ac compre LAND ROVER DISCOVERY 2002 Workshop Manual
[x] Cancel search | Manufacturer: LAND ROVER, Model Year: 2002, Model line: DISCOVERY, Model: LAND ROVER DISCOVERY 2002Pages: 1672, PDF Size: 46.1 MB
Page 4 of 1672
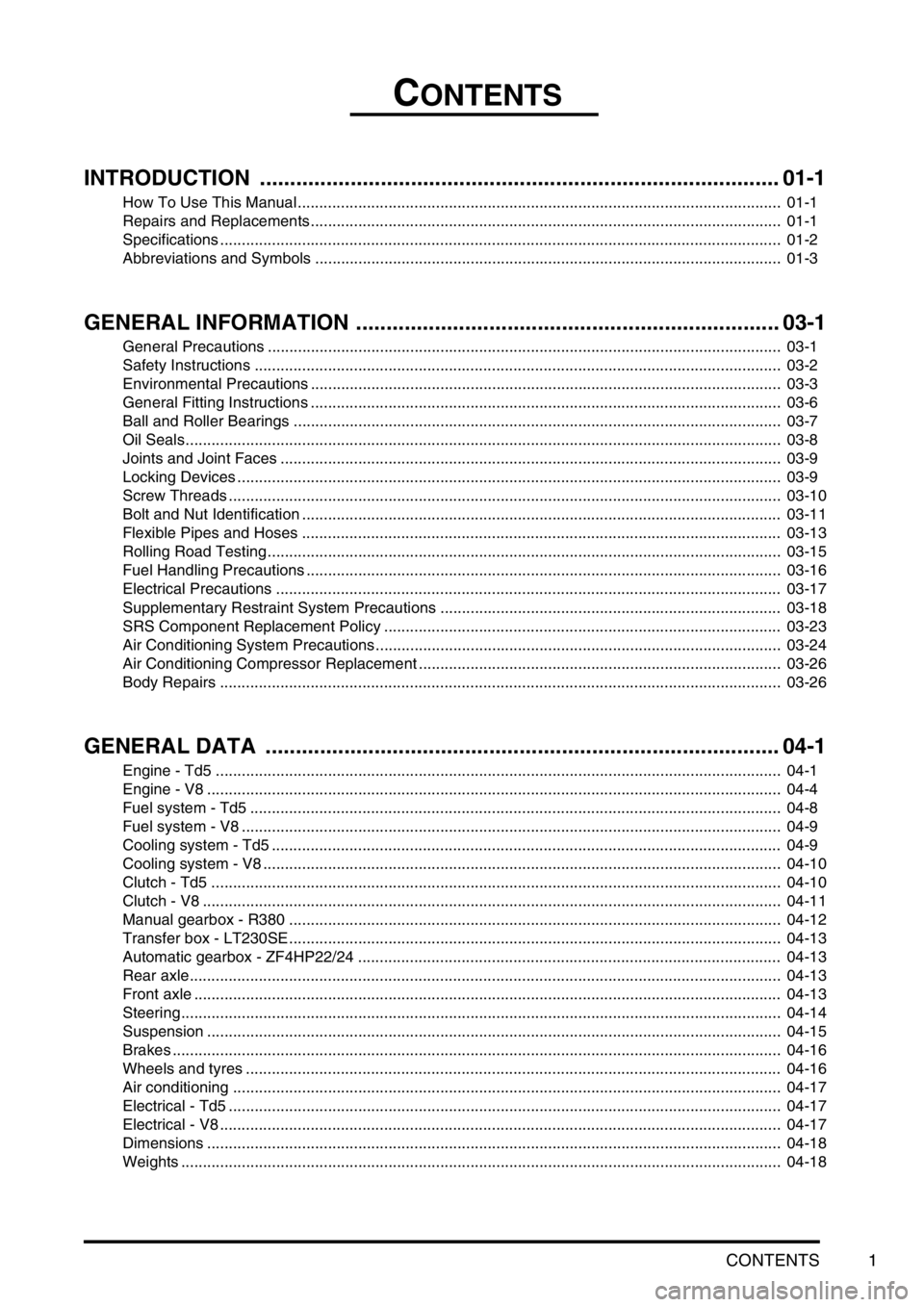
CONTENTS
CONTENTS 1
INTRODUCTION ...................................................................................... 01-1
How To Use This Manual................................................................................................................ 01-1
Repairs and Replacements ............................................................................................................. 01-1
Specifications .................................................................................................................................. 01-2
Abbreviations and Symbols ............................................................................................................ 01-3
GENERAL INFORMATION ...................................................................... 03-1
General Precautions ....................................................................................................................... 03-1
Safety Instructions .......................................................................................................................... 03-2
Environmental Precautions ............................................................................................................. 03-3
General Fitting Instructions ............................................................................................................. 03-6
Ball and Roller Bearings ................................................................................................................. 03-7
Oil Seals.......................................................................................................................................... 03-8
Joints and Joint Faces .................................................................................................................... 03-9
Locking Devices .............................................................................................................................. 03-9
Screw Threads ................................................................................................................................ 03-10
Bolt and Nut Identification ............................................................................................................... 03-11
Flexible Pipes and Hoses ............................................................................................................... 03-13
Rolling Road Testing....................................................................................................................... 03-15
Fuel Handling Precautions .............................................................................................................. 03-16
Electrical Precautions ..................................................................................................................... 03-17
Supplementary Restraint System Precautions ............................................................................... 03-18
SRS Component Replacement Policy ............................................................................................ 03-23
Air Conditioning System Precautions .............................................................................................. 03-24
Air Conditioning Compressor Replacement .................................................................................... 03-26
Body Repairs .................................................................................................................................. 03-26
GENERAL DATA ..................................................................................... 04-1
Engine - Td5 ................................................................................................................................... 04-1
Engine - V8 ..................................................................................................................................... 04-4
Fuel system - Td5 ........................................................................................................................... 04-8
Fuel system - V8 ............................................................................................................................. 04-9
Cooling system - Td5 ...................................................................................................................... 04-9
Cooling system - V8 ........................................................................................................................ 04-10
Clutch - Td5 .................................................................................................................................... 04-10
Clutch - V8 ...................................................................................................................................... 04-11
Manual gearbox - R380 .................................................................................................................. 04-12
Transfer box - LT230SE .................................................................................................................. 04-13
Automatic gearbox - ZF4HP22/24 .................................................................................................. 04-13
Rear axle......................................................................................................................................... 04-13
Front axle ........................................................................................................................................ 04-13
Steering........................................................................................................................................... 04-14
Suspension ..................................................................................................................................... 04-15
Brakes ............................................................................................................................................. 04-16
Wheels and tyres ............................................................................................................................ 04-16
Air conditioning ............................................................................................................................... 04-17
Electrical - Td5 ................................................................................................................................ 04-17
Electrical - V8 .................................................................................................................................. 04-17
Dimensions ..................................................................................................................................... 04-18
Weights ........................................................................................................................................... 04-18
Page 18 of 1672
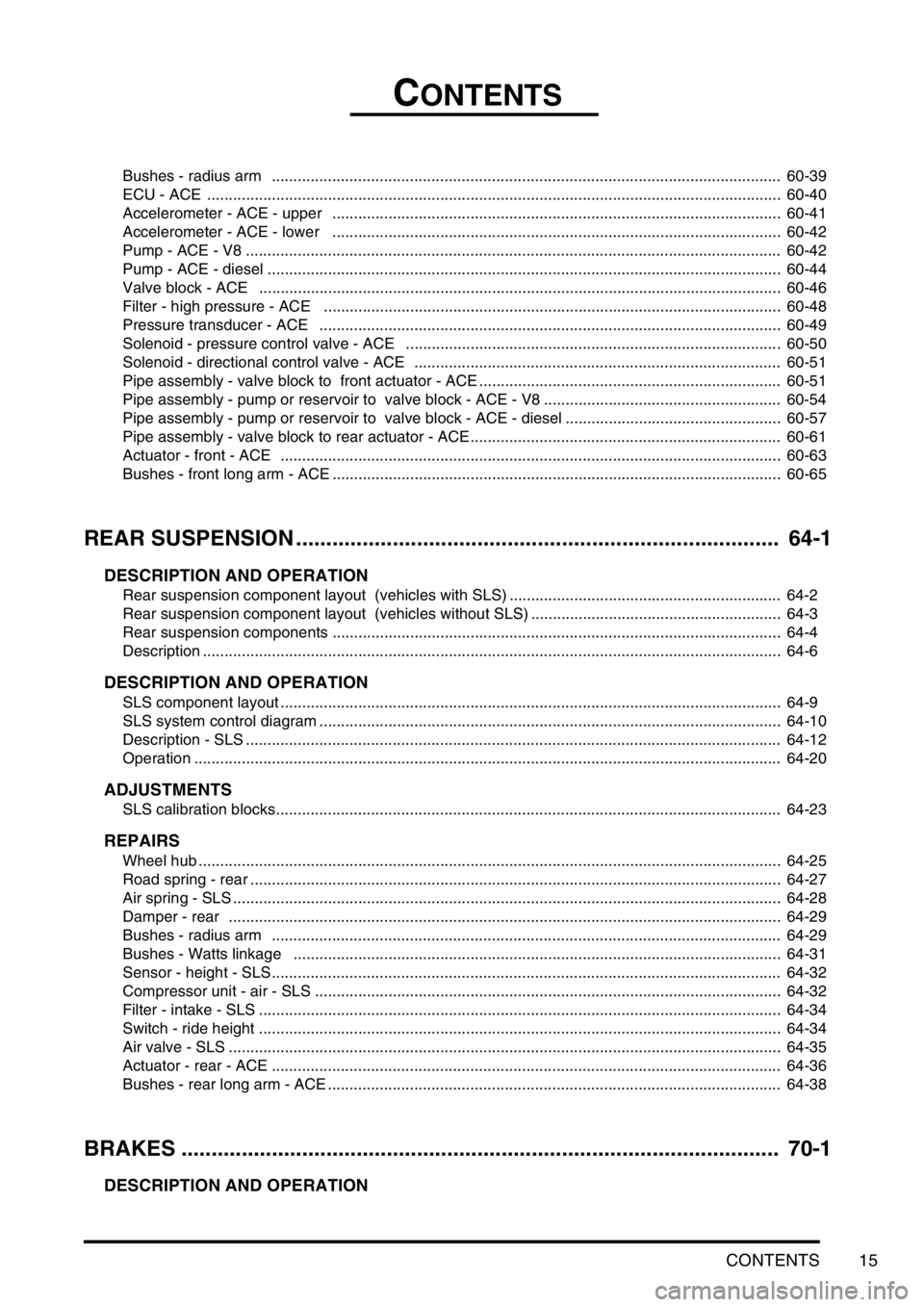
CONTENTS
CONTENTS 15
Bushes - radius arm ...................................................................................................................... 60-39
ECU - ACE ..................................................................................................................................... 60-40
Accelerometer - ACE - upper ........................................................................................................ 60-41
Accelerometer - ACE - lower ........................................................................................................ 60-42
Pump - ACE - V8 ............................................................................................................................ 60-42
Pump - ACE - diesel ....................................................................................................................... 60-44
Valve block - ACE ......................................................................................................................... 60-46
Filter - high pressure - ACE .......................................................................................................... 60-48
Pressure transducer - ACE ........................................................................................................... 60-49
Solenoid - pressure control valve - ACE ....................................................................................... 60-50
Solenoid - directional control valve - ACE ..................................................................................... 60-51
Pipe assembly - valve block to front actuator - ACE ...................................................................... 60-51
Pipe assembly - pump or reservoir to valve block - ACE - V8 ....................................................... 60-54
Pipe assembly - pump or reservoir to valve block - ACE - diesel .................................................. 60-57
Pipe assembly - valve block to rear actuator - ACE ........................................................................ 60-61
Actuator - front - ACE .................................................................................................................... 60-63
Bushes - front long arm - ACE ........................................................................................................ 60-65
REAR SUSPENSION ................................................................................ 64-1
DESCRIPTION AND OPERATION
Rear suspension component layout (vehicles with SLS) ............................................................... 64-2
Rear suspension component layout (vehicles without SLS) .......................................................... 64-3
Rear suspension components ........................................................................................................ 64-4
Description ...................................................................................................................................... 64-6
DESCRIPTION AND OPERATION
SLS component layout .................................................................................................................... 64-9
SLS system control diagram ........................................................................................................... 64-10
Description - SLS ............................................................................................................................ 64-12
Operation ........................................................................................................................................ 64-20
ADJUSTMENTS
SLS calibration blocks..................................................................................................................... 64-23
REPAIRS
Wheel hub ....................................................................................................................................... 64-25
Road spring - rear ........................................................................................................................... 64-27
Air spring - SLS ............................................................................................................................... 64-28
Damper - rear ................................................................................................................................ 64-29
Bushes - radius arm ...................................................................................................................... 64-29
Bushes - Watts linkage ................................................................................................................. 64-31
Sensor - height - SLS...................................................................................................................... 64-32
Compressor unit - air - SLS ............................................................................................................ 64-32
Filter - intake - SLS ......................................................................................................................... 64-34
Switch - ride height ......................................................................................................................... 64-34
Air valve - SLS ................................................................................................................................ 64-35
Actuator - rear - ACE ...................................................................................................................... 64-36
Bushes - rear long arm - ACE ......................................................................................................... 64-38
BRAKES ................................................................................................... 70-1
DESCRIPTION AND OPERATION
Page 24 of 1672
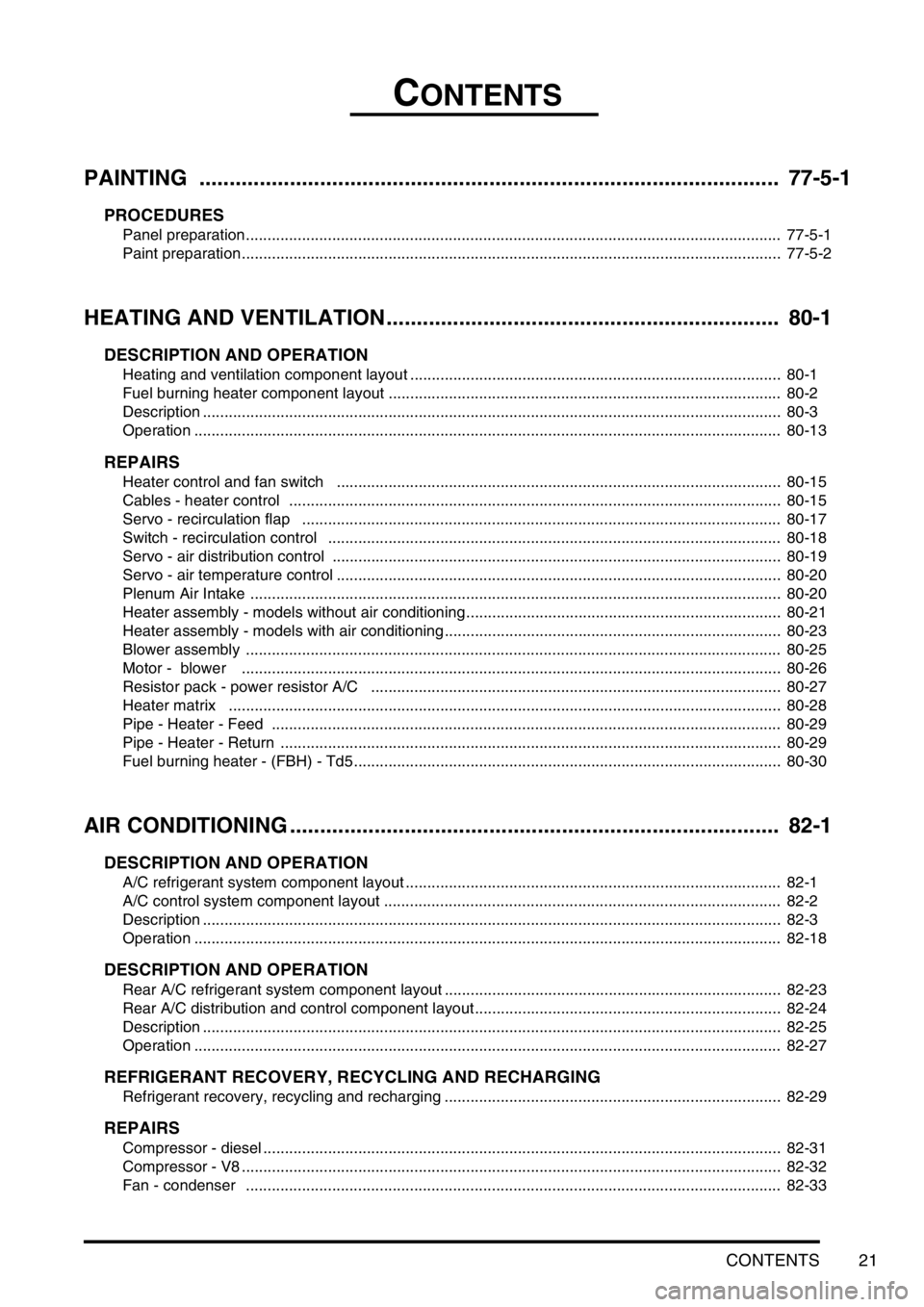
CONTENTS
CONTENTS 21
PAINTING ................................................................................................ 77-5-1
PROCEDURES
Panel preparation............................................................................................................................ 77-5-1
Paint preparation............................................................................................................................. 77-5-2
HEATING AND VENTILATION................................................................. 80-1
DESCRIPTION AND OPERATION
Heating and ventilation component layout ...................................................................................... 80-1
Fuel burning heater component layout ........................................................................................... 80-2
Description ...................................................................................................................................... 80-3
Operation ........................................................................................................................................ 80-13
REPAIRS
Heater control and fan switch ....................................................................................................... 80-15
Cables - heater control .................................................................................................................. 80-15
Servo - recirculation flap ............................................................................................................... 80-17
Switch - recirculation control ......................................................................................................... 80-18
Servo - air distribution control ........................................................................................................ 80-19
Servo - air temperature control ....................................................................................................... 80-20
Plenum Air Intake ........................................................................................................................... 80-20
Heater assembly - models without air conditioning ......................................................................... 80-21
Heater assembly - models with air conditioning .............................................................................. 80-23
Blower assembly ............................................................................................................................ 80-25
Motor - blower ............................................................................................................................. 80-26
Resistor pack - power resistor A/C ............................................................................................... 80-27
Heater matrix ................................................................................................................................ 80-28
Pipe - Heater - Feed ...................................................................................................................... 80-29
Pipe - Heater - Return .................................................................................................................... 80-29
Fuel burning heater - (FBH) - Td5................................................................................................... 80-30
AIR CONDITIONING ................................................................................. 82-1
DESCRIPTION AND OPERATION
A/C refrigerant system component layout ....................................................................................... 82-1
A/C control system component layout ............................................................................................ 82-2
Description ...................................................................................................................................... 82-3
Operation ........................................................................................................................................ 82-18
DESCRIPTION AND OPERATION
Rear A/C refrigerant system component layout .............................................................................. 82-23
Rear A/C distribution and control component layout ....................................................................... 82-24
Description ...................................................................................................................................... 82-25
Operation ........................................................................................................................................ 82-27
REFRIGERANT RECOVERY, RECYCLING AND RECHARGING
Refrigerant recovery, recycling and recharging .............................................................................. 82-29
REPAIRS
Compressor - diesel ........................................................................................................................ 82-31
Compressor - V8 ............................................................................................................................. 82-32
Fan - condenser ............................................................................................................................ 82-33
Page 32 of 1672
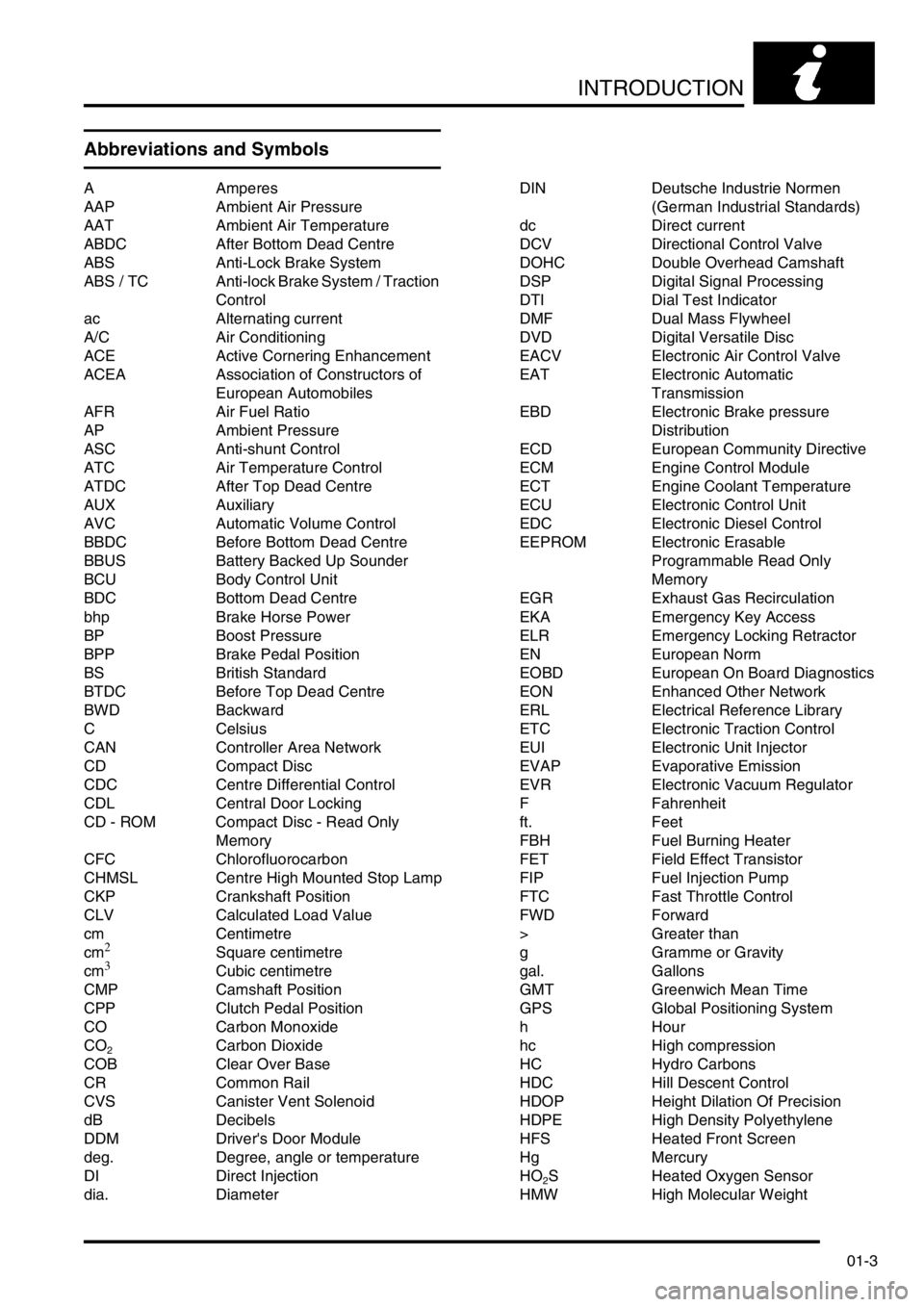
INTRODUCTION
01-3
Abbreviations and Symbols
A Amperes
AAP Ambient Air Pressure
AAT Ambient Air Temperature
ABDC After Bottom Dead Centre
ABS Anti-Lock Brake System
ABS / TC Anti-lock Brake System / Traction
Control
ac Alternating current
A/C Air Conditioning
ACE Active Cornering Enhancement
ACEA Association of Constructors of
European Automobiles
AFR Air Fuel Ratio
AP Ambient Pressure
ASC Anti-shunt Control
ATC Air Temperature Control
ATDC After Top Dead Centre
AUX Auxiliary
AVC Automatic Volume Control
BBDC Before Bottom Dead Centre
BBUS Battery Backed Up Sounder
BCU Body Control Unit
BDC Bottom Dead Centre
bhp Brake Horse Power
BP Boost Pressure
BPP Brake Pedal Position
BS British Standard
BTDC Before Top Dead Centre
BWD Backward
C Celsius
CAN Controller Area Network
CD Compact Disc
CDC Centre Differential Control
CDL Central Door Locking
CD - ROM Compact Disc - Read Only
Memory
CFC Chlorofluorocarbon
CHMSL Centre High Mounted Stop Lamp
CKP Crankshaft Position
CLV Calculated Load Value
cm Centimetre
cm
2Square centimetre
cm3Cubic centimetre
CMP Camshaft Position
CPP Clutch Pedal Position
CO Carbon Monoxide
CO
2Carbon Dioxide
COB Clear Over Base
CR Common Rail
CVS Canister Vent Solenoid
dB Decibels
DDM Driver's Door Module
deg. Degree, angle or temperature
DI Direct Injection
dia. DiameterDIN Deutsche Industrie Normen
(German Industrial Standards)
dc Direct current
DCV Directional Control Valve
DOHC Double Overhead Camshaft
DSP Digital Signal Processing
DTI Dial Test Indicator
DMF Dual Mass Flywheel
DVD Digital Versatile Disc
EACV Electronic Air Control Valve
EAT Electronic Automatic
Transmission
EBD Electronic Brake pressure
Distribution
ECD European Community Directive
ECM Engine Control Module
ECT Engine Coolant Temperature
ECU Electronic Control Unit
EDC Electronic Diesel Control
EEPROM Electronic Erasable
Programmable Read Only
Memory
EGR Exhaust Gas Recirculation
EKA Emergency Key Access
ELR Emergency Locking Retractor
EN European Norm
EOBD European On Board Diagnostics
EON Enhanced Other Network
ERL Electrical Reference Library
ETC Electronic Traction Control
EUI Electronic Unit Injector
EVAP Evaporative Emission
EVR Electronic Vacuum Regulator
F Fahrenheit
ft. Feet
FBH Fuel Burning Heater
FET Field Effect Transistor
FIP Fuel Injection Pump
FTC Fast Throttle Control
FWD Forward
> Greater than
g Gramme or Gravity
gal. Gallons
GMT Greenwich Mean Time
GPS Global Positioning System
hHour
hc High compression
HC Hydro Carbons
HDC Hill Descent Control
HDOP Height Dilation Of Precision
HDPE High Density Polyethylene
HFS Heated Front Screen
Hg Mercury
HO
2S Heated Oxygen Sensor
HMW High Molecular Weight
Page 33 of 1672
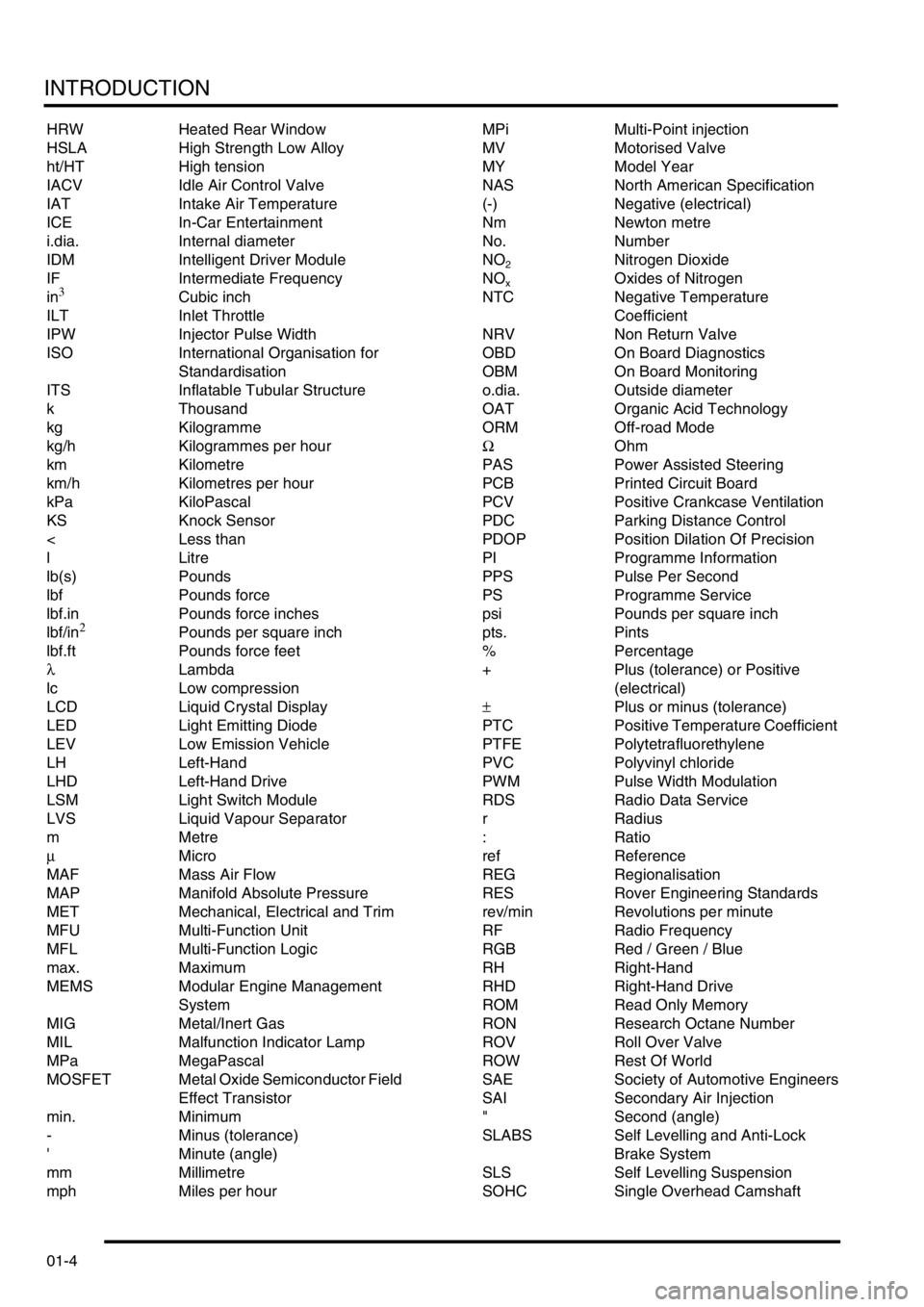
INTRODUCTION
01-4
HRW Heated Rear Window
HSLA High Strength Low Alloy
ht/HT High tension
IACV Idle Air Control Valve
IAT Intake Air Temperature
ICE In-Car Entertainment
i.dia. Internal diameter
IDM Intelligent Driver Module
IF Intermediate Frequency
in
3Cubic inch
ILT Inlet Throttle
IPW Injector Pulse Width
ISO International Organisation for
Standardisation
ITS Inflatable Tubular Structure
k Thousand
kg Kilogramme
kg/h Kilogrammes per hour
km Kilometre
km/h Kilometres per hour
kPa KiloPascal
KS Knock Sensor
lb(s) Pounds
lbf Pounds force
lbf.in Pounds force inches
lbf/in
2Pounds per square inch
lbf.ft Pounds force feet
λLambda
lc Low compression
LCD Liquid Crystal Display
LED Light Emitting Diode
LEV Low Emission Vehicle
LH Left-Hand
LHD Left-Hand Drive
LSM Light Switch Module
LVS Liquid Vapour Separator
mMetre
µMicro
MAF Mass Air Flow
MAP Manifold Absolute Pressure
MET Mechanical, Electrical and Trim
MFU Multi-Function Unit
MFL Multi-Function Logic
max. Maximum
MEMS Modular Engine Management
System
MIG Metal/Inert Gas
MIL Malfunction Indicator Lamp
MPa MegaPascal
MOSFET Metal Oxide Semiconductor Field
Effect Transistor
min. Minimum
- Minus (tolerance)
' Minute (angle)
mm Millimetre
mph Miles per hour MPi Multi-Point injection
MV Motorised Valve
MY Model Year
NAS North American Specification
(-) Negative (electrical)
Nm Newton metre
No. Number
NO
2Nitrogen Dioxide
NO
xOxides of Nitrogen
NTC Negative Temperature
Coefficient
NRV Non Return Valve
OBD On Board Diagnostics
OBM On Board Monitoring
o.dia. Outside diameter
OAT Organic Acid Technology
ORM Off-road Mode
ΩOhm
PAS Power Assisted Steering
PCB Printed Circuit Board
PCV Positive Crankcase Ventilation
PDC Parking Distance Control
PDOP Position Dilation Of Precision
PI Programme Information
PPS Pulse Per Second
PS Programme Service
psi Pounds per square inch
pts. Pints
% Percentage
+ Plus (tolerance) or Positive
(electrical)
±Plus or minus (tolerance)
PTC Positive Temperature Coefficient
PTFE Polytetrafluorethylene
PVC Polyvinyl chloride
PWM Pulse Width Modulation
RDS Radio Data Service
rRadius
:Ratio
ref Reference
REG Regionalisation
RES Rover Engineering Standards
rev/min Revolutions per minute
RF Radio Frequency
RGB Red / Green / Blue
RH Right-Hand
RHD Right-Hand Drive
ROM Read Only Memory
RON Research Octane Number
ROV Roll Over Valve
ROW Rest Of World
SAE Society of Automotive Engineers
SAI Secondary Air Injection
" Second (angle)
SLABS Self Levelling and Anti-Lock
Brake System
SLS Self Levelling Suspension
SOHC Single Overhead Camshaft
Page 39 of 1672
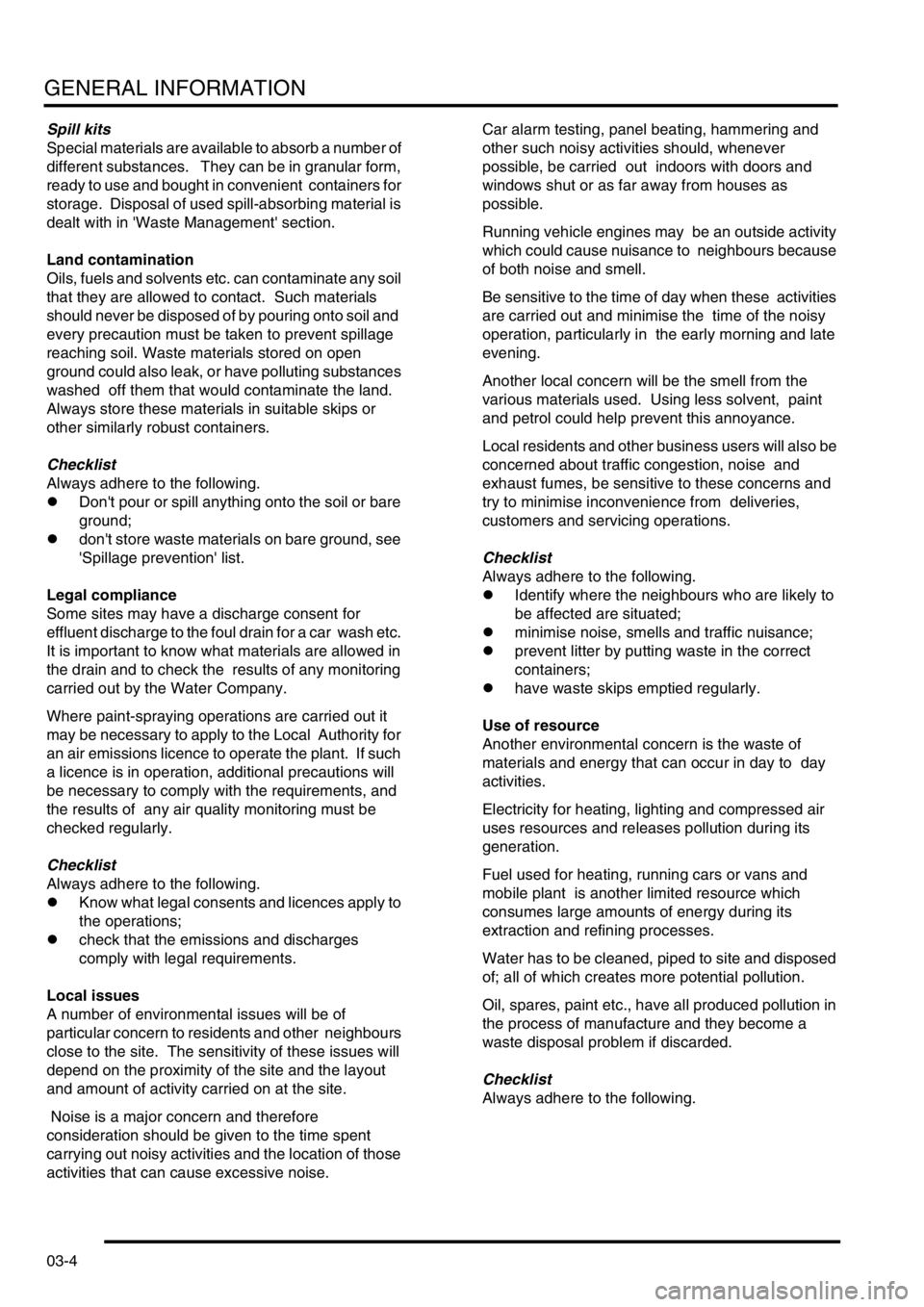
GENERAL INFORMATION
03-4
Spill kits
Special materials are available to absorb a number of
different substances. They can be in granular form,
ready to use and bought in convenient containers for
storage. Disposal of used spill-absorbing material is
dealt with in 'Waste Management' section.
Land contamination
Oils, fuels and solvents etc. can contaminate any soil
that they are allowed to contact. Such materials
should never be disposed of by pouring onto soil and
every precaution must be taken to prevent spillage
reaching soil. Waste materials stored on open
ground could also leak, or have polluting substances
washed off them that would contaminate the land.
Always store these materials in suitable skips or
other similarly robust containers.
Checklist
Always adhere to the following.
lDon't pour or spill anything onto the soil or bare
ground;
ldon't store waste materials on bare ground, see
'Spillage prevention' list.
Legal compliance
Some sites may have a discharge consent for
effluent discharge to the foul drain for a car wash etc.
It is important to know what materials are allowed in
the drain and to check the results of any monitoring
carried out by the Water Company.
Where paint-spraying operations are carried out it
may be necessary to apply to the Local Authority for
an air emissions licence to operate the plant. If such
a licence is in operation, additional precautions will
be necessary to comply with the requirements, and
the results of any air quality monitoring must be
checked regularly.
Checklist
Always adhere to the following.
lKnow what legal consents and licences apply to
the operations;
lcheck that the emissions and discharges
comply with legal requirements.
Local issues
A number of environmental issues will be of
particular concern to residents and other neighbours
close to the site. The sensitivity of these issues will
depend on the proximity of the site and the layout
and amount of activity carried on at the site.
Noise is a major concern and therefore
consideration should be given to the time spent
carrying out noisy activities and the location of those
activities that can cause excessive noise. Car alarm testing, panel beating, hammering and
other such noisy activities should, whenever
possible, be carried out indoors with doors and
windows shut or as far away from houses as
possible.
Running vehicle engines may be an outside activity
which could cause nuisance to neighbours because
of both noise and smell.
Be sensitive to the time of day when these activities
are carried out and minimise the time of the noisy
operation, particularly in the early morning and late
evening.
Another local concern will be the smell from the
various materials used. Using less solvent, paint
and petrol could help prevent this annoyance.
Local residents and other business users will also be
concerned about traffic congestion, noise and
exhaust fumes, be sensitive to these concerns and
try to minimise inconvenience from deliveries,
customers and servicing operations.
Checklist
Always adhere to the following.
lIdentify where the neighbours who are likely to
be affected are situated;
lminimise noise, smells and traffic nuisance;
lprevent litter by putting waste in the correct
containers;
lhave waste skips emptied regularly.
Use of resource
Another environmental concern is the waste of
materials and energy that can occur in day to day
activities.
Electricity for heating, lighting and compressed air
uses resources and releases pollution during its
generation.
Fuel used for heating, running cars or vans and
mobile plant is another limited resource which
consumes large amounts of energy during its
extraction and refining processes.
Water has to be cleaned, piped to site and disposed
of; all of which creates more potential pollution.
Oil, spares, paint etc., have all produced pollution in
the process of manufacture and they become a
waste disposal problem if discarded.
Checklist
Always adhere to the following.
Page 40 of 1672
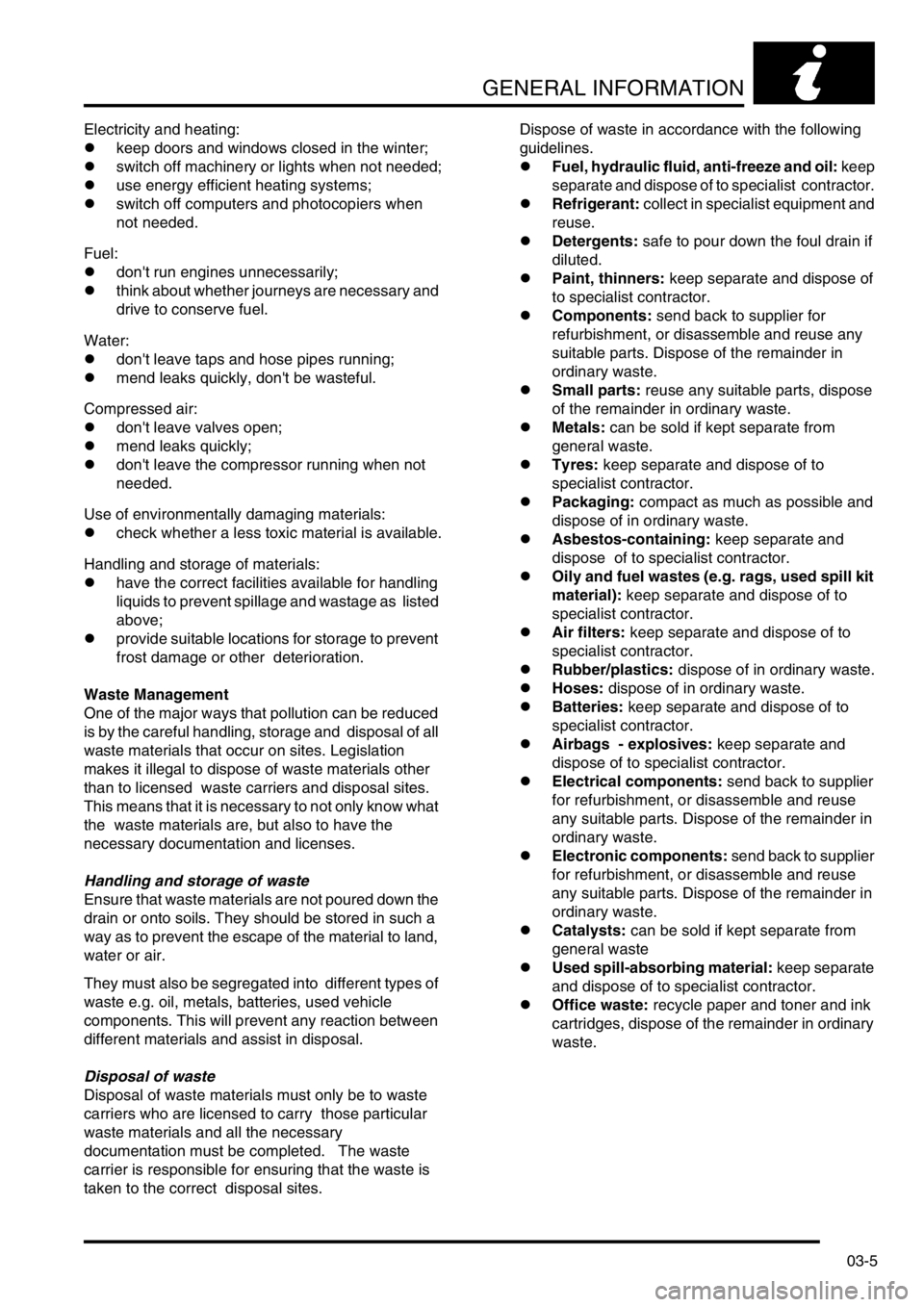
GENERAL INFORMATION
03-5
Electricity and heating:
lkeep doors and windows closed in the winter;
lswitch off machinery or lights when not needed;
luse energy efficient heating systems;
lswitch off computers and photocopiers when
not needed.
Fuel:
ldon't run engines unnecessarily;
lthink about whether journeys are necessary and
drive to conserve fuel.
Water:
ldon't leave taps and hose pipes running;
lmend leaks quickly, don't be wasteful.
Compressed air:
ldon't leave valves open;
lmend leaks quickly;
ldon't leave the compressor running when not
needed.
Use of environmentally damaging materials:
lcheck whether a less toxic material is available.
Handling and storage of materials:
lhave the correct facilities available for handling
liquids to prevent spillage and wastage as listed
above;
lprovide suitable locations for storage to prevent
frost damage or other deterioration.
Waste Management
One of the major ways that pollution can be reduced
is by the careful handling, storage and disposal of all
waste materials that occur on sites. Legislation
makes it illegal to dispose of waste materials other
than to licensed waste carriers and disposal sites.
This means that it is necessary to not only know what
the waste materials are, but also to have the
necessary documentation and licenses.
Handling and storage of waste
Ensure that waste materials are not poured down the
drain or onto soils. They should be stored in such a
way as to prevent the escape of the material to land,
water or air.
They must also be segregated into different types of
waste e.g. oil, metals, batteries, used vehicle
components. This will prevent any reaction between
different materials and assist in disposal.
Disposal of waste
Disposal of waste materials must only be to waste
carriers who are licensed to carry those particular
waste materials and all the necessary
documentation must be completed. The waste
carrier is responsible for ensuring that the waste is
taken to the correct disposal sites.Dispose of waste in accordance with the following
guidelines.
lFuel, hydraulic fluid, anti-freeze and oil: keep
separate and dispose of to specialist contractor.
lRefrigerant: collect in specialist equipment and
reuse.
lDetergents: safe to pour down the foul drain if
diluted.
lPaint, thinners: keep separate and dispose of
to specialist contractor.
lComponents: send back to supplier for
refurbishment, or disassemble and reuse any
suitable parts. Dispose of the remainder in
ordinary waste.
lSmall parts: reuse any suitable parts, dispose
of the remainder in ordinary waste.
lMetals: can be sold if kept separate from
general waste.
lTyres: keep separate and dispose of to
specialist contractor.
lPackaging: compact as much as possible and
dispose of in ordinary waste.
lAsbestos-containing: keep separate and
dispose of to specialist contractor.
lOily and fuel wastes (e.g. rags, used spill kit
material): keep separate and dispose of to
specialist contractor.
lAir filters: keep separate and dispose of to
specialist contractor.
lRubber/plastics: dispose of in ordinary waste.
lHoses: dispose of in ordinary waste.
lBatteries: keep separate and dispose of to
specialist contractor.
lAirbags - explosives: keep separate and
dispose of to specialist contractor.
lElectrical components: send back to supplier
for refurbishment, or disassemble and reuse
any suitable parts. Dispose of the remainder in
ordinary waste.
lElectronic components: send back to supplier
for refurbishment, or disassemble and reuse
any suitable parts. Dispose of the remainder in
ordinary waste.
lCatalysts: can be sold if kept separate from
general waste
lUsed spill-absorbing material: keep separate
and dispose of to specialist contractor.
lOffice waste: recycle paper and toner and ink
cartridges, dispose of the remainder in ordinary
waste.
Page 44 of 1672
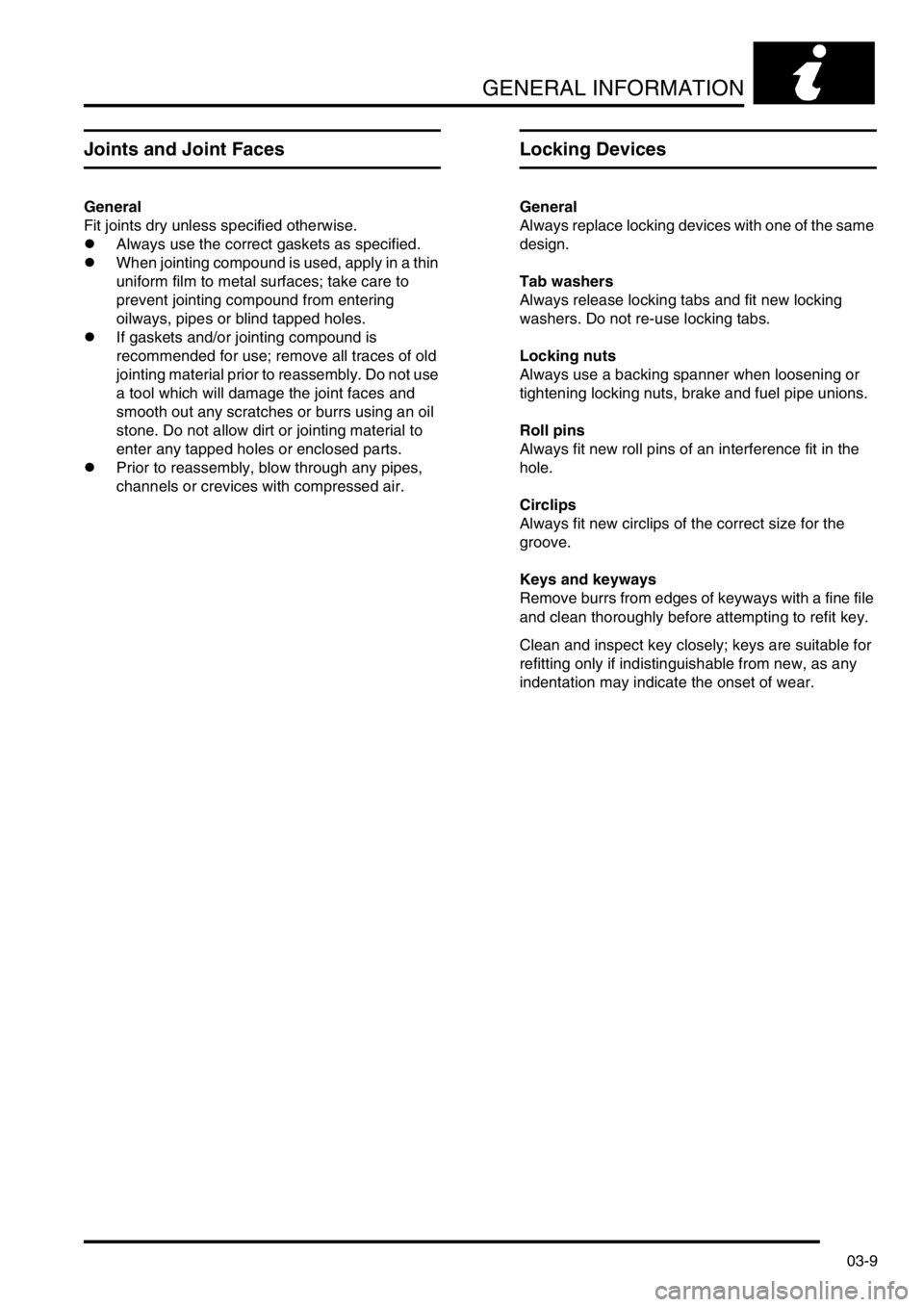
GENERAL INFORMATION
03-9
Joints and Joint Faces
General
Fit joints dry unless specified otherwise.
lAlways use the correct gaskets as specified.
lWhen jointing compound is used, apply in a thin
uniform film to metal surfaces; take care to
prevent jointing compound from entering
oilways, pipes or blind tapped holes.
lIf gaskets and/or jointing compound is
recommended for use; remove all traces of old
jointing material prior to reassembly. Do not use
a tool which will damage the joint faces and
smooth out any scratches or burrs using an oil
stone. Do not allow dirt or jointing material to
enter any tapped holes or enclosed parts.
lPrior to reassembly, blow through any pipes,
channels or crevices with compressed air.
Locking Devices
General
Always replace locking devices with one of the same
design.
Tab washers
Always release locking tabs and fit new locking
washers. Do not re-use locking tabs.
Locking nuts
Always use a backing spanner when loosening or
tightening locking nuts, brake and fuel pipe unions.
Roll pins
Always fit new roll pins of an interference fit in the
hole.
Circlips
Always fit new circlips of the correct size for the
groove.
Keys and keyways
Remove burrs from edges of keyways with a fine file
and clean thoroughly before attempting to refit key.
Clean and inspect key closely; keys are suitable for
refitting only if indistinguishable from new, as any
indentation may indicate the onset of wear.
Page 60 of 1672
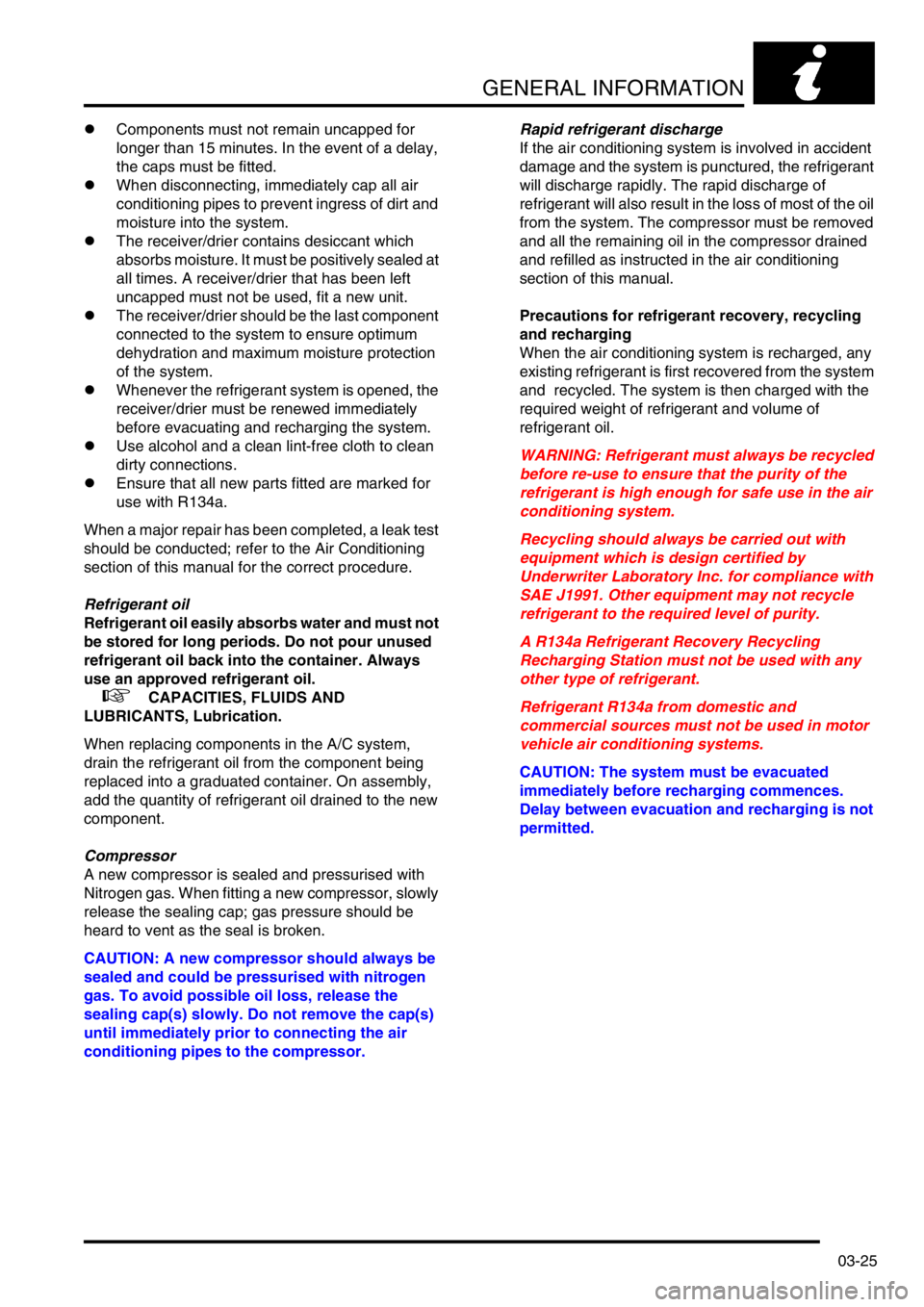
GENERAL INFORMATION
03-25
lComponents must not remain uncapped for
longer than 15 minutes. In the event of a delay,
the caps must be fitted.
lWhen disconnecting, immediately cap all air
conditioning pipes to prevent ingress of dirt and
moisture into the system.
lThe receiver/drier contains desiccant which
absorbs moisture. It must be positively sealed at
all times. A receiver/drier that has been left
uncapped must not be used, fit a new unit.
lThe receiver/drier should be the last component
connected to the system to ensure optimum
dehydration and maximum moisture protection
of the system.
lWhenever the refrigerant system is opened, the
receiver/drier must be renewed immediately
before evacuating and recharging the system.
lUse alcohol and a clean lint-free cloth to clean
dirty connections.
lEnsure that all new parts fitted are marked for
use with R134a.
When a major repair has been completed, a leak test
should be conducted; refer to the Air Conditioning
section of this manual for the correct procedure.
Refrigerant oil
Refrigerant oil easily absorbs water and must not
be stored for long periods. Do not pour unused
refrigerant oil back into the container. Always
use an approved refrigerant oil.
+ CAPACITIES, FLUIDS AND
LUBRICANTS, Lubrication.
When replacing components in the A/C system,
drain the refrigerant oil from the component being
replaced into a graduated container. On assembly,
add the quantity of refrigerant oil drained to the new
component.
Compressor
A new compressor is sealed and pressurised with
Nitrogen gas. When fitting a new compressor, slowly
release the sealing cap; gas pressure should be
heard to vent as the seal is broken.
CAUTION: A new compressor should always be
sealed and could be pressurised with nitrogen
gas. To avoid possible oil loss, release the
sealing cap(s) slowly. Do not remove the cap(s)
until immediately prior to connecting the air
conditioning pipes to the compressor.Rapid refrigerant discharge
If the air conditioning system is involved in accident
damage and the system is punctured, the refrigerant
will discharge rapidly. The rapid discharge of
refrigerant will also result in the loss of most of the oil
from the system. The compressor must be removed
and all the remaining oil in the compressor drained
and refilled as instructed in the air conditioning
section of this manual.
Precautions for refrigerant recovery, recycling
and recharging
When the air conditioning system is recharged, any
existing refrigerant is first recovered from the system
and recycled. The system is then charged with the
required weight of refrigerant and volume of
refrigerant oil.
WARNING: Refrigerant must always be recycled
before re-use to ensure that the purity of the
refrigerant is high enough for safe use in the air
conditioning system.
Recycling should always be carried out with
equipment which is design certified by
Underwriter Laboratory Inc. for compliance with
SAE J1991. Other equipment may not recycle
refrigerant to the required level of purity.
A R134a Refrigerant Recovery Recycling
Recharging Station must not be used with any
other type of refrigerant.
Refrigerant R134a from domestic and
commercial sources must not be used in motor
vehicle air conditioning systems.
CAUTION: The system must be evacuated
immediately before recharging commences.
Delay between evacuation and recharging is not
permitted.
Page 61 of 1672
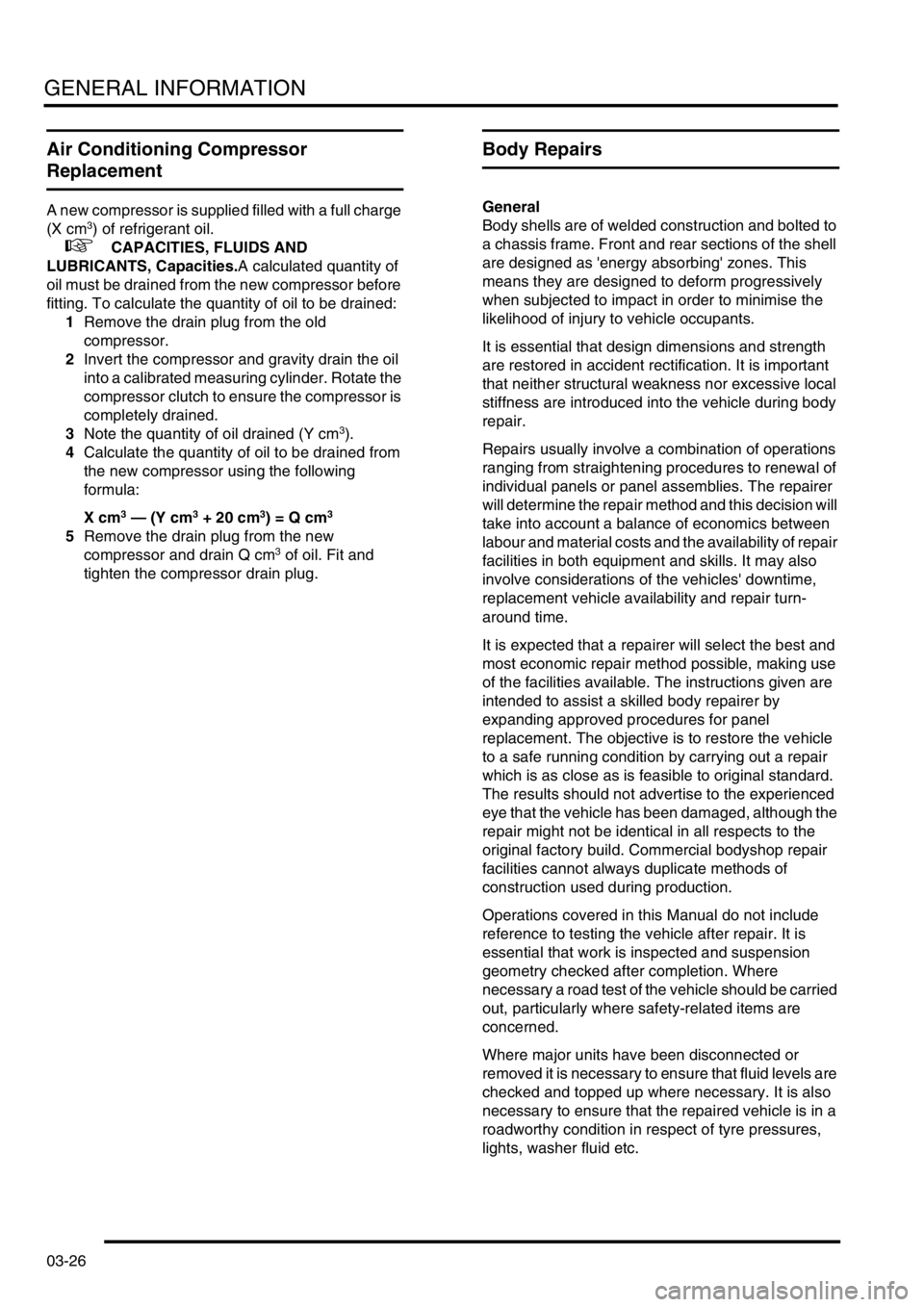
GENERAL INFORMATION
03-26
Air Conditioning Compressor
Replacement
A new compressor is supplied filled with a full charge
(X cm3) of refrigerant oil.
+ CAPACITIES, FLUIDS AND
LUBRICANTS, Capacities.A calculated quantity of
oil must be drained from the new compressor before
fitting. To calculate the quantity of oil to be drained:
1Remove the drain plug from the old
compressor.
2Invert the compressor and gravity drain the oil
into a calibrated measuring cylinder. Rotate the
compressor clutch to ensure the compressor is
completely drained.
3Note the quantity of oil drained (Y cm
3).
4Calculate the quantity of oil to be drained from
the new compressor using the following
formula:
X cm
3 — (Y cm3 + 20 cm3) = Q cm3
5Remove the drain plug from the new
compressor and drain Q cm3 of oil. Fit and
tighten the compressor drain plug.
Body Repairs
General
Body shells are of welded construction and bolted to
a chassis frame. Front and rear sections of the shell
are designed as 'energy absorbing' zones. This
means they are designed to deform progressively
when subjected to impact in order to minimise the
likelihood of injury to vehicle occupants.
It is essential that design dimensions and strength
are restored in accident rectification. It is important
that neither structural weakness nor excessive local
stiffness are introduced into the vehicle during body
repair.
Repairs usually involve a combination of operations
ranging from straightening procedures to renewal of
individual panels or panel assemblies. The repairer
will determine the repair method and this decision will
take into account a balance of economics between
labour and material costs and the availability of repair
facilities in both equipment and skills. It may also
involve considerations of the vehicles' downtime,
replacement vehicle availability and repair turn-
around time.
It is expected that a repairer will select the best and
most economic repair method possible, making use
of the facilities available. The instructions given are
intended to assist a skilled body repairer by
expanding approved procedures for panel
replacement. The objective is to restore the vehicle
to a safe running condition by carrying out a repair
which is as close as is feasible to original standard.
The results should not advertise to the experienced
eye that the vehicle has been damaged, although the
repair might not be identical in all respects to the
original factory build. Commercial bodyshop repair
facilities cannot always duplicate methods of
construction used during production.
Operations covered in this Manual do not include
reference to testing the vehicle after repair. It is
essential that work is inspected and suspension
geometry checked after completion. Where
necessary a road test of the vehicle should be carried
out, particularly where safety-related items are
concerned.
Where major units have been disconnected or
removed it is necessary to ensure that fluid levels are
checked and topped up where necessary. It is also
necessary to ensure that the repaired vehicle is in a
roadworthy condition in respect of tyre pressures,
lights, washer fluid etc.