fuse box LAND ROVER DISCOVERY 2002 Repair Manual
[x] Cancel search | Manufacturer: LAND ROVER, Model Year: 2002, Model line: DISCOVERY, Model: LAND ROVER DISCOVERY 2002Pages: 1672, PDF Size: 46.1 MB
Page 1429 of 1672
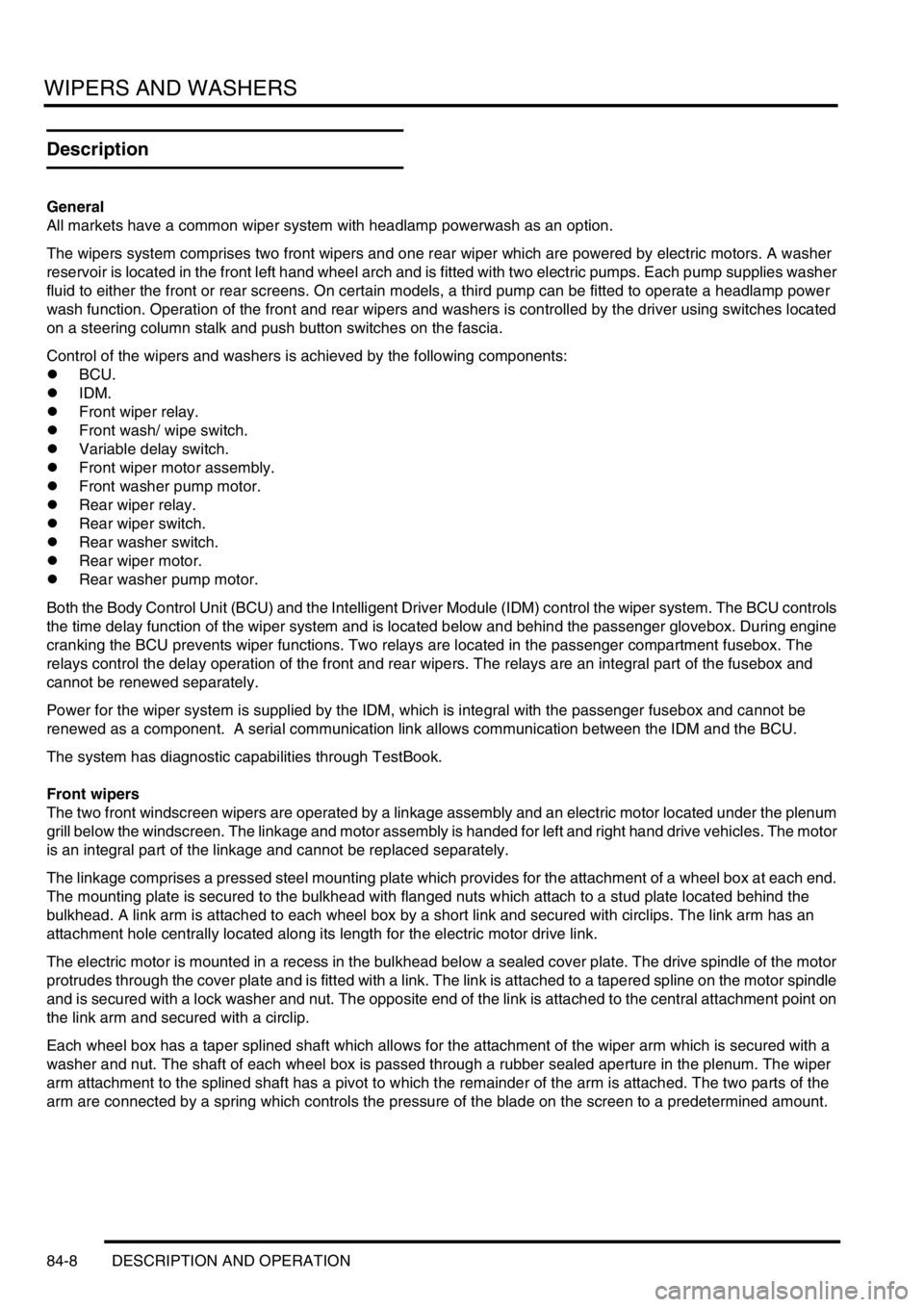
WIPERS AND WASHERS
84-8 DESCRIPTION AND OPERATION
Description
General
All markets have a common wiper system with headlamp powerwash as an option.
The wipers system comprises two front wipers and one rear wiper which are powered by electric motors. A washer
reservoir is located in the front left hand wheel arch and is fitted with two electric pumps. Each pump supplies washer
fluid to either the front or rear screens. On certain models, a third pump can be fitted to operate a headlamp power
wash function. Operation of the front and rear wipers and washers is controlled by the driver using switches located
on a steering column stalk and push button switches on the fascia.
Control of the wipers and washers is achieved by the following components:
lBCU.
lIDM.
lFront wiper relay.
lFront wash/ wipe switch.
lVariable delay switch.
lFront wiper motor assembly.
lFront washer pump motor.
lRear wiper relay.
lRear wiper switch.
lRear washer switch.
lRear wiper motor.
lRear washer pump motor.
Both the Body Control Unit (BCU) and the Intelligent Driver Module (IDM) control the wiper system. The BCU controls
the time delay function of the wiper system and is located below and behind the passenger glovebox. During engine
cranking the BCU prevents wiper functions. Two relays are located in the passenger compartment fusebox. The
relays control the delay operation of the front and rear wipers. The relays are an integral part of the fusebox and
cannot be renewed separately.
Power for the wiper system is supplied by the IDM, which is integral with the passenger fusebox and cannot be
renewed as a component. A serial communication link allows communication between the IDM and the BCU.
The system has diagnostic capabilities through TestBook.
Front wipers
The two front windscreen wipers are operated by a linkage assembly and an electric motor located under the plenum
grill below the windscreen. The linkage and motor assembly is handed for left and right hand drive vehicles. The motor
is an integral part of the linkage and cannot be replaced separately.
The linkage comprises a pressed steel mounting plate which provides for the attachment of a wheel box at each end.
The mounting plate is secured to the bulkhead with flanged nuts which attach to a stud plate located behind the
bulkhead. A link arm is attached to each wheel box by a short link and secured with circlips. The link arm has an
attachment hole centrally located along its length for the electric motor drive link.
The electric motor is mounted in a recess in the bulkhead below a sealed cover plate. The drive spindle of the motor
protrudes through the cover plate and is fitted with a link. The link is attached to a tapered spline on the motor spindle
and is secured with a lock washer and nut. The opposite end of the link is attached to the central attachment point on
the link arm and secured with a circlip.
Each wheel box has a taper splined shaft which allows for the attachment of the wiper arm which is secured with a
washer and nut. The shaft of each wheel box is passed through a rubber sealed aperture in the plenum. The wiper
arm attachment to the splined shaft has a pivot to which the remainder of the arm is attached. The two parts of the
arm are connected by a spring which controls the pressure of the blade on the screen to a predetermined amount.
Page 1430 of 1672
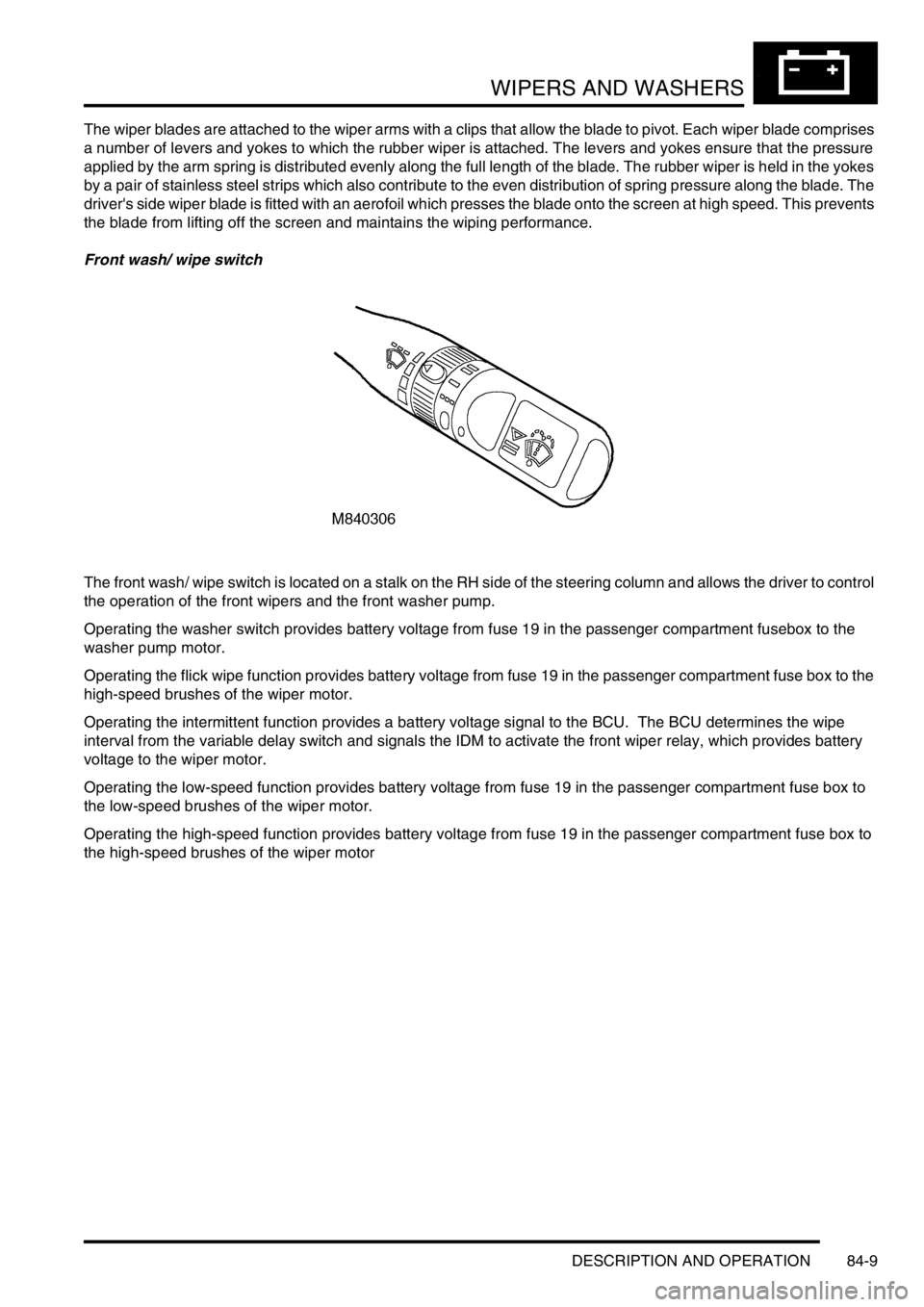
WIPERS AND WASHERS
DESCRIPTION AND OPERATION 84-9
The wiper blades are attached to the wiper arms with a clips that allow the blade to pivot. Each wiper blade comprises
a number of levers and yokes to which the rubber wiper is attached. The levers and yokes ensure that the pressure
applied by the arm spring is distributed evenly along the full length of the blade. The rubber wiper is held in the yokes
by a pair of stainless steel strips which also contribute to the even distribution of spring pressure along the blade. The
driver's side wiper blade is fitted with an aerofoil which presses the blade onto the screen at high speed. This prevents
the blade from lifting off the screen and maintains the wiping performance.
Front wash/ wipe switch
The front wash/ wipe switch is located on a stalk on the RH side of the steering column and allows the driver to control
the operation of the front wipers and the front washer pump.
Operating the washer switch provides battery voltage from fuse 19 in the passenger compartment fusebox to the
washer pump motor.
Operating the flick wipe function provides battery voltage from fuse 19 in the passenger compartment fuse box to the
high-speed brushes of the wiper motor.
Operating the intermittent function provides a battery voltage signal to the BCU. The BCU determines the wipe
interval from the variable delay switch and signals the IDM to activate the front wiper relay, which provides battery
voltage to the wiper motor.
Operating the low-speed function provides battery voltage from fuse 19 in the passenger compartment fuse box to
the low-speed brushes of the wiper motor.
Operating the high-speed function provides battery voltage from fuse 19 in the passenger compartment fuse box to
the high-speed brushes of the wiper motor
Page 1432 of 1672
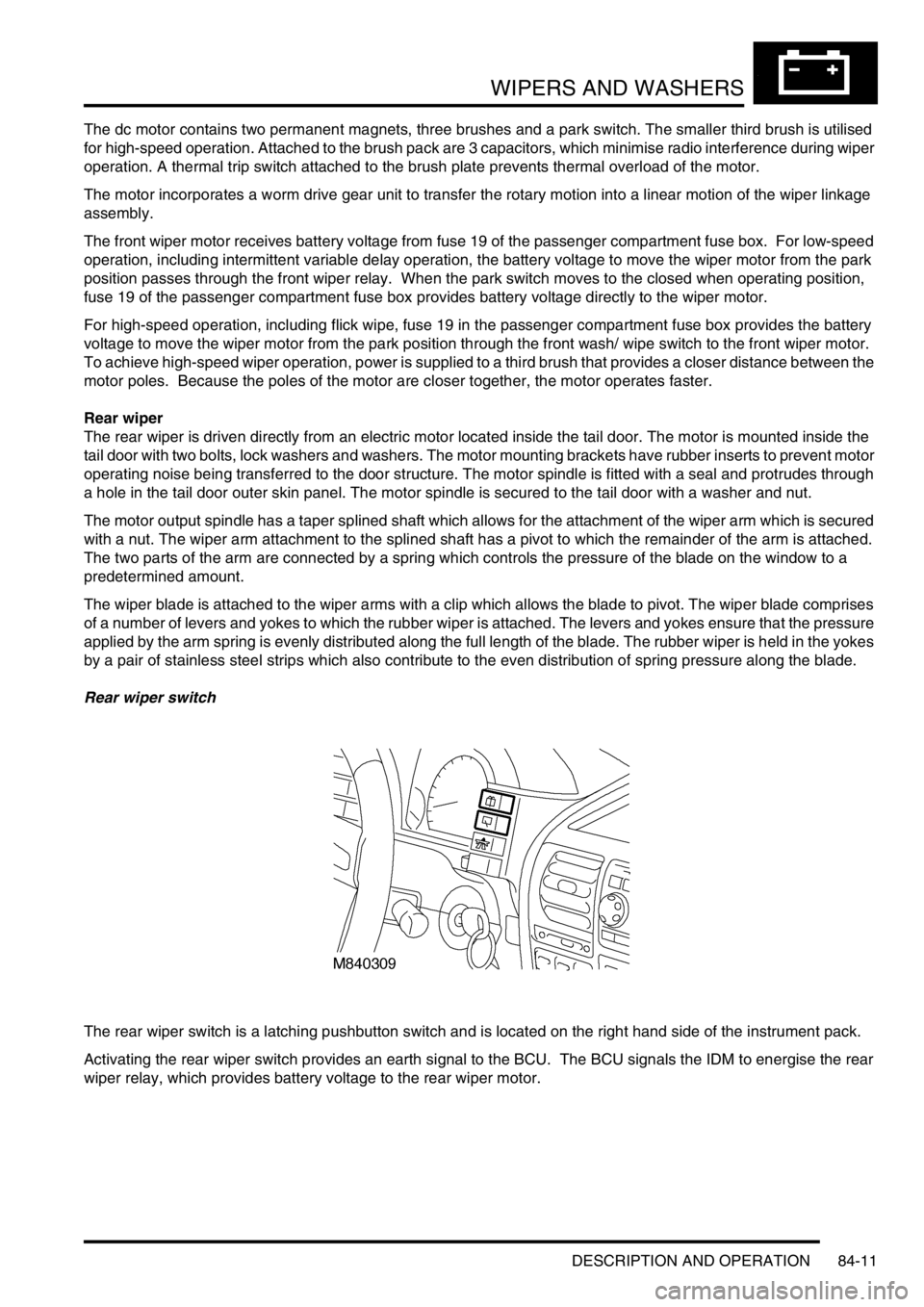
WIPERS AND WASHERS
DESCRIPTION AND OPERATION 84-11
The dc motor contains two permanent magnets, three brushes and a park switch. The smaller third brush is utilised
for high-speed operation. Attached to the brush pack are 3 capacitors, which minimise radio interference during wiper
operation. A thermal trip switch attached to the brush plate prevents thermal overload of the motor.
The motor incorporates a worm drive gear unit to transfer the rotary motion into a linear motion of the wiper linkage
assembly.
The front wiper motor receives battery voltage from fuse 19 of the passenger compartment fuse box. For low-speed
operation, including intermittent variable delay operation, the battery voltage to move the wiper motor from the park
position passes through the front wiper relay. When the park switch moves to the closed when operating position,
fuse 19 of the passenger compartment fuse box provides battery voltage directly to the wiper motor.
For high-speed operation, including flick wipe, fuse 19 in the passenger compartment fuse box provides the battery
voltage to move the wiper motor from the park position through the front wash/ wipe switch to the front wiper motor.
To achieve high-speed wiper operation, power is supplied to a third brush that provides a closer distance between the
motor poles. Because the poles of the motor are closer together, the motor operates faster.
Rear wiper
The rear wiper is driven directly from an electric motor located inside the tail door. The motor is mounted inside the
tail door with two bolts, lock washers and washers. The motor mounting brackets have rubber inserts to prevent motor
operating noise being transferred to the door structure. The motor spindle is fitted with a seal and protrudes through
a hole in the tail door outer skin panel. The motor spindle is secured to the tail door with a washer and nut.
The motor output spindle has a taper splined shaft which allows for the attachment of the wiper arm which is secured
with a nut. The wiper arm attachment to the splined shaft has a pivot to which the remainder of the arm is attached.
The two parts of the arm are connected by a spring which controls the pressure of the blade on the window to a
predetermined amount.
The wiper blade is attached to the wiper arms with a clip which allows the blade to pivot. The wiper blade comprises
of a number of levers and yokes to which the rubber wiper is attached. The levers and yokes ensure that the pressure
applied by the arm spring is evenly distributed along the full length of the blade. The rubber wiper is held in the yokes
by a pair of stainless steel strips which also contribute to the even distribution of spring pressure along the blade.
Rear wiper switch
The rear wiper switch is a latching pushbutton switch and is located on the right hand side of the instrument pack.
Activating the rear wiper switch provides an earth signal to the BCU. The BCU signals the IDM to energise the rear
wiper relay, which provides battery voltage to the rear wiper motor.
Page 1434 of 1672
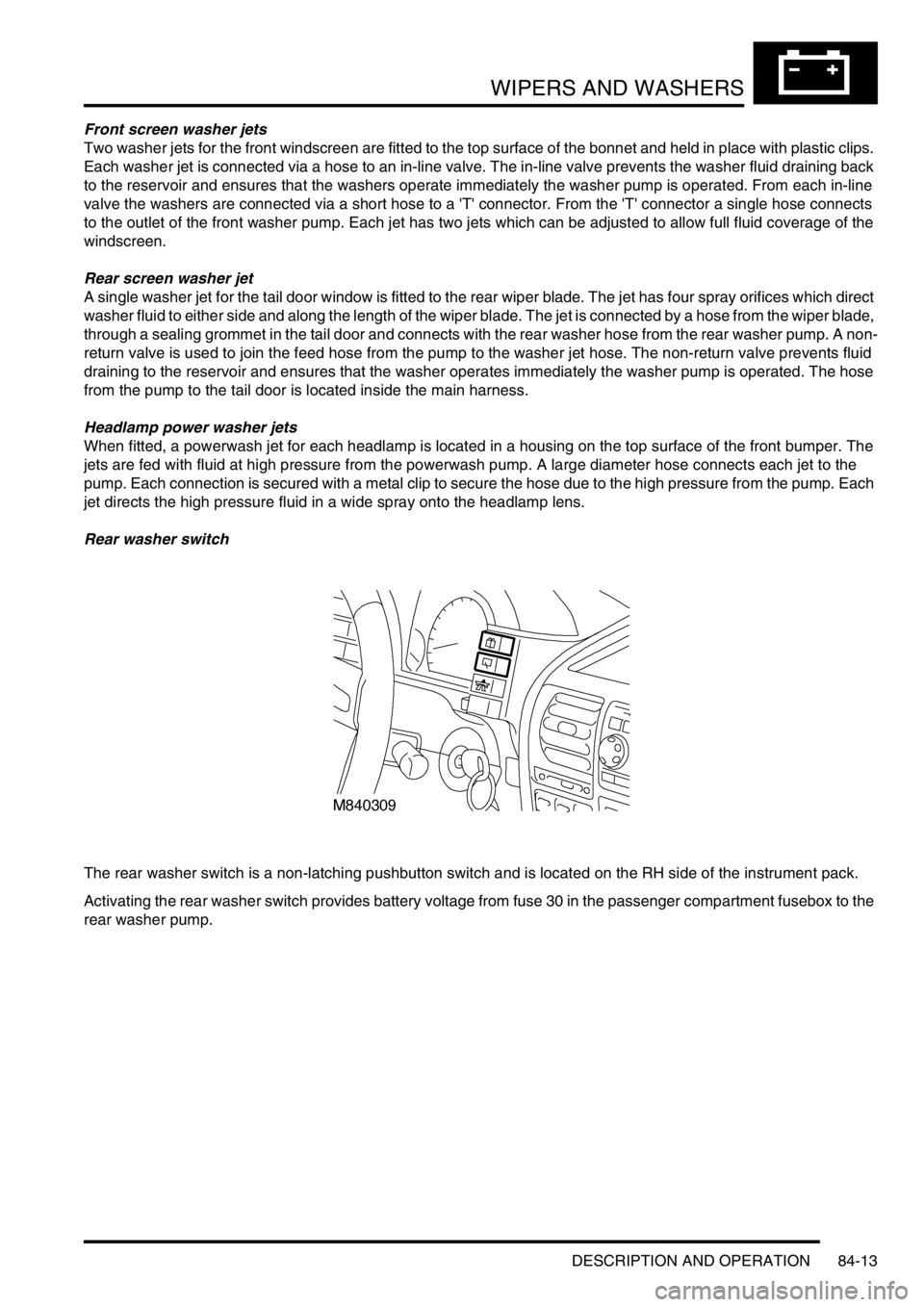
WIPERS AND WASHERS
DESCRIPTION AND OPERATION 84-13
Front screen washer jets
Two washer jets for the front windscreen are fitted to the top surface of the bonnet and held in place with plastic clips.
Each washer jet is connected via a hose to an in-line valve. The in-line valve prevents the washer fluid draining back
to the reservoir and ensures that the washers operate immediately the washer pump is operated. From each in-line
valve the washers are connected via a short hose to a 'T' connector. From the 'T' connector a single hose connects
to the outlet of the front washer pump. Each jet has two jets which can be adjusted to allow full fluid coverage of the
windscreen.
Rear screen washer jet
A single washer jet for the tail door window is fitted to the rear wiper blade. The jet has four spray orifices which direct
washer fluid to either side and along the length of the wiper blade. The jet is connected by a hose from the wiper blade,
through a sealing grommet in the tail door and connects with the rear washer hose from the rear washer pump. A non-
return valve is used to join the feed hose from the pump to the washer jet hose. The non-return valve prevents fluid
draining to the reservoir and ensures that the washer operates immediately the washer pump is operated. The hose
from the pump to the tail door is located inside the main harness.
Headlamp power washer jets
When fitted, a powerwash jet for each headlamp is located in a housing on the top surface of the front bumper. The
jets are fed with fluid at high pressure from the powerwash pump. A large diameter hose connects each jet to the
pump. Each connection is secured with a metal clip to secure the hose due to the high pressure from the pump. Each
jet directs the high pressure fluid in a wide spray onto the headlamp lens.
Rear washer switch
The rear washer switch is a non-latching pushbutton switch and is located on the RH side of the instrument pack.
Activating the rear washer switch provides battery voltage from fuse 30 in the passenger compartment fusebox to the
rear washer pump.
Page 1436 of 1672
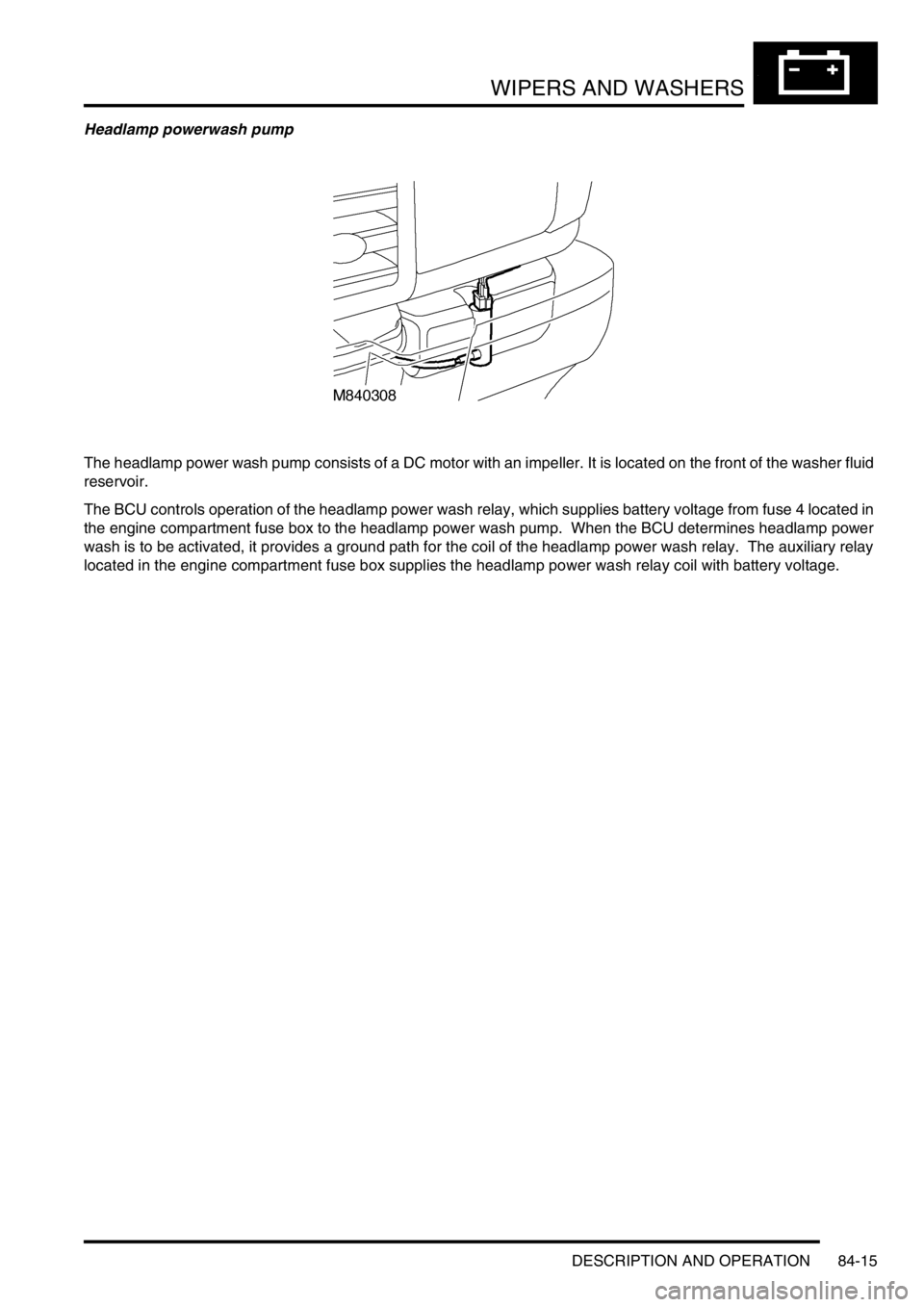
WIPERS AND WASHERS
DESCRIPTION AND OPERATION 84-15
Headlamp powerwash pump
The headlamp power wash pump consists of a DC motor with an impeller. It is located on the front of the washer fluid
reservoir.
The BCU controls operation of the headlamp power wash relay, which supplies battery voltage from fuse 4 located in
the engine compartment fuse box to the headlamp power wash pump. When the BCU determines headlamp power
wash is to be activated, it provides a ground path for the coil of the headlamp power wash relay. The auxiliary relay
located in the engine compartment fuse box supplies the headlamp power wash relay coil with battery voltage.
Page 1470 of 1672
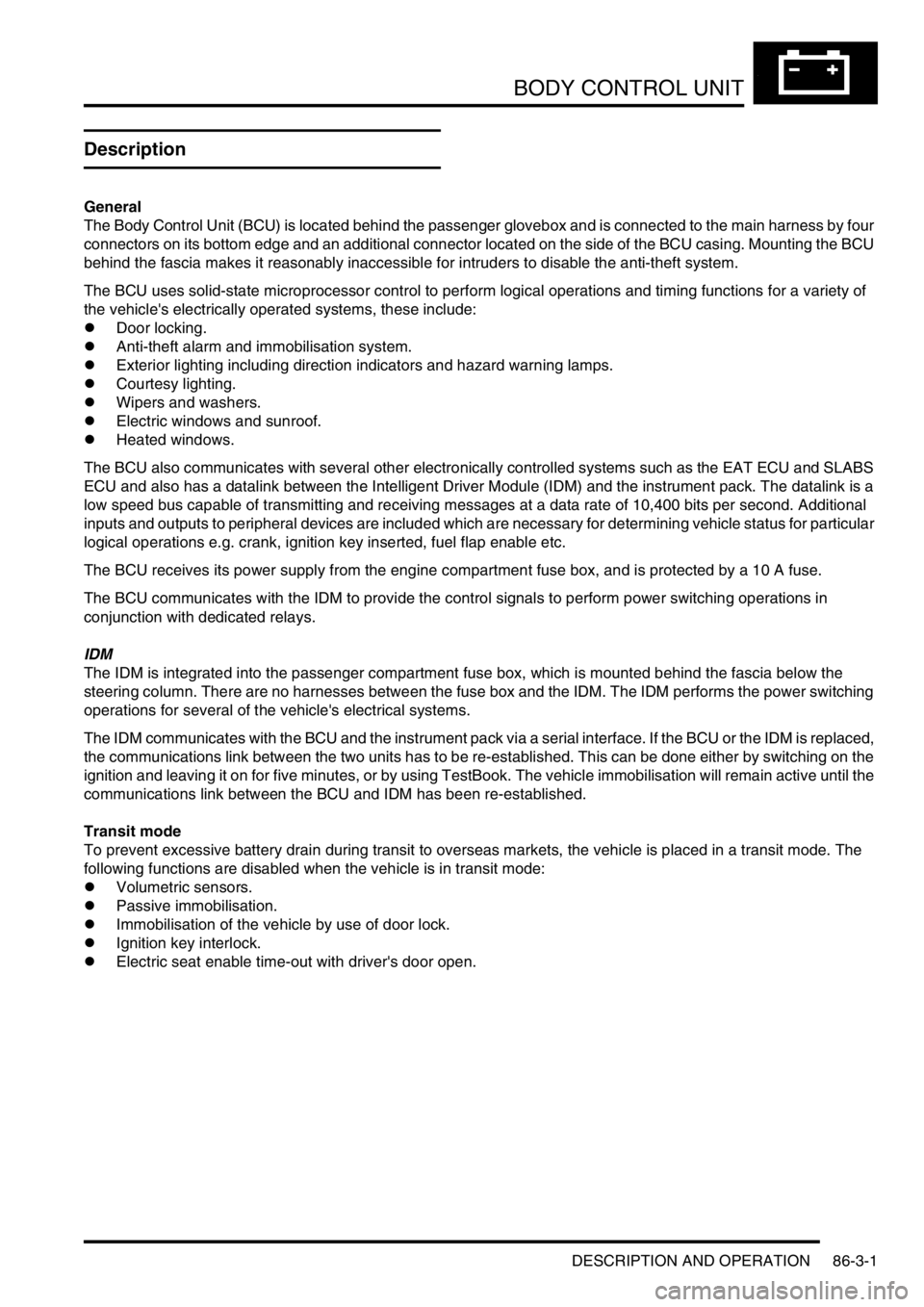
BODY CONTROL UNIT
DESCRIPTION AND OPERATION 86-3-1
BODY CONTROL UNIT DESCRIPTION AND OPERAT ION
Description
General
The Body Control Unit (BCU) is located behind the passenger glovebox and is connected to the main harness by four
connectors on its bottom edge and an additional connector located on the side of the BCU casing. Mounting the BCU
behind the fascia makes it reasonably inaccessible for intruders to disable the anti-theft system.
The BCU uses solid-state microprocessor control to perform logical operations and timing functions for a variety of
the vehicle's electrically operated systems, these include:
lDoor locking.
lAnti-theft alarm and immobilisation system.
lExterior lighting including direction indicators and hazard warning lamps.
lCourtesy lighting.
lWipers and washers.
lElectric windows and sunroof.
lHeated windows.
The BCU also communicates with several other electronically controlled systems such as the EAT ECU and SLABS
ECU and also has a datalink between the Intelligent Driver Module (IDM) and the instrument pack. The datalink is a
low speed bus capable of transmitting and receiving messages at a data rate of 10,400 bits per second. Additional
inputs and outputs to peripheral devices are included which are necessary for determining vehicle status for particular
logical operations e.g. crank, ignition key inserted, fuel flap enable etc.
The BCU receives its power supply from the engine compartment fuse box, and is protected by a 10 A fuse.
The BCU communicates with the IDM to provide the control signals to perform power switching operations in
conjunction with dedicated relays.
IDM
The IDM is integrated into the passenger compartment fuse box, which is mounted behind the fascia below the
steering column. There are no harnesses between the fuse box and the IDM. The IDM performs the power switching
operations for several of the vehicle's electrical systems.
The IDM communicates with the BCU and the instrument pack via a serial interface. If the BCU or the IDM is replaced,
the communications link between the two units has to be re-established. This can be done either by switching on the
ignition and leaving it on for five minutes, or by using TestBook. The vehicle immobilisation will remain active until the
communications link between the BCU and IDM has been re-established.
Transit mode
To prevent excessive battery drain during transit to overseas markets, the vehicle is placed in a transit mode. The
following functions are disabled when the vehicle is in transit mode:
lVolumetric sensors.
lPassive immobilisation.
lImmobilisation of the vehicle by use of door lock.
lIgnition key interlock.
lElectric seat enable time-out with driver's door open.
Page 1471 of 1672
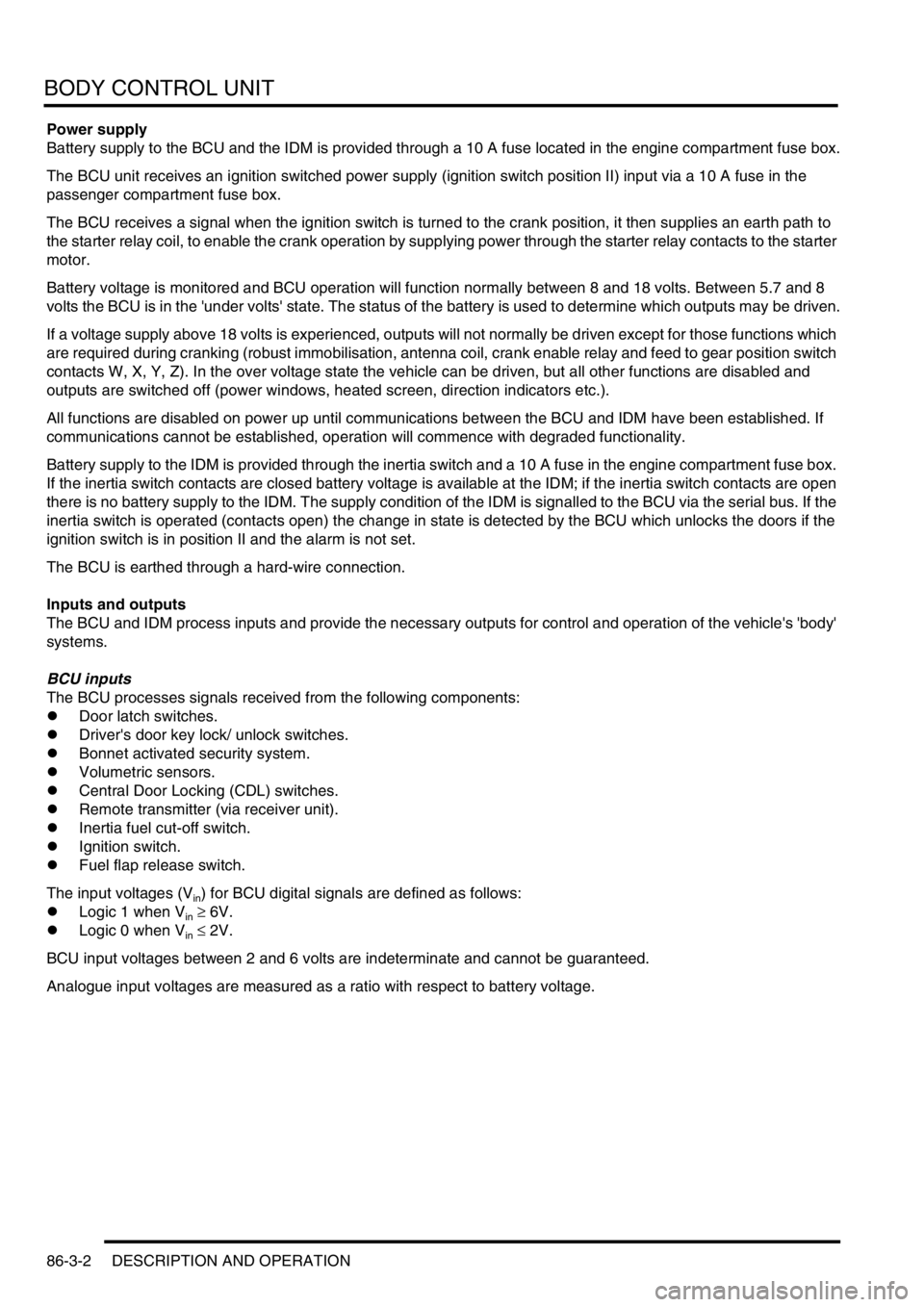
BODY CONTROL UNIT
86-3-2 DESCRIPTION AND OPERATION
Power supply
Battery supply to the BCU and the IDM is provided through a 10 A fuse located in the engine compartment fuse box.
The BCU unit receives an ignition switched power supply (ignition switch position II) input via a 10 A fuse in the
passenger compartment fuse box.
The BCU receives a signal when the ignition switch is turned to the crank position, it then supplies an earth path to
the starter relay coil, to enable the crank operation by supplying power through the starter relay contacts to the starter
motor.
Battery voltage is monitored and BCU operation will function normally between 8 and 18 volts. Between 5.7 and 8
volts the BCU is in the 'under volts' state. The status of the battery is used to determine which outputs may be driven.
If a voltage supply above 18 volts is experienced, outputs will not normally be driven except for those functions which
are required during cranking (robust immobilisation, antenna coil, crank enable relay and feed to gear position switch
contacts W, X, Y, Z). In the over voltage state the vehicle can be driven, but all other functions are disabled and
outputs are switched off (power windows, heated screen, direction indicators etc.).
All functions are disabled on power up until communications between the BCU and IDM have been established. If
communications cannot be established, operation will commence with degraded functionality.
Battery supply to the IDM is provided through the inertia switch and a 10 A fuse in the engine compartment fuse box.
If the inertia switch contacts are closed battery voltage is available at the IDM; if the inertia switch contacts are open
there is no battery supply to the IDM. The supply condition of the IDM is signalled to the BCU via the serial bus. If the
inertia switch is operated (contacts open) the change in state is detected by the BCU which unlocks the doors if the
ignition switch is in position II and the alarm is not set.
The BCU is earthed through a hard-wire connection.
Inputs and outputs
The BCU and IDM process inputs and provide the necessary outputs for control and operation of the vehicle's 'body'
systems.
BCU inputs
The BCU processes signals received from the following components:
lDoor latch switches.
lDriver's door key lock/ unlock switches.
lBonnet activated security system.
lVolumetric sensors.
lCentral Door Locking (CDL) switches.
lRemote transmitter (via receiver unit).
lInertia fuel cut-off switch.
lIgnition switch.
lFuel flap release switch.
The input voltages (V
in) for BCU digital signals are defined as follows:
lLogic 1 when V
in ≥ 6V.
lLogic 0 when V
in ≤ 2V.
BCU input voltages between 2 and 6 volts are indeterminate and cannot be guaranteed.
Analogue input voltages are measured as a ratio with respect to battery voltage.
Page 1474 of 1672
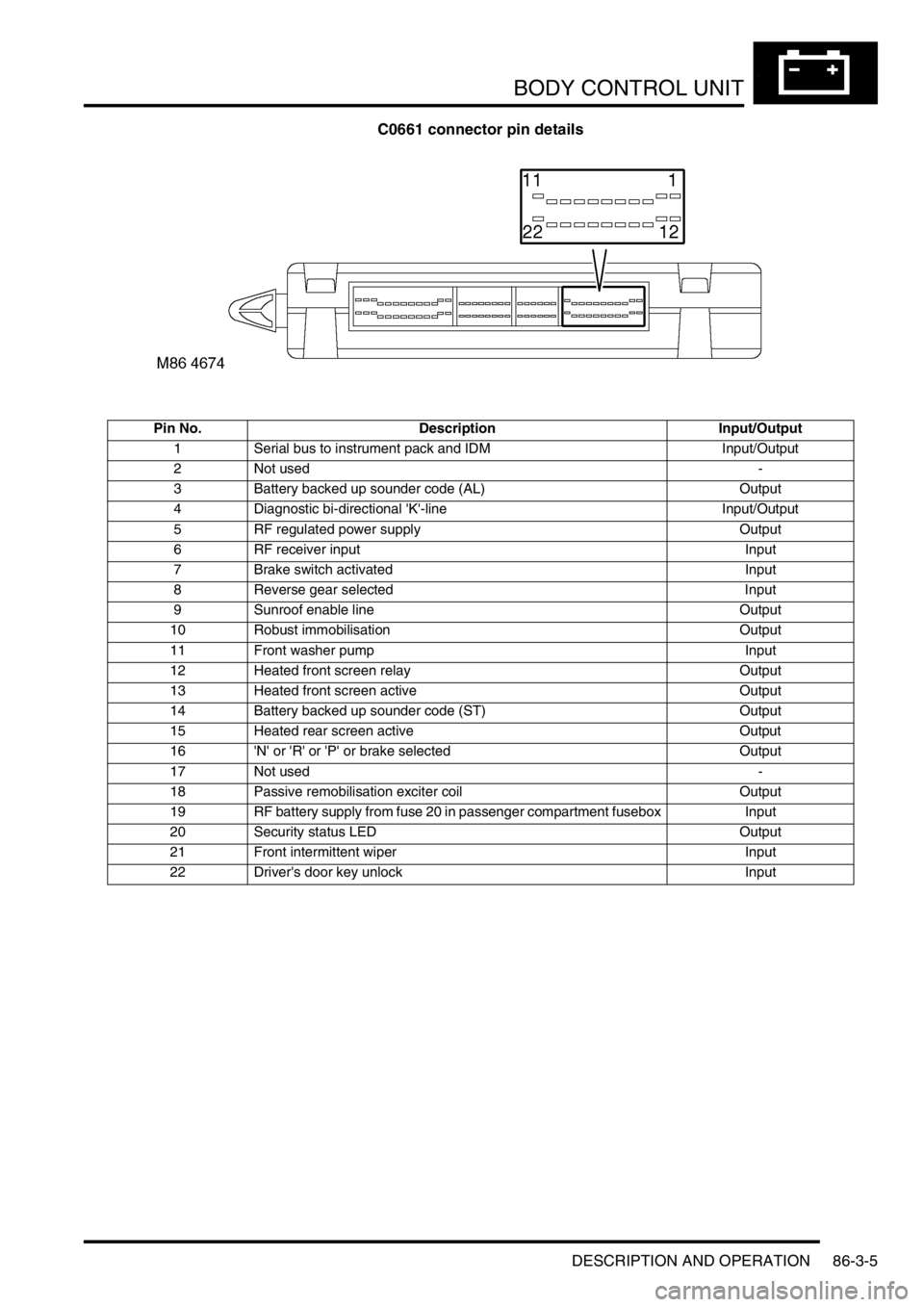
BODY CONTROL UNIT
DESCRIPTION AND OPERATION 86-3-5
C0661 connector pin details
Pin No. Description Input/Output
1 Serial bus to instrument pack and IDM Input/Output
2 Not used-
3 Battery backed up sounder code (AL) Output
4 Diagnostic bi-directional 'K'-line Input/Output
5 RF regulated power supply Output
6 RF receiver input Input
7 Brake switch activated Input
8 Reverse gear selected Input
9 Sunroof enable line Output
10 Robust immobilisation Output
11 Front washer pump Input
12 Heated front screen relay Output
13 Heated front screen active Output
14 Battery backed up sounder code (ST) Output
15 Heated rear screen active Output
16 'N' or 'R' or 'P' or brake selected Output
17 Not used-
18 Passive remobilisation exciter coil Output
19 RF battery supply from fuse 20 in passenger compartment fusebox Input
20 Security status LED Output
21 Front intermittent wiper Input
22 Driver's door key unlock Input
Page 1483 of 1672
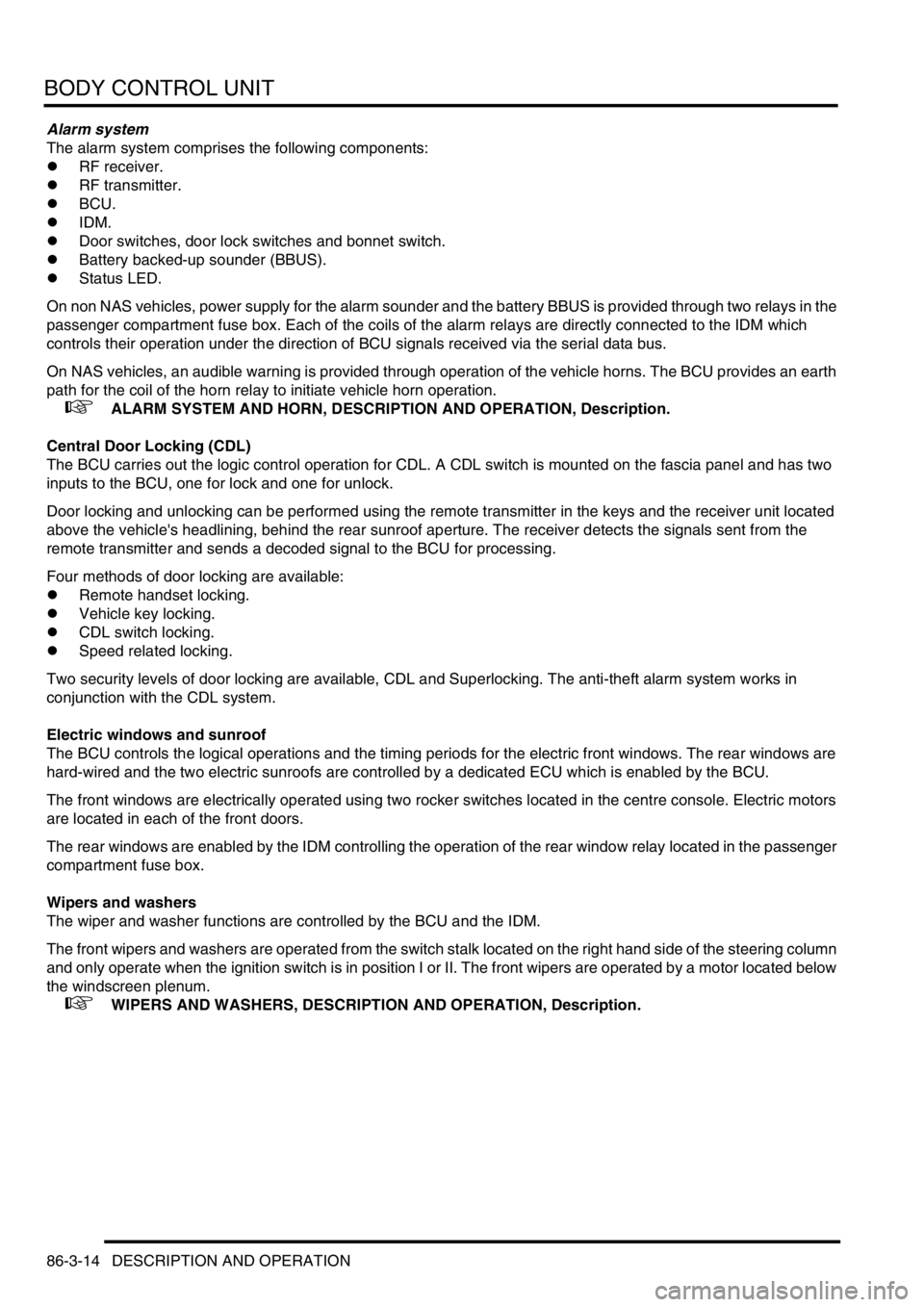
BODY CONTROL UNIT
86-3-14 DESCRIPTION AND OPERATION
Alarm system
The alarm system comprises the following components:
lRF receiver.
lRF transmitter.
lBCU.
lIDM.
lDoor switches, door lock switches and bonnet switch.
lBattery backed-up sounder (BBUS).
lStatus LED.
On non NAS vehicles, power supply for the alarm sounder and the battery BBUS is provided through two relays in the
passenger compartment fuse box. Each of the coils of the alarm relays are directly connected to the IDM which
controls their operation under the direction of BCU signals received via the serial data bus.
On NAS vehicles, an audible warning is provided through operation of the vehicle horns. The BCU provides an earth
path for the coil of the horn relay to initiate vehicle horn operation.
+ ALARM SYSTEM AND HORN, DESCRIPTION AND OPERATION, Description.
Central Door Locking (CDL)
The BCU carries out the logic control operation for CDL. A CDL switch is mounted on the fascia panel and has two
inputs to the BCU, one for lock and one for unlock.
Door locking and unlocking can be performed using the remote transmitter in the keys and the receiver unit located
above the vehicle's headlining, behind the rear sunroof aperture. The receiver detects the signals sent from the
remote transmitter and sends a decoded signal to the BCU for processing.
Four methods of door locking are available:
lRemote handset locking.
lVehicle key locking.
lCDL switch locking.
lSpeed related locking.
Two security levels of door locking are available, CDL and Superlocking. The anti-theft alarm system works in
conjunction with the CDL system.
Electric windows and sunroof
The BCU controls the logical operations and the timing periods for the electric front windows. The rear windows are
hard-wired and the two electric sunroofs are controlled by a dedicated ECU which is enabled by the BCU.
The front windows are electrically operated using two rocker switches located in the centre console. Electric motors
are located in each of the front doors.
The rear windows are enabled by the IDM controlling the operation of the rear window relay located in the passenger
compartment fuse box.
Wipers and washers
The wiper and washer functions are controlled by the BCU and the IDM.
The front wipers and washers are operated from the switch stalk located on the right hand side of the steering column
and only operate when the ignition switch is in position I or II. The front wipers are operated by a motor located below
the windscreen plenum.
+ WIPERS AND WASHERS, DESCRIPTION AND OPERATION, Description.
Page 1484 of 1672
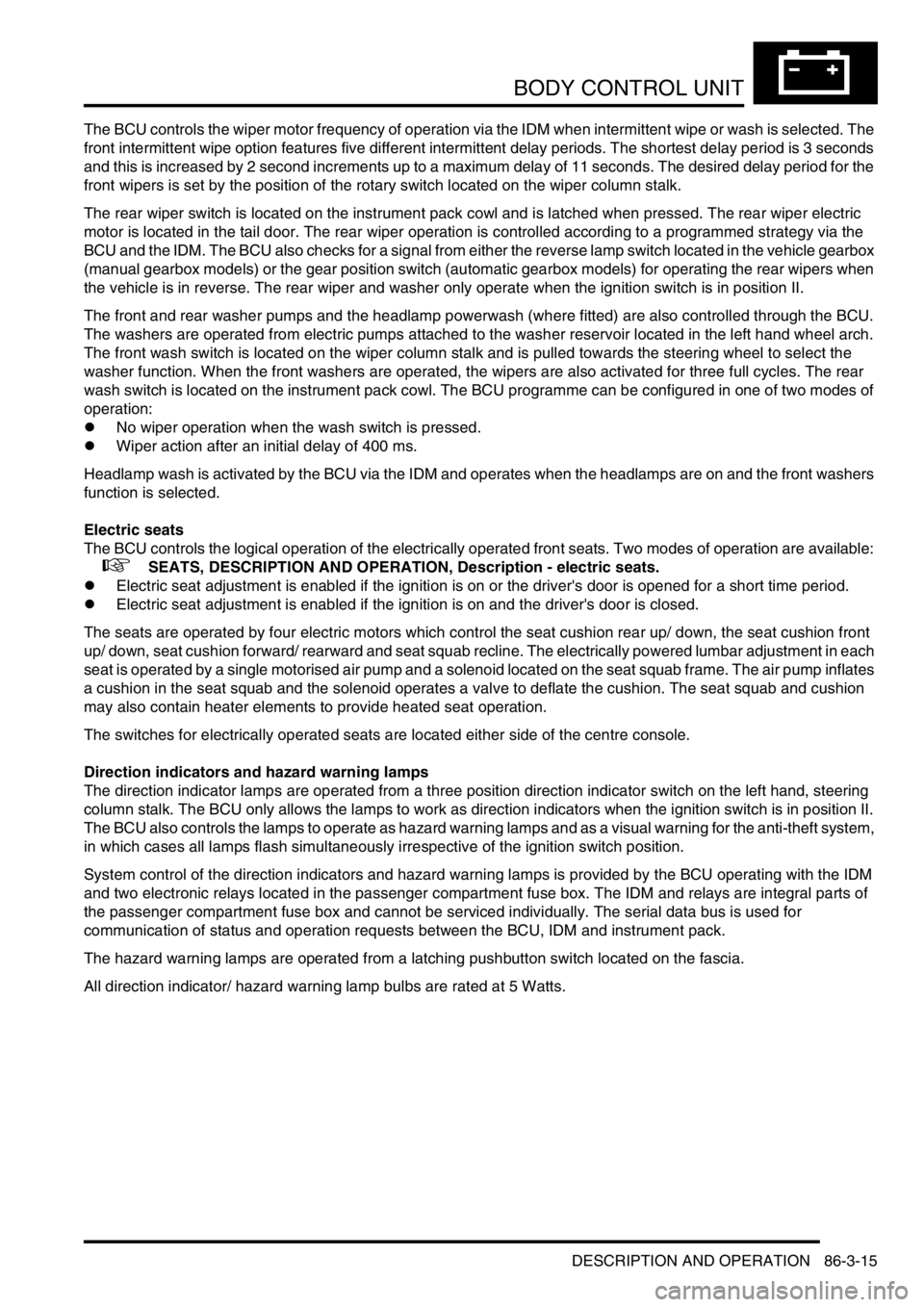
BODY CONTROL UNIT
DESCRIPTION AND OPERATION 86-3-15
The BCU controls the wiper motor frequency of operation via the IDM when intermittent wipe or wash is selected. The
front intermittent wipe option features five different intermittent delay periods. The shortest delay period is 3 seconds
and this is increased by 2 second increments up to a maximum delay of 11 seconds. The desired delay period for the
front wipers is set by the position of the rotary switch located on the wiper column stalk.
The rear wiper switch is located on the instrument pack cowl and is latched when pressed. The rear wiper electric
motor is located in the tail door. The rear wiper operation is controlled according to a programmed strategy via the
BCU and the IDM. The BCU also checks for a signal from either the reverse lamp switch located in the vehicle gearbox
(manual gearbox models) or the gear position switch (automatic gearbox models) for operating the rear wipers when
the vehicle is in reverse. The rear wiper and washer only operate when the ignition switch is in position II.
The front and rear washer pumps and the headlamp powerwash (where fitted) are also controlled through the BCU.
The washers are operated from electric pumps attached to the washer reservoir located in the left hand wheel arch.
The front wash switch is located on the wiper column stalk and is pulled towards the steering wheel to select the
washer function. When the front washers are operated, the wipers are also activated for three full cycles. The rear
wash switch is located on the instrument pack cowl. The BCU programme can be configured in one of two modes of
operation:
lNo wiper operation when the wash switch is pressed.
lWiper action after an initial delay of 400 ms.
Headlamp wash is activated by the BCU via the IDM and operates when the headlamps are on and the front washers
function is selected.
Electric seats
The BCU controls the logical operation of the electrically operated front seats. Two modes of operation are available:
+ SEATS, DESCRIPTION AND OPERATION, Description - electric seats.
lElectric seat adjustment is enabled if the ignition is on or the driver's door is opened for a short time period.
lElectric seat adjustment is enabled if the ignition is on and the driver's door is closed.
The seats are operated by four electric motors which control the seat cushion rear up/ down, the seat cushion front
up/ down, seat cushion forward/ rearward and seat squab recline. The electrically powered lumbar adjustment in each
seat is operated by a single motorised air pump and a solenoid located on the seat squab frame. The air pump inflates
a cushion in the seat squab and the solenoid operates a valve to deflate the cushion. The seat squab and cushion
may also contain heater elements to provide heated seat operation.
The switches for electrically operated seats are located either side of the centre console.
Direction indicators and hazard warning lamps
The direction indicator lamps are operated from a three position direction indicator switch on the left hand, steering
column stalk. The BCU only allows the lamps to work as direction indicators when the ignition switch is in position II.
The BCU also controls the lamps to operate as hazard warning lamps and as a visual warning for the anti-theft system,
in which cases all lamps flash simultaneously irrespective of the ignition switch position.
System control of the direction indicators and hazard warning lamps is provided by the BCU operating with the IDM
and two electronic relays located in the passenger compartment fuse box. The IDM and relays are integral parts of
the passenger compartment fuse box and cannot be serviced individually. The serial data bus is used for
communication of status and operation requests between the BCU, IDM and instrument pack.
The hazard warning lamps are operated from a latching pushbutton switch located on the fascia.
All direction indicator/ hazard warning lamp bulbs are rated at 5 Watts.