relay MITSUBISHI MONTERO 1998 User Guide
[x] Cancel search | Manufacturer: MITSUBISHI, Model Year: 1998, Model line: MONTERO, Model: MITSUBISHI MONTERO 1998Pages: 1501, PDF Size: 25.81 MB
Page 132 of 1501
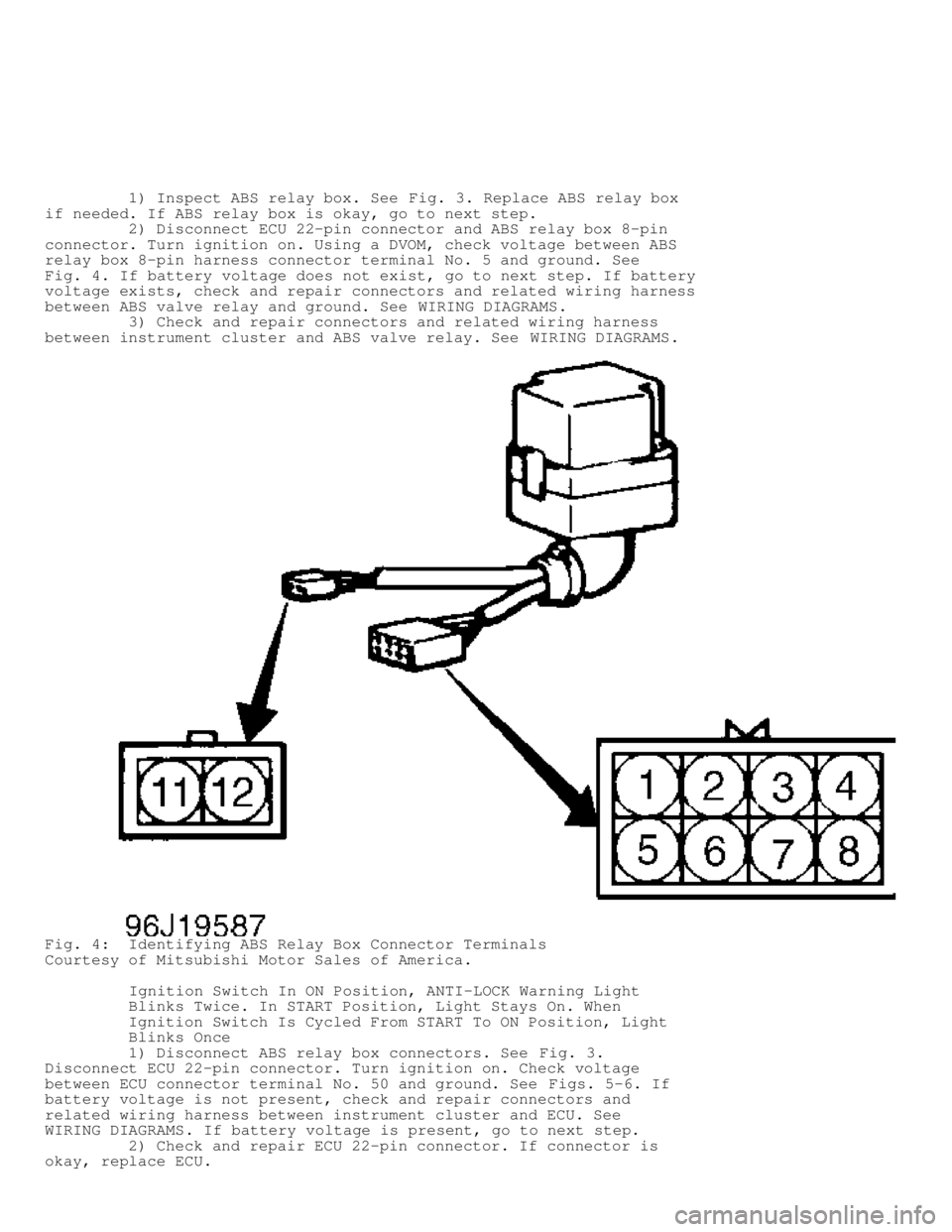
1) Inspect ABS relay box. See Fig. 3. Replace ABS relay box
if needed. If ABS relay box is okay, go to next step.
2) Disconnect ECU 22-pin connector and ABS relay box 8-pin
connector. Turn ignition on. Using a DVOM, check voltage between ABS
relay box 8-pin harness connector terminal No. 5 and ground. See
Fig. 4 . If battery voltage does not exist, go to next step. If battery
voltage exists, check and repair connectors and related wiring harness
between ABS valve relay and ground. See WIRING DIAGRAMS.
3) Check and repair connectors and related wiring harness
between instrument cluster and ABS valve relay. See WIRING DIAGRAMS.
Fig. 4: Identifying ABS Relay Box Connector Terminals
Courtesy of Mitsubishi Motor Sales of America.
Ignition Switch In ON Position, ANTI-LOCK Warning Light
Blinks Twice. In START Position, Light Stays On. When
Ignition Switch Is Cycled From START To ON Position, Light
Blinks Once
1) Disconnect ABS relay box connectors. See Fig. 3.
Disconnect ECU 22-pin connector. Turn ignition on. Check voltage
between ECU connector terminal No. 50 and ground. See Figs. 5-6. If
battery voltage is not present, check and repair connectors and
related wiring harness between instrument cluster and ECU. See
WIRING DIAGRAMS . If battery voltage is present, go to next step.
2) Check and repair ECU 22-pin connector. If connector is
okay, replace ECU.
Page 134 of 1501
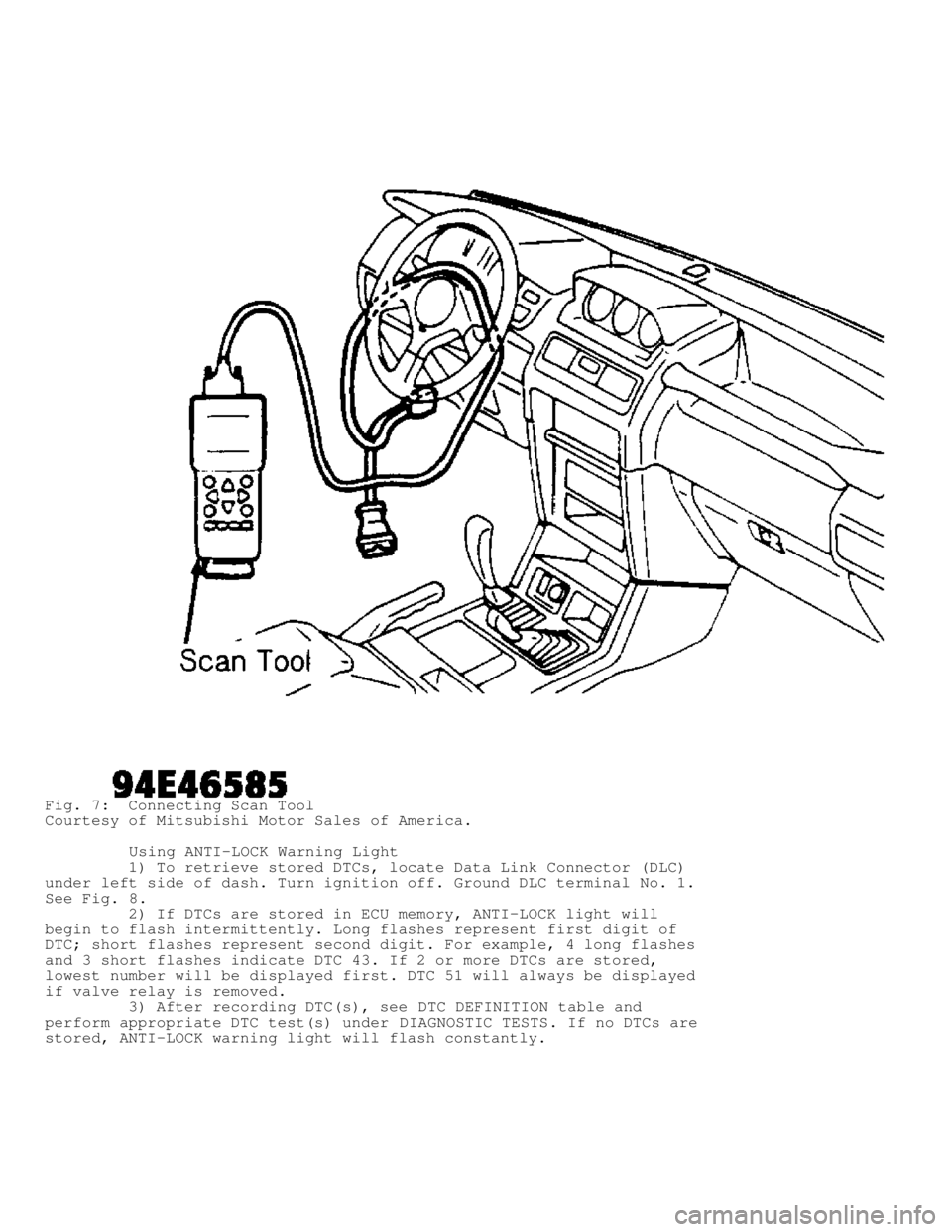
Fig. 7: Connecting Scan Tool
Courtesy of Mitsubishi Motor Sales of America.
Using ANTI-LOCK Warning Light
1) To retrieve stored DTCs, locate Data Link Connector (DLC)\
under left side of dash. Turn ignition off. Ground DLC terminal No. 1.
See Fig. 8 .
2) If DTCs are stored in ECU memory, ANTI-LOCK light will
begin to flash intermittently. Long flashes represent first digit of
DTC; short flashes represent second digit. For example, 4 long flashes
and 3 short flashes indicate DTC 43. If 2 or more DTCs are stored,
lowest number will be displayed first. DTC 51 will always be displayed
if valve relay is removed.
3) After recording DTC(s), see DTC DEFINITION table and
perform appropriate DTC test(s) under DIAGNOSTIC TESTS. If no DTCs are
stored, ANTI-LOCK warning light will flash constantly.
Page 136 of 1501
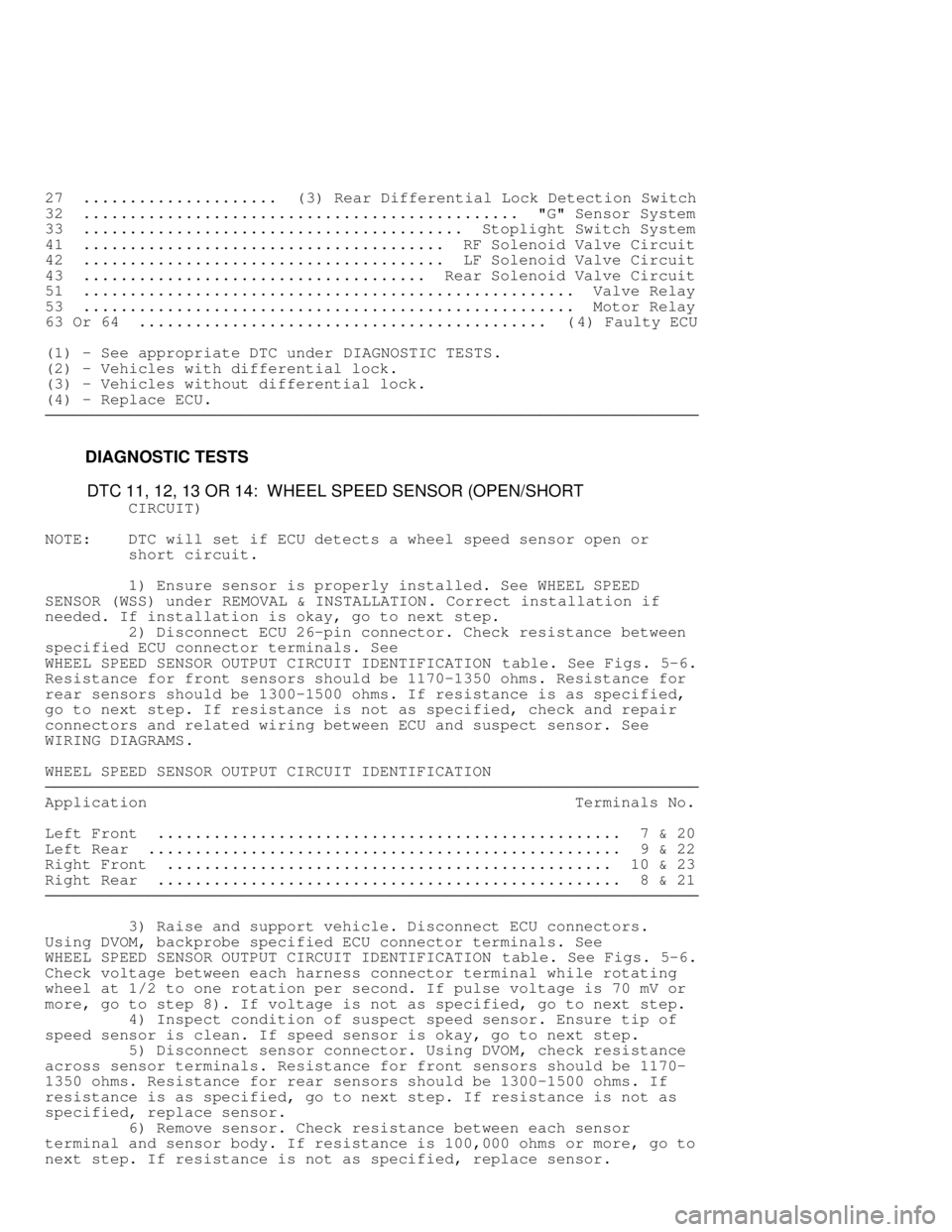
27 ..................... (3) Rear Differential Lock Detection Switch
32 ............................................... "G" Sensor System
33 ......................................... Stoplight Switch System
41 ....................................... RF Solenoid Valve Circuit
42 ....................................... LF Solenoid Valve Circuit
43 ..................................... Rear Solenoid Valve Circuit
51 ..................................................... Valve Relay
53 ..................................................... Motor Relay
63 Or 64 ............................................ ( 4) Faulty ECU
( 1) - See appropriate DTC under DIAGNOSTIC TESTS.
( 2) - Vehicles with differential lock.
( 3) - Vehicles without differential lock.
( 4) - Replace ECU.
\
\
\
\
\
\
\
DIAGNOSTIC TESTS
DTC 11, 12, 13 OR 14: WHEEL SPEED SENSOR (OPEN/SHORT
CIRCUIT)
NOTE: DTC will set if ECU detects a wheel speed sensor open or
short circuit.
1) Ensure sensor is properly installed. See WHEEL SPEED
SENSOR (WSS) under REMOVAL & INSTALLATION . Correct installation if
needed. If installation is okay, go to next step.
2) Disconnect ECU 26-pin connector. Check resistance between
specified ECU connector terminals. See
WHEEL SPEED SENSOR OUTPUT CIRCUIT IDENTIFICATION table. See Figs. 5-6.
Resistance for front sensors should be 1170-1350 ohms. Resistance for
rear sensors should be 1300-1500 ohms. If resistance is as specified,
go to next step. If resistance is not as specified, check and repair
connectors and related wiring between ECU and suspect sensor. See
WIRING DIAGRAMS .
WHEEL SPEED SENSOR OUTPUT CIRCUIT IDENTIFICATION
\
\
\
\
\
\
\
Application Terminals No.
Left Front .................................................. 7 & 20
Left Rear ................................................... 9 & 22
Right Front ................................................ 10 & 23
Right Rear .................................................. 8 & 21
\
\
\
\
\
\
\
3) Raise and support vehicle. Disconnect ECU connectors.
Using DVOM, backprobe specified ECU connector terminals. See
WHEEL SPEED SENSOR OUTPUT CIRCUIT IDENTIFICATION table. See Figs. 5-6.
Check voltage between each harness connector terminal while rotating
wheel at 1/2 to one rotation per second. If pulse voltage is 70 mV or
more, go to step 8). If voltage is not as specified, go to next step.
4) Inspect condition of suspect speed sensor. Ensure tip of
speed sensor is clean. If speed sensor is okay, go to next step.
5) Disconnect sensor connector. Using DVOM, check resistance
across sensor terminals. Resistance for front sensors should be 1170-
1350 ohms. Resistance for rear sensors should be 1300-1500 ohms. If
resistance is as specified, go to next step. If resistance is not as
specified, replace sensor.
6) Remove sensor. Check resistance between each sensor
terminal and sensor body. If resistance is 100,000 ohms or more, go to
next step. If resistance is not as specified, replace sensor.
Page 142 of 1501
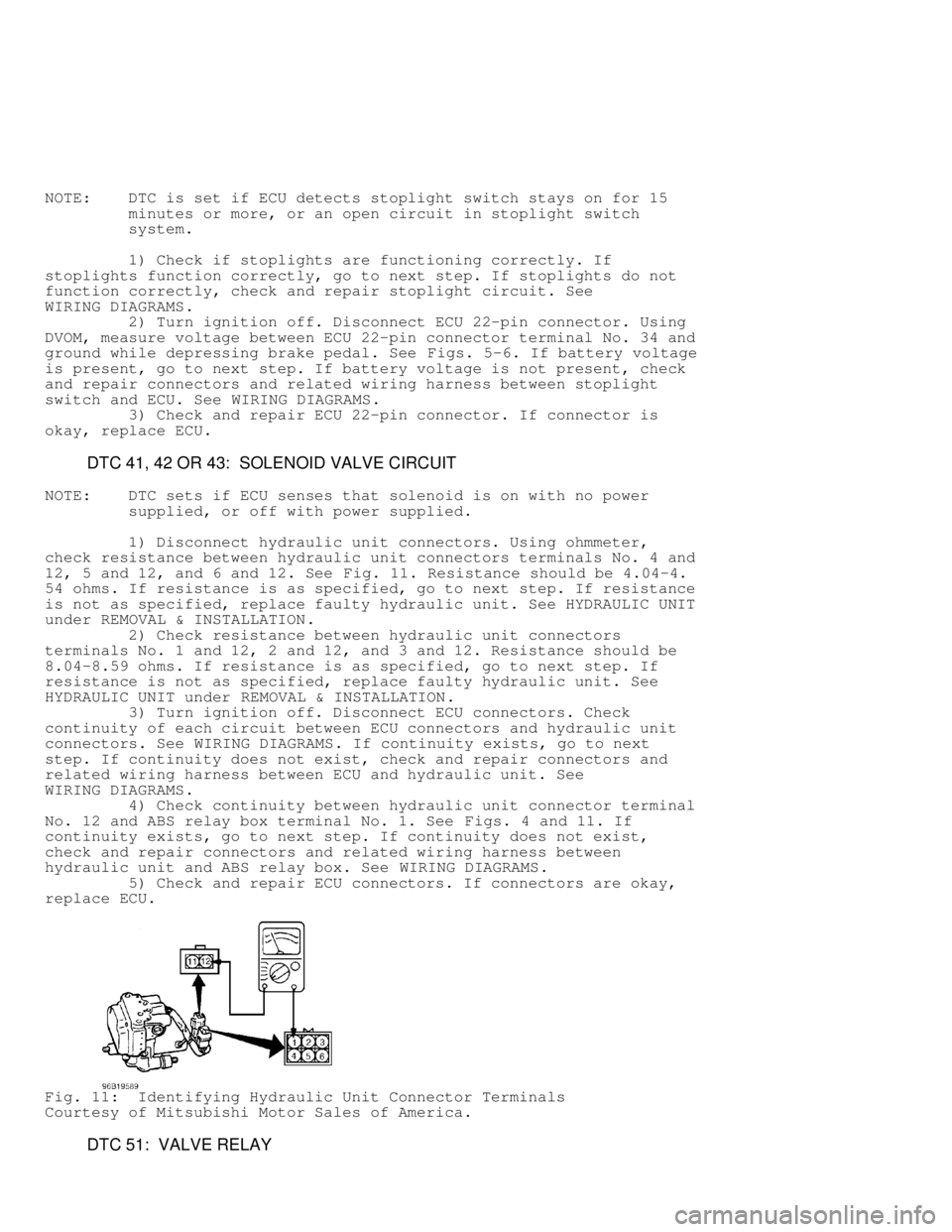
NOTE: DTC is set if ECU detects stoplight switch stays on for 15
minutes or more, or an open circuit in stoplight switch
system.
1) Check if stoplights are functioning correctly. If
stoplights function correctly, go to next step. If stoplights do not
function correctly, check and repair stoplight circuit. See
WIRING DIAGRAMS.
2) Turn ignition off. Disconnect ECU 22-pin connector. Using
DVOM, measure voltage between ECU 22-pin connector terminal No. 34 and
ground while depressing brake pedal. See Figs. 5-6. If battery voltage
is present, go to next step. If battery voltage is not present, check
and repair connectors and related wiring harness between stoplight
switch and ECU. See WIRING DIAGRAMS.
3) Check and repair ECU 22-pin connector. If connector is
okay, replace ECU.
DTC 41, 42 OR 43: SOLENOID VALVE CIRCUIT
NOTE: DTC sets if ECU senses that solenoid is on with no power
supplied, or off with power supplied.
1) Disconnect hydraulic unit connectors. Using ohmmeter,
check resistance between hydraulic unit connectors terminals No. 4 and
12, 5 and 12, and 6 and 12. See Fig. 11. Resistance should be 4.04-4.
54 ohms. If resistance is as specified, go to next step. If resistance
is not as specified, replace faulty hydraulic unit. See HYDRAULIC UNIT
under REMOVAL & INSTALLATION .
2) Check resistance between hydraulic unit connectors
terminals No. 1 and 12, 2 and 12, and 3 and 12. Resistance should be
8.04-8.59 ohms. If resistance is as specified, go to next step. If
resistance is not as specified, replace faulty hydraulic unit. See
HYDRAULIC UNIT under REMOVAL & INSTALLATION .
3) Turn ignition off. Disconnect ECU connectors. Check
continuity of each circuit between ECU connectors and hydraulic unit
connectors. See WIRING DIAGRAMS. If continuity exists, go to next
step. If continuity does not exist, check and repair connectors and
related wiring harness between ECU and hydraulic unit. See
WIRING DIAGRAMS .
4) Check continuity between hydraulic unit connector terminal
No. 12 and ABS relay box terminal No. 1. See Figs. 4 and 11. If
continuity exists, go to next step. If continuity does not exist,
check and repair connectors and related wiring harness between
hydraulic unit and ABS relay box. See WIRING DIAGRAMS.
5) Check and repair ECU connectors. If connectors are okay,
replace ECU.
Fig. 11: Identifying Hydraulic Unit Connector Terminals
Courtesy of Mitsubishi Motor Sales of America.
DTC 51: VALVE RELAY
Page 143 of 1501
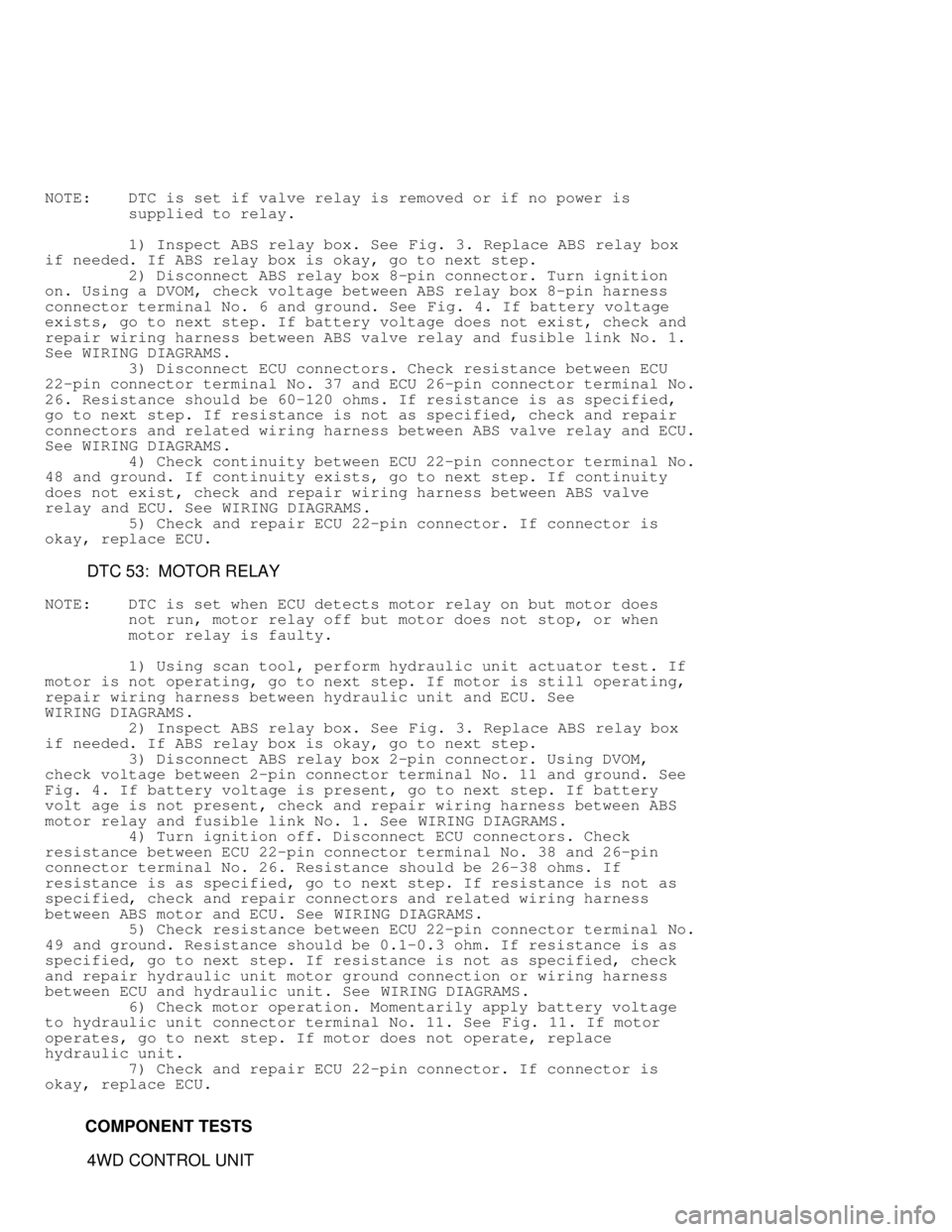
NOTE: DTC is set if valve relay is removed or if no power is
supplied to relay.
1) Inspect ABS relay box. See Fig. 3. Replace ABS relay box
if needed. If ABS relay box is okay, go to next step.
2) Disconnect ABS relay box 8-pin connector. Turn ignition
on. Using a DVOM, check voltage between ABS relay box 8-pin harness
connector terminal No. 6 and ground. See Fig. 4. If battery voltage
exists, go to next step. If battery voltage does not exist, check and
repair wiring harness between ABS valve relay and fusible link No. 1.
See WIRING DIAGRAMS .
3) Disconnect ECU connectors. Check resistance between ECU
22-pin connector terminal No. 37 and ECU 26-pin connector terminal No.
26. Resistance should be 60-120 ohms. If resistance is as specified,
go to next step. If resistance is not as specified, check and repair
connectors and related wiring harness between ABS valve relay and ECU.
See WIRING DIAGRAMS .
4) Check continuity between ECU 22-pin connector terminal No.
48 and ground. If continuity exists, go to next step. If continuity
does not exist, check and repair wiring harness between ABS valve
relay and ECU. See WIRING DIAGRAMS.
5) Check and repair ECU 22-pin connector. If connector is
okay, replace ECU.
DTC 53: MOTOR RELAY
NOTE: DTC is set when ECU detects motor relay on but motor does
not run, motor relay off but motor does not stop, or when
motor relay is faulty.
1) Using scan tool, perform hydraulic unit actuator test. If
motor is not operating, go to next step. If motor is still operating,
repair wiring harness between hydraulic unit and ECU. See
WIRING DIAGRAMS .
2) Inspect ABS relay box. See Fig. 3. Replace ABS relay box
if needed. If ABS relay box is okay, go to next step.
3) Disconnect ABS relay box 2-pin connector. Using DVOM,
check voltage between 2-pin connector terminal No. 11 and ground. See
Fig. 4 . If battery voltage is present, go to next step. If battery
volt age is not present, check and repair wiring harness between ABS
motor relay and fusible link No. 1. See WIRING DIAGRAMS.
4) Turn ignition off. Disconnect ECU connectors. Check
resistance between ECU 22-pin connector terminal No. 38 and 26-pin
connector terminal No. 26. Resistance should be 26-38 ohms. If
resistance is as specified, go to next step. If resistance is not as
specified, check and repair connectors and related wiring harness
between ABS motor and ECU. See WIRING DIAGRAMS.
5) Check resistance between ECU 22-pin connector terminal No.
49 and ground. Resistance should be 0.1-0.3 ohm. If resistance is as
specified, go to next step. If resistance is not as specified, check
and repair hydraulic unit motor ground connection or wiring harness
between ECU and hydraulic unit. See WIRING DIAGRAMS.
6) Check motor operation. Momentarily apply battery voltage
to hydraulic unit connector terminal No. 11. See Fig. 11. If motor
operates, go to next step. If motor does not operate, replace
hydraulic unit.
7) Check and repair ECU 22-pin connector. If connector is
okay, replace ECU.
COMPONENT TESTS
4WD CONTROL UNIT
Page 147 of 1501
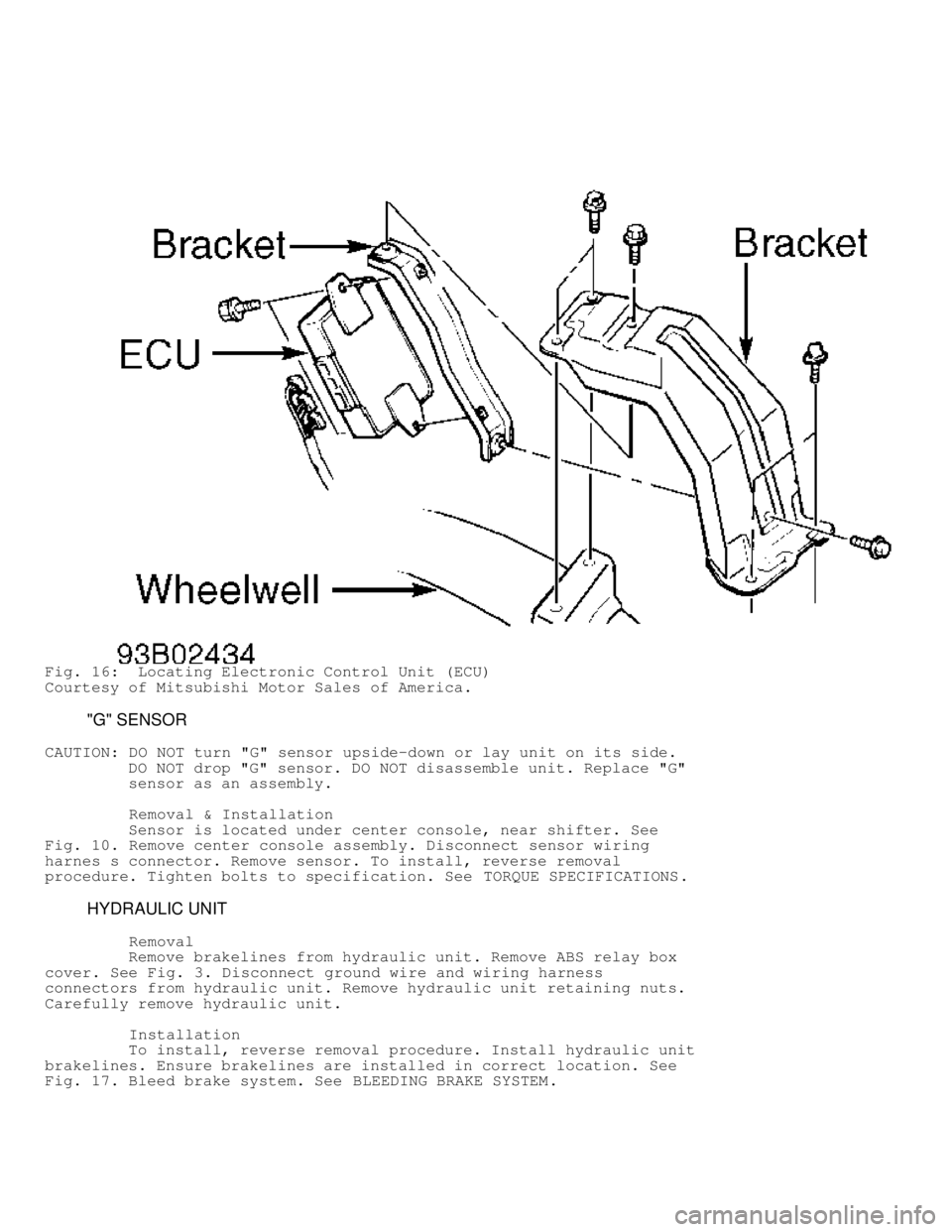
Fig. 16: Locating Electronic Control Unit (ECU)
Courtesy of Mitsubishi Motor Sales of America.
"G" SENSOR
CAUTION: DO NOT turn "G" sensor upside-down or lay unit on its side.
DO NOT drop "G" sensor. DO NOT disassemble unit. Replace "G"
sensor as an assembly.
Removal & Installation
Sensor is located under center console, near shifter. See
Fig. 10 . Remove center console assembly. Disconnect sensor wiring
harnes s connector. Remove sensor. To install, reverse removal
procedure. Tighten bolts to specification. See TORQUE SPECIFICATIONS.
HYDRAULIC UNIT
Removal
Remove brakelines from hydraulic unit. Remove ABS relay box
cover. See Fig. 3. Disconnect ground wire and wiring harness
connectors from hydraulic unit. Remove hydraulic unit retaining nuts.
Carefully remove hydraulic unit.
Installation
To install, reverse removal procedure. Install hydraulic unit
brakelines. Ensure brakelines are installed in correct location. See
Fig. 17. Bleed brake system. See BLEEDING BRAKE SYSTEM.
Page 184 of 1501
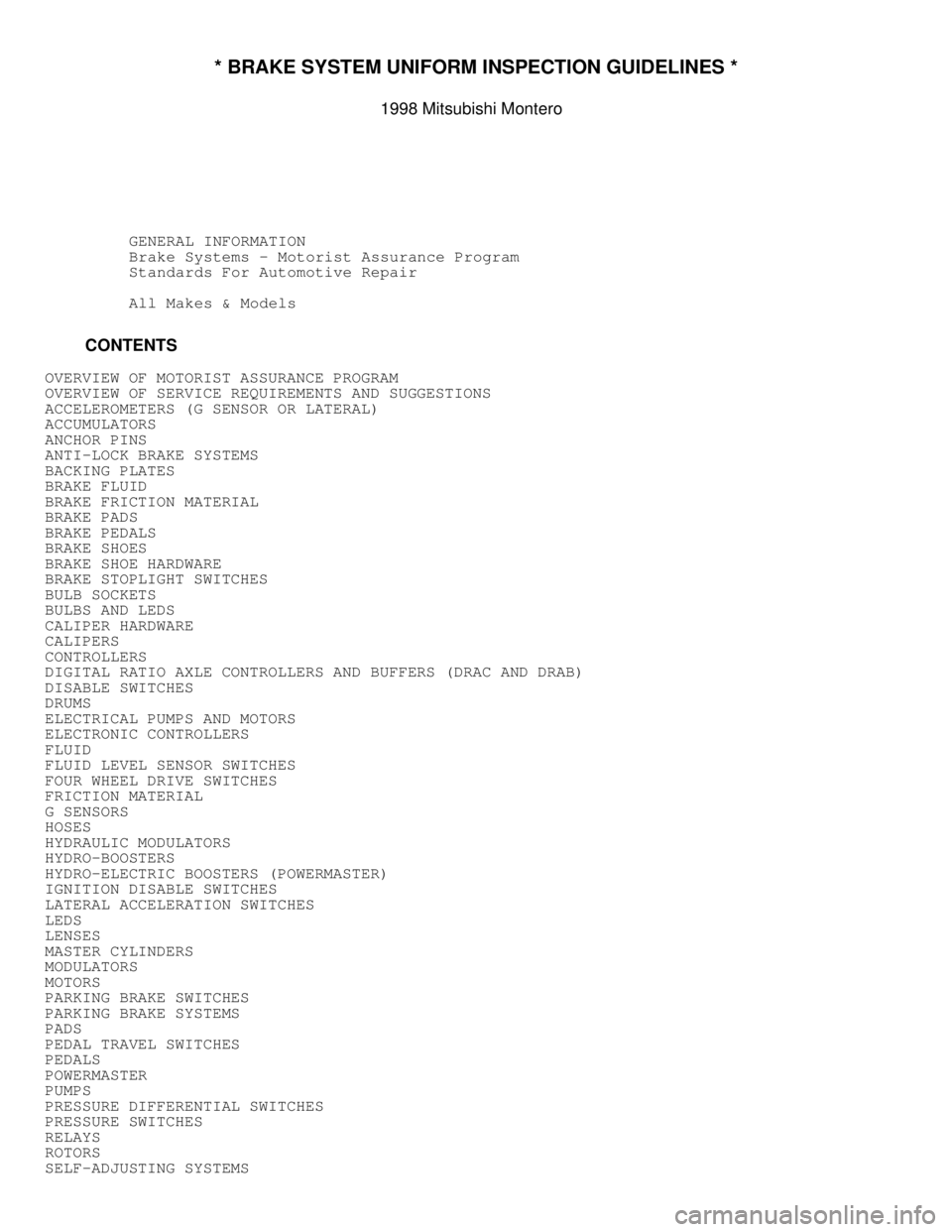
* BRAKE SYSTEM UNIFORM INSPECTION GUIDELINES *
1998 Mitsubishi Montero
GENERAL INFORMATION
Brake Systems - Motorist Assurance Program
Standards For Automotive Repair
All Makes & Models
CONTENTS
OVERVIEW OF MOTORIST ASSURANCE PROGRAM
OVERVIEW OF SERVICE REQUIREMENTS AND SUGGESTIONS
ACCELEROMETERS (G SENSOR OR LATERAL)
ACCUMULATORS
ANCHOR PINS
ANTI-LOCK BRAKE SYSTEMS
BACKING PLATES
BRAKE FLUID
BRAKE FRICTION MATERIAL
BRAKE PADS
BRAKE PEDALS
BRAKE SHOES
BRAKE SHOE HARDWARE
BRAKE STOPLIGHT SWITCHES
BULB SOCKETS
BULBS AND LEDS
CALIPER HARDWARE
CALIPERS
CONTROLLERS
DIGITAL RATIO AXLE CONTROLLERS AND BUFFERS (DRAC AND DRAB)
DISABLE SWITCHES
DRUMS
ELECTRICAL PUMPS AND MOTORS
ELECTRONIC CONTROLLERS
FLUID
FLUID LEVEL SENSOR SWITCHES
FOUR WHEEL DRIVE SWITCHES
FRICTION MATERIAL
G SENSORS
HOSES
HYDRAULIC MODULATORS
HYDRO-BOOSTERS
HYDRO-ELECTRIC BOOSTERS (POWERMASTER)
IGNITION DISABLE SWITCHES
LATERAL ACCELERATION SWITCHES
LEDS
LENSES
MASTER CYLINDERS
MODULATORS
MOTORS
PARKING BRAKE SWITCHES
PARKING BRAKE SYSTEMS
PADS
PEDAL TRAVEL SWITCHES
PEDALS
POWERMASTER
PUMPS
PRESSURE DIFFERENTIAL SWITCHES
PRESSURE SWITCHES
RELAYS
ROTORS
SELF-ADJUSTING SYSTEMS
Page 205 of 1501
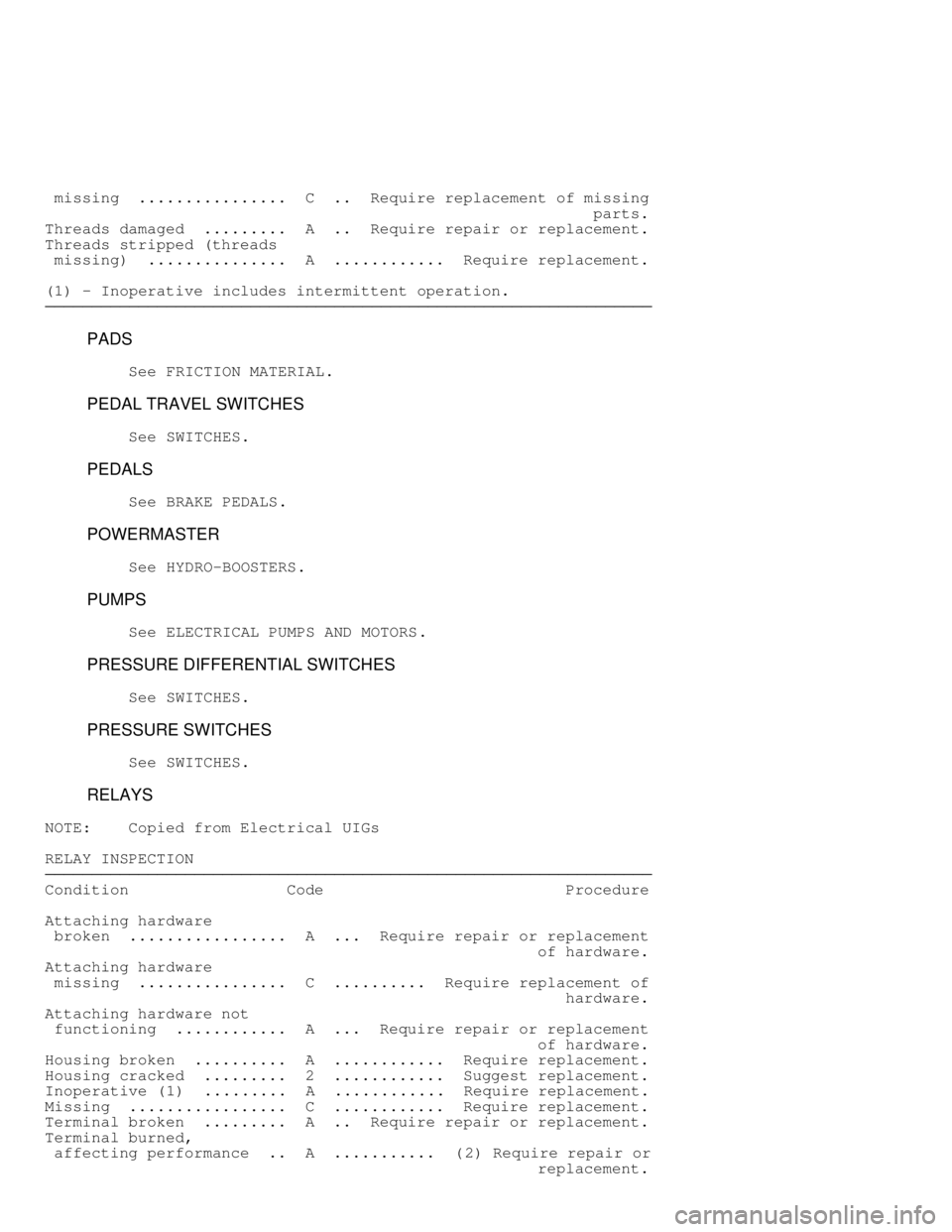
missing ................ C .. Require replacement of missing
parts.
Threads damaged ......... A .. Require repair or replacement.
Threads stripped (threads
missing) ............... A ............ Require replacement.
(1) - Inoperative includes intermittent operation.
\
\
\
\
\
\
\
PADS
See FRICTION MATERIAL .
PEDAL TRAVEL SWITCHES
See SWITCHES.
PEDALS
See BRAKE PEDALS.
POWERMASTER
See HYDRO-BOOSTERS .
PUMPS
See ELECTRICAL PUMPS AND MOTORS .
PRESSURE DIFFERENTIAL SWITCHES
See SWITCHES.
PRESSURE SWITCHES
See SWITCHES.
RELAYS
NOTE: Copied from Electrical UIGs
RELAY INSPECTION
\
\
\
\
\
\
\
Condition Code Procedure
Attaching hardware
broken ................. A ... Require repair or replacement
of hardware.
Attaching hardware
missing ................ C .......... Require replacement of
hardware.
Attaching hardware not
functioning ............ A ... Require repair or replacement
of hardware.
Housing broken .......... A ............ Require replacement.
Housing cracked ......... 2 ............ Suggest replacement.
Inoperative ( 1) ......... A ............ Require replacement.
Missing ................. C ............ Require replacement.
Terminal broken ......... A .. Require repair or replacement.
Terminal burned,
affecting performance .. A ........... ( 2) Require repair or
replacement.
Page 279 of 1501
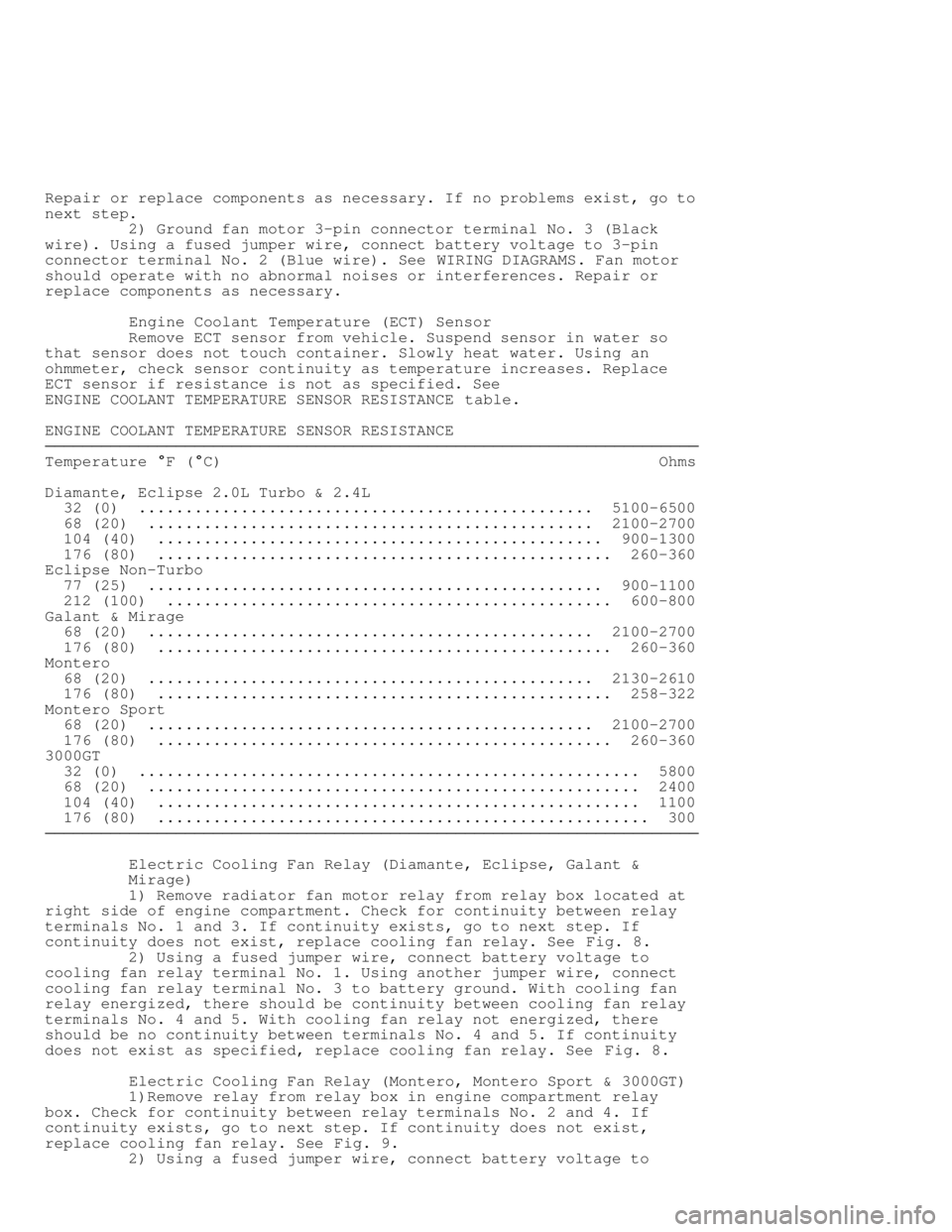
Repair or replace components as necessary. If no problems exist, go to
next step.
2) Ground fan motor 3-pin connector terminal No. 3 (Black
wire). Using a fused jumper wire, connect battery voltage to 3-pin
connector terminal No. 2 (Blue wire). See WIRING DIAGRAMS. Fan motor
should operate with no abnormal noises or interferences. Repair or
replace components as necessary.
Engine Coolant Temperature (ECT) Sensor
Remove ECT sensor from vehicle. Suspend sensor in water so
that sensor does not touch container. Slowly heat water. Using an
ohmmeter, check sensor continuity as temperature increases. Replace
ECT sensor if resistance is not as specified. See
ENGINE COOLANT TEMPERATURE SENSOR RESISTANCE table.
ENGINE COOLANT TEMPERATURE SENSOR RESISTANCE
\
\
\
\
\
\
\
Temperature F (C) Ohms
Diamante, Eclipse 2.0L Turbo & 2.4L
32 (0) ................................................. 5100-6500\
68 (20) ................................................ 2100-2700\
104 (40) ................................................ 900-1300\
176 (80) ................................................. 260-360\
Eclipse Non-Turbo
77 (25) ................................................. 900-1100\
212 (100) ................................................ 600-800\
Galant & Mirage
68 (20) ................................................ 2100-2700\
176 (80) ................................................. 260-360\
Montero
68 (20) ................................................ 2130-2610\
176 (80) ................................................. 258-322\
Montero Sport
68 (20) ................................................ 2100-2700\
176 (80) ................................................. 260-360\
3000GT
32 (0) ...................................................... 5800\
68 (20) ..................................................... 2400\
104 (40) .................................................... 1100\
176 (80) ..................................................... 300\
\
\
\
\
\
\
\
Electric Cooling Fan Relay (Diamante, Eclipse, Galant &
Mirage)
1) Remove radiator fan motor relay from relay box located at
right side of engine compartment. Check for continuity between relay
terminals No. 1 and 3. If continuity exists, go to next step. If
continuity does not exist, replace cooling fan relay. See Fig. 8.
2) Using a fused jumper wire, connect battery voltage to
cooling fan relay terminal No. 1. Using another jumper wire, connect
cooling fan relay terminal No. 3 to battery ground. With cooling fan
relay energized, there should be continuity between cooling fan relay
terminals No. 4 and 5. With cooling fan relay not energized, there
should be no continuity between terminals No. 4 and 5. If continuity
does not exist as specified, replace cooling fan relay. See Fig. 8.
Electric Cooling Fan Relay (Montero, Montero Sport & 3000GT)
1)Remove relay from relay box in engine compartment relay
box. Check for continuity between relay terminals No. 2 and 4. If
continuity exists, go to next step. If continuity does not exist,
replace cooling fan relay. See Fig. 9.
2) Using a fused jumper wire, connect battery voltage to
Page 280 of 1501
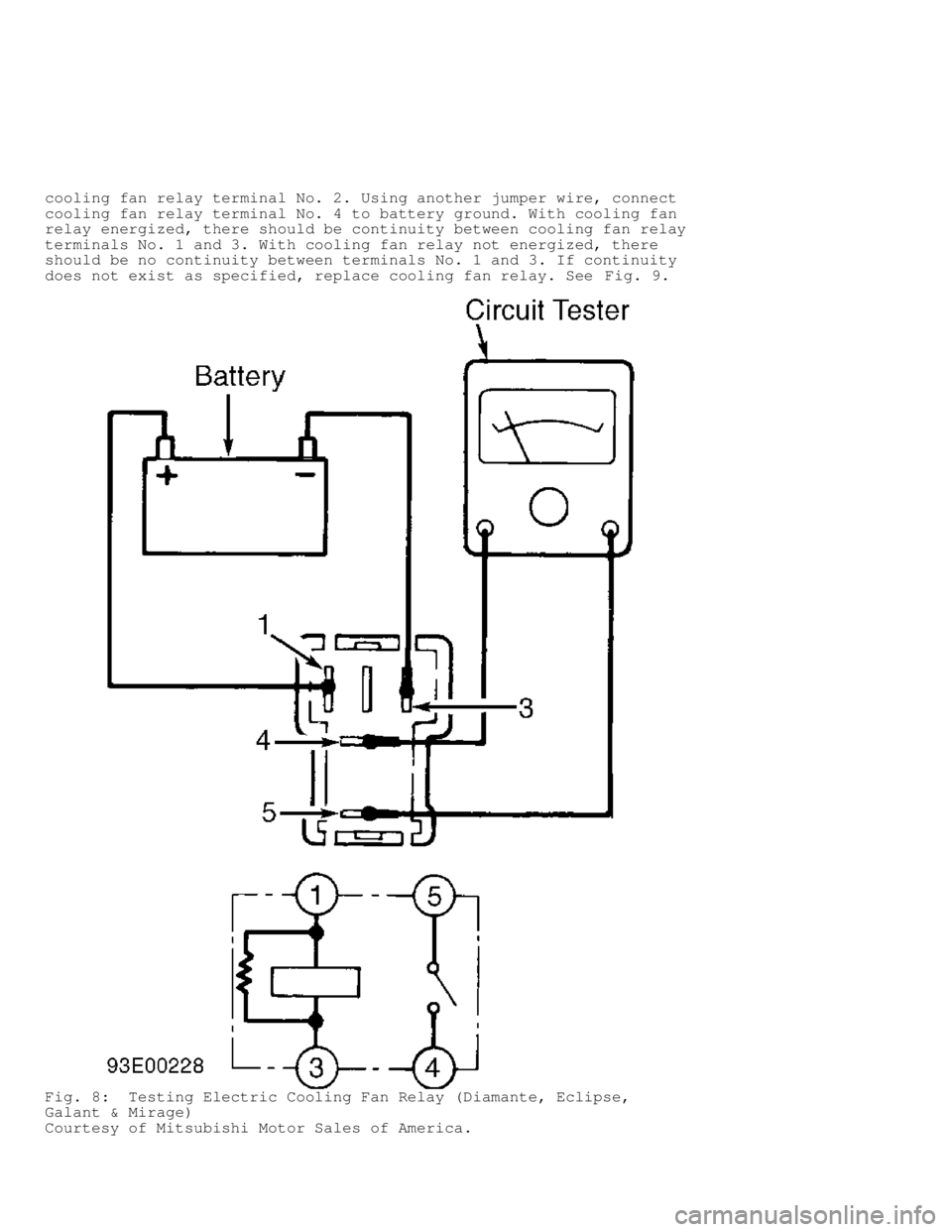
cooling fan relay terminal No. 2. Using another jumper wire, connect
cooling fan relay terminal No. 4 to battery ground. With cooling fan
relay energized, there should be continuity between cooling fan relay
terminals No. 1 and 3. With cooling fan relay not energized, there
should be no continuity between terminals No. 1 and 3. If continuity
does not exist as specified, replace cooling fan relay. See Fig. 9.
Fig. 8: Testing Electric Cooling Fan Relay (Diamante, Eclipse,
Galant & Mirage)
Courtesy of Mitsubishi Motor Sales of America.