check engine light LAND ROVER DISCOVERY 1995 Workshop Manual
[x] Cancel search | Manufacturer: LAND ROVER, Model Year: 1995, Model line: DISCOVERY, Model: LAND ROVER DISCOVERY 1995Pages: 873, PDF Size: 12.89 MB
Page 9 of 873
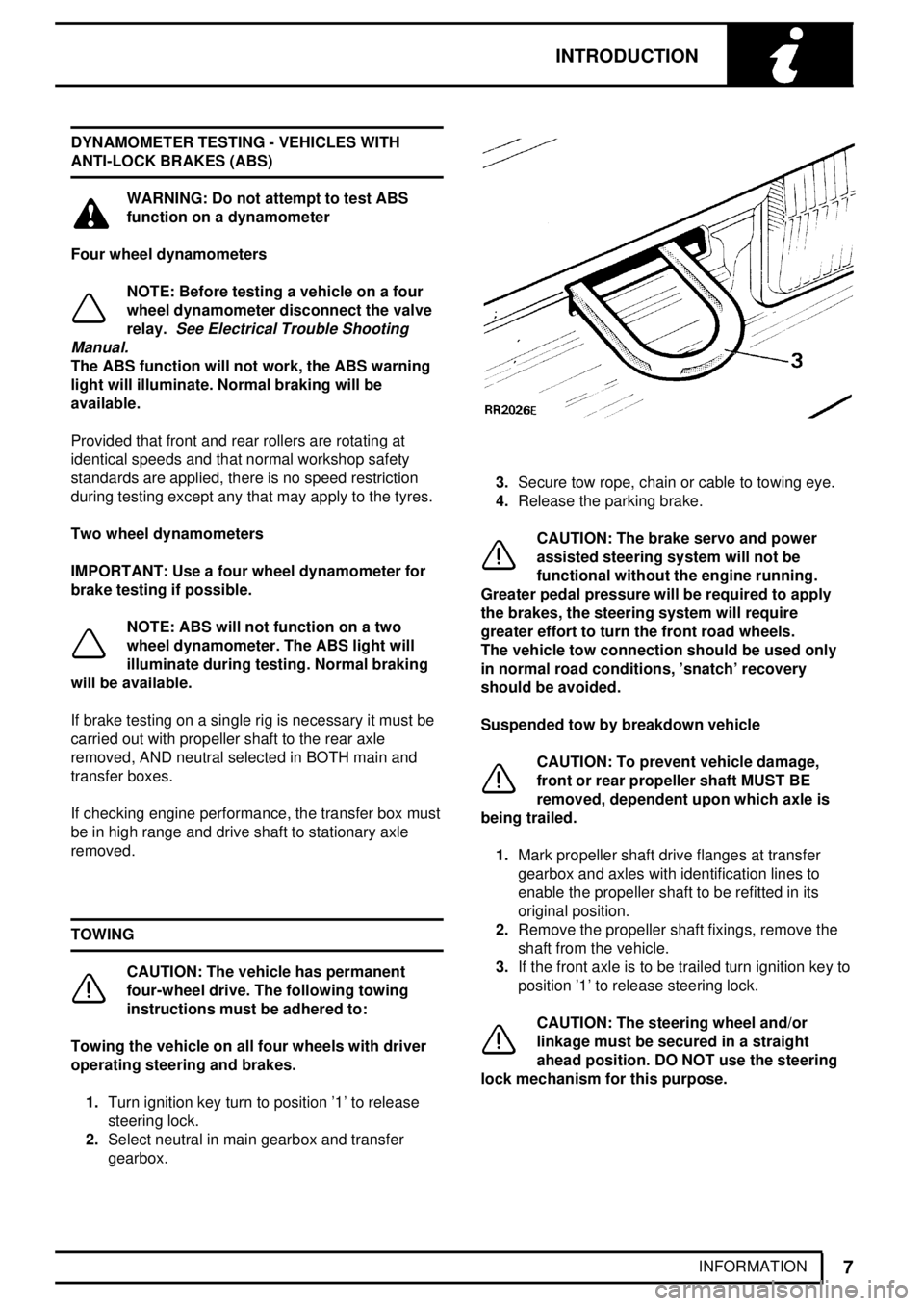
INTRODUCTION
7
INFORMATION DYNAMOMETER TESTING - VEHICLES WITH
ANTI-LOCK BRAKES (ABS)
WARNING: Do not attempt to test ABS
function on a dynamometer
Four wheel dynamometers
NOTE: Before testing a vehicle on a four
wheel dynamometer disconnect the valve
relay.
See Electrical Trouble Shooting
Manual.
The ABS function will not work, the ABS warning
light will illuminate. Normal braking will be
available.
Provided that front and rear rollers are rotating at
identical speeds and that normal workshop safety
standards are applied, there is no speed restriction
during testing except any that may apply to the tyres.
Two wheel dynamometers
IMPORTANT: Use a four wheel dynamometer for
brake testing if possible.
NOTE: ABS will not function on a two
wheel dynamometer. The ABS light will
illuminate during testing. Normal braking
will be available.
If brake testing on a single rig is necessary it must be
carried out with propeller shaft to the rear axle
removed, AND neutral selected in BOTH main and
transfer boxes.
If checking engine performance, the transfer box must
be in high range and drive shaft to stationary axle
removed.
TOWING
CAUTION: The vehicle has permanent
four-wheel drive. The following towing
instructions must be adhered to:
Towing the vehicle on all four wheels with driver
operating steering and brakes.
1.Turn ignition key turn to position '1' to release
steering lock.
2.Select neutral in main gearbox and transfer
gearbox.
3.Secure tow rope, chain or cable to towing eye.
4.Release the parking brake.
CAUTION: The brake servo and power
assisted steering system will not be
functional without the engine running.
Greater pedal pressure will be required to apply
the brakes, the steering system will require
greater effort to turn the front road wheels.
The vehicle tow connection should be used only
in normal road conditions, 'snatch' recovery
should be avoided.
Suspended tow by breakdown vehicle
CAUTION: To prevent vehicle damage,
front or rear propeller shaft MUST BE
removed, dependent upon which axle is
being trailed.
1.Mark propeller shaft drive flanges at transfer
gearbox and axles with identification lines to
enable the propeller shaft to be refitted in its
original position.
2.Remove the propeller shaft fixings, remove the
shaft from the vehicle.
3.If the front axle is to be trailed turn ignition key to
position '1' to release steering lock.
CAUTION: The steering wheel and/or
linkage must be secured in a straight
ahead position. DO NOT use the steering
lock mechanism for this purpose.
Page 13 of 873
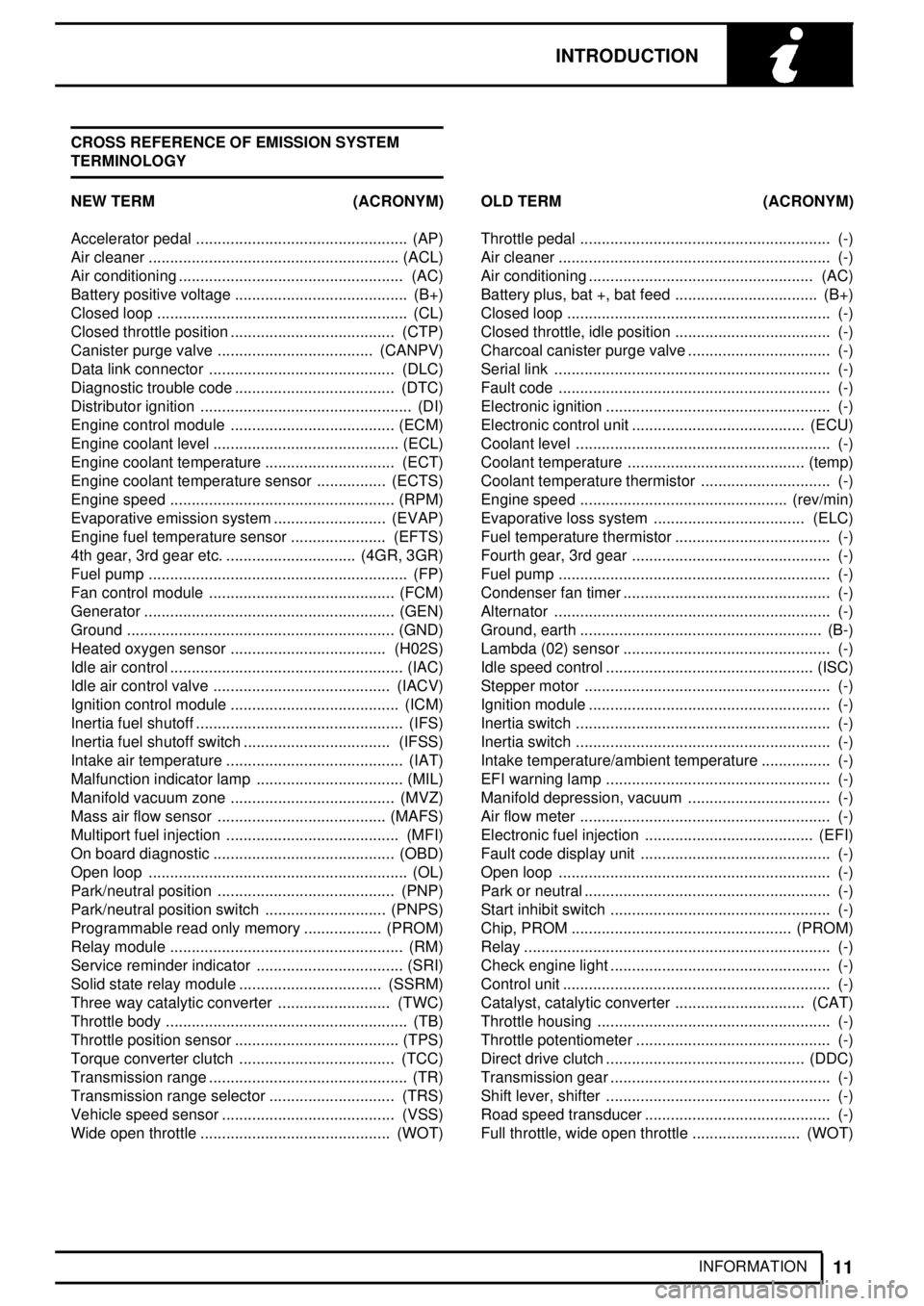
INTRODUCTION
11
INFORMATION CROSS REFERENCE OF EMISSION SYSTEM
TERMINOLOGY
NEW TERM (ACRONYM)
Accelerator pedal (AP).................................................
Air cleaner (ACL)..........................................................
Air conditioning (AC)....................................................
Battery positive voltage (B+)........................................
Closed loop (CL)..........................................................
Closed throttle position (CTP)......................................
Canister purge valve (CANPV)....................................
Data link connector (DLC)...........................................
Diagnostic trouble code (DTC).....................................
Distributor ignition (DI).................................................
Engine control module (ECM)......................................
Engine coolant level (ECL)...........................................
Engine coolant temperature (ECT)..............................
Engine coolant temperature sensor (ECTS)................
Engine speed (RPM)....................................................
Evaporative emission system (EVAP)..........................
Engine fuel temperature sensor (EFTS)......................
4th gear, 3rd gear etc. (4GR, 3GR)..............................
Fuel pump (FP)............................................................
Fan control module (FCM)...........................................
Generator (GEN)..........................................................
Ground (GND)..............................................................
Heated oxygen sensor (H02S)....................................
Idle air control (IAC)......................................................
Idle air control valve (IACV).........................................
Ignition control module (ICM).......................................
Inertia fuel shutoff (IFS)................................................
Inertia fuel shutoff switch (IFSS)..................................
Intake air temperature (IAT).........................................
Malfunction indicator lamp (MIL)..................................
Manifold vacuum zone (MVZ)......................................
Mass air flow sensor (MAFS).......................................
Multiport fuel injection (MFI)........................................
On board diagnostic (OBD)..........................................
Open loop (OL)............................................................
Park/neutral position (PNP).........................................
Park/neutral position switch (PNPS)............................
Programmable read only memory (PROM)..................
Relay module (RM)......................................................
Service reminder indicator (SRI)..................................
Solid state relay module (SSRM).................................
Three way catalytic converter (TWC)..........................
Throttle body (TB)........................................................
Throttle position sensor (TPS)......................................
Torque converter clutch (TCC)....................................
Transmission range (TR)..............................................
Transmission range selector (TRS).............................
Vehicle speed sensor (VSS)........................................
Wide open throttle (WOT)............................................OLD TERM (ACRONYM)
Throttle pedal (-)..........................................................
Air cleaner (-)...............................................................
Air conditioning (AC)....................................................
Battery plus, bat +, bat feed (B+).................................
Closed loop (-).............................................................
Closed throttle, idle position (-)....................................
Charcoal canister purge valve (-).................................
Serial link (-)................................................................
Fault code (-)...............................................................
Electronic ignition (-)....................................................
Electronic control unit (ECU)........................................
Coolant level (-)...........................................................
Coolant temperature (temp).........................................
Coolant temperature thermistor (-)..............................
Engine speed (rev/min)................................................
Evaporative loss system (ELC)...................................
Fuel temperature thermistor (-)....................................
Fourth gear, 3rd gear (-)..............................................
Fuel pump (-)...............................................................
Condenser fan timer (-)................................................
Alternator (-)................................................................
Ground, earth (B-)........................................................
Lambda (02) sensor (-)................................................
Idle speed control (ISC)................................................
Stepper motor (-).........................................................
Ignition module (-)........................................................
Inertia switch (-)...........................................................
Inertia switch (-)...........................................................
Intake temperature/ambient temperature (-)................
EFI warning lamp (-)....................................................
Manifold depression, vacuum (-).................................
Air flow meter (-)..........................................................
Electronic fuel injection (EFI).......................................
Fault code display unit (-)............................................
Open loop (-)...............................................................
Park or neutral (-).........................................................
Start inhibit switch (-)...................................................
Chip, PROM (PROM)...................................................
Relay (-).......................................................................
Check engine light (-)...................................................
Control unit (-)..............................................................
Catalyst, catalytic converter (CAT)..............................
Throttle housing (-)......................................................
Throttle potentiometer (-).............................................
Direct drive clutch (DDC)..............................................
Transmission gear (-)...................................................
Shift lever, shifter (-)....................................................
Road speed transducer (-)...........................................
Full throttle, wide open throttle (WOT).........................
Page 81 of 873
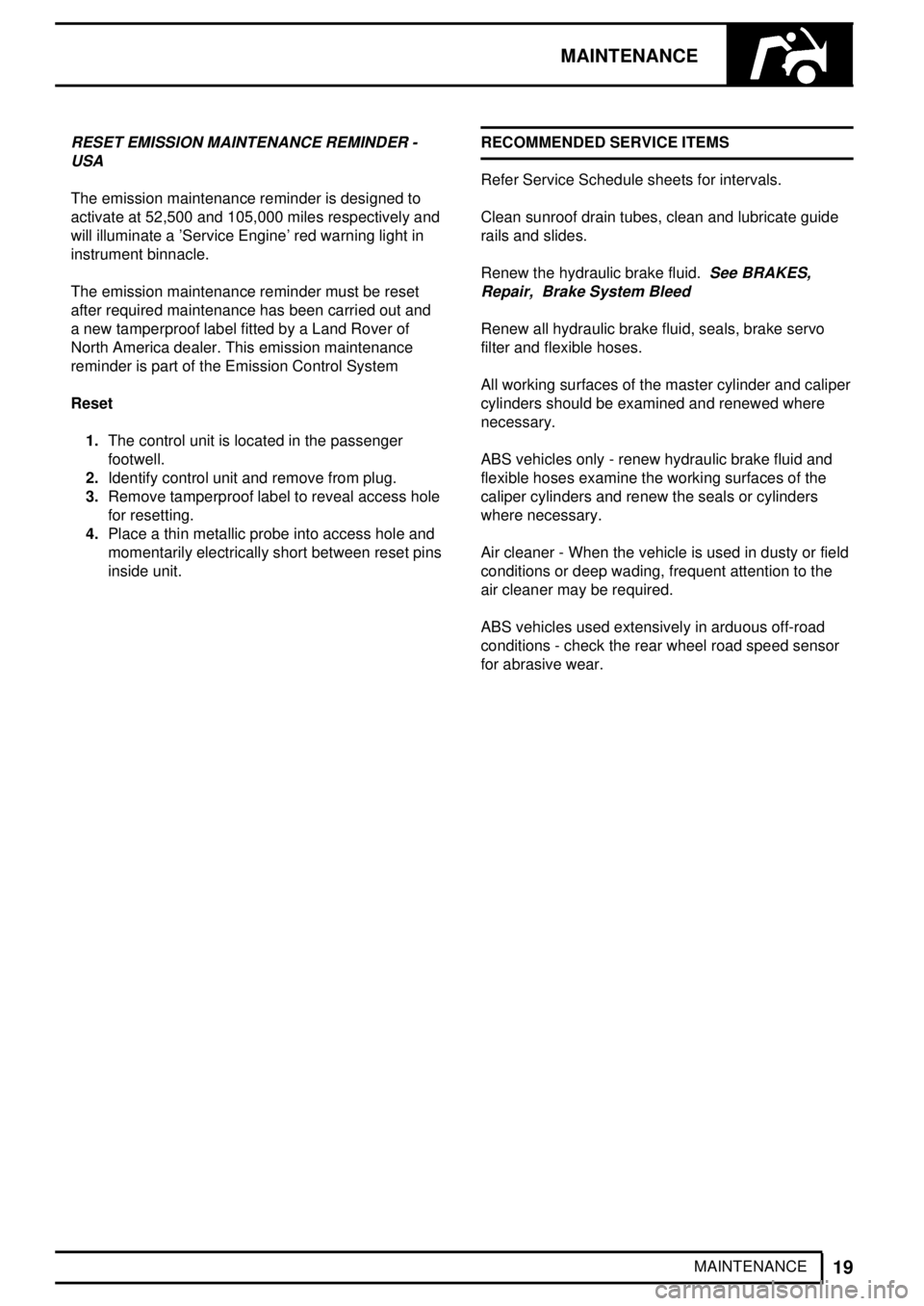
MAINTENANCE
19
MAINTENANCE
RESET EMISSION MAINTENANCE REMINDER -
USA
The emission maintenance reminder is designed to
activate at 52,500 and 105,000 miles respectively and
will illuminate a 'Service Engine' red warning light in
instrument binnacle.
The emission maintenance reminder must be reset
after required maintenance has been carried out and
a new tamperproof label fitted by a Land Rover of
North America dealer. This emission maintenance
reminder is part of the Emission Control System
Reset
1.The control unit is located in the passenger
footwell.
2.Identify control unit and remove from plug.
3.Remove tamperproof label to reveal access hole
for resetting.
4.Place a thin metallic probe into access hole and
momentarily electrically short between reset pins
inside unit.RECOMMENDED SERVICE ITEMS
Refer Service Schedule sheets for intervals.
Clean sunroof drain tubes, clean and lubricate guide
rails and slides.
Renew the hydraulic brake fluid.
See BRAKES,
Repair, Brake System Bleed
Renew all hydraulic brake fluid, seals, brake servo
filter and flexible hoses.
All working surfaces of the master cylinder and caliper
cylinders should be examined and renewed where
necessary.
ABS vehicles only - renew hydraulic brake fluid and
flexible hoses examine the working surfaces of the
caliper cylinders and renew the seals or cylinders
where necessary.
Air cleaner - When the vehicle is used in dusty or field
conditions or deep wading, frequent attention to the
air cleaner may be required.
ABS vehicles used extensively in arduous off-road
conditions - check the rear wheel road speed sensor
for abrasive wear.
Page 115 of 873
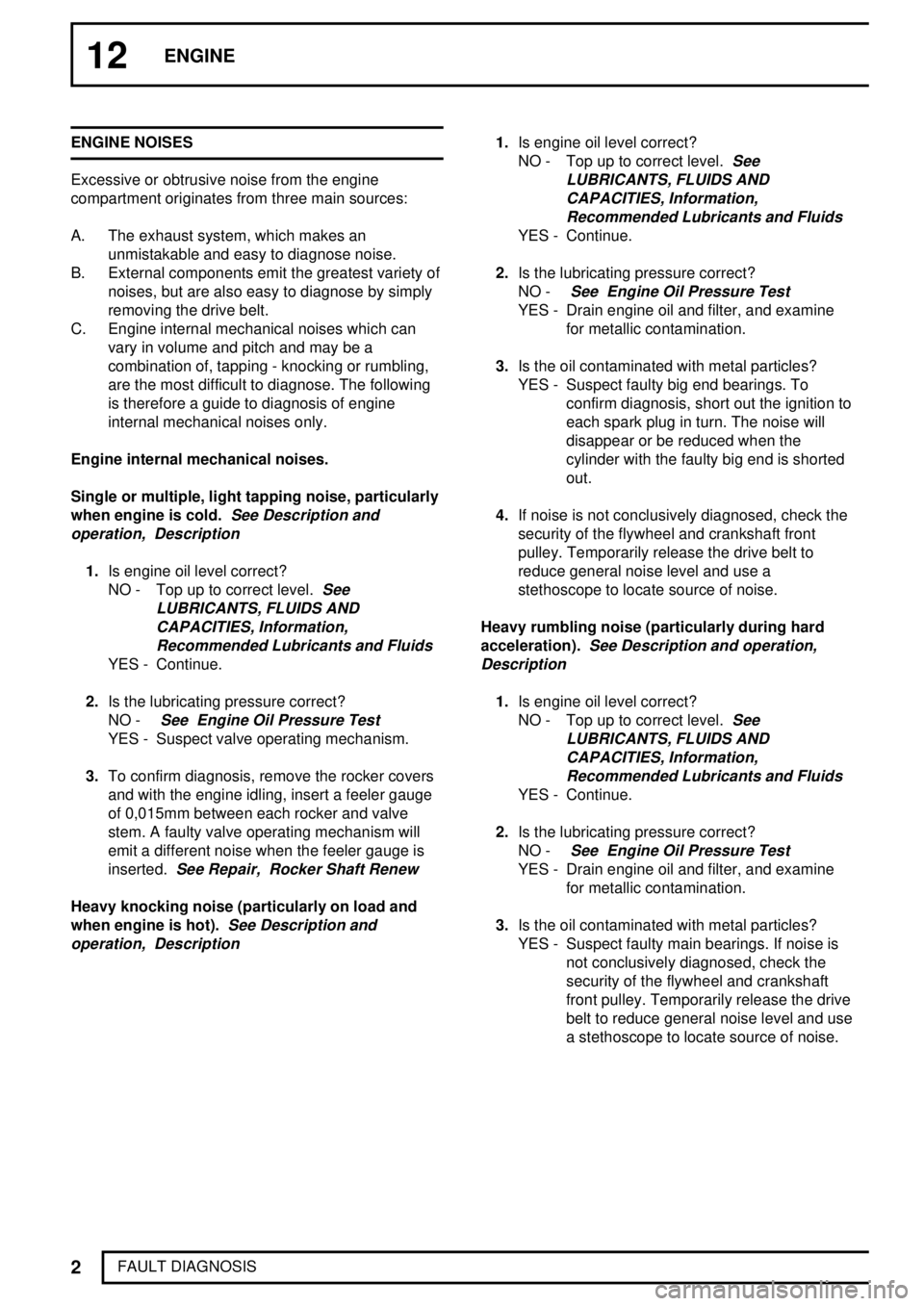
12ENGINE
2
FAULT DIAGNOSIS ENGINE NOISES
Excessive or obtrusive noise from the engine
compartment originates from three main sources:
A. The exhaust system, which makes an
unmistakable and easy to diagnose noise.
B. External components emit the greatest variety of
noises, but are also easy to diagnose by simply
removing the drive belt.
C. Engine internal mechanical noises which can
vary in volume and pitch and may be a
combination of, tapping - knocking or rumbling,
are the most difficult to diagnose. The following
is therefore a guide to diagnosis of engine
internal mechanical noises only.
Engine internal mechanical noises.
Single or multiple, light tapping noise, particularly
when engine is cold.
See Description and
operation, Description
1.Is engine oil level correct?
NO - Top up to correct level.
See
LUBRICANTS, FLUIDS AND
CAPACITIES, Information,
Recommended Lubricants and Fluids
YES - Continue.
2.Is the lubricating pressure correct?
NO -
See Engine Oil Pressure Test
YES - Suspect valve operating mechanism.
3.To confirm diagnosis, remove the rocker covers
and with the engine idling, insert a feeler gauge
of 0,015mm between each rocker and valve
stem. A faulty valve operating mechanism will
emit a different noise when the feeler gauge is
inserted.
See Repair, Rocker Shaft Renew
Heavy knocking noise (particularly on load and
when engine is hot).
See Description and
operation, Description
1.Is engine oil level correct?
NO - Top up to correct level.
See
LUBRICANTS, FLUIDS AND
CAPACITIES, Information,
Recommended Lubricants and Fluids
YES - Continue.
2.Is the lubricating pressure correct?
NO -
See Engine Oil Pressure Test
YES - Drain engine oil and filter, and examine
for metallic contamination.
3.Is the oil contaminated with metal particles?
YES - Suspect faulty big end bearings. To
confirm diagnosis, short out the ignition to
each spark plug in turn. The noise will
disappear or be reduced when the
cylinder with the faulty big end is shorted
out.
4.If noise is not conclusively diagnosed, check the
security of the flywheel and crankshaft front
pulley. Temporarily release the drive belt to
reduce general noise level and use a
stethoscope to locate source of noise.
Heavy rumbling noise (particularly during hard
acceleration).
See Description and operation,
Description
1.Is engine oil level correct?
NO - Top up to correct level.
See
LUBRICANTS, FLUIDS AND
CAPACITIES, Information,
Recommended Lubricants and Fluids
YES - Continue.
2.Is the lubricating pressure correct?
NO -
See Engine Oil Pressure Test
YES - Drain engine oil and filter, and examine
for metallic contamination.
3.Is the oil contaminated with metal particles?
YES - Suspect faulty main bearings. If noise is
not conclusively diagnosed, check the
security of the flywheel and crankshaft
front pulley. Temporarily release the drive
belt to reduce general noise level and use
a stethoscope to locate source of noise.
Page 127 of 873
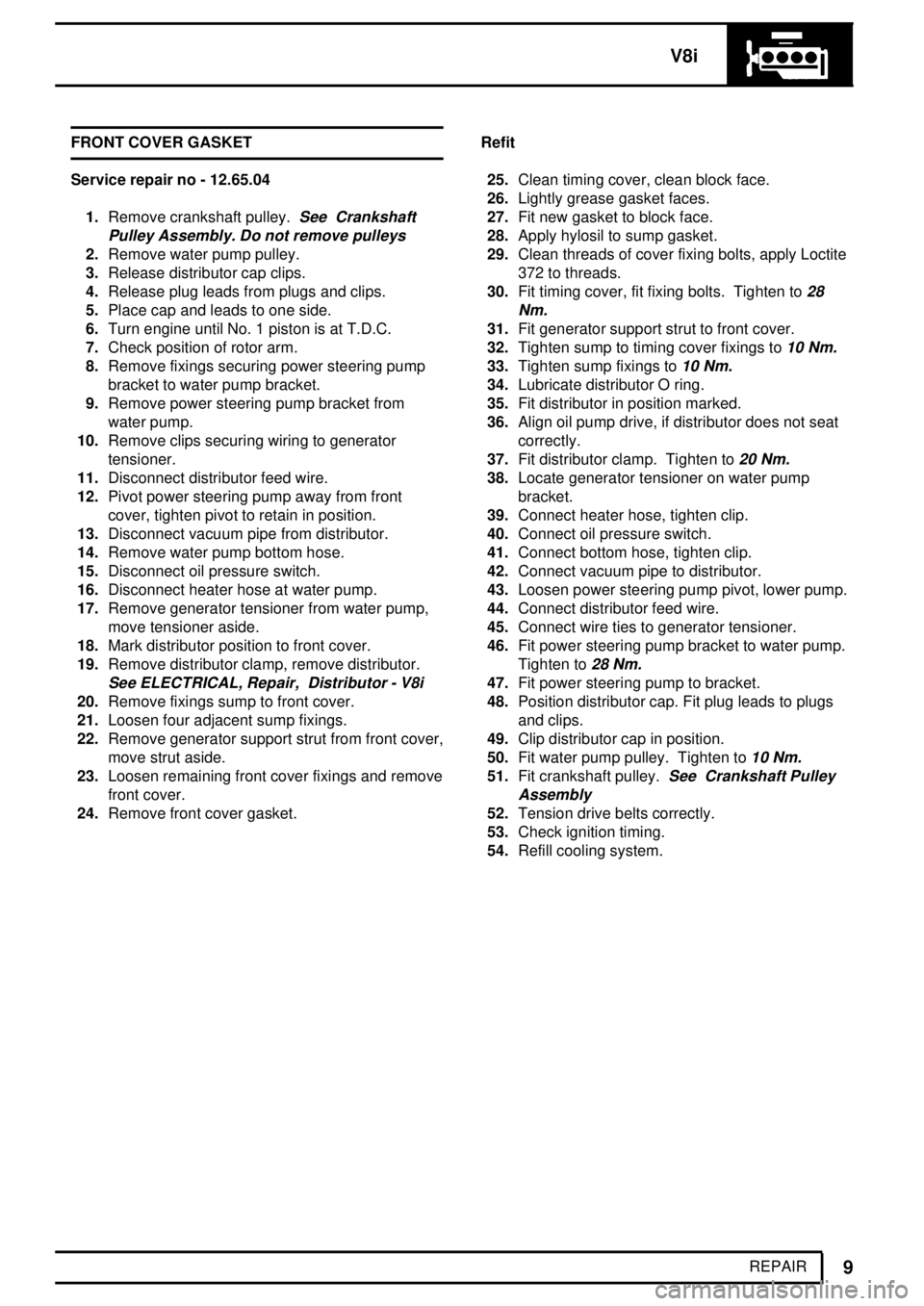
V8i
9
REPAIR FRONT COVER GASKET
Service repair no - 12.65.04
1.Remove crankshaft pulley.
See Crankshaft
Pulley Assembly. Do not remove pulleys
2.Remove water pump pulley.
3.Release distributor cap clips.
4.Release plug leads from plugs and clips.
5.Place cap and leads to one side.
6.Turn engine until No. 1 piston is at T.D.C.
7.Check position of rotor arm.
8.Remove fixings securing power steering pump
bracket to water pump bracket.
9.Remove power steering pump bracket from
water pump.
10.Remove clips securing wiring to generator
tensioner.
11.Disconnect distributor feed wire.
12.Pivot power steering pump away from front
cover, tighten pivot to retain in position.
13.Disconnect vacuum pipe from distributor.
14.Remove water pump bottom hose.
15.Disconnect oil pressure switch.
16.Disconnect heater hose at water pump.
17.Remove generator tensioner from water pump,
move tensioner aside.
18.Mark distributor position to front cover.
19.Remove distributor clamp, remove distributor.
See ELECTRICAL, Repair, Distributor - V8i
20.Remove fixings sump to front cover.
21.Loosen four adjacent sump fixings.
22.Remove generator support strut from front cover,
move strut aside.
23.Loosen remaining front cover fixings and remove
front cover.
24.Remove front cover gasket.Refit
25.Clean timing cover, clean block face.
26.Lightly grease gasket faces.
27.Fit new gasket to block face.
28.Apply hylosil to sump gasket.
29.Clean threads of cover fixing bolts, apply Loctite
372 to threads.
30.Fit timing cover, fit fixing bolts. Tighten to
28
Nm.
31.Fit generator support strut to front cover.
32.Tighten sump to timing cover fixings to
10 Nm.
33.Tighten sump fixings to10 Nm.
34.Lubricate distributor O ring.
35.Fit distributor in position marked.
36.Align oil pump drive, if distributor does not seat
correctly.
37.Fit distributor clamp. Tighten to
20 Nm.
38.Locate generator tensioner on water pump
bracket.
39.Connect heater hose, tighten clip.
40.Connect oil pressure switch.
41.Connect bottom hose, tighten clip.
42.Connect vacuum pipe to distributor.
43.Loosen power steering pump pivot, lower pump.
44.Connect distributor feed wire.
45.Connect wire ties to generator tensioner.
46.Fit power steering pump bracket to water pump.
Tighten to
28 Nm.
47.Fit power steering pump to bracket.
48.Position distributor cap. Fit plug leads to plugs
and clips.
49.Clip distributor cap in position.
50.Fit water pump pulley. Tighten to
10 Nm.
51.Fit crankshaft pulley.See Crankshaft Pulley
Assembly
52.Tension drive belts correctly.
53.Check ignition timing.
54.Refill cooling system.
Page 195 of 873
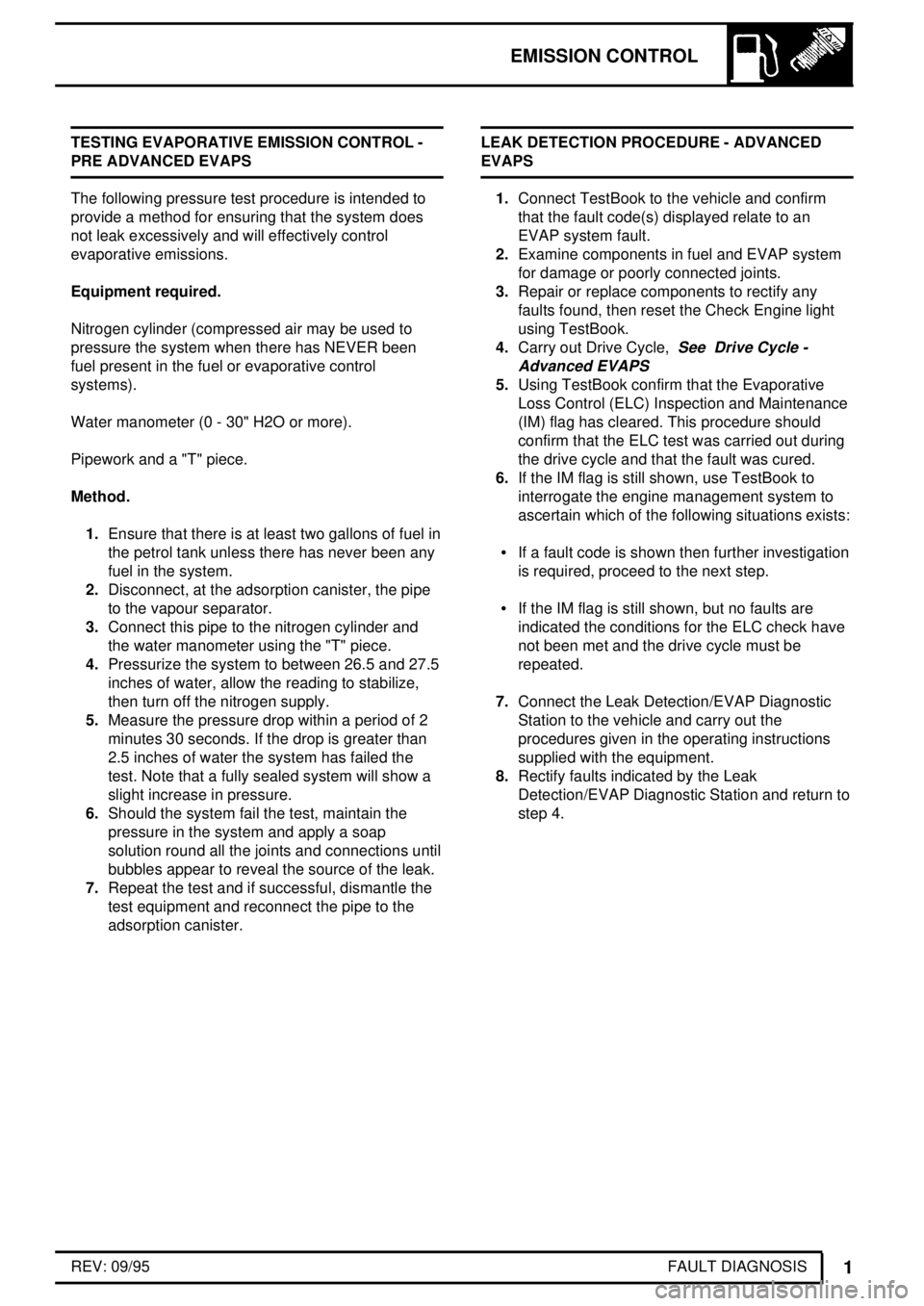
EMISSION CONTROL
1
FAULT DIAGNOSIS REV: 09/95 TESTING EVAPORATIVE EMISSION CONTROL -
PRE ADVANCED EVAPS
The following pressure test procedure is intended to
provide a method for ensuring that the system does
not leak excessively and will effectively control
evaporative emissions.
Equipment required.
Nitrogen cylinder (compressed air may be used to
pressure the system when there has NEVER been
fuel present in the fuel or evaporative control
systems).
Water manometer (0 - 30" H2O or more).
Pipework and a "T" piece.
Method.
1.Ensure that there is at least two gallons of fuel in
the petrol tank unless there has never been any
fuel in the system.
2.Disconnect, at the adsorption canister, the pipe
to the vapour separator.
3.Connect this pipe to the nitrogen cylinder and
the water manometer using the "T" piece.
4.Pressurize the system to between 26.5 and 27.5
inches of water, allow the reading to stabilize,
then turn off the nitrogen supply.
5.Measure the pressure drop within a period of 2
minutes 30 seconds. If the drop is greater than
2.5 inches of water the system has failed the
test. Note that a fully sealed system will show a
slight increase in pressure.
6.Should the system fail the test, maintain the
pressure in the system and apply a soap
solution round all the joints and connections until
bubbles appear to reveal the source of the leak.
7.Repeat the test and if successful, dismantle the
test equipment and reconnect the pipe to the
adsorption canister.LEAK DETECTION PROCEDURE - ADVANCED
EVAPS
1.Connect TestBook to the vehicle and confirm
that the fault code(s) displayed relate to an
EVAP system fault.
2.Examine components in fuel and EVAP system
for damage or poorly connected joints.
3.Repair or replace components to rectify any
faults found, then reset the Check Engine light
using TestBook.
4.Carry out Drive Cycle,
See Drive Cycle -
Advanced EVAPS
5.Using TestBook confirm that the Evaporative
Loss Control (ELC) Inspection and Maintenance
(IM) flag has cleared. This procedure should
confirm that the ELC test was carried out during
the drive cycle and that the fault was cured.
6.If the IM flag is still shown, use TestBook to
interrogate the engine management system to
ascertain which of the following situations exists:
·If a fault code is shown then further investigation
is required, proceed to the next step.
·If the IM flag is still shown, but no faults are
indicated the conditions for the ELC check have
not been met and the drive cycle must be
repeated.
7.Connect the Leak Detection/EVAP Diagnostic
Station to the vehicle and carry out the
procedures given in the operating instructions
supplied with the equipment.
8.Rectify faults indicated by the Leak
Detection/EVAP Diagnostic Station and return to
step 4.
Page 196 of 873
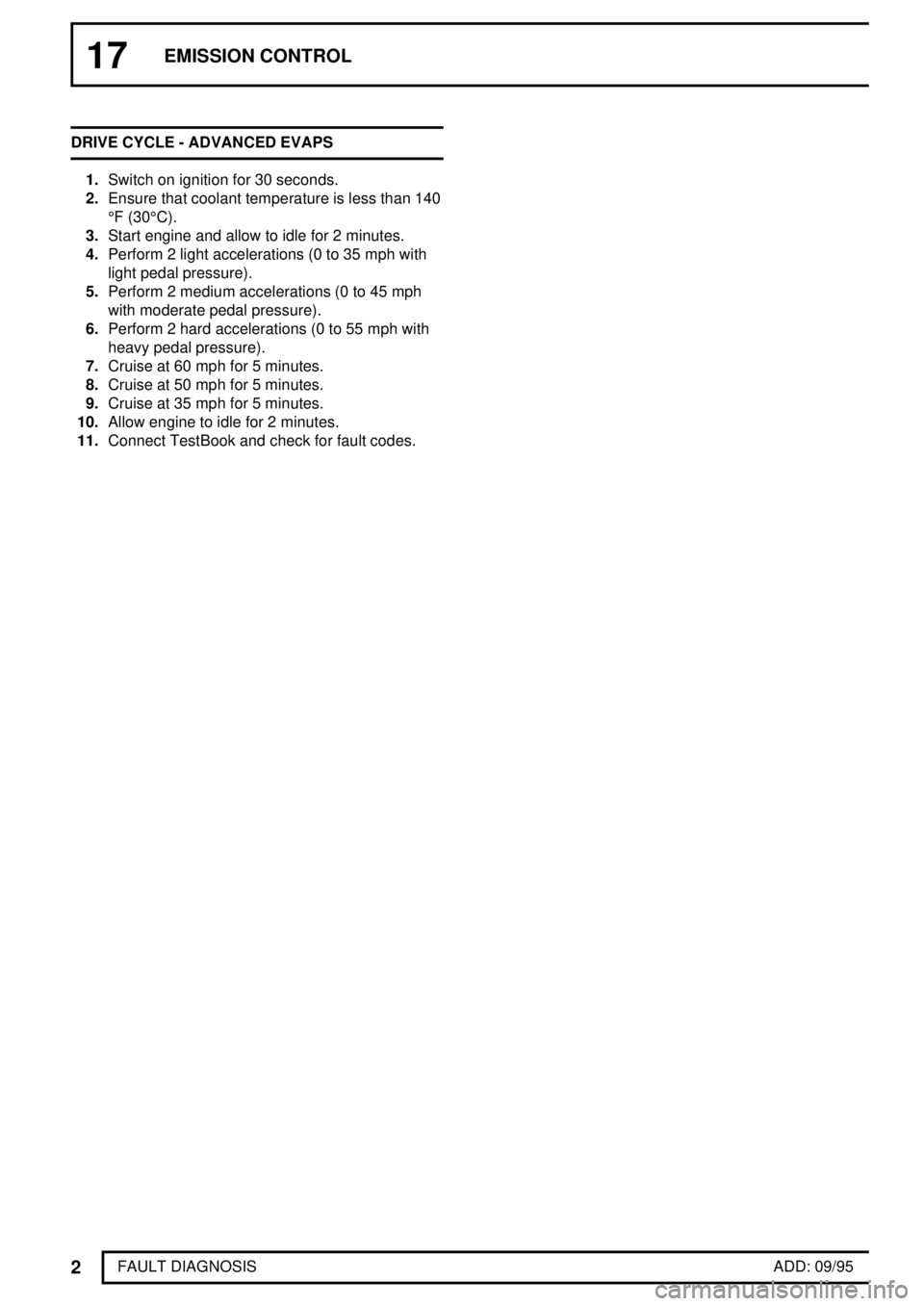
17EMISSION CONTROL
2
FAULT DIAGNOSISADD: 09/95 DRIVE CYCLE - ADVANCED EVAPS
1.Switch on ignition for 30 seconds.
2.Ensure that coolant temperature is less than 140
°F (30°C).
3.Start engine and allow to idle for 2 minutes.
4.Perform 2 light accelerations (0 to 35 mph with
light pedal pressure).
5.Perform 2 medium accelerations (0 to 45 mph
with moderate pedal pressure).
6.Perform 2 hard accelerations (0 to 55 mph with
heavy pedal pressure).
7.Cruise at 60 mph for 5 minutes.
8.Cruise at 50 mph for 5 minutes.
9.Cruise at 35 mph for 5 minutes.
10.Allow engine to idle for 2 minutes.
11.Connect TestBook and check for fault codes.
Page 369 of 873
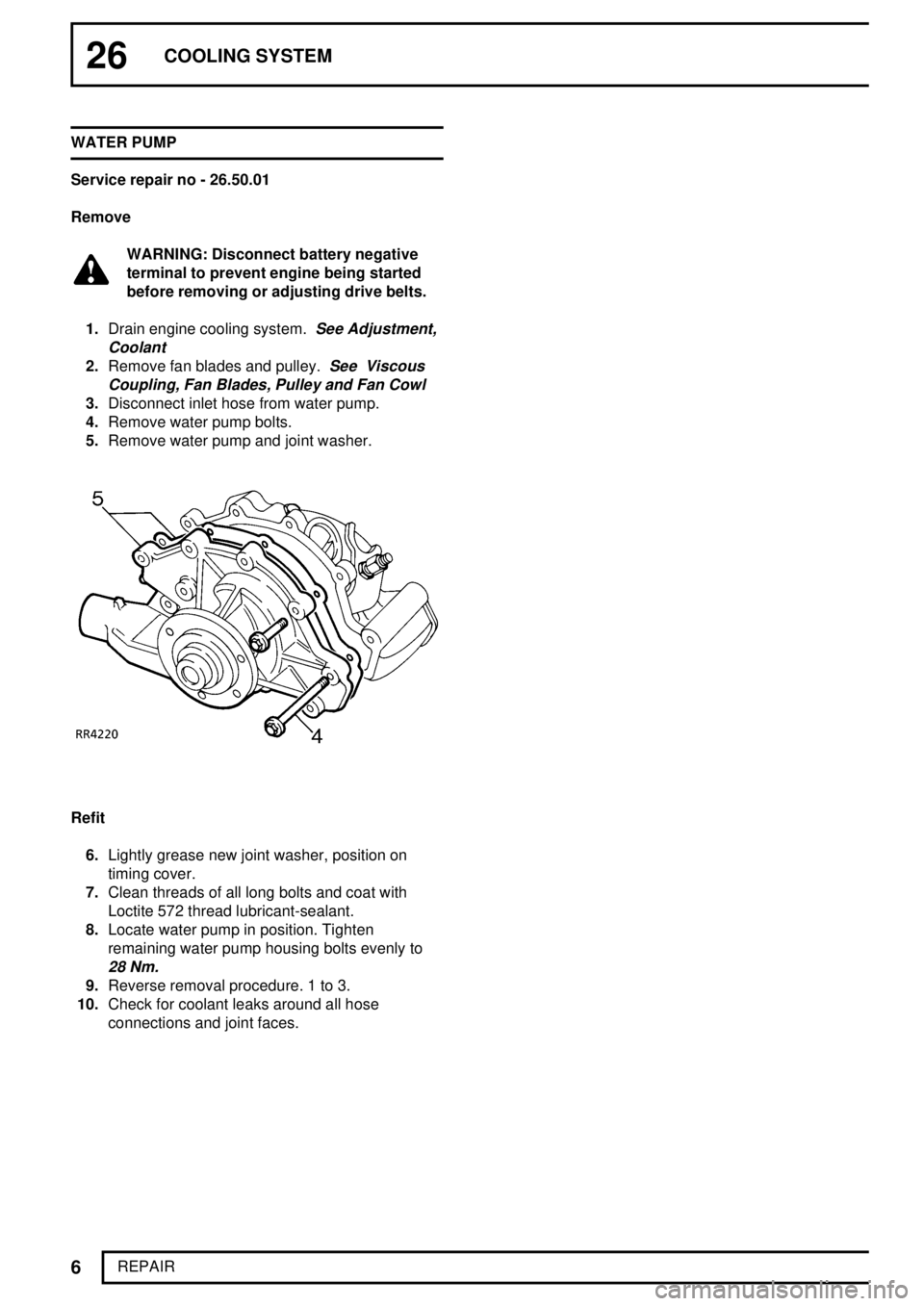
26COOLING SYSTEM
6
REPAIR WATER PUMP
Service repair no - 26.50.01
Remove
WARNING: Disconnect battery negative
terminal to prevent engine being started
before removing or adjusting drive belts.
1.Drain engine cooling system.
See Adjustment,
Coolant
2.Remove fan blades and pulley.See Viscous
Coupling, Fan Blades, Pulley and Fan Cowl
3.Disconnect inlet hose from water pump.
4.Remove water pump bolts.
5.Remove water pump and joint washer.
Refit
6.Lightly grease new joint washer, position on
timing cover.
7.Clean threads of all long bolts and coat with
Loctite 572 thread lubricant-sealant.
8.Locate water pump in position. Tighten
remaining water pump housing bolts evenly to
28 Nm.
9.Reverse removal procedure. 1 to 3.
10.Check for coolant leaks around all hose
connections and joint faces.
Page 416 of 873
![LAND ROVER DISCOVERY 1995 Workshop Manual 41TRANSFER GEARBOX
2
REPAIR Remove
1.Site vehicle on a ramp [hoist].
2.Disconnect battery negative lead.
3.Remove fan cowl from radiator.
4.Remove transfer gear lever knob and gaiter.
5.Raise vehicle LAND ROVER DISCOVERY 1995 Workshop Manual 41TRANSFER GEARBOX
2
REPAIR Remove
1.Site vehicle on a ramp [hoist].
2.Disconnect battery negative lead.
3.Remove fan cowl from radiator.
4.Remove transfer gear lever knob and gaiter.
5.Raise vehicle](/img/64/57248/w960_57248-415.png)
41TRANSFER GEARBOX
2
REPAIR Remove
1.Site vehicle on a ramp [hoist].
2.Disconnect battery negative lead.
3.Remove fan cowl from radiator.
4.Remove transfer gear lever knob and gaiter.
5.Raise vehicle on ramp [hoist].
6.Drain oil and refit plug.
7.Detach heat shield at front exhaust pipe to
manifold.
8.Disconnect electrics to Lambda sensors.
9.Remove catalytic converter assembly.
10.Remove chassis crossmember from under
gearbox.
11.Remove heat shield from speedometer cable at
transfer gearbox.
12.Remove clamp and disconnect speedometer
cable from transfer gearbox. Tie cable to one
side.
13.Mark for reassembly then disconnect propeller
shaft to output flange, tie to one side.
14.Repeat on front propeller shaft to output flange.
15.Remove bolts retaining silencer front and rear
securing brackets and tie silencer to one side.
16.Place four 30mm long spacers between top of
hoist and adaptor plate, at securing points, and
secure adaptor plate to hoist.17.Remove four central bolts from transfer gearbox
bottom cover, move hoist into position and
secure adaptor plate to transfer gearbox.
18.Adjust hoist to take weight of transfer gearbox.
19.Remove tie bar, transfer gearbox to main
gearbox.
20.Remove nuts and bolts securing right transfer
gearbox mounting bracket to chassis.
21.Repeat for left mounting bracket. Removal of
these fixings will also free speedometer
transducer bracket.
22.Remove right side mounting bracket to flexible
mounting rubber.
23.Lower hoist until rear brake drum clears
passenger footwell. Check engine does not
crush any components while lowering.
24.Loosen park brake adjustment nut.
25.Remove park brake drum.
26.Remove park brake assembly complete from
rear output flange.
27.Disconnect leads from transfer gearbox
temperature sensor and differential lock warning
light switch.
28.Remove banjo bolt from breather pipe, retrieve
sealing washers and lay pipe aside.
29.Remove split [cotter] pin and washers securing
differential lock to connecting rod and disconnect
rod from lever.
30.Select low range transfer gearbox position.
31.Remove high/low rod lower lock nut and remove
rod from yoke.
32.Position hoist jack channel under bell housing.
33.Using wooden block support the main gearbox
and bell housing.
34.Remove upper and lower bolts securing transfer
gearbox to main gearbox.
35.Fit guide studs 18G 1425 to main gearbox and
move transfer gearbox rearwards to detach.
Page 426 of 873
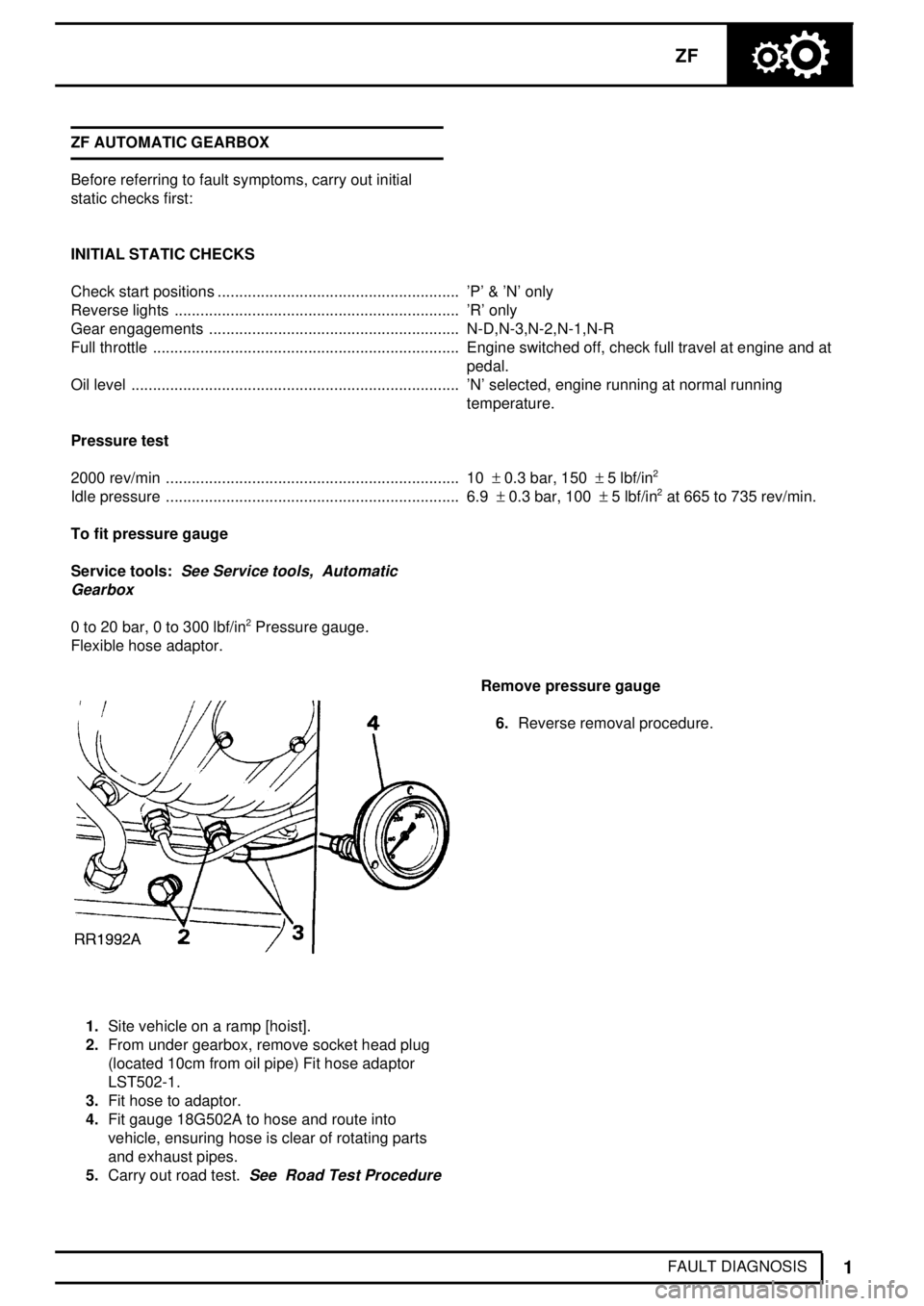
ZF
1
FAULT DIAGNOSIS ZF AUTOMATIC GEARBOX
Before referring to fault symptoms, carry out initial
static checks first:
INITIAL STATIC CHECKS
Check start positions 'P' & 'N' only........................................................
Reverse lights 'R' only..................................................................
Gear engagements N-D,N-3,N-2,N-1,N-R..........................................................
Full throttle Engine switched off, check full travel at engine and at.......................................................................
pedal.
Oil level 'N' selected, engine running at normal running............................................................................
temperature.
Pressure test
2000 rev/min 10±0.3 bar, 150±5 lbf/in
2....................................................................
Idle pressure 6.9±0.3 bar, 100±5 lbf/in2at 665 to 735 rev/min. ....................................................................
To fit pressure gauge
Service tools:
See Service tools, Automatic
Gearbox
0 to 20 bar, 0 to 300 lbf/in2Pressure gauge.
Flexible hose adaptor.
1.Site vehicle on a ramp [hoist].
2.From under gearbox, remove socket head plug
(located 10cm from oil pipe) Fit hose adaptor
LST502-1.
3.Fit hose to adaptor.
4.Fit gauge 18G502A to hose and route into
vehicle, ensuring hose is clear of rotating parts
and exhaust pipes.
5.Carry out road test.
See Road Test Procedure
Remove pressure gauge
6.Reverse removal procedure.