NISSAN 350Z 2007 Z33 Engine Control Workshop Manual
Manufacturer: NISSAN, Model Year: 2007, Model line: 350Z, Model: NISSAN 350Z 2007 Z33Pages: 720
Page 191 of 720
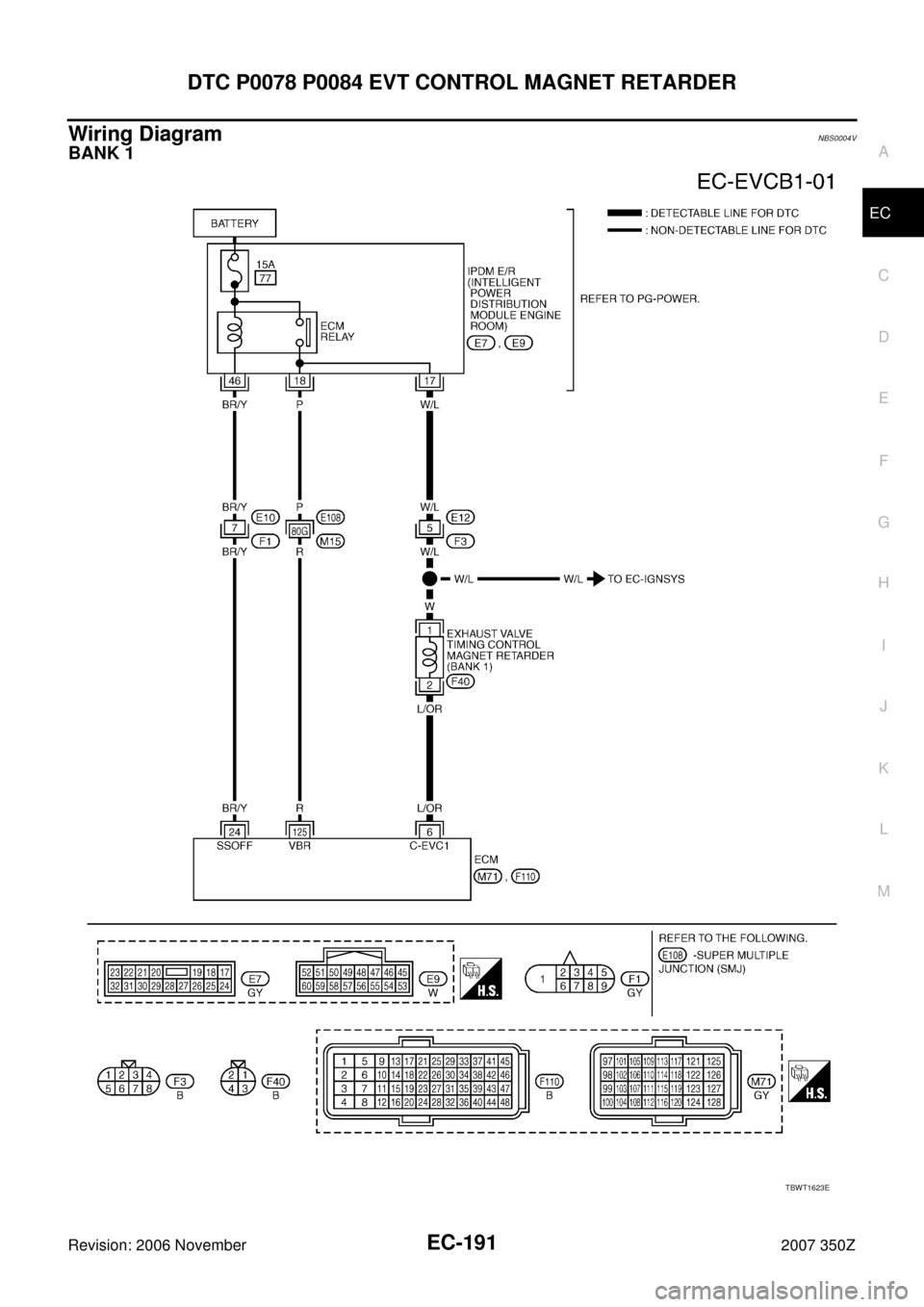
DTC P0078 P0084 EVT CONTROL MAGNET RETARDER
EC-191
C
D
E
F
G
H
I
J
K
L
MA
EC
Revision: 2006 November2007 350Z
Wiring DiagramNBS0004V
BANK 1
TBWT1623E
Page 192 of 720
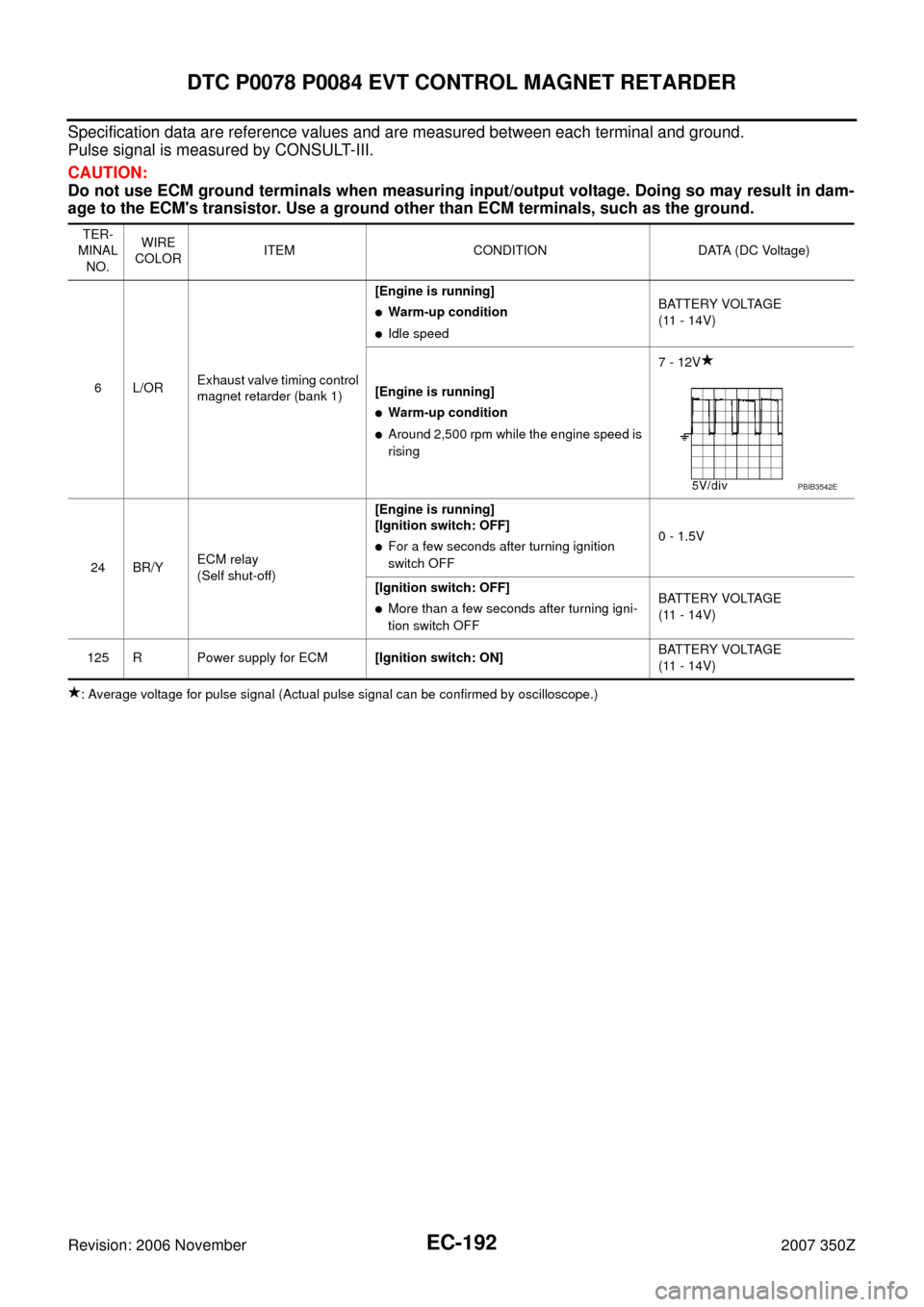
EC-192
DTC P0078 P0084 EVT CONTROL MAGNET RETARDER
Revision: 2006 November2007 350Z
Specification data are reference values and are measured between each terminal and ground.
Pulse signal is measured by CONSULT-III.
CAUTION:
Do not use ECM ground terminals when measuring input/output voltage. Doing so may result in dam-
age to the ECM's transistor. Use a ground other than ECM terminals, such as the ground.
: Average voltage for pulse signal (Actual pulse signal can be confirmed by oscilloscope.)TER-
MINAL
NO.WIRE
COLORITEM CONDITION DATA (DC Voltage)
6 L/ORExhaust valve timing control
magnet retarder (bank 1)[Engine is running]
Warm-up condition
Idle speedBATTERY VOLTAGE
(11 - 14V)
[Engine is running]
Warm-up condition
Around 2,500 rpm while the engine speed is
rising7 - 12V
24 BR/YECM relay
(Self shut-off)[Engine is running]
[Ignition switch: OFF]
For a few seconds after turning ignition
switch OFF0 - 1.5V
[Ignition switch: OFF]
More than a few seconds after turning igni-
tion switch OFFBATTERY VOLTAGE
(11 - 14V)
125 R Power supply for ECM[Ignition switch: ON]BATTERY VOLTAGE
(11 - 14V)
PBIB3542E
Page 193 of 720

DTC P0078 P0084 EVT CONTROL MAGNET RETARDER
EC-193
C
D
E
F
G
H
I
J
K
L
MA
EC
Revision: 2006 November2007 350Z
BANK 2
TBWT1624E
Page 194 of 720
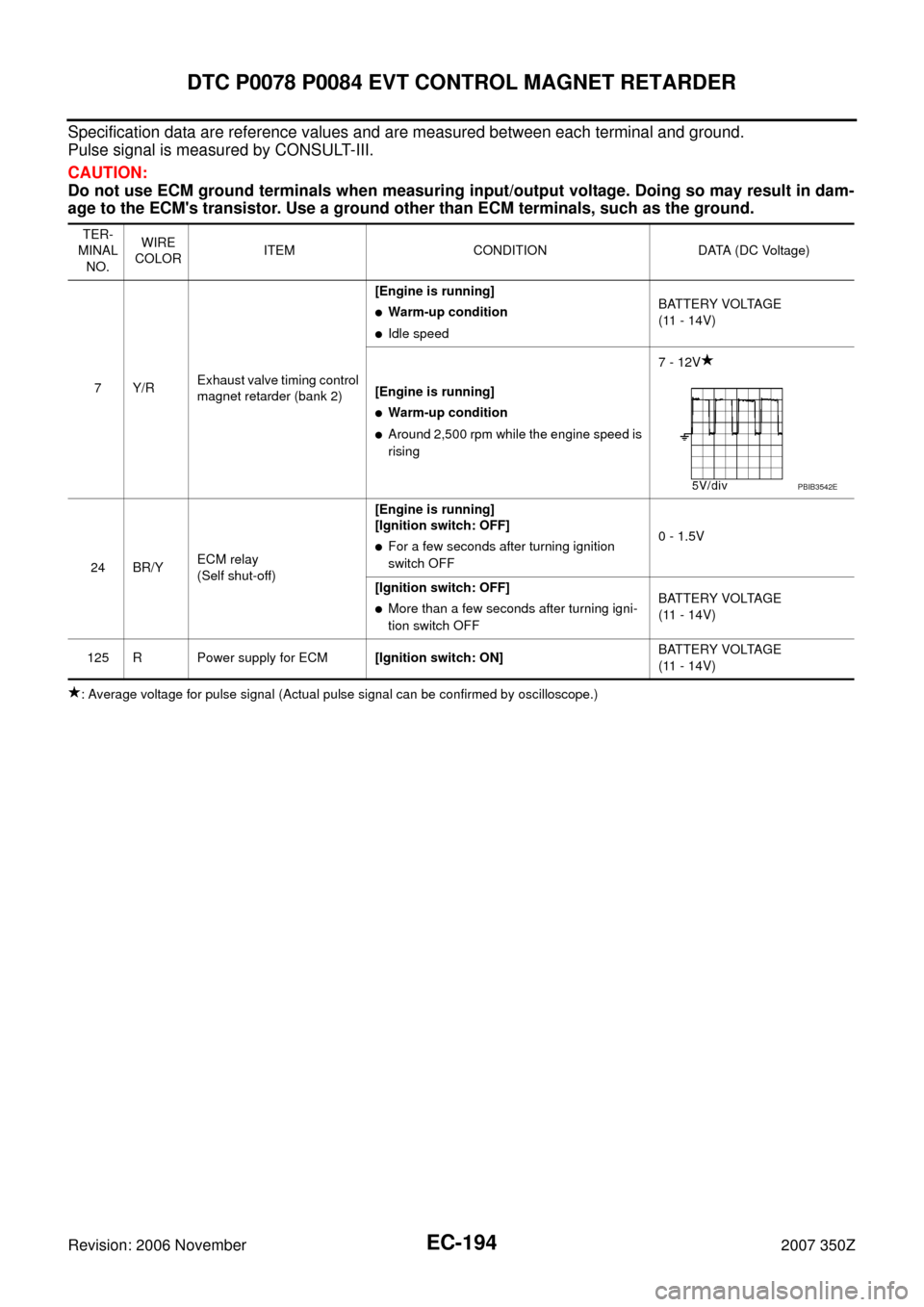
EC-194
DTC P0078 P0084 EVT CONTROL MAGNET RETARDER
Revision: 2006 November2007 350Z
Specification data are reference values and are measured between each terminal and ground.
Pulse signal is measured by CONSULT-III.
CAUTION:
Do not use ECM ground terminals when measuring input/output voltage. Doing so may result in dam-
age to the ECM's transistor. Use a ground other than ECM terminals, such as the ground.
: Average voltage for pulse signal (Actual pulse signal can be confirmed by oscilloscope.)TER-
MINAL
NO.WIRE
COLORITEM CONDITION DATA (DC Voltage)
7Y/RExhaust valve timing control
magnet retarder (bank 2)[Engine is running]
Warm-up condition
Idle speedBATTERY VOLTAGE
(11 - 14V)
[Engine is running]
Warm-up condition
Around 2,500 rpm while the engine speed is
rising7 - 12V
24 BR/YECM relay
(Self shut-off)[Engine is running]
[Ignition switch: OFF]
For a few seconds after turning ignition
switch OFF0 - 1.5V
[Ignition switch: OFF]
More than a few seconds after turning igni-
tion switch OFFBATTERY VOLTAGE
(11 - 14V)
125 R Power supply for ECM[Ignition switch: ON]BATTERY VOLTAGE
(11 - 14V)
PBIB3542E
Page 195 of 720
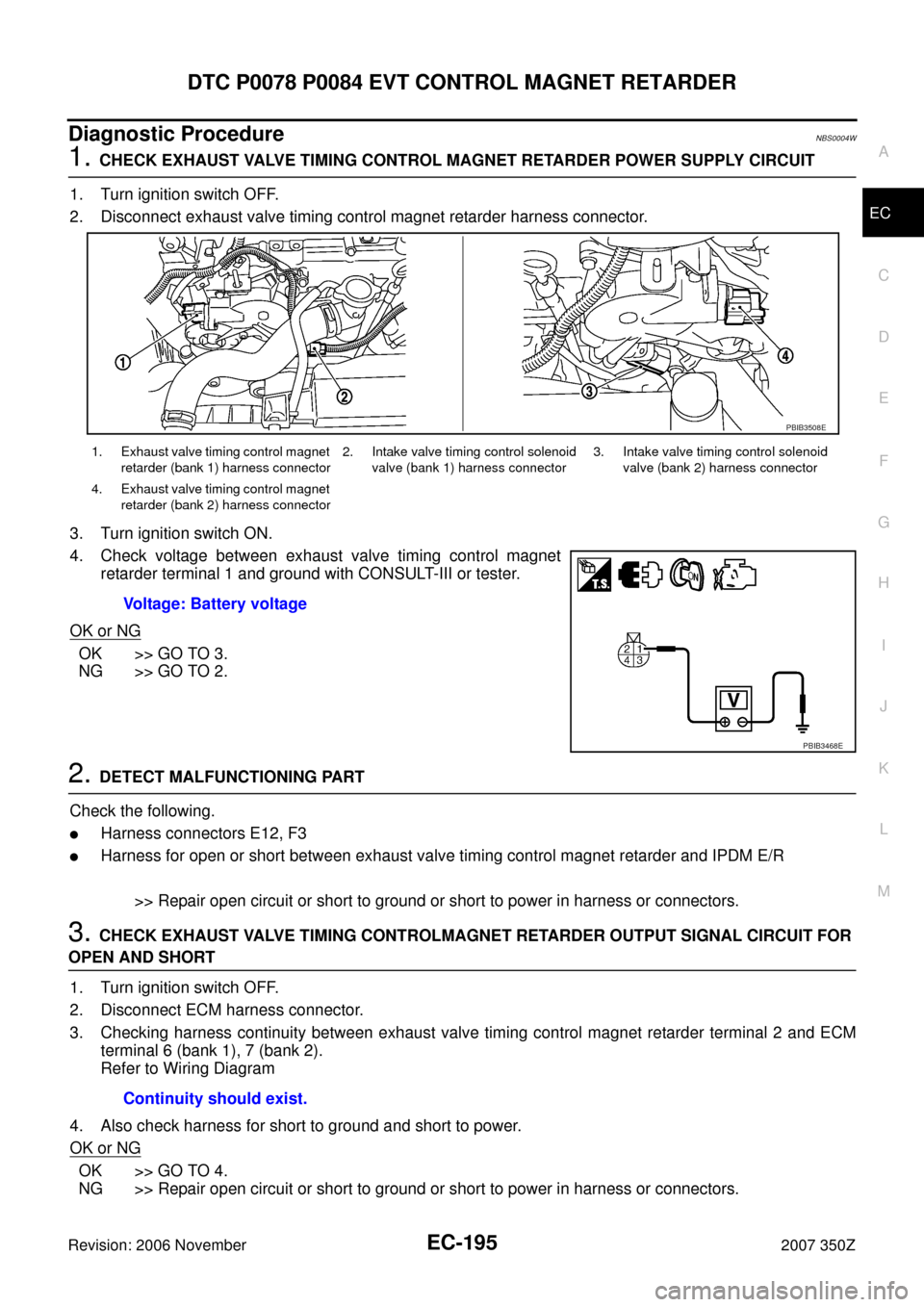
DTC P0078 P0084 EVT CONTROL MAGNET RETARDER
EC-195
C
D
E
F
G
H
I
J
K
L
MA
EC
Revision: 2006 November2007 350Z
Diagnostic ProcedureNBS0004W
1. CHECK EXHAUST VALVE TIMING CONTROL MAGNET RETARDER POWER SUPPLY CIRCUIT
1. Turn ignition switch OFF.
2. Disconnect exhaust valve timing control magnet retarder harness connector.
3. Turn ignition switch ON.
4. Check voltage between exhaust valve timing control magnet
retarder terminal 1 and ground with CONSULT-III or tester.
OK or NG
OK >> GO TO 3.
NG >> GO TO 2.
2. DETECT MALFUNCTIONING PART
Check the following.
Harness connectors E12, F3
Harness for open or short between exhaust valve timing control magnet retarder and IPDM E/R
>> Repair open circuit or short to ground or short to power in harness or connectors.
3. CHECK EXHAUST VALVE TIMING CONTROLMAGNET RETARDER OUTPUT SIGNAL CIRCUIT FOR
OPEN AND SHORT
1. Turn ignition switch OFF.
2. Disconnect ECM harness connector.
3. Checking harness continuity between exhaust valve timing control magnet retarder terminal 2 and ECM
terminal 6 (bank 1), 7 (bank 2).
Refer to Wiring Diagram
4. Also check harness for short to ground and short to power.
OK or NG
OK >> GO TO 4.
NG >> Repair open circuit or short to ground or short to power in harness or connectors.
1. Exhaust valve timing control magnet
retarder (bank 1) harness connector2. Intake valve timing control solenoid
valve (bank 1) harness connector3. Intake valve timing control solenoid
valve (bank 2) harness connector
4. Exhaust valve timing control magnet
retarder (bank 2) harness connector
Voltage: Battery voltage
PBIB3508E
PBIB3468E
Continuity should exist.
Page 196 of 720
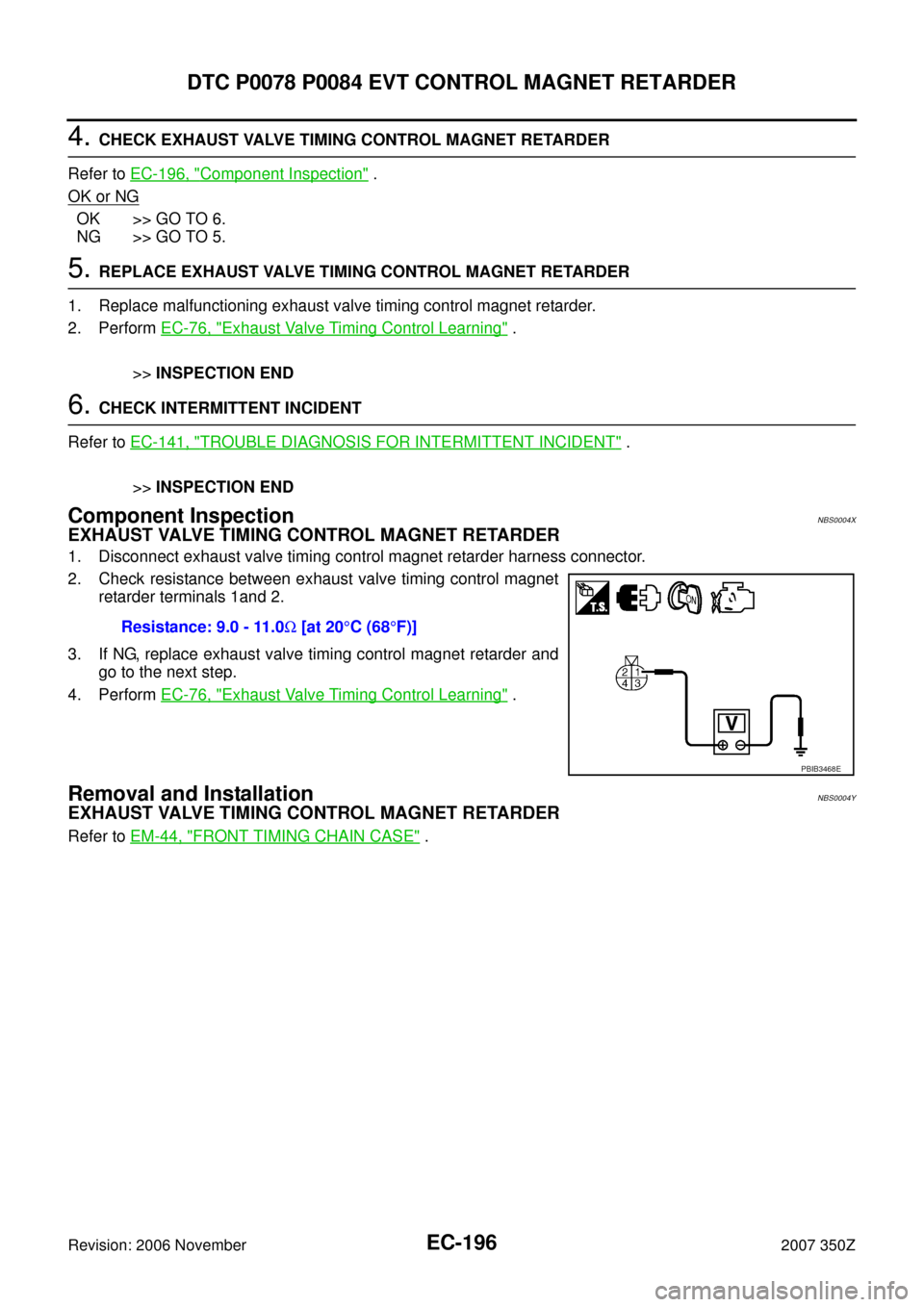
EC-196
DTC P0078 P0084 EVT CONTROL MAGNET RETARDER
Revision: 2006 November2007 350Z
4. CHECK EXHAUST VALVE TIMING CONTROL MAGNET RETARDER
Refer to EC-196, "
Component Inspection" .
OK or NG
OK >> GO TO 6.
NG >> GO TO 5.
5. REPLACE EXHAUST VALVE TIMING CONTROL MAGNET RETARDER
1. Replace malfunctioning exhaust valve timing control magnet retarder.
2. Perform EC-76, "
Exhaust Valve Timing Control Learning" .
>>INSPECTION END
6. CHECK INTERMITTENT INCIDENT
Refer to EC-141, "
TROUBLE DIAGNOSIS FOR INTERMITTENT INCIDENT" .
>>INSPECTION END
Component InspectionNBS0004X
EXHAUST VALVE TIMING CONTROL MAGNET RETARDER
1. Disconnect exhaust valve timing control magnet retarder harness connector.
2. Check resistance between exhaust valve timing control magnet
retarder terminals 1and 2.
3. If NG, replace exhaust valve timing control magnet retarder and
go to the next step.
4. Perform EC-76, "
Exhaust Valve Timing Control Learning" .
Removal and InstallationNBS0004Y
EXHAUST VALVE TIMING CONTROL MAGNET RETARDER
Refer to EM-44, "FRONT TIMING CHAIN CASE" . Resistance: 9.0 - 11.0Ω [at 20°C (68°F)]
PBIB3468E
Page 197 of 720
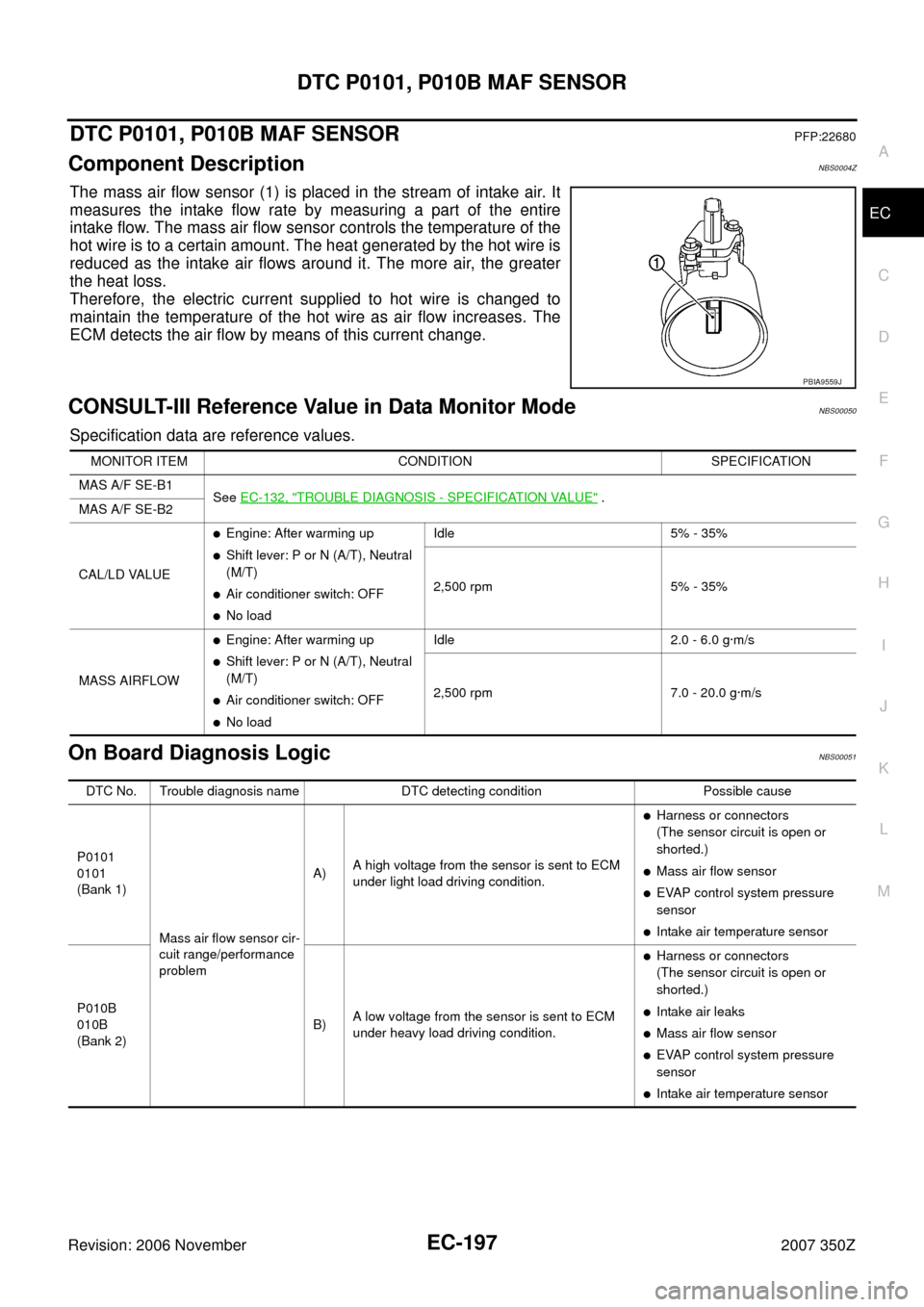
DTC P0101, P010B MAF SENSOR
EC-197
C
D
E
F
G
H
I
J
K
L
MA
EC
Revision: 2006 November2007 350Z
DTC P0101, P010B MAF SENSORPFP:22680
Component DescriptionNBS0004Z
The mass air flow sensor (1) is placed in the stream of intake air. It
measures the intake flow rate by measuring a part of the entire
intake flow. The mass air flow sensor controls the temperature of the
hot wire is to a certain amount. The heat generated by the hot wire is
reduced as the intake air flows around it. The more air, the greater
the heat loss.
Therefore, the electric current supplied to hot wire is changed to
maintain the temperature of the hot wire as air flow increases. The
ECM detects the air flow by means of this current change.
CONSULT-III Reference Value in Data Monitor ModeNBS00050
Specification data are reference values.
On Board Diagnosis LogicNBS00051
PBIA9559J
MONITOR ITEM CONDITION SPECIFICATION
MAS A/F SE-B1
See EC-132, "
TROUBLE DIAGNOSIS - SPECIFICATION VALUE" .
MAS A/F SE-B2
CAL/LD VALUE
Engine: After warming up
Shift lever: P or N (A/T), Neutral
(M/T)
Air conditioner switch: OFF
No loadIdle 5% - 35%
2,500 rpm 5% - 35%
MASS AIRFLOW
Engine: After warming up
Shift lever: P or N (A/T), Neutral
(M/T)
Air conditioner switch: OFF
No loadIdle 2.0 - 6.0 g·m/s
2,500 rpm 7.0 - 20.0 g·m/s
DTC No. Trouble diagnosis name DTC detecting condition Possible cause
P0101
0101
(Bank 1)
Mass air flow sensor cir-
cuit range/performance
problemA)A high voltage from the sensor is sent to ECM
under light load driving condition.
Harness or connectors
(The sensor circuit is open or
shorted.)
Mass air flow sensor
EVAP control system pressure
sensor
Intake air temperature sensor
P010B
010B
(Bank 2)B)A low voltage from the sensor is sent to ECM
under heavy load driving condition.
Harness or connectors
(The sensor circuit is open or
shorted.)
Intake air leaks
Mass air flow sensor
EVAP control system pressure
sensor
Intake air temperature sensor
Page 198 of 720
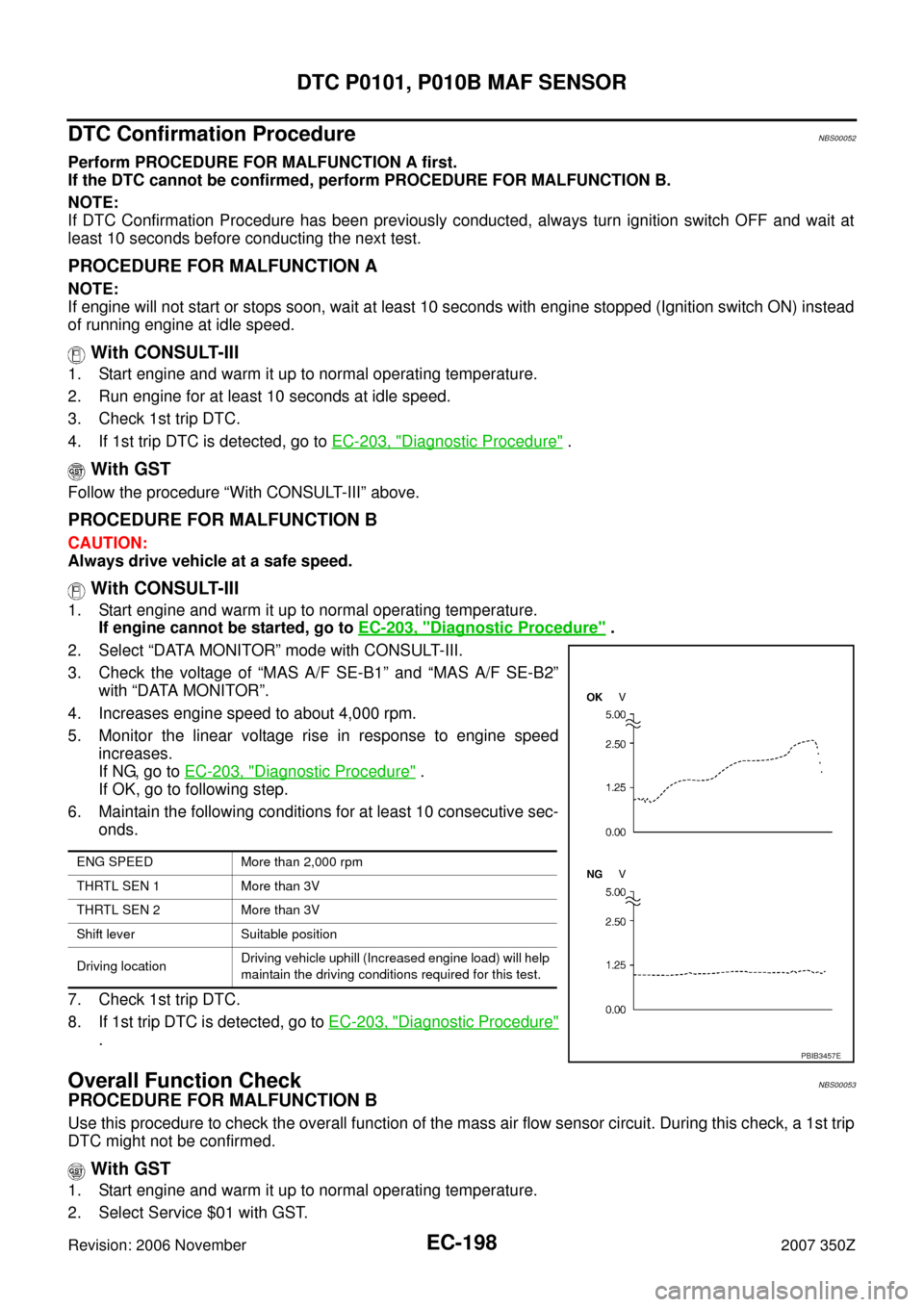
EC-198
DTC P0101, P010B MAF SENSOR
Revision: 2006 November2007 350Z
DTC Confirmation ProcedureNBS00052
Perform PROCEDURE FOR MALFUNCTION A first.
If the DTC cannot be confirmed, perform PROCEDURE FOR MALFUNCTION B.
NOTE:
If DTC Confirmation Procedure has been previously conducted, always turn ignition switch OFF and wait at
least 10 seconds before conducting the next test.
PROCEDURE FOR MALFUNCTION A
NOTE:
If engine will not start or stops soon, wait at least 10 seconds with engine stopped (Ignition switch ON) instead
of running engine at idle speed.
With CONSULT-III
1. Start engine and warm it up to normal operating temperature.
2. Run engine for at least 10 seconds at idle speed.
3. Check 1st trip DTC.
4. If 1st trip DTC is detected, go to EC-203, "
Diagnostic Procedure" .
With GST
Follow the procedure “With CONSULT-III” above.
PROCEDURE FOR MALFUNCTION B
CAUTION:
Always drive vehicle at a safe speed.
With CONSULT-III
1. Start engine and warm it up to normal operating temperature.
If engine cannot be started, go to EC-203, "
Diagnostic Procedure" .
2. Select “DATA MONITOR” mode with CONSULT-III.
3. Check the voltage of “MAS A/F SE-B1” and “MAS A/F SE-B2”
with “DATA MONITOR”.
4. Increases engine speed to about 4,000 rpm.
5. Monitor the linear voltage rise in response to engine speed
increases.
If NG, go to EC-203, "
Diagnostic Procedure" .
If OK, go to following step.
6. Maintain the following conditions for at least 10 consecutive sec-
onds.
7. Check 1st trip DTC.
8. If 1st trip DTC is detected, go to EC-203, "
Diagnostic Procedure"
.
Overall Function CheckNBS00053
PROCEDURE FOR MALFUNCTION B
Use this procedure to check the overall function of the mass air flow sensor circuit. During this check, a 1st trip
DTC might not be confirmed.
With GST
1. Start engine and warm it up to normal operating temperature.
2. Select Service $01 with GST.
ENG SPEED More than 2,000 rpm
THRTL SEN 1 More than 3V
THRTL SEN 2 More than 3V
Shift lever Suitable position
Driving locationDriving vehicle uphill (Increased engine load) will help
maintain the driving conditions required for this test.
PBIB3457E
Page 199 of 720
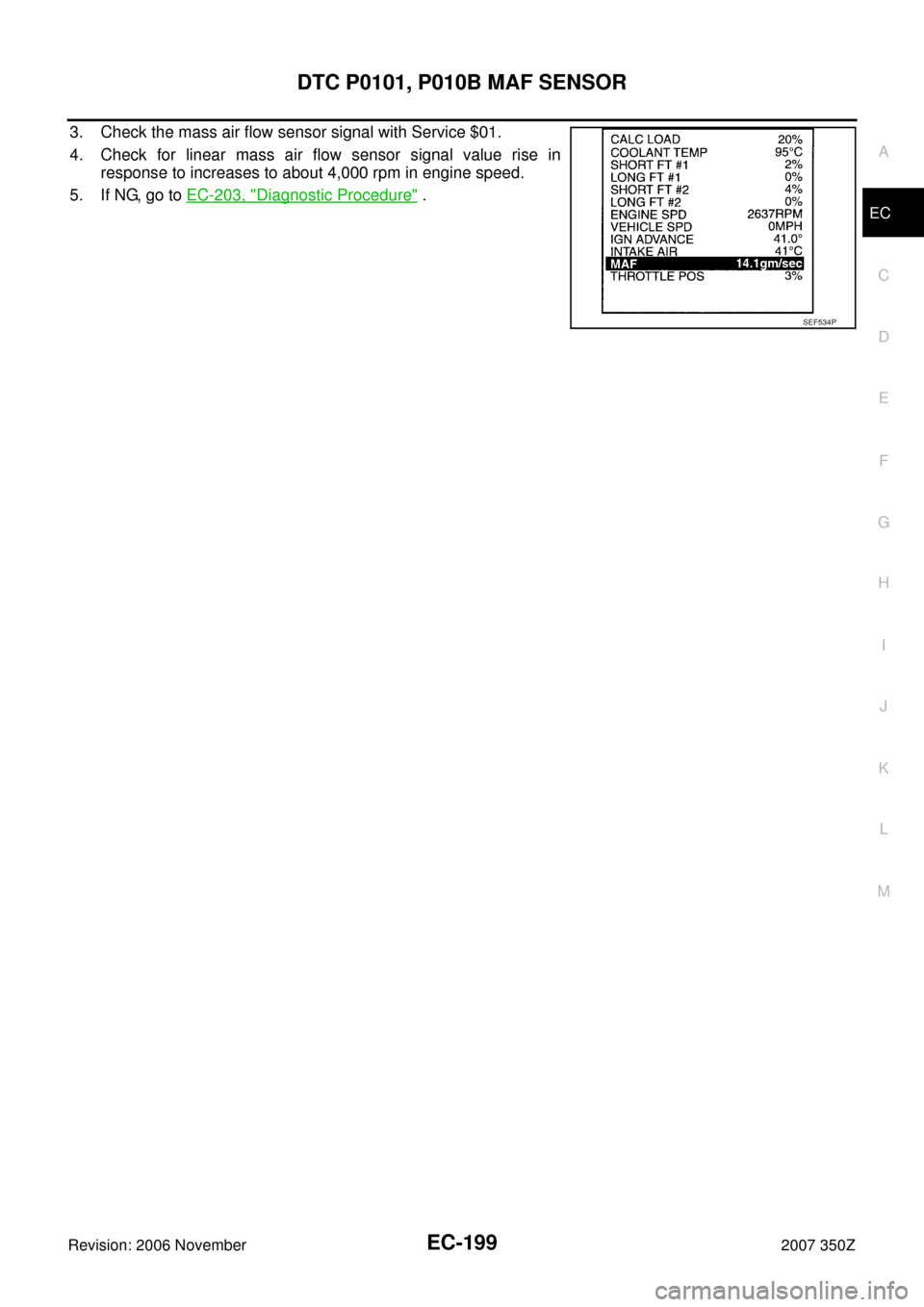
DTC P0101, P010B MAF SENSOR
EC-199
C
D
E
F
G
H
I
J
K
L
MA
EC
Revision: 2006 November2007 350Z
3. Check the mass air flow sensor signal with Service $01.
4. Check for linear mass air flow sensor signal value rise in
response to increases to about 4,000 rpm in engine speed.
5. If NG, go to EC-203, "
Diagnostic Procedure" .
SEF534P
Page 200 of 720
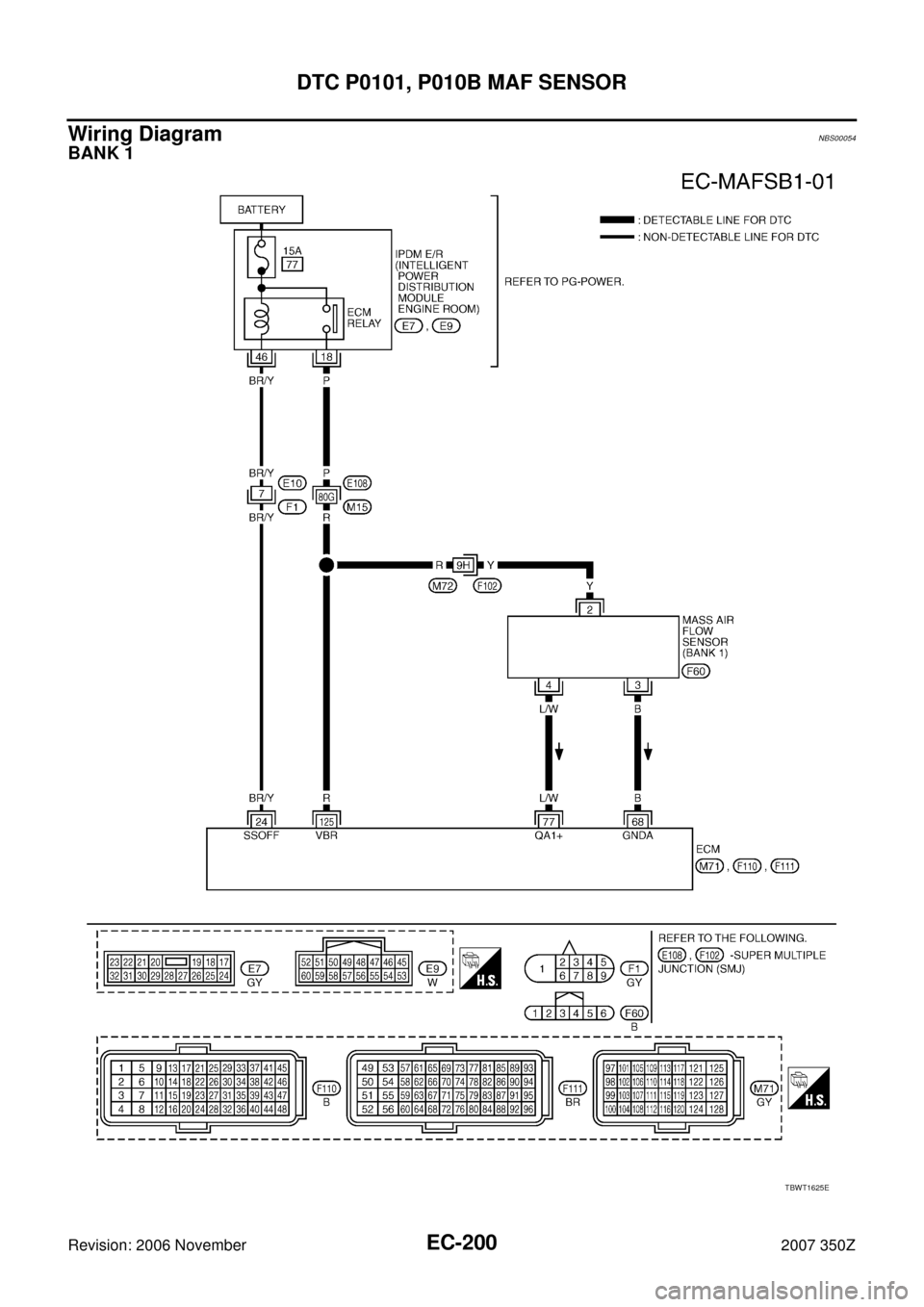
EC-200
DTC P0101, P010B MAF SENSOR
Revision: 2006 November2007 350Z
Wiring DiagramNBS00054
BANK 1
TBWT1625E