wheel size LAND ROVER DISCOVERY 2002 Workshop Manual
[x] Cancel search | Manufacturer: LAND ROVER, Model Year: 2002, Model line: DISCOVERY, Model: LAND ROVER DISCOVERY 2002Pages: 1672, PDF Size: 46.1 MB
Page 79 of 1672
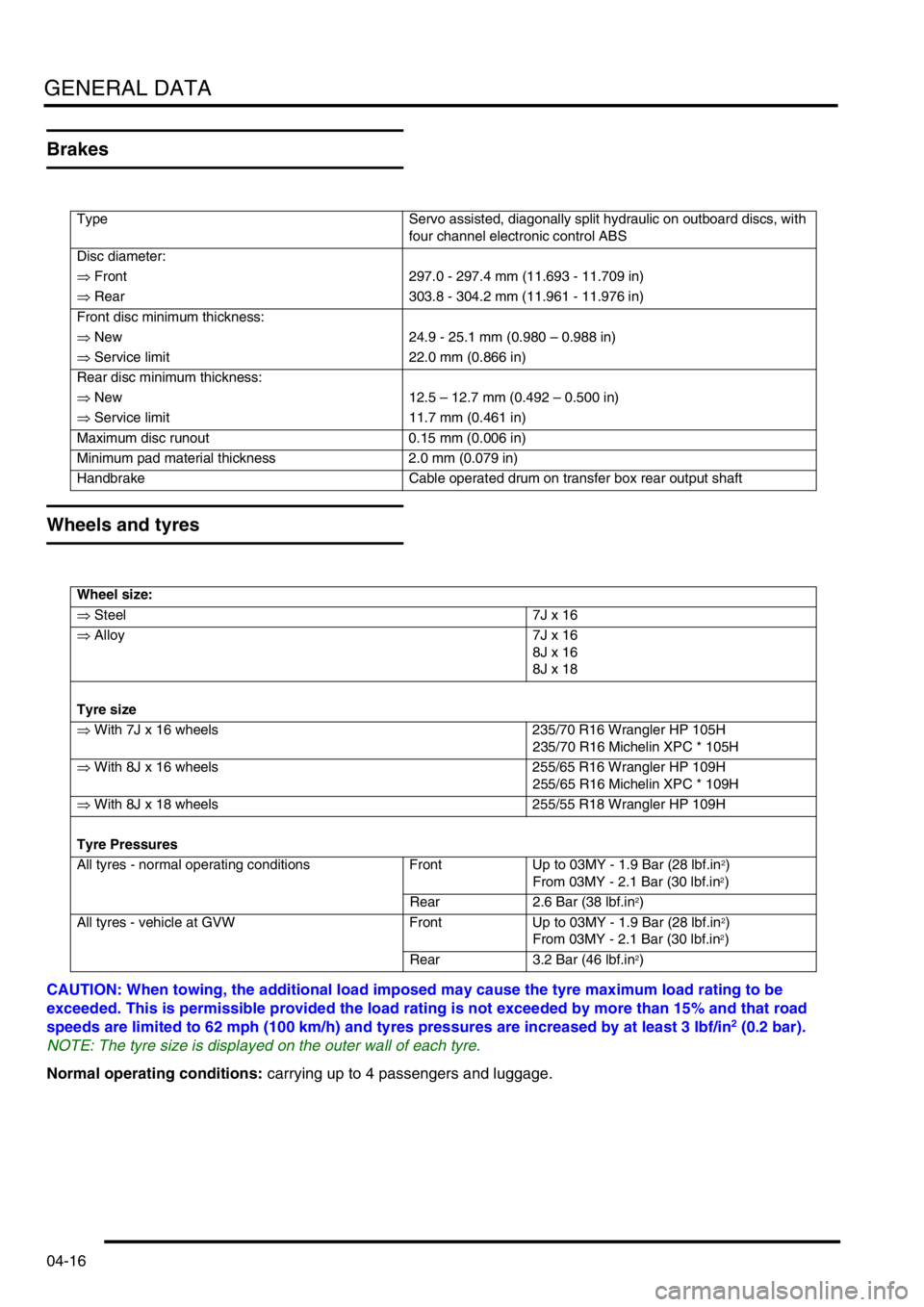
GENERAL DATA
04-16
Brakes
Wheels and tyres
CAUTION: When towing, the additional load imposed may cause the tyre maximum load rating to be
exceeded. This is permissible provided the load rating is not exceeded by more than 15% and that road
speeds are limited to 62 mph (100 km/h) and tyres pressures are increased by at least 3 lbf/in
2 (0.2 bar).
NOTE: The tyre size is displayed on the outer wall of each tyre.
Normal operating conditions: carrying up to 4 passengers and luggage.
Type Servo assisted, diagonally split hydraulic on outboard discs, with
four channel electronic control ABS
Disc diameter:
Front 297.0 - 297.4 mm (11.693 - 11.709 in)
Rear 303.8 - 304.2 mm (11.961 - 11.976 in)
Front disc minimum thickness:
New 24.9 - 25.1 mm (0.980 – 0.988 in)
Service limit 22.0 mm (0.866 in)
Rear disc minimum thickness:
New 12.5 – 12.7 mm (0.492 – 0.500 in)
Service limit 11.7 mm (0.461 in)
Maximum disc runout 0.15 mm (0.006 in)
Minimum pad material thickness 2.0 mm (0.079 in)
Handbrake Cable operated drum on transfer box rear output shaft
Wheel size:
Steel 7J x 16
Alloy 7J x 16
8J x 16
8J x 18
Tyre size
With 7J x 16 wheels 235/70 R16 Wrangler HP 105H
235/70 R16 Michelin XPC * 105H
With 8J x 16 wheels 255/65 R16 Wrangler HP 109H
255/65 R16 Michelin XPC * 109H
With 8J x 18 wheels 255/55 R18 Wrangler HP 109H
Tyre Pressures
All tyres - normal operating conditions Front Up to 03MY - 1.9 Bar (28 lbf.in
2)
From 03MY - 2.1 Bar (30 lbf.in2)
Rear 2.6 Bar (38 lbf.in
2)
All tyres - vehicle at GVW Front Up to 03MY - 1.9 Bar (28 lbf.in
2)
From 03MY - 2.1 Bar (30 lbf.in2)
Rear 3.2 Bar (46 lbf.in
2)
Page 872 of 1672
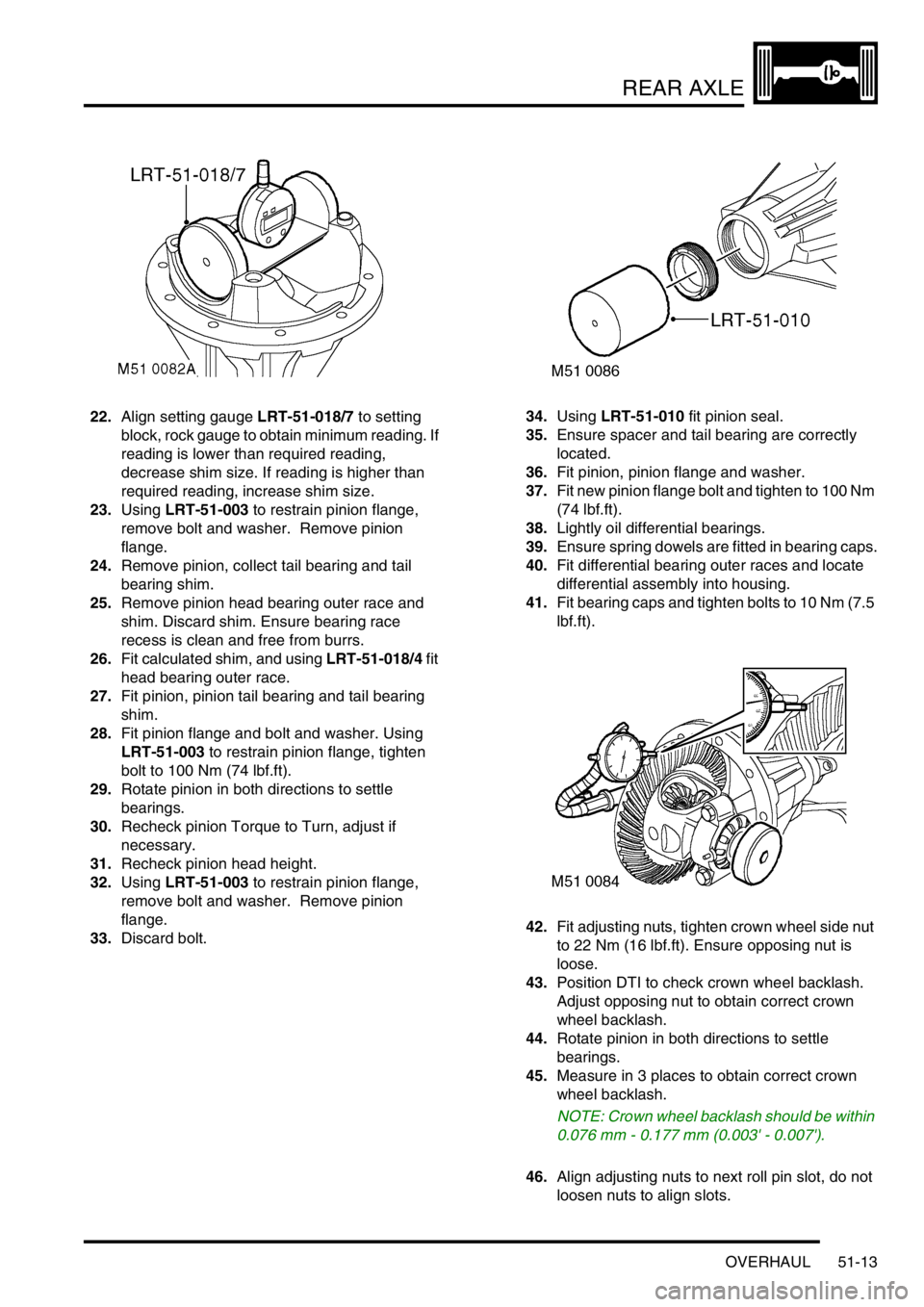
REAR AXLE
OVERHAUL 51-13
22.Align setting gauge LRT-51-018/7 to setting
block, rock gauge to obtain minimum reading. If
reading is lower than required reading,
decrease shim size. If reading is higher than
required reading, increase shim size.
23.Using LRT-51-003 to restrain pinion flange,
remove bolt and washer. Remove pinion
flange.
24.Remove pinion, collect tail bearing and tail
bearing shim.
25.Remove pinion head bearing outer race and
shim. Discard shim. Ensure bearing race
recess is clean and free from burrs.
26.Fit calculated shim, and using LRT-51-018/4 fit
head bearing outer race.
27.Fit pinion, pinion tail bearing and tail bearing
shim.
28.Fit pinion flange and bolt and washer. Using
LRT-51-003 to restrain pinion flange, tighten
bolt to 100 Nm (74 lbf.ft).
29.Rotate pinion in both directions to settle
bearings.
30.Recheck pinion Torque to Turn, adjust if
necessary.
31.Recheck pinion head height.
32.Using LRT-51-003 to restrain pinion flange,
remove bolt and washer. Remove pinion
flange.
33.Discard bolt.34.Using LRT-51-010 fit pinion seal.
35.Ensure spacer and tail bearing are correctly
located.
36.Fit pinion, pinion flange and washer.
37.Fit new pinion flange bolt and tighten to 100 Nm
(74 lbf.ft).
38.Lightly oil differential bearings.
39.Ensure spring dowels are fitted in bearing caps.
40.Fit differential bearing outer races and locate
differential assembly into housing.
41.Fit bearing caps and tighten bolts to 10 Nm (7.5
lbf.ft).
42.Fit adjusting nuts, tighten crown wheel side nut
to 22 Nm (16 lbf.ft). Ensure opposing nut is
loose.
43.Position DTI to check crown wheel backlash.
Adjust opposing nut to obtain correct crown
wheel backlash.
44.Rotate pinion in both directions to settle
bearings.
45.Measure in 3 places to obtain correct crown
wheel backlash.
NOTE: Crown wheel backlash should be within
0.076 mm - 0.177 mm (0.003' - 0.007').
46.Align adjusting nuts to next roll pin slot, do not
loosen nuts to align slots.
Page 1322 of 1672
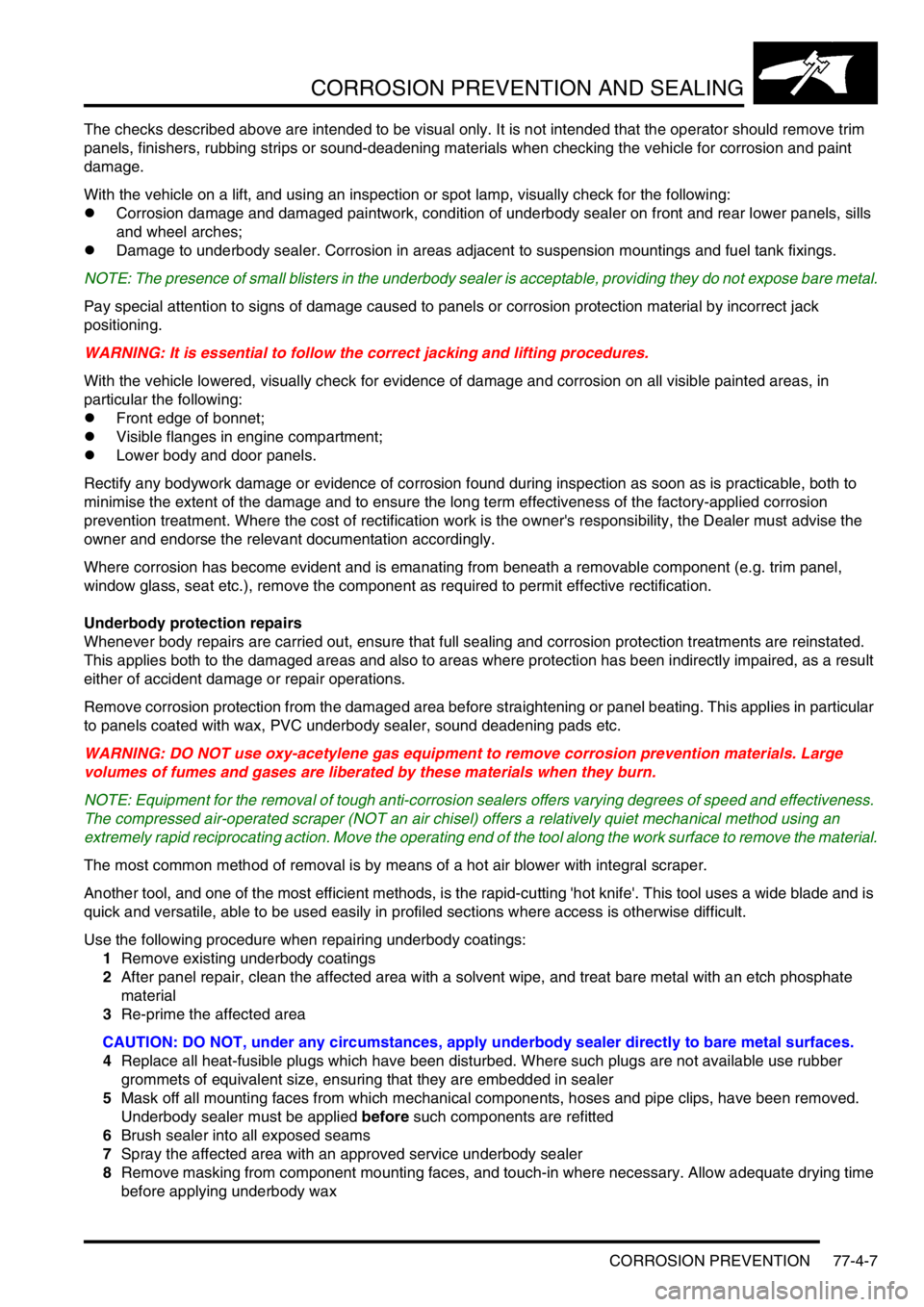
CORROSION PREVENTION AND SEALING
CORROSION PREVENTION 77-4-7
The checks described above are intended to be visual only. It is not intended that the operator should remove trim
panels, finishers, rubbing strips or sound-deadening materials when checking the vehicle for corrosion and paint
damage.
With the vehicle on a lift, and using an inspection or spot lamp, visually check for the following:
lCorrosion damage and damaged paintwork, condition of underbody sealer on front and rear lower panels, sills
and wheel arches;
lDamage to underbody sealer. Corrosion in areas adjacent to suspension mountings and fuel tank fixings.
NOTE: The presence of small blisters in the underbody sealer is acceptable, providing they do not expose bare metal.
Pay special attention to signs of damage caused to panels or corrosion protection material by incorrect jack
positioning.
WARNING: It is essential to follow the correct jacking and lifting procedures.
With the vehicle lowered, visually check for evidence of damage and corrosion on all visible painted areas, in
particular the following:
lFront edge of bonnet;
lVisible flanges in engine compartment;
lLower body and door panels.
Rectify any bodywork damage or evidence of corrosion found during inspection as soon as is practicable, both to
minimise the extent of the damage and to ensure the long term effectiveness of the factory-applied corrosion
prevention treatment. Where the cost of rectification work is the owner's responsibility, the Dealer must advise the
owner and endorse the relevant documentation accordingly.
Where corrosion has become evident and is emanating from beneath a removable component (e.g. trim panel,
window glass, seat etc.), remove the component as required to permit effective rectification.
Underbody protection repairs
Whenever body repairs are carried out, ensure that full sealing and corrosion protection treatments are reinstated.
This applies both to the damaged areas and also to areas where protection has been indirectly impaired, as a result
either of accident damage or repair operations.
Remove corrosion protection from the damaged area before straightening or panel beating. This applies in particular
to panels coated with wax, PVC underbody sealer, sound deadening pads etc.
WARNING: DO NOT use oxy-acetylene gas equipment to remove corrosion prevention materials. Large
volumes of fumes and gases are liberated by these materials when they burn.
NOTE: Equipment for the removal of tough anti-corrosion sealers offers varying degrees of speed and effectiveness.
The compressed air-operated scraper (NOT an air chisel) offers a relatively quiet mechanical method using an
extremely rapid reciprocating action. Move the operating end of the tool along the work surface to remove the material.
The most common method of removal is by means of a hot air blower with integral scraper.
Another tool, and one of the most efficient methods, is the rapid-cutting 'hot knife'. This tool uses a wide blade and is
quick and versatile, able to be used easily in profiled sections where access is otherwise difficult.
Use the following procedure when repairing underbody coatings:
1Remove existing underbody coatings
2After panel repair, clean the affected area with a solvent wipe, and treat bare metal with an etch phosphate
material
3Re-prime the affected area
CAUTION: DO NOT, under any circumstances, apply underbody sealer directly to bare metal surfaces.
4Replace all heat-fusible plugs which have been disturbed. Where such plugs are not available use rubber
grommets of equivalent size, ensuring that they are embedded in sealer
5Mask off all mounting faces from which mechanical components, hoses and pipe clips, have been removed.
Underbody sealer must be applied before such components are refitted
6Brush sealer into all exposed seams
7Spray the affected area with an approved service underbody sealer
8Remove masking from component mounting faces, and touch-in where necessary. Allow adequate drying time
before applying underbody wax
Page 1621 of 1672
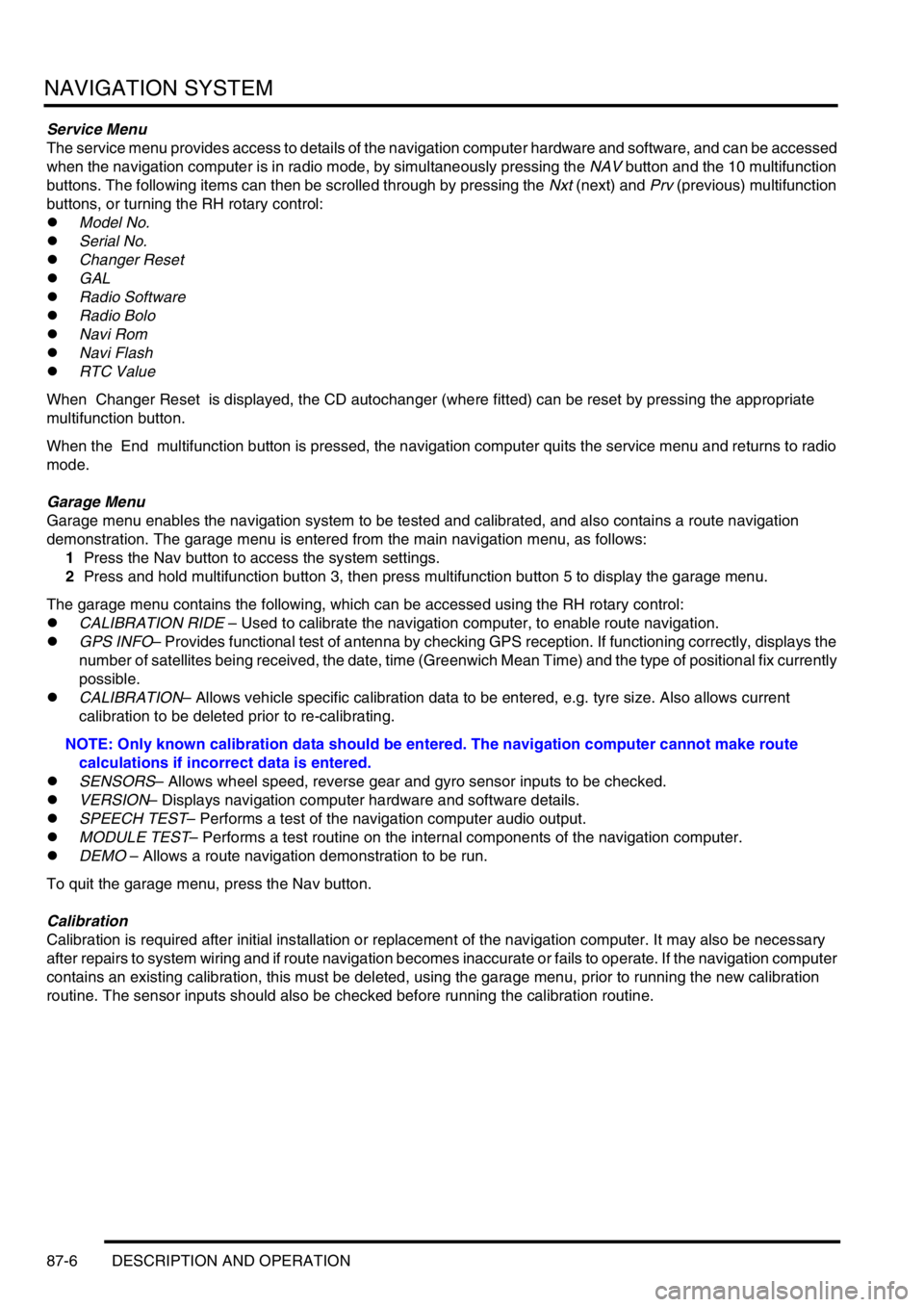
NAVIGATION SYSTEM
87-6 DESCRIPTION AND OPERATION
Service Menu
The service menu provides access to details of the navigation computer hardware and software, and can be accessed
when the navigation computer is in radio mode, by simultaneously pressing the NAV button and the 10 multifunction
buttons. The following items can then be scrolled through by pressing the Nxt (next) and Prv (previous) multifunction
buttons, or turning the RH rotary control:
lModel No.
lSerial No.
lChanger Reset
lGAL
lRadio Software
lRadio Bolo
lNavi Rom
lNavi Flash
lRTC Value
When Changer Reset is displayed, the CD autochanger (where fitted) can be reset by pressing the appropriate
multifunction button.
When the End multifunction button is pressed, the navigation computer quits the service menu and returns to radio
mode.
Garage Menu
Garage menu enables the navigation system to be tested and calibrated, and also contains a route navigation
demonstration. The garage menu is entered from the main navigation menu, as follows:
1Press the Nav button to access the system settings.
2Press and hold multifunction button 3, then press multifunction button 5 to display the garage menu.
The garage menu contains the following, which can be accessed using the RH rotary control:
lCALIBRATION RIDE – Used to calibrate the navigation computer, to enable route navigation.
lGPS INFO– Provides functional test of antenna by checking GPS reception. If functioning correctly, displays the
number of satellites being received, the date, time (Greenwich Mean Time) and the type of positional fix currently
possible.
lCALIBRATION– Allows vehicle specific calibration data to be entered, e.g. tyre size. Also allows current
calibration to be deleted prior to re-calibrating.
NOTE: Only known calibration data should be entered. The navigation computer cannot make route
calculations if incorrect data is entered.
lSENSORS– Allows wheel speed, reverse gear and gyro sensor inputs to be checked.
lVERSION– Displays navigation computer hardware and software details.
lSPEECH TEST– Performs a test of the navigation computer audio output.
lMODULE TEST– Performs a test routine on the internal components of the navigation computer.
lDEMO – Allows a route navigation demonstration to be run.
To quit the garage menu, press the Nav button.
Calibration
Calibration is required after initial installation or replacement of the navigation computer. It may also be necessary
after repairs to system wiring and if route navigation becomes inaccurate or fails to operate. If the navigation computer
contains an existing calibration, this must be deleted, using the garage menu, prior to running the new calibration
routine. The sensor inputs should also be checked before running the calibration routine.