OBD port LAND ROVER DISCOVERY 2002 Workshop Manual
[x] Cancel search | Manufacturer: LAND ROVER, Model Year: 2002, Model line: DISCOVERY, Model: LAND ROVER DISCOVERY 2002Pages: 1672, PDF Size: 46.1 MB
Page 346 of 1672
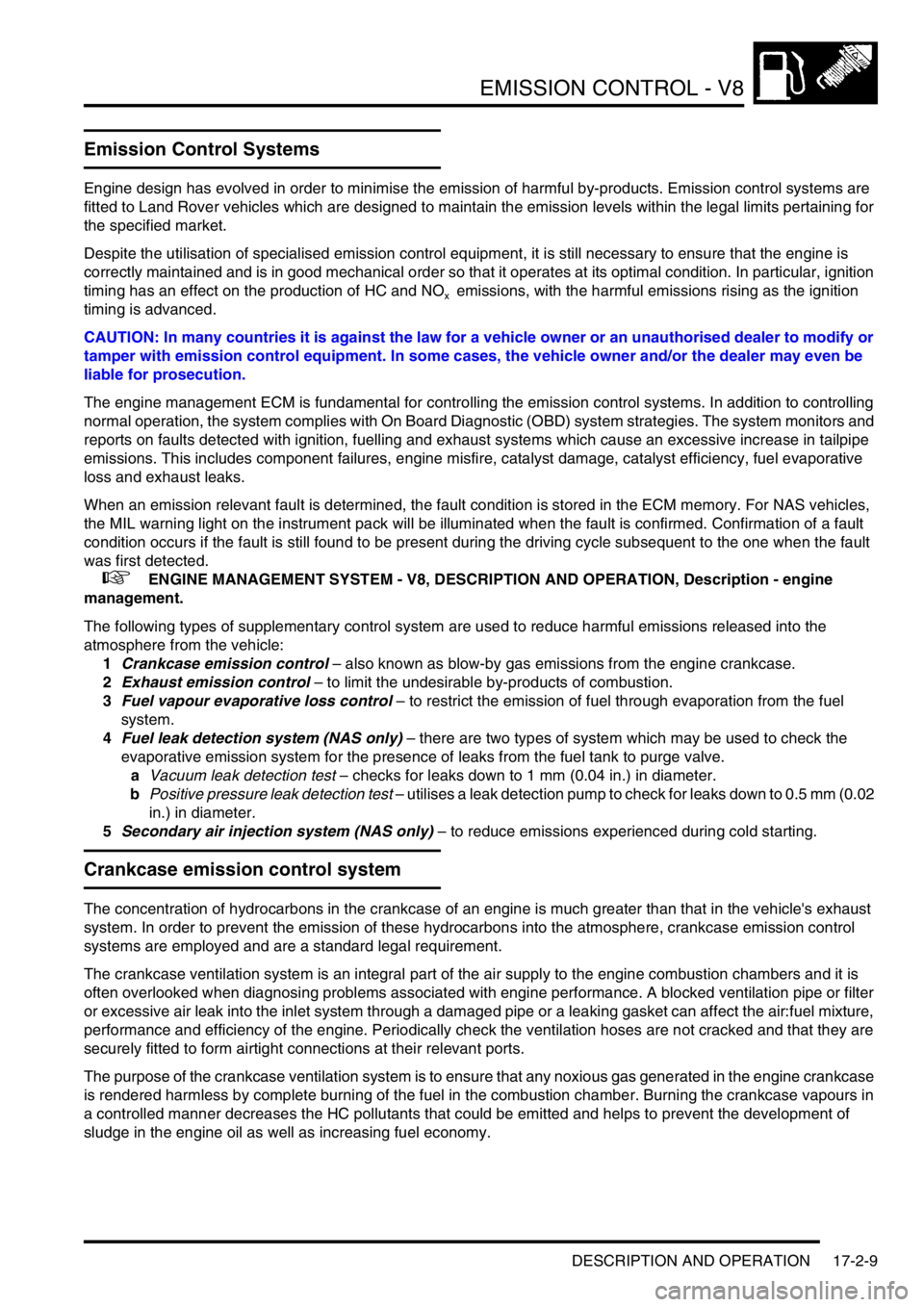
EMISSION CONTROL - V8
DESCRIPTION AND OPERATION 17-2-9
Emission Control Systems
Engine design has evolved in order to minimise the emission of harmful by-products. Emission control systems are
fitted to Land Rover vehicles which are designed to maintain the emission levels within the legal limits pertaining for
the specified market.
Despite the utilisation of specialised emission control equipment, it is still necessary to ensure that the engine is
correctly maintained and is in good mechanical order so that it operates at its optimal condition. In particular, ignition
timing has an effect on the production of HC and NO
x emissions, with the harmful emissions rising as the ignition
timing is advanced.
CAUTION: In many countries it is against the law for a vehicle owner or an unauthorised dealer to modify or
tamper with emission control equipment. In some cases, the vehicle owner and/or the dealer may even be
liable for prosecution.
The engine management ECM is fundamental for controlling the emission control systems. In addition to controlling
normal operation, the system complies with On Board Diagnostic (OBD) system strategies. The system monitors and
reports on faults detected with ignition, fuelling and exhaust systems which cause an excessive increase in tailpipe
emissions. This includes component failures, engine misfire, catalyst damage, catalyst efficiency, fuel evaporative
loss and exhaust leaks.
When an emission relevant fault is determined, the fault condition is stored in the ECM memory. For NAS vehicles,
the MIL warning light on the instrument pack will be illuminated when the fault is confirmed. Confirmation of a fault
condition occurs if the fault is still found to be present during the driving cycle subsequent to the one when the fault
was first detected.
+ ENGINE MANAGEMENT SYSTEM - V8, DESCRIPTION AND OPERATION, Description - engine
management.
The following types of supplementary control system are used to reduce harmful emissions released into the
atmosphere from the vehicle:
1Crankcase emission control – also known as blow-by gas emissions from the engine crankcase.
2Exhaust emission control – to limit the undesirable by-products of combustion.
3Fuel vapour evaporative loss control – to restrict the emission of fuel through evaporation from the fuel
system.
4Fuel leak detection system (NAS only) – there are two types of system which may be used to check the
evaporative emission system for the presence of leaks from the fuel tank to purge valve.
aVacuum leak detection test – checks for leaks down to 1 mm (0.04 in.) in diameter.
bPositive pressure leak detection test – utilises a leak detection pump to check for leaks down to 0.5 mm (0.02
in.) in diameter.
5Secondary air injection system (NAS only) – to reduce emissions experienced during cold starting.
Crankcase emission control system
The concentration of hydrocarbons in the crankcase of an engine is much greater than that in the vehicle's exhaust
system. In order to prevent the emission of these hydrocarbons into the atmosphere, crankcase emission control
systems are employed and are a standard legal requirement.
The crankcase ventilation system is an integral part of the air supply to the engine combustion chambers and it is
often overlooked when diagnosing problems associated with engine performance. A blocked ventilation pipe or filter
or excessive air leak into the inlet system through a damaged pipe or a leaking gasket can affect the air:fuel mixture,
performance and efficiency of the engine. Periodically check the ventilation hoses are not cracked and that they are
securely fitted to form airtight connections at their relevant ports.
The purpose of the crankcase ventilation system is to ensure that any noxious gas generated in the engine crankcase
is rendered harmless by complete burning of the fuel in the combustion chamber. Burning the crankcase vapours in
a controlled manner decreases the HC pollutants that could be emitted and helps to prevent the development of
sludge in the engine oil as well as increasing fuel economy.
Page 433 of 1672
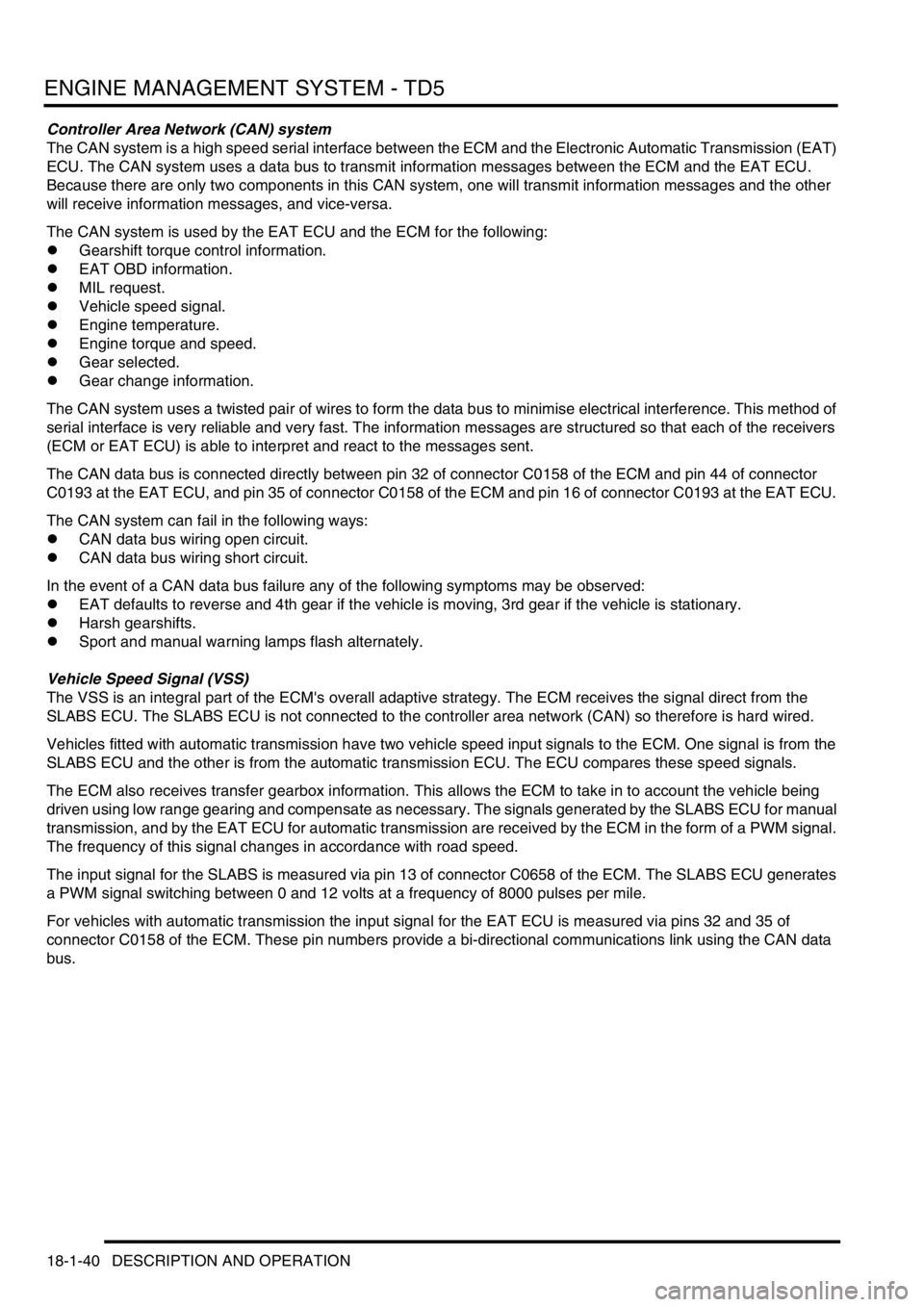
ENGINE MANAGEMENT SYSTEM - TD5
18-1-40 DESCRIPTION AND OPERATION
Controller Area Network (CAN) system
The CAN system is a high speed serial interface between the ECM and the Electronic Automatic Transmission (EAT)
ECU. The CAN system uses a data bus to transmit information messages between the ECM and the EAT ECU.
Because there are only two components in this CAN system, one will transmit information messages and the other
will receive information messages, and vice-versa.
The CAN system is used by the EAT ECU and the ECM for the following:
lGearshift torque control information.
lEAT OBD information.
lMIL request.
lVehicle speed signal.
lEngine temperature.
lEngine torque and speed.
lGear selected.
lGear change information.
The CAN system uses a twisted pair of wires to form the data bus to minimise electrical interference. This method of
serial interface is very reliable and very fast. The information messages are structured so that each of the receivers
(ECM or EAT ECU) is able to interpret and react to the messages sent.
The CAN data bus is connected directly between pin 32 of connector C0158 of the ECM and pin 44 of connector
C0193 at the EAT ECU, and pin 35 of connector C0158 of the ECM and pin 16 of connector C0193 at the EAT ECU.
The CAN system can fail in the following ways:
lCAN data bus wiring open circuit.
lCAN data bus wiring short circuit.
In the event of a CAN data bus failure any of the following symptoms may be observed:
lEAT defaults to reverse and 4th gear if the vehicle is moving, 3rd gear if the vehicle is stationary.
lHarsh gearshifts.
lSport and manual warning lamps flash alternately.
Vehicle Speed Signal (VSS)
The VSS is an integral part of the ECM's overall adaptive strategy. The ECM receives the signal direct from the
SLABS ECU. The SLABS ECU is not connected to the controller area network (CAN) so therefore is hard wired.
Vehicles fitted with automatic transmission have two vehicle speed input signals to the ECM. One signal is from the
SLABS ECU and the other is from the automatic transmission ECU. The ECU compares these speed signals.
The ECM also receives transfer gearbox information. This allows the ECM to take in to account the vehicle being
driven using low range gearing and compensate as necessary. The signals generated by the SLABS ECU for manual
transmission, and by the EAT ECU for automatic transmission are received by the ECM in the form of a PWM signal.
The frequency of this signal changes in accordance with road speed.
The input signal for the SLABS is measured via pin 13 of connector C0658 of the ECM. The SLABS ECU generates
a PWM signal switching between 0 and 12 volts at a frequency of 8000 pulses per mile.
For vehicles with automatic transmission the input signal for the EAT ECU is measured via pins 32 and 35 of
connector C0158 of the ECM. These pin numbers provide a bi-directional communications link using the CAN data
bus.
Page 463 of 1672
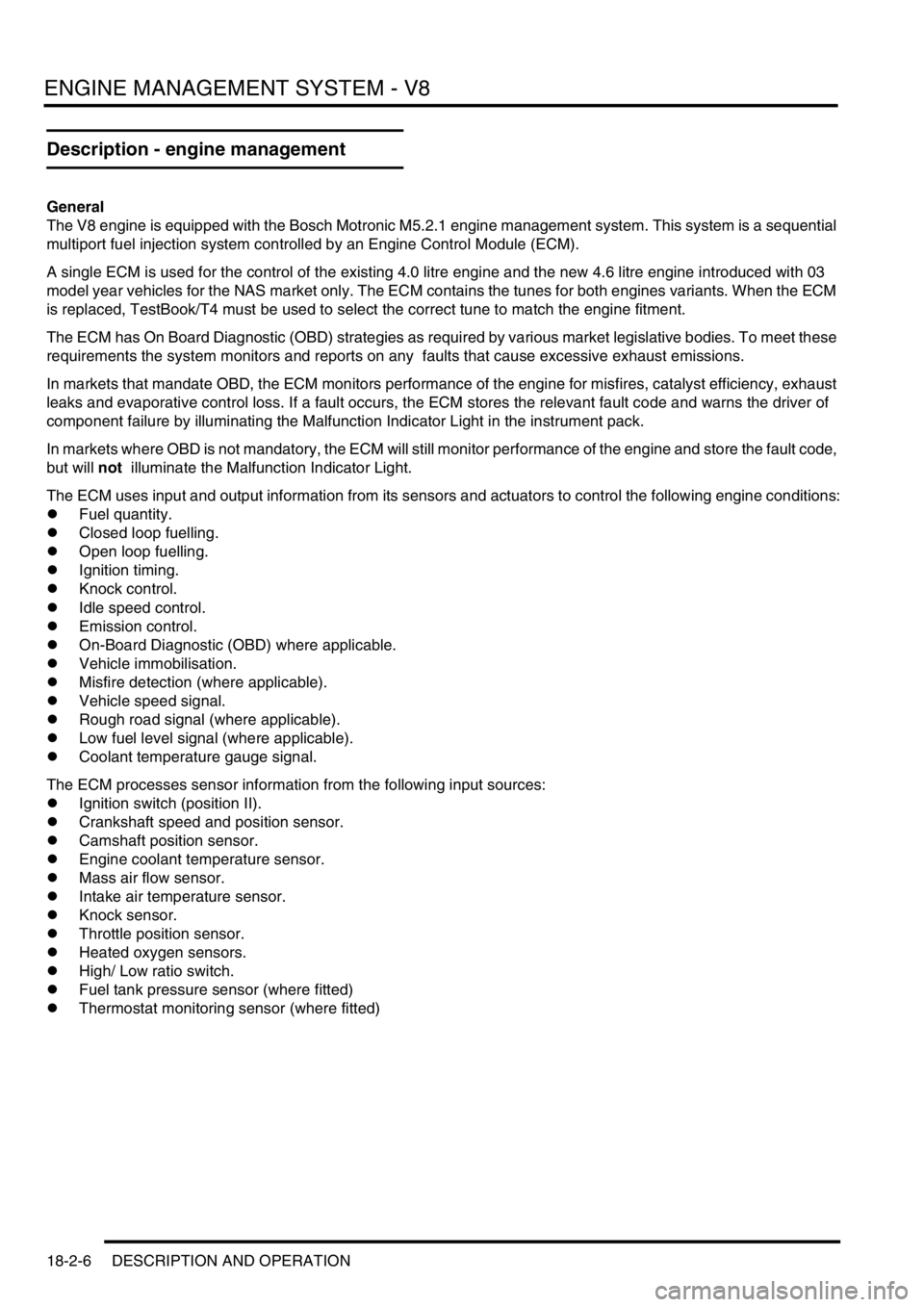
ENGINE MANAGEMENT SYSTEM - V8
18-2-6 DESCRIPTION AND OPERATION
Description - engine management
General
The V8 engine is equipped with the Bosch Motronic M5.2.1 engine management system. This system is a sequential
multiport fuel injection system controlled by an Engine Control Module (ECM).
A single ECM is used for the control of the existing 4.0 litre engine and the new 4.6 litre engine introduced with 03
model year vehicles for the NAS market only. The ECM contains the tunes for both engines variants. When the ECM
is replaced, TestBook/T4 must be used to select the correct tune to match the engine fitment.
The ECM has On Board Diagnostic (OBD) strategies as required by various market legislative bodies. To meet these
requirements the system monitors and reports on any faults that cause excessive exhaust emissions.
In markets that mandate OBD, the ECM monitors performance of the engine for misfires, catalyst efficiency, exhaust
leaks and evaporative control loss. If a fault occurs, the ECM stores the relevant fault code and warns the driver of
component failure by illuminating the Malfunction Indicator Light in the instrument pack.
In markets where OBD is not mandatory, the ECM will still monitor performance of the engine and store the fault code,
but will not illuminate the Malfunction Indicator Light.
The ECM uses input and output information from its sensors and actuators to control the following engine conditions:
lFuel quantity.
lClosed loop fuelling.
lOpen loop fuelling.
lIgnition timing.
lKnock control.
lIdle speed control.
lEmission control.
lOn-Board Diagnostic (OBD) where applicable.
lVehicle immobilisation.
lMisfire detection (where applicable).
lVehicle speed signal.
lRough road signal (where applicable).
lLow fuel level signal (where applicable).
lCoolant temperature gauge signal.
The ECM processes sensor information from the following input sources:
lIgnition switch (position II).
lCrankshaft speed and position sensor.
lCamshaft position sensor.
lEngine coolant temperature sensor.
lMass air flow sensor.
lIntake air temperature sensor.
lKnock sensor.
lThrottle position sensor.
lHeated oxygen sensors.
lHigh/ Low ratio switch.
lFuel tank pressure sensor (where fitted)
lThermostat monitoring sensor (where fitted)
Page 570 of 1672
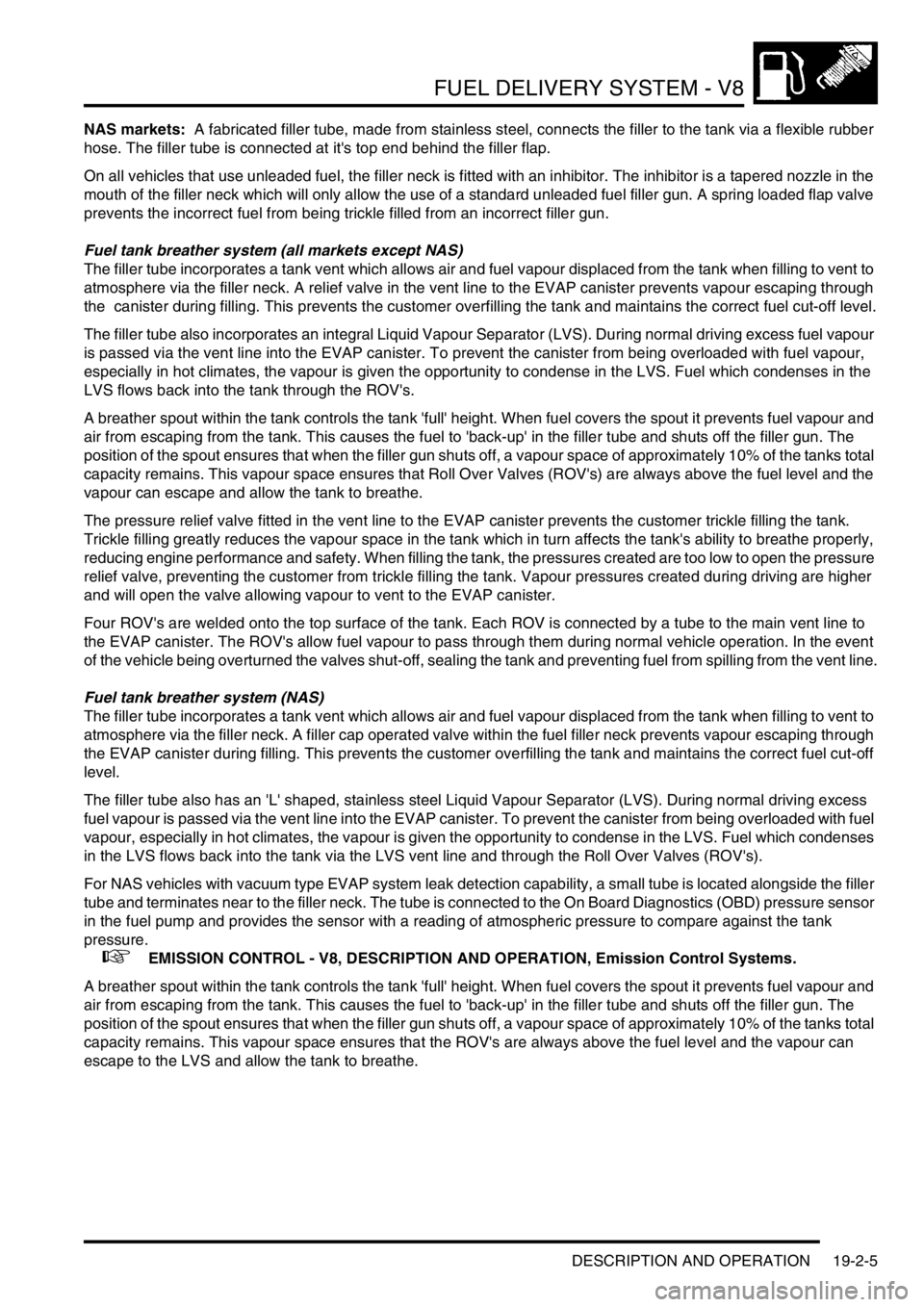
FUEL DELIVERY SYSTEM - V8
DESCRIPTION AND OPERATION 19-2-5
NAS markets: A fabricated filler tube, made from stainless steel, connects the filler to the tank via a flexible rubber
hose. The filler tube is connected at it's top end behind the filler flap.
On all vehicles that use unleaded fuel, the filler neck is fitted with an inhibitor. The inhibitor is a tapered nozzle in the
mouth of the filler neck which will only allow the use of a standard unleaded fuel filler gun. A spring loaded flap valve
prevents the incorrect fuel from being trickle filled from an incorrect filler gun.
Fuel tank breather system (all markets except NAS)
The filler tube incorporates a tank vent which allows air and fuel vapour displaced from the tank when filling to vent to
atmosphere via the filler neck. A relief valve in the vent line to the EVAP canister prevents vapour escaping through
the canister during filling. This prevents the customer overfilling the tank and maintains the correct fuel cut-off level.
The filler tube also incorporates an integral Liquid Vapour Separator (LVS). During normal driving excess fuel vapour
is passed via the vent line into the EVAP canister. To prevent the canister from being overloaded with fuel vapour,
especially in hot climates, the vapour is given the opportunity to condense in the LVS. Fuel which condenses in the
LVS flows back into the tank through the ROV's.
A breather spout within the tank controls the tank 'full' height. When fuel covers the spout it prevents fuel vapour and
air from escaping from the tank. This causes the fuel to 'back-up' in the filler tube and shuts off the filler gun. The
position of the spout ensures that when the filler gun shuts off, a vapour space of approximately 10% of the tanks total
capacity remains. This vapour space ensures that Roll Over Valves (ROV's) are always above the fuel level and the
vapour can escape and allow the tank to breathe.
The pressure relief valve fitted in the vent line to the EVAP canister prevents the customer trickle filling the tank.
Trickle filling greatly reduces the vapour space in the tank which in turn affects the tank's ability to breathe properly,
reducing engine performance and safety. When filling the tank, the pressures created are too low to open the pressure
relief valve, preventing the customer from trickle filling the tank. Vapour pressures created during driving are higher
and will open the valve allowing vapour to vent to the EVAP canister.
Four ROV's are welded onto the top surface of the tank. Each ROV is connected by a tube to the main vent line to
the EVAP canister. The ROV's allow fuel vapour to pass through them during normal vehicle operation. In the event
of the vehicle being overturned the valves shut-off, sealing the tank and preventing fuel from spilling from the vent line.
Fuel tank breather system (NAS)
The filler tube incorporates a tank vent which allows air and fuel vapour displaced from the tank when filling to vent to
atmosphere via the filler neck. A filler cap operated valve within the fuel filler neck prevents vapour escaping through
the EVAP canister during filling. This prevents the customer overfilling the tank and maintains the correct fuel cut-off
level.
The filler tube also has an 'L' shaped, stainless steel Liquid Vapour Separator (LVS). During normal driving excess
fuel vapour is passed via the vent line into the EVAP canister. To prevent the canister from being overloaded with fuel
vapour, especially in hot climates, the vapour is given the opportunity to condense in the LVS. Fuel which condenses
in the LVS flows back into the tank via the LVS vent line and through the Roll Over Valves (ROV's).
For NAS vehicles with vacuum type EVAP system leak detection capability, a small tube is located alongside the filler
tube and terminates near to the filler neck. The tube is connected to the On Board Diagnostics (OBD) pressure sensor
in the fuel pump and provides the sensor with a reading of atmospheric pressure to compare against the tank
pressure.
+ EMISSION CONTROL - V8, DESCRIPTION AND OPERATION, Emission Control Systems.
A breather spout within the tank controls the tank 'full' height. When fuel covers the spout it prevents fuel vapour and
air from escaping from the tank. This causes the fuel to 'back-up' in the filler tube and shuts off the filler gun. The
position of the spout ensures that when the filler gun shuts off, a vapour space of approximately 10% of the tanks total
capacity remains. This vapour space ensures that the ROV's are always above the fuel level and the vapour can
escape to the LVS and allow the tank to breathe.
Page 816 of 1672
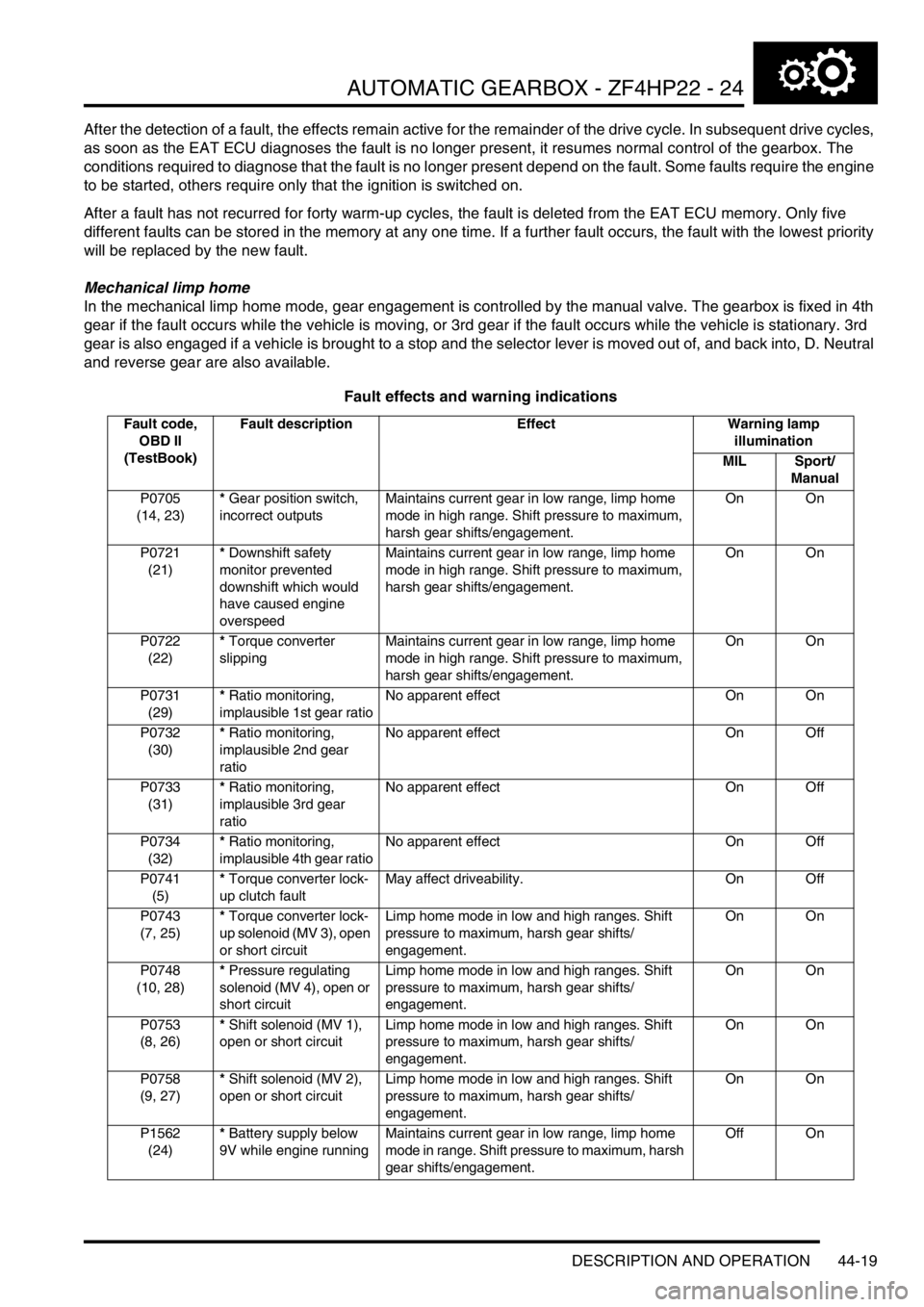
AUTOMATIC GEARBOX - ZF4HP22 - 24
DESCRIPTION AND OPERATION 44-19
After the detection of a fault, the effects remain active for the remainder of the drive cycle. In subsequent drive cycles,
as soon as the EAT ECU diagnoses the fault is no longer present, it resumes normal control of the gearbox. The
conditions required to diagnose that the fault is no longer present depend on the fault. Some faults require the engine
to be started, others require only that the ignition is switched on.
After a fault has not recurred for forty warm-up cycles, the fault is deleted from the EAT ECU memory. Only five
different faults can be stored in the memory at any one time. If a further fault occurs, the fault with the lowest priority
will be replaced by the new fault.
Mechanical limp home
In the mechanical limp home mode, gear engagement is controlled by the manual valve. The gearbox is fixed in 4th
gear if the fault occurs while the vehicle is moving, or 3rd gear if the fault occurs while the vehicle is stationary. 3rd
gear is also engaged if a vehicle is brought to a stop and the selector lever is moved out of, and back into, D. Neutral
and reverse gear are also available.
Fault effects and warning indications
Fault code,
OBD II
(TestBook)Fault description Effect Warning lamp
illumination
MIL Sport/
Manual
P0705
(14, 23)* Gear position switch,
incorrect outputsMaintains current gear in low range, limp home
mode in high range. Shift pressure to maximum,
harsh gear shifts/engagement.On On
P0721
(21)* Downshift safety
monitor prevented
downshift which would
have caused engine
overspeedMaintains current gear in low range, limp home
mode in high range. Shift pressure to maximum,
harsh gear shifts/engagement.On On
P0722
(22)* Torque converter
slippingMaintains current gear in low range, limp home
mode in high range. Shift pressure to maximum,
harsh gear shifts/engagement.On On
P0731
(29)* Ratio monitoring,
implausible 1st gear ratioNo apparent effect On On
P0732
(30)* Ratio monitoring,
implausible 2nd gear
ratioNo apparent effect On Off
P0733
(31)* Ratio monitoring,
implausible 3rd gear
ratioNo apparent effect On Off
P0734
(32)* Ratio monitoring,
implausible 4th gear ratioNo apparent effect On Off
P0741
(5)* Torque converter lock-
up clutch faultMay affect driveability. On Off
P0743
(7, 25)* Torque converter lock-
up solenoid (MV 3), open
or short circuitLimp home mode in low and high ranges. Shift
pressure to maximum, harsh gear shifts/
engagement.On On
P0748
(10, 28)* Pressure regulating
solenoid (MV 4), open or
short circuitLimp home mode in low and high ranges. Shift
pressure to maximum, harsh gear shifts/
engagement.On On
P0753
(8, 26)* Shift solenoid (MV 1),
open or short circuitLimp home mode in low and high ranges. Shift
pressure to maximum, harsh gear shifts/
engagement.On On
P0758
(9, 27)* Shift solenoid (MV 2),
open or short circuitLimp home mode in low and high ranges. Shift
pressure to maximum, harsh gear shifts/
engagement.On On
P1562
(24)* Battery supply below
9V while engine runningMaintains current gear in low range, limp home
mode in range. Shift pressure to maximum, harsh
gear shifts/engagement.Off On
Page 817 of 1672
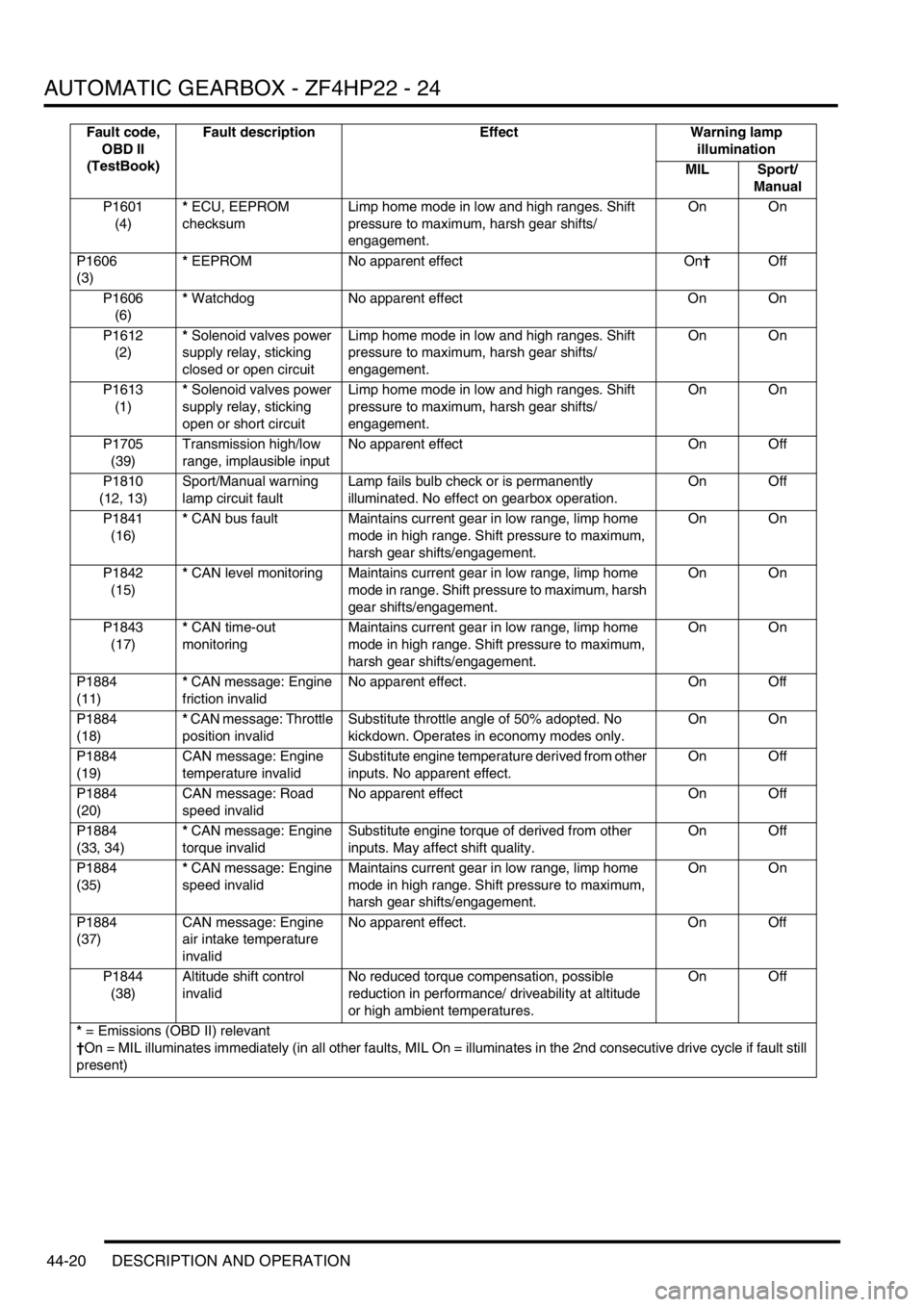
AUTOMATIC GEARBOX - ZF4HP22 - 24
44-20 DESCRIPTION AND OPERATION
P1601
(4)* ECU, EEPROM
checksumLimp home mode in low and high ranges. Shift
pressure to maximum, harsh gear shifts/
engagement.On On
P1606
(3)* EEPROM No apparent effect On†Off
P1606
(6)* Watchdog No apparent effect On On
P1612
(2)* Solenoid valves power
supply relay, sticking
closed or open circuitLimp home mode in low and high ranges. Shift
pressure to maximum, harsh gear shifts/
engagement.On On
P1613
(1)* Solenoid valves power
supply relay, sticking
open or short circuitLimp home mode in low and high ranges. Shift
pressure to maximum, harsh gear shifts/
engagement.On On
P1705
(39)Transmission high/low
range, implausible inputNo apparent effect On Off
P1810
(12, 13)Sport/Manual warning
lamp circuit faultLamp fails bulb check or is permanently
illuminated. No effect on gearbox operation.On Off
P1841
(16)* CAN bus fault Maintains current gear in low range, limp home
mode in high range. Shift pressure to maximum,
harsh gear shifts/engagement.On On
P1842
(15)* CAN level monitoring Maintains current gear in low range, limp home
mode in range. Shift pressure to maximum, harsh
gear shifts/engagement.On On
P1843
(17)* CAN time-out
monitoringMaintains current gear in low range, limp home
mode in high range. Shift pressure to maximum,
harsh gear shifts/engagement.On On
P1884
(11)* CAN message: Engine
friction invalidNo apparent effect. On Off
P1884
(18)* CAN message: Throttle
position invalidSubstitute throttle angle of 50% adopted. No
kickdown. Operates in economy modes only.On On
P1884
(19)CAN message: Engine
temperature invalidSubstitute engine temperature derived from other
inputs. No apparent effect.On Off
P1884
(20)CAN message: Road
speed invalidNo apparent effect On Off
P1884
(33, 34)* CAN message: Engine
torque invalidSubstitute engine torque of derived from other
inputs. May affect shift quality.On Off
P1884
(35)* CAN message: Engine
speed invalidMaintains current gear in low range, limp home
mode in high range. Shift pressure to maximum,
harsh gear shifts/engagement.On On
P1884
(37)CAN message: Engine
air intake temperature
invalidNo apparent effect. On Off
P1844
(38)Altitude shift control
invalidNo reduced torque compensation, possible
reduction in performance/ driveability at altitude
or high ambient temperatures.On Off
* = Emissions (OBD II) relevant
†On = MIL illuminates immediately (in all other faults, MIL On = illuminates in the 2nd consecutive drive cycle if fault still
present)Fault code,
OBD II
(TestBook)Fault description Effect Warning lamp
illumination
MIL Sport/
Manual