key MAZDA 6 2002 Workshop Manual Suplement
[x] Cancel search | Manufacturer: MAZDA, Model Year: 2002, Model line: 6, Model: MAZDA 6 2002Pages: 909, PDF Size: 17.16 MB
Page 10 of 909
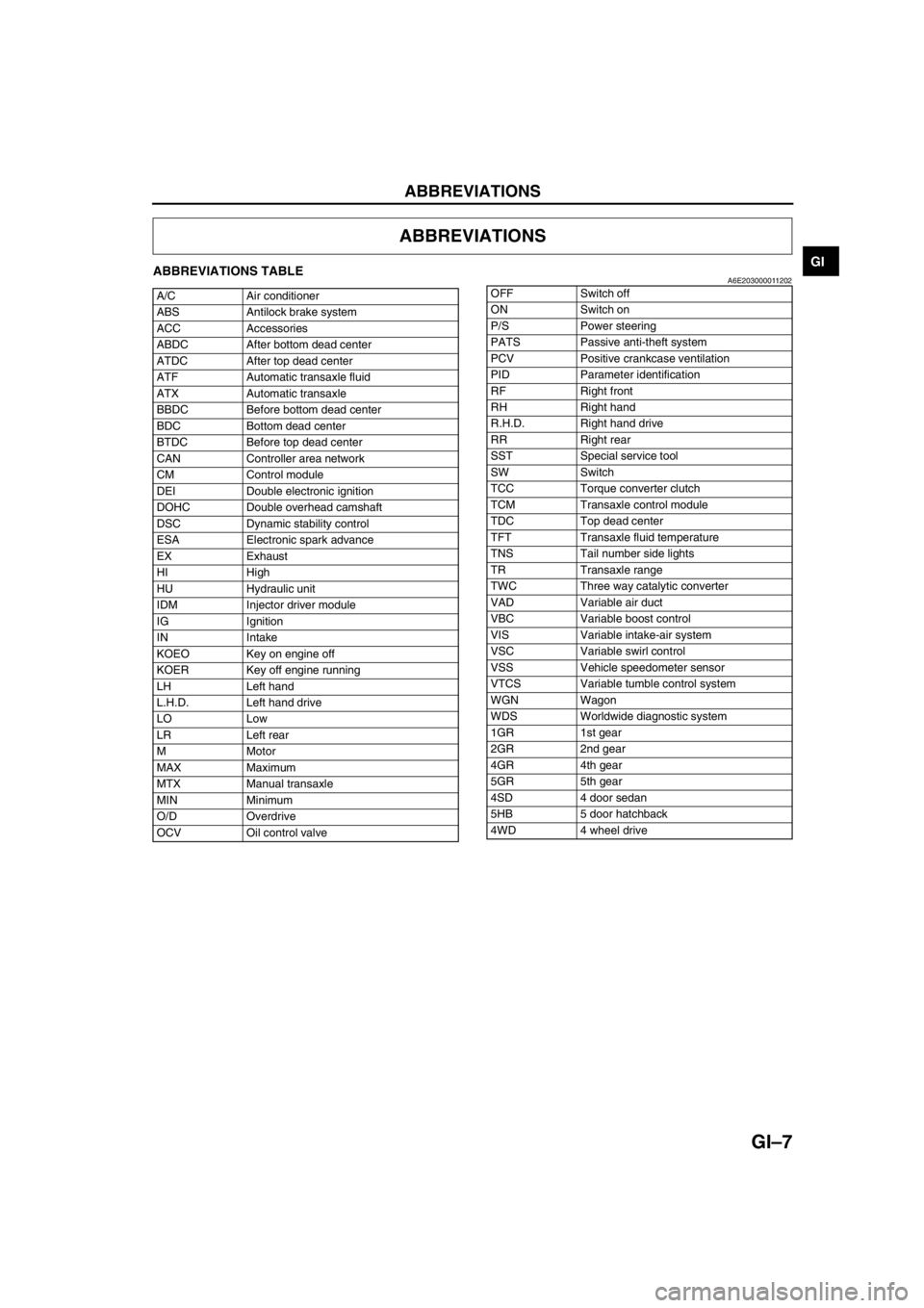
ABBREVIATIONS
GI–7
GIABBREVIATIONS TABLEA6E203000011202
End Of Sie
ABBREVIATIONS
A/C Air conditioner
ABS Antilock brake system
ACC Accessories
ABDC After bottom dead center
ATDC After top dead center
ATF Automatic transaxle fluid
ATX Automatic transaxle
BBDC Before bottom dead center
BDC Bottom dead center
BTDC Before top dead center
CAN Controller area network
CM Control module
DEI Double electronic ignition
DOHC Double overhead camshaft
DSC Dynamic stability control
ESA Electronic spark advance
EX Exhaust
HI High
HU Hydraulic unit
IDM Injector driver module
IG Ignition
IN Intake
KOEO Key on engine off
KOER Key off engine running
LH Left hand
L.H.D. Left hand drive
LO Low
LR Left rear
M Motor
MAX Maximum
MTX Manual transaxle
MIN Minimum
O/D Overdrive
OCV Oil control valveOFF Switch off
ON Switch on
P/S Power steering
PATS Passive anti-theft system
PCV Positive crankcase ventilation
PID Parameter identification
RF Right front
RH Right hand
R.H.D. Right hand drive
RR Right rear
SST Special service tool
SW Switch
TCC Torque converter clutch
TCM Transaxle control module
TDC Top dead center
TFT Transaxle fluid temperature
TNS Tail number side lights
TR Transaxle range
TWC Three way catalytic converter
VAD Variable air duct
VBC Variable boost control
VIS Variable intake-air system
VSC Variable swirl control
VSS Vehicle speedometer sensor
VTCS Variable tumble control system
WGN Wagon
WDS Worldwide diagnostic system
1GR 1st gear
2GR 2nd gear
4GR 4th gear
5GR 5th gear
4SD 4 door sedan
5HB 5 door hatchback
4WD 4 wheel drive
Page 55 of 909
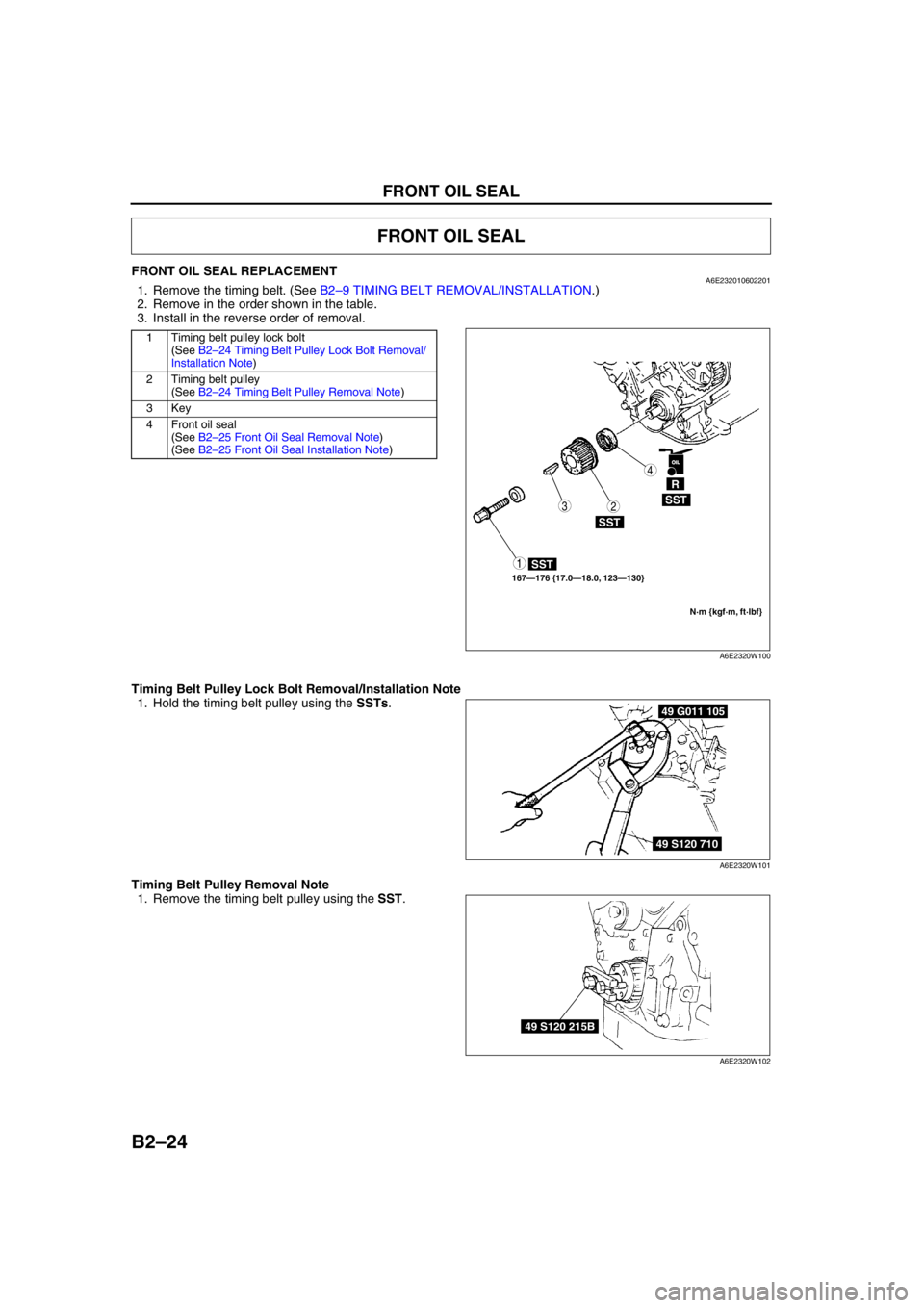
B2–24
FRONT OIL SEAL
FRONT OIL SEAL REPLACEMENTA6E2320106022011. Remove the timing belt. (See B2–9 TIMING BELT REMOVAL/INSTALLATION.)
2. Remove in the order shown in the table.
3. Install in the reverse order of removal.
.
Timing Belt Pulley Lock Bolt Removal/Installation Note
1. Hold the timing belt pulley using the SSTs.
Timing Belt Pulley Removal Note
1. Remove the timing belt pulley using the SST.
FRONT OIL SEAL
1 Timing belt pulley lock bolt
(See B2–24 Timing Belt Pulley Lock Bolt Removal/
Installation Note)
2 Timing belt pulley
(See B2–24 Timing Belt Pulley Removal Note)
3Key
4 Front oil seal
(See B2–25 Front Oil Seal Removal Note)
(See B2–25 Front Oil Seal Installation Note)
SST
SST
SST
R
OILOIL
167—176 {17.0—18.0, 123—130}
N·m {kgf·m, ft·lbf}
3
1
2
4
A6E2320W100
49 G011 105
49 S120 710
A6E2320W101
49 S120 215B
A6E2320W102
Page 141 of 909
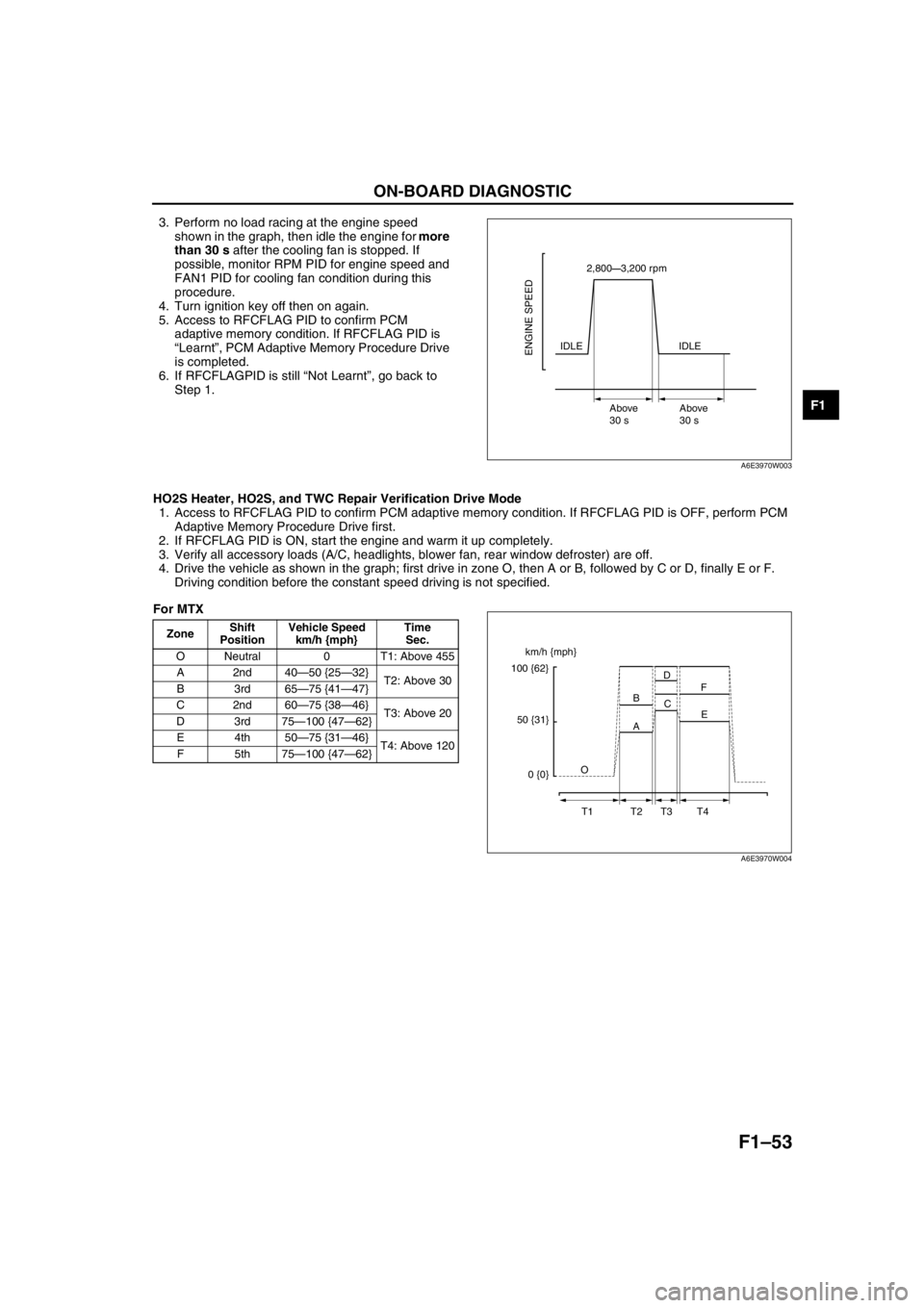
ON-BOARD DIAGNOSTIC
F1–53
F1
3. Perform no load racing at the engine speed
shown in the graph, then idle the engine for more
than 30 s after the cooling fan is stopped. If
possible, monitor RPM PID for engine speed and
FAN1 PID for cooling fan condition during this
procedure.
4. Turn ignition key off then on again.
5. Access to RFCFLAG PID to confirm PCM
adaptive memory condition. If RFCFLAG PID is
“Learnt”, PCM Adaptive Memory Procedure Drive
is completed.
6. If RFCFLAGPID is still “Not Learnt”, go back to
Step 1.
HO2S Heater, HO2S, and TWC Repair Verification Drive Mode
1. Access to RFCFLAG PID to confirm PCM adaptive memory condition. If RFCFLAG PID is OFF, perform PCM
Adaptive Memory Procedure Drive first.
2. If RFCFLAG PID is ON, start the engine and warm it up completely.
3. Verify all accessory loads (A/C, headlights, blower fan, rear window defroster) are off.
4. Drive the vehicle as shown in the graph; first drive in zone O, then A or B, followed by C or D, finally E or F.
Driving condition before the constant speed driving is not specified.
For MTX
2,800—3,200 rpm
IDLE
Above
30 sAbove
30 s
ENGINE SPEEDIDLE
A6E3970W003
ZoneShift
PositionVehicle Speed
km/h {mph}Time
Sec.
O Neutral 0 T1: Above 455
A2nd40—50 {25—32}
T2: Above 30
B3rd65—75 {41—47}
C2nd60—75 {38—46}
T3: Above 20
D3rd75—100 {47—62}
E4th50—75 {31—46}
T4: Above 120
F5th75—100 {47—62}
km/h {mph}
100 {62}
50 {31}
0 {0}O
T1 T2 T3 T4A BD
C
E F
A6E3970W004
Page 142 of 909
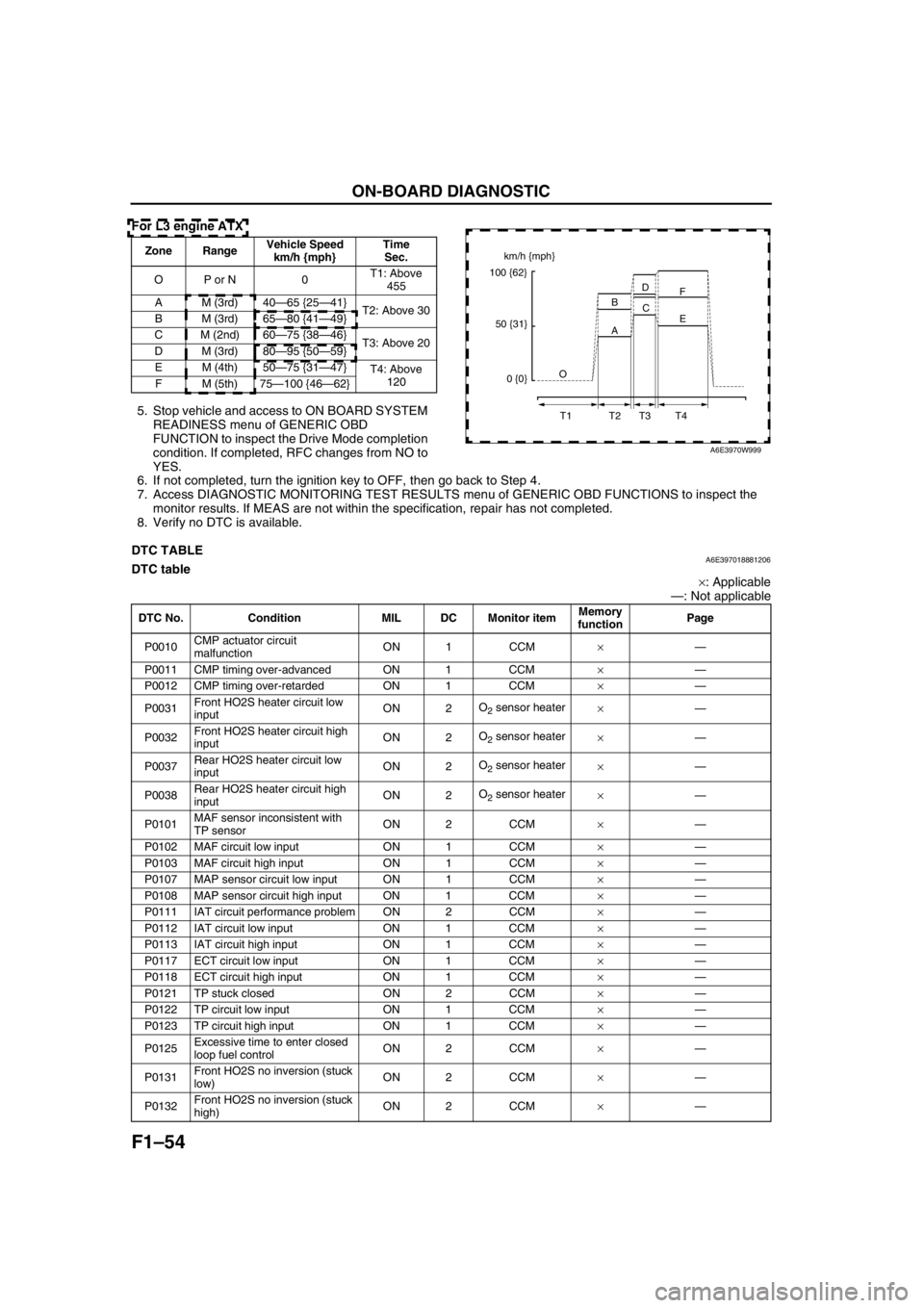
F1–54
ON-BOARD DIAGNOSTIC
For L3 engine ATX
5. Stop vehicle and access to ON BOARD SYSTEM
READINESS menu of GENERIC OBD
FUNCTION to inspect the Drive Mode completion
condition. If completed, RFC changes from NO to
YES.
6. If not completed, turn the ignition key to OFF, then go back to Step 4.
7. Access DIAGNOSTIC MONITORING TEST RESULTS menu of GENERIC OBD FUNCTIONS to inspect the
monitor results. If MEAS are not within the specification, repair has not completed.
8. Verify no DTC is available.
End Of Sie
DTC TABLEA6E397018881206DTC table
×: Applicable
—: Not applicable
Zone RangeVehicle Speed
km/h {mph}Time
Sec.
OP or N 0T1: Above
455
A M (3rd) 40—65 {25—41}
T2: Above 30
B M (3rd) 65—80 {41—49}
C M (2nd) 60—75 {38—46}
T3: Above 20
D M (3rd) 80—95 {50—59}
EM (4th)50—75 {31—47}
T4: Above
120
FM (5th)75—100 {46—62}km/h {mph}
100 {62}
50 {31}
0 {0}O
T1 T2 T3 T4A BD
C
E F
A6E3970W999
DTC No. Condition MIL DC Monitor itemMemory
functionPage
P0010CMP actuator circuit
malfunctionON 1 CCM×—
P0011 CMP timing over-advanced ON 1 CCM×—
P0012 CMP timing over-retarded ON 1 CCM×—
P0031Front HO2S heater circuit low
inputON 2O
2 sensor heater
×—
P0032Front HO2S heater circuit high
inputON 2O
2 sensor heater
×—
P0037Rear HO2S heater circuit low
inputON 2O
2 sensor heater
×—
P0038Rear HO2S heater circuit high
inputON 2O
2 sensor heater
×—
P0101MAF sensor inconsistent with
TP sensorON 2 CCM×—
P0102 MAF circuit low input ON 1 CCM×—
P0103 MAF circuit high input ON 1 CCM×—
P0107 MAP sensor circuit low input ON 1 CCM×—
P0108 MAP sensor circuit high input ON 1 CCM×—
P0111 IAT circuit performance problem ON 2 CCM×—
P0112 IAT circuit low input ON 1 CCM×—
P0113 IAT circuit high input ON 1 CCM×—
P0117 ECT circuit low input ON 1 CCM×—
P0118 ECT circuit high input ON 1 CCM×—
P0121 TP stuck closed ON 2 CCM×—
P0122 TP circuit low input ON 1 CCM×—
P0123 TP circuit high input ON 1 CCM×—
P0125Excessive time to enter closed
loop fuel controlON 2 CCM×—
P0131Front HO2S no inversion (stuck
low)ON 2 CCM×—
P0132Front HO2S no inversion (stuck
high)ON 2 CCM×—
Page 179 of 909
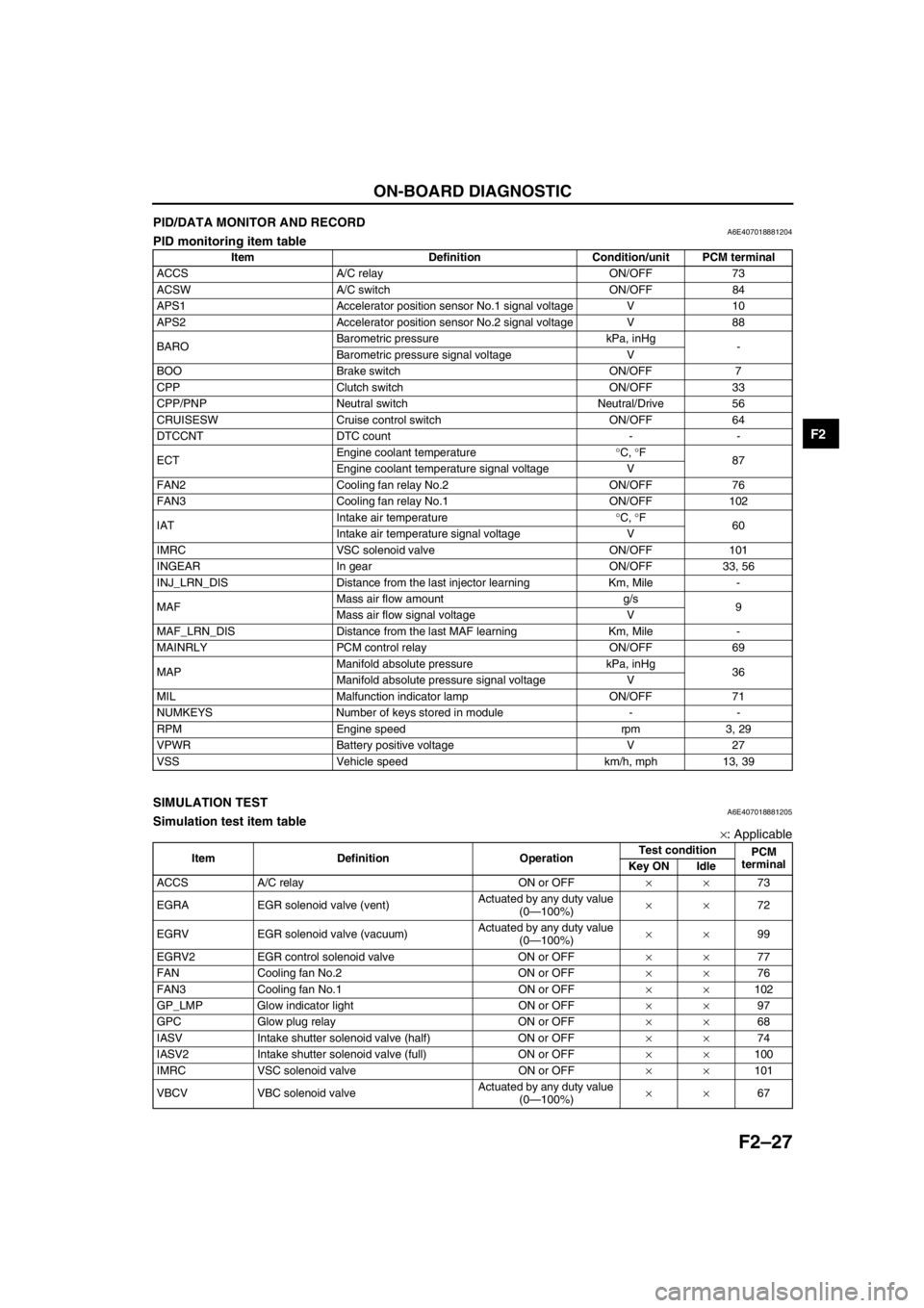
ON-BOARD DIAGNOSTIC
F2–27
F2
PID/DATA MONITOR AND RECORDA6E407018881204PID monitoring item table
End Of Sie
SIMULATION TESTA6E407018881205Simulation test item table
×: Applicable
Item Definition Condition/unit PCM terminal
ACCS A/C relay ON/OFF 73
ACSW A/C switch ON/OFF 84
APS1 Accelerator position sensor No.1 signal voltage V 10
APS2 Accelerator position sensor No.2 signal voltage V 88
BAROBarometric pressure kPa, inHg
-
Barometric pressure signal voltage V
BOO Brake switch ON/OFF 7
CPP Clutch switch ON/OFF 33
CPP/PNP Neutral switch Neutral/Drive 56
CRUISESW Cruise control switch ON/OFF 64
DTCCNT DTC count - -
ECTEngine coolant temperature°C, °F
87
Engine coolant temperature signal voltage V
FAN2 Cooling fan relay No.2 ON/OFF 76
FAN3 Cooling fan relay No.1 ON/OFF 102
IATIntake air temperature°C, °F
60
Intake air temperature signal voltage V
IMRC VSC solenoid valve ON/OFF 101
INGEAR In gear ON/OFF 33, 56
INJ_LRN_DIS Distance from the last injector learning Km, Mile -
MAFMass air flow amount g/s
9
Mass air flow signal voltage V
MAF_LRN_DIS Distance from the last MAF learning Km, Mile -
MAINRLY PCM control relay ON/OFF 69
MAPManifold absolute pressure kPa, inHg
36
Manifold absolute pressure signal voltage V
MIL Malfunction indicator lamp ON/OFF 71
NUMKEYS Number of keys stored in module - -
RPM Engine speed rpm 3, 29
VPWR Battery positive voltage V 27
VSS Vehicle speed km/h, mph 13, 39
Item Definition OperationTest condition
PCM
terminal
Key ON Idle
ACCS A/C relay ON or OFF××73
EGRA EGR solenoid valve (vent)Actuated by any duty value
(0—100%)××72
EGRV EGR solenoid valve (vacuum)Actuated by any duty value
(0—100%)××99
EGRV2 EGR control solenoid valve ON or OFF××77
FAN Cooling fan No.2 ON or OFF××76
FAN3 Cooling fan No.1 ON or OFF××102
GP_LMP Glow indicator light ON or OFF××97
GPC Glow plug relay ON or OFF××68
IASV Intake shutter solenoid valve (half) ON or OFF××74
IASV2 Intake shutter solenoid valve (full) ON or OFF××100
IMRC VSC solenoid valve ON or OFF××101
VBCV VBC solenoid valveActuated by any duty value
(0—100%)××67
Page 218 of 909
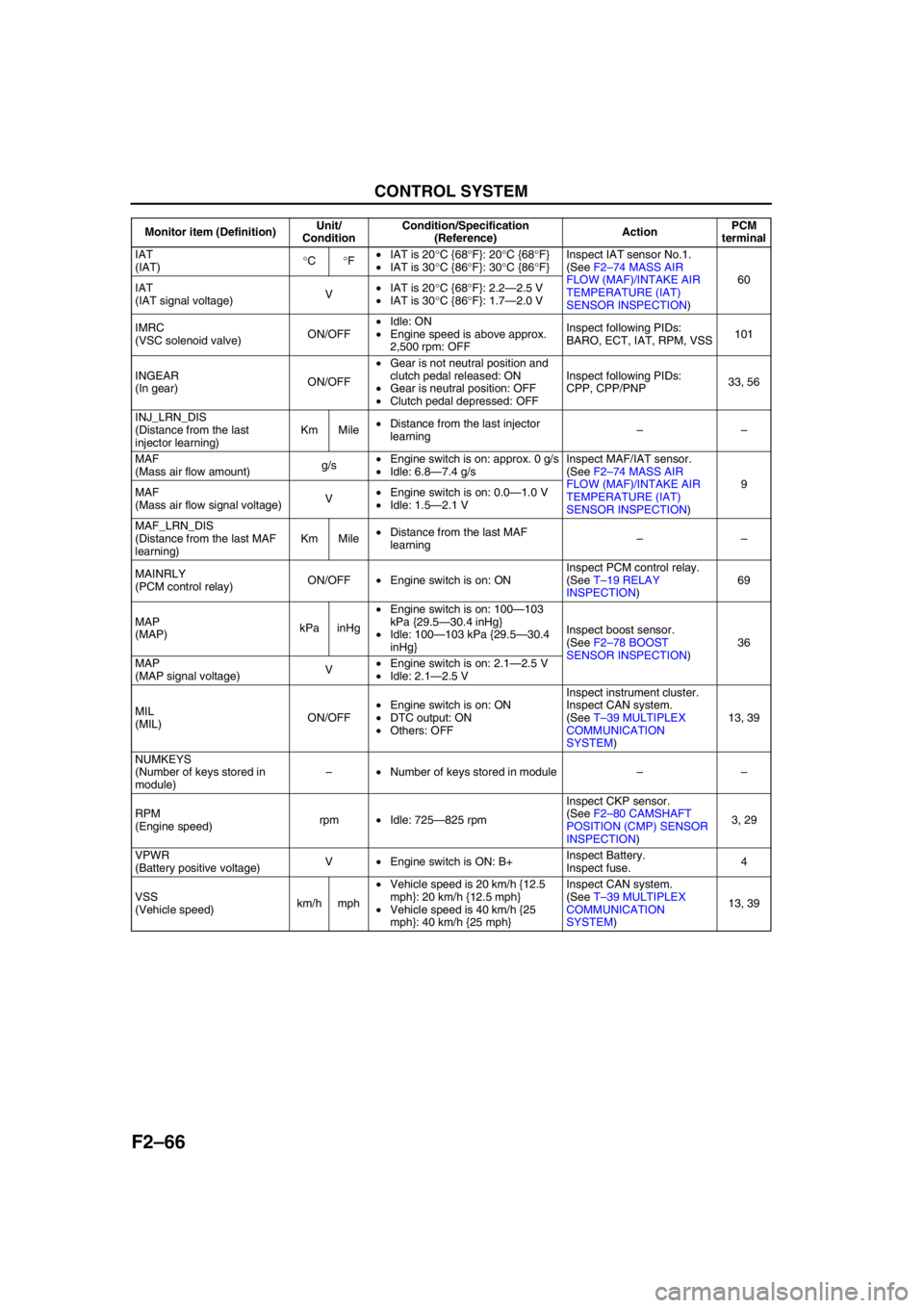
F2–66
CONTROL SYSTEM
IAT
(IAT)°C°F•IAT is 20°C {68°F}: 20°C {68°F}
•IAT is 30°C {86°F}: 30°C {86°F}Inspect IAT sensor No.1.
(See F2–74 MASS AIR
FLOW (MAF)/INTAKE AIR
TEMPERATURE (IAT)
SENSOR INSPECTION)60
IAT
(IAT signal voltage)V•IAT is 20°C {68°F}: 2.2—2.5 V
•IAT is 30°C {86°F}: 1.7—2.0 V
IMRC
(VSC solenoid valve)ON/OFF•Idle: ON
•Engine speed is above approx.
2,500 rpm: OFFInspect following PIDs:
BARO, ECT, IAT, RPM, VSS101
INGEAR
(In gear)ON/OFF•Gear is not neutral position and
clutch pedal released: ON
•Gear is neutral position: OFF
•Clutch pedal depressed: OFFInspect following PIDs:
CPP, CPP/PNP33, 56
INJ_LRN_DIS
(Distance from the last
injector learning)Km Mile•Distance from the last injector
learning––
MAF
(Mass air flow amount)g/s•Engine switch is on: approx. 0 g/s
•Idle: 6.8—7.4 g/sInspect MAF/IAT sensor.
(See F2–74 MASS AIR
FLOW (MAF)/INTAKE AIR
TEMPERATURE (IAT)
SENSOR INSPECTION)9
MAF
(Mass air flow signal voltage)V•Engine switch is on: 0.0—1.0 V
•Idle: 1.5—2.1 V
MAF_LRN_DIS
(Distance from the last MAF
learning)Km Mile•Distance from the last MAF
learning––
MAINRLY
(PCM control relay)ON/OFF•Engine switch is on: ONInspect PCM control relay.
(See T–19 RELAY
INSPECTION)69
MAP
(MAP)kPa inHg•Engine switch is on: 100—103
kPa {29.5—30.4 inHg}
•Idle: 100—103 kPa {29.5—30.4
inHg}Inspect boost sensor.
(See F2–78 BOOST
SENSOR INSPECTION)36
MAP
(MAP signal voltage)V•Engine switch is on: 2.1—2.5 V
•Idle: 2.1—2.5 V
MIL
(MIL)ON/OFF•Engine switch is on: ON
•DTC output: ON
•Others: OFFInspect instrument cluster.
Inspect CAN system.
(See T–39 MULTIPLEX
COMMUNICATION
SYSTEM)13, 39
NUMKEYS
(Number of keys stored in
module)–•Number of keys stored in module––
RPM
(Engine speed)rpm•Idle: 725—825 rpmInspect CKP sensor.
(See F2–80 CAMSHAFT
POSITION (CMP) SENSOR
INSPECTION)3, 29
VPWR
(Battery positive voltage)V•Engine switch is ON: B+Inspect Battery.
Inspect fuse.4
VSS
(Vehicle speed)km/h mph•Vehicle speed is 20 km/h {12.5
mph}: 20 km/h {12.5 mph}
•Vehicle speed is 40 km/h {25
mph}: 40 km/h {25 mph}Inspect CAN system.
(See T–39 MULTIPLEX
COMMUNICATION
SYSTEM)13, 39 Monitor item (Definition)Unit/
ConditionCondition/Specification
(Reference)ActionPCM
terminal
Page 325 of 909
![MAZDA 6 2002 Workshop Manual Suplement TROUBLESHOOTING
F2–173
F2
NO.1 MELTING OF MAIN OR OTHER FUSESA6E408018881203
End Of Sie
1 Melting of main or other fuses
[TROUBLESHOOTING HINTS]
Inspect condition of fuse.
Damaged fuse Related wiri MAZDA 6 2002 Workshop Manual Suplement TROUBLESHOOTING
F2–173
F2
NO.1 MELTING OF MAIN OR OTHER FUSESA6E408018881203
End Of Sie
1 Melting of main or other fuses
[TROUBLESHOOTING HINTS]
Inspect condition of fuse.
Damaged fuse Related wiri](/img/28/57057/w960_57057-324.png)
TROUBLESHOOTING
F2–173
F2
NO.1 MELTING OF MAIN OR OTHER FUSESA6E408018881203
End Of Sie
1 Melting of main or other fuses
[TROUBLESHOOTING HINTS]
Inspect condition of fuse.
Damaged fuse Related wiring harness
MAINMAIN fuse
•BTN fuse
•FAN fuse
•AD FAN fuse
•IG KEY 2 fuse
IG KEY 1IG KEY 1 fuse
•Engine switch
—ENGINE fuse
FUEL PUMPFUEL PUMP fuse
•Fuel warmer
•PCM control relay
BTNBTN fuse
•ROOM fuse
IG KEY 2IG KEY 2 fuse
•Engine switch
ROOMROOM fuse
•DLC-2
ENGINEENGINE fuse
•PCM
INJINJ fuse
•PCM
•IDM
•MAF/IAT sensor
•VSC solenoid valve
•VBC solenoid valve
•EGR control solenoid valve
•EGR solenoid valve (vacuum)
•EGR solenoid valve (vent)
•Intake shutter solenoid valve (half)
•Intake shutter solenoid valve (full)
GLOWGLOW fuse
•Glow plug relay
—Glow plug
—GLOW SIG
ENG+BENG+B fuse
•PCM
FANFAN fuse
•Cooling fan relay No.2
AD FANAD FAN fuse
•Cooling fan relay No.1
Shorted harness
Repair shorted harness and replace fuseFuseDeterioration
Replace fuse
Page 341 of 909
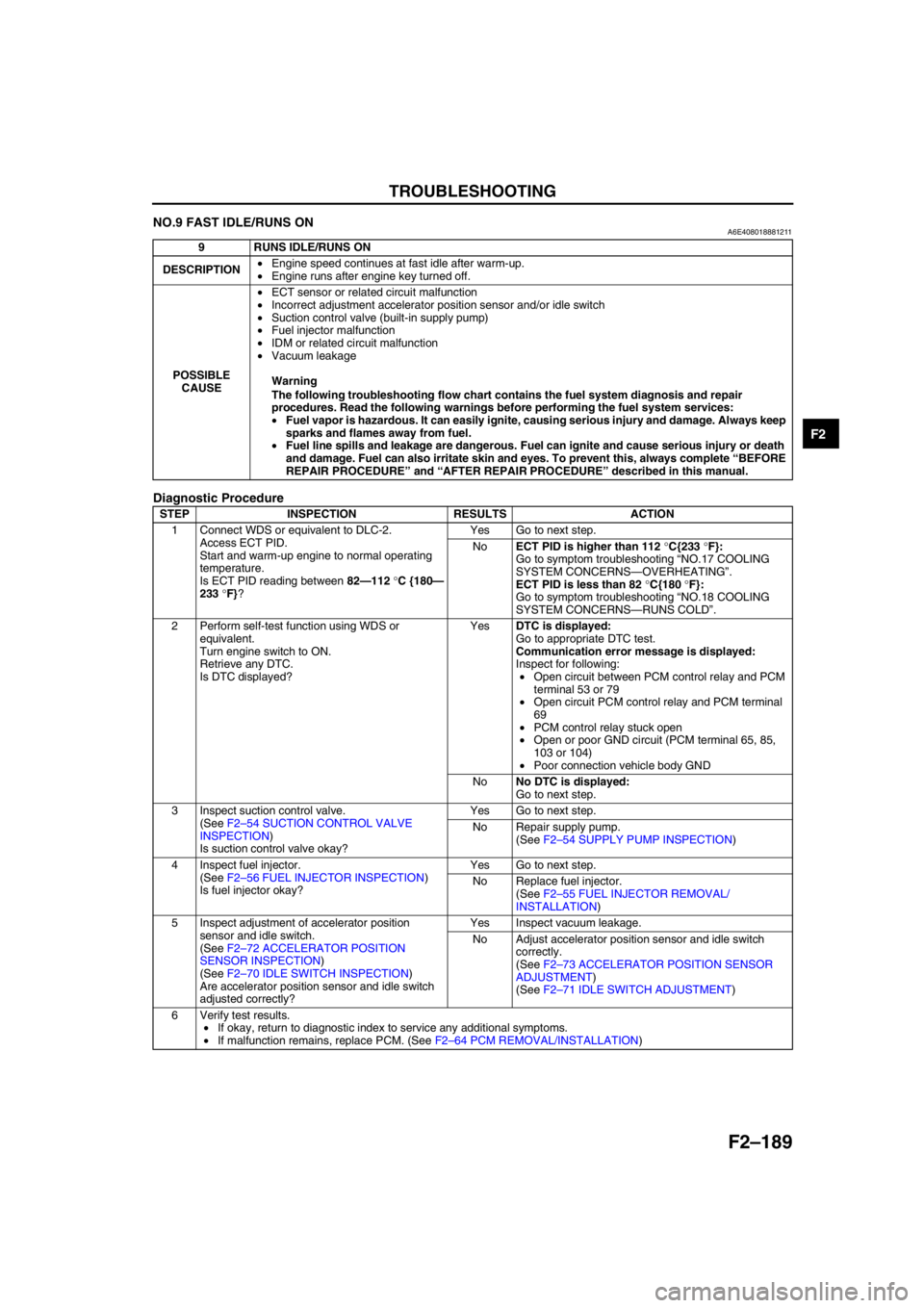
TROUBLESHOOTING
F2–189
F2
NO.9 FAST IDLE/RUNS ONA6E408018881211
Diagnostic Procedure
End Of Sie
9 RUNS IDLE/RUNS ON
DESCRIPTION•Engine speed continues at fast idle after warm-up.
•Engine runs after engine key turned off.
POSSIBLE
CAUSE•ECT sensor or related circuit malfunction
•Incorrect adjustment accelerator position sensor and/or idle switch
•Suction control valve (built-in supply pump)
•Fuel injector malfunction
•IDM or related circuit malfunction
•Vacuum leakage
Warning
The following troubleshooting flow chart contains the fuel system diagnosis and repair
procedures. Read the following warnings before performing the fuel system services:
•Fuel vapor is hazardous. It can easily ignite, causing serious injury and damage. Always keep
sparks and flames away from fuel.
•Fuel line spills and leakage are dangerous. Fuel can ignite and cause serious injury or death
and damage. Fuel can also irritate skin and eyes. To prevent this, always complete “BEFORE
REPAIR PROCEDURE” and “AFTER REPAIR PROCEDURE” described in this manual.
STEP INSPECTION RESULTS ACTION
1 Connect WDS or equivalent to DLC-2.
Access ECT PID.
Start and warm-up engine to normal operating
temperature.
Is ECT PID reading between 82—112 °C {180—
233 °F}?Yes Go to next step.
NoECT PID is higher than 112 °C{233 °F}:
Go to symptom troubleshooting “NO.17 COOLING
SYSTEM CONCERNS—OVERHEATING”.
ECT PID is less than 82 °C{180 °F}:
Go to symptom troubleshooting “NO.18 COOLING
SYSTEM CONCERNS—RUNS COLD”.
2 Perform self-test function using WDS or
equivalent.
Turn engine switch to ON.
Retrieve any DTC.
Is DTC displayed?YesDTC is displayed:
Go to appropriate DTC test.
Communication error message is displayed:
Inspect for following:
•Open circuit between PCM control relay and PCM
terminal 53 or 79
•Open circuit PCM control relay and PCM terminal
69
•PCM control relay stuck open
•Open or poor GND circuit (PCM terminal 65, 85,
103 or 104)
•Poor connection vehicle body GND
NoNo DTC is displayed:
Go to next step.
3 Inspect suction control valve.
(See F2–54 SUCTION CONTROL VALVE
INSPECTION)
Is suction control valve okay?Yes Go to next step.
No Repair supply pump.
(See F2–54 SUPPLY PUMP INSPECTION)
4 Inspect fuel injector.
(See F2–56 FUEL INJECTOR INSPECTION)
Is fuel injector okay?Yes Go to next step.
No Replace fuel injector.
(See F2–55 FUEL INJECTOR REMOVAL/
INSTALLATION)
5 Inspect adjustment of accelerator position
sensor and idle switch.
(See F2–72 ACCELERATOR POSITION
SENSOR INSPECTION)
(See F2–70 IDLE SWITCH INSPECTION)
Are accelerator position sensor and idle switch
adjusted correctly?Yes Inspect vacuum leakage.
No Adjust accelerator position sensor and idle switch
correctly.
(See F2–73 ACCELERATOR POSITION SENSOR
ADJUSTMENT)
(See F2–71 IDLE SWITCH ADJUSTMENT)
6 Verify test results.
•If okay, return to diagnostic index to service any additional symptoms.
•If malfunction remains, replace PCM. (See F2–64 PCM REMOVAL/INSTALLATION)
Page 389 of 909
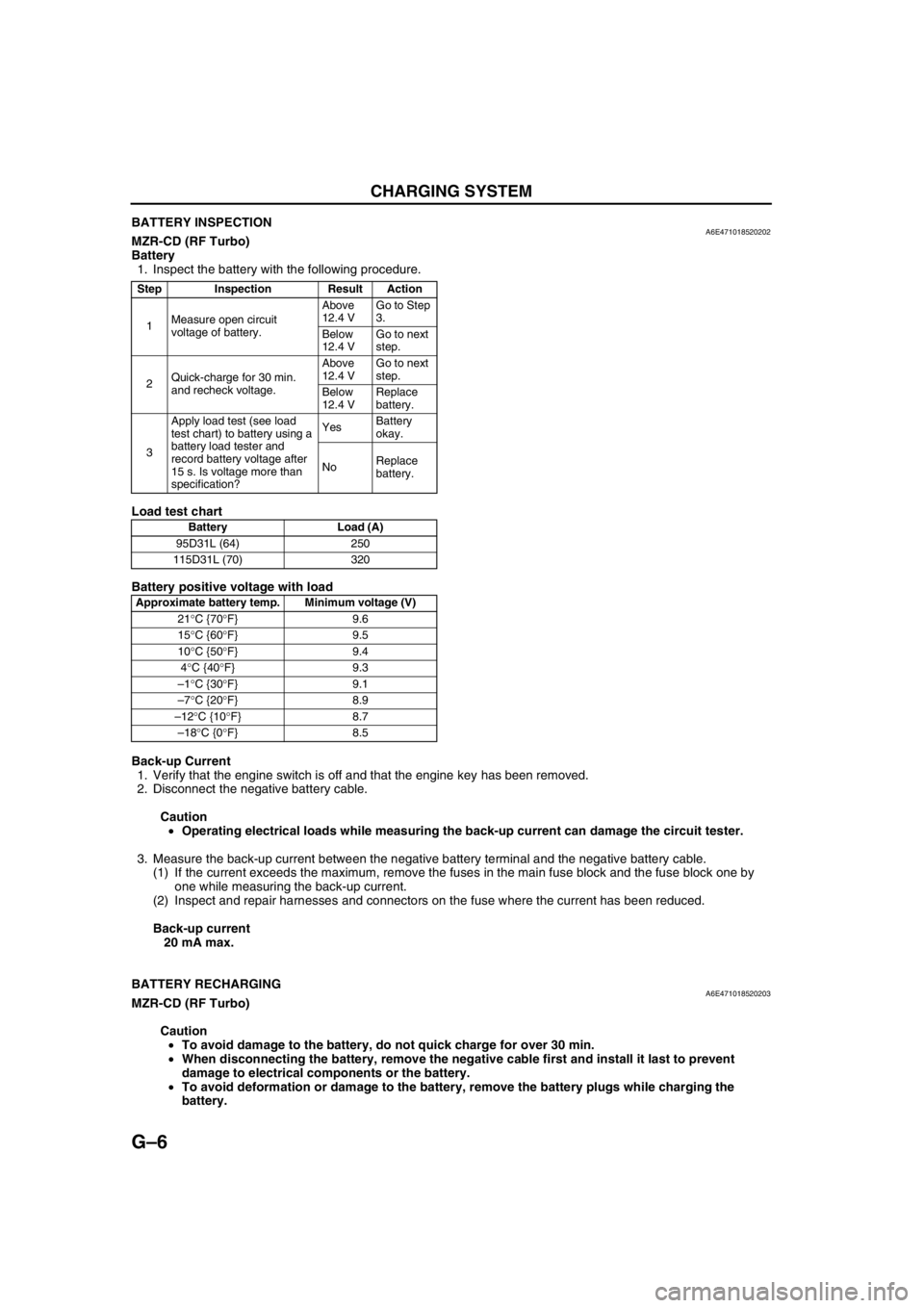
G–6
CHARGING SYSTEM
BATTERY INSPECTIONA6E471018520202MZR-CD (RF Turbo)
Battery
1. Inspect the battery with the following procedure.
Load test chart
Battery positive voltage with load
Back-up Current
1. Verify that the engine switch is off and that the engine key has been removed.
2. Disconnect the negative battery cable.
Caution
•Operating electrical loads while measuring the back-up current can damage the circuit tester.
3. Measure the back-up current between the negative battery terminal and the negative battery cable.
(1) If the current exceeds the maximum, remove the fuses in the main fuse block and the fuse block one by
one while measuring the back-up current.
(2) Inspect and repair harnesses and connectors on the fuse where the current has been reduced.
Back-up current
20 mA max.
End Of Sie
BATTERY RECHARGINGA6E471018520203MZR-CD (RF Turbo)
Caution
•To avoid damage to the battery, do not quick charge for over 30 min.
•When disconnecting the battery, remove the negative cable first and install it last to prevent
damage to electrical components or the battery.
•To avoid deformation or damage to the battery, remove the battery plugs while charging the
battery.
Step Inspection Result Action
1Measure open circuit
voltage of battery.Above
12.4 VGo to Step
3.
Below
12.4 VGo to next
step.
2Quick-charge for 30 min.
and recheck voltage.Above
12.4 VGo to next
step.
Below
12.4 VReplace
battery.
3Apply load test (see load
test chart) to battery using a
battery load tester and
record battery voltage after
15 s. Is voltage more than
specification?YesBattery
okay.
NoReplace
battery.
Battery Load (A)
95D31L (64) 250
115D31L (70) 320
Approximate battery temp. Minimum voltage (V)
21°C {70°F} 9.6
15°C {60°F} 9.5
10°C {50°F} 9.4
4°C {40°F} 9.3
–1°C {30°F} 9.1
–7°C {20°F} 8.9
–12°C {10°F} 8.7
–18°C {0°F} 8.5
Page 539 of 909
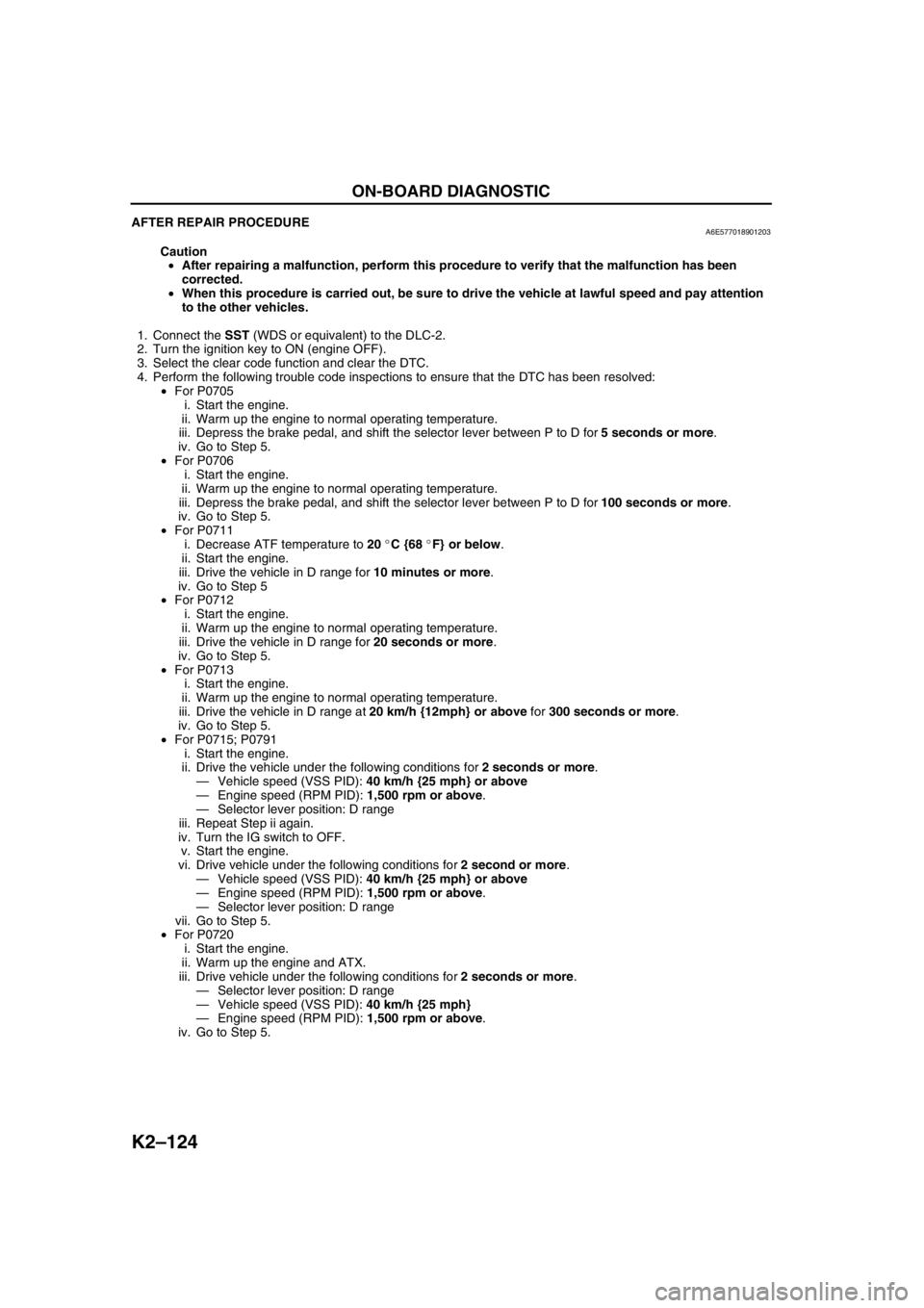
K2–124
ON-BOARD DIAGNOSTIC
AFTER REPAIR PROCEDUREA6E577018901203
Caution
•After repairing a malfunction, perform this procedure to verify that the malfunction has been
corrected.
•When this procedure is carried out, be sure to drive the vehicle at lawful speed and pay attention
to the other vehicles.
1. Connect the SST (WDS or equivalent) to the DLC-2.
2. Turn the ignition key to ON (engine OFF).
3. Select the clear code function and clear the DTC.
4. Perform the following trouble code inspections to ensure that the DTC has been resolved:
•For P0705
i. Start the engine.
ii. Warm up the engine to normal operating temperature.
iii. Depress the brake pedal, and shift the selector lever between P to D for 5 seconds or more.
iv. Go to Step 5.
•For P0706
i. Start the engine.
ii. Warm up the engine to normal operating temperature.
iii. Depress the brake pedal, and shift the selector lever between P to D for 100 seconds or more.
iv. Go to Step 5.
•For P0711
i. Decrease ATF temperature to 20 °C {68 °F} or below.
ii. Start the engine.
iii. Drive the vehicle in D range for 10 minutes or more.
iv. Go to Step 5
•For P0712
i. Start the engine.
ii. Warm up the engine to normal operating temperature.
iii. Drive the vehicle in D range for 20 seconds or more.
iv. Go to Step 5.
•For P0713
i. Start the engine.
ii. Warm up the engine to normal operating temperature.
iii. Drive the vehicle in D range at 20 km/h {12mph} or above for 300 seconds or more.
iv. Go to Step 5.
•For P0715; P0791
i. Start the engine.
ii. Drive the vehicle under the following conditions for 2 seconds or more.
—Vehicle speed (VSS PID): 40 km/h {25 mph} or above
—Engine speed (RPM PID): 1,500 rpm or above.
—Selector lever position: D range
iii. Repeat Step ii again.
iv. Turn the IG switch to OFF.
v. Start the engine.
vi. Drive vehicle under the following conditions for 2 second or more.
—Vehicle speed (VSS PID): 40 km/h {25 mph} or above
—Engine speed (RPM PID): 1,500 rpm or above.
—Selector lever position: D range
vii. Go to Step 5.
•For P0720
i. Start the engine.
ii. Warm up the engine and ATX.
iii. Drive vehicle under the following conditions for 2 seconds or more.
—Selector lever position: D range
—Vehicle speed (VSS PID): 40 km/h {25 mph}
—Engine speed (RPM PID): 1,500 rpm or above.
iv. Go to Step 5.