LAND ROVER DEFENDER 1999 Workshop Manual
Manufacturer: LAND ROVER, Model Year: 1999, Model line: DEFENDER, Model: LAND ROVER DEFENDER 1999Pages: 667, PDF Size: 8.76 MB
Page 191 of 667
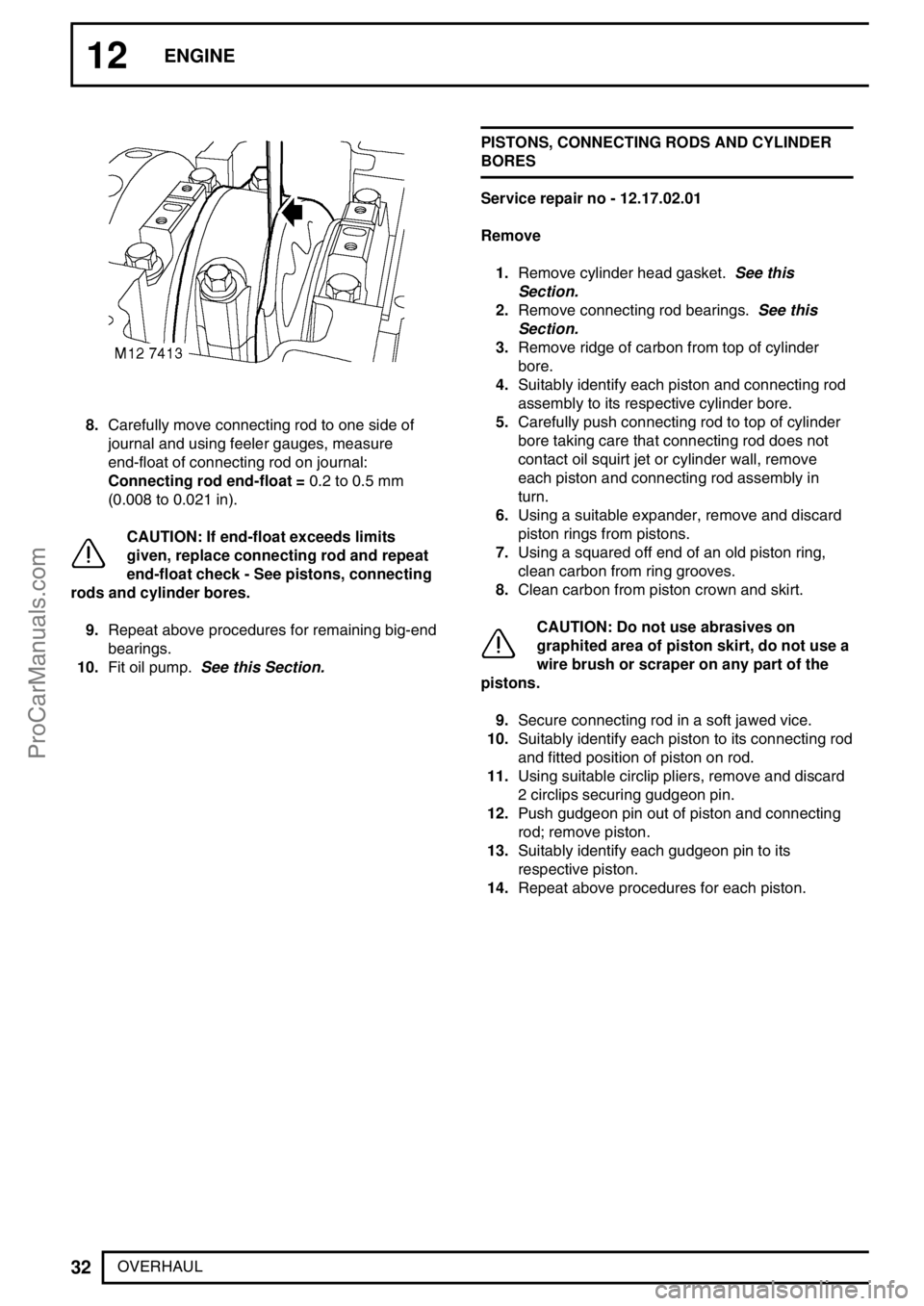
12ENGINE
32
OVERHAUL
8.Carefully move connecting rod to one side of
journal and using feeler gauges, measure
end-float of connecting rod on journal:
Connecting rod end-float =0.2 to 0.5 mm
(0.008 to 0.021 in).
CAUTION: If end-float exceeds limits
given, replace connecting rod and repeat
end-float check - See pistons, connecting
rods and cylinder bores.
9.Repeat above procedures for remaining big-end
bearings.
10.Fit oil pump.See this Section.PISTONS, CONNECTING RODS AND CYLINDER
BORES
Service repair no - 12.17.02.01
Remove
1.Remove cylinder head gasket.See this
Section.
2.Remove connecting rod bearings.See this
Section.
3.Remove ridge of carbon from top of cylinder
bore.
4.Suitably identify each piston and connecting rod
assembly to its respective cylinder bore.
5.Carefully push connecting rod to top of cylinder
bore taking care that connecting rod does not
contact oil squirt jet or cylinder wall, remove
each piston and connecting rod assembly in
turn.
6.Using a suitable expander, remove and discard
piston rings from pistons.
7.Using a squared off end of an old piston ring,
clean carbon from ring grooves.
8.Clean carbon from piston crown and skirt.
CAUTION: Do not use abrasives on
graphited area of piston skirt, do not use a
wire brush or scraper on any part of the
pistons.
9.Secure connecting rod in a soft jawed vice.
10.Suitably identify each piston to its connecting rod
and fitted position of piston on rod.
11.Using suitable circlip pliers, remove and discard
2 circlips securing gudgeon pin.
12.Push gudgeon pin out of piston and connecting
rod; remove piston.
13.Suitably identify each gudgeon pin to its
respective piston.
14.Repeat above procedures for each piston.
ProCarManuals.com
Page 192 of 667
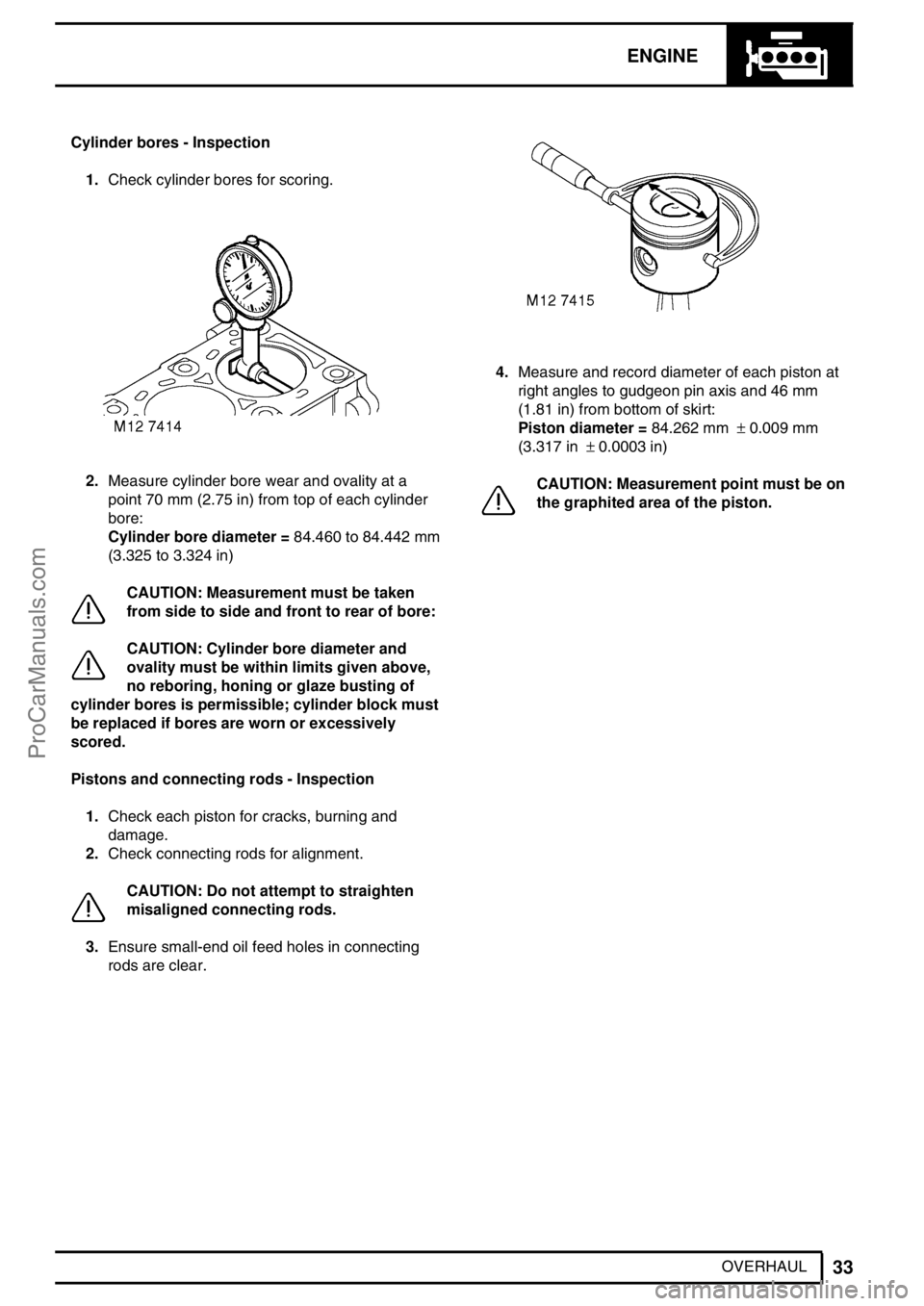
ENGINE
33
OVERHAUL Cylinder bores - Inspection
1.Check cylinder bores for scoring.
2.Measure cylinder bore wear and ovality at a
point 70 mm (2.75 in) from top of each cylinder
bore:
Cylinder bore diameter =84.460 to 84.442 mm
(3.325 to 3.324 in)
CAUTION: Measurement must be taken
from side to side and front to rear of bore:
CAUTION: Cylinder bore diameter and
ovality must be within limits given above,
no reboring, honing or glaze busting of
cylinder bores is permissible; cylinder block must
be replaced if bores are worn or excessively
scored.
Pistons and connecting rods - Inspection
1.Check each piston for cracks, burning and
damage.
2.Check connecting rods for alignment.
CAUTION: Do not attempt to straighten
misaligned connecting rods.
3.Ensure small-end oil feed holes in connecting
rods are clear.
4.Measure and record diameter of each piston at
right angles to gudgeon pin axis and 46 mm
(1.81 in) from bottom of skirt:
Piston diameter =84.262 mm±0.009 mm
(3.317 in±0.0003 in)
CAUTION: Measurement point must be on
the graphited area of the piston.
ProCarManuals.com
Page 193 of 667
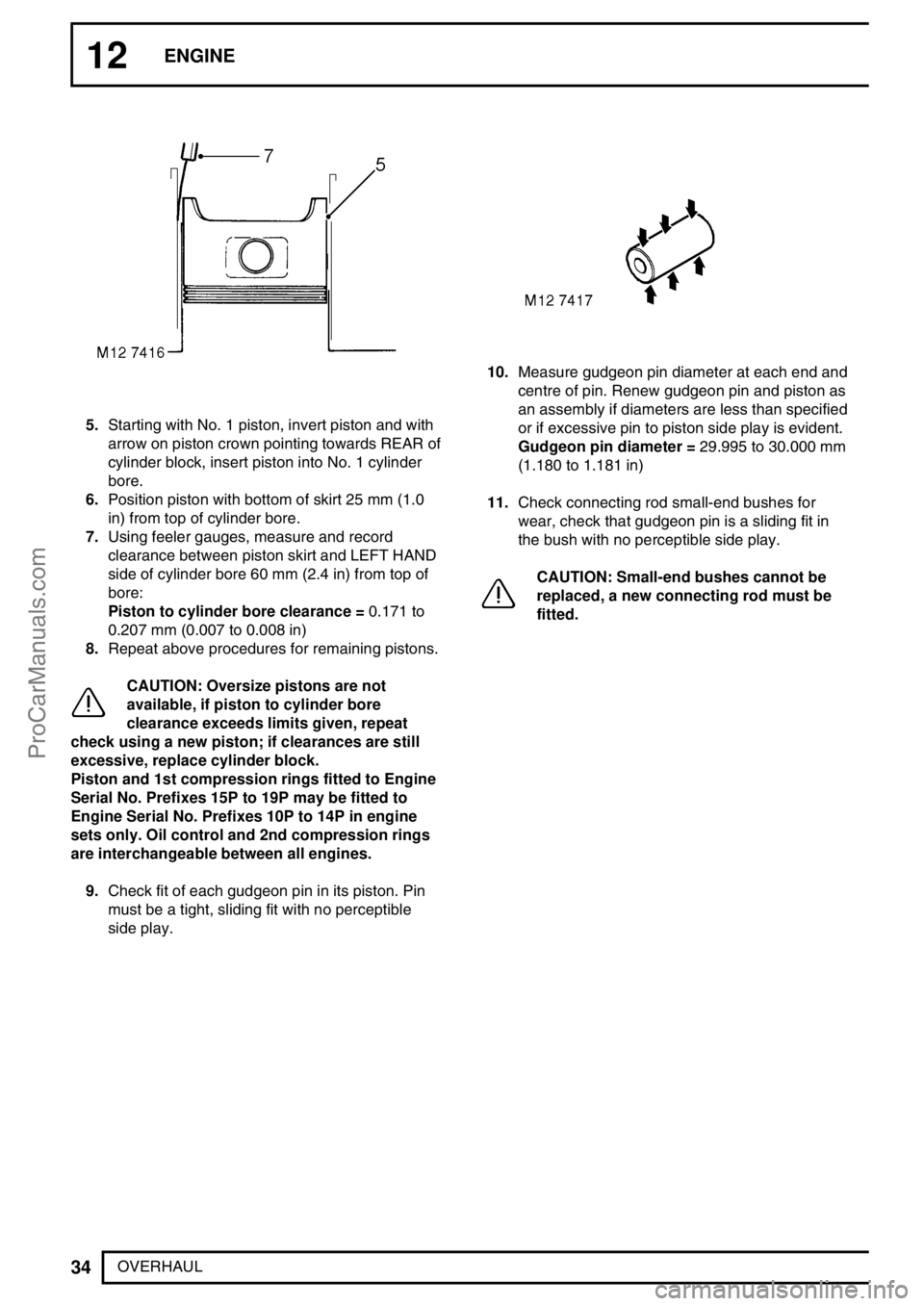
12ENGINE
34
OVERHAUL
5.Starting with No. 1 piston, invert piston and with
arrow on piston crown pointing towards REAR of
cylinder block, insert piston into No. 1 cylinder
bore.
6.Position piston with bottom of skirt 25 mm (1.0
in) from top of cylinder bore.
7.Using feeler gauges, measure and record
clearance between piston skirt and LEFT HAND
side of cylinder bore 60 mm (2.4 in) from top of
bore:
Piston to cylinder bore clearance =0.171 to
0.207 mm (0.007 to 0.008 in)
8.Repeat above procedures for remaining pistons.
CAUTION: Oversize pistons are not
available, if piston to cylinder bore
clearance exceeds limits given, repeat
check using a new piston; if clearances are still
excessive, replace cylinder block.
Piston and 1st compression rings fitted to Engine
Serial No. Prefixes 15P to 19P may be fitted to
Engine Serial No. Prefixes 10P to 14P in engine
sets only. Oil control and 2nd compression rings
are interchangeable between all engines.
9.Check fit of each gudgeon pin in its piston. Pin
must be a tight, sliding fit with no perceptible
side play.
10.Measure gudgeon pin diameter at each end and
centre of pin. Renew gudgeon pin and piston as
an assembly if diameters are less than specified
or if excessive pin to piston side play is evident.
Gudgeon pin diameter =29.995 to 30.000 mm
(1.180 to 1.181 in)
11.Check connecting rod small-end bushes for
wear, check that gudgeon pin is a sliding fit in
the bush with no perceptible side play.
CAUTION: Small-end bushes cannot be
replaced, a new connecting rod must be
fitted.
ProCarManuals.com
Page 194 of 667

ENGINE
35
OVERHAUL Piston ring gaps - Checking
1.Insert new compression and oil control piston
rings in turn into No. 1 cylinder bore 30 mm (1.25
in) from top of bore and check ring fitted gaps;
ensure rings are kept square to bore when
checking gaps.
1st compression ring fitted gap =0.30 to 0.40
mm (0.012 to 0.016 in)
2nd compression ring fitted gap =0.40 to 0.60
mm (0.016 to 0.024 in)
Oil control ring fitted gap =0.25 to 0.50 mm
(0.01 to 0.02 in)
Repeat for each cylinder bore in turn.
CAUTION: Ensure rings are suitably
identified with the cylinder bore in which
they were checked and are fitted to the
piston for that bore.
2.Fit oil control expander and ring to piston.
3.Fit 2nd compression ring with’TOP’marking
upwards.
4.Fit 1st compression ring with’TOP’marking
upwards.
5.Check piston ring to groove clearance:
1st compression ring -Not measured
2nd compression ring =0.050 to 0.082 mm
(0.02 to 0.003 in)
Oil control ring =0.050 to 0.082 mm (0.02 to
0.003 in)
Pistons and connecting rods - Assembling
1.Lubricate gudgeon pin, gudgeon pin holes in
piston and small-end bush with engine oil.
2.Position piston to its respective connecting rod
with arrow on piston crown on the same side as
the cast boss on the connecting rod.
3.Fit gudgeon pin to its respective piston and
connecting rod; secure with new circlips.
CAUTION: Ensure circlips are fully seated
in their grooves.
4.Repeat above procedures for remaining pistons.
5.Lubricate piston rings and cylinder bores with
engine oil.
6.Check that rings are free to rotate, position ring
gaps at 120°to each other and away from the
thrust - LH side of piston - viewed from front of
piston.
7.Using a suitable piston ring clamp, compress
piston rings.
8.Insert connecting rod and piston into its
respective cylinder bore, ensuring that the arrow
on piston crown and the cast boss on connecting
rod are facing towards the front of the cylinder
block.
CAUTION: Ensure that connecting rod
does not contact cylinder bore or oil squirt
jet. Do not pull connecting rod fully down
cylinder bore at this stage.
ProCarManuals.com
Page 195 of 667
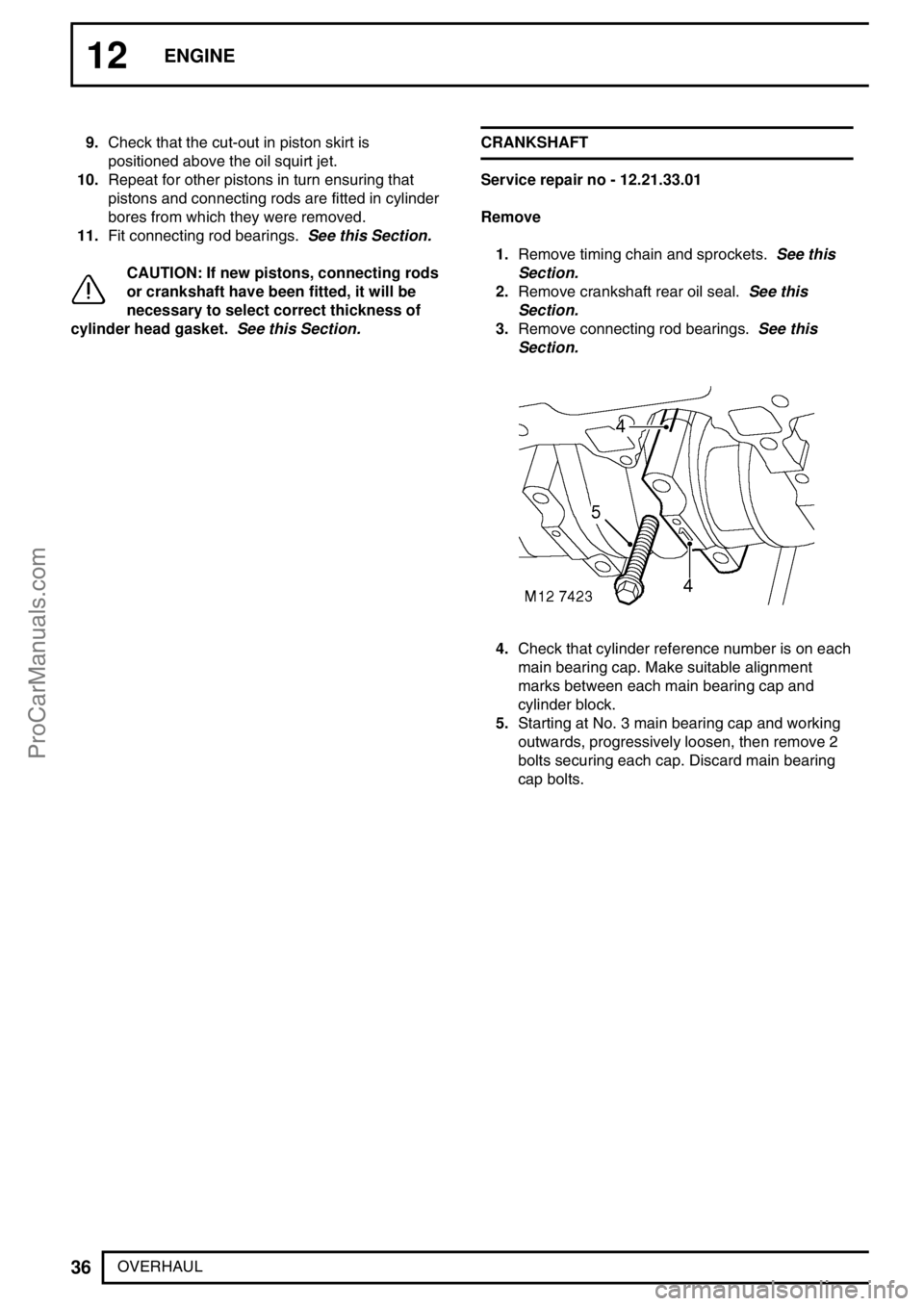
12ENGINE
36
OVERHAUL 9.Check that the cut-out in piston skirt is
positioned above the oil squirt jet.
10.Repeat for other pistons in turn ensuring that
pistons and connecting rods are fitted in cylinder
bores from which they were removed.
11.Fit connecting rod bearings.See this Section.
CAUTION: If new pistons, connecting rods
or crankshaft have been fitted, it will be
necessary to select correct thickness of
cylinder head gasket.See this Section.CRANKSHAFT
Service repair no - 12.21.33.01
Remove
1.Remove timing chain and sprockets.See this
Section.
2.Remove crankshaft rear oil seal.See this
Section.
3.Remove connecting rod bearings.See this
Section.
4.Check that cylinder reference number is on each
main bearing cap. Make suitable alignment
marks between each main bearing cap and
cylinder block.
5.Starting at No. 3 main bearing cap and working
outwards, progressively loosen, then remove 2
bolts securing each cap. Discard main bearing
cap bolts.
ProCarManuals.com
Page 196 of 667
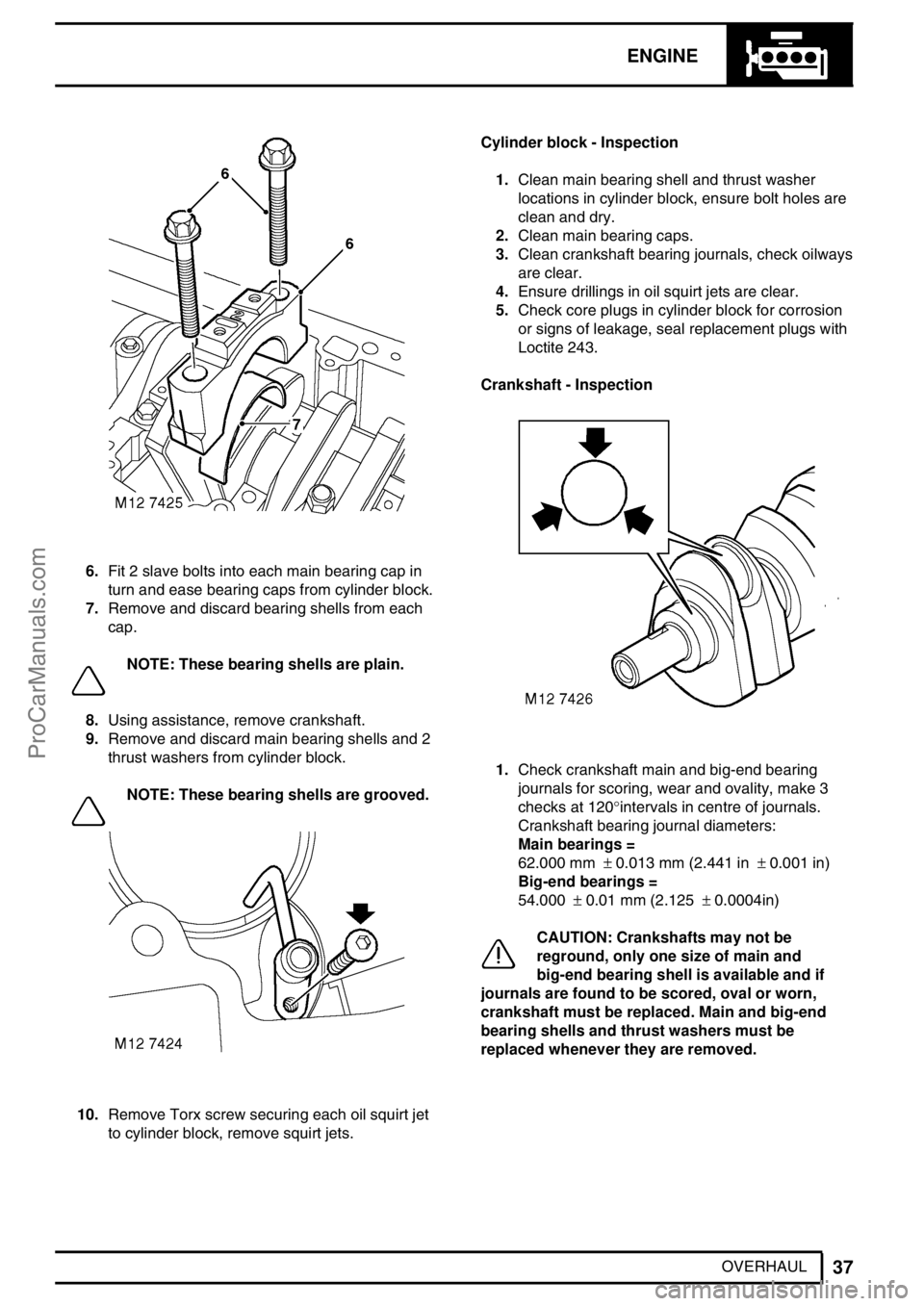
ENGINE
37
OVERHAUL
6.Fit 2 slave bolts into each main bearing cap in
turn and ease bearing caps from cylinder block.
7.Remove and discard bearing shells from each
cap.
NOTE: These bearing shells are plain.
8.Using assistance, remove crankshaft.
9.Remove and discard main bearing shells and 2
thrust washers from cylinder block.
NOTE: These bearing shells are grooved.
10.Remove Torx screw securing each oil squirt jet
to cylinder block, remove squirt jets.Cylinder block - Inspection
1.Clean main bearing shell and thrust washer
locations in cylinder block, ensure bolt holes are
clean and dry.
2.Clean main bearing caps.
3.Clean crankshaft bearing journals, check oilways
are clear.
4.Ensure drillings in oil squirt jets are clear.
5.Check core plugs in cylinder block for corrosion
or signs of leakage, seal replacement plugs with
Loctite 243.
Crankshaft - Inspection
1.Check crankshaft main and big-end bearing
journals for scoring, wear and ovality, make 3
checks at 120°intervals in centre of journals.
Crankshaft bearing journal diameters:
Main bearings =
62.000 mm±0.013 mm (2.441 in±0.001 in)
Big-end bearings =
54.000±0.01 mm (2.125±0.0004in)
CAUTION: Crankshafts may not be
reground, only one size of main and
big-end bearing shell is available and if
journals are found to be scored, oval or worn,
crankshaft must be replaced. Main and big-end
bearing shells and thrust washers must be
replaced whenever they are removed.
ProCarManuals.com
Page 197 of 667
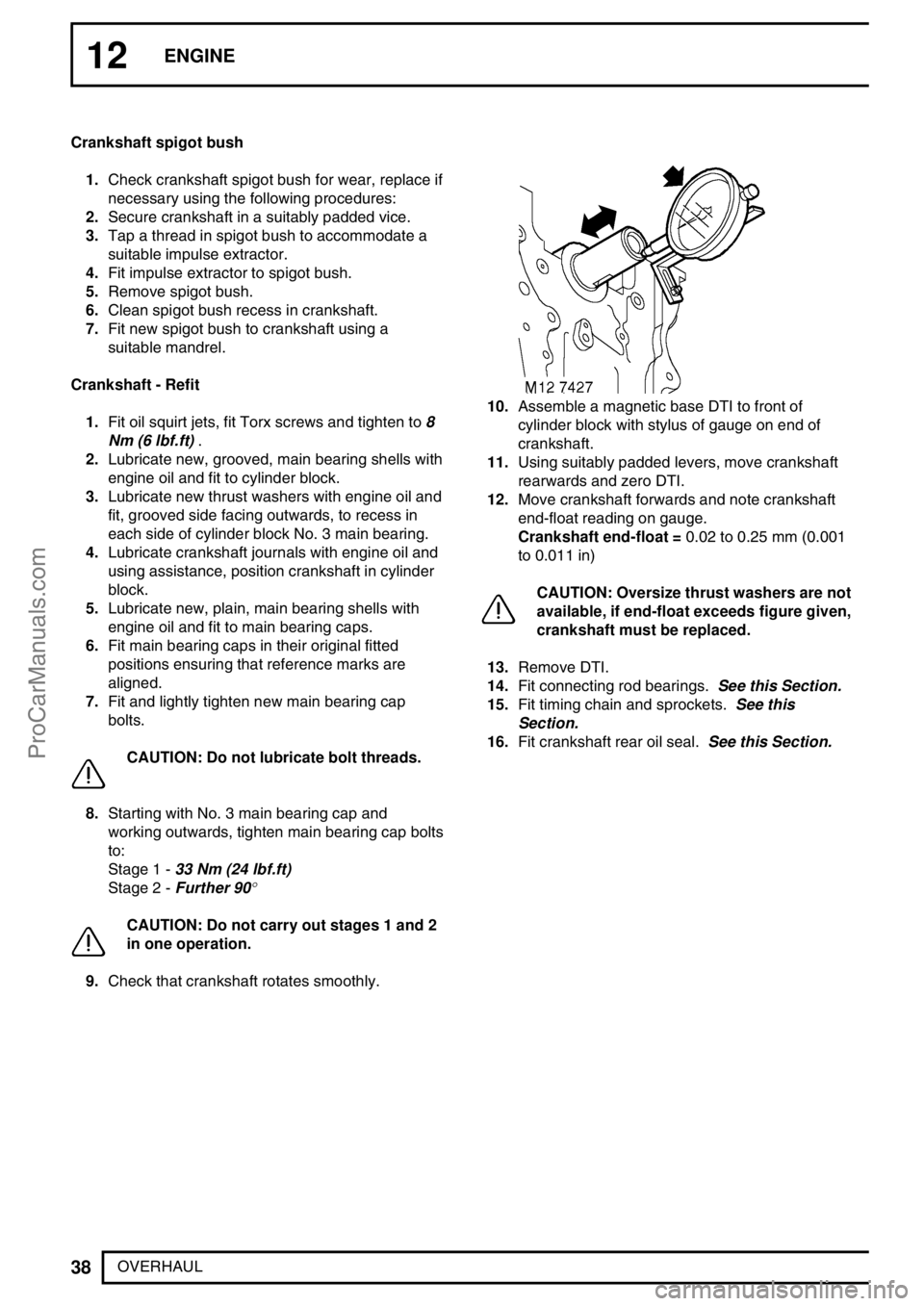
12ENGINE
38
OVERHAUL Crankshaft spigot bush
1.Check crankshaft spigot bush for wear, replace if
necessary using the following procedures:
2.Secure crankshaft in a suitably padded vice.
3.Tap a thread in spigot bush to accommodate a
suitable impulse extractor.
4.Fit impulse extractor to spigot bush.
5.Remove spigot bush.
6.Clean spigot bush recess in crankshaft.
7.Fit new spigot bush to crankshaft using a
suitable mandrel.
Crankshaft - Refit
1.Fit oil squirt jets, fit Torx screws and tighten to8
Nm (6 lbf.ft).
2.Lubricate new, grooved, main bearing shells with
engine oil and fit to cylinder block.
3.Lubricate new thrust washers with engine oil and
fit, grooved side facing outwards, to recess in
each side of cylinder block No. 3 main bearing.
4.Lubricate crankshaft journals with engine oil and
using assistance, position crankshaft in cylinder
block.
5.Lubricate new, plain, main bearing shells with
engine oil and fit to main bearing caps.
6.Fit main bearing caps in their original fitted
positions ensuring that reference marks are
aligned.
7.Fit and lightly tighten new main bearing cap
bolts.
CAUTION: Do not lubricate bolt threads.
8.Starting with No. 3 main bearing cap and
working outwards, tighten main bearing cap bolts
to:
Stage 1 -33 Nm (24 lbf.ft)
Stage 2 -Further 90
°
CAUTION: Do not carry out stages 1 and 2
in one operation.
9.Check that crankshaft rotates smoothly.
10.Assemble a magnetic base DTI to front of
cylinder block with stylus of gauge on end of
crankshaft.
11.Using suitably padded levers, move crankshaft
rearwards and zero DTI.
12.Move crankshaft forwards and note crankshaft
end-float reading on gauge.
Crankshaft end-float =0.02 to 0.25 mm (0.001
to 0.011 in)
CAUTION: Oversize thrust washers are not
available, if end-float exceeds figure given,
crankshaft must be replaced.
13.Remove DTI.
14.Fit connecting rod bearings.See this Section.
15.Fit timing chain and sprockets.See this
Section.
16.Fit crankshaft rear oil seal.See this Section.
ProCarManuals.com
Page 198 of 667
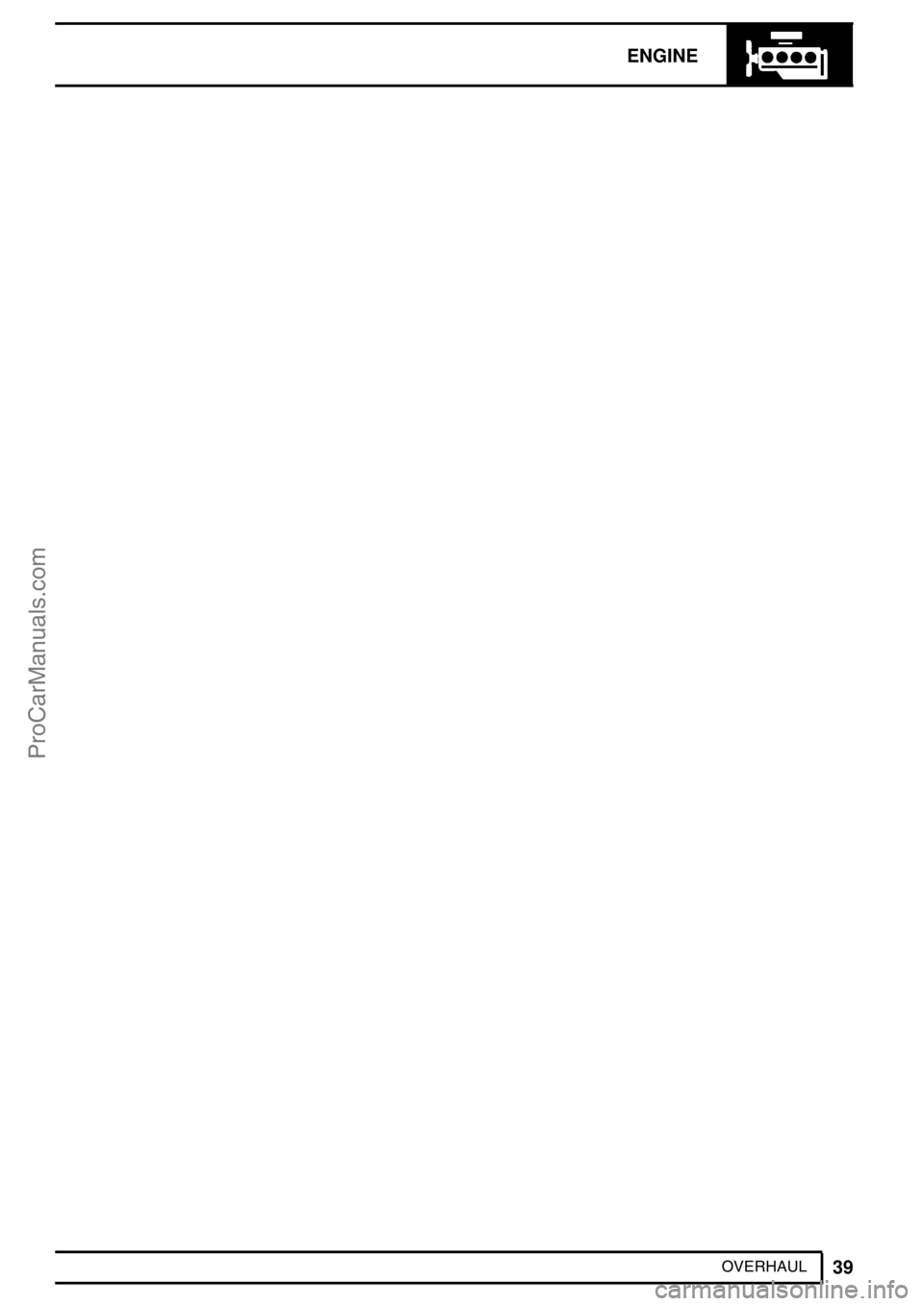
ENGINE
39
OVERHAUL
ProCarManuals.com
Page 199 of 667
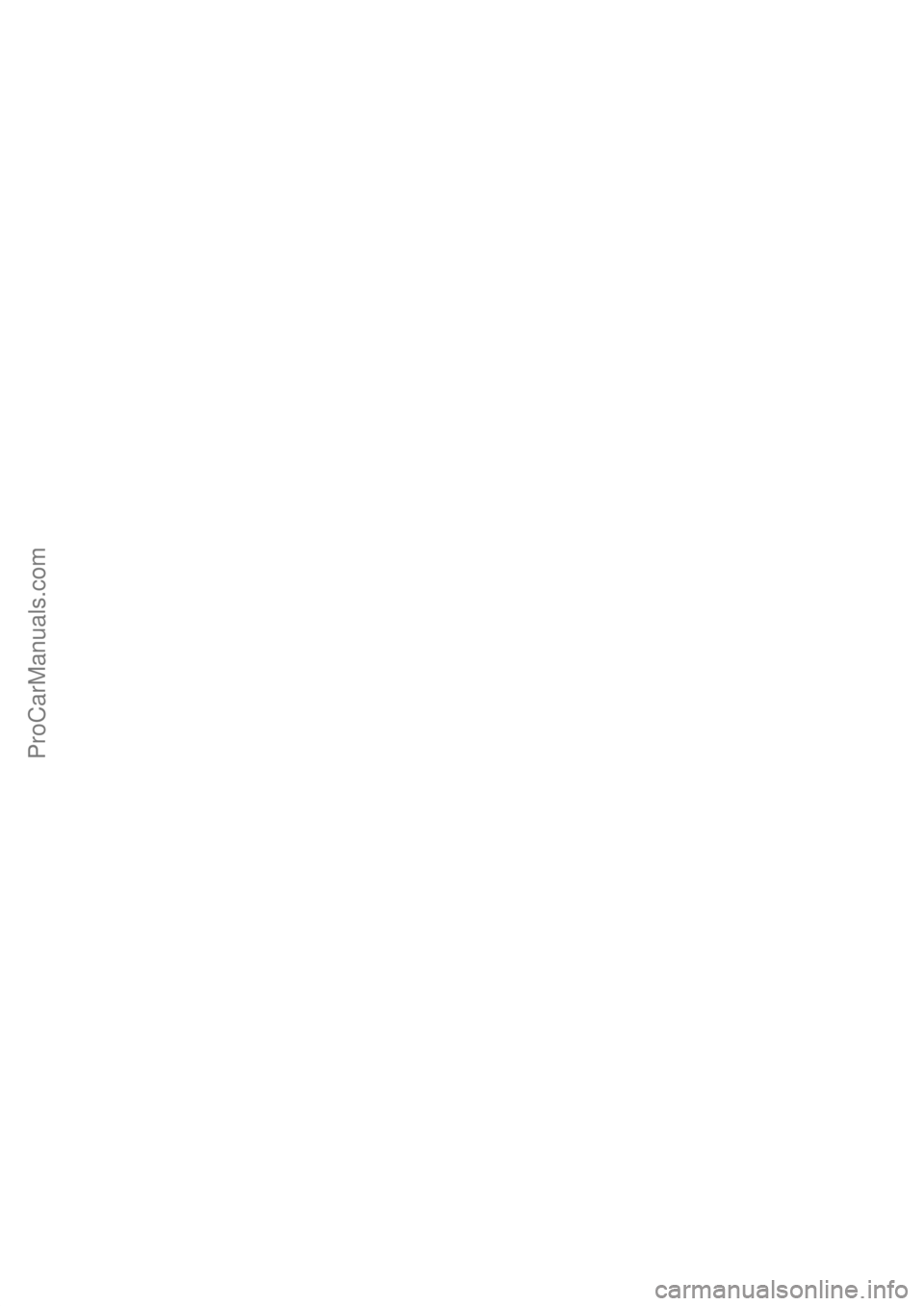
ProCarManuals.com
Page 200 of 667
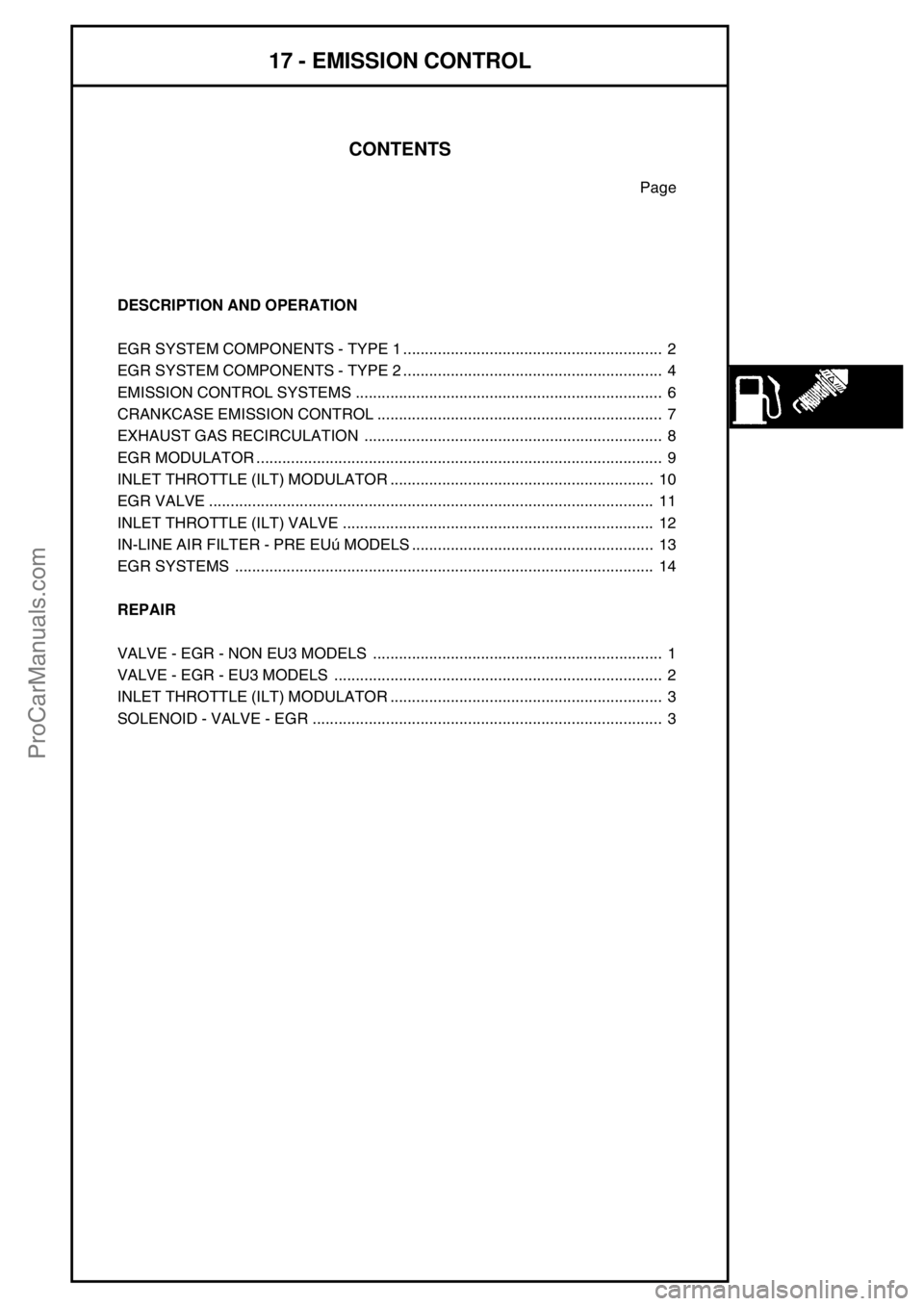
17 - EMISSION CONTROL
CONTENTS
Page
DESCRIPTION AND OPERATION
EGR SYSTEM COMPONENTS - TYPE 1 2............................................................
EGR SYSTEM COMPONENTS - TYPE 2 4............................................................
EMISSION CONTROL SYSTEMS 6.......................................................................
CRANKCASE EMISSION CONTROL 7..................................................................
EXHAUST GAS RECIRCULATION 8.....................................................................
EGR MODULATOR 9..............................................................................................
INLET THROTTLE (ILT) MODULATOR 10.............................................................
EGR VALVE 11.......................................................................................................
INLET THROTTLE (ILT) VALVE 12........................................................................
IN-LINE AIR FILTER - PRE EU´ u MODELS 13........................................................
EGR SYSTEMS 14.................................................................................................
REPAIR
VALVE - EGR - NON EU3 MODELS 1...................................................................
VALVE - EGR - EU3 MODELS 2............................................................................
INLET THROTTLE (ILT) MODULATOR 3...............................................................
SOLENOID - VALVE - EGR 3.................................................................................
ProCarManuals.com