service indicator LAND ROVER DEFENDER 1996 Workshop Manual
[x] Cancel search | Manufacturer: LAND ROVER, Model Year: 1996, Model line: DEFENDER, Model: LAND ROVER DEFENDER 1996Pages: 455, PDF Size: 6.44 MB
Page 44 of 455
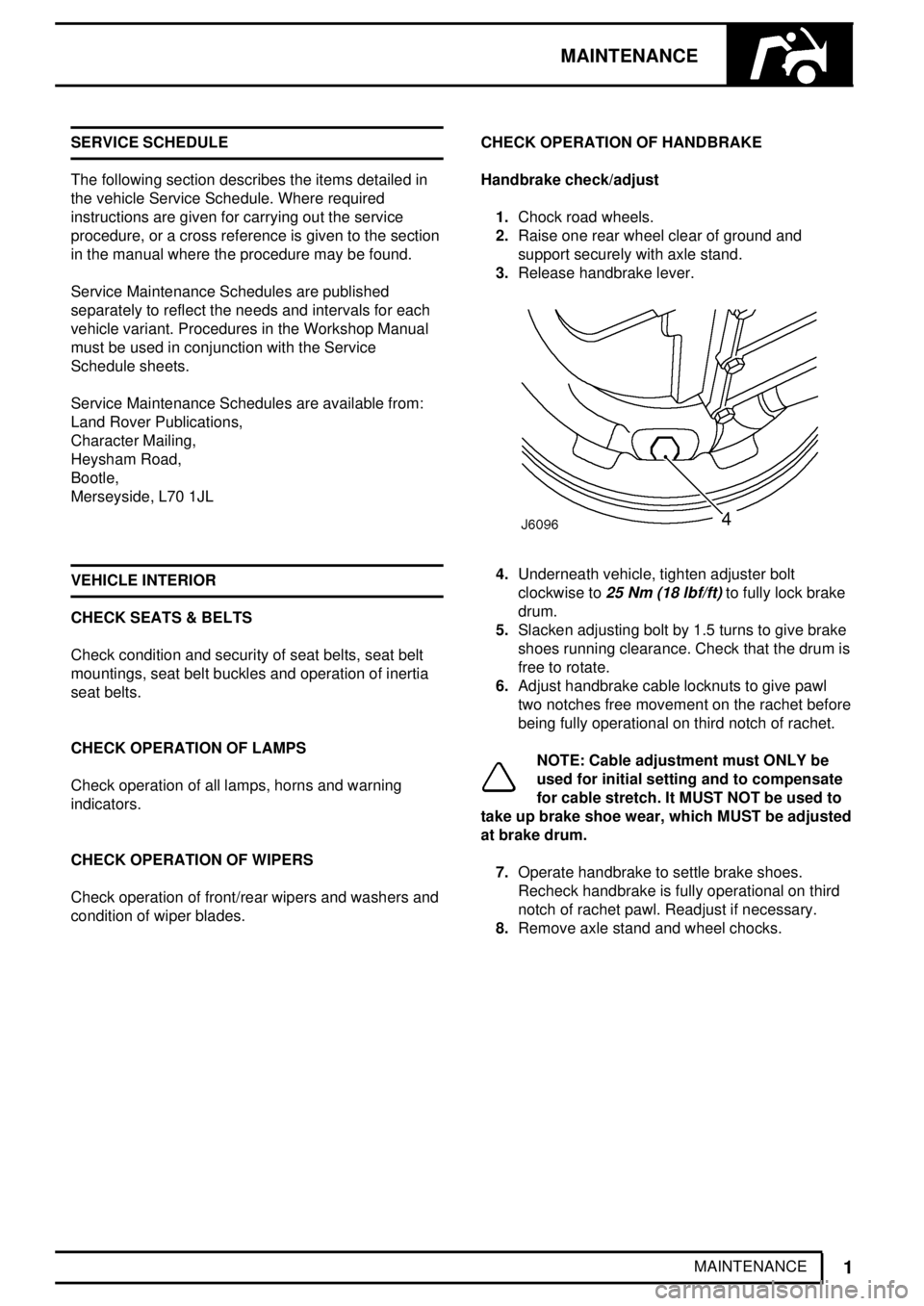
MAINTENANCE
1
MAINTENANCE SERVICE SCHEDULE
The following section describes the items detailed in
the vehicle Service Schedule. Where required
instructions are given for carrying out the service
procedure, or a cross reference is given to the section
in the manual where the procedure may be found.
Service Maintenance Schedules are published
separately to reflect the needs and intervals for each
vehicle variant. Procedures in the Workshop Manual
must be used in conjunction with the Service
Schedule sheets.
Service Maintenance Schedules are available from:
Land Rover Publications,
Character Mailing,
Heysham Road,
Bootle,
Merseyside, L70 1JL
VEHICLE INTERIOR
CHECK SEATS & BELTS
Check condition and security of seat belts, seat belt
mountings, seat belt buckles and operation of inertia
seat belts.
CHECK OPERATION OF LAMPS
Check operation of all lamps, horns and warning
indicators.
CHECK OPERATION OF WIPERS
Check operation of front/rear wipers and washers and
condition of wiper blades.CHECK OPERATION OF HANDBRAKE
Handbrake check/adjust
1.Chock road wheels.
2.Raise one rear wheel clear of ground and
support securely with axle stand.
3.Release handbrake lever.
4.Underneath vehicle, tighten adjuster bolt
clockwise to
25 Nm (18 lbf/ft)to fully lock brake
drum.
5.Slacken adjusting bolt by 1.5 turns to give brake
shoes running clearance. Check that the drum is
free to rotate.
6.Adjust handbrake cable locknuts to give pawl
two notches free movement on the rachet before
being fully operational on third notch of rachet.
NOTE: Cable adjustment must ONLY be
used for initial setting and to compensate
for cable stretch. It MUST NOT be used to
take up brake shoe wear, which MUST be adjusted
at brake drum.
7.Operate handbrake to settle brake shoes.
Recheck handbrake is fully operational on third
notch of rachet pawl. Readjust if necessary.
8.Remove axle stand and wheel chocks.
Page 56 of 455
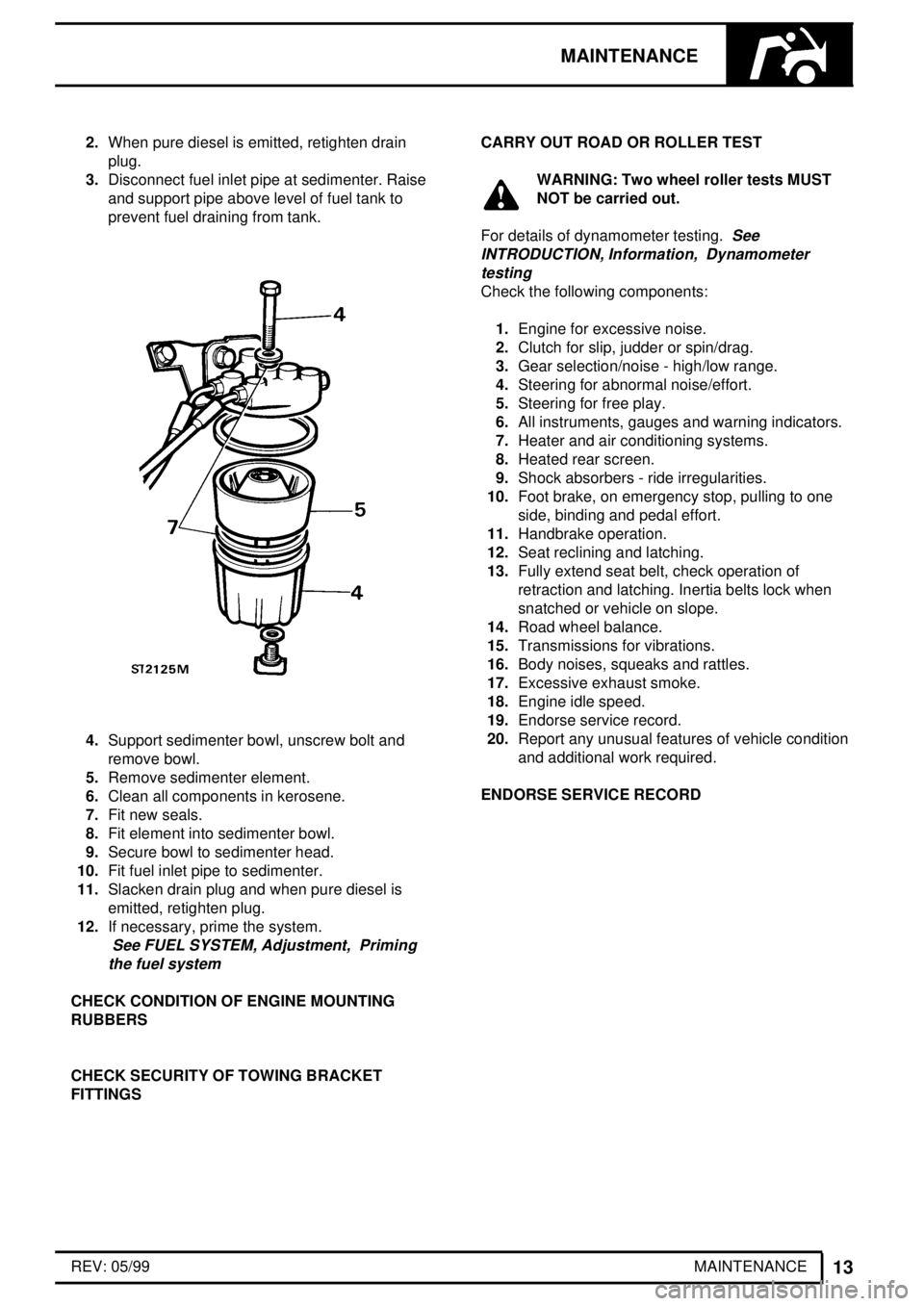
MAINTENANCE
13
MAINTENANCE REV: 05/992.When pure diesel is emitted, retighten drain
plug.
3.Disconnect fuel inlet pipe at sedimenter. Raise
and support pipe above level of fuel tank to
prevent fuel draining from tank.
4.Support sedimenter bowl, unscrew bolt and
remove bowl.
5.Remove sedimenter element.
6.Clean all components in kerosene.
7.Fit new seals.
8.Fit element into sedimenter bowl.
9.Secure bowl to sedimenter head.
10.Fit fuel inlet pipe to sedimenter.
11.Slacken drain plug and when pure diesel is
emitted, retighten plug.
12.If necessary, prime the system.
See FUEL SYSTEM, Adjustment, Priming
the fuel system
CHECK CONDITION OF ENGINE MOUNTING
RUBBERS
CHECK SECURITY OF TOWING BRACKET
FITTINGSCARRY OUT ROAD OR ROLLER TEST
WARNING: Two wheel roller tests MUST
NOT be carried out.
For details of dynamometer testing.
See
INTRODUCTION, Information, Dynamometer
testing
Check the following components:
1.Engine for excessive noise.
2.Clutch for slip, judder or spin/drag.
3.Gear selection/noise - high/low range.
4.Steering for abnormal noise/effort.
5.Steering for free play.
6.All instruments, gauges and warning indicators.
7.Heater and air conditioning systems.
8.Heated rear screen.
9.Shock absorbers - ride irregularities.
10.Foot brake, on emergency stop, pulling to one
side, binding and pedal effort.
11.Handbrake operation.
12.Seat reclining and latching.
13.Fully extend seat belt, check operation of
retraction and latching. Inertia belts lock when
snatched or vehicle on slope.
14.Road wheel balance.
15.Transmissions for vibrations.
16.Body noises, squeaks and rattles.
17.Excessive exhaust smoke.
18.Engine idle speed.
19.Endorse service record.
20.Report any unusual features of vehicle condition
and additional work required.
ENDORSE SERVICE RECORD
Page 74 of 455
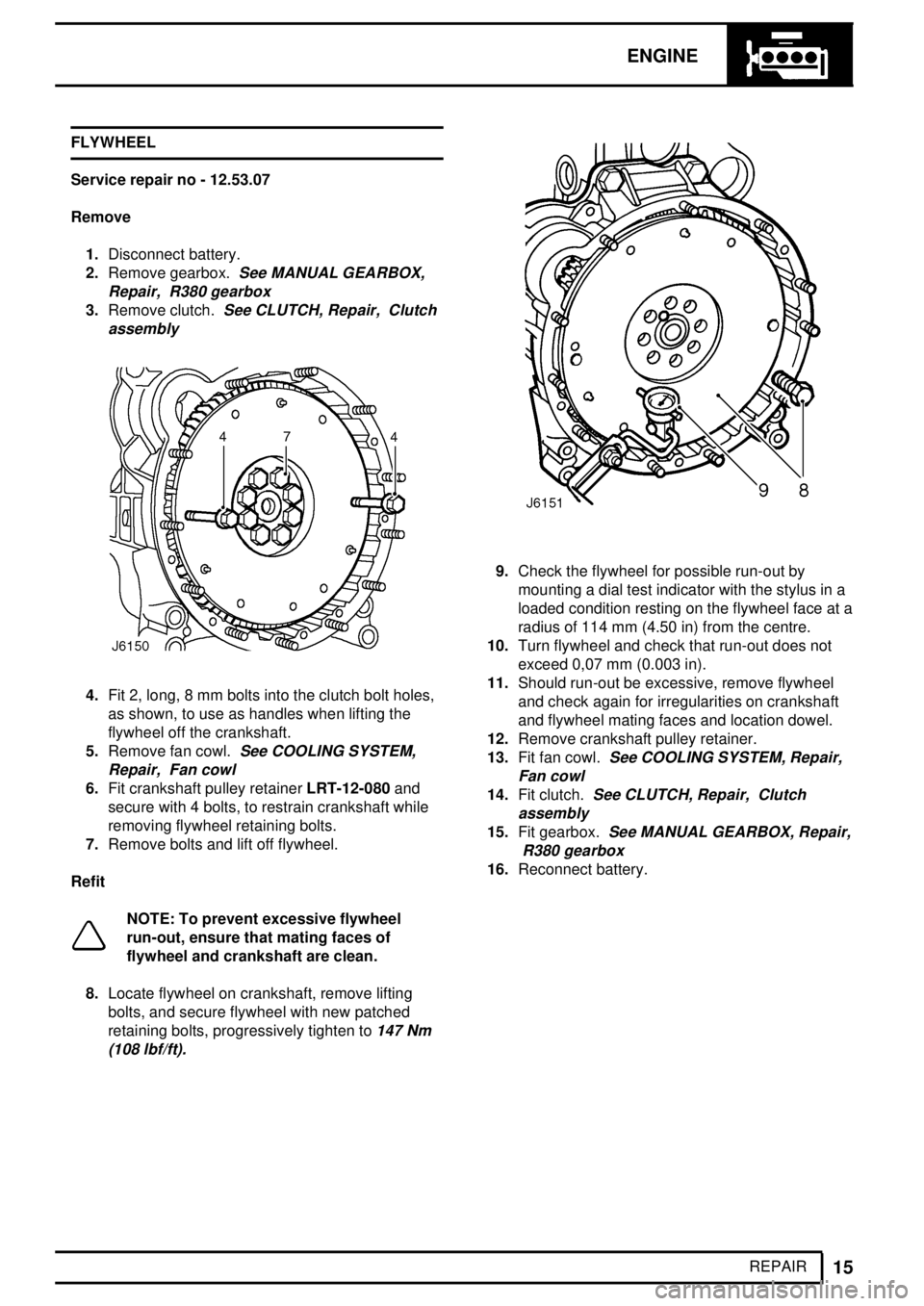
ENGINE
15
REPAIR FLYWHEEL
Service repair no - 12.53.07
Remove
1.Disconnect battery.
2.Remove gearbox.
See MANUAL GEARBOX,
Repair, R380 gearbox
3.Remove clutch.See CLUTCH, Repair, Clutch
assembly
4.Fit 2, long, 8 mm bolts into the clutch bolt holes,
as shown, to use as handles when lifting the
flywheel off the crankshaft.
5.Remove fan cowl.
See COOLING SYSTEM,
Repair, Fan cowl
6.Fit crankshaft pulley retainerLRT-12-080and
secure with 4 bolts, to restrain crankshaft while
removing flywheel retaining bolts.
7.Remove bolts and lift off flywheel.
Refit
NOTE: To prevent excessive flywheel
run-out, ensure that mating faces of
flywheel and crankshaft are clean.
8.Locate flywheel on crankshaft, remove lifting
bolts, and secure flywheel with new patched
retaining bolts, progressively tighten to
147 Nm
(108 lbf/ft).
9.Check the flywheel for possible run-out by
mounting a dial test indicator with the stylus in a
loaded condition resting on the flywheel face at a
radius of 114 mm (4.50 in) from the centre.
10.Turn flywheel and check that run-out does not
exceed 0,07 mm (0.003 in).
11.Should run-out be excessive, remove flywheel
and check again for irregularities on crankshaft
and flywheel mating faces and location dowel.
12.Remove crankshaft pulley retainer.
13.Fit fan cowl.
See COOLING SYSTEM, Repair,
Fan cowl
14.Fit clutch.See CLUTCH, Repair, Clutch
assembly
15.Fit gearbox.See MANUAL GEARBOX, Repair,
R380 gearbox
16.Reconnect battery.
Page 125 of 455
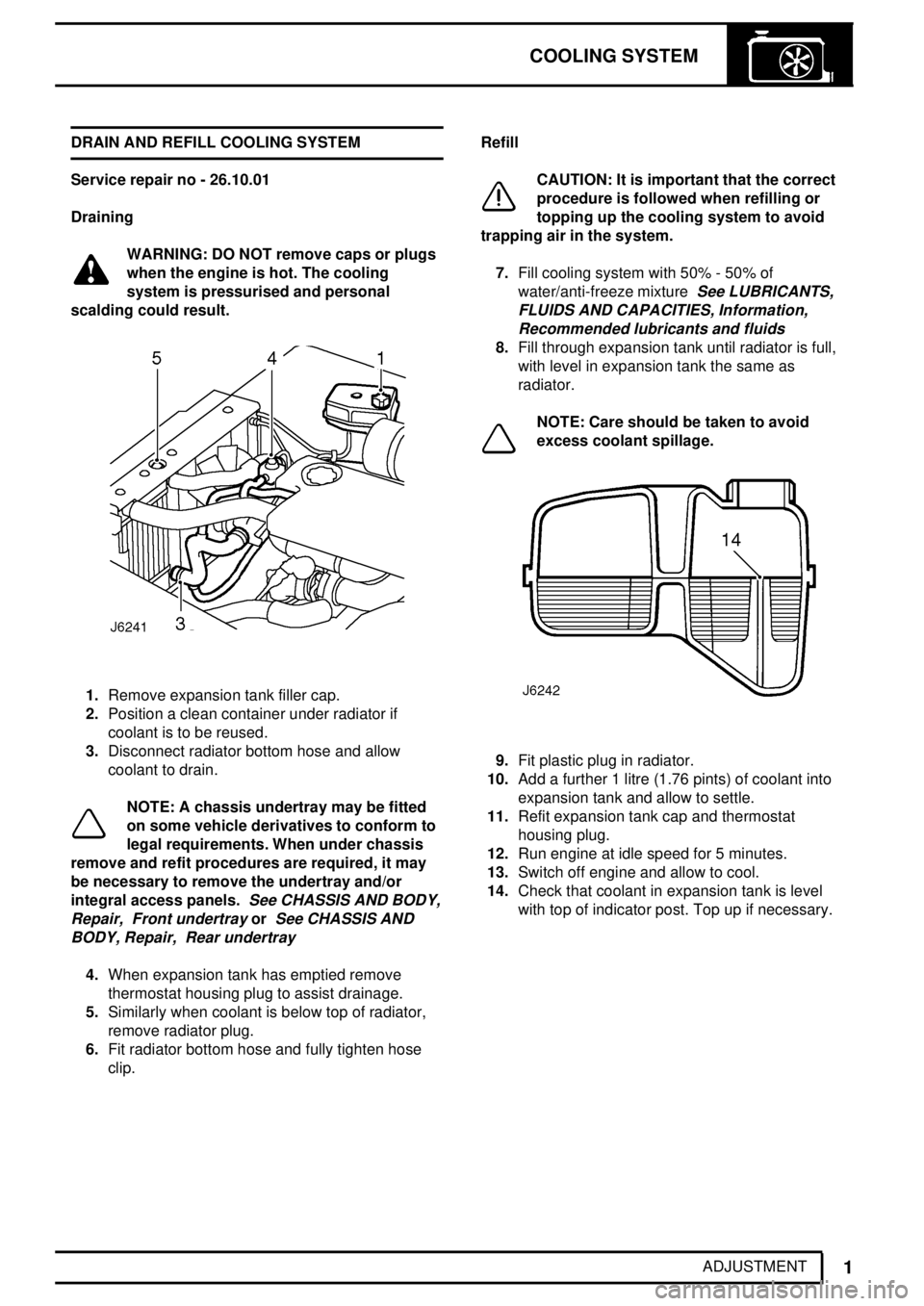
COOLING SYSTEM
1
ADJUSTMENT DRAIN AND REFILL COOLING SYSTEM
Service repair no - 26.10.01
Draining
WARNING: DO NOT remove caps or plugs
when the engine is hot. The cooling
system is pressurised and personal
scalding could result.
1.Remove expansion tank filler cap.
2.Position a clean container under radiator if
coolant is to be reused.
3.Disconnect radiator bottom hose and allow
coolant to drain.
NOTE: A chassis undertray may be fitted
on some vehicle derivatives to conform to
legal requirements. When under chassis
remove and refit procedures are required, it may
be necessary to remove the undertray and/or
integral access panels.
See CHASSIS AND BODY,
Repair, Front undertray
orSee CHASSIS AND
BODY, Repair, Rear undertray
4.When expansion tank has emptied remove
thermostat housing plug to assist drainage.
5.Similarly when coolant is below top of radiator,
remove radiator plug.
6.Fit radiator bottom hose and fully tighten hose
clip.Refill
CAUTION: It is important that the correct
procedure is followed when refilling or
topping up the cooling system to avoid
trapping air in the system.
7.Fill cooling system with 50% - 50% of
water/anti-freeze mixture
See LUBRICANTS,
FLUIDS AND CAPACITIES, Information,
Recommended lubricants and fluids
8.Fill through expansion tank until radiator is full,
with level in expansion tank the same as
radiator.
NOTE: Care should be taken to avoid
excess coolant spillage.
9.Fit plastic plug in radiator.
10.Add a further 1 litre (1.76 pints) of coolant into
expansion tank and allow to settle.
11.Refit expansion tank cap and thermostat
housing plug.
12.Run engine at idle speed for 5 minutes.
13.Switch off engine and allow to cool.
14.Check that coolant in expansion tank is level
with top of indicator post. Top up if necessary.
Page 240 of 455
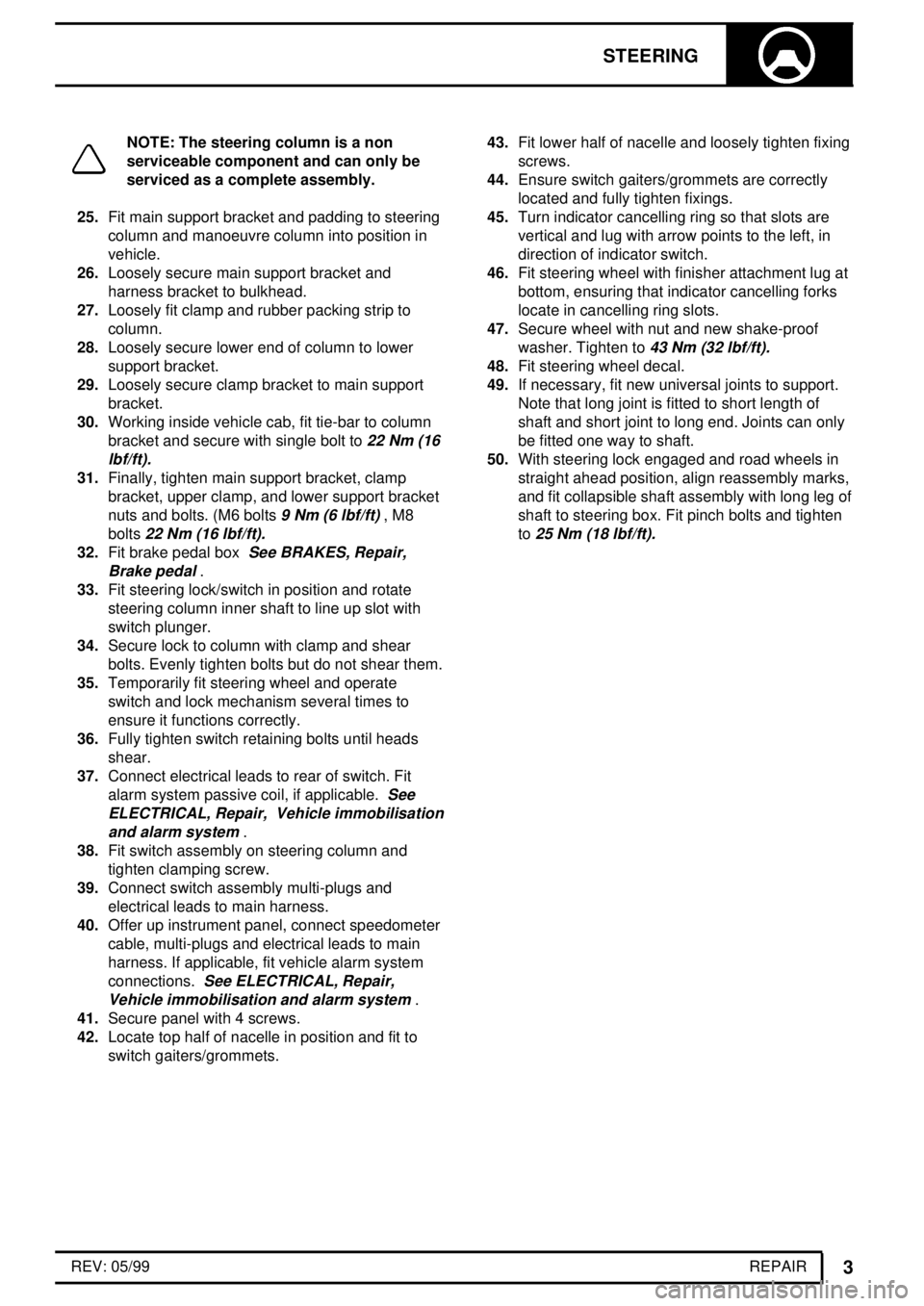
STEERING
3
REPAIR REV: 05/99
NOTE: The steering column is a non
serviceable component and can only be
serviced as a complete assembly.
25.Fit main support bracket and padding to steering
column and manoeuvre column into position in
vehicle.
26.Loosely secure main support bracket and
harness bracket to bulkhead.
27.Loosely fit clamp and rubber packing strip to
column.
28.Loosely secure lower end of column to lower
support bracket.
29.Loosely secure clamp bracket to main support
bracket.
30.Working inside vehicle cab, fit tie-bar to column
bracket and secure with single bolt to
22 Nm (16
lbf/ft).
31.Finally, tighten main support bracket, clamp
bracket, upper clamp, and lower support bracket
nuts and bolts. (M6 bolts
9 Nm (6 lbf/ft),M8
bolts
22 Nm (16 lbf/ft).
32.Fit brake pedal boxSee BRAKES, Repair,
Brake pedal
.
33.Fit steering lock/switch in position and rotate
steering column inner shaft to line up slot with
switch plunger.
34.Secure lock to column with clamp and shear
bolts. Evenly tighten bolts but do not shear them.
35.Temporarily fit steering wheel and operate
switch and lock mechanism several times to
ensure it functions correctly.
36.Fully tighten switch retaining bolts until heads
shear.
37.Connect electrical leads to rear of switch. Fit
alarm system passive coil, if applicable.
See
ELECTRICAL, Repair, Vehicle immobilisation
and alarm system
.
38.Fit switch assembly on steering column and
tighten clamping screw.
39.Connect switch assembly multi-plugs and
electrical leads to main harness.
40.Offer up instrument panel, connect speedometer
cable, multi-plugs and electrical leads to main
harness. If applicable, fit vehicle alarm system
connections.
See ELECTRICAL, Repair,
Vehicle immobilisation and alarm system
.
41.Secure panel with 4 screws.
42.Locate top half of nacelle in position and fit to
switch gaiters/grommets.43.Fit lower half of nacelle and loosely tighten fixing
screws.
44.Ensure switch gaiters/grommets are correctly
located and fully tighten fixings.
45.Turn indicator cancelling ring so that slots are
vertical and lug with arrow points to the left, in
direction of indicator switch.
46.Fit steering wheel with finisher attachment lug at
bottom, ensuring that indicator cancelling forks
locate in cancelling ring slots.
47.Secure wheel with nut and new shake-proof
washer. Tighten to
43 Nm (32 lbf/ft).
48.Fit steering wheel decal.
49.If necessary, fit new universal joints to support.
Note that long joint is fitted to short length of
shaft and short joint to long end. Joints can only
be fitted one way to shaft.
50.With steering lock engaged and road wheels in
straight ahead position, align reassembly marks,
and fit collapsible shaft assembly with long leg of
shaft to steering box. Fit pinch bolts and tighten
to
25 Nm (18 lbf/ft).
Page 245 of 455
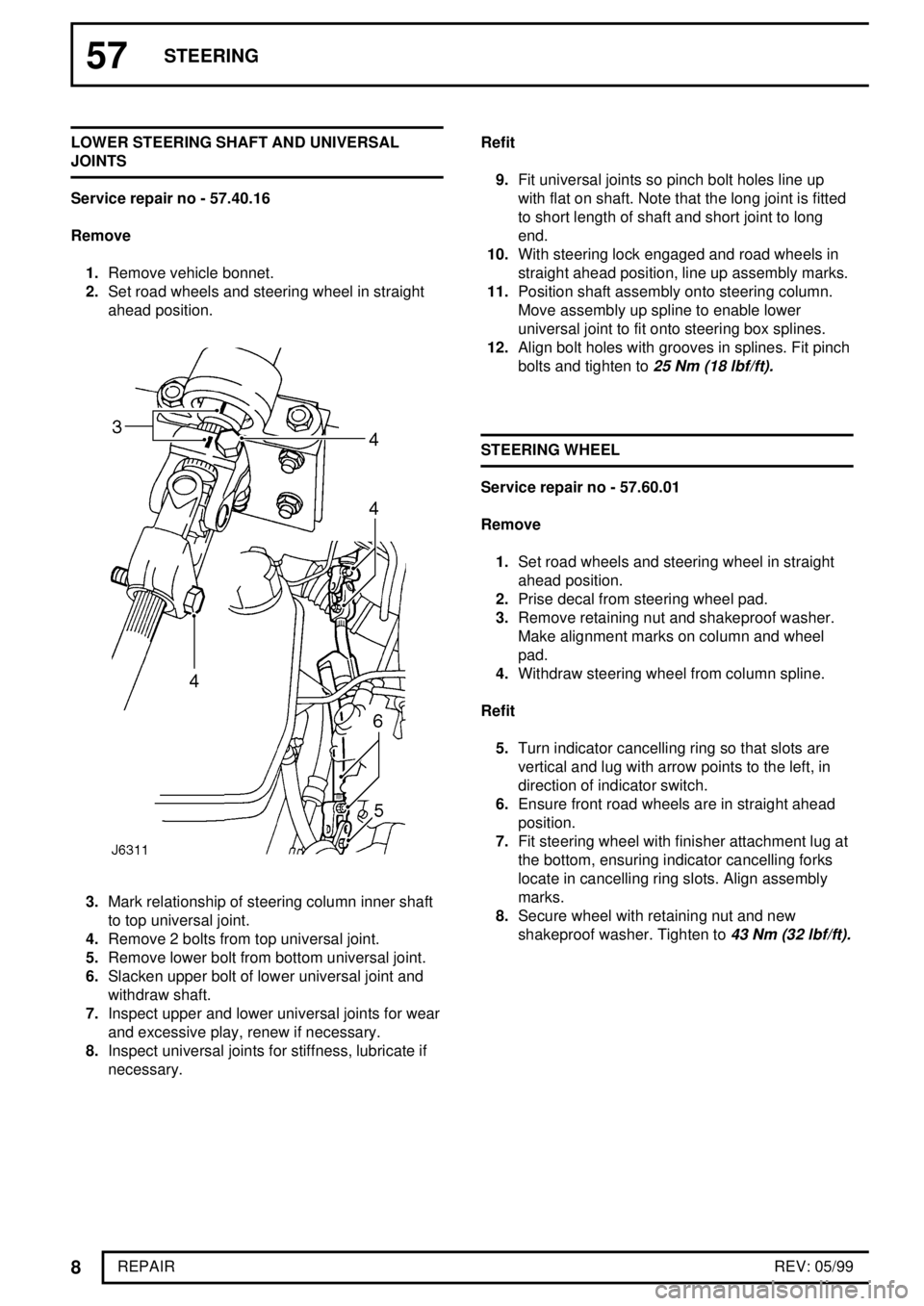
57STEERING
8
REPAIRREV: 05/99 LOWER STEERING SHAFT AND UNIVERSAL
JOINTS
Service repair no - 57.40.16
Remove
1.Remove vehicle bonnet.
2.Set road wheels and steering wheel in straight
ahead position.
3.Mark relationship of steering column inner shaft
to top universal joint.
4.Remove 2 bolts from top universal joint.
5.Remove lower bolt from bottom universal joint.
6.Slacken upper bolt of lower universal joint and
withdraw shaft.
7.Inspect upper and lower universal joints for wear
and excessive play, renew if necessary.
8.Inspect universal joints for stiffness, lubricate if
necessary.Refit
9.Fit universal joints so pinch bolt holes line up
with flat on shaft. Note that the long joint is fitted
to short length of shaft and short joint to long
end.
10.With steering lock engaged and road wheels in
straight ahead position, line up assembly marks.
11.Position shaft assembly onto steering column.
Move assembly up spline to enable lower
universal joint to fit onto steering box splines.
12.Align bolt holes with grooves in splines. Fit pinch
bolts and tighten to
25 Nm (18 lbf/ft).
STEERING WHEEL
Service repair no - 57.60.01
Remove
1.Set road wheels and steering wheel in straight
ahead position.
2.Prise decal from steering wheel pad.
3.Remove retaining nut and shakeproof washer.
Make alignment marks on column and wheel
pad.
4.Withdraw steering wheel from column spline.
Refit
5.Turn indicator cancelling ring so that slots are
vertical and lug with arrow points to the left, in
direction of indicator switch.
6.Ensure front road wheels are in straight ahead
position.
7.Fit steering wheel with finisher attachment lug at
the bottom, ensuring indicator cancelling forks
locate in cancelling ring slots. Align assembly
marks.
8.Secure wheel with retaining nut and new
shakeproof washer. Tighten to
43 Nm (32 lbf/ft).
Page 292 of 455
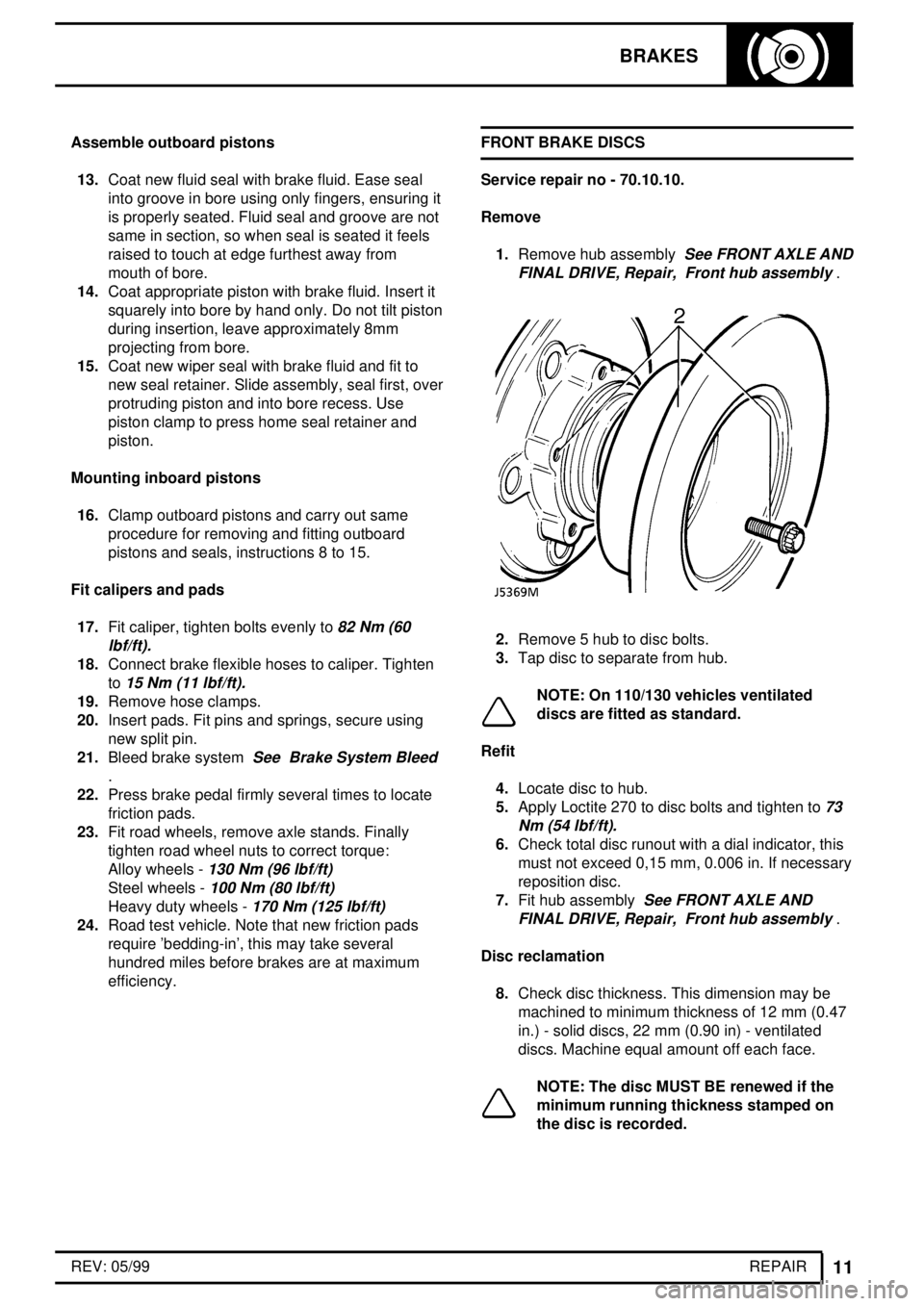
BRAKES
11
REPAIR REV: 05/99 Assemble outboard pistons
13.Coat new fluid seal with brake fluid. Ease seal
into groove in bore using only fingers, ensuring it
is properly seated. Fluid seal and groove are not
same in section, so when seal is seated it feels
raised to touch at edge furthest away from
mouth of bore.
14.Coat appropriate piston with brake fluid. Insert it
squarely into bore by hand only. Do not tilt piston
during insertion, leave approximately 8mm
projecting from bore.
15.Coat new wiper seal with brake fluid and fit to
new seal retainer. Slide assembly, seal first, over
protruding piston and into bore recess. Use
piston clamp to press home seal retainer and
piston.
Mounting inboard pistons
16.Clamp outboard pistons and carry out same
procedure for removing and fitting outboard
pistons and seals, instructions 8 to 15.
Fit calipers and pads
17.Fit caliper, tighten bolts evenly to
82 Nm (60
lbf/ft).
18.Connect brake flexible hoses to caliper. Tighten
to
15 Nm (11 lbf/ft).
19.Remove hose clamps.
20.Insert pads. Fit pins and springs, secure using
new split pin.
21.Bleed brake system
See Brake System Bleed
.
22.Press brake pedal firmly several times to locate
friction pads.
23.Fit road wheels, remove axle stands. Finally
tighten road wheel nuts to correct torque:
Alloy wheels -
130 Nm (96 lbf/ft)
Steel wheels -100 Nm (80 lbf/ft)
Heavy duty wheels -170 Nm (125 lbf/ft)
24.Road test vehicle. Note that new friction pads
require 'bedding-in', this may take several
hundred miles before brakes are at maximum
efficiency.FRONT BRAKE DISCS
Service repair no - 70.10.10.
Remove
1.Remove hub assembly
See FRONT AXLE AND
FINAL DRIVE, Repair, Front hub assembly
.
2.Remove 5 hub to disc bolts.
3.Tap disc to separate from hub.
NOTE: On 110/130 vehicles ventilated
discs are fitted as standard.
Refit
4.Locate disc to hub.
5.Apply Loctite 270 to disc bolts and tighten to
73
Nm (54 lbf/ft).
6.Check total disc runout with a dial indicator, this
must not exceed 0,15 mm, 0.006 in. If necessary
reposition disc.
7.Fit hub assembly
See FRONT AXLE AND
FINAL DRIVE, Repair, Front hub assembly
.
Disc reclamation
8.Check disc thickness. This dimension may be
machined to minimum thickness of 12 mm (0.47
in.) - solid discs, 22 mm (0.90 in) - ventilated
discs. Machine equal amount off each face.
NOTE: The disc MUST BE renewed if the
minimum running thickness stamped on
the disc is recorded.
Page 311 of 455
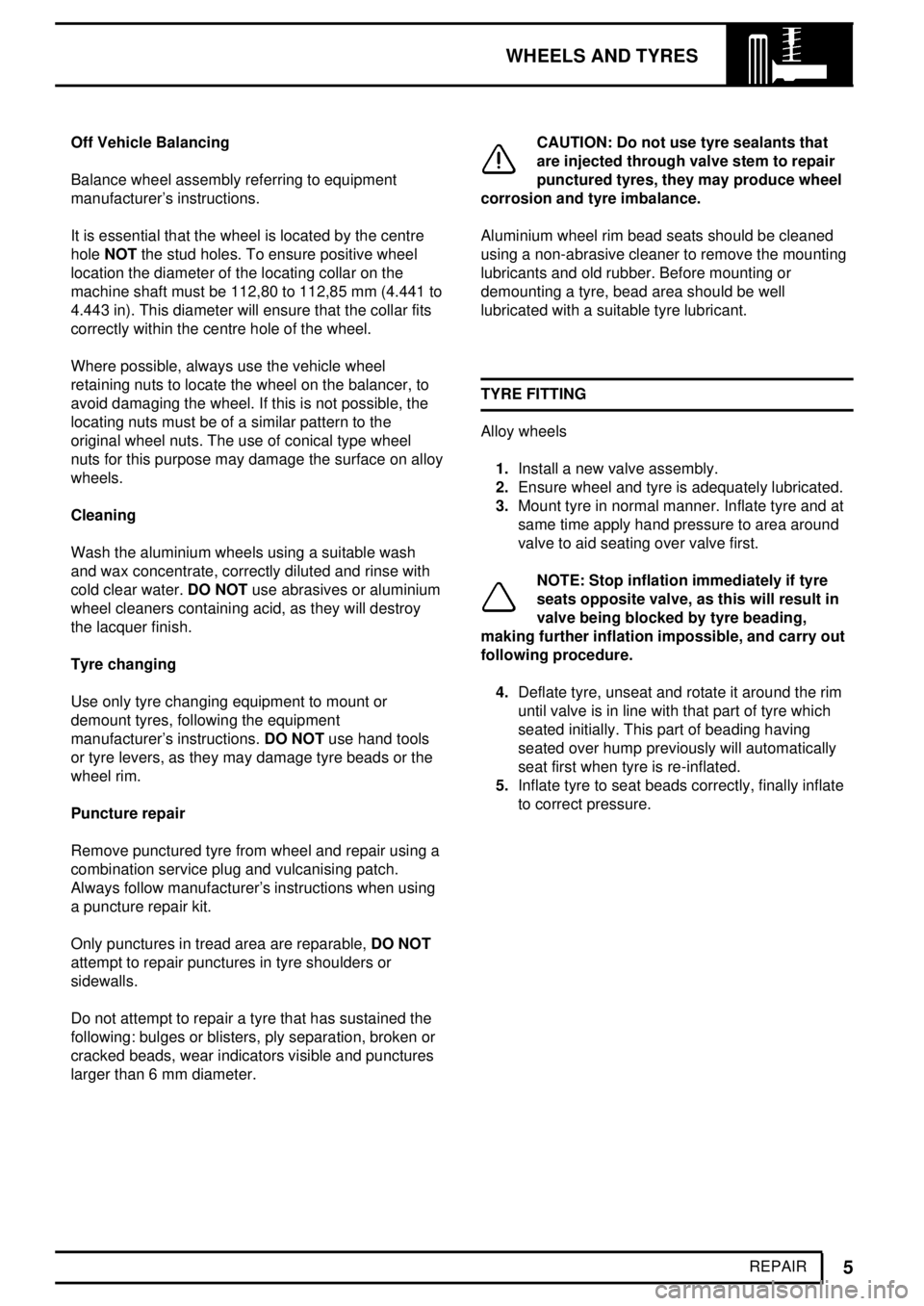
WHEELS AND TYRES
5
REPAIR Off Vehicle Balancing
Balance wheel assembly referring to equipment
manufacturer's instructions.
It is essential that the wheel is located by the centre
holeNOTthe stud holes. To ensure positive wheel
location the diameter of the locating collar on the
machine shaft must be 112,80 to 112,85 mm (4.441 to
4.443 in). This diameter will ensure that the collar fits
correctly within the centre hole of the wheel.
Where possible, always use the vehicle wheel
retaining nuts to locate the wheel on the balancer, to
avoid damaging the wheel. If this is not possible, the
locating nuts must be of a similar pattern to the
original wheel nuts. The use of conical type wheel
nuts for this purpose may damage the surface on alloy
wheels.
Cleaning
Wash the aluminium wheels using a suitable wash
and wax concentrate, correctly diluted and rinse with
cold clear water.DO NOTuse abrasives or aluminium
wheel cleaners containing acid, as they will destroy
the lacquer finish.
Tyre changing
Use only tyre changing equipment to mount or
demount tyres, following the equipment
manufacturer's instructions.DO NOTuse hand tools
or tyre levers, as they may damage tyre beads or the
wheel rim.
Puncture repair
Remove punctured tyre from wheel and repair using a
combination service plug and vulcanising patch.
Always follow manufacturer's instructions when using
a puncture repair kit.
Only punctures in tread area are reparable,DO NOT
attempt to repair punctures in tyre shoulders or
sidewalls.
Do not attempt to repair a tyre that has sustained the
following: bulges or blisters, ply separation, broken or
cracked beads, wear indicators visible and punctures
larger than 6 mm diameter.
CAUTION: Do not use tyre sealants that
are injected through valve stem to repair
punctured tyres, they may produce wheel
corrosion and tyre imbalance.
Aluminium wheel rim bead seats should be cleaned
using a non-abrasive cleaner to remove the mounting
lubricants and old rubber. Before mounting or
demounting a tyre, bead area should be well
lubricated with a suitable tyre lubricant.
TYRE FITTING
Alloy wheels
1.Install a new valve assembly.
2.Ensure wheel and tyre is adequately lubricated.
3.Mount tyre in normal manner. Inflate tyre and at
same time apply hand pressure to area around
valve to aid seating over valve first.
NOTE: Stop inflation immediately if tyre
seats opposite valve, as this will result in
valve being blocked by tyre beading,
making further inflation impossible, and carry out
following procedure.
4.Deflate tyre, unseat and rotate it around the rim
until valve is in line with that part of tyre which
seated initially. This part of beading having
seated over hump previously will automatically
seat first when tyre is re-inflated.
5.Inflate tyre to seat beads correctly, finally inflate
to correct pressure.
Page 413 of 455
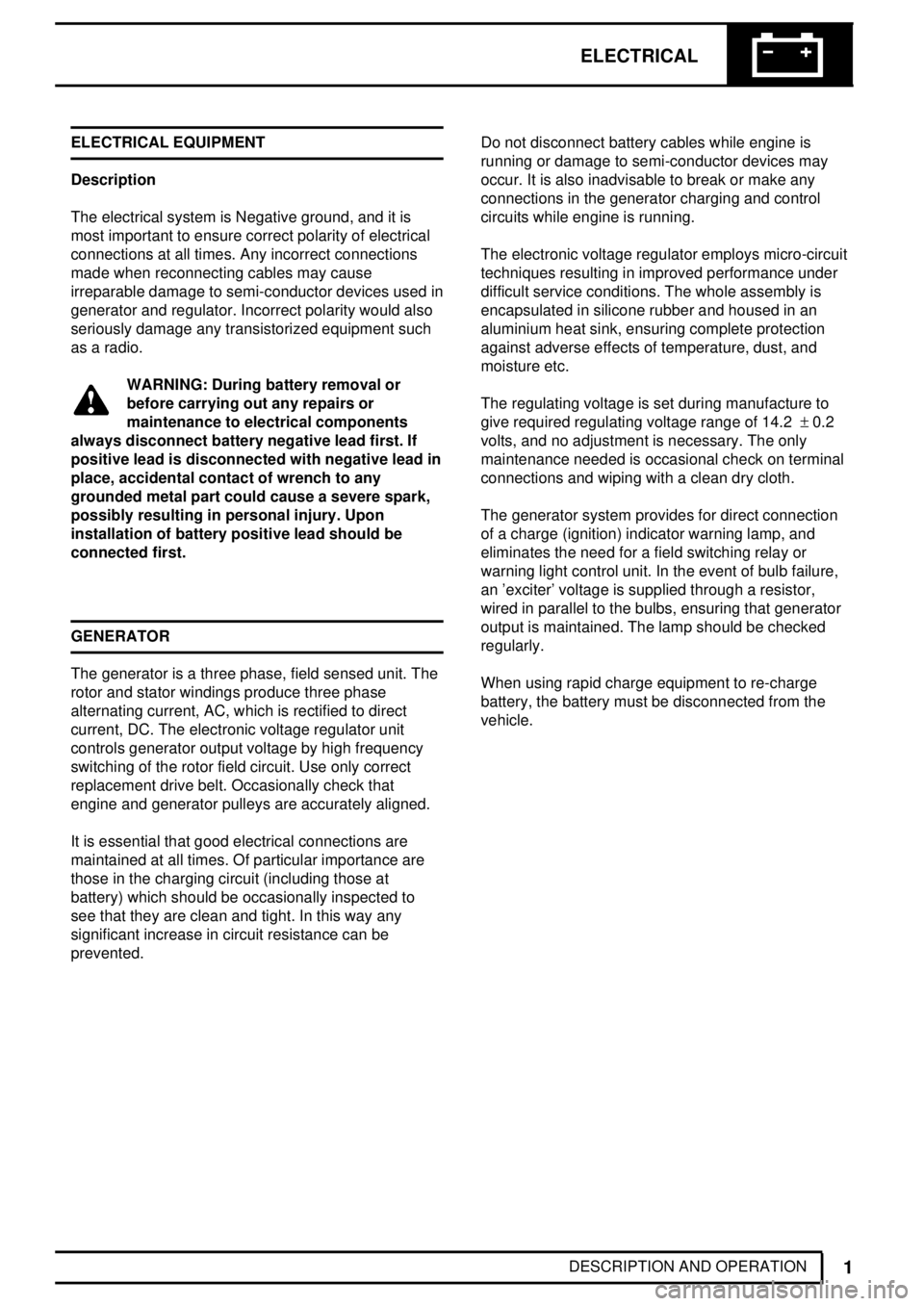
ELECTRICAL
1
DESCRIPTION AND OPERATION ELECTRICAL EQUIPMENT
Description
The electrical system is Negative ground, and it is
most important to ensure correct polarity of electrical
connections at all times. Any incorrect connections
made when reconnecting cables may cause
irreparable damage to semi-conductor devices used in
generator and regulator. Incorrect polarity would also
seriously damage any transistorized equipment such
as a radio.
WARNING: During battery removal or
before carrying out any repairs or
maintenance to electrical components
always disconnect battery negative lead first. If
positive lead is disconnected with negative lead in
place, accidental contact of wrench to any
grounded metal part could cause a severe spark,
possibly resulting in personal injury. Upon
installation of battery positive lead should be
connected first.
GENERATOR
The generator is a three phase, field sensed unit. The
rotor and stator windings produce three phase
alternating current, AC, which is rectified to direct
current, DC. The electronic voltage regulator unit
controls generator output voltage by high frequency
switching of the rotor field circuit. Use only correct
replacement drive belt. Occasionally check that
engine and generator pulleys are accurately aligned.
It is essential that good electrical connections are
maintained at all times. Of particular importance are
those in the charging circuit (including those at
battery) which should be occasionally inspected to
see that they are clean and tight. In this way any
significant increase in circuit resistance can be
prevented.Do not disconnect battery cables while engine is
running or damage to semi-conductor devices may
occur. It is also inadvisable to break or make any
connections in the generator charging and control
circuits while engine is running.
The electronic voltage regulator employs micro-circuit
techniques resulting in improved performance under
difficult service conditions. The whole assembly is
encapsulated in silicone rubber and housed in an
aluminium heat sink, ensuring complete protection
against adverse effects of temperature, dust, and
moisture etc.
The regulating voltage is set during manufacture to
give required regulating voltage range of 14.2±0.2
volts, and no adjustment is necessary. The only
maintenance needed is occasional check on terminal
connections and wiping with a clean dry cloth.
The generator system provides for direct connection
of a charge (ignition) indicator warning lamp, and
eliminates the need for a field switching relay or
warning light control unit. In the event of bulb failure,
an 'exciter' voltage is supplied through a resistor,
wired in parallel to the bulbs, ensuring that generator
output is maintained. The lamp should be checked
regularly.
When using rapid charge equipment to re-charge
battery, the battery must be disconnected from the
vehicle.
Page 434 of 455
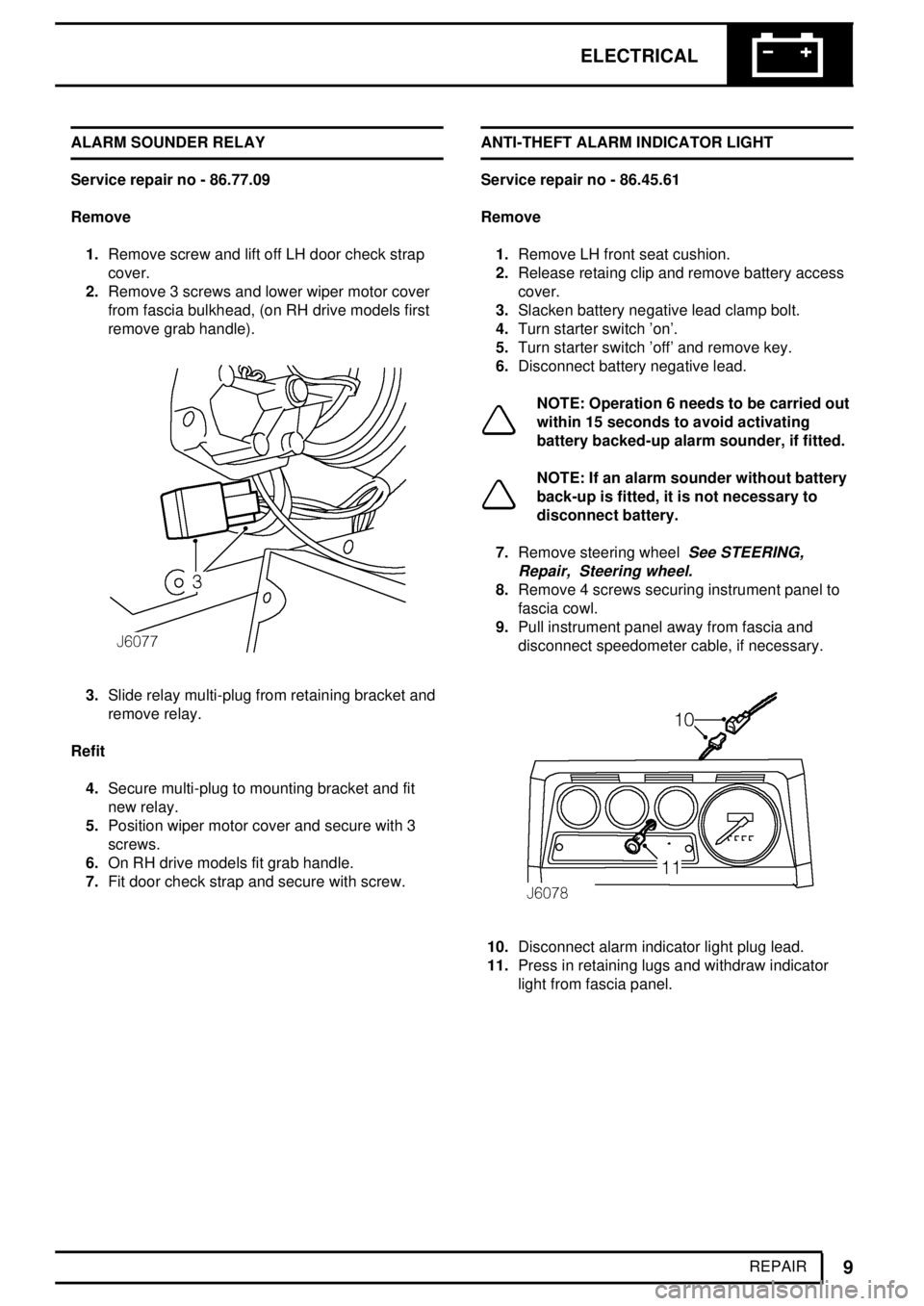
ELECTRICAL
9
REPAIR ALARM SOUNDER RELAY
Service repair no - 86.77.09
Remove
1.Remove screw and lift off LH door check strap
cover.
2.Remove 3 screws and lower wiper motor cover
from fascia bulkhead, (on RH drive models first
remove grab handle).
3.Slide relay multi-plug from retaining bracket and
remove relay.
Refit
4.Secure multi-plug to mounting bracket and fit
new relay.
5.Position wiper motor cover and secure with 3
screws.
6.On RH drive models fit grab handle.
7.Fit door check strap and secure with screw.ANTI-THEFT ALARM INDICATOR LIGHT
Service repair no - 86.45.61
Remove
1.Remove LH front seat cushion.
2.Release retaing clip and remove battery access
cover.
3.Slacken battery negative lead clamp bolt.
4.Turn starter switch 'on'.
5.Turn starter switch 'off' and remove key.
6.Disconnect battery negative lead.
NOTE: Operation 6 needs to be carried out
within 15 seconds to avoid activating
battery backed-up alarm sounder, if fitted.
NOTE: If an alarm sounder without battery
back-up is fitted, it is not necessary to
disconnect battery.
7.Remove steering wheel
See STEERING,
Repair, Steering wheel.
8.Remove 4 screws securing instrument panel to
fascia cowl.
9.Pull instrument panel away from fascia and
disconnect speedometer cable, if necessary.
10.Disconnect alarm indicator light plug lead.
11.Press in retaining lugs and withdraw indicator
light from fascia panel.