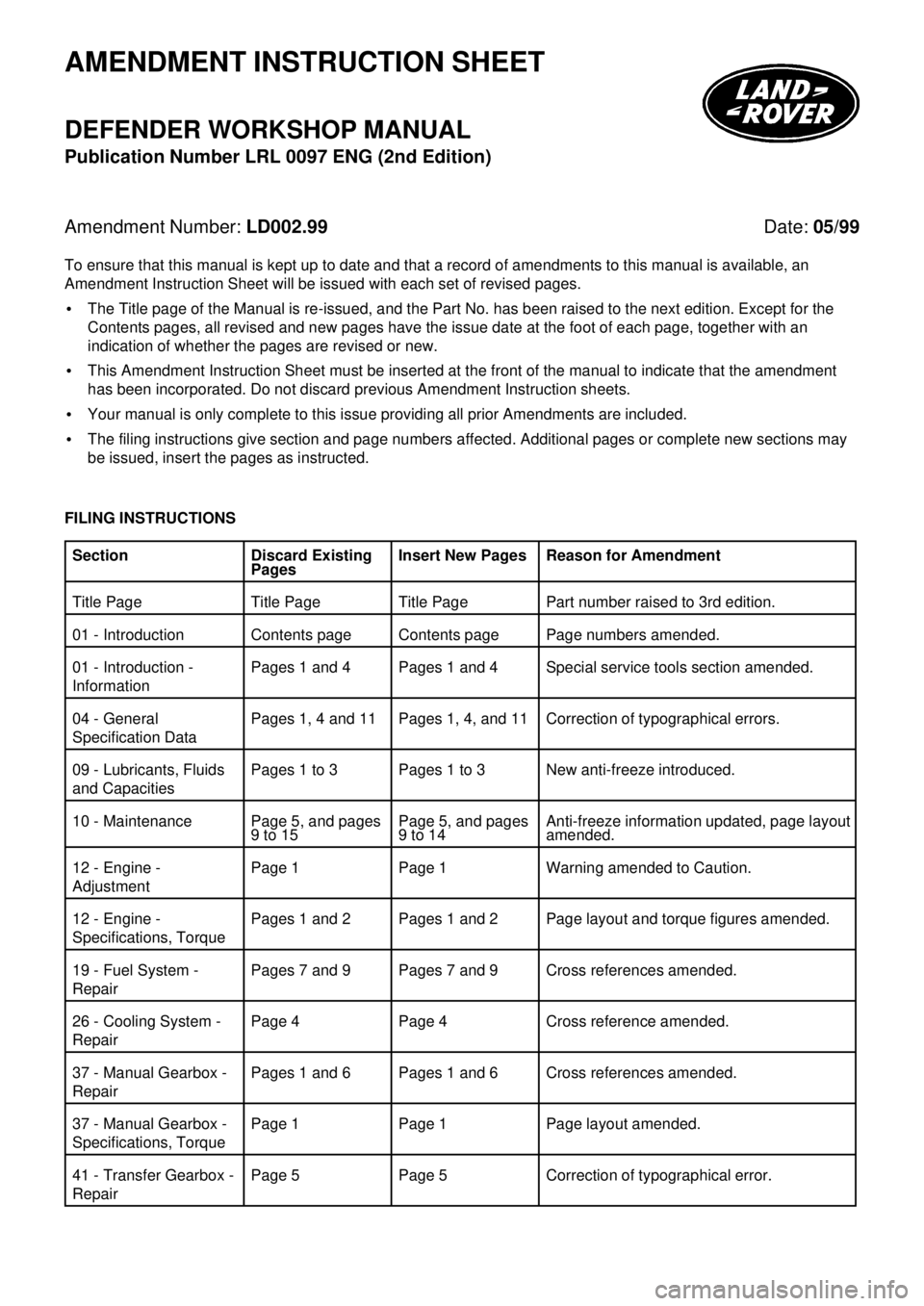
AMENDMENT INSTRUCTION SHEET
DEFENDER WORKSHOP MANUAL
Publication Number LRL 0097 ENG (2nd Edition)
Amendment Number:LD002.99Date:05/99
To ensure that this manual is kept up to date and that a record of amendments to this manual is available, an
Amendment Instruction Sheet will be issued with each set of revised pages.
·The Title page of the Manual is re-issued, and the Part No. has been raised to the next edition. Except for the
Contents pages, all revised and new pages have the issue date at the foot of each page, together with an
indication of whether the pages are revised or new.
·This Amendment Instruction Sheet must be inserted at the front of the manual to indicate that the amendment
has been incorporated. Do not discard previous Amendment Instruction sheets.
·Your manual is only complete to this issue providing all prior Amendments are included.
·The filing instructions give section and page numbers affected. Additional pages or complete new sections may
be issued, insert the pages as instructed.
FILING INSTRUCTIONS
Section Discard Existing
PagesInsert New Pages Reason for Amendment
Title Page Title Page Title Page Part number raised to 3rd edition.
01 - Introduction Contents page Contents page Page numbers amended.
01 - Introduction -
InformationPages 1 and 4 Pages 1 and 4 Special service tools section amended.
04 - General
Specification DataPages 1, 4 and 11 Pages 1, 4, and 11 Correction of typographical errors.
09 - Lubricants, Fluids
and CapacitiesPages 1 to 3 Pages 1 to 3 New anti-freeze introduced.
10 - Maintenance Page 5, and pages
9to15Page 5, and pages
9to14Anti-freeze information updated, page layout
amended.
12 - Engine -
AdjustmentPage 1 Page 1 Warning amended to Caution.
12 - Engine -
Specifications, TorquePages 1 and 2 Pages 1 and 2 Page layout and torque figures amended.
19 - Fuel System -
RepairPages 7 and 9 Pages 7 and 9 Cross references amended.
26 - Cooling System -
RepairPage 4 Page 4 Cross reference amended.
37 - Manual Gearbox -
RepairPages 1 and 6 Pages 1 and 6 Cross references amended.
37 - Manual Gearbox -
Specifications, TorquePage 1 Page 1 Page layout amended.
41 - Transfer Gearbox -
RepairPage 5 Page 5 Correction of typographical error.
Page 11 of 455
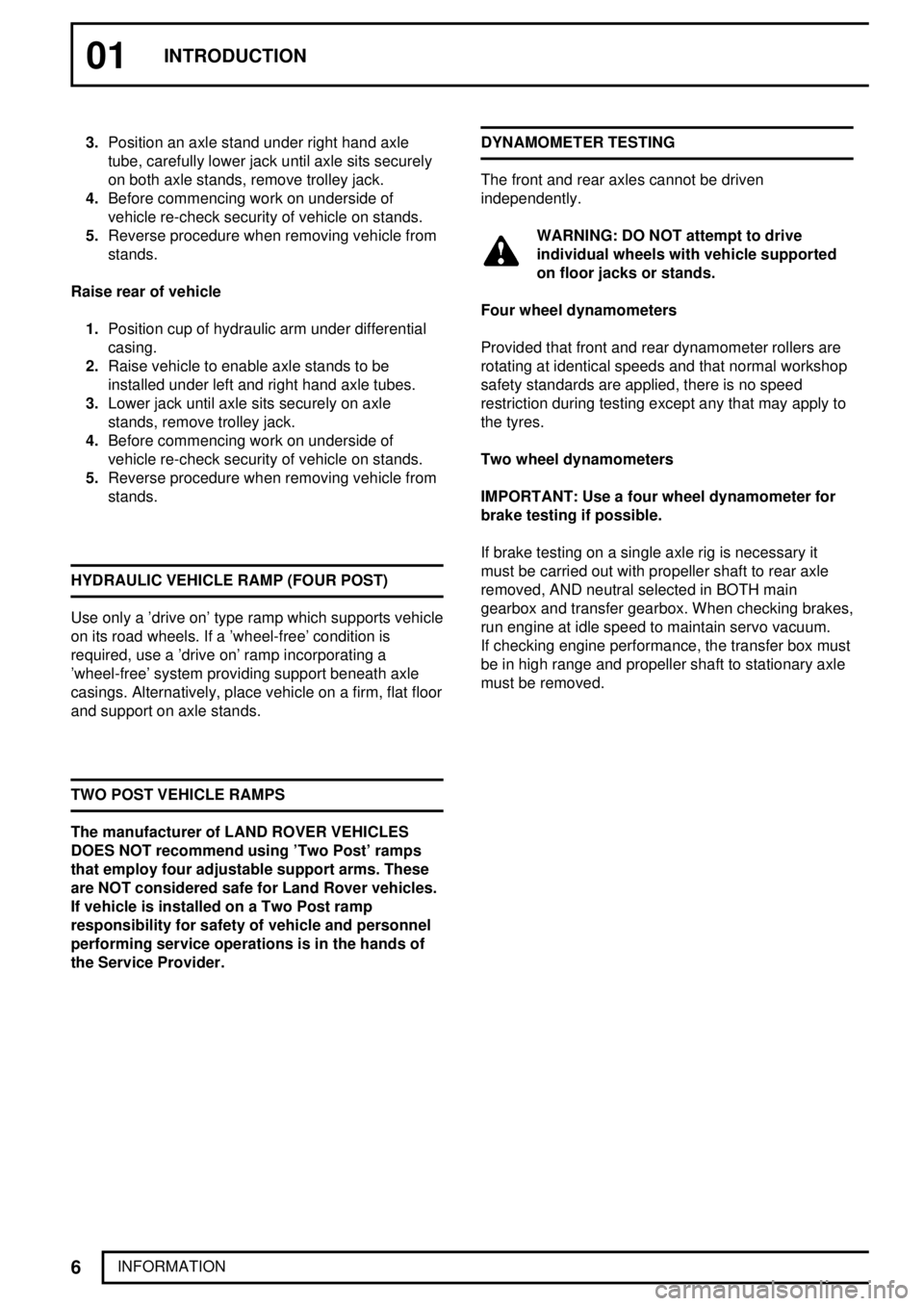
01INTRODUCTION
6
INFORMATION 3.Position an axle stand under right hand axle
tube, carefully lower jack until axle sits securely
on both axle stands, remove trolley jack.
4.Before commencing work on underside of
vehicle re-check security of vehicle on stands.
5.Reverse procedure when removing vehicle from
stands.
Raise rear of vehicle
1.Position cup of hydraulic arm under differential
casing.
2.Raise vehicle to enable axle stands to be
installed under left and right hand axle tubes.
3.Lower jack until axle sits securely on axle
stands, remove trolley jack.
4.Before commencing work on underside of
vehicle re-check security of vehicle on stands.
5.Reverse procedure when removing vehicle from
stands.
HYDRAULIC VEHICLE RAMP (FOUR POST)
Use only a 'drive on' type ramp which supports vehicle
on its road wheels. If a 'wheel-free' condition is
required, use a 'drive on' ramp incorporating a
'wheel-free' system providing support beneath axle
casings. Alternatively, place vehicle on a firm, flat floor
and support on axle stands.
TWO POST VEHICLE RAMPS
The manufacturer of LAND ROVER VEHICLES
DOES NOT recommend using 'Two Post' ramps
that employ four adjustable support arms. These
are NOT considered safe for Land Rover vehicles.
If vehicle is installed on a Two Post ramp
responsibility for safety of vehicle and personnel
performing service operations is in the hands of
the Service Provider.DYNAMOMETER TESTING
The front and rear axles cannot be driven
independently.
WARNING: DO NOT attempt to drive
individual wheels with vehicle supported
on floor jacks or stands.
Four wheel dynamometers
Provided that front and rear dynamometer rollers are
rotating at identical speeds and that normal workshop
safety standards are applied, there is no speed
restriction during testing except any that may apply to
the tyres.
Two wheel dynamometers
IMPORTANT: Use a four wheel dynamometer for
brake testing if possible.
If brake testing on a single axle rig is necessary it
must be carried out with propeller shaft to rear axle
removed, AND neutral selected in BOTH main
gearbox and transfer gearbox. When checking brakes,
run engine at idle speed to maintain servo vacuum.
If checking engine performance, the transfer box must
be in high range and propeller shaft to stationary axle
must be removed.
Page 27 of 455
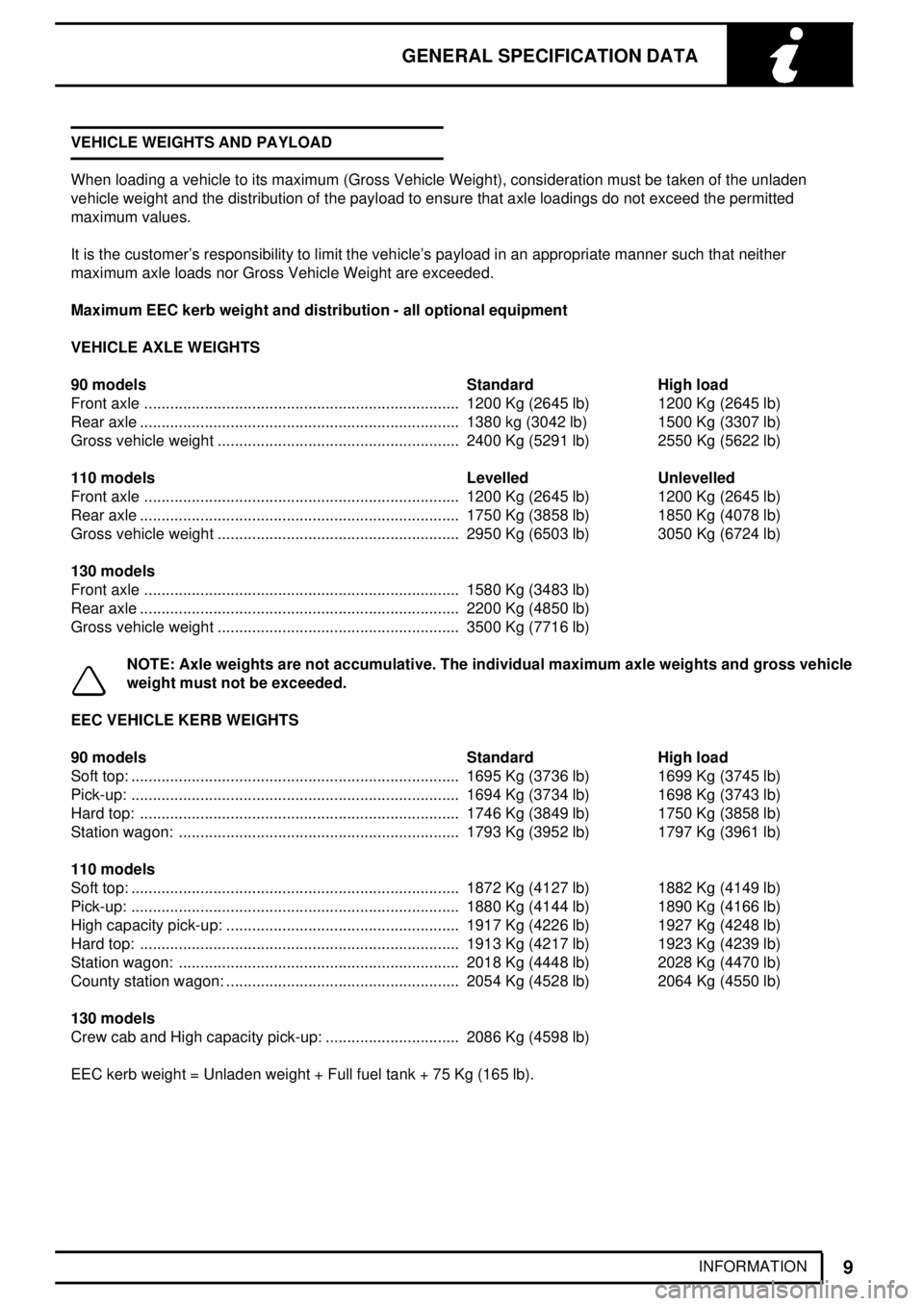
GENERAL SPECIFICATION DATA
9
INFORMATION VEHICLE WEIGHTS AND PAYLOAD
When loading a vehicle to its maximum (Gross Vehicle Weight), consideration must be taken of the unladen
vehicle weight and the distribution of the payload to ensure that axle loadings do not exceed the permitted
maximum values.
It is the customer's responsibility to limit the vehicle's payload in an appropriate manner such that neither
maximum axle loads nor Gross Vehicle Weight are exceeded.
Maximum EEC kerb weight and distribution - all optional equipment
VEHICLE AXLE WEIGHTS
90 models Standard High load
Front axle 1200 Kg (2645 lb)......................................................................... 1200 Kg (2645 lb)
Rear axle 1380 kg (3042 lb).......................................................................... 1500 Kg (3307 lb)
Gross vehicle weight 2400 Kg (5291 lb)........................................................ 2550 Kg (5622 lb)
110 models Levelled Unlevelled
Front axle 1200 Kg (2645 lb)......................................................................... 1200 Kg (2645 lb)
Rear axle 1750 Kg (3858 lb).......................................................................... 1850 Kg (4078 lb)
Gross vehicle weight 2950 Kg (6503 lb)........................................................ 3050 Kg (6724 lb)
130 models
Front axle 1580 Kg (3483 lb).........................................................................
Rear axle 2200 Kg (4850 lb)..........................................................................
Gross vehicle weight 3500 Kg (7716 lb)........................................................
NOTE: Axle weights are not accumulative. The individual maximum axle weights and gross vehicle
weight must not be exceeded.
EEC VEHICLE KERB WEIGHTS
90 models Standard High load
Soft top: 1695 Kg (3736 lb)............................................................................ 1699 Kg (3745 lb)
Pick-up: 1694 Kg (3734 lb)............................................................................ 1698 Kg (3743 lb)
Hard top: 1746 Kg (3849 lb).......................................................................... 1750 Kg (3858 lb)
Station wagon: 1793 Kg (3952 lb)................................................................. 1797 Kg (3961 lb)
110 models
Soft top: 1872 Kg (4127 lb)............................................................................ 1882 Kg (4149 lb)
Pick-up: 1880 Kg (4144 lb)............................................................................ 1890 Kg (4166 lb)
High capacity pick-up: 1917 Kg (4226 lb)...................................................... 1927 Kg (4248 lb)
Hard top: 1913 Kg (4217 lb).......................................................................... 1923 Kg (4239 lb)
Station wagon: 2018 Kg (4448 lb)................................................................. 2028 Kg (4470 lb)
County station wagon: 2054 Kg (4528 lb)...................................................... 2064 Kg (4550 lb)
130 models
Crew cab and High capacity pick-up: 2086 Kg (4598 lb)...............................
EEC kerb weight = Unladen weight + Full fuel tank + 75 Kg (165 lb).
Page 33 of 455
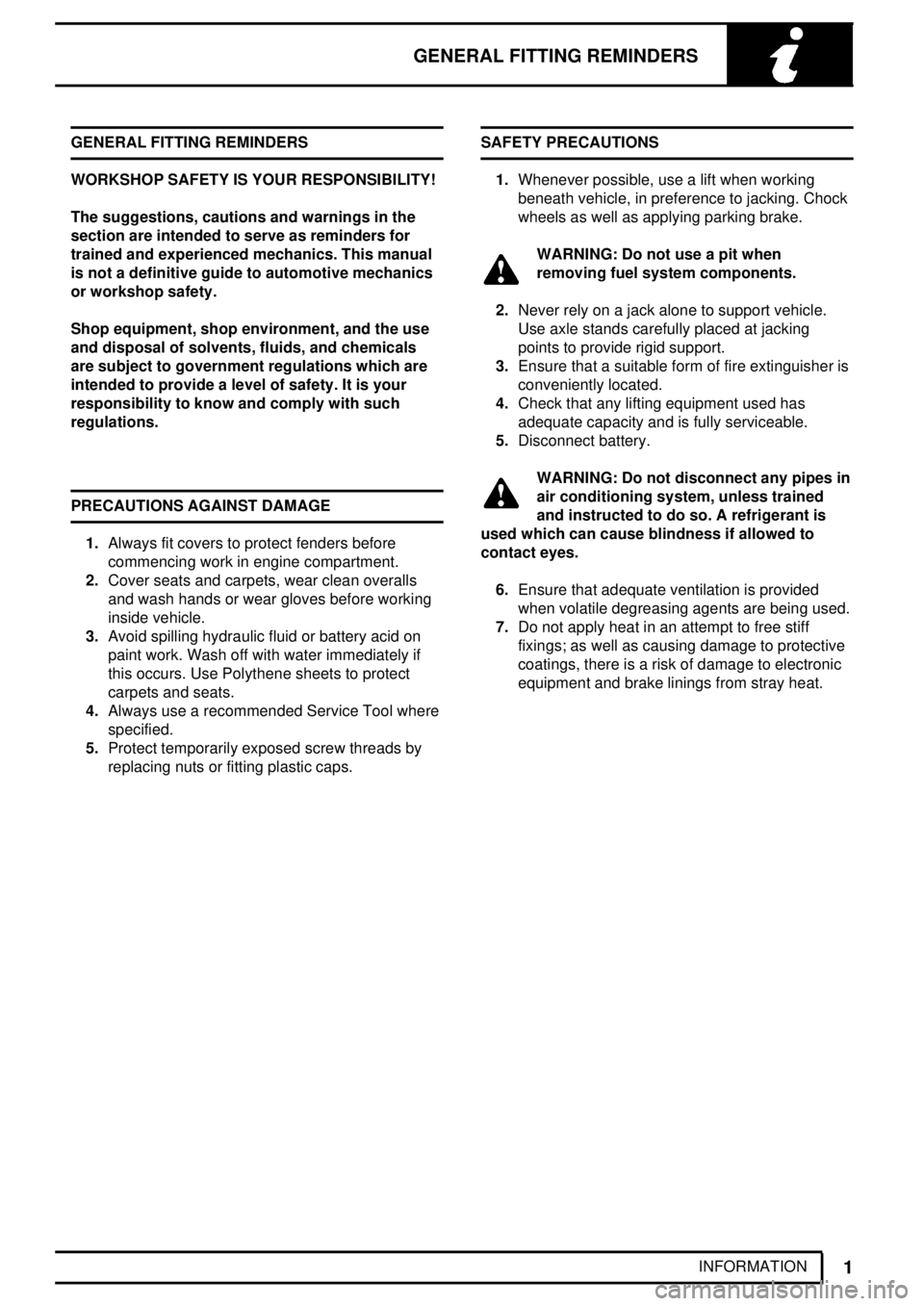
GENERAL FITTING REMINDERS
1
INFORMATION GENERAL FITTING REMINDERS
WORKSHOP SAFETY IS YOUR RESPONSIBILITY!
The suggestions, cautions and warnings in the
section are intended to serve as reminders for
trained and experienced mechanics. This manual
is not a definitive guide to automotive mechanics
or workshop safety.
Shop equipment, shop environment, and the use
and disposal of solvents, fluids, and chemicals
are subject to government regulations which are
intended to provide a level of safety. It is your
responsibility to know and comply with such
regulations.
PRECAUTIONS AGAINST DAMAGE
1.Always fit covers to protect fenders before
commencing work in engine compartment.
2.Cover seats and carpets, wear clean overalls
and wash hands or wear gloves before working
inside vehicle.
3.Avoid spilling hydraulic fluid or battery acid on
paint work. Wash off with water immediately if
this occurs. Use Polythene sheets to protect
carpets and seats.
4.Always use a recommended Service Tool where
specified.
5.Protect temporarily exposed screw threads by
replacing nuts or fitting plastic caps.SAFETY PRECAUTIONS
1.Whenever possible, use a lift when working
beneath vehicle, in preference to jacking. Chock
wheels as well as applying parking brake.
WARNING: Do not use a pit when
removing fuel system components.
2.Never rely on a jack alone to support vehicle.
Use axle stands carefully placed at jacking
points to provide rigid support.
3.Ensure that a suitable form of fire extinguisher is
conveniently located.
4.Check that any lifting equipment used has
adequate capacity and is fully serviceable.
5.Disconnect battery.
WARNING: Do not disconnect any pipes in
air conditioning system, unless trained
and instructed to do so. A refrigerant is
used which can cause blindness if allowed to
contact eyes.
6.Ensure that adequate ventilation is provided
when volatile degreasing agents are being used.
7.Do not apply heat in an attempt to free stiff
fixings; as well as causing damage to protective
coatings, there is a risk of damage to electronic
equipment and brake linings from stray heat.
Page 96 of 455
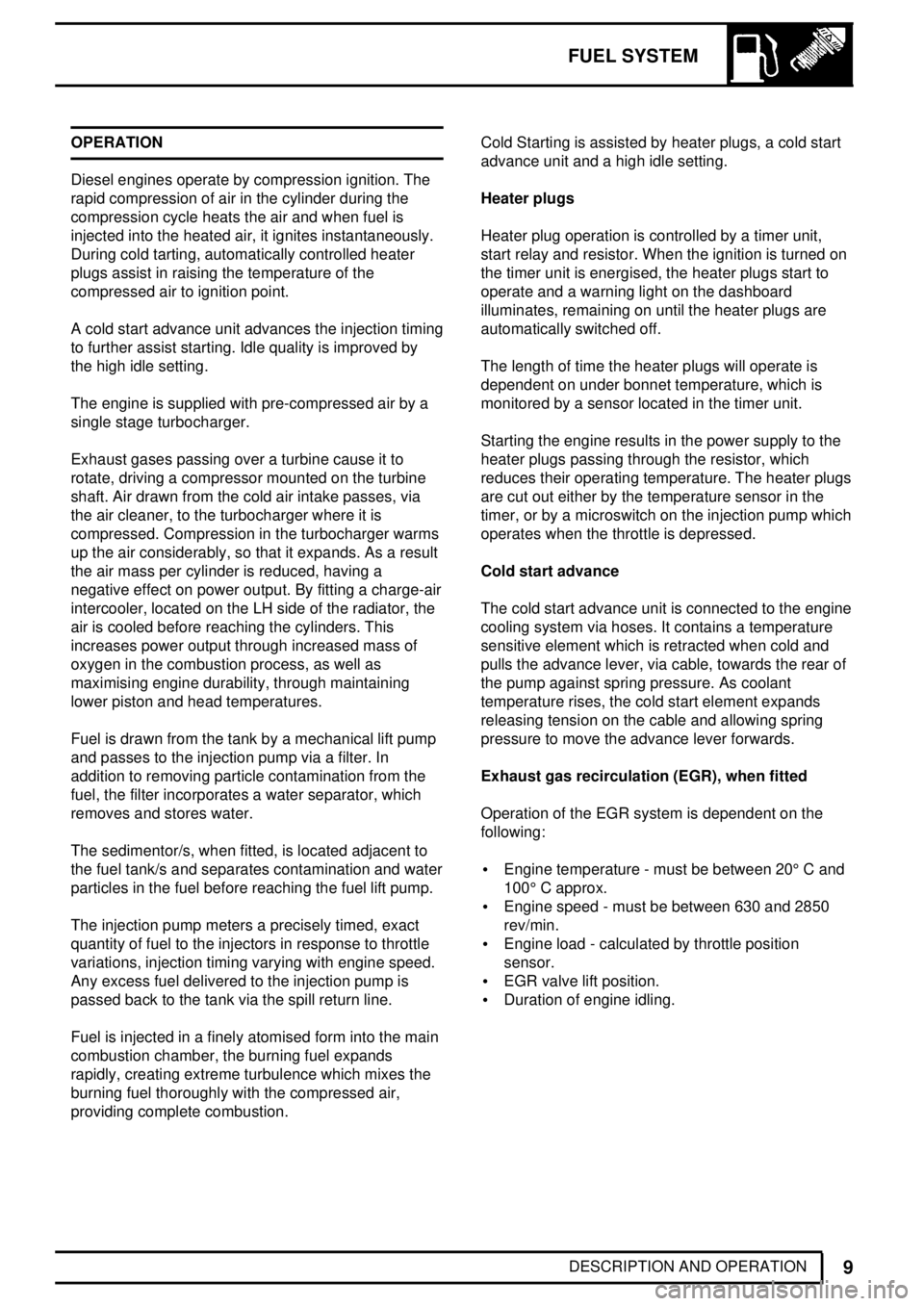
FUEL SYSTEM
9
DESCRIPTION AND OPERATION OPERATION
Diesel engines operate by compression ignition. The
rapid compression of air in the cylinder during the
compression cycle heats the air and when fuel is
injected into the heated air, it ignites instantaneously.
During cold tarting, automatically controlled heater
plugs assist in raising the temperature of the
compressed air to ignition point.
A cold start advance unit advances the injection timing
to further assist starting. Idle quality is improved by
the high idle setting.
The engine is supplied with pre-compressed air by a
single stage turbocharger.
Exhaust gases passing over a turbine cause it to
rotate, driving a compressor mounted on the turbine
shaft. Air drawn from the cold air intake passes, via
the air cleaner, to the turbocharger where it is
compressed. Compression in the turbocharger warms
up the air considerably, so that it expands. As a result
the air mass per cylinder is reduced, having a
negative effect on power output. By fitting a charge-air
intercooler, located on the LH side of the radiator, the
air is cooled before reaching the cylinders. This
increases power output through increased mass of
oxygen in the combustion process, as well as
maximising engine durability, through maintaining
lower piston and head temperatures.
Fuel is drawn from the tank by a mechanical lift pump
and passes to the injection pump via a filter. In
addition to removing particle contamination from the
fuel, the filter incorporates a water separator, which
removes and stores water.
The sedimentor/s, when fitted, is located adjacent to
the fuel tank/s and separates contamination and water
particles in the fuel before reaching the fuel lift pump.
The injection pump meters a precisely timed, exact
quantity of fuel to the injectors in response to throttle
variations, injection timing varying with engine speed.
Any excess fuel delivered to the injection pump is
passed back to the tank via the spill return line.
Fuel is injected in a finely atomised form into the main
combustion chamber, the burning fuel expands
rapidly, creating extreme turbulence which mixes the
burning fuel thoroughly with the compressed air,
providing complete combustion.Cold Starting is assisted by heater plugs, a cold start
advance unit and a high idle setting.
Heater plugs
Heater plug operation is controlled by a timer unit,
start relay and resistor. When the ignition is turned on
the timer unit is energised, the heater plugs start to
operate and a warning light on the dashboard
illuminates, remaining on until the heater plugs are
automatically switched off.
The length of time the heater plugs will operate is
dependent on under bonnet temperature, which is
monitored by a sensor located in the timer unit.
Starting the engine results in the power supply to the
heater plugs passing through the resistor, which
reduces their operating temperature. The heater plugs
are cut out either by the temperature sensor in the
timer, or by a microswitch on the injection pump which
operates when the throttle is depressed.
Cold start advance
The cold start advance unit is connected to the engine
cooling system via hoses. It contains a temperature
sensitive element which is retracted when cold and
pulls the advance lever, via cable, towards the rear of
the pump against spring pressure. As coolant
temperature rises, the cold start element expands
releasing tension on the cable and allowing spring
pressure to move the advance lever forwards.
Exhaust gas recirculation (EGR), when fitted
Operation of the EGR system is dependent on the
following:
·Engine temperature - must be between 20°C and
100°C approx.
·Engine speed - must be between 630 and 2850
rev/min.
·Engine load - calculated by throttle position
sensor.
·EGR valve lift position.
·Duration of engine idling.
Page 111 of 455
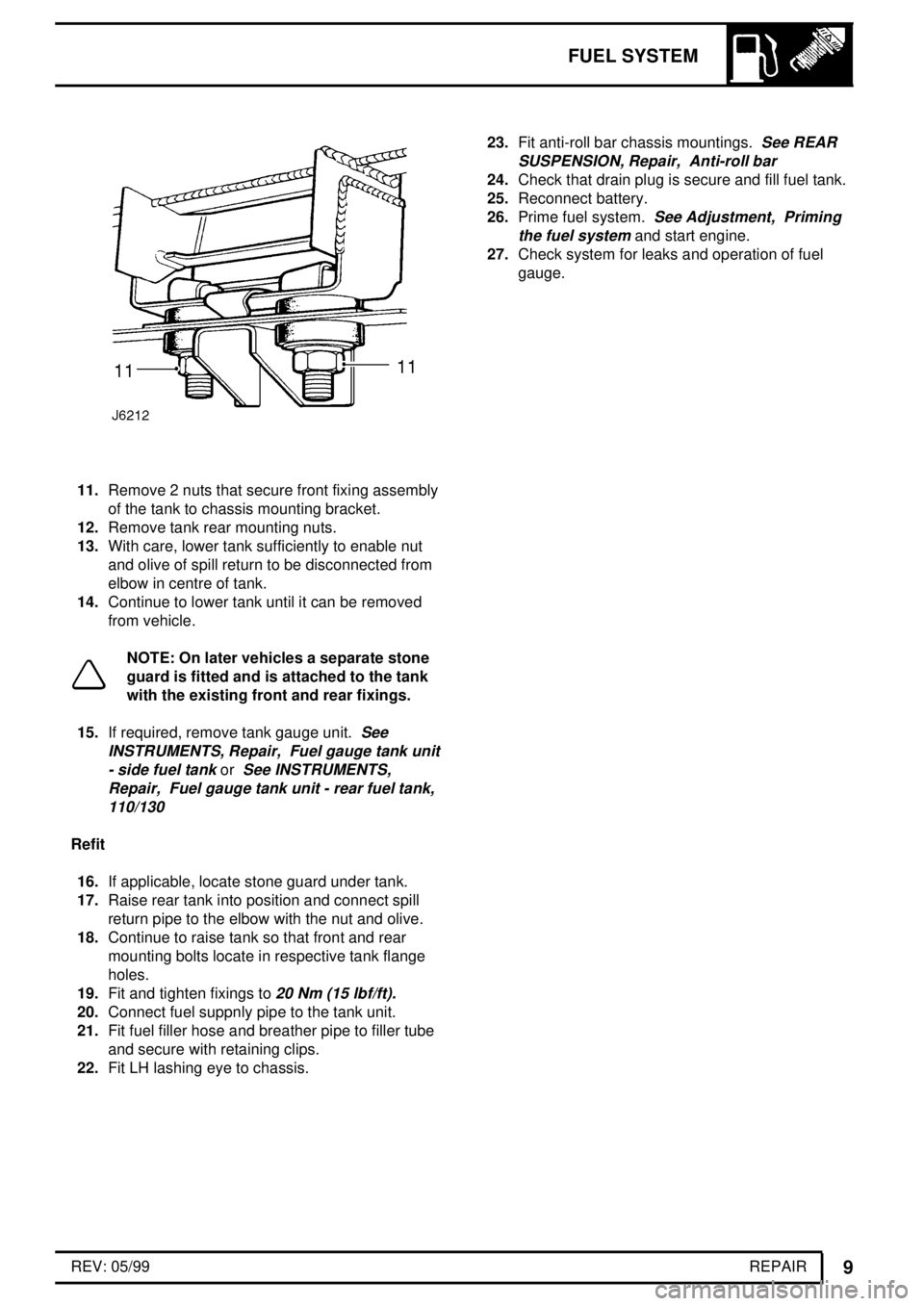
FUEL SYSTEM
9
REPAIR REV: 05/99
11.Remove 2 nuts that secure front fixing assembly
of the tank to chassis mounting bracket.
12.Remove tank rear mounting nuts.
13.With care, lower tank sufficiently to enable nut
and olive of spill return to be disconnected from
elbow in centre of tank.
14.Continue to lower tank until it can be removed
from vehicle.
NOTE: On later vehicles a separate stone
guard is fitted and is attached to the tank
with the existing front and rear fixings.
15.If required, remove tank gauge unit.
See
INSTRUMENTS, Repair, Fuel gauge tank unit
- side fuel tank
orSee INSTRUMENTS,
Repair, Fuel gauge tank unit - rear fuel tank,
110/130
Refit
16.If applicable, locate stone guard under tank.
17.Raise rear tank into position and connect spill
return pipe to the elbow with the nut and olive.
18.Continue to raise tank so that front and rear
mounting bolts locate in respective tank flange
holes.
19.Fit and tighten fixings to
20 Nm (15 lbf/ft).
20.Connect fuel suppnly pipe to the tank unit.
21.Fit fuel filler hose and breather pipe to filler tube
and secure with retaining clips.
22.Fit LH lashing eye to chassis.23.Fit anti-roll bar chassis mountings.
See REAR
SUSPENSION, Repair, Anti-roll bar
24.Check that drain plug is secure and fill fuel tank.
25.Reconnect battery.
26.Prime fuel system.
See Adjustment, Priming
the fuel system
and start engine.
27.Check system for leaks and operation of fuel
gauge.
Page 142 of 455
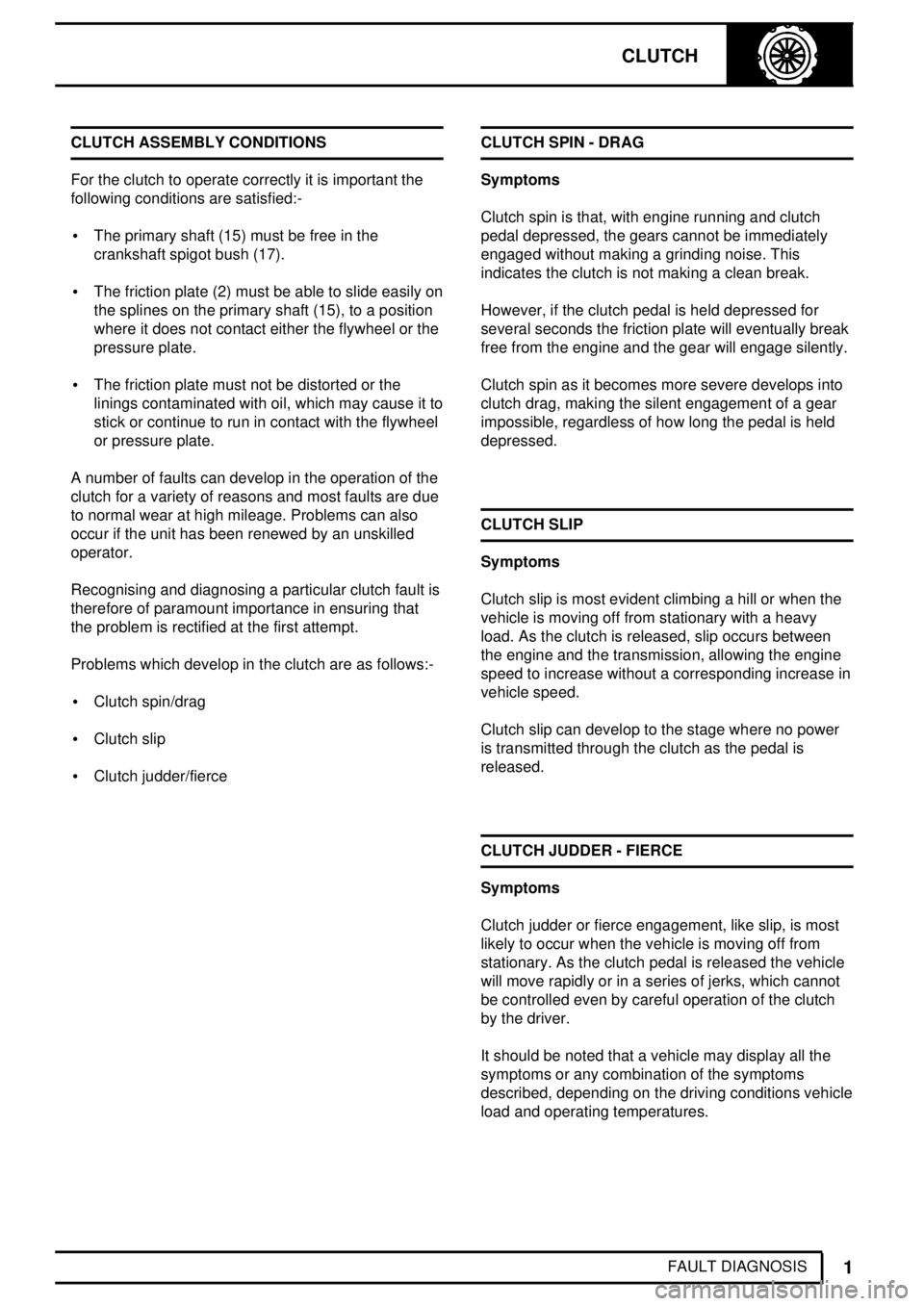
CLUTCH
1
FAULT DIAGNOSIS CLUTCH ASSEMBLY CONDITIONS
For the clutch to operate correctly it is important the
following conditions are satisfied:-
·The primary shaft (15) must be free in the
crankshaft spigot bush (17).
·The friction plate (2) must be able to slide easily on
the splines on the primary shaft (15), to a position
where it does not contact either the flywheel or the
pressure plate.
·The friction plate must not be distorted or the
linings contaminated with oil, which may cause it to
stick or continue to run in contact with the flywheel
or pressure plate.
A number of faults can develop in the operation of the
clutch for a variety of reasons and most faults are due
to normal wear at high mileage. Problems can also
occur if the unit has been renewed by an unskilled
operator.
Recognising and diagnosing a particular clutch fault is
therefore of paramount importance in ensuring that
the problem is rectified at the first attempt.
Problems which develop in the clutch are as follows:-
·Clutch spin/drag
·Clutch slip
·Clutch judder/fierceCLUTCH SPIN - DRAG
Symptoms
Clutch spin is that, with engine running and clutch
pedal depressed, the gears cannot be immediately
engaged without making a grinding noise. This
indicates the clutch is not making a clean break.
However, if the clutch pedal is held depressed for
several seconds the friction plate will eventually break
free from the engine and the gear will engage silently.
Clutch spin as it becomes more severe develops into
clutch drag, making the silent engagement of a gear
impossible, regardless of how long the pedal is held
depressed.
CLUTCH SLIP
Symptoms
Clutch slip is most evident climbing a hill or when the
vehicle is moving off from stationary with a heavy
load. As the clutch is released, slip occurs between
the engine and the transmission, allowing the engine
speed to increase without a corresponding increase in
vehicle speed.
Clutch slip can develop to the stage where no power
is transmitted through the clutch as the pedal is
released.
CLUTCH JUDDER - FIERCE
Symptoms
Clutch judder or fierce engagement, like slip, is most
likely to occur when the vehicle is moving off from
stationary. As the clutch pedal is released the vehicle
will move rapidly or in a series of jerks, which cannot
be controlled even by careful operation of the clutch
by the driver.
It should be noted that a vehicle may display all the
symptoms or any combination of the symptoms
described, depending on the driving conditions vehicle
load and operating temperatures.
Page 177 of 455
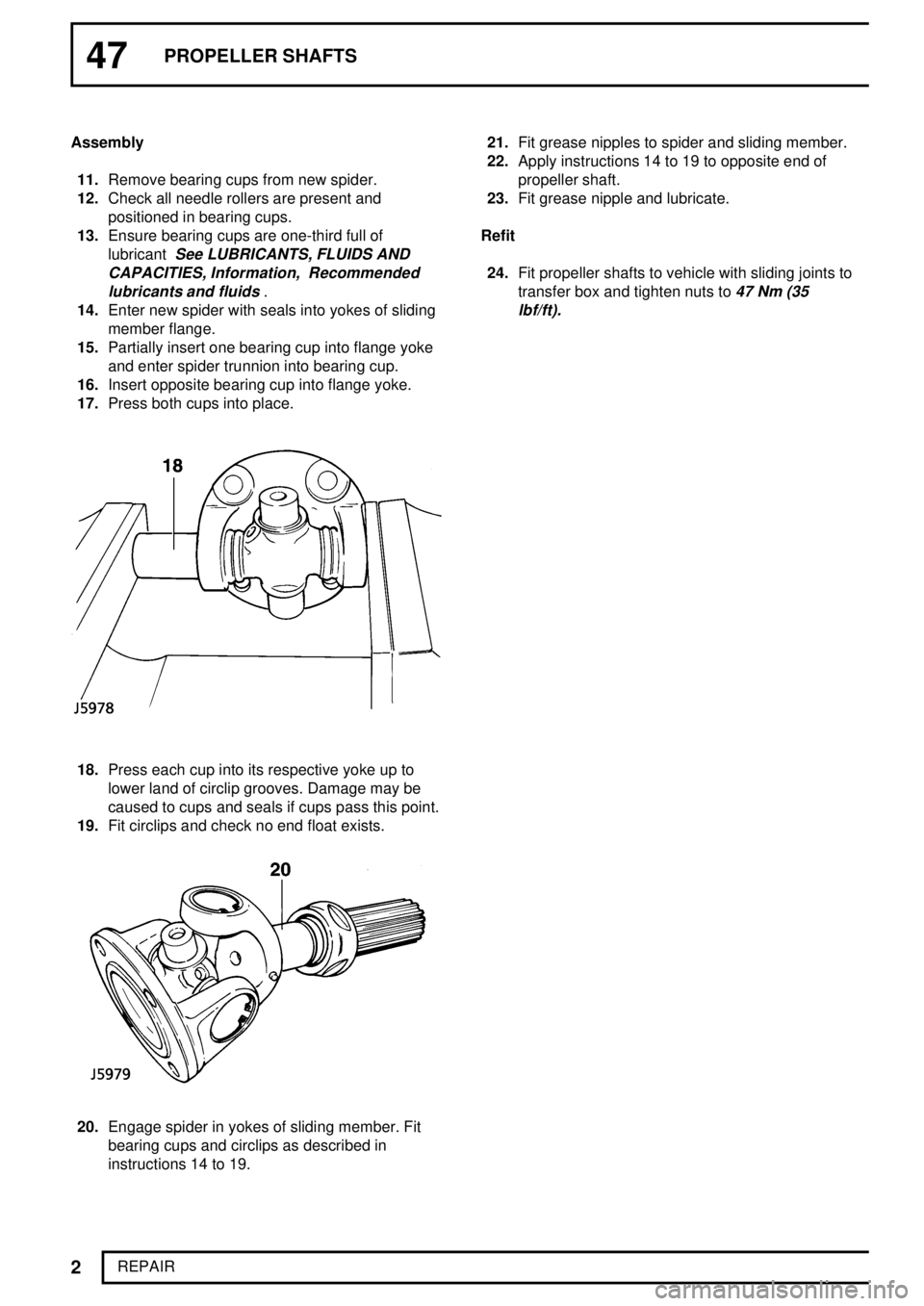
47PROPELLER SHAFTS
2
REPAIR Assembly
11.Remove bearing cups from new spider.
12.Check all needle rollers are present and
positioned in bearing cups.
13.Ensure bearing cups are one-third full of
lubricant
See LUBRICANTS, FLUIDS AND
CAPACITIES, Information, Recommended
lubricants and fluids
.
14.Enter new spider with seals into yokes of sliding
member flange.
15.Partially insert one bearing cup into flange yoke
and enter spider trunnion into bearing cup.
16.Insert opposite bearing cup into flange yoke.
17.Press both cups into place.
18.Press each cup into its respective yoke up to
lower land of circlip grooves. Damage may be
caused to cups and seals if cups pass this point.
19.Fit circlips and check no end float exists.
20.Engage spider in yokes of sliding member. Fit
bearing cups and circlips as described in
instructions 14 to 19.21.Fit grease nipples to spider and sliding member.
22.Apply instructions 14 to 19 to opposite end of
propeller shaft.
23.Fit grease nipple and lubricate.
Refit
24.Fit propeller shafts to vehicle with sliding joints to
transfer box and tighten nuts to
47 Nm (35
lbf/ft).
Page 178 of 455
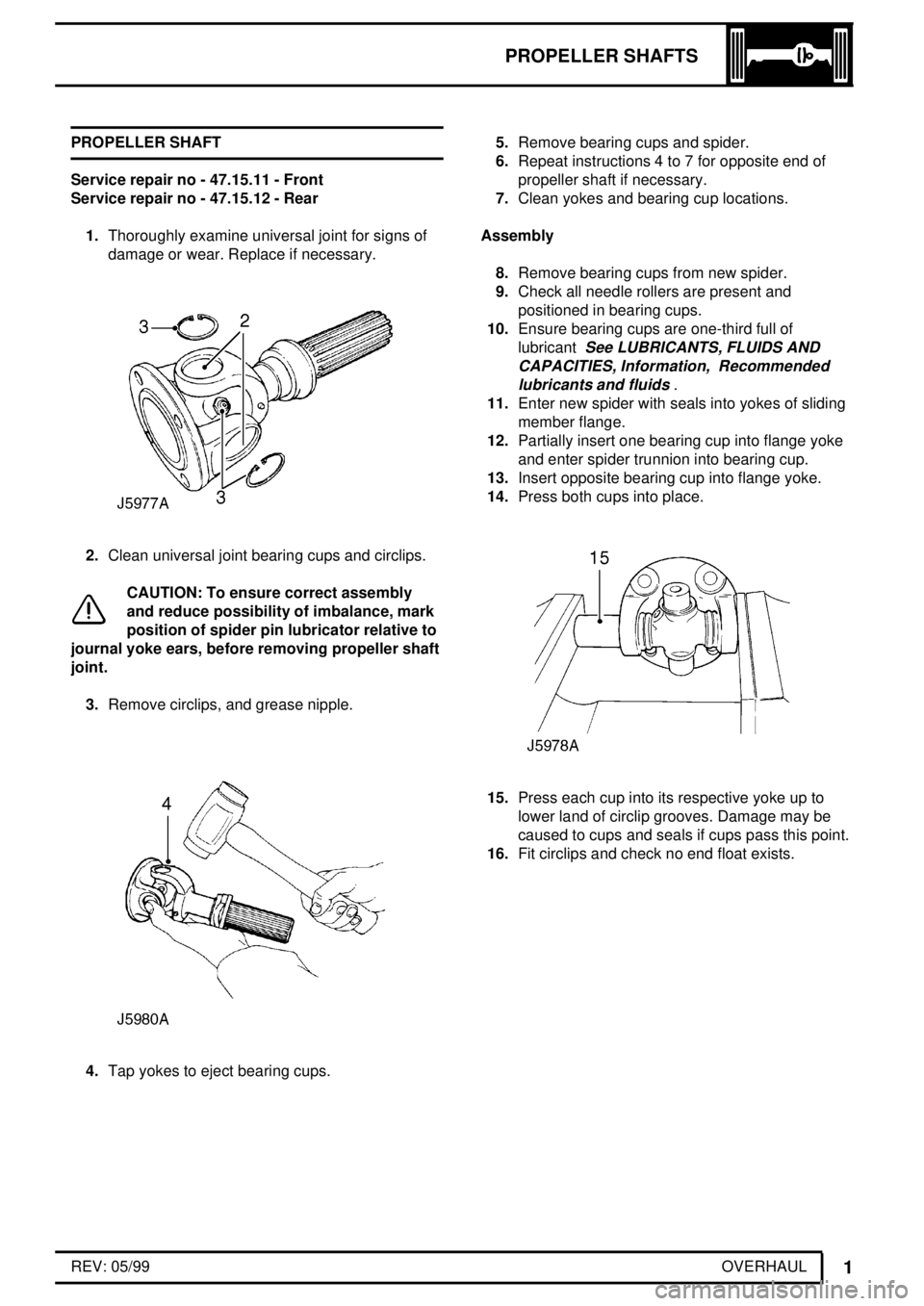
PROPELLER SHAFTS
1
OVERHAUL REV: 05/99 PROPELLER SHAFT
Service repair no - 47.15.11 - Front
Service repair no - 47.15.12 - Rear
1.Thoroughly examine universal joint for signs of
damage or wear. Replace if necessary.
2.Clean universal joint bearing cups and circlips.
CAUTION: To ensure correct assembly
and reduce possibility of imbalance, mark
position of spider pin lubricator relative to
journal yoke ears, before removing propeller shaft
joint.
3.Remove circlips, and grease nipple.
4.Tap yokes to eject bearing cups.5.Remove bearing cups and spider.
6.Repeat instructions 4 to 7 for opposite end of
propeller shaft if necessary.
7.Clean yokes and bearing cup locations.
Assembly
8.Remove bearing cups from new spider.
9.Check all needle rollers are present and
positioned in bearing cups.
10.Ensure bearing cups are one-third full of
lubricant
See LUBRICANTS, FLUIDS AND
CAPACITIES, Information, Recommended
lubricants and fluids
.
11.Enter new spider with seals into yokes of sliding
member flange.
12.Partially insert one bearing cup into flange yoke
and enter spider trunnion into bearing cup.
13.Insert opposite bearing cup into flange yoke.
14.Press both cups into place.
15.Press each cup into its respective yoke up to
lower land of circlip grooves. Damage may be
caused to cups and seals if cups pass this point.
16.Fit circlips and check no end float exists.
Page 280 of 455
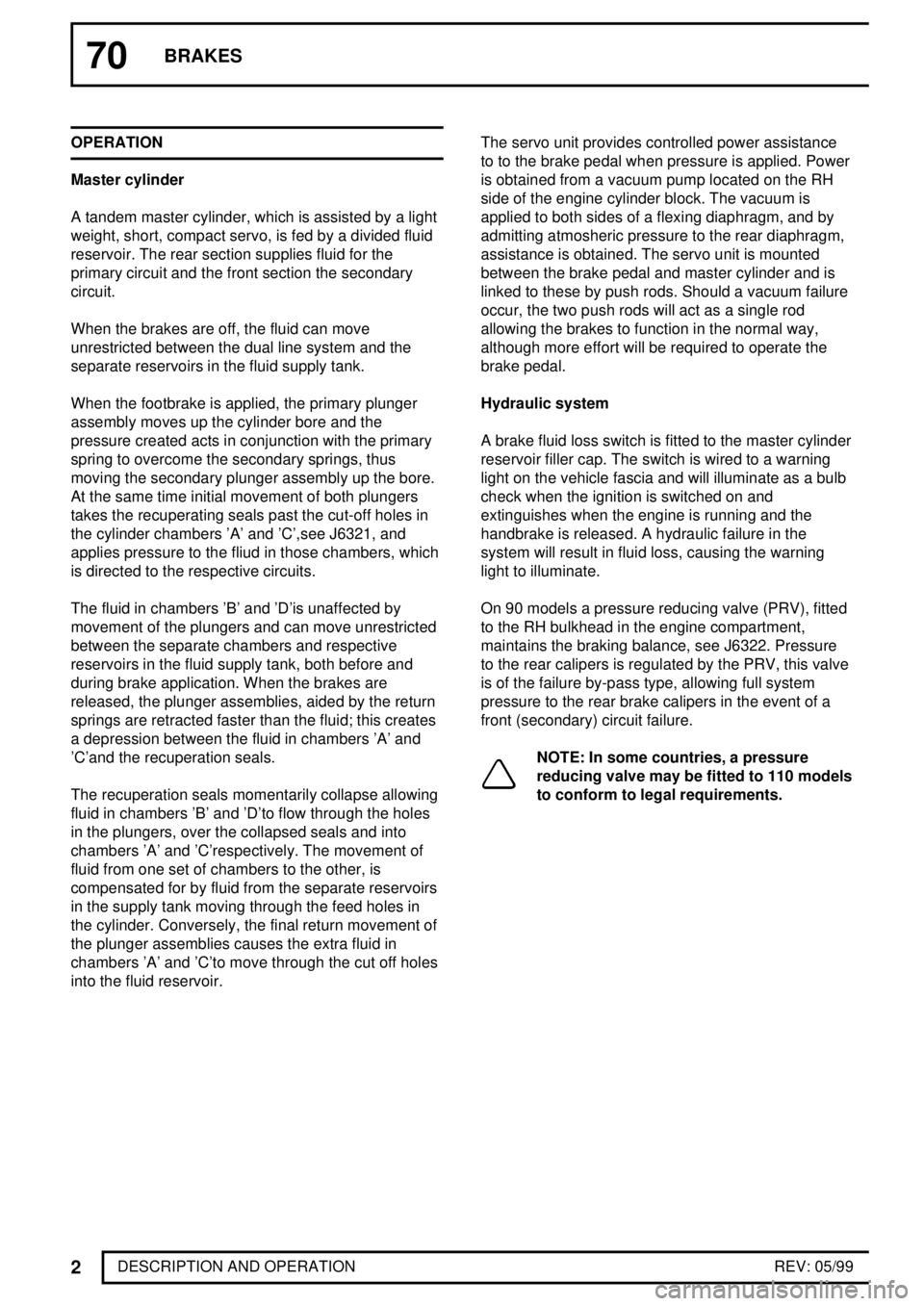
70BRAKES
2
DESCRIPTION AND OPERATION REV: 05/99 OPERATION
Master cylinder
A tandem master cylinder, which is assisted by a light
weight, short, compact servo, is fed by a divided fluid
reservoir. The rear section supplies fluid for the
primary circuit and the front section the secondary
circuit.
When the brakes are off, the fluid can move
unrestricted between the dual line system and the
separate reservoirs in the fluid supply tank.
When the footbrake is applied, the primary plunger
assembly moves up the cylinder bore and the
pressure created acts in conjunction with the primary
spring to overcome the secondary springs, thus
moving the secondary plunger assembly up the bore.
At the same time initial movement of both plungers
takes the recuperating seals past the cut-off holes in
the cylinder chambers 'A' and 'C',see J6321, and
applies pressure to the fliud in those chambers, which
is directed to the respective circuits.
The fluid in chambers 'B' and 'D'is unaffected by
movement of the plungers and can move unrestricted
between the separate chambers and respective
reservoirs in the fluid supply tank, both before and
during brake application. When the brakes are
released, the plunger assemblies, aided by the return
springs are retracted faster than the fluid; this creates
a depression between the fluid in chambers 'A' and
'C'and the recuperation seals.
The recuperation seals momentarily collapse allowing
fluid in chambers 'B' and 'D'to flow through the holes
in the plungers, over the collapsed seals and into
chambers 'A' and 'C'respectively. The movement of
fluid from one set of chambers to the other, is
compensated for by fluid from the separate reservoirs
in the supply tank moving through the feed holes in
the cylinder. Conversely, the final return movement of
the plunger assemblies causes the extra fluid in
chambers 'A' and 'C'to move through the cut off holes
into the fluid reservoir.The servo unit provides controlled power assistance
to to the brake pedal when pressure is applied. Power
is obtained from a vacuum pump located on the RH
side of the engine cylinder block. The vacuum is
applied to both sides of a flexing diaphragm, and by
admitting atmosheric pressure to the rear diaphragm,
assistance is obtained. The servo unit is mounted
between the brake pedal and master cylinder and is
linked to these by push rods. Should a vacuum failure
occur, the two push rods will act as a single rod
allowing the brakes to function in the normal way,
although more effort will be required to operate the
brake pedal.
Hydraulic system
A brake fluid loss switch is fitted to the master cylinder
reservoir filler cap. The switch is wired to a warning
light on the vehicle fascia and will illuminate as a bulb
check when the ignition is switched on and
extinguishes when the engine is running and the
handbrake is released. A hydraulic failure in the
system will result in fluid loss, causing the warning
light to illuminate.
On 90 models a pressure reducing valve (PRV), fitted
to the RH bulkhead in the engine compartment,
maintains the braking balance, see J6322. Pressure
to the rear calipers is regulated by the PRV, this valve
is of the failure by-pass type, allowing full system
pressure to the rear brake calipers in the event of a
front (secondary) circuit failure.
NOTE: In some countries, a pressure
reducing valve may be fitted to 110 models
to conform to legal requirements.