relay LAND ROVER DISCOVERY 1995 User Guide
[x] Cancel search | Manufacturer: LAND ROVER, Model Year: 1995, Model line: DISCOVERY, Model: LAND ROVER DISCOVERY 1995Pages: 873, PDF Size: 12.89 MB
Page 250 of 873
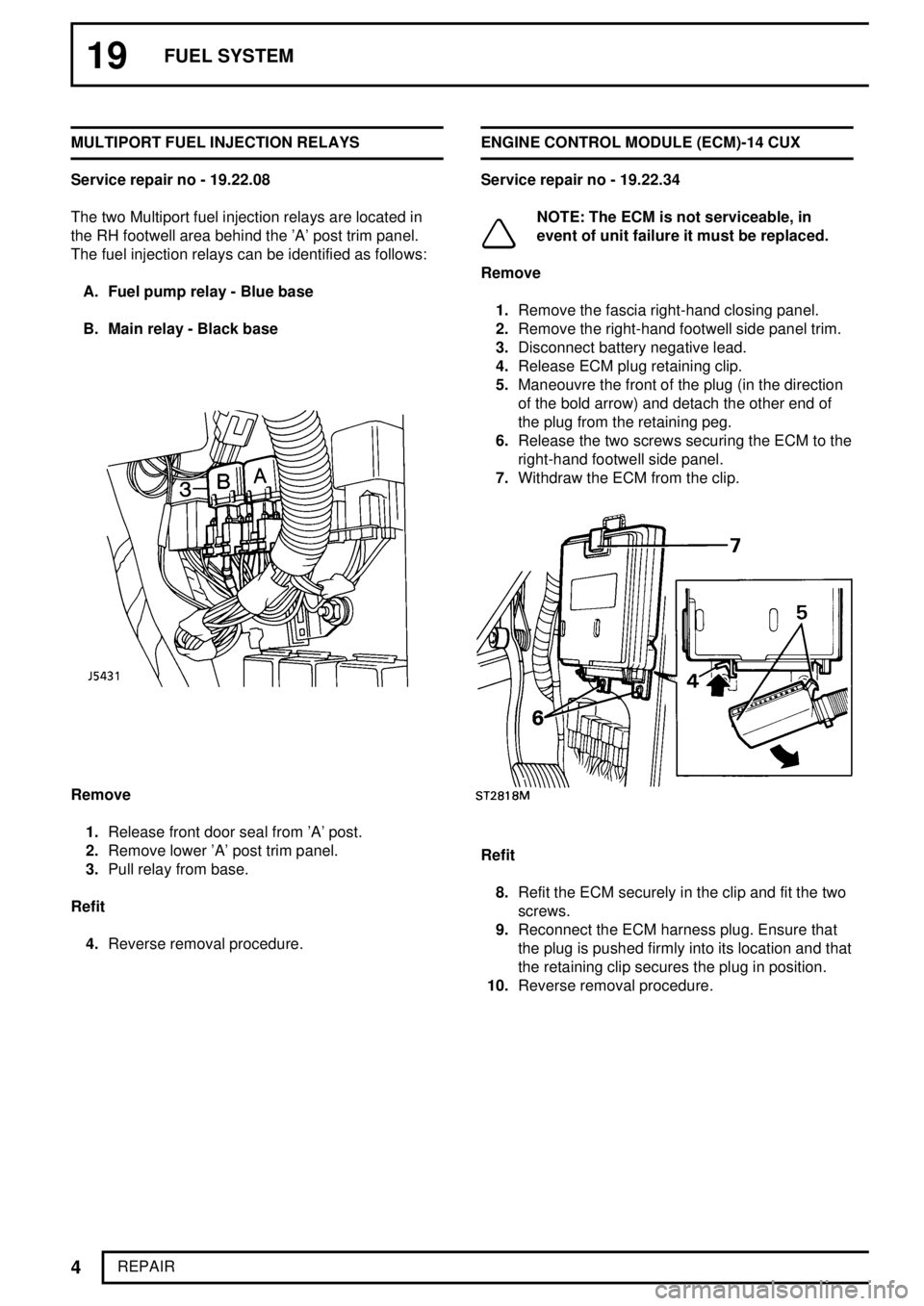
19FUEL SYSTEM
4
REPAIR MULTIPORT FUEL INJECTION RELAYS
Service repair no - 19.22.08
The two Multiport fuel injection relays are located in
the RH footwell area behind the 'A' post trim panel.
The fuel injection relays can be identified as follows:
A. Fuel pump relay - Blue base
B. Main relay - Black base
Remove
1.Release front door seal from 'A' post.
2.Remove lower 'A' post trim panel.
3.Pull relay from base.
Refit
4.Reverse removal procedure.ENGINE CONTROL MODULE (ECM)-14 CUX
Service repair no - 19.22.34
NOTE: The ECM is not serviceable, in
event of unit failure it must be replaced.
Remove
1.Remove the fascia right-hand closing panel.
2.Remove the right-hand footwell side panel trim.
3.Disconnect battery negative lead.
4.Release ECM plug retaining clip.
5.Maneouvre the front of the plug (in the direction
of the bold arrow) and detach the other end of
the plug from the retaining peg.
6.Release the two screws securing the ECM to the
right-hand footwell side panel.
7.Withdraw the ECM from the clip.
Refit
8.Refit the ECM securely in the clip and fit the two
screws.
9.Reconnect the ECM harness plug. Ensure that
the plug is pushed firmly into its location and that
the retaining clip secures the plug in position.
10.Reverse removal procedure.
Page 252 of 873
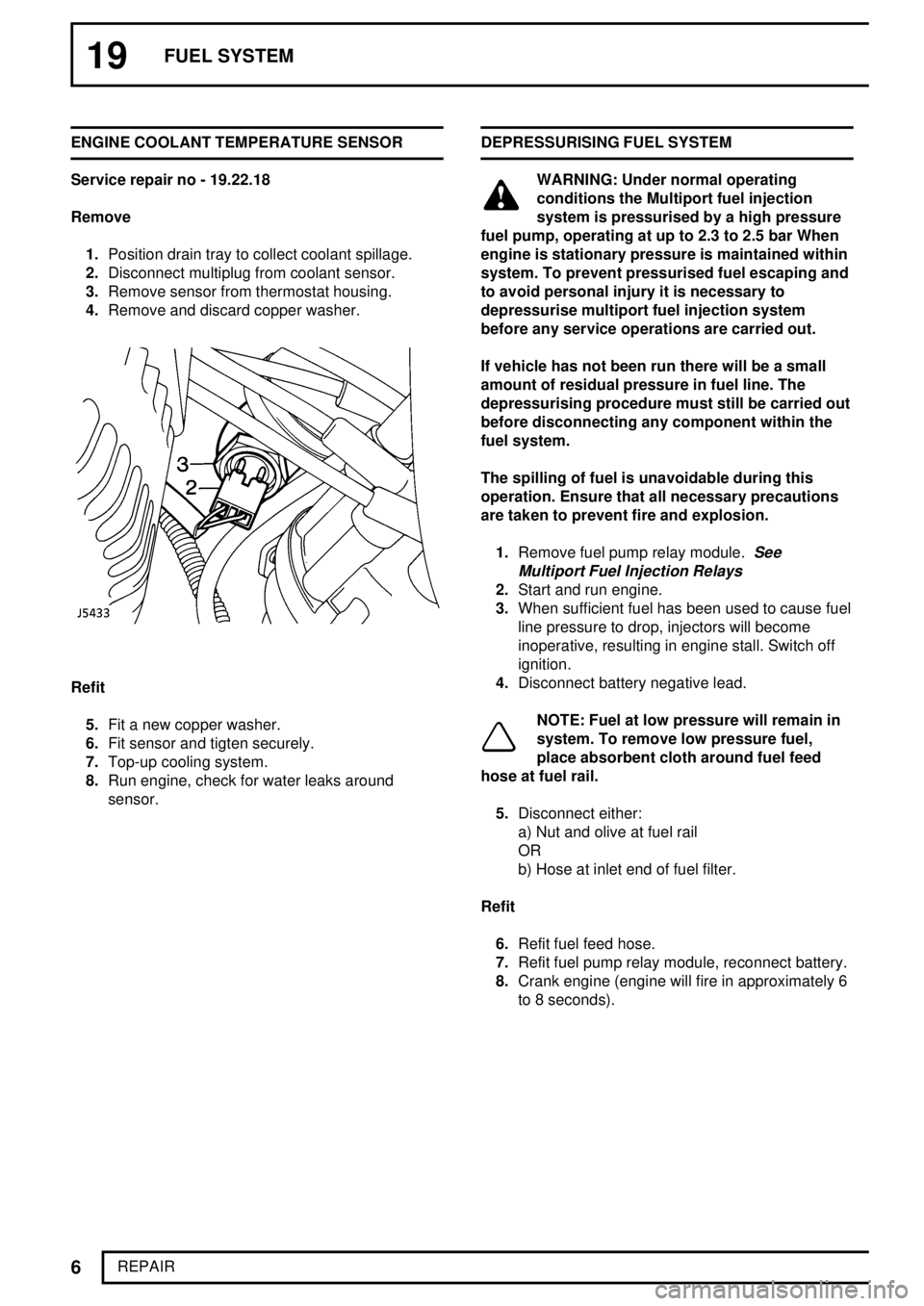
19FUEL SYSTEM
6
REPAIR ENGINE COOLANT TEMPERATURE SENSOR
Service repair no - 19.22.18
Remove
1.Position drain tray to collect coolant spillage.
2.Disconnect multiplug from coolant sensor.
3.Remove sensor from thermostat housing.
4.Remove and discard copper washer.
Refit
5.Fit a new copper washer.
6.Fit sensor and tigten securely.
7.Top-up cooling system.
8.Run engine, check for water leaks around
sensor.DEPRESSURISING FUEL SYSTEM
WARNING: Under normal operating
conditions the Multiport fuel injection
system is pressurised by a high pressure
fuel pump, operating at up to 2.3 to 2.5 bar When
engine is stationary pressure is maintained within
system. To prevent pressurised fuel escaping and
to avoid personal injury it is necessary to
depressurise multiport fuel injection system
before any service operations are carried out.
If vehicle has not been run there will be a small
amount of residual pressure in fuel line. The
depressurising procedure must still be carried out
before disconnecting any component within the
fuel system.
The spilling of fuel is unavoidable during this
operation. Ensure that all necessary precautions
are taken to prevent fire and explosion.
1.Remove fuel pump relay module.
See
Multiport Fuel Injection Relays
2.Start and run engine.
3.When sufficient fuel has been used to cause fuel
line pressure to drop, injectors will become
inoperative, resulting in engine stall. Switch off
ignition.
4.Disconnect battery negative lead.
NOTE: Fuel at low pressure will remain in
system. To remove low pressure fuel,
place absorbent cloth around fuel feed
hose at fuel rail.
5.Disconnect either:
a) Nut and olive at fuel rail
OR
b) Hose at inlet end of fuel filter.
Refit
6.Refit fuel feed hose.
7.Refit fuel pump relay module, reconnect battery.
8.Crank engine (engine will fire in approximately 6
to 8 seconds).
Page 263 of 873
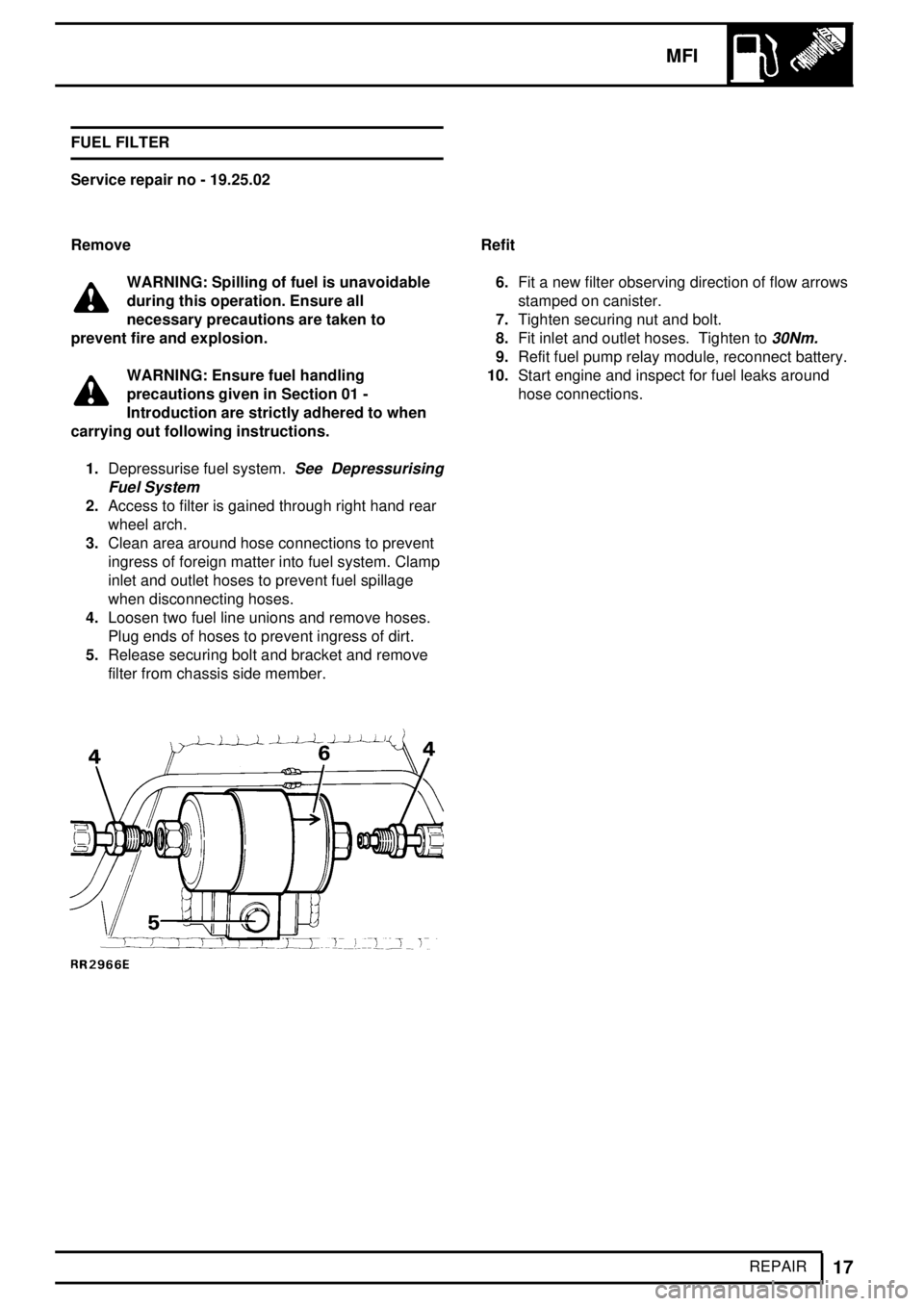
MFI
17
REPAIR FUEL FILTER
Service repair no - 19.25.02
Remove
WARNING: Spilling of fuel is unavoidable
during this operation. Ensure all
necessary precautions are taken to
prevent fire and explosion.
WARNING: Ensure fuel handling
precautions given in Section 01 -
Introduction are strictly adhered to when
carrying out following instructions.
1.Depressurise fuel system.
See Depressurising
Fuel System
2.Access to filter is gained through right hand rear
wheel arch.
3.Clean area around hose connections to prevent
ingress of foreign matter into fuel system. Clamp
inlet and outlet hoses to prevent fuel spillage
when disconnecting hoses.
4.Loosen two fuel line unions and remove hoses.
Plug ends of hoses to prevent ingress of dirt.
5.Release securing bolt and bracket and remove
filter from chassis side member.
Refit
6.Fit a new filter observing direction of flow arrows
stamped on canister.
7.Tighten securing nut and bolt.
8.Fit inlet and outlet hoses. Tighten to
30Nm.
9.Refit fuel pump relay module, reconnect battery.
10.Start engine and inspect for fuel leaks around
hose connections.
Page 273 of 873

19FUEL SYSTEM
2
DESCRIPTION AND OPERATION REV: 09/95 ENGINE MANAGEMENT SYSTEM COMPONENT
LOCATION - PRE ADVANCED EVAPS
1. Engine control module
2. Ignition coils
3. Fuel pressure regulator
4. Mass air flow sensor
5. Relay module
- Main relay
- Fuel pump relay
6. Engine coolant temperature sensor
7. Camshaft position sensor
8. Throttle position sensor
Page 278 of 873
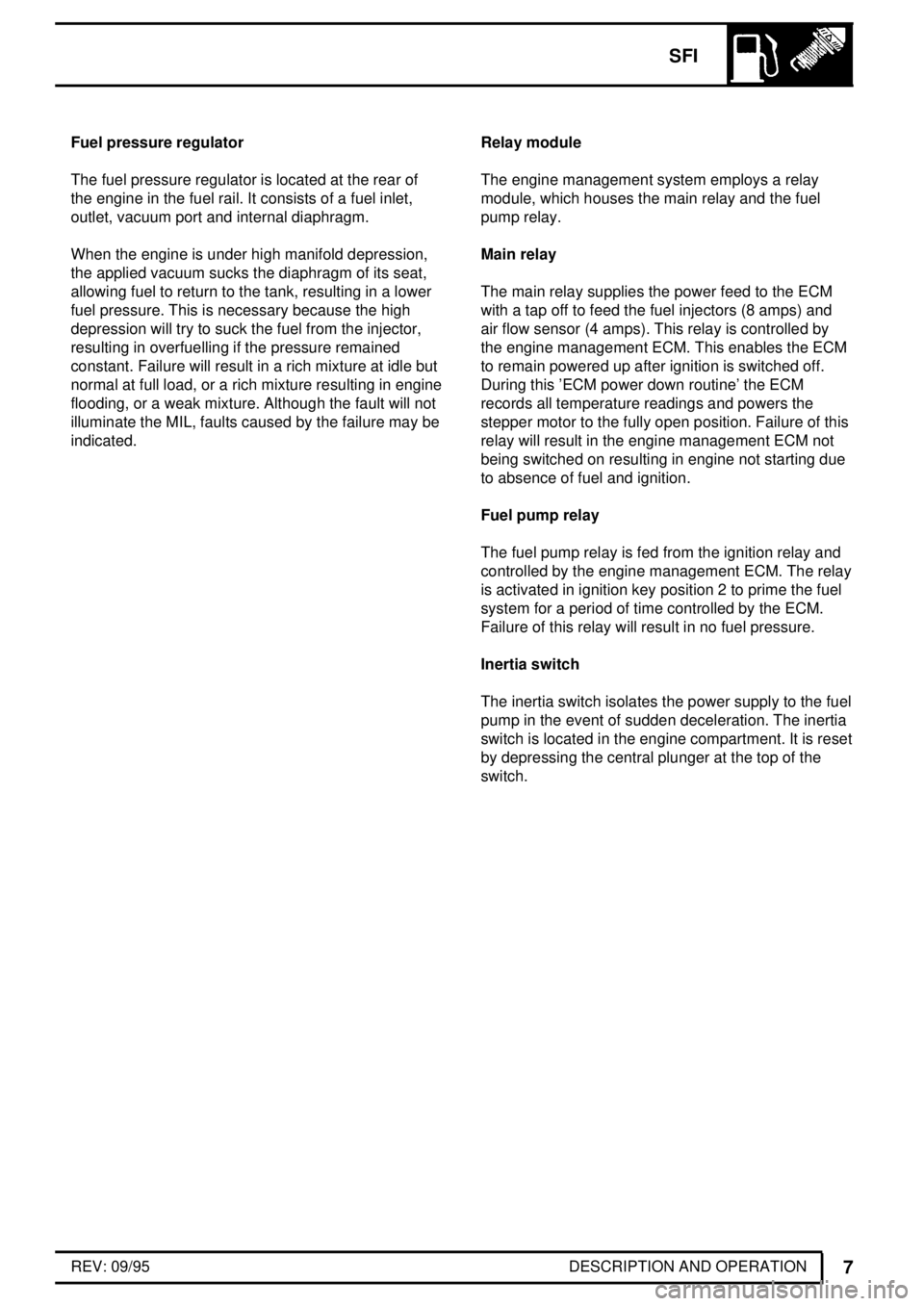
SFI
7
DESCRIPTION AND OPERATION REV: 09/95 Fuel pressure regulator
The fuel pressure regulator is located at the rear of
the engine in the fuel rail. It consists of a fuel inlet,
outlet, vacuum port and internal diaphragm.
When the engine is under high manifold depression,
the applied vacuum sucks the diaphragm of its seat,
allowing fuel to return to the tank, resulting in a lower
fuel pressure. This is necessary because the high
depression will try to suck the fuel from the injector,
resulting in overfuelling if the pressure remained
constant. Failure will result in a rich mixture at idle but
normal at full load, or a rich mixture resulting in engine
flooding, or a weak mixture. Although the fault will not
illuminate the MIL, faults caused by the failure may be
indicated.Relay module
The engine management system employs a relay
module, which houses the main relay and the fuel
pump relay.
Main relay
The main relay supplies the power feed to the ECM
with a tap off to feed the fuel injectors (8 amps) and
air flow sensor (4 amps). This relay is controlled by
the engine management ECM. This enables the ECM
to remain powered up after ignition is switched off.
During this 'ECM power down routine' the ECM
records all temperature readings and powers the
stepper motor to the fully open position. Failure of this
relay will result in the engine management ECM not
being switched on resulting in engine not starting due
to absence of fuel and ignition.
Fuel pump relay
The fuel pump relay is fed from the ignition relay and
controlled by the engine management ECM. The relay
is activated in ignition key position 2 to prime the fuel
system for a period of time controlled by the ECM.
Failure of this relay will result in no fuel pressure.
Inertia switch
The inertia switch isolates the power supply to the fuel
pump in the event of sudden deceleration. The inertia
switch is located in the engine compartment. It is reset
by depressing the central plunger at the top of the
switch.
Page 279 of 873
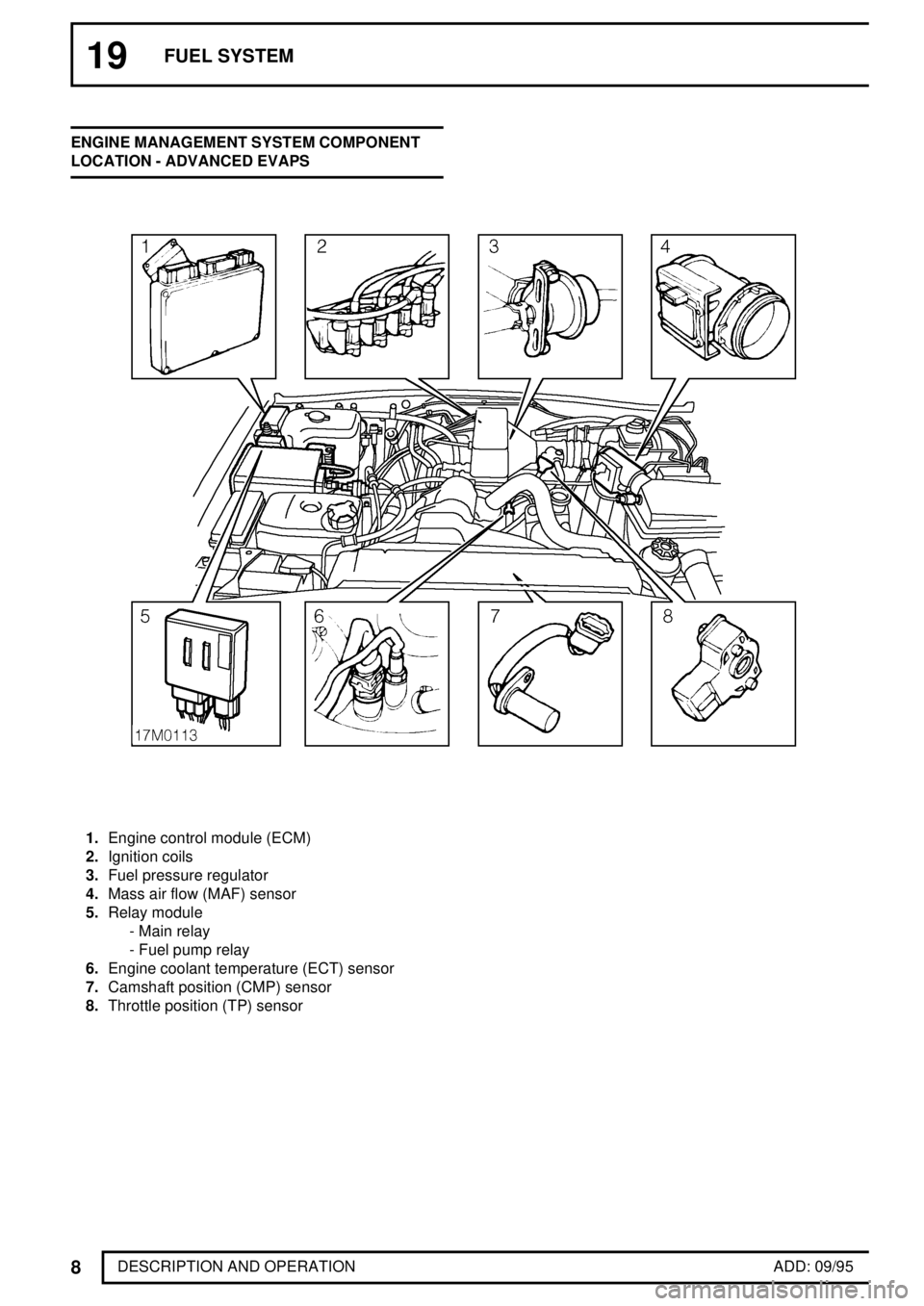
19FUEL SYSTEM
8
DESCRIPTION AND OPERATION ADD: 09/95 ENGINE MANAGEMENT SYSTEM COMPONENT
LOCATION - ADVANCED EVAPS
1.Engine control module (ECM)
2.Ignition coils
3.Fuel pressure regulator
4.Mass air flow (MAF) sensor
5.Relay module
- Main relay
- Fuel pump relay
6.Engine coolant temperature (ECT) sensor
7.Camshaft position (CMP) sensor
8.Throttle position (TP) sensor
Page 298 of 873
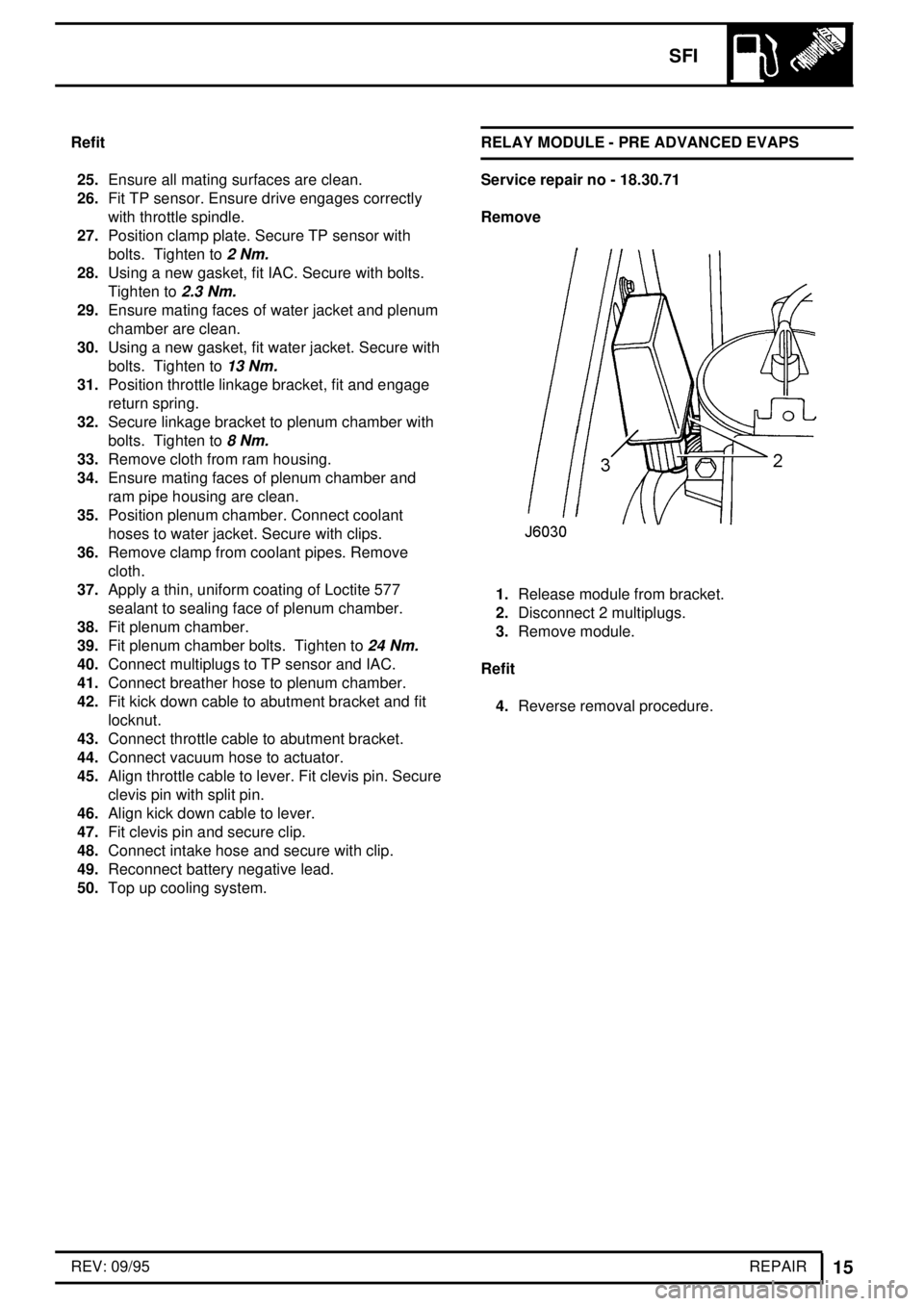
SFI
15
REPAIR REV: 09/95 Refit
25.Ensure all mating surfaces are clean.
26.Fit TP sensor. Ensure drive engages correctly
with throttle spindle.
27.Position clamp plate. Secure TP sensor with
bolts. Tighten to
2 Nm.
28.Using a new gasket, fit IAC. Secure with bolts.
Tighten to
2.3 Nm.
29.Ensure mating faces of water jacket and plenum
chamber are clean.
30.Using a new gasket, fit water jacket. Secure with
bolts. Tighten to
13 Nm.
31.Position throttle linkage bracket, fit and engage
return spring.
32.Secure linkage bracket to plenum chamber with
bolts. Tighten to
8 Nm.
33.Remove cloth from ram housing.
34.Ensure mating faces of plenum chamber and
ram pipe housing are clean.
35.Position plenum chamber. Connect coolant
hoses to water jacket. Secure with clips.
36.Remove clamp from coolant pipes. Remove
cloth.
37.Apply a thin, uniform coating of Loctite 577
sealant to sealing face of plenum chamber.
38.Fit plenum chamber.
39.Fit plenum chamber bolts. Tighten to
24 Nm.
40.Connect multiplugs to TP sensor and IAC.
41.Connect breather hose to plenum chamber.
42.Fit kick down cable to abutment bracket and fit
locknut.
43.Connect throttle cable to abutment bracket.
44.Connect vacuum hose to actuator.
45.Align throttle cable to lever. Fit clevis pin. Secure
clevis pin with split pin.
46.Align kick down cable to lever.
47.Fit clevis pin and secure clip.
48.Connect intake hose and secure with clip.
49.Reconnect battery negative lead.
50.Top up cooling system.RELAY MODULE - PRE ADVANCED EVAPS
Service repair no - 18.30.71
Remove
1.Release module from bracket.
2.Disconnect 2 multiplugs.
3.Remove module.
Refit
4.Reverse removal procedure.
Page 299 of 873
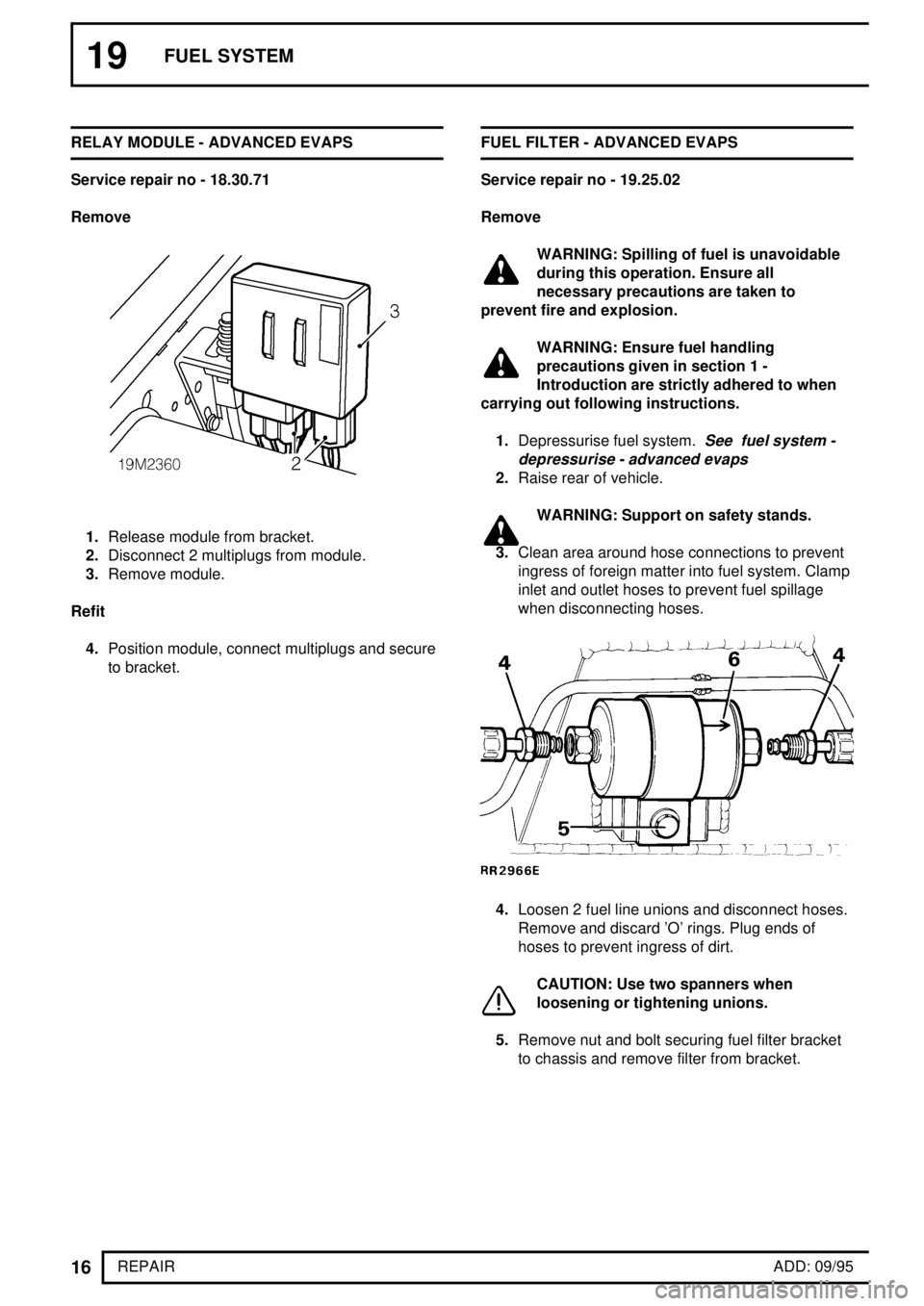
19FUEL SYSTEM
16
REPAIRADD: 09/95 RELAY MODULE - ADVANCED EVAPS
Service repair no - 18.30.71
Remove
1.Release module from bracket.
2.Disconnect 2 multiplugs from module.
3.Remove module.
Refit
4.Position module, connect multiplugs and secure
to bracket.FUEL FILTER - ADVANCED EVAPS
Service repair no - 19.25.02
Remove
WARNING: Spilling of fuel is unavoidable
during this operation. Ensure all
necessary precautions are taken to
prevent fire and explosion.
WARNING: Ensure fuel handling
precautions given in section 1 -
Introduction are strictly adhered to when
carrying out following instructions.
1.Depressurise fuel system.
See fuel system -
depressurise - advanced evaps
2.Raise rear of vehicle.
WARNING: Support on safety stands.
3.Clean area around hose connections to prevent
ingress of foreign matter into fuel system. Clamp
inlet and outlet hoses to prevent fuel spillage
when disconnecting hoses.
4.Loosen 2 fuel line unions and disconnect hoses.
Remove and discard 'O' rings. Plug ends of
hoses to prevent ingress of dirt.
CAUTION: Use two spanners when
loosening or tightening unions.
5.Remove nut and bolt securing fuel filter bracket
to chassis and remove filter from bracket.
Page 313 of 873
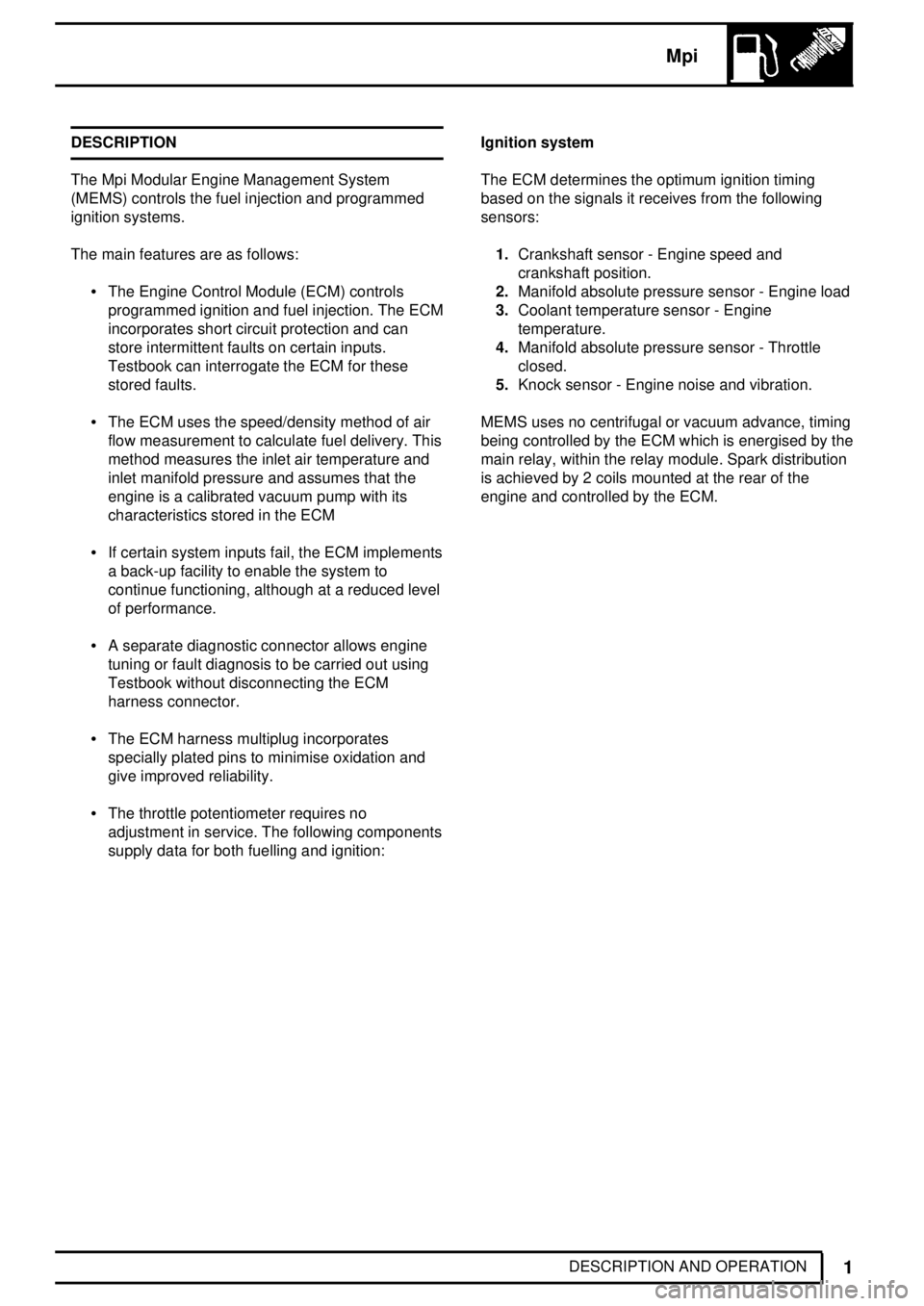
Mpi
1
DESCRIPTION AND OPERATION DESCRIPTION
The Mpi Modular Engine Management System
(MEMS) controls the fuel injection and programmed
ignition systems.
The main features are as follows:
·The Engine Control Module (ECM) controls
programmed ignition and fuel injection. The ECM
incorporates short circuit protection and can
store intermittent faults on certain inputs.
Testbook can interrogate the ECM for these
stored faults.
·The ECM uses the speed/density method of air
flow measurement to calculate fuel delivery. This
method measures the inlet air temperature and
inlet manifold pressure and assumes that the
engine is a calibrated vacuum pump with its
characteristics stored in the ECM
·If certain system inputs fail, the ECM implements
a back-up facility to enable the system to
continue functioning, although at a reduced level
of performance.
·A separate diagnostic connector allows engine
tuning or fault diagnosis to be carried out using
Testbook without disconnecting the ECM
harness connector.
·The ECM harness multiplug incorporates
specially plated pins to minimise oxidation and
give improved reliability.
·The throttle potentiometer requires no
adjustment in service. The following components
supply data for both fuelling and ignition:Ignition system
The ECM determines the optimum ignition timing
based on the signals it receives from the following
sensors:
1.Crankshaft sensor - Engine speed and
crankshaft position.
2.Manifold absolute pressure sensor - Engine load
3.Coolant temperature sensor - Engine
temperature.
4.Manifold absolute pressure sensor - Throttle
closed.
5.Knock sensor - Engine noise and vibration.
MEMS uses no centrifugal or vacuum advance, timing
being controlled by the ECM which is energised by the
main relay, within the relay module. Spark distribution
is achieved by 2 coils mounted at the rear of the
engine and controlled by the ECM.
Page 315 of 873
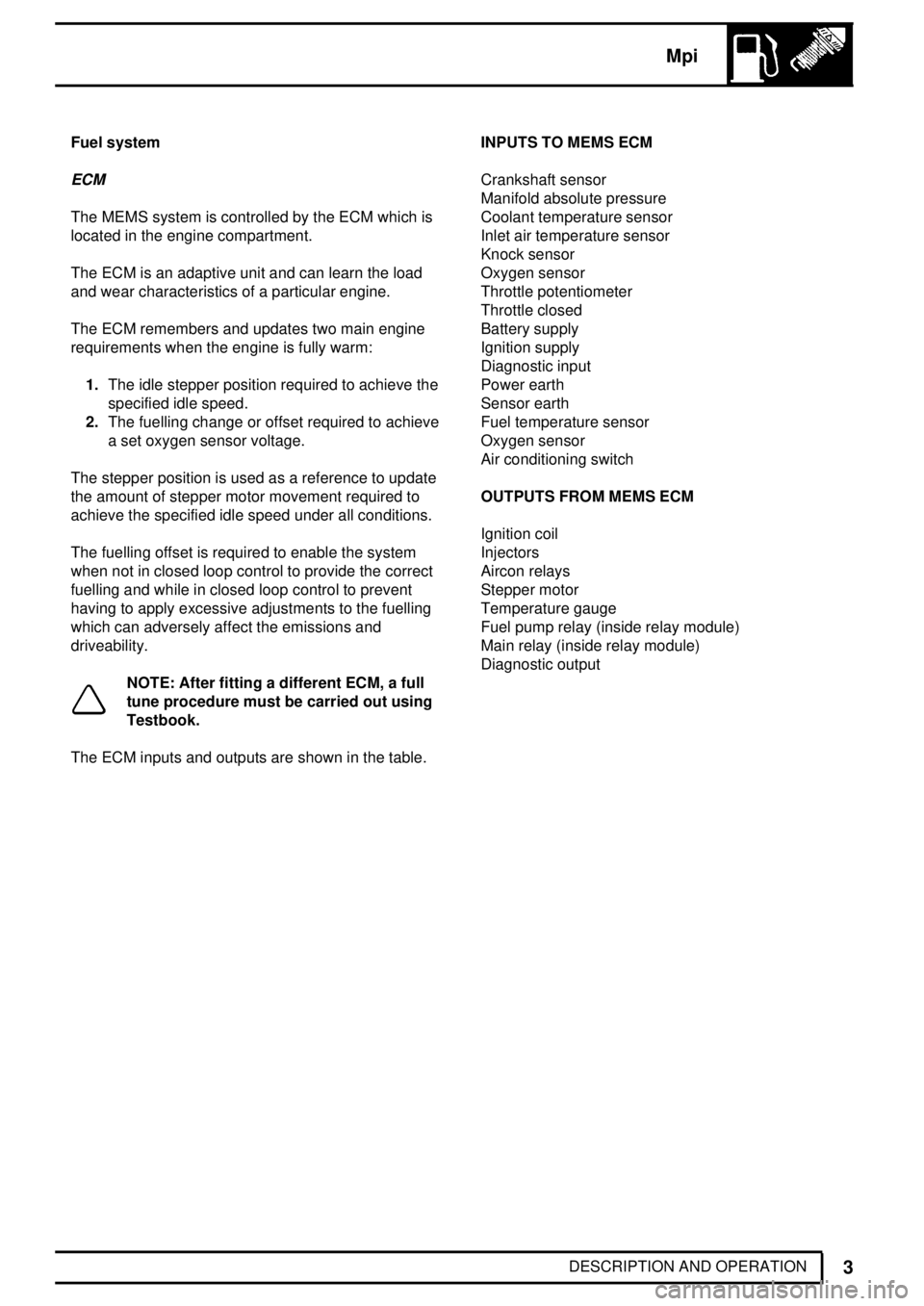
Mpi
3
DESCRIPTION AND OPERATION Fuel system
ECM
The MEMS system is controlled by the ECM which is
located in the engine compartment.
The ECM is an adaptive unit and can learn the load
and wear characteristics of a particular engine.
The ECM remembers and updates two main engine
requirements when the engine is fully warm:
1.The idle stepper position required to achieve the
specified idle speed.
2.The fuelling change or offset required to achieve
a set oxygen sensor voltage.
The stepper position is used as a reference to update
the amount of stepper motor movement required to
achieve the specified idle speed under all conditions.
The fuelling offset is required to enable the system
when not in closed loop control to provide the correct
fuelling and while in closed loop control to prevent
having to apply excessive adjustments to the fuelling
which can adversely affect the emissions and
driveability.
NOTE: After fitting a different ECM, a full
tune procedure must be carried out using
Testbook.
The ECM inputs and outputs are shown in the table.INPUTS TO MEMS ECM
Crankshaft sensor
Manifold absolute pressure
Coolant temperature sensor
Inlet air temperature sensor
Knock sensor
Oxygen sensor
Throttle potentiometer
Throttle closed
Battery supply
Ignition supply
Diagnostic input
Power earth
Sensor earth
Fuel temperature sensor
Oxygen sensor
Air conditioning switch
OUTPUTS FROM MEMS ECM
Ignition coil
Injectors
Aircon relays
Stepper motor
Temperature gauge
Fuel pump relay (inside relay module)
Main relay (inside relay module)
Diagnostic output