fuse box LAND ROVER DISCOVERY 2002 Owner's Manual
[x] Cancel search | Manufacturer: LAND ROVER, Model Year: 2002, Model line: DISCOVERY, Model: LAND ROVER DISCOVERY 2002Pages: 1672, PDF Size: 46.1 MB
Page 472 of 1672
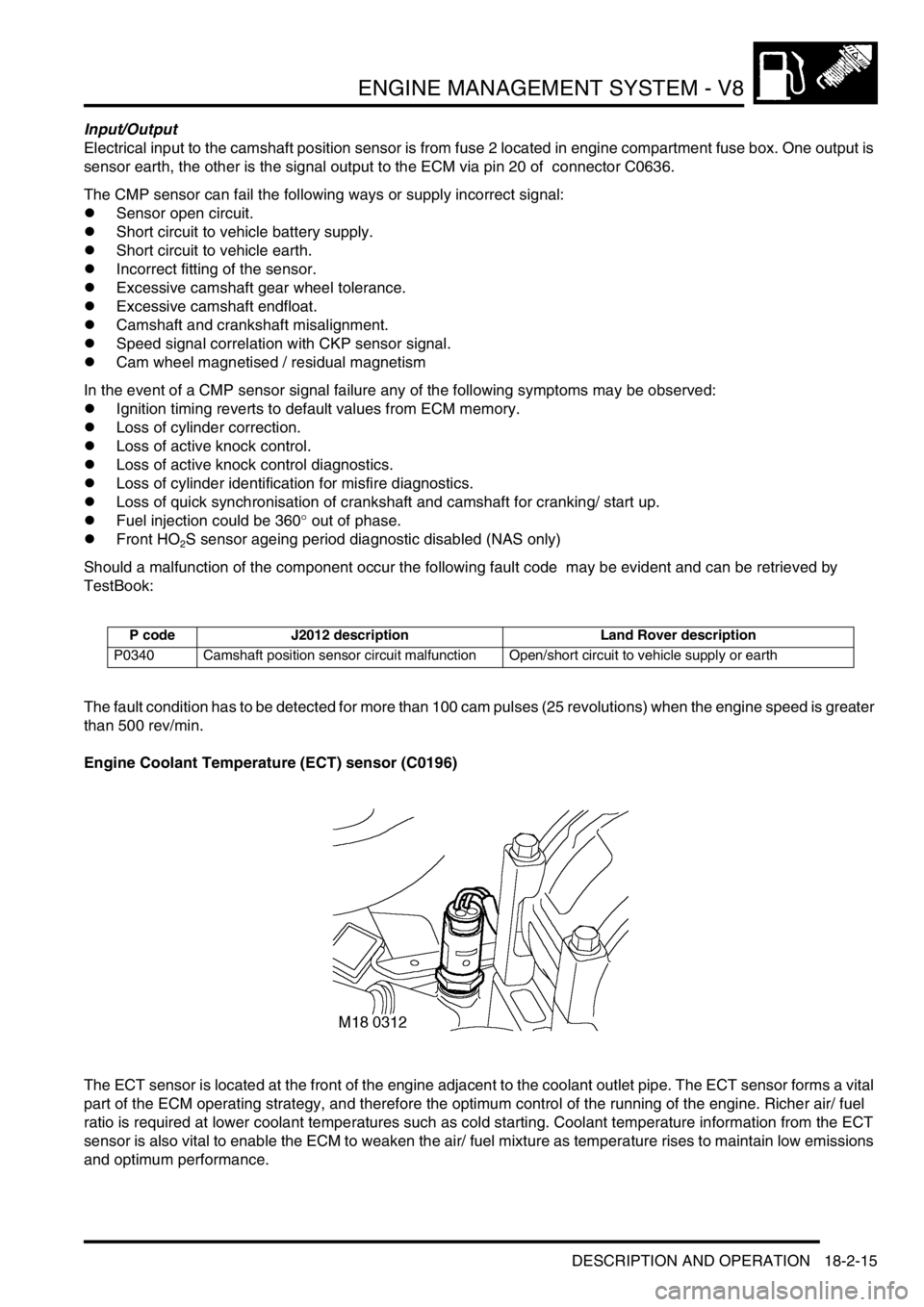
ENGINE MANAGEMENT SYSTEM - V8
DESCRIPTION AND OPERATION 18-2-15
Input/Output
Electrical input to the camshaft position sensor is from fuse 2 located in engine compartment fuse box. One output is
sensor earth, the other is the signal output to the ECM via pin 20 of connector C0636.
The CMP sensor can fail the following ways or supply incorrect signal:
lSensor open circuit.
lShort circuit to vehicle battery supply.
lShort circuit to vehicle earth.
lIncorrect fitting of the sensor.
lExcessive camshaft gear wheel tolerance.
lExcessive camshaft endfloat.
lCamshaft and crankshaft misalignment.
lSpeed signal correlation with CKP sensor signal.
lCam wheel magnetised / residual magnetism
In the event of a CMP sensor signal failure any of the following symptoms may be observed:
lIgnition timing reverts to default values from ECM memory.
lLoss of cylinder correction.
lLoss of active knock control.
lLoss of active knock control diagnostics.
lLoss of cylinder identification for misfire diagnostics.
lLoss of quick synchronisation of crankshaft and camshaft for cranking/ start up.
lFuel injection could be 360
° out of phase.
lFront HO
2S sensor ageing period diagnostic disabled (NAS only)
Should a malfunction of the component occur the following fault code may be evident and can be retrieved by
TestBook:
The fault condition has to be detected for more than 100 cam pulses (25 revolutions) when the engine speed is greater
than 500 rev/min.
Engine Coolant Temperature (ECT) sensor (C0196)
The ECT sensor is located at the front of the engine adjacent to the coolant outlet pipe. The ECT sensor forms a vital
part of the ECM operating strategy, and therefore the optimum control of the running of the engine. Richer air/ fuel
ratio is required at lower coolant temperatures such as cold starting. Coolant temperature information from the ECT
sensor is also vital to enable the ECM to weaken the air/ fuel mixture as temperature rises to maintain low emissions
and optimum performance.
P code J2012 description Land Rover description
P0340 Camshaft position sensor circuit malfunction Open/short circuit to vehicle supply or earth
Page 477 of 1672

ENGINE MANAGEMENT SYSTEM - V8
18-2-20 DESCRIPTION AND OPERATION
Should a malfunction occur, the following fault codes may be evident and can be retrieved by TestBook:
Mass Air Flow (MAF)/ Inlet Air Temperature (IAT) sensor (C0149)
The MAF/ IAT sensors are combined into a single unit and located between the air filter housing and the inlet manifold.
The ECM receives input signals from the MAF/ IAT sensor to calculate the mass of air flowing into the engine inlet
manifold.
Input/Output
The MAF sensor has both electrical input and output. Input to the MAF sensor comes from two different sources.
Battery voltage is supplied to the MAF sensor via fuse 2 of the engine compartment fuse box. The MAF sensor also
utilises a 5 volt reference input via pin 7 of connector C0636 of the ECM. The MAF sensor output voltage is measured
via pin 23 of connector C0636 of the ECM.
The IAT sensor has only electrical output. Output from the IAT sensor is measured at pin 34 of connector C0636 of
the ECM, this is a variable voltage/ resistance measured by the sensor to provide air temperature information to the
ECM.
The MAF/ IAT sensor share the same sensor earth. Sensor earth is via pin 9 of connector C0636 of the ECM.
The MAF/ IAT sensor and its connector has silver plated terminals for its low current signals to protect against
corrosion. DO NOT apply 12V to the 5V supply, as this will destroy the internal circuitry. The MAF/IAT sensor should
not be dropped or roughly handled and should be kept free from contamination.
P code J2012 description Land Rover description
P1117 Radiator outlet temperature
thermister lowThermostat reading below -33 °C (-
27 °F)
P1118 Radiator outlet temperature
thermister highThermostat reading above 140 °C
(284 °F)
P0126 Engine thermostat defective Difference in radiator and engine
coolant temperatures too small
Page 484 of 1672
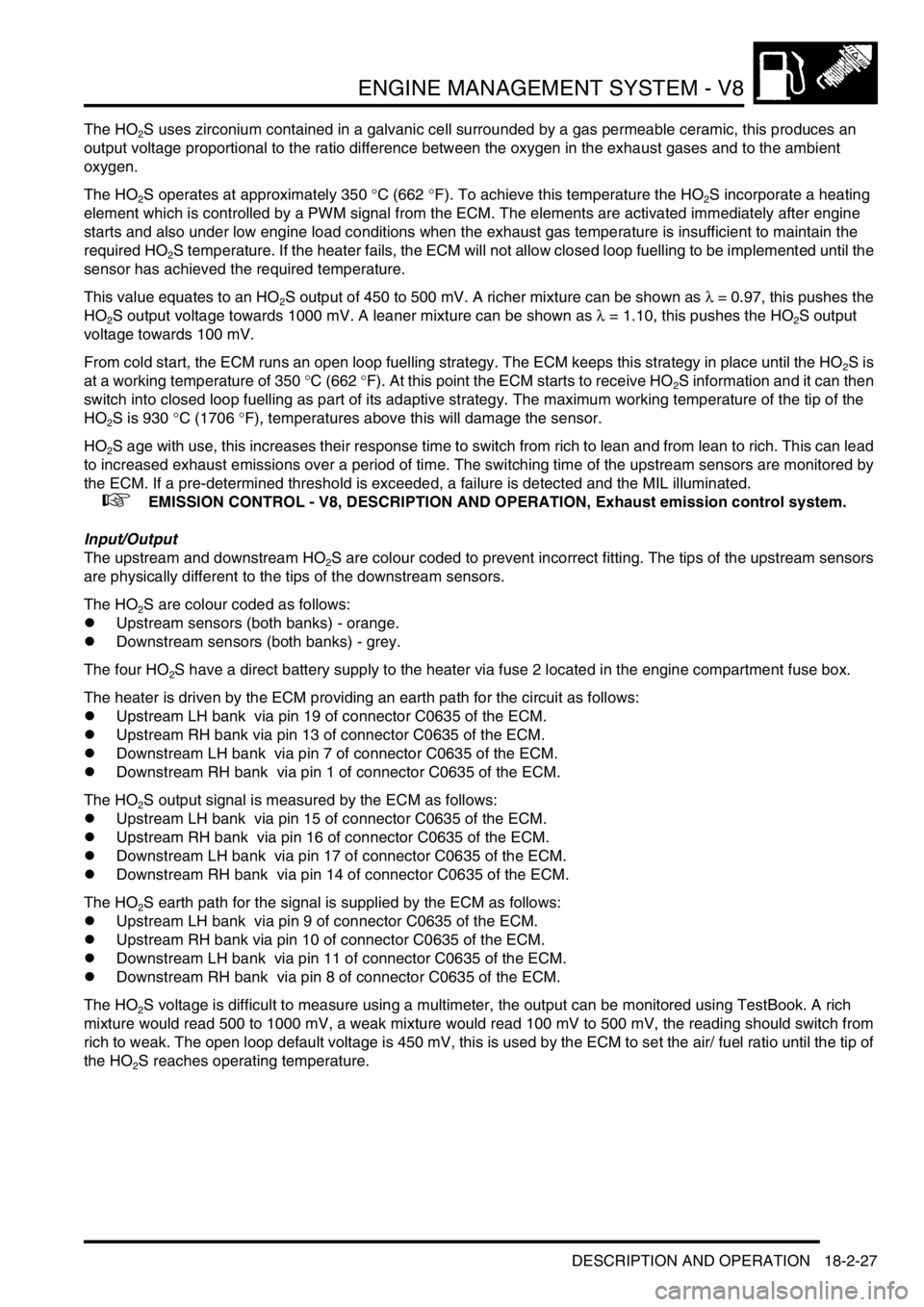
ENGINE MANAGEMENT SYSTEM - V8
DESCRIPTION AND OPERATION 18-2-27
The HO2S uses zirconium contained in a galvanic cell surrounded by a gas permeable ceramic, this produces an
output voltage proportional to the ratio difference between the oxygen in the exhaust gases and to the ambient
oxygen.
The HO
2S operates at approximately 350 °C (662 °F). To achieve this temperature the HO2S incorporate a heating
element which is controlled by a PWM signal from the ECM. The elements are activated immediately after engine
starts and also under low engine load conditions when the exhaust gas temperature is insufficient to maintain the
required HO
2S temperature. If the heater fails, the ECM will not allow closed loop fuelling to be implemented until the
sensor has achieved the required temperature.
This value equates to an HO
2S output of 450 to 500 mV. A richer mixture can be shown as λ = 0.97, this pushes the
HO
2S output voltage towards 1000 mV. A leaner mixture can be shown as λ = 1.10, this pushes the HO2S output
voltage towards 100 mV.
From cold start, the ECM runs an open loop fuelling strategy. The ECM keeps this strategy in place until the HO
2S is
at a working temperature of 350
°C (662 °F). At this point the ECM starts to receive HO2S information and it can then
switch into closed loop fuelling as part of its adaptive strategy. The maximum working temperature of the tip of the
HO
2S is 930 °C (1706 °F), temperatures above this will damage the sensor.
HO
2S age with use, this increases their response time to switch from rich to lean and from lean to rich. This can lead
to increased exhaust emissions over a period of time. The switching time of the upstream sensors are monitored by
the ECM. If a pre-determined threshold is exceeded, a failure is detected and the MIL illuminated.
+ EMISSION CONTROL - V8, DESCRIPTION AND OPERATION, Exhaust emission control system.
Input/Output
The upstream and downstream HO
2S are colour coded to prevent incorrect fitting. The tips of the upstream sensors
are physically different to the tips of the downstream sensors.
The HO
2S are colour coded as follows:
lUpstream sensors (both banks) - orange.
lDownstream sensors (both banks) - grey.
The four HO
2S have a direct battery supply to the heater via fuse 2 located in the engine compartment fuse box.
The heater is driven by the ECM providing an earth path for the circuit as follows:
lUpstream LH bank via pin 19 of connector C0635 of the ECM.
lUpstream RH bank via pin 13 of connector C0635 of the ECM.
lDownstream LH bank via pin 7 of connector C0635 of the ECM.
lDownstream RH bank via pin 1 of connector C0635 of the ECM.
The HO
2S output signal is measured by the ECM as follows:
lUpstream LH bank via pin 15 of connector C0635 of the ECM.
lUpstream RH bank via pin 16 of connector C0635 of the ECM.
lDownstream LH bank via pin 17 of connector C0635 of the ECM.
lDownstream RH bank via pin 14 of connector C0635 of the ECM.
The HO
2S earth path for the signal is supplied by the ECM as follows:
lUpstream LH bank via pin 9 of connector C0635 of the ECM.
lUpstream RH bank via pin 10 of connector C0635 of the ECM.
lDownstream LH bank via pin 11 of connector C0635 of the ECM.
lDownstream RH bank via pin 8 of connector C0635 of the ECM.
The HO
2S voltage is difficult to measure using a multimeter, the output can be monitored using TestBook. A rich
mixture would read 500 to 1000 mV, a weak mixture would read 100 mV to 500 mV, the reading should switch from
rich to weak. The open loop default voltage is 450 mV, this is used by the ECM to set the air/ fuel ratio until the tip of
the HO
2S reaches operating temperature.
Page 487 of 1672
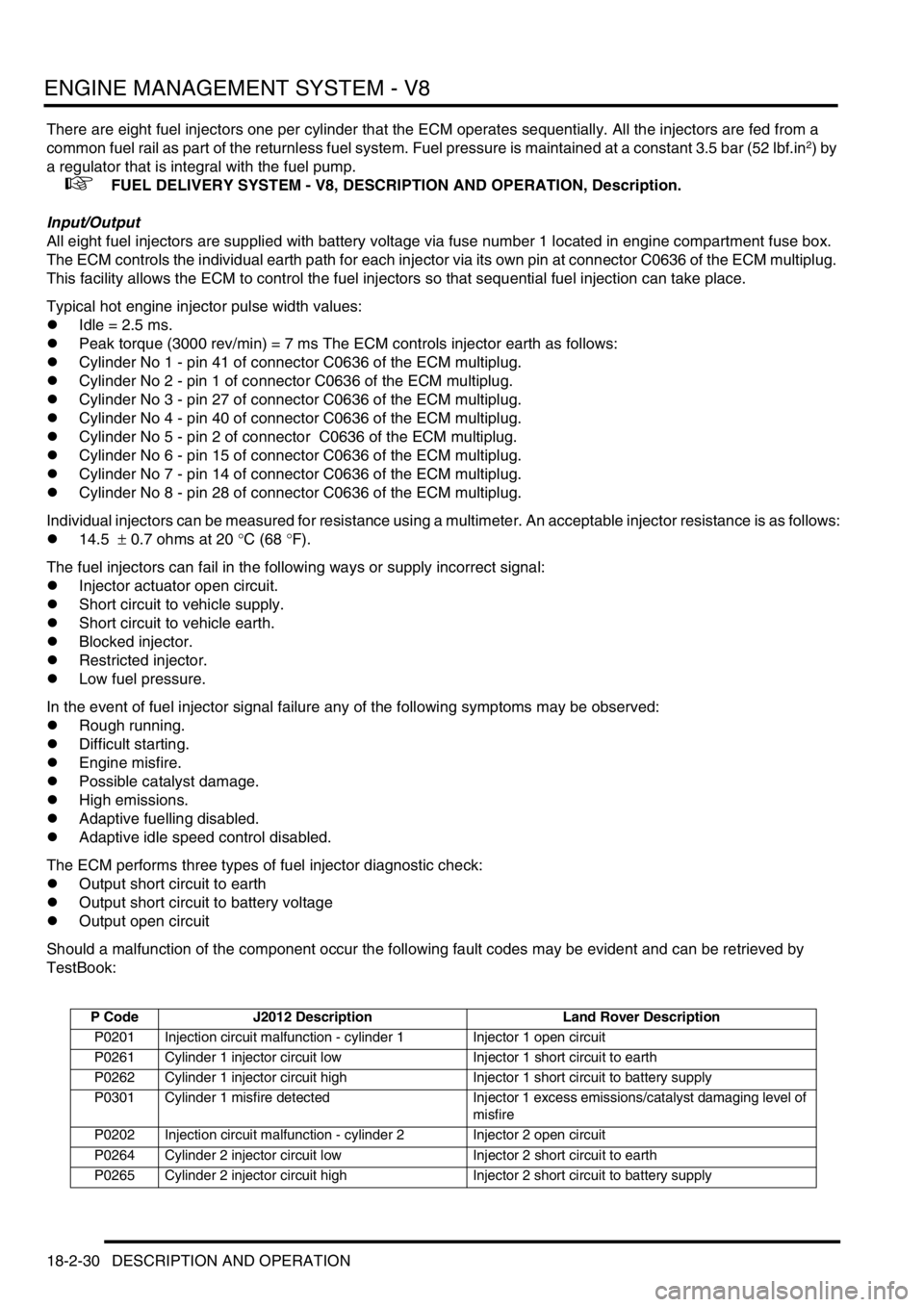
ENGINE MANAGEMENT SYSTEM - V8
18-2-30 DESCRIPTION AND OPERATION
There are eight fuel injectors one per cylinder that the ECM operates sequentially. All the injectors are fed from a
common fuel rail as part of the returnless fuel system. Fuel pressure is maintained at a constant 3.5 bar (52 lbf.in2) by
a regulator that is integral with the fuel pump.
+ FUEL DELIVERY SYSTEM - V8, DESCRIPTION AND OPERATION, Description.
Input/Output
All eight fuel injectors are supplied with battery voltage via fuse number 1 located in engine compartment fuse box.
The ECM controls the individual earth path for each injector via its own pin at connector C0636 of the ECM multiplug.
This facility allows the ECM to control the fuel injectors so that sequential fuel injection can take place.
Typical hot engine injector pulse width values:
lIdle = 2.5 ms.
lPeak torque (3000 rev/min) = 7 ms The ECM controls injector earth as follows:
lCylinder No 1 - pin 41 of connector C0636 of the ECM multiplug.
lCylinder No 2 - pin 1 of connector C0636 of the ECM multiplug.
lCylinder No 3 - pin 27 of connector C0636 of the ECM multiplug.
lCylinder No 4 - pin 40 of connector C0636 of the ECM multiplug.
lCylinder No 5 - pin 2 of connector C0636 of the ECM multiplug.
lCylinder No 6 - pin 15 of connector C0636 of the ECM multiplug.
lCylinder No 7 - pin 14 of connector C0636 of the ECM multiplug.
lCylinder No 8 - pin 28 of connector C0636 of the ECM multiplug.
Individual injectors can be measured for resistance using a multimeter. An acceptable injector resistance is as follows:
l14.5
± 0.7 ohms at 20 °C (68 °F).
The fuel injectors can fail in the following ways or supply incorrect signal:
lInjector actuator open circuit.
lShort circuit to vehicle supply.
lShort circuit to vehicle earth.
lBlocked injector.
lRestricted injector.
lLow fuel pressure.
In the event of fuel injector signal failure any of the following symptoms may be observed:
lRough running.
lDifficult starting.
lEngine misfire.
lPossible catalyst damage.
lHigh emissions.
lAdaptive fuelling disabled.
lAdaptive idle speed control disabled.
The ECM performs three types of fuel injector diagnostic check:
lOutput short circuit to earth
lOutput short circuit to battery voltage
lOutput open circuit
Should a malfunction of the component occur the following fault codes may be evident and can be retrieved by
TestBook:
P Code J2012 Description Land Rover Description
P0201 Injection circuit malfunction - cylinder 1 Injector 1 open circuit
P0261 Cylinder 1 injector circuit low Injector 1 short circuit to earth
P0262 Cylinder 1 injector circuit high Injector 1 short circuit to battery supply
P0301 Cylinder 1 misfire detected Injector 1 excess emissions/catalyst damaging level of
misfire
P0202 Injection circuit malfunction - cylinder 2 Injector 2 open circuit
P0264 Cylinder 2 injector circuit low Injector 2 short circuit to earth
P0265 Cylinder 2 injector circuit high Injector 2 short circuit to battery supply
Page 489 of 1672
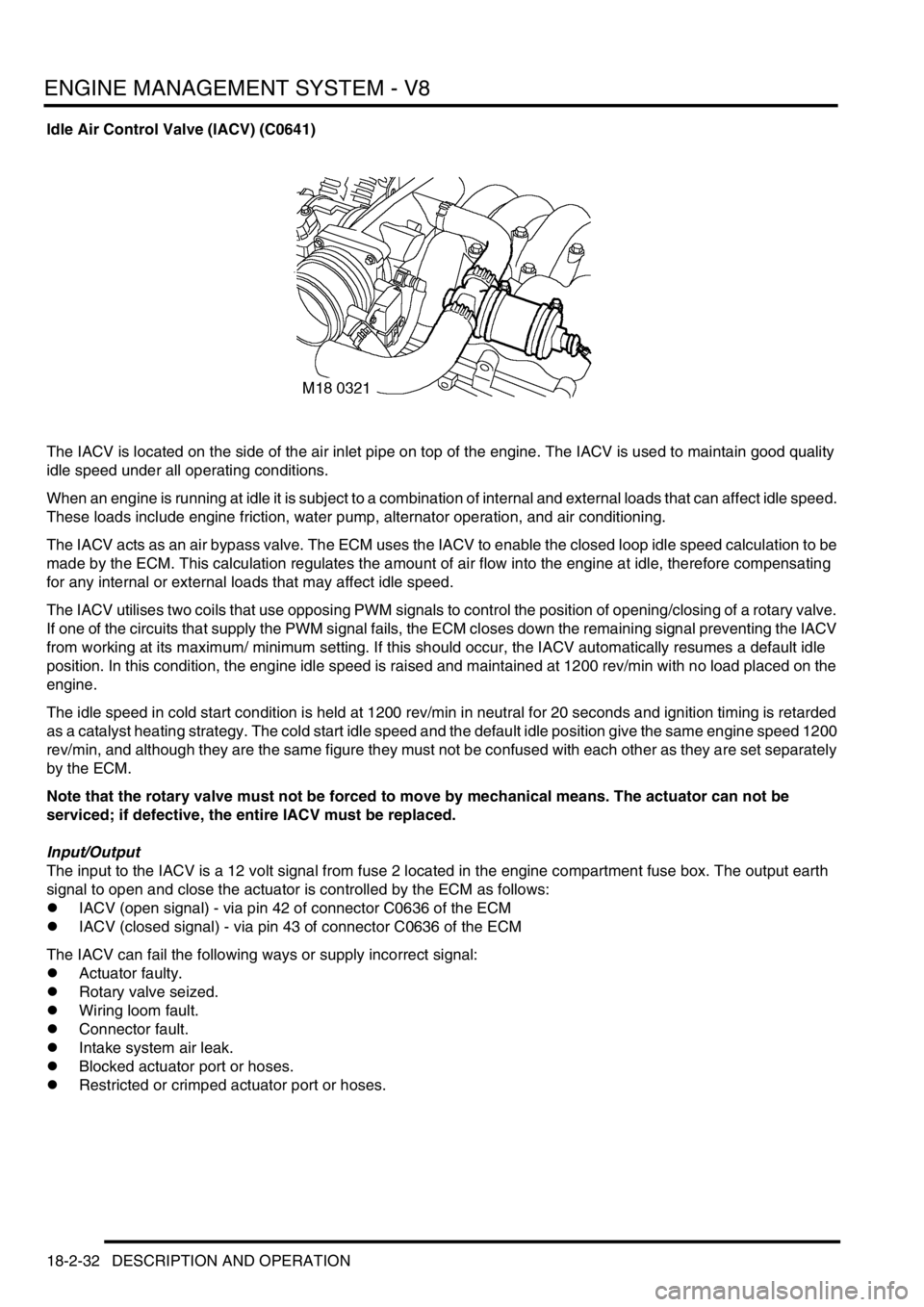
ENGINE MANAGEMENT SYSTEM - V8
18-2-32 DESCRIPTION AND OPERATION
Idle Air Control Valve (IACV) (C0641)
The IACV is located on the side of the air inlet pipe on top of the engine. The IACV is used to maintain good quality
idle speed under all operating conditions.
When an engine is running at idle it is subject to a combination of internal and external loads that can affect idle speed.
These loads include engine friction, water pump, alternator operation, and air conditioning.
The IACV acts as an air bypass valve. The ECM uses the IACV to enable the closed loop idle speed calculation to be
made by the ECM. This calculation regulates the amount of air flow into the engine at idle, therefore compensating
for any internal or external loads that may affect idle speed.
The IACV utilises two coils that use opposing PWM signals to control the position of opening/closing of a rotary valve.
If one of the circuits that supply the PWM signal fails, the ECM closes down the remaining signal preventing the IACV
from working at its maximum/ minimum setting. If this should occur, the IACV automatically resumes a default idle
position. In this condition, the engine idle speed is raised and maintained at 1200 rev/min with no load placed on the
engine.
The idle speed in cold start condition is held at 1200 rev/min in neutral for 20 seconds and ignition timing is retarded
as a catalyst heating strategy. The cold start idle speed and the default idle position give the same engine speed 1200
rev/min, and although they are the same figure they must not be confused with each other as they are set separately
by the ECM.
Note that the rotary valve must not be forced to move by mechanical means. The actuator can not be
serviced; if defective, the entire IACV must be replaced.
Input/Output
The input to the IACV is a 12 volt signal from fuse 2 located in the engine compartment fuse box. The output earth
signal to open and close the actuator is controlled by the ECM as follows:
lIACV (open signal) - via pin 42 of connector C0636 of the ECM
lIACV (closed signal) - via pin 43 of connector C0636 of the ECM
The IACV can fail the following ways or supply incorrect signal:
lActuator faulty.
lRotary valve seized.
lWiring loom fault.
lConnector fault.
lIntake system air leak.
lBlocked actuator port or hoses.
lRestricted or crimped actuator port or hoses.
Page 490 of 1672
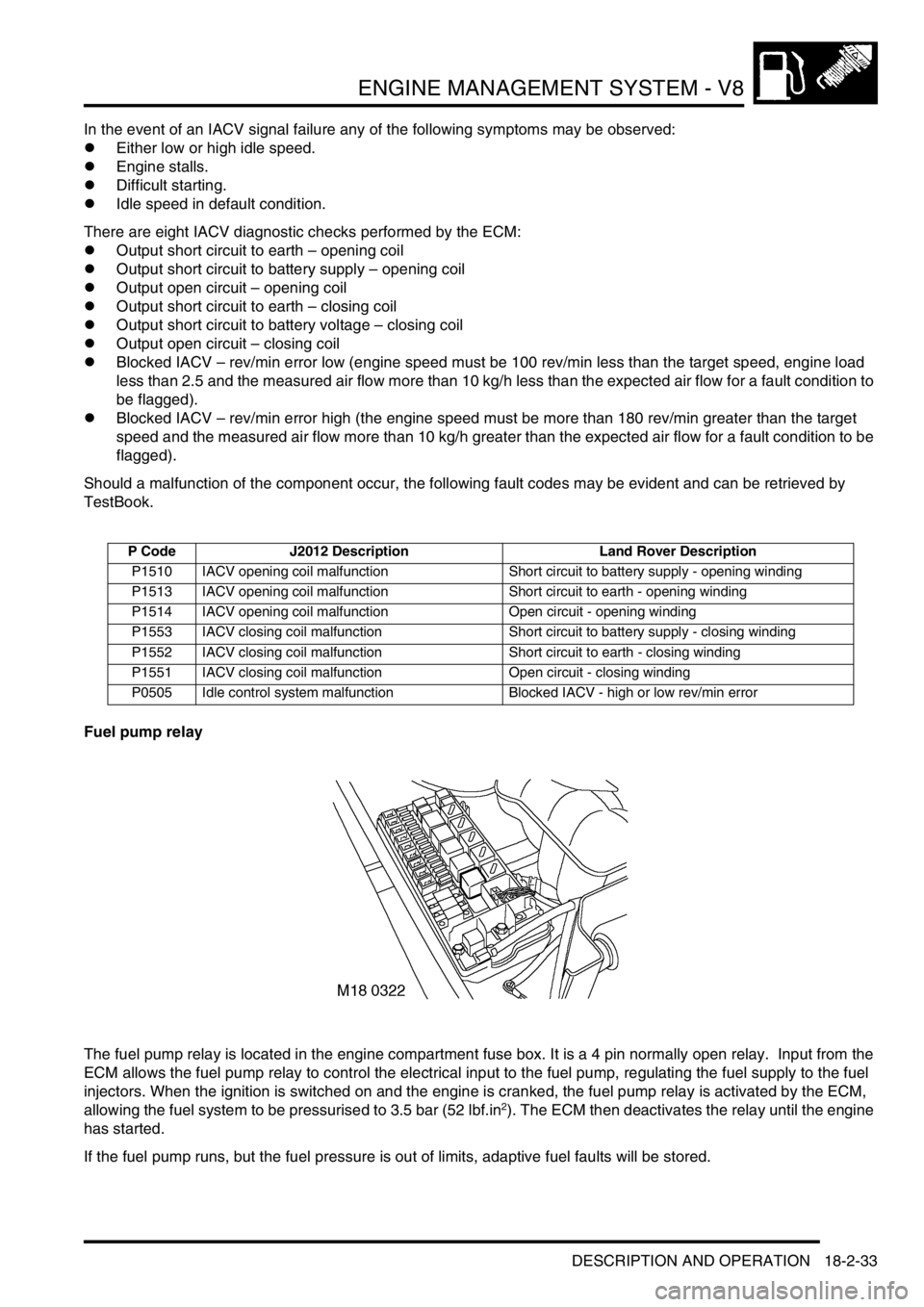
ENGINE MANAGEMENT SYSTEM - V8
DESCRIPTION AND OPERATION 18-2-33
In the event of an IACV signal failure any of the following symptoms may be observed:
lEither low or high idle speed.
lEngine stalls.
lDifficult starting.
lIdle speed in default condition.
There are eight IACV diagnostic checks performed by the ECM:
lOutput short circuit to earth – opening coil
lOutput short circuit to battery supply – opening coil
lOutput open circuit – opening coil
lOutput short circuit to earth – closing coil
lOutput short circuit to battery voltage – closing coil
lOutput open circuit – closing coil
lBlocked IACV – rev/min error low (engine speed must be 100 rev/min less than the target speed, engine load
less than 2.5 and the measured air flow more than 10 kg/h less than the expected air flow for a fault condition to
be flagged).
lBlocked IACV – rev/min error high (the engine speed must be more than 180 rev/min greater than the target
speed and the measured air flow more than 10 kg/h greater than the expected air flow for a fault condition to be
flagged).
Should a malfunction of the component occur, the following fault codes may be evident and can be retrieved by
TestBook.
Fuel pump relay
The fuel pump relay is located in the engine compartment fuse box. It is a 4 pin normally open relay. Input from the
ECM allows the fuel pump relay to control the electrical input to the fuel pump, regulating the fuel supply to the fuel
injectors. When the ignition is switched on and the engine is cranked, the fuel pump relay is activated by the ECM,
allowing the fuel system to be pressurised to 3.5 bar (52 lbf.in
2). The ECM then deactivates the relay until the engine
has started.
If the fuel pump runs, but the fuel pressure is out of limits, adaptive fuel faults will be stored.
P Code J2012 Description Land Rover Description
P1510 IACV opening coil malfunction Short circuit to battery supply - opening winding
P1513 IACV opening coil malfunction Short circuit to earth - opening winding
P1514 IACV opening coil malfunction Open circuit - opening winding
P1553 IACV closing coil malfunction Short circuit to battery supply - closing winding
P1552 IACV closing coil malfunction Short circuit to earth - closing winding
P1551 IACV closing coil malfunction Open circuit - closing winding
P0505 Idle control system malfunction Blocked IACV - high or low rev/min error
Page 491 of 1672
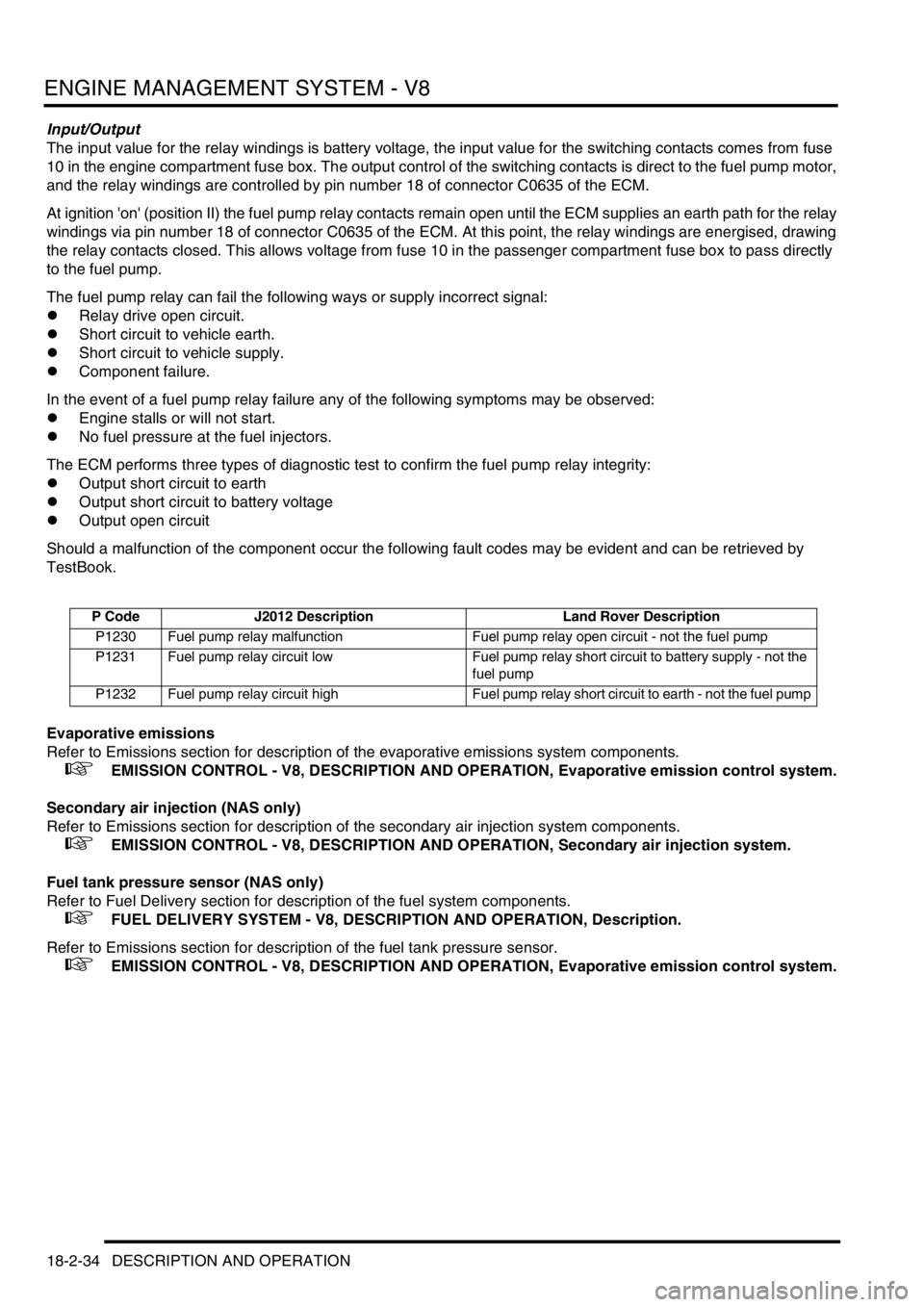
ENGINE MANAGEMENT SYSTEM - V8
18-2-34 DESCRIPTION AND OPERATION
Input/Output
The input value for the relay windings is battery voltage, the input value for the switching contacts comes from fuse
10 in the engine compartment fuse box. The output control of the switching contacts is direct to the fuel pump motor,
and the relay windings are controlled by pin number 18 of connector C0635 of the ECM.
At ignition 'on' (position II) the fuel pump relay contacts remain open until the ECM supplies an earth path for the relay
windings via pin number 18 of connector C0635 of the ECM. At this point, the relay windings are energised, drawing
the relay contacts closed. This allows voltage from fuse 10 in the passenger compartment fuse box to pass directly
to the fuel pump.
The fuel pump relay can fail the following ways or supply incorrect signal:
lRelay drive open circuit.
lShort circuit to vehicle earth.
lShort circuit to vehicle supply.
lComponent failure.
In the event of a fuel pump relay failure any of the following symptoms may be observed:
lEngine stalls or will not start.
lNo fuel pressure at the fuel injectors.
The ECM performs three types of diagnostic test to confirm the fuel pump relay integrity:
lOutput short circuit to earth
lOutput short circuit to battery voltage
lOutput open circuit
Should a malfunction of the component occur the following fault codes may be evident and can be retrieved by
TestBook.
Evaporative emissions
Refer to Emissions section for description of the evaporative emissions system components.
+ EMISSION CONTROL - V8, DESCRIPTION AND OPERATION, Evaporative emission control system.
Secondary air injection (NAS only)
Refer to Emissions section for description of the secondary air injection system components.
+ EMISSION CONTROL - V8, DESCRIPTION AND OPERATION, Secondary air injection system.
Fuel tank pressure sensor (NAS only)
Refer to Fuel Delivery section for description of the fuel system components.
+ FUEL DELIVERY SYSTEM - V8, DESCRIPTION AND OPERATION, Description.
Refer to Emissions section for description of the fuel tank pressure sensor.
+ EMISSION CONTROL - V8, DESCRIPTION AND OPERATION, Evaporative emission control system.
P Code J2012 Description Land Rover Description
P1230 Fuel pump relay malfunction Fuel pump relay open circuit - not the fuel pump
P1231 Fuel pump relay circuit low Fuel pump relay short circuit to battery supply - not the
fuel pump
P1232 Fuel pump relay circuit high Fuel pump relay short circuit to earth - not the fuel pump
Page 492 of 1672
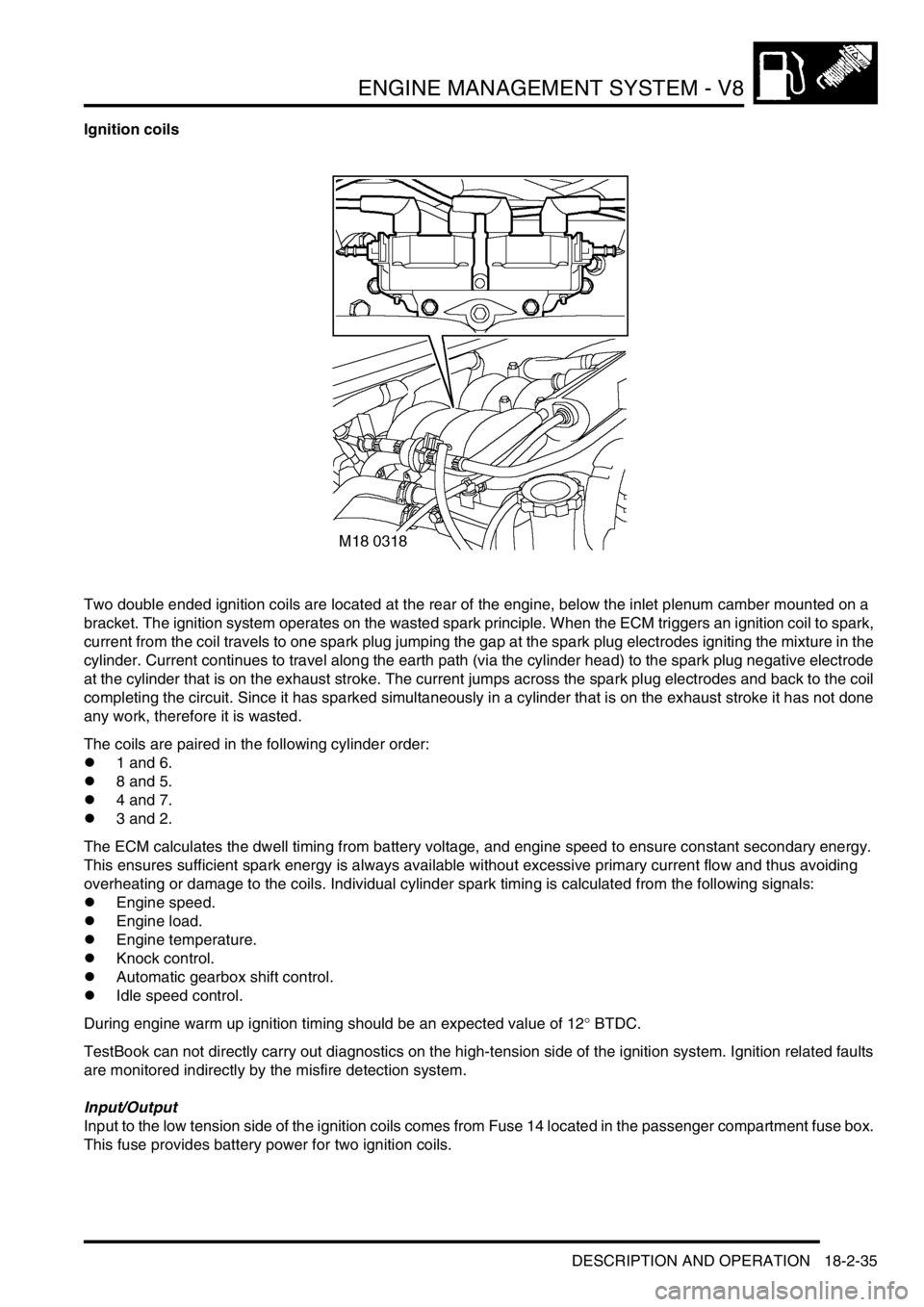
ENGINE MANAGEMENT SYSTEM - V8
DESCRIPTION AND OPERATION 18-2-35
Ignition coils
Two double ended ignition coils are located at the rear of the engine, below the inlet plenum camber mounted on a
bracket. The ignition system operates on the wasted spark principle. When the ECM triggers an ignition coil to spark,
current from the coil travels to one spark plug jumping the gap at the spark plug electrodes igniting the mixture in the
cylinder. Current continues to travel along the earth path (via the cylinder head) to the spark plug negative electrode
at the cylinder that is on the exhaust stroke. The current jumps across the spark plug electrodes and back to the coil
completing the circuit. Since it has sparked simultaneously in a cylinder that is on the exhaust stroke it has not done
any work, therefore it is wasted.
The coils are paired in the following cylinder order:
l1 and 6.
l8 and 5.
l4 and 7.
l3 and 2.
The ECM calculates the dwell timing from battery voltage, and engine speed to ensure constant secondary energy.
This ensures sufficient spark energy is always available without excessive primary current flow and thus avoiding
overheating or damage to the coils. Individual cylinder spark timing is calculated from the following signals:
lEngine speed.
lEngine load.
lEngine temperature.
lKnock control.
lAutomatic gearbox shift control.
lIdle speed control.
During engine warm up ignition timing should be an expected value of 12
° BTDC.
TestBook can not directly carry out diagnostics on the high-tension side of the ignition system. Ignition related faults
are monitored indirectly by the misfire detection system.
Input/Output
Input to the low tension side of the ignition coils comes from Fuse 14 located in the passenger compartment fuse box.
This fuse provides battery power for two ignition coils.
Page 497 of 1672
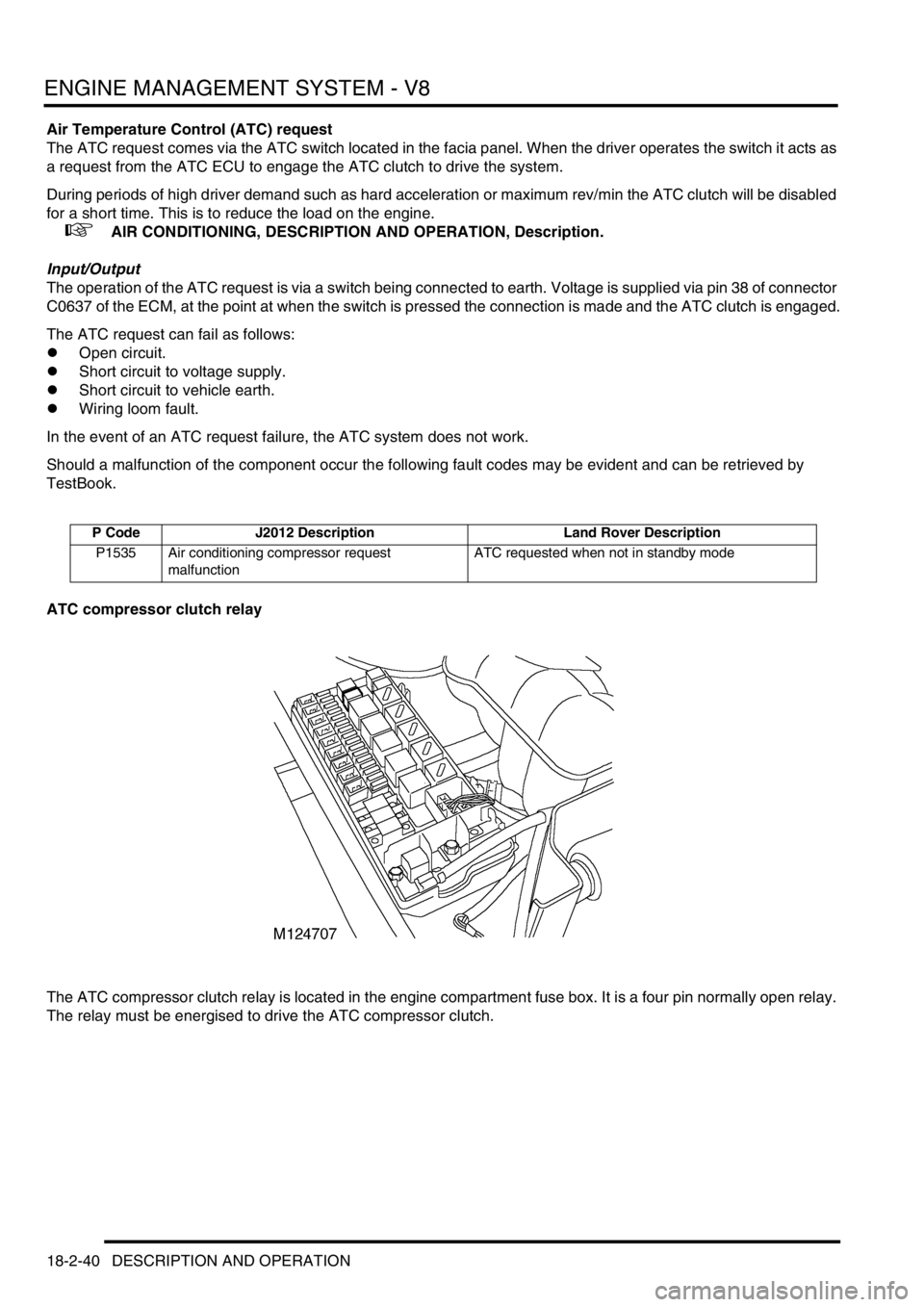
ENGINE MANAGEMENT SYSTEM - V8
18-2-40 DESCRIPTION AND OPERATION
Air Temperature Control (ATC) request
The ATC request comes via the ATC switch located in the facia panel. When the driver operates the switch it acts as
a request from the ATC ECU to engage the ATC clutch to drive the system.
During periods of high driver demand such as hard acceleration or maximum rev/min the ATC clutch will be disabled
for a short time. This is to reduce the load on the engine.
+ AIR CONDITIONING, DESCRIPTION AND OPERATION, Description.
Input/Output
The operation of the ATC request is via a switch being connected to earth. Voltage is supplied via pin 38 of connector
C0637 of the ECM, at the point at when the switch is pressed the connection is made and the ATC clutch is engaged.
The ATC request can fail as follows:
lOpen circuit.
lShort circuit to voltage supply.
lShort circuit to vehicle earth.
lWiring loom fault.
In the event of an ATC request failure, the ATC system does not work.
Should a malfunction of the component occur the following fault codes may be evident and can be retrieved by
TestBook.
ATC compressor clutch relay
The ATC compressor clutch relay is located in the engine compartment fuse box. It is a four pin normally open relay.
The relay must be energised to drive the ATC compressor clutch.
P Code J2012 Description Land Rover Description
P1535 Air conditioning compressor request
malfunctionATC requested when not in standby mode
Page 498 of 1672
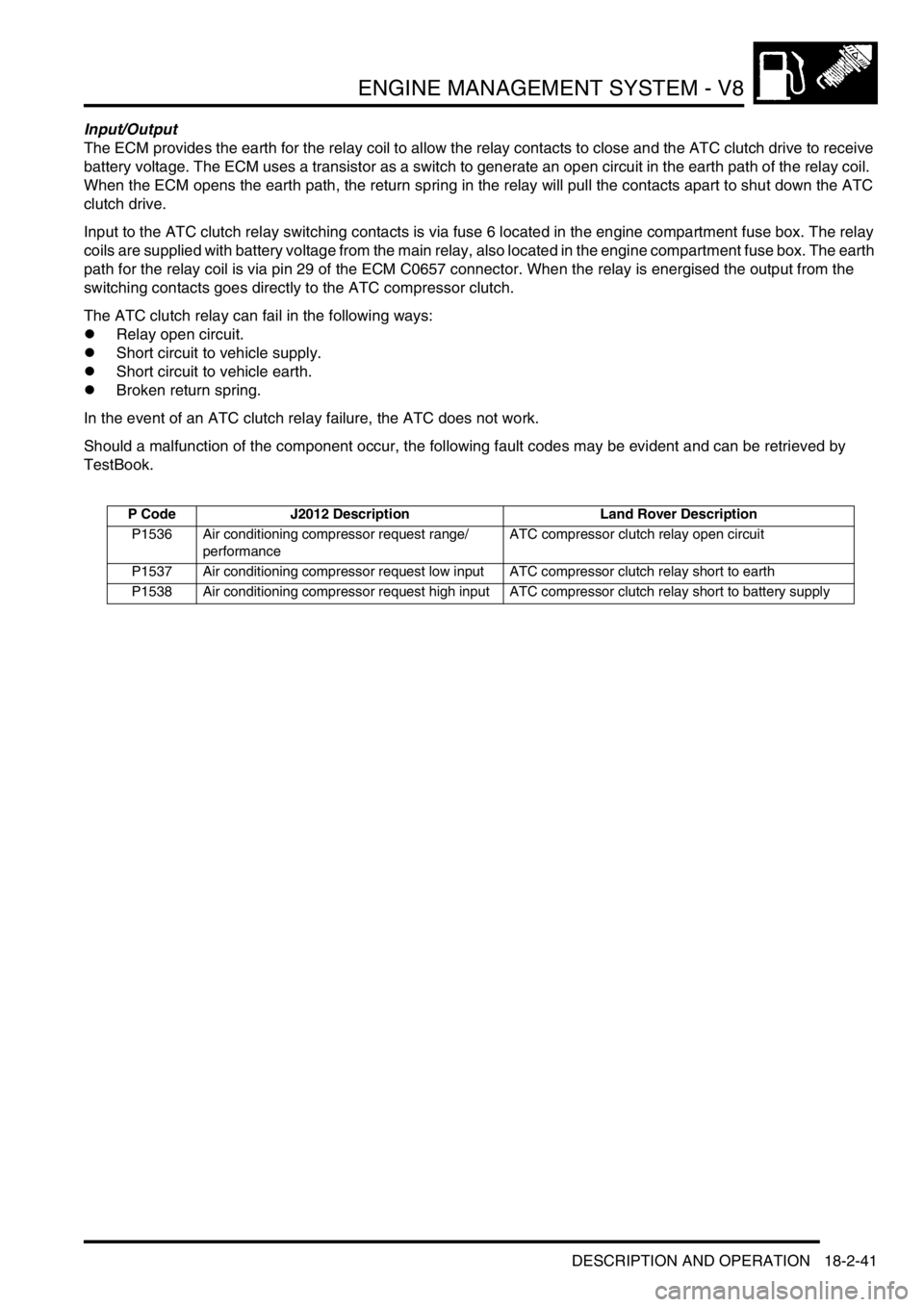
ENGINE MANAGEMENT SYSTEM - V8
DESCRIPTION AND OPERATION 18-2-41
Input/Output
The ECM provides the earth for the relay coil to allow the relay contacts to close and the ATC clutch drive to receive
battery voltage. The ECM uses a transistor as a switch to generate an open circuit in the earth path of the relay coil.
When the ECM opens the earth path, the return spring in the relay will pull the contacts apart to shut down the ATC
clutch drive.
Input to the ATC clutch relay switching contacts is via fuse 6 located in the engine compartment fuse box. The relay
coils are supplied with battery voltage from the main relay, also located in the engine compartment fuse box. The earth
path for the relay coil is via pin 29 of the ECM C0657 connector. When the relay is energised the output from the
switching contacts goes directly to the ATC compressor clutch.
The ATC clutch relay can fail in the following ways:
lRelay open circuit.
lShort circuit to vehicle supply.
lShort circuit to vehicle earth.
lBroken return spring.
In the event of an ATC clutch relay failure, the ATC does not work.
Should a malfunction of the component occur, the following fault codes may be evident and can be retrieved by
TestBook.
P Code J2012 Description Land Rover Description
P1536 Air conditioning compressor request range/
performanceATC compressor clutch relay open circuit
P1537 Air conditioning compressor request low input ATC compressor clutch relay short to earth
P1538 Air conditioning compressor request high input ATC compressor clutch relay short to battery supply