fuse box LAND ROVER DISCOVERY 2002 Owner's Guide
[x] Cancel search | Manufacturer: LAND ROVER, Model Year: 2002, Model line: DISCOVERY, Model: LAND ROVER DISCOVERY 2002Pages: 1672, PDF Size: 46.1 MB
Page 499 of 1672
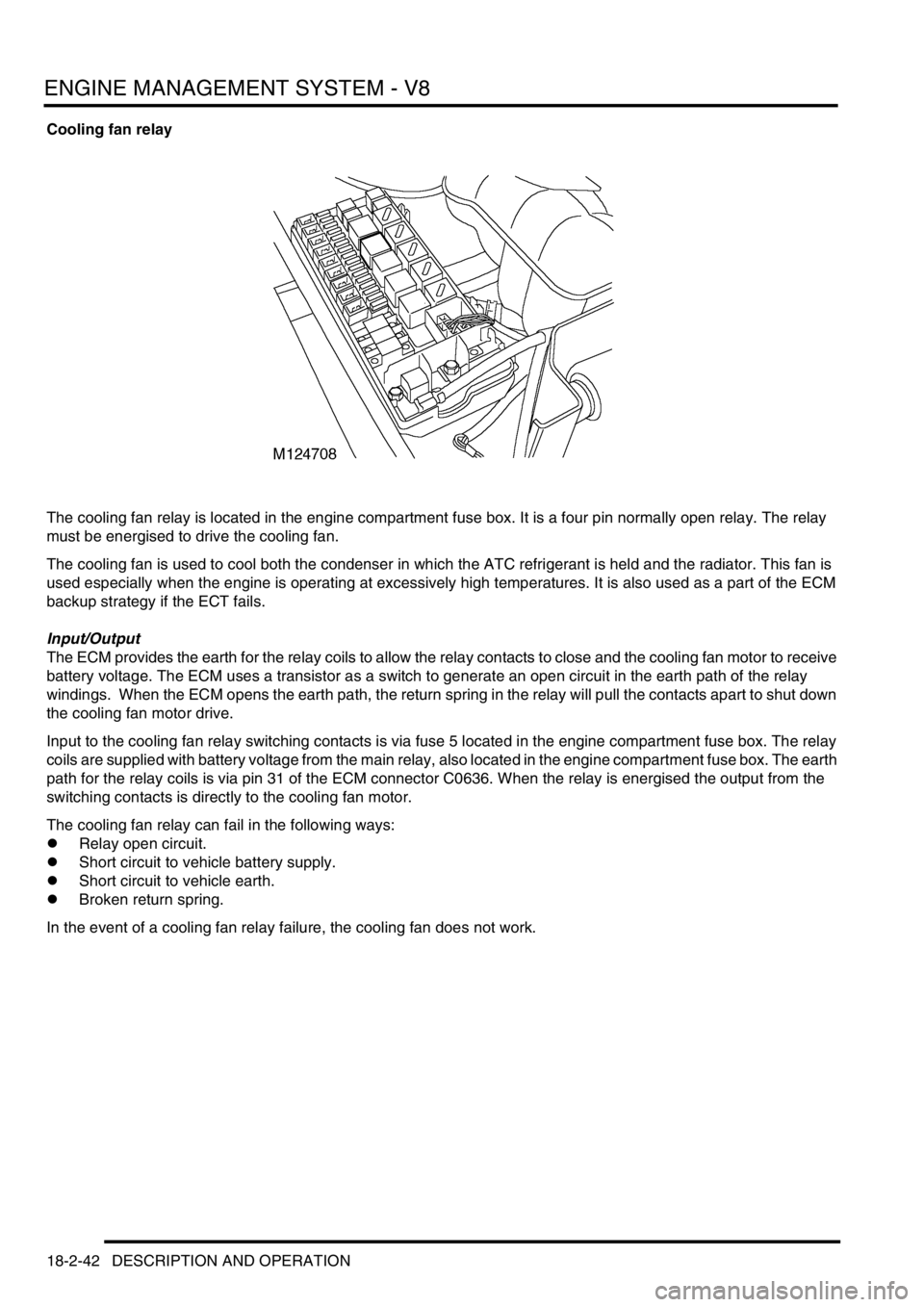
ENGINE MANAGEMENT SYSTEM - V8
18-2-42 DESCRIPTION AND OPERATION
Cooling fan relay
The cooling fan relay is located in the engine compartment fuse box. It is a four pin normally open relay. The relay
must be energised to drive the cooling fan.
The cooling fan is used to cool both the condenser in which the ATC refrigerant is held and the radiator. This fan is
used especially when the engine is operating at excessively high temperatures. It is also used as a part of the ECM
backup strategy if the ECT fails.
Input/Output
The ECM provides the earth for the relay coils to allow the relay contacts to close and the cooling fan motor to receive
battery voltage. The ECM uses a transistor as a switch to generate an open circuit in the earth path of the relay
windings. When the ECM opens the earth path, the return spring in the relay will pull the contacts apart to shut down
the cooling fan motor drive.
Input to the cooling fan relay switching contacts is via fuse 5 located in the engine compartment fuse box. The relay
coils are supplied with battery voltage from the main relay, also located in the engine compartment fuse box. The earth
path for the relay coils is via pin 31 of the ECM connector C0636. When the relay is energised the output from the
switching contacts is directly to the cooling fan motor.
The cooling fan relay can fail in the following ways:
lRelay open circuit.
lShort circuit to vehicle battery supply.
lShort circuit to vehicle earth.
lBroken return spring.
In the event of a cooling fan relay failure, the cooling fan does not work.
Page 550 of 1672
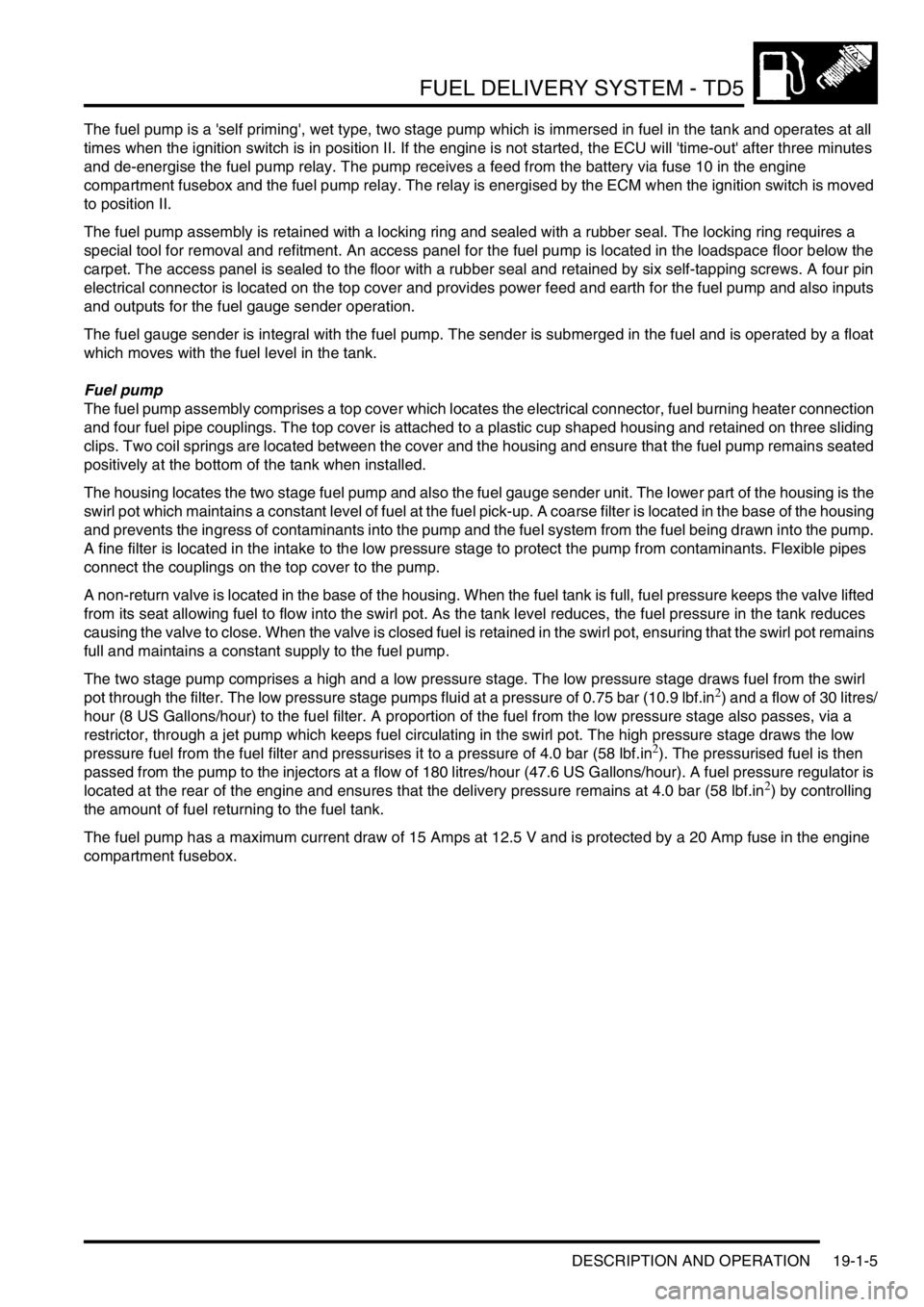
FUEL DELIVERY SYSTEM - TD5
DESCRIPTION AND OPERATION 19-1-5
The fuel pump is a 'self priming', wet type, two stage pump which is immersed in fuel in the tank and operates at all
times when the ignition switch is in position II. If the engine is not started, the ECU will 'time-out' after three minutes
and de-energise the fuel pump relay. The pump receives a feed from the battery via fuse 10 in the engine
compartment fusebox and the fuel pump relay. The relay is energised by the ECM when the ignition switch is moved
to position II.
The fuel pump assembly is retained with a locking ring and sealed with a rubber seal. The locking ring requires a
special tool for removal and refitment. An access panel for the fuel pump is located in the loadspace floor below the
carpet. The access panel is sealed to the floor with a rubber seal and retained by six self-tapping screws. A four pin
electrical connector is located on the top cover and provides power feed and earth for the fuel pump and also inputs
and outputs for the fuel gauge sender operation.
The fuel gauge sender is integral with the fuel pump. The sender is submerged in the fuel and is operated by a float
which moves with the fuel level in the tank.
Fuel pump
The fuel pump assembly comprises a top cover which locates the electrical connector, fuel burning heater connection
and four fuel pipe couplings. The top cover is attached to a plastic cup shaped housing and retained on three sliding
clips. Two coil springs are located between the cover and the housing and ensure that the fuel pump remains seated
positively at the bottom of the tank when installed.
The housing locates the two stage fuel pump and also the fuel gauge sender unit. The lower part of the housing is the
swirl pot which maintains a constant level of fuel at the fuel pick-up. A coarse filter is located in the base of the housing
and prevents the ingress of contaminants into the pump and the fuel system from the fuel being drawn into the pump.
A fine filter is located in the intake to the low pressure stage to protect the pump from contaminants. Flexible pipes
connect the couplings on the top cover to the pump.
A non-return valve is located in the base of the housing. When the fuel tank is full, fuel pressure keeps the valve lifted
from its seat allowing fuel to flow into the swirl pot. As the tank level reduces, the fuel pressure in the tank reduces
causing the valve to close. When the valve is closed fuel is retained in the swirl pot, ensuring that the swirl pot remains
full and maintains a constant supply to the fuel pump.
The two stage pump comprises a high and a low pressure stage. The low pressure stage draws fuel from the swirl
pot through the filter. The low pressure stage pumps fluid at a pressure of 0.75 bar (10.9 lbf.in
2) and a flow of 30 litres/
hour (8 US Gallons/hour) to the fuel filter. A proportion of the fuel from the low pressure stage also passes, via a
restrictor, through a jet pump which keeps fuel circulating in the swirl pot. The high pressure stage draws the low
pressure fuel from the fuel filter and pressurises it to a pressure of 4.0 bar (58 lbf.in
2). The pressurised fuel is then
passed from the pump to the injectors at a flow of 180 litres/hour (47.6 US Gallons/hour). A fuel pressure regulator is
located at the rear of the engine and ensures that the delivery pressure remains at 4.0 bar (58 lbf.in
2) by controlling
the amount of fuel returning to the fuel tank.
The fuel pump has a maximum current draw of 15 Amps at 12.5 V and is protected by a 20 Amp fuse in the engine
compartment fusebox.
Page 555 of 1672
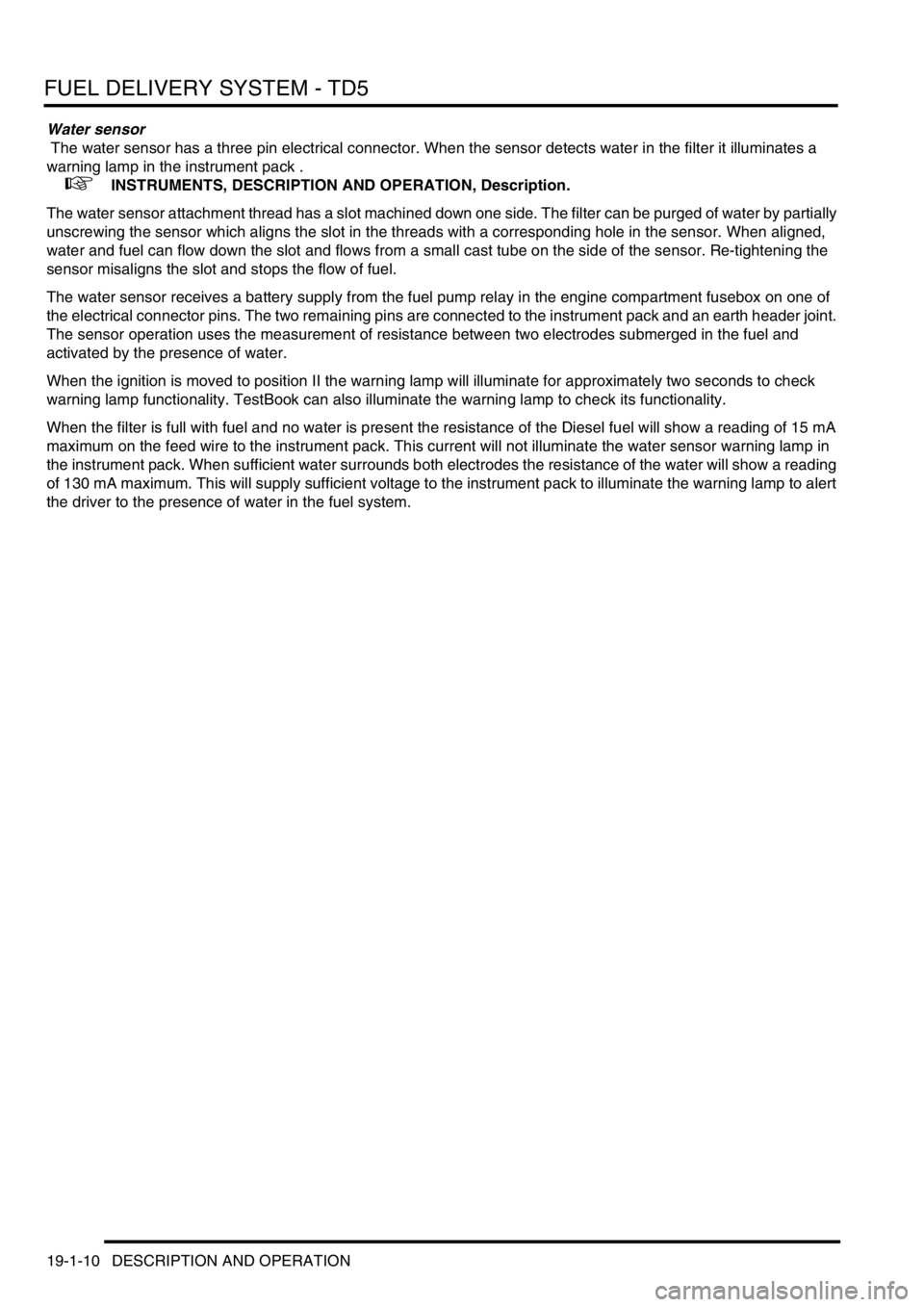
FUEL DELIVERY SYSTEM - TD5
19-1-10 DESCRIPTION AND OPERATION
Water sensor
The water sensor has a three pin electrical connector. When the sensor detects water in the filter it illuminates a
warning lamp in the instrument pack .
+ INSTRUMENTS, DESCRIPTION AND OPERATION, Description.
The water sensor attachment thread has a slot machined down one side. The filter can be purged of water by partially
unscrewing the sensor which aligns the slot in the threads with a corresponding hole in the sensor. When aligned,
water and fuel can flow down the slot and flows from a small cast tube on the side of the sensor. Re-tightening the
sensor misaligns the slot and stops the flow of fuel.
The water sensor receives a battery supply from the fuel pump relay in the engine compartment fusebox on one of
the electrical connector pins. The two remaining pins are connected to the instrument pack and an earth header joint.
The sensor operation uses the measurement of resistance between two electrodes submerged in the fuel and
activated by the presence of water.
When the ignition is moved to position II the warning lamp will illuminate for approximately two seconds to check
warning lamp functionality. TestBook can also illuminate the warning lamp to check its functionality.
When the filter is full with fuel and no water is present the resistance of the Diesel fuel will show a reading of 15 mA
maximum on the feed wire to the instrument pack. This current will not illuminate the water sensor warning lamp in
the instrument pack. When sufficient water surrounds both electrodes the resistance of the water will show a reading
of 130 mA maximum. This will supply sufficient voltage to the instrument pack to illuminate the warning lamp to alert
the driver to the presence of water in the fuel system.
Page 556 of 1672
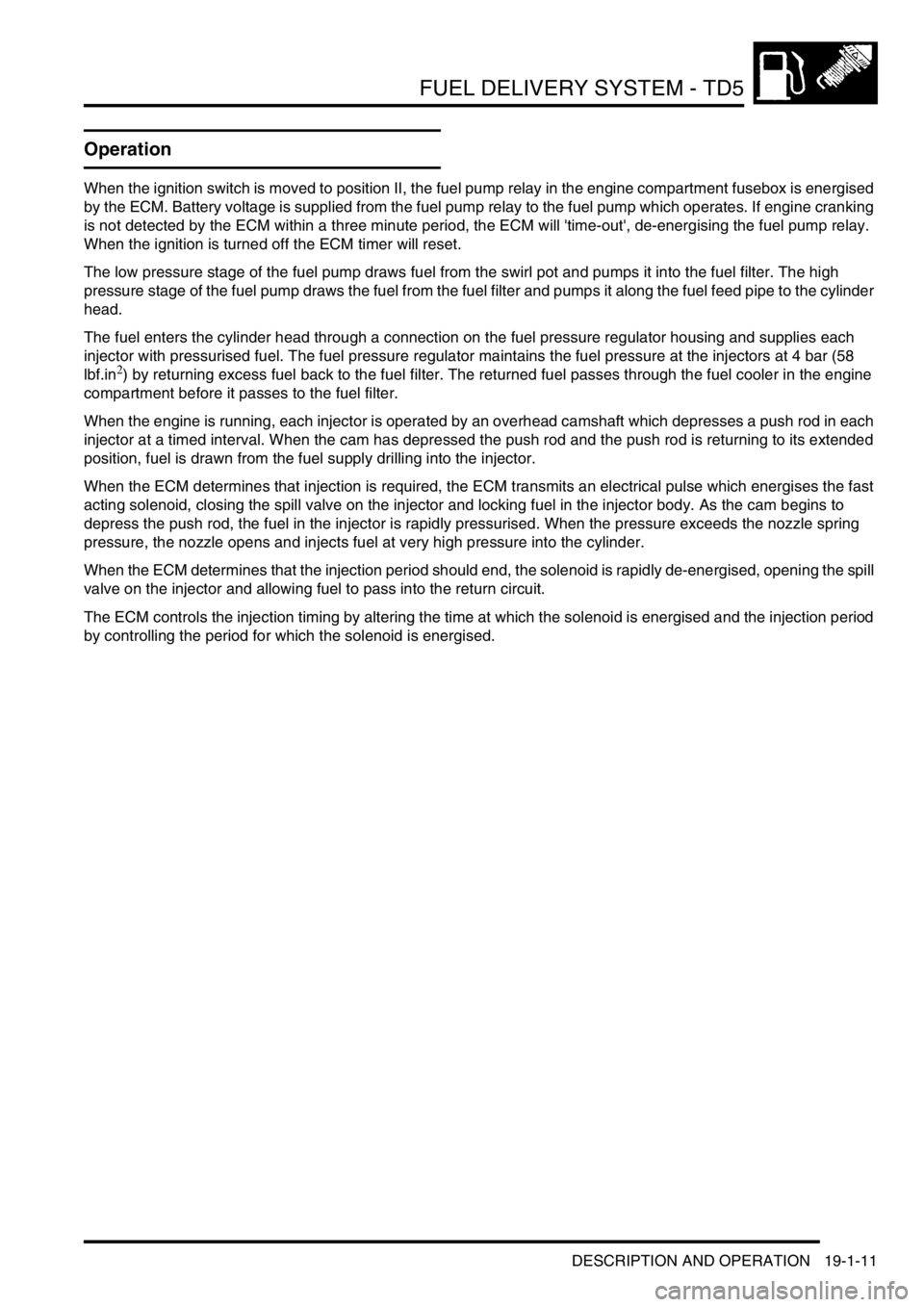
FUEL DELIVERY SYSTEM - TD5
DESCRIPTION AND OPERATION 19-1-11
Operation
When the ignition switch is moved to position II, the fuel pump relay in the engine compartment fusebox is energised
by the ECM. Battery voltage is supplied from the fuel pump relay to the fuel pump which operates. If engine cranking
is not detected by the ECM within a three minute period, the ECM will 'time-out', de-energising the fuel pump relay.
When the ignition is turned off the ECM timer will reset.
The low pressure stage of the fuel pump draws fuel from the swirl pot and pumps it into the fuel filter. The high
pressure stage of the fuel pump draws the fuel from the fuel filter and pumps it along the fuel feed pipe to the cylinder
head.
The fuel enters the cylinder head through a connection on the fuel pressure regulator housing and supplies each
injector with pressurised fuel. The fuel pressure regulator maintains the fuel pressure at the injectors at 4 bar (58
lbf.in
2) by returning excess fuel back to the fuel filter. The returned fuel passes through the fuel cooler in the engine
compartment before it passes to the fuel filter.
When the engine is running, each injector is operated by an overhead camshaft which depresses a push rod in each
injector at a timed interval. When the cam has depressed the push rod and the push rod is returning to its extended
position, fuel is drawn from the fuel supply drilling into the injector.
When the ECM determines that injection is required, the ECM transmits an electrical pulse which energises the fast
acting solenoid, closing the spill valve on the injector and locking fuel in the injector body. As the cam begins to
depress the push rod, the fuel in the injector is rapidly pressurised. When the pressure exceeds the nozzle spring
pressure, the nozzle opens and injects fuel at very high pressure into the cylinder.
When the ECM determines that the injection period should end, the solenoid is rapidly de-energised, opening the spill
valve on the injector and allowing fuel to pass into the return circuit.
The ECM controls the injection timing by altering the time at which the solenoid is energised and the injection period
by controlling the period for which the solenoid is energised.
Page 572 of 1672
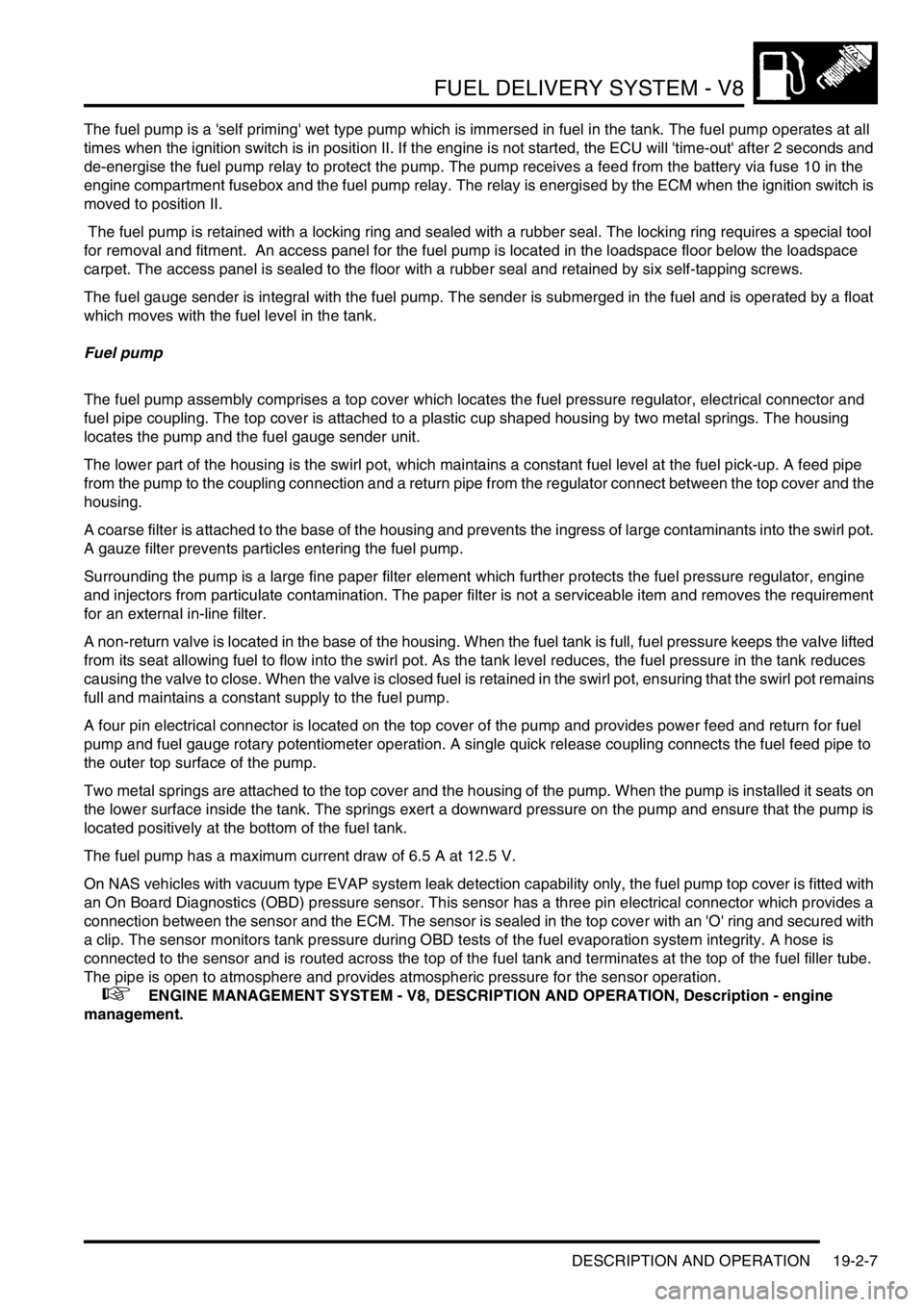
FUEL DELIVERY SYSTEM - V8
DESCRIPTION AND OPERATION 19-2-7
The fuel pump is a 'self priming' wet type pump which is immersed in fuel in the tank. The fuel pump operates at all
times when the ignition switch is in position II. If the engine is not started, the ECU will 'time-out' after 2 seconds and
de-energise the fuel pump relay to protect the pump. The pump receives a feed from the battery via fuse 10 in the
engine compartment fusebox and the fuel pump relay. The relay is energised by the ECM when the ignition switch is
moved to position II.
The fuel pump is retained with a locking ring and sealed with a rubber seal. The locking ring requires a special tool
for removal and fitment. An access panel for the fuel pump is located in the loadspace floor below the loadspace
carpet. The access panel is sealed to the floor with a rubber seal and retained by six self-tapping screws.
The fuel gauge sender is integral with the fuel pump. The sender is submerged in the fuel and is operated by a float
which moves with the fuel level in the tank.
Fuel pump
The fuel pump assembly comprises a top cover which locates the fuel pressure regulator, electrical connector and
fuel pipe coupling. The top cover is attached to a plastic cup shaped housing by two metal springs. The housing
locates the pump and the fuel gauge sender unit.
The lower part of the housing is the swirl pot, which maintains a constant fuel level at the fuel pick-up. A feed pipe
from the pump to the coupling connection and a return pipe from the regulator connect between the top cover and the
housing.
A coarse filter is attached to the base of the housing and prevents the ingress of large contaminants into the swirl pot.
A gauze filter prevents particles entering the fuel pump.
Surrounding the pump is a large fine paper filter element which further protects the fuel pressure regulator, engine
and injectors from particulate contamination. The paper filter is not a serviceable item and removes the requirement
for an external in-line filter.
A non-return valve is located in the base of the housing. When the fuel tank is full, fuel pressure keeps the valve lifted
from its seat allowing fuel to flow into the swirl pot. As the tank level reduces, the fuel pressure in the tank reduces
causing the valve to close. When the valve is closed fuel is retained in the swirl pot, ensuring that the swirl pot remains
full and maintains a constant supply to the fuel pump.
A four pin electrical connector is located on the top cover of the pump and provides power feed and return for fuel
pump and fuel gauge rotary potentiometer operation. A single quick release coupling connects the fuel feed pipe to
the outer top surface of the pump.
Two metal springs are attached to the top cover and the housing of the pump. When the pump is installed it seats on
the lower surface inside the tank. The springs exert a downward pressure on the pump and ensure that the pump is
located positively at the bottom of the fuel tank.
The fuel pump has a maximum current draw of 6.5 A at 12.5 V.
On NAS vehicles with vacuum type EVAP system leak detection capability only, the fuel pump top cover is fitted with
an On Board Diagnostics (OBD) pressure sensor. This sensor has a three pin electrical connector which provides a
connection between the sensor and the ECM. The sensor is sealed in the top cover with an 'O' ring and secured with
a clip. The sensor monitors tank pressure during OBD tests of the fuel evaporation system integrity. A hose is
connected to the sensor and is routed across the top of the fuel tank and terminates at the top of the fuel filler tube.
The pipe is open to atmosphere and provides atmospheric pressure for the sensor operation.
+ ENGINE MANAGEMENT SYSTEM - V8, DESCRIPTION AND OPERATION, Description - engine
management.
Page 574 of 1672
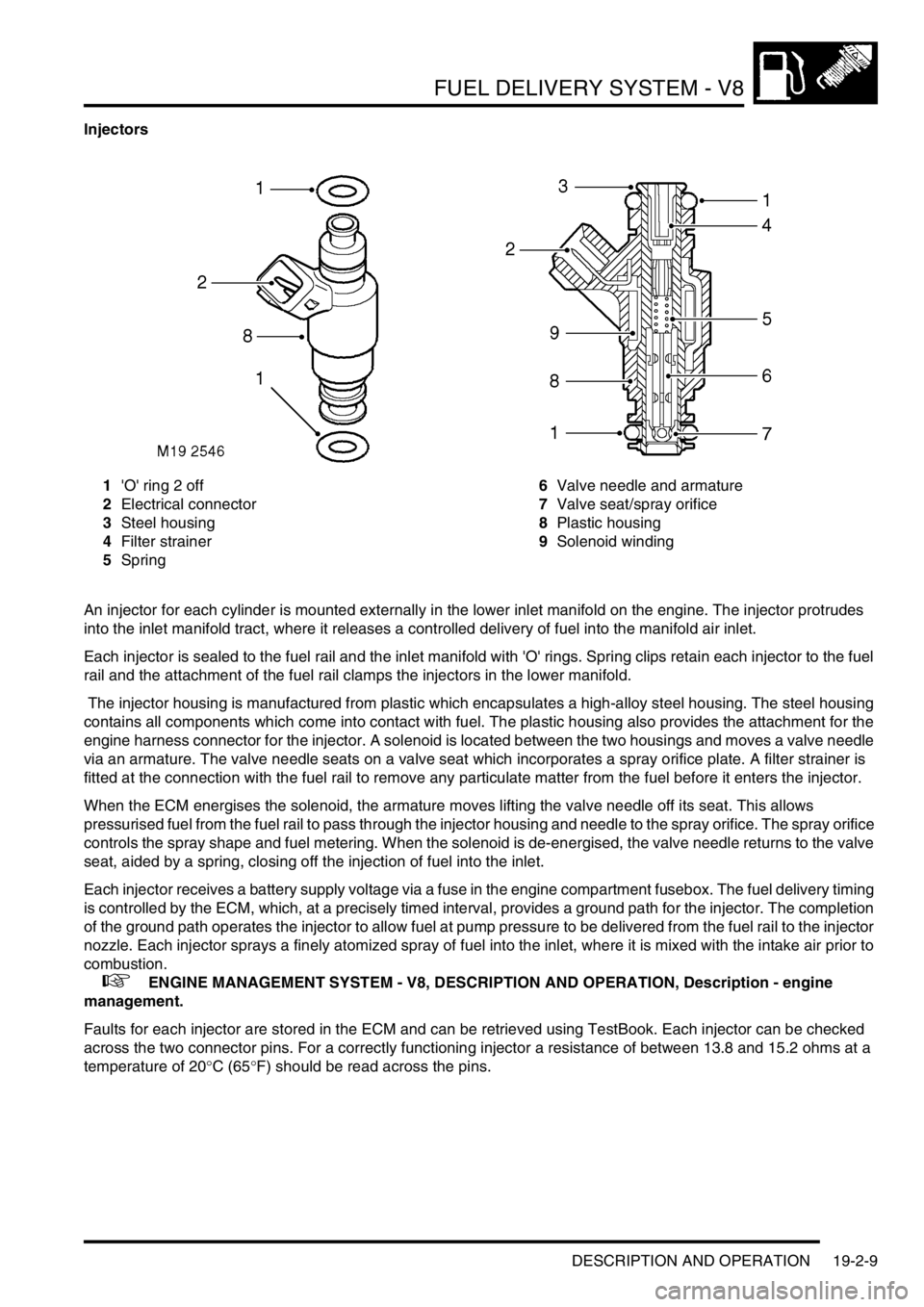
FUEL DELIVERY SYSTEM - V8
DESCRIPTION AND OPERATION 19-2-9
Injectors
1'O' ring 2 off
2Electrical connector
3Steel housing
4Filter strainer
5Spring6Valve needle and armature
7Valve seat/spray orifice
8Plastic housing
9Solenoid winding
An injector for each cylinder is mounted externally in the lower inlet manifold on the engine. The injector protrudes
into the inlet manifold tract, where it releases a controlled delivery of fuel into the manifold air inlet.
Each injector is sealed to the fuel rail and the inlet manifold with 'O' rings. Spring clips retain each injector to the fuel
rail and the attachment of the fuel rail clamps the injectors in the lower manifold.
The injector housing is manufactured from plastic which encapsulates a high-alloy steel housing. The steel housing
contains all components which come into contact with fuel. The plastic housing also provides the attachment for the
engine harness connector for the injector. A solenoid is located between the two housings and moves a valve needle
via an armature. The valve needle seats on a valve seat which incorporates a spray orifice plate. A filter strainer is
fitted at the connection with the fuel rail to remove any particulate matter from the fuel before it enters the injector.
When the ECM energises the solenoid, the armature moves lifting the valve needle off its seat. This allows
pressurised fuel from the fuel rail to pass through the injector housing and needle to the spray orifice. The spray orifice
controls the spray shape and fuel metering. When the solenoid is de-energised, the valve needle returns to the valve
seat, aided by a spring, closing off the injection of fuel into the inlet.
Each injector receives a battery supply voltage via a fuse in the engine compartment fusebox. The fuel delivery timing
is controlled by the ECM, which, at a precisely timed interval, provides a ground path for the injector. The completion
of the ground path operates the injector to allow fuel at pump pressure to be delivered from the fuel rail to the injector
nozzle. Each injector sprays a finely atomized spray of fuel into the inlet, where it is mixed with the intake air prior to
combustion.
+ ENGINE MANAGEMENT SYSTEM - V8, DESCRIPTION AND OPERATION, Description - engine
management.
Faults for each injector are stored in the ECM and can be retrieved using TestBook. Each injector can be checked
across the two connector pins. For a correctly functioning injector a resistance of between 13.8 and 15.2 ohms at a
temperature of 20
°C (65°F) should be read across the pins.
Page 575 of 1672
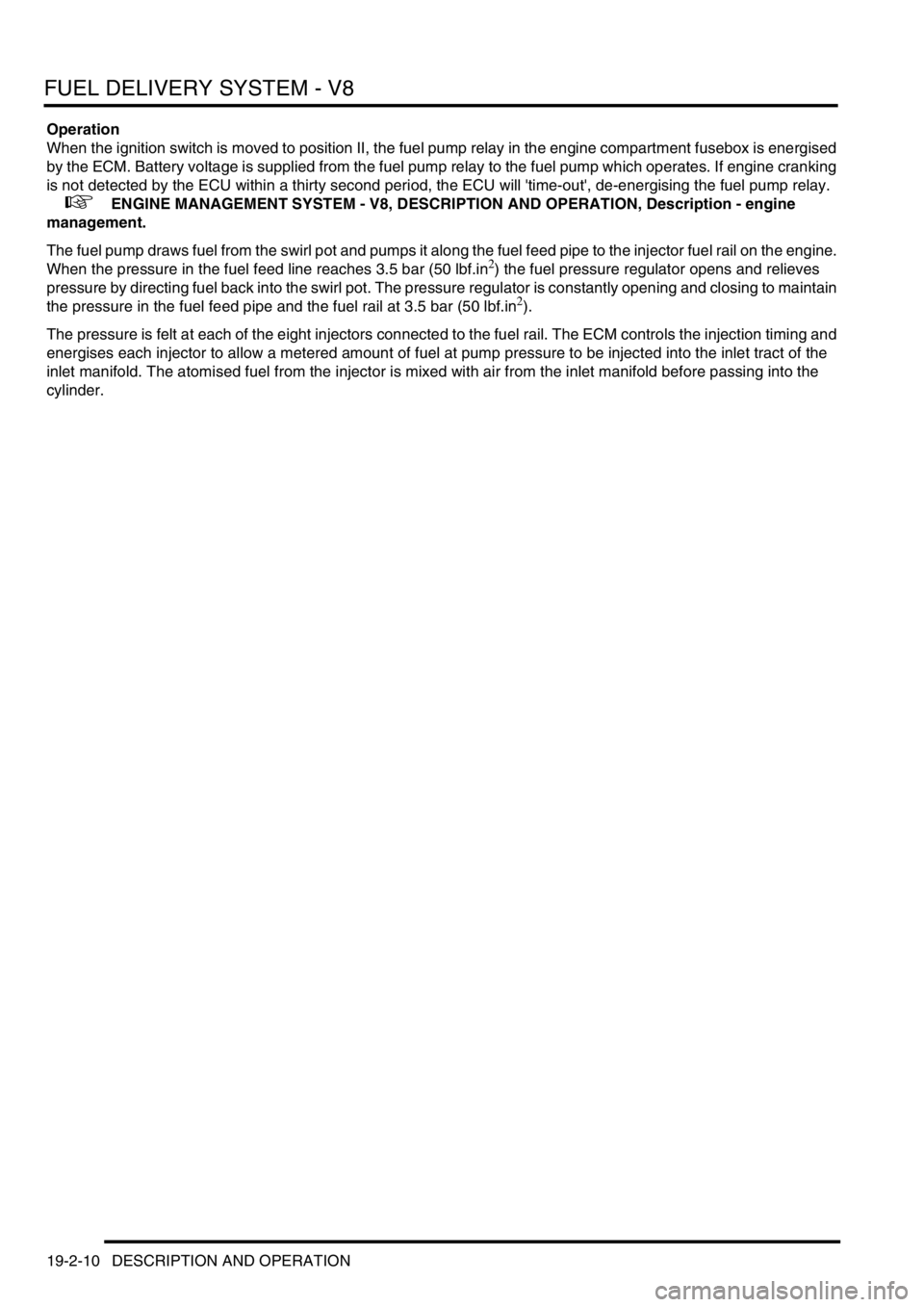
FUEL DELIVERY SYSTEM - V8
19-2-10 DESCRIPTION AND OPERATION
Operation
When the ignition switch is moved to position II, the fuel pump relay in the engine compartment fusebox is energised
by the ECM. Battery voltage is supplied from the fuel pump relay to the fuel pump which operates. If engine cranking
is not detected by the ECU within a thirty second period, the ECU will 'time-out', de-energising the fuel pump relay.
+ ENGINE MANAGEMENT SYSTEM - V8, DESCRIPTION AND OPERATION, Description - engine
management.
The fuel pump draws fuel from the swirl pot and pumps it along the fuel feed pipe to the injector fuel rail on the engine.
When the pressure in the fuel feed line reaches 3.5 bar (50 lbf.in
2) the fuel pressure regulator opens and relieves
pressure by directing fuel back into the swirl pot. The pressure regulator is constantly opening and closing to maintain
the pressure in the fuel feed pipe and the fuel rail at 3.5 bar (50 lbf.in
2).
The pressure is felt at each of the eight injectors connected to the fuel rail. The ECM controls the injection timing and
energises each injector to allow a metered amount of fuel at pump pressure to be injected into the inlet tract of the
inlet manifold. The atomised fuel from the injector is mixed with air from the inlet manifold before passing into the
cylinder.
Page 690 of 1672
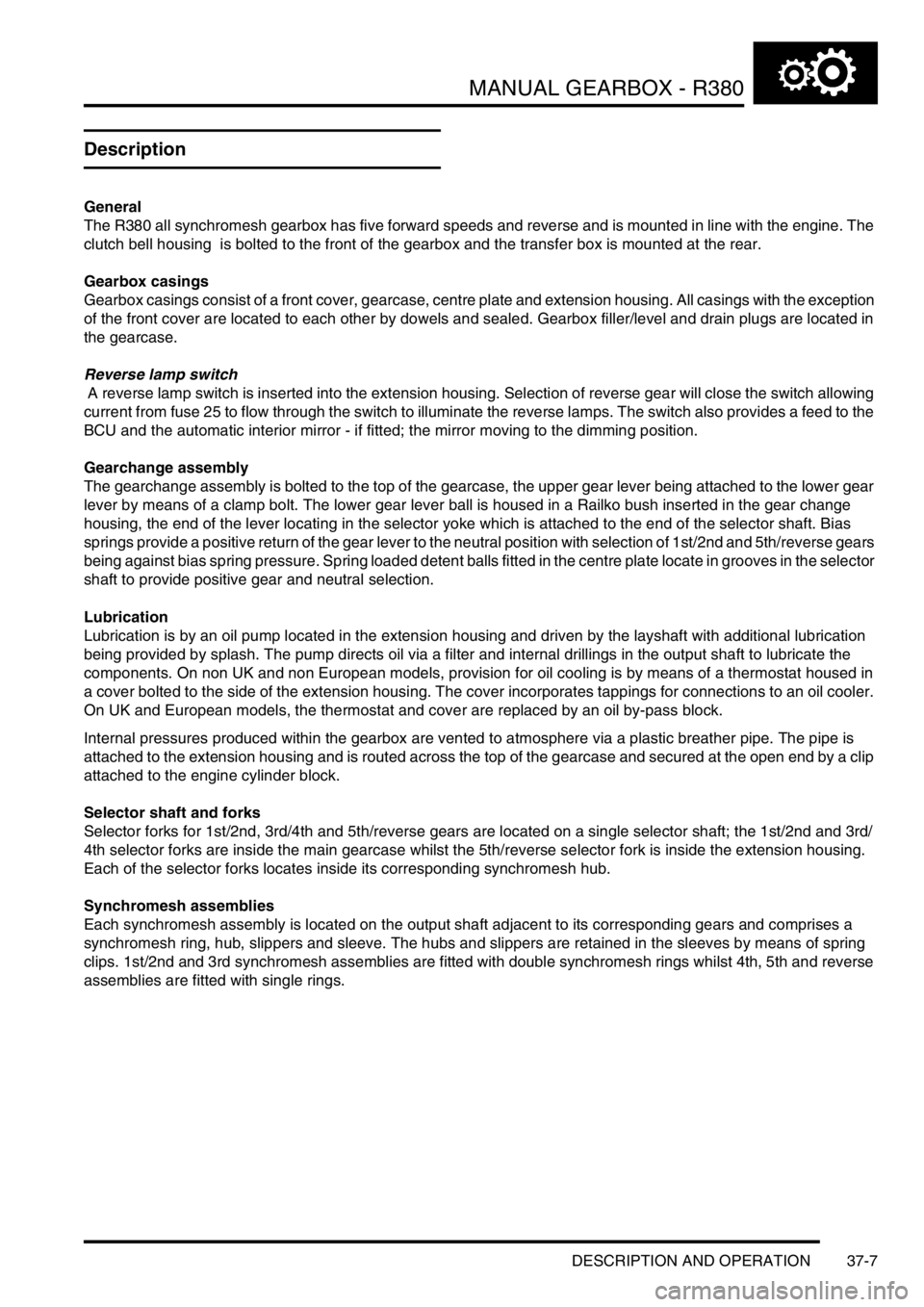
MANUAL GEARBOX - R380
DESCRIPTION AND OPERATION 37-7
Description
General
The R380 all synchromesh gearbox has five forward speeds and reverse and is mounted in line with the engine. The
clutch bell housing is bolted to the front of the gearbox and the transfer box is mounted at the rear.
Gearbox casings
Gearbox casings consist of a front cover, gearcase, centre plate and extension housing. All casings with the exception
of the front cover are located to each other by dowels and sealed. Gearbox filler/level and drain plugs are located in
the gearcase.
Reverse lamp switch
A reverse lamp switch is inserted into the extension housing. Selection of reverse gear will close the switch allowing
current from fuse 25 to flow through the switch to illuminate the reverse lamps. The switch also provides a feed to the
BCU and the automatic interior mirror - if fitted; the mirror moving to the dimming position.
Gearchange assembly
The gearchange assembly is bolted to the top of the gearcase, the upper gear lever being attached to the lower gear
lever by means of a clamp bolt. The lower gear lever ball is housed in a Railko bush inserted in the gear change
housing, the end of the lever locating in the selector yoke which is attached to the end of the selector shaft. Bias
springs provide a positive return of the gear lever to the neutral position with selection of 1st/2nd and 5th/reverse gears
being against bias spring pressure. Spring loaded detent balls fitted in the centre plate locate in grooves in the selector
shaft to provide positive gear and neutral selection.
Lubrication
Lubrication is by an oil pump located in the extension housing and driven by the layshaft with additional lubrication
being provided by splash. The pump directs oil via a filter and internal drillings in the output shaft to lubricate the
components. On non UK and non European models, provision for oil cooling is by means of a thermostat housed in
a cover bolted to the side of the extension housing. The cover incorporates tappings for connections to an oil cooler.
On UK and European models, the thermostat and cover are replaced by an oil by-pass block.
Internal pressures produced within the gearbox are vented to atmosphere via a plastic breather pipe. The pipe is
attached to the extension housing and is routed across the top of the gearcase and secured at the open end by a clip
attached to the engine cylinder block.
Selector shaft and forks
Selector forks for 1st/2nd, 3rd/4th and 5th/reverse gears are located on a single selector shaft; the 1st/2nd and 3rd/
4th selector forks are inside the main gearcase whilst the 5th/reverse selector fork is inside the extension housing.
Each of the selector forks locates inside its corresponding synchromesh hub.
Synchromesh assemblies
Each synchromesh assembly is located on the output shaft adjacent to its corresponding gears and comprises a
synchromesh ring, hub, slippers and sleeve. The hubs and slippers are retained in the sleeves by means of spring
clips. 1st/2nd and 3rd synchromesh assemblies are fitted with double synchromesh rings whilst 4th, 5th and reverse
assemblies are fitted with single rings.
Page 749 of 1672
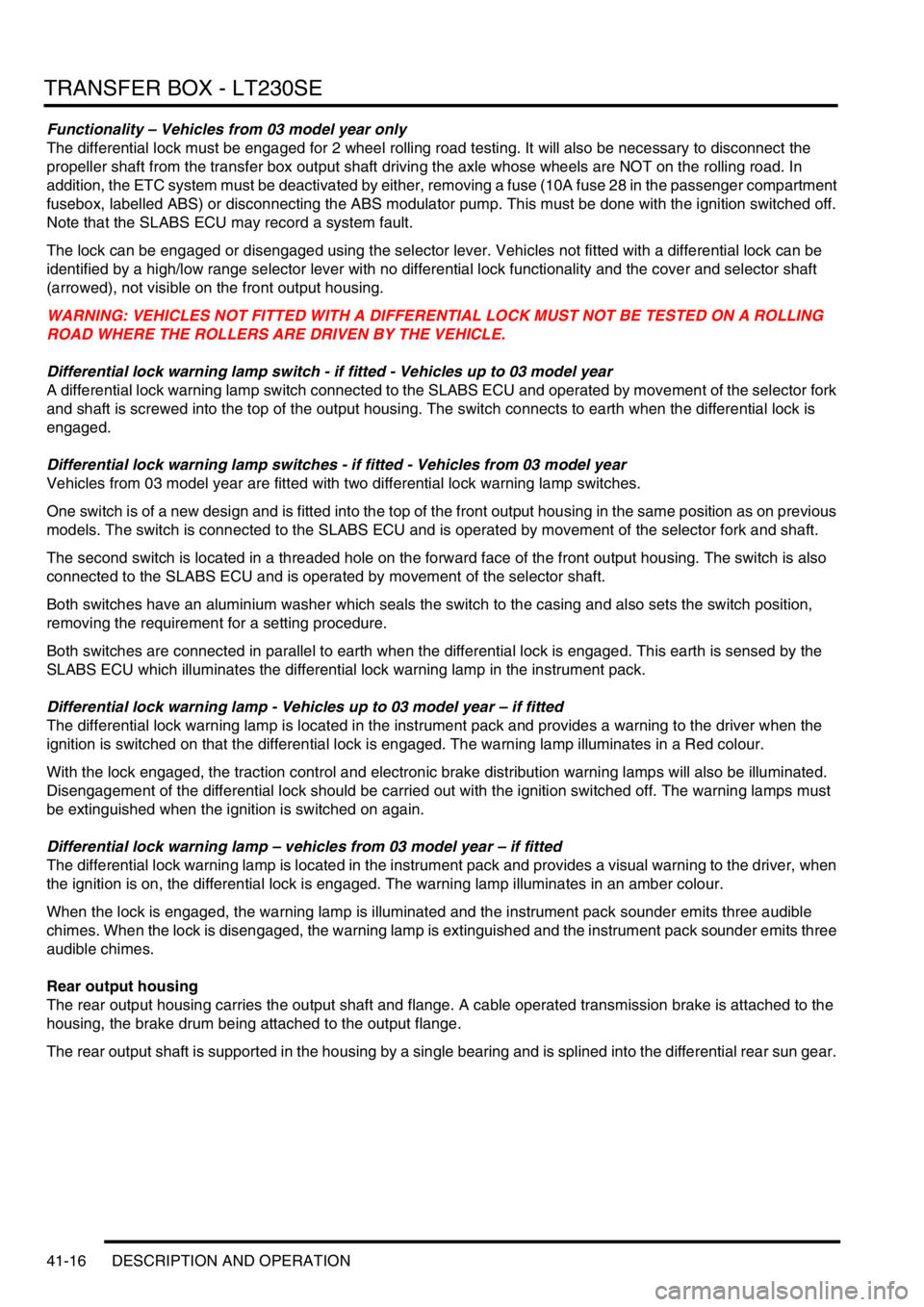
TRANSFER BOX - LT230SE
41-16 DESCRIPTION AND OPERATION
Functionality – Vehicles from 03 model year only
The differential lock must be engaged for 2 wheel rolling road testing. It will also be necessary to disconnect the
propeller shaft from the transfer box output shaft driving the axle whose wheels are NOT on the rolling road. In
addition, the ETC system must be deactivated by either, removing a fuse (10A fuse 28 in the passenger compartment
fusebox, labelled ABS) or disconnecting the ABS modulator pump. This must be done with the ignition switched off.
Note that the SLABS ECU may record a system fault.
The lock can be engaged or disengaged using the selector lever. Vehicles not fitted with a differential lock can be
identified by a high/low range selector lever with no differential lock functionality and the cover and selector shaft
(arrowed), not visible on the front output housing.
WARNING: VEHICLES NOT FITTED WITH A DIFFERENTIAL LOCK MUST NOT BE TESTED ON A ROLLING
ROAD WHERE THE ROLLERS ARE DRIVEN BY THE VEHICLE.
Differential lock warning lamp switch - if fitted - Vehicles up to 03 model year
A differential lock warning lamp switch connected to the SLABS ECU and operated by movement of the selector fork
and shaft is screwed into the top of the output housing. The switch connects to earth when the differential lock is
engaged.
Differential lock warning lamp switches - if fitted - Vehicles from 03 model year
Vehicles from 03 model year are fitted with two differential lock warning lamp switches.
One switch is of a new design and is fitted into the top of the front output housing in the same position as on previous
models. The switch is connected to the SLABS ECU and is operated by movement of the selector fork and shaft.
The second switch is located in a threaded hole on the forward face of the front output housing. The switch is also
connected to the SLABS ECU and is operated by movement of the selector shaft.
Both switches have an aluminium washer which seals the switch to the casing and also sets the switch position,
removing the requirement for a setting procedure.
Both switches are connected in parallel to earth when the differential lock is engaged. This earth is sensed by the
SLABS ECU which illuminates the differential lock warning lamp in the instrument pack.
Differential lock warning lamp - Vehicles up to 03 model year – if fitted
The differential lock warning lamp is located in the instrument pack and provides a warning to the driver when the
ignition is switched on that the differential lock is engaged. The warning lamp illuminates in a Red colour.
With the lock engaged, the traction control and electronic brake distribution warning lamps will also be illuminated.
Disengagement of the differential lock should be carried out with the ignition switched off. The warning lamps must
be extinguished when the ignition is switched on again.
Differential lock warning lamp – vehicles from 03 model year – if fitted
The differential lock warning lamp is located in the instrument pack and provides a visual warning to the driver, when
the ignition is on, the differential lock is engaged. The warning lamp illuminates in an amber colour.
When the lock is engaged, the warning lamp is illuminated and the instrument pack sounder emits three audible
chimes. When the lock is disengaged, the warning lamp is extinguished and the instrument pack sounder emits three
audible chimes.
Rear output housing
The rear output housing carries the output shaft and flange. A cable operated transmission brake is attached to the
housing, the brake drum being attached to the output flange.
The rear output shaft is supported in the housing by a single bearing and is splined into the differential rear sun gear.
Page 809 of 1672
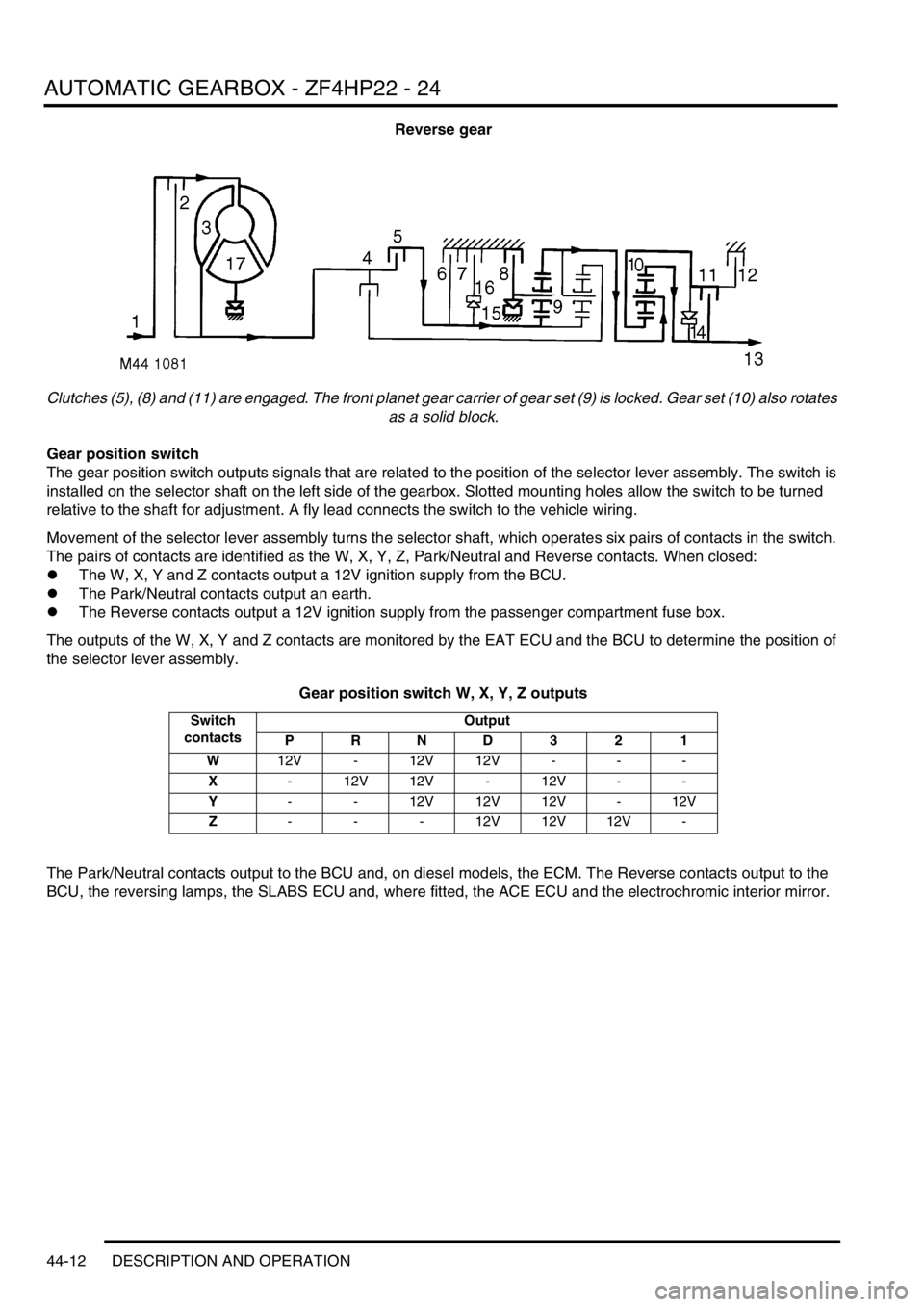
AUTOMATIC GEARBOX - ZF4HP22 - 24
44-12 DESCRIPTION AND OPERATION
Reverse gear
Clutches (5), (8) and (11) are engaged. The front planet gear carrier of gear set (9) is locked. Gear set (10) also rotates
as a solid block.
Gear position switch
The gear position switch outputs signals that are related to the position of the selector lever assembly. The switch is
installed on the selector shaft on the left side of the gearbox. Slotted mounting holes allow the switch to be turned
relative to the shaft for adjustment. A fly lead connects the switch to the vehicle wiring.
Movement of the selector lever assembly turns the selector shaft, which operates six pairs of contacts in the switch.
The pairs of contacts are identified as the W, X, Y, Z, Park/Neutral and Reverse contacts. When closed:
lThe W, X, Y and Z contacts output a 12V ignition supply from the BCU.
lThe Park/Neutral contacts output an earth.
lThe Reverse contacts output a 12V ignition supply from the passenger compartment fuse box.
The outputs of the W, X, Y and Z contacts are monitored by the EAT ECU and the BCU to determine the position of
the selector lever assembly.
Gear position switch W, X, Y, Z outputs
The Park/Neutral contacts output to the BCU and, on diesel models, the ECM. The Reverse contacts output to the
BCU, the reversing lamps, the SLABS ECU and, where fitted, the ACE ECU and the electrochromic interior mirror.
Switch
contactsOutput
PRND 3 2 1
W12V - 12V 12V - - -
X- 12V 12V - 12V - -
Y- - 12V 12V 12V - 12V
Z- - - 12V 12V 12V -