LAND ROVER DISCOVERY 1999 Workshop Manual
Manufacturer: LAND ROVER, Model Year: 1999, Model line: DISCOVERY, Model: LAND ROVER DISCOVERY 1999Pages: 1529, PDF Size: 34.8 MB
Page 751 of 1529
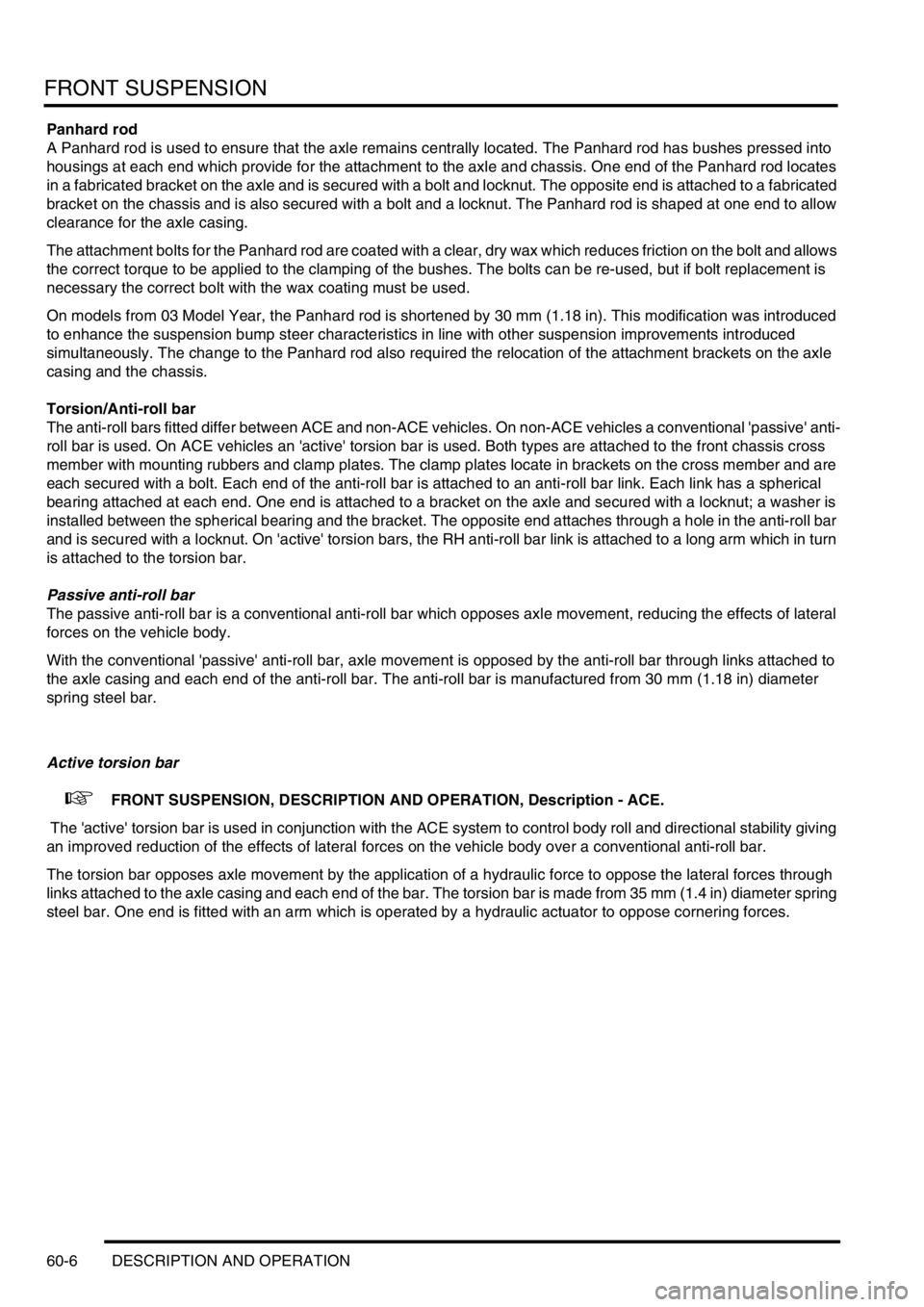
FRONT SUSPENSION
60-6 DESCRIPTION AND OPERATION
Panhard rod
A Panhard rod is used to ensure that the axle remains centrally located. The Panhard rod has bushes pressed into
housings at each end which provide for the attachment to the axle and chassis. One end of the Panhard rod locates
in a fabricated bracket on the axle and is secured with a bolt and locknut. The opposite end is attached to a fabricated
bracket on the chassis and is also secured with a bolt and a locknut. The Panhard rod is shaped at one end to allow
clearance for the axle casing.
The attachment bolts for the Panhard rod are coated with a clear, dry wax which reduces friction on the bolt and allows
the correct torque to be applied to the clamping of the bushes. The bolts can be re-used, but if bolt replacement is
necessary the correct bolt with the wax coating must be used.
On models from 03 Model Year, the Panhard rod is shortened by 30 mm (1.18 in). This modification was introduced
to enhance the suspension bump steer characteristics in line with other suspension improvements introduced
simultaneously. The change to the Panhard rod also required the relocation of the attachment brackets on the axle
casing and the chassis.
Torsion/Anti-roll bar
The anti-roll bars fitted differ between ACE and non-ACE vehicles. On non-ACE vehicles a conventional 'passive' anti-
roll bar is used. On ACE vehicles an 'active' torsion bar is used. Both types are attached to the front chassis cross
member with mounting rubbers and clamp plates. The clamp plates locate in brackets on the cross member and are
each secured with a bolt. Each end of the anti-roll bar is attached to an anti-roll bar link. Each link has a spherical
bearing attached at each end. One end is attached to a bracket on the axle and secured with a locknut; a washer is
installed between the spherical bearing and the bracket. The opposite end attaches through a hole in the anti-roll bar
and is secured with a locknut. On 'active' torsion bars, the RH anti-roll bar link is attached to a long arm which in turn
is attached to the torsion bar.
Passive anti-roll bar
The passive anti-roll bar is a conventional anti-roll bar which opposes axle movement, reducing the effects of lateral
forces on the vehicle body.
With the conventional 'passive' anti-roll bar, axle movement is opposed by the anti-roll bar through links attached to
the axle casing and each end of the anti-roll bar. The anti-roll bar is manufactured from 30 mm (1.18 in) diameter
spring steel bar.
Active torsion bar
+ FRONT SUSPENSION, DESCRIPTION AND OPERATION, Description - ACE.
The 'active' torsion bar is used in conjunction with the ACE system to control body roll and directional stability giving
an improved reduction of the effects of lateral forces on the vehicle body over a conventional anti-roll bar.
The torsion bar opposes axle movement by the application of a hydraulic force to oppose the lateral forces through
links attached to the axle casing and each end of the bar. The torsion bar is made from 35 mm (1.4 in) diameter spring
steel bar. One end is fitted with an arm which is operated by a hydraulic actuator to oppose cornering forces.
Page 752 of 1529
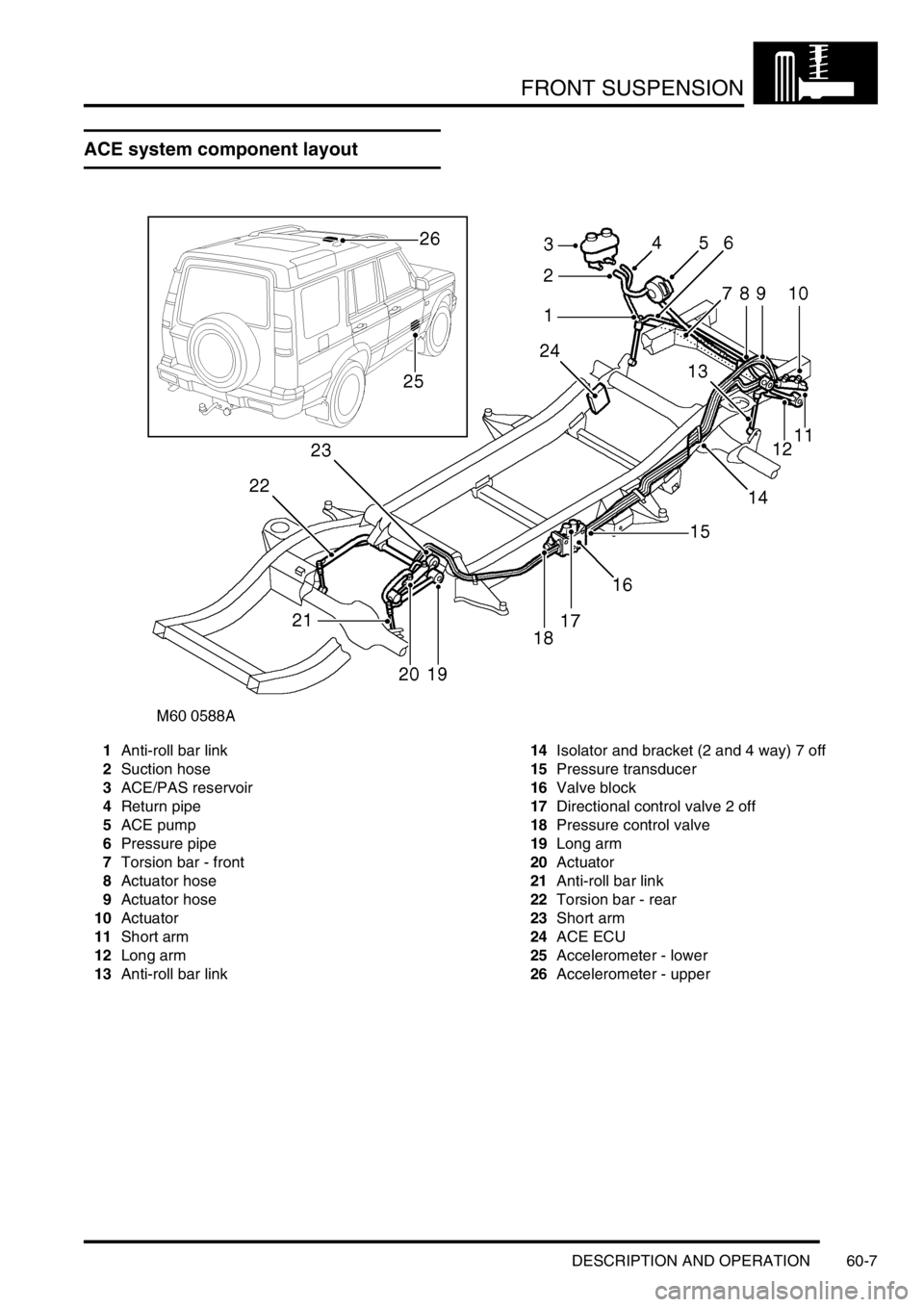
FRONT SUSPENSION
DESCRIPTION AND OPERATION 60-7
DESCRIPTION AND OPERAT ION
ACE system component layout
1Anti-roll bar link
2Suction hose
3ACE/PAS reservoir
4Return pipe
5ACE pump
6Pressure pipe
7Torsion bar - front
8Actuator hose
9Actuator hose
10Actuator
11Short arm
12Long arm
13Anti-roll bar link14Isolator and bracket (2 and 4 way) 7 off
15Pressure transducer
16Valve block
17Directional control valve 2 off
18Pressure control valve
19Long arm
20Actuator
21Anti-roll bar link
22Torsion bar - rear
23Short arm
24ACE ECU
25Accelerometer - lower
26Accelerometer - upper
Page 753 of 1529
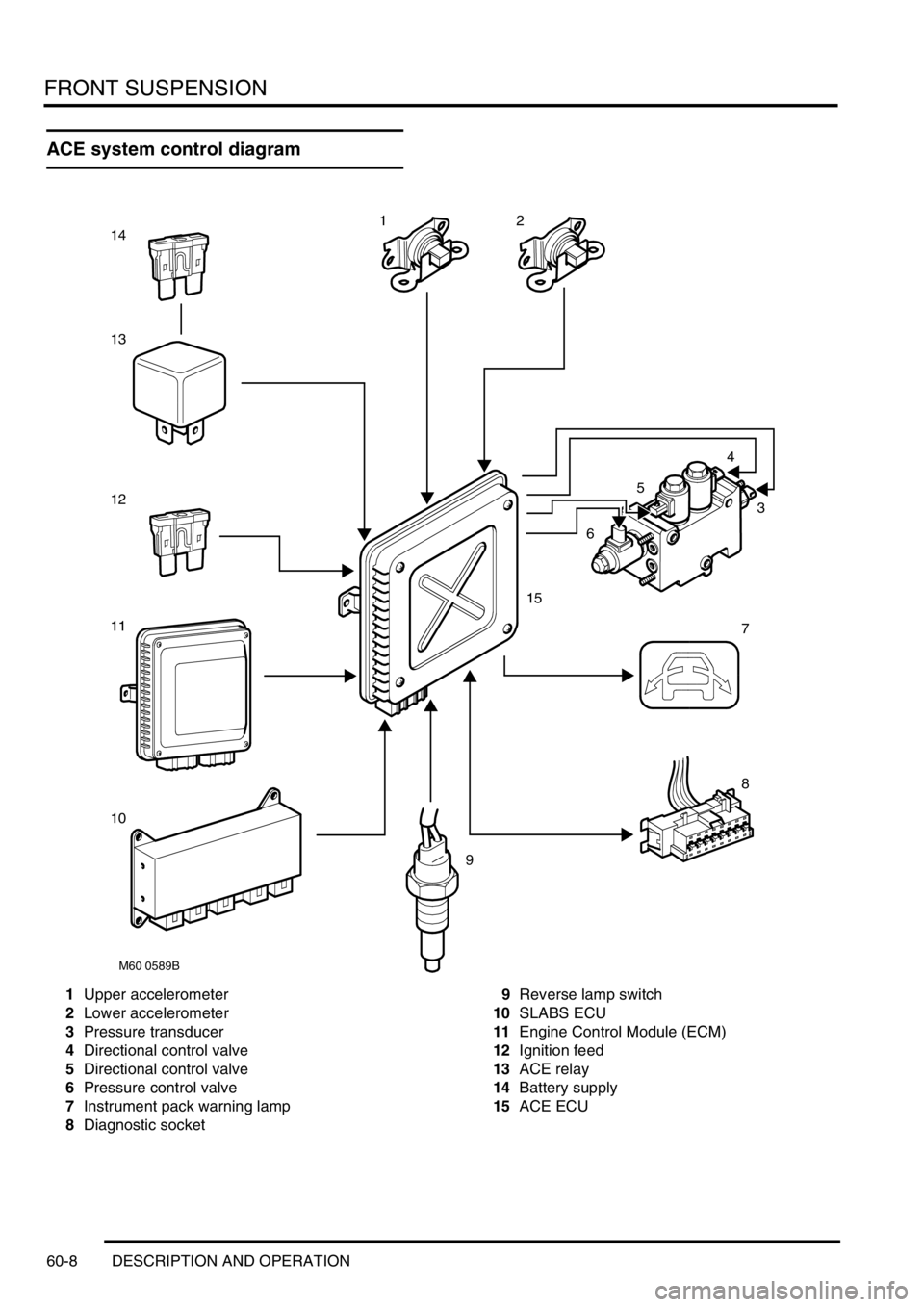
FRONT SUSPENSION
60-8 DESCRIPTION AND OPERATION
ACE system control diagram
1Upper accelerometer
2Lower accelerometer
3Pressure transducer
4Directional control valve
5Directional control valve
6Pressure control valve
7Instrument pack warning lamp
8Diagnostic socket9Reverse lamp switch
10SLABS ECU
11Engine Control Module (ECM)
12Ignition feed
13ACE relay
14Battery supply
15ACE ECU
M60 0589B
12
5
4
3
6
7
8
9
10
11
12
13
14
15
Page 754 of 1529
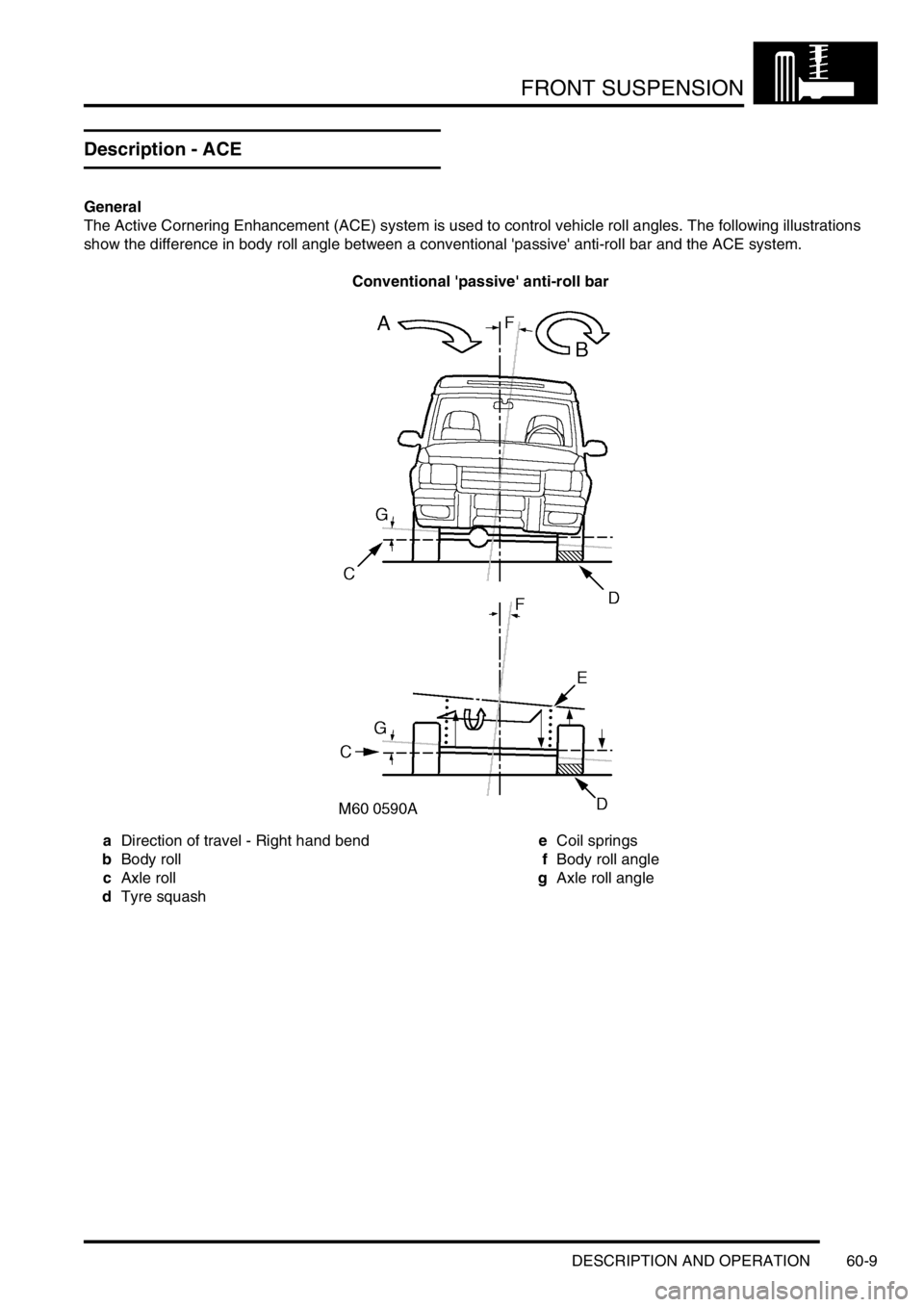
FRONT SUSPENSION
DESCRIPTION AND OPERATION 60-9
Description - ACE
General
The Active Cornering Enhancement (ACE) system is used to control vehicle roll angles. The following illustrations
show the difference in body roll angle between a conventional 'passive' anti-roll bar and the ACE system.
Conventional 'passive' anti-roll bar
aDirection of travel - Right hand bend
bBody roll
cAxle roll
dTyre squasheCoil springs
fBody roll angle
gAxle roll angle
Page 755 of 1529
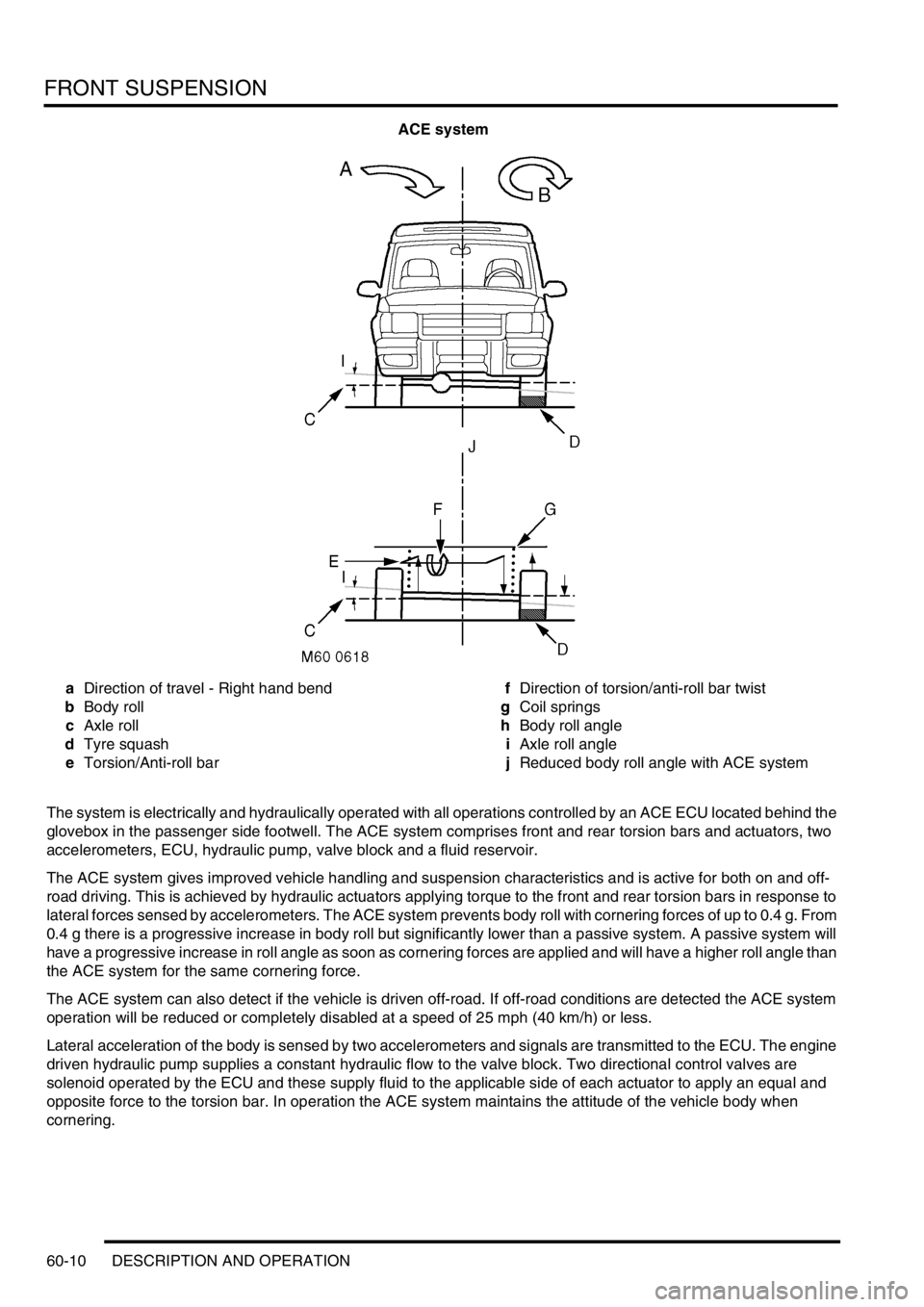
FRONT SUSPENSION
60-10 DESCRIPTION AND OPERATION
ACE system
aDirection of travel - Right hand bend
bBody roll
cAxle roll
dTyre squash
eTorsion/Anti-roll barfDirection of torsion/anti-roll bar twist
gCoil springs
hBody roll angle
iAxle roll angle
jReduced body roll angle with ACE system
The system is electrically and hydraulically operated with all operations controlled by an ACE ECU located behind the
glovebox in the passenger side footwell. The ACE system comprises front and rear torsion bars and actuators, two
accelerometers, ECU, hydraulic pump, valve block and a fluid reservoir.
The ACE system gives improved vehicle handling and suspension characteristics and is active for both on and off-
road driving. This is achieved by hydraulic actuators applying torque to the front and rear torsion bars in response to
lateral forces sensed by accelerometers. The ACE system prevents body roll with cornering forces of up to 0.4 g. From
0.4 g there is a progressive increase in body roll but significantly lower than a passive system. A passive system will
have a progressive increase in roll angle as soon as cornering forces are applied and will have a higher roll angle than
the ACE system for the same cornering force.
The ACE system can also detect if the vehicle is driven off-road. If off-road conditions are detected the ACE system
operation will be reduced or completely disabled at a speed of 25 mph (40 km/h) or less.
Lateral acceleration of the body is sensed by two accelerometers and signals are transmitted to the ECU. The engine
driven hydraulic pump supplies a constant hydraulic flow to the valve block. Two directional control valves are
solenoid operated by the ECU and these supply fluid to the applicable side of each actuator to apply an equal and
opposite force to the torsion bar. In operation the ACE system maintains the attitude of the vehicle body when
cornering.
Page 756 of 1529
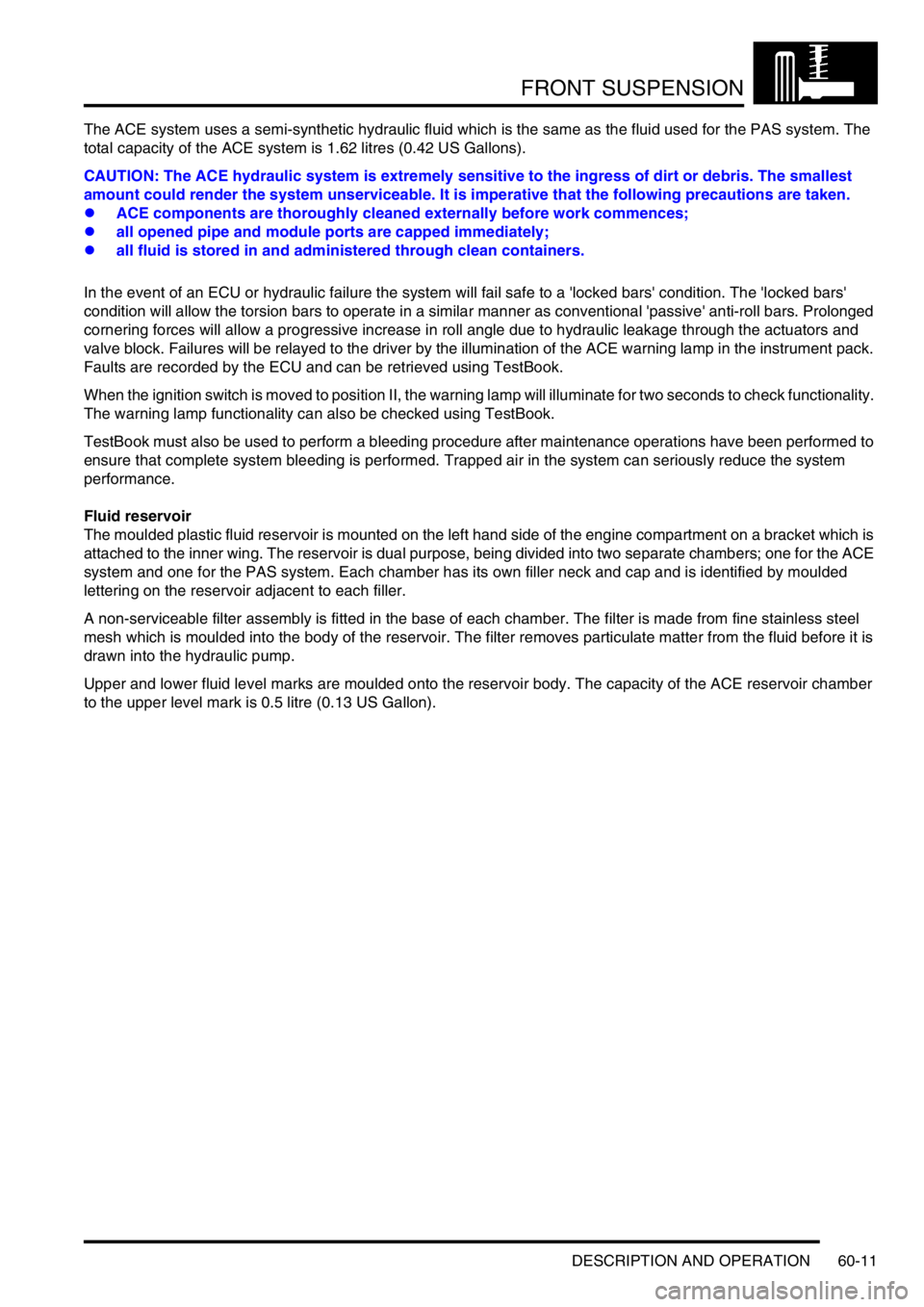
FRONT SUSPENSION
DESCRIPTION AND OPERATION 60-11
The ACE system uses a semi-synthetic hydraulic fluid which is the same as the fluid used for the PAS system. The
total capacity of the ACE system is 1.62 litres (0.42 US Gallons).
CAUTION: The ACE hydraulic system is extremely sensitive to the ingress of dirt or debris. The smallest
amount could render the system unserviceable. It is imperative that the following precautions are taken.
lACE components are thoroughly cleaned externally before work commences;
lall opened pipe and module ports are capped immediately;
lall fluid is stored in and administered through clean containers.
In the event of an ECU or hydraulic failure the system will fail safe to a 'locked bars' condition. The 'locked bars'
condition will allow the torsion bars to operate in a similar manner as conventional 'passive' anti-roll bars. Prolonged
cornering forces will allow a progressive increase in roll angle due to hydraulic leakage through the actuators and
valve block. Failures will be relayed to the driver by the illumination of the ACE warning lamp in the instrument pack.
Faults are recorded by the ECU and can be retrieved using TestBook.
When the ignition switch is moved to position II, the warning lamp will illuminate for two seconds to check functionality.
The warning lamp functionality can also be checked using TestBook.
TestBook must also be used to perform a bleeding procedure after maintenance operations have been performed to
ensure that complete system bleeding is performed. Trapped air in the system can seriously reduce the system
performance.
Fluid reservoir
The moulded plastic fluid reservoir is mounted on the left hand side of the engine compartment on a bracket which is
attached to the inner wing. The reservoir is dual purpose, being divided into two separate chambers; one for the ACE
system and one for the PAS system. Each chamber has its own filler neck and cap and is identified by moulded
lettering on the reservoir adjacent to each filler.
A non-serviceable filter assembly is fitted in the base of each chamber. The filter is made from fine stainless steel
mesh which is moulded into the body of the reservoir. The filter removes particulate matter from the fluid before it is
drawn into the hydraulic pump.
Upper and lower fluid level marks are moulded onto the reservoir body. The capacity of the ACE reservoir chamber
to the upper level mark is 0.5 litre (0.13 US Gallon).
Page 757 of 1529
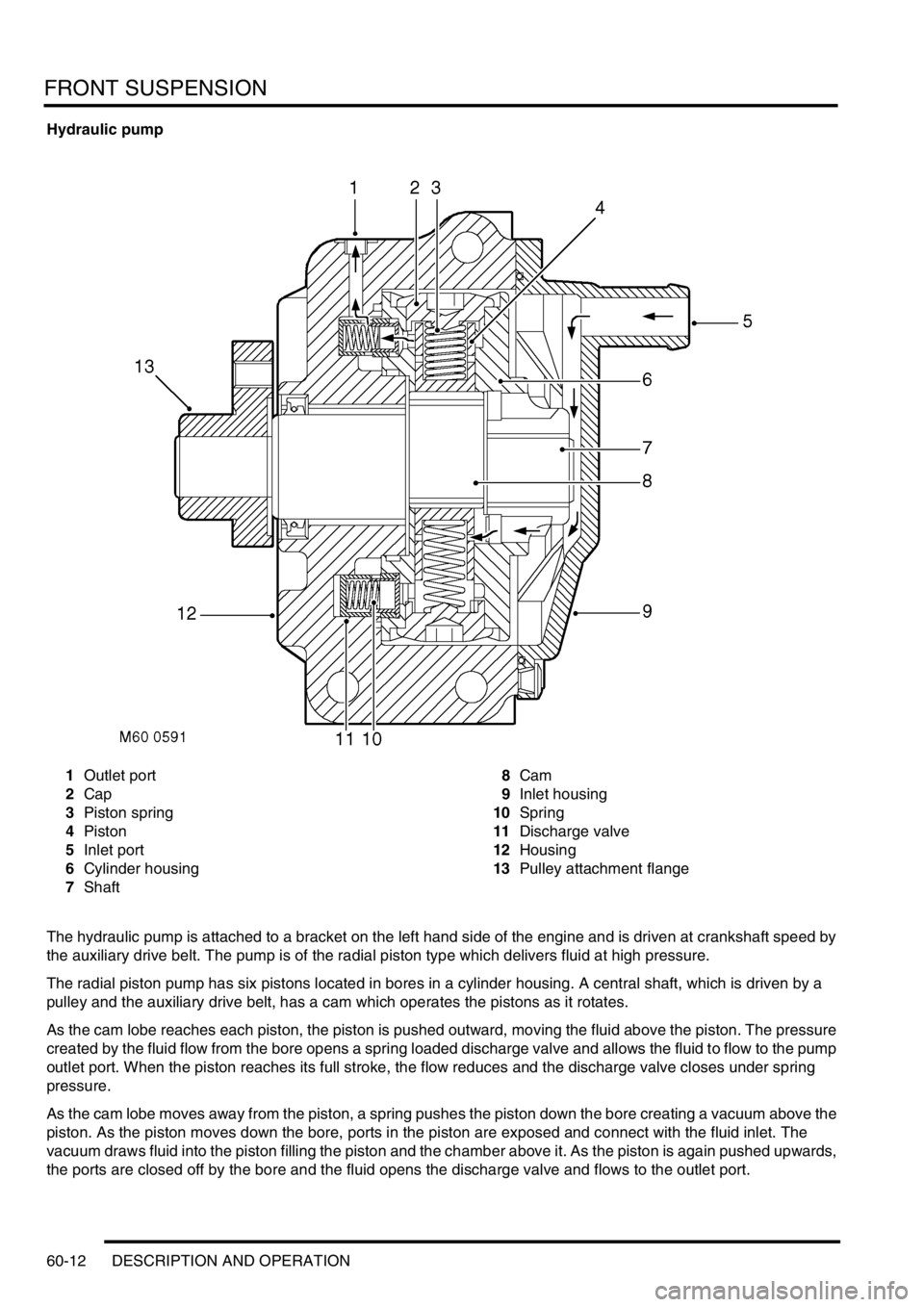
FRONT SUSPENSION
60-12 DESCRIPTION AND OPERATION
Hydraulic pump
1Outlet port
2Cap
3Piston spring
4Piston
5Inlet port
6Cylinder housing
7Shaft8Cam
9Inlet housing
10Spring
11Discharge valve
12Housing
13Pulley attachment flange
The hydraulic pump is attached to a bracket on the left hand side of the engine and is driven at crankshaft speed by
the auxiliary drive belt. The pump is of the radial piston type which delivers fluid at high pressure.
The radial piston pump has six pistons located in bores in a cylinder housing. A central shaft, which is driven by a
pulley and the auxiliary drive belt, has a cam which operates the pistons as it rotates.
As the cam lobe reaches each piston, the piston is pushed outward, moving the fluid above the piston. The pressure
created by the fluid flow from the bore opens a spring loaded discharge valve and allows the fluid to flow to the pump
outlet port. When the piston reaches its full stroke, the flow reduces and the discharge valve closes under spring
pressure.
As the cam lobe moves away from the piston, a spring pushes the piston down the bore creating a vacuum above the
piston. As the piston moves down the bore, ports in the piston are exposed and connect with the fluid inlet. The
vacuum draws fluid into the piston filling the piston and the chamber above it. As the piston is again pushed upwards,
the ports are closed off by the bore and the fluid opens the discharge valve and flows to the outlet port.
Page 758 of 1529
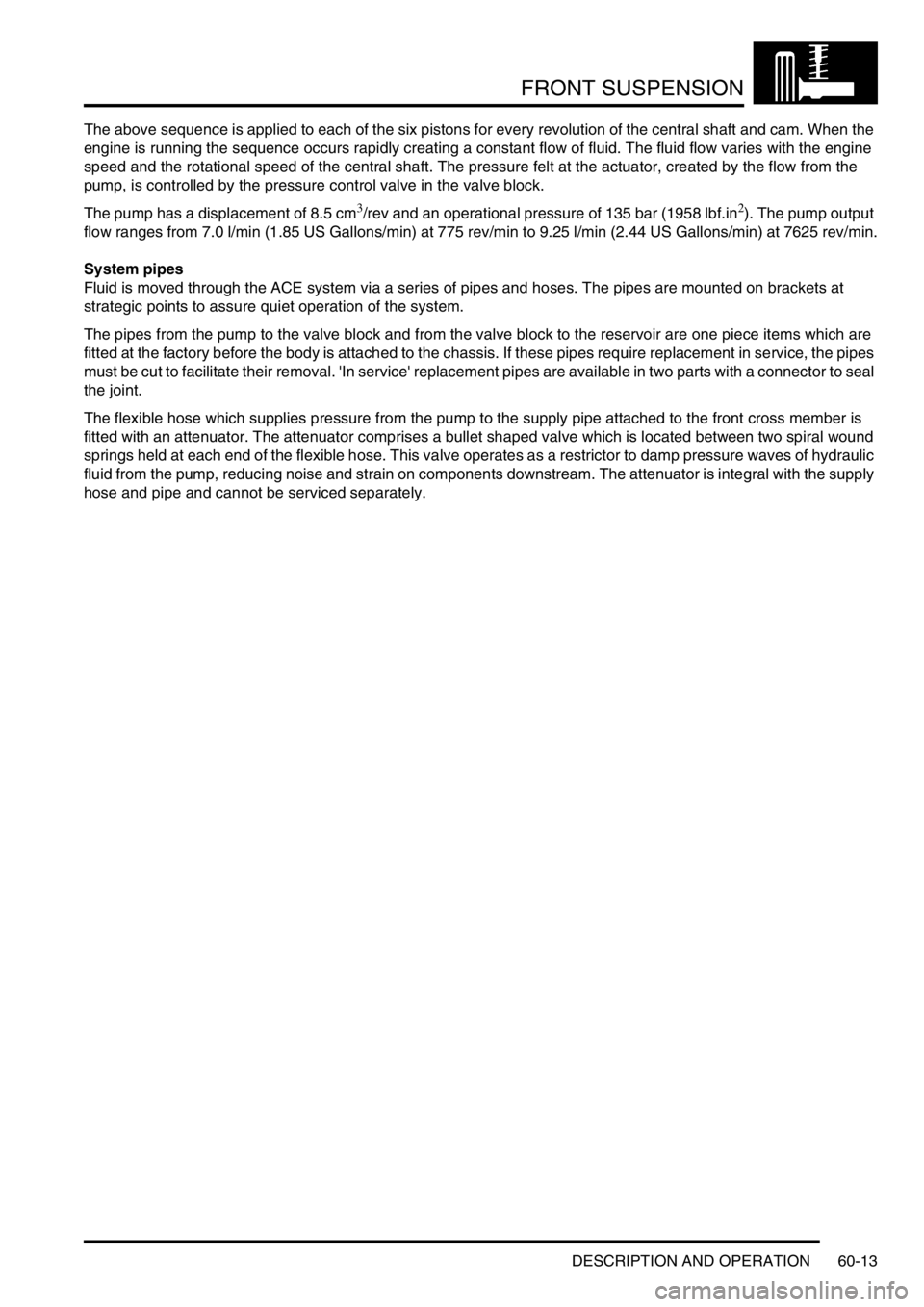
FRONT SUSPENSION
DESCRIPTION AND OPERATION 60-13
The above sequence is applied to each of the six pistons for every revolution of the central shaft and cam. When the
engine is running the sequence occurs rapidly creating a constant flow of fluid. The fluid flow varies with the engine
speed and the rotational speed of the central shaft. The pressure felt at the actuator, created by the flow from the
pump, is controlled by the pressure control valve in the valve block.
The pump has a displacement of 8.5 cm
3/rev and an operational pressure of 135 bar (1958 lbf.in2). The pump output
flow ranges from 7.0 l/min (1.85 US Gallons/min) at 775 rev/min to 9.25 l/min (2.44 US Gallons/min) at 7625 rev/min.
System pipes
Fluid is moved through the ACE system via a series of pipes and hoses. The pipes are mounted on brackets at
strategic points to assure quiet operation of the system.
The pipes from the pump to the valve block and from the valve block to the reservoir are one piece items which are
fitted at the factory before the body is attached to the chassis. If these pipes require replacement in service, the pipes
must be cut to facilitate their removal. 'In service' replacement pipes are available in two parts with a connector to seal
the joint.
The flexible hose which supplies pressure from the pump to the supply pipe attached to the front cross member is
fitted with an attenuator. The attenuator comprises a bullet shaped valve which is located between two spiral wound
springs held at each end of the flexible hose. This valve operates as a restrictor to damp pressure waves of hydraulic
fluid from the pump, reducing noise and strain on components downstream. The attenuator is integral with the supply
hose and pipe and cannot be serviced separately.
Page 759 of 1529
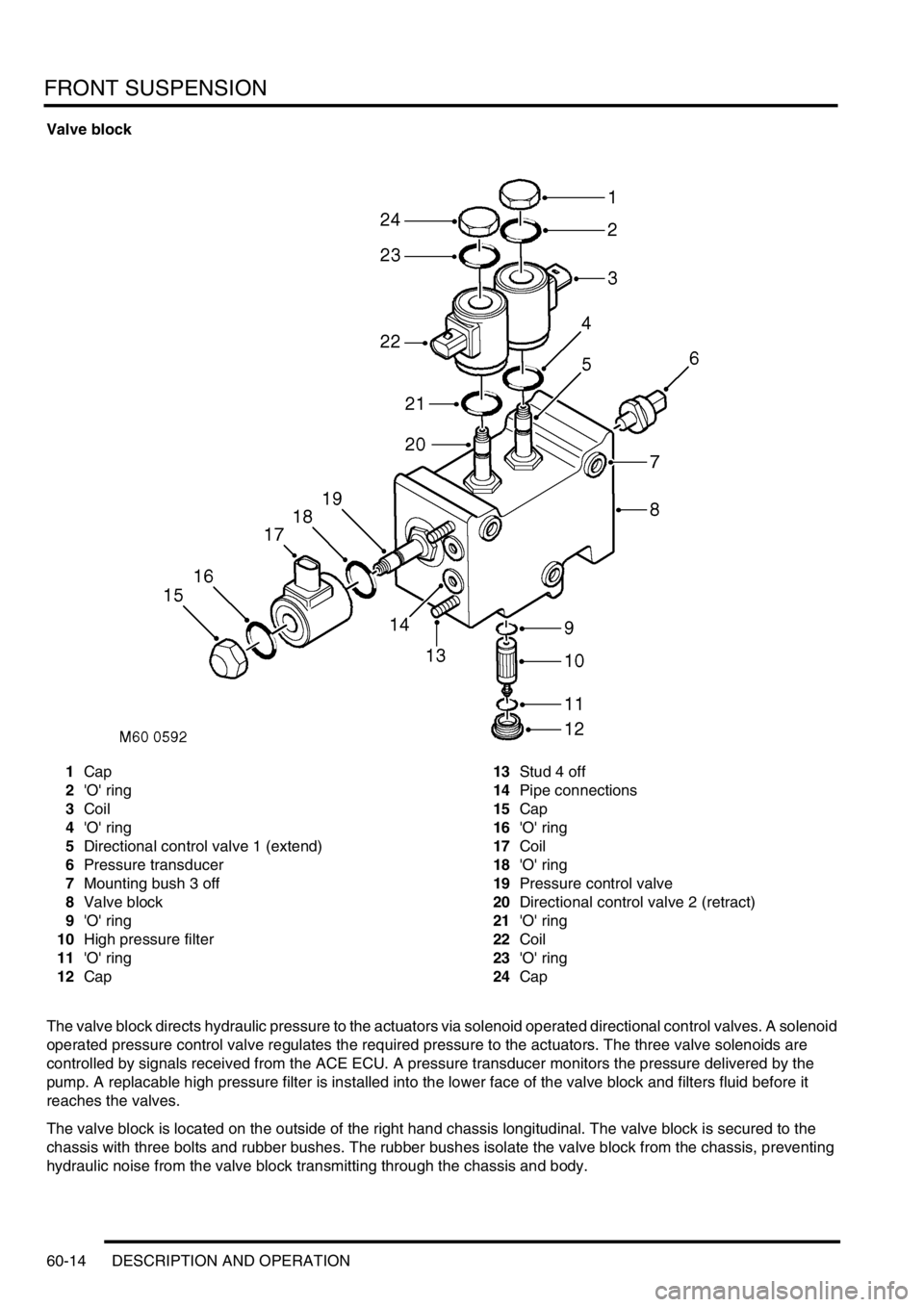
FRONT SUSPENSION
60-14 DESCRIPTION AND OPERATION
Valve block
1Cap
2'O' ring
3Coil
4'O' ring
5Directional control valve 1 (extend)
6Pressure transducer
7Mounting bush 3 off
8Valve block
9'O' ring
10High pressure filter
11'O' ring
12Cap13Stud 4 off
14Pipe connections
15Cap
16'O' ring
17Coil
18'O' ring
19Pressure control valve
20Directional control valve 2 (retract)
21'O' ring
22Coil
23'O' ring
24Cap
The valve block directs hydraulic pressure to the actuators via solenoid operated directional control valves. A solenoid
operated pressure control valve regulates the required pressure to the actuators. The three valve solenoids are
controlled by signals received from the ACE ECU. A pressure transducer monitors the pressure delivered by the
pump. A replacable high pressure filter is installed into the lower face of the valve block and filters fluid before it
reaches the valves.
The valve block is located on the outside of the right hand chassis longitudinal. The valve block is secured to the
chassis with three bolts and rubber bushes. The rubber bushes isolate the valve block from the chassis, preventing
hydraulic noise from the valve block transmitting through the chassis and body.
Page 760 of 1529
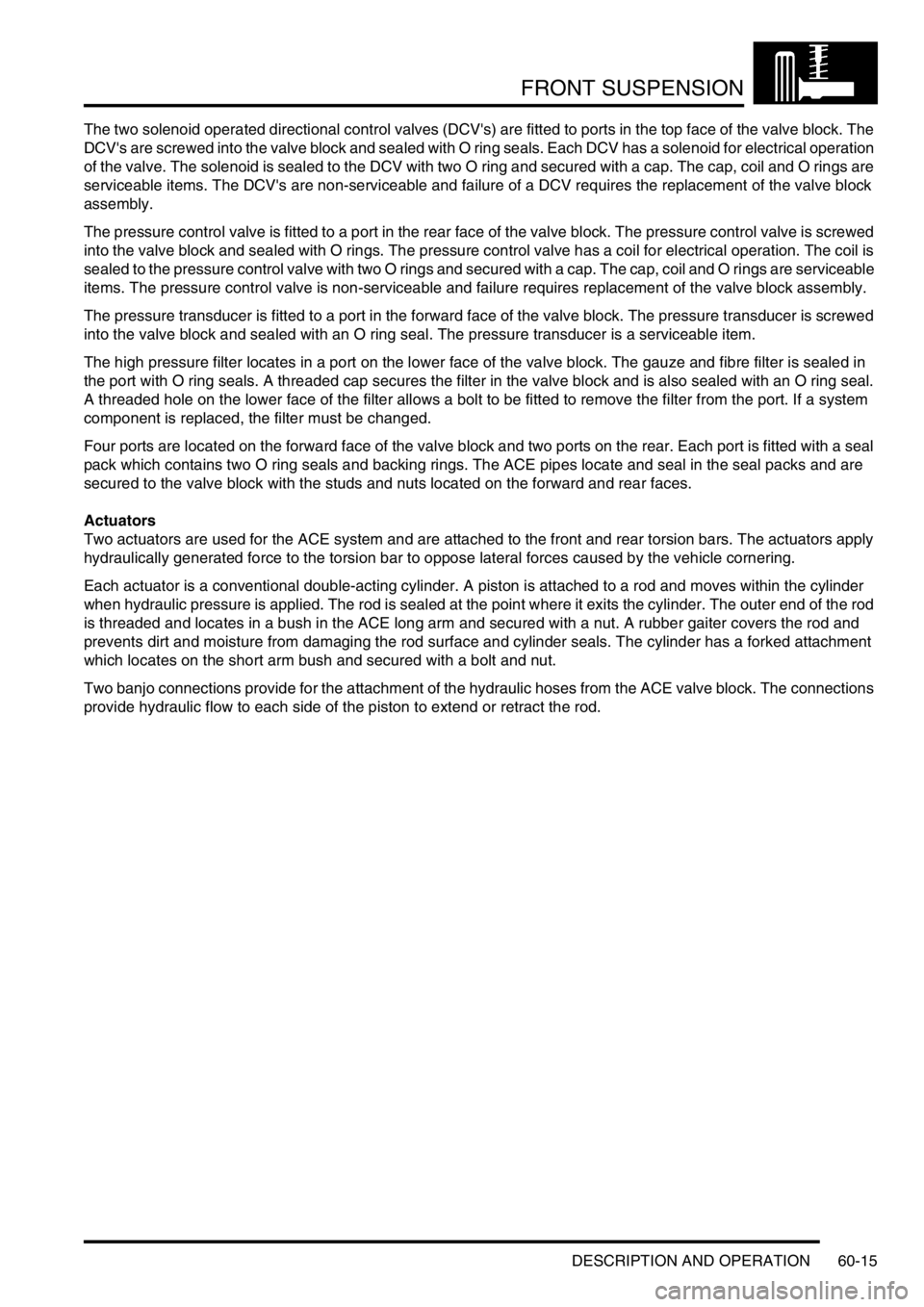
FRONT SUSPENSION
DESCRIPTION AND OPERATION 60-15
The two solenoid operated directional control valves (DCV's) are fitted to ports in the top face of the valve block. The
DCV's are screwed into the valve block and sealed with O ring seals. Each DCV has a solenoid for electrical operation
of the valve. The solenoid is sealed to the DCV with two O ring and secured with a cap. The cap, coil and O rings are
serviceable items. The DCV's are non-serviceable and failure of a DCV requires the replacement of the valve block
assembly.
The pressure control valve is fitted to a port in the rear face of the valve block. The pressure control valve is screwed
into the valve block and sealed with O rings. The pressure control valve has a coil for electrical operation. The coil is
sealed to the pressure control valve with two O rings and secured with a cap. The cap, coil and O rings are serviceable
items. The pressure control valve is non-serviceable and failure requires replacement of the valve block assembly.
The pressure transducer is fitted to a port in the forward face of the valve block. The pressure transducer is screwed
into the valve block and sealed with an O ring seal. The pressure transducer is a serviceable item.
The high pressure filter locates in a port on the lower face of the valve block. The gauze and fibre filter is sealed in
the port with O ring seals. A threaded cap secures the filter in the valve block and is also sealed with an O ring seal.
A threaded hole on the lower face of the filter allows a bolt to be fitted to remove the filter from the port. If a system
component is replaced, the filter must be changed.
Four ports are located on the forward face of the valve block and two ports on the rear. Each port is fitted with a seal
pack which contains two O ring seals and backing rings. The ACE pipes locate and seal in the seal packs and are
secured to the valve block with the studs and nuts located on the forward and rear faces.
Actuators
Two actuators are used for the ACE system and are attached to the front and rear torsion bars. The actuators apply
hydraulically generated force to the torsion bar to oppose lateral forces caused by the vehicle cornering.
Each actuator is a conventional double-acting cylinder. A piston is attached to a rod and moves within the cylinder
when hydraulic pressure is applied. The rod is sealed at the point where it exits the cylinder. The outer end of the rod
is threaded and locates in a bush in the ACE long arm and secured with a nut. A rubber gaiter covers the rod and
prevents dirt and moisture from damaging the rod surface and cylinder seals. The cylinder has a forked attachment
which locates on the short arm bush and secured with a bolt and nut.
Two banjo connections provide for the attachment of the hydraulic hoses from the ACE valve block. The connections
provide hydraulic flow to each side of the piston to extend or retract the rod.