ESP LAND ROVER DISCOVERY 2002 Repair Manual
[x] Cancel search | Manufacturer: LAND ROVER, Model Year: 2002, Model line: DISCOVERY, Model: LAND ROVER DISCOVERY 2002Pages: 1672, PDF Size: 46.1 MB
Page 804 of 1672
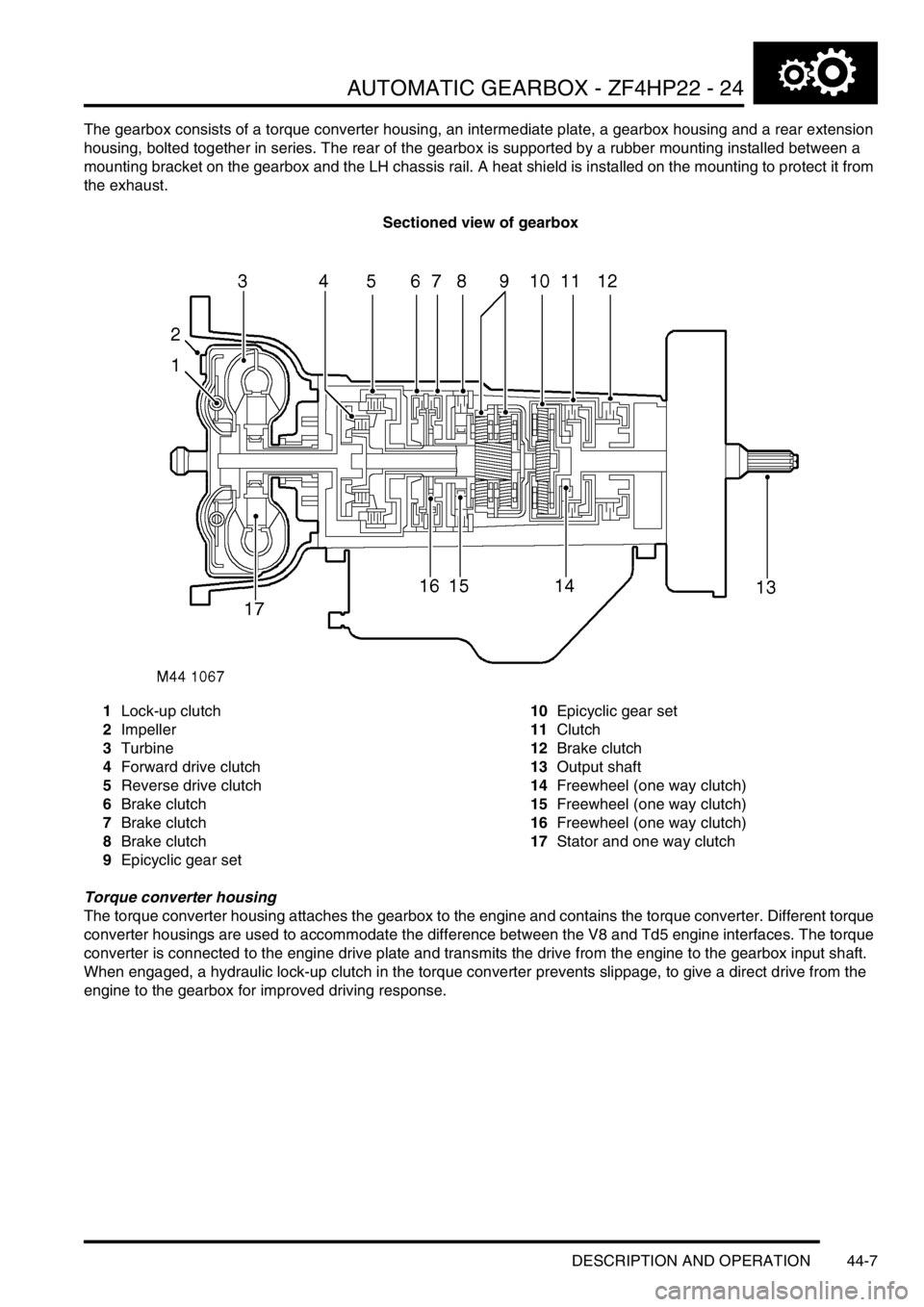
AUTOMATIC GEARBOX - ZF4HP22 - 24
DESCRIPTION AND OPERATION 44-7
The gearbox consists of a torque converter housing, an intermediate plate, a gearbox housing and a rear extension
housing, bolted together in series. The rear of the gearbox is supported by a rubber mounting installed between a
mounting bracket on the gearbox and the LH chassis rail. A heat shield is installed on the mounting to protect it from
the exhaust.
Sectioned view of gearbox
1Lock-up clutch
2Impeller
3Turbine
4Forward drive clutch
5Reverse drive clutch
6Brake clutch
7Brake clutch
8Brake clutch
9Epicyclic gear set10Epicyclic gear set
11Clutch
12Brake clutch
13Output shaft
14Freewheel (one way clutch)
15Freewheel (one way clutch)
16Freewheel (one way clutch)
17Stator and one way clutch
Torque converter housing
The torque converter housing attaches the gearbox to the engine and contains the torque converter. Different torque
converter housings are used to accommodate the difference between the V8 and Td5 engine interfaces. The torque
converter is connected to the engine drive plate and transmits the drive from the engine to the gearbox input shaft.
When engaged, a hydraulic lock-up clutch in the torque converter prevents slippage, to give a direct drive from the
engine to the gearbox for improved driving response.
Page 814 of 1672
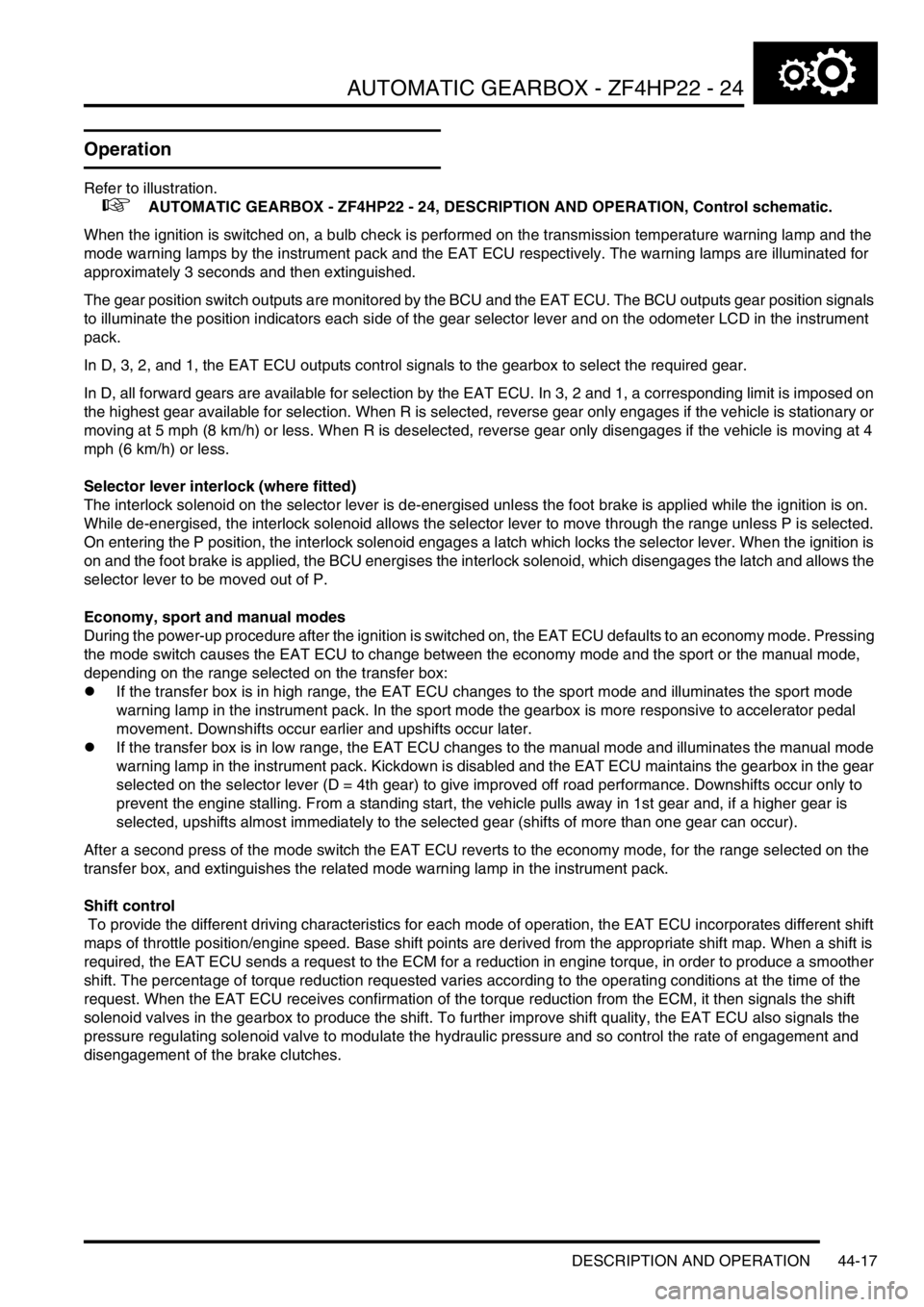
AUTOMATIC GEARBOX - ZF4HP22 - 24
DESCRIPTION AND OPERATION 44-17
Operation
Refer to illustration.
+ AUTOMATIC GEARBOX - ZF4HP22 - 24, DESCRIPTION AND OPERATION, Control schematic.
When the ignition is switched on, a bulb check is performed on the transmission temperature warning lamp and the
mode warning lamps by the instrument pack and the EAT ECU respectively. The warning lamps are illuminated for
approximately 3 seconds and then extinguished.
The gear position switch outputs are monitored by the BCU and the EAT ECU. The BCU outputs gear position signals
to illuminate the position indicators each side of the gear selector lever and on the odometer LCD in the instrument
pack.
In D, 3, 2, and 1, the EAT ECU outputs control signals to the gearbox to select the required gear.
In D, all forward gears are available for selection by the EAT ECU. In 3, 2 and 1, a corresponding limit is imposed on
the highest gear available for selection. When R is selected, reverse gear only engages if the vehicle is stationary or
moving at 5 mph (8 km/h) or less. When R is deselected, reverse gear only disengages if the vehicle is moving at 4
mph (6 km/h) or less.
Selector lever interlock (where fitted)
The interlock solenoid on the selector lever is de-energised unless the foot brake is applied while the ignition is on.
While de-energised, the interlock solenoid allows the selector lever to move through the range unless P is selected.
On entering the P position, the interlock solenoid engages a latch which locks the selector lever. When the ignition is
on and the foot brake is applied, the BCU energises the interlock solenoid, which disengages the latch and allows the
selector lever to be moved out of P.
Economy, sport and manual modes
During the power-up procedure after the ignition is switched on, the EAT ECU defaults to an economy mode. Pressing
the mode switch causes the EAT ECU to change between the economy mode and the sport or the manual mode,
depending on the range selected on the transfer box:
lIf the transfer box is in high range, the EAT ECU changes to the sport mode and illuminates the sport mode
warning lamp in the instrument pack. In the sport mode the gearbox is more responsive to accelerator pedal
movement. Downshifts occur earlier and upshifts occur later.
lIf the transfer box is in low range, the EAT ECU changes to the manual mode and illuminates the manual mode
warning lamp in the instrument pack. Kickdown is disabled and the EAT ECU maintains the gearbox in the gear
selected on the selector lever (D = 4th gear) to give improved off road performance. Downshifts occur only to
prevent the engine stalling. From a standing start, the vehicle pulls away in 1st gear and, if a higher gear is
selected, upshifts almost immediately to the selected gear (shifts of more than one gear can occur).
After a second press of the mode switch the EAT ECU reverts to the economy mode, for the range selected on the
transfer box, and extinguishes the related mode warning lamp in the instrument pack.
Shift control
To provide the different driving characteristics for each mode of operation, the EAT ECU incorporates different shift
maps of throttle position/engine speed. Base shift points are derived from the appropriate shift map. When a shift is
required, the EAT ECU sends a request to the ECM for a reduction in engine torque, in order to produce a smoother
shift. The percentage of torque reduction requested varies according to the operating conditions at the time of the
request. When the EAT ECU receives confirmation of the torque reduction from the ECM, it then signals the shift
solenoid valves in the gearbox to produce the shift. To further improve shift quality, the EAT ECU also signals the
pressure regulating solenoid valve to modulate the hydraulic pressure and so control the rate of engagement and
disengagement of the brake clutches.
Page 858 of 1672
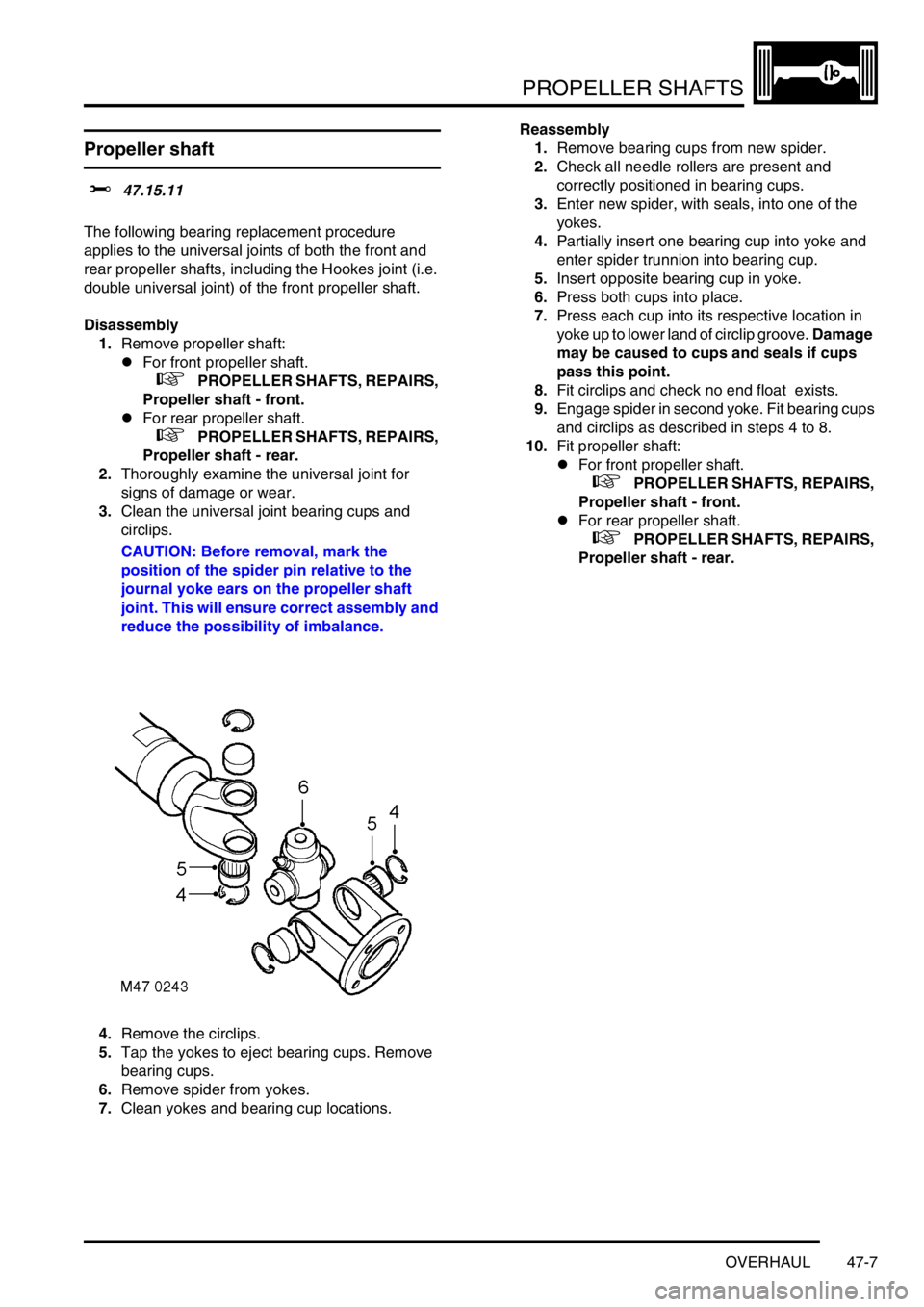
PROPELLER SHAFTS
OVERHAUL 47-7
OVERHAUL
Propeller shaft
$% 47.15.11
The following bearing replacement procedure
applies to the universal joints of both the front and
rear propeller shafts, including the Hookes joint (i.e.
double universal joint) of the front propeller shaft.
Disassembly
1.Remove propeller shaft:
lFor front propeller shaft.
+ PROPELLER SHAFTS, REPAIRS,
Propeller shaft - front.
lFor rear propeller shaft.
+ PROPELLER SHAFTS, REPAIRS,
Propeller shaft - rear.
2.Thoroughly examine the universal joint for
signs of damage or wear.
3.Clean the universal joint bearing cups and
circlips.
CAUTION: Before removal, mark the
position of the spider pin relative to the
journal yoke ears on the propeller shaft
joint. This will ensure correct assembly and
reduce the possibility of imbalance.
4.Remove the circlips.
5.Tap the yokes to eject bearing cups. Remove
bearing cups.
6.Remove spider from yokes.
7.Clean yokes and bearing cup locations. Reassembly
1.Remove bearing cups from new spider.
2.Check all needle rollers are present and
correctly positioned in bearing cups.
3.Enter new spider, with seals, into one of the
yokes.
4.Partially insert one bearing cup into yoke and
enter spider trunnion into bearing cup.
5.Insert opposite bearing cup in yoke.
6.Press both cups into place.
7.Press each cup into its respective location in
yoke up to lower land of circlip groove. Damage
may be caused to cups and seals if cups
pass this point.
8.Fit circlips and check no end float exists.
9.Engage spider in second yoke. Fit bearing cups
and circlips as described in steps 4 to 8.
10.Fit propeller shaft:
lFor front propeller shaft.
+ PROPELLER SHAFTS, REPAIRS,
Propeller shaft - front.
lFor rear propeller shaft.
+ PROPELLER SHAFTS, REPAIRS,
Propeller shaft - rear.
Page 943 of 1672
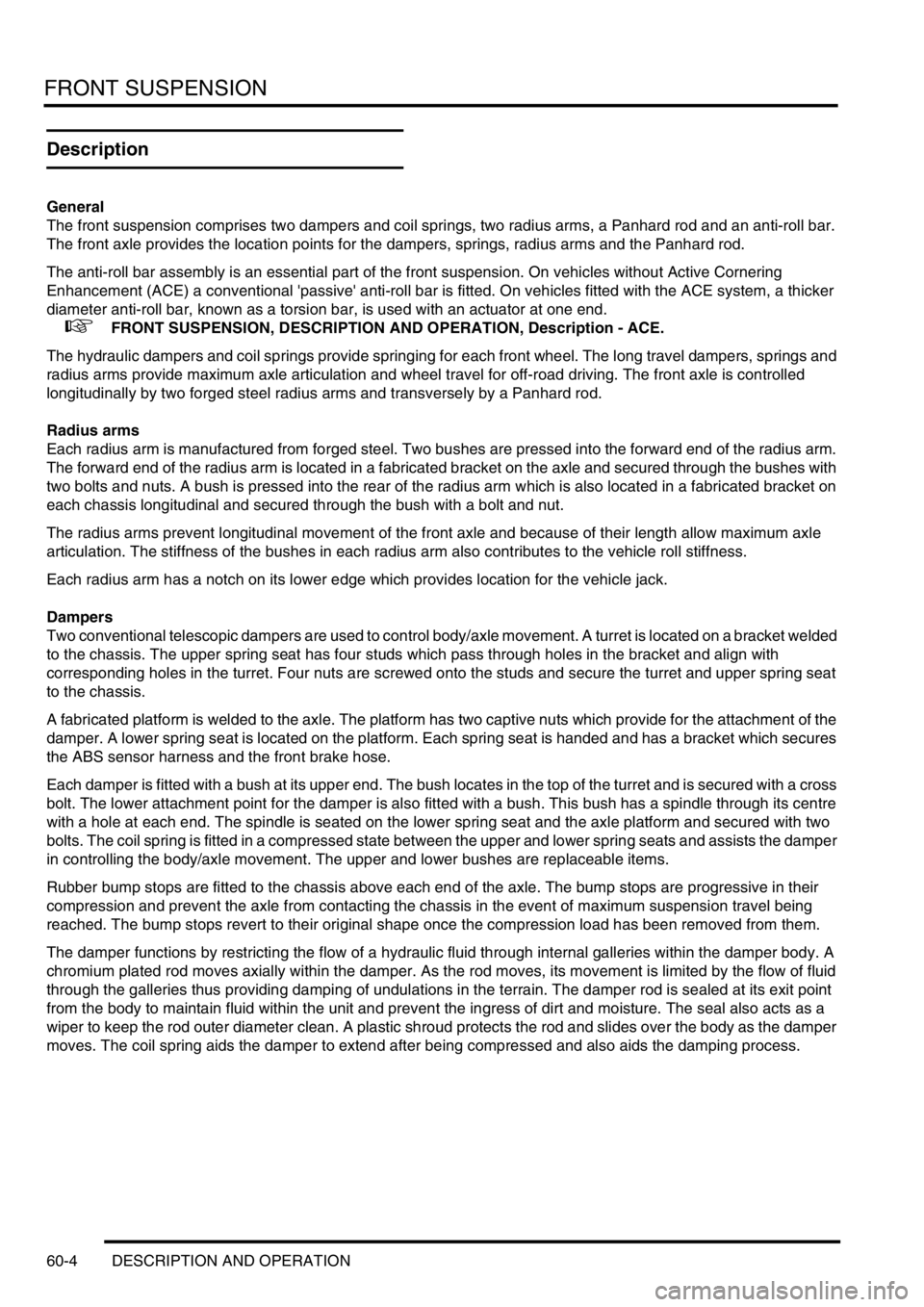
FRONT SUSPENSION
60-4 DESCRIPTION AND OPERATION
Description
General
The front suspension comprises two dampers and coil springs, two radius arms, a Panhard rod and an anti-roll bar.
The front axle provides the location points for the dampers, springs, radius arms and the Panhard rod.
The anti-roll bar assembly is an essential part of the front suspension. On vehicles without Active Cornering
Enhancement (ACE) a conventional 'passive' anti-roll bar is fitted. On vehicles fitted with the ACE system, a thicker
diameter anti-roll bar, known as a torsion bar, is used with an actuator at one end.
+ FRONT SUSPENSION, DESCRIPTION AND OPERATION, Description - ACE.
The hydraulic dampers and coil springs provide springing for each front wheel. The long travel dampers, springs and
radius arms provide maximum axle articulation and wheel travel for off-road driving. The front axle is controlled
longitudinally by two forged steel radius arms and transversely by a Panhard rod.
Radius arms
Each radius arm is manufactured from forged steel. Two bushes are pressed into the forward end of the radius arm.
The forward end of the radius arm is located in a fabricated bracket on the axle and secured through the bushes with
two bolts and nuts. A bush is pressed into the rear of the radius arm which is also located in a fabricated bracket on
each chassis longitudinal and secured through the bush with a bolt and nut.
The radius arms prevent longitudinal movement of the front axle and because of their length allow maximum axle
articulation. The stiffness of the bushes in each radius arm also contributes to the vehicle roll stiffness.
Each radius arm has a notch on its lower edge which provides location for the vehicle jack.
Dampers
Two conventional telescopic dampers are used to control body/axle movement. A turret is located on a bracket welded
to the chassis. The upper spring seat has four studs which pass through holes in the bracket and align with
corresponding holes in the turret. Four nuts are screwed onto the studs and secure the turret and upper spring seat
to the chassis.
A fabricated platform is welded to the axle. The platform has two captive nuts which provide for the attachment of the
damper. A lower spring seat is located on the platform. Each spring seat is handed and has a bracket which secures
the ABS sensor harness and the front brake hose.
Each damper is fitted with a bush at its upper end. The bush locates in the top of the turret and is secured with a cross
bolt. The lower attachment point for the damper is also fitted with a bush. This bush has a spindle through its centre
with a hole at each end. The spindle is seated on the lower spring seat and the axle platform and secured with two
bolts. The coil spring is fitted in a compressed state between the upper and lower spring seats and assists the damper
in controlling the body/axle movement. The upper and lower bushes are replaceable items.
Rubber bump stops are fitted to the chassis above each end of the axle. The bump stops are progressive in their
compression and prevent the axle from contacting the chassis in the event of maximum suspension travel being
reached. The bump stops revert to their original shape once the compression load has been removed from them.
The damper functions by restricting the flow of a hydraulic fluid through internal galleries within the damper body. A
chromium plated rod moves axially within the damper. As the rod moves, its movement is limited by the flow of fluid
through the galleries thus providing damping of undulations in the terrain. The damper rod is sealed at its exit point
from the body to maintain fluid within the unit and prevent the ingress of dirt and moisture. The seal also acts as a
wiper to keep the rod outer diameter clean. A plastic shroud protects the rod and slides over the body as the damper
moves. The coil spring aids the damper to extend after being compressed and also aids the damping process.
Page 951 of 1672
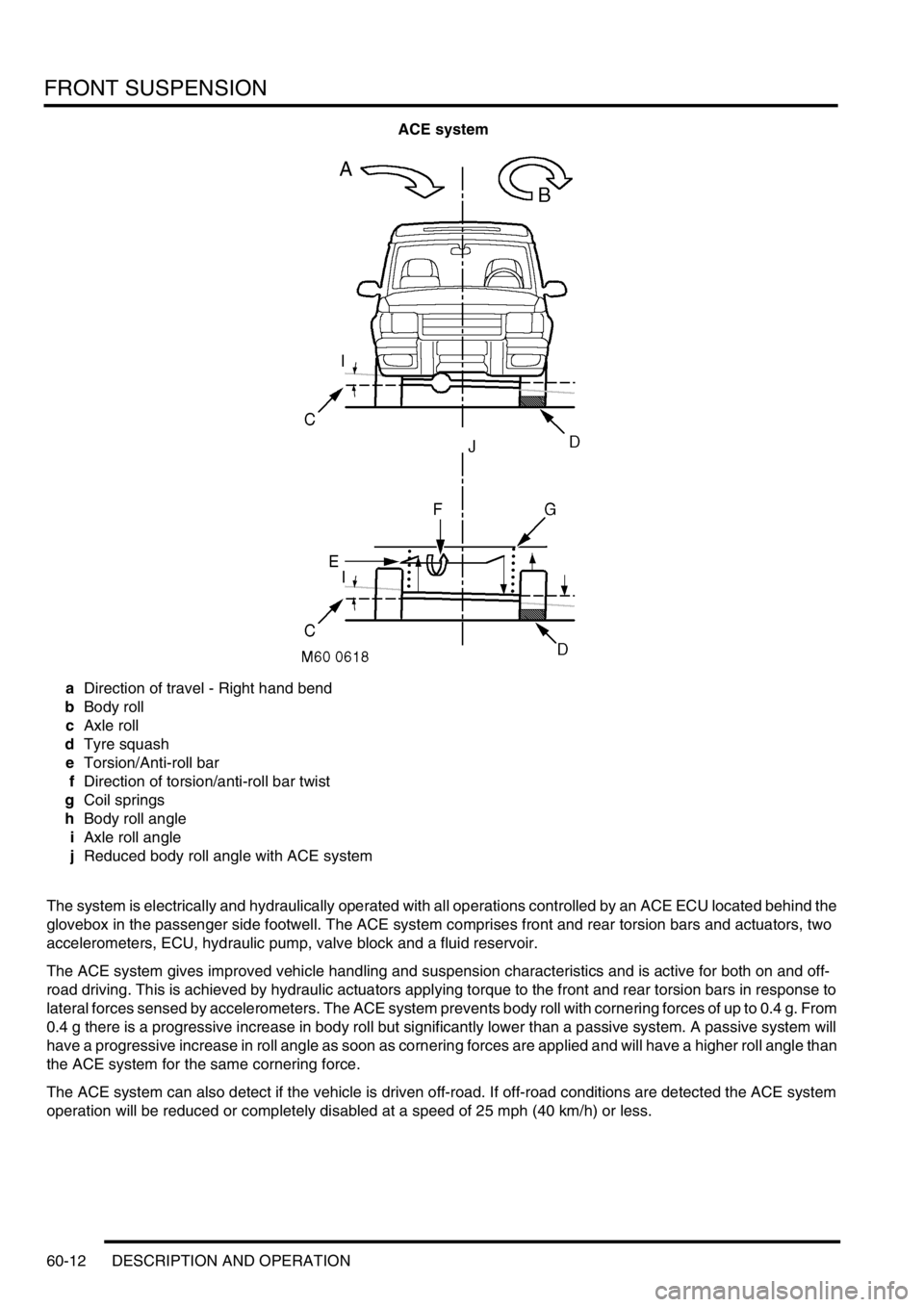
FRONT SUSPENSION
60-12 DESCRIPTION AND OPERATION
ACE system
aDirection of travel - Right hand bend
bBody roll
cAxle roll
dTyre squash
eTorsion/Anti-roll bar
fDirection of torsion/anti-roll bar twist
gCoil springs
hBody roll angle
iAxle roll angle
jReduced body roll angle with ACE system
The system is electrically and hydraulically operated with all operations controlled by an ACE ECU located behind the
glovebox in the passenger side footwell. The ACE system comprises front and rear torsion bars and actuators, two
accelerometers, ECU, hydraulic pump, valve block and a fluid reservoir.
The ACE system gives improved vehicle handling and suspension characteristics and is active for both on and off-
road driving. This is achieved by hydraulic actuators applying torque to the front and rear torsion bars in response to
lateral forces sensed by accelerometers. The ACE system prevents body roll with cornering forces of up to 0.4 g. From
0.4 g there is a progressive increase in body roll but significantly lower than a passive system. A passive system will
have a progressive increase in roll angle as soon as cornering forces are applied and will have a higher roll angle than
the ACE system for the same cornering force.
The ACE system can also detect if the vehicle is driven off-road. If off-road conditions are detected the ACE system
operation will be reduced or completely disabled at a speed of 25 mph (40 km/h) or less.
Page 965 of 1672
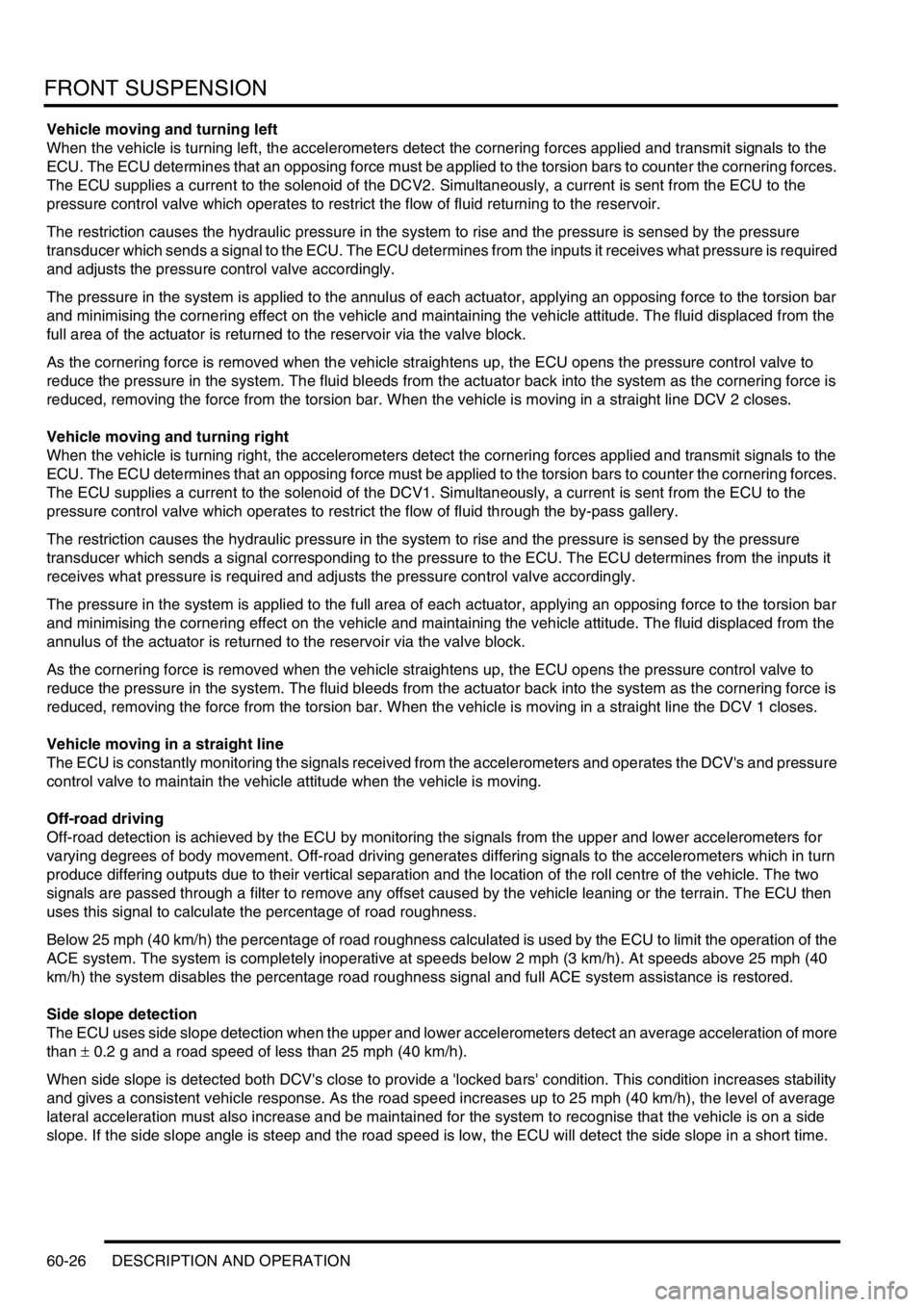
FRONT SUSPENSION
60-26 DESCRIPTION AND OPERATION
Vehicle moving and turning left
When the vehicle is turning left, the accelerometers detect the cornering forces applied and transmit signals to the
ECU. The ECU determines that an opposing force must be applied to the torsion bars to counter the cornering forces.
The ECU supplies a current to the solenoid of the DCV2. Simultaneously, a current is sent from the ECU to the
pressure control valve which operates to restrict the flow of fluid returning to the reservoir.
The restriction causes the hydraulic pressure in the system to rise and the pressure is sensed by the pressure
transducer which sends a signal to the ECU. The ECU determines from the inputs it receives what pressure is required
and adjusts the pressure control valve accordingly.
The pressure in the system is applied to the annulus of each actuator, applying an opposing force to the torsion bar
and minimising the cornering effect on the vehicle and maintaining the vehicle attitude. The fluid displaced from the
full area of the actuator is returned to the reservoir via the valve block.
As the cornering force is removed when the vehicle straightens up, the ECU opens the pressure control valve to
reduce the pressure in the system. The fluid bleeds from the actuator back into the system as the cornering force is
reduced, removing the force from the torsion bar. When the vehicle is moving in a straight line DCV 2 closes.
Vehicle moving and turning right
When the vehicle is turning right, the accelerometers detect the cornering forces applied and transmit signals to the
ECU. The ECU determines that an opposing force must be applied to the torsion bars to counter the cornering forces.
The ECU supplies a current to the solenoid of the DCV1. Simultaneously, a current is sent from the ECU to the
pressure control valve which operates to restrict the flow of fluid through the by-pass gallery.
The restriction causes the hydraulic pressure in the system to rise and the pressure is sensed by the pressure
transducer which sends a signal corresponding to the pressure to the ECU. The ECU determines from the inputs it
receives what pressure is required and adjusts the pressure control valve accordingly.
The pressure in the system is applied to the full area of each actuator, applying an opposing force to the torsion bar
and minimising the cornering effect on the vehicle and maintaining the vehicle attitude. The fluid displaced from the
annulus of the actuator is returned to the reservoir via the valve block.
As the cornering force is removed when the vehicle straightens up, the ECU opens the pressure control valve to
reduce the pressure in the system. The fluid bleeds from the actuator back into the system as the cornering force is
reduced, removing the force from the torsion bar. When the vehicle is moving in a straight line the DCV 1 closes.
Vehicle moving in a straight line
The ECU is constantly monitoring the signals received from the accelerometers and operates the DCV's and pressure
control valve to maintain the vehicle attitude when the vehicle is moving.
Off-road driving
Off-road detection is achieved by the ECU by monitoring the signals from the upper and lower accelerometers for
varying degrees of body movement. Off-road driving generates differing signals to the accelerometers which in turn
produce differing outputs due to their vertical separation and the location of the roll centre of the vehicle. The two
signals are passed through a filter to remove any offset caused by the vehicle leaning or the terrain. The ECU then
uses this signal to calculate the percentage of road roughness.
Below 25 mph (40 km/h) the percentage of road roughness calculated is used by the ECU to limit the operation of the
ACE system. The system is completely inoperative at speeds below 2 mph (3 km/h). At speeds above 25 mph (40
km/h) the system disables the percentage road roughness signal and full ACE system assistance is restored.
Side slope detection
The ECU uses side slope detection when the upper and lower accelerometers detect an average acceleration of more
than
± 0.2 g and a road speed of less than 25 mph (40 km/h).
When side slope is detected both DCV's close to provide a 'locked bars' condition. This condition increases stability
and gives a consistent vehicle response. As the road speed increases up to 25 mph (40 km/h), the level of average
lateral acceleration must also increase and be maintained for the system to recognise that the vehicle is on a side
slope. If the side slope angle is steep and the road speed is low, the ECU will detect the side slope in a short time.
Page 1019 of 1672
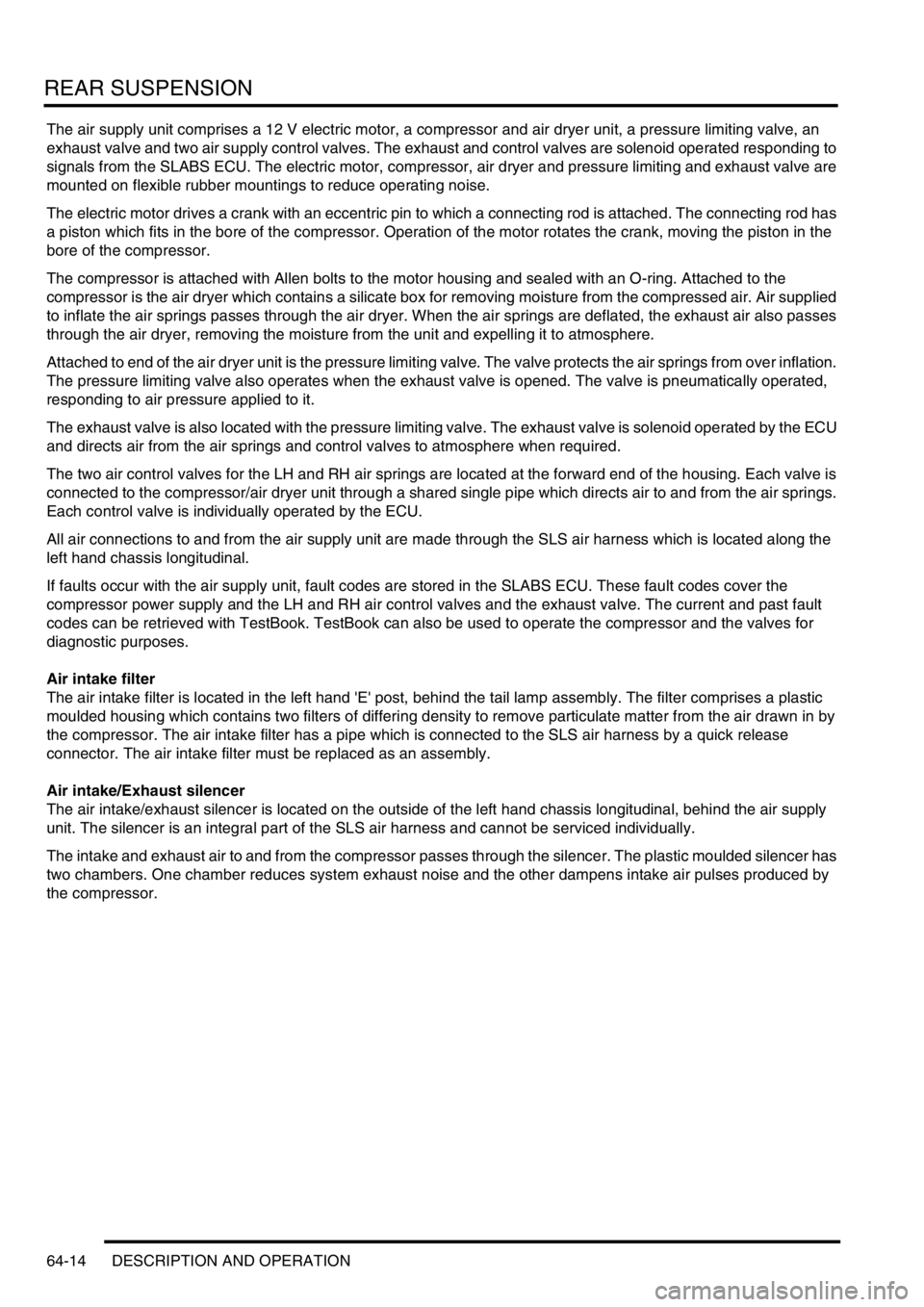
REAR SUSPENSION
64-14 DESCRIPTION AND OPERATION
The air supply unit comprises a 12 V electric motor, a compressor and air dryer unit, a pressure limiting valve, an
exhaust valve and two air supply control valves. The exhaust and control valves are solenoid operated responding to
signals from the SLABS ECU. The electric motor, compressor, air dryer and pressure limiting and exhaust valve are
mounted on flexible rubber mountings to reduce operating noise.
The electric motor drives a crank with an eccentric pin to which a connecting rod is attached. The connecting rod has
a piston which fits in the bore of the compressor. Operation of the motor rotates the crank, moving the piston in the
bore of the compressor.
The compressor is attached with Allen bolts to the motor housing and sealed with an O-ring. Attached to the
compressor is the air dryer which contains a silicate box for removing moisture from the compressed air. Air supplied
to inflate the air springs passes through the air dryer. When the air springs are deflated, the exhaust air also passes
through the air dryer, removing the moisture from the unit and expelling it to atmosphere.
Attached to end of the air dryer unit is the pressure limiting valve. The valve protects the air springs from over inflation.
The pressure limiting valve also operates when the exhaust valve is opened. The valve is pneumatically operated,
responding to air pressure applied to it.
The exhaust valve is also located with the pressure limiting valve. The exhaust valve is solenoid operated by the ECU
and directs air from the air springs and control valves to atmosphere when required.
The two air control valves for the LH and RH air springs are located at the forward end of the housing. Each valve is
connected to the compressor/air dryer unit through a shared single pipe which directs air to and from the air springs.
Each control valve is individually operated by the ECU.
All air connections to and from the air supply unit are made through the SLS air harness which is located along the
left hand chassis longitudinal.
If faults occur with the air supply unit, fault codes are stored in the SLABS ECU. These fault codes cover the
compressor power supply and the LH and RH air control valves and the exhaust valve. The current and past fault
codes can be retrieved with TestBook. TestBook can also be used to operate the compressor and the valves for
diagnostic purposes.
Air intake filter
The air intake filter is located in the left hand 'E' post, behind the tail lamp assembly. The filter comprises a plastic
moulded housing which contains two filters of differing density to remove particulate matter from the air drawn in by
the compressor. The air intake filter has a pipe which is connected to the SLS air harness by a quick release
connector. The air intake filter must be replaced as an assembly.
Air intake/Exhaust silencer
The air intake/exhaust silencer is located on the outside of the left hand chassis longitudinal, behind the air supply
unit. The silencer is an integral part of the SLS air harness and cannot be serviced individually.
The intake and exhaust air to and from the compressor passes through the silencer. The plastic moulded silencer has
two chambers. One chamber reduces system exhaust noise and the other dampens intake air pulses produced by
the compressor.
Page 1022 of 1672
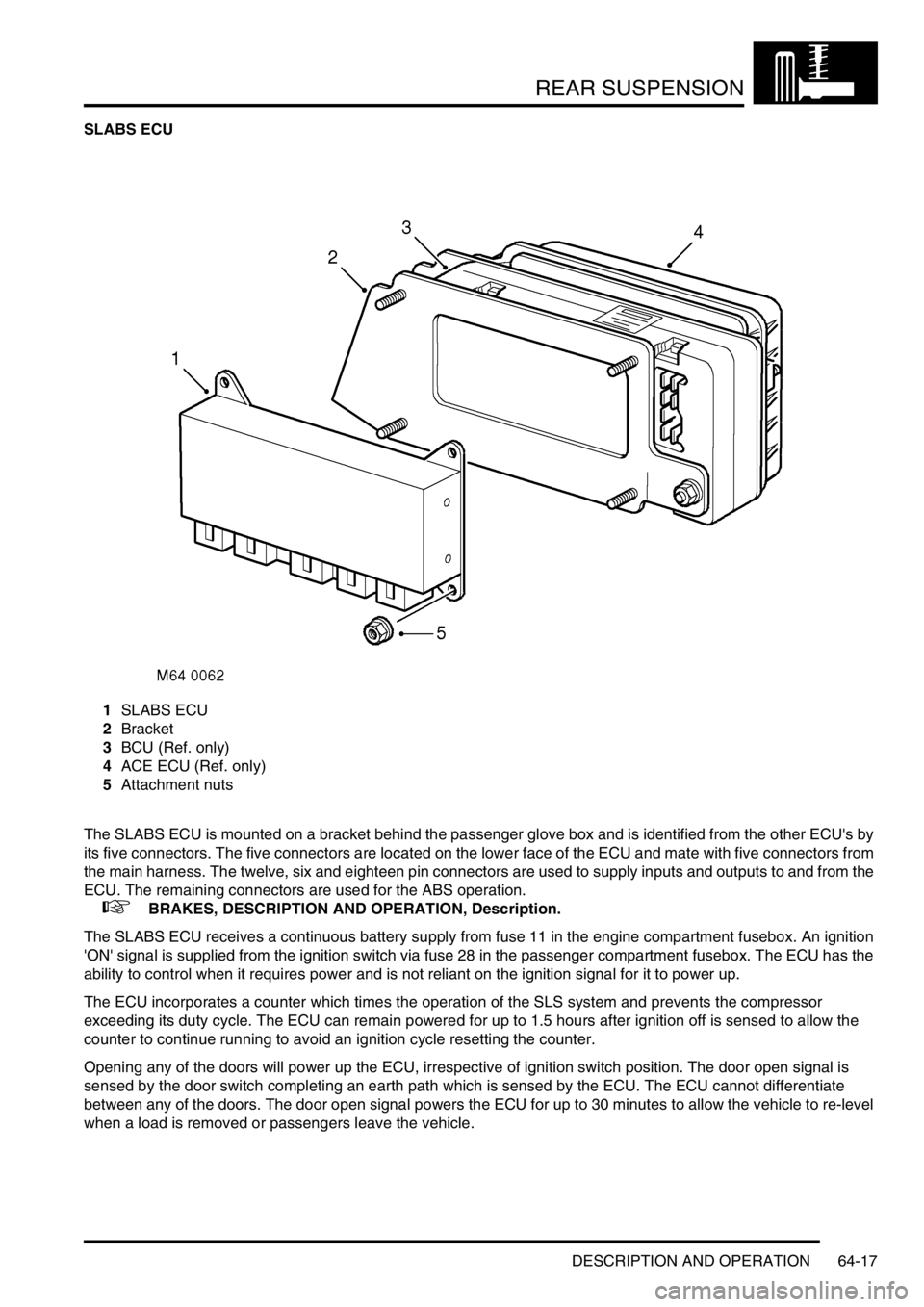
REAR SUSPENSION
DESCRIPTION AND OPERATION 64-17
SLABS ECU
1SLABS ECU
2Bracket
3BCU (Ref. only)
4ACE ECU (Ref. only)
5Attachment nuts
The SLABS ECU is mounted on a bracket behind the passenger glove box and is identified from the other ECU's by
its five connectors. The five connectors are located on the lower face of the ECU and mate with five connectors from
the main harness. The twelve, six and eighteen pin connectors are used to supply inputs and outputs to and from the
ECU. The remaining connectors are used for the ABS operation.
+ BRAKES, DESCRIPTION AND OPERATION, Description.
The SLABS ECU receives a continuous battery supply from fuse 11 in the engine compartment fusebox. An ignition
'ON' signal is supplied from the ignition switch via fuse 28 in the passenger compartment fusebox. The ECU has the
ability to control when it requires power and is not reliant on the ignition signal for it to power up.
The ECU incorporates a counter which times the operation of the SLS system and prevents the compressor
exceeding its duty cycle. The ECU can remain powered for up to 1.5 hours after ignition off is sensed to allow the
counter to continue running to avoid an ignition cycle resetting the counter.
Opening any of the doors will power up the ECU, irrespective of ignition switch position. The door open signal is
sensed by the door switch completing an earth path which is sensed by the ECU. The ECU cannot differentiate
between any of the doors. The door open signal powers the ECU for up to 30 minutes to allow the vehicle to re-level
when a load is removed or passengers leave the vehicle.
Page 1026 of 1672
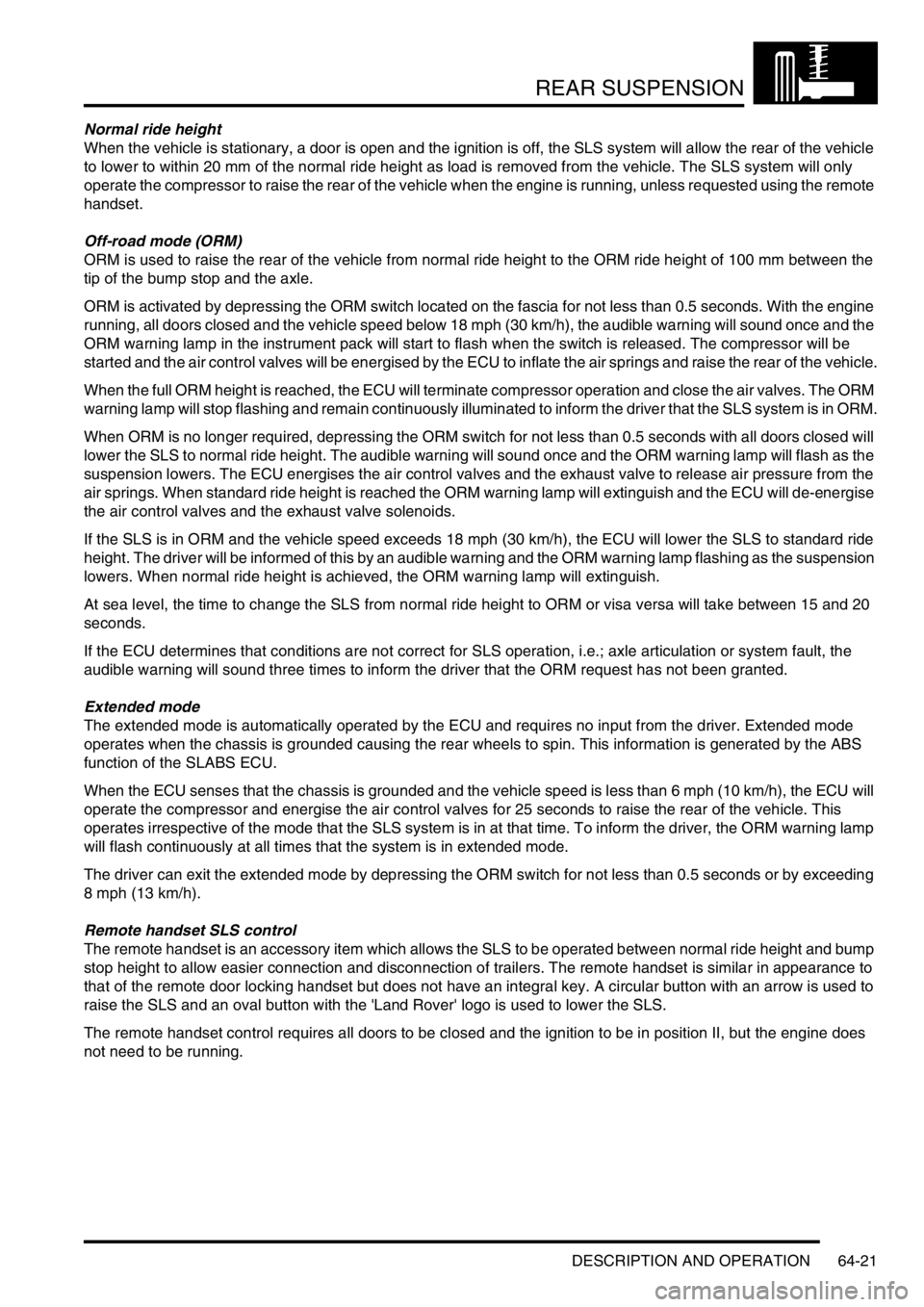
REAR SUSPENSION
DESCRIPTION AND OPERATION 64-21
Normal ride height
When the vehicle is stationary, a door is open and the ignition is off, the SLS system will allow the rear of the vehicle
to lower to within 20 mm of the normal ride height as load is removed from the vehicle. The SLS system will only
operate the compressor to raise the rear of the vehicle when the engine is running, unless requested using the remote
handset.
Off-road mode (ORM)
ORM is used to raise the rear of the vehicle from normal ride height to the ORM ride height of 100 mm between the
tip of the bump stop and the axle.
ORM is activated by depressing the ORM switch located on the fascia for not less than 0.5 seconds. With the engine
running, all doors closed and the vehicle speed below 18 mph (30 km/h), the audible warning will sound once and the
ORM warning lamp in the instrument pack will start to flash when the switch is released. The compressor will be
started and the air control valves will be energised by the ECU to inflate the air springs and raise the rear of the vehicle.
When the full ORM height is reached, the ECU will terminate compressor operation and close the air valves. The ORM
warning lamp will stop flashing and remain continuously illuminated to inform the driver that the SLS system is in ORM.
When ORM is no longer required, depressing the ORM switch for not less than 0.5 seconds with all doors closed will
lower the SLS to normal ride height. The audible warning will sound once and the ORM warning lamp will flash as the
suspension lowers. The ECU energises the air control valves and the exhaust valve to release air pressure from the
air springs. When standard ride height is reached the ORM warning lamp will extinguish and the ECU will de-energise
the air control valves and the exhaust valve solenoids.
If the SLS is in ORM and the vehicle speed exceeds 18 mph (30 km/h), the ECU will lower the SLS to standard ride
height. The driver will be informed of this by an audible warning and the ORM warning lamp flashing as the suspension
lowers. When normal ride height is achieved, the ORM warning lamp will extinguish.
At sea level, the time to change the SLS from normal ride height to ORM or visa versa will take between 15 and 20
seconds.
If the ECU determines that conditions are not correct for SLS operation, i.e.; axle articulation or system fault, the
audible warning will sound three times to inform the driver that the ORM request has not been granted.
Extended mode
The extended mode is automatically operated by the ECU and requires no input from the driver. Extended mode
operates when the chassis is grounded causing the rear wheels to spin. This information is generated by the ABS
function of the SLABS ECU.
When the ECU senses that the chassis is grounded and the vehicle speed is less than 6 mph (10 km/h), the ECU will
operate the compressor and energise the air control valves for 25 seconds to raise the rear of the vehicle. This
operates irrespective of the mode that the SLS system is in at that time. To inform the driver, the ORM warning lamp
will flash continuously at all times that the system is in extended mode.
The driver can exit the extended mode by depressing the ORM switch for not less than 0.5 seconds or by exceeding
8 mph (13 km/h).
Remote handset SLS control
The remote handset is an accessory item which allows the SLS to be operated between normal ride height and bump
stop height to allow easier connection and disconnection of trailers. The remote handset is similar in appearance to
that of the remote door locking handset but does not have an integral key. A circular button with an arrow is used to
raise the SLS and an oval button with the 'Land Rover' logo is used to lower the SLS.
The remote handset control requires all doors to be closed and the ignition to be in position II, but the engine does
not need to be running.
Page 1059 of 1672
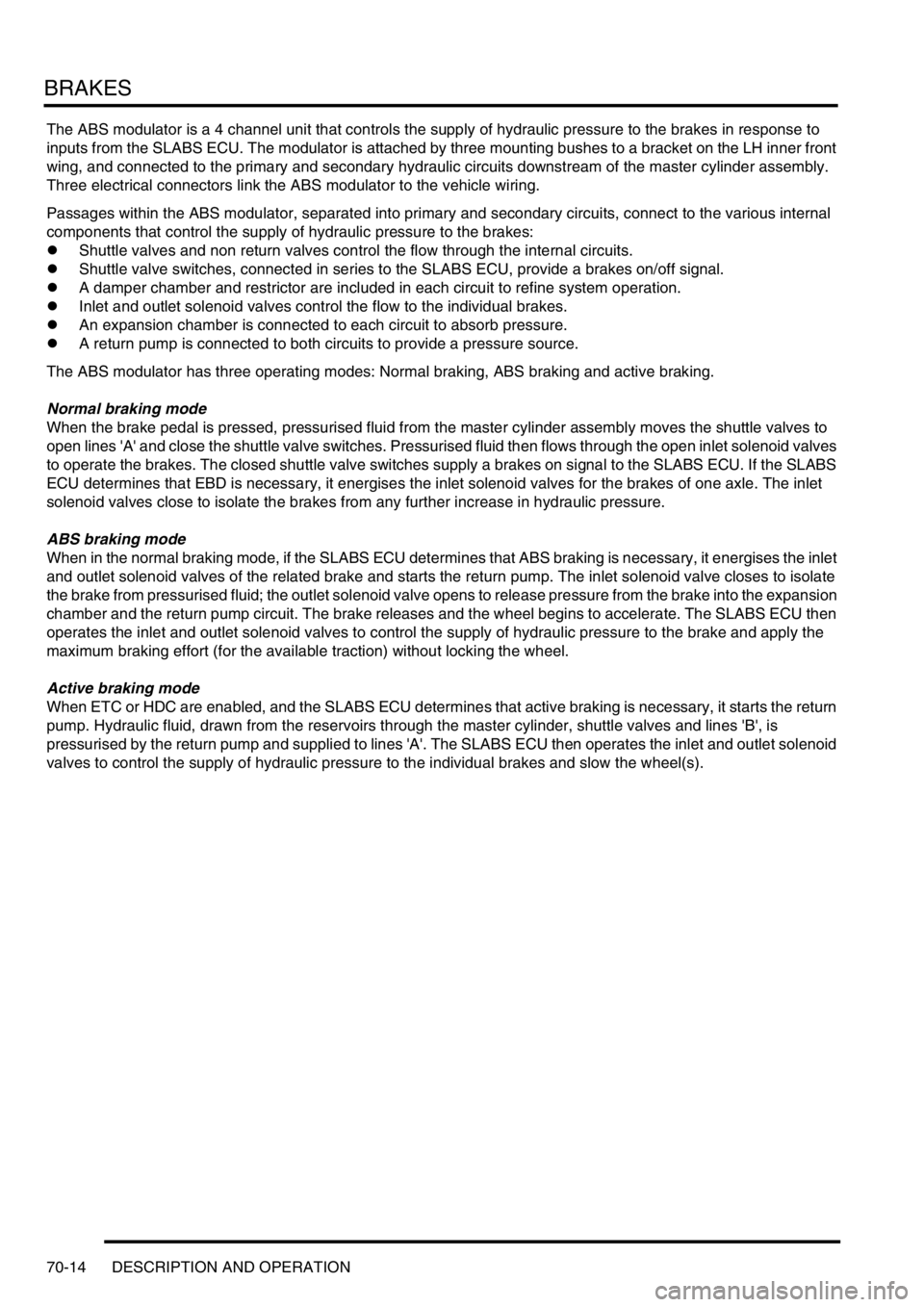
BRAKES
70-14 DESCRIPTION AND OPERATION
The ABS modulator is a 4 channel unit that controls the supply of hydraulic pressure to the brakes in response to
inputs from the SLABS ECU. The modulator is attached by three mounting bushes to a bracket on the LH inner front
wing, and connected to the primary and secondary hydraulic circuits downstream of the master cylinder assembly.
Three electrical connectors link the ABS modulator to the vehicle wiring.
Passages within the ABS modulator, separated into primary and secondary circuits, connect to the various internal
components that control the supply of hydraulic pressure to the brakes:
lShuttle valves and non return valves control the flow through the internal circuits.
lShuttle valve switches, connected in series to the SLABS ECU, provide a brakes on/off signal.
lA damper chamber and restrictor are included in each circuit to refine system operation.
lInlet and outlet solenoid valves control the flow to the individual brakes.
lAn expansion chamber is connected to each circuit to absorb pressure.
lA return pump is connected to both circuits to provide a pressure source.
The ABS modulator has three operating modes: Normal braking, ABS braking and active braking.
Normal braking mode
When the brake pedal is pressed, pressurised fluid from the master cylinder assembly moves the shuttle valves to
open lines 'A' and close the shuttle valve switches. Pressurised fluid then flows through the open inlet solenoid valves
to operate the brakes. The closed shuttle valve switches supply a brakes on signal to the SLABS ECU. If the SLABS
ECU determines that EBD is necessary, it energises the inlet solenoid valves for the brakes of one axle. The inlet
solenoid valves close to isolate the brakes from any further increase in hydraulic pressure.
ABS braking mode
When in the normal braking mode, if the SLABS ECU determines that ABS braking is necessary, it energises the inlet
and outlet solenoid valves of the related brake and starts the return pump. The inlet solenoid valve closes to isolate
the brake from pressurised fluid; the outlet solenoid valve opens to release pressure from the brake into the expansion
chamber and the return pump circuit. The brake releases and the wheel begins to accelerate. The SLABS ECU then
operates the inlet and outlet solenoid valves to control the supply of hydraulic pressure to the brake and apply the
maximum braking effort (for the available traction) without locking the wheel.
Active braking mode
When ETC or HDC are enabled, and the SLABS ECU determines that active braking is necessary, it starts the return
pump. Hydraulic fluid, drawn from the reservoirs through the master cylinder, shuttle valves and lines 'B', is
pressurised by the return pump and supplied to lines 'A'. The SLABS ECU then operates the inlet and outlet solenoid
valves to control the supply of hydraulic pressure to the individual brakes and slow the wheel(s).