relay LAND ROVER DISCOVERY 1995 Owner's Manual
[x] Cancel search | Manufacturer: LAND ROVER, Model Year: 1995, Model line: DISCOVERY, Model: LAND ROVER DISCOVERY 1995Pages: 873, PDF Size: 12.89 MB
Page 317 of 873
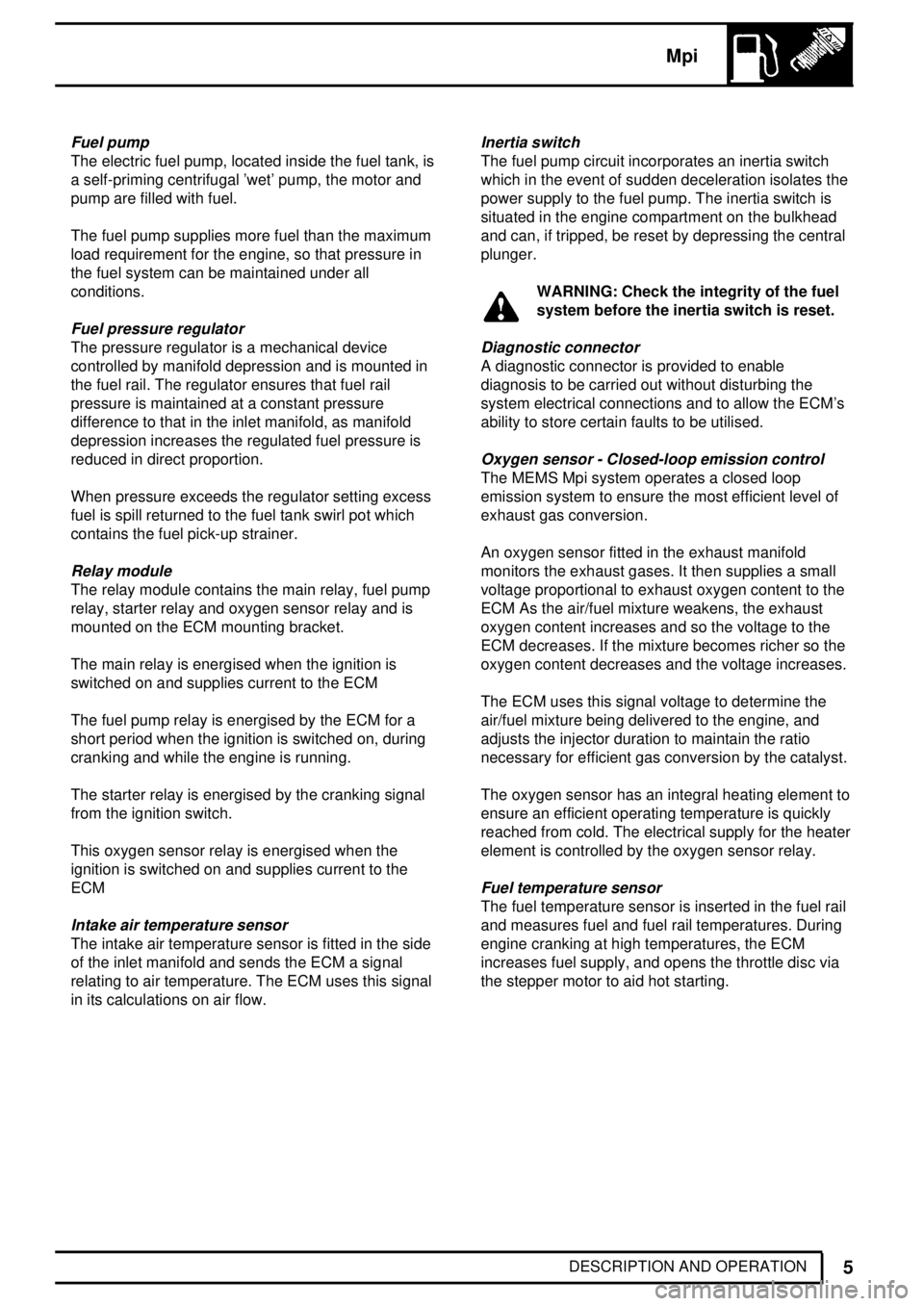
Mpi
5
DESCRIPTION AND OPERATION
Fuel pump
The electric fuel pump, located inside the fuel tank, is
a self-priming centrifugal 'wet' pump, the motor and
pump are filled with fuel.
The fuel pump supplies more fuel than the maximum
load requirement for the engine, so that pressure in
the fuel system can be maintained under all
conditions.
Fuel pressure regulator
The pressure regulator is a mechanical device
controlled by manifold depression and is mounted in
the fuel rail. The regulator ensures that fuel rail
pressure is maintained at a constant pressure
difference to that in the inlet manifold, as manifold
depression increases the regulated fuel pressure is
reduced in direct proportion.
When pressure exceeds the regulator setting excess
fuel is spill returned to the fuel tank swirl pot which
contains the fuel pick-up strainer.
Relay module
The relay module contains the main relay, fuel pump
relay, starter relay and oxygen sensor relay and is
mounted on the ECM mounting bracket.
The main relay is energised when the ignition is
switched on and supplies current to the ECM
The fuel pump relay is energised by the ECM for a
short period when the ignition is switched on, during
cranking and while the engine is running.
The starter relay is energised by the cranking signal
from the ignition switch.
This oxygen sensor relay is energised when the
ignition is switched on and supplies current to the
ECM
Intake air temperature sensor
The intake air temperature sensor is fitted in the side
of the inlet manifold and sends the ECM a signal
relating to air temperature. The ECM uses this signal
in its calculations on air flow.
Inertia switch
The fuel pump circuit incorporates an inertia switch
which in the event of sudden deceleration isolates the
power supply to the fuel pump. The inertia switch is
situated in the engine compartment on the bulkhead
and can, if tripped, be reset by depressing the central
plunger.
WARNING: Check the integrity of the fuel
system before the inertia switch is reset.
Diagnostic connector
A diagnostic connector is provided to enable
diagnosis to be carried out without disturbing the
system electrical connections and to allow the ECM's
ability to store certain faults to be utilised.
Oxygen sensor - Closed-loop emission control
The MEMS Mpi system operates a closed loop
emission system to ensure the most efficient level of
exhaust gas conversion.
An oxygen sensor fitted in the exhaust manifold
monitors the exhaust gases. It then supplies a small
voltage proportional to exhaust oxygen content to the
ECM As the air/fuel mixture weakens, the exhaust
oxygen content increases and so the voltage to the
ECM decreases. If the mixture becomes richer so the
oxygen content decreases and the voltage increases.
The ECM uses this signal voltage to determine the
air/fuel mixture being delivered to the engine, and
adjusts the injector duration to maintain the ratio
necessary for efficient gas conversion by the catalyst.
The oxygen sensor has an integral heating element to
ensure an efficient operating temperature is quickly
reached from cold. The electrical supply for the heater
element is controlled by the oxygen sensor relay.
Fuel temperature sensor
The fuel temperature sensor is inserted in the fuel rail
and measures fuel and fuel rail temperatures. During
engine cranking at high temperatures, the ECM
increases fuel supply, and opens the throttle disc via
the stepper motor to aid hot starting.
Page 319 of 873
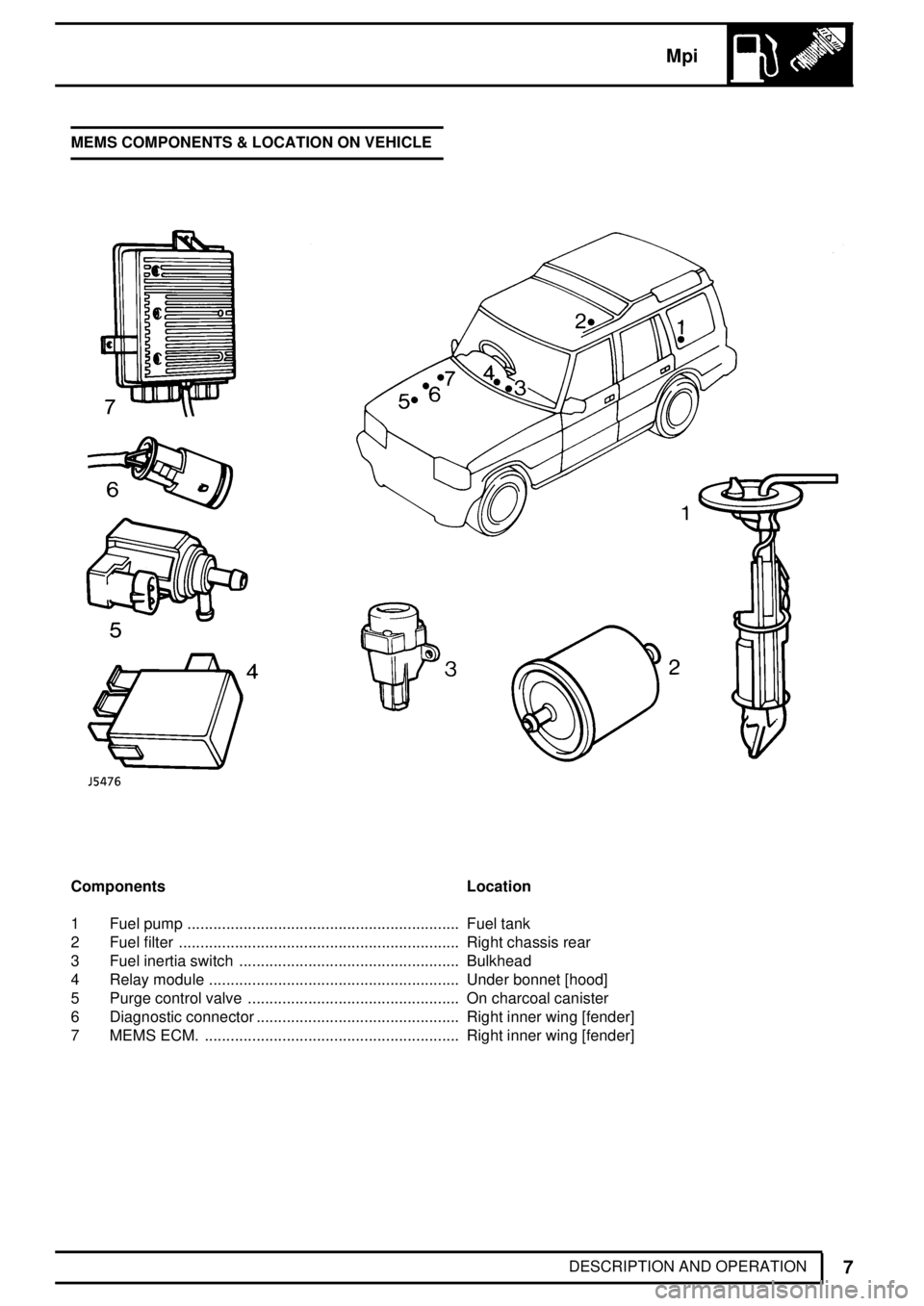
Mpi
7
DESCRIPTION AND OPERATION MEMS COMPONENTS & LOCATION ON VEHICLE
Components Location
1 Fuel pump Fuel tank...............................................................
2 Fuel filter Right chassis rear.................................................................
3 Fuel inertia switch Bulkhead...................................................
4 Relay module Under bonnet [hood]..........................................................
5 Purge control valve On charcoal canister.................................................
6 Diagnostic connector Right inner wing [fender]...............................................
7 MEMS ECM. Right inner wing [fender]...........................................................
Page 321 of 873
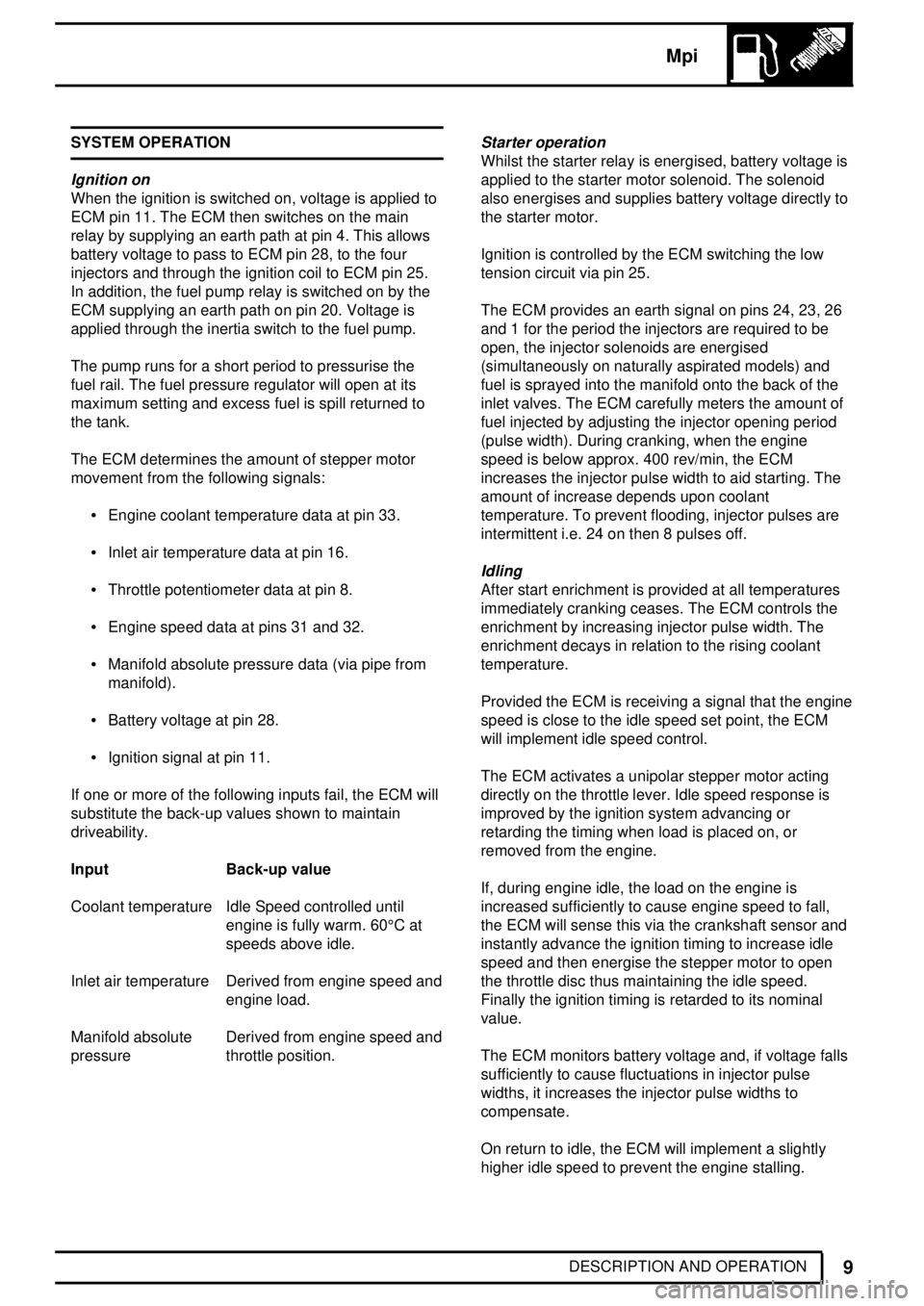
Mpi
9
DESCRIPTION AND OPERATION SYSTEM OPERATION
Ignition on
When the ignition is switched on, voltage is applied to
ECM pin 11. The ECM then switches on the main
relay by supplying an earth path at pin 4. This allows
battery voltage to pass to ECM pin 28, to the four
injectors and through the ignition coil to ECM pin 25.
In addition, the fuel pump relay is switched on by the
ECM supplying an earth path on pin 20. Voltage is
applied through the inertia switch to the fuel pump.
The pump runs for a short period to pressurise the
fuel rail. The fuel pressure regulator will open at its
maximum setting and excess fuel is spill returned to
the tank.
The ECM determines the amount of stepper motor
movement from the following signals:
·Engine coolant temperature data at pin 33.
·Inlet air temperature data at pin 16.
·Throttle potentiometer data at pin 8.
·Engine speed data at pins 31 and 32.
·Manifold absolute pressure data (via pipe from
manifold).
·Battery voltage at pin 28.
·Ignition signal at pin 11.
If one or more of the following inputs fail, the ECM will
substitute the back-up values shown to maintain
driveability.
Input Back-up value
Coolant temperature Idle Speed controlled until
engine is fully warm. 60°Cat
speeds above idle.
Inlet air temperature Derived from engine speed and
engine load.
Manifold absolute Derived from engine speed and
pressure throttle position.
Starter operation
Whilst the starter relay is energised, battery voltage is
applied to the starter motor solenoid. The solenoid
also energises and supplies battery voltage directly to
the starter motor.
Ignition is controlled by the ECM switching the low
tension circuit via pin 25.
The ECM provides an earth signal on pins 24, 23, 26
and 1 for the period the injectors are required to be
open, the injector solenoids are energised
(simultaneously on naturally aspirated models) and
fuel is sprayed into the manifold onto the back of the
inlet valves. The ECM carefully meters the amount of
fuel injected by adjusting the injector opening period
(pulse width). During cranking, when the engine
speed is below approx. 400 rev/min, the ECM
increases the injector pulse width to aid starting. The
amount of increase depends upon coolant
temperature. To prevent flooding, injector pulses are
intermittent i.e. 24 on then 8 pulses off.
Idling
After start enrichment is provided at all temperatures
immediately cranking ceases. The ECM controls the
enrichment by increasing injector pulse width. The
enrichment decays in relation to the rising coolant
temperature.
Provided the ECM is receiving a signal that the engine
speed is close to the idle speed set point, the ECM
will implement idle speed control.
The ECM activates a unipolar stepper motor acting
directly on the throttle lever. Idle speed response is
improved by the ignition system advancing or
retarding the timing when load is placed on, or
removed from the engine.
If, during engine idle, the load on the engine is
increased sufficiently to cause engine speed to fall,
the ECM will sense this via the crankshaft sensor and
instantly advance the ignition timing to increase idle
speed and then energise the stepper motor to open
the throttle disc thus maintaining the idle speed.
Finally the ignition timing is retarded to its nominal
value.
The ECM monitors battery voltage and, if voltage falls
sufficiently to cause fluctuations in injector pulse
widths, it increases the injector pulse widths to
compensate.
On return to idle, the ECM will implement a slightly
higher idle speed to prevent the engine stalling.
Page 322 of 873
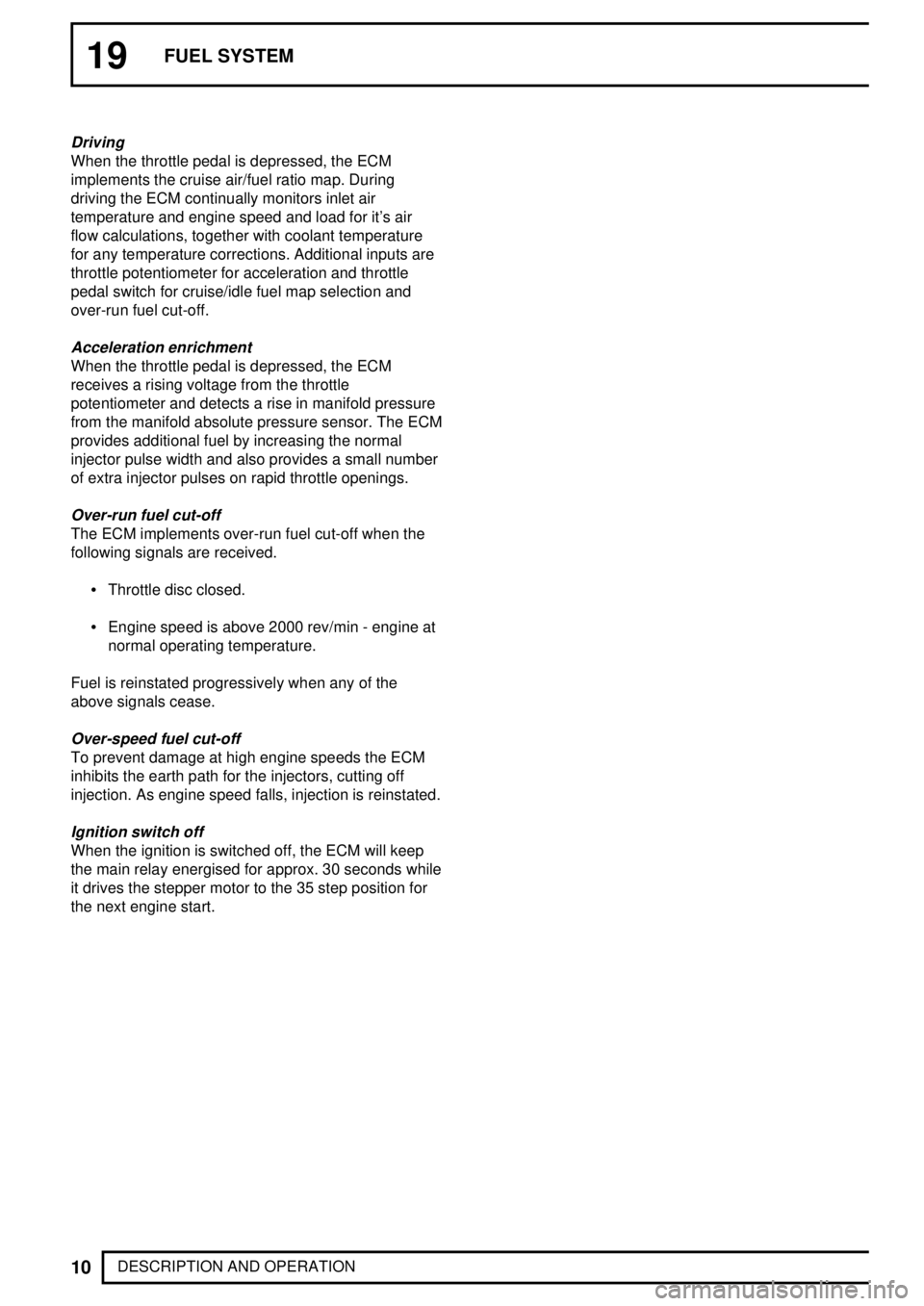
19FUEL SYSTEM
10
DESCRIPTION AND OPERATION
Driving
When the throttle pedal is depressed, the ECM
implements the cruise air/fuel ratio map. During
driving the ECM continually monitors inlet air
temperature and engine speed and load for it's air
flow calculations, together with coolant temperature
for any temperature corrections. Additional inputs are
throttle potentiometer for acceleration and throttle
pedal switch for cruise/idle fuel map selection and
over-run fuel cut-off.
Acceleration enrichment
When the throttle pedal is depressed, the ECM
receives a rising voltage from the throttle
potentiometer and detects a rise in manifold pressure
from the manifold absolute pressure sensor. The ECM
provides additional fuel by increasing the normal
injector pulse width and also provides a small number
of extra injector pulses on rapid throttle openings.
Over-run fuel cut-off
The ECM implements over-run fuel cut-off when the
following signals are received.
·Throttle disc closed.
·Engine speed is above 2000 rev/min - engine at
normal operating temperature.
Fuel is reinstated progressively when any of the
above signals cease.
Over-speed fuel cut-off
To prevent damage at high engine speeds the ECM
inhibits the earth path for the injectors, cutting off
injection. As engine speed falls, injection is reinstated.
Ignition switch off
When the ignition is switched off, the ECM will keep
the main relay energised for approx. 30 seconds while
it drives the stepper motor to the 35 step position for
the next engine start.
Page 335 of 873
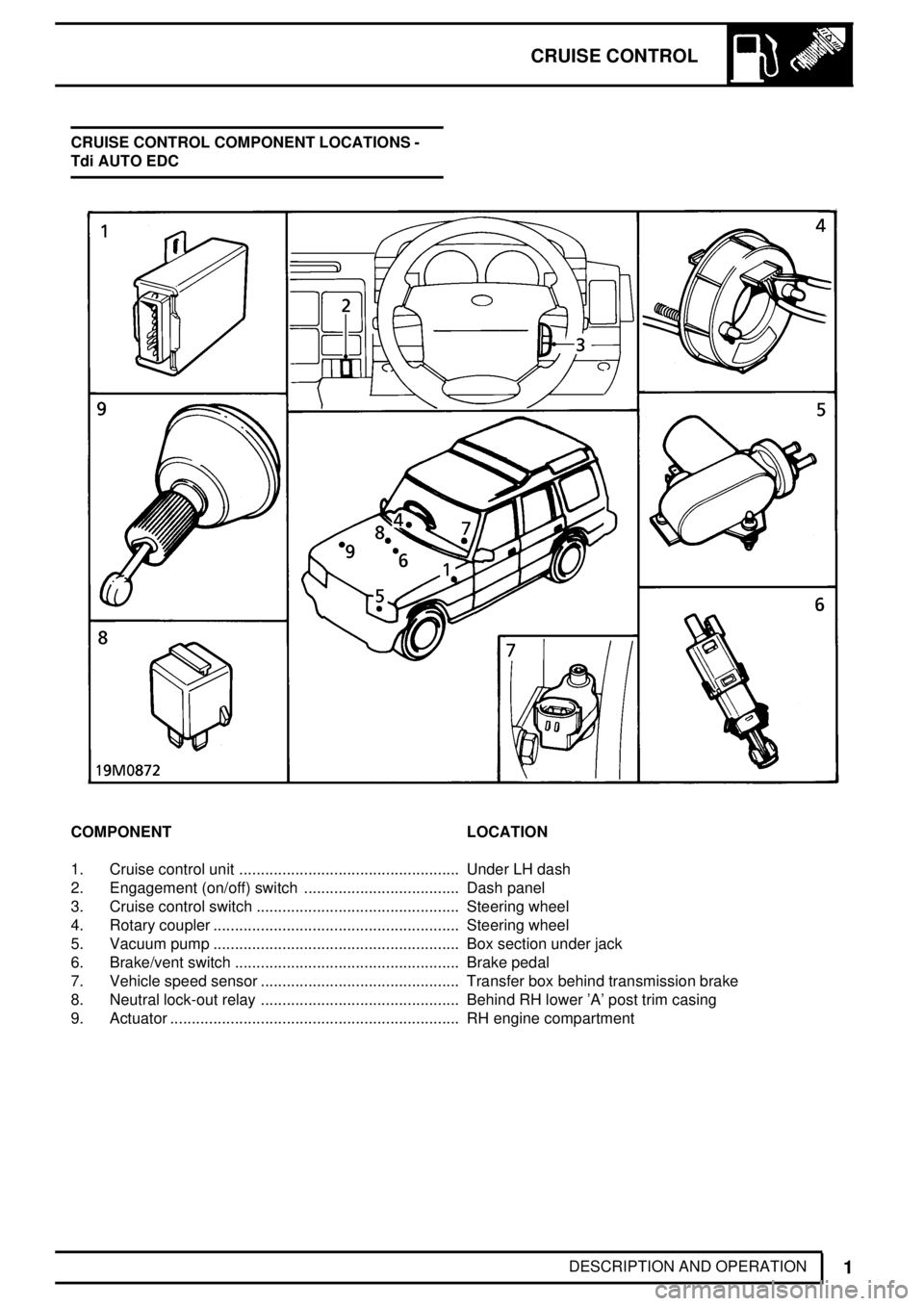
CRUISE CONTROL
1
DESCRIPTION AND OPERATION CRUISE CONTROL COMPONENT LOCATIONS -
Tdi AUTO EDC
COMPONENT LOCATION
1. Cruise control unit Under LH dash...................................................
2. Engagement (on/off) switch Dash panel....................................
3. Cruise control switch Steering wheel...............................................
4. Rotary coupler Steering wheel.........................................................
5. Vacuum pump Box section under jack.........................................................
6. Brake/vent switch Brake pedal....................................................
7. Vehicle speed sensor Transfer box behind transmission brake..............................................
8. Neutral lock-out relay Behind RH lower 'A' post trim casing..............................................
9. Actuator RH engine compartment...................................................................
Page 336 of 873
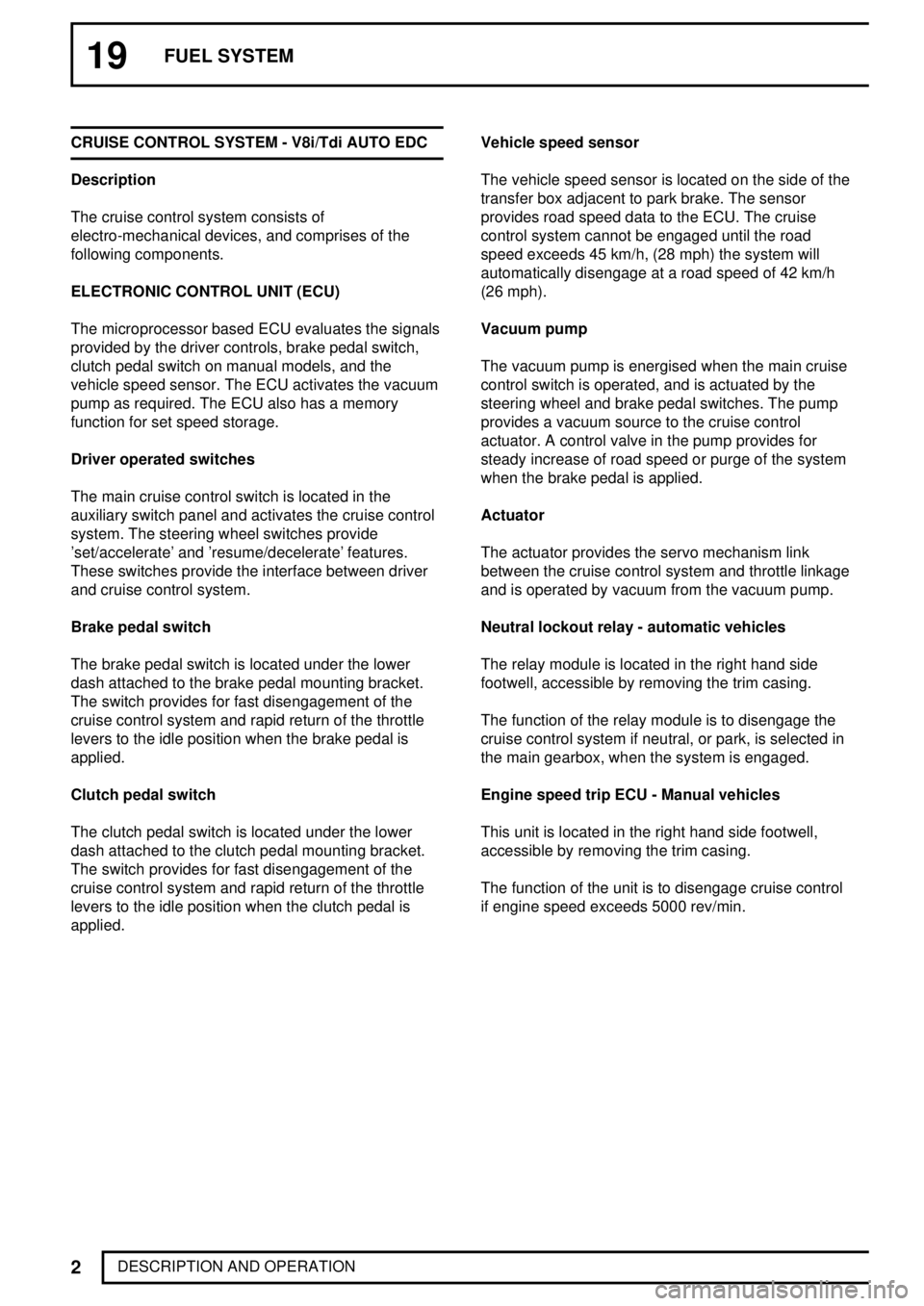
19FUEL SYSTEM
2
DESCRIPTION AND OPERATION CRUISE CONTROL SYSTEM - V8i/Tdi AUTO EDC
Description
The cruise control system consists of
electro-mechanical devices, and comprises of the
following components.
ELECTRONIC CONTROL UNIT (ECU)
The microprocessor based ECU evaluates the signals
provided by the driver controls, brake pedal switch,
clutch pedal switch on manual models, and the
vehicle speed sensor. The ECU activates the vacuum
pump as required. The ECU also has a memory
function for set speed storage.
Driver operated switches
The main cruise control switch is located in the
auxiliary switch panel and activates the cruise control
system. The steering wheel switches provide
'set/accelerate' and 'resume/decelerate' features.
These switches provide the interface between driver
and cruise control system.
Brake pedal switch
The brake pedal switch is located under the lower
dash attached to the brake pedal mounting bracket.
The switch provides for fast disengagement of the
cruise control system and rapid return of the throttle
levers to the idle position when the brake pedal is
applied.
Clutch pedal switch
The clutch pedal switch is located under the lower
dash attached to the clutch pedal mounting bracket.
The switch provides for fast disengagement of the
cruise control system and rapid return of the throttle
levers to the idle position when the clutch pedal is
applied.Vehicle speed sensor
The vehicle speed sensor is located on the side of the
transfer box adjacent to park brake. The sensor
provides road speed data to the ECU. The cruise
control system cannot be engaged until the road
speed exceeds 45 km/h, (28 mph) the system will
automatically disengage at a road speed of 42 km/h
(26 mph).
Vacuum pump
The vacuum pump is energised when the main cruise
control switch is operated, and is actuated by the
steering wheel and brake pedal switches. The pump
provides a vacuum source to the cruise control
actuator. A control valve in the pump provides for
steady increase of road speed or purge of the system
when the brake pedal is applied.
Actuator
The actuator provides the servo mechanism link
between the cruise control system and throttle linkage
and is operated by vacuum from the vacuum pump.
Neutral lockout relay - automatic vehicles
The relay module is located in the right hand side
footwell, accessible by removing the trim casing.
The function of the relay module is to disengage the
cruise control system if neutral, or park, is selected in
the main gearbox, when the system is engaged.
Engine speed trip ECU - Manual vehicles
This unit is located in the right hand side footwell,
accessible by removing the trim casing.
The function of the unit is to disengage cruise control
if engine speed exceeds 5000 rev/min.
Page 344 of 873
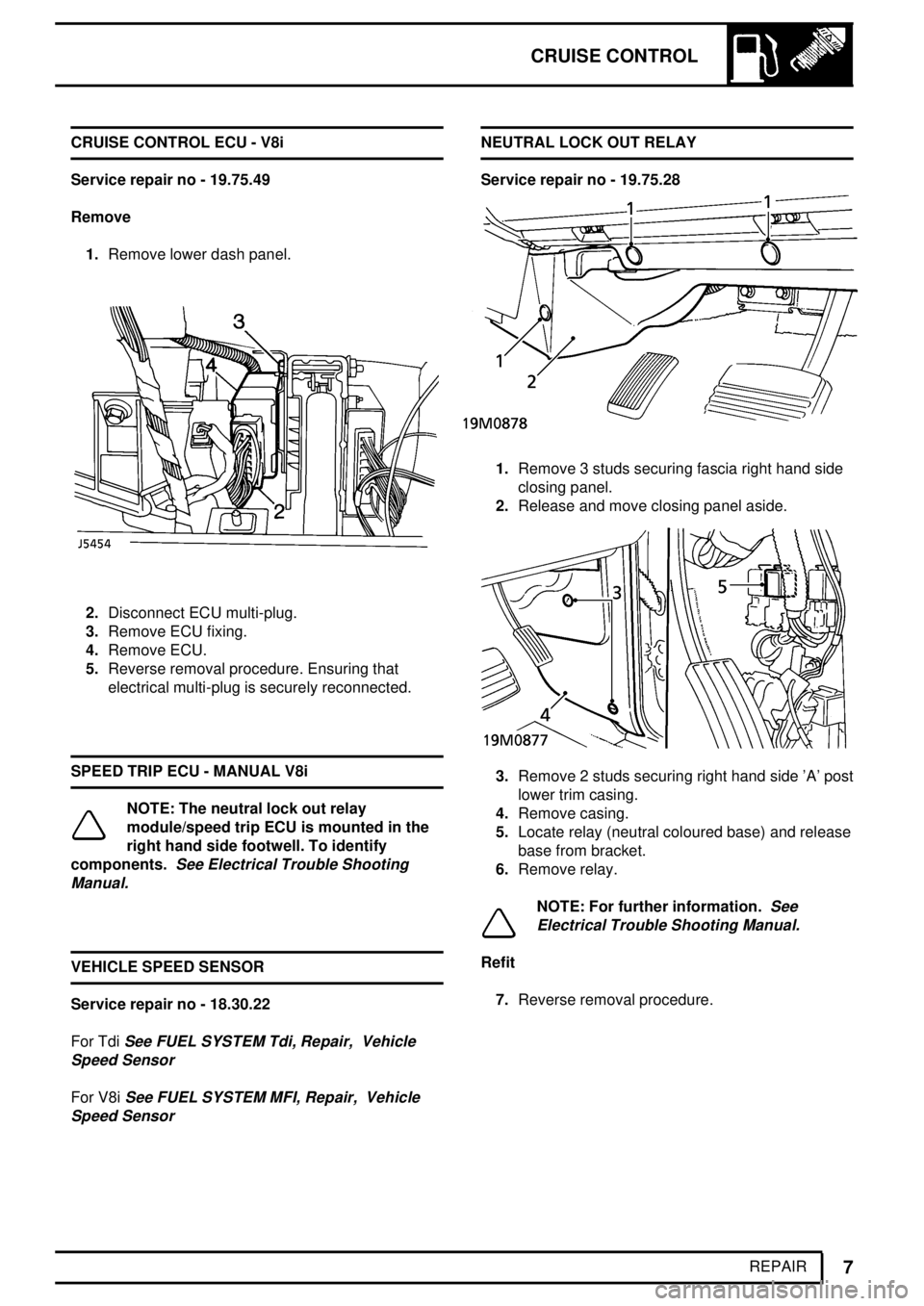
CRUISE CONTROL
7
REPAIR CRUISE CONTROL ECU - V8i
Service repair no - 19.75.49
Remove
1.Remove lower dash panel.
2.Disconnect ECU multi-plug.
3.Remove ECU fixing.
4.Remove ECU.
5.Reverse removal procedure. Ensuring that
electrical multi-plug is securely reconnected.
SPEED TRIP ECU - MANUAL V8i
NOTE: The neutral lock out relay
module/speed trip ECU is mounted in the
right hand side footwell. To identify
components.
See Electrical Trouble Shooting
Manual.
VEHICLE SPEED SENSOR
Service repair no - 18.30.22
For Tdi
See FUEL SYSTEM Tdi, Repair, Vehicle
Speed Sensor
For V8iSee FUEL SYSTEM MFI, Repair, Vehicle
Speed Sensor
NEUTRAL LOCK OUT RELAY
Service repair no - 19.75.28
1.Remove 3 studs securing fascia right hand side
closing panel.
2.Release and move closing panel aside.
3.Remove 2 studs securing right hand side 'A' post
lower trim casing.
4.Remove casing.
5.Locate relay (neutral coloured base) and release
base from bracket.
6.Remove relay.
NOTE: For further information.See
Electrical Trouble Shooting Manual.
Refit
7.Reverse removal procedure.
Page 346 of 873
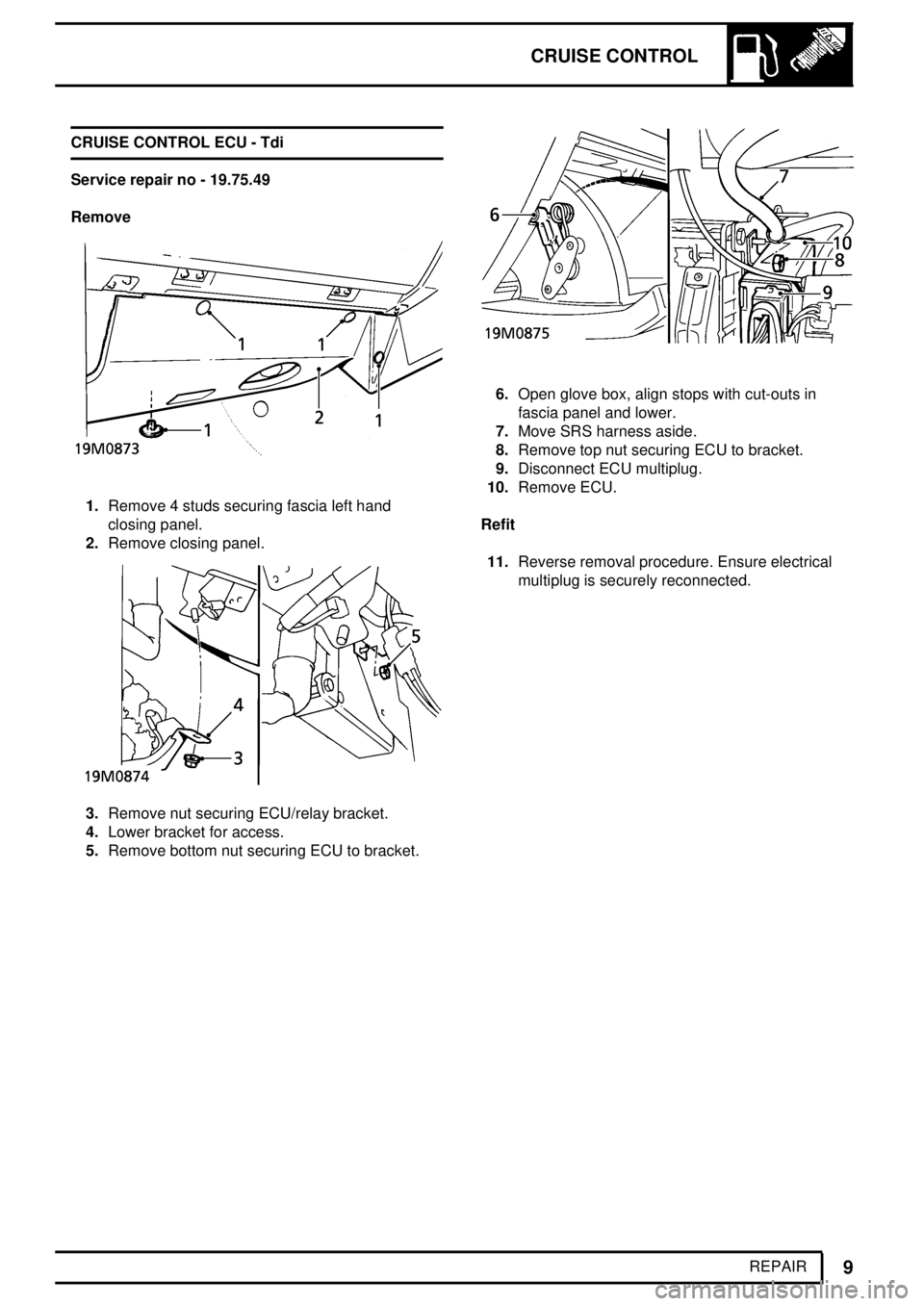
CRUISE CONTROL
9
REPAIR CRUISE CONTROL ECU - Tdi
Service repair no - 19.75.49
Remove
1.Remove 4 studs securing fascia left hand
closing panel.
2.Remove closing panel.
3.Remove nut securing ECU/relay bracket.
4.Lower bracket for access.
5.Remove bottom nut securing ECU to bracket.
6.Open glove box, align stops with cut-outs in
fascia panel and lower.
7.Move SRS harness aside.
8.Remove top nut securing ECU to bracket.
9.Disconnect ECU multiplug.
10.Remove ECU.
Refit
11.Reverse removal procedure. Ensure electrical
multiplug is securely reconnected.
Page 594 of 873
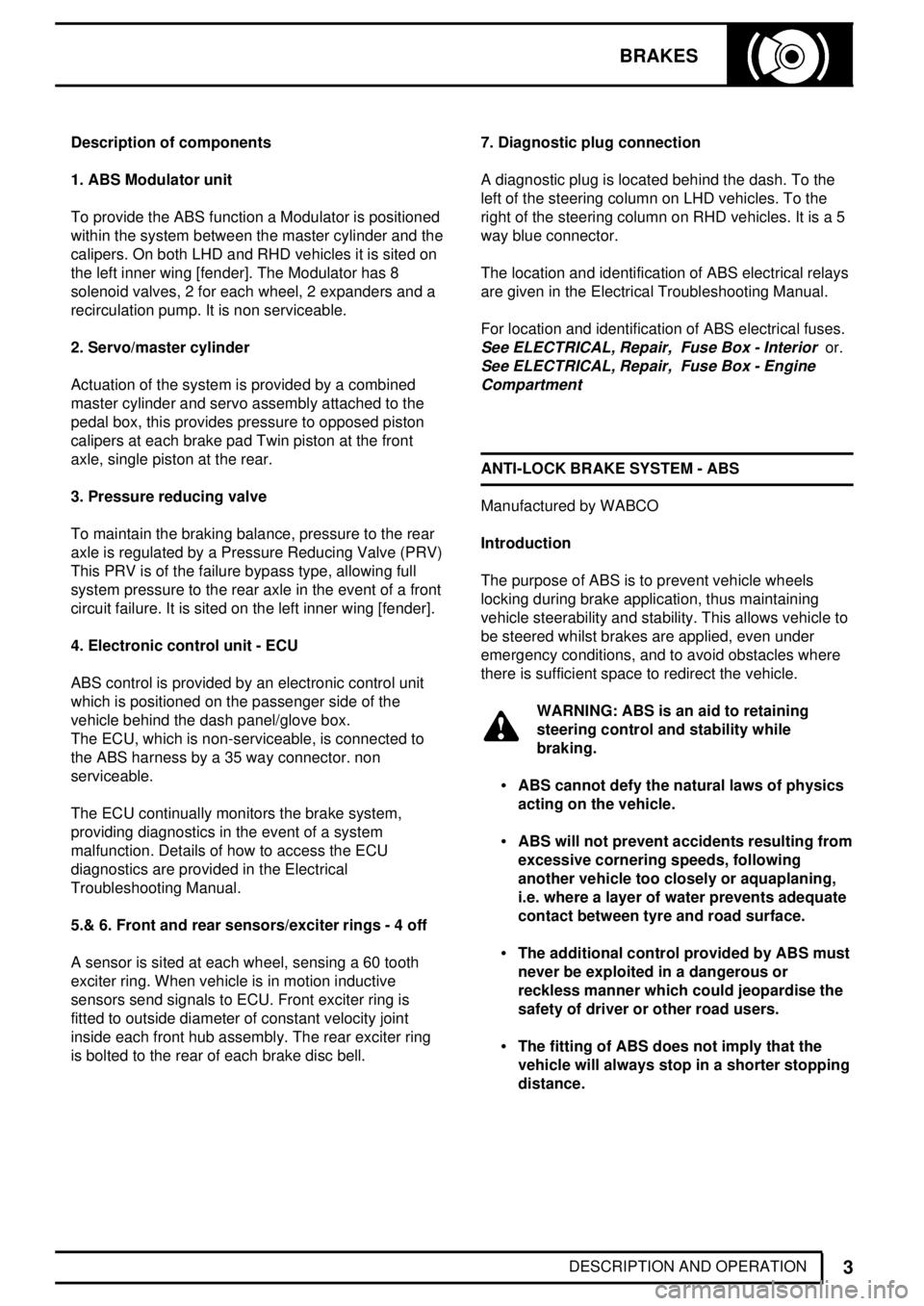
BRAKES
3
DESCRIPTION AND OPERATION Description of components
1. ABS Modulator unit
To provide the ABS function a Modulator is positioned
within the system between the master cylinder and the
calipers. On both LHD and RHD vehicles it is sited on
the left inner wing [fender]. The Modulator has 8
solenoid valves, 2 for each wheel, 2 expanders and a
recirculation pump. It is non serviceable.
2. Servo/master cylinder
Actuation of the system is provided by a combined
master cylinder and servo assembly attached to the
pedal box, this provides pressure to opposed piston
calipers at each brake pad Twin piston at the front
axle, single piston at the rear.
3. Pressure reducing valve
To maintain the braking balance, pressure to the rear
axle is regulated by a Pressure Reducing Valve (PRV)
This PRV is of the failure bypass type, allowing full
system pressure to the rear axle in the event of a front
circuit failure. It is sited on the left inner wing [fender].
4. Electronic control unit - ECU
ABS control is provided by an electronic control unit
which is positioned on the passenger side of the
vehicle behind the dash panel/glove box.
The ECU, which is non-serviceable, is connected to
the ABS harness by a 35 way connector. non
serviceable.
The ECU continually monitors the brake system,
providing diagnostics in the event of a system
malfunction. Details of how to access the ECU
diagnostics are provided in the Electrical
Troubleshooting Manual.
5.& 6. Front and rear sensors/exciter rings - 4 off
A sensor is sited at each wheel, sensing a 60 tooth
exciter ring. When vehicle is in motion inductive
sensors send signals to ECU. Front exciter ring is
fitted to outside diameter of constant velocity joint
inside each front hub assembly. The rear exciter ring
is bolted to the rear of each brake disc bell.7. Diagnostic plug connection
A diagnostic plug is located behind the dash. To the
left of the steering column on LHD vehicles. To the
right of the steering column on RHD vehicles. It is a 5
way blue connector.
The location and identification of ABS electrical relays
are given in the Electrical Troubleshooting Manual.
For location and identification of ABS electrical fuses.
See ELECTRICAL, Repair, Fuse Box - Interioror.
See ELECTRICAL, Repair, Fuse Box - Engine
Compartment
ANTI-LOCK BRAKE SYSTEM - ABS
Manufactured by WABCO
Introduction
The purpose of ABS is to prevent vehicle wheels
locking during brake application, thus maintaining
vehicle steerability and stability. This allows vehicle to
be steered whilst brakes are applied, even under
emergency conditions, and to avoid obstacles where
there is sufficient space to redirect the vehicle.
WARNING: ABS is an aid to retaining
steering control and stability while
braking.
·ABS cannot defy the natural laws of physics
acting on the vehicle.
·ABS will not prevent accidents resulting from
excessive cornering speeds, following
another vehicle too closely or aquaplaning,
i.e. where a layer of water prevents adequate
contact between tyre and road surface.
·The additional control provided by ABS must
never be exploited in a dangerous or
reckless manner which could jeopardise the
safety of driver or other road users.
·The fitting of ABS does not imply that the
vehicle will always stop in a shorter stopping
distance.
Page 595 of 873
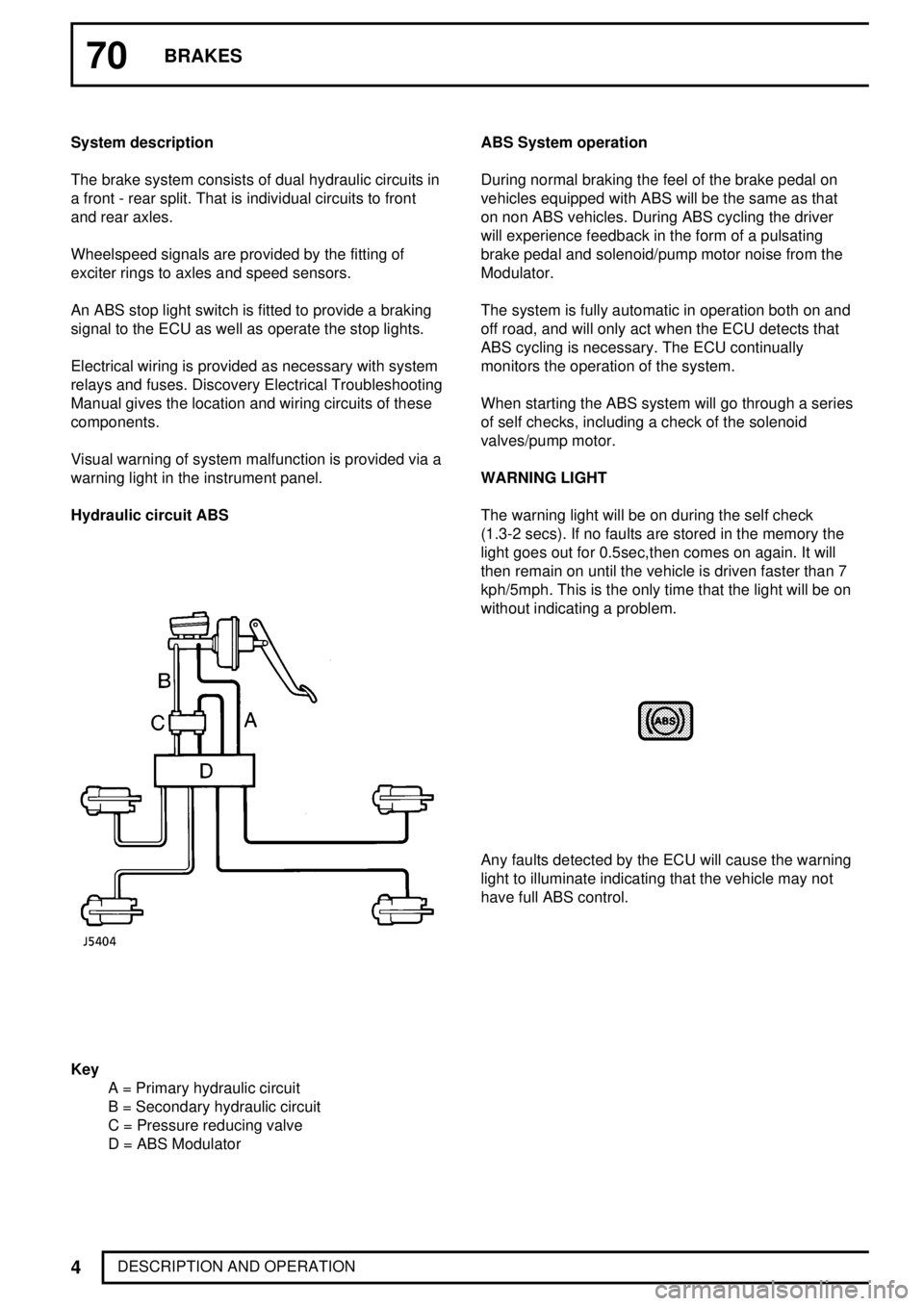
70BRAKES
4
DESCRIPTION AND OPERATION System description
The brake system consists of dual hydraulic circuits in
a front - rear split. That is individual circuits to front
and rear axles.
Wheelspeed signals are provided by the fitting of
exciter rings to axles and speed sensors.
An ABS stop light switch is fitted to provide a braking
signal to the ECU as well as operate the stop lights.
Electrical wiring is provided as necessary with system
relays and fuses. Discovery Electrical Troubleshooting
Manual gives the location and wiring circuits of these
components.
Visual warning of system malfunction is provided via a
warning light in the instrument panel.
Hydraulic circuit ABS
Key
A = Primary hydraulic circuit
B = Secondary hydraulic circuit
C = Pressure reducing valve
D = ABS ModulatorABS System operation
During normal braking the feel of the brake pedal on
vehicles equipped with ABS will be the same as that
on non ABS vehicles. During ABS cycling the driver
will experience feedback in the form of a pulsating
brake pedal and solenoid/pump motor noise from the
Modulator.
The system is fully automatic in operation both on and
off road, and will only act when the ECU detects that
ABS cycling is necessary. The ECU continually
monitors the operation of the system.
When starting the ABS system will go through a series
of self checks, including a check of the solenoid
valves/pump motor.
WARNING LIGHT
The warning light will be on during the self check
(1.3-2 secs). If no faults are stored in the memory the
light goes out for 0.5sec,then comes on again. It will
then remain on until the vehicle is driven faster than 7
kph/5mph. This is the only time that the light will be on
without indicating a problem.
Any faults detected by the ECU will cause the warning
light to illuminate indicating that the vehicle may not
have full ABS control.