fuse box LAND ROVER DISCOVERY 1999 Owner's Manual
[x] Cancel search | Manufacturer: LAND ROVER, Model Year: 1999, Model line: DISCOVERY, Model: LAND ROVER DISCOVERY 1999Pages: 1529, PDF Size: 34.8 MB
Page 347 of 1529
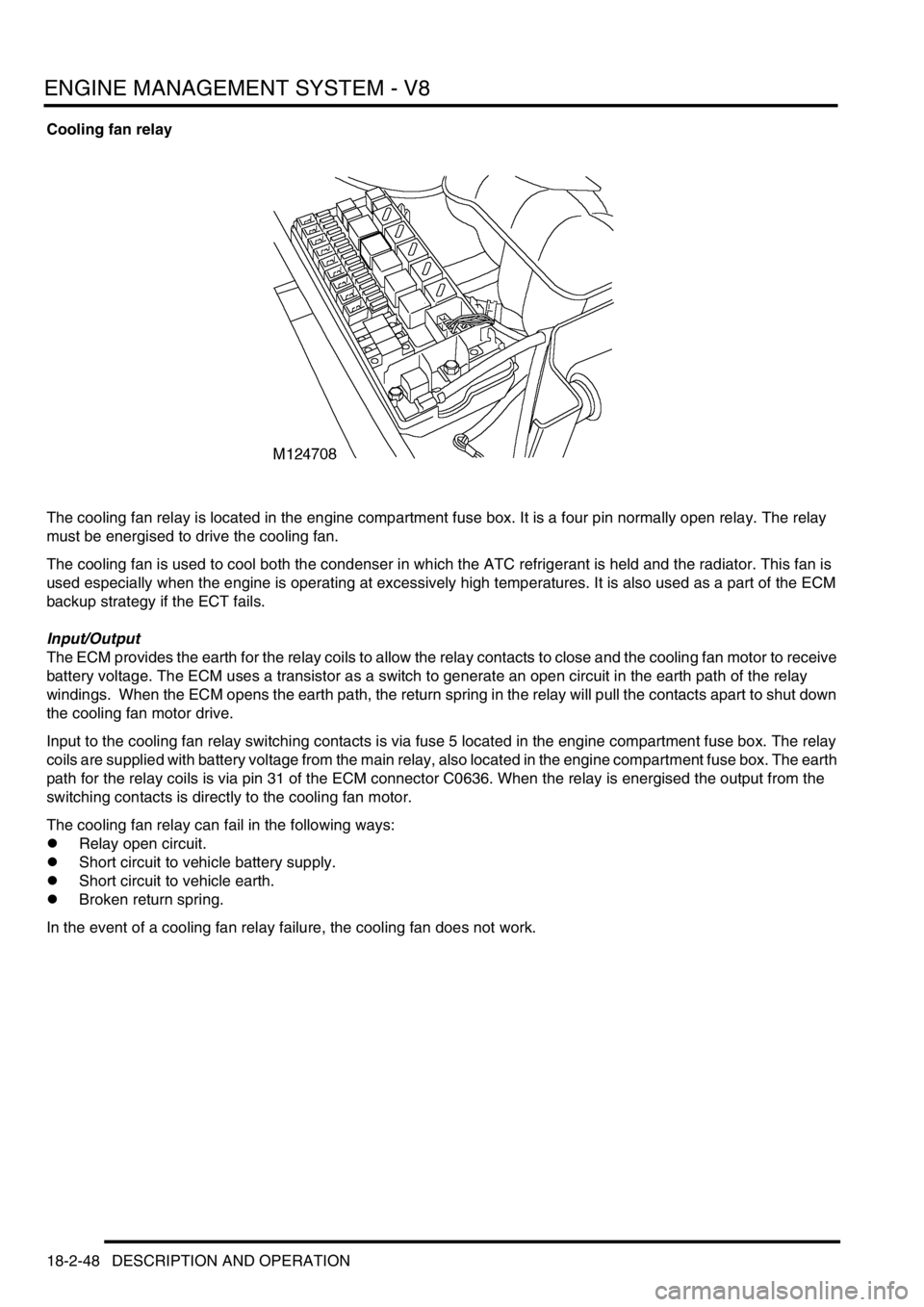
ENGINE MANAGEMENT SYSTEM - V8
18-2-48 DESCRIPTION AND OPERATION
Cooling fan relay
The cooling fan relay is located in the engine compartment fuse box. It is a four pin normally open relay. The relay
must be energised to drive the cooling fan.
The cooling fan is used to cool both the condenser in which the ATC refrigerant is held and the radiator. This fan is
used especially when the engine is operating at excessively high temperatures. It is also used as a part of the ECM
backup strategy if the ECT fails.
Input/Output
The ECM provides the earth for the relay coils to allow the relay contacts to close and the cooling fan motor to receive
battery voltage. The ECM uses a transistor as a switch to generate an open circuit in the earth path of the relay
windings. When the ECM opens the earth path, the return spring in the relay will pull the contacts apart to shut down
the cooling fan motor drive.
Input to the cooling fan relay switching contacts is via fuse 5 located in the engine compartment fuse box. The relay
coils are supplied with battery voltage from the main relay, also located in the engine compartment fuse box. The earth
path for the relay coils is via pin 31 of the ECM connector C0636. When the relay is energised the output from the
switching contacts is directly to the cooling fan motor.
The cooling fan relay can fail in the following ways:
lRelay open circuit.
lShort circuit to vehicle battery supply.
lShort circuit to vehicle earth.
lBroken return spring.
In the event of a cooling fan relay failure, the cooling fan does not work.
Page 403 of 1529
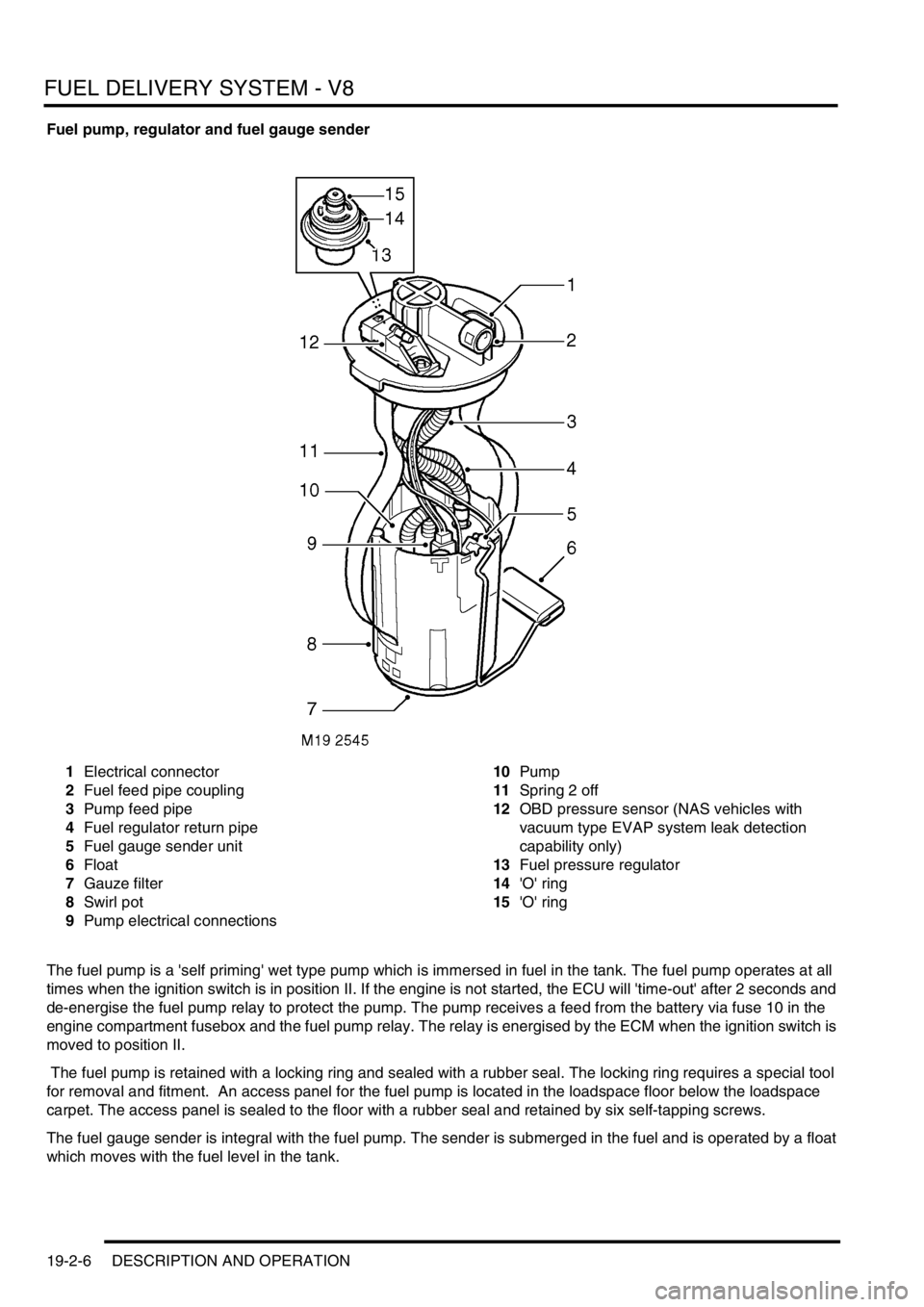
FUEL DELIVERY SYSTEM - V8
19-2-6 DESCRIPTION AND OPERATION
Fuel pump, regulator and fuel gauge sender
1Electrical connector
2Fuel feed pipe coupling
3Pump feed pipe
4Fuel regulator return pipe
5Fuel gauge sender unit
6Float
7Gauze filter
8Swirl pot
9Pump electrical connections10Pump
11Spring 2 off
12OBD pressure sensor (NAS vehicles with
vacuum type EVAP system leak detection
capability only)
13Fuel pressure regulator
14'O' ring
15'O' ring
The fuel pump is a 'self priming' wet type pump which is immersed in fuel in the tank. The fuel pump operates at all
times when the ignition switch is in position II. If the engine is not started, the ECU will 'time-out' after 2 seconds and
de-energise the fuel pump relay to protect the pump. The pump receives a feed from the battery via fuse 10 in the
engine compartment fusebox and the fuel pump relay. The relay is energised by the ECM when the ignition switch is
moved to position II.
The fuel pump is retained with a locking ring and sealed with a rubber seal. The locking ring requires a special tool
for removal and fitment. An access panel for the fuel pump is located in the loadspace floor below the loadspace
carpet. The access panel is sealed to the floor with a rubber seal and retained by six self-tapping screws.
The fuel gauge sender is integral with the fuel pump. The sender is submerged in the fuel and is operated by a float
which moves with the fuel level in the tank.
Page 406 of 1529
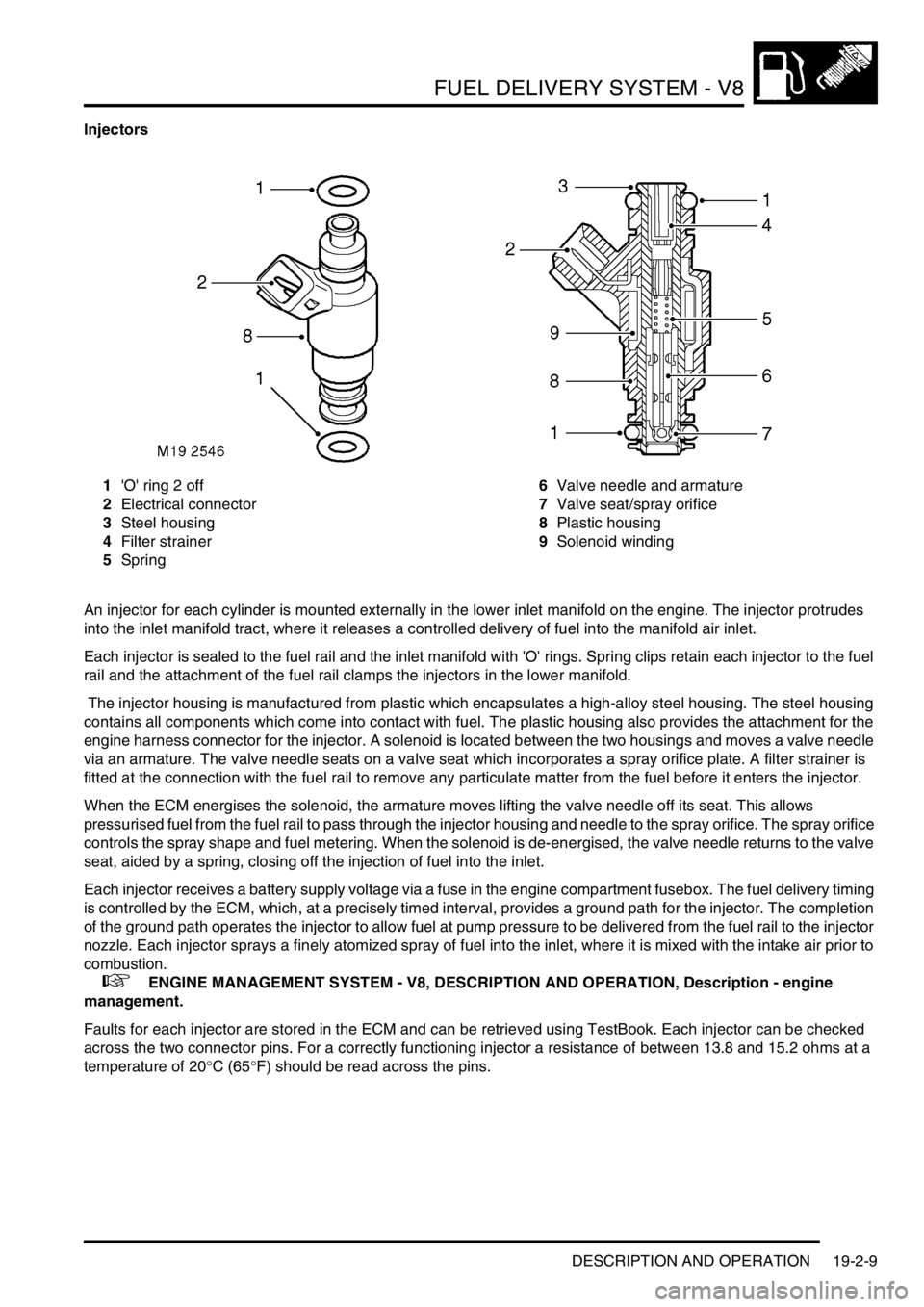
FUEL DELIVERY SYSTEM - V8
DESCRIPTION AND OPERATION 19-2-9
Injectors
1'O' ring 2 off
2Electrical connector
3Steel housing
4Filter strainer
5Spring6Valve needle and armature
7Valve seat/spray orifice
8Plastic housing
9Solenoid winding
An injector for each cylinder is mounted externally in the lower inlet manifold on the engine. The injector protrudes
into the inlet manifold tract, where it releases a controlled delivery of fuel into the manifold air inlet.
Each injector is sealed to the fuel rail and the inlet manifold with 'O' rings. Spring clips retain each injector to the fuel
rail and the attachment of the fuel rail clamps the injectors in the lower manifold.
The injector housing is manufactured from plastic which encapsulates a high-alloy steel housing. The steel housing
contains all components which come into contact with fuel. The plastic housing also provides the attachment for the
engine harness connector for the injector. A solenoid is located between the two housings and moves a valve needle
via an armature. The valve needle seats on a valve seat which incorporates a spray orifice plate. A filter strainer is
fitted at the connection with the fuel rail to remove any particulate matter from the fuel before it enters the injector.
When the ECM energises the solenoid, the armature moves lifting the valve needle off its seat. This allows
pressurised fuel from the fuel rail to pass through the injector housing and needle to the spray orifice. The spray orifice
controls the spray shape and fuel metering. When the solenoid is de-energised, the valve needle returns to the valve
seat, aided by a spring, closing off the injection of fuel into the inlet.
Each injector receives a battery supply voltage via a fuse in the engine compartment fusebox. The fuel delivery timing
is controlled by the ECM, which, at a precisely timed interval, provides a ground path for the injector. The completion
of the ground path operates the injector to allow fuel at pump pressure to be delivered from the fuel rail to the injector
nozzle. Each injector sprays a finely atomized spray of fuel into the inlet, where it is mixed with the intake air prior to
combustion.
+ ENGINE MANAGEMENT SYSTEM - V8, DESCRIPTION AND OPERATION, Description - engine
management.
Faults for each injector are stored in the ECM and can be retrieved using TestBook. Each injector can be checked
across the two connector pins. For a correctly functioning injector a resistance of between 13.8 and 15.2 ohms at a
temperature of 20°C (65°F) should be read across the pins.
Page 407 of 1529
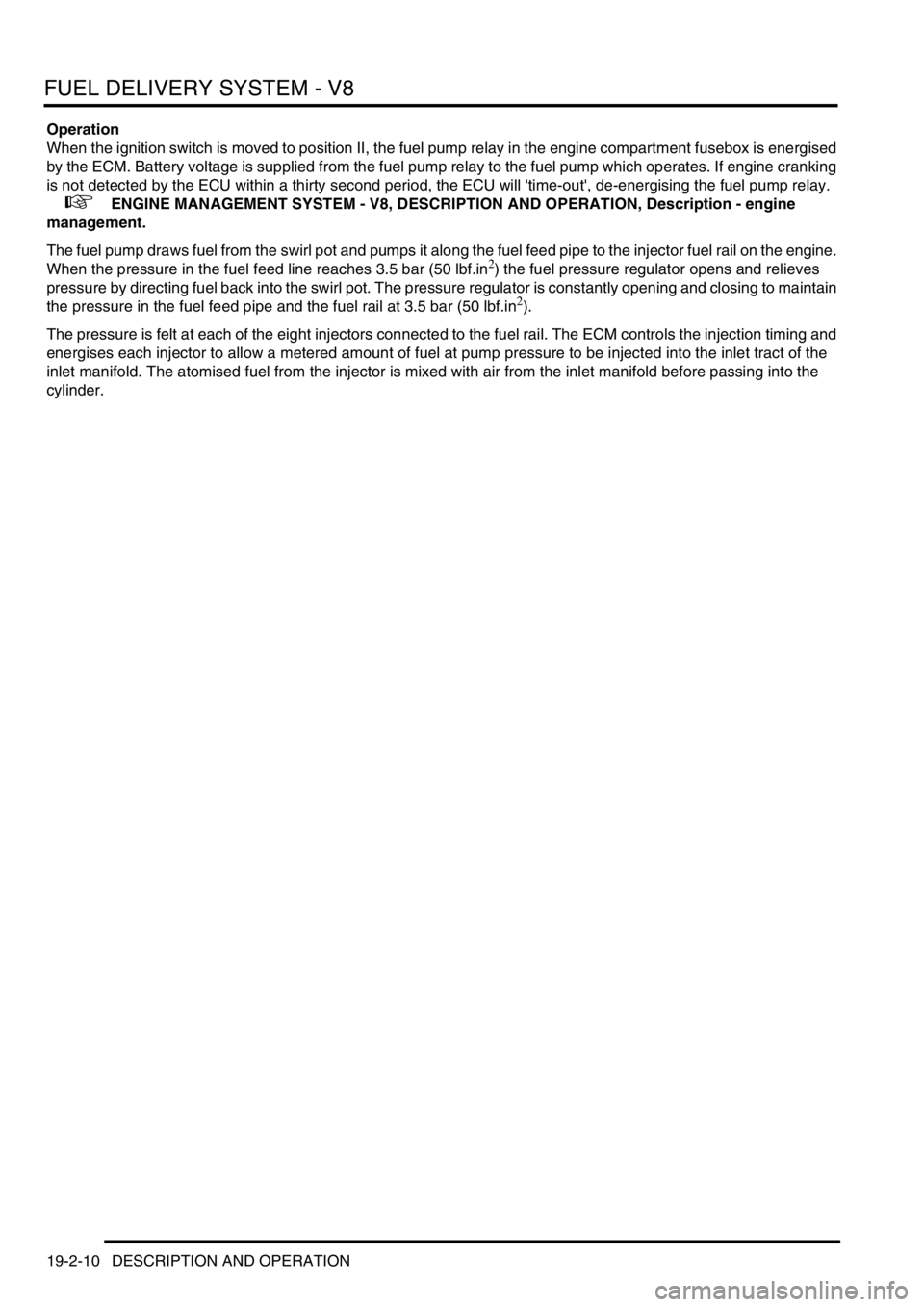
FUEL DELIVERY SYSTEM - V8
19-2-10 DESCRIPTION AND OPERATION
Operation
When the ignition switch is moved to position II, the fuel pump relay in the engine compartment fusebox is energised
by the ECM. Battery voltage is supplied from the fuel pump relay to the fuel pump which operates. If engine cranking
is not detected by the ECU within a thirty second period, the ECU will 'time-out', de-energising the fuel pump relay.
+ ENGINE MANAGEMENT SYSTEM - V8, DESCRIPTION AND OPERATION, Description - engine
management.
The fuel pump draws fuel from the swirl pot and pumps it along the fuel feed pipe to the injector fuel rail on the engine.
When the pressure in the fuel feed line reaches 3.5 bar (50 lbf.in
2) the fuel pressure regulator opens and relieves
pressure by directing fuel back into the swirl pot. The pressure regulator is constantly opening and closing to maintain
the pressure in the fuel feed pipe and the fuel rail at 3.5 bar (50 lbf.in
2).
The pressure is felt at each of the eight injectors connected to the fuel rail. The ECM controls the injection timing and
energises each injector to allow a metered amount of fuel at pump pressure to be injected into the inlet tract of the
inlet manifold. The atomised fuel from the injector is mixed with air from the inlet manifold before passing into the
cylinder.
Page 478 of 1529
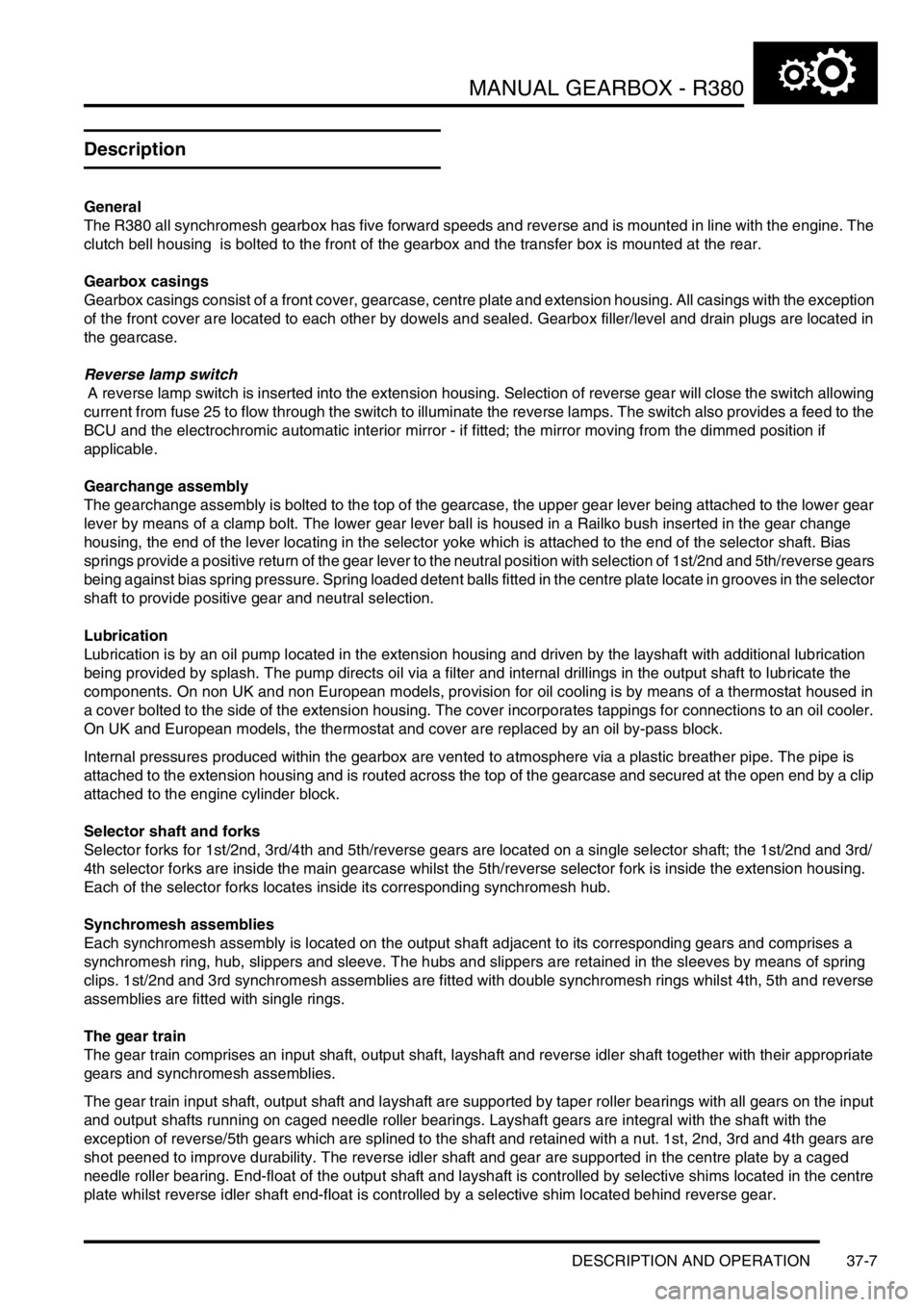
MANUAL GEARBOX - R380
DESCRIPTION AND OPERATION 37-7
Description
General
The R380 all synchromesh gearbox has five forward speeds and reverse and is mounted in line with the engine. The
clutch bell housing is bolted to the front of the gearbox and the transfer box is mounted at the rear.
Gearbox casings
Gearbox casings consist of a front cover, gearcase, centre plate and extension housing. All casings with the exception
of the front cover are located to each other by dowels and sealed. Gearbox filler/level and drain plugs are located in
the gearcase.
Reverse lamp switch
A reverse lamp switch is inserted into the extension housing. Selection of reverse gear will close the switch allowing
current from fuse 25 to flow through the switch to illuminate the reverse lamps. The switch also provides a feed to the
BCU and the electrochromic automatic interior mirror - if fitted; the mirror moving from the dimmed position if
applicable.
Gearchange assembly
The gearchange assembly is bolted to the top of the gearcase, the upper gear lever being attached to the lower gear
lever by means of a clamp bolt. The lower gear lever ball is housed in a Railko bush inserted in the gear change
housing, the end of the lever locating in the selector yoke which is attached to the end of the selector shaft. Bias
springs provide a positive return of the gear lever to the neutral position with selection of 1st/2nd and 5th/reverse gears
being against bias spring pressure. Spring loaded detent balls fitted in the centre plate locate in grooves in the selector
shaft to provide positive gear and neutral selection.
Lubrication
Lubrication is by an oil pump located in the extension housing and driven by the layshaft with additional lubrication
being provided by splash. The pump directs oil via a filter and internal drillings in the output shaft to lubricate the
components. On non UK and non European models, provision for oil cooling is by means of a thermostat housed in
a cover bolted to the side of the extension housing. The cover incorporates tappings for connections to an oil cooler.
On UK and European models, the thermostat and cover are replaced by an oil by-pass block.
Internal pressures produced within the gearbox are vented to atmosphere via a plastic breather pipe. The pipe is
attached to the extension housing and is routed across the top of the gearcase and secured at the open end by a clip
attached to the engine cylinder block.
Selector shaft and forks
Selector forks for 1st/2nd, 3rd/4th and 5th/reverse gears are located on a single selector shaft; the 1st/2nd and 3rd/
4th selector forks are inside the main gearcase whilst the 5th/reverse selector fork is inside the extension housing.
Each of the selector forks locates inside its corresponding synchromesh hub.
Synchromesh assemblies
Each synchromesh assembly is located on the output shaft adjacent to its corresponding gears and comprises a
synchromesh ring, hub, slippers and sleeve. The hubs and slippers are retained in the sleeves by means of spring
clips. 1st/2nd and 3rd synchromesh assemblies are fitted with double synchromesh rings whilst 4th, 5th and reverse
assemblies are fitted with single rings.
The gear train
The gear train comprises an input shaft, output shaft, layshaft and reverse idler shaft together with their appropriate
gears and synchromesh assemblies.
The gear train input shaft, output shaft and layshaft are supported by taper roller bearings with all gears on the input
and output shafts running on caged needle roller bearings. Layshaft gears are integral with the shaft with the
exception of reverse/5th gears which are splined to the shaft and retained with a nut. 1st, 2nd, 3rd and 4th gears are
shot peened to improve durability. The reverse idler shaft and gear are supported in the centre plate by a caged
needle roller bearing. End-float of the output shaft and layshaft is controlled by selective shims located in the centre
plate whilst reverse idler shaft end-float is controlled by a selective shim located behind reverse gear.
Page 540 of 1529
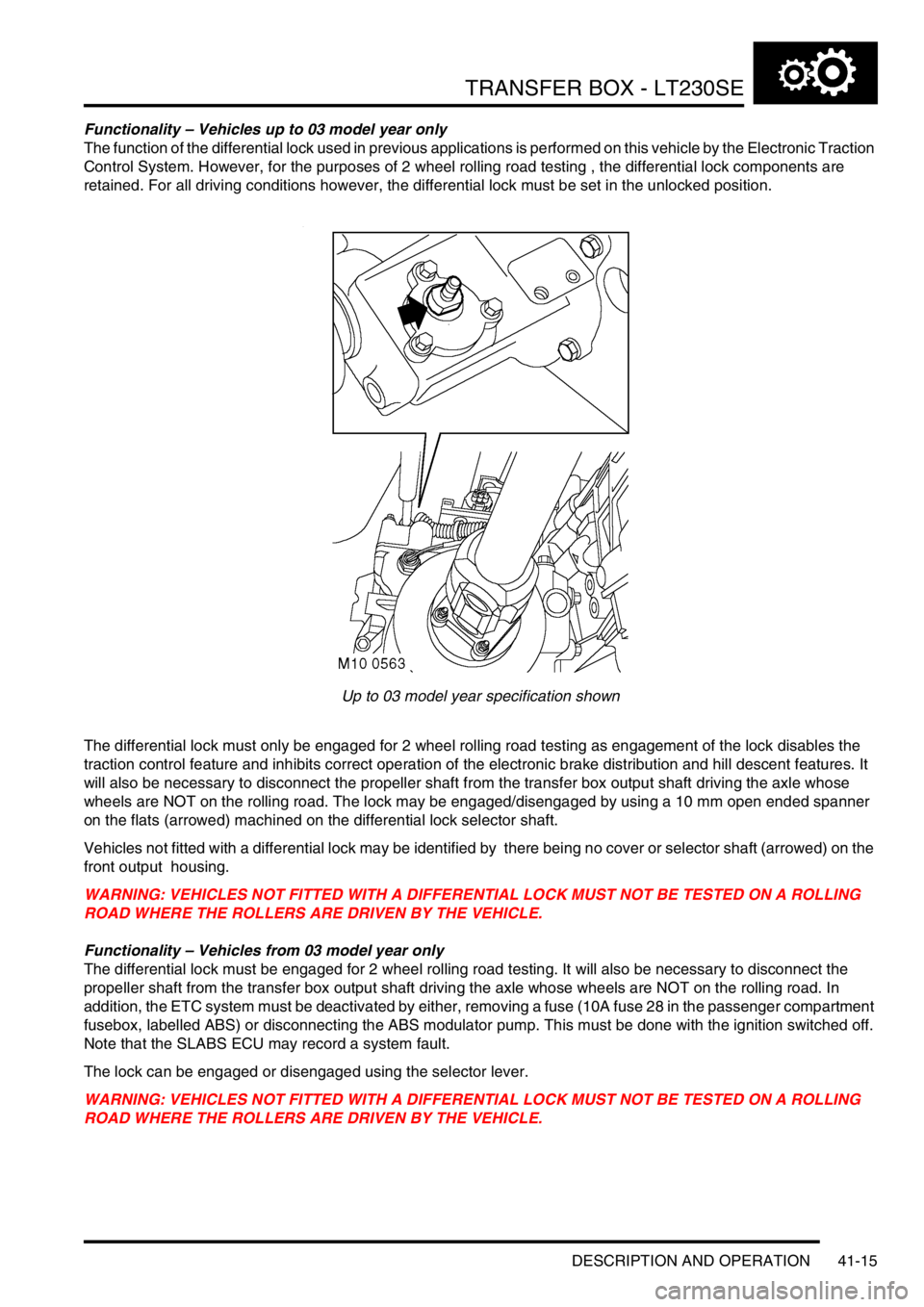
TRANSFER BOX - LT230SE
DESCRIPTION AND OPERATION 41-15
Functionality – Vehicles up to 03 model year only
The function of the differential lock used in previous applications is performed on this vehicle by the Electronic Traction
Control System. However, for the purposes of 2 wheel rolling road testing , the differential lock components are
retained. For all driving conditions however, the differential lock must be set in the unlocked position.
Up to 03 model year specification shown
The differential lock must only be engaged for 2 wheel rolling road testing as engagement of the lock disables the
traction control feature and inhibits correct operation of the electronic brake distribution and hill descent features. It
will also be necessary to disconnect the propeller shaft from the transfer box output shaft driving the axle whose
wheels are NOT on the rolling road. The lock may be engaged/disengaged by using a 10 mm open ended spanner
on the flats (arrowed) machined on the differential lock selector shaft.
Vehicles not fitted with a differential lock may be identified by there being no cover or selector shaft (arrowed) on the
front output housing.
WARNING: VEHICLES NOT FITTED WITH A DIFFERENTIAL LOCK MUST NOT BE TESTED ON A ROLLING
ROAD WHERE THE ROLLERS ARE DRIVEN BY THE VEHICLE.
Functionality – Vehicles from 03 model year only
The differential lock must be engaged for 2 wheel rolling road testing. It will also be necessary to disconnect the
propeller shaft from the transfer box output shaft driving the axle whose wheels are NOT on the rolling road. In
addition, the ETC system must be deactivated by either, removing a fuse (10A fuse 28 in the passenger compartment
fusebox, labelled ABS) or disconnecting the ABS modulator pump. This must be done with the ignition switched off.
Note that the SLABS ECU may record a system fault.
The lock can be engaged or disengaged using the selector lever.
WARNING: VEHICLES NOT FITTED WITH A DIFFERENTIAL LOCK MUST NOT BE TESTED ON A ROLLING
ROAD WHERE THE ROLLERS ARE DRIVEN BY THE VEHICLE.
Page 609 of 1529
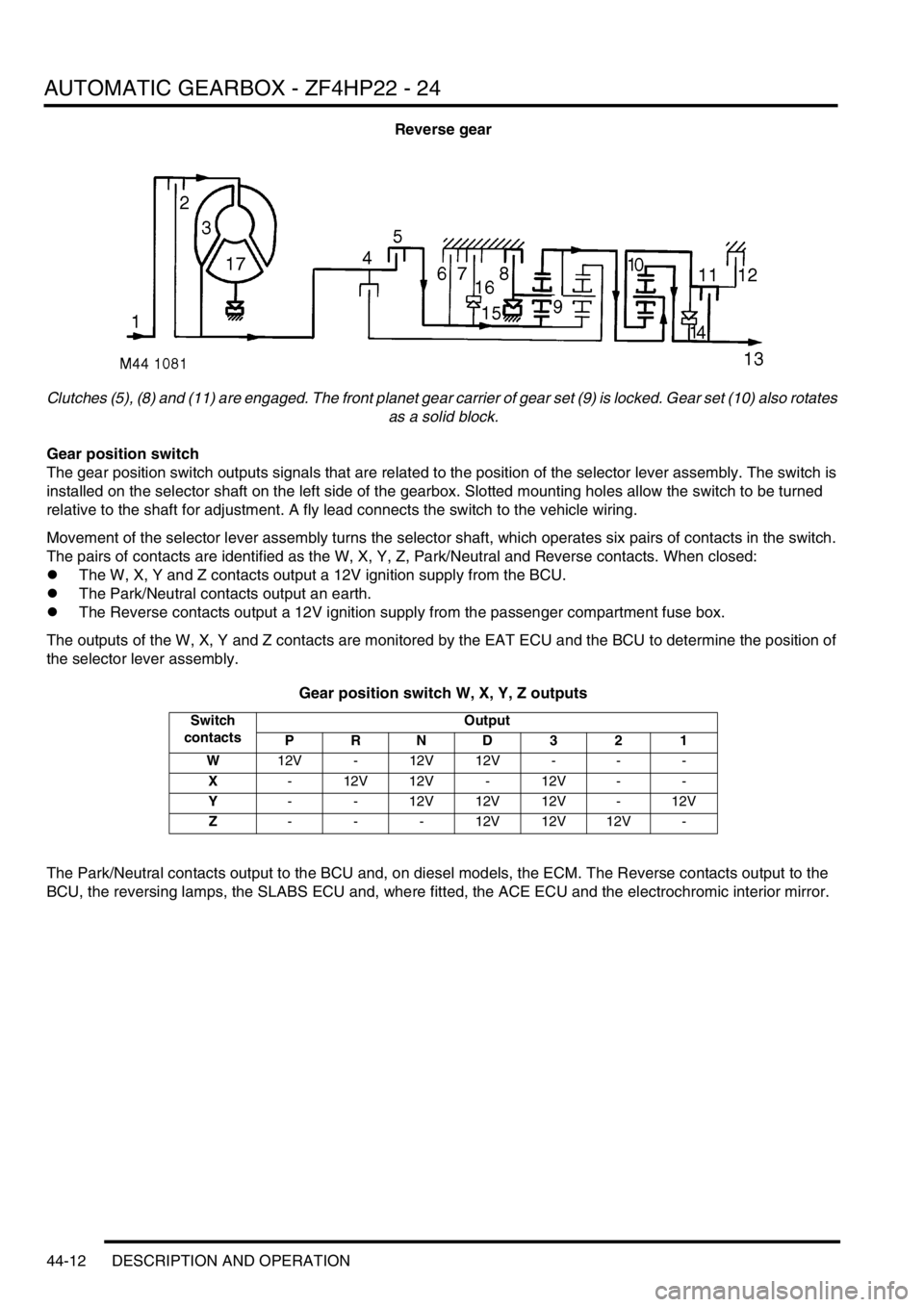
AUTOMATIC GEARBOX - ZF4HP22 - 24
44-12 DESCRIPTION AND OPERATION
Reverse gear
Clutches (5), (8) and (11) are engaged. The front planet gear carrier of gear set (9) is locked. Gear set (10) also rotates
as a solid block.
Gear position switch
The gear position switch outputs signals that are related to the position of the selector lever assembly. The switch is
installed on the selector shaft on the left side of the gearbox. Slotted mounting holes allow the switch to be turned
relative to the shaft for adjustment. A fly lead connects the switch to the vehicle wiring.
Movement of the selector lever assembly turns the selector shaft, which operates six pairs of contacts in the switch.
The pairs of contacts are identified as the W, X, Y, Z, Park/Neutral and Reverse contacts. When closed:
lThe W, X, Y and Z contacts output a 12V ignition supply from the BCU.
lThe Park/Neutral contacts output an earth.
lThe Reverse contacts output a 12V ignition supply from the passenger compartment fuse box.
The outputs of the W, X, Y and Z contacts are monitored by the EAT ECU and the BCU to determine the position of
the selector lever assembly.
Gear position switch W, X, Y, Z outputs
The Park/Neutral contacts output to the BCU and, on diesel models, the ECM. The Reverse contacts output to the
BCU, the reversing lamps, the SLABS ECU and, where fitted, the ACE ECU and the electrochromic interior mirror.
Switch
contactsOutput
PRND 3 2 1
W12V - 12V 12V - - -
X- 12V 12V - 12V - -
Y- - 12V 12V 12V - 12V
Z- - - 12V 12V 12V -
Page 763 of 1529
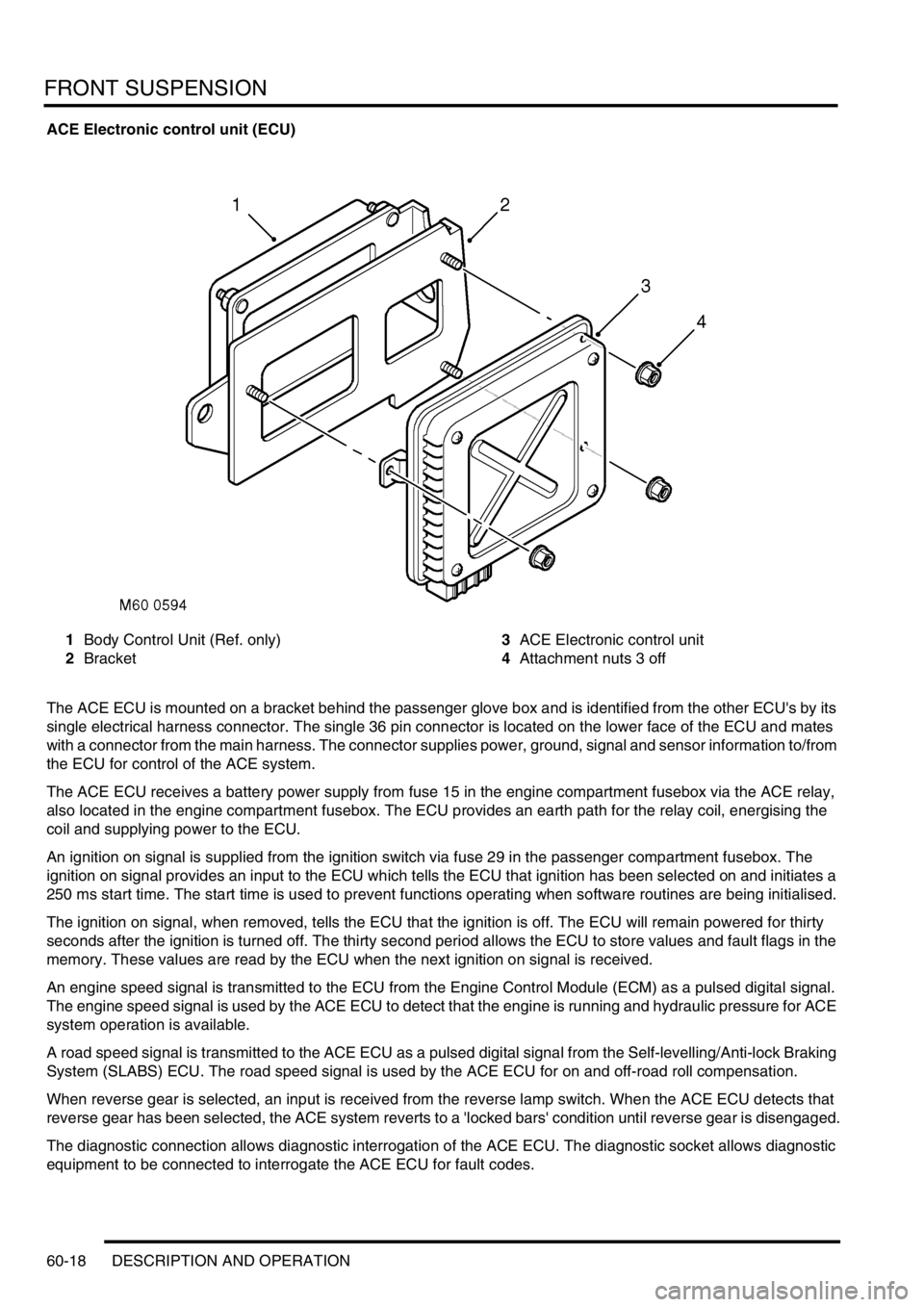
FRONT SUSPENSION
60-18 DESCRIPTION AND OPERATION
ACE Electronic control unit (ECU)
1Body Control Unit (Ref. only)
2Bracket3ACE Electronic control unit
4Attachment nuts 3 off
The ACE ECU is mounted on a bracket behind the passenger glove box and is identified from the other ECU's by its
single electrical harness connector. The single 36 pin connector is located on the lower face of the ECU and mates
with a connector from the main harness. The connector supplies power, ground, signal and sensor information to/from
the ECU for control of the ACE system.
The ACE ECU receives a battery power supply from fuse 15 in the engine compartment fusebox via the ACE relay,
also located in the engine compartment fusebox. The ECU provides an earth path for the relay coil, energising the
coil and supplying power to the ECU.
An ignition on signal is supplied from the ignition switch via fuse 29 in the passenger compartment fusebox. The
ignition on signal provides an input to the ECU which tells the ECU that ignition has been selected on and initiates a
250 ms start time. The start time is used to prevent functions operating when software routines are being initialised.
The ignition on signal, when removed, tells the ECU that the ignition is off. The ECU will remain powered for thirty
seconds after the ignition is turned off. The thirty second period allows the ECU to store values and fault flags in the
memory. These values are read by the ECU when the next ignition on signal is received.
An engine speed signal is transmitted to the ECU from the Engine Control Module (ECM) as a pulsed digital signal.
The engine speed signal is used by the ACE ECU to detect that the engine is running and hydraulic pressure for ACE
system operation is available.
A road speed signal is transmitted to the ACE ECU as a pulsed digital signal from the Self-levelling/Anti-lock Braking
System (SLABS) ECU. The road speed signal is used by the ACE ECU for on and off-road roll compensation.
When reverse gear is selected, an input is received from the reverse lamp switch. When the ACE ECU detects that
reverse gear has been selected, the ACE system reverts to a 'locked bars' condition until reverse gear is disengaged.
The diagnostic connection allows diagnostic interrogation of the ACE ECU. The diagnostic socket allows diagnostic
equipment to be connected to interrogate the ACE ECU for fault codes.
Page 826 of 1529
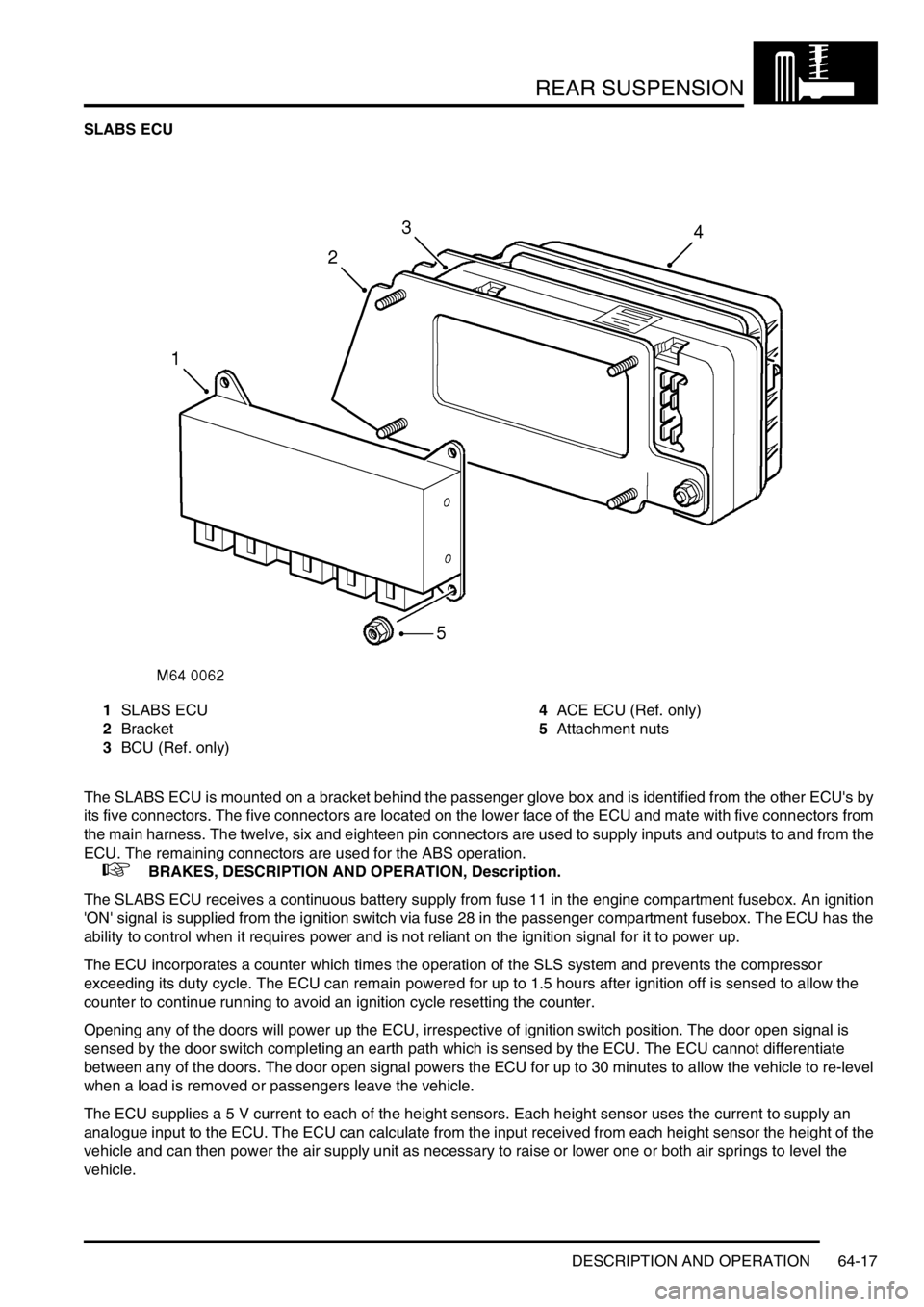
REAR SUSPENSION
DESCRIPTION AND OPERATION 64-17
SLABS ECU
1SLABS ECU
2Bracket
3BCU (Ref. only)4ACE ECU (Ref. only)
5Attachment nuts
The SLABS ECU is mounted on a bracket behind the passenger glove box and is identified from the other ECU's by
its five connectors. The five connectors are located on the lower face of the ECU and mate with five connectors from
the main harness. The twelve, six and eighteen pin connectors are used to supply inputs and outputs to and from the
ECU. The remaining connectors are used for the ABS operation.
+ BRAKES, DESCRIPTION AND OPERATION, Description.
The SLABS ECU receives a continuous battery supply from fuse 11 in the engine compartment fusebox. An ignition
'ON' signal is supplied from the ignition switch via fuse 28 in the passenger compartment fusebox. The ECU has the
ability to control when it requires power and is not reliant on the ignition signal for it to power up.
The ECU incorporates a counter which times the operation of the SLS system and prevents the compressor
exceeding its duty cycle. The ECU can remain powered for up to 1.5 hours after ignition off is sensed to allow the
counter to continue running to avoid an ignition cycle resetting the counter.
Opening any of the doors will power up the ECU, irrespective of ignition switch position. The door open signal is
sensed by the door switch completing an earth path which is sensed by the ECU. The ECU cannot differentiate
between any of the doors. The door open signal powers the ECU for up to 30 minutes to allow the vehicle to re-level
when a load is removed or passengers leave the vehicle.
The ECU supplies a 5 V current to each of the height sensors. Each height sensor uses the current to supply an
analogue input to the ECU. The ECU can calculate from the input received from each height sensor the height of the
vehicle and can then power the air supply unit as necessary to raise or lower one or both air springs to level the
vehicle.
Page 827 of 1529
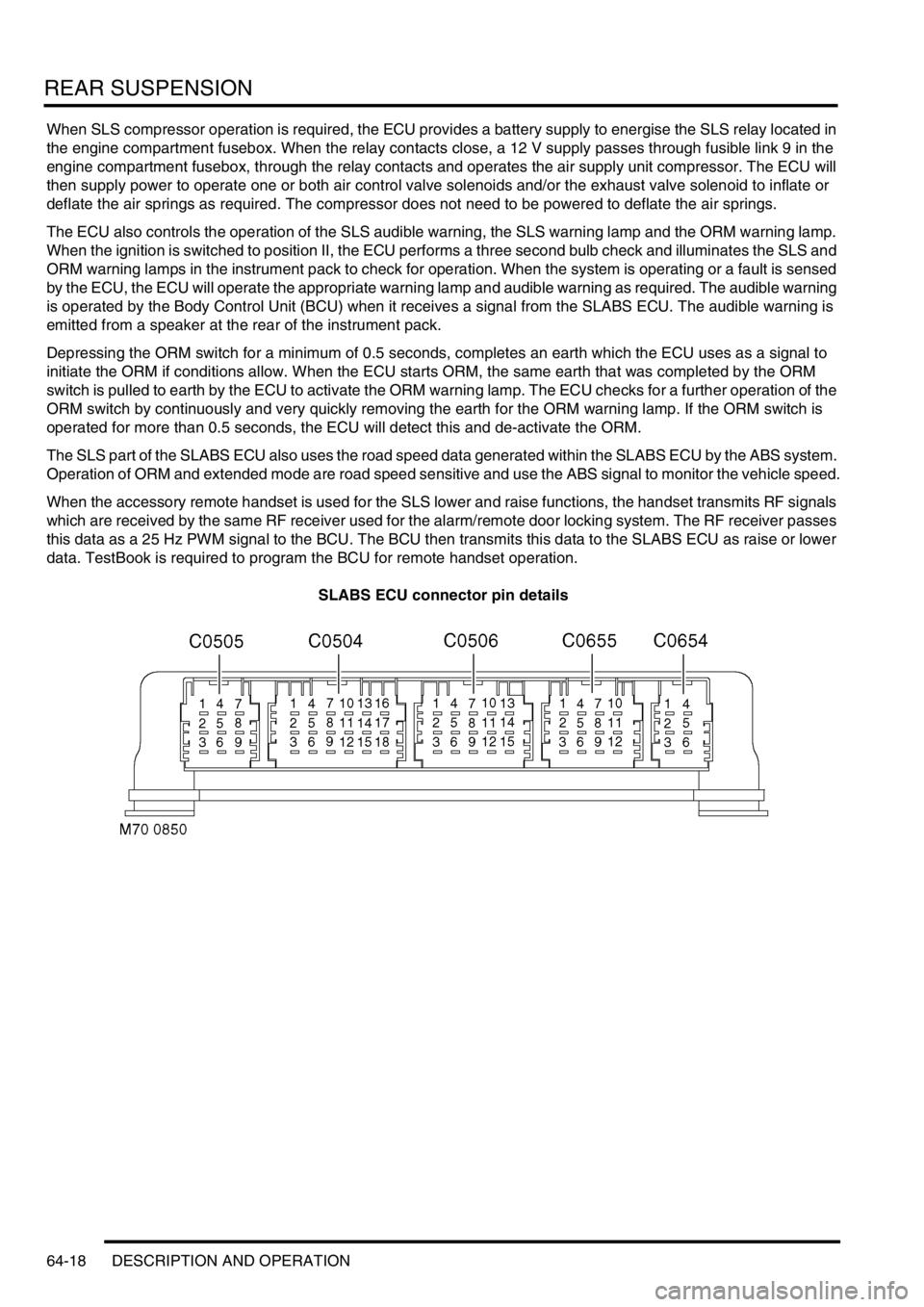
REAR SUSPENSION
64-18 DESCRIPTION AND OPERATION
When SLS compressor operation is required, the ECU provides a battery supply to energise the SLS relay located in
the engine compartment fusebox. When the relay contacts close, a 12 V supply passes through fusible link 9 in the
engine compartment fusebox, through the relay contacts and operates the air supply unit compressor. The ECU will
then supply power to operate one or both air control valve solenoids and/or the exhaust valve solenoid to inflate or
deflate the air springs as required. The compressor does not need to be powered to deflate the air springs.
The ECU also controls the operation of the SLS audible warning, the SLS warning lamp and the ORM warning lamp.
When the ignition is switched to position II, the ECU performs a three second bulb check and illuminates the SLS and
ORM warning lamps in the instrument pack to check for operation. When the system is operating or a fault is sensed
by the ECU, the ECU will operate the appropriate warning lamp and audible warning as required. The audible warning
is operated by the Body Control Unit (BCU) when it receives a signal from the SLABS ECU. The audible warning is
emitted from a speaker at the rear of the instrument pack.
Depressing the ORM switch for a minimum of 0.5 seconds, completes an earth which the ECU uses as a signal to
initiate the ORM if conditions allow. When the ECU starts ORM, the same earth that was completed by the ORM
switch is pulled to earth by the ECU to activate the ORM warning lamp. The ECU checks for a further operation of the
ORM switch by continuously and very quickly removing the earth for the ORM warning lamp. If the ORM switch is
operated for more than 0.5 seconds, the ECU will detect this and de-activate the ORM.
The SLS part of the SLABS ECU also uses the road speed data generated within the SLABS ECU by the ABS system.
Operation of ORM and extended mode are road speed sensitive and use the ABS signal to monitor the vehicle speed.
When the accessory remote handset is used for the SLS lower and raise functions, the handset transmits RF signals
which are received by the same RF receiver used for the alarm/remote door locking system. The RF receiver passes
this data as a 25 Hz PWM signal to the BCU. The BCU then transmits this data to the SLABS ECU as raise or lower
data. TestBook is required to program the BCU for remote handset operation.
SLABS ECU connector pin details