MITSUBISHI MONTERO 1998 Service Manual
Manufacturer: MITSUBISHI, Model Year: 1998, Model line: MONTERO, Model: MITSUBISHI MONTERO 1998Pages: 1501, PDF Size: 25.81 MB
Page 1231 of 1501
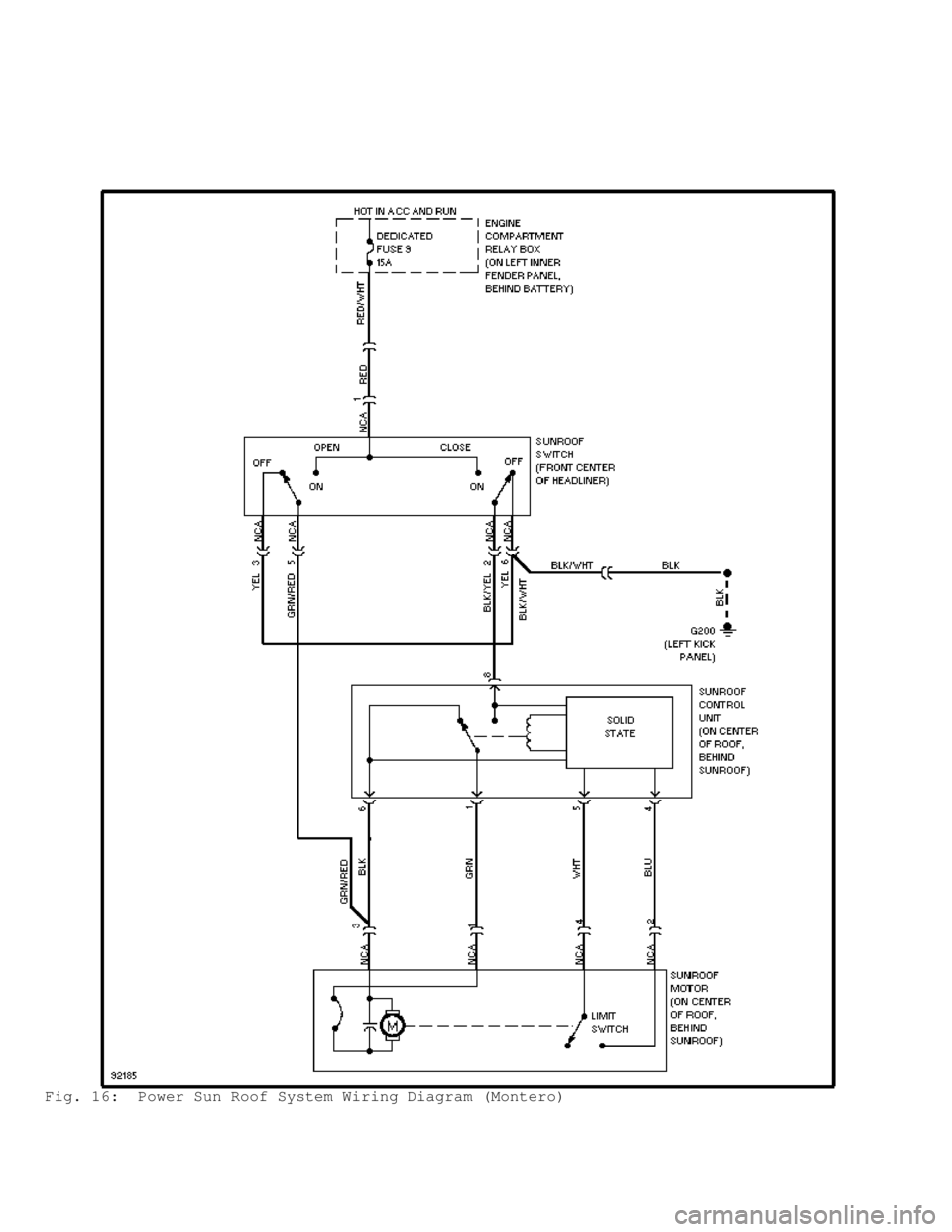
Fig. 16: Power Sun Roof System Wiring Diagram (Montero)
Page 1232 of 1501
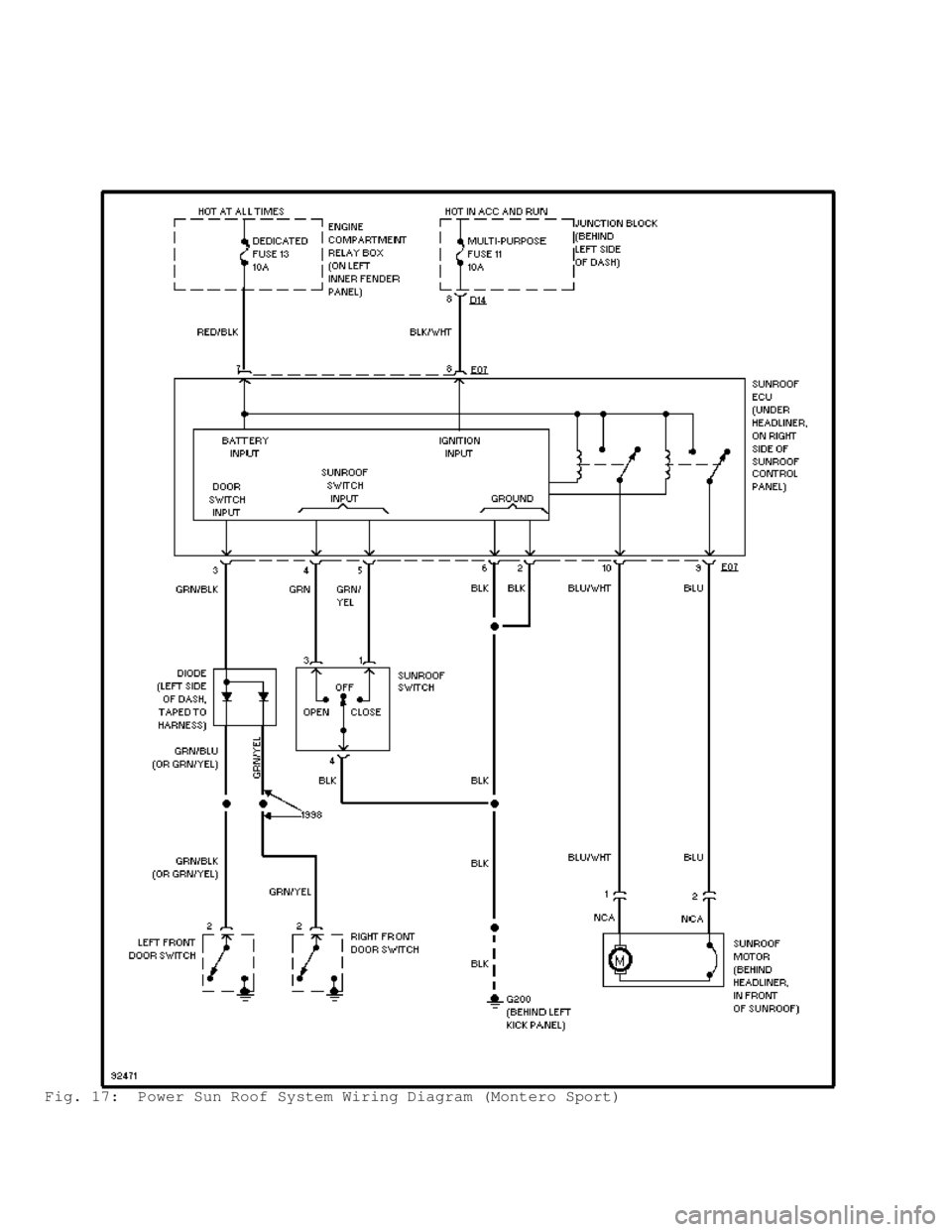
Fig. 17: Power Sun Roof System Wiring Diagram (Montero Sport)
Page 1233 of 1501
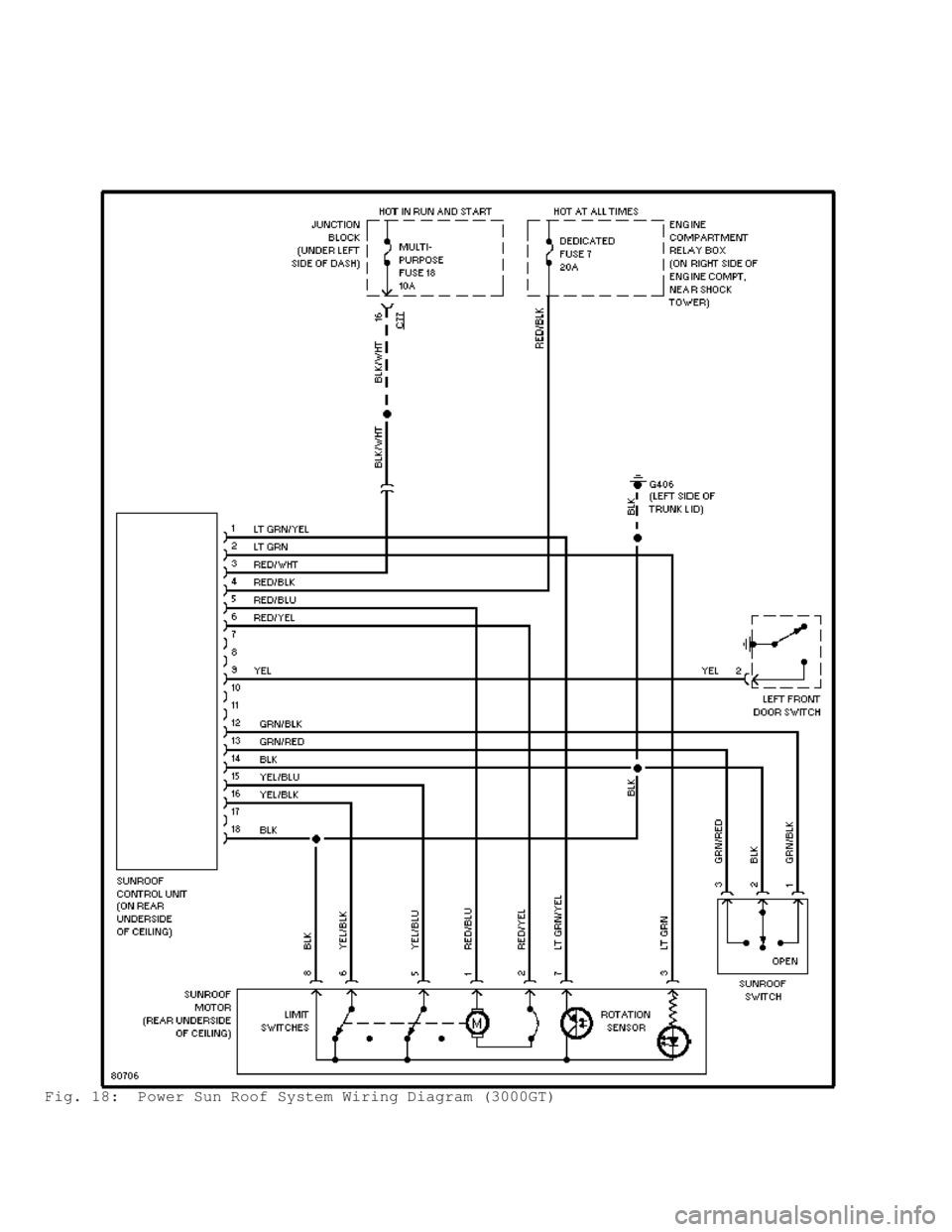
Fig. 18: Power Sun Roof System Wiring Diagram (3000GT)
Page 1234 of 1501
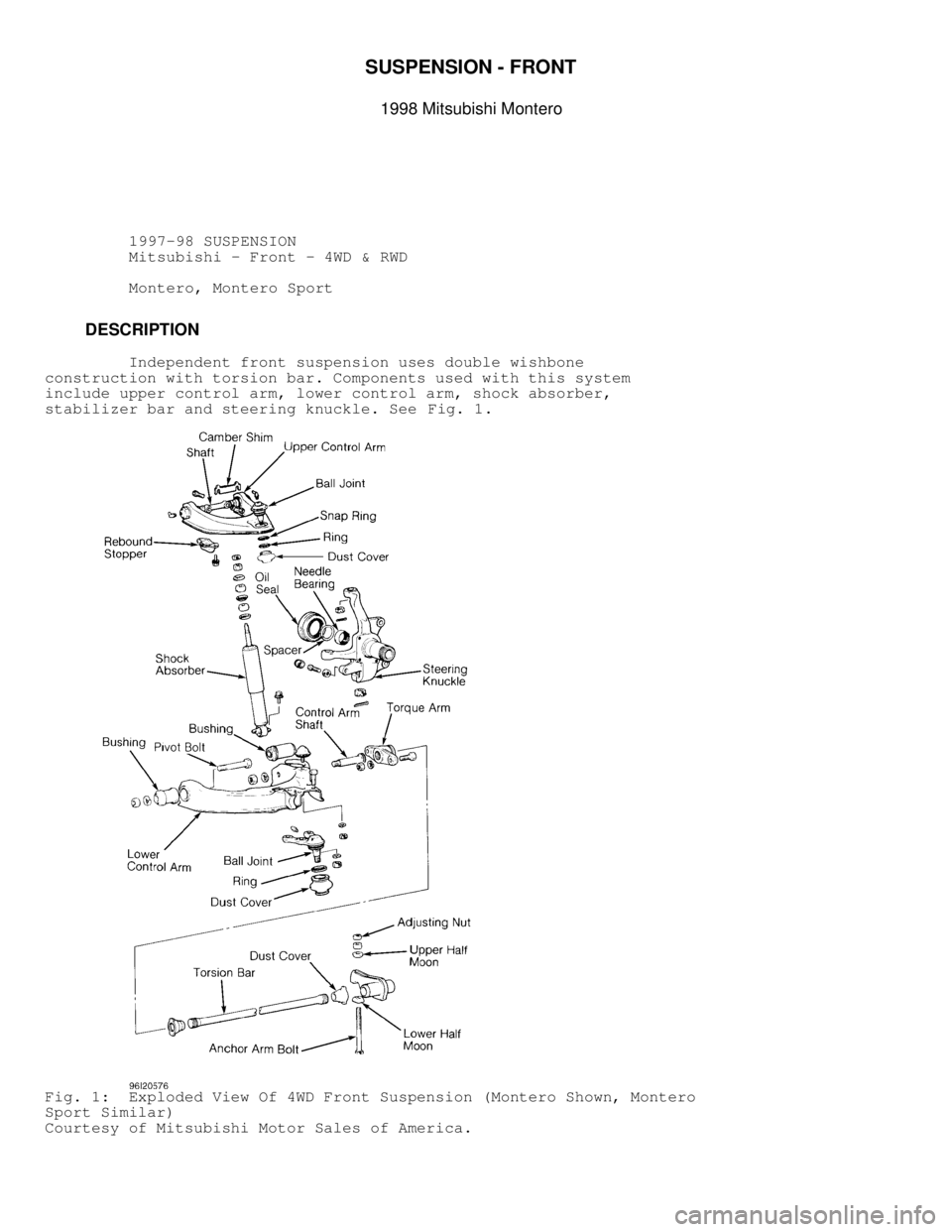
SUSPENSION - FRONT
1998 Mitsubishi Montero
1997-98 SUSPENSION
Mitsubishi - Front - 4WD & RWD
Montero, Montero Sport
DESCRIPTION
Independent front suspension uses double wishbone
construction with torsion bar. Components used with this system
include upper control arm, lower control arm, shock absorber,
stabilizer bar and steering knuckle. See Fig. 1.
Fig. 1: Exploded View Of 4WD Front Suspension (Montero Shown, Montero
Sport Similar)
Courtesy of Mitsubishi Motor Sales of America.
Page 1235 of 1501
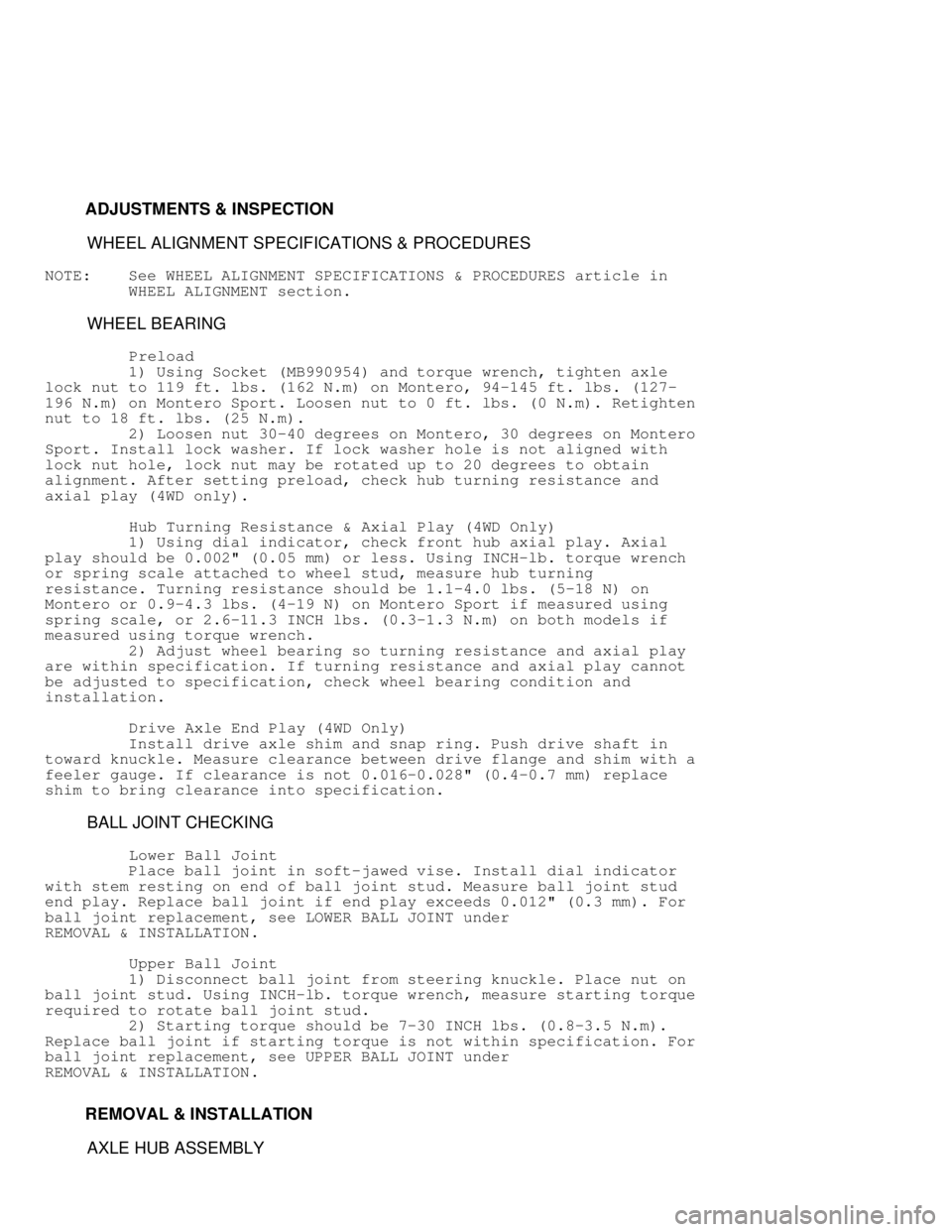
ADJUSTMENTS & INSPECTION
WHEEL ALIGNMENT SPECIFICATIONS & PROCEDURES
NOTE: See WHEEL ALIGNMENT SPECIFICATIONS & PROCEDURES article in
WHEEL ALIGNMENT section.
WHEEL BEARING
Preload
1) Using Socket (MB990954) and torque wrench, tighten axle
lock nut to 119 ft. lbs. (162 N.m) on Montero, 94-145 ft. lbs. (127-
196 N.m) on Montero Sport. Loosen nut to 0 ft. lbs. (0 N.m). Retighte\
n
nut to 18 ft. lbs. (25 N.m).
2) Loosen nut 30-40 degrees on Montero, 30 degrees on Montero
Sport. Install lock washer. If lock washer hole is not aligned with
lock nut hole, lock nut may be rotated up to 20 degrees to obtain
alignment. After setting preload, check hub turning resistance and
axial play (4WD only).
Hub Turning Resistance & Axial Play (4WD Only)
1) Using dial indicator, check front hub axial play. Axial
play should be 0.002" (0.05 mm) or less. Using INCH-lb. torque wrench
or spring scale attached to wheel stud, measure hub turning
resistance. Turning resistance should be 1.1-4.0 lbs. (5-18 N) on
Montero or 0.9-4.3 lbs. (4-19 N) on Montero Sport if measured using
spring scale, or 2.6-11.3 INCH lbs. (0.3-1.3 N.m) on both models if
measured using torque wrench.
2) Adjust wheel bearing so turning resistance and axial play
are within specification. If turning resistance and axial play cannot
be adjusted to specification, check wheel bearing condition and
installation.
Drive Axle End Play (4WD Only)
Install drive axle shim and snap ring. Push drive shaft in
toward knuckle. Measure clearance between drive flange and shim with a
feeler gauge. If clearance is not 0.016-0.028" (0.4-0.7 mm) replace
shim to bring clearance into specification.
BALL JOINT CHECKING
Lower Ball Joint
Place ball joint in soft-jawed vise. Install dial indicator
with stem resting on end of ball joint stud. Measure ball joint stud
end play. Replace ball joint if end play exceeds 0.012" (0.3 mm). For
ball joint replacement, see LOWER BALL JOINT under
REMOVAL & INSTALLATION .
Upper Ball Joint
1) Disconnect ball joint from steering knuckle. Place nut on
ball joint stud. Using INCH-lb. torque wrench, measure starting torque
required to rotate ball joint stud.
2) Starting torque should be 7-30 INCH lbs. (0.8-3.5 N.m).
Replace ball joint if starting torque is not within specification. For
ball joint replacement, see UPPER BALL JOINT under
REMOVAL & INSTALLATION .
REMOVAL & INSTALLATION
AXLE HUB ASSEMBLY
Page 1236 of 1501
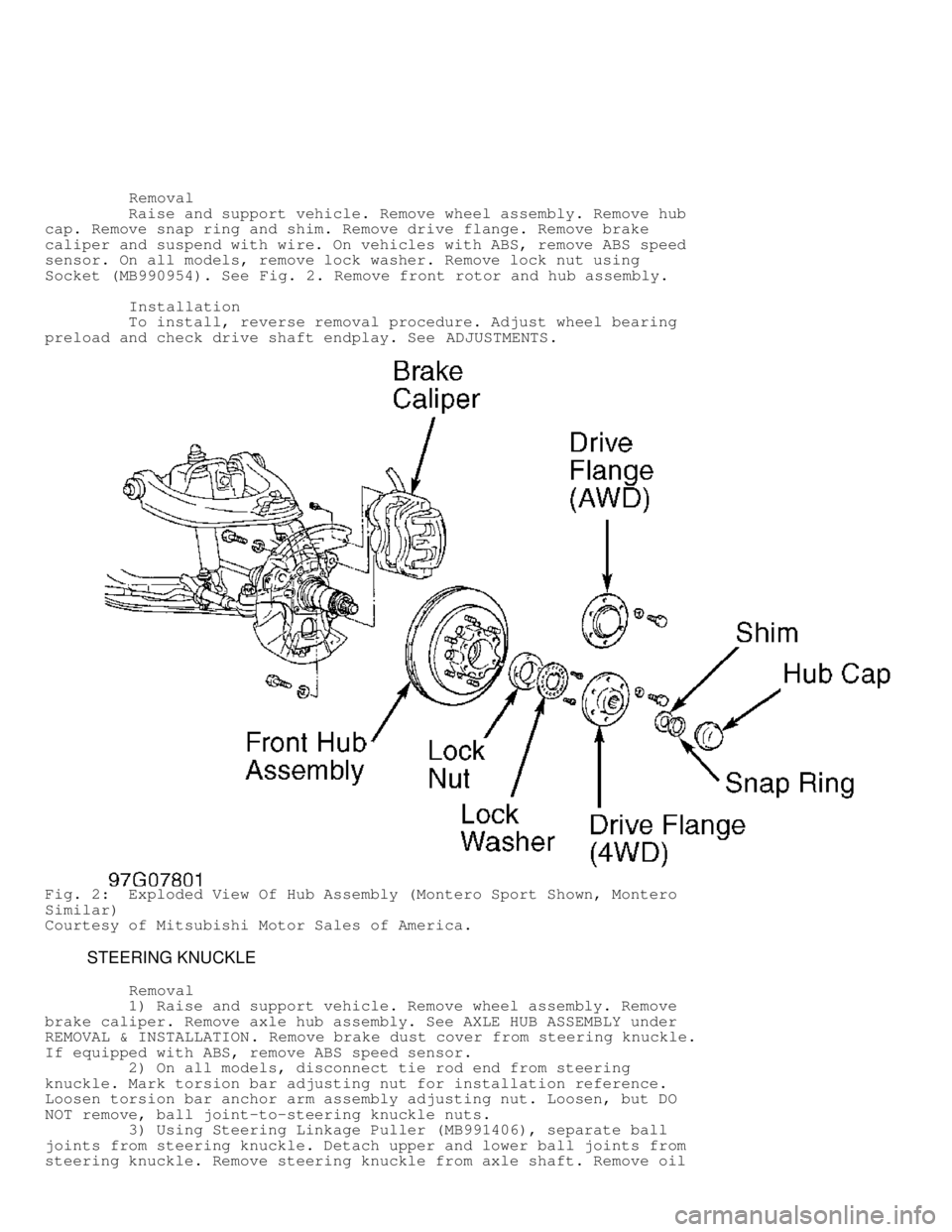
Removal
Raise and support vehicle. Remove wheel assembly. Remove hub
cap. Remove snap ring and shim. Remove drive flange. Remove brake
caliper and suspend with wire. On vehicles with ABS, remove ABS speed
sensor. On all models, remove lock washer. Remove lock nut using
Socket (MB990954). See Fig. 2. Remove front rotor and hub assembly.
Installation
To install, reverse removal procedure. Adjust wheel bearing
preload and check drive shaft endplay. See ADJUSTMENTS.
Fig. 2: Exploded View Of Hub Assembly (Montero Sport Shown, Montero
Similar)
Courtesy of Mitsubishi Motor Sales of America.
STEERING KNUCKLE
Removal
1) Raise and support vehicle. Remove wheel assembly. Remove
brake caliper. Remove axle hub assembly. See AXLE HUB ASSEMBLY under
REMOVAL & INSTALLATION . Remove brake dust cover from steering knuckle.
If equipped with ABS, remove ABS speed sensor.
2) On all models, disconnect tie rod end from steering
knuckle. Mark torsion bar adjusting nut for installation reference.
Loosen torsion bar anchor arm assembly adjusting nut. Loosen, but DO
NOT remove, ball joint-to-steering knuckle nuts.
3) Using Steering Linkage Puller (MB991406), separate ball
joints from steering knuckle. Detach upper and lower ball joints from
steering knuckle. Remove steering knuckle from axle shaft. Remove oil
Page 1237 of 1501
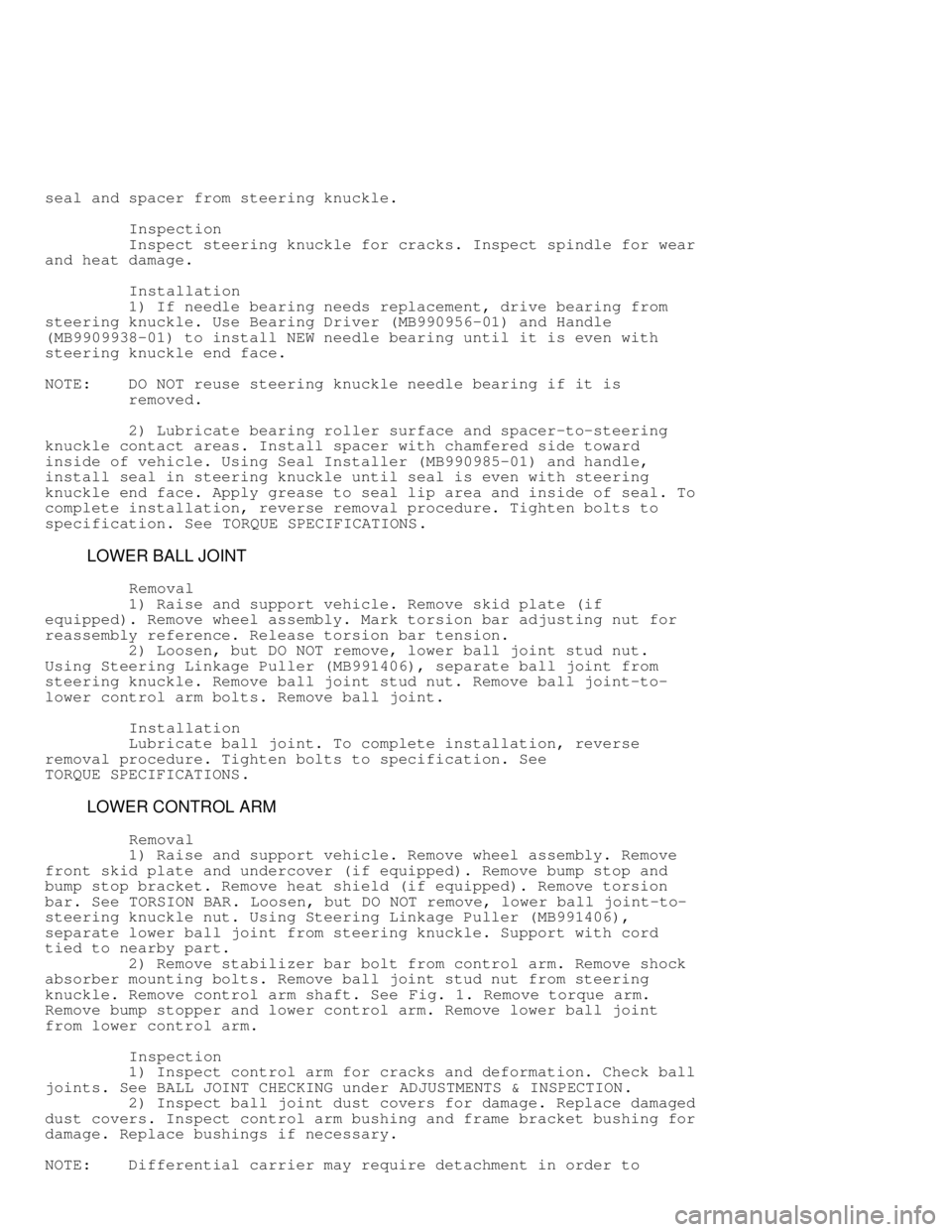
seal and spacer from steering knuckle.
Inspection
Inspect steering knuckle for cracks. Inspect spindle for wear
and heat damage.
Installation
1) If needle bearing needs replacement, drive bearing from
steering knuckle. Use Bearing Driver (MB990956-01) and Handle
(MB9909938-01) to install NEW needle bearing until it is even with
steering knuckle end face.
NOTE: DO NOT reuse steering knuckle needle bearing if it is
removed.
2) Lubricate bearing roller surface and spacer-to-steering
knuckle contact areas. Install spacer with chamfered side toward
inside of vehicle. Using Seal Installer (MB990985-01) and handle,
install seal in steering knuckle until seal is even with steering
knuckle end face. Apply grease to seal lip area and inside of seal. To
complete installation, reverse removal procedure. Tighten bolts to
specification. See TORQUE SPECIFICATIONS .
LOWER BALL JOINT
Removal
1) Raise and support vehicle. Remove skid plate (if
equipped). Remove wheel assembly. Mark torsion bar adjusting nut for
reassembly reference. Release torsion bar tension.
2) Loosen, but DO NOT remove, lower ball joint stud nut.
Using Steering Linkage Puller (MB991406), separate ball joint from
steering knuckle. Remove ball joint stud nut. Remove ball joint-to-
lower control arm bolts. Remove ball joint.
Installation
Lubricate ball joint. To complete installation, reverse
removal procedure. Tighten bolts to specification. See
TORQUE SPECIFICATIONS .
LOWER CONTROL ARM
Removal
1) Raise and support vehicle. Remove wheel assembly. Remove
front skid plate and undercover (if equipped). Remove bump stop and
bump stop bracket. Remove heat shield (if equipped). Remove torsion
bar. See TORSION BAR . Loosen, but DO NOT remove, lower ball joint-to-
steering knuckle nut. Using Steering Linkage Puller (MB991406),
separate lower ball joint from steering knuckle. Support with cord
tied to nearby part.
2) Remove stabilizer bar bolt from control arm. Remove shock
absorber mounting bolts. Remove ball joint stud nut from steering
knuckle. Remove control arm shaft. See Fig. 1. Remove torque arm.
Remove bump stopper and lower control arm. Remove lower ball joint
from lower control arm.
Inspection
1) Inspect control arm for cracks and deformation. Check ball
joints. See BALL JOINT CHECKING under ADJUSTMENTS & INSPECTION.
2) Inspect ball joint dust covers for damage. Replace damaged
dust covers. Inspect control arm bushing and frame bracket bushing for
damage. Replace bushings if necessary.
NOTE: Differential carrier may require detachment in order to
Page 1238 of 1501
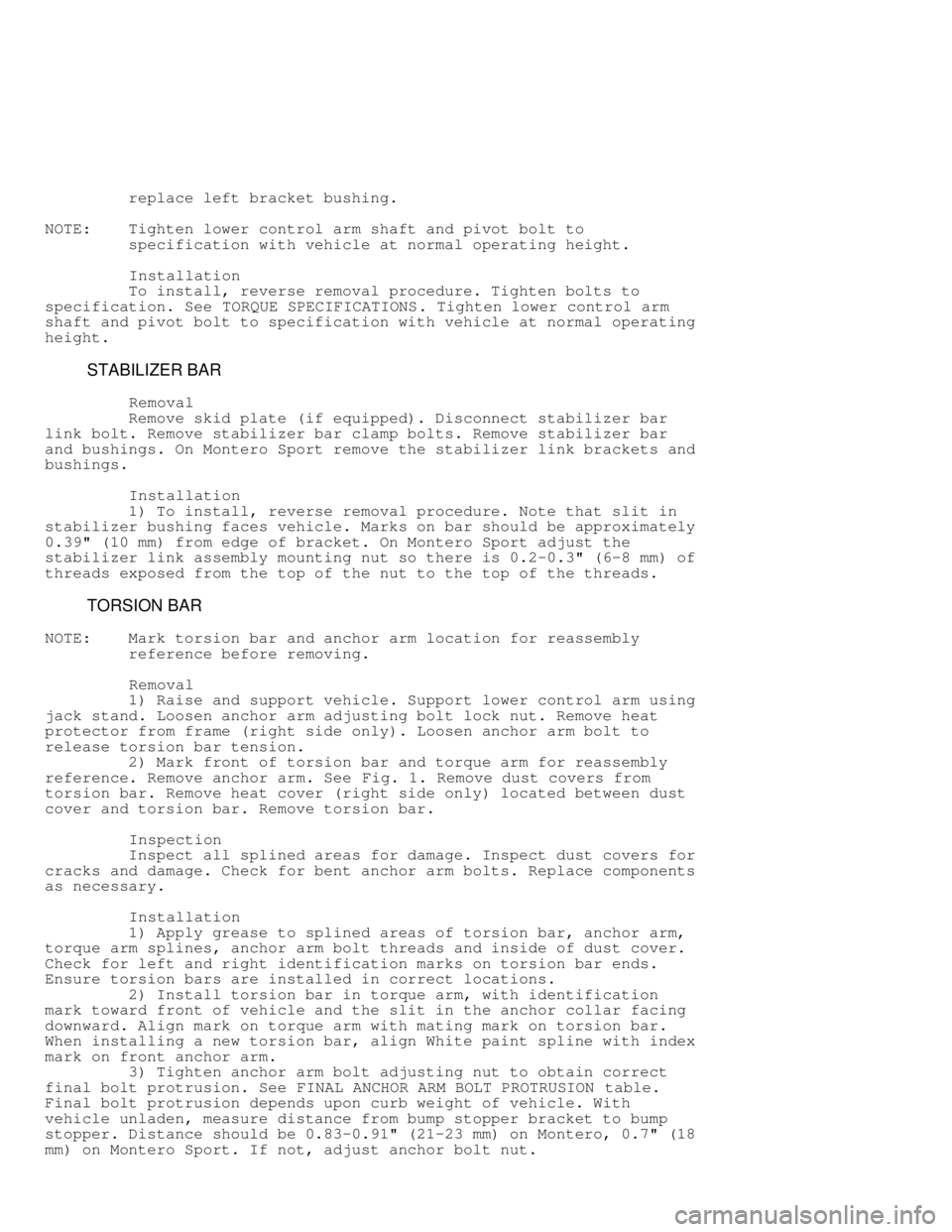
replace left bracket bushing.
NOTE: Tighten lower control arm shaft and pivot bolt to
specification with vehicle at normal operating height.
Installation
To install, reverse removal procedure. Tighten bolts to
specification. See TORQUE SPECIFICATIONS . Tighten lower control arm
shaft and pivot bolt to specification with vehicle at normal operating
height.
STABILIZER BAR
Removal
Remove skid plate (if equipped). Disconnect stabilizer bar
link bolt. Remove stabilizer bar clamp bolts. Remove stabilizer bar
and bushings. On Montero Sport remove the stabilizer link brackets and
bushings.
Installation
1) To install, reverse removal procedure. Note that slit in
stabilizer bushing faces vehicle. Marks on bar should be approximately
0.39" (10 mm) from edge of bracket. On Montero Sport adjust the
stabilizer link assembly mounting nut so there is 0.2-0.3" (6-8 mm) of\
threads exposed from the top of the nut to the top of the threads.
TORSION BAR
NOTE: Mark torsion bar and anchor arm location for reassembly
reference before removing.
Removal
1) Raise and support vehicle. Support lower control arm using
jack stand. Loosen anchor arm adjusting bolt lock nut. Remove heat
protector from frame (right side only). Loosen anchor arm bolt to
release torsion bar tension.
2) Mark front of torsion bar and torque arm for reassembly
reference. Remove anchor arm. See Fig. 1. Remove dust covers from
torsion bar. Remove heat cover (right side only) located between dust
cover and torsion bar. Remove torsion bar.
Inspection
Inspect all splined areas for damage. Inspect dust covers for
cracks and damage. Check for bent anchor arm bolts. Replace components
as necessary.
Installation
1) Apply grease to splined areas of torsion bar, anchor arm,
torque arm splines, anchor arm bolt threads and inside of dust cover.
Check for left and right identification marks on torsion bar ends.
Ensure torsion bars are installed in correct locations.
2) Install torsion bar in torque arm, with identification
mark toward front of vehicle and the slit in the anchor collar facing
downward. Align mark on torque arm with mating mark on torsion bar.
When installing a new torsion bar, align White paint spline with index
mark on front anchor arm.
3) Tighten anchor arm bolt adjusting nut to obtain correct
final bolt protrusion. See FINAL ANCHOR ARM BOLT PROTRUSION table.
Final bolt protrusion depends upon curb weight of vehicle. With
vehicle unladen, measure distance from bump stopper bracket to bump
stopper. Distance should be 0.83-0.91" (21-23 mm) on Montero, 0.7" (1\
8
mm) on Montero Sport. If not, adjust anchor bolt nut.