ECU LAND ROVER DISCOVERY 2002 Workshop Manual
[x] Cancel search | Manufacturer: LAND ROVER, Model Year: 2002, Model line: DISCOVERY, Model: LAND ROVER DISCOVERY 2002Pages: 1672, PDF Size: 46.1 MB
Page 1042 of 1672
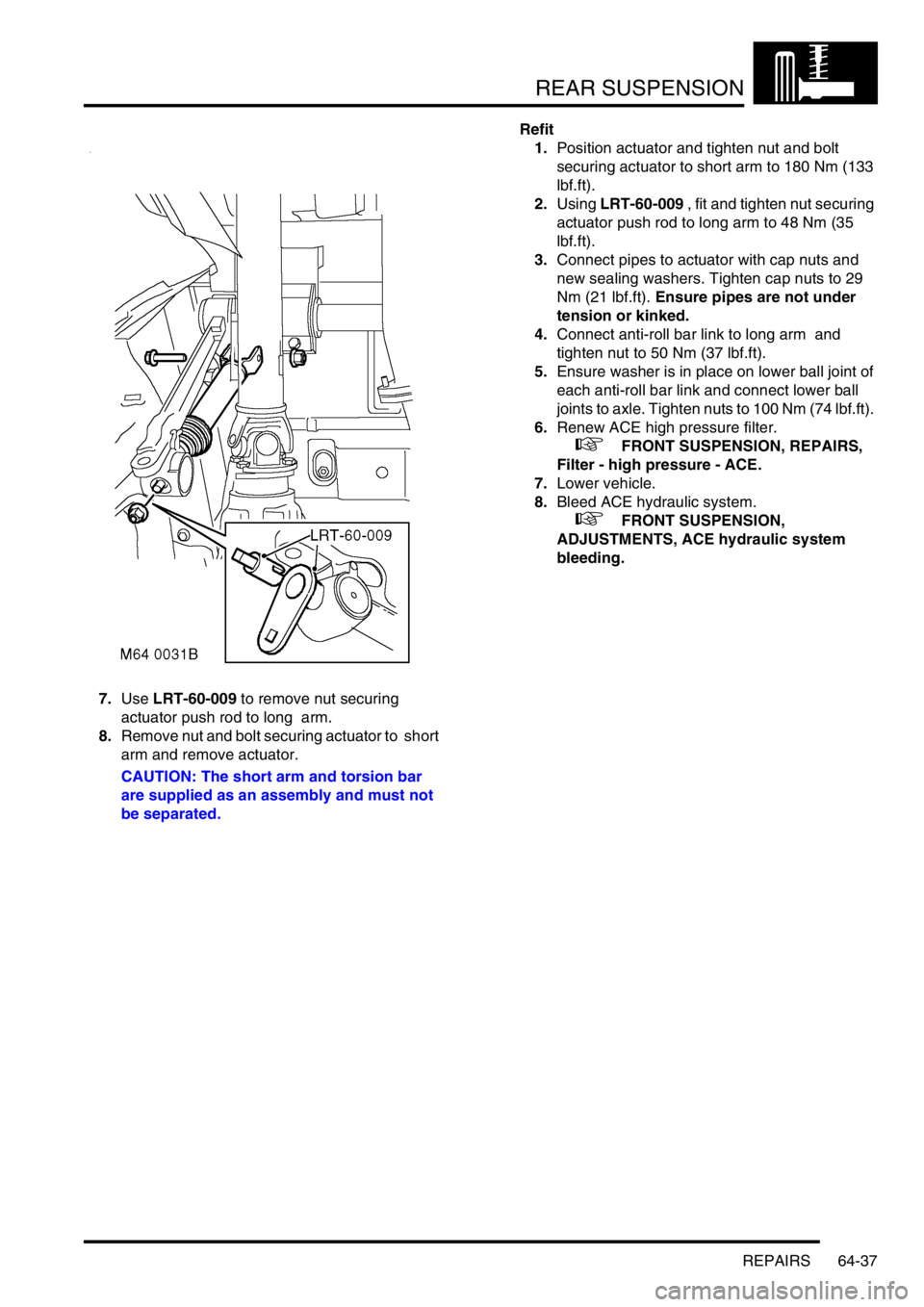
REAR SUSPENSION
REPAIRS 64-37
7.Use LRT-60-009 to remove nut securing
actuator push rod to long arm.
8.Remove nut and bolt securing actuator to short
arm and remove actuator.
CAUTION: The short arm and torsion bar
are supplied as an assembly and must not
be separated.Refit
1.Position actuator and tighten nut and bolt
securing actuator to short arm to 180 Nm (133
lbf.ft).
2.Using LRT-60-009 , fit and tighten nut securing
actuator push rod to long arm to 48 Nm (35
lbf.ft).
3.Connect pipes to actuator with cap nuts and
new sealing washers. Tighten cap nuts to 29
Nm (21 lbf.ft). Ensure pipes are not under
tension or kinked.
4.Connect anti-roll bar link to long arm and
tighten nut to 50 Nm (37 lbf.ft).
5.Ensure washer is in place on lower ball joint of
each anti-roll bar link and connect lower ball
joints to axle. Tighten nuts to 100 Nm (74 lbf.ft).
6.Renew ACE high pressure filter.
+ FRONT SUSPENSION, REPAIRS,
Filter - high pressure - ACE.
7.Lower vehicle.
8.Bleed ACE hydraulic system.
+ FRONT SUSPENSION,
ADJUSTMENTS, ACE hydraulic system
bleeding.
Page 1043 of 1672
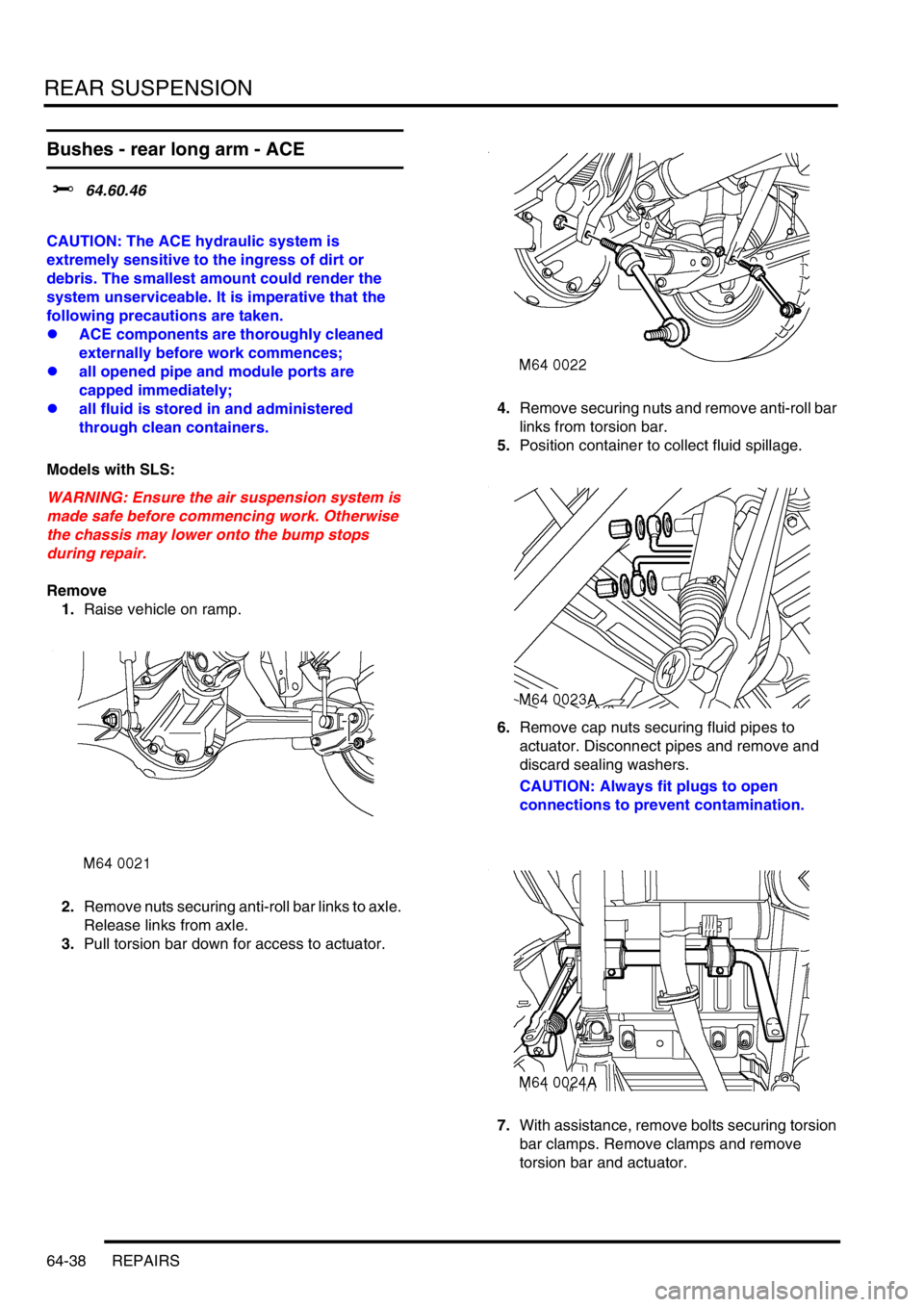
REAR SUSPENSION
64-38 REPAIRS
Bushes - rear long arm - ACE
$% 64.60.46
CAUTION: The ACE hydraulic system is
extremely sensitive to the ingress of dirt or
debris. The smallest amount could render the
system unserviceable. It is imperative that the
following precautions are taken.
lACE components are thoroughly cleaned
externally before work commences;
lall opened pipe and module ports are
capped immediately;
lall fluid is stored in and administered
through clean containers.
Models with SLS:
WARNING: Ensure the air suspension system is
made safe before commencing work. Otherwise
the chassis may lower onto the bump stops
during repair.
Remove
1.Raise vehicle on ramp.
2.Remove nuts securing anti-roll bar links to axle.
Release links from axle.
3.Pull torsion bar down for access to actuator.4.Remove securing nuts and remove anti-roll bar
links from torsion bar.
5.Position container to collect fluid spillage.
6.Remove cap nuts securing fluid pipes to
actuator. Disconnect pipes and remove and
discard sealing washers.
CAUTION: Always fit plugs to open
connections to prevent contamination.
7.With assistance, remove bolts securing torsion
bar clamps. Remove clamps and remove
torsion bar and actuator.
Page 1044 of 1672
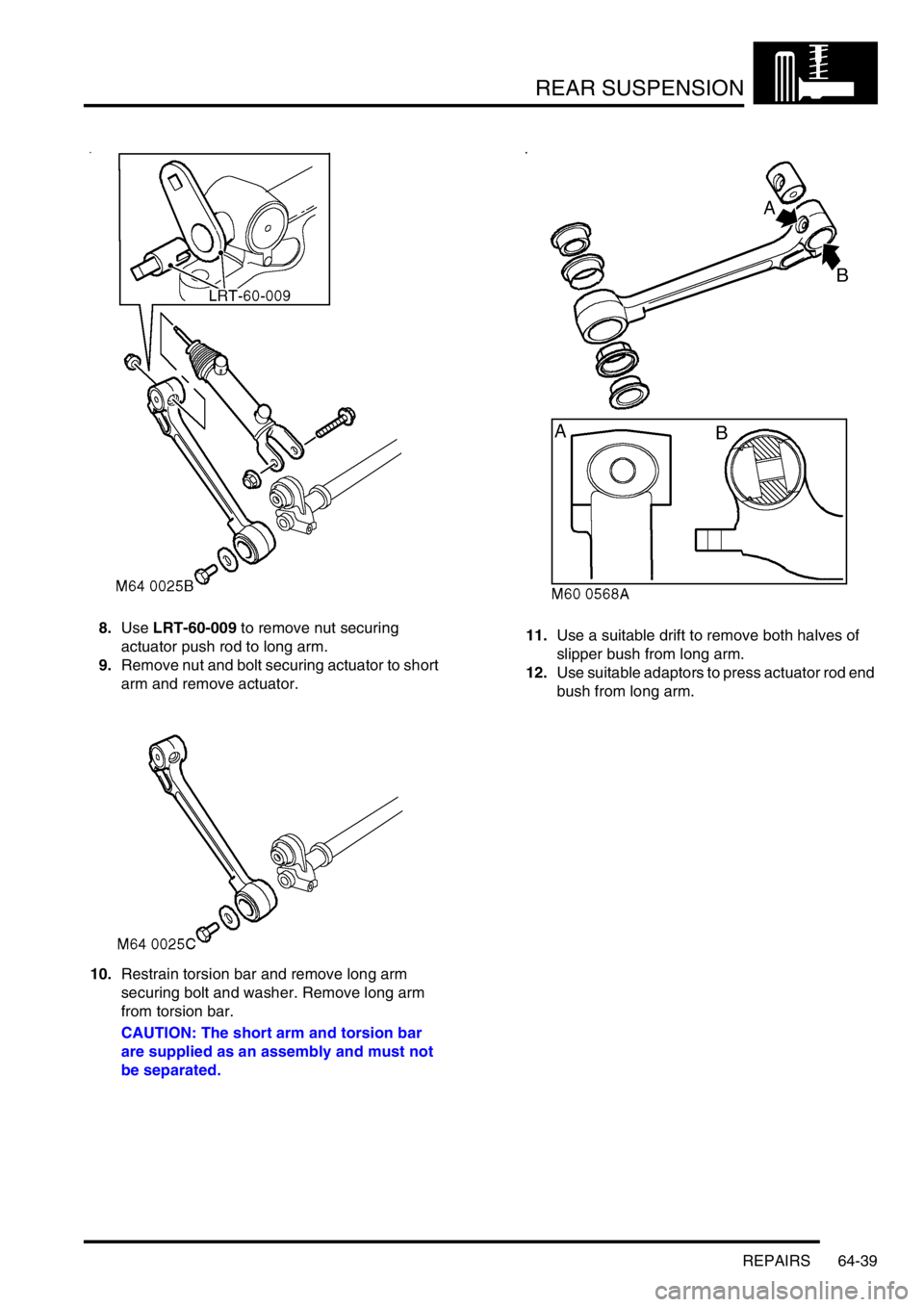
REAR SUSPENSION
REPAIRS 64-39
8.Use LRT-60-009 to remove nut securing
actuator push rod to long arm.
9.Remove nut and bolt securing actuator to short
arm and remove actuator.
10.Restrain torsion bar and remove long arm
securing bolt and washer. Remove long arm
from torsion bar.
CAUTION: The short arm and torsion bar
are supplied as an assembly and must not
be separated.11.Use a suitable drift to remove both halves of
slipper bush from long arm.
12.Use suitable adaptors to press actuator rod end
bush from long arm.
Page 1045 of 1672
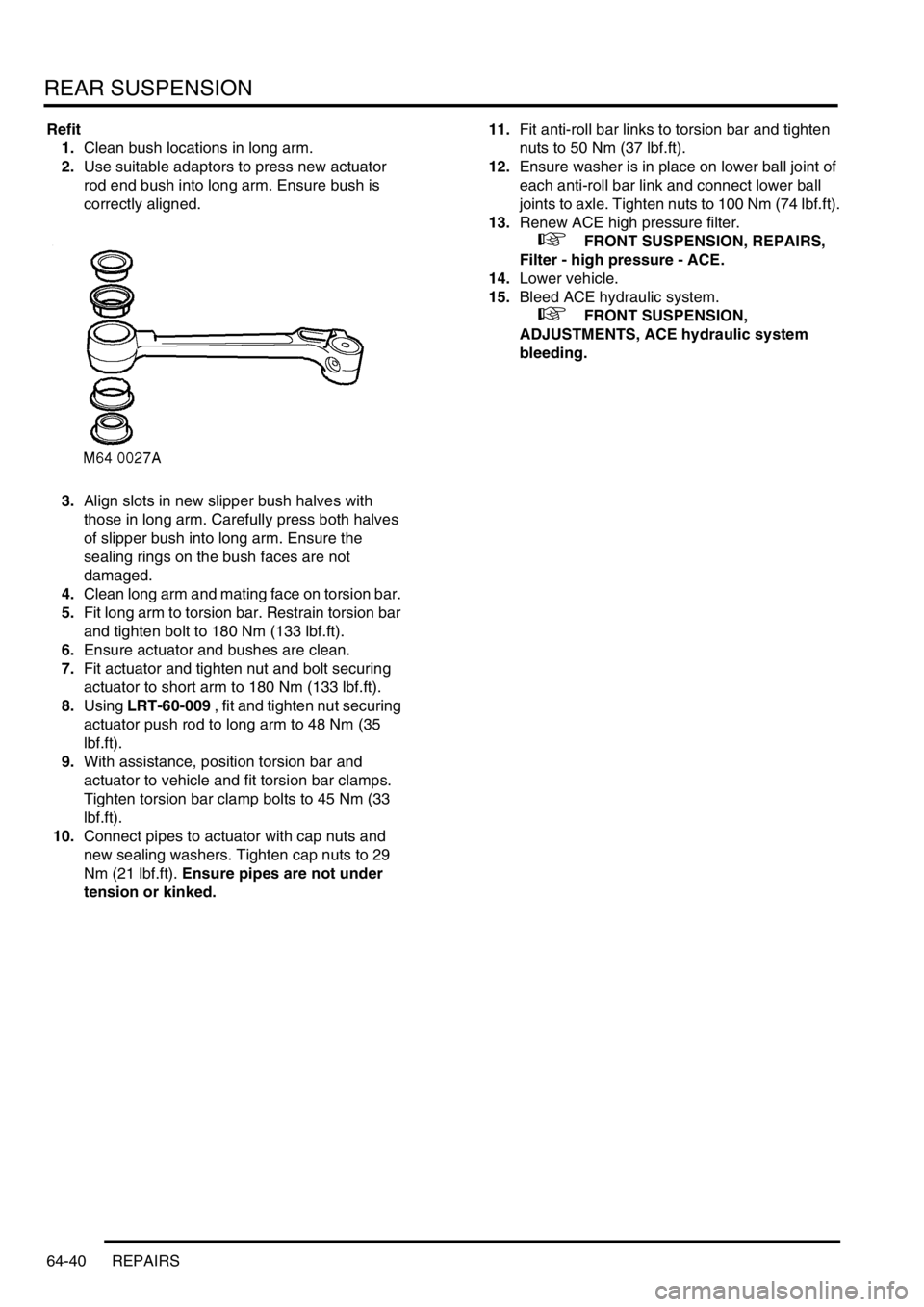
REAR SUSPENSION
64-40 REPAIRS
Refit
1.Clean bush locations in long arm.
2.Use suitable adaptors to press new actuator
rod end bush into long arm. Ensure bush is
correctly aligned.
3.Align slots in new slipper bush halves with
those in long arm. Carefully press both halves
of slipper bush into long arm. Ensure the
sealing rings on the bush faces are not
damaged.
4.Clean long arm and mating face on torsion bar.
5.Fit long arm to torsion bar. Restrain torsion bar
and tighten bolt to 180 Nm (133 lbf.ft).
6.Ensure actuator and bushes are clean.
7.Fit actuator and tighten nut and bolt securing
actuator to short arm to 180 Nm (133 lbf.ft).
8.Using LRT-60-009 , fit and tighten nut securing
actuator push rod to long arm to 48 Nm (35
lbf.ft).
9.With assistance, position torsion bar and
actuator to vehicle and fit torsion bar clamps.
Tighten torsion bar clamp bolts to 45 Nm (33
lbf.ft).
10.Connect pipes to actuator with cap nuts and
new sealing washers. Tighten cap nuts to 29
Nm (21 lbf.ft). Ensure pipes are not under
tension or kinked.11.Fit anti-roll bar links to torsion bar and tighten
nuts to 50 Nm (37 lbf.ft).
12.Ensure washer is in place on lower ball joint of
each anti-roll bar link and connect lower ball
joints to axle. Tighten nuts to 100 Nm (74 lbf.ft).
13.Renew ACE high pressure filter.
+ FRONT SUSPENSION, REPAIRS,
Filter - high pressure - ACE.
14.Lower vehicle.
15.Bleed ACE hydraulic system.
+ FRONT SUSPENSION,
ADJUSTMENTS, ACE hydraulic system
bleeding.
Page 1046 of 1672
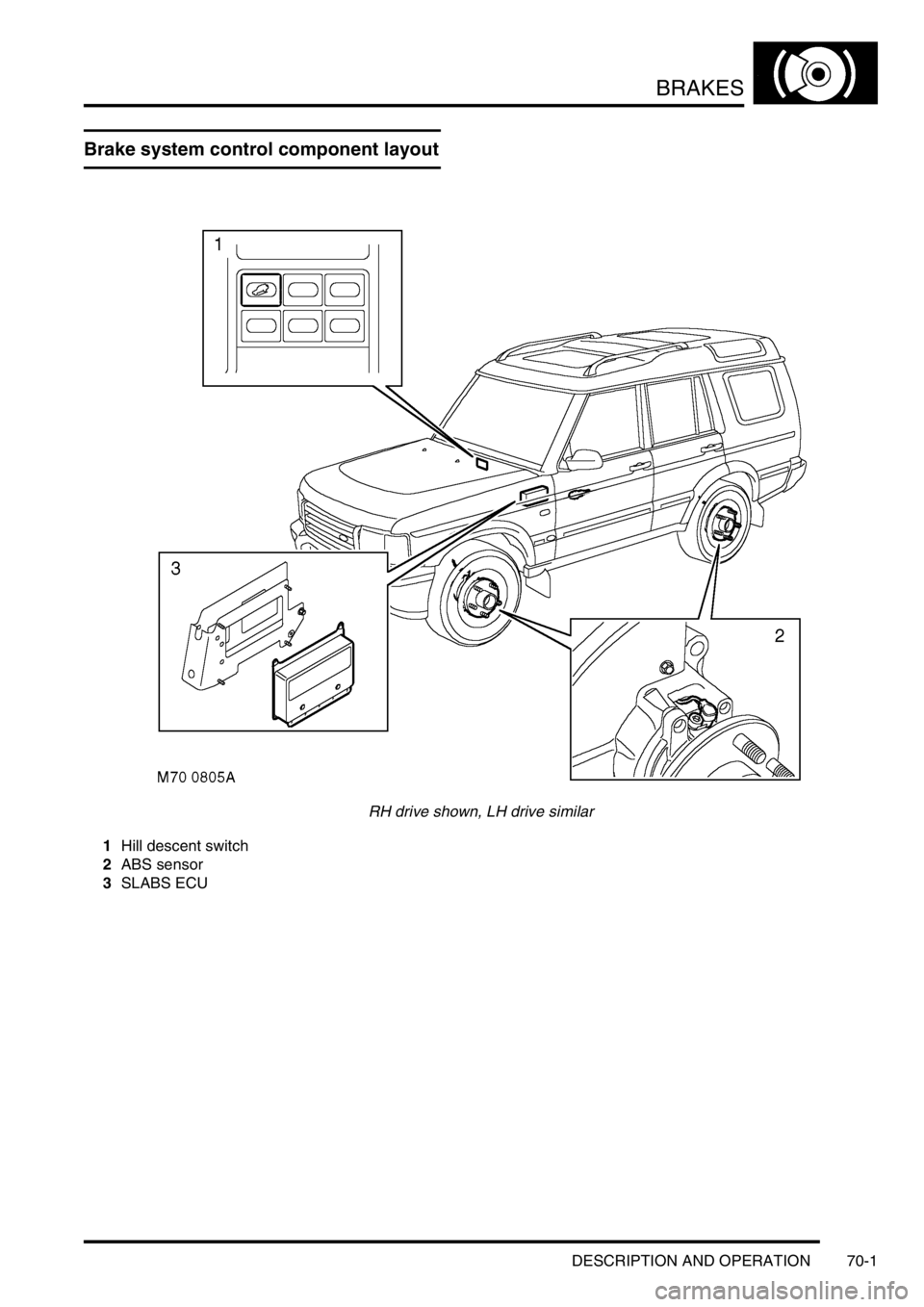
BRAKES
DESCRIPTION AND OPERATION 70-1
BRAKES DESCRIPTION AND OPERAT ION
Brake system control component layout
RH drive shown, LH drive similar
1Hill descent switch
2ABS sensor
3SLABS ECU
Page 1048 of 1672
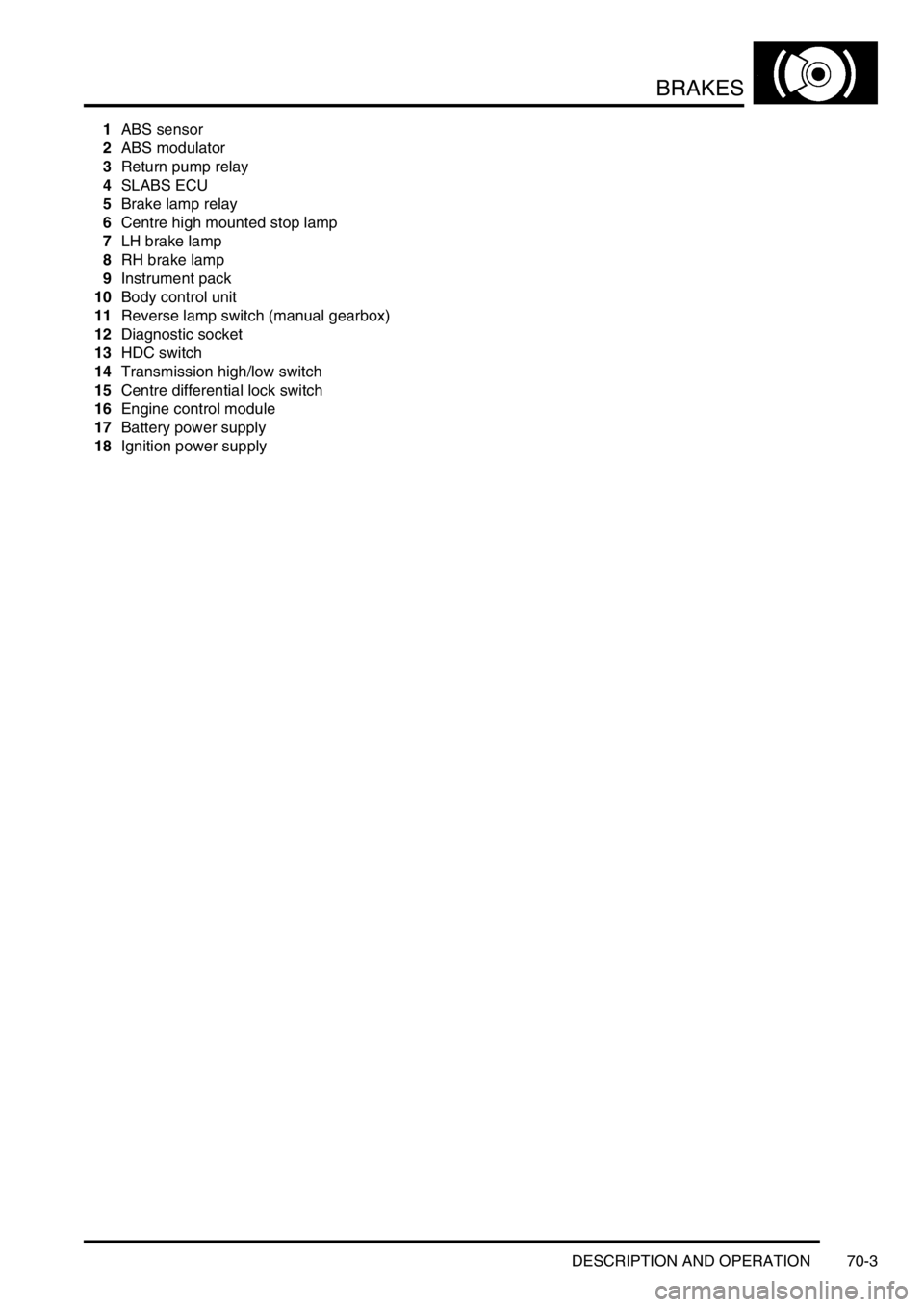
BRAKES
DESCRIPTION AND OPERATION 70-3
1ABS sensor
2ABS modulator
3Return pump relay
4SLABS ECU
5Brake lamp relay
6Centre high mounted stop lamp
7LH brake lamp
8RH brake lamp
9Instrument pack
10Body control unit
11Reverse lamp switch (manual gearbox)
12Diagnostic socket
13HDC switch
14Transmission high/low switch
15Centre differential lock switch
16Engine control module
17Battery power supply
18Ignition power supply
Page 1051 of 1672
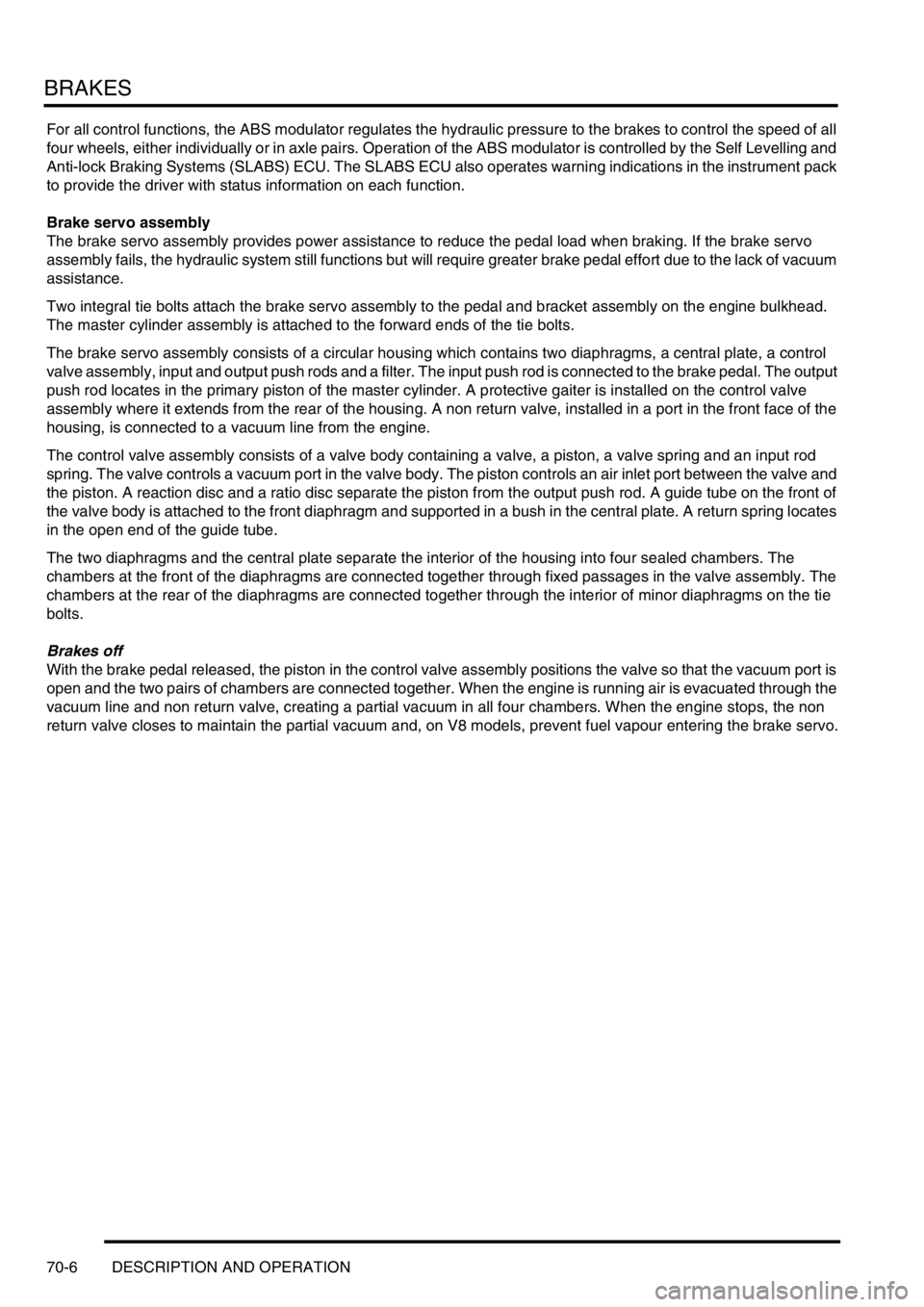
BRAKES
70-6 DESCRIPTION AND OPERATION
For all control functions, the ABS modulator regulates the hydraulic pressure to the brakes to control the speed of all
four wheels, either individually or in axle pairs. Operation of the ABS modulator is controlled by the Self Levelling and
Anti-lock Braking Systems (SLABS) ECU. The SLABS ECU also operates warning indications in the instrument pack
to provide the driver with status information on each function.
Brake servo assembly
The brake servo assembly provides power assistance to reduce the pedal load when braking. If the brake servo
assembly fails, the hydraulic system still functions but will require greater brake pedal effort due to the lack of vacuum
assistance.
Two integral tie bolts attach the brake servo assembly to the pedal and bracket assembly on the engine bulkhead.
The master cylinder assembly is attached to the forward ends of the tie bolts.
The brake servo assembly consists of a circular housing which contains two diaphragms, a central plate, a control
valve assembly, input and output push rods and a filter. The input push rod is connected to the brake pedal. The output
push rod locates in the primary piston of the master cylinder. A protective gaiter is installed on the control valve
assembly where it extends from the rear of the housing. A non return valve, installed in a port in the front face of the
housing, is connected to a vacuum line from the engine.
The control valve assembly consists of a valve body containing a valve, a piston, a valve spring and an input rod
spring. The valve controls a vacuum port in the valve body. The piston controls an air inlet port between the valve and
the piston. A reaction disc and a ratio disc separate the piston from the output push rod. A guide tube on the front of
the valve body is attached to the front diaphragm and supported in a bush in the central plate. A return spring locates
in the open end of the guide tube.
The two diaphragms and the central plate separate the interior of the housing into four sealed chambers. The
chambers at the front of the diaphragms are connected together through fixed passages in the valve assembly. The
chambers at the rear of the diaphragms are connected together through the interior of minor diaphragms on the tie
bolts.
Brakes off
With the brake pedal released, the piston in the control valve assembly positions the valve so that the vacuum port is
open and the two pairs of chambers are connected together. When the engine is running air is evacuated through the
vacuum line and non return valve, creating a partial vacuum in all four chambers. When the engine stops, the non
return valve closes to maintain the partial vacuum and, on V8 models, prevent fuel vapour entering the brake servo.
Page 1059 of 1672
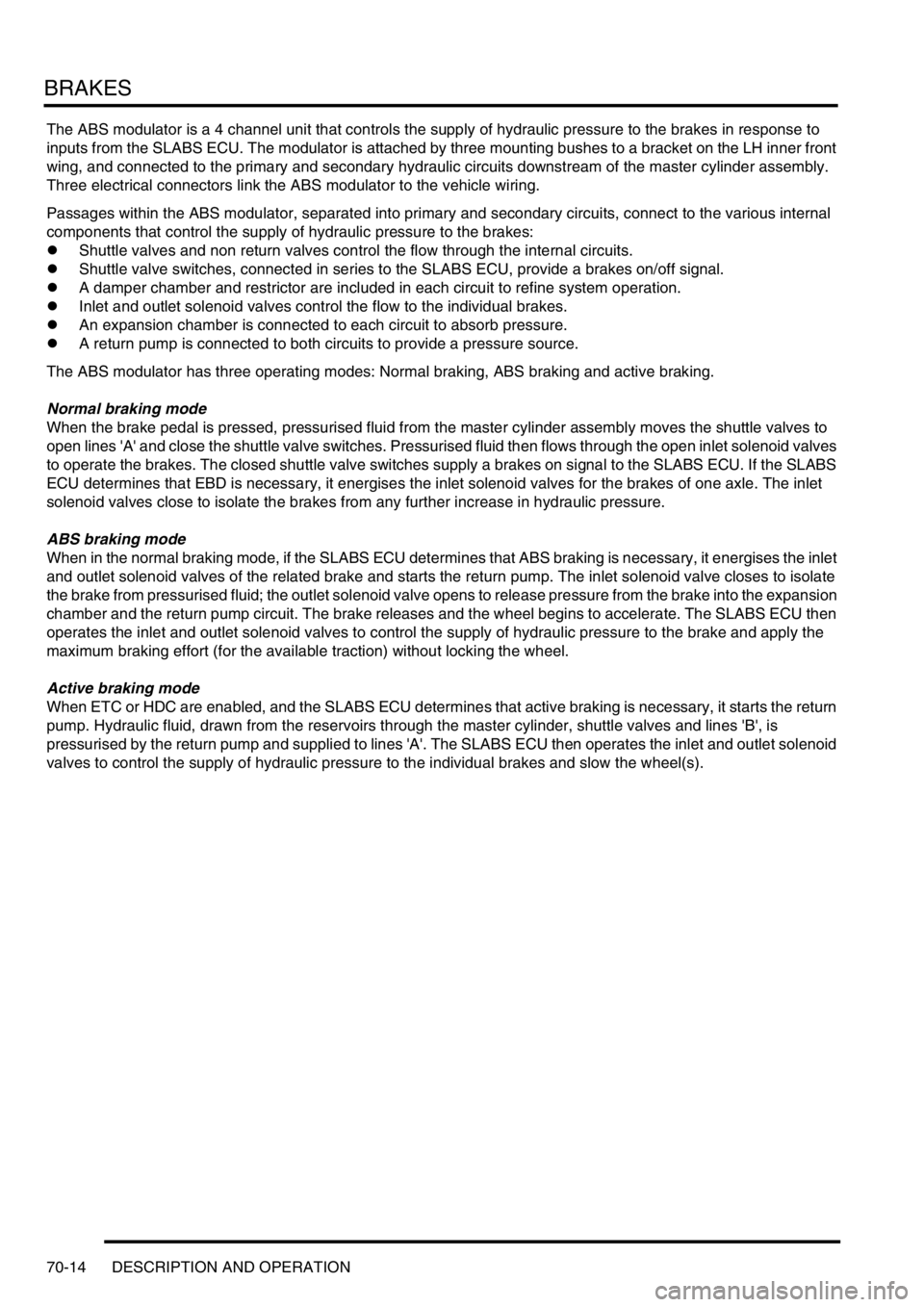
BRAKES
70-14 DESCRIPTION AND OPERATION
The ABS modulator is a 4 channel unit that controls the supply of hydraulic pressure to the brakes in response to
inputs from the SLABS ECU. The modulator is attached by three mounting bushes to a bracket on the LH inner front
wing, and connected to the primary and secondary hydraulic circuits downstream of the master cylinder assembly.
Three electrical connectors link the ABS modulator to the vehicle wiring.
Passages within the ABS modulator, separated into primary and secondary circuits, connect to the various internal
components that control the supply of hydraulic pressure to the brakes:
lShuttle valves and non return valves control the flow through the internal circuits.
lShuttle valve switches, connected in series to the SLABS ECU, provide a brakes on/off signal.
lA damper chamber and restrictor are included in each circuit to refine system operation.
lInlet and outlet solenoid valves control the flow to the individual brakes.
lAn expansion chamber is connected to each circuit to absorb pressure.
lA return pump is connected to both circuits to provide a pressure source.
The ABS modulator has three operating modes: Normal braking, ABS braking and active braking.
Normal braking mode
When the brake pedal is pressed, pressurised fluid from the master cylinder assembly moves the shuttle valves to
open lines 'A' and close the shuttle valve switches. Pressurised fluid then flows through the open inlet solenoid valves
to operate the brakes. The closed shuttle valve switches supply a brakes on signal to the SLABS ECU. If the SLABS
ECU determines that EBD is necessary, it energises the inlet solenoid valves for the brakes of one axle. The inlet
solenoid valves close to isolate the brakes from any further increase in hydraulic pressure.
ABS braking mode
When in the normal braking mode, if the SLABS ECU determines that ABS braking is necessary, it energises the inlet
and outlet solenoid valves of the related brake and starts the return pump. The inlet solenoid valve closes to isolate
the brake from pressurised fluid; the outlet solenoid valve opens to release pressure from the brake into the expansion
chamber and the return pump circuit. The brake releases and the wheel begins to accelerate. The SLABS ECU then
operates the inlet and outlet solenoid valves to control the supply of hydraulic pressure to the brake and apply the
maximum braking effort (for the available traction) without locking the wheel.
Active braking mode
When ETC or HDC are enabled, and the SLABS ECU determines that active braking is necessary, it starts the return
pump. Hydraulic fluid, drawn from the reservoirs through the master cylinder, shuttle valves and lines 'B', is
pressurised by the return pump and supplied to lines 'A'. The SLABS ECU then operates the inlet and outlet solenoid
valves to control the supply of hydraulic pressure to the individual brakes and slow the wheel(s).
Page 1062 of 1672
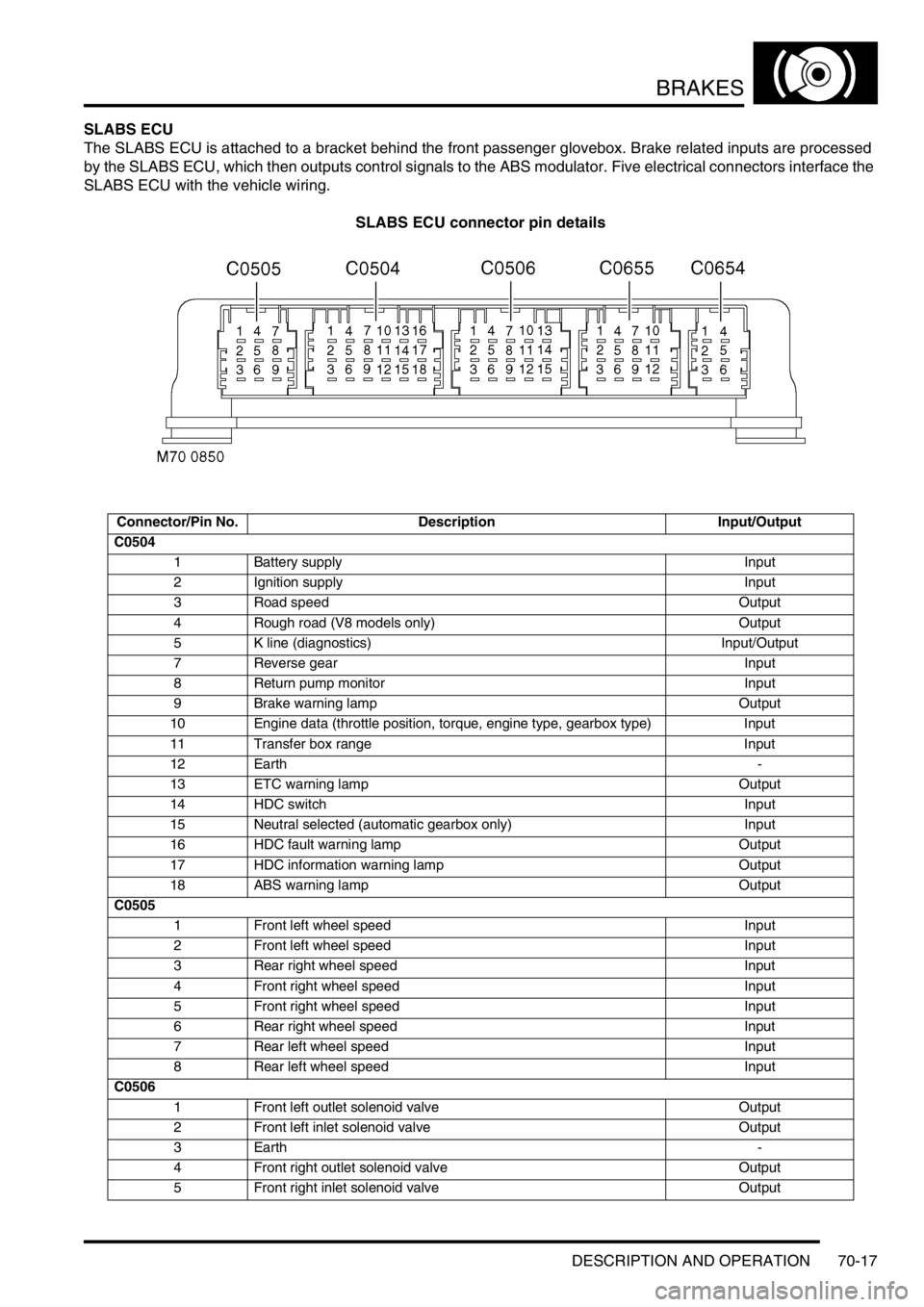
BRAKES
DESCRIPTION AND OPERATION 70-17
SLABS ECU
The SLABS ECU is attached to a bracket behind the front passenger glovebox. Brake related inputs are processed
by the SLABS ECU, which then outputs control signals to the ABS modulator. Five electrical connectors interface the
SLABS ECU with the vehicle wiring.
SLABS ECU connector pin details
Connector/Pin No. Description Input/Output
C0504
1 Battery supply Input
2 Ignition supply Input
3 Road speed Output
4 Rough road (V8 models only) Output
5 K line (diagnostics) Input/Output
7 Reverse gear Input
8 Return pump monitor Input
9 Brake warning lamp Output
10 Engine data (throttle position, torque, engine type, gearbox type) Input
11 Transfer box range Input
12 Earth-
13 ETC warning lamp Output
14 HDC switch Input
15 Neutral selected (automatic gearbox only) Input
16 HDC fault warning lamp Output
17 HDC information warning lamp Output
18 ABS warning lamp Output
C0505
1 Front left wheel speed Input
2 Front left wheel speed Input
3 Rear right wheel speed Input
4 Front right wheel speed Input
5 Front right wheel speed Input
6 Rear right wheel speed Input
7 Rear left wheel speed Input
8 Rear left wheel speed Input
C0506
1 Front left outlet solenoid valve Output
2 Front left inlet solenoid valve Output
3Earth-
4 Front right outlet solenoid valve Output
5 Front right inlet solenoid valve Output
Page 1063 of 1672
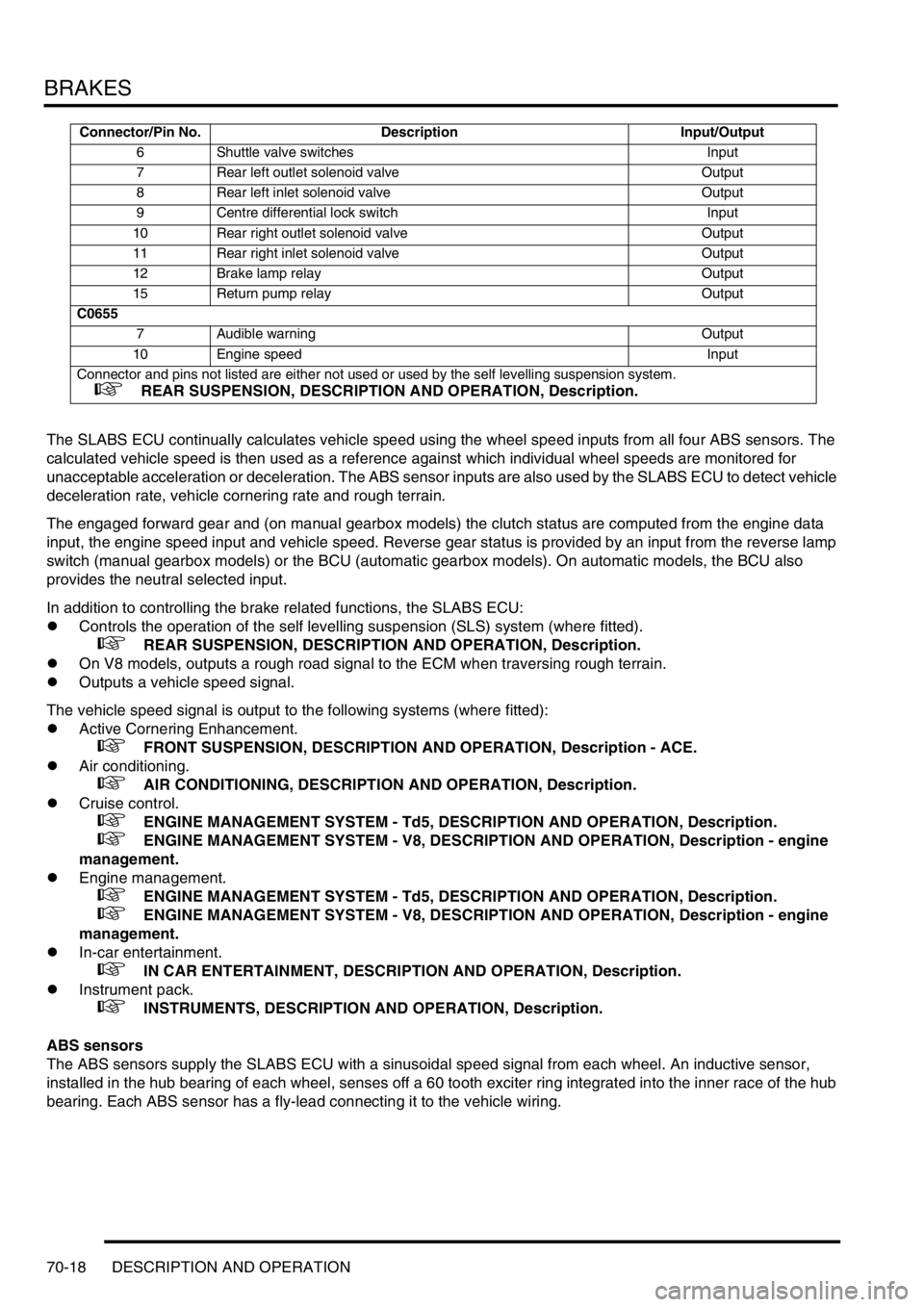
BRAKES
70-18 DESCRIPTION AND OPERATION
The SLABS ECU continually calculates vehicle speed using the wheel speed inputs from all four ABS sensors. The
calculated vehicle speed is then used as a reference against which individual wheel speeds are monitored for
unacceptable acceleration or deceleration. The ABS sensor inputs are also used by the SLABS ECU to detect vehicle
deceleration rate, vehicle cornering rate and rough terrain.
The engaged forward gear and (on manual gearbox models) the clutch status are computed from the engine data
input, the engine speed input and vehicle speed. Reverse gear status is provided by an input from the reverse lamp
switch (manual gearbox models) or the BCU (automatic gearbox models). On automatic models, the BCU also
provides the neutral selected input.
In addition to controlling the brake related functions, the SLABS ECU:
lControls the operation of the self levelling suspension (SLS) system (where fitted).
+ REAR SUSPENSION, DESCRIPTION AND OPERATION, Description.
lOn V8 models, outputs a rough road signal to the ECM when traversing rough terrain.
lOutputs a vehicle speed signal.
The vehicle speed signal is output to the following systems (where fitted):
lActive Cornering Enhancement.
+ FRONT SUSPENSION, DESCRIPTION AND OPERATION, Description - ACE.
lAir conditioning.
+ AIR CONDITIONING, DESCRIPTION AND OPERATION, Description.
lCruise control.
+ ENGINE MANAGEMENT SYSTEM - Td5, DESCRIPTION AND OPERATION, Description.
+ ENGINE MANAGEMENT SYSTEM - V8, DESCRIPTION AND OPERATION, Description - engine
management.
lEngine management.
+ ENGINE MANAGEMENT SYSTEM - Td5, DESCRIPTION AND OPERATION, Description.
+ ENGINE MANAGEMENT SYSTEM - V8, DESCRIPTION AND OPERATION, Description - engine
management.
lIn-car entertainment.
+ IN CAR ENTERTAINMENT, DESCRIPTION AND OPERATION, Description.
lInstrument pack.
+ INSTRUMENTS, DESCRIPTION AND OPERATION, Description.
ABS sensors
The ABS sensors supply the SLABS ECU with a sinusoidal speed signal from each wheel. An inductive sensor,
installed in the hub bearing of each wheel, senses off a 60 tooth exciter ring integrated into the inner race of the hub
bearing. Each ABS sensor has a fly-lead connecting it to the vehicle wiring.
6 Shuttle valve switches Input
7 Rear left outlet solenoid valve Output
8 Rear left inlet solenoid valve Output
9 Centre differential lock switch Input
10 Rear right outlet solenoid valve Output
11 Rear right inlet solenoid valve Output
12 Brake lamp relay Output
15 Return pump relay Output
C0655
7 Audible warning Output
10 Engine speed Input
Connector and pins not listed are either not used or used by the self levelling suspension system.
+ REAR SUSPENSION, DESCRIPTION AND OPERATION, Description.
Connector/Pin No. Description Input/Output