sensor LAND ROVER DISCOVERY 2002 Owner's Manual
[x] Cancel search | Manufacturer: LAND ROVER, Model Year: 2002, Model line: DISCOVERY, Model: LAND ROVER DISCOVERY 2002Pages: 1672, PDF Size: 46.1 MB
Page 116 of 1672
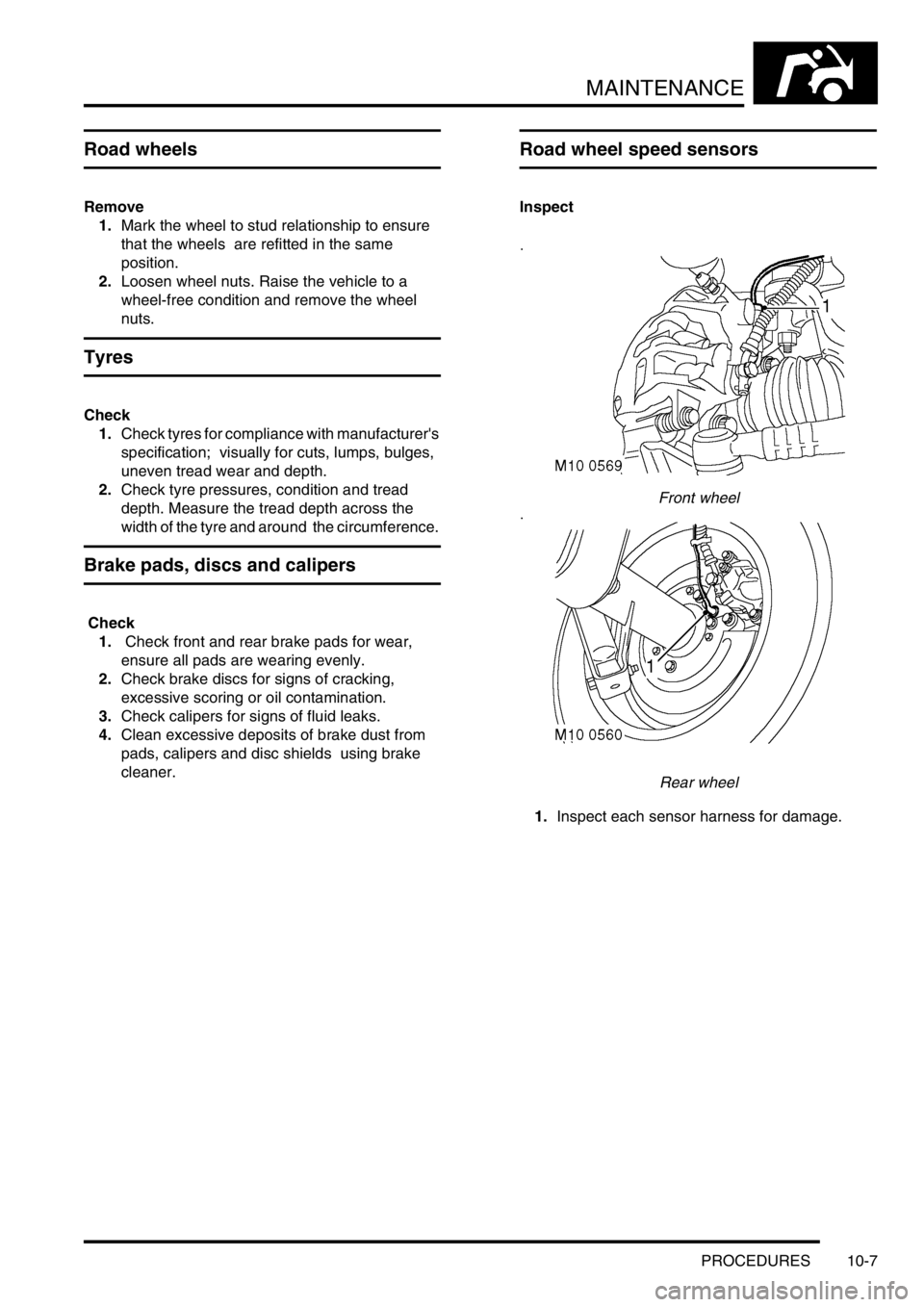
MAINTENANCE
PROCEDURES 10-7
Road wheels
Remove
1.Mark the wheel to stud relationship to ensure
that the wheels are refitted in the same
position.
2.Loosen wheel nuts. Raise the vehicle to a
wheel-free condition and remove the wheel
nuts.
Tyres
Check
1.Check tyres for compliance with manufacturer's
specification; visually for cuts, lumps, bulges,
uneven tread wear and depth.
2.Check tyre pressures, condition and tread
depth. Measure the tread depth across the
width of the tyre and around the circumference.
Brake pads, discs and calipers
Check
1. Check front and rear brake pads for wear,
ensure all pads are wearing evenly.
2.Check brake discs for signs of cracking,
excessive scoring or oil contamination.
3.Check calipers for signs of fluid leaks.
4.Clean excessive deposits of brake dust from
pads, calipers and disc shields using brake
cleaner.
Road wheel speed sensors
Inspect
Front wheel
Rear wheel
1.Inspect each sensor harness for damage.
Page 117 of 1672
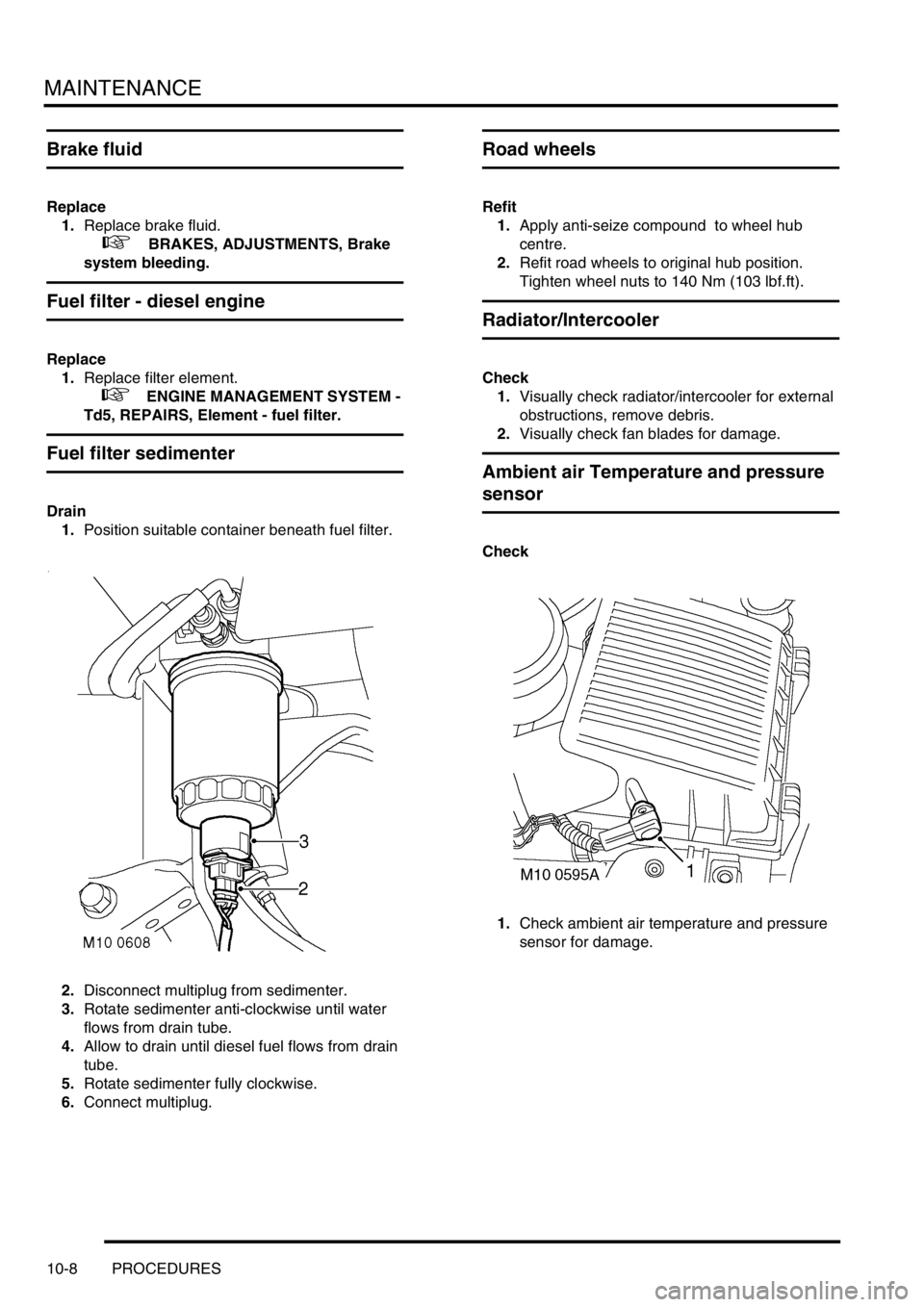
MAINTENANCE
10-8 PROCEDURES
Brake fluid
Replace
1.Replace brake fluid.
+ BRAKES, ADJUSTMENTS, Brake
system bleeding.
Fuel filter - diesel engine
Replace
1.Replace filter element.
+ ENGINE MANAGEMENT SYSTEM -
Td5, REPAIRS, Element - fuel filter.
Fuel filter sedimenter
Drain
1.Position suitable container beneath fuel filter.
2.Disconnect multiplug from sedimenter.
3.Rotate sedimenter anti-clockwise until water
flows from drain tube.
4.Allow to drain until diesel fuel flows from drain
tube.
5.Rotate sedimenter fully clockwise.
6.Connect multiplug.
Road wheels
Refit
1.Apply anti-seize compound to wheel hub
centre.
2.Refit road wheels to original hub position.
Tighten wheel nuts to 140 Nm (103 lbf.ft).
Radiator/Intercooler
Check
1.Visually check radiator/intercooler for external
obstructions, remove debris.
2.Visually check fan blades for damage.
Ambient air Temperature and pressure
sensor
Check
1.Check ambient air temperature and pressure
sensor for damage.
Page 134 of 1672
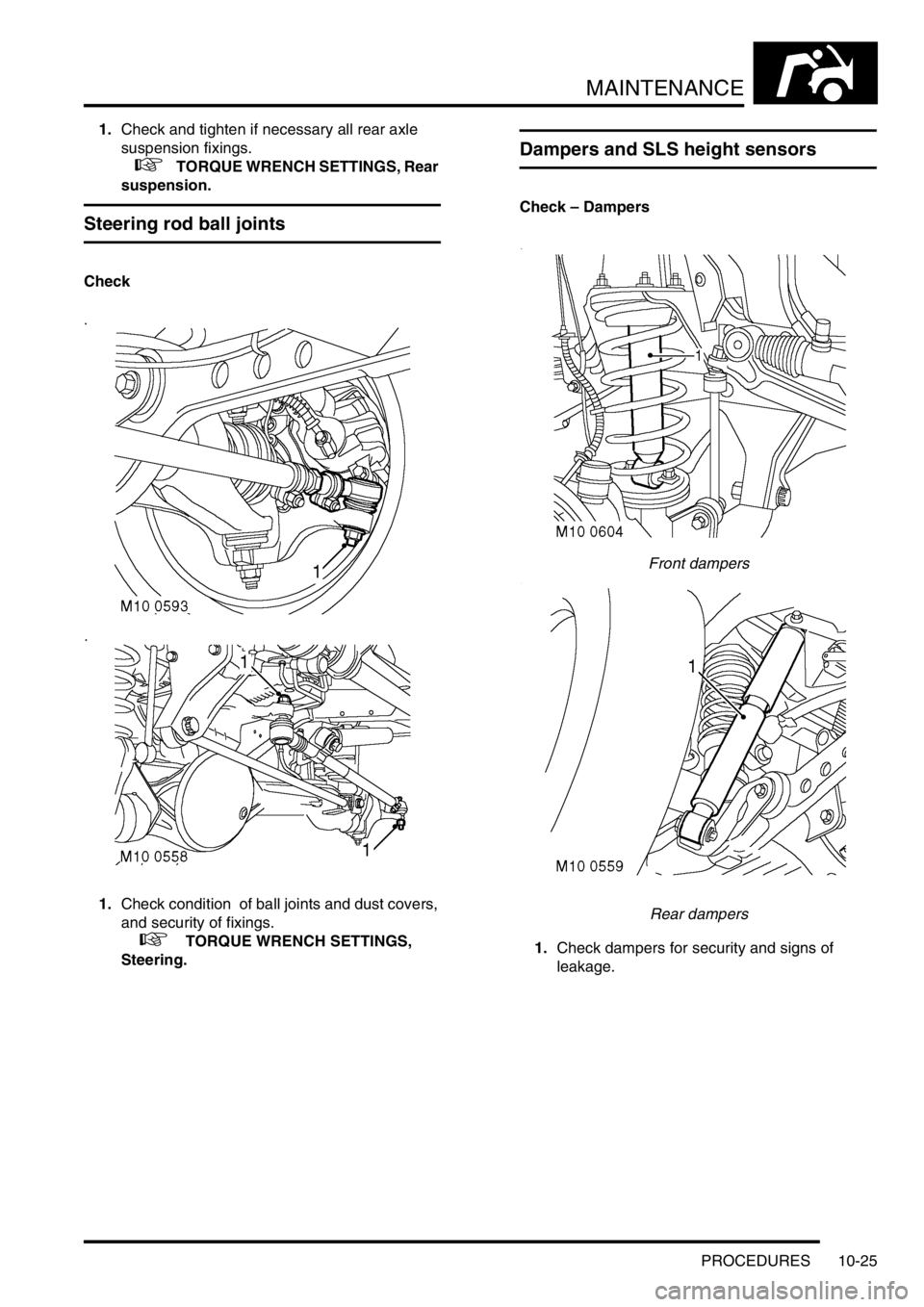
MAINTENANCE
PROCEDURES 10-25
1.Check and tighten if necessary all rear axle
suspension fixings.
+ TORQUE WRENCH SETTINGS, Rear
suspension.
Steering rod ball joints
Check
1.Check condition of ball joints and dust covers,
and security of fixings.
+ TORQUE WRENCH SETTINGS,
Steering.
Dampers and SLS height sensors
Check – Dampers
Front dampers
Rear dampers
1.Check dampers for security and signs of
leakage.
Page 135 of 1672
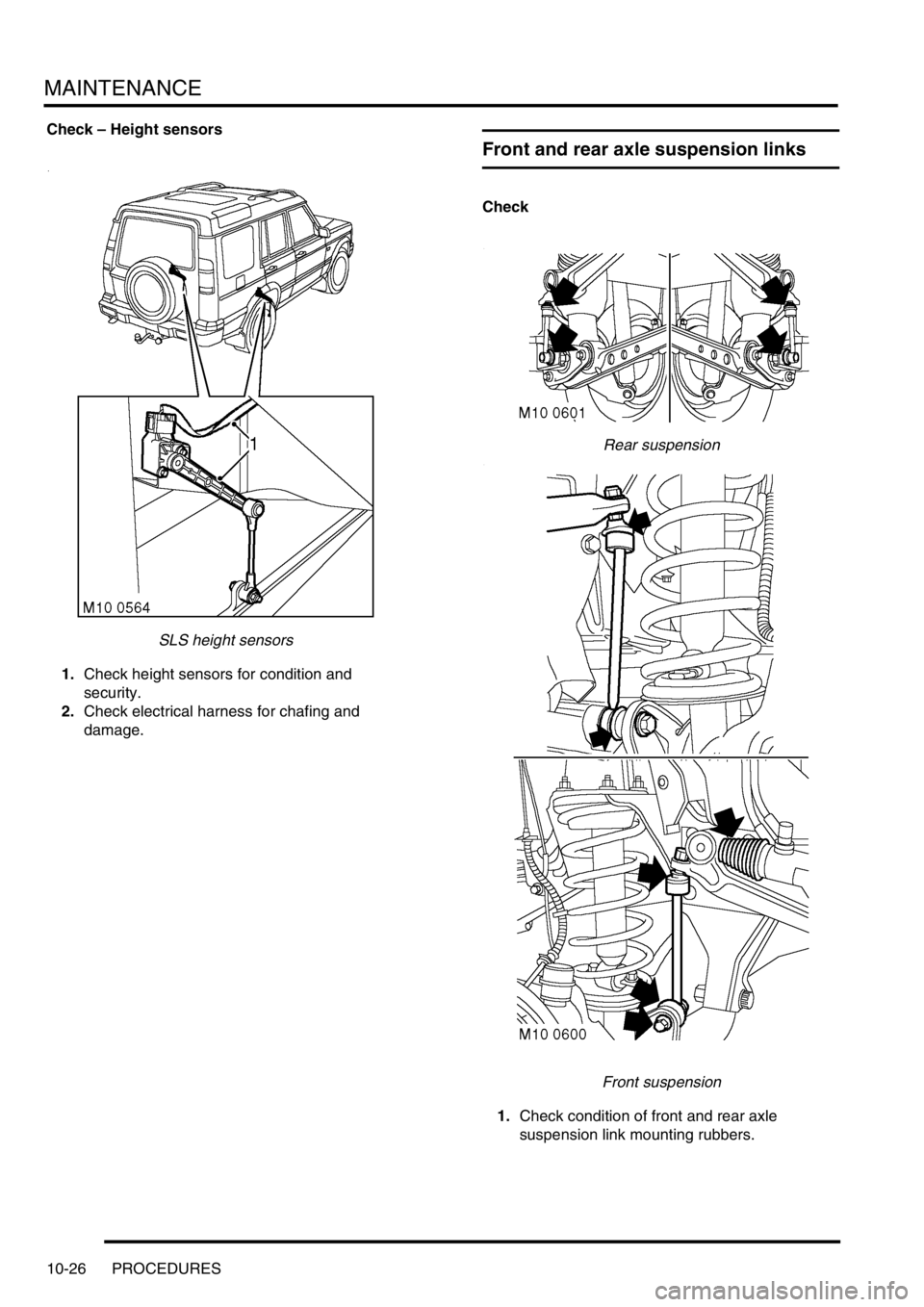
MAINTENANCE
10-26 PROCEDURES
Check – Height sensors
SLS height sensors
1.Check height sensors for condition and
security.
2.Check electrical harness for chafing and
damage.
Front and rear axle suspension links
Check
Rear suspension
Front suspension
1.Check condition of front and rear axle
suspension link mounting rubbers.
Page 161 of 1672
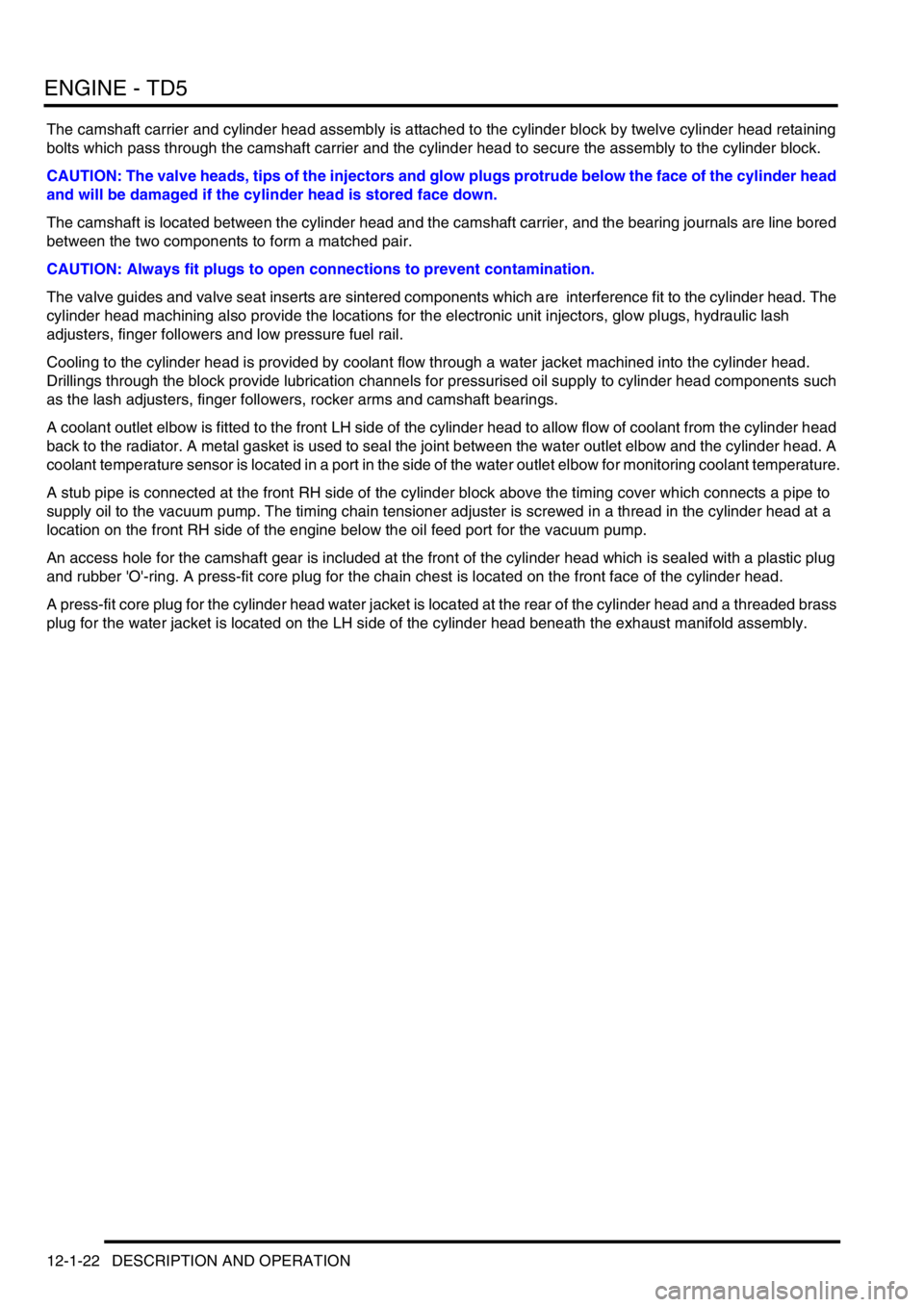
ENGINE - TD5
12-1-22 DESCRIPTION AND OPERATION
The camshaft carrier and cylinder head assembly is attached to the cylinder block by twelve cylinder head retaining
bolts which pass through the camshaft carrier and the cylinder head to secure the assembly to the cylinder block.
CAUTION: The valve heads, tips of the injectors and glow plugs protrude below the face of the cylinder head
and will be damaged if the cylinder head is stored face down.
The camshaft is located between the cylinder head and the camshaft carrier, and the bearing journals are line bored
between the two components to form a matched pair.
CAUTION: Always fit plugs to open connections to prevent contamination.
The valve guides and valve seat inserts are sintered components which are interference fit to the cylinder head. The
cylinder head machining also provide the locations for the electronic unit injectors, glow plugs, hydraulic lash
adjusters, finger followers and low pressure fuel rail.
Cooling to the cylinder head is provided by coolant flow through a water jacket machined into the cylinder head.
Drillings through the block provide lubrication channels for pressurised oil supply to cylinder head components such
as the lash adjusters, finger followers, rocker arms and camshaft bearings.
A coolant outlet elbow is fitted to the front LH side of the cylinder head to allow flow of coolant from the cylinder head
back to the radiator. A metal gasket is used to seal the joint between the water outlet elbow and the cylinder head. A
coolant temperature sensor is located in a port in the side of the water outlet elbow for monitoring coolant temperature.
A stub pipe is connected at the front RH side of the cylinder block above the timing cover which connects a pipe to
supply oil to the vacuum pump. The timing chain tensioner adjuster is screwed in a thread in the cylinder head at a
location on the front RH side of the engine below the oil feed port for the vacuum pump.
An access hole for the camshaft gear is included at the front of the cylinder head which is sealed with a plastic plug
and rubber 'O'-ring. A press-fit core plug for the chain chest is located on the front face of the cylinder head.
A press-fit core plug for the cylinder head water jacket is located at the rear of the cylinder head and a threaded brass
plug for the water jacket is located on the LH side of the cylinder head beneath the exhaust manifold assembly.
Page 162 of 1672
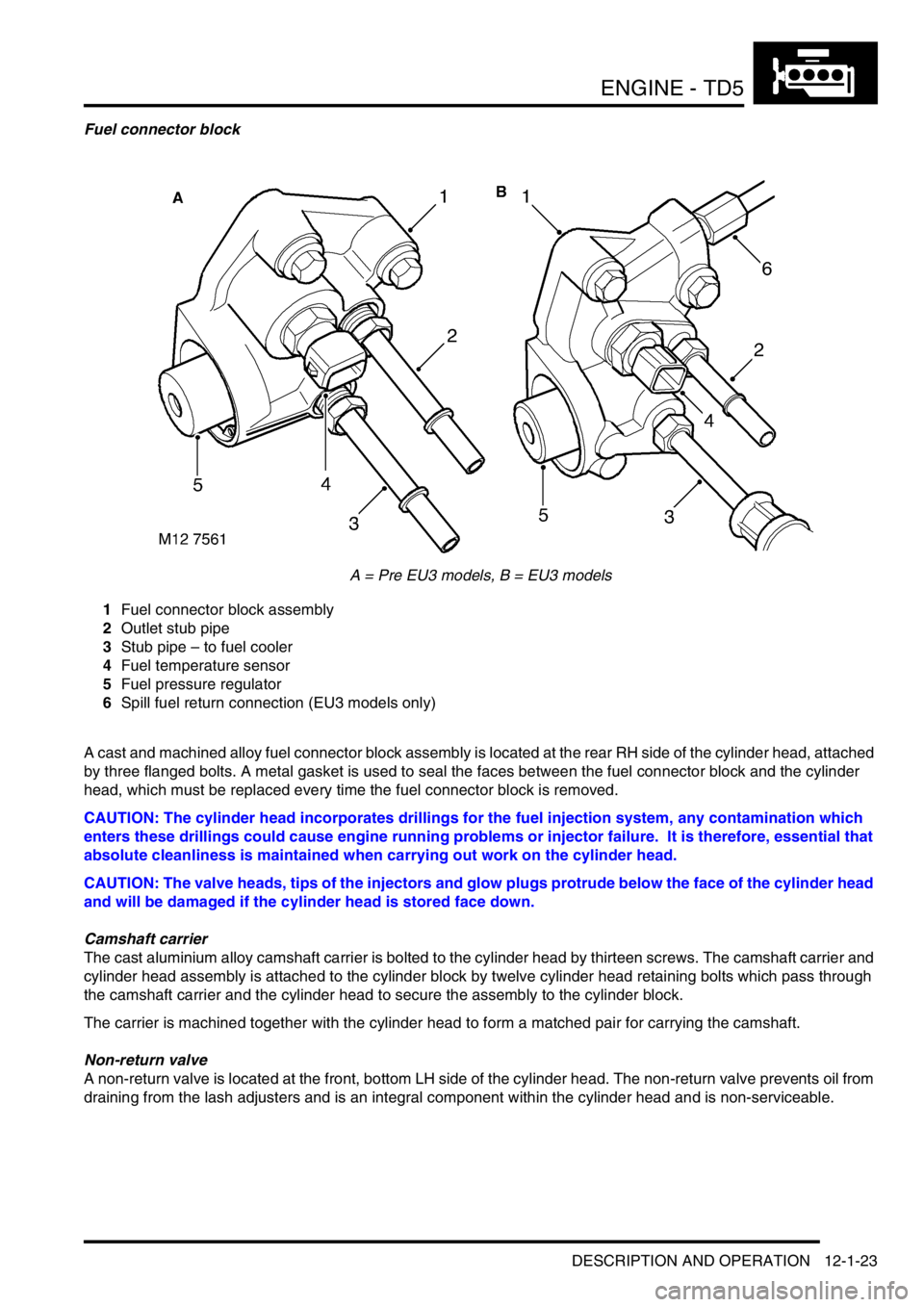
ENGINE - TD5
DESCRIPTION AND OPERATION 12-1-23
Fuel connector block
A = Pre EU3 models, B = EU3 models
1Fuel connector block assembly
2Outlet stub pipe
3Stub pipe – to fuel cooler
4Fuel temperature sensor
5Fuel pressure regulator
6Spill fuel return connection (EU3 models only)
A cast and machined alloy fuel connector block assembly is located at the rear RH side of the cylinder head, attached
by three flanged bolts. A metal gasket is used to seal the faces between the fuel connector block and the cylinder
head, which must be replaced every time the fuel connector block is removed.
CAUTION: The cylinder head incorporates drillings for the fuel injection system, any contamination which
enters these drillings could cause engine running problems or injector failure. It is therefore, essential that
absolute cleanliness is maintained when carrying out work on the cylinder head.
CAUTION: The valve heads, tips of the injectors and glow plugs protrude below the face of the cylinder head
and will be damaged if the cylinder head is stored face down.
Camshaft carrier
The cast aluminium alloy camshaft carrier is bolted to the cylinder head by thirteen screws. The camshaft carrier and
cylinder head assembly is attached to the cylinder block by twelve cylinder head retaining bolts which pass through
the camshaft carrier and the cylinder head to secure the assembly to the cylinder block.
The carrier is machined together with the cylinder head to form a matched pair for carrying the camshaft.
Non-return valve
A non-return valve is located at the front, bottom LH side of the cylinder head. The non-return valve prevents oil from
draining from the lash adjusters and is an integral component within the cylinder head and is non-serviceable.
Page 178 of 1672
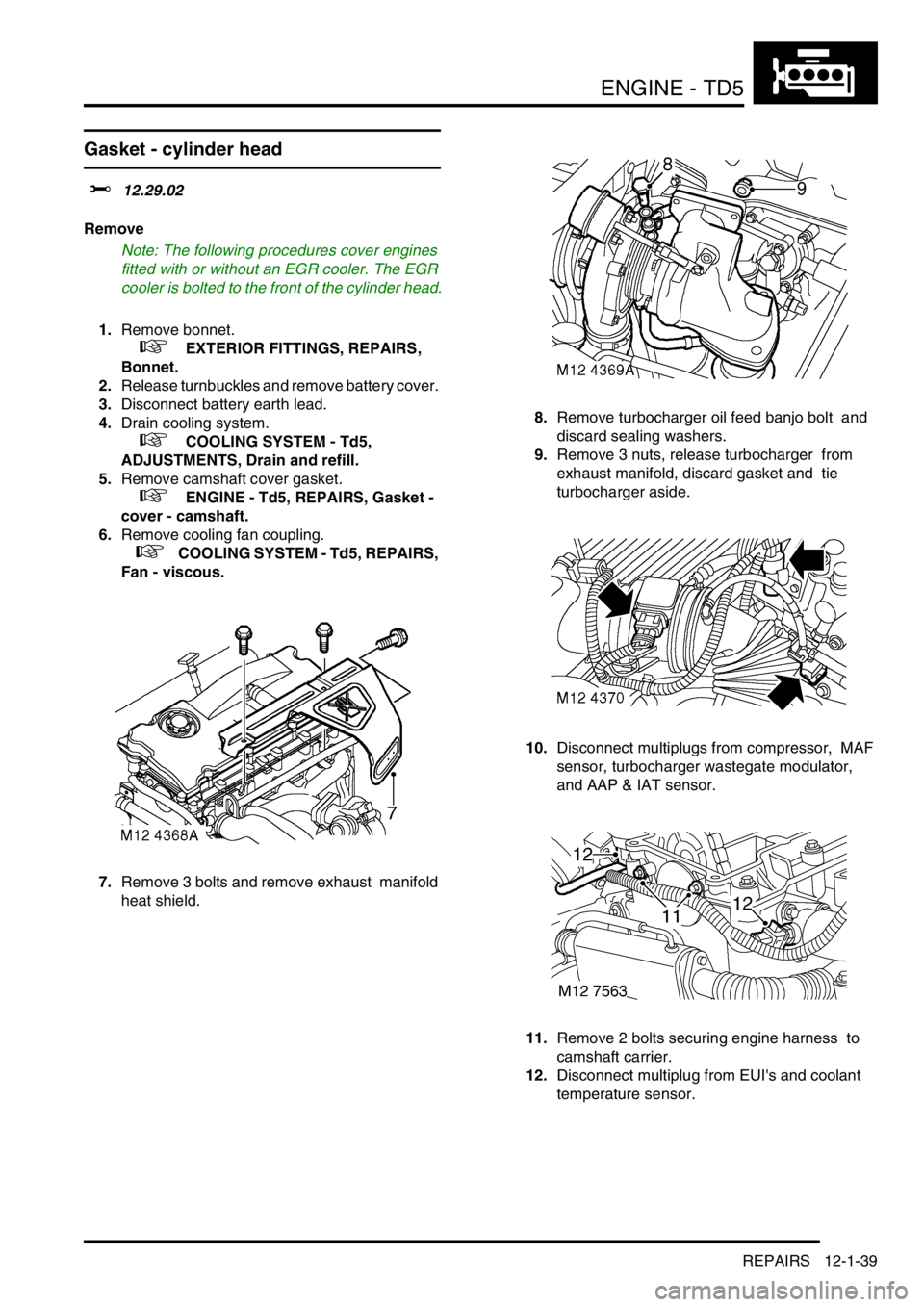
ENGINE - TD5
REPAIRS 12-1-39
Gasket - cylinder head
$% 12.29.02
Remove
Note: The following procedures cover engines
fitted with or without an EGR cooler. The EGR
cooler is bolted to the front of the cylinder head.
1.Remove bonnet.
+ EXTERIOR FITTINGS, REPAIRS,
Bonnet.
2.Release turnbuckles and remove battery cover.
3.Disconnect battery earth lead.
4.Drain cooling system.
+ COOLING SYSTEM - Td5,
ADJUSTMENTS, Drain and refill.
5.Remove camshaft cover gasket.
+ ENGINE - Td5, REPAIRS, Gasket -
cover - camshaft.
6.Remove cooling fan coupling.
+ COOLING SYSTEM - Td5, REPAIRS,
Fan - viscous.
7.Remove 3 bolts and remove exhaust manifold
heat shield. 8.Remove turbocharger oil feed banjo bolt and
discard sealing washers.
9.Remove 3 nuts, release turbocharger from
exhaust manifold, discard gasket and tie
turbocharger aside.
10.Disconnect multiplugs from compressor, MAF
sensor, turbocharger wastegate modulator,
and AAP & IAT sensor.
11.Remove 2 bolts securing engine harness to
camshaft carrier.
12.Disconnect multiplug from EUI's and coolant
temperature sensor.
Page 179 of 1672
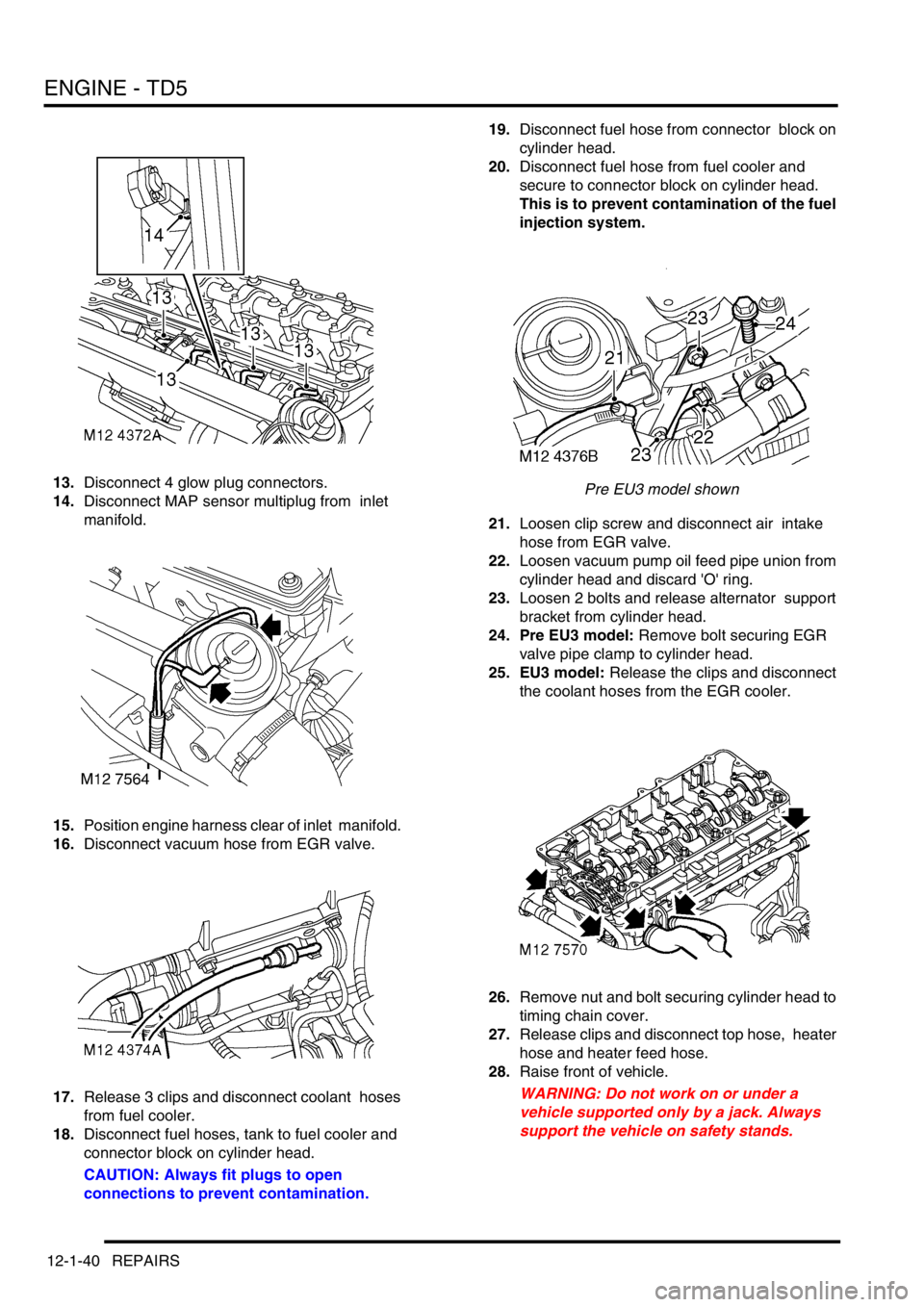
ENGINE - TD5
12-1-40 REPAIRS
13.Disconnect 4 glow plug connectors.
14.Disconnect MAP sensor multiplug from inlet
manifold.
15.Position engine harness clear of inlet manifold.
16.Disconnect vacuum hose from EGR valve.
17.Release 3 clips and disconnect coolant hoses
from fuel cooler.
18.Disconnect fuel hoses, tank to fuel cooler and
connector block on cylinder head.
CAUTION: Always fit plugs to open
connections to prevent contamination.19.Disconnect fuel hose from connector block on
cylinder head.
20.Disconnect fuel hose from fuel cooler and
secure to connector block on cylinder head.
This is to prevent contamination of the fuel
injection system.
Pre EU3 model shown
21.Loosen clip screw and disconnect air intake
hose from EGR valve.
22.Loosen vacuum pump oil feed pipe union from
cylinder head and discard 'O' ring.
23.Loosen 2 bolts and release alternator support
bracket from cylinder head.
24. Pre EU3 model: Remove bolt securing EGR
valve pipe clamp to cylinder head.
25. EU3 model: Release the clips and disconnect
the coolant hoses from the EGR cooler.
26.Remove nut and bolt securing cylinder head to
timing chain cover.
27.Release clips and disconnect top hose, heater
hose and heater feed hose.
28.Raise front of vehicle.
WARNING: Do not work on or under a
vehicle supported only by a jack. Always
support the vehicle on safety stands.
Page 188 of 1672
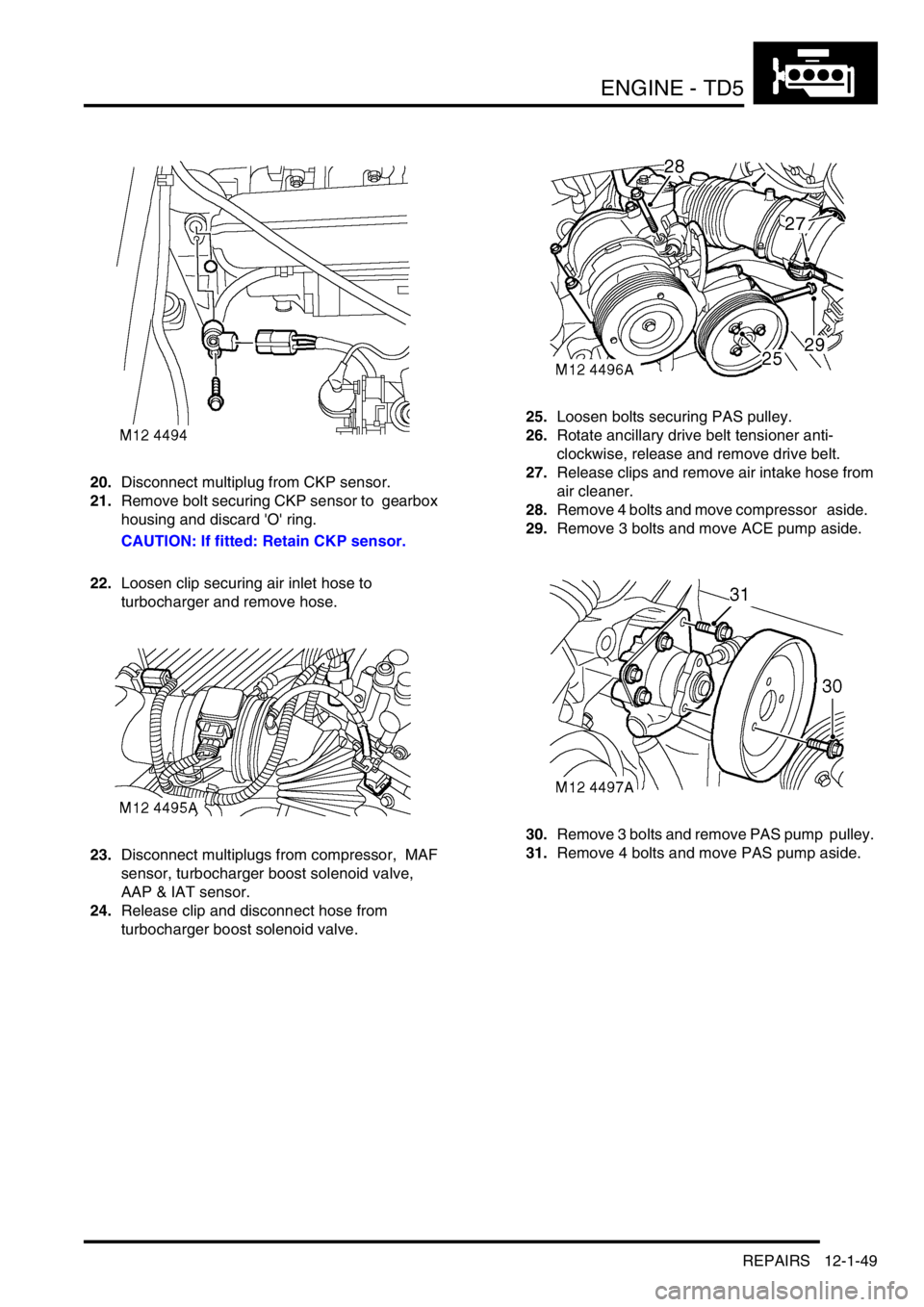
ENGINE - TD5
REPAIRS 12-1-49
20.Disconnect multiplug from CKP sensor.
21.Remove bolt securing CKP sensor to gearbox
housing and discard 'O' ring.
CAUTION: If fitted: Retain CKP sensor.
22.Loosen clip securing air inlet hose to
turbocharger and remove hose.
23.Disconnect multiplugs from compressor, MAF
sensor, turbocharger boost solenoid valve,
AAP & IAT sensor.
24.Release clip and disconnect hose from
turbocharger boost solenoid valve. 25.Loosen bolts securing PAS pulley.
26.Rotate ancillary drive belt tensioner anti-
clockwise, release and remove drive belt.
27.Release clips and remove air intake hose from
air cleaner.
28.Remove 4 bolts and move compressor aside.
29.Remove 3 bolts and move ACE pump aside.
30.Remove 3 bolts and remove PAS pump pulley.
31.Remove 4 bolts and move PAS pump aside.
Page 191 of 1672
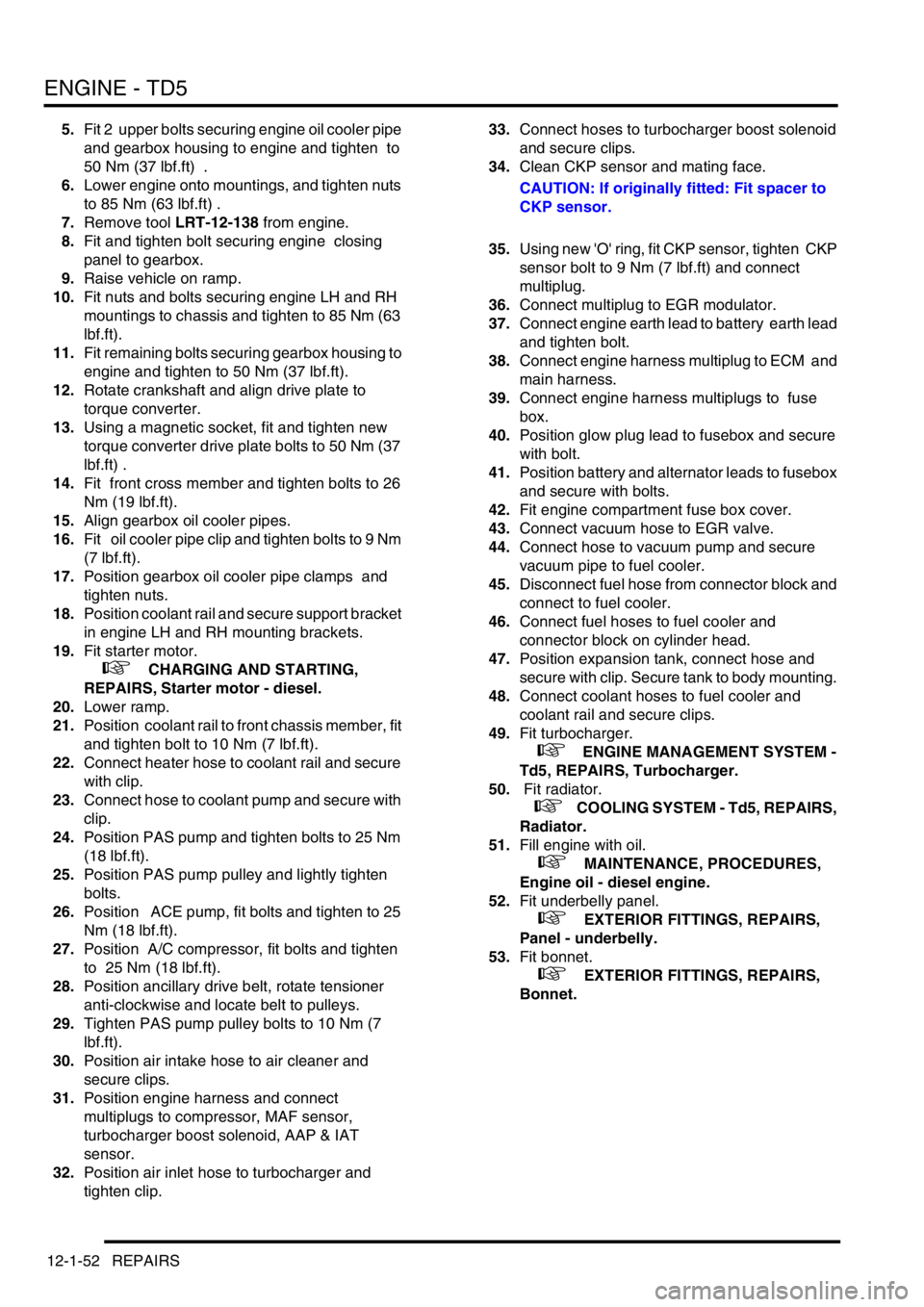
ENGINE - TD5
12-1-52 REPAIRS
5.Fit 2 upper bolts securing engine oil cooler pipe
and gearbox housing to engine and tighten to
50 Nm (37 lbf.ft) .
6.Lower engine onto mountings, and tighten nuts
to 85 Nm (63 lbf.ft) .
7.Remove tool LRT-12-138 from engine.
8.Fit and tighten bolt securing engine closing
panel to gearbox.
9.Raise vehicle on ramp.
10.Fit nuts and bolts securing engine LH and RH
mountings to chassis and tighten to 85 Nm (63
lbf.ft).
11.Fit remaining bolts securing gearbox housing to
engine and tighten to 50 Nm (37 lbf.ft).
12.Rotate crankshaft and align drive plate to
torque converter.
13.Using a magnetic socket, fit and tighten new
torque converter drive plate bolts to 50 Nm (37
lbf.ft) .
14.Fit front cross member and tighten bolts to 26
Nm (19 lbf.ft).
15.Align gearbox oil cooler pipes.
16.Fit oil cooler pipe clip and tighten bolts to 9 Nm
(7 lbf.ft).
17.Position gearbox oil cooler pipe clamps and
tighten nuts.
18.Position coolant rail and secure support bracket
in engine LH and RH mounting brackets.
19.Fit starter motor.
+ CHARGING AND STARTING,
REPAIRS, Starter motor - diesel.
20.Lower ramp.
21.Position coolant rail to front chassis member, fit
and tighten bolt to 10 Nm (7 lbf.ft).
22.Connect heater hose to coolant rail and secure
with clip.
23.Connect hose to coolant pump and secure with
clip.
24.Position PAS pump and tighten bolts to 25 Nm
(18 lbf.ft).
25.Position PAS pump pulley and lightly tighten
bolts.
26.Position ACE pump, fit bolts and tighten to 25
Nm (18 lbf.ft).
27.Position A/C compressor, fit bolts and tighten
to 25 Nm (18 lbf.ft).
28.Position ancillary drive belt, rotate tensioner
anti-clockwise and locate belt to pulleys.
29.Tighten PAS pump pulley bolts to 10 Nm (7
lbf.ft).
30.Position air intake hose to air cleaner and
secure clips.
31.Position engine harness and connect
multiplugs to compressor, MAF sensor,
turbocharger boost solenoid, AAP & IAT
sensor.
32.Position air inlet hose to turbocharger and
tighten clip. 33.Connect hoses to turbocharger boost solenoid
and secure clips.
34.Clean CKP sensor and mating face.
CAUTION: If originally fitted: Fit spacer to
CKP sensor.
35.Using new 'O' ring, fit CKP sensor, tighten CKP
sensor bolt to 9 Nm (7 lbf.ft) and connect
multiplug.
36.Connect multiplug to EGR modulator.
37.Connect engine earth lead to battery earth lead
and tighten bolt.
38.Connect engine harness multiplug to ECM and
main harness.
39.Connect engine harness multiplugs to fuse
box.
40.Position glow plug lead to fusebox and secure
with bolt.
41.Position battery and alternator leads to fusebox
and secure with bolts.
42.Fit engine compartment fuse box cover.
43.Connect vacuum hose to EGR valve.
44.Connect hose to vacuum pump and secure
vacuum pipe to fuel cooler.
45.Disconnect fuel hose from connector block and
connect to fuel cooler.
46.Connect fuel hoses to fuel cooler and
connector block on cylinder head.
47.Position expansion tank, connect hose and
secure with clip. Secure tank to body mounting.
48.Connect coolant hoses to fuel cooler and
coolant rail and secure clips.
49.Fit turbocharger.
+ ENGINE MANAGEMENT SYSTEM -
Td5, REPAIRS, Turbocharger.
50. Fit radiator.
+ COOLING SYSTEM - Td5, REPAIRS,
Radiator.
51.Fill engine with oil.
+ MAINTENANCE, PROCEDURES,
Engine oil - diesel engine.
52.Fit underbelly panel.
+ EXTERIOR FITTINGS, REPAIRS,
Panel - underbelly.
53.Fit bonnet.
+ EXTERIOR FITTINGS, REPAIRS,
Bonnet.