differential LAND ROVER DISCOVERY 2002 User Guide
[x] Cancel search | Manufacturer: LAND ROVER, Model Year: 2002, Model line: DISCOVERY, Model: LAND ROVER DISCOVERY 2002Pages: 1672, PDF Size: 46.1 MB
Page 137 of 1672
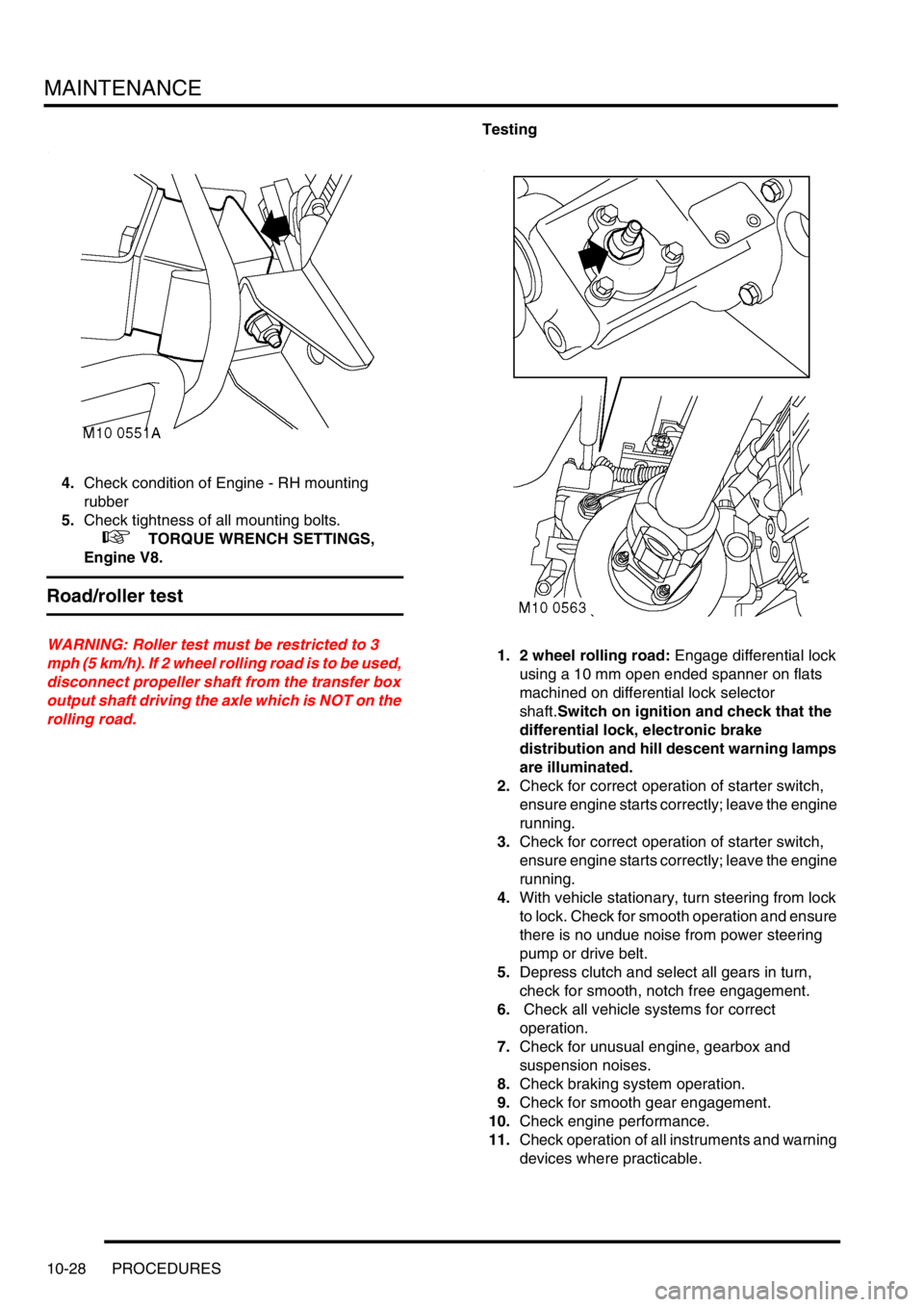
MAINTENANCE
10-28 PROCEDURES
4.Check condition of Engine - RH mounting
rubber
5.Check tightness of all mounting bolts.
+ TORQUE WRENCH SETTINGS,
Engine V8.
Road/roller test
WARNING: Roller test must be restricted to 3
mph (5 km/h). If 2 wheel rolling road is to be used,
disconnect propeller shaft from the transfer box
output shaft driving the axle which is NOT on the
rolling road.Testing
1. 2 wheel rolling road: Engage differential lock
using a 10 mm open ended spanner on flats
machined on differential lock selector
shaft.Switch on ignition and check that the
differential lock, electronic brake
distribution and hill descent warning lamps
are illuminated.
2.Check for correct operation of starter switch,
ensure engine starts correctly; leave the engine
running.
3.Check for correct operation of starter switch,
ensure engine starts correctly; leave the engine
running.
4.With vehicle stationary, turn steering from lock
to lock. Check for smooth operation and ensure
there is no undue noise from power steering
pump or drive belt.
5.Depress clutch and select all gears in turn,
check for smooth, notch free engagement.
6. Check all vehicle systems for correct
operation.
7.Check for unusual engine, gearbox and
suspension noises.
8.Check braking system operation.
9.Check for smooth gear engagement.
10.Check engine performance.
11.Check operation of all instruments and warning
devices where practicable.
Page 138 of 1672
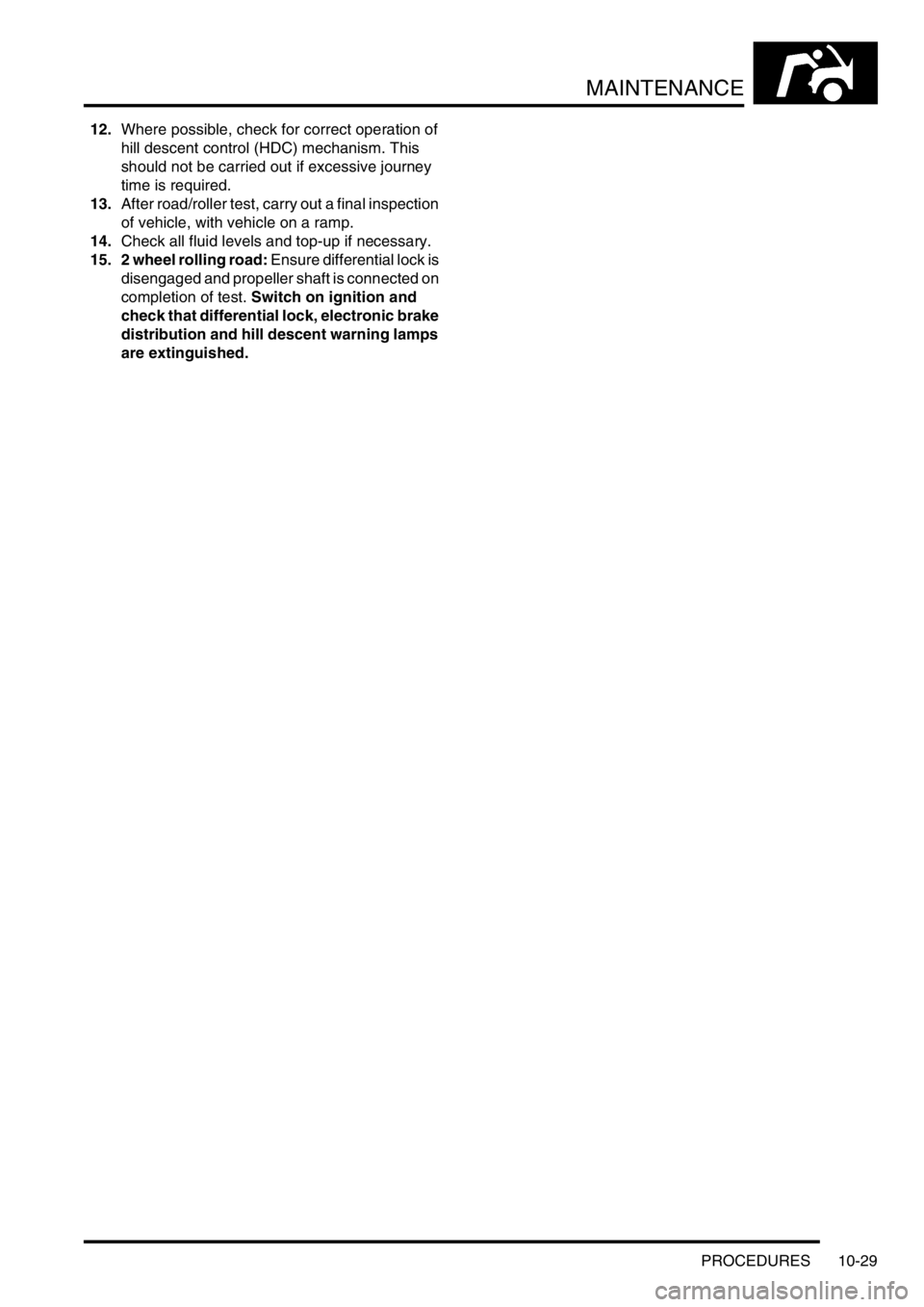
MAINTENANCE
PROCEDURES 10-29
12.Where possible, check for correct operation of
hill descent control (HDC) mechanism. This
should not be carried out if excessive journey
time is required.
13.After road/roller test, carry out a final inspection
of vehicle, with vehicle on a ramp.
14.Check all fluid levels and top-up if necessary.
15. 2 wheel rolling road: Ensure differential lock is
disengaged and propeller shaft is connected on
completion of test. Switch on ignition and
check that differential lock, electronic brake
distribution and hill descent warning lamps
are extinguished.
Page 378 of 1672
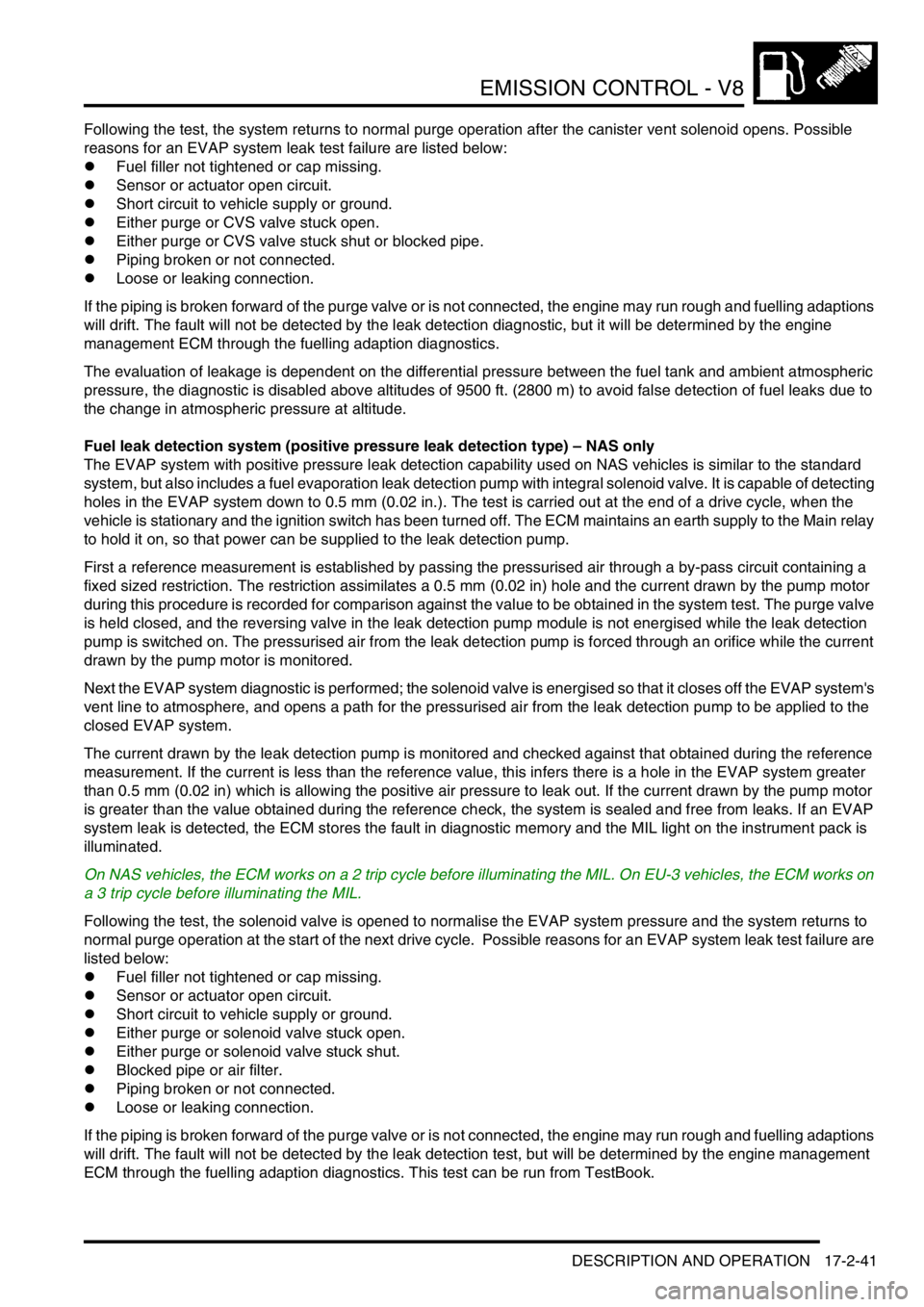
EMISSION CONTROL - V8
DESCRIPTION AND OPERATION 17-2-41
Following the test, the system returns to normal purge operation after the canister vent solenoid opens. Possible
reasons for an EVAP system leak test failure are listed below:
lFuel filler not tightened or cap missing.
lSensor or actuator open circuit.
lShort circuit to vehicle supply or ground.
lEither purge or CVS valve stuck open.
lEither purge or CVS valve stuck shut or blocked pipe.
lPiping broken or not connected.
lLoose or leaking connection.
If the piping is broken forward of the purge valve or is not connected, the engine may run rough and fuelling adaptions
will drift. The fault will not be detected by the leak detection diagnostic, but it will be determined by the engine
management ECM through the fuelling adaption diagnostics.
The evaluation of leakage is dependent on the differential pressure between the fuel tank and ambient atmospheric
pressure, the diagnostic is disabled above altitudes of 9500 ft. (2800 m) to avoid false detection of fuel leaks due to
the change in atmospheric pressure at altitude.
Fuel leak detection system (positive pressure leak detection type) – NAS only
The EVAP system with positive pressure leak detection capability used on NAS vehicles is similar to the standard
system, but also includes a fuel evaporation leak detection pump with integral solenoid valve. It is capable of detecting
holes in the EVAP system down to 0.5 mm (0.02 in.). The test is carried out at the end of a drive cycle, when the
vehicle is stationary and the ignition switch has been turned off. The ECM maintains an earth supply to the Main relay
to hold it on, so that power can be supplied to the leak detection pump.
First a reference measurement is established by passing the pressurised air through a by-pass circuit containing a
fixed sized restriction. The restriction assimilates a 0.5 mm (0.02 in) hole and the current drawn by the pump motor
during this procedure is recorded for comparison against the value to be obtained in the system test. The purge valve
is held closed, and the reversing valve in the leak detection pump module is not energised while the leak detection
pump is switched on. The pressurised air from the leak detection pump is forced through an orifice while the current
drawn by the pump motor is monitored.
Next the EVAP system diagnostic is performed; the solenoid valve is energised so that it closes off the EVAP system's
vent line to atmosphere, and opens a path for the pressurised air from the leak detection pump to be applied to the
closed EVAP system.
The current drawn by the leak detection pump is monitored and checked against that obtained during the reference
measurement. If the current is less than the reference value, this infers there is a hole in the EVAP system greater
than 0.5 mm (0.02 in) which is allowing the positive air pressure to leak out. If the current drawn by the pump motor
is greater than the value obtained during the reference check, the system is sealed and free from leaks. If an EVAP
system leak is detected, the ECM stores the fault in diagnostic memory and the MIL light on the instrument pack is
illuminated.
On NAS vehicles, the ECM works on a 2 trip cycle before illuminating the MIL. On EU-3 vehicles, the ECM works on
a 3 trip cycle before illuminating the MIL.
Following the test, the solenoid valve is opened to normalise the EVAP system pressure and the system returns to
normal purge operation at the start of the next drive cycle. Possible reasons for an EVAP system leak test failure are
listed below:
lFuel filler not tightened or cap missing.
lSensor or actuator open circuit.
lShort circuit to vehicle supply or ground.
lEither purge or solenoid valve stuck open.
lEither purge or solenoid valve stuck shut.
lBlocked pipe or air filter.
lPiping broken or not connected.
lLoose or leaking connection.
If the piping is broken forward of the purge valve or is not connected, the engine may run rough and fuelling adaptions
will drift. The fault will not be detected by the leak detection test, but will be determined by the engine management
ECM through the fuelling adaption diagnostics. This test can be run from TestBook.
Page 590 of 1672
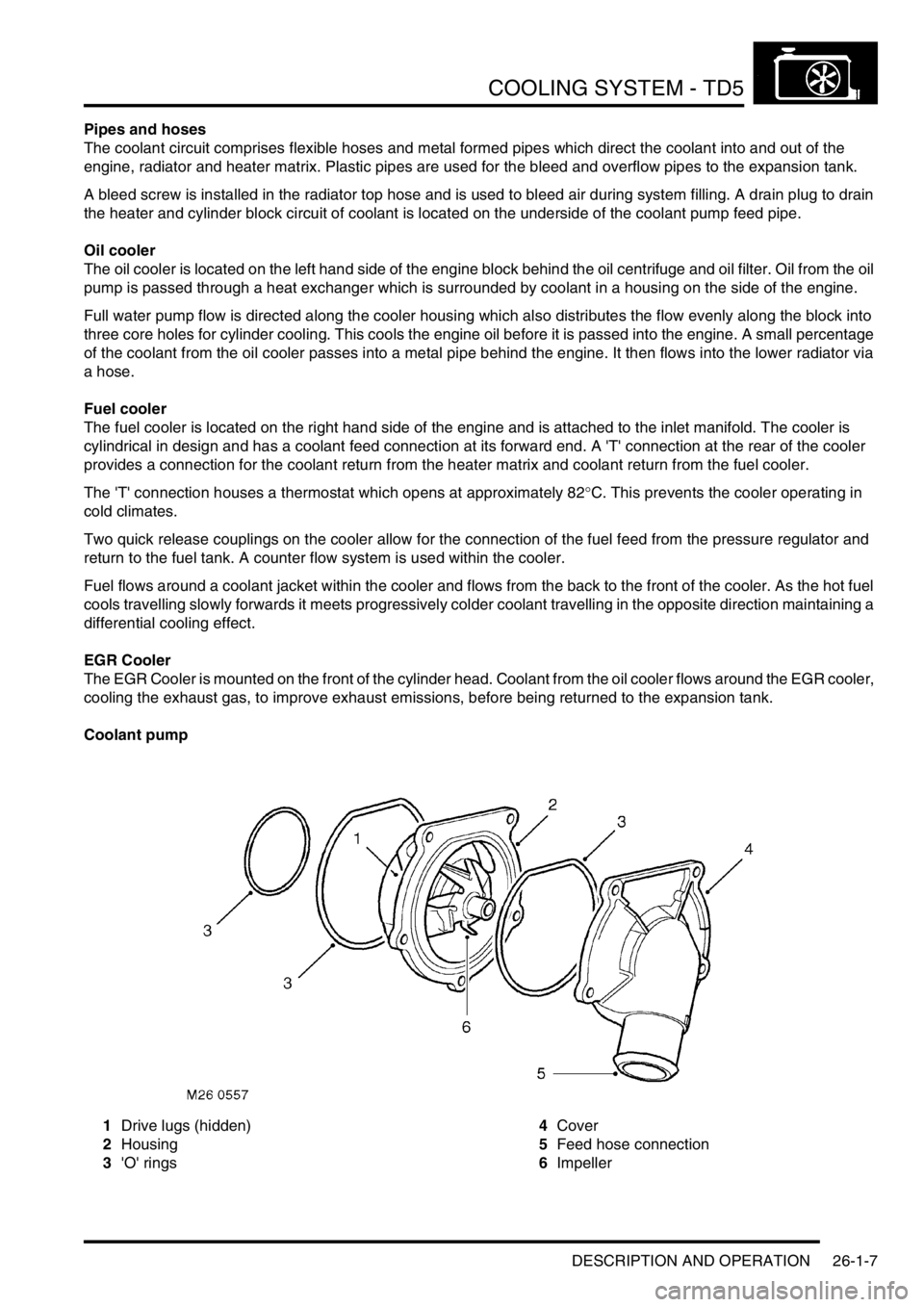
COOLING SYSTEM - TD5
DESCRIPTION AND OPERATION 26-1-7
Pipes and hoses
The coolant circuit comprises flexible hoses and metal formed pipes which direct the coolant into and out of the
engine, radiator and heater matrix. Plastic pipes are used for the bleed and overflow pipes to the expansion tank.
A bleed screw is installed in the radiator top hose and is used to bleed air during system filling. A drain plug to drain
the heater and cylinder block circuit of coolant is located on the underside of the coolant pump feed pipe.
Oil cooler
The oil cooler is located on the left hand side of the engine block behind the oil centrifuge and oil filter. Oil from the oil
pump is passed through a heat exchanger which is surrounded by coolant in a housing on the side of the engine.
Full water pump flow is directed along the cooler housing which also distributes the flow evenly along the block into
three core holes for cylinder cooling. This cools the engine oil before it is passed into the engine. A small percentage
of the coolant from the oil cooler passes into a metal pipe behind the engine. It then flows into the lower radiator via
a hose.
Fuel cooler
The fuel cooler is located on the right hand side of the engine and is attached to the inlet manifold. The cooler is
cylindrical in design and has a coolant feed connection at its forward end. A 'T' connection at the rear of the cooler
provides a connection for the coolant return from the heater matrix and coolant return from the fuel cooler.
The 'T' connection houses a thermostat which opens at approximately 82
°C. This prevents the cooler operating in
cold climates.
Two quick release couplings on the cooler allow for the connection of the fuel feed from the pressure regulator and
return to the fuel tank. A counter flow system is used within the cooler.
Fuel flows around a coolant jacket within the cooler and flows from the back to the front of the cooler. As the hot fuel
cools travelling slowly forwards it meets progressively colder coolant travelling in the opposite direction maintaining a
differential cooling effect.
EGR Cooler
The EGR Cooler is mounted on the front of the cylinder head. Coolant from the oil cooler flows around the EGR cooler,
cooling the exhaust gas, to improve exhaust emissions, before being returned to the expansion tank.
Coolant pump
1Drive lugs (hidden)
2Housing
3'O' rings4Cover
5Feed hose connection
6Impeller
Page 695 of 1672
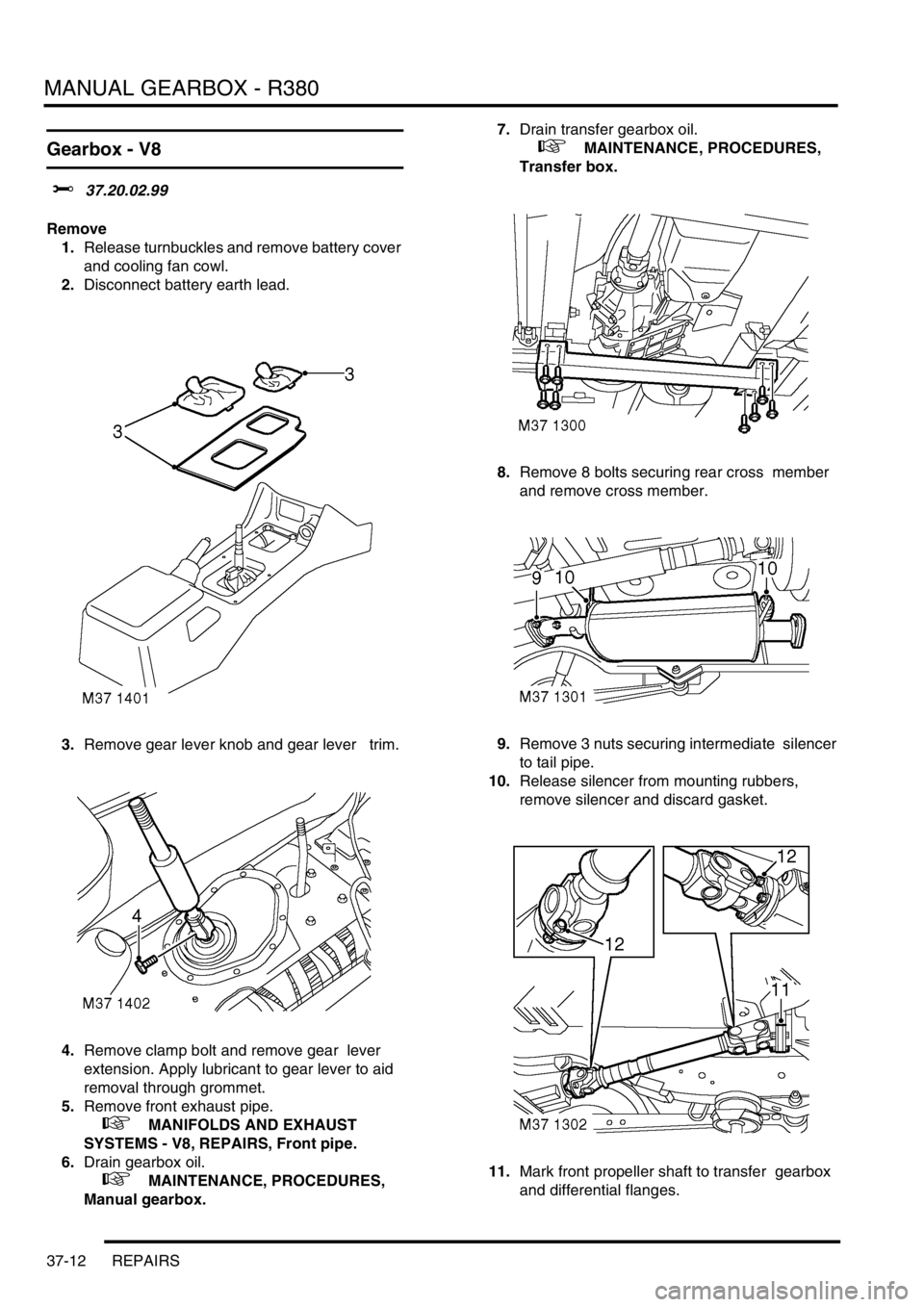
MANUAL GEARBOX - R380
37-12 REPAIRS
Gearbox - V8
$% 37.20.02.99
Remove
1.Release turnbuckles and remove battery cover
and cooling fan cowl.
2.Disconnect battery earth lead.
3.Remove gear lever knob and gear lever trim.
4.Remove clamp bolt and remove gear lever
extension. Apply lubricant to gear lever to aid
removal through grommet.
5.Remove front exhaust pipe.
+ MANIFOLDS AND EXHAUST
SYSTEMS - V8, REPAIRS, Front pipe.
6.Drain gearbox oil.
+ MAINTENANCE, PROCEDURES,
Manual gearbox.7.Drain transfer gearbox oil.
+ MAINTENANCE, PROCEDURES,
Transfer box.
8.Remove 8 bolts securing rear cross member
and remove cross member.
9.Remove 3 nuts securing intermediate silencer
to tail pipe.
10.Release silencer from mounting rubbers,
remove silencer and discard gasket.
11.Mark front propeller shaft to transfer gearbox
and differential flanges.
Page 696 of 1672
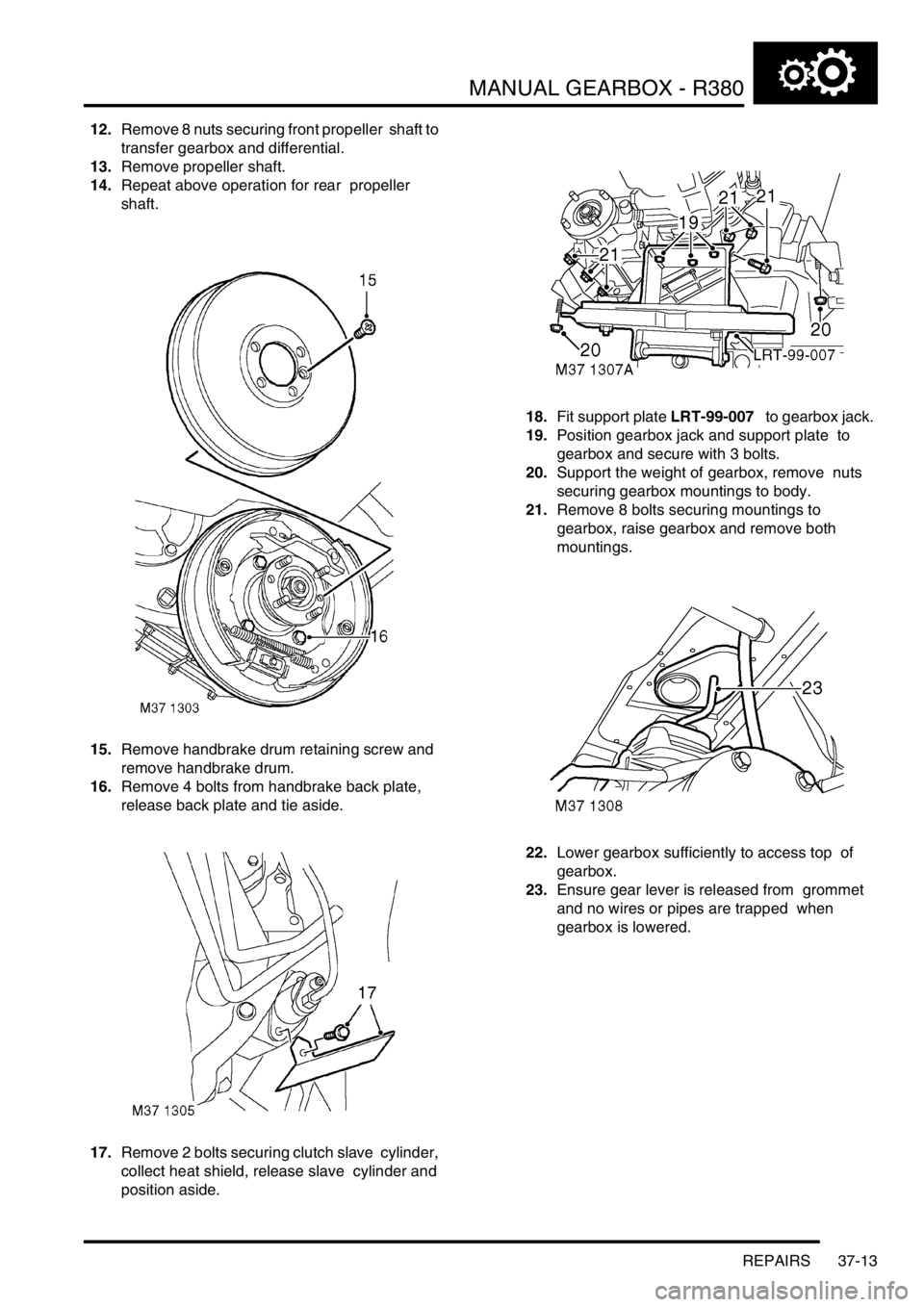
MANUAL GEARBOX - R380
REPAIRS 37-13
12.Remove 8 nuts securing front propeller shaft to
transfer gearbox and differential.
13.Remove propeller shaft.
14.Repeat above operation for rear propeller
shaft.
15.Remove handbrake drum retaining screw and
remove handbrake drum.
16.Remove 4 bolts from handbrake back plate,
release back plate and tie aside.
17.Remove 2 bolts securing clutch slave cylinder,
collect heat shield, release slave cylinder and
position aside. 18.Fit support plate LRT-99-007 to gearbox jack.
19.Position gearbox jack and support plate to
gearbox and secure with 3 bolts.
20.Support the weight of gearbox, remove nuts
securing gearbox mountings to body.
21.Remove 8 bolts securing mountings to
gearbox, raise gearbox and remove both
mountings.
22.Lower gearbox sufficiently to access top of
gearbox.
23.Ensure gear lever is released from grommet
and no wires or pipes are trapped when
gearbox is lowered.
Page 697 of 1672
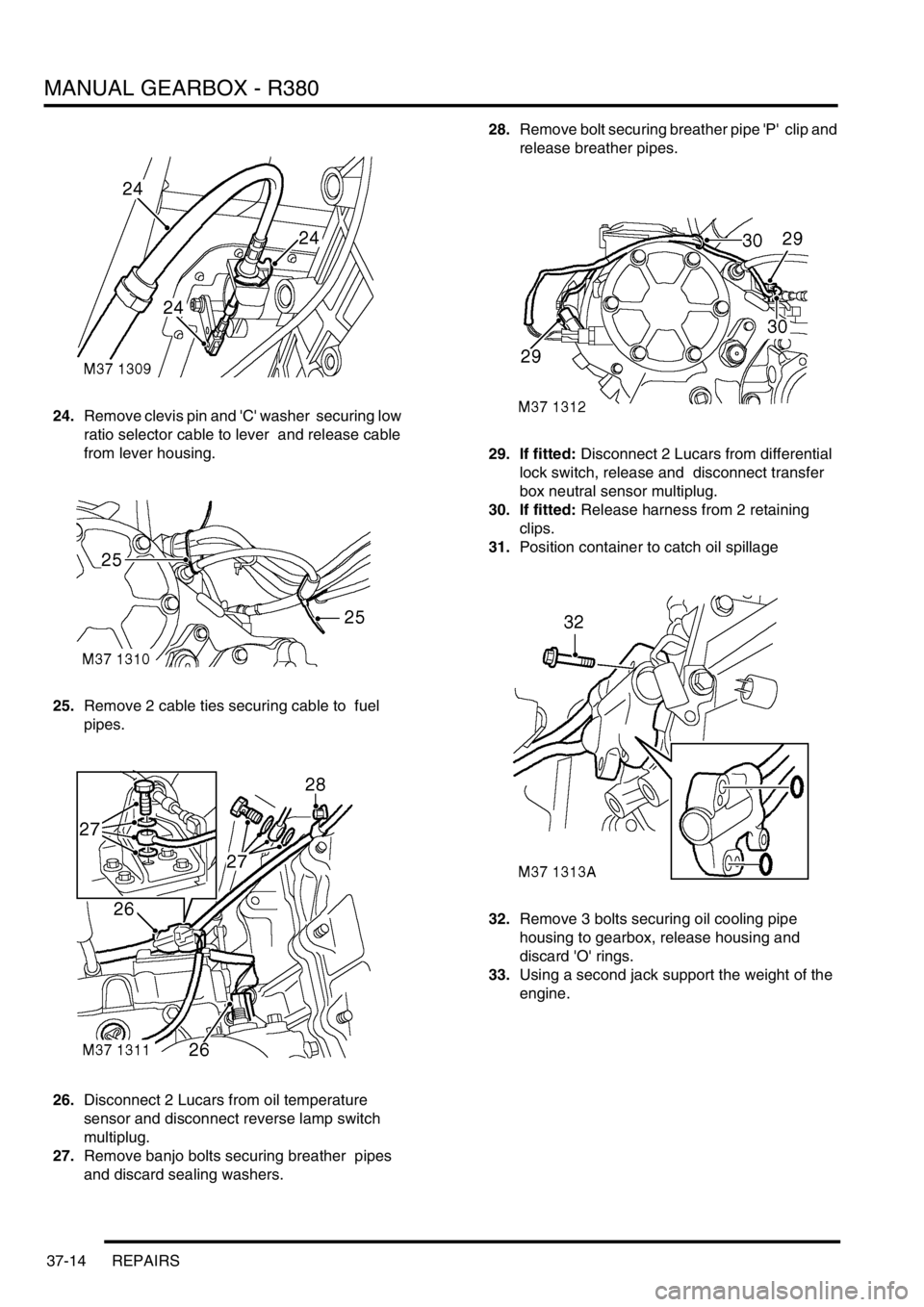
MANUAL GEARBOX - R380
37-14 REPAIRS
24.Remove clevis pin and 'C' washer securing low
ratio selector cable to lever and release cable
from lever housing.
25.Remove 2 cable ties securing cable to fuel
pipes.
26.Disconnect 2 Lucars from oil temperature
sensor and disconnect reverse lamp switch
multiplug.
27.Remove banjo bolts securing breather pipes
and discard sealing washers. 28.Remove bolt securing breather pipe 'P' clip and
release breather pipes.
29. If fitted: Disconnect 2 Lucars from differential
lock switch, release and disconnect transfer
box neutral sensor multiplug.
30. If fitted: Release harness from 2 retaining
clips.
31.Position container to catch oil spillage
32.Remove 3 bolts securing oil cooling pipe
housing to gearbox, release housing and
discard 'O' rings.
33.Using a second jack support the weight of the
engine.
Page 698 of 1672
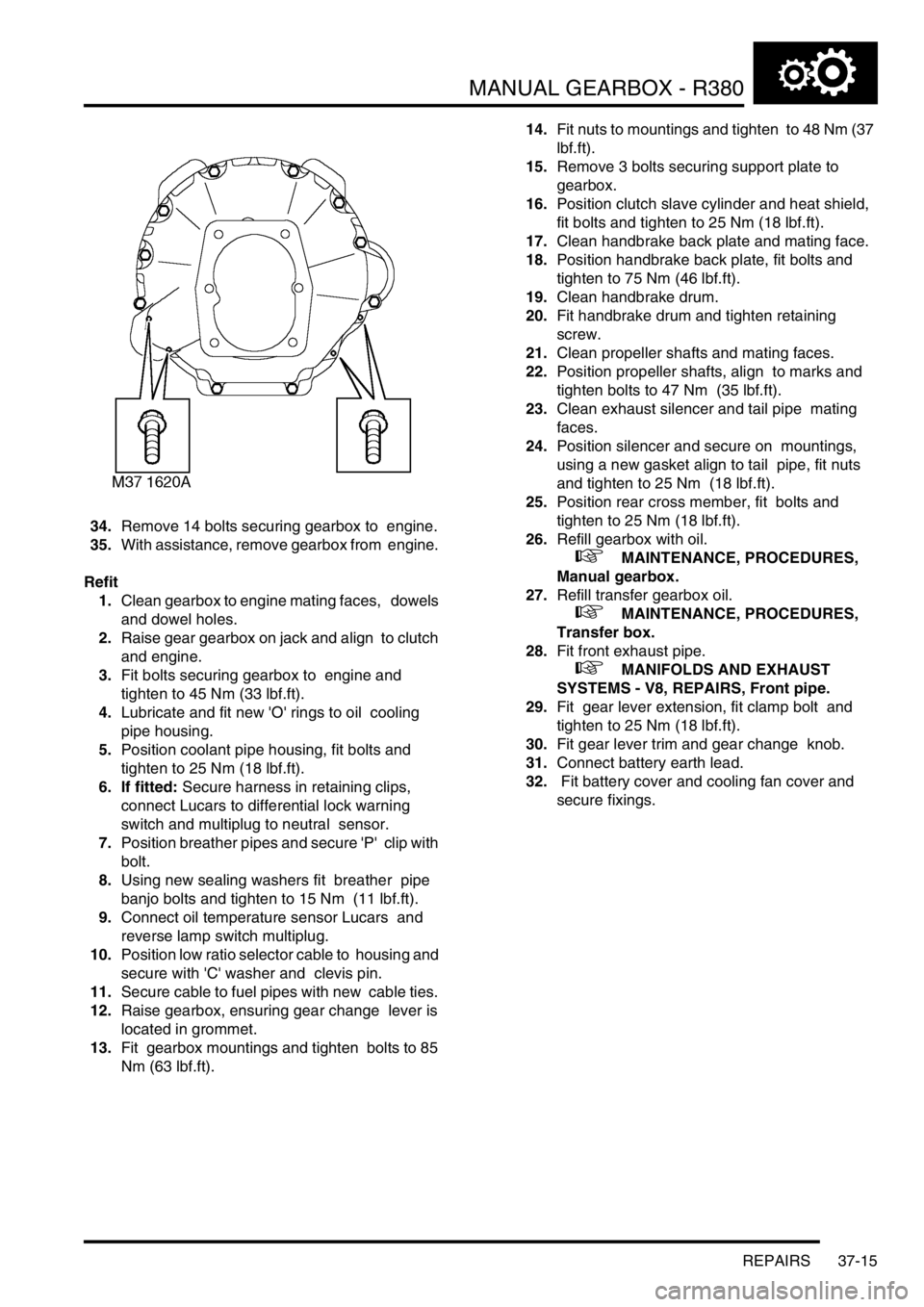
MANUAL GEARBOX - R380
REPAIRS 37-15
34.Remove 14 bolts securing gearbox to engine.
35.With assistance, remove gearbox from engine.
Refit
1.Clean gearbox to engine mating faces, dowels
and dowel holes.
2.Raise gear gearbox on jack and align to clutch
and engine.
3.Fit bolts securing gearbox to engine and
tighten to 45 Nm (33 lbf.ft).
4.Lubricate and fit new 'O' rings to oil cooling
pipe housing.
5.Position coolant pipe housing, fit bolts and
tighten to 25 Nm (18 lbf.ft).
6. If fitted: Secure harness in retaining clips,
connect Lucars to differential lock warning
switch and multiplug to neutral sensor.
7.Position breather pipes and secure 'P' clip with
bolt.
8.Using new sealing washers fit breather pipe
banjo bolts and tighten to 15 Nm (11 lbf.ft).
9.Connect oil temperature sensor Lucars and
reverse lamp switch multiplug.
10.Position low ratio selector cable to housing and
secure with 'C' washer and clevis pin.
11.Secure cable to fuel pipes with new cable ties.
12.Raise gearbox, ensuring gear change lever is
located in grommet.
13.Fit gearbox mountings and tighten bolts to 85
Nm (63 lbf.ft). 14.Fit nuts to mountings and tighten to 48 Nm (37
lbf.ft).
15.Remove 3 bolts securing support plate to
gearbox.
16.Position clutch slave cylinder and heat shield,
fit bolts and tighten to 25 Nm (18 lbf.ft).
17.Clean handbrake back plate and mating face.
18.Position handbrake back plate, fit bolts and
tighten to 75 Nm (46 lbf.ft).
19.Clean handbrake drum.
20.Fit handbrake drum and tighten retaining
screw.
21.Clean propeller shafts and mating faces.
22.Position propeller shafts, align to marks and
tighten bolts to 47 Nm (35 lbf.ft).
23.Clean exhaust silencer and tail pipe mating
faces.
24.Position silencer and secure on mountings,
using a new gasket align to tail pipe, fit nuts
and tighten to 25 Nm (18 lbf.ft).
25.Position rear cross member, fit bolts and
tighten to 25 Nm (18 lbf.ft).
26.Refill gearbox with oil.
+ MAINTENANCE, PROCEDURES,
Manual gearbox.
27.Refill transfer gearbox oil.
+ MAINTENANCE, PROCEDURES,
Transfer box.
28.Fit front exhaust pipe.
+ MANIFOLDS AND EXHAUST
SYSTEMS - V8, REPAIRS, Front pipe.
29.Fit gear lever extension, fit clamp bolt and
tighten to 25 Nm (18 lbf.ft).
30.Fit gear lever trim and gear change knob.
31.Connect battery earth lead.
32. Fit battery cover and cooling fan cover and
secure fixings.
Page 701 of 1672
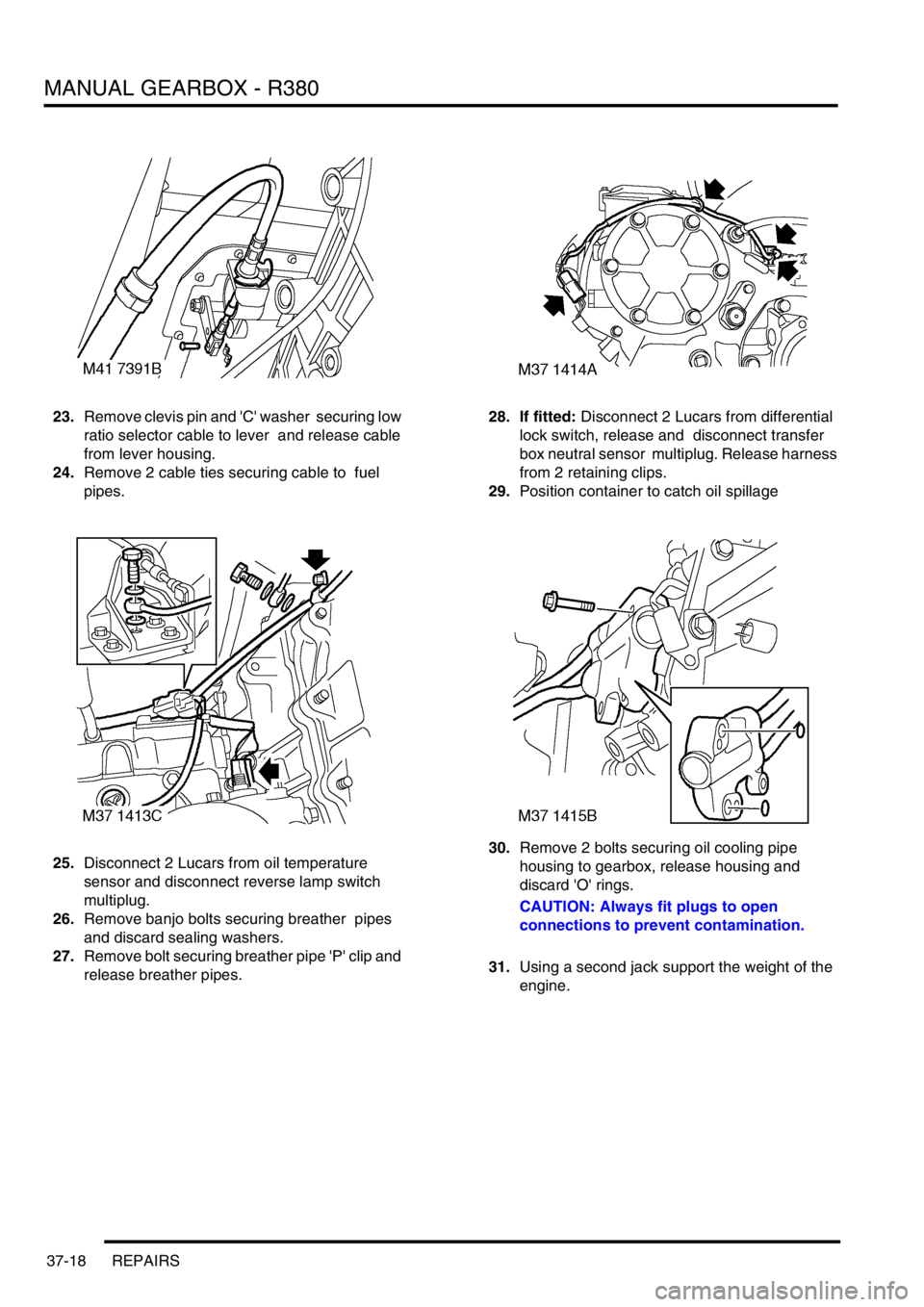
MANUAL GEARBOX - R380
37-18 REPAIRS
23.Remove clevis pin and 'C' washer securing low
ratio selector cable to lever and release cable
from lever housing.
24.Remove 2 cable ties securing cable to fuel
pipes.
25.Disconnect 2 Lucars from oil temperature
sensor and disconnect reverse lamp switch
multiplug.
26.Remove banjo bolts securing breather pipes
and discard sealing washers.
27.Remove bolt securing breather pipe 'P' clip and
release breather pipes. 28. If fitted: Disconnect 2 Lucars from differential
lock switch, release and disconnect transfer
box neutral sensor multiplug. Release harness
from 2 retaining clips.
29.Position container to catch oil spillage
30.Remove 2 bolts securing oil cooling pipe
housing to gearbox, release housing and
discard 'O' rings.
CAUTION: Always fit plugs to open
connections to prevent contamination.
31.Using a second jack support the weight of the
engine.
Page 702 of 1672
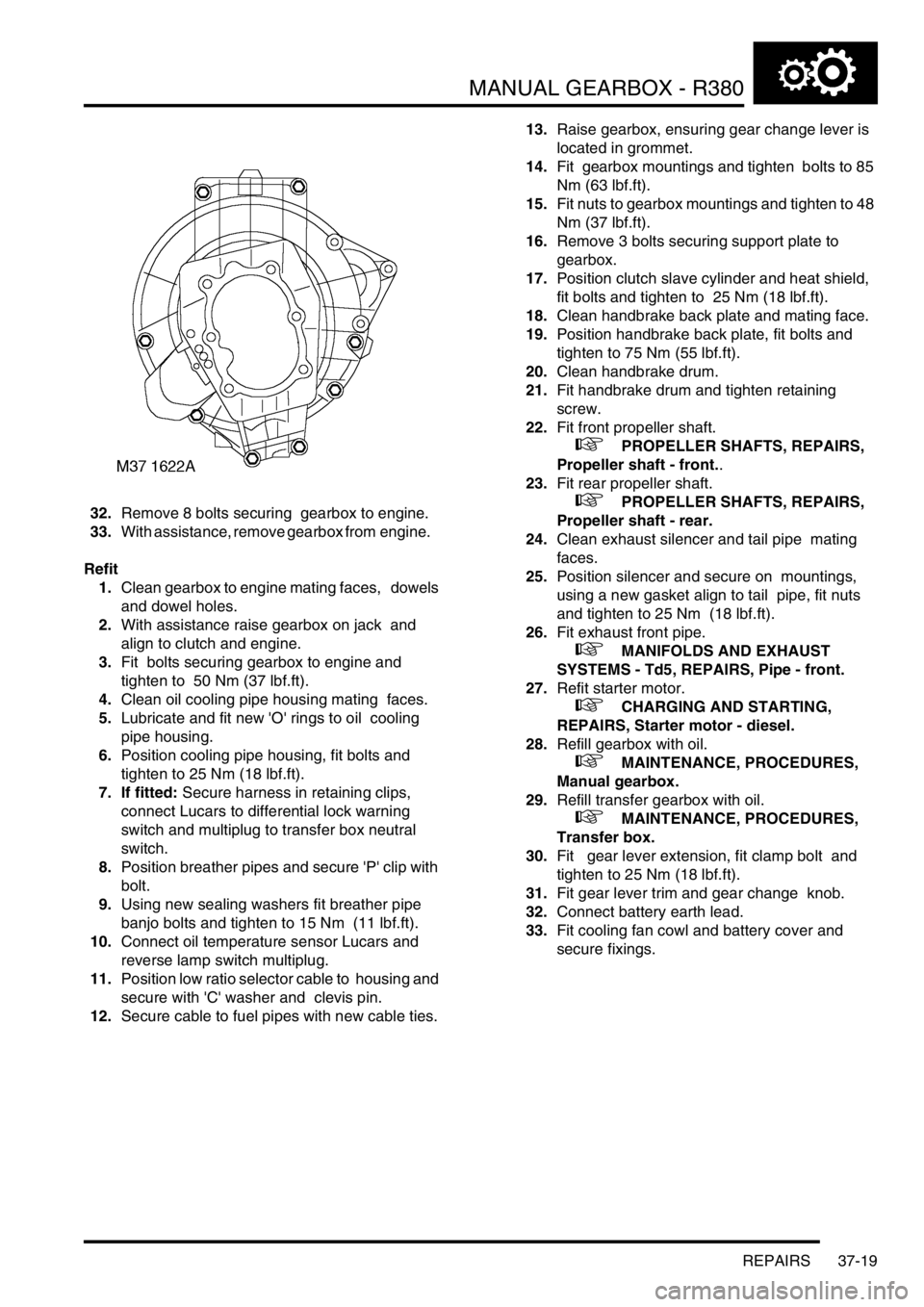
MANUAL GEARBOX - R380
REPAIRS 37-19
32.Remove 8 bolts securing gearbox to engine.
33.With assistance, remove gearbox from engine.
Refit
1.Clean gearbox to engine mating faces, dowels
and dowel holes.
2.With assistance raise gearbox on jack and
align to clutch and engine.
3.Fit bolts securing gearbox to engine and
tighten to 50 Nm (37 lbf.ft).
4.Clean oil cooling pipe housing mating faces.
5.Lubricate and fit new 'O' rings to oil cooling
pipe housing.
6.Position cooling pipe housing, fit bolts and
tighten to 25 Nm (18 lbf.ft).
7. If fitted: Secure harness in retaining clips,
connect Lucars to differential lock warning
switch and multiplug to transfer box neutral
switch.
8.Position breather pipes and secure 'P' clip with
bolt.
9.Using new sealing washers fit breather pipe
banjo bolts and tighten to 15 Nm (11 lbf.ft).
10.Connect oil temperature sensor Lucars and
reverse lamp switch multiplug.
11.Position low ratio selector cable to housing and
secure with 'C' washer and clevis pin.
12.Secure cable to fuel pipes with new cable ties. 13.Raise gearbox, ensuring gear change lever is
located in grommet.
14.Fit gearbox mountings and tighten bolts to 85
Nm (63 lbf.ft).
15.Fit nuts to gearbox mountings and tighten to 48
Nm (37 lbf.ft).
16.Remove 3 bolts securing support plate to
gearbox.
17.Position clutch slave cylinder and heat shield,
fit bolts and tighten to 25 Nm (18 lbf.ft).
18.Clean handbrake back plate and mating face.
19.Position handbrake back plate, fit bolts and
tighten to 75 Nm (55 lbf.ft).
20.Clean handbrake drum.
21.Fit handbrake drum and tighten retaining
screw.
22.Fit front propeller shaft.
+ PROPELLER SHAFTS, REPAIRS,
Propeller shaft - front..
23.Fit rear propeller shaft.
+ PROPELLER SHAFTS, REPAIRS,
Propeller shaft - rear.
24.Clean exhaust silencer and tail pipe mating
faces.
25.Position silencer and secure on mountings,
using a new gasket align to tail pipe, fit nuts
and tighten to 25 Nm (18 lbf.ft).
26.Fit exhaust front pipe.
+ MANIFOLDS AND EXHAUST
SYSTEMS - Td5, REPAIRS, Pipe - front.
27.Refit starter motor.
+ CHARGING AND STARTING,
REPAIRS, Starter motor - diesel.
28.Refill gearbox with oil.
+ MAINTENANCE, PROCEDURES,
Manual gearbox.
29.Refill transfer gearbox with oil.
+ MAINTENANCE, PROCEDURES,
Transfer box.
30.Fit gear lever extension, fit clamp bolt and
tighten to 25 Nm (18 lbf.ft).
31.Fit gear lever trim and gear change knob.
32.Connect battery earth lead.
33.Fit cooling fan cowl and battery cover and
secure fixings.