check engine MITSUBISHI MONTERO 1987 1.G Owner's Manual
[x] Cancel search | Manufacturer: MITSUBISHI, Model Year: 1987, Model line: MONTERO, Model: MITSUBISHI MONTERO 1987 1.GPages: 284, PDF Size: 14.74 MB
Page 266 of 284
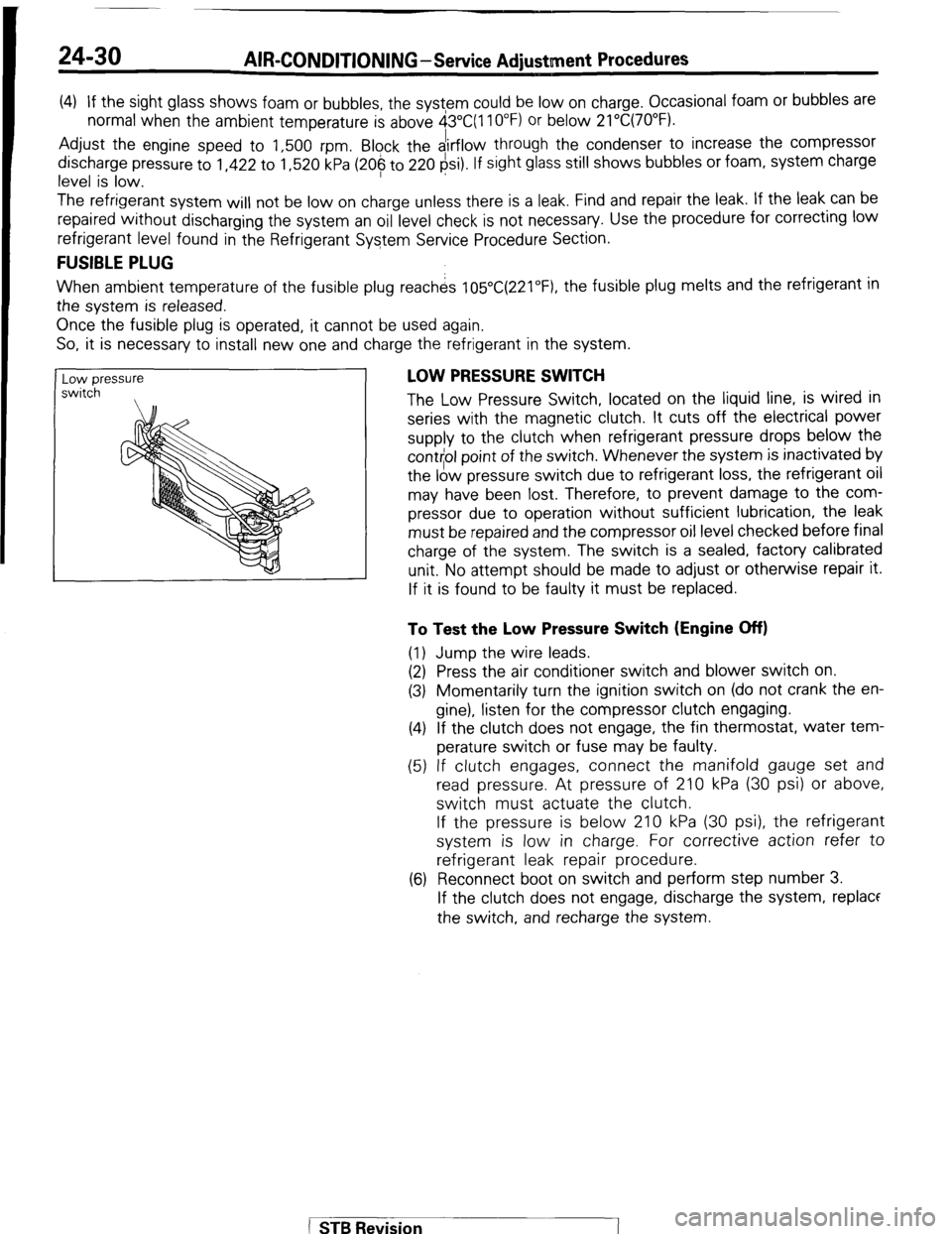
24-30 AIR-CONDITIONING -Service Adjustunent Procedures
(4) If the sight glass shows foam or bubbles, the systpm could be low on charge. Occasional foam or bubbles are
normal when the ambient temperature is above 43”C(110”F) or below 21”C(7O”F).
Adjust the engine speed to 1,500 rpm. Block the airflow through the condenser to increase the compressor
discharge pressure to 1,422 to 1,520 kPa (20$ to 220 dsi). If sight glass still shows bubbles or foam, system charge
level is low.
The refrigerant system will not be low on charge unless there is a leak. Find and repair the leak. If the leak can be
repaired without discharging the system an oil level check is not necessary. Use the procedure for correcting low
refrigerant level found in the Refrigerant Sy$em Service Procedure Section.
FUSIBLE PLUG
When ambient temperature of the fusible plug reach& 105~221~F), the fusible plug melts and the refrigerant in
the system is released.
Once the fusible plug is operated, it cannot be used again.
SO, it is necessary to install new one and charge the refrigerant in the system.
Low pressure
switch , LOW PRESSURE SWITCH
The Low Pressure Switch, located on the liquid line, is wired in
series with the magnetic clutch. It cuts off the electrical power
supply to the clutch when refrigerant pressure drops below the
cont$ol point of the switch. Whenever the system is inactivated by
the low pressure switch due to refrigerant loss, the refrigerant oil
may have been lost. Therefore, to prevent damage to the com-
pressor due to operation without sufficient lubrication, the leak
must be repaired and the compressor oil level checked before final
charge of the system. The switch is a sealed, factory calibrated
unit. No attempt should be made to adjust or otherwise repair it.
If it is found to be faulty it must be replaced.
To Test the Low Pressure Switch (Engine Off)
(1) Jump the wire leads.
(2) Press the air conditioner switch and blower switch on.
(3) Momentarily turn the ignition switch on (do not crank the en-
gine), listen for the compressor clutch engaging.
(4) If the clutch does not engage, the fin thermostat, water tem-
perature switch or fuse may be faulty.
(5) If clutch engages, connect the manifold gauge set and
read pressure. At pressure of 210 kPa (30 psi) or above,
switch must actuate the clutch.
If the pressure is below 210 kPa (30 psi), the refrigerant
system is low in charge. For corrective action refer to
refrigerant leak repair procedure.
(6) Reconnect boot on switch and perform step number 3.
If the clutch does not engage, discharge the system, replace
the switch, and recharge the system.
[
STB Revision
Page 267 of 284
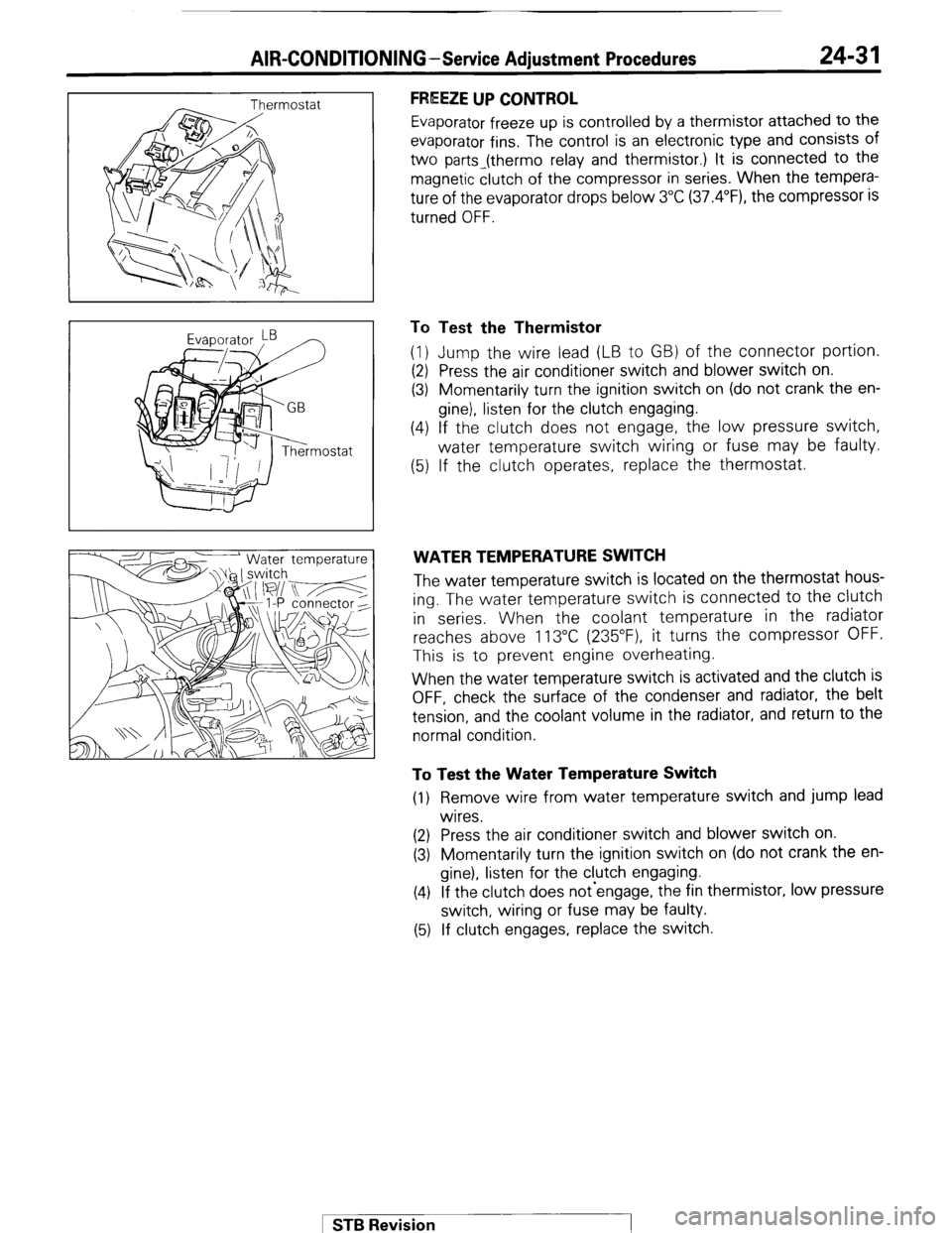
AIR-CONDITIONING-Service Adiustment Procedures 24-31
FREEZE UP CONTROL
Evaporator freeze up is controlled by a thermistor attached to the
evaporator fins. The control is an electronic type and consists of
two parts_(thermo relay and thermistor.) It is connected to the
magnetic clutch of the compressor in series. When the tempera-
ture of the evaporator drops below 3°C (37.4”F), the compressor is
turned OFF.
To Test the Thermistor
(1) Jump the wire lead (LB to GB) of the connector portion.
(2) Press the air conditioner switch and blower switch on.
(3) Momentarily turn the ignition switch on (do not crank the en-
gine), listen for the clutch engaging.
(4) If the clutch does not engage, the low pressure switch,
water temperature switch wiring or fuse may be faulty.
(5) If the clutch operates, replace the thermostat.
WATER TEMPERATURE SWITCH
The water temperature switch is located on the thermostat hous-
ing. The water temperature switch is connected to the clutch
in series. When the coolant temperature in the radiator
reaches above 113°C (235”F), it turns the compressor OFF.
This is to prevent engine overheating.
When the water temperature switch is activated and the clutch is
OFF, check the surface of the condenser and radiator, the belt
tension, and the coolant volume in the radiator, and return to the
normal condition.
To Test the Water Temperature Switch
(1) Remove wire from water temperature switch and jump lead
wires.
(2) Press the air conditioner switch and blower switch on.
(3) Momentarily turn the ignition switch on (do not crank the en-
gine), listen for the clutch engaging.
(4) If the clutch does not-engage, the fin thermistor, low pressure
switch, wiring or fuse may be faulty.
(5) If clutch engages, replace the switch.
1 STB Revision
Page 270 of 284
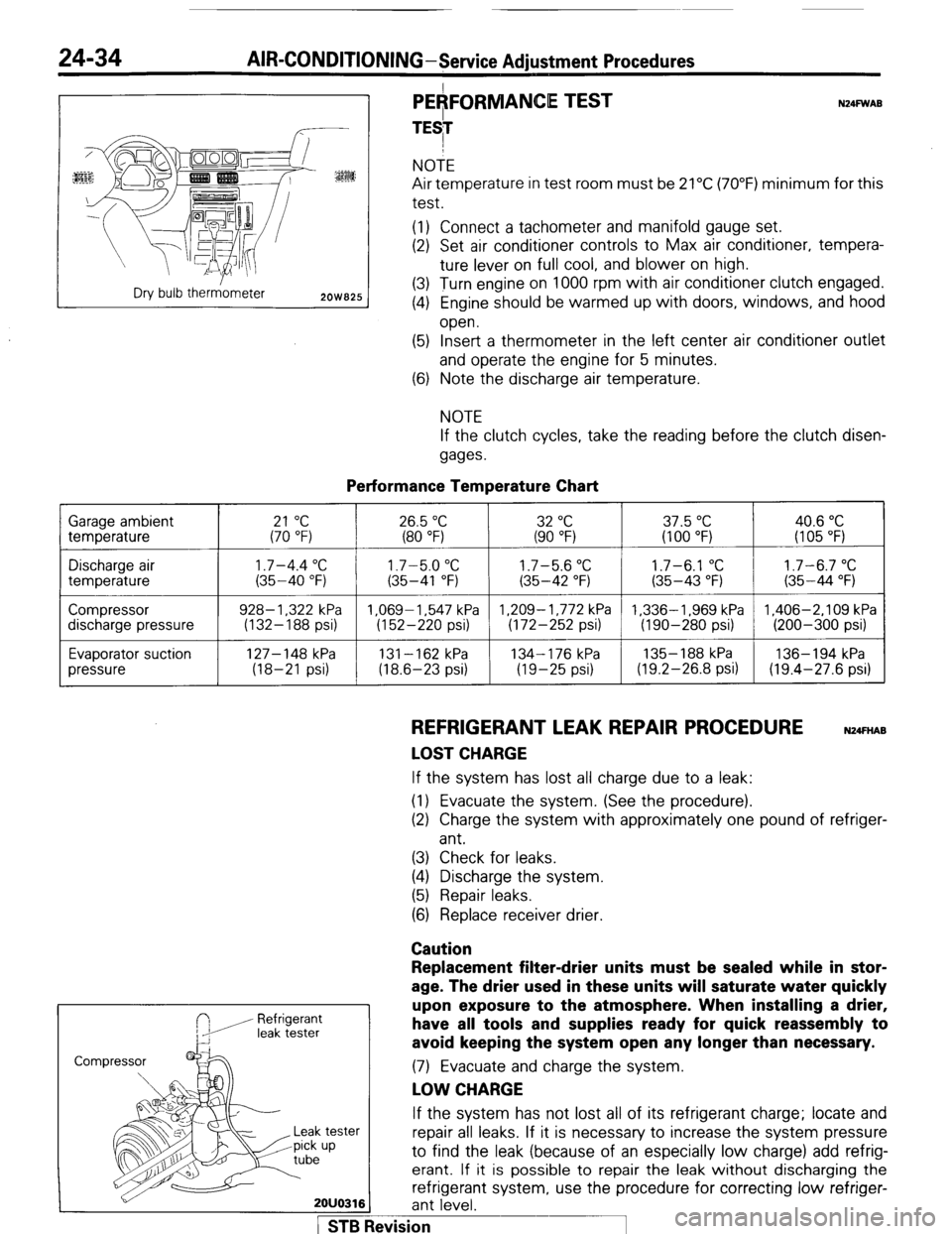
24-34 AIR-CONDITIONING-Service Adiustment Procedures
r---- :
:ES
Dry bulb therr&neter
2OW825
PEAFORMANCE TEST
TESI N24FWAB NOTE
Air temperature in test room must be 21°C (70°F) minimum for this
test.
(1) Connect a tachometer and manifold gauge set.
(2) Set air conditioner controls to Max air conditioner, tempera-
ture lever on full cool, and blower on high.
(3) Turn engine on 1000 rpm with air conditioner clutch engaged.
(4) Engine should be warmed up with doors, windows, and hood
open.
(5) Insert a thermometer in the left center air conditioner outlet
and operate the engine for 5 minutes.
(6) Note the discharge air temperature.
NOTE
If the clutch cycles, take the reading before the clutch disen-
gages.
Performance Temperature Chart Garage ambient
temperature
21 “C 26.5 “C 32 “C 37.5 “C 40.6 “C (70 “F) (80 “F) (90 “F) (100 “F) (I 05 “F)
Discharge air
temperature
Compressor
discharge pressure
Evaporator suction
pressure
1.7-4.4 “C 1.7-5.0 “C 1.7-5.6 “C 1.7-6.1 “C 1.7-6.7 “C (35-40 “F) (35-41 “F) (35-42 “F) (35-43 “F) (35-44 “F)
928- 1,322 kPa 1.069-1.547 kPa 1,209-1,772 kPa 1,336-1,969 kPa 1,406-2,109 kPa
(132-188 psi) (152-220 psi) (172-252 psi) (190-280 psi) (200-300 psi)
127-148 kPa
131-162 kPa 134-176 kPa 135- 188 kPa 136-194 kPa
(18-21 psi) (18.6-23 psi) (19-25 psi) (19.2-26.8 psi) (19.4-27.6 psi)
REFRIGERANT LEAK REPAIR PROCEDURE N24FnAB
LOST CHARGE If the system has lost all charge due to a leak:
(1) Evacuate the system. (See the procedure).
(2) Charge the system with approximately one pound of refriger-
ant.
(3) Check for leaks.
(4) Discharge the system.
(5) Repair leaks.
(6) Replace receiver drier.
Caution
Refrigerant
leak tester
Replacement filter-drier units must be sealed while in stor-
age. The drier used in these units will saturate water quickly
upon exposure to the atmosphere. When installing a drier,
have all tools and supplies ready for quick reassembly to
avoid keeping the system open any longer than necessary. (7) Evacuate and charge the system.
LOW CHARGE If the system has not lost all of its refrigerant charge; locate and
tester repair all leaks. If it is necessary to increase the system pressure
up to find the leak (because of an especially low charge) add refrig-
erant. If it is possible to repair the leak without discharging the
refrigerant system, use the procedure for correcting low refriger-
2OUO316 ant level.
1 STB Revision
Page 277 of 284
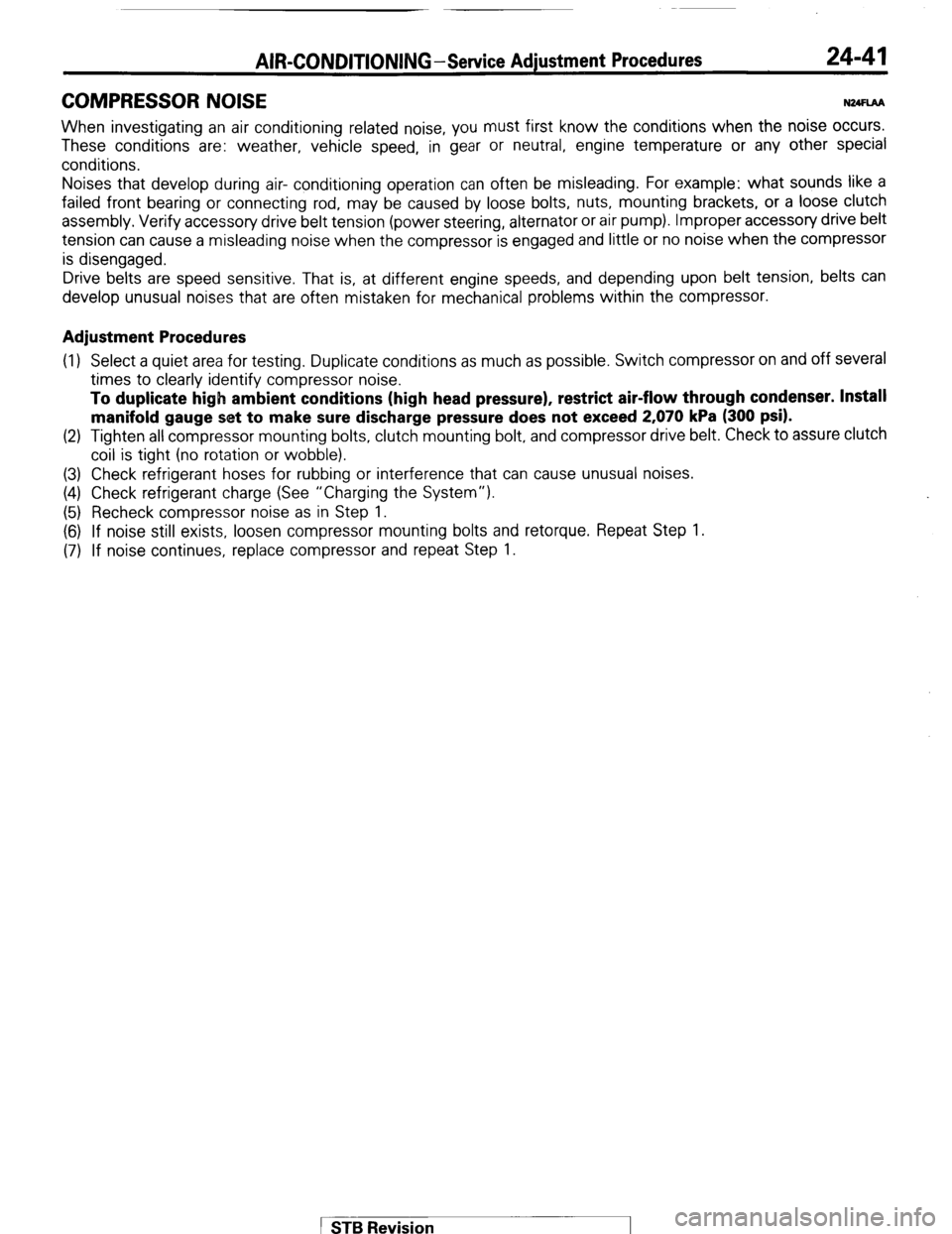
AIR-CONDITIONING -Service Adjustment Procedures 24-41
COMPRESSOR NOISE NWLM
When investigating an air conditioning related noise, you must first know the conditions when the noise occurs.
These conditions are: weather, vehicle speed, in gear or neutral, engine temperature or any other special
conditions.
Noises that develop during air- conditioning operation can often be misleading. For example: what sounds like a
failed front bearing or connecting rod, may be caused by loose bolts, nuts, mounting brackets, or a loose clutch
assembly. Verify accessory drive belt tension (power
steering, alternator or air pump). Improper accessory drive belt
tension can cause a misleading noise when the compressor is engaged and little or no noise when the compressor
is disengaged.
Drive belts are speed sensitive. That is, at different engine speeds, and depending upon belt tension, belts can
develop unusual noises that are often mistaken for mechanical problems within the compressor.
Adjustment Procedures
(1) Select a quiet area for testing. Duplicate conditions as much as possible. Switch compressor on and off several
times to clearly identify compressor noise.
To duplicate high ambient conditions (high head pressure), restrict air-flow through
condenser. Install
manifold gauge set to make sure discharge pressure does not exceed 2,070 kPa (300 psi).
(2) Tighten all compressor mounting bolts, clutch mounting bolt, and compressor drive belt. Check to assure clutch
coil is tight (no rotation or wobble).
(3) Check refrigerant hoses for rubbing or interference that can cause unusual noises.
(4) Check refrigerant charge (See “Charging the System”).
(5) Recheck compressor noise as in Step 1.
(6) If noise still exists, loosen compressor mounting bolts and retorque. Repeat Step 1.
(7) If noise continues, replace compressor and repeat Step 1.
1 STB Revision