steering MITSUBISHI ECLIPSE 1991 Manual Online
[x] Cancel search | Manufacturer: MITSUBISHI, Model Year: 1991, Model line: ECLIPSE, Model: MITSUBISHI ECLIPSE 1991Pages: 1216, PDF Size: 67.42 MB
Page 662 of 1216
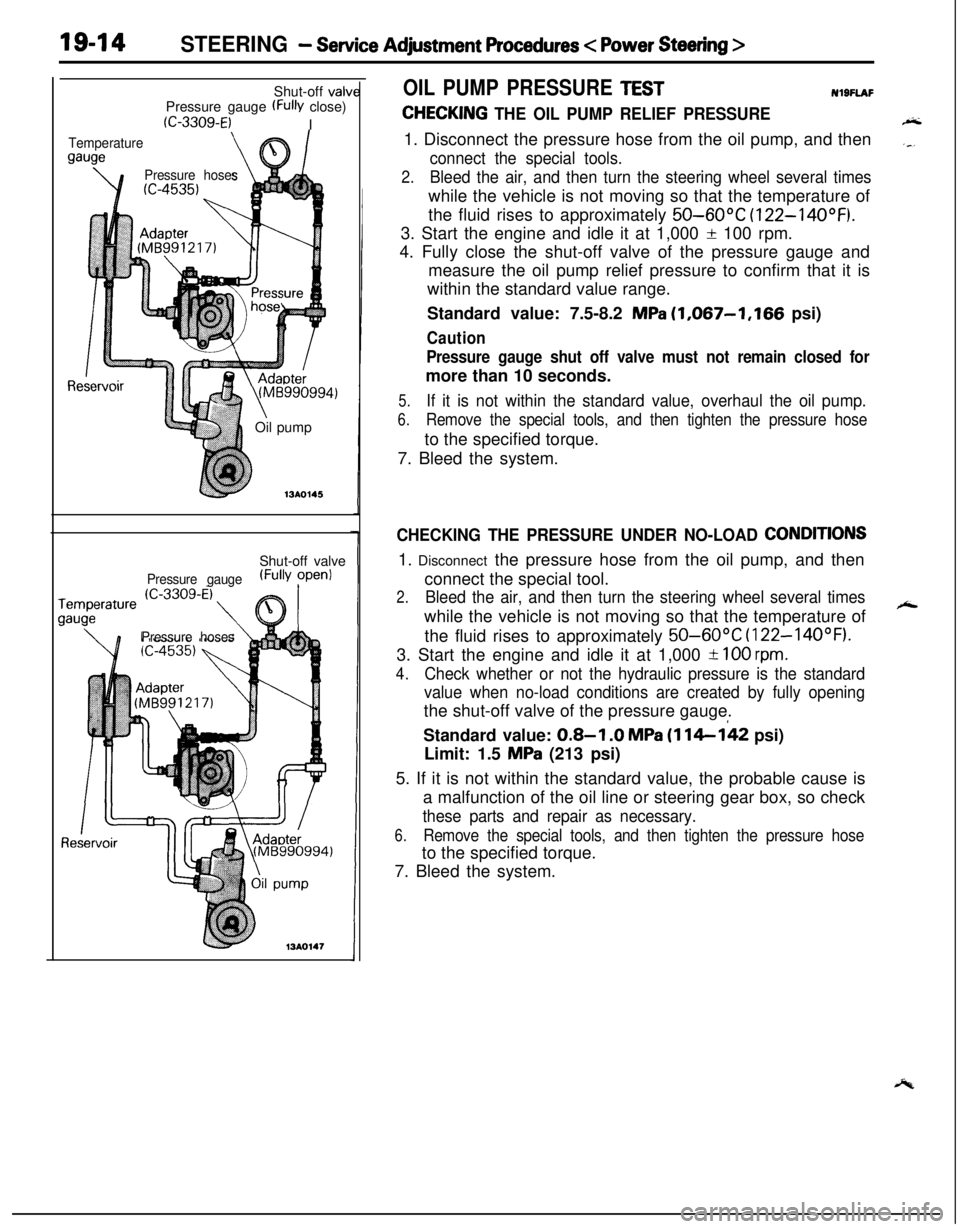
19-14STEERING - Service Adjustment Procedures < Power Steering >Shut-off valv
Pressure gauge
(FW close)
(C-3309-E)I
Temperature
gauge
\e’\
Pressure hoses
Re(Mti990994)
\Oil pump
713AO145Shut-off valve
Pressure gauge(FullY ?penl
Pressure hoses
OIL PUMP PRESSURE TESTNl9FlAF
CHECKING THE OIL PUMP RELIEF PRESSURE1. Disconnect the pressure hose from the oil pump, and then
connect the special tools.
2.Bleed the air, and then turn the steering wheel several timeswhile the vehicle is not moving so that the temperature of
the fluid rises to approximately
50-60°C (122-14OOF).3. Start the engine and idle it at 1,000
f 100 rpm.
4. Fully close the shut-off valve of the pressure gauge and
measure the oil pump relief pressure to confirm that it is
within the standard value range.
Standard value: 7.5-8.2
MPa (1,067-1,166 psi)
Caution
Pressure gauge shut off valve must not remain closed formore than 10 seconds.
5.If it is not within the standard value, overhaul the oil pump.
6.Remove the special tools, and then tighten the pressure hoseto the specified torque.
7. Bleed the system.
CHECKING THE PRESSURE UNDER NO-LOAD CONDITIONS1. Disconnect the pressure hose from the oil pump, and then
connect the special tool.
2.Bleed the air, and then turn the steering wheel several timeswhile the vehicle is not moving so that the temperature of
the fluid rises to approximately
50-60°C (122-14OOF).3. Start the engine and idle it at 1,000
-t 100 rpm.
4.
Check whether or not the hydraulic pressure is the standard
value when no-load conditions are created by fully openingthe shut-off valve of the pressure gauge.
Standard value:
0.8-I .O MPa (114-142 psi)
Limit: 1.5
MPa (213 psi)
5. If it is not within the standard value, the probable cause is
a malfunction of the oil line or steering gear box, so check
these parts and repair as necessary.
6.Remove the special tools, and then tighten the pressure hoseto the specified torque.
7. Bleed the system.
Page 663 of 1216
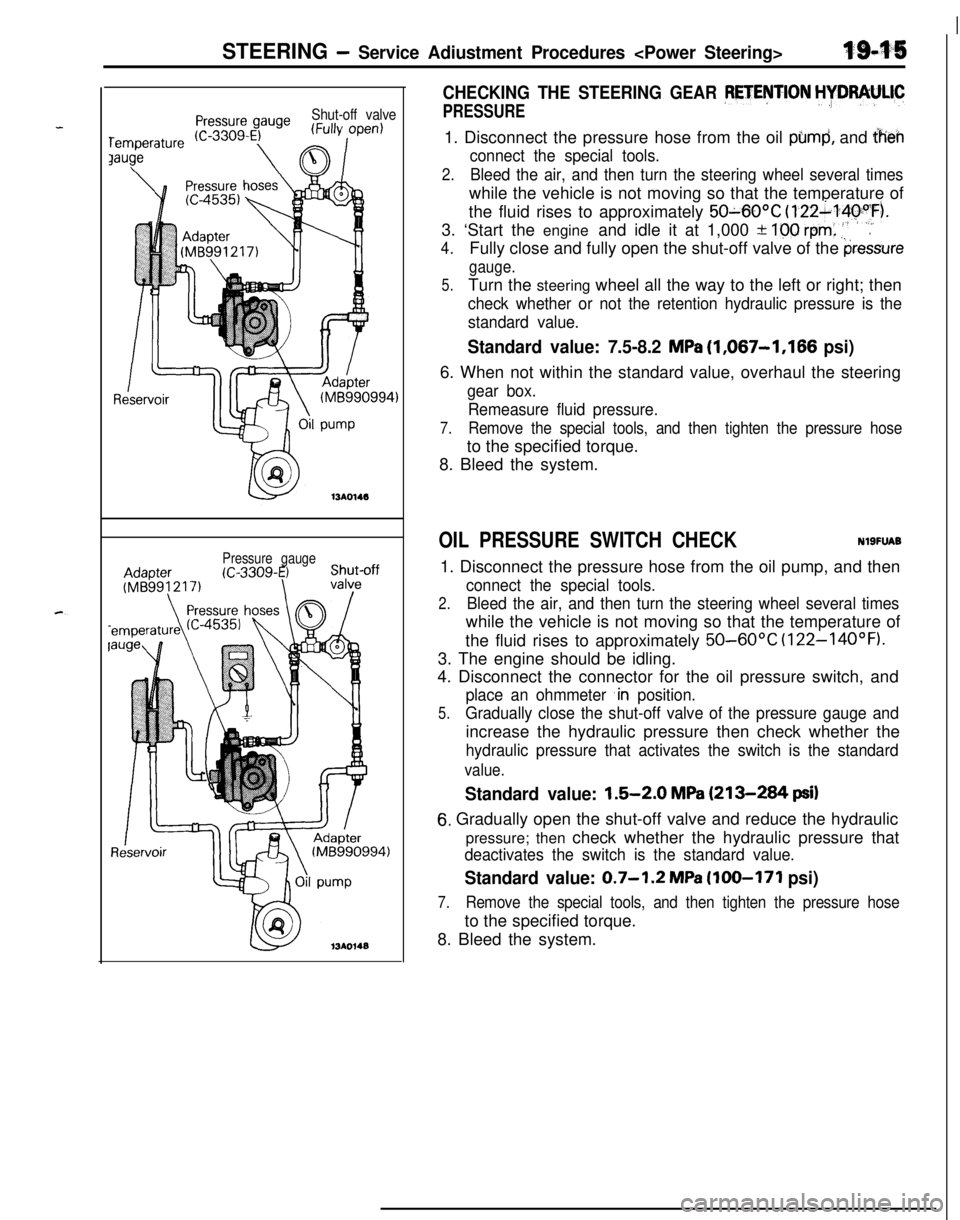
-
c. .
STEERING - Service Adiustment Procedures
Shut-off valve
Pressure gauge
CHECKING THE STEERING GEAR PETENTION HYDRAULIC
PRESSURE1. Disconnect the pressure hose from the oil
pbmd, and iheh
connect the special tools.
2.Bleed the air, and then turn the steering wheel several timeswhile the vehicle is not moving so that the temperature of
the fluid rises to approximately
50~60OC (122~14pyF).
3. ‘Start the engine and idle it at 1,000 +
100 rem: .‘,’.
4.Fully close and fully open the shut-off valve of the pressure
gauge.
5.Turn the steering wheel all the way to the left or right; then
check whether or not the retention hydraulic pressure is the
standard value.
Standard value: 7.5-8.2 MPa (1,067-1,166 psi)6. When not within the standard value, overhaul the steering
gear box.
Remeasure fluid pressure.
7.Remove the special tools, and then tighten the pressure hoseto the specified torque.
8. Bleed the system.
OIL PRESSURE SWITCH CHECKNlSFUAB1. Disconnect the pressure hose from the oil pump, and then
connect the special tools.
2.Bleed the air, and then turn the steering wheel several timeswhile the vehicle is not moving so that the temperature of
the fluid rises to approximately
50-60°C (122-14OOF).3. The engine should be idling.
4. Disconnect the connector for the oil pressure switch, and
place an ohmmeter ,in position.
5.Gradually close the shut-off valve of the pressure gauge andincrease the hydraulic pressure then check whether the
hydraulic pressure that activates the switch is the standard
value.
Standard value: 1.5-2.0 MPa (213-284 psi)
6. Gradually open the shut-off valve and reduce the hydraulic
pressure; then check whether the hydraulic pressure that
deactivates the switch is the standard value.
Standard value: 0.7-1.2 MPa (100-171 psi)
7.Remove the special tools, and then tighten the pressure hoseto the specified torque.
8. Bleed the system.
Page 664 of 1216

19-16STEERING - Steering Wheel and Shaft
STEERING WHEEL AND SHAFT
REMOVAL AND INSTALLATIONNlL)GA- ‘-
Post-installation Operationl Checking of Steering Wheel Posi-
tion with Wheels Straight Ahead
835-45 Nm
725-33 ft.lbs.
\
3
\\
15-20 Nm
11-14 ft.lbs.Removal steps
1.
“,c$t assembly and gear box connecting
l *2. Horn pad
4*3. Steering wheel
+* ++ 4. Instrument under cover
5. Foot shower duct and lap shower duct
6. Column cover lower
7. Column cover upper
8. Cover
assembly side)
\8-i2 Nm’11 6-9 ft.lbs.0
413AO296
+4 10. Slide lever 11. Cover attaching bolts
12. Lower bracket installation bolts
13. Tilt bracket installation bolts
14. Steering column assembly
15. Column support
NOTE(I) Reverse the removal procedures to reinstall.(2) a* : Refer to “Service Points of Removal”.(3) +a : Refer to “Service Points of Installation”.
Page 665 of 1216
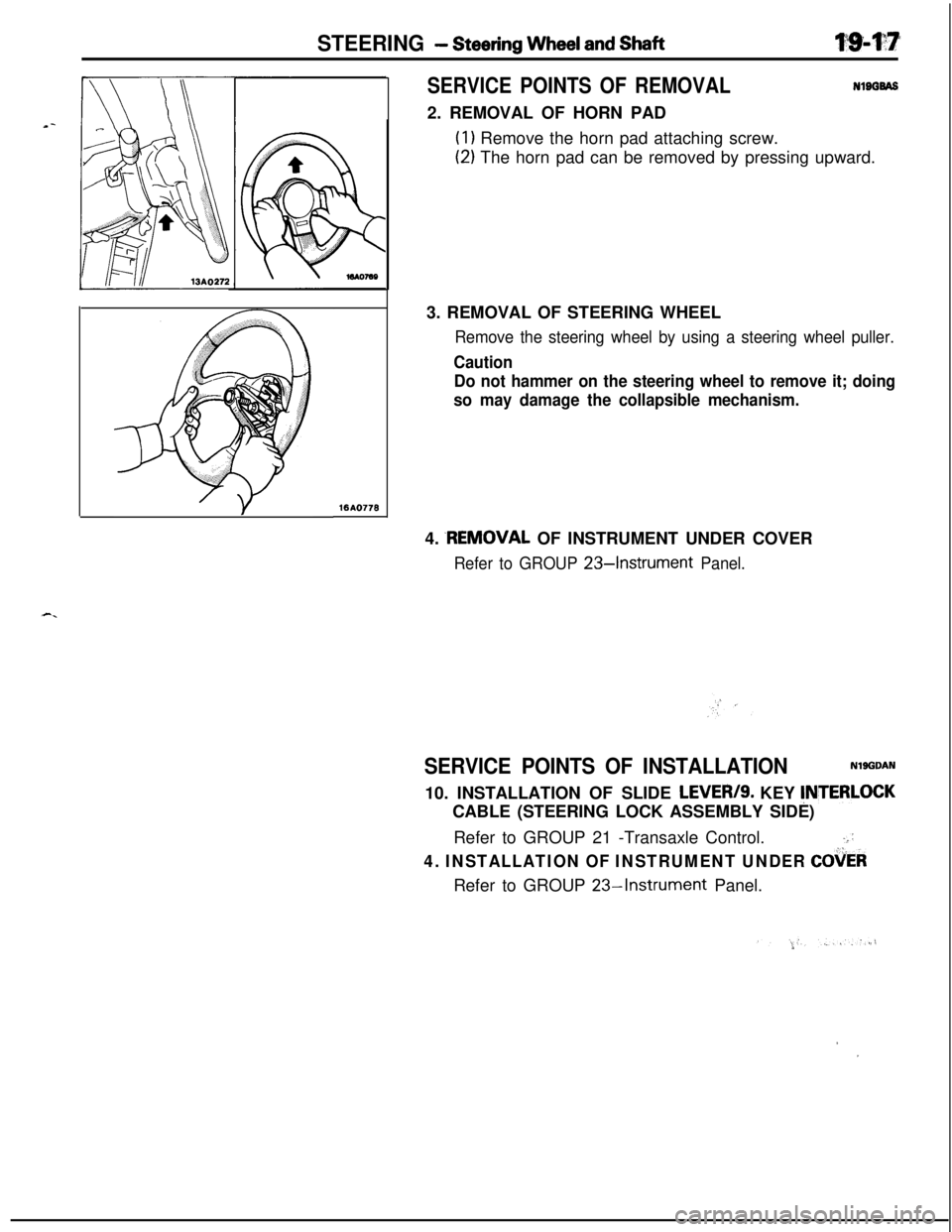
STEERING - Steering Wheel and Shaft
1610778
SERVICE POINTS OF REMOVALNlBGBAS2. REMOVAL OF HORN PAD
(1) Remove the horn pad attaching screw.
(2) The horn pad can be removed by pressing upward.
3. REMOVAL OF STEERING WHEEL
Remove the steering wheel by using a steering wheel puller.
Caution
Do not hammer on the steering wheel to remove it; doing
so may damage the collapsible mechanism.4.
.REMOVAL OF INSTRUMENT UNDER COVER
Refer to GROUP 234nstrument Panel.
SERVICE POINTS OF INSTALLATIONNlgGDAN10. INSTALLATION OF SLIDE
LEVER/S. KEY !NTERLOCKCABLE (STEERING LOCK ASSEMBLY SIDE)
Refer to GROUP 21 -Transaxle Control.
.::
4. INSTALLATION OF INSTRUMENT UNDER COiiERRefer to GROUP
23-Instrument Panel.
,I
Page 666 of 1216
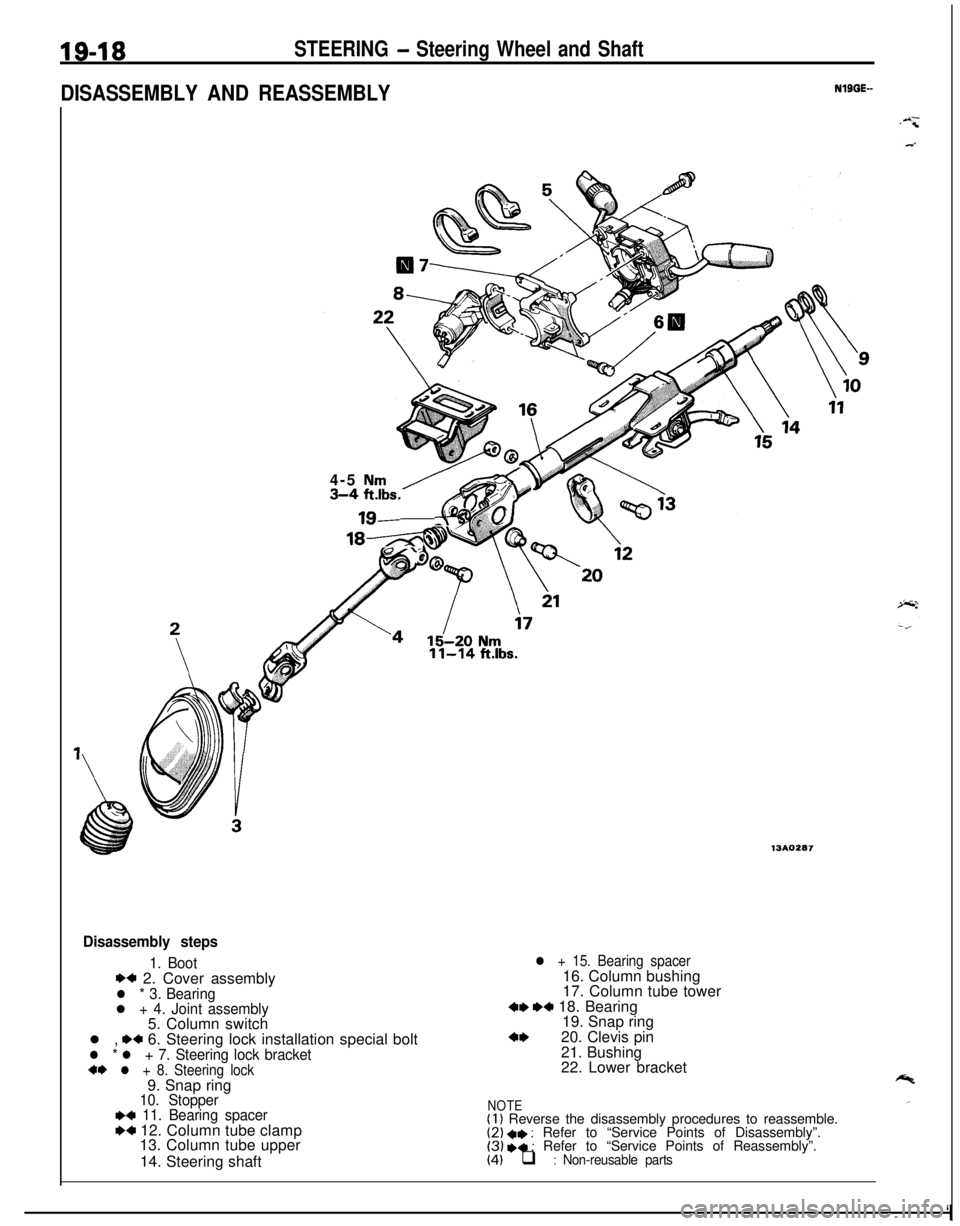
19-18STEERING - Steering Wheel and Shaft
DISASSEMBLY AND REASSEMBLYNlBGE-
4-5
Nm3-4;lbs. -6
18-z.
11-14 ft.lbs.
13AO287
Disassembly steps
1. Boot*+ 2. Cover assemblyl * 3. Bearingl + 4. Joint assembly5. Column switch
l ,
.+ 6. Steering lock installation special boltl * l + 7. Steering lock bracket+I) l + 8. Steering lock9. Snap ring
10. Stopper~~ 11. Bearing spacerW 12. Column tube clamp
13. Column tube upper
14. Steering shaft
l + 15. Bearing spacer16. Column bushing
17. Column tube tower
4, ,+ 18. Bearing
19. Snap ring
4,20. Clevis pin
21. Bushing
22. Lower bracket
NOTE(I 1 Reverse the disassembly procedures to reassemble.(2) +I) : Refer to “Service Points of Disassembly”.(3) I)+ : Refer to “Service Points of Reassembly”.(4) q : Non-reusable parts
‘I
Page 667 of 1216
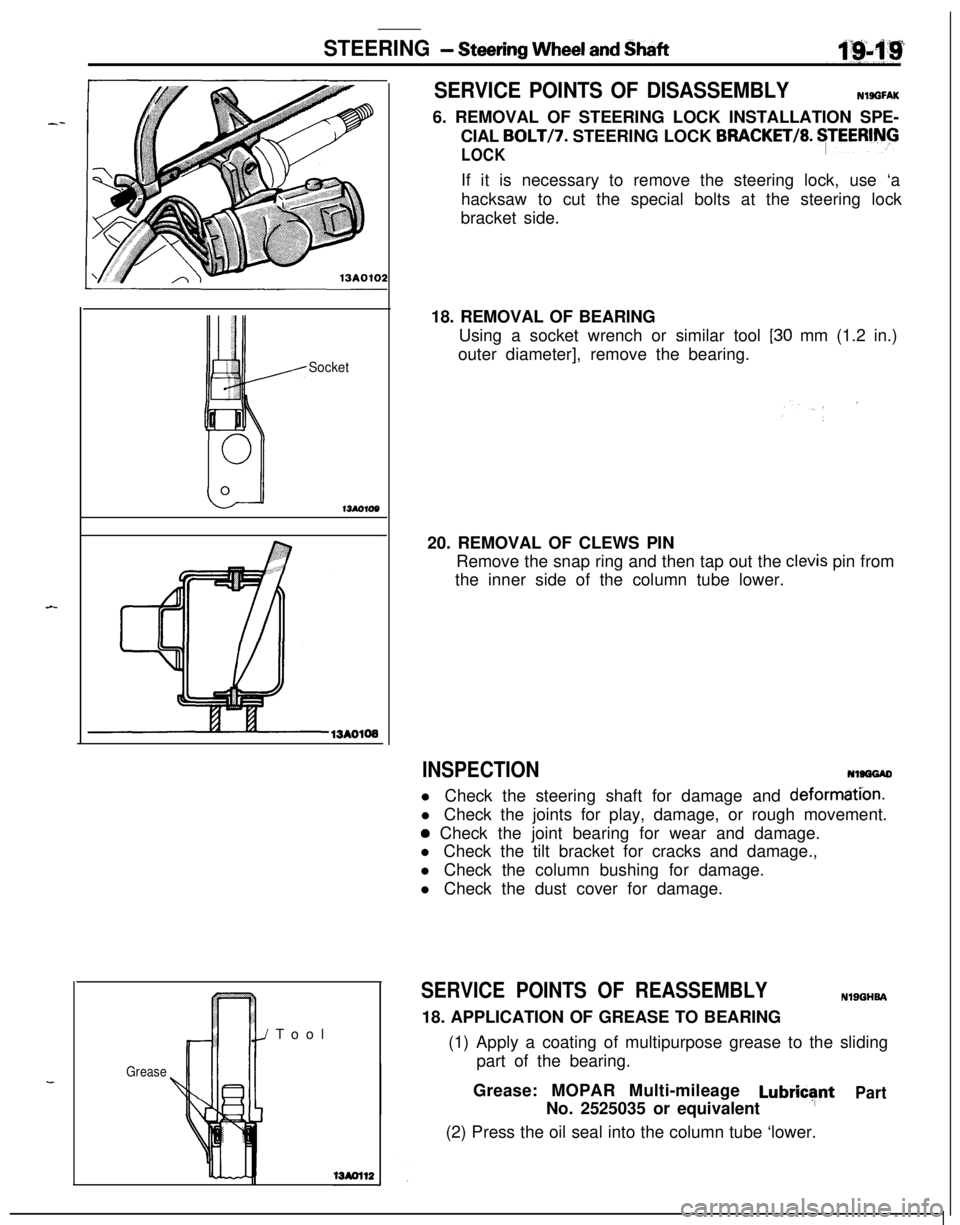
STEERING - Steering Wheel and Shaft
Socket13AO106
SERVICE POINTS OF DISASSEMBLYNlSGFAK6. REMOVAL OF STEERING LOCK INSTALLATION SPE-
CIAL
BOLTI7. STEERING LOCK BRACKET/8. $EERlNG
LOCKIf it is necessary to remove the steering lock, use ‘a
hacksaw to cut the special bolts at the steering lock
bracket side.
18. REMOVAL OF BEARING
Using a socket wrench or similar tool
[30 mm (1.2 in.)
outer diameter], remove the bearing.
20. REMOVAL OF CLEWS PIN
Remove the snap ring and then tap out the
clevis pin from
the inner side of the column tube lower.
INSPECTIONNlSGGADl Check the steering shaft for damage and
deformati’on.l Check the joints for play, damage, or rough movement.
a Check the joint bearing for wear and damage.
l Check the tilt bracket for cracks and damage.,
l Check the column bushing for damage.
l Check the dust cover for damage.
Grease/Tool
SERVICE POINTS OF REASSEMBLYNlSGHSA18. APPLICATION OF GREASE TO BEARING
(1) Apply a coating of multipurpose grease to the sliding
part of the bearing.
Grease: MOPAR Multi-mileage
LubricsfntPartNo. 2525035 or equivalent
(2) Press the oil seal into the column tube ‘lower.
Page 668 of 1216
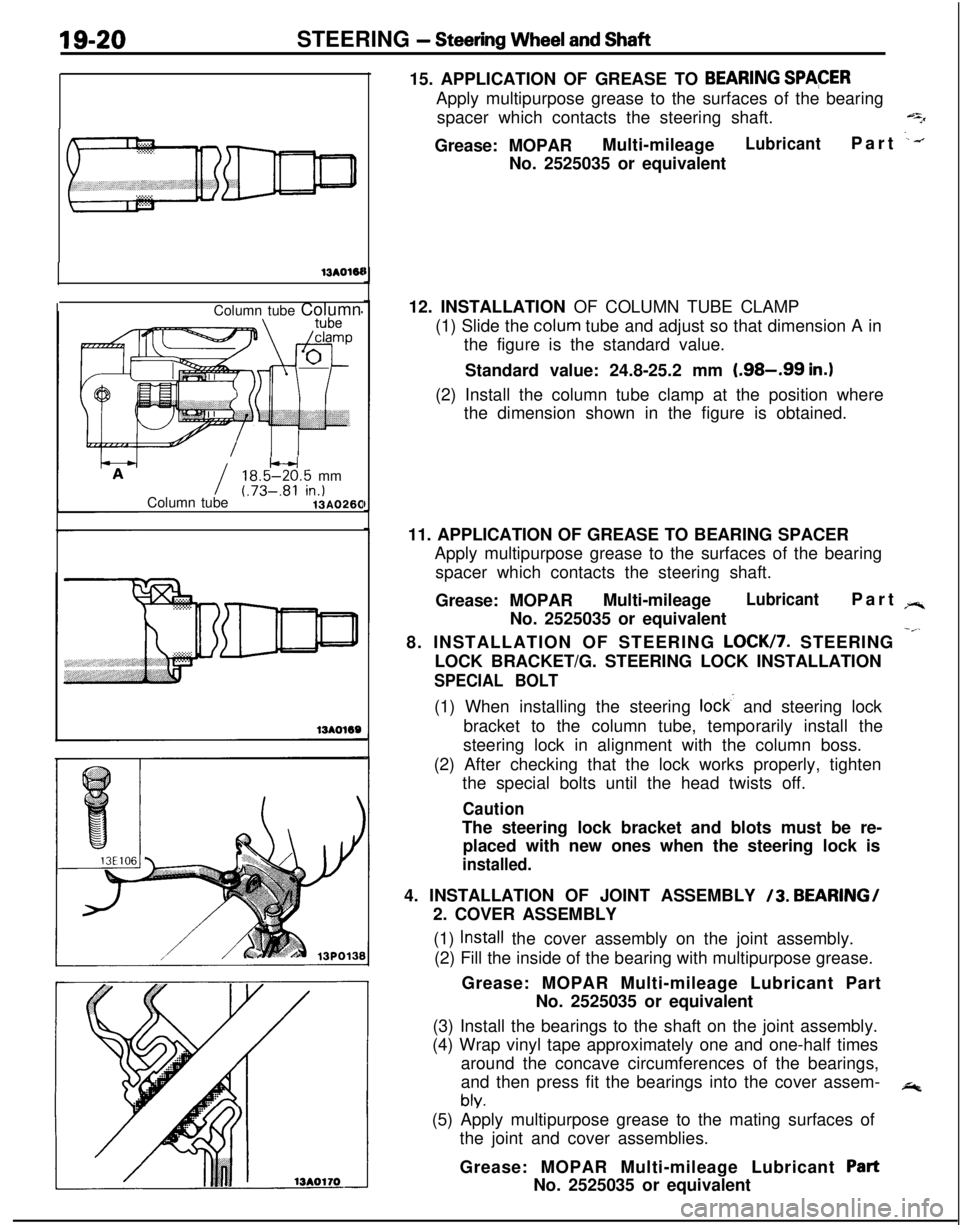
19-20STEERING - Steering Wheel and Shaft
13AOWColumn tube Column
I18.5W.5 mm
Column tube(.73-.81 in.)13AO26015. APPLICATION OF GREASE TO
BEARING SPACERApply multipurpose grease to the surfaces of the bearing
spacer which contacts the steering shaft.
qGrease: MOPARMulti-mileage
LubricantPart .--.No. 2525035 or equivalent
12. INSTALLATION OF COLUMN TUBE CLAMP
(1) Slide the colum tube and adjust so that dimension A in
the figure is the standard value.
Standard value: 24.8-25.2 mm
(.98-.99 in.)(2) Install the column tube clamp at the position where
the dimension shown in the figure is obtained.
11. APPLICATION OF GREASE TO BEARING SPACER
Apply multipurpose grease to the surfaces of the bearing
spacer which contacts the steering shaft.
Grease: MOPARMulti-mileage
LubricantPart rr.No. 2525035 or equivalent
8. INSTALLATION OF STEERING
LOCK/7. STEERING -”LOCK BRACKET/G. STEERING LOCK INSTALLATION
SPECIAL BOLT(1) When installing the steering
lock- and steering lock
bracket to the column tube, temporarily install the
steering lock in alignment with the column boss.
(2) After checking that the lock works properly, tighten
the special bolts until the head twists off.
CautionThe steering lock bracket and blots must be re-
placed with new ones when the steering lock is
installed.4. INSTALLATION OF JOINT ASSEMBLY
/3. BEARING/
2. COVER ASSEMBLY
(1)
Install the cover assembly on the joint assembly.
(2) Fill the inside of the bearing with multipurpose grease.
Grease: MOPAR Multi-mileage Lubricant Part
No. 2525035 or equivalent
(3) Install the bearings to the shaft on the joint assembly.
(4) Wrap vinyl tape approximately one and one-half times
around the concave circumferences of the bearings,
and then press fit the bearings into the cover assem-
*
bly.(5) Apply multipurpose grease to the mating surfaces of
the joint and cover assemblies.
Grease: MOPAR Multi-mileage Lubricant
PartNo. 2525035 or equivalent
Page 669 of 1216
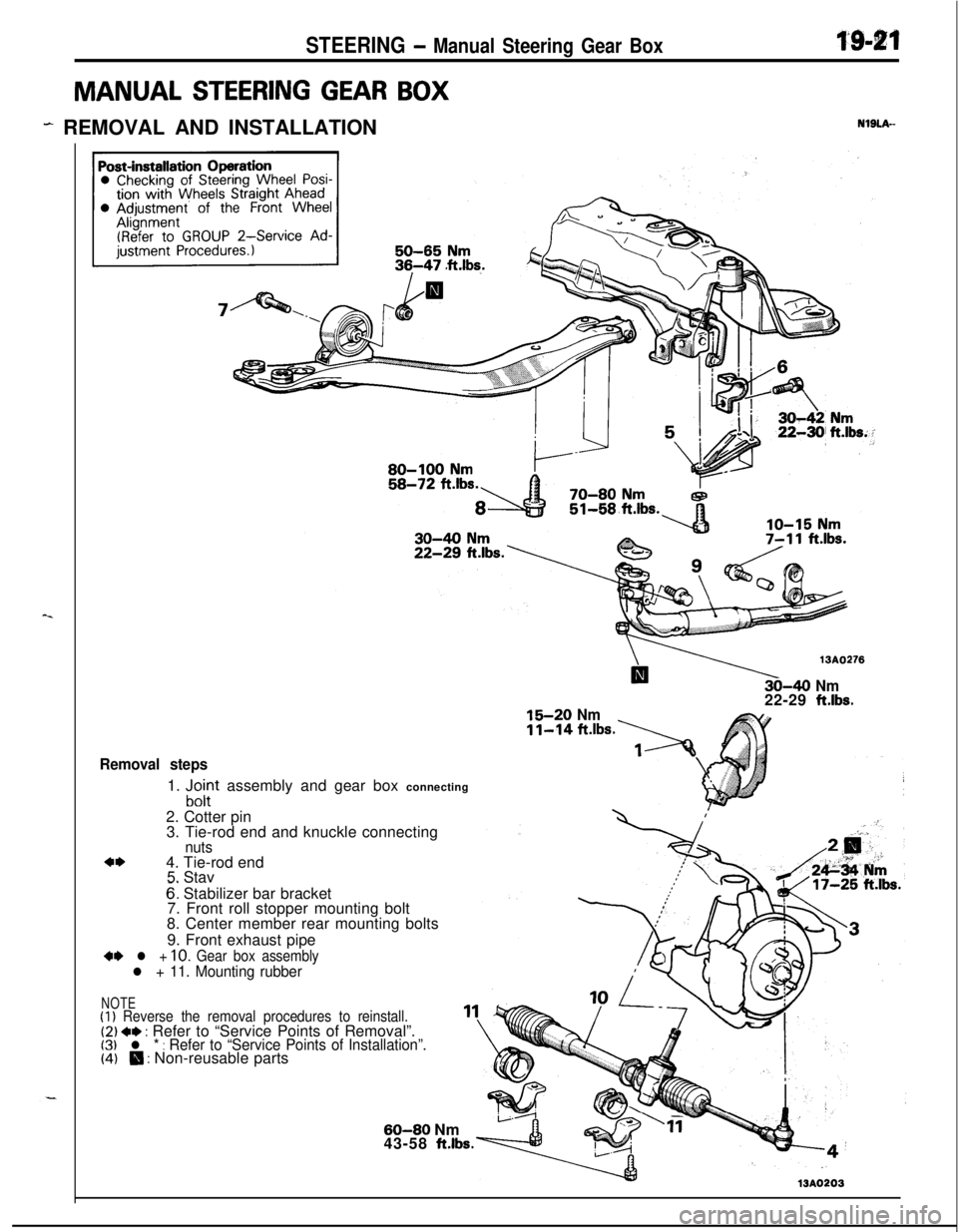
STEERING - Manual Steering Gear Box
MANUAL STEERING GEAR BOX
- REMOVAL AND INSTALLATION
1’94tf
NlSLA--
iI\13A027630-40 Nm22-29 ft.lbs.15-20 Nm11-14 ft.lbs.
Removal steps1.
J,O,Itt assembly and gear box connecting
2. Cotter pin
3. Tie-rod end and knuckle connecting
nuts4. Tie-rod end
5. Stav
6; Stabilizer bar bracket
7. Front roll stopper mounting bolt
8. Center member rear mounting bolts
9. Front exhaust pipe
+* l + 10. Gear box assemblyl + 11. Mounting rubber
NOTE(1) Reverse the removal procedures to reinstall.11 4(2) +* : Refer to “Service Points of Removal”.\
(3) l * : Refer to “Service Points of Installation”.\L?/ : Non-reusable parts(4) 0
60-60 Nm
43-58 ft.lbs.4.
WA0203
Page 670 of 1216
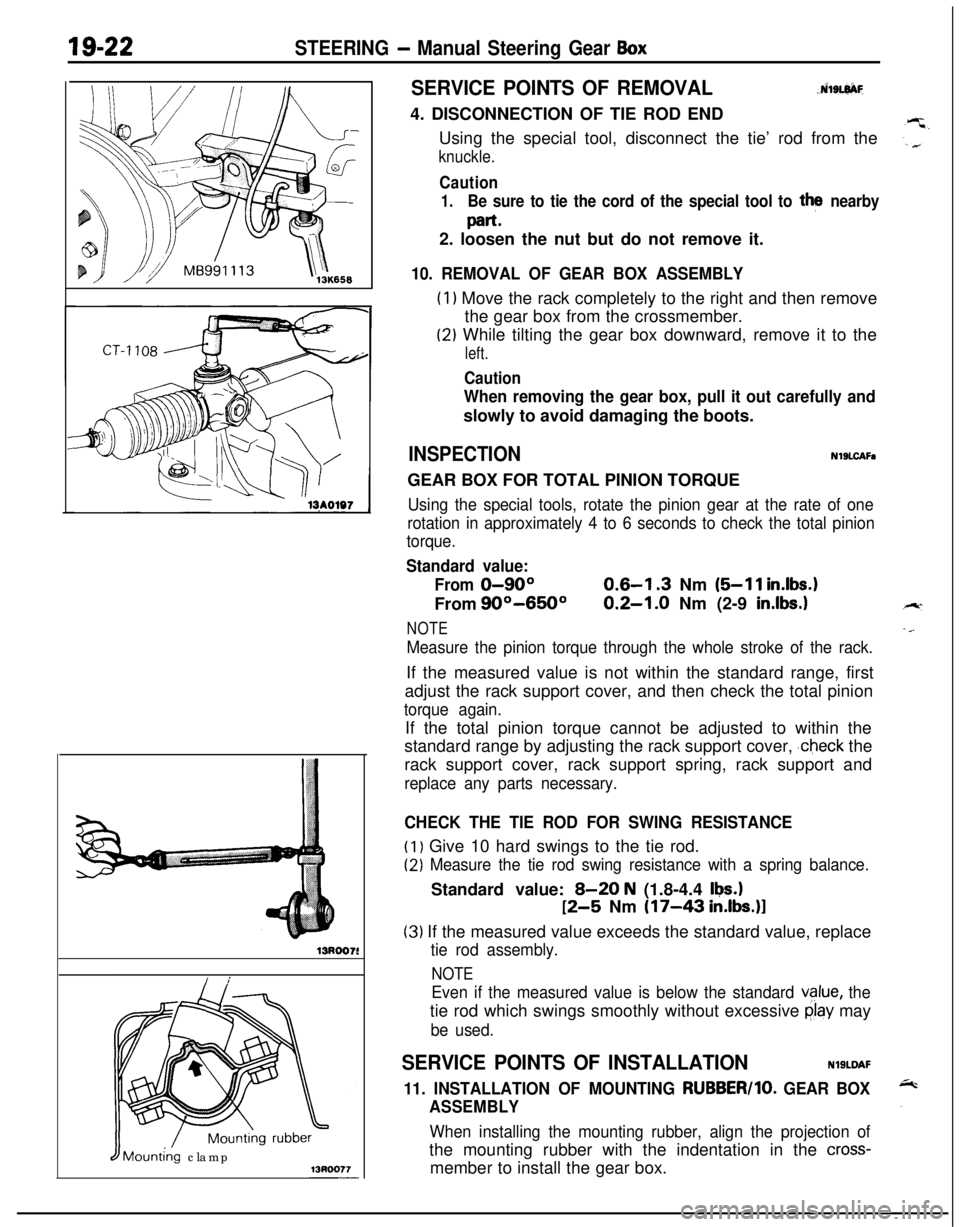
19-22STEERING - Manual Steering Gear Box
13Roo7!
J Mow&g clamp
SERVICE POINTS OF REMOVAL.dlSLl$iF
4. DISCONNECTION OF TIE ROD END
Using the special tool, disconnect the tie’ rod from the
knuckle.
Caution
1.Be sure to tie the cord of the special tool to the nearby
part*2. loosen the nut but do not remove it.
10. REMOVAL OF GEAR BOX ASSEMBLY
(1) Move the rack completely to the right and then remove
the gear box from the crossmember.
(2) While tilting the gear box downward, remove it to the
left.
Caution
When removing the gear box, pull it out carefully andslowly to avoid damaging the boots.
INSPECTIONNlSLCAFaGEAR BOX FOR TOTAL PINION TORQUE
Using the special tools, rotate the pinion gear at the rate of one
rotation in approximately 4 to 6 seconds to check the total pinion
torque.
Standard value:
From
0-90°0.6-l .3 Nm (5-11 in.lbs.1From
90°-650°0.2-1.0 Nm (2-9 in.lbs.1
NOTE
Measure the pinion torque through the whole stroke of the rack.If the measured value is not within the standard range, first
adjust the rack support cover, and then check the total pinion
torque again.If the total pinion torque cannot be adjusted to within the
standard range by adjusting the rack support cover,
,check the
rack support cover, rack support spring, rack support and
replace any parts necessary.
CHECK THE TIE ROD FOR SWING RESISTANCE
(1) Give 10 hard swings to the tie rod.
(2) Measure the tie rod swing resistance with a spring balance.Standard value:
B-20 N (1.8-4.4 Ikw.1
12-5 Nm (17-43 in.lbs.)l
(3) If the measured value exceeds the standard value, replace
tie rod assembly.
NOTE
Even if the measured value is below the standard vglue, thetie rod which swings smoothly without excessive
clay may
be used.
SERVICE POINTS OF INSTALLATIONNlSLDAF
11. INSTALLATION OF MOUNTING RUBBER/lo. GEAR BOX
ASSEMBLY
When installing the mounting rubber, align the projection ofthe mounting rubber with the indentation in the
cross-member to install the gear box.
Page 671 of 1216
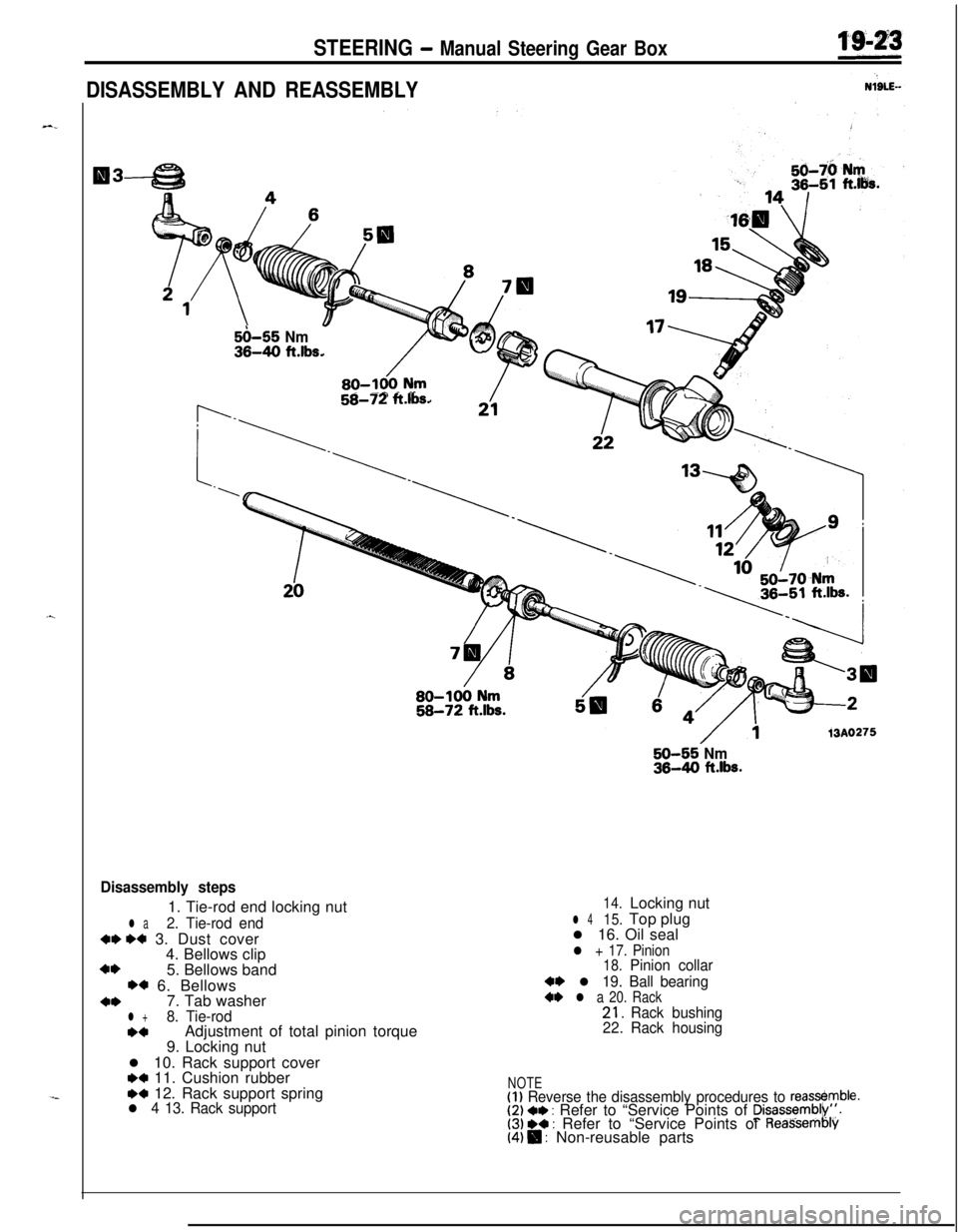
STEERING - Manual Steering Gear Box
DISASSEMBLY AND REASSEMBLY
5i)-55 Nm36-40 ft.lbs.
58-72 ft.lbs.
50-55 Nm36-40 ft.lbs.
13A0275
Disassembly steps1. Tie-rod end locking nut
l a2. Tie-rod end
W M 3. Dust cover
4. Bellows clip
+I)5. Bellows band
w 6. Bellows
+*7. Tab washerl +8. Tie-rod*aAdjustment of total pinion torque
9. Locking nut
l 10. Rack support cover
H 11. Cushion rubberw 12. Rack support springl 4 13. Rack support
14.Locking nut
l 415.Top plug
l 16. Oil seal
l + 17. Pinion
18.Pinion collar
4~ l 19. Ball bearing+* l a 20. Rack21.Rack bushing
22.Rack housing
NOTE(1) Reverse the disassembly procedures to reass&mble.(2) +e : Refer to “Service Points of Disassemblk’,‘.(3) ** : Refer to “Service Points of Reas’sembly(4) $I : Non-reusable parts