service MITSUBISHI MONTERO 1987 1.G Manual Online
[x] Cancel search | Manufacturer: MITSUBISHI, Model Year: 1987, Model line: MONTERO, Model: MITSUBISHI MONTERO 1987 1.GPages: 284, PDF Size: 14.74 MB
Page 265 of 284
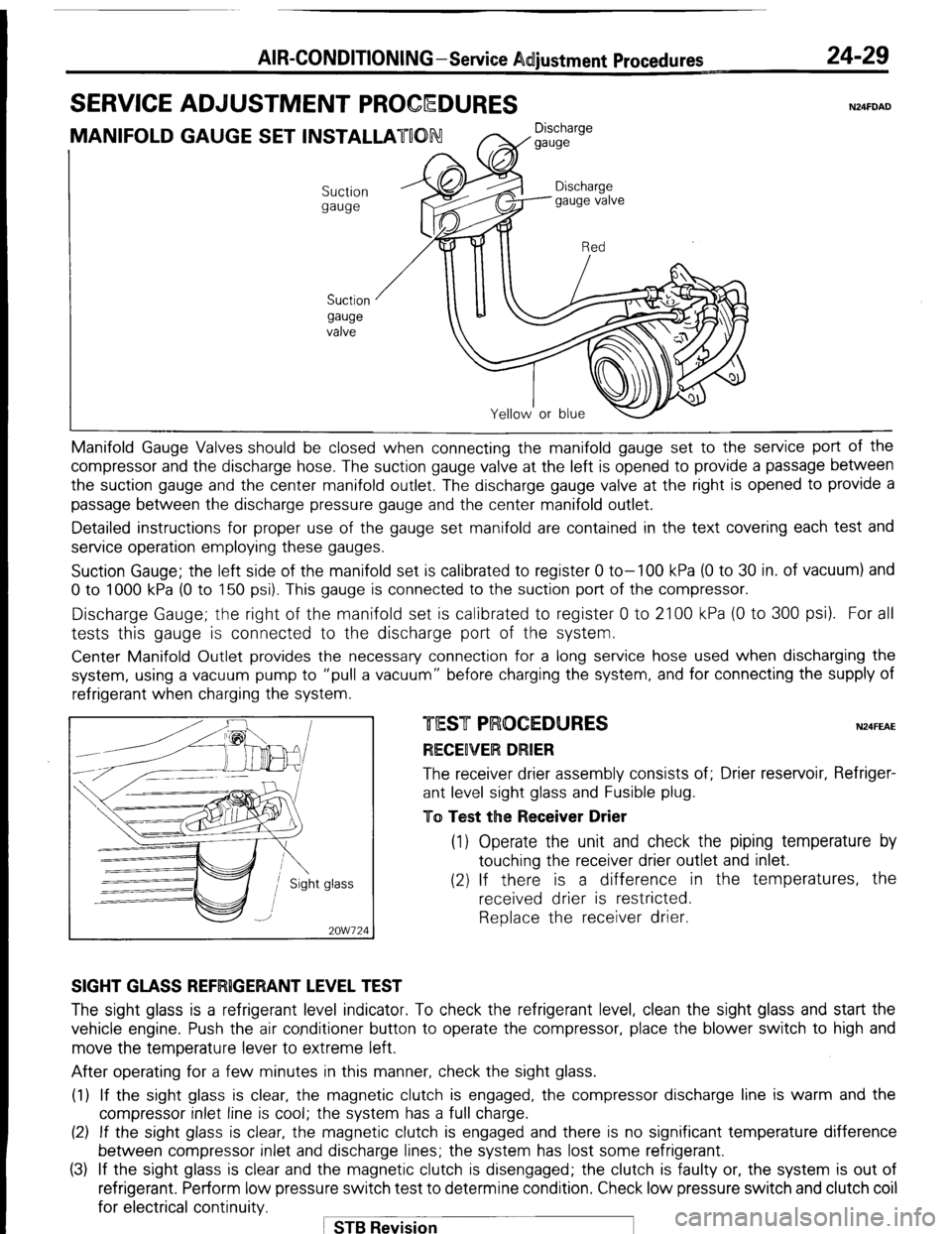
AIR-CONDITIONING-Service Adjustment Procedures
SERVICE ADJUSTMENT PROCQDURES 24-29 N24FDAD
MANIFOLD GAUGE SET INSTALLATUON Discharge
W gauge
Suction
gauge
Suction
gauge
valve Manifold Gauge Valves should be closed
when connecting the manifold gauge set to the service port of the
compressor and the discharge hose. The suction gauge valve at the left is opened to provide a passage between
the suction gauge and the center manifold outlet. The discharge gauge valve at the right is opened to provide a
passage between the discharge pressure gauge and the center manifold outlet.
Detailed instructions for proper use of the gauge set manifold are contained in the text covering each test and
service operation employing these gauges.
Suction Gauge; the left side of the manifold set is calibrated to register 0 to-100 kPa (0 to 30 in. of vacuum) and
0 to 1000 kPa (0 to 150 psi). This gauge is connected to the suction port of the compressor.
Discharge Gauge; the right of the manifold set is calibrated to register 0 to 2100 kPa (0 to 300 psi). For all
tests this gauge is connected to the discharge port of the system.
Center Manifold Outlet provides the necessary connection for a long service hose used when discharging the
system, using a vacuum pump to “pull a vacuum” before charging the system, and for connecting the supply of
refrigerant when charging the system
glass -
2OW724 N24FEAE The receiver drier assembly consists of; Drier reservoir, Refriger-
ant level sight glass and Fusible plug.
To Test the Receiver Drier (1) Operate the unit and check the piping temperature by
touching the receiver drier outlet and inlet.
(2) If there is a difference in the temperatures, the
received drier is restricted.
Replace the receiver drier.
SIGHT GLASS REFRlGERANT LEVEL TEST The sight glass is a refrigerant level indicator. To check the refrigerant level, clean the sight glass and start the
vehicle engine. Push the air conditioner button to operate the compressor, place the blower switch to high and
move the temperature lever to extreme left.
After operating for a few minutes in this manner, check the sight glass.
(1) If the sight glass is clear, the magnetic clutch is engaged, the compressor discharge line is warm and the
compressor inlet line is cool; the system has a full charge.
(2) If the sight glass is clear, the magnetic clutch is engaged and there is no significant temperature difference
between compressor inlet and discharge lines; the system has lost some refrigerant.
(3) If the sight glass is clear and the magnetic clutch is disengaged; the clutch is faulty or, the system is out of
refrigerant. Perform low pressure switch test to determine condition. Check low pressure switch and clutch coil
for electrical continuity.
1 STB Revision
Page 266 of 284
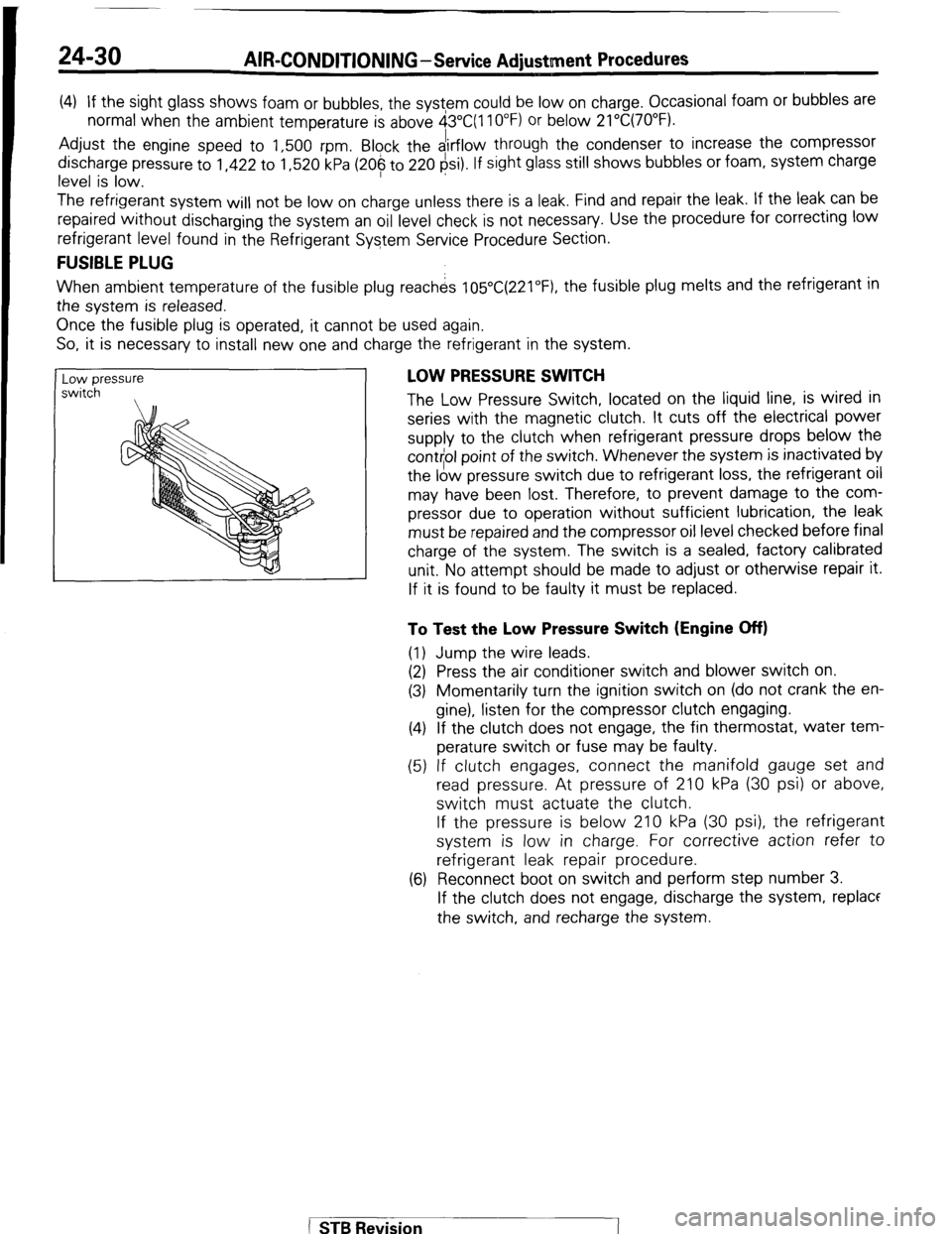
24-30 AIR-CONDITIONING -Service Adjustunent Procedures
(4) If the sight glass shows foam or bubbles, the systpm could be low on charge. Occasional foam or bubbles are
normal when the ambient temperature is above 43”C(110”F) or below 21”C(7O”F).
Adjust the engine speed to 1,500 rpm. Block the airflow through the condenser to increase the compressor
discharge pressure to 1,422 to 1,520 kPa (20$ to 220 dsi). If sight glass still shows bubbles or foam, system charge
level is low.
The refrigerant system will not be low on charge unless there is a leak. Find and repair the leak. If the leak can be
repaired without discharging the system an oil level check is not necessary. Use the procedure for correcting low
refrigerant level found in the Refrigerant Sy$em Service Procedure Section.
FUSIBLE PLUG
When ambient temperature of the fusible plug reach& 105~221~F), the fusible plug melts and the refrigerant in
the system is released.
Once the fusible plug is operated, it cannot be used again.
SO, it is necessary to install new one and charge the refrigerant in the system.
Low pressure
switch , LOW PRESSURE SWITCH
The Low Pressure Switch, located on the liquid line, is wired in
series with the magnetic clutch. It cuts off the electrical power
supply to the clutch when refrigerant pressure drops below the
cont$ol point of the switch. Whenever the system is inactivated by
the low pressure switch due to refrigerant loss, the refrigerant oil
may have been lost. Therefore, to prevent damage to the com-
pressor due to operation without sufficient lubrication, the leak
must be repaired and the compressor oil level checked before final
charge of the system. The switch is a sealed, factory calibrated
unit. No attempt should be made to adjust or otherwise repair it.
If it is found to be faulty it must be replaced.
To Test the Low Pressure Switch (Engine Off)
(1) Jump the wire leads.
(2) Press the air conditioner switch and blower switch on.
(3) Momentarily turn the ignition switch on (do not crank the en-
gine), listen for the compressor clutch engaging.
(4) If the clutch does not engage, the fin thermostat, water tem-
perature switch or fuse may be faulty.
(5) If clutch engages, connect the manifold gauge set and
read pressure. At pressure of 210 kPa (30 psi) or above,
switch must actuate the clutch.
If the pressure is below 210 kPa (30 psi), the refrigerant
system is low in charge. For corrective action refer to
refrigerant leak repair procedure.
(6) Reconnect boot on switch and perform step number 3.
If the clutch does not engage, discharge the system, replace
the switch, and recharge the system.
[
STB Revision
Page 267 of 284
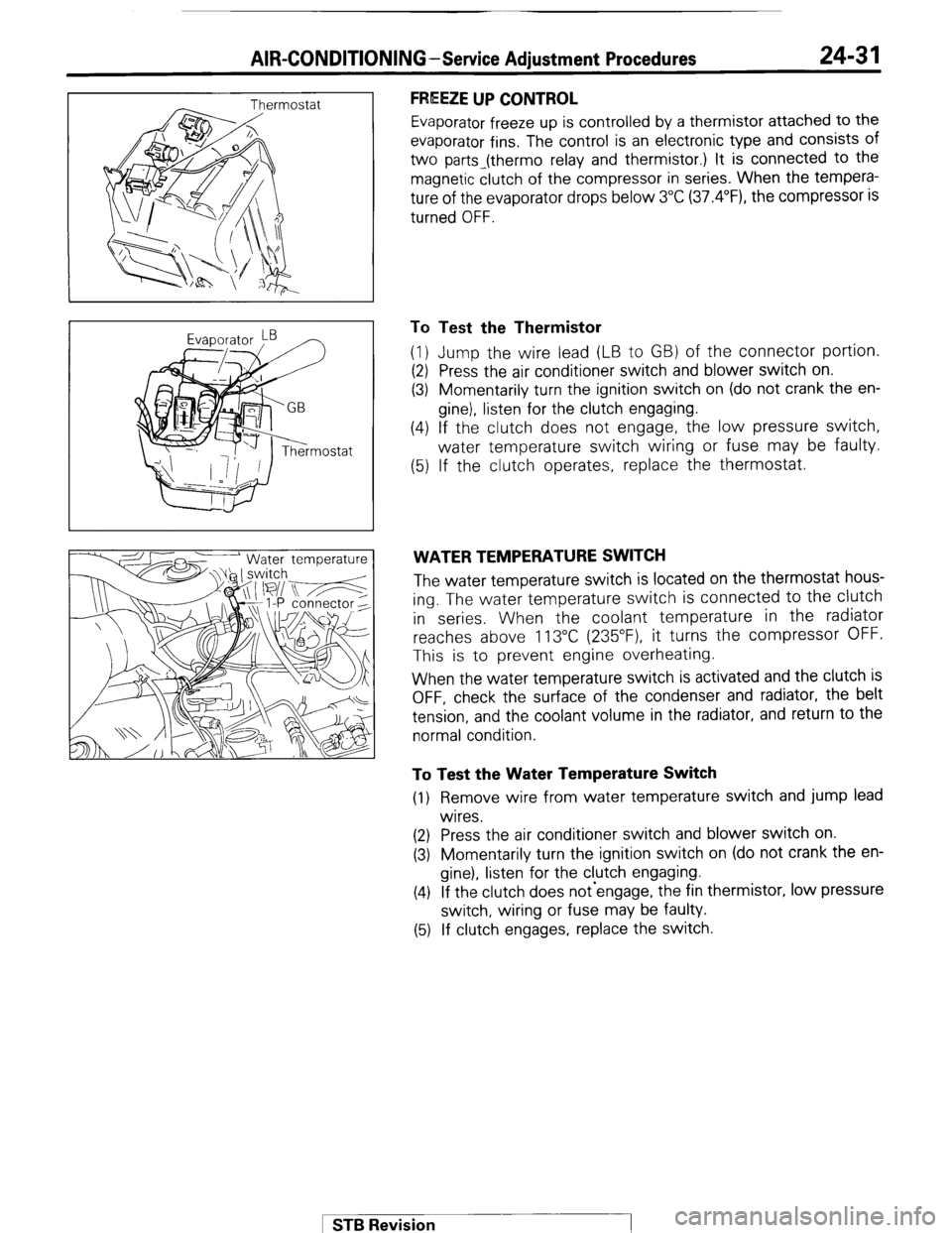
AIR-CONDITIONING-Service Adiustment Procedures 24-31
FREEZE UP CONTROL
Evaporator freeze up is controlled by a thermistor attached to the
evaporator fins. The control is an electronic type and consists of
two parts_(thermo relay and thermistor.) It is connected to the
magnetic clutch of the compressor in series. When the tempera-
ture of the evaporator drops below 3°C (37.4”F), the compressor is
turned OFF.
To Test the Thermistor
(1) Jump the wire lead (LB to GB) of the connector portion.
(2) Press the air conditioner switch and blower switch on.
(3) Momentarily turn the ignition switch on (do not crank the en-
gine), listen for the clutch engaging.
(4) If the clutch does not engage, the low pressure switch,
water temperature switch wiring or fuse may be faulty.
(5) If the clutch operates, replace the thermostat.
WATER TEMPERATURE SWITCH
The water temperature switch is located on the thermostat hous-
ing. The water temperature switch is connected to the clutch
in series. When the coolant temperature in the radiator
reaches above 113°C (235”F), it turns the compressor OFF.
This is to prevent engine overheating.
When the water temperature switch is activated and the clutch is
OFF, check the surface of the condenser and radiator, the belt
tension, and the coolant volume in the radiator, and return to the
normal condition.
To Test the Water Temperature Switch
(1) Remove wire from water temperature switch and jump lead
wires.
(2) Press the air conditioner switch and blower switch on.
(3) Momentarily turn the ignition switch on (do not crank the en-
gine), listen for the clutch engaging.
(4) If the clutch does not-engage, the fin thermistor, low pressure
switch, wiring or fuse may be faulty.
(5) If clutch engages, replace the switch.
1 STB Revision
Page 268 of 284
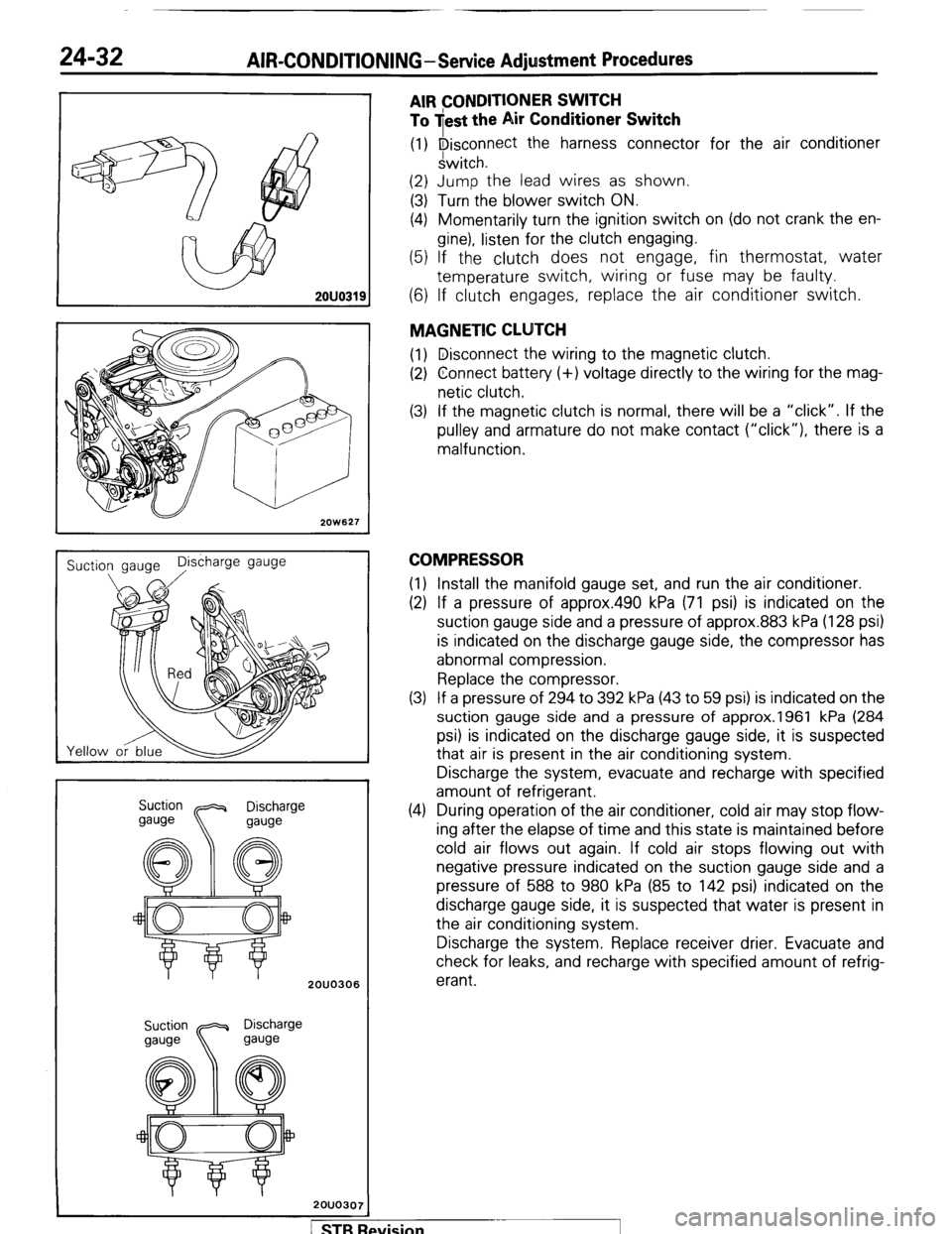
24-32 AIR-CONDITIONING-Service Adjustment Procedures
i--
9 >
@
r
2ouo319
- 2OW627 I
Suction gauge Discharge w-w
/ I
Suction
ww Discharge
w-w
2OUO306
Suction
w-w Discharge
gauge
2OUO307
AIR CONDITIONER SWITCH
To jest the Air Conditioner Switch
(1) Disconnect the harness connector for the air conditioner
switch.
(2) Jump the lead wires as shown.
(3) Turn the blower switch ON.
(4) Momentarily turn the ignition switch on (do not crank the en-
gine), listen for the clutch engaging.
(5) If the clutch does not engage, fin thermostat, water
temperature switch, wiring or fuse may be faulty.
(6) If clutch engages, replace the air conditioner switch.
MAGNETIC CLUTCH
(1) Disconnect the wiring to the magnetic clutch.
(2) Connect battery (+) voltage directly to the wiring for the mag-
netic clutch.
(3) If the magnetic clutch is normal, there will be a “click”. If the
pulley and armature do not make contact (“click”), there is a
malfunction.
COMPRESSOR
(1) Install the manifold gauge set, and run the air conditioner.
(2) If a pressure of approx.490 kPa (71 psi) is indicated on the
suction gauge side and a pressure of approx.883 kPa (128 psi)
is indicated on the discharge gauge side, the compressor has
abnormal compression.
Replace the compressor.
(3) If a pressure of 294 to 392 kPa (43 to 59 psi) is indicated on the
suction gauge side and a pressure of approx.1961 kPa (284
psi) is indicated on the discharge gauge side, it is suspected
that air is present in the air conditioning system.
Discharge the system, evacuate and recharge with specified
amount of refrigerant.
(4) During operation of the air conditioner, cold air may stop flow-
ing after the elapse of time and this state is maintained before
cold air flows out again. If cold air stops flowing out with
negative pressure indicated on the suction gauge side and a
pressure of 588 to 980 kPa (85 to 142 psi) indicated on the
discharge gauge side, it is suspected that water is present in
the air conditioning system.
Discharge the system. Replace receiver drier. Evacuate and
check for leaks, and recharge with specified amount of refrig-
erant.
/ STB Revision
Page 269 of 284
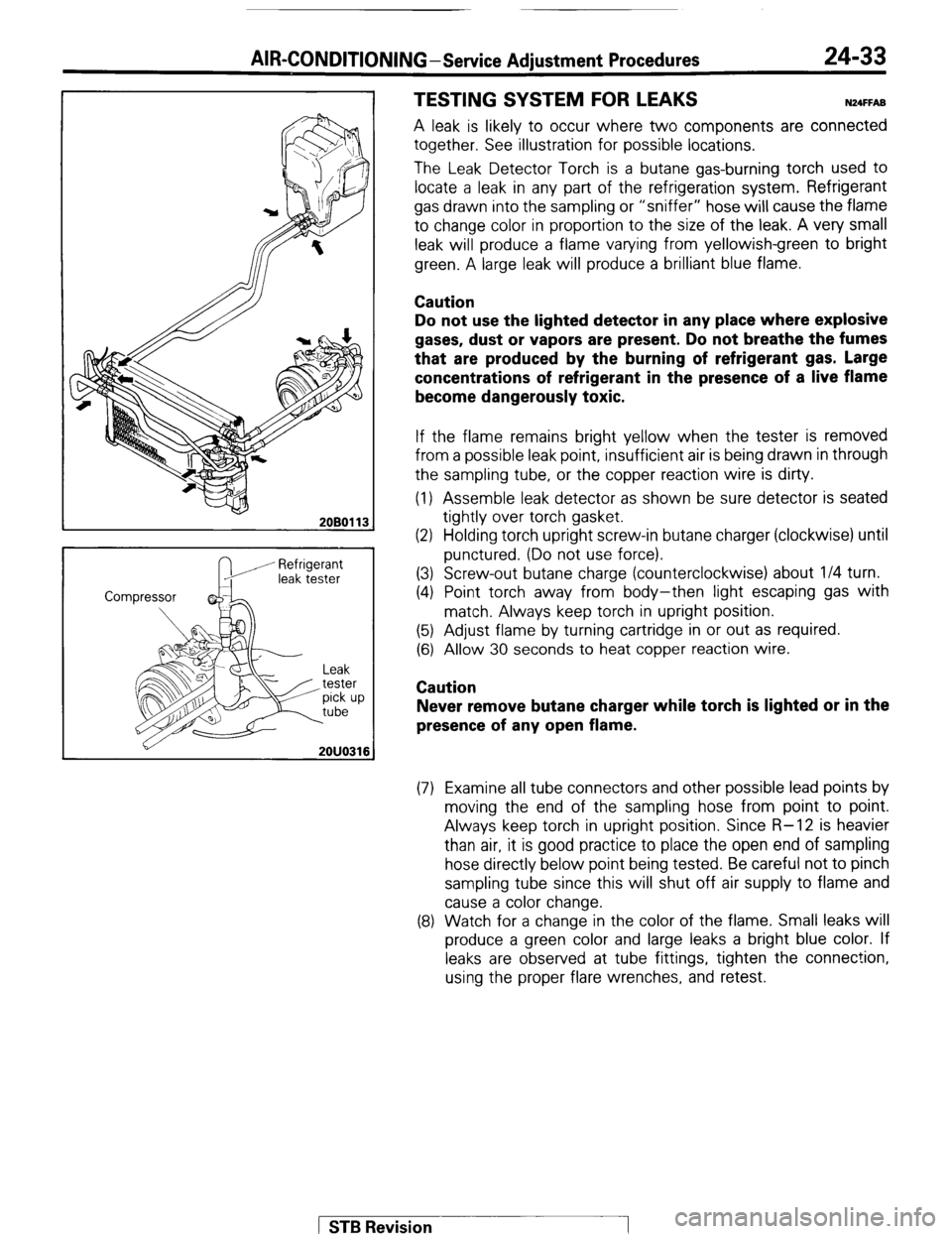
AIR-CONDITIONING-Service Adjustment Procedures 24-33
2080113
6
Refrigerant
Compressor
Cl”“” tester T-7
Leak
, tester
pick up
tube
b/
2OUO316
TESTING SYSTEM FOR LEAKS N24FFA8
A leak is likely to occur where two components are connected
together. See illustration for possible locations.
The Leak Detector Torch is a butane gas-burning torch used to
locate a leak in any part of the refrigeration system. Refrigerant
gas drawn into the sampling or “sniffer” hose will cause the flame
to change color in proportion to the size of the leak. A very small
leak will produce a flame varying from yellowish-green to bright
green. A large leak will produce a brilliant blue flame.
Caution
Do not use the lighted detector in any place where explosive
gases, dust or vapors are present. Do not breathe the
fumes
that are produced by the burning of refrigerant gas. Large
concentrations of refrigerant in the presence of a live flame
become dangerously toxic.
If the flame remains bright yellow when the tester is removed
from a possible leak point, insufficient air is being drawn in through
the sampling tube, or the copper reaction wire is dirty.
(1) Assemble leak detector as shown be sure detector is seated
tightly over torch gasket.
(2) Holding torch upright screw-in butane charger (clockwise) until
punctured. (Do not use force).
(3) Screw-out butane charge (counterclockwise) about l/4 turn.
(4) Point torch away from body-then light escaping gas with
match. Always keep torch in upright position.
(5) Adjust flame by turning cartridge in or out as required.
(6) Allow 30 seconds to heat copper reaction wire.
Caution
Never remove butane charger while torch is lighted or in the
presence of any open flame.
(7) Examine all tube connectors and other possible lead points by
moving the end of the sampling hose from point to point.
Always keep torch in upright position. Since R-12 is heavier
than air, it is good practice to place the open end of sampling
hose directly below point being tested. Be careful not to pinch
sampling tube since this will shut off air supply to flame and
cause a color change.
(8) Watch for a change in the color of the flame. Small leaks will
produce a green color and large leaks a bright blue color. If
leaks are observed at tube fittings, tighten the connection,
using the proper flare wrenches, and retest.
1 STB Revision
Page 270 of 284
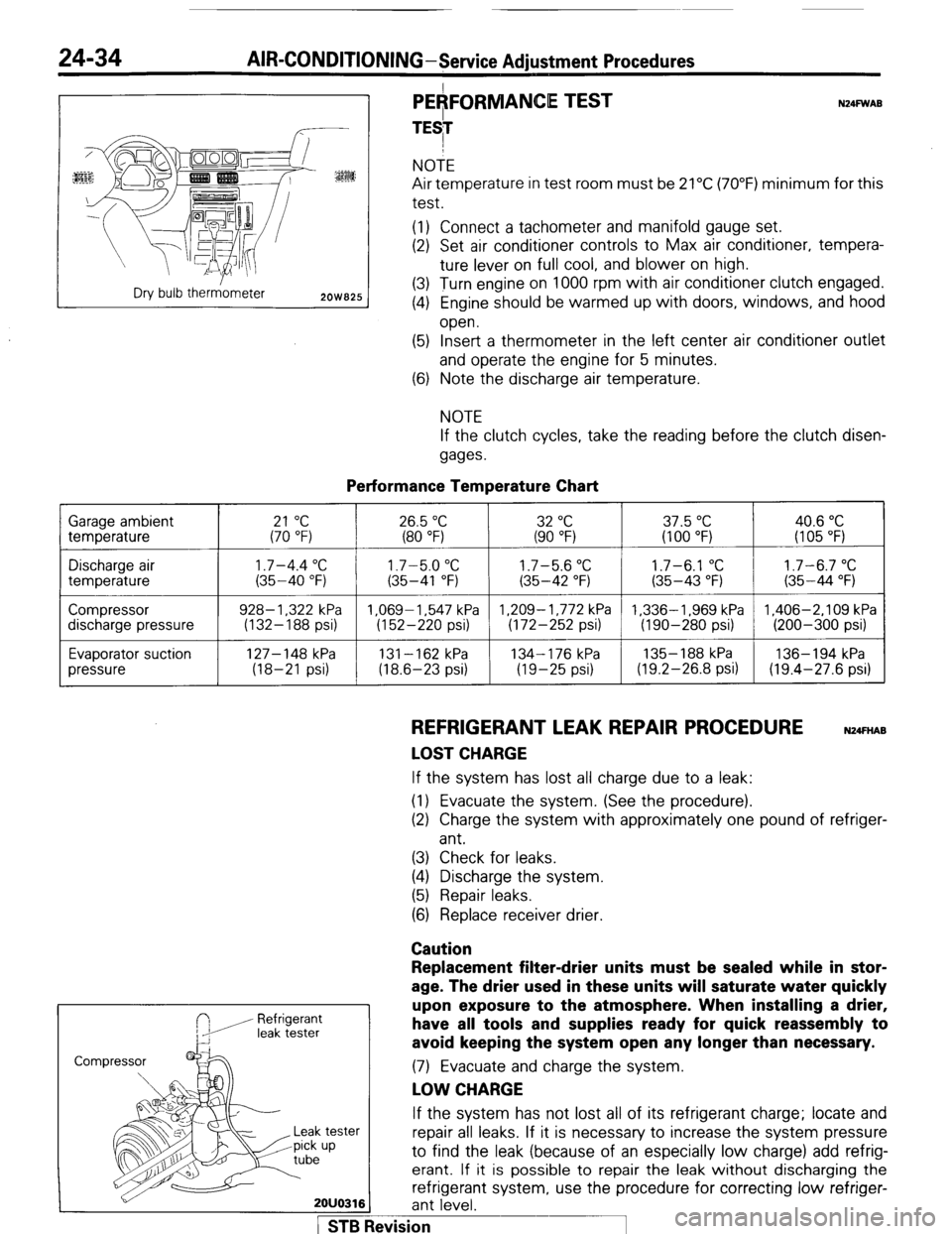
24-34 AIR-CONDITIONING-Service Adiustment Procedures
r---- :
:ES
Dry bulb therr&neter
2OW825
PEAFORMANCE TEST
TESI N24FWAB NOTE
Air temperature in test room must be 21°C (70°F) minimum for this
test.
(1) Connect a tachometer and manifold gauge set.
(2) Set air conditioner controls to Max air conditioner, tempera-
ture lever on full cool, and blower on high.
(3) Turn engine on 1000 rpm with air conditioner clutch engaged.
(4) Engine should be warmed up with doors, windows, and hood
open.
(5) Insert a thermometer in the left center air conditioner outlet
and operate the engine for 5 minutes.
(6) Note the discharge air temperature.
NOTE
If the clutch cycles, take the reading before the clutch disen-
gages.
Performance Temperature Chart Garage ambient
temperature
21 “C 26.5 “C 32 “C 37.5 “C 40.6 “C (70 “F) (80 “F) (90 “F) (100 “F) (I 05 “F)
Discharge air
temperature
Compressor
discharge pressure
Evaporator suction
pressure
1.7-4.4 “C 1.7-5.0 “C 1.7-5.6 “C 1.7-6.1 “C 1.7-6.7 “C (35-40 “F) (35-41 “F) (35-42 “F) (35-43 “F) (35-44 “F)
928- 1,322 kPa 1.069-1.547 kPa 1,209-1,772 kPa 1,336-1,969 kPa 1,406-2,109 kPa
(132-188 psi) (152-220 psi) (172-252 psi) (190-280 psi) (200-300 psi)
127-148 kPa
131-162 kPa 134-176 kPa 135- 188 kPa 136-194 kPa
(18-21 psi) (18.6-23 psi) (19-25 psi) (19.2-26.8 psi) (19.4-27.6 psi)
REFRIGERANT LEAK REPAIR PROCEDURE N24FnAB
LOST CHARGE If the system has lost all charge due to a leak:
(1) Evacuate the system. (See the procedure).
(2) Charge the system with approximately one pound of refriger-
ant.
(3) Check for leaks.
(4) Discharge the system.
(5) Repair leaks.
(6) Replace receiver drier.
Caution
Refrigerant
leak tester
Replacement filter-drier units must be sealed while in stor-
age. The drier used in these units will saturate water quickly
upon exposure to the atmosphere. When installing a drier,
have all tools and supplies ready for quick reassembly to
avoid keeping the system open any longer than necessary. (7) Evacuate and charge the system.
LOW CHARGE If the system has not lost all of its refrigerant charge; locate and
tester repair all leaks. If it is necessary to increase the system pressure
up to find the leak (because of an especially low charge) add refrig-
erant. If it is possible to repair the leak without discharging the
refrigerant system, use the procedure for correcting low refriger-
2OUO316 ant level.
1 STB Revision
Page 271 of 284
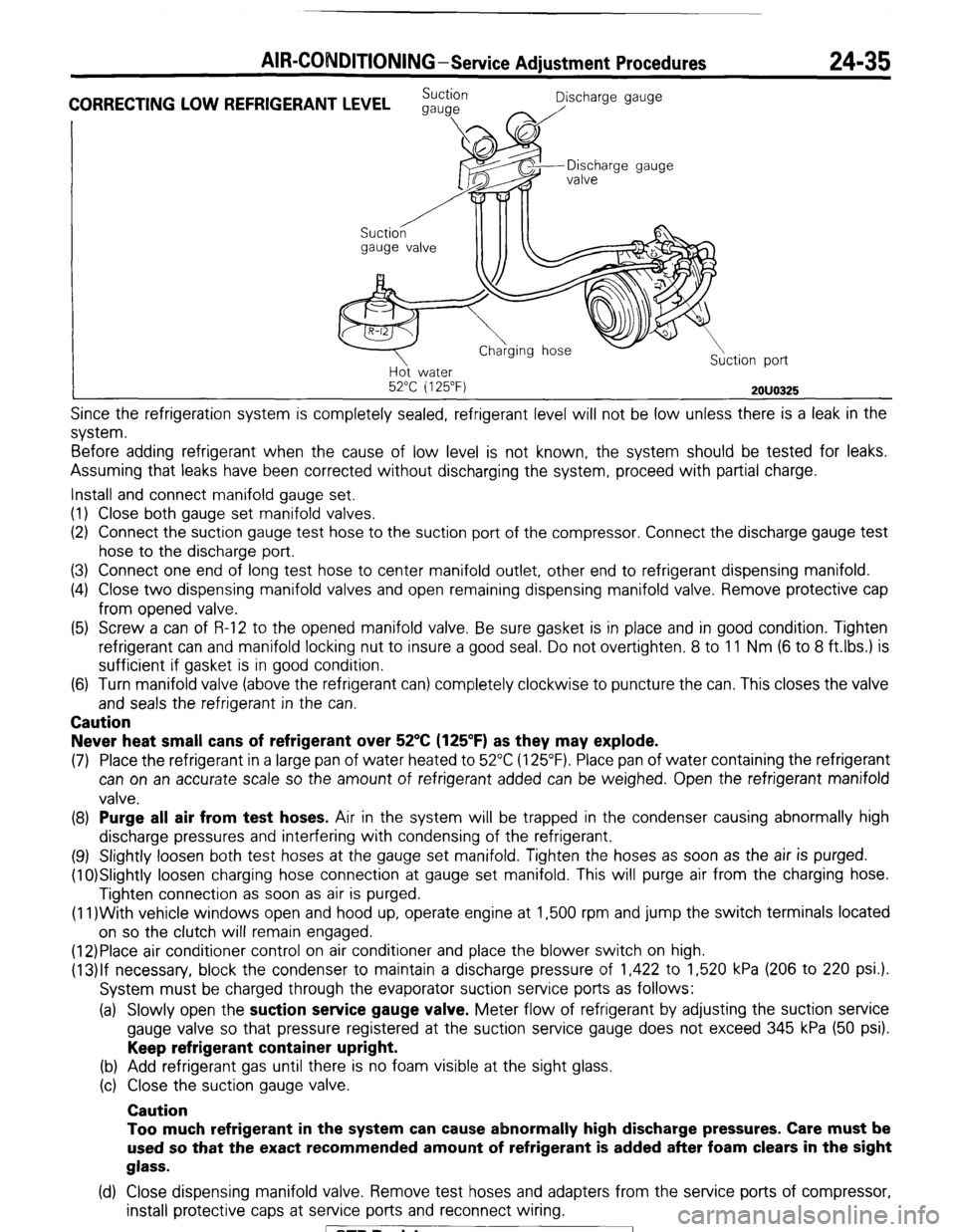
AIR-CONDITIONING-Service Adiustment Procedures 24-35
CORRECTING LOW REFRIGERANT LEVEL Suction
Discharge gauge
gauge
I \- a/
gauge valve
II II Discharge gauge
Ho water
52°C i 125°F)
2OUO325
Since the refrigeration system is completely sealed, refrigerant level will not be low unless there is a leak in the
system.
Before adding refrigerant when the cause of low level is not known, the system should be tested for leaks.
Assuming that leaks have been corrected without discharging the system, proceed with partial charge.
Install and connect manifold gauge set.
(I) Close both gauge set manifold valves.
(2) Connect the suction gauge test hose to the suction port of the compressor. Connect the discharge gauge test
hose to the discharge port.
(3) Connect one end of long test hose to center manifold outlet, other end to refrigerant dispensing manifold.
(4) Close two dispensing manifold valves and open remaining dispensing manifold valve. Remove protective cap
from opened valve.
(5) Screw a can of R-12 to the opened manifold valve. Be sure gasket is in place and in good condition. Tighten
refrigerant can and manifold locking nut to insure a good seal. Do not overtighten. 8 to 11 Nm (6 to 8 ft.lbs.) is
sufficient if gasket is in good condition.
(6) Turn manifold valve (above the refrigerant can) completely clockwise to puncture the can. This closes the valve
and seals the refrigerant in the can. Caution
Never heat small cans of refrigerant over 52°C (125’F) as they may explode.
(7) Place the refrigerant in a large pan of water heated to 52°C (125°F). Place pan of water containing the refrigerant
can on an accurate scale so the amount of refrigerant added can be weighed. Open the refrigerant manifold
valve. (8) Purge all air from test hoses.
Air in the system will be trapped in the condenser causing abnormally high
discharge pressures and interfering with condensing of the refrigerant.
(9) Slightly loosen both test hoses at the gauge set manifold. Tighten the hoses as soon as the air is purged.
(10)Slightly loosen charging hose connection at gauge set manifold. This will purge air from the charging hose.
Tighten connection as soon as air is purged.
(1l)With vehicle windows open and hood up, operate engine at 1,500 rpm and jump the switch terminals located
on so the clutch will remain engaged.
(12)Place air conditioner control on air conditioner and place the blower switch on high.
(13)lf necessary, block the condenser to maintain a discharge pressure of 1,422 to 1,520 kPa (206 to 220 psi.).
System must be charged through the evaporator suction service ports as follows:
(a) Slowly open the suction service gauge valve.
Meter flow of refrigerant by adjusting the suction service
gauge valve so that pressure registered at the suction service gauge does not exceed 345 kPa (50 psi). Keep refrigerant container upright.
(b) Add refrigerant gas until there is no foam visible at the sight glass.
(c) Close the suction gauge valve. Caution
Too much refrigerant in the system can cause abnormally high discharge pressures. Care must be
used so that the exact recommended amount of refrigerant is added after foam clears in the sight
glass.
(d) Close dispensing manifold valve. Remove test hoses and adapters from the service ports of compressor,
install protective caps at service ports and reconnect wiring. / STB Revision
Page 272 of 284
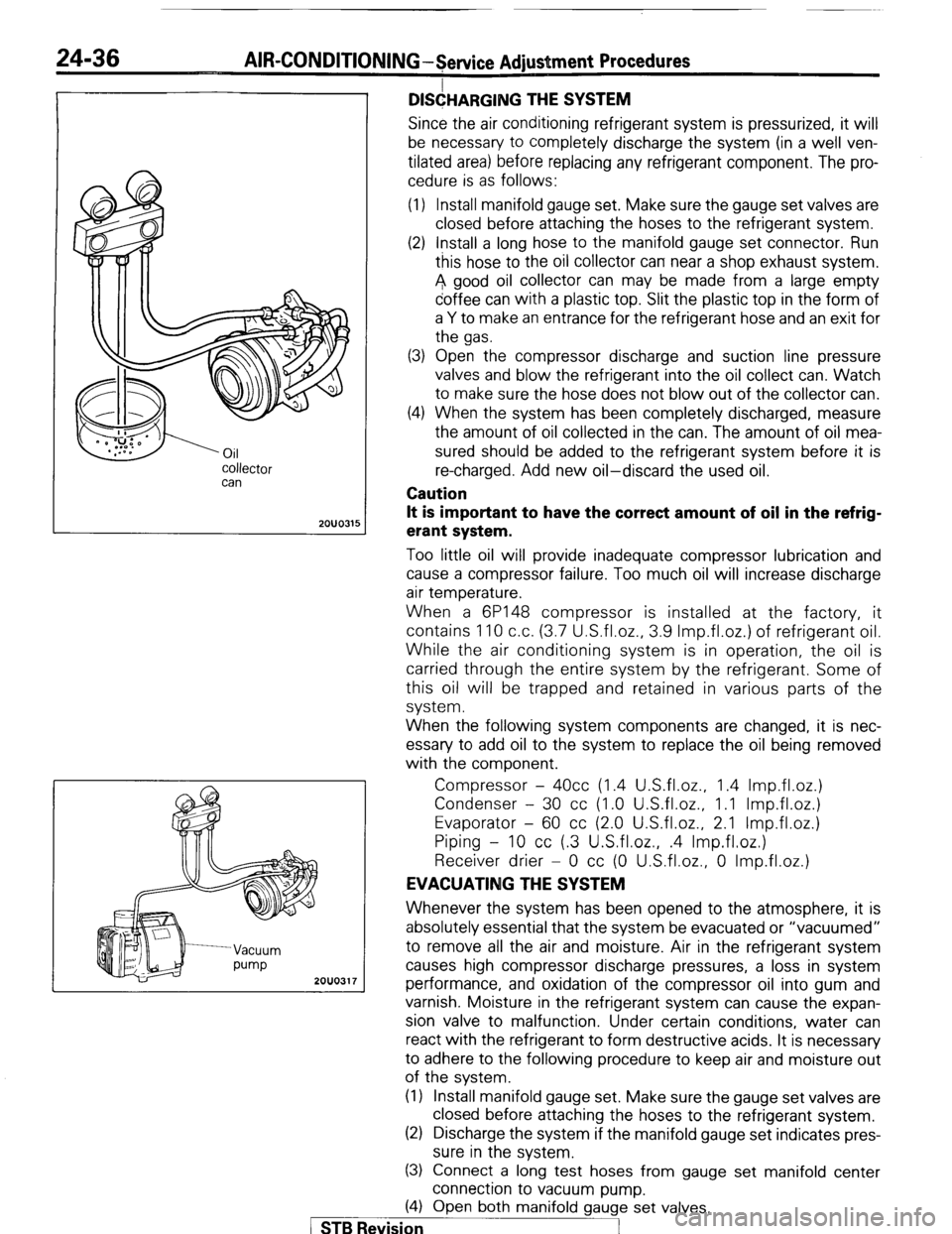
COllector
can
2OUO315
24-36 AIR-CONDITIONING-Service Adjustment Procedures
D&ARG,NG THE SYSTEM
Since the air conditioning refrigerant system is pressurized, it will
be necessary to completely discharge the system (in a well ven-
tilated area) before replacing any refrigerant component. The pro-
cedure is as follows:
(1) Install manifold gauge set. Make sure the gauge set valves are
closed before attaching the hoses to the refrigerant system.
(2) Install a long hose to the manifold gauge set connector. Run
this hose to the oil collector can near a shop exhaust system.
A good oil collector can may be made from a large empty
coffee can with a plastic top. Slit the plastic top in the form of
a Y to make an entrance for the refrigerant hose and an exit for
the gas.
(3) Open the compressor discharge and suction line pressure
valves and blow the refrigerant into the oil collect can. Watch
to make sure the hose does not blow out of the collector can.
(4) When the system has been completely discharged, measure
the amount of oil collected in the can. The amount of oil mea-
sured should be added to the refrigerant system before it is
re-charged. Add new oil-discard the used oil.
Caution
It is important to have the correct amount of oil in the refrig-
erant system.
Too little oil will provide inadequate compressor lubrication and
cause a compressor failure. Too much oil will increase discharge
air temperature.
When a 6P148 compressor is installed at the factory, it
contains 110 c.c. (3.7 U.S.fl.oz., 3.9 Imp.fl.oz.) of refrigerant oil.
While the air conditioning system is in operation, the oil is
carried through the entire system by the refrigerant. Some of
this oil will be trapped and retained in various parts of the
system.
When the following system components are changed, it is nec-
essary to add oil to the system to replace the oil being removed
with the component.
Compressor - 4Occ (1.4 U.S.fl.oz., 1.4 Imp.fl.oz.)
Condenser - 30 cc (1.0 U.S.fl.oz., 1.1 Imp.fl.oz.)
Evaporator - 60 cc (2.0 U.S.fl.oz., 2.1 Imp.fl.oz.)
Piping - 10 cc (.3 U.S.fl.oz., .4 Imp.fl.oz.)
Receiver drier - 0 cc (0 U.S.fl.oz., 0 Imp.fl.oz.)
EVACUATING THE SYSTEM
2OUO31
Whenever the system has been opened to the atmosphere, it is
absolutely essential that the system be evacuated or “vacuumed”
to remove all the air and moisture. Air in the refrigerant system
causes high compressor discharge pressures, a loss in system
performance, and oxidation of the compressor oil into gum and
varnish. Moisture in the refrigerant system can cause the expan-
sion valve to malfunction. Under certain conditions, water can
react with the refrigerant to form destructive acids. It is necessary
to adhere to the following procedure to keep air and moisture out
of the system.
(1) Install manifold gauge set. Make sure the gauge set valves are
closed before attaching the hoses to the refrigerant system.
(2) Discharge the system if the manifold gauge set indicates pres-
sure in the system.
(3) Connect a long test hoses from gauge set manifold center
connection to vacuum pump.
(4) Open both manifold gauge set valves.
/
/vision I
Page 273 of 284
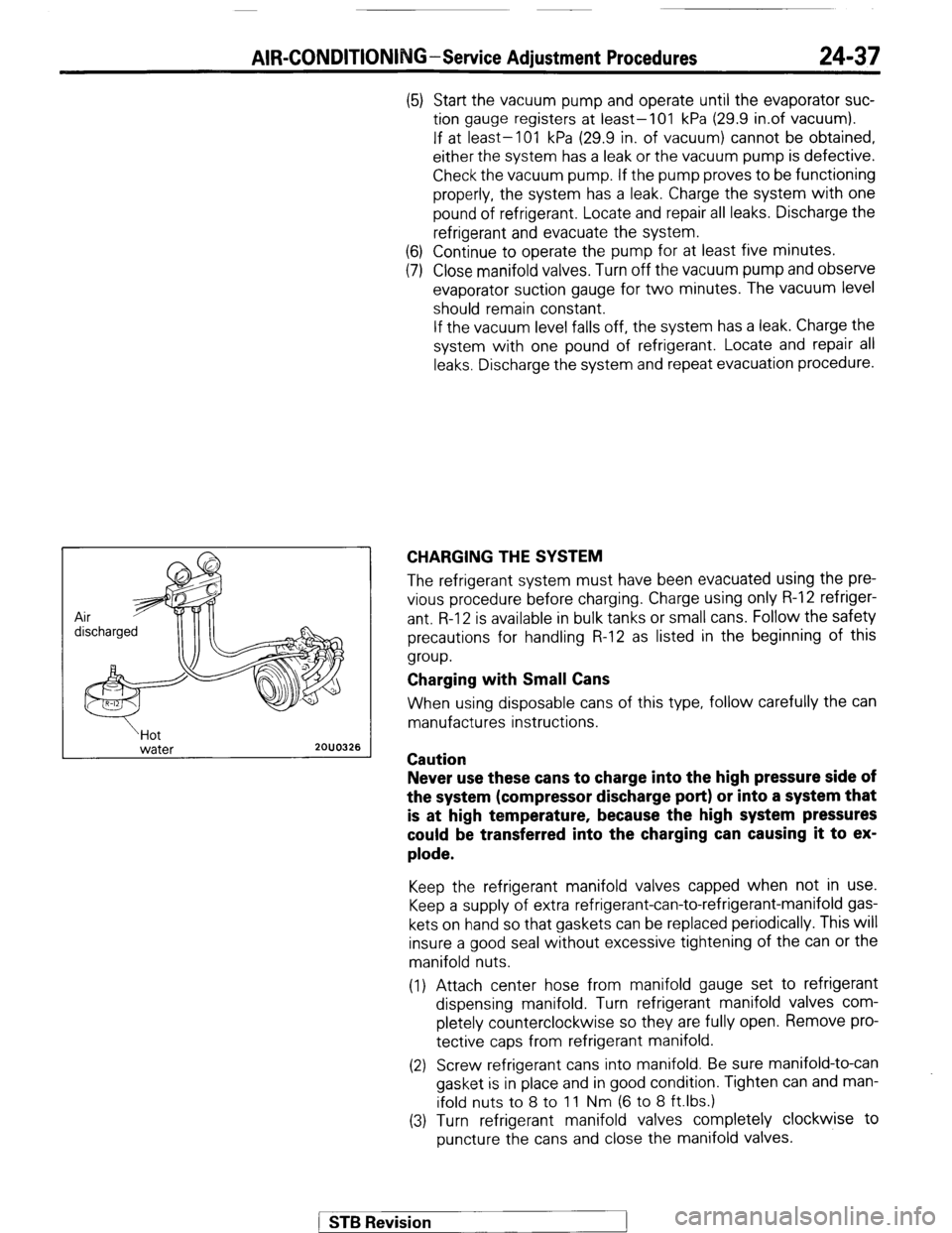
AIR-CONDITION1 G-Service Adjustment Procedures 24-37
water 2OUO326
(5) Start the vacuum pump and operate until the evaporator suc-
tion gauge registers at least-101 kPa (29.9 in.of vacuum).
If at least-101 kPa (29.9 in. of vacuum) cannot be obtained,
either the system has a leak or the vacuum pump is defective.
Check the vacuum pump. If the pump proves to be functioning
properly, the system has a leak. Charge the system with one
pound of refrigerant. Locate and repair all leaks. Discharge the
refrigerant and evacuate the system.
(6) Continue to operate the pump for at least five minutes.
(7) Close manifold valves. Turn off the vacuum pump and observe
evaporator suction gauge for two minutes. The vacuum level
should remain constant.
If the vacuum level falls off, the system has a leak. Charge the
system with one pound of refrigerant. Locate and repair all
leaks. Discharge the system and repeat evacuation procedure.
CHARGING THE SYSTEM
The refrigerant system must have been evacuated using the pre-
vious procedure before charging. Charge using only R-l 2 refriger-
ant R-l 2 is available in bulk tanks or small cans. Follow the safety
precautions for handling R-12 as listed in the beginning of this
group.
Charging with Small Cans
When using disposable cans of this type, follow carefully the can
manufactures instructions.
Caution
Never use these cans to charge into the high pressure side of
the system (compressor discharge port) or into a system that
is at high temperature, because the high system pressures
could be transferred into the charging can causing it to ex-
plode.
Keep the refrigerant manifold valves capped when not in use.
Keep a supply of extra refrigerant-can-to-refrigerant-manifold gas-
kets on hand so that gaskets can be replaced periodically. This will
insure a good seal without excessive tightening of the can or the
manifold nuts.
(1) Attach center hose from manifold gauge set to refrigerant
dispensing manifold. Turn refrigerant manifold valves com-
pletely counterclockwise so they are fully open. Remove pro-
tective caps from refrigerant manifold.
(2) Screw refrigerant cans into manifold. Be sure manifold-to-can
gasket is in place and in good condition. Tighten can and man-
ifold nuts to 8 to 11 Nm (6 to 8 ft.lbs.)
(3) Turn refrigerant manifold valves completely clockwise to
puncture the cans and close the manifold valves.
/ ST6 Revision
Page 274 of 284
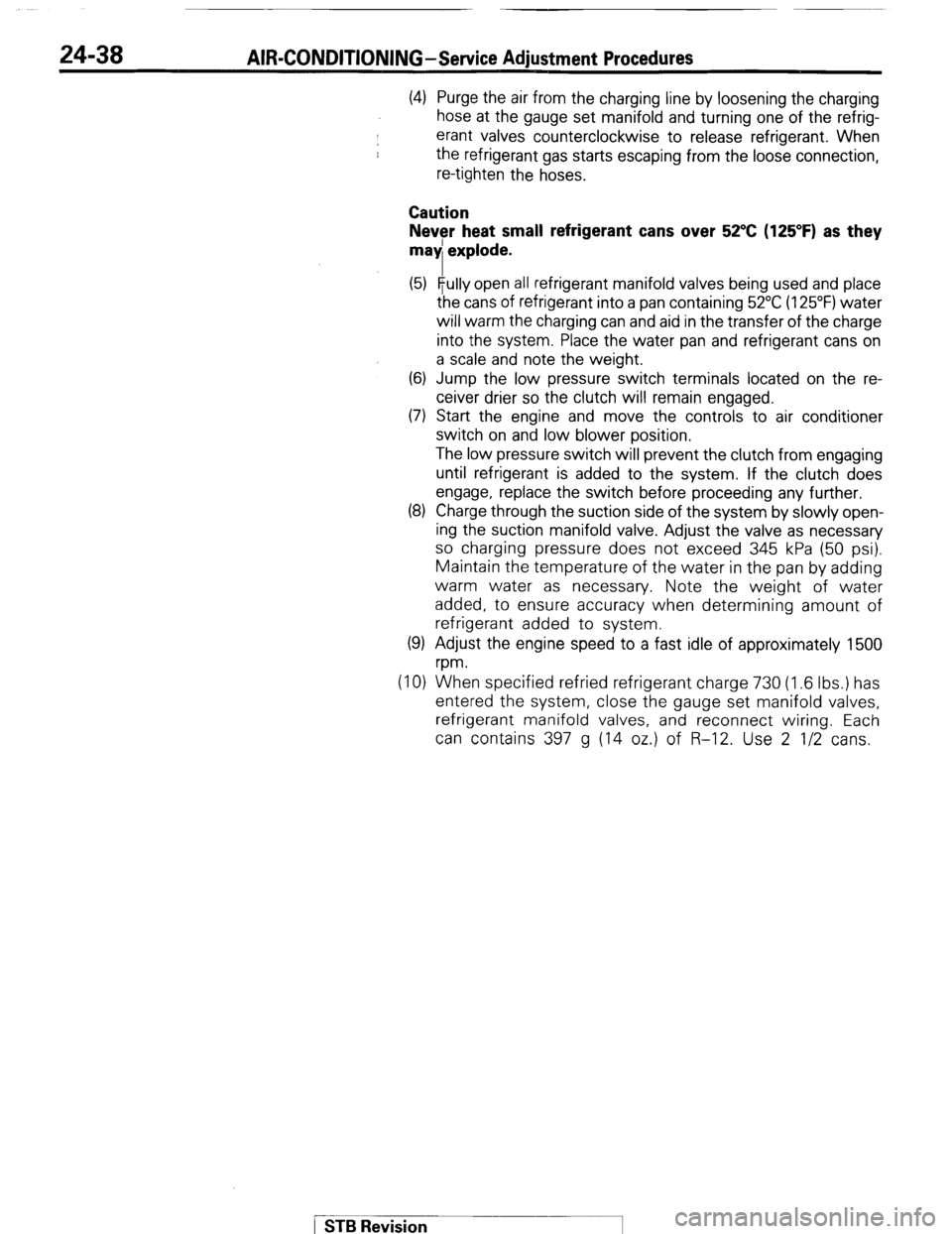
24-38 AIR-CONDITIONING-Service Adjustment Procedures
(4) Purge the air from the charging line by loosening the charging
hose at the gauge set manifold and turning one of the refrig-
erant valves counterclockwise to release refrigerant. When
the refrigerant gas starts escaping from the loose connection,
re-tighten the hoses.
Caution
Never heat small refrigerant cans over 52°C (125°F) as they
mad explode.
(5) qully open all refrigerant manifold valves being used and place
the cans of refrigerant into a pan containing 52°C (125°F) water
will warm the charging can and aid in the transfer of the charge
into the system. Place the water pan and refrigerant cans on
a scale and note the weight.
(6) Jump the low pressure switch terminals located on the re-
ceiver drier so the clutch will remain engaged.
(7) Start the engine and move the controls to air conditioner
switch on and low blower position.
The low pressure switch will prevent the clutch from engaging
until refrigerant is added to the system. If the clutch does
engage, replace the switch before proceeding any further.
(8) Charge through the suction side of the system by slowly open-
ing the suction manifold valve. Adjust the valve as necessary
so charging pressure does not exceed 345 kPa (50 psi).
Maintain the temperature of the water in the pan by adding
warm water as necessary. Note the weight of water
added, to ensure accuracy when determining amount of
refrigerant added to system.
(9) Adjust the engine speed to a fast idle of approximately 1500
rpm.
(IO) When specified refried refrigerant charge 730 (1.6 Ibs.) has
entered the system, close the gauge set manifold valves,
refrigerant manifold valves, and reconnect wiring. Each
can contains 397 g (14 oz.) of R-12. Use 2 l/2 cans.
1 STB Revision
-1