torque MITSUBISHI ECLIPSE 1991 Service Manual
[x] Cancel search | Manufacturer: MITSUBISHI, Model Year: 1991, Model line: ECLIPSE, Model: MITSUBISHI ECLIPSE 1991Pages: 1216, PDF Size: 67.42 MB
Page 24 of 1216
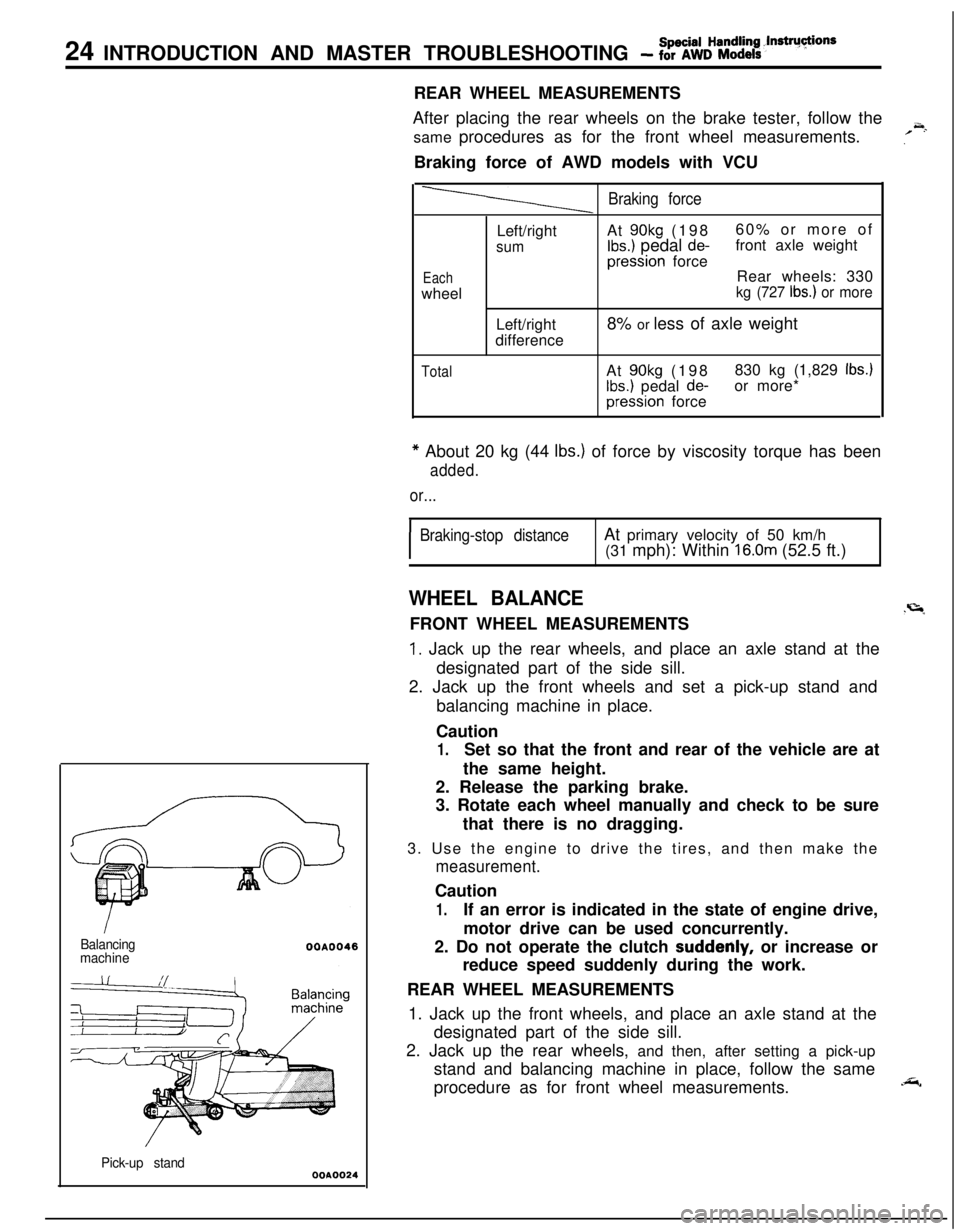
24 INTRODUCTION AND MASTER TROUBLESHOOTING - fSo%k%:~~it’ndrU~ionsREAR WHEEL MEASUREMENTS
After placing the rear wheels on the brake tester, follow the
same procedures as for the front wheel measurements.
,’
~.Braking force of AWD models with VCU
Balancing
machine
Pick-up stand
WA0024
Braking force
EachwheelLeft/right
sumLeft/right
differenceAt
90kg (19860% or more ofIbs.) pedal de-front axle weightpression force
Rear wheels: 330
kg (727 Ibs.) or more8% or less of axle weight
TotalAt 90kg (198830 kg (1,829 Ibs.)
Ibs.) pedal de-or more*pression force
* About 20 kg (44 Ibs.) of force by viscosity torque has been
added.
or...
I
Braking-stop distanceAt primary velocity of 50 km/h
(31 mph): Within 16.0m (52.5 ft.)
WHEEL BALANCE.r=lFRONT WHEEL MEASUREMENTS
1. Jack up the rear wheels, and place an axle stand at the
designated part of the side sill.
2. Jack up the front wheels and set a pick-up stand and
balancing machine in place.
Caution
1.Set so that the front and rear of the vehicle are at
the same height.
2. Release the parking brake.
3. Rotate each wheel manually and check to be sure
that there is no dragging.
3. Use the engine to drive the tires, and then make the
measurement.Caution
1.If an error is indicated in the state of engine drive,
motor drive can be used concurrently.
2. Do not operate the clutch
suddenly, or increase or
reduce speed suddenly during the work.
REAR WHEEL MEASUREMENTS
1. Jack up the front wheels, and place an axle stand at the
designated part of the side sill.
2. Jack up the rear wheels, and then, after setting a pick-up
stand and balancing machine in place, follow the same
procedure as for front wheel measurements.
.&,
Page 28 of 1216
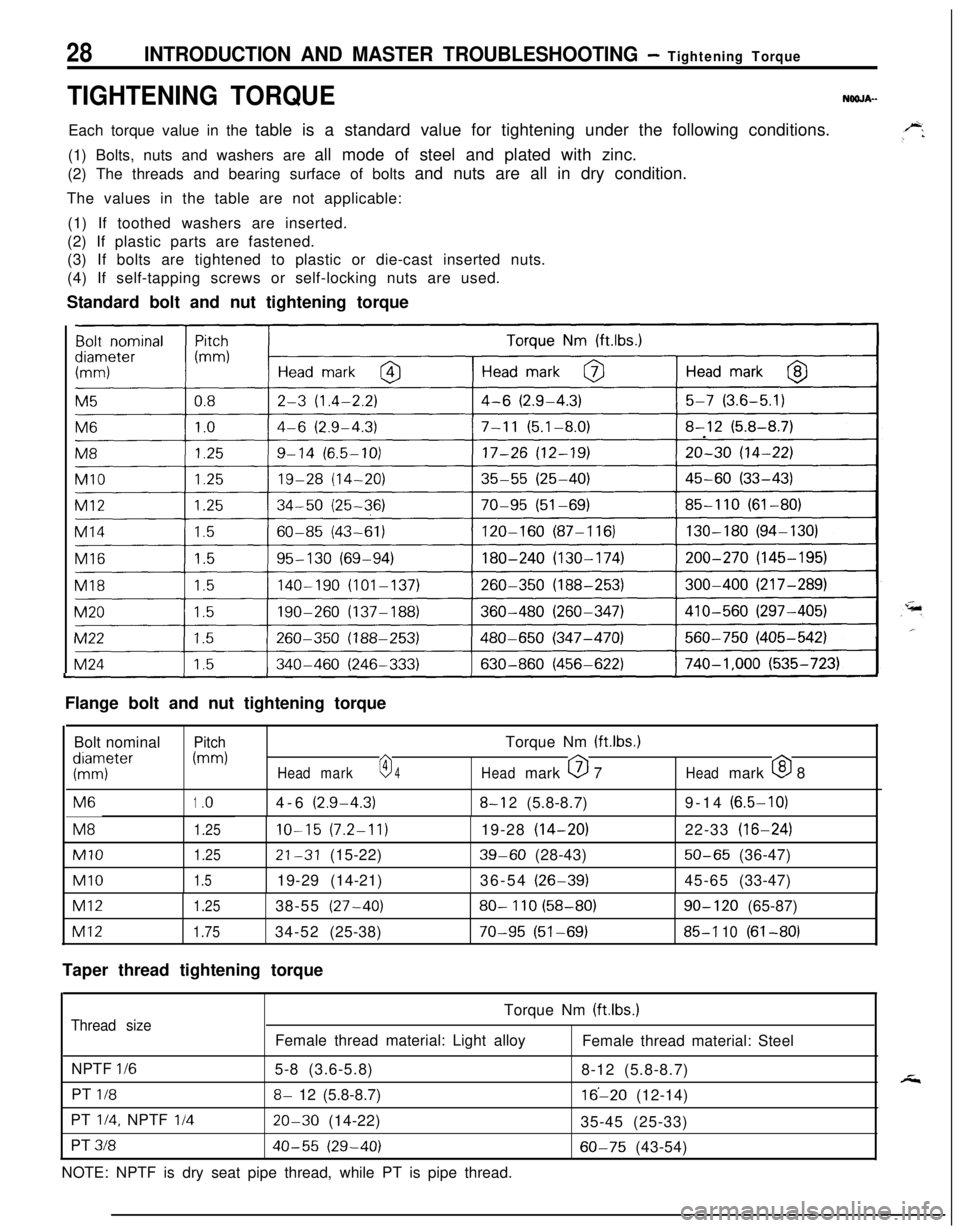
28INTRODUCTION AND MASTER TROUBLESHOOTING - Tightening Torque
TIGHTENING TORQUENOOJA-Each torque value in the table is a standard value for tightening under the following conditions.
(1) Bolts, nuts and washers are all mode of steel and plated with zinc.
(2) The threads and bearing surface of bolts and nuts are all in dry condition.
The values in the table are not applicable:
(1) If toothed washers are inserted.
(2) If plastic parts are fastened.
(3) If bolts are tightened to plastic or die-cast inserted nuts.
(4) If self-tapping screws or self-locking nuts are used.
Standard bolt and nut tightening torque
I
I
ILFlange bolt and nut tightening torque
Bolt nominal
PitchTorque Nm (ftlbs.)
KTter
(mm)
Headmark0 4Headmark 0 7Headmark 0 8M6
1.o4-6(2.9-4.3)8-l 2(5.8-8.7)9-14(6.5-10)M8
1.25IO-15(7.2-11)19-28(14-20)22-33(16-24)
Ml01.2521-31(15-22)39-60(28-43)50-65(36-47)
Ml01.519-29(14-21)36-54(26-39)45-65(33-47)
Ml21.2538-55(27-40)80- 110 (58-80)90- 120(65-87)
Ml21.7534-52(25-38)70-95 (51-69)85-l 10(61-80)
Taper thread tightening torque
Torque Nm (ftlbs.)
Thread sizeFemale thread material: Light alloy
Female thread material: Steel
NPTF
l/65-8 (3.6-5.8)
8-12 (5.8-8.7)
PT
l/88- 12 (5.8-8.7)16’-20 (12-14)
PT
l/4, NPTF I/420-30 (14-22)
35-45 (25-33)
PT
31840-55 (29-40)60-75 (43-54)
NOTE: NPTF is dry seat pipe thread, while PT is pipe thread.
Page 44 of 1216
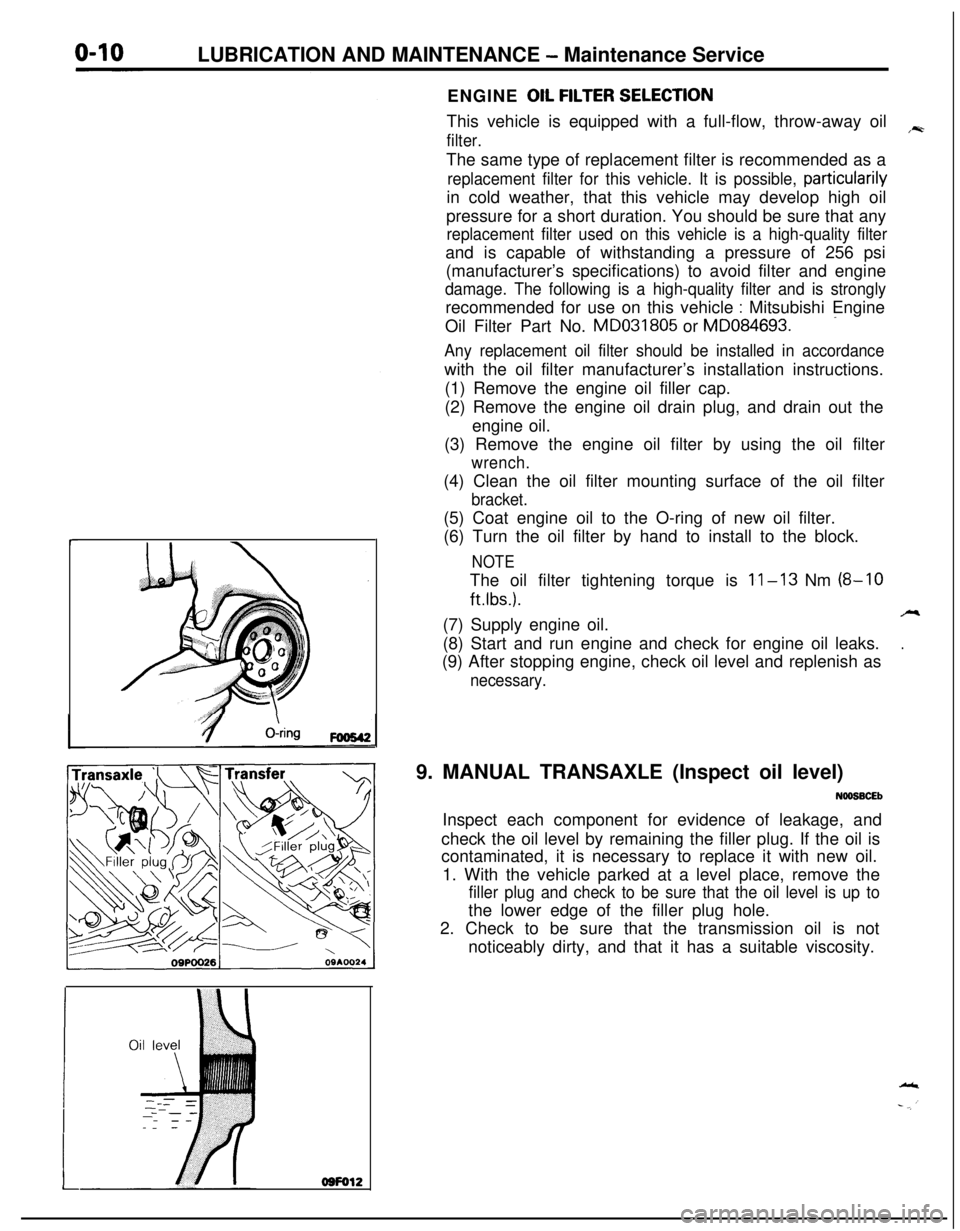
LUBRICATION AND MAINTENANCE - Maintenance Service
osFol2ENGINE
OIL FtLTER SELECTtONThis vehicle is equipped with a full-flow, throw-away oil
,~
filter.The same type of replacement filter is recommended as a
replacement filter for this vehicle. It is possible, particularilyin cold weather, that this vehicle may develop high oil
pressure for a short duration. You should be sure that any
replacement filter used on this vehicle is a high-quality filterand is capable of withstanding a pressure of 256 psi
(manufacturer’s specifications) to avoid filter and engine
damage. The following is a high-quality filter and is stronglyrecommended for use on this vehicle
: Mitsubishi Engine
-Oil Filter Part No. MD031805 or MD084693.
Any replacement oil filter should be installed in accordancewith the oil filter manufacturer’s installation instructions.
(1) Remove the engine oil filler cap.
(2) Remove the engine oil drain plug, and drain out the
engine oil.
(3) Remove the engine oil filter by using the oil filter
wrench.(4) Clean the oil filter mounting surface of the oil filter
bracket.(5) Coat engine oil to the O-ring of new oil filter.
(6) Turn the oil filter by hand to install to the block.
NOTEThe oil filter tightening torque is
11-13 Nm (8-10
ftlbs.).A(7) Supply engine oil.
.(8) Start and run engine and check for engine oil leaks.
(9) After stopping engine, check oil level and replenish as
necessary.9. MANUAL TRANSAXLE (Inspect oil level)
NOOSBCEbInspect each component for evidence of leakage, and
check the oil level by remaining the filler plug. If the oil is
contaminated, it is necessary to replace it with new oil.
1. With the vehicle parked at a level place, remove the
filler plug and check to be sure that the oil level is up tothe lower edge of the filler plug hole.
2. Check to be sure that the transmission oil is not
noticeably dirty, and that it has a suitable viscosity.
Page 45 of 1216
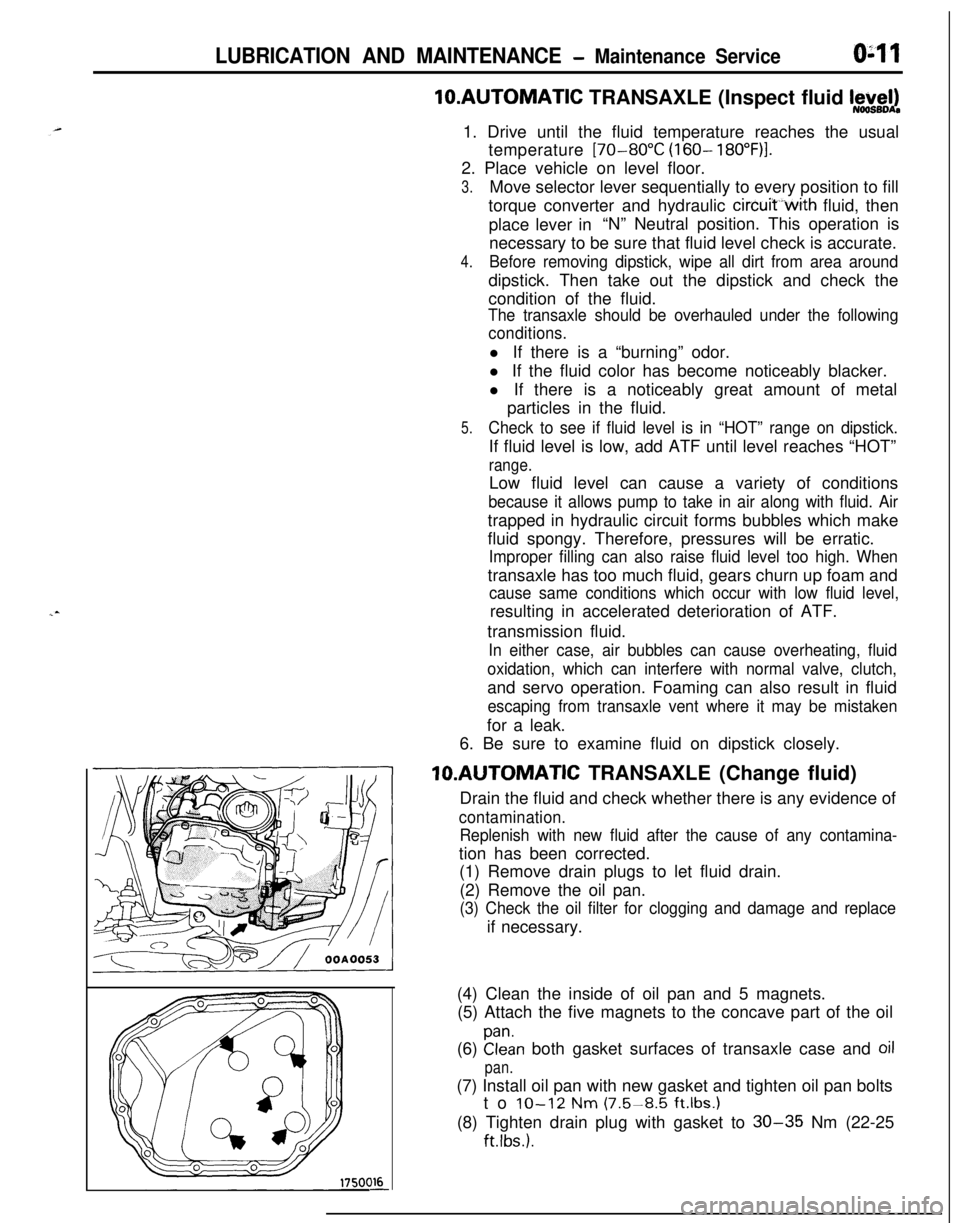
LUBRICATION AND MAINTENANCE - Maintenance ServiceO:lllO.AUTOMATIC TRANSAXLE (Inspect fluid
I~~+v~!1. Drive until the fluid temperature reaches the usual
temperature
[70-80°C (160- 18O”F)l.2. Place vehicle on level floor.
3.Move selector lever sequentially to every position to fill
torque converter and hydraulic
circuitwith fluid, then
place lever in“N” Neutral position. This operation is
necessary to be sure that fluid level check is accurate.
4.Before removing dipstick, wipe all dirt from area arounddipstick. Then take out the dipstick and check the
condition of the fluid.
The transaxle should be overhauled under the following
conditions.l If there is a “burning” odor.
l If the fluid color has become noticeably blacker.
l If there is a noticeably great amount of metal
particles in the fluid.
5.Check to see if fluid level is in “HOT” range on dipstick.If fluid level is low, add ATF until level reaches “HOT”
range.Low fluid level can cause a variety of conditions
because it allows pump to take in air along with fluid. Airtrapped in hydraulic circuit forms bubbles which make
fluid spongy. Therefore, pressures will be erratic.
Improper filling can also raise fluid level too high. Whentransaxle has too much fluid, gears churn up foam and
cause same conditions which occur with low fluid level,resulting in accelerated deterioration of ATF.
transmission fluid.
In either case, air bubbles can cause overheating, fluid
oxidation, which can interfere with normal valve, clutch,and servo operation. Foaming can also result in fluid
escaping from transaxle vent where it may be mistakenfor a leak.
6. Be sure to examine fluid on dipstick closely.lO.AUTOMATIC TRANSAXLE (Change fluid)
Drain the fluid and check whether there is any evidence of
contamination.
Replenish with new fluid after the cause of any contamina-tion has been corrected.
(1) Remove drain plugs to let fluid drain.
(2) Remove the oil pan.
(3) Check the oil filter for clogging and damage and replaceif necessary.
(4) Clean the inside of oil pan and 5 magnets.
(5) Attach the five magnets to the concave part of the oil
(6)
Elan both gasket surfaces of transaxle case and oil
pan.(7) Install oil pan with new gasket and tighten oil pan bolts
to
IO-12 Nm (7.5-8.5 ft.lbs.1(8) Tighten drain plug with gasket to
30-35 Nm (22-25
ftlbs.).
Page 46 of 1216
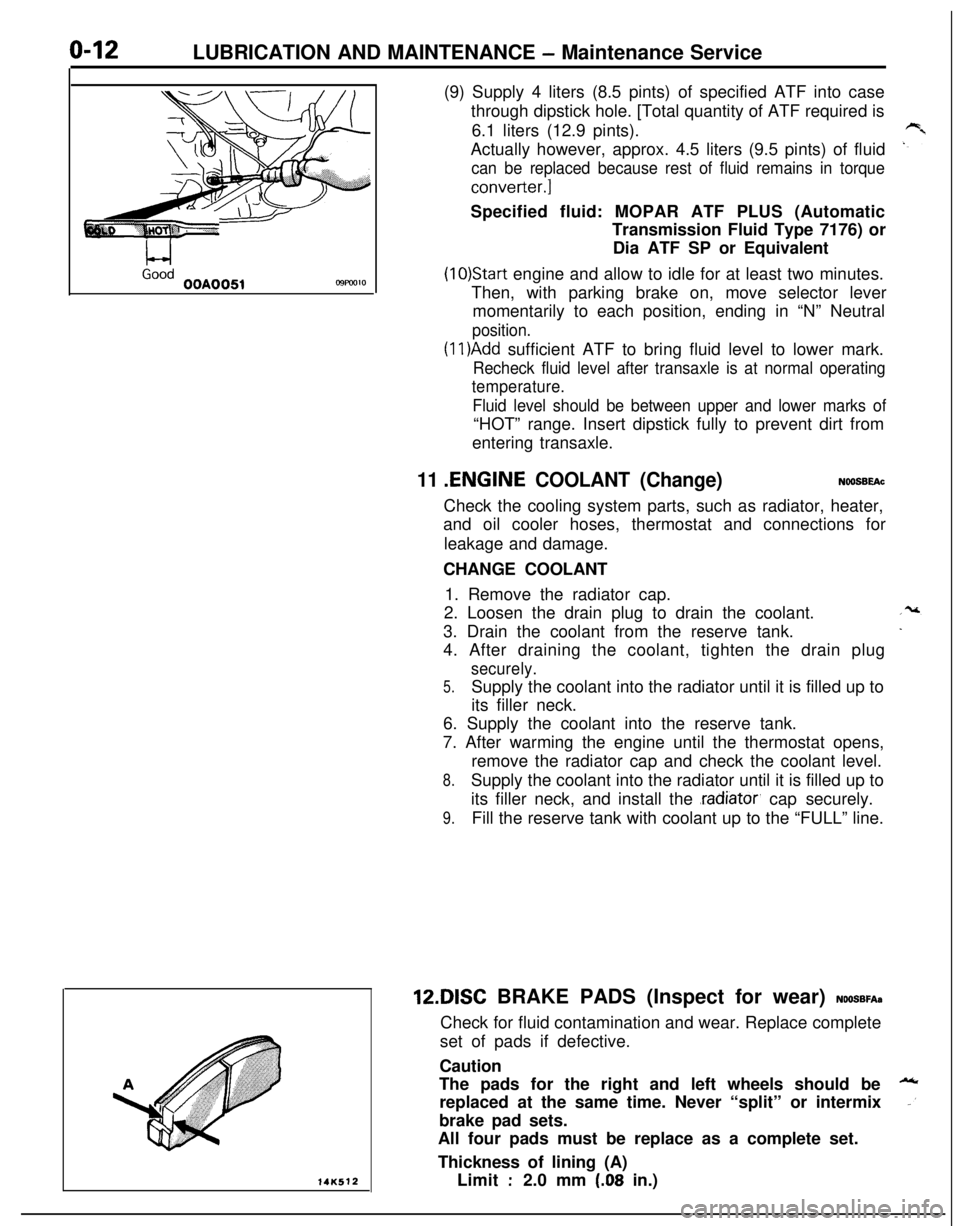
LUBRICATION AND MAINTENANCE - Maintenance Service
L-4GoodOOA0051C9FW1014K512(9) Supply 4 liters (8.5 pints) of specified ATF into case
through dipstick hole. [Total quantity of ATF required is
6.1 liters (12.9 pints).
Actually however, approx. 4.5 liters (9.5 pints) of fluid
can be replaced because rest of fluid remains in torque
converter.]Specified fluid: MOPAR ATF PLUS (Automatic
Transmission Fluid Type 7176) or
Dia ATF SP or Equivalent
(10)Start engine and allow to idle for at least two minutes.
Then, with parking brake on, move selector lever
momentarily to each position, ending in “N” Neutral
position.
(1 l)Add sufficient ATF to bring fluid level to lower mark.
Recheck fluid level after transaxle is at normal operating
temperature.
Fluid level should be between upper and lower marks of“HOT” range. Insert dipstick fully to prevent dirt from
entering transaxle.
11 .ENGINE COOLANT (Change)NOOSBEAcCheck the cooling system parts, such as radiator, heater,
and oil cooler hoses, thermostat and connections for
leakage and damage.
CHANGE COOLANT
1. Remove the radiator cap.
2. Loosen the drain plug to drain the coolant.
3. Drain the coolant from the reserve tank.
4. After draining the coolant, tighten the drain plug
securely.
5.Supply the coolant into the radiator until it is filled up to
its filler neck.
6. Supply the coolant into the reserve tank.
7. After warming the engine until the thermostat opens,
remove the radiator cap and check the coolant level.
8.Supply the coolant into the radiator until it is filled up to
its filler neck, and install the
.radiator, cap securely.
9.Fill the reserve tank with coolant up to the “FULL” line.12DISC BRAKE PADS (Inspect for wear)
NOOSBFA~Check for fluid contamination and wear. Replace complete
set of pads if defective.
Caution
The pads for the right and left wheels should be
replaced at the same time. Never “split” or intermix
brake pad sets.
All four pads must be replace as a complete set.
Thickness of lining (A)
Limit
:2.0 mm (.08 in.)
Page 49 of 1216
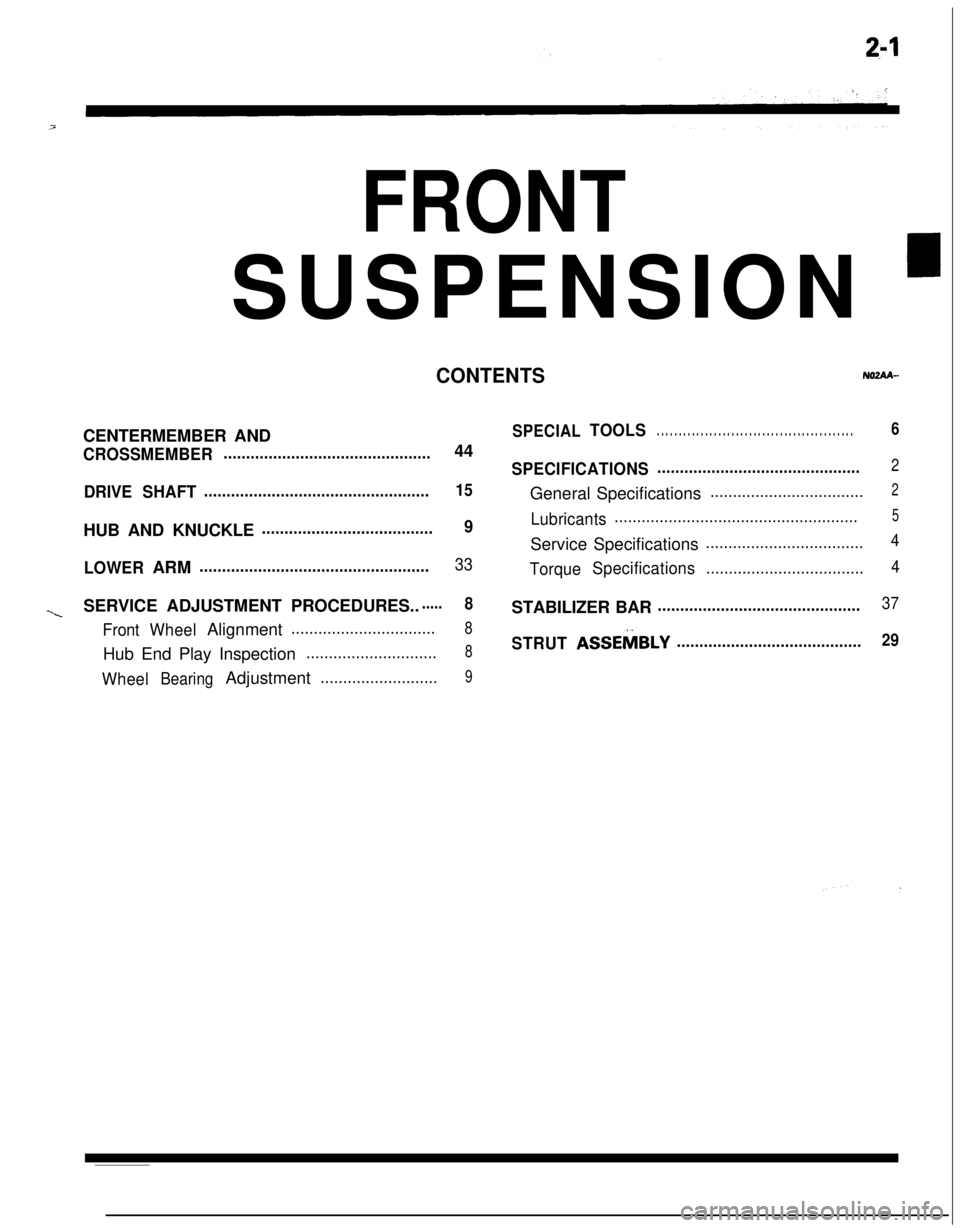
FRONTSUSPENSION
’
CONTENTSNOZAA-CENTERMEMBER AND
CROSSMEMBER..............................................44
DRIVESHAFT..................................................15HUB AND KNUCKLE
......................................9
LOWERARM
...................................................33
~SERVICE ADJUSTMENT PROCEDURES.......8
FrontWheelAlignment................................8Hub End Play Inspection
.............................8
WheelBearingAdjustment..........................9
SPECIALTOOLS. . . . . . . . . . . . . . . . . . . . . . . . . . . . . . . . . . . . . . . . . . . . .6
SPECIFICATIONS.............................................2General Specifications
..................................2
Lubricants......................................................5Service Specifications
...................................4
TorqueSpecifications...................................4STABILIZER BAR
.............................................37
STRUTASSEMBLY.........................................29
Page 52 of 1216
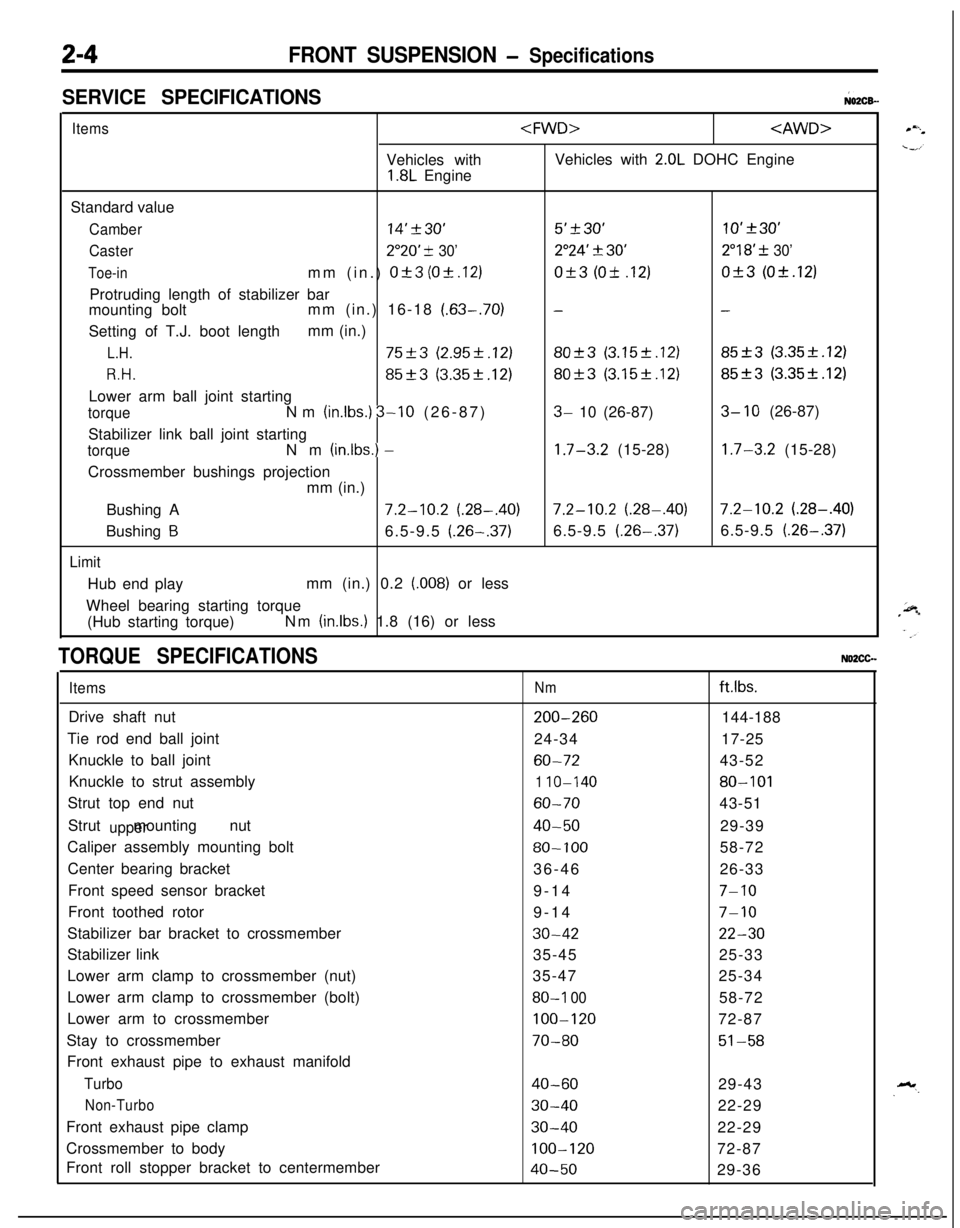
2-4FRONT SUSPENSION - Specifications
SERVICE SPECIFICATIONS;02CB-
ItemsVehicles with
1.8L Engine
2.0L DOHC Engine
Standard value
Camber14’230’5’+30’10’+30’
Caster2”20’ -t 30’2”24’ 3130’2”18’ f 30’
Toe-inmm (in.) Of3 (Ok.12)Of3 (Ok .12)Of3 (Ok.12)
Protruding length of stabilizer bar
mounting boltmm (in.) 16-18
(.63-.70)--Setting of T.J. boot lengthmm (in.)
L.H.75+3 (2.95f.12)80-+3 (3.15f.12)85_+3 (3.35k.12)
R.H.85f3 (3.35k.12)80+3 (3.15k.12)85f3 (3.35f.12)Lower arm ball joint starting
torqueNm (in.lbs.) 3-10 (26-87)3- 10 (26-87)3- 10 (26-87)
Stabilizer link ball joint starting
torqueNm (inlbs.) -1.7-3.2 (15-28)1.7-3.2 (15-28)
Crossmember bushings projection
mm (in.)
Bushing A
7.2-10.2 (.28-.40)7.2-10.2 (.28-.40)7.2-10.2 (.28-.40)
Bushing
B6.5-9.5 (.26-.37)6.5-9.5 (.26-.37)6.5-9.5 (.26-.37)
LimitHub end playmm (in.) 0.2
(.008) or less
Wheel bearing starting torque
(Hub starting torque)Nm
(in.lbs.) 1.8 (16) or less
TORQUE SPECIFICATIONSNO2CG.
ItemsDrive shaft nut
Tie rod end ball joint
Knuckle to ball joint
Knuckle to strut assembly
Strut top end nut
Strut mounting nut
upperCaliper assembly mounting bolt
Center bearing bracket
Front speed sensor bracket
Front toothed rotor
Stabilizer bar bracket to crossmember
Stabilizer link
Lower arm clamp to crossmember (nut)
Lower arm clamp to crossmember (bolt)
Lower arm to crossmember
Stay to crossmember
Front exhaust pipe to exhaust manifold
Turbo
Non-TurboFront exhaust pipe clamp
Crossmember to body
Front roll stopper bracket to centermember
Nmftlbs.
200-260144-188
24-3417-25
60-7243-52
1 IO-14080-101
60-7043-51
40-5029-39
80-10058-72
36-4626-33
9-14
7-109-14
7-10
30-4222-3035-4525-33
35-4725-34
80-I 0058-72
100-12072-87
70-8051-58
40-6029-43
30-4022-29
30-4022-29
100-12072-87
40-5029-36
Page 60 of 1216
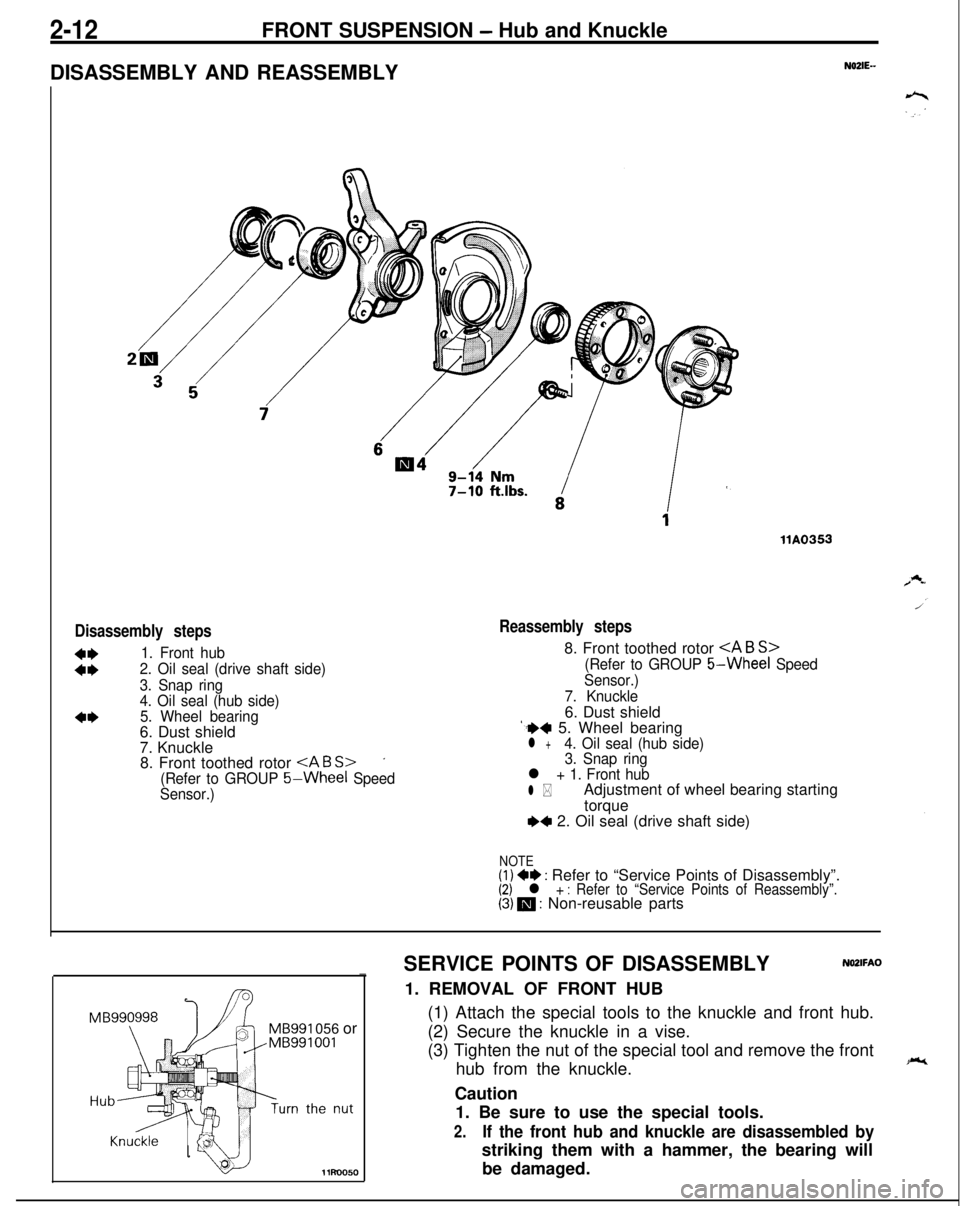
2-12FRONT SUSPENSION - Hub and Knuckle
DISASSEMBLY AND REASSEMBLY
N02lE--
Disassembly steps
:t
1. Front hub
2. Oil seal (drive shaft side)
3. Snap ring
4. Oil seal (hub side)
5. Wheel bearing6. Dust shield
7. Knuckle
8. Front toothed rotor
’
(Refer to GROUP 5-Wheel Speed
Sensor.)
llA0353
Reassembly steps8. Front toothed rotor
(Refer to GROUP 5-Wheel Speed
Sensor.)
7. Knuckle6. Dust shield
‘.++ 5. Wheel bearingl +4. Oil seal (hub side)
3. Snap ring
l + 1. Front hub
l *Adjustment of wheel bearing starting
torque
~~ 2. Oil seal (drive shaft side)
NOTE(1) +e : Refer to “Service Points of Disassembly”.(2) l + : Refer to “Service Points of Reassembly”.(3) m : Non-reusable parts
MB991 056 or
11uo050SERVICE POINTS OF DISASSEMBLY
NO2lFAO-1. REMOVAL OF FRONT HUB
(1) Attach the special tools to the knuckle and front hub.
(2) Secure the knuckle in a vise.
(3) Tighten the nut of the special tool and remove the front
hub from the knuckle.
Caution
1. Be sure to use the special tools.
2.If the front hub and knuckle are disassembled bystriking them with a hammer, the bearing will
be damaged.
Page 62 of 1216
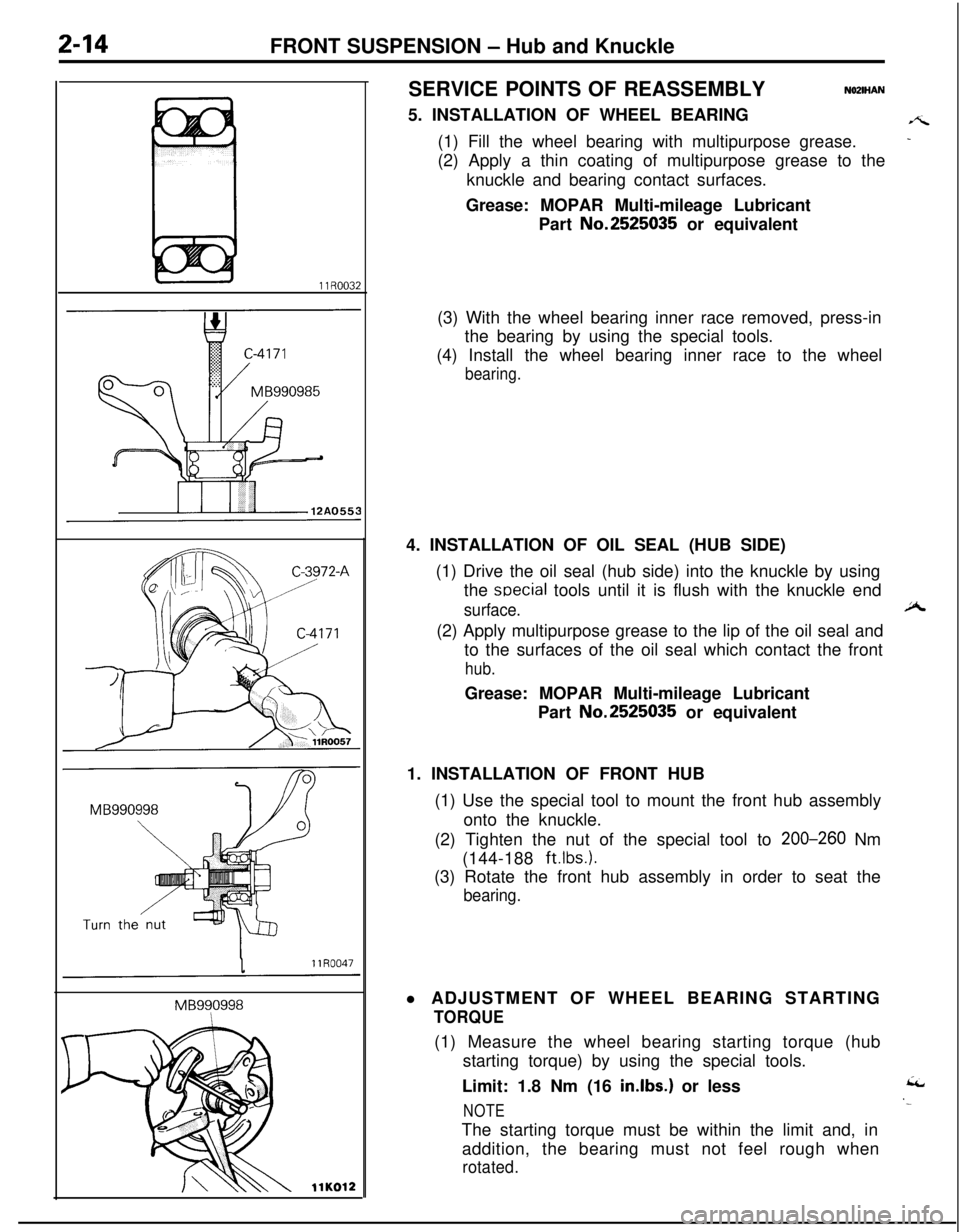
2-14FRONT SUSPENSION - Hub and Knuckle
llR0032
llK012SERVICE POINTS OF REASSEMBLY
NOZIHAN5. INSTALLATION OF WHEEL BEARING
A(1) Fill the wheel bearing with multipurpose grease.
-(2) Apply a thin coating of multipurpose grease to the
knuckle and bearing contact surfaces.
Grease: MOPAR Multi-mileage Lubricant
Part No.2525035 or equivalent
(3) With the wheel bearing inner race removed, press-in
the bearing by using the special tools.
(4) Install the wheel bearing inner race to the wheel
bearing.4. INSTALLATION OF OIL SEAL (HUB SIDE)
(1) Drive the oil seal (hub side) into the knuckle by using
the
soecial tools until it is flush with the knuckle end
surface.A(2) Apply multipurpose grease to the lip of the oil seal and
to the surfaces of the oil seal which contact the front
hub.Grease: MOPAR Multi-mileage Lubricant
Part No.2525035 or equivalent
1. INSTALLATION OF FRONT HUB
(1) Use the special tool to mount the front hub assembly
onto the knuckle.
(2) Tighten the nut of the special tool to 200-260 Nm
(144-188
ft.lbs.).(3) Rotate the front hub assembly in order to seat the
bearing.l ADJUSTMENT OF WHEEL BEARING STARTING
TORQUE(1) Measure the wheel bearing starting torque (hub
starting torque) by using the special tools.
Limit: 1.8 Nm (16
in.lbs.) or lessic
‘-NOTEThe starting torque must be within the limit and, in
addition, the bearing must not feel rough when
rotated.
Page 63 of 1216
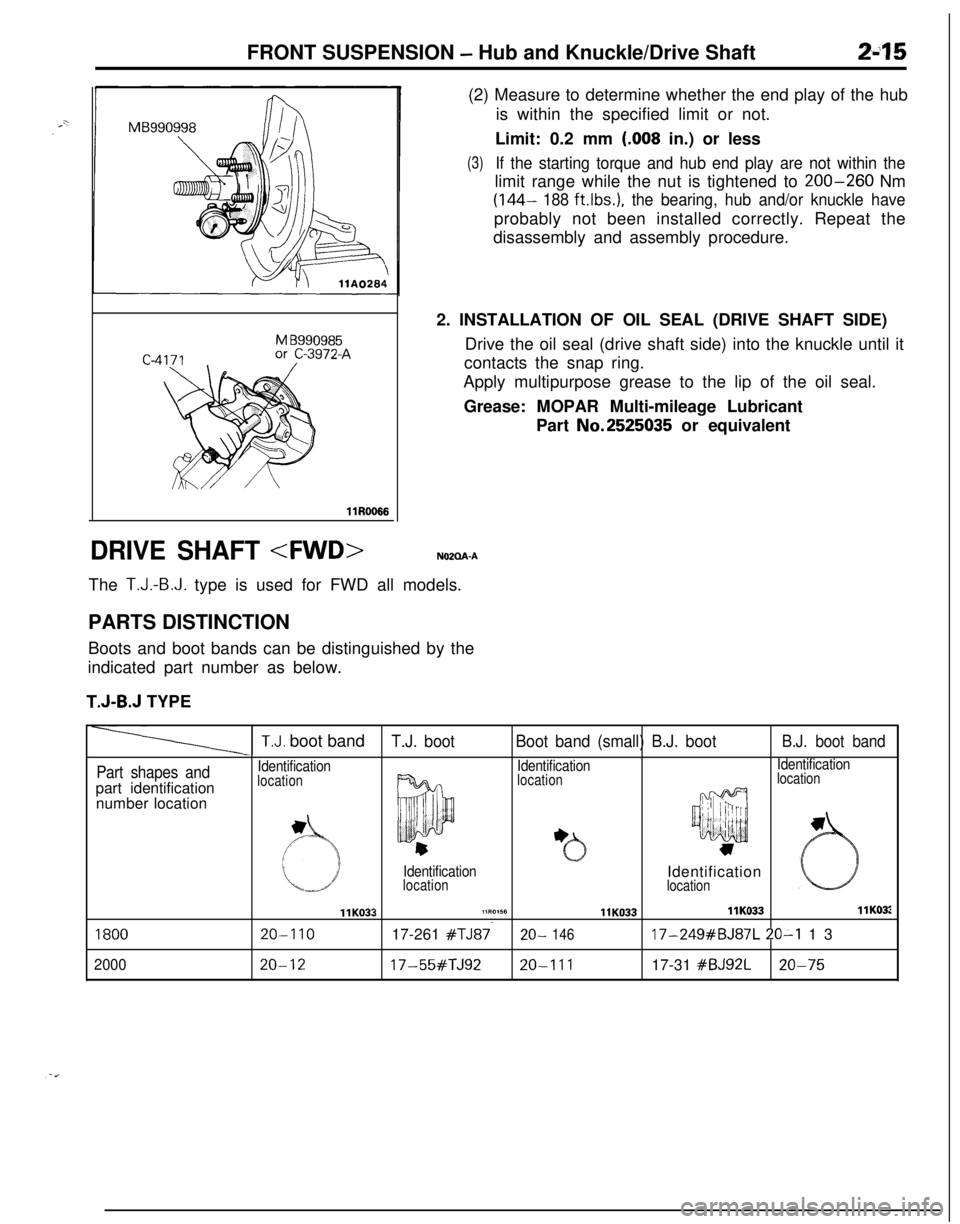
FRONT SUSPENSION - Hub and Knuckle/Drive Shaft245
M B990985
llR0066
DRIVE SHAFT
is within the specified limit or not.
Limit: 0.2 mm
(.008 in.) or less
(3)If the starting torque and hub end play are not within thelimit range while the nut is tightened to
200-260 Nm
(144- 188 ftlbs.), the bearing, hub and/or knuckle haveprobably not been installed correctly. Repeat the
disassembly and assembly procedure.
The
T.J.-B.J. type is used for FWD all models.
PARTS DISTINCTION
Boots and boot bands can be distinguished by the
indicated part number as below.
T.J-B.J TYPE2. INSTALLATION OF OIL SEAL (DRIVE SHAFT SIDE)
Drive the oil seal (drive shaft side) into the knuckle until it
contacts the snap ring.
Apply multipurpose grease to the lip of the oil seal.
Grease: MOPAR Multi-mileage Lubricant
Part No.2525035 or equivalent
Part shapes andpart identification
number location
T.J. boot bandT.J. bootBoot band (small) B.J. bootB.J. boot band
IdentificationIdentificationIdentificationlocation
locationlocation
1800
2000
IdentificationIdentificationlocation
location
llK033llR0156llK033llK033llK03:
20-I 1017-261 #TJ87.20- 14617-249#BJ87L 20-I 13
20-1217-55#TJ9220-11117-31 #BJ92L20-75