relay MITSUBISHI LANCER EVOLUTION IX 2005 Workshop Manual
[x] Cancel search | Manufacturer: MITSUBISHI, Model Year: 2005, Model line: LANCER EVOLUTION IX, Model: MITSUBISHI LANCER EVOLUTION IX 2005Pages: 364, PDF Size: 14.38 MB
Page 42 of 364

MPI – GENERAL13A-2
MPI system diagram
Engine ECU
H1. O
2 sensor
H2. Air flow sensor
H3. Intake air temp.
sensor
H4. Throttle position
sensor
H5. Intake Cam position
sensor
H6. Exhaust Cam
position sensor
H7. Crank angle
sensor
H8. Atmospheric
pressure sensor
H9. Water temp.
sensor
H10. Knock sensor
H11. Manifold absolute
pressure (MAP)
sensor
H12. Air temp. sensor• Power supply
• Ignition switch IG
• Ignition switch ST
• Vehicle speed
sensor
• A/C switch
• A/C load signal
• Power steering
fluid pressure switch
• Alternator FR signal
• Inter-cooler water spray
switch (auto)
•Inter-cooler water spray
switch (manual)I1. Injector
I2. ISC servo (Stepper
motor)
I3. Fuel pressure
control solenoid valve
I4. No. 1 Waste gate
solenoid valve
I5. No. 2 Waste gate
solenoid valve
I6. Purge control
solenoid valve
I7. Secondary air
control solenoid valve
I8. Oil feeder control
valve• Engine control relay
• Fuel pump relay 2,3
(ON/OFF)
• Fuel pump relay (HI/LO
switch)
• A/C relay
• Ignition coil
• Fan controller
• Condenser fan relay (HI)
• Condenser fan relay
(LO)
• Engine warning light
• Diagnosis output
terminal
• Alternator G terminal
• Inter-cooler water spray
relay
•Inter-cooler water spray
lamp
• O
2sensor heater
ÈÈ
I 6. Purge control
solenoid valve
I 7. Secondary
air control
solenoid valveCheck
valve
Secondary air
valve
To fuel
tank
H 6. Exhaust cam
position sensor
H 8. Atmospheric
pressure sensor
H 2. Air flow sensor
Intake
Waste gate actuator
I 4. No.1 waste gate
solenoid valve H 3. Intake air
temperature
sensor
I 5. No.2 waste gate
solenoid valve
H 1. O
2sensor
H 5. Intake cam
position sensorCatalyst
H 7. Crank angle sensor
H 10. Knock sensor
H 9. Water temperature sensor
I 1. Injector From fuel
pump
Fuel pressure
regulatorI 8. Oil feeder control
valve I 3. Fuel pressure
control solenoid
valve
Vacuum
tank
I 2. ISC servoH 11. MAP sensor
H 12. Air temperature sensor
H 4. Throttle
position
sensor
From fuel tank
Canister
By-pass valve
Page 49 of 364
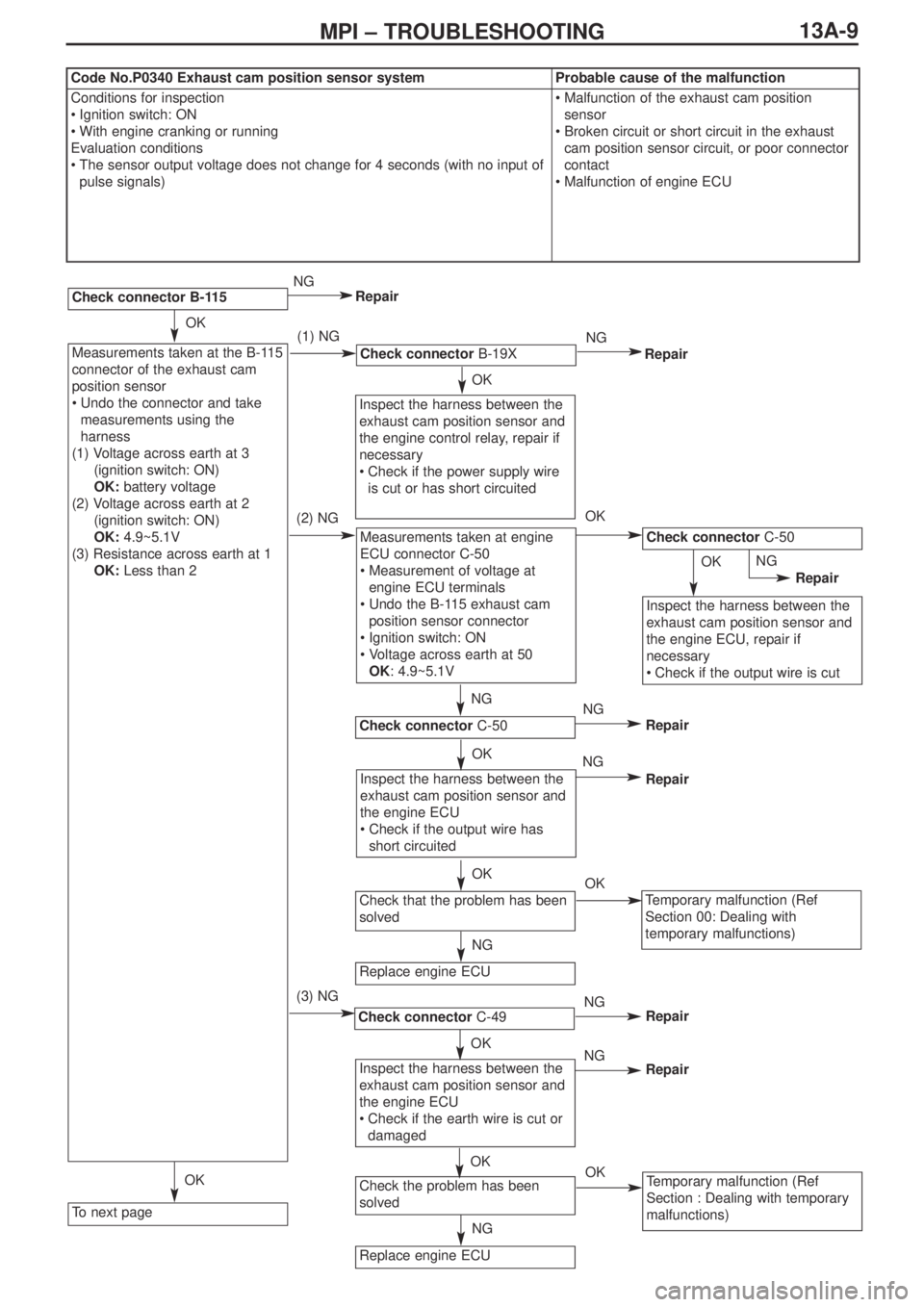
13A-9MPI – TROUBLESHOOTING
Check connector B-115
To next page
Check connectorB-19X
Measurements taken at engine
ECU connector C-50
•Measurement of voltage at
engine ECU terminals
•Undo the B-115 exhaust cam
position sensor connector
•Ignition switch: ON
•Voltage across earth at 50
OK: 4.9~5.1V
Inspect the harness between the
exhaust cam position sensor and
the engine control relay, repair if
necessary
•Check if the power supply wire
is cut or has short circuited
Inspect the harness between the
exhaust cam position sensor and
the engine ECU
•Check if the output wire has
short circuited
Check that the problem has been
solved
Check connectorC-50
Check connectorC-50
Inspect the harness between the
exhaust cam position sensor and
the engine ECU, repair if
necessary
•Check if the output wire is cut
Temporary malfunction (Ref
Section : Dealing with temporary
malfunctions)
Temporary malfunction (Ref
Section 00: Dealing with
temporary malfunctions)
Measurements taken at the B-115
connector of the exhaust cam
position sensor
•Undo the connector and take
measurements using the
harness
(1) Voltage across earth at 3
(ignition switch: ON)
OK:battery voltage
(2) Voltage across earth at 2
(ignition switch: ON)
OK:4.9~5.1V
(3) Resistance across earth at 1
OK:Less than 2Ω
NGRepair
Repair
OK
NG
OK
OK
NG
OK
NG
NG
OK
NGNG
NGOK
Inspect the harness between the
exhaust cam position sensor and
the engine ECU
•Check if the earth wire is cut or
damaged
Check connectorC-49
OK
OK
Replace engine ECU
NG
Check the problem has been
solved
Replace engine ECU
NG
OK
(1) NG
(2) NG
(3) NG
OK
OK
Repair
Repair
Repair
Repair
Repair
Code No.P0340 Exhaust cam position sensor systemProbable cause of the malfunction
Conditions for inspection
•Ignition switch: ON
•With engine cranking or running
Evaluation conditions
•The sensor output voltage does not change for 4 seconds (with no input of
pulse signals)•Malfunction of the exhaust cam position
sensor
•Broken circuit or short circuit in the exhaust
cam position sensor circuit, or poor connector
contact
•Malfunction of engine ECU
Page 50 of 364
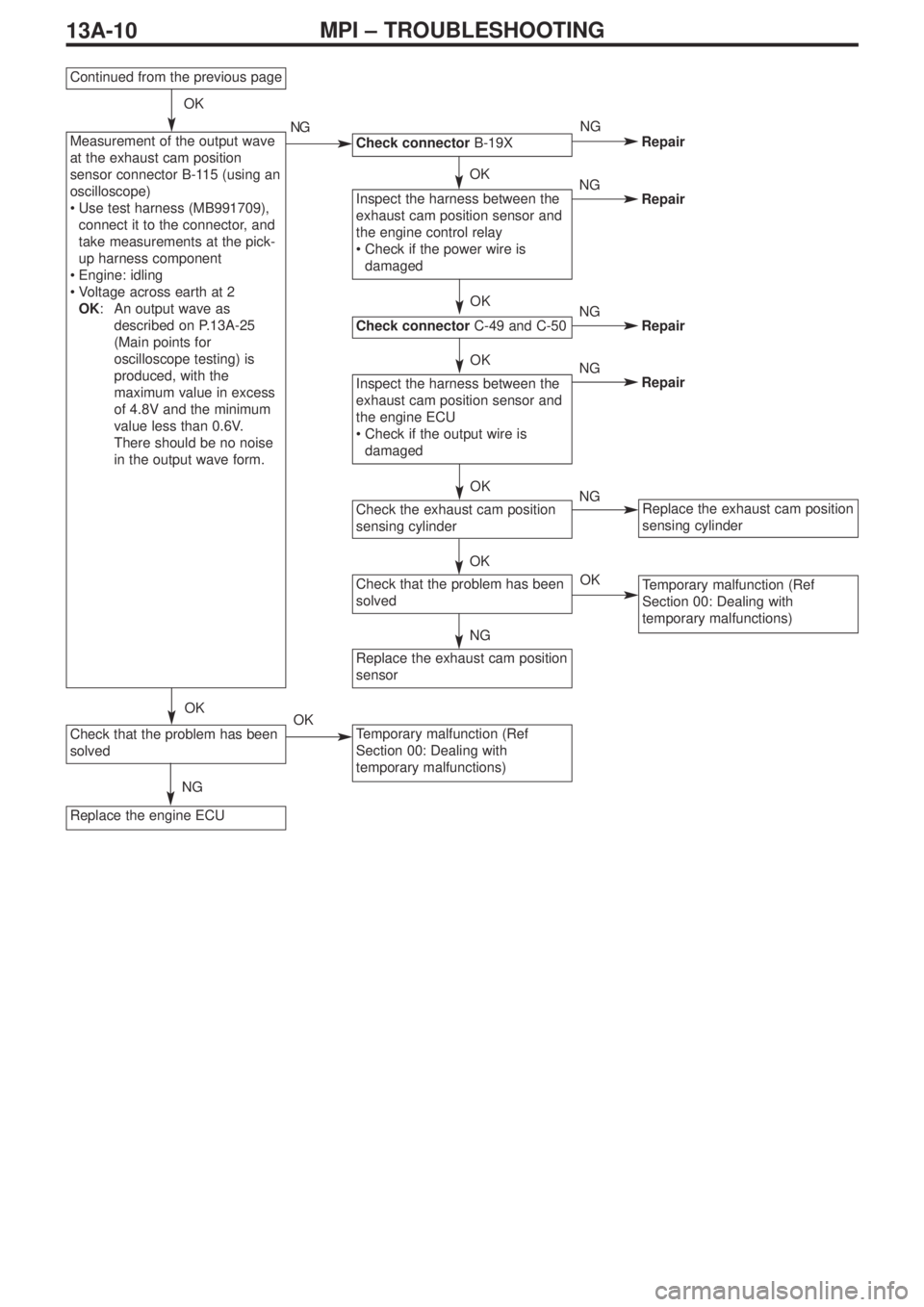
13A-10MPI – TROUBLESHOOTING
Continued from the previous page
Replace the engine ECU
Check connectorB-19X
Inspect the harness between the
exhaust cam position sensor and
the engine control relay
•Check if the power wire is
damaged
Check the exhaust cam position
sensing cylinder
Check connectorC-49 and C-50
Check that the problem has been
solved
Inspect the harness between the
exhaust cam position sensor and
the engine ECU
•Check if the output wire is
damaged
Temporary malfunction (Ref
Section 00: Dealing with
temporary malfunctions)
Measurement of the output wave
at the exhaust cam position
sensor connector B-115 (using an
oscilloscope)
•Use test harness (MB991709),
connect it to the connector, and
take measurements at the pick-
up harness component
•Engine: idling
•Voltage across earth at 2
OK: An output wave as
described on P.13A-25
(Main points for
oscilloscope testing) is
produced, with the
maximum value in excess
of 4.8V and the minimum
value less than 0.6V.
There should be no noise
in the output wave form.
Check that the problem has been
solved
OK
OK
NG
NG
OK
OK
OK
Replace the exhaust cam position
sensor
NG
OK
Replace the exhaust cam position
sensing cylinder
Temporary malfunction (Ref
Section 00: Dealing with
temporary malfunctions)
OK
OK
Repair
Repair
NG
NG
Repair NG
Repair NG
NG
OK
Page 51 of 364
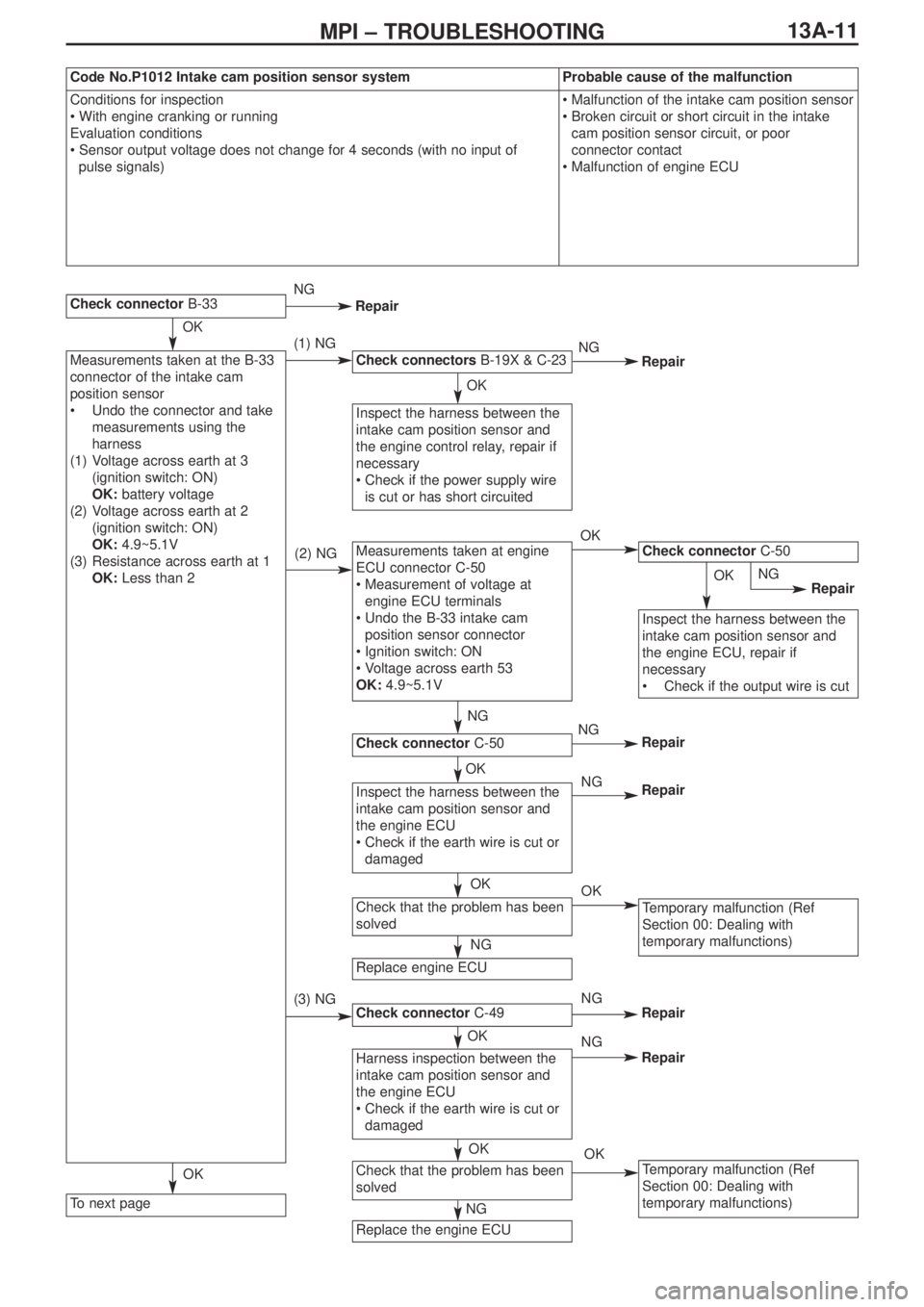
13A-11MPI – TROUBLESHOOTING
Check connectorB-33
To next page
Check connectorsB-19X & C-23
Inspect the harness between the
intake cam position sensor and
the engine control relay, repair if
necessary
•Check if the power supply wire
is cut or has short circuited
Measurements taken at engine
ECU connector C-50
•Measurement of voltage at
engine ECU terminals
•Undo the B-33 intake cam
position sensor connector
•Ignition switch: ON
•Voltage across earth 53
OK:4.9~5.1V
Check connectorC-50
Check connectorC-49
Inspect the harness between the
intake cam position sensor and
the engine ECU
•Check if the earth wire is cut or
damaged
Harness inspection between the
intake cam position sensor and
the engine ECU
•Check if the earth wire is cut or
damaged
Replace the engine ECU
Replace engine ECU
Check that the problem has been
solved
Check that the problem has been
solved
Check connector C-50
Inspect the harness between the
intake cam position sensor and
the engine ECU, repair if
necessary
•Check if the output wire is cut
Temporary malfunction (Ref
Section 00: Dealing with
temporary malfunctions)
Temporary malfunction (Ref
Section 00: Dealing with
temporary malfunctions)
Measurements taken at the B-33
connector of the intake cam
position sensor
•Undo the connector and take
measurements using the
harness
(1) Voltage across earth at 3
(ignition switch: ON)
OK:battery voltage
(2) Voltage across earth at 2
(ignition switch: ON)
OK:4.9~5.1V
(3) Resistance across earth at 1
OK:Less than 2Ω
Code No.P1012 Intake cam position sensor systemProbable cause of the malfunction
Conditions for inspection
• With engine cranking or running
Evaluation conditions
• Sensor output voltage does not change for 4 seconds (with no input of
pulse signals)•Malfunction of the intake cam position sensor
•Broken circuit or short circuit in the intake
cam position sensor circuit, or poor
connector contact
•Malfunction of engine ECU
OK
OK
NG
(1) NG
(2) NG
(3) NG
OK
NG
NG
OK
OK
OK
NG
NG
NG
OK
NG
OK OK
NG
NG
OK
OKNG
Repair
Repair
Repair
Repair
Repair
Repair
Repair
Page 52 of 364

13A-12MPI – TROUBLESHOOTING
Continued from the previous page
Check connectors B-19X & C-23
Check the intake cam position
sensing cylinder
Check that the problem has been
solved
Replace the intake cam position
sensor
Temporary malfunction (Ref
Section 00: Dealing with
temporary malfunctions)
Replace the intake cam position
sensing cylinder
Temporary malfunction (Ref
Section 00: Dealing with
temporary malfunctions)
Inspect the harness between the
intake cam position sensor and
the engine ECU
•Check if the output wire is
damaged
Inspect the harness between the
intake cam position sensor and
the engine control relay
•Check if the power wire is
damaged
Measurement of the output wave
at the intake cam position
sensor connector B-33 (using an
oscilloscope)
•Use test harness (MB991709),
connect it to the connector, and
take measurements at the pick-
up harness component
•Engine: idling
•Voltage across earth at 2
OK:An output wave as described
on P.13A-25 (Main points for
oscilloscope testing) is
produced, with the maximum
value in excess of 4.8V and
the minimum value less than
0.6V. There should be no
noise in the output wave form.
Replace engine ECU
Check that the problem has been
solved
Check connectorsC-49 & C-50
OK
OKOK
NG
NG
OK
OK
OK
OK
OK
NG
NG
Repair
NG
Repair
NG
Repair
NG
NG
OK
Repair
Page 53 of 364
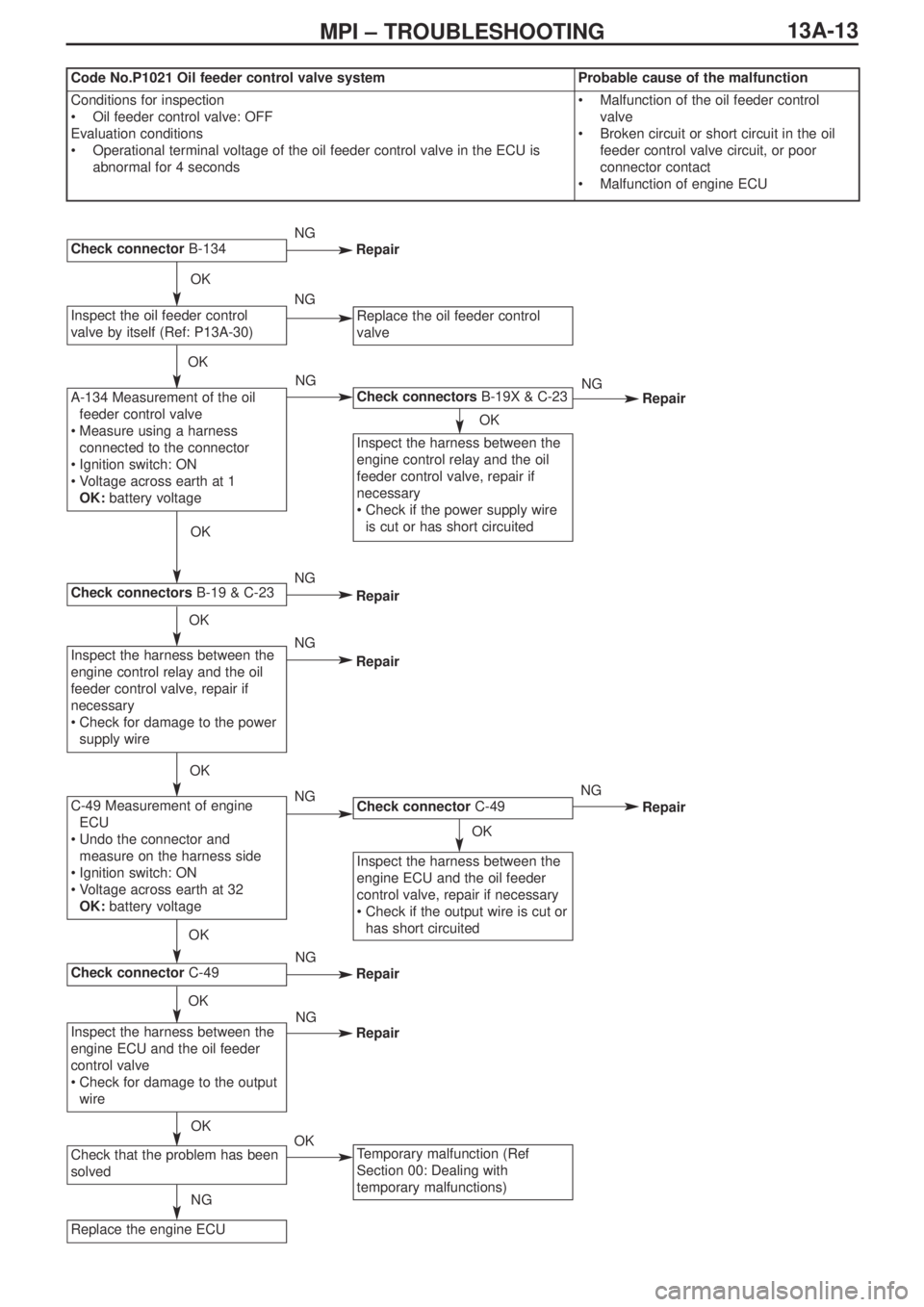
13A-13MPI – TROUBLESHOOTING
Replace the engine ECU
Check connectors B-19X & C-23
Check connector B-134
Check connectors B-19 & C-23
Check connector C-49
Check that the problem has been
solved
Inspect the oil feeder control
valve by itself (Ref: P13A-30)
Inspect the harness between the
engine control relay and the oil
feeder control valve, repair if
necessary
•Check for damage to the power
supply wire
Inspect the harness between the
engine control relay and the oil
feeder control valve, repair if
necessary
•Check if the power supply wire
is cut or has short circuited
Check connectorC-49
Inspect the harness between the
engine ECU and the oil feeder
control valve, repair if necessary
•Check if the output wire is cut or
has short circuited
Temporary malfunction (Ref
Section 00: Dealing with
temporary malfunctions)
Replace the oil feeder control
valve
A-134 Measurement of the oil
feeder control valve
•Measure using a harness
connected to the connector
•Ignition switch: ON
•Voltage across earth at 1
OK:battery voltage
C-49 Measurement of engine
ECU
•Undo the connector and
measure on the harness side
•Ignition switch: ON
•Voltage across earth at 32
OK:battery voltage
Inspect the harness between the
engine ECU and the oil feeder
control valve
•Check for damage to the output
wire
OK
NG
OKOK
OK
OK
OK
OK
OK
OK
NG
NG
NG
NG
NG
NG
NG
NG
NG
NG
OK
OK
Repair
Repair
Repair
Repair
Repair
Repair
Repair
Code No.P1021 Oil feeder control valve systemProbable cause of the malfunction
Conditions for inspection
•Oil feeder control valve: OFF
Evaluation conditions
•Operational terminal voltage of the oil feeder control valve in the ECU is
abnormal for 4 seconds•Malfunction of the oil feeder control
valve
•Broken circuit or short circuit in the oil
feeder control valve circuit, or poor
connector contact
•Malfunction of engine ECU
Page 59 of 364
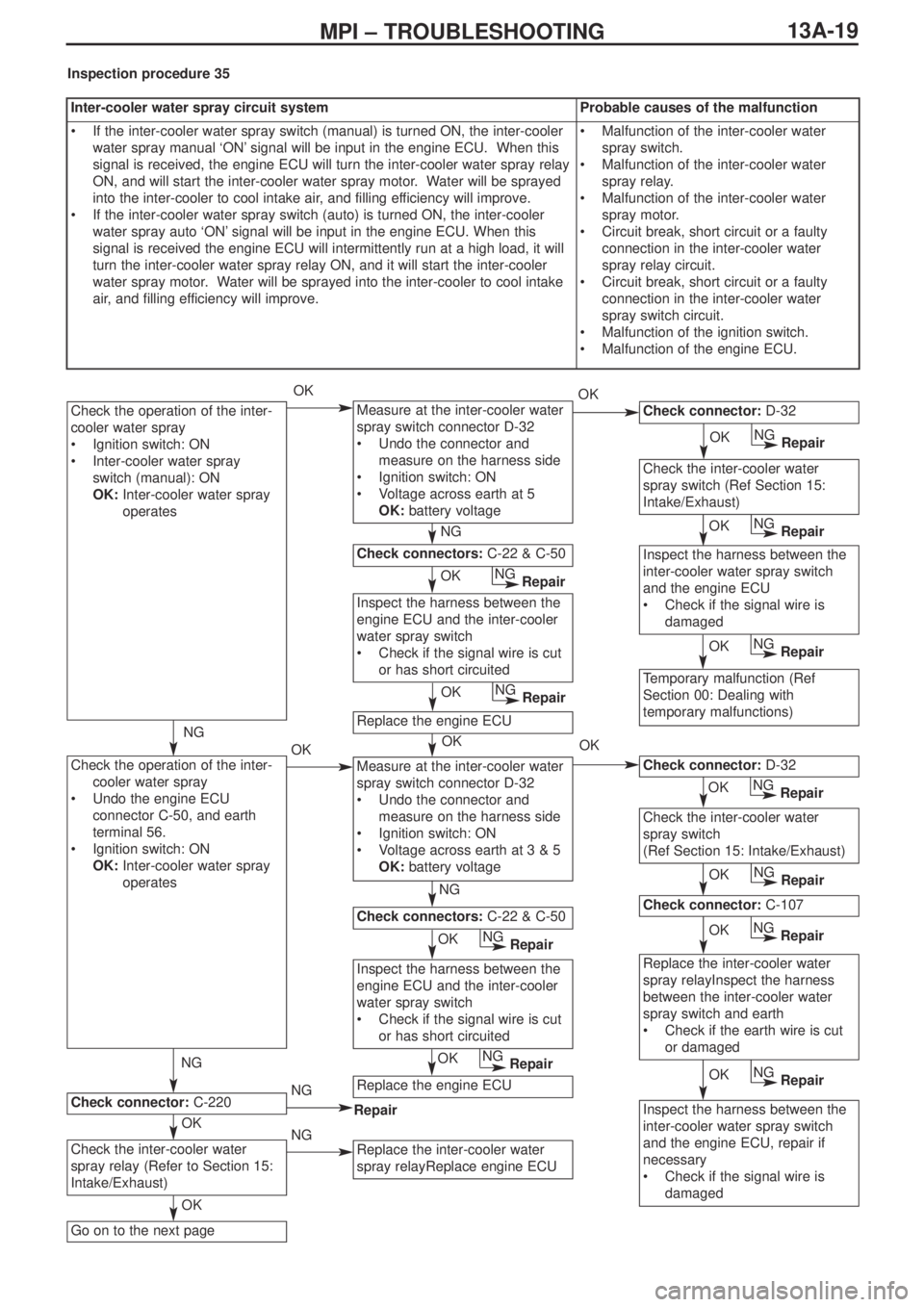
13A-19MPI – TROUBLESHOOTING
Check the operation of the inter-
cooler water spray
•Ignition switch: ON
•Inter-cooler water spray
switch (manual): ON
OK:Inter-cooler water spray
operates
Check the operation of the inter-
cooler water spray
•Undo the engine ECU
connector C-50, and earth
terminal 56.
•Ignition switch: ON
OK:Inter-cooler water spray
operates
Check connector:C-220
Check the inter-cooler water
spray relay (Refer to Section 15:
Intake/Exhaust)
Go on to the next page
Measure at the inter-cooler water
spray switch connector D-32
•Undo the connector and
measure on the harness side
•Ignition switch: ON
•Voltage across earth at 5
OK:battery voltage
Check connectors: C-22 & C-50
Check connector: D-32
Inspect the harness between the
engine ECU and the inter-cooler
water spray switch
•Check if the signal wire is cut
or has short circuited
Replace the engine ECU
Check connectors: C-22 & C-50
Measure at the inter-cooler water
spray switch connector D-32
•Undo the connector and
measure on the harness side
•Ignition switch: ON
•Voltage across earth at 3 & 5
OK:battery voltage
Replace the inter-cooler water
spray relayReplace engine ECU
Check the inter-cooler water
spray switch (Ref Section 15:
Intake/Exhaust)
Inspect the harness between the
inter-cooler water spray switch
and the engine ECU
•Check if the signal wire is
damaged
Temporary malfunction (Ref
Section 00: Dealing with
temporary malfunctions)
Check connector:D-32
Check the inter-cooler water
spray switch
(Ref Section 15: Intake/Exhaust)
Check connector:C-107
Replace the inter-cooler water
spray relayInspect the harness
between the inter-cooler water
spray switch and earth
•Check if the earth wire is cut
or damaged
Inspect the harness between the
inter-cooler water spray switch
and the engine ECU, repair if
necessary
•Check if the signal wire is
damaged
Inspect the harness between the
engine ECU and the inter-cooler
water spray switch
•Check if the signal wire is cut
or has short circuited
OK
NG
NG
OK
NG
NG
OK
OK
OK
OK
NG
OK
OK
NG
NG
Repair
Inspection procedure 35
Inter-cooler water spray circuit systemProbable causes of the malfunction
•If the inter-cooler water spray switch (manual) is turned ON, the inter-cooler
water spray manual ‘ON’ signal will be input in the engine ECU. When this
signal is received, the engine ECU will turn the inter-cooler water spray relay
ON, and will start the inter-cooler water spray motor. Water will be sprayed
into the inter-cooler to cool intake air, and filling efficiency will improve.
•If the inter-cooler water spray switch (auto) is turned ON, the inter-cooler
water spray auto ‘ON’ signal will be input in the engine ECU. When this
signal is received the engine ECU will intermittently run at a high load, it will
turn the inter-cooler water spray relay ON, and it will start the inter-cooler
water spray motor. Water will be sprayed into the inter-cooler to cool intake
air, and filling efficiency will improve.•Malfunction of the inter-cooler water
spray switch.
•Malfunction of the inter-cooler water
spray relay.
•Malfunction of the inter-cooler water
spray motor.
•Circuit break, short circuit or a faulty
connection in the inter-cooler water
spray relay circuit.
•Circuit break, short circuit or a faulty
connection in the inter-cooler water
spray switch circuit.
•Malfunction of the ignition switch.
•Malfunction of the engine ECU.
Replace the engine ECU
OKNGRepair
OKNGRepair
OKNGRepair
OKNGRepair
OKNGRepair
OKNGRepair
OKNGRepair
OKNGRepair
OKNGRepair
OKNGRepair
Repair
Page 60 of 364
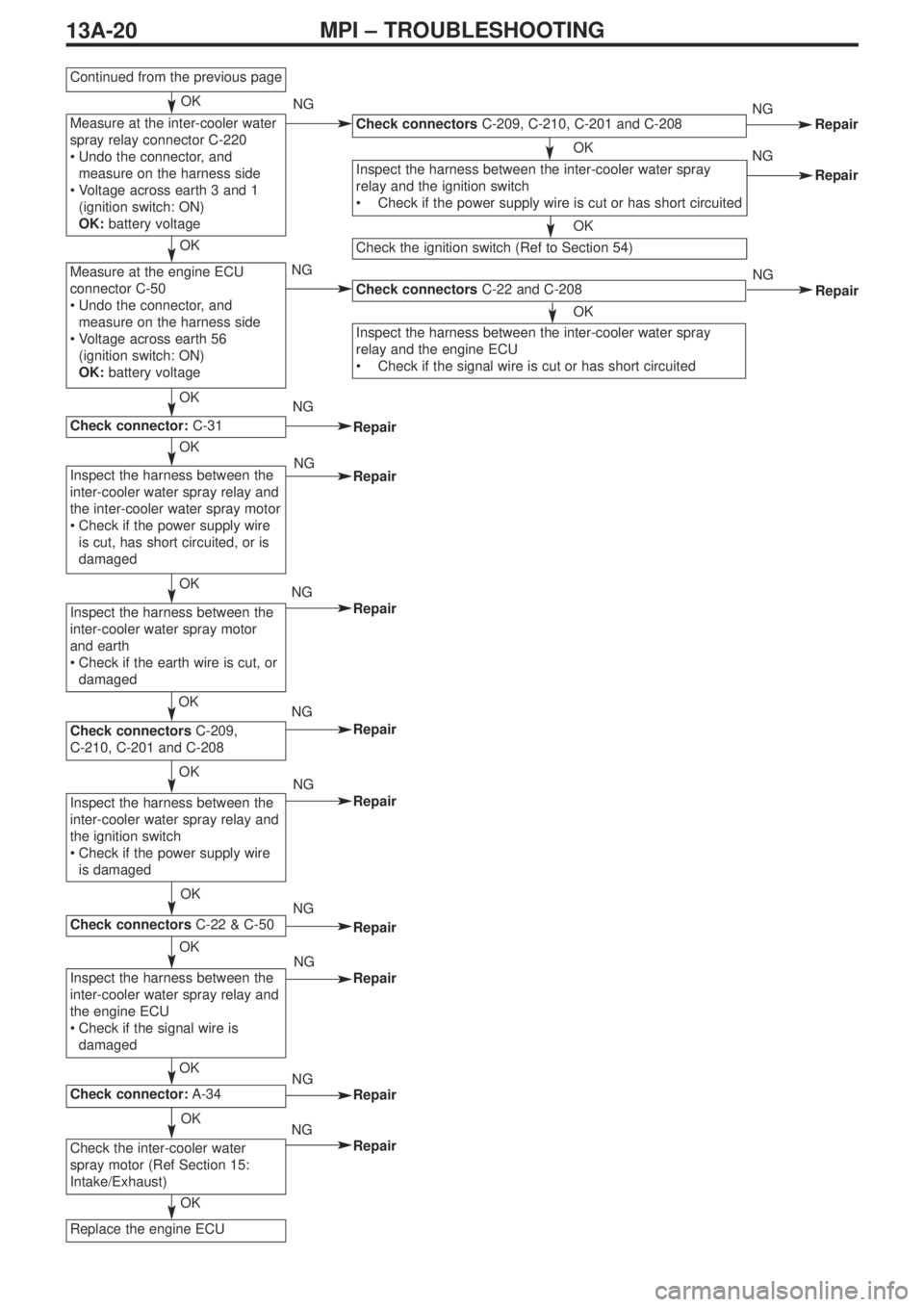
13A-20MPI – TROUBLESHOOTING
Measure at the inter-cooler water
spray relay connector C-220
•Undo the connector, and
measure on the harness side
•Voltage across earth 3 and 1
(ignition switch: ON)
OK:battery voltage
Measure at the engine ECU
connector C-50
•Undo the connector, and
measure on the harness side
•Voltage across earth 56
(ignition switch: ON)
OK:battery voltage
Check connector:C-31
Inspect the harness between the
inter-cooler water spray relay and
the inter-cooler water spray motor
•Check if the power supply wire
is cut, has short circuited, or is
damaged
Inspect the harness between the
inter-cooler water spray motor
and earth
•Check if the earth wire is cut, or
damaged
Check connectors C-209,
C-210, C-201 and C-208
Inspect the harness between the
inter-cooler water spray relay and
the ignition switch
•Check if the power supply wire
is damaged
Check connectors C-22 & C-50
Inspect the harness between the
inter-cooler water spray relay and
the engine ECU
•Check if the signal wire is
damaged
Check connector:A-34
Replace the engine ECU
Check the inter-cooler water
spray motor (Ref Section 15:
Intake/Exhaust)
Check connectorsC-209, C-210, C-201 and C-208
Inspect the harness between the inter-cooler water spray
relay and the ignition switch
•Check if the power supply wire is cut or has short circuited
Continued from the previous page
Check the ignition switch (Ref to Section 54)
Check connectorsC-22 and C-208
Inspect the harness between the inter-cooler water spray
relay and the engine ECU
•Check if the signal wire is cut or has short circuited
OK
OK
OK
OK
OK
OK
OK
OK
OK
OK
OK
OK
OK
OK
OK
NGNG
NG
NGNG
NG
NG
NG
NG
NG
NG
NG
NG
NG
Repair
Repair
Repair
Repair
Repair
Repair
Repair
Repair
Repair
Repair
Repair
Repair
Page 61 of 364
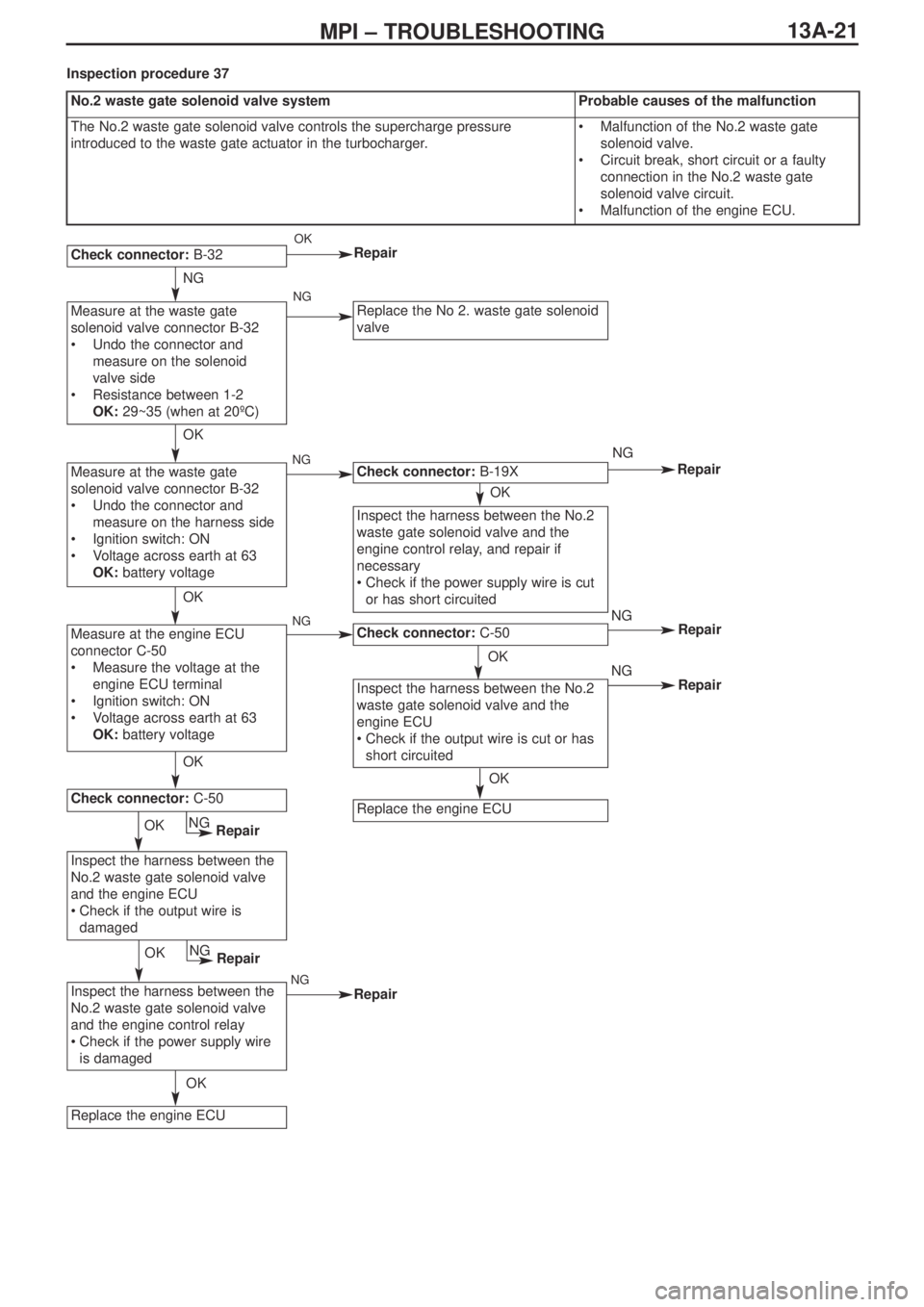
13A-21MPI – TROUBLESHOOTING
Check connector: B-32
Replace the No 2. waste gate solenoid
valve
Check connector:B-19X
Measure at the waste gate
solenoid valve connector B-32
•Undo the connector and
measure on the solenoid
valve side
•Resistance between 1-2
OK:29~35Ω(when at 20ºC)
Measure at the waste gate
solenoid valve connector B-32
•Undo the connector and
measure on the harness side
•Ignition switch: ON
•Voltage across earth at 63
OK:battery voltage
Measure at the engine ECU
connector C-50
•Measure the voltage at the
engine ECU terminal
•Ignition switch: ON
•Voltage across earth at 63
OK:battery voltage
Check connector:C-50
Inspect the harness between the
No.2 waste gate solenoid valve
and the engine ECU
•Check if the output wire is
damaged
Inspect the harness between the
No.2 waste gate solenoid valve
and the engine control relay
•Check if the power supply wire
is damaged
Replace the engine ECU
Inspect the harness between the No.2
waste gate solenoid valve and the
engine control relay, and repair if
necessary
•Check if the power supply wire is cut
or has short circuited
Check connector:C-50
Inspect the harness between the No.2
waste gate solenoid valve and the
engine ECU
•Check if the output wire is cut or has
short circuited
Replace the engine ECU
NG
OK
OK
OK
OK
OK
NG
NG
NG
NG
Repair
Repair
OK
OK
NG
NG
OK
Repair
NGRepair
Repair
No.2 waste gate solenoid valve systemProbable causes of the malfunction
The No.2 waste gate solenoid valve controls the supercharge pressure
introduced to the waste gate actuator in the turbocharger.•Malfunction of the No.2 waste gate
solenoid valve.
•Circuit break, short circuit or a faulty
connection in the No.2 waste gate
solenoid valve circuit.
•Malfunction of the engine ECU.
OKNGRepair
OKNGRepair
Inspection procedure 37
Page 142 of 364
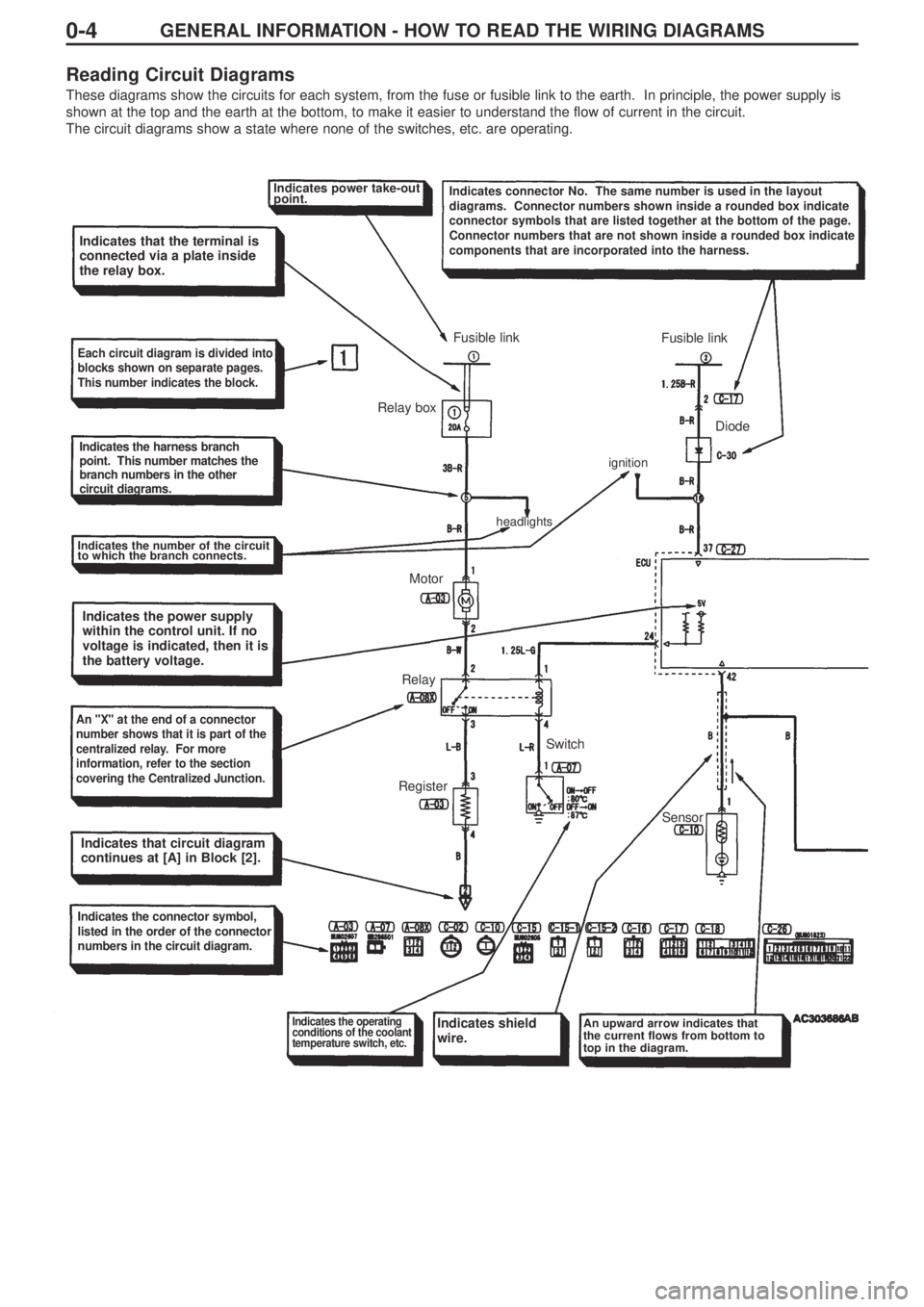
GENERAL INFORMATION - HOW TO READ THE WIRING DIAGRAMS0-4
Reading Circuit Diagrams
These diagrams show the circuits for each system, from the fuse or fusible link to the earth. In principle, the power supply is
shown at the top and the earth at the bottom, to make it easier to understand the flow of current in the circuit.
The circuit diagrams show a state where none of the switches, etc. are operating.
Indicates power take-out
point.Indicates connector No. The same number is used in the layout
diagrams. Connector numbers shown inside a rounded box indicate
connector symbols that are listed together at the bottom of the page.
Connector numbers that are not shown inside a rounded box indicate
components that are incorporated into the harness.
Indicates that the terminal is
connected via a plate inside
the relay box.
Each circuit diagram is divided into
blocks shown on separate pages.
This number indicates the block.
Indicates the harness branch
point. This number matches the
branch numbers in the other
circuit diagrams.
Indicates the number of the circuit
to which the branch connects.
Indicates the power supply
within the control unit. If no
voltage is indicated, then it is
the battery voltage.
An "X" at the end of a connector
number shows that it is part of the
centralized relay. For more
information, refer to the section
covering the Centralized Junction.
Indicates that circuit diagram
continues at [A] in Block [2].
Indicates the connector symbol,
listed in the order of the connector
numbers in the circuit diagram.
Indicates the operating
conditions of the coolant
temperature switch, etc.Indicates shield
wire.An upward arrow indicates that
the current flows from bottom to
top in the diagram.
RegisterRelayMotor Relay boxFusible link
Fusible link
Diode
Sensor Switch
headlightsignition