check engine LAND ROVER DISCOVERY 1999 Owner's Manual
[x] Cancel search | Manufacturer: LAND ROVER, Model Year: 1999, Model line: DISCOVERY, Model: LAND ROVER DISCOVERY 1999Pages: 1529, PDF Size: 34.8 MB
Page 173 of 1529
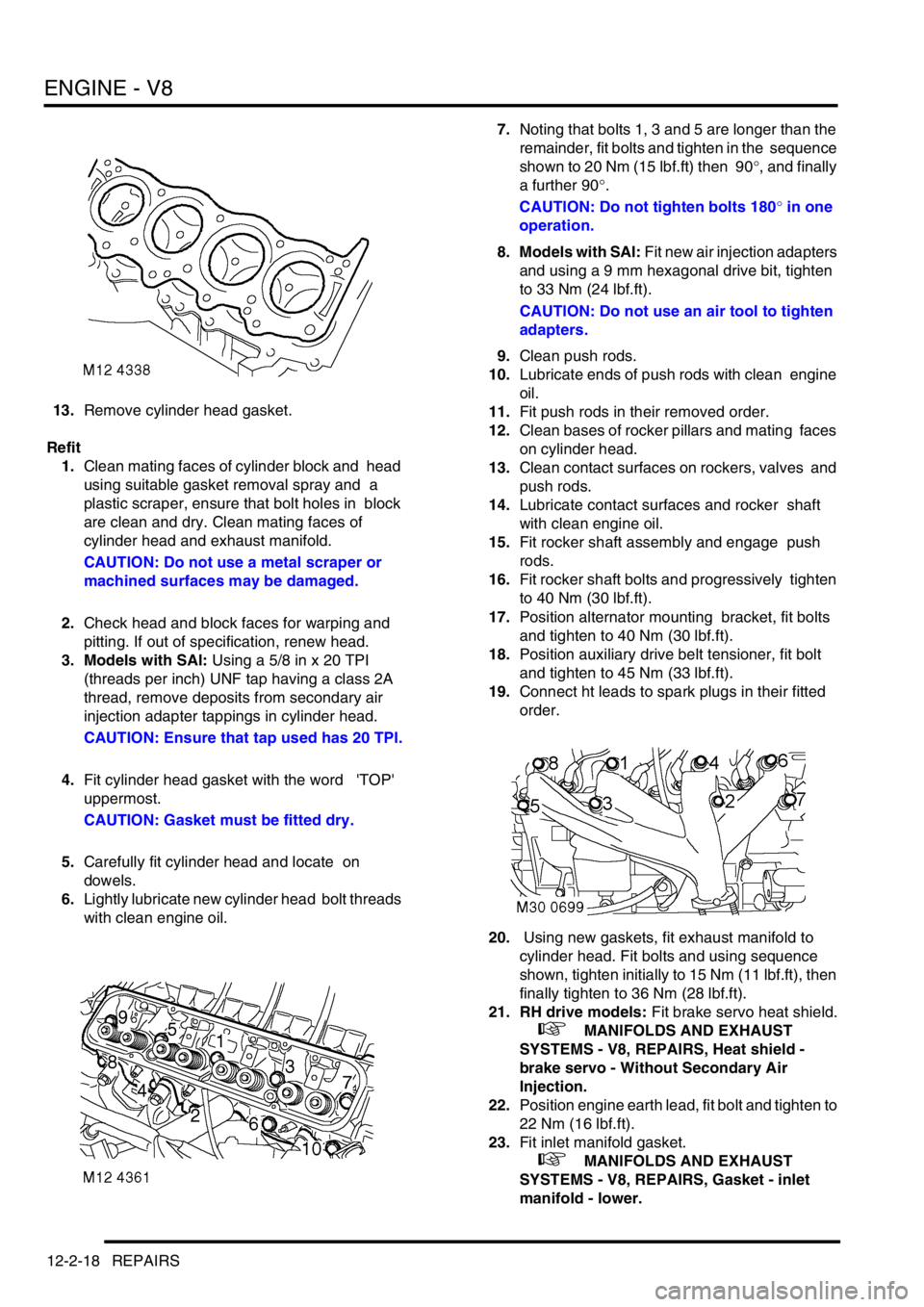
ENGINE - V8
12-2-18 REPAIRS
13.Remove cylinder head gasket.
Refit
1.Clean mating faces of cylinder block and head
using suitable gasket removal spray and a
plastic scraper, ensure that bolt holes in block
are clean and dry. Clean mating faces of
cylinder head and exhaust manifold.
CAUTION: Do not use a metal scraper or
machined surfaces may be damaged.
2.Check head and block faces for warping and
pitting. If out of specification, renew head.
3. Models with SAI: Using a 5/8 in x 20 TPI
(threads per inch) UNF tap having a class 2A
thread, remove deposits from secondary air
injection adapter tappings in cylinder head.
CAUTION: Ensure that tap used has 20 TPI.
4.Fit cylinder head gasket with the word 'TOP'
uppermost.
CAUTION: Gasket must be fitted dry.
5.Carefully fit cylinder head and locate on
dowels.
6.Lightly lubricate new cylinder head bolt threads
with clean engine oil. 7.Noting that bolts 1, 3 and 5 are longer than the
remainder, fit bolts and tighten in the sequence
shown to 20 Nm (15 lbf.ft) then 90°, and finally
a further 90°.
CAUTION: Do not tighten bolts 180° in one
operation.
8. Models with SAI: Fit new air injection adapters
and using a 9 mm hexagonal drive bit, tighten
to 33 Nm (24 lbf.ft).
CAUTION: Do not use an air tool to tighten
adapters.
9.Clean push rods.
10.Lubricate ends of push rods with clean engine
oil.
11.Fit push rods in their removed order.
12.Clean bases of rocker pillars and mating faces
on cylinder head.
13.Clean contact surfaces on rockers, valves and
push rods.
14.Lubricate contact surfaces and rocker shaft
with clean engine oil.
15.Fit rocker shaft assembly and engage push
rods.
16.Fit rocker shaft bolts and progressively tighten
to 40 Nm (30 lbf.ft).
17.Position alternator mounting bracket, fit bolts
and tighten to 40 Nm (30 lbf.ft).
18.Position auxiliary drive belt tensioner, fit bolt
and tighten to 45 Nm (33 lbf.ft).
19.Connect ht leads to spark plugs in their fitted
order.
20. Using new gaskets, fit exhaust manifold to
cylinder head. Fit bolts and using sequence
shown, tighten initially to 15 Nm (11 lbf.ft), then
finally tighten to 36 Nm (28 lbf.ft).
21. RH drive models: Fit brake servo heat shield.
+ MANIFOLDS AND EXHAUST
SYSTEMS - V8, REPAIRS, Heat shield -
brake servo - Without Secondary Air
Injection.
22.Position engine earth lead, fit bolt and tighten to
22 Nm (16 lbf.ft).
23.Fit inlet manifold gasket.
+ MANIFOLDS AND EXHAUST
SYSTEMS - V8, REPAIRS, Gasket - inlet
manifold - lower.
Page 188 of 1529
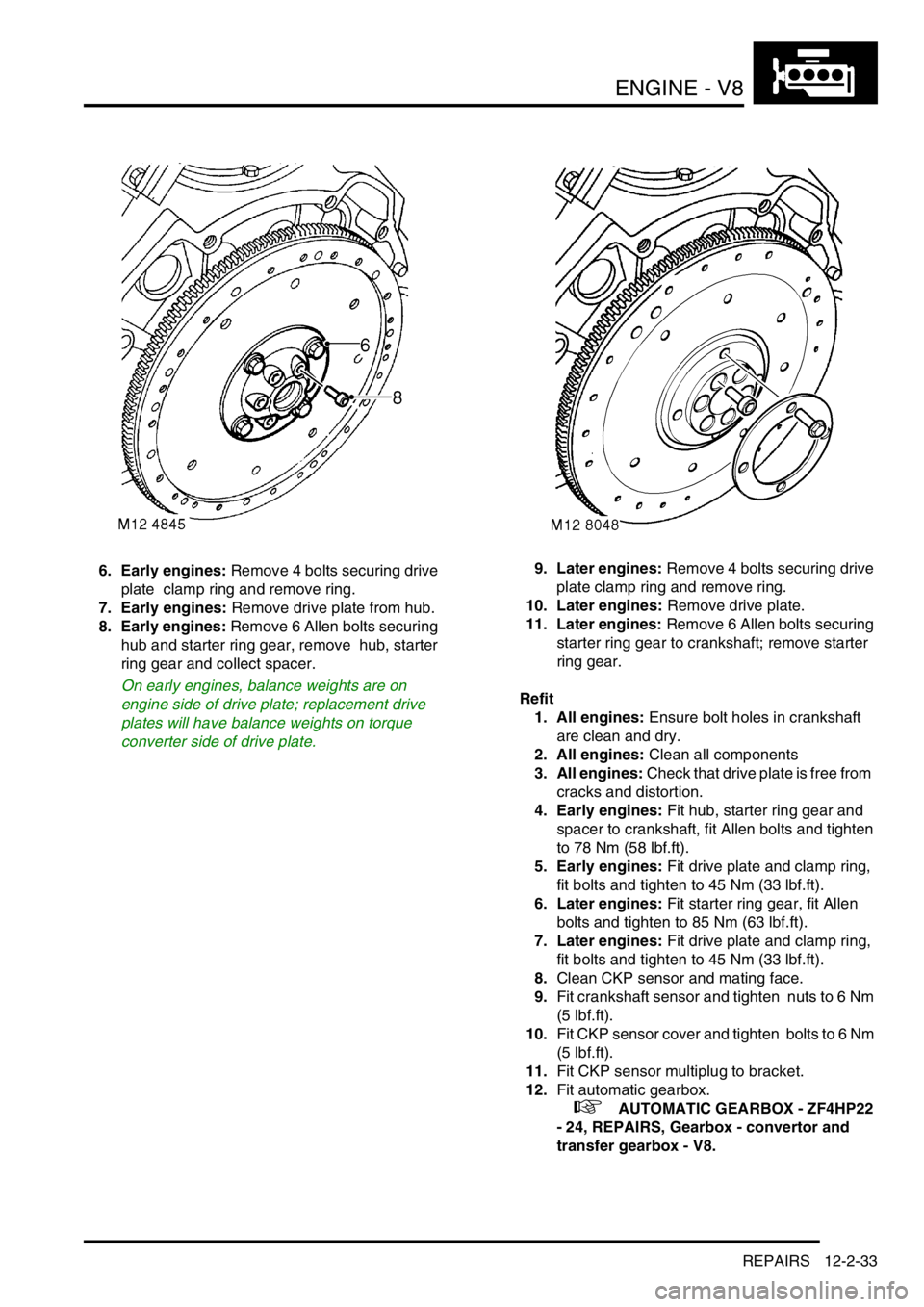
ENGINE - V8
REPAIRS 12-2-33
6. Early engines: Remove 4 bolts securing drive
plate clamp ring and remove ring.
7. Early engines: Remove drive plate from hub.
8. Early engines: Remove 6 Allen bolts securing
hub and starter ring gear, remove hub, starter
ring gear and collect spacer.
On early engines, balance weights are on
engine side of drive plate; replacement drive
plates will have balance weights on torque
converter side of drive plate.9. Later engines: Remove 4 bolts securing drive
plate clamp ring and remove ring.
10. Later engines: Remove drive plate.
11. Later engines: Remove 6 Allen bolts securing
starter ring gear to crankshaft; remove starter
ring gear.
Refit
1. All engines: Ensure bolt holes in crankshaft
are clean and dry.
2. All engines: Clean all components
3. All engines: Check that drive plate is free from
cracks and distortion.
4. Early engines: Fit hub, starter ring gear and
spacer to crankshaft, fit Allen bolts and tighten
to 78 Nm (58 lbf.ft).
5. Early engines: Fit drive plate and clamp ring,
fit bolts and tighten to 45 Nm (33 lbf.ft).
6. Later engines: Fit starter ring gear, fit Allen
bolts and tighten to 85 Nm (63 lbf.ft).
7. Later engines: Fit drive plate and clamp ring,
fit bolts and tighten to 45 Nm (33 lbf.ft).
8.Clean CKP sensor and mating face.
9.Fit crankshaft sensor and tighten nuts to 6 Nm
(5 lbf.ft).
10.Fit CKP sensor cover and tighten bolts to 6 Nm
(5 lbf.ft).
11.Fit CKP sensor multiplug to bracket.
12.Fit automatic gearbox.
+ AUTOMATIC GEARBOX - ZF4HP22
- 24, REPAIRS, Gearbox - convertor and
transfer gearbox - V8.
Page 190 of 1529
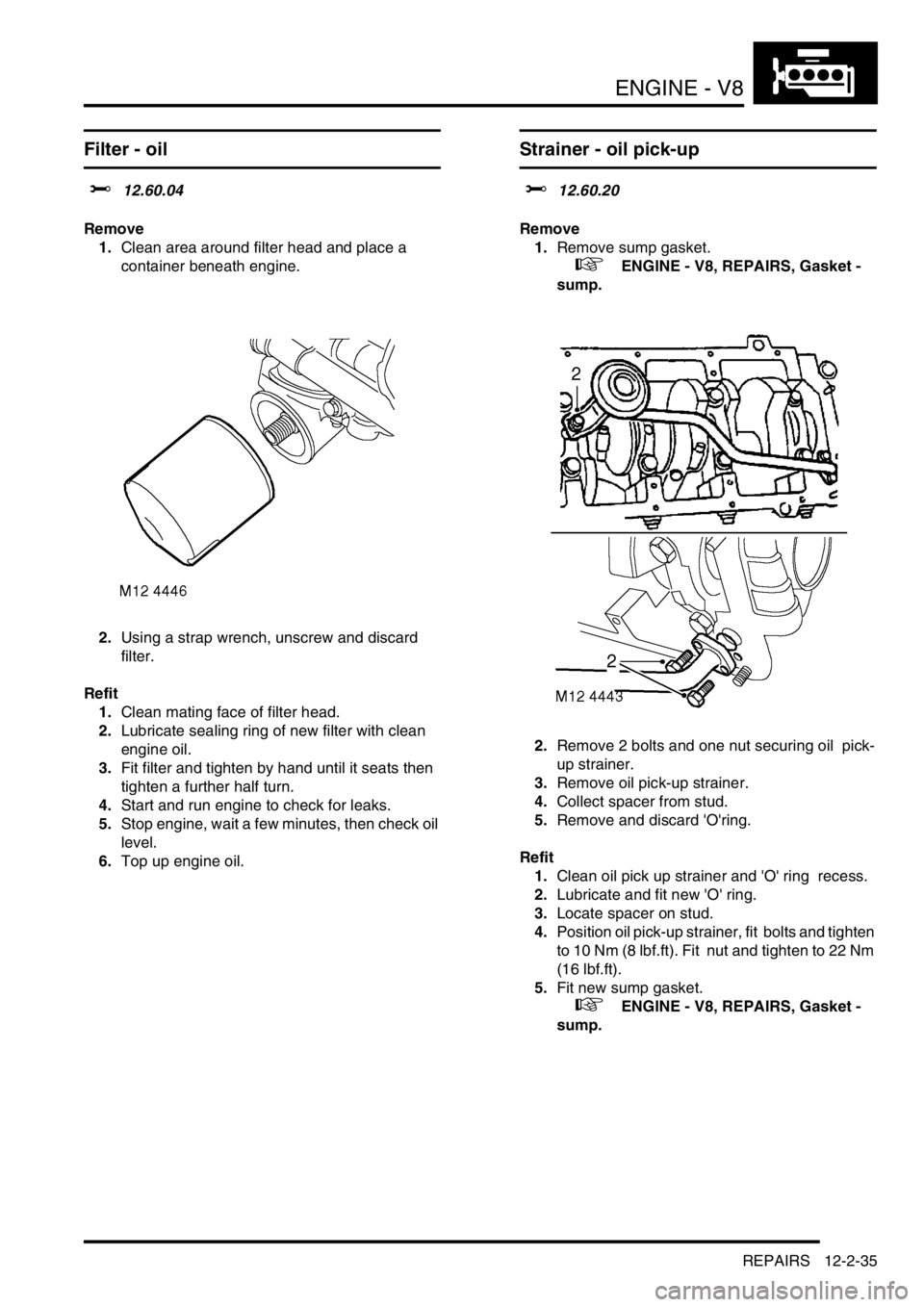
ENGINE - V8
REPAIRS 12-2-35
Filter - oil
$% 12.60.04
Remove
1.Clean area around filter head and place a
container beneath engine.
2.Using a strap wrench, unscrew and discard
filter.
Refit
1.Clean mating face of filter head.
2.Lubricate sealing ring of new filter with clean
engine oil.
3.Fit filter and tighten by hand until it seats then
tighten a further half turn.
4.Start and run engine to check for leaks.
5.Stop engine, wait a few minutes, then check oil
level.
6.Top up engine oil.
Strainer - oil pick-up
$% 12.60.20
Remove
1.Remove sump gasket.
+ ENGINE - V8, REPAIRS, Gasket -
sump.
2.Remove 2 bolts and one nut securing oil pick-
up strainer.
3.Remove oil pick-up strainer.
4.Collect spacer from stud.
5.Remove and discard 'O'ring.
Refit
1.Clean oil pick up strainer and 'O' ring recess.
2.Lubricate and fit new 'O' ring.
3.Locate spacer on stud.
4.Position oil pick-up strainer, fit bolts and tighten
to 10 Nm (8 lbf.ft). Fit nut and tighten to 22 Nm
(16 lbf.ft).
5.Fit new sump gasket.
+ ENGINE - V8, REPAIRS, Gasket -
sump.
Page 205 of 1529
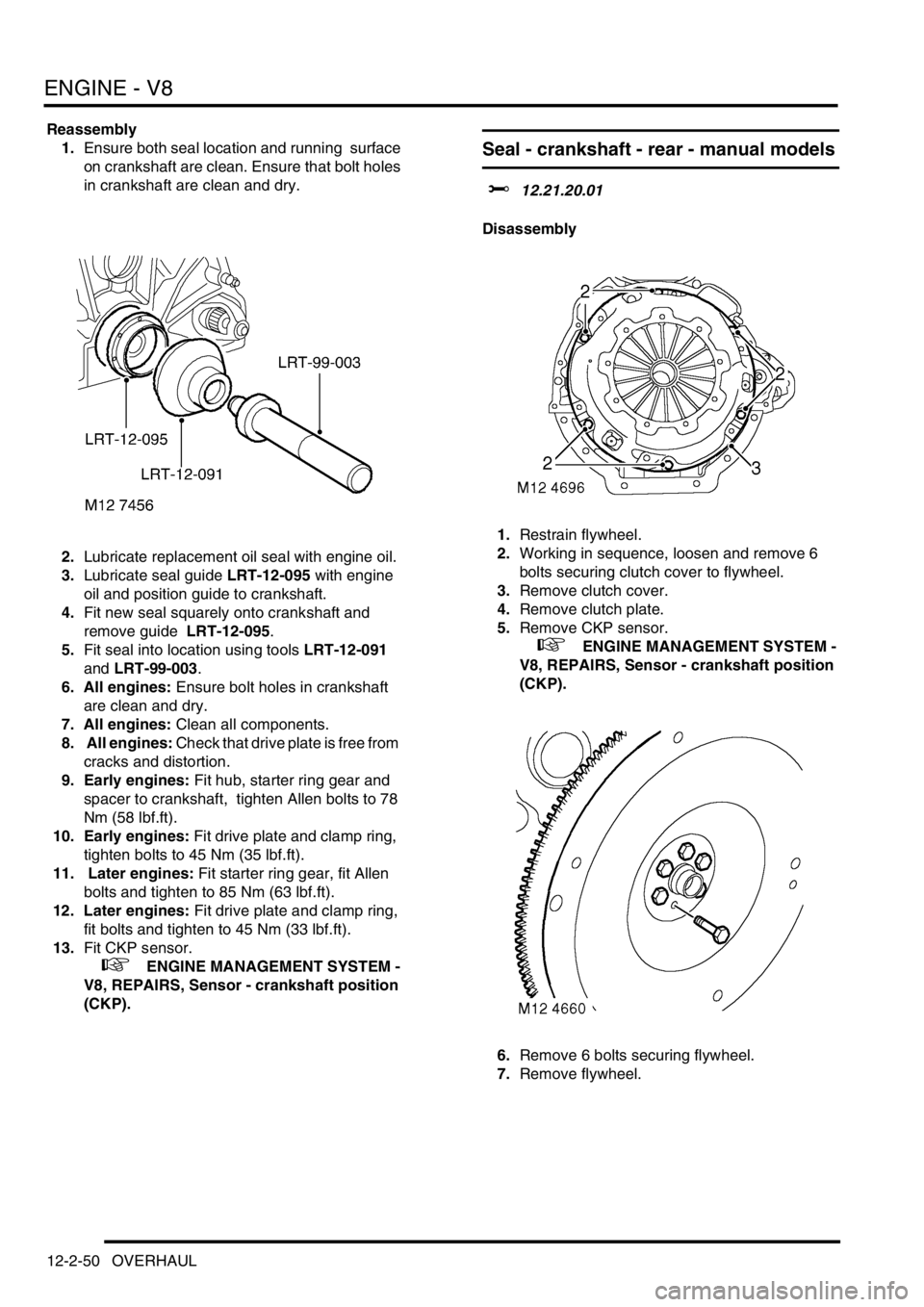
ENGINE - V8
12-2-50 OVERHAUL
Reassembly
1.Ensure both seal location and running surface
on crankshaft are clean. Ensure that bolt holes
in crankshaft are clean and dry.
2.Lubricate replacement oil seal with engine oil.
3.Lubricate seal guide LRT-12-095 with engine
oil and position guide to crankshaft.
4.Fit new seal squarely onto crankshaft and
remove guide LRT-12-095.
5.Fit seal into location using tools LRT-12-091
and LRT-99-003.
6. All engines: Ensure bolt holes in crankshaft
are clean and dry.
7. All engines: Clean all components.
8. All engines: Check that drive plate is free from
cracks and distortion.
9. Early engines: Fit hub, starter ring gear and
spacer to crankshaft, tighten Allen bolts to 78
Nm (58 lbf.ft).
10. Early engines: Fit drive plate and clamp ring,
tighten bolts to 45 Nm (35 lbf.ft).
11. Later engines: Fit starter ring gear, fit Allen
bolts and tighten to 85 Nm (63 lbf.ft).
12. Later engines: Fit drive plate and clamp ring,
fit bolts and tighten to 45 Nm (33 lbf.ft).
13.Fit CKP sensor.
+ ENGINE MANAGEMENT SYSTEM -
V8, REPAIRS, Sensor - crankshaft position
(CKP).
Seal - crankshaft - rear - manual models
$% 12.21.20.01
Disassembly
1.Restrain flywheel.
2.Working in sequence, loosen and remove 6
bolts securing clutch cover to flywheel.
3.Remove clutch cover.
4.Remove clutch plate.
5.Remove CKP sensor.
+ ENGINE MANAGEMENT SYSTEM -
V8, REPAIRS, Sensor - crankshaft position
(CKP).
6.Remove 6 bolts securing flywheel.
7.Remove flywheel.
Page 217 of 1529
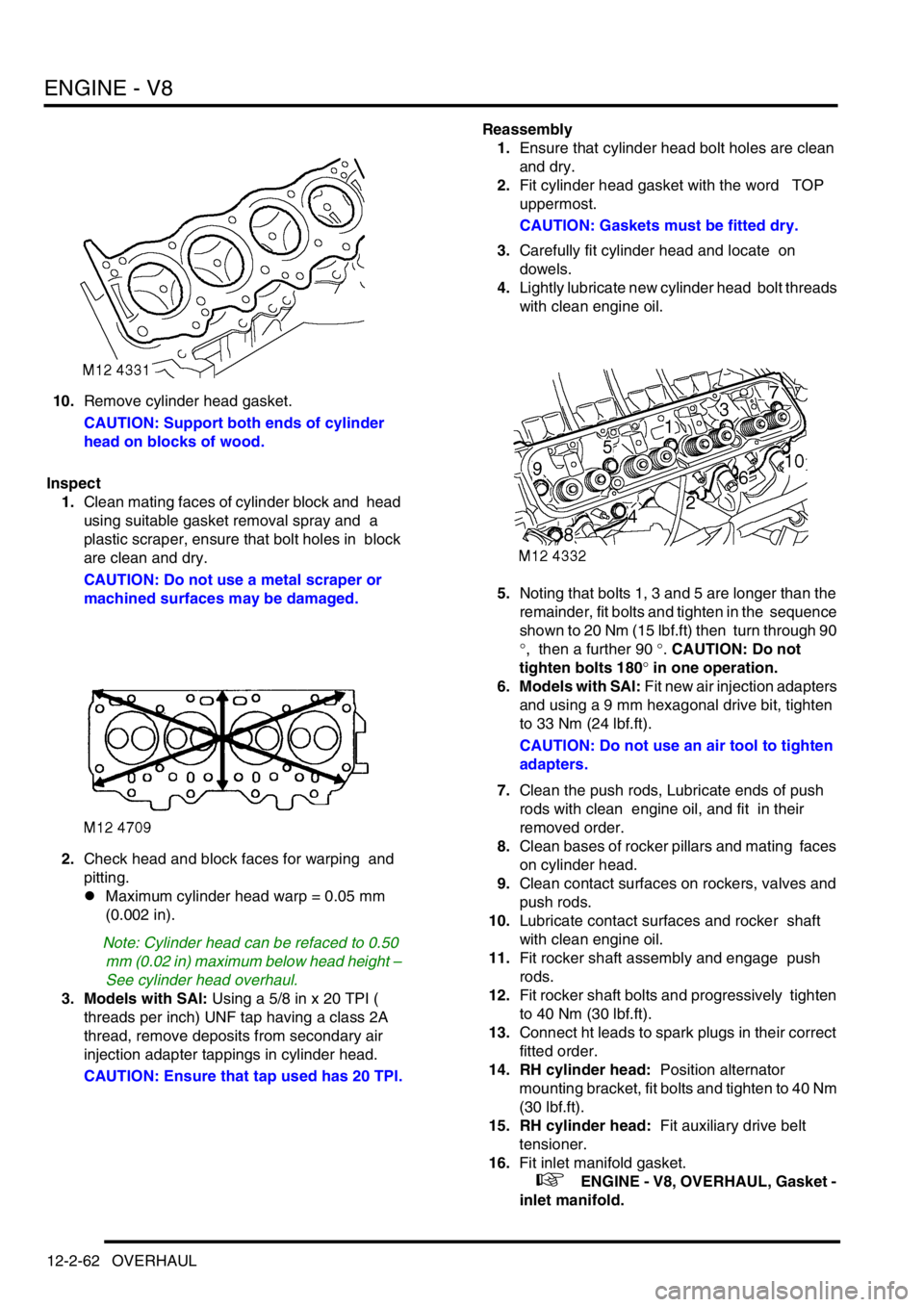
ENGINE - V8
12-2-62 OVERHAUL
10.Remove cylinder head gasket.
CAUTION: Support both ends of cylinder
head on blocks of wood.
Inspect
1.Clean mating faces of cylinder block and head
using suitable gasket removal spray and a
plastic scraper, ensure that bolt holes in block
are clean and dry.
CAUTION: Do not use a metal scraper or
machined surfaces may be damaged.
2.Check head and block faces for warping and
pitting.
lMaximum cylinder head warp = 0.05 mm
(0.002 in).
Note: Cylinder head can be refaced to 0.50
mm (0.02 in) maximum below head height –
See cylinder head overhaul.
3. Models with SAI: Using a 5/8 in x 20 TPI (
threads per inch) UNF tap having a class 2A
thread, remove deposits from secondary air
injection adapter tappings in cylinder head.
CAUTION: Ensure that tap used has 20 TPI.Reassembly
1.Ensure that cylinder head bolt holes are clean
and dry.
2.Fit cylinder head gasket with the word TOP
uppermost.
CAUTION: Gaskets must be fitted dry.
3.Carefully fit cylinder head and locate on
dowels.
4.Lightly lubricate new cylinder head bolt threads
with clean engine oil.
5.Noting that bolts 1, 3 and 5 are longer than the
remainder, fit bolts and tighten in the sequence
shown to 20 Nm (15 lbf.ft) then turn through 90
°, then a further 90 °. CAUTION: Do not
tighten bolts 180° in one operation.
6. Models with SAI: Fit new air injection adapters
and using a 9 mm hexagonal drive bit, tighten
to 33 Nm (24 lbf.ft).
CAUTION: Do not use an air tool to tighten
adapters.
7.Clean the push rods, Lubricate ends of push
rods with clean engine oil, and fit in their
removed order.
8.Clean bases of rocker pillars and mating faces
on cylinder head.
9.Clean contact surfaces on rockers, valves and
push rods.
10.Lubricate contact surfaces and rocker shaft
with clean engine oil.
11.Fit rocker shaft assembly and engage push
rods.
12.Fit rocker shaft bolts and progressively tighten
to 40 Nm (30 lbf.ft).
13.Connect ht leads to spark plugs in their correct
fitted order.
14. RH cylinder head: Position alternator
mounting bracket, fit bolts and tighten to 40 Nm
(30 lbf.ft).
15. RH cylinder head: Fit auxiliary drive belt
tensioner.
16.Fit inlet manifold gasket.
+ ENGINE - V8, OVERHAUL, Gasket -
inlet manifold.
Page 218 of 1529
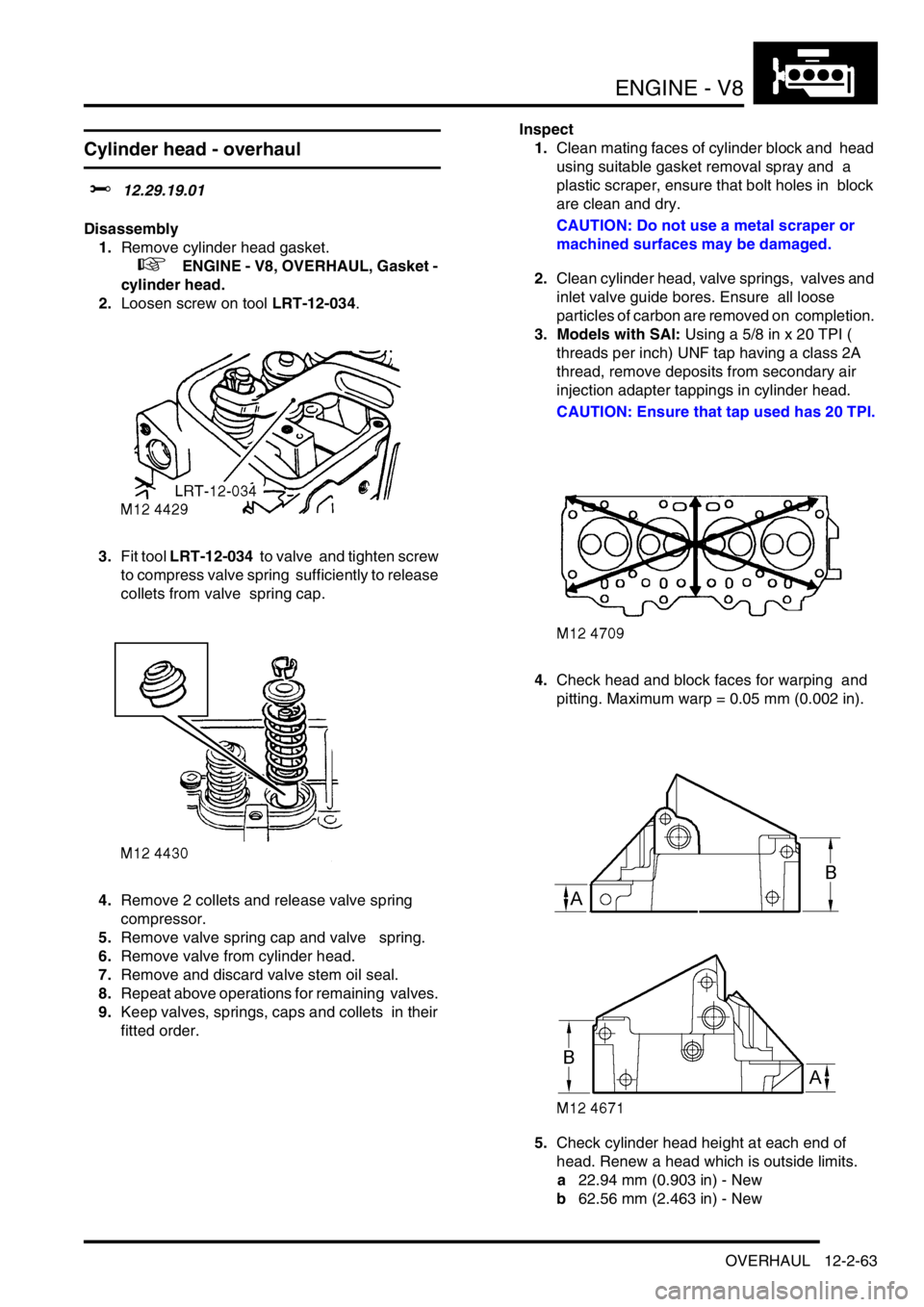
ENGINE - V8
OVERHAUL 12-2-63
Cylinder head - overhaul
$% 12.29.19.01
Disassembly
1.Remove cylinder head gasket.
+ ENGINE - V8, OVERHAUL, Gasket -
cylinder head.
2.Loosen screw on tool LRT-12-034.
3.Fit tool LRT-12-034 to valve and tighten screw
to compress valve spring sufficiently to release
collets from valve spring cap.
4.Remove 2 collets and release valve spring
compressor.
5.Remove valve spring cap and valve spring.
6.Remove valve from cylinder head.
7.Remove and discard valve stem oil seal.
8.Repeat above operations for remaining valves.
9.Keep valves, springs, caps and collets in their
fitted order. Inspect
1.Clean mating faces of cylinder block and head
using suitable gasket removal spray and a
plastic scraper, ensure that bolt holes in block
are clean and dry.
CAUTION: Do not use a metal scraper or
machined surfaces may be damaged.
2.Clean cylinder head, valve springs, valves and
inlet valve guide bores. Ensure all loose
particles of carbon are removed on completion.
3. Models with SAI: Using a 5/8 in x 20 TPI (
threads per inch) UNF tap having a class 2A
thread, remove deposits from secondary air
injection adapter tappings in cylinder head.
CAUTION: Ensure that tap used has 20 TPI.
4.Check head and block faces for warping and
pitting. Maximum warp = 0.05 mm (0.002 in).
5.Check cylinder head height at each end of
head. Renew a head which is outside limits.
a22.94 mm (0.903 in) - New
b62.56 mm (2.463 in) - New
Page 220 of 1529
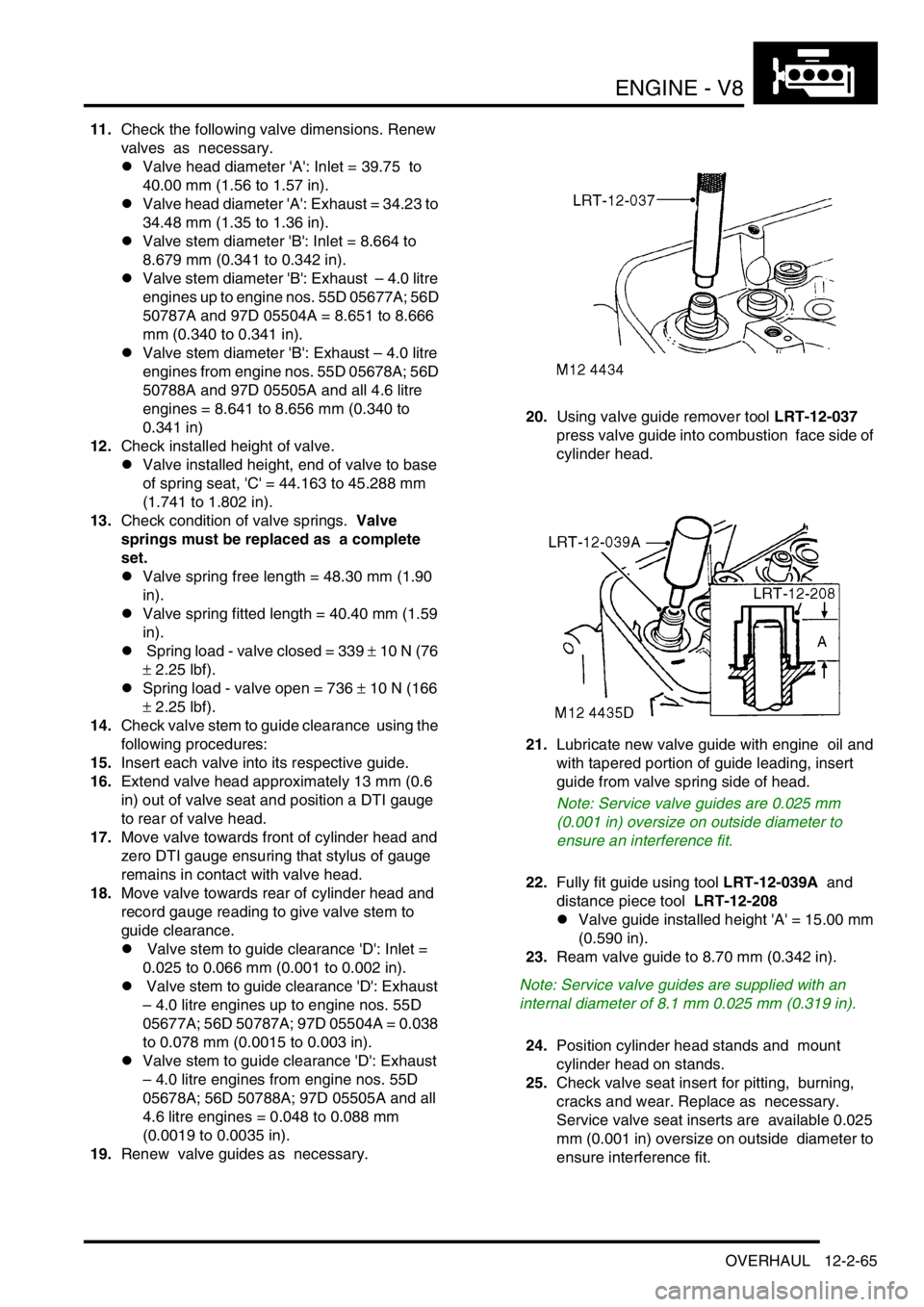
ENGINE - V8
OVERHAUL 12-2-65
11.Check the following valve dimensions. Renew
valves as necessary.
lValve head diameter 'A': Inlet = 39.75 to
40.00 mm (1.56 to 1.57 in).
lValve head diameter 'A': Exhaust = 34.23 to
34.48 mm (1.35 to 1.36 in).
lValve stem diameter 'B': Inlet = 8.664 to
8.679 mm (0.341 to 0.342 in).
lValve stem diameter 'B': Exhaust – 4.0 litre
engines up to engine nos. 55D 05677A; 56D
50787A and 97D 05504A = 8.651 to 8.666
mm (0.340 to 0.341 in).
lValve stem diameter 'B': Exhaust – 4.0 litre
engines from engine nos. 55D 05678A; 56D
50788A and 97D 05505A and all 4.6 litre
engines = 8.641 to 8.656 mm (0.340 to
0.341 in)
12.Check installed height of valve.
lValve installed height, end of valve to base
of spring seat, 'C' = 44.163 to 45.288 mm
(1.741 to 1.802 in).
13.Check condition of valve springs. Valve
springs must be replaced as a complete
set.
lValve spring free length = 48.30 mm (1.90
in).
lValve spring fitted length = 40.40 mm (1.59
in).
l Spring load - valve closed = 339 ± 10 N (76
± 2.25 lbf).
lSpring load - valve open = 736 ± 10 N (166
± 2.25 lbf).
14.Check valve stem to guide clearance using the
following procedures:
15.Insert each valve into its respective guide.
16.Extend valve head approximately 13 mm (0.6
in) out of valve seat and position a DTI gauge
to rear of valve head.
17.Move valve towards front of cylinder head and
zero DTI gauge ensuring that stylus of gauge
remains in contact with valve head.
18.Move valve towards rear of cylinder head and
record gauge reading to give valve stem to
guide clearance.
l Valve stem to guide clearance 'D': Inlet =
0.025 to 0.066 mm (0.001 to 0.002 in).
l Valve stem to guide clearance 'D': Exhaust
– 4.0 litre engines up to engine nos. 55D
05677A; 56D 50787A; 97D 05504A = 0.038
to 0.078 mm (0.0015 to 0.003 in).
lValve stem to guide clearance 'D': Exhaust
– 4.0 litre engines from engine nos. 55D
05678A; 56D 50788A; 97D 05505A and all
4.6 litre engines = 0.048 to 0.088 mm
(0.0019 to 0.0035 in).
19.Renew valve guides as necessary. 20.Using valve guide remover tool LRT-12-037
press valve guide into combustion face side of
cylinder head.
21.Lubricate new valve guide with engine oil and
with tapered portion of guide leading, insert
guide from valve spring side of head.
Note: Service valve guides are 0.025 mm
(0.001 in) oversize on outside diameter to
ensure an interference fit.
22.Fully fit guide using tool LRT-12-039A and
distance piece tool LRT-12-208
lValve guide installed height 'A' = 15.00 mm
(0.590 in).
23.Ream valve guide to 8.70 mm (0.342 in).
Note: Service valve guides are supplied with an
internal diameter of 8.1 mm 0.025 mm (0.319 in).
24.Position cylinder head stands and mount
cylinder head on stands.
25.Check valve seat insert for pitting, burning,
cracks and wear. Replace as necessary.
Service valve seat inserts are available 0.025
mm (0.001 in) oversize on outside diameter to
ensure interference fit.
Page 221 of 1529
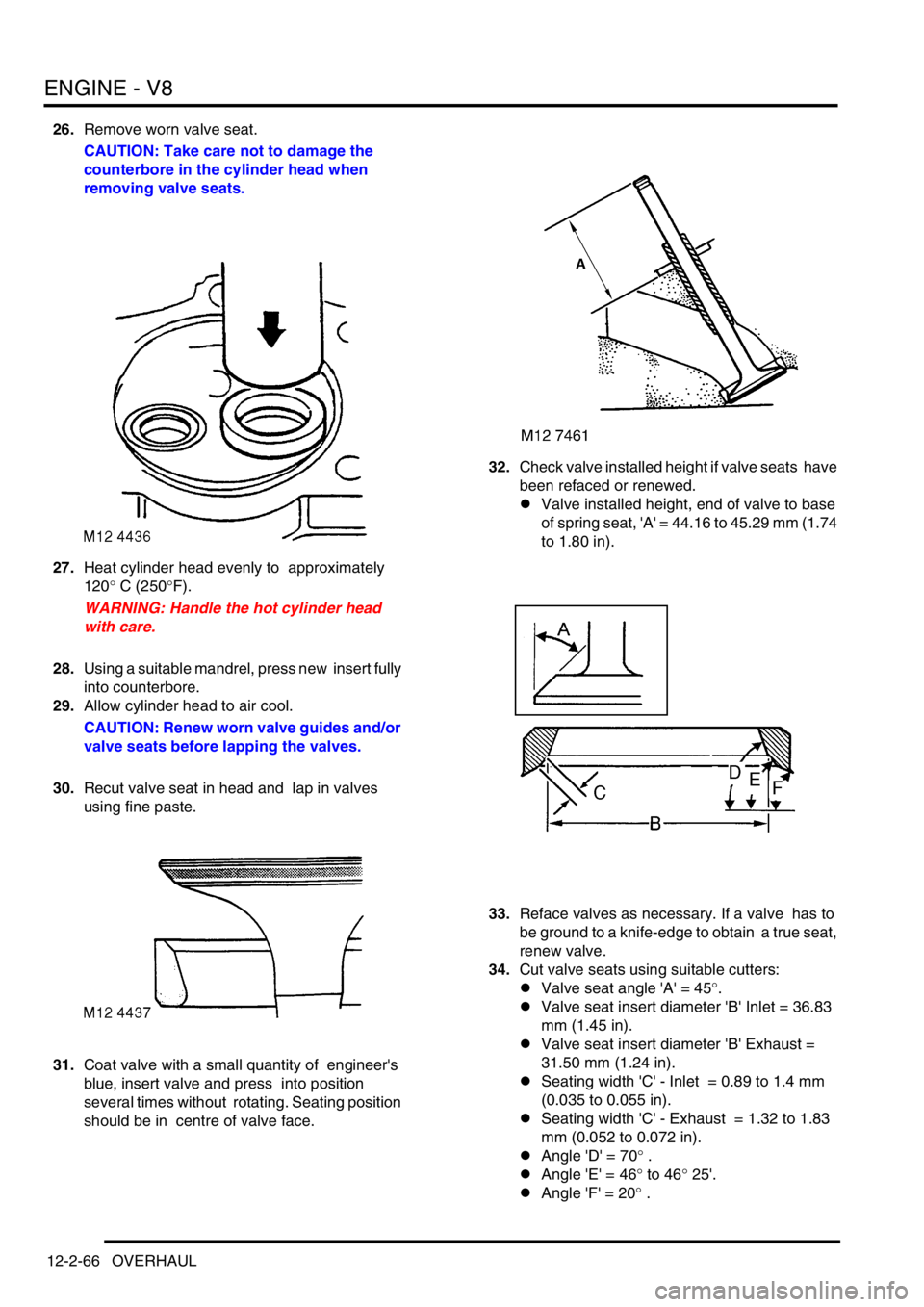
ENGINE - V8
12-2-66 OVERHAUL
26.Remove worn valve seat.
CAUTION: Take care not to damage the
counterbore in the cylinder head when
removing valve seats.
27.Heat cylinder head evenly to approximately
120° C (250°F).
WARNING: Handle the hot cylinder head
with care.
28.Using a suitable mandrel, press new insert fully
into counterbore.
29.Allow cylinder head to air cool.
CAUTION: Renew worn valve guides and/or
valve seats before lapping the valves.
30.Recut valve seat in head and lap in valves
using fine paste.
31.Coat valve with a small quantity of engineer's
blue, insert valve and press into position
several times without rotating. Seating position
should be in centre of valve face. 32.Check valve installed height if valve seats have
been refaced or renewed.
lValve installed height, end of valve to base
of spring seat, 'A' = 44.16 to 45.29 mm (1.74
to 1.80 in).
33.Reface valves as necessary. If a valve has to
be ground to a knife-edge to obtain a true seat,
renew valve.
34.Cut valve seats using suitable cutters:
lValve seat angle 'A' = 45°.
lValve seat insert diameter 'B' Inlet = 36.83
mm (1.45 in).
lValve seat insert diameter 'B' Exhaust =
31.50 mm (1.24 in).
lSeating width 'C' - Inlet = 0.89 to 1.4 mm
(0.035 to 0.055 in).
lSeating width 'C' - Exhaust = 1.32 to 1.83
mm (0.052 to 0.072 in).
lAngle 'D' = 70° .
lAngle 'E' = 46° to 46° 25'.
lAngle 'F' = 20° .
Page 222 of 1529
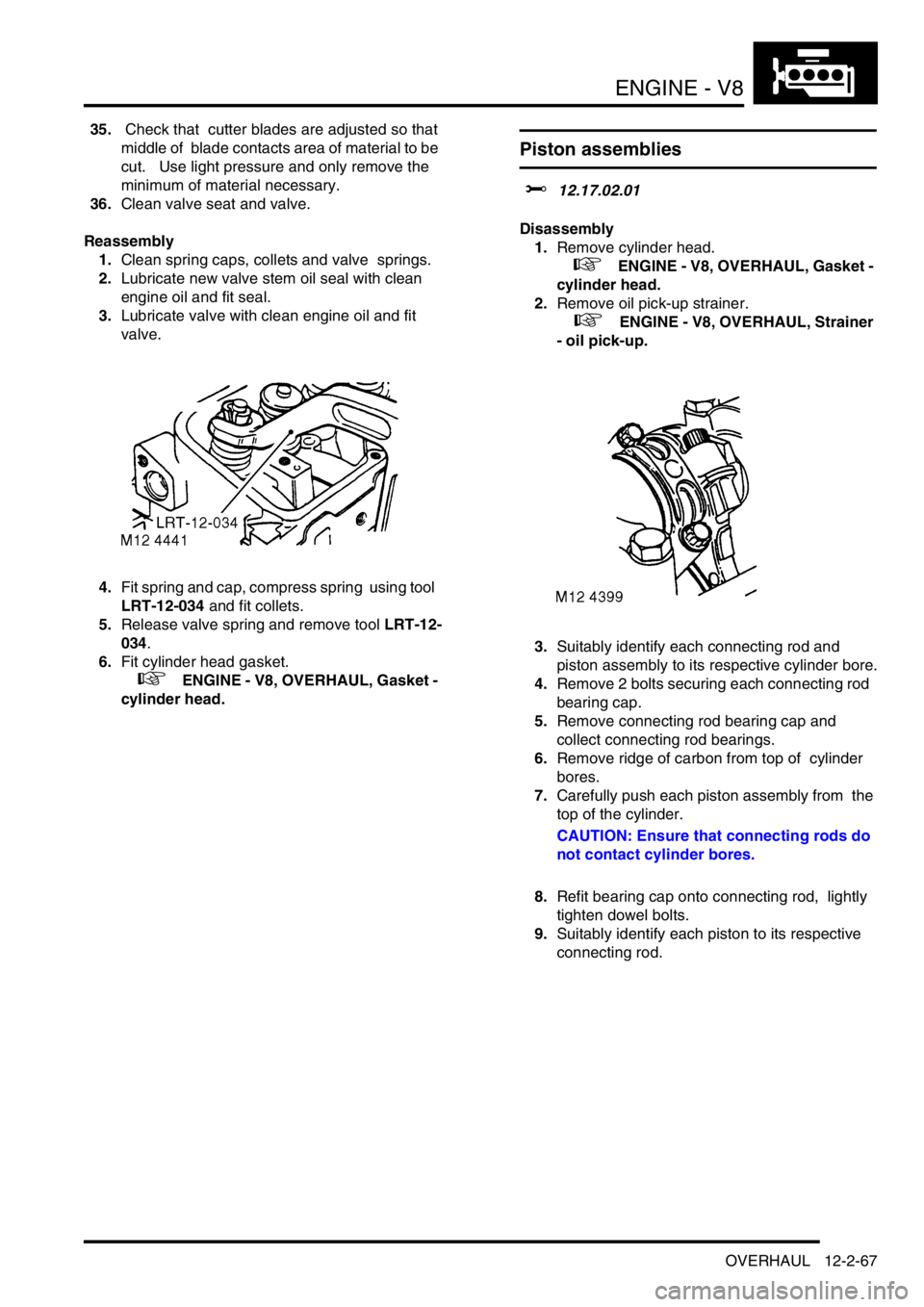
ENGINE - V8
OVERHAUL 12-2-67
35. Check that cutter blades are adjusted so that
middle of blade contacts area of material to be
cut. Use light pressure and only remove the
minimum of material necessary.
36.Clean valve seat and valve.
Reassembly
1.Clean spring caps, collets and valve springs.
2.Lubricate new valve stem oil seal with clean
engine oil and fit seal.
3.Lubricate valve with clean engine oil and fit
valve.
4.Fit spring and cap, compress spring using tool
LRT-12-034 and fit collets.
5.Release valve spring and remove tool LRT-12-
034.
6.Fit cylinder head gasket.
+ ENGINE - V8, OVERHAUL, Gasket -
cylinder head.
Piston assemblies
$% 12.17.02.01
Disassembly
1.Remove cylinder head.
+ ENGINE - V8, OVERHAUL, Gasket -
cylinder head.
2.Remove oil pick-up strainer.
+ ENGINE - V8, OVERHAUL, Strainer
- oil pick-up.
3.Suitably identify each connecting rod and
piston assembly to its respective cylinder bore.
4.Remove 2 bolts securing each connecting rod
bearing cap.
5.Remove connecting rod bearing cap and
collect connecting rod bearings.
6.Remove ridge of carbon from top of cylinder
bores.
7.Carefully push each piston assembly from the
top of the cylinder.
CAUTION: Ensure that connecting rods do
not contact cylinder bores.
8.Refit bearing cap onto connecting rod, lightly
tighten dowel bolts.
9.Suitably identify each piston to its respective
connecting rod.
Page 223 of 1529
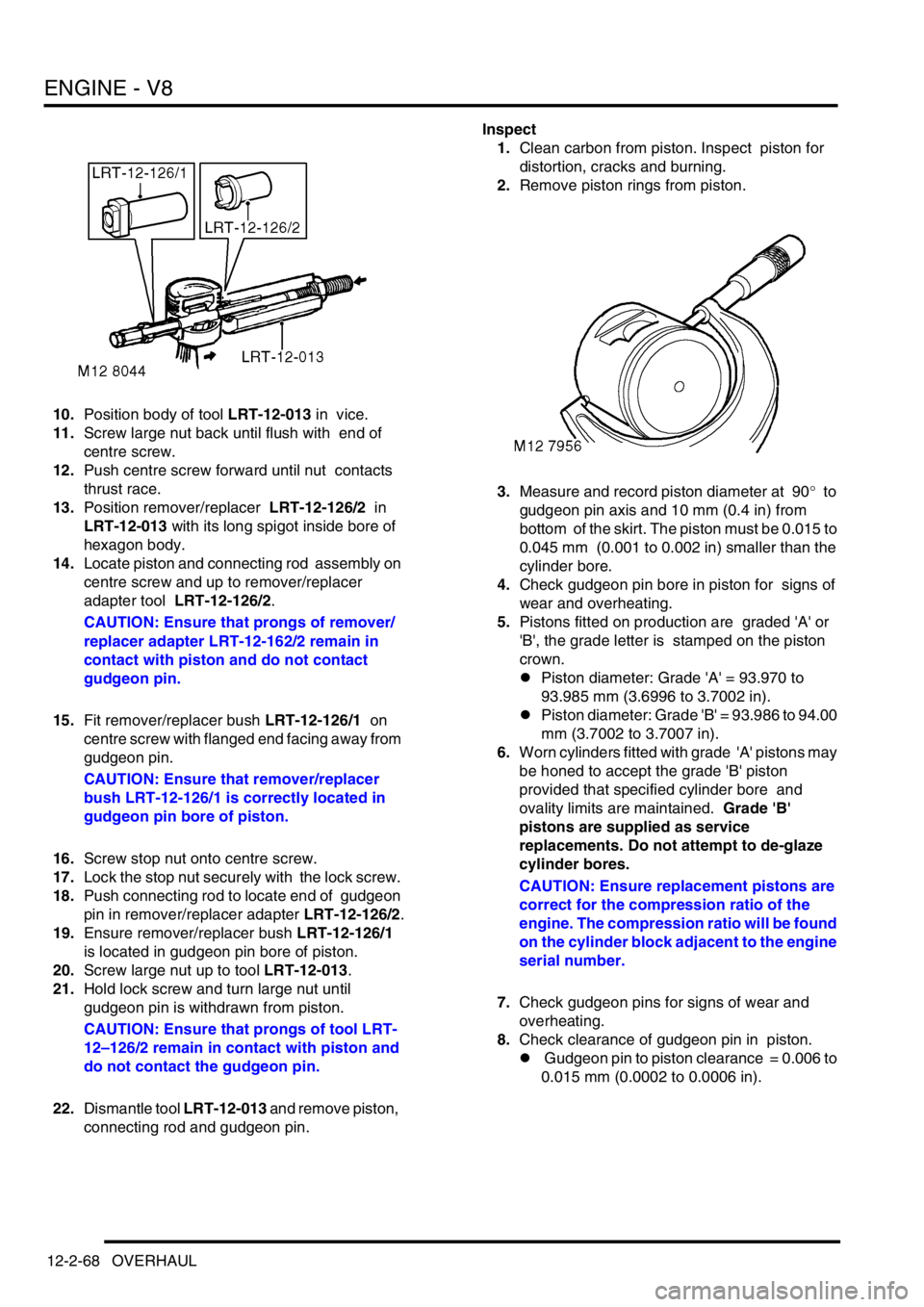
ENGINE - V8
12-2-68 OVERHAUL
10.Position body of tool LRT-12-013 in vice.
11.Screw large nut back until flush with end of
centre screw.
12.Push centre screw forward until nut contacts
thrust race.
13.Position remover/replacer LRT-12-126/2 in
LRT-12-013 with its long spigot inside bore of
hexagon body.
14.Locate piston and connecting rod assembly on
centre screw and up to remover/replacer
adapter tool LRT-12-126/2.
CAUTION: Ensure that prongs of remover/
replacer adapter LRT-12-162/2 remain in
contact with piston and do not contact
gudgeon pin.
15.Fit remover/replacer bush LRT-12-126/1 on
centre screw with flanged end facing away from
gudgeon pin.
CAUTION: Ensure that remover/replacer
bush LRT-12-126/1 is correctly located in
gudgeon pin bore of piston.
16.Screw stop nut onto centre screw.
17.Lock the stop nut securely with the lock screw.
18.Push connecting rod to locate end of gudgeon
pin in remover/replacer adapter LRT-12-126/2.
19.Ensure remover/replacer bush LRT-12-126/1
is located in gudgeon pin bore of piston.
20.Screw large nut up to tool LRT-12-013.
21.Hold lock screw and turn large nut until
gudgeon pin is withdrawn from piston.
CAUTION: Ensure that prongs of tool LRT-
12–126/2 remain in contact with piston and
do not contact the gudgeon pin.
22.Dismantle tool LRT-12-013 and remove piston,
connecting rod and gudgeon pin. Inspect
1.Clean carbon from piston. Inspect piston for
distortion, cracks and burning.
2.Remove piston rings from piston.
3.Measure and record piston diameter at 90° to
gudgeon pin axis and 10 mm (0.4 in) from
bottom of the skirt. The piston must be 0.015 to
0.045 mm (0.001 to 0.002 in) smaller than the
cylinder bore.
4.Check gudgeon pin bore in piston for signs of
wear and overheating.
5.Pistons fitted on production are graded 'A' or
'B', the grade letter is stamped on the piston
crown.
lPiston diameter: Grade 'A' = 93.970 to
93.985 mm (3.6996 to 3.7002 in).
lPiston diameter: Grade 'B' = 93.986 to 94.00
mm (3.7002 to 3.7007 in).
6.Worn cylinders fitted with grade 'A' pistons may
be honed to accept the grade 'B' piston
provided that specified cylinder bore and
ovality limits are maintained. Grade 'B'
pistons are supplied as service
replacements. Do not attempt to de-glaze
cylinder bores.
CAUTION: Ensure replacement pistons are
correct for the compression ratio of the
engine. The compression ratio will be found
on the cylinder block adjacent to the engine
serial number.
7.Check gudgeon pins for signs of wear and
overheating.
8.Check clearance of gudgeon pin in piston.
l Gudgeon pin to piston clearance = 0.006 to
0.015 mm (0.0002 to 0.0006 in).