LAND ROVER DISCOVERY 1995 Workshop Manual
Manufacturer: LAND ROVER, Model Year: 1995, Model line: DISCOVERY, Model: LAND ROVER DISCOVERY 1995Pages: 873, PDF Size: 12.89 MB
Page 431 of 873
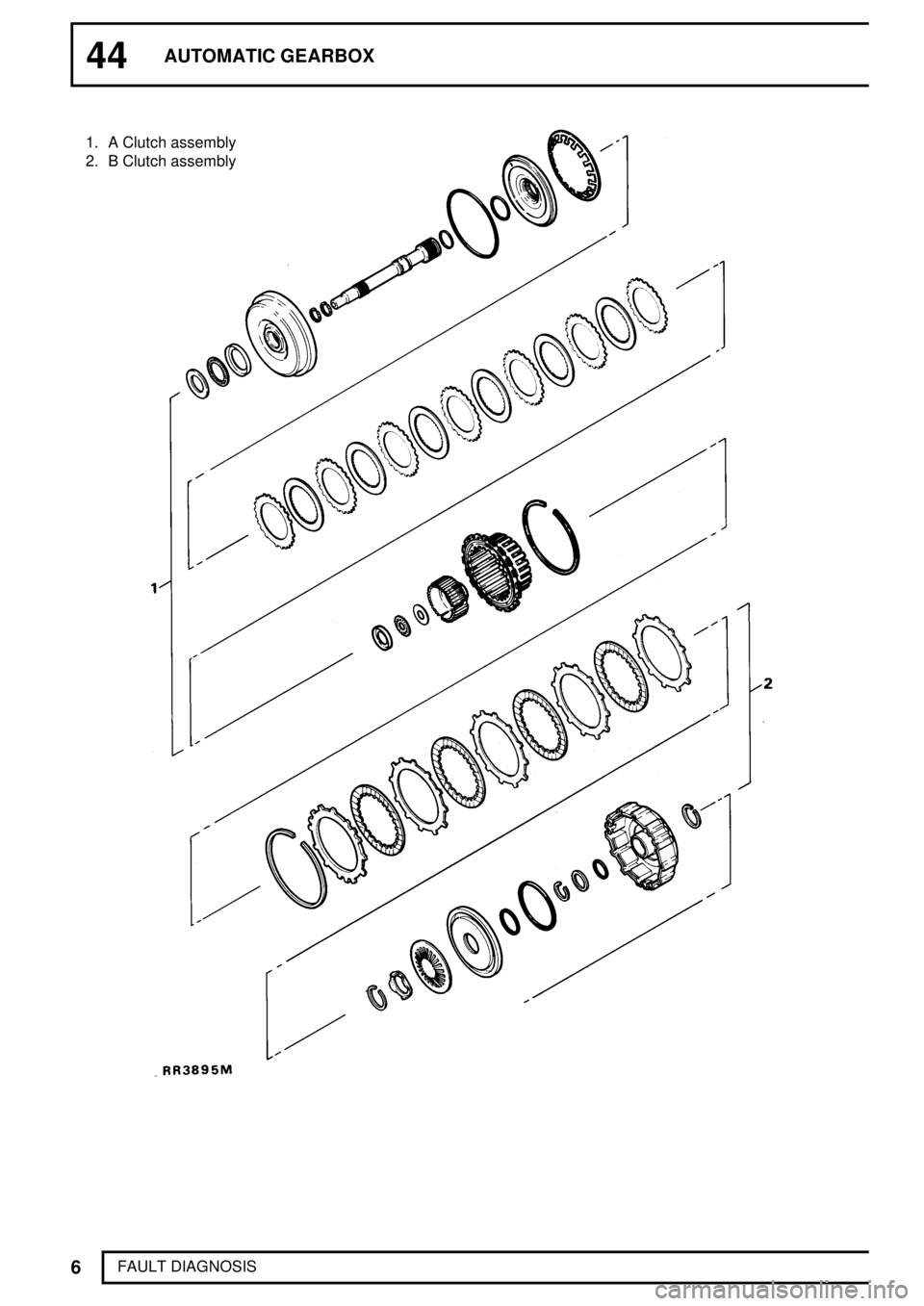
44AUTOMATIC GEARBOX
6
FAULT DIAGNOSIS 1. A Clutch assembly
2. B Clutch assembly
Page 432 of 873
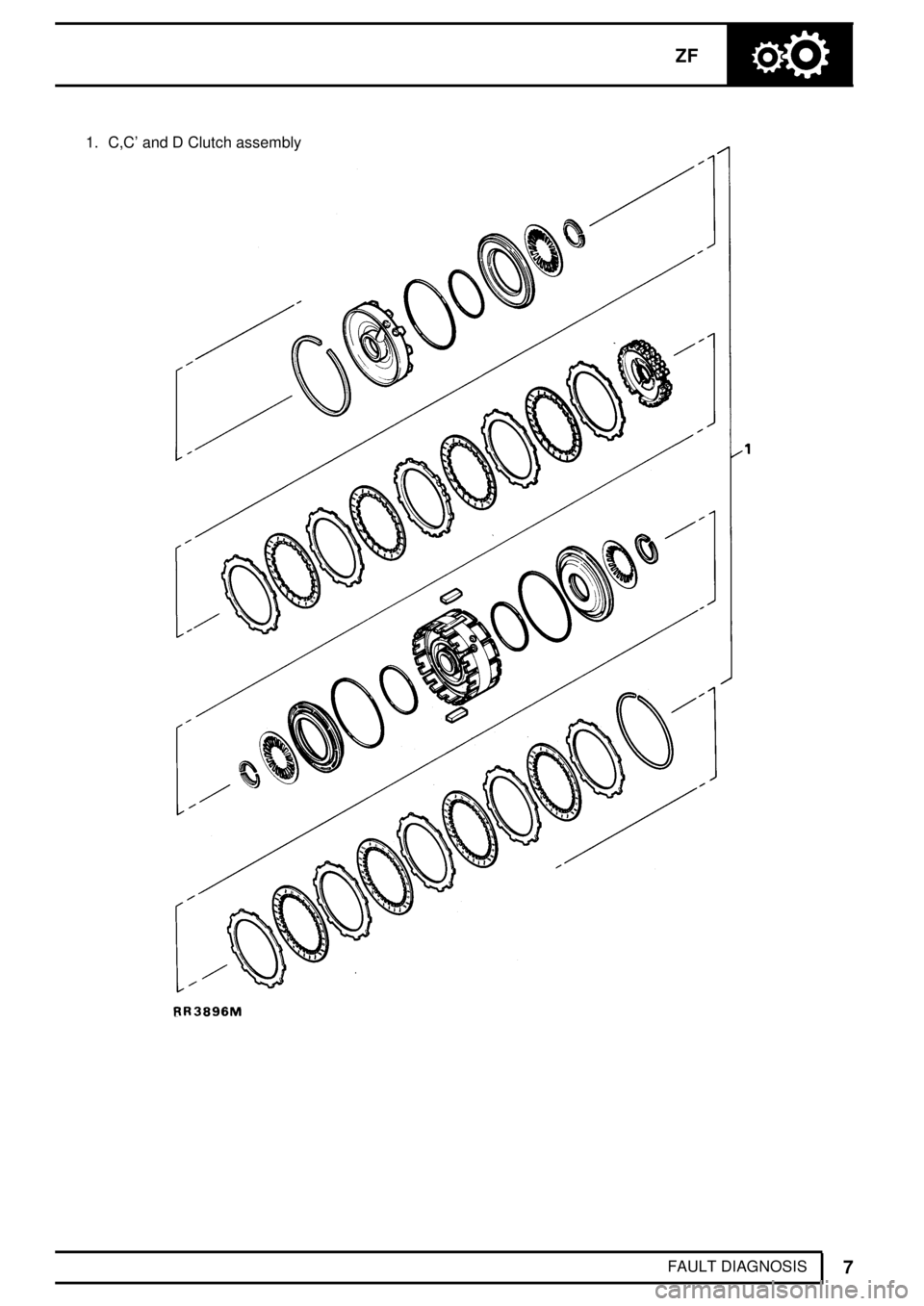
ZF
7
FAULT DIAGNOSIS 1. C,C' and D Clutch assembly
Page 433 of 873
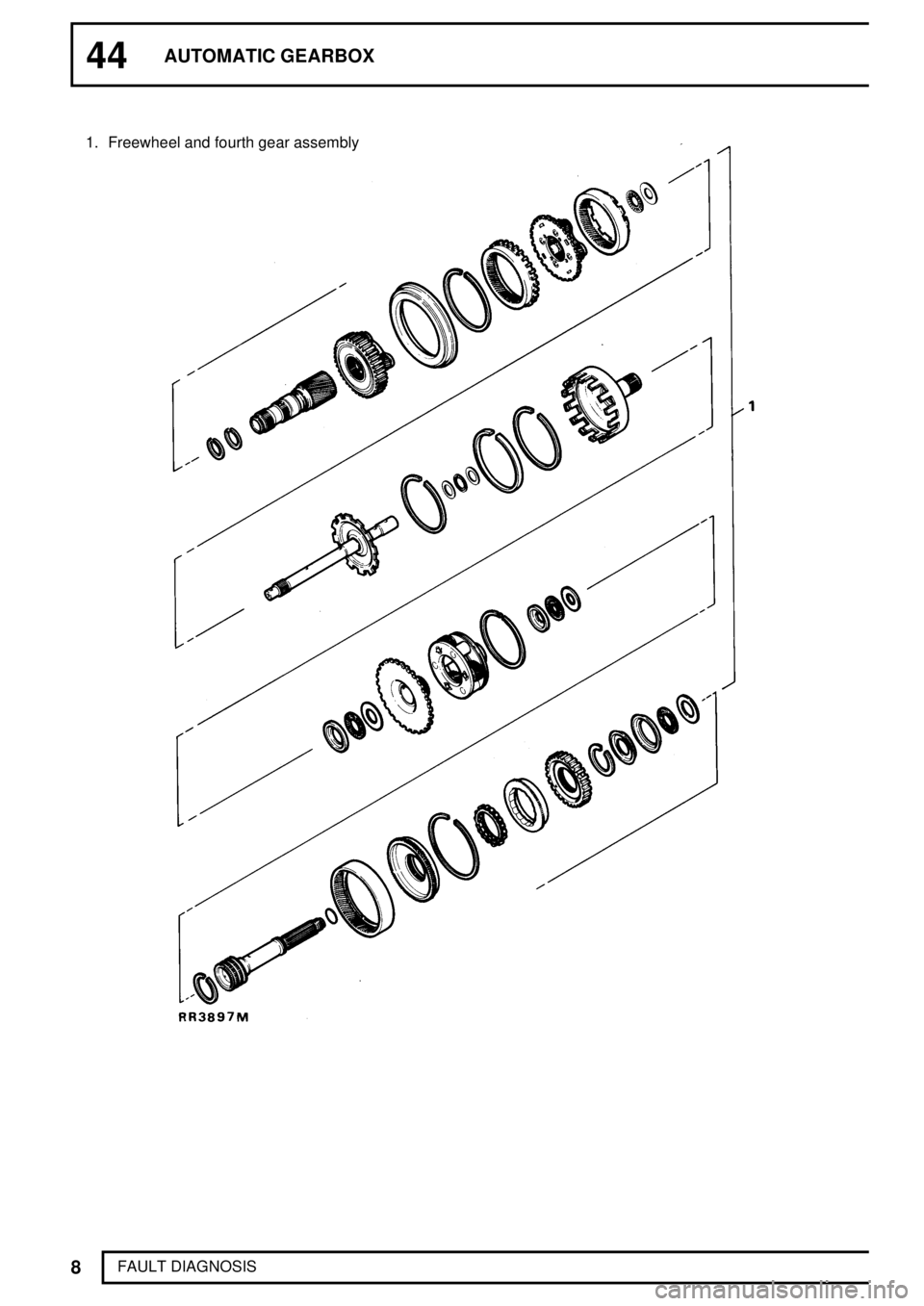
44AUTOMATIC GEARBOX
8
FAULT DIAGNOSIS 1. Freewheel and fourth gear assembly
Page 434 of 873
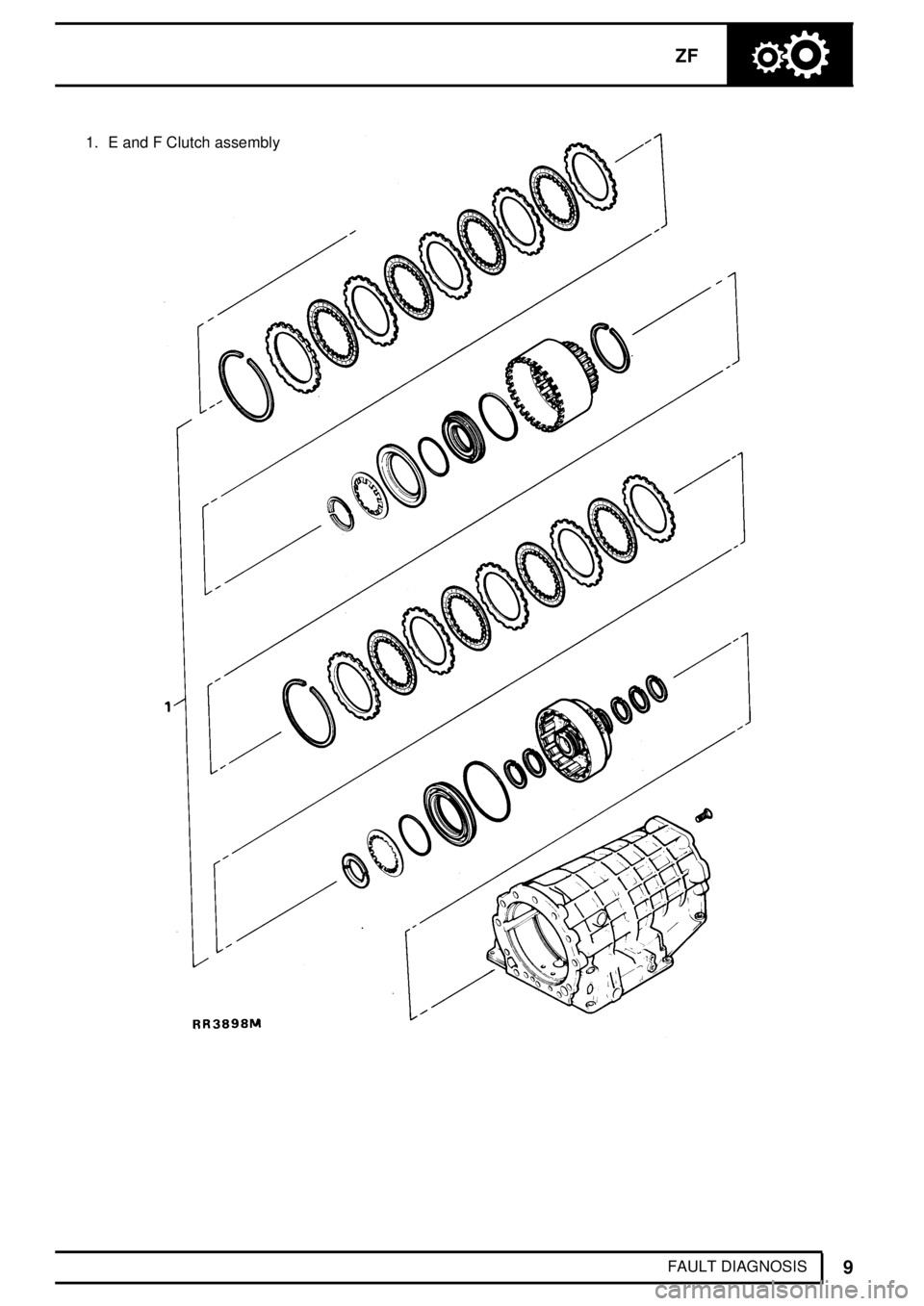
ZF
9
FAULT DIAGNOSIS 1. E and F Clutch assembly
Page 435 of 873
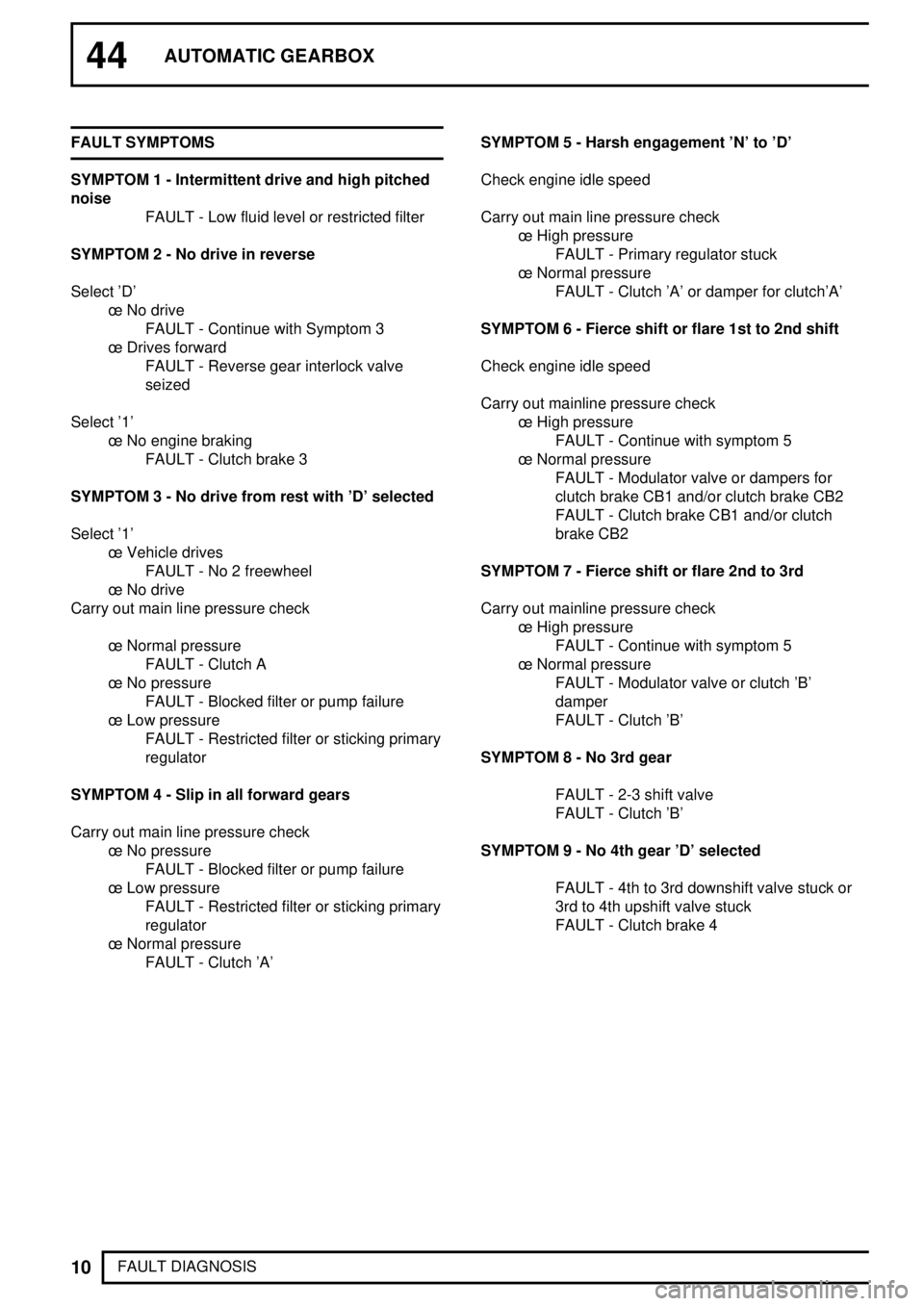
44AUTOMATIC GEARBOX
10
FAULT DIAGNOSIS FAULT SYMPTOMS
SYMPTOM 1 - Intermittent drive and high pitched
noise
FAULT - Low fluid level or restricted filter
SYMPTOM 2 - No drive in reverse
Select 'D'
ú No drive
FAULT - Continue with Symptom 3
ú Drives forward
FAULT - Reverse gear interlock valve
seized
Select '1'
ú No engine braking
FAULT - Clutch brake 3
SYMPTOM 3 - No drive from rest with 'D' selected
Select '1'
ú Vehicle drives
FAULT - No 2 freewheel
ú No drive
Carry out main line pressure check
ú Normal pressure
FAULT - Clutch A
ú No pressure
FAULT - Blocked filter or pump failure
ú Low pressure
FAULT - Restricted filter or sticking primary
regulator
SYMPTOM 4 - Slip in all forward gears
Carry out main line pressure check
ú No pressure
FAULT - Blocked filter or pump failure
ú Low pressure
FAULT - Restricted filter or sticking primary
regulator
ú Normal pressure
FAULT - Clutch 'A'SYMPTOM 5 - Harsh engagement 'N' to 'D'
Check engine idle speed
Carry out main line pressure check
ú High pressure
FAULT - Primary regulator stuck
ú Normal pressure
FAULT - Clutch 'A' or damper for clutch'A'
SYMPTOM 6 - Fierce shift or flare 1st to 2nd shift
Check engine idle speed
Carry out mainline pressure check
ú High pressure
FAULT - Continue with symptom 5
ú Normal pressure
FAULT - Modulator valve or dampers for
clutch brake CB1 and/or clutch brake CB2
FAULT - Clutch brake CB1 and/or clutch
brake CB2
SYMPTOM 7 - Fierce shift or flare 2nd to 3rd
Carry out mainline pressure check
ú High pressure
FAULT - Continue with symptom 5
ú Normal pressure
FAULT - Modulator valve or clutch 'B'
damper
FAULT - Clutch 'B'
SYMPTOM 8 - No 3rd gear
FAULT - 2-3 shift valve
FAULT - Clutch 'B'
SYMPTOM 9 - No 4th gear 'D' selected
FAULT - 4th to 3rd downshift valve stuck or
3rd to 4th upshift valve stuck
FAULT - Clutch brake 4
Page 436 of 873
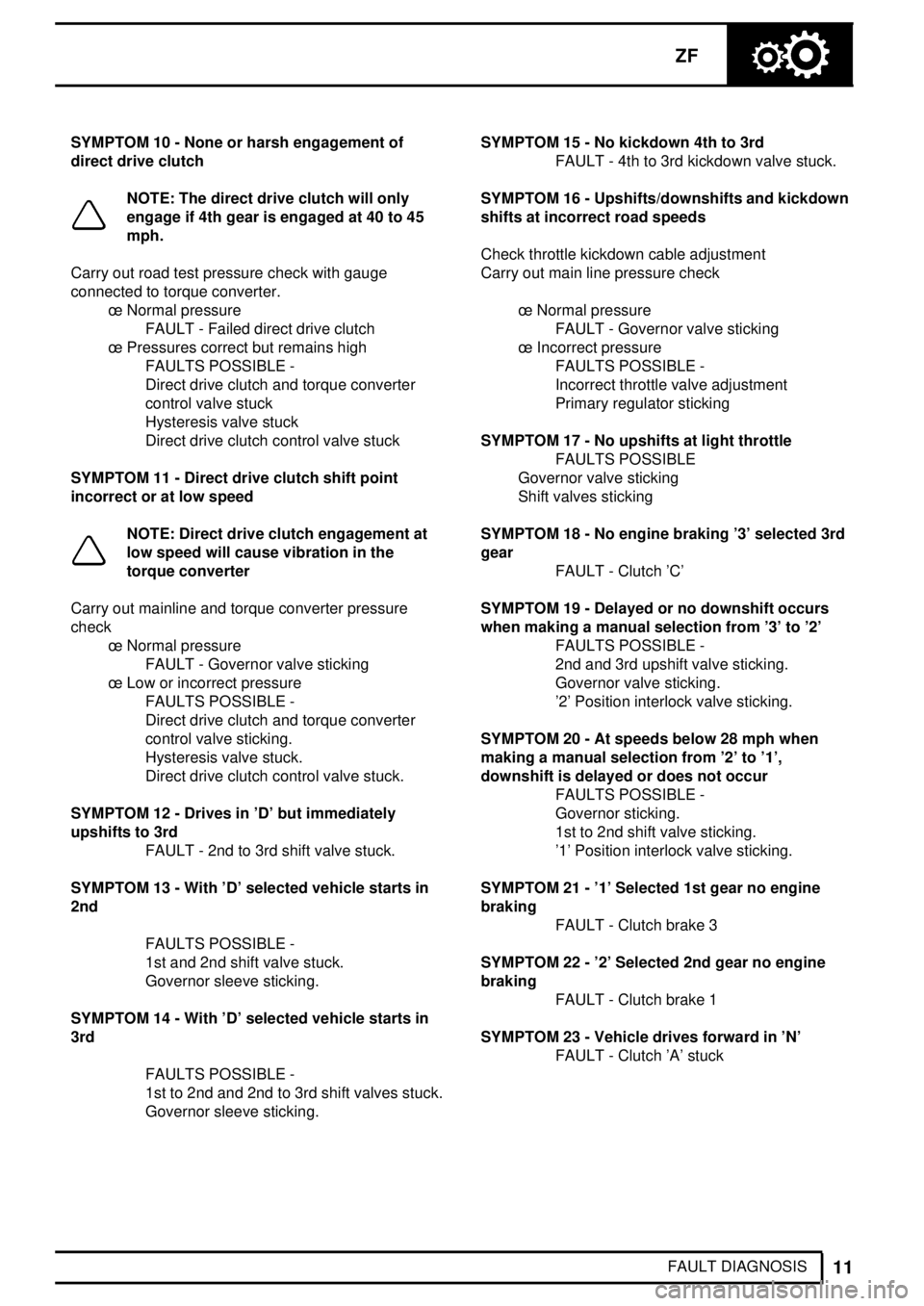
ZF
11
FAULT DIAGNOSIS SYMPTOM 10 - None or harsh engagement of
direct drive clutch
NOTE: The direct drive clutch will only
engage if 4th gear is engaged at 40 to 45
mph.
Carry out road test pressure check with gauge
connected to torque converter.
ú Normal pressure
FAULT - Failed direct drive clutch
ú Pressures correct but remains high
FAULTS POSSIBLE -
Direct drive clutch and torque converter
control valve stuck
Hysteresis valve stuck
Direct drive clutch control valve stuck
SYMPTOM 11 - Direct drive clutch shift point
incorrect or at low speed
NOTE: Direct drive clutch engagement at
low speed will cause vibration in the
torque converter
Carry out mainline and torque converter pressure
check
ú Normal pressure
FAULT - Governor valve sticking
ú Low or incorrect pressure
FAULTS POSSIBLE -
Direct drive clutch and torque converter
control valve sticking.
Hysteresis valve stuck.
Direct drive clutch control valve stuck.
SYMPTOM 12 - Drives in 'D' but immediately
upshifts to 3rd
FAULT - 2nd to 3rd shift valve stuck.
SYMPTOM 13 - With 'D' selected vehicle starts in
2nd
FAULTS POSSIBLE -
1st and 2nd shift valve stuck.
Governor sleeve sticking.
SYMPTOM 14 - With 'D' selected vehicle starts in
3rd
FAULTS POSSIBLE -
1st to 2nd and 2nd to 3rd shift valves stuck.
Governor sleeve sticking.SYMPTOM 15 - No kickdown 4th to 3rd
FAULT - 4th to 3rd kickdown valve stuck.
SYMPTOM 16 - Upshifts/downshifts and kickdown
shifts at incorrect road speeds
Check throttle kickdown cable adjustment
Carry out main line pressure check
ú Normal pressure
FAULT - Governor valve sticking
ú Incorrect pressure
FAULTS POSSIBLE -
Incorrect throttle valve adjustment
Primary regulator sticking
SYMPTOM 17 - No upshifts at light throttle
FAULTS POSSIBLE
Governor valve sticking
Shift valves sticking
SYMPTOM 18 - No engine braking '3' selected 3rd
gear
FAULT - Clutch 'C'
SYMPTOM 19 - Delayed or no downshift occurs
when making a manual selection from '3' to '2'
FAULTS POSSIBLE -
2nd and 3rd upshift valve sticking.
Governor valve sticking.
'2' Position interlock valve sticking.
SYMPTOM 20 - At speeds below 28 mph when
making a manual selection from '2' to '1',
downshift is delayed or does not occur
FAULTS POSSIBLE -
Governor sticking.
1st to 2nd shift valve sticking.
'1' Position interlock valve sticking.
SYMPTOM 21 - '1' Selected 1st gear no engine
braking
FAULT - Clutch brake 3
SYMPTOM 22 - '2' Selected 2nd gear no engine
braking
FAULT - Clutch brake 1
SYMPTOM 23 - Vehicle drives forward in 'N'
FAULT - Clutch 'A' stuck
Page 437 of 873
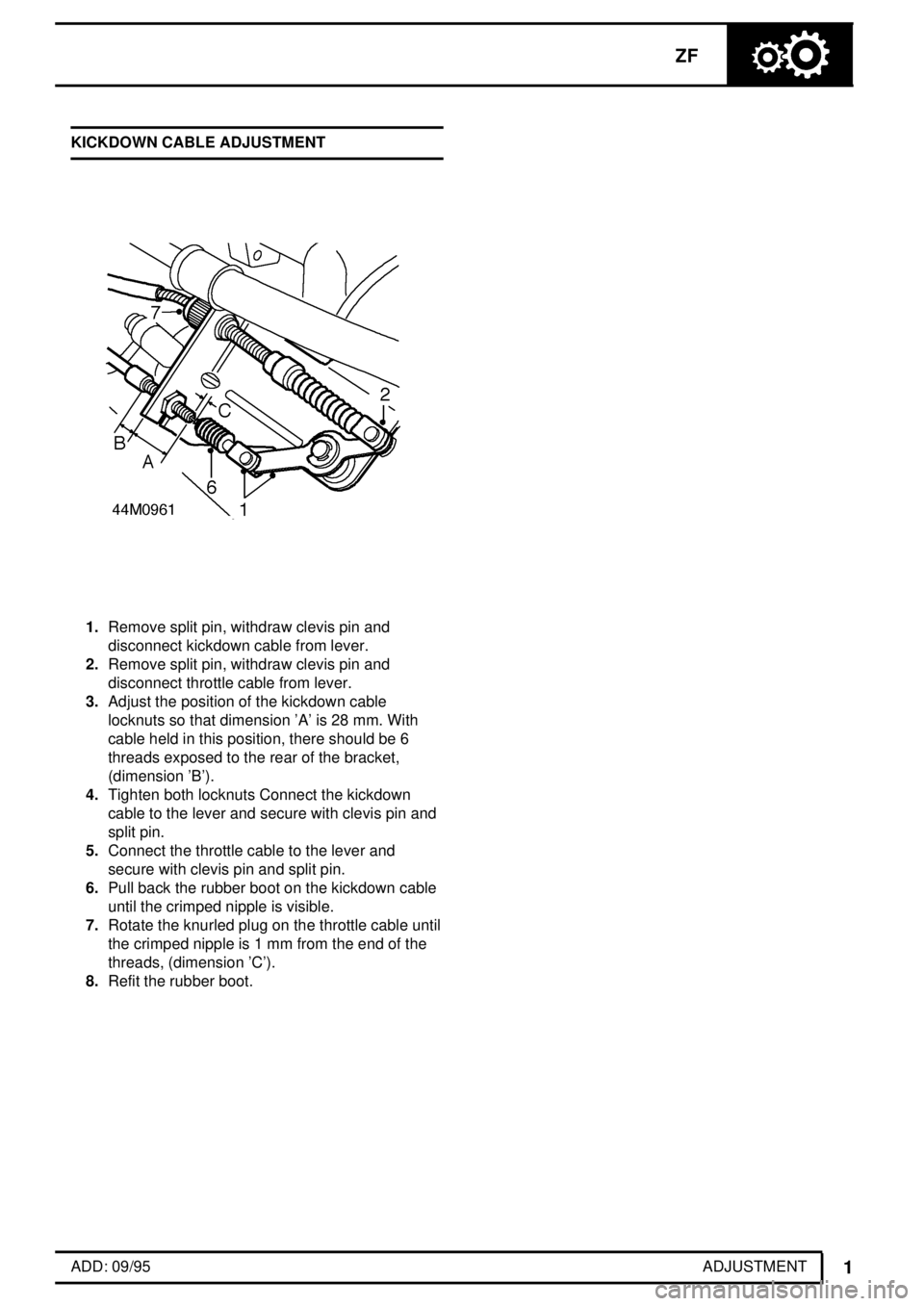
ZF
1
ADJUSTMENT ADD: 09/95 KICKDOWN CABLE ADJUSTMENT
1.Remove split pin, withdraw clevis pin and
disconnect kickdown cable from lever.
2.Remove split pin, withdraw clevis pin and
disconnect throttle cable from lever.
3.Adjust the position of the kickdown cable
locknuts so that dimension 'A' is 28 mm. With
cable held in this position, there should be 6
threads exposed to the rear of the bracket,
(dimension 'B').
4.Tighten both locknuts Connect the kickdown
cable to the lever and secure with clevis pin and
split pin.
5.Connect the throttle cable to the lever and
secure with clevis pin and split pin.
6.Pull back the rubber boot on the kickdown cable
until the crimped nipple is visible.
7.Rotate the knurled plug on the throttle cable until
the crimped nipple is 1 mm from the end of the
threads, (dimension 'C').
8.Refit the rubber boot.
Page 438 of 873
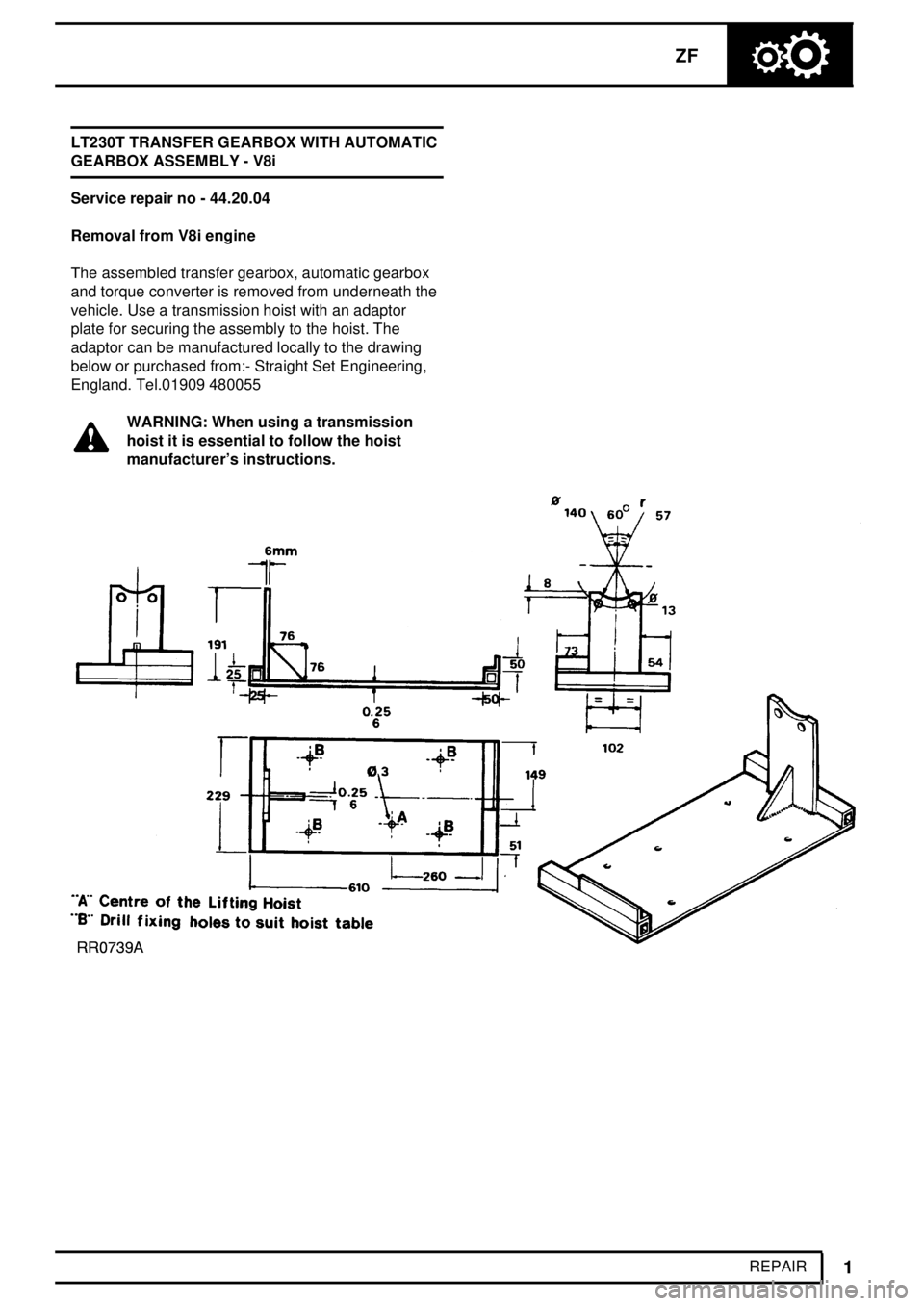
ZF
1
REPAIR LT230T TRANSFER GEARBOX WITH AUTOMATIC
GEARBOX ASSEMBLY - V8i
Service repair no - 44.20.04
Removal from V8i engine
The assembled transfer gearbox, automatic gearbox
and torque converter is removed from underneath the
vehicle. Use a transmission hoist with an adaptor
plate for securing the assembly to the hoist. The
adaptor can be manufactured locally to the drawing
below or purchased from:- Straight Set Engineering,
England. Tel.01909 480055
WARNING: When using a transmission
hoist it is essential to follow the hoist
manufacturer's instructions.
Page 439 of 873
![LAND ROVER DISCOVERY 1995 Workshop Manual 44AUTOMATIC GEARBOX
2
REPAIR 1.Site vehicle on a four post ramp [hoist].
2.Disconnect battery negative lead.
3.Remove fan cowl securing screws and release
cowl from radiator.
4.Loosen securing clip an LAND ROVER DISCOVERY 1995 Workshop Manual 44AUTOMATIC GEARBOX
2
REPAIR 1.Site vehicle on a four post ramp [hoist].
2.Disconnect battery negative lead.
3.Remove fan cowl securing screws and release
cowl from radiator.
4.Loosen securing clip an](/img/64/57248/w960_57248-438.png)
44AUTOMATIC GEARBOX
2
REPAIR 1.Site vehicle on a four post ramp [hoist].
2.Disconnect battery negative lead.
3.Remove fan cowl securing screws and release
cowl from radiator.
4.Loosen securing clip and disconnect air flow
hose from plenum chamber.
5.Disconnect stepper motor hose from top of
plenum chamber.
6.Disconnect kickdown cable from throttle linkage
and release from clipping.7.Release two gearbox breather pipes from clip
located on lifting eye at rear of right hand
cylinder head.
8.Remove dipstick from main gearbox oil filler
tube.
9.Working inside vehicle detach transfer gear lever
gaiter from console, unscrew knob and withdraw
gaiter and knob.
10.Raise vehicle on ramp [hoist].
11.Remove drain plugs and drain oil from transfer
gearbox and main gearbox. Refit plugs.
12.Detach heat shield at front exhaust pipe to
manifold.
13.Disconnect electrics to Lambda sensors.
14.Remove catalytic converter assembly.
15.Remove chassis cross-member from under
gearbox.16.Remove heat shield from speedometer cable at
transfer gearbox.
17.Remove clamp and disconnect speedometer
cable from transfer gearbox. Tie cable to one
side.
18.Mark for reassembly propeller shaft to transfer
gearbox mating flanges.
Page 440 of 873
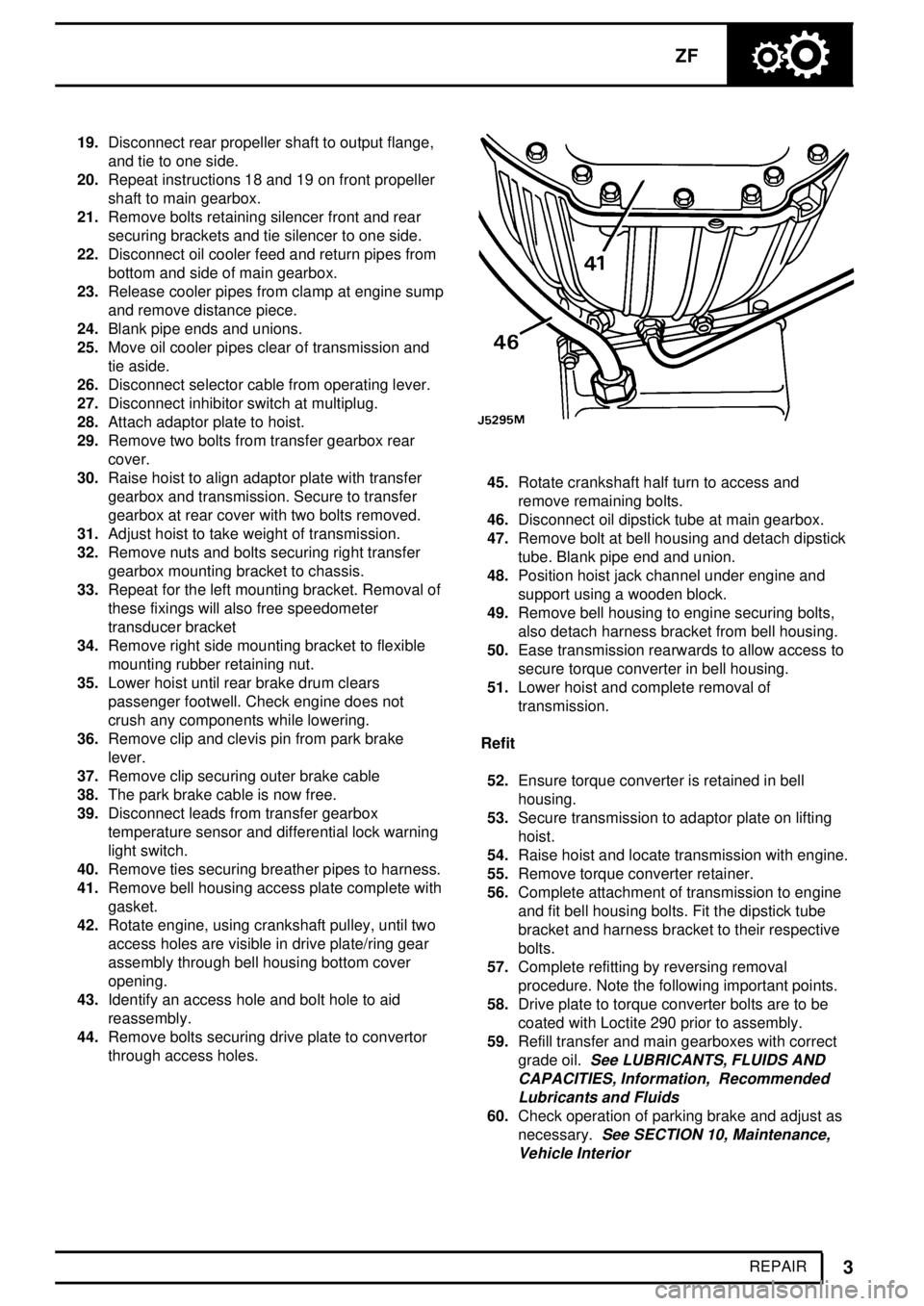
ZF
3
REPAIR 19.Disconnect rear propeller shaft to output flange,
and tie to one side.
20.Repeat instructions 18 and 19 on front propeller
shaft to main gearbox.
21.Remove bolts retaining silencer front and rear
securing brackets and tie silencer to one side.
22.Disconnect oil cooler feed and return pipes from
bottom and side of main gearbox.
23.Release cooler pipes from clamp at engine sump
and remove distance piece.
24.Blank pipe ends and unions.
25.Move oil cooler pipes clear of transmission and
tie aside.
26.Disconnect selector cable from operating lever.
27.Disconnect inhibitor switch at multiplug.
28.Attach adaptor plate to hoist.
29.Remove two bolts from transfer gearbox rear
cover.
30.Raise hoist to align adaptor plate with transfer
gearbox and transmission. Secure to transfer
gearbox at rear cover with two bolts removed.
31.Adjust hoist to take weight of transmission.
32.Remove nuts and bolts securing right transfer
gearbox mounting bracket to chassis.
33.Repeat for the left mounting bracket. Removal of
these fixings will also free speedometer
transducer bracket
34.Remove right side mounting bracket to flexible
mounting rubber retaining nut.
35.Lower hoist until rear brake drum clears
passenger footwell. Check engine does not
crush any components while lowering.
36.Remove clip and clevis pin from park brake
lever.
37.Remove clip securing outer brake cable
38.The park brake cable is now free.
39.Disconnect leads from transfer gearbox
temperature sensor and differential lock warning
light switch.
40.Remove ties securing breather pipes to harness.
41.Remove bell housing access plate complete with
gasket.
42.Rotate engine, using crankshaft pulley, until two
access holes are visible in drive plate/ring gear
assembly through bell housing bottom cover
opening.
43.Identify an access hole and bolt hole to aid
reassembly.
44.Remove bolts securing drive plate to convertor
through access holes.
45.Rotate crankshaft half turn to access and
remove remaining bolts.
46.Disconnect oil dipstick tube at main gearbox.
47.Remove bolt at bell housing and detach dipstick
tube. Blank pipe end and union.
48.Position hoist jack channel under engine and
support using a wooden block.
49.Remove bell housing to engine securing bolts,
also detach harness bracket from bell housing.
50.Ease transmission rearwards to allow access to
secure torque converter in bell housing.
51.Lower hoist and complete removal of
transmission.
Refit
52.Ensure torque converter is retained in bell
housing.
53.Secure transmission to adaptor plate on lifting
hoist.
54.Raise hoist and locate transmission with engine.
55.Remove torque converter retainer.
56.Complete attachment of transmission to engine
and fit bell housing bolts. Fit the dipstick tube
bracket and harness bracket to their respective
bolts.
57.Complete refitting by reversing removal
procedure. Note the following important points.
58.Drive plate to torque converter bolts are to be
coated with Loctite 290 prior to assembly.
59.Refill transfer and main gearboxes with correct
grade oil.
See LUBRICANTS, FLUIDS AND
CAPACITIES, Information, Recommended
Lubricants and Fluids
60.Check operation of parking brake and adjust as
necessary.
See SECTION 10, Maintenance,
Vehicle Interior