relay LAND ROVER DISCOVERY 1995 Workshop Manual
[x] Cancel search | Manufacturer: LAND ROVER, Model Year: 1995, Model line: DISCOVERY, Model: LAND ROVER DISCOVERY 1995Pages: 873, PDF Size: 12.89 MB
Page 9 of 873
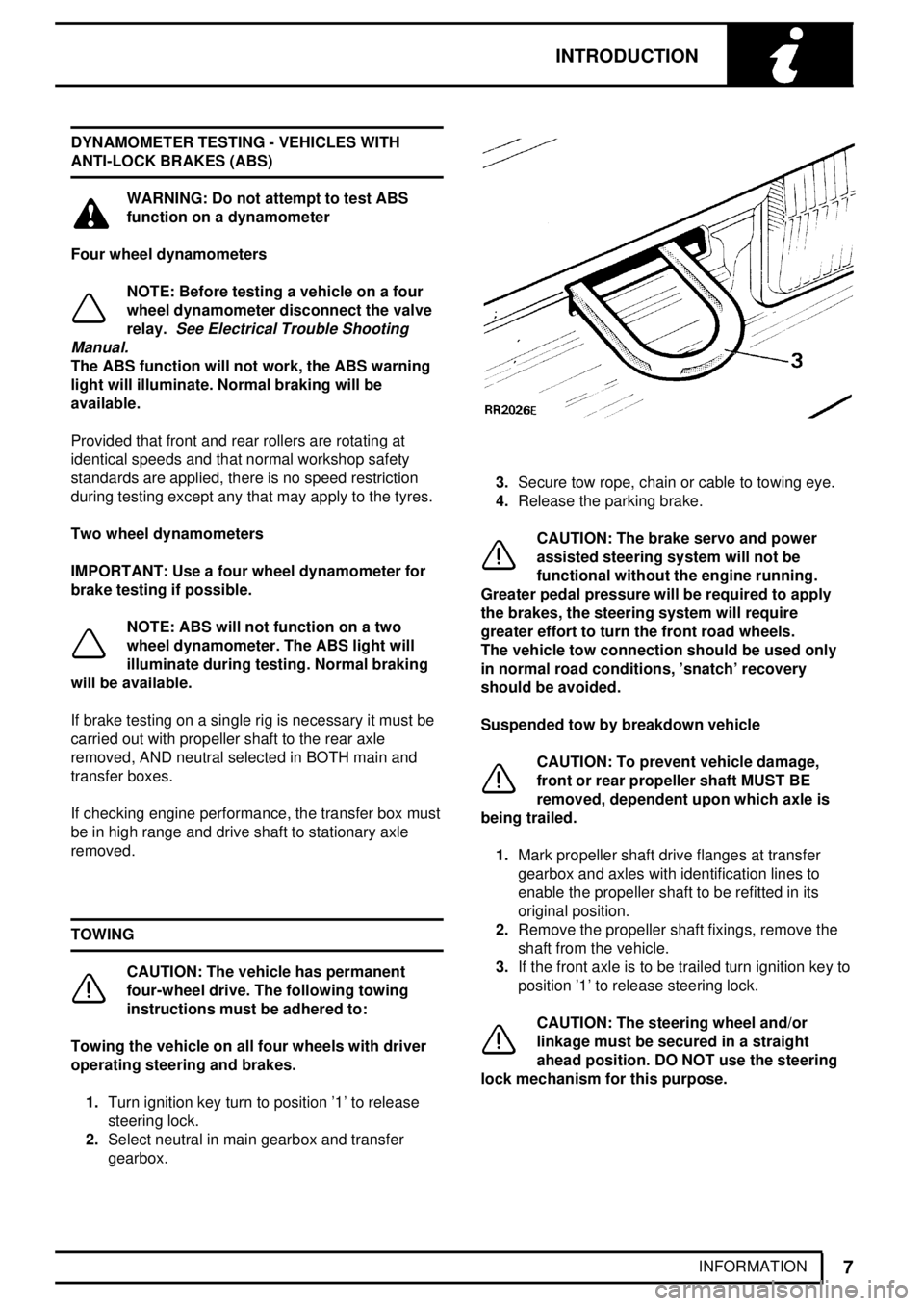
INTRODUCTION
7
INFORMATION DYNAMOMETER TESTING - VEHICLES WITH
ANTI-LOCK BRAKES (ABS)
WARNING: Do not attempt to test ABS
function on a dynamometer
Four wheel dynamometers
NOTE: Before testing a vehicle on a four
wheel dynamometer disconnect the valve
relay.
See Electrical Trouble Shooting
Manual.
The ABS function will not work, the ABS warning
light will illuminate. Normal braking will be
available.
Provided that front and rear rollers are rotating at
identical speeds and that normal workshop safety
standards are applied, there is no speed restriction
during testing except any that may apply to the tyres.
Two wheel dynamometers
IMPORTANT: Use a four wheel dynamometer for
brake testing if possible.
NOTE: ABS will not function on a two
wheel dynamometer. The ABS light will
illuminate during testing. Normal braking
will be available.
If brake testing on a single rig is necessary it must be
carried out with propeller shaft to the rear axle
removed, AND neutral selected in BOTH main and
transfer boxes.
If checking engine performance, the transfer box must
be in high range and drive shaft to stationary axle
removed.
TOWING
CAUTION: The vehicle has permanent
four-wheel drive. The following towing
instructions must be adhered to:
Towing the vehicle on all four wheels with driver
operating steering and brakes.
1.Turn ignition key turn to position '1' to release
steering lock.
2.Select neutral in main gearbox and transfer
gearbox.
3.Secure tow rope, chain or cable to towing eye.
4.Release the parking brake.
CAUTION: The brake servo and power
assisted steering system will not be
functional without the engine running.
Greater pedal pressure will be required to apply
the brakes, the steering system will require
greater effort to turn the front road wheels.
The vehicle tow connection should be used only
in normal road conditions, 'snatch' recovery
should be avoided.
Suspended tow by breakdown vehicle
CAUTION: To prevent vehicle damage,
front or rear propeller shaft MUST BE
removed, dependent upon which axle is
being trailed.
1.Mark propeller shaft drive flanges at transfer
gearbox and axles with identification lines to
enable the propeller shaft to be refitted in its
original position.
2.Remove the propeller shaft fixings, remove the
shaft from the vehicle.
3.If the front axle is to be trailed turn ignition key to
position '1' to release steering lock.
CAUTION: The steering wheel and/or
linkage must be secured in a straight
ahead position. DO NOT use the steering
lock mechanism for this purpose.
Page 13 of 873
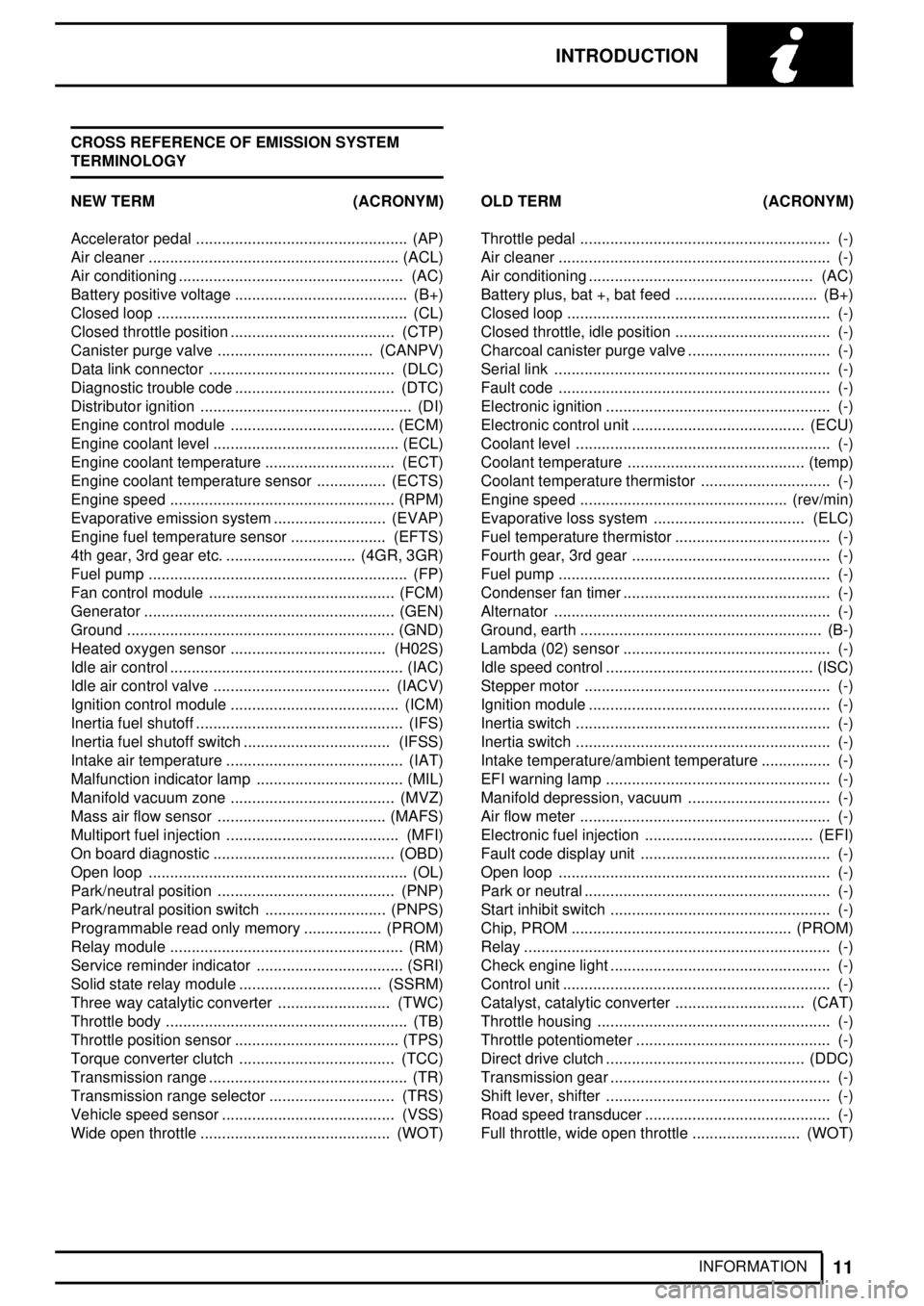
INTRODUCTION
11
INFORMATION CROSS REFERENCE OF EMISSION SYSTEM
TERMINOLOGY
NEW TERM (ACRONYM)
Accelerator pedal (AP).................................................
Air cleaner (ACL)..........................................................
Air conditioning (AC)....................................................
Battery positive voltage (B+)........................................
Closed loop (CL)..........................................................
Closed throttle position (CTP)......................................
Canister purge valve (CANPV)....................................
Data link connector (DLC)...........................................
Diagnostic trouble code (DTC).....................................
Distributor ignition (DI).................................................
Engine control module (ECM)......................................
Engine coolant level (ECL)...........................................
Engine coolant temperature (ECT)..............................
Engine coolant temperature sensor (ECTS)................
Engine speed (RPM)....................................................
Evaporative emission system (EVAP)..........................
Engine fuel temperature sensor (EFTS)......................
4th gear, 3rd gear etc. (4GR, 3GR)..............................
Fuel pump (FP)............................................................
Fan control module (FCM)...........................................
Generator (GEN)..........................................................
Ground (GND)..............................................................
Heated oxygen sensor (H02S)....................................
Idle air control (IAC)......................................................
Idle air control valve (IACV).........................................
Ignition control module (ICM).......................................
Inertia fuel shutoff (IFS)................................................
Inertia fuel shutoff switch (IFSS)..................................
Intake air temperature (IAT).........................................
Malfunction indicator lamp (MIL)..................................
Manifold vacuum zone (MVZ)......................................
Mass air flow sensor (MAFS).......................................
Multiport fuel injection (MFI)........................................
On board diagnostic (OBD)..........................................
Open loop (OL)............................................................
Park/neutral position (PNP).........................................
Park/neutral position switch (PNPS)............................
Programmable read only memory (PROM)..................
Relay module (RM)......................................................
Service reminder indicator (SRI)..................................
Solid state relay module (SSRM).................................
Three way catalytic converter (TWC)..........................
Throttle body (TB)........................................................
Throttle position sensor (TPS)......................................
Torque converter clutch (TCC)....................................
Transmission range (TR)..............................................
Transmission range selector (TRS).............................
Vehicle speed sensor (VSS)........................................
Wide open throttle (WOT)............................................OLD TERM (ACRONYM)
Throttle pedal (-)..........................................................
Air cleaner (-)...............................................................
Air conditioning (AC)....................................................
Battery plus, bat +, bat feed (B+).................................
Closed loop (-).............................................................
Closed throttle, idle position (-)....................................
Charcoal canister purge valve (-).................................
Serial link (-)................................................................
Fault code (-)...............................................................
Electronic ignition (-)....................................................
Electronic control unit (ECU)........................................
Coolant level (-)...........................................................
Coolant temperature (temp).........................................
Coolant temperature thermistor (-)..............................
Engine speed (rev/min)................................................
Evaporative loss system (ELC)...................................
Fuel temperature thermistor (-)....................................
Fourth gear, 3rd gear (-)..............................................
Fuel pump (-)...............................................................
Condenser fan timer (-)................................................
Alternator (-)................................................................
Ground, earth (B-)........................................................
Lambda (02) sensor (-)................................................
Idle speed control (ISC)................................................
Stepper motor (-).........................................................
Ignition module (-)........................................................
Inertia switch (-)...........................................................
Inertia switch (-)...........................................................
Intake temperature/ambient temperature (-)................
EFI warning lamp (-)....................................................
Manifold depression, vacuum (-).................................
Air flow meter (-)..........................................................
Electronic fuel injection (EFI).......................................
Fault code display unit (-)............................................
Open loop (-)...............................................................
Park or neutral (-).........................................................
Start inhibit switch (-)...................................................
Chip, PROM (PROM)...................................................
Relay (-).......................................................................
Check engine light (-)...................................................
Control unit (-)..............................................................
Catalyst, catalytic converter (CAT)..............................
Throttle housing (-)......................................................
Throttle potentiometer (-).............................................
Direct drive clutch (DDC)..............................................
Transmission gear (-)...................................................
Shift lever, shifter (-)....................................................
Road speed transducer (-)...........................................
Full throttle, wide open throttle (WOT).........................
Page 79 of 873
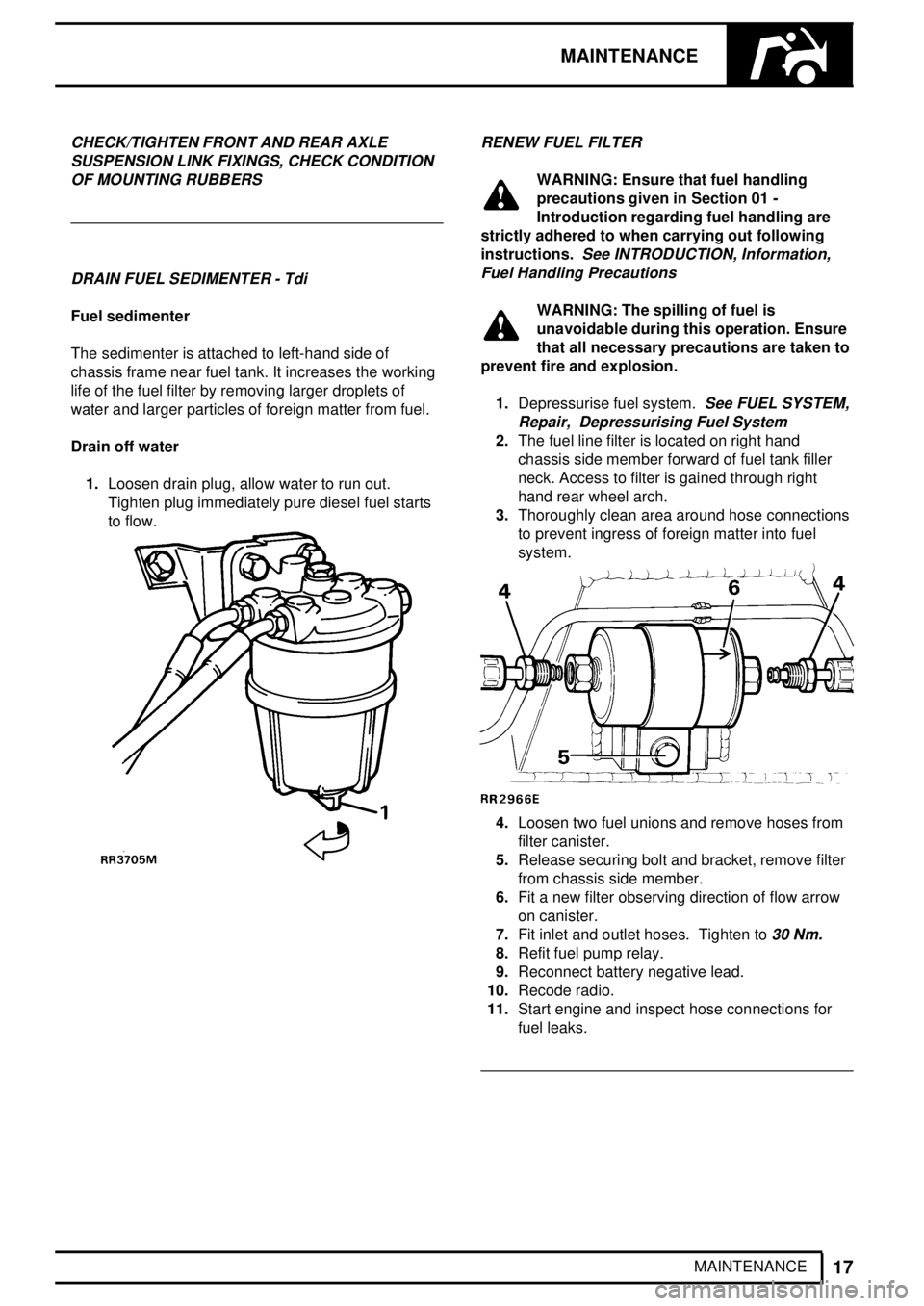
MAINTENANCE
17
MAINTENANCE
CHECK/TIGHTEN FRONT AND REAR AXLE
SUSPENSION LINK FIXINGS, CHECK CONDITION
OF MOUNTING RUBBERS
DRAIN FUEL SEDIMENTER - Tdi
Fuel sedimenter
The sedimenter is attached to left-hand side of
chassis frame near fuel tank. It increases the working
life of the fuel filter by removing larger droplets of
water and larger particles of foreign matter from fuel.
Drain off water
1.Loosen drain plug, allow water to run out.
Tighten plug immediately pure diesel fuel starts
to flow.
RENEW FUEL FILTER
WARNING: Ensure that fuel handling
precautions given in Section 01 -
Introduction regarding fuel handling are
strictly adhered to when carrying out following
instructions.
See INTRODUCTION, Information,
Fuel Handling Precautions
WARNING: The spilling of fuel is
unavoidable during this operation. Ensure
that all necessary precautions are taken to
prevent fire and explosion.
1.Depressurise fuel system.
See FUEL SYSTEM,
Repair, Depressurising Fuel System
2.The fuel line filter is located on right hand
chassis side member forward of fuel tank filler
neck. Access to filter is gained through right
hand rear wheel arch.
3.Thoroughly clean area around hose connections
to prevent ingress of foreign matter into fuel
system.
4.Loosen two fuel unions and remove hoses from
filter canister.
5.Release securing bolt and bracket, remove filter
from chassis side member.
6.Fit a new filter observing direction of flow arrow
on canister.
7.Fit inlet and outlet hoses. Tighten to
30 Nm.
8.Refit fuel pump relay.
9.Reconnect battery negative lead.
10.Recode radio.
11.Start engine and inspect hose connections for
fuel leaks.
Page 84 of 873
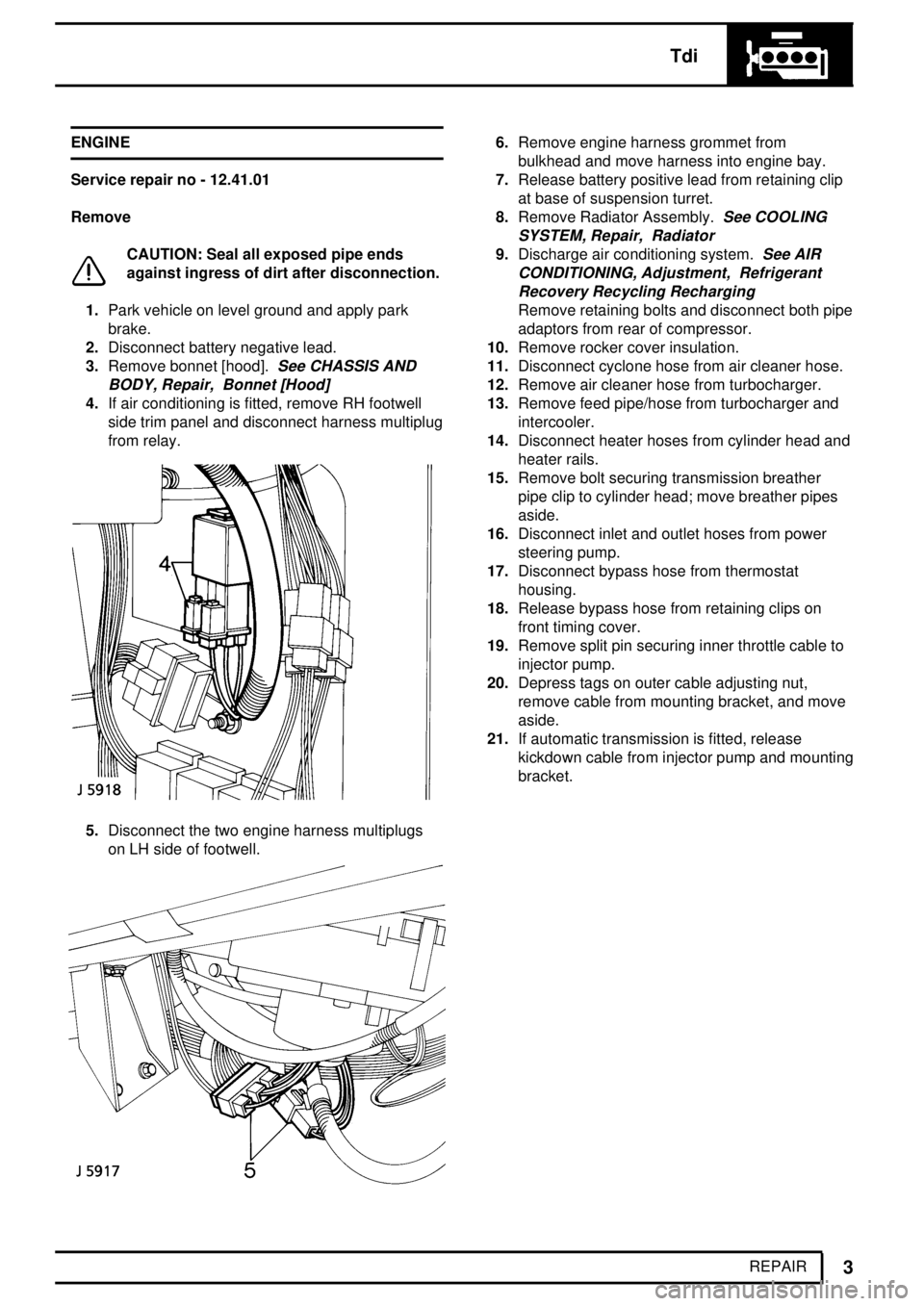
Tdi
3
REPAIR ENGINE
Service repair no - 12.41.01
Remove
CAUTION: Seal all exposed pipe ends
against ingress of dirt after disconnection.
1.Park vehicle on level ground and apply park
brake.
2.Disconnect battery negative lead.
3.Remove bonnet [hood].
See CHASSIS AND
BODY, Repair, Bonnet [Hood]
4.If air conditioning is fitted, remove RH footwell
side trim panel and disconnect harness multiplug
from relay.
5.Disconnect the two engine harness multiplugs
on LH side of footwell.
6.Remove engine harness grommet from
bulkhead and move harness into engine bay.
7.Release battery positive lead from retaining clip
at base of suspension turret.
8.Remove Radiator Assembly.
See COOLING
SYSTEM, Repair, Radiator
9.Discharge air conditioning system.See AIR
CONDITIONING, Adjustment, Refrigerant
Recovery Recycling Recharging
Remove retaining bolts and disconnect both pipe
adaptors from rear of compressor.
10.Remove rocker cover insulation.
11.Disconnect cyclone hose from air cleaner hose.
12.Remove air cleaner hose from turbocharger.
13.Remove feed pipe/hose from turbocharger and
intercooler.
14.Disconnect heater hoses from cylinder head and
heater rails.
15.Remove bolt securing transmission breather
pipe clip to cylinder head; move breather pipes
aside.
16.Disconnect inlet and outlet hoses from power
steering pump.
17.Disconnect bypass hose from thermostat
housing.
18.Release bypass hose from retaining clips on
front timing cover.
19.Remove split pin securing inner throttle cable to
injector pump.
20.Depress tags on outer cable adjusting nut,
remove cable from mounting bracket, and move
aside.
21.If automatic transmission is fitted, release
kickdown cable from injector pump and mounting
bracket.
Page 209 of 873
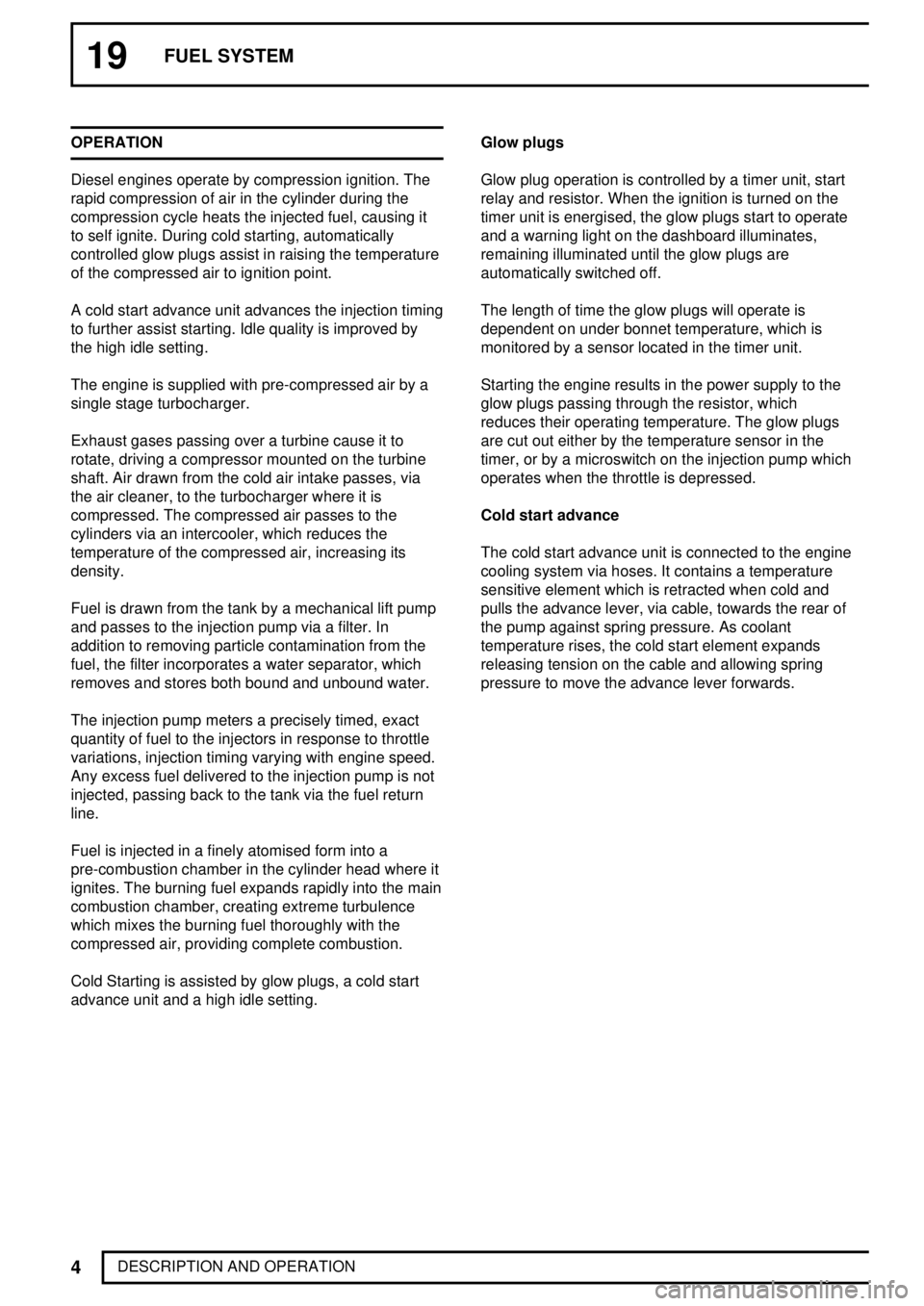
19FUEL SYSTEM
4
DESCRIPTION AND OPERATION OPERATION
Diesel engines operate by compression ignition. The
rapid compression of air in the cylinder during the
compression cycle heats the injected fuel, causing it
to self ignite. During cold starting, automatically
controlled glow plugs assist in raising the temperature
of the compressed air to ignition point.
A cold start advance unit advances the injection timing
to further assist starting. Idle quality is improved by
the high idle setting.
The engine is supplied with pre-compressed air by a
single stage turbocharger.
Exhaust gases passing over a turbine cause it to
rotate, driving a compressor mounted on the turbine
shaft. Air drawn from the cold air intake passes, via
the air cleaner, to the turbocharger where it is
compressed. The compressed air passes to the
cylinders via an intercooler, which reduces the
temperature of the compressed air, increasing its
density.
Fuel is drawn from the tank by a mechanical lift pump
and passes to the injection pump via a filter. In
addition to removing particle contamination from the
fuel, the filter incorporates a water separator, which
removes and stores both bound and unbound water.
The injection pump meters a precisely timed, exact
quantity of fuel to the injectors in response to throttle
variations, injection timing varying with engine speed.
Any excess fuel delivered to the injection pump is not
injected, passing back to the tank via the fuel return
line.
Fuel is injected in a finely atomised form into a
pre-combustion chamber in the cylinder head where it
ignites. The burning fuel expands rapidly into the main
combustion chamber, creating extreme turbulence
which mixes the burning fuel thoroughly with the
compressed air, providing complete combustion.
Cold Starting is assisted by glow plugs, a cold start
advance unit and a high idle setting.Glow plugs
Glow plug operation is controlled by a timer unit, start
relay and resistor. When the ignition is turned on the
timer unit is energised, the glow plugs start to operate
and a warning light on the dashboard illuminates,
remaining illuminated until the glow plugs are
automatically switched off.
The length of time the glow plugs will operate is
dependent on under bonnet temperature, which is
monitored by a sensor located in the timer unit.
Starting the engine results in the power supply to the
glow plugs passing through the resistor, which
reduces their operating temperature. The glow plugs
are cut out either by the temperature sensor in the
timer, or by a microswitch on the injection pump which
operates when the throttle is depressed.
Cold start advance
The cold start advance unit is connected to the engine
cooling system via hoses. It contains a temperature
sensitive element which is retracted when cold and
pulls the advance lever, via cable, towards the rear of
the pump against spring pressure. As coolant
temperature rises, the cold start element expands
releasing tension on the cable and allowing spring
pressure to move the advance lever forwards.
Page 214 of 873
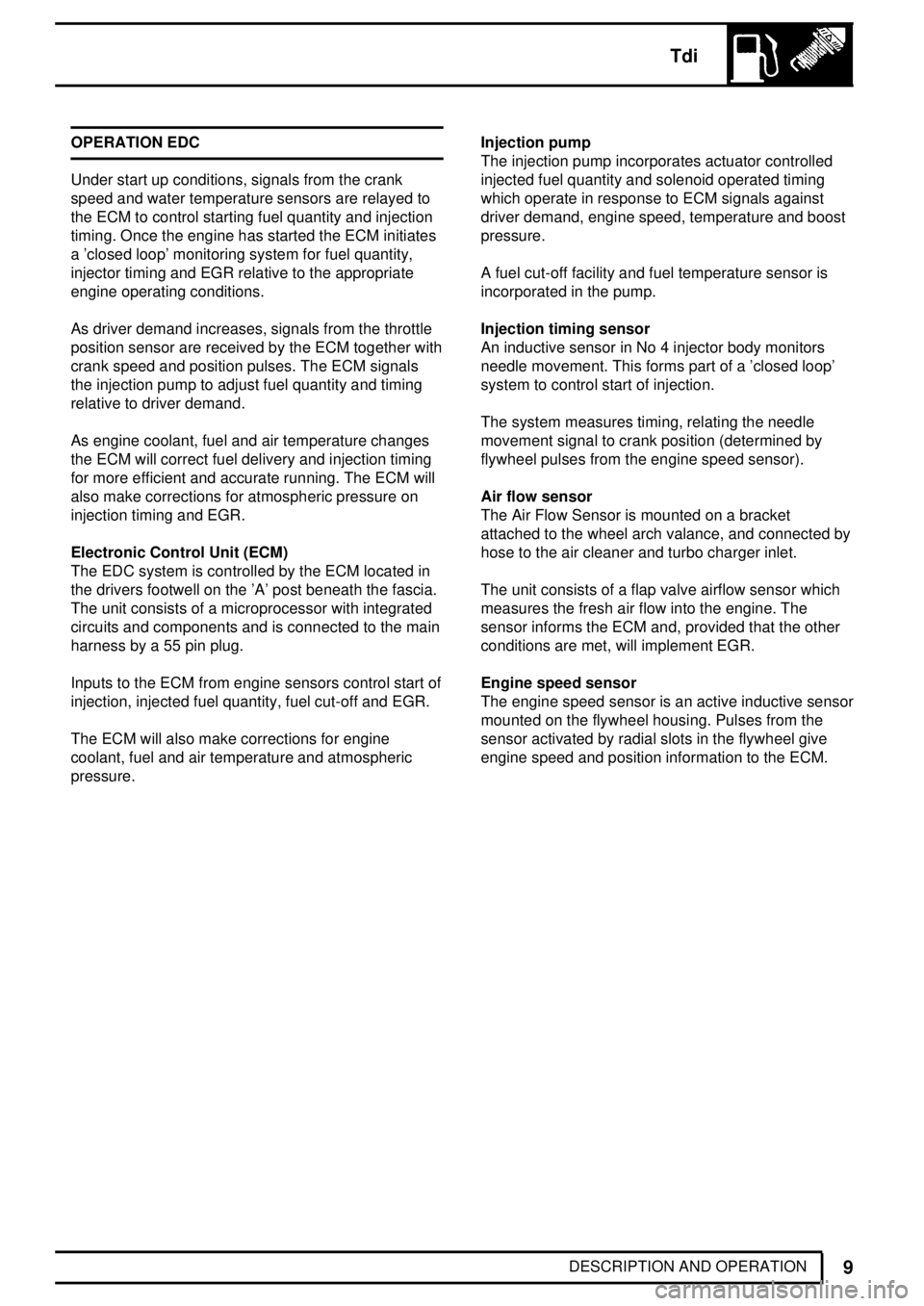
Tdi
9
DESCRIPTION AND OPERATION OPERATION EDC
Under start up conditions, signals from the crank
speed and water temperature sensors are relayed to
the ECM to control starting fuel quantity and injection
timing. Once the engine has started the ECM initiates
a 'closed loop' monitoring system for fuel quantity,
injector timing and EGR relative to the appropriate
engine operating conditions.
As driver demand increases, signals from the throttle
position sensor are received by the ECM together with
crank speed and position pulses. The ECM signals
the injection pump to adjust fuel quantity and timing
relative to driver demand.
As engine coolant, fuel and air temperature changes
the ECM will correct fuel delivery and injection timing
for more efficient and accurate running. The ECM will
also make corrections for atmospheric pressure on
injection timing and EGR.
Electronic Control Unit (ECM)
The EDC system is controlled by the ECM located in
the drivers footwell on the 'A' post beneath the fascia.
The unit consists of a microprocessor with integrated
circuits and components and is connected to the main
harness by a 55 pin plug.
Inputs to the ECM from engine sensors control start of
injection, injected fuel quantity, fuel cut-off and EGR.
The ECM will also make corrections for engine
coolant, fuel and air temperature and atmospheric
pressure.Injection pump
The injection pump incorporates actuator controlled
injected fuel quantity and solenoid operated timing
which operate in response to ECM signals against
driver demand, engine speed, temperature and boost
pressure.
A fuel cut-off facility and fuel temperature sensor is
incorporated in the pump.
Injection timing sensor
An inductive sensor in No 4 injector body monitors
needle movement. This forms part of a 'closed loop'
system to control start of injection.
The system measures timing, relating the needle
movement signal to crank position (determined by
flywheel pulses from the engine speed sensor).
Air flow sensor
The Air Flow Sensor is mounted on a bracket
attached to the wheel arch valance, and connected by
hose to the air cleaner and turbo charger inlet.
The unit consists of a flap valve airflow sensor which
measures the fresh air flow into the engine. The
sensor informs the ECM and, provided that the other
conditions are met, will implement EGR.
Engine speed sensor
The engine speed sensor is an active inductive sensor
mounted on the flywheel housing. Pulses from the
sensor activated by radial slots in the flywheel give
engine speed and position information to the ECM.
Page 215 of 873
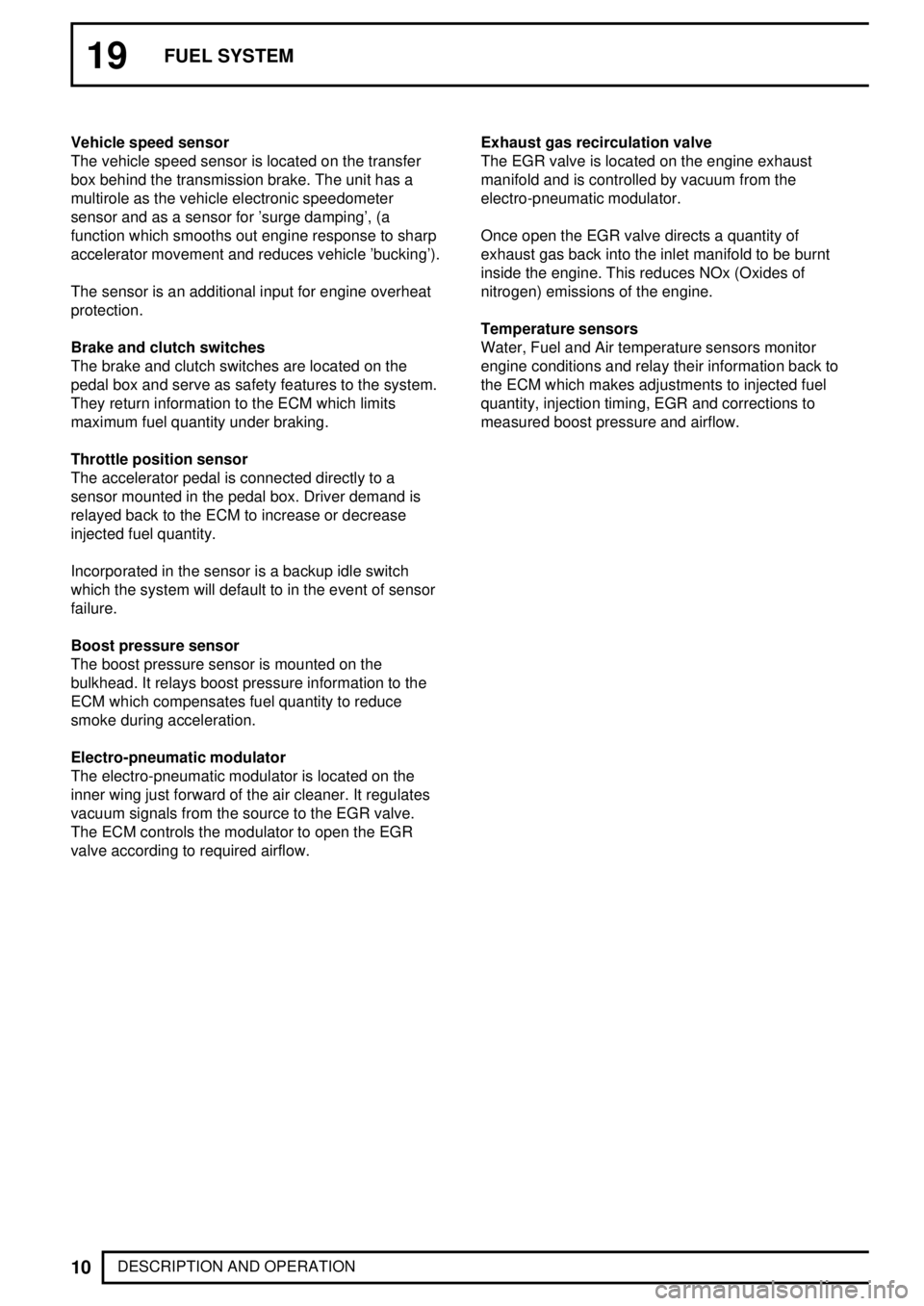
19FUEL SYSTEM
10
DESCRIPTION AND OPERATION Vehicle speed sensor
The vehicle speed sensor is located on the transfer
box behind the transmission brake. The unit has a
multirole as the vehicle electronic speedometer
sensor and as a sensor for 'surge damping', (a
function which smooths out engine response to sharp
accelerator movement and reduces vehicle 'bucking').
The sensor is an additional input for engine overheat
protection.
Brake and clutch switches
The brake and clutch switches are located on the
pedal box and serve as safety features to the system.
They return information to the ECM which limits
maximum fuel quantity under braking.
Throttle position sensor
The accelerator pedal is connected directly to a
sensor mounted in the pedal box. Driver demand is
relayed back to the ECM to increase or decrease
injected fuel quantity.
Incorporated in the sensor is a backup idle switch
which the system will default to in the event of sensor
failure.
Boost pressure sensor
The boost pressure sensor is mounted on the
bulkhead. It relays boost pressure information to the
ECM which compensates fuel quantity to reduce
smoke during acceleration.
Electro-pneumatic modulator
The electro-pneumatic modulator is located on the
inner wing just forward of the air cleaner. It regulates
vacuum signals from the source to the EGR valve.
The ECM controls the modulator to open the EGR
valve according to required airflow.Exhaust gas recirculation valve
The EGR valve is located on the engine exhaust
manifold and is controlled by vacuum from the
electro-pneumatic modulator.
Once open the EGR valve directs a quantity of
exhaust gas back into the inlet manifold to be burnt
inside the engine. This reduces NOx (Oxides of
nitrogen) emissions of the engine.
Temperature sensors
Water, Fuel and Air temperature sensors monitor
engine conditions and relay their information back to
the ECM which makes adjustments to injected fuel
quantity, injection timing, EGR and corrections to
measured boost pressure and airflow.
Page 239 of 873
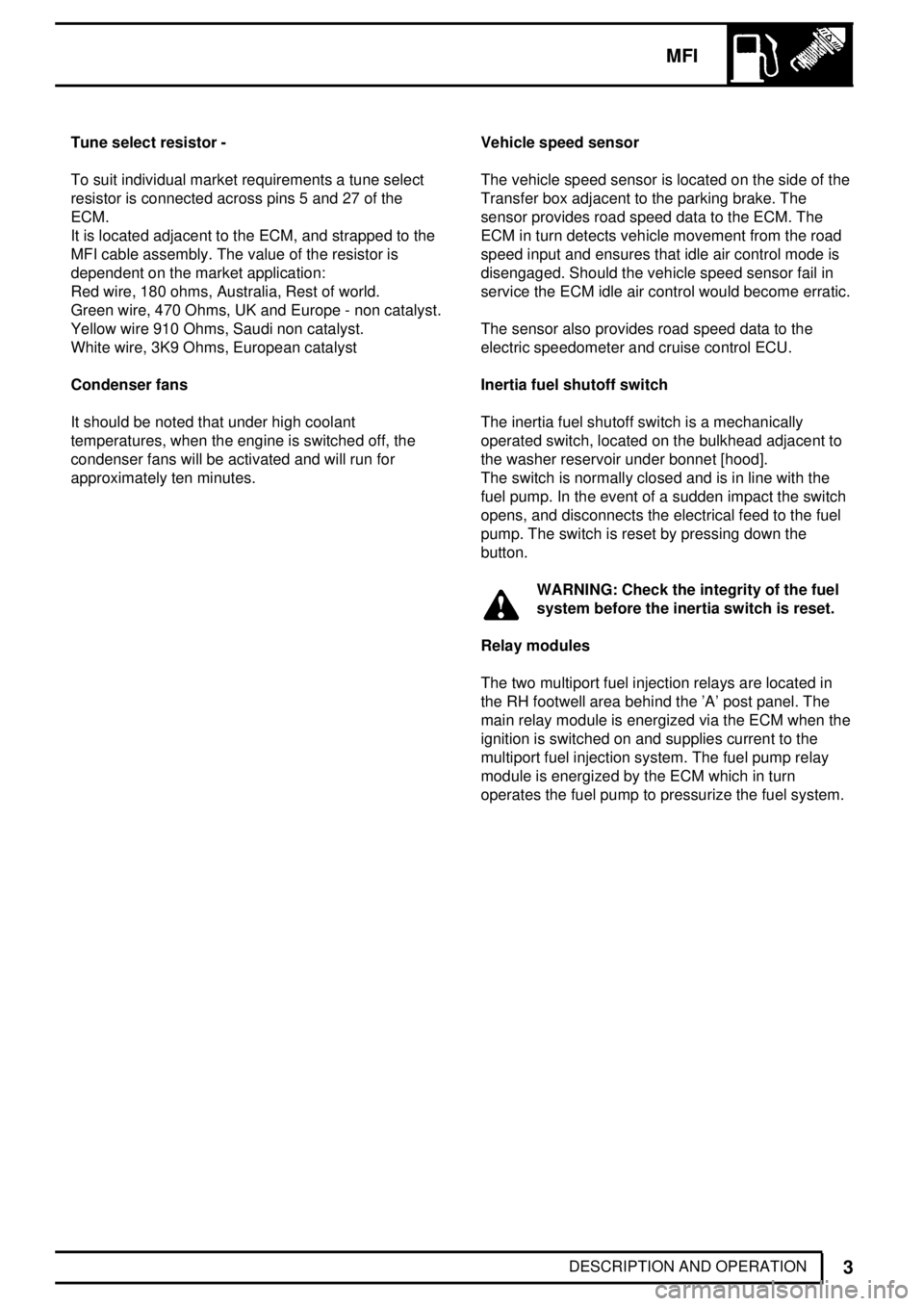
MFI
3
DESCRIPTION AND OPERATION Tune select resistor -
To suit individual market requirements a tune select
resistor is connected across pins 5 and 27 of the
ECM.
It is located adjacent to the ECM, and strapped to the
MFI cable assembly. The value of the resistor is
dependent on the market application:
Red wire, 180 ohms, Australia, Rest of world.
Green wire, 470 Ohms, UK and Europe - non catalyst.
Yellow wire 910 Ohms, Saudi non catalyst.
White wire, 3K9 Ohms, European catalyst
Condenser fans
It should be noted that under high coolant
temperatures, when the engine is switched off, the
condenser fans will be activated and will run for
approximately ten minutes.Vehicle speed sensor
The vehicle speed sensor is located on the side of the
Transfer box adjacent to the parking brake. The
sensor provides road speed data to the ECM. The
ECM in turn detects vehicle movement from the road
speed input and ensures that idle air control mode is
disengaged. Should the vehicle speed sensor fail in
service the ECM idle air control would become erratic.
The sensor also provides road speed data to the
electric speedometer and cruise control ECU.
Inertia fuel shutoff switch
The inertia fuel shutoff switch is a mechanically
operated switch, located on the bulkhead adjacent to
the washer reservoir under bonnet [hood].
The switch is normally closed and is in line with the
fuel pump. In the event of a sudden impact the switch
opens, and disconnects the electrical feed to the fuel
pump. The switch is reset by pressing down the
button.
WARNING: Check the integrity of the fuel
system before the inertia switch is reset.
Relay modules
The two multiport fuel injection relays are located in
the RH footwell area behind the 'A' post panel. The
main relay module is energized via the ECM when the
ignition is switched on and supplies current to the
multiport fuel injection system. The fuel pump relay
module is energized by the ECM which in turn
operates the fuel pump to pressurize the fuel system.
Page 242 of 873
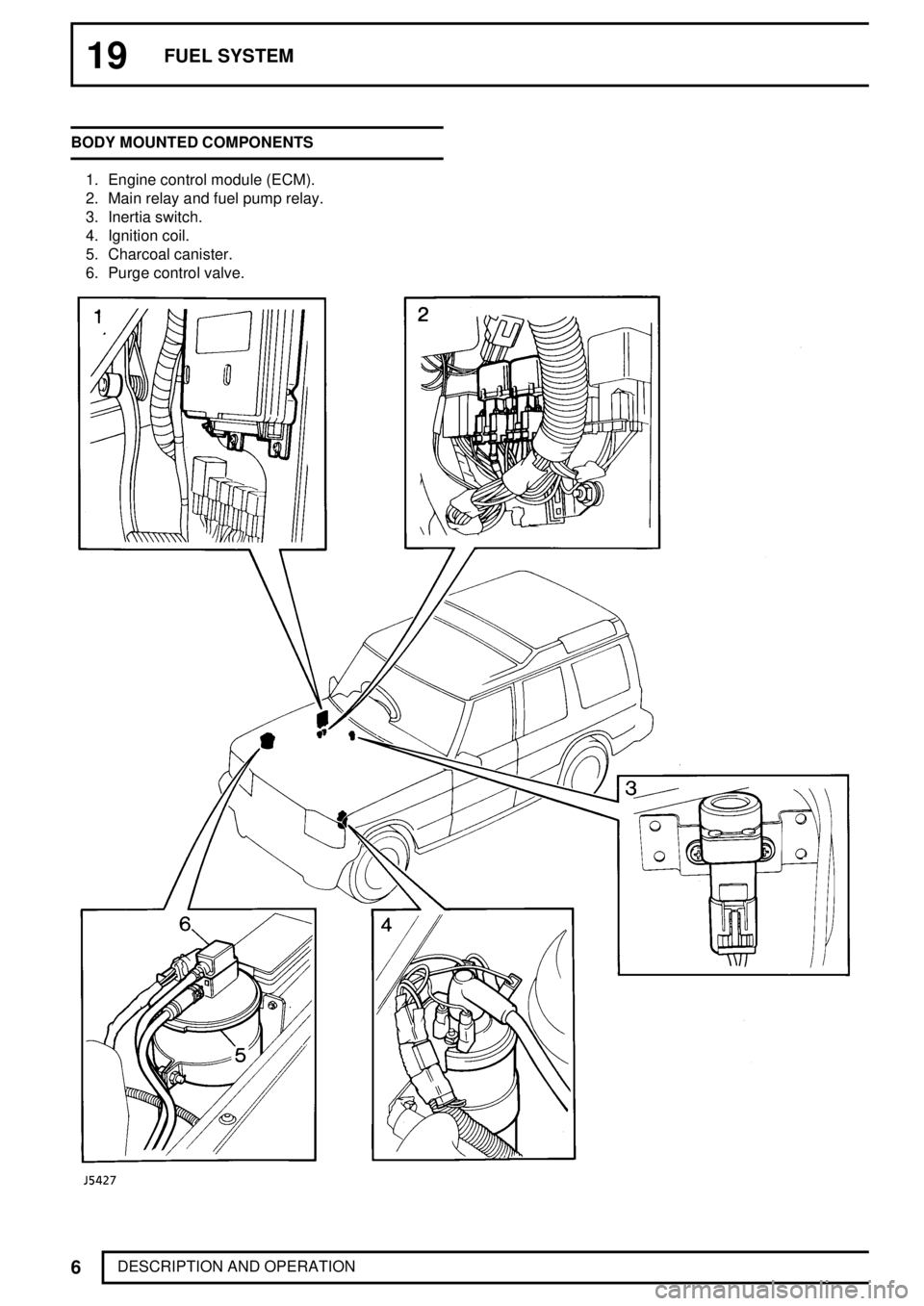
19FUEL SYSTEM
6
DESCRIPTION AND OPERATION BODY MOUNTED COMPONENTS
1. Engine control module (ECM).
2. Main relay and fuel pump relay.
3. Inertia switch.
4. Ignition coil.
5. Charcoal canister.
6. Purge control valve.
Page 246 of 873
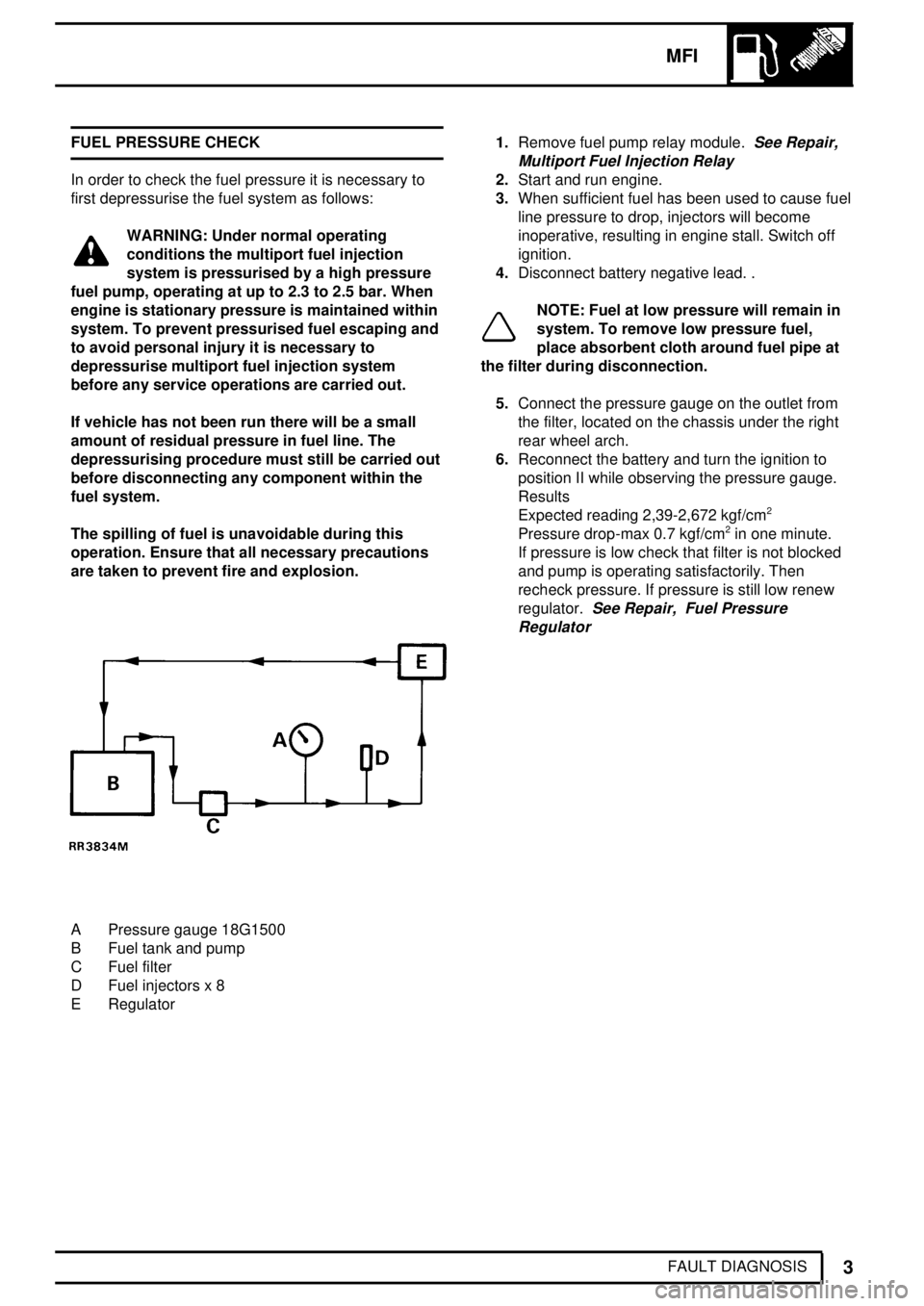
MFI
3
FAULT DIAGNOSIS FUEL PRESSURE CHECK
In order to check the fuel pressure it is necessary to
first depressurise the fuel system as follows:
WARNING: Under normal operating
conditions the multiport fuel injection
system is pressurised by a high pressure
fuel pump, operating at up to 2.3 to 2.5 bar. When
engine is stationary pressure is maintained within
system. To prevent pressurised fuel escaping and
to avoid personal injury it is necessary to
depressurise multiport fuel injection system
before any service operations are carried out.
If vehicle has not been run there will be a small
amount of residual pressure in fuel line. The
depressurising procedure must still be carried out
before disconnecting any component within the
fuel system.
The spilling of fuel is unavoidable during this
operation. Ensure that all necessary precautions
are taken to prevent fire and explosion.
A Pressure gauge 18G1500
B Fuel tank and pump
C Fuel filter
D Fuel injectors x 8
E Regulator1.Remove fuel pump relay module.
See Repair,
Multiport Fuel Injection Relay
2.Start and run engine.
3.When sufficient fuel has been used to cause fuel
line pressure to drop, injectors will become
inoperative, resulting in engine stall. Switch off
ignition.
4.Disconnect battery negative lead. .
NOTE: Fuel at low pressure will remain in
system. To remove low pressure fuel,
place absorbent cloth around fuel pipe at
the filter during disconnection.
5.Connect the pressure gauge on the outlet from
the filter, located on the chassis under the right
rear wheel arch.
6.Reconnect the battery and turn the ignition to
position II while observing the pressure gauge.
Results
Expected reading 2,39-2,672 kgf/cm
2
Pressure drop-max 0.7 kgf/cm2in one minute.
If pressure is low check that filter is not blocked
and pump is operating satisfactorily. Then
recheck pressure. If pressure is still low renew
regulator.
See Repair, Fuel Pressure
Regulator