NISSAN ALMERA TINO 2001 Service Repair Manual
Manufacturer: NISSAN, Model Year: 2001, Model line: ALMERA TINO, Model: NISSAN ALMERA TINO 2001Pages: 3051, PDF Size: 46.38 MB
Page 3031 of 3051
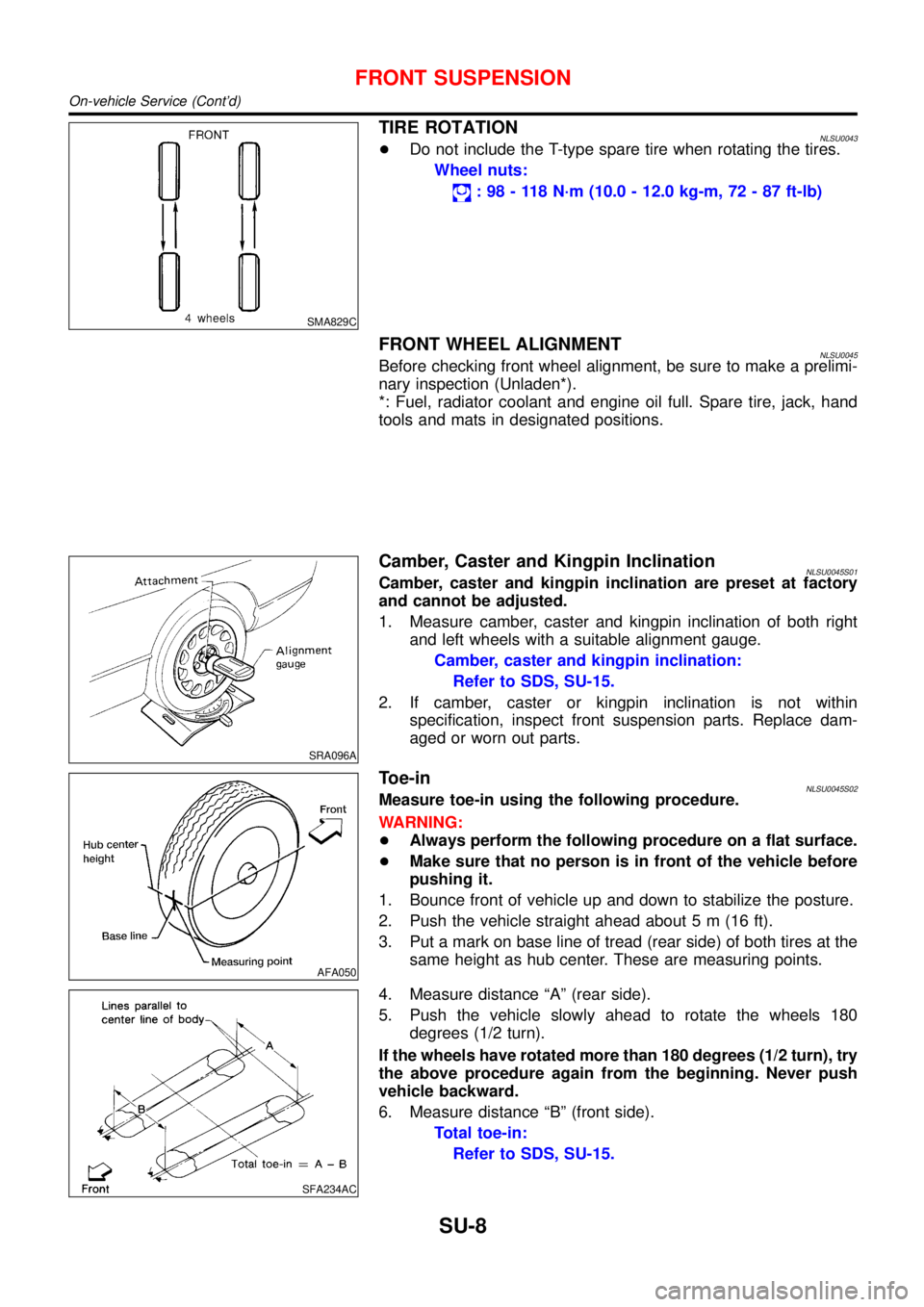
SMA829C
TIRE ROTATIONNLSU0043+Do not include the T-type spare tire when rotating the tires.
Wheel nuts:
:98-118N·m (10.0 - 12.0 kg-m, 72 - 87 ft-lb)
FRONT WHEEL ALIGNMENTNLSU0045Before checking front wheel alignment, be sure to make a prelimi-
nary inspection (Unladen*).
*: Fuel, radiator coolant and engine oil full. Spare tire, jack, hand
tools and mats in designated positions.
SRA096A
Camber, Caster and Kingpin InclinationNLSU0045S01Camber, caster and kingpin inclination are preset at factory
and cannot be adjusted.
1. Measure camber, caster and kingpin inclination of both right
and left wheels with a suitable alignment gauge.
Camber, caster and kingpin inclination:
Refer to SDS, SU-15.
2. If camber, caster or kingpin inclination is not within
specification, inspect front suspension parts. Replace dam-
aged or worn out parts.
AFA050
Toe-inNLSU0045S02Measure toe-in using the following procedure.
WARNING:
+Always perform the following procedure on a flat surface.
+Make sure that no person is in front of the vehicle before
pushing it.
1. Bounce front of vehicle up and down to stabilize the posture.
2. Push the vehicle straight ahead about 5 m (16 ft).
3. Put a mark on base line of tread (rear side) of both tires at the
same height as hub center. These are measuring points.
SFA234AC
4. Measure distance“A”(rear side).
5. Push the vehicle slowly ahead to rotate the wheels 180
degrees (1/2 turn).
If the wheels have rotated more than 180 degrees (1/2 turn), try
the above procedure again from the beginning. Never push
vehicle backward.
6. Measure distance“B”(front side).
Total toe-in:
Refer to SDS, SU-15.
FRONT SUSPENSION
On-vehicle Service (Cont’d)
SU-8
Page 3032 of 3051
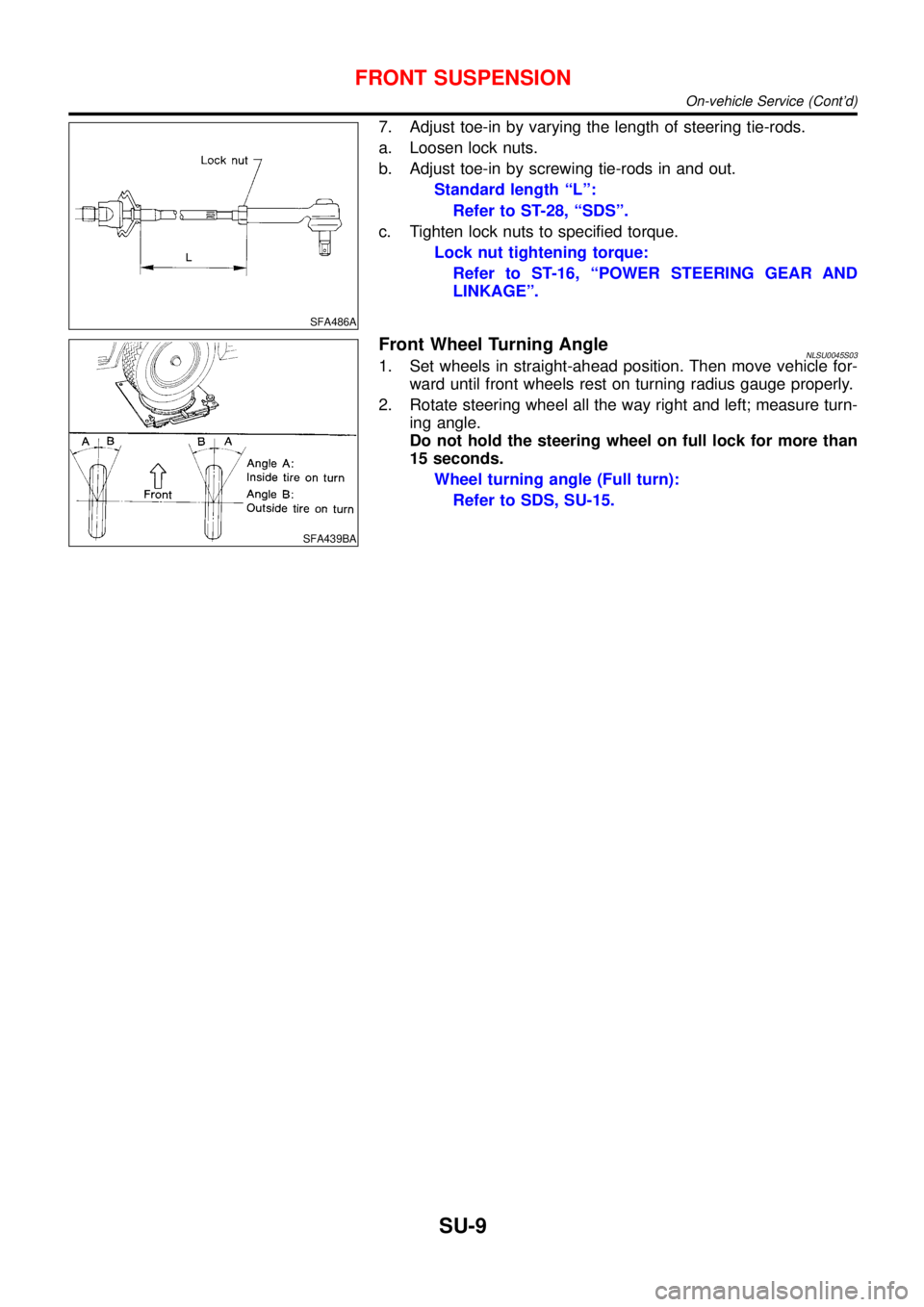
SFA486A
7. Adjust toe-in by varying the length of steering tie-rods.
a. Loosen lock nuts.
b. Adjust toe-in by screwing tie-rods in and out.
Standard length“L”:
Refer to ST-28,“SDS”.
c. Tighten lock nuts to specified torque.
Lock nut tightening torque:
Refer to ST-16,“POWER STEERING GEAR AND
LINKAGE”.
SFA439BA
Front Wheel Turning AngleNLSU0045S031. Set wheels in straight-ahead position. Then move vehicle for-
ward until front wheels rest on turning radius gauge properly.
2. Rotate steering wheel all the way right and left; measure turn-
ing angle.
Do not hold the steering wheel on full lock for more than
15 seconds.
Wheel turning angle (Full turn):
Refer to SDS, SU-15.
FRONT SUSPENSION
On-vehicle Service (Cont’d)
SU-9
Page 3033 of 3051
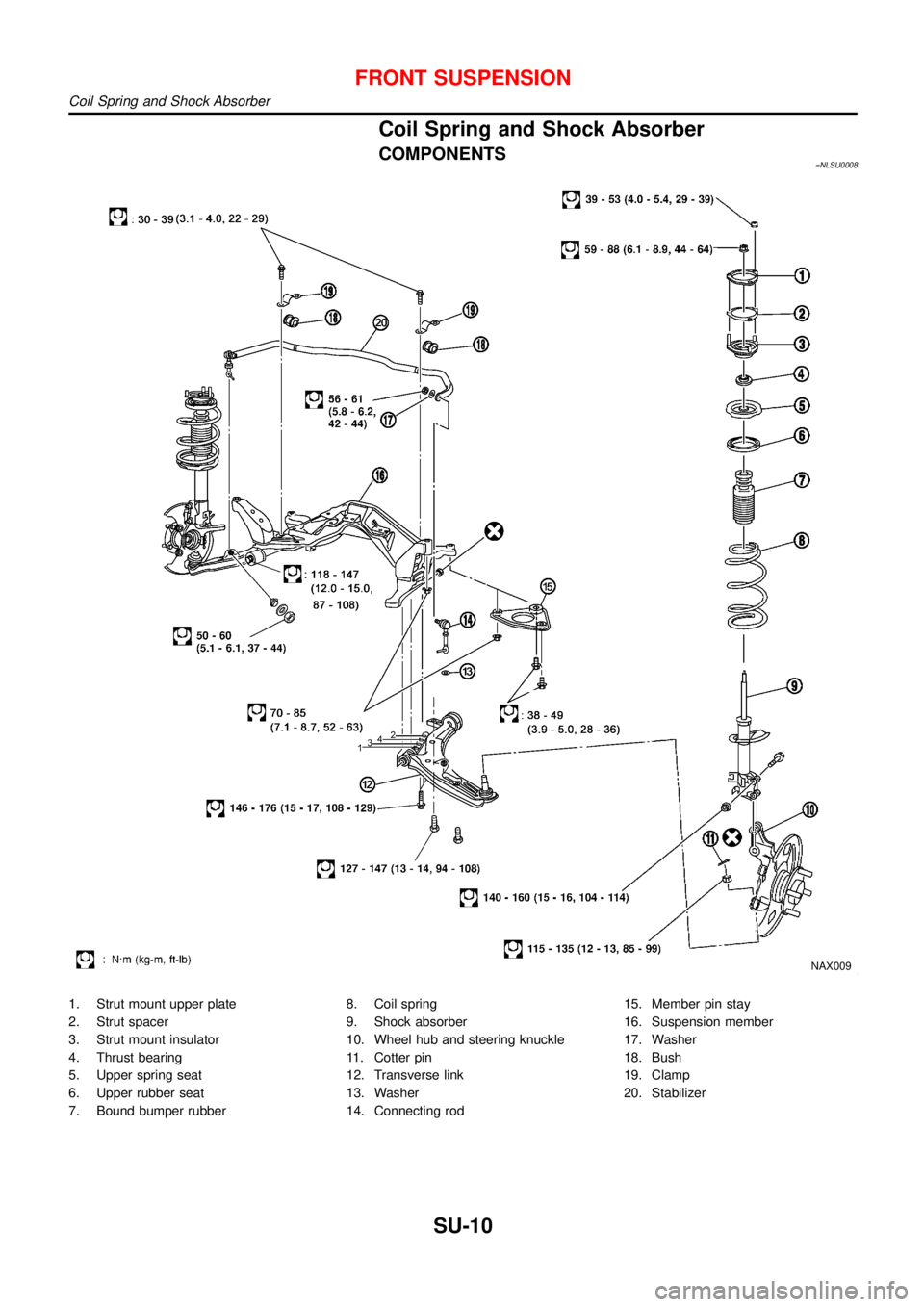
Coil Spring and Shock Absorber
COMPONENTS=NLSU0008
NAX009
1. Strut mount upper plate
2. Strut spacer
3. Strut mount insulator
4. Thrust bearing
5. Upper spring seat
6. Upper rubber seat
7. Bound bumper rubber8. Coil spring
9. Shock absorber
10. Wheel hub and steering knuckle
11. Cotter pin
12. Transverse link
13. Washer
14. Connecting rod15. Member pin stay
16. Suspension member
17. Washer
18. Bush
19. Clamp
20. Stabilizer
FRONT SUSPENSION
Coil Spring and Shock Absorber
SU-10
Page 3034 of 3051
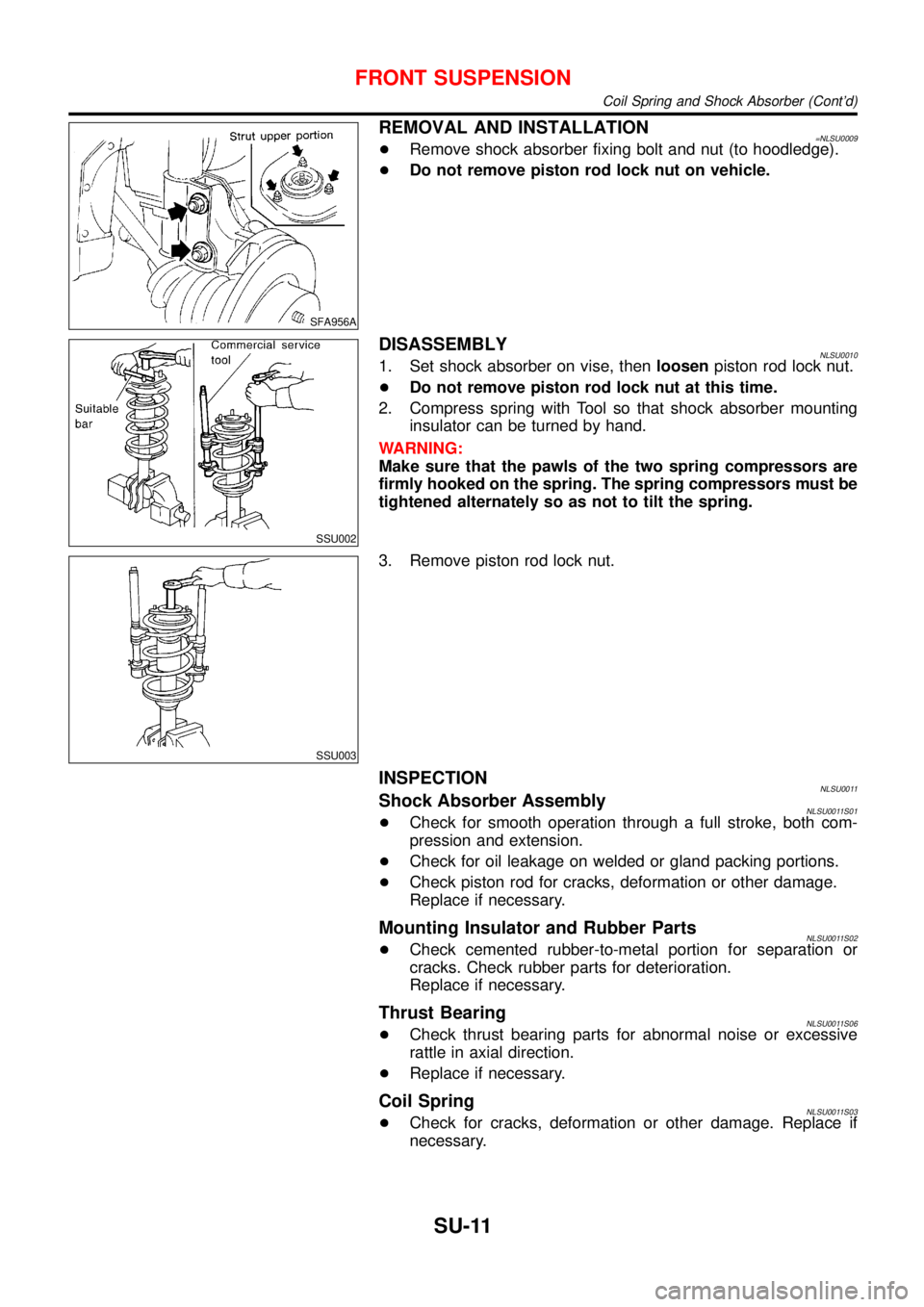
SFA956A
REMOVAL AND INSTALLATION=NLSU0009+Remove shock absorber fixing bolt and nut (to hoodledge).
+Do not remove piston rod lock nut on vehicle.
SSU002
DISASSEMBLYNLSU00101. Set shock absorber on vise, thenloosenpiston rod lock nut.
+Do not remove piston rod lock nut at this time.
2. Compress spring with Tool so that shock absorber mounting
insulator can be turned by hand.
WARNING:
Make sure that the pawls of the two spring compressors are
firmly hooked on the spring. The spring compressors must be
tightened alternately so as not to tilt the spring.
SSU003
3. Remove piston rod lock nut.
INSPECTIONNLSU0011Shock Absorber AssemblyNLSU0011S01+Check for smooth operation through a full stroke, both com-
pression and extension.
+Check for oil leakage on welded or gland packing portions.
+Check piston rod for cracks, deformation or other damage.
Replace if necessary.
Mounting Insulator and Rubber PartsNLSU0011S02+Check cemented rubber-to-metal portion for separation or
cracks. Check rubber parts for deterioration.
Replace if necessary.
Thrust BearingNLSU0011S06+Check thrust bearing parts for abnormal noise or excessive
rattle in axial direction.
+Replace if necessary.
Coil SpringNLSU0011S03+Check for cracks, deformation or other damage. Replace if
necessary.
FRONT SUSPENSION
Coil Spring and Shock Absorber (Cont’d)
SU-11
Page 3035 of 3051
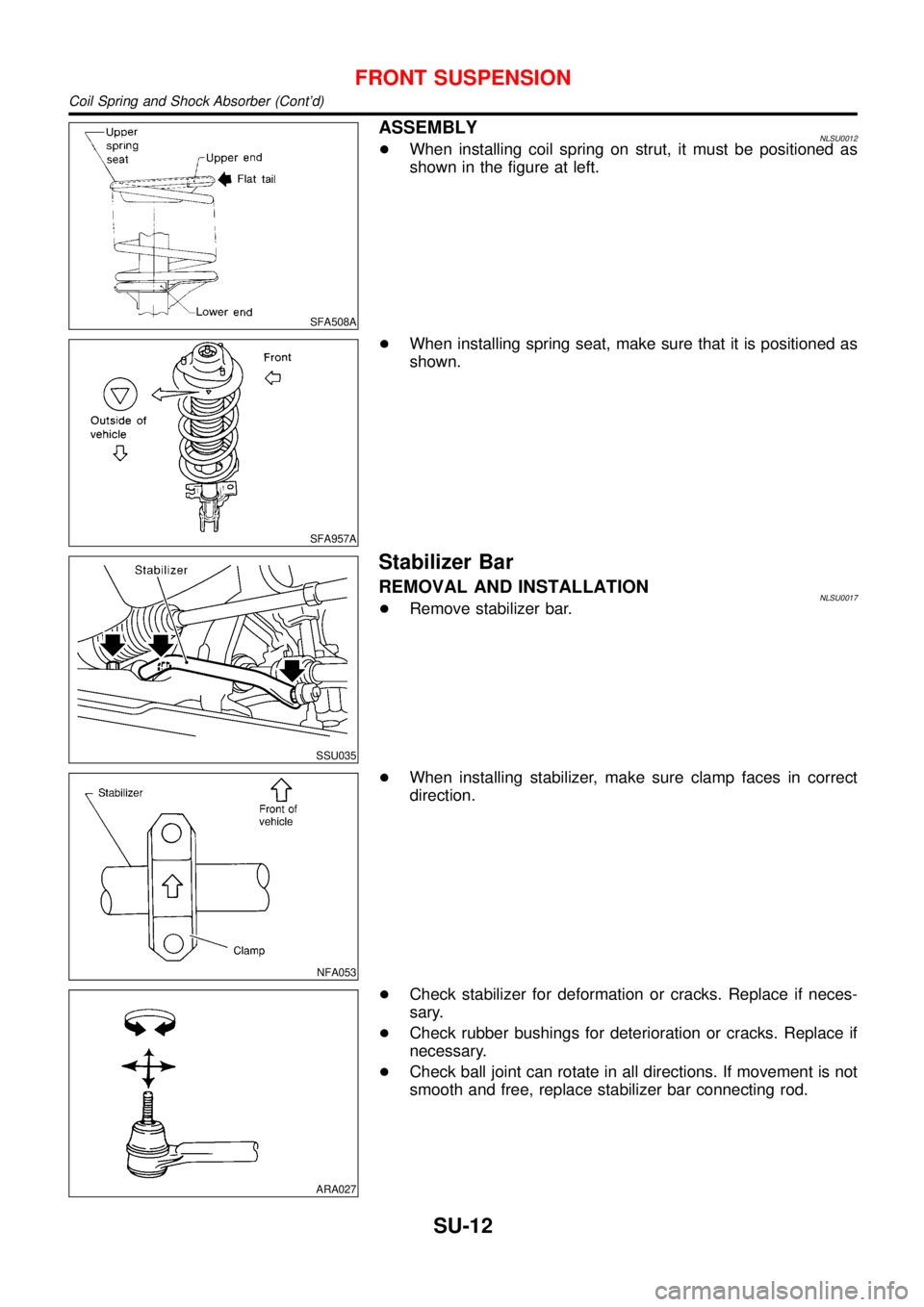
SFA508A
ASSEMBLYNLSU0012+When installing coil spring on strut, it must be positioned as
shown in the figure at left.
SFA957A
+When installing spring seat, make sure that it is positioned as
shown.
SSU035
Stabilizer Bar
REMOVAL AND INSTALLATIONNLSU0017+Remove stabilizer bar.
NFA053
+When installing stabilizer, make sure clamp faces in correct
direction.
ARA027
+Check stabilizer for deformation or cracks. Replace if neces-
sary.
+Check rubber bushings for deterioration or cracks. Replace if
necessary.
+Check ball joint can rotate in all directions. If movement is not
smooth and free, replace stabilizer bar connecting rod.
FRONT SUSPENSION
Coil Spring and Shock Absorber (Cont’d)
SU-12
Page 3036 of 3051
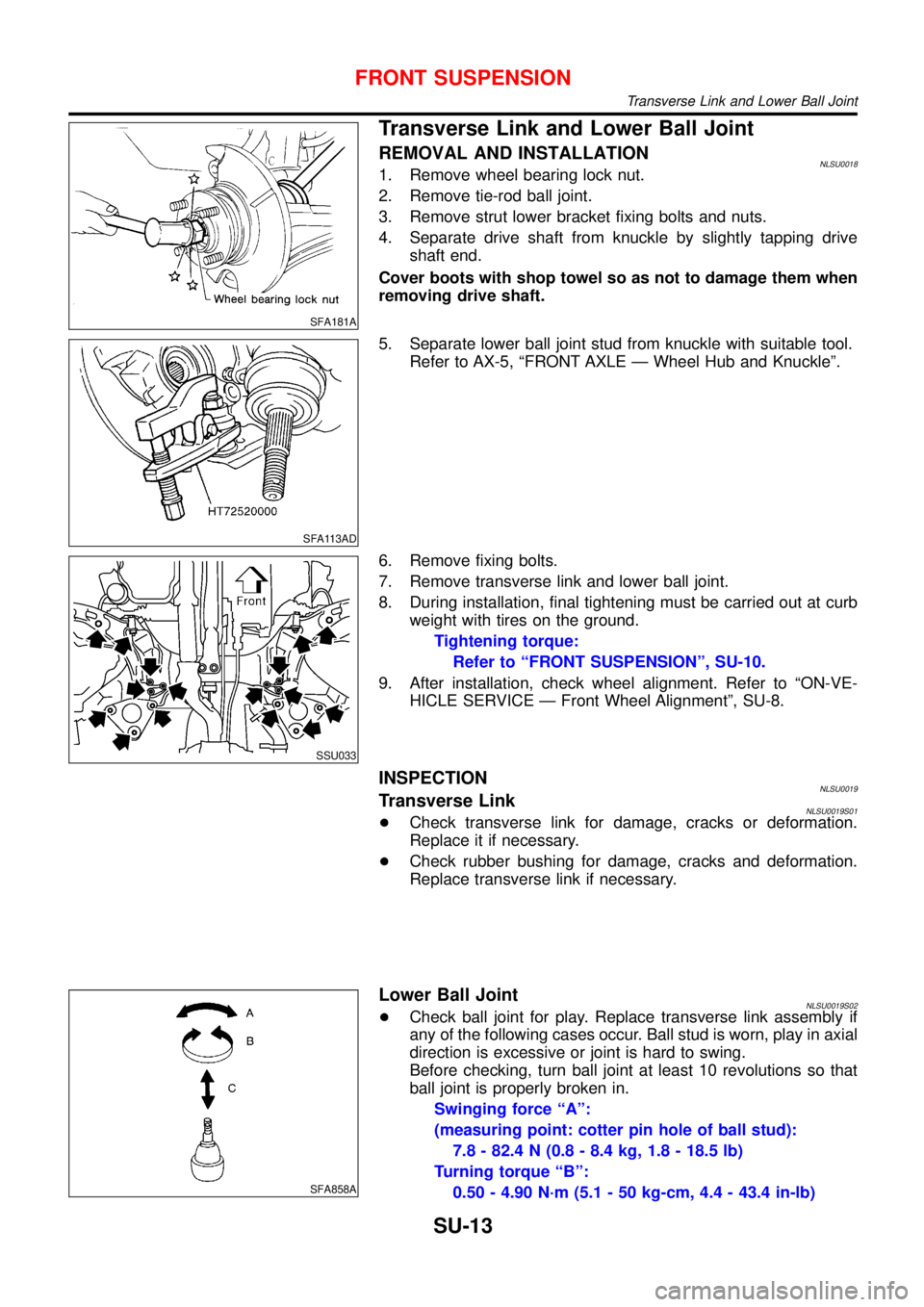
SFA181A
Transverse Link and Lower Ball Joint
REMOVAL AND INSTALLATIONNLSU00181. Remove wheel bearing lock nut.
2. Remove tie-rod ball joint.
3. Remove strut lower bracket fixing bolts and nuts.
4. Separate drive shaft from knuckle by slightly tapping drive
shaft end.
Cover boots with shop towel so as not to damage them when
removing drive shaft.
SFA113AD
5. Separate lower ball joint stud from knuckle with suitable tool.
Refer to AX-5,“FRONT AXLE—Wheel Hub and Knuckle”.
SSU033
6. Remove fixing bolts.
7. Remove transverse link and lower ball joint.
8. During installation, final tightening must be carried out at curb
weight with tires on the ground.
Tightening torque:
Refer to“FRONT SUSPENSION”, SU-10.
9. After installation, check wheel alignment. Refer to“ON-VE-
HICLE SERVICE—Front Wheel Alignment”, SU-8.
INSPECTIONNLSU0019Transverse LinkNLSU0019S01+Check transverse link for damage, cracks or deformation.
Replace it if necessary.
+Check rubber bushing for damage, cracks and deformation.
Replace transverse link if necessary.
SFA858A
Lower Ball JointNLSU0019S02+Check ball joint for play. Replace transverse link assembly if
any of the following cases occur. Ball stud is worn, play in axial
direction is excessive or joint is hard to swing.
Before checking, turn ball joint at least 10 revolutions so that
ball joint is properly broken in.
Swinging force“A”:
(measuring point: cotter pin hole of ball stud):
7.8 - 82.4 N (0.8 - 8.4 kg, 1.8 - 18.5 lb)
Turning torque“B”:
0.50 - 4.90 N·m (5.1 - 50 kg-cm, 4.4 - 43.4 in-lb)
FRONT SUSPENSION
Transverse Link and Lower Ball Joint
SU-13
Page 3037 of 3051
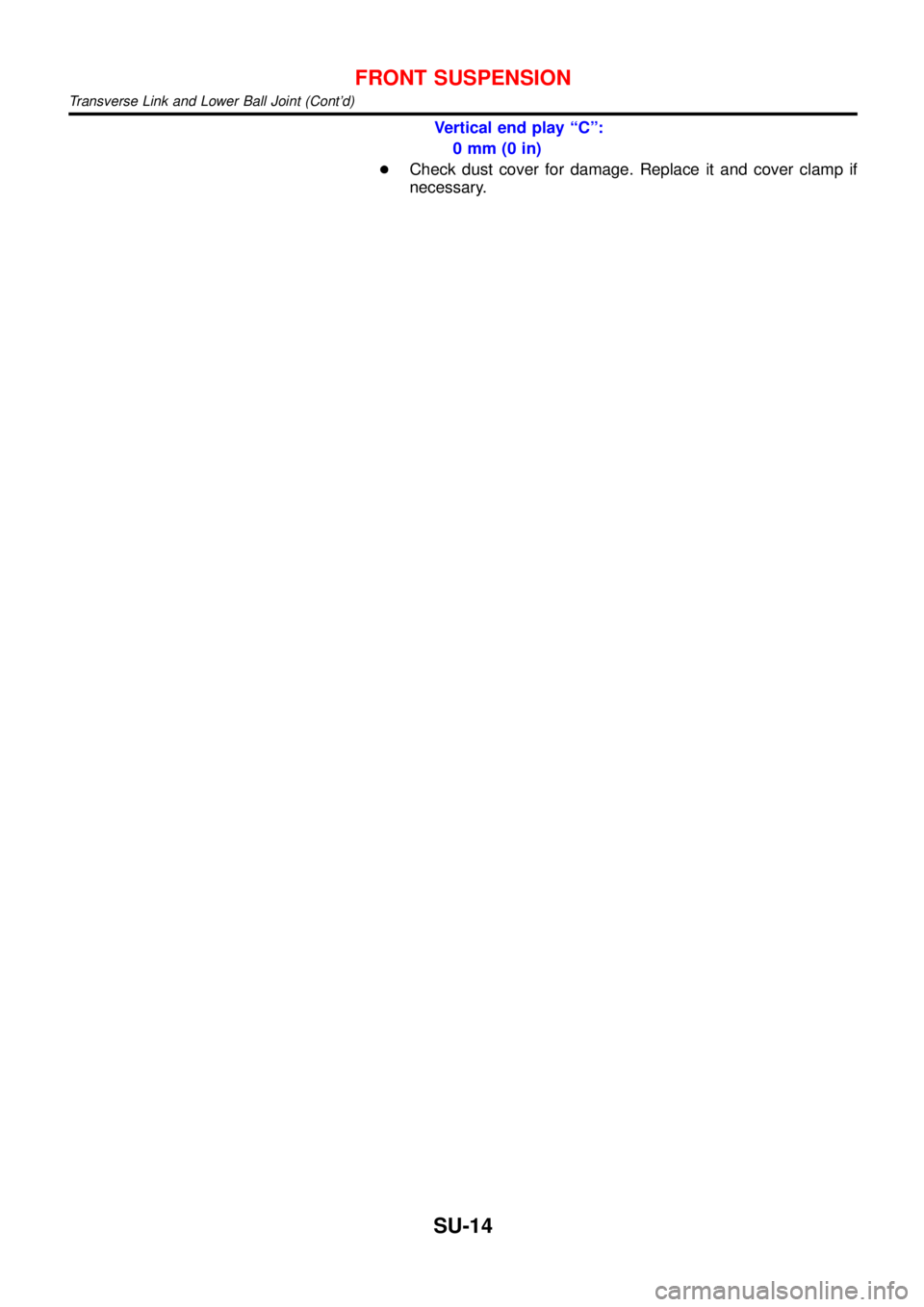
Vertical end play“C”:
0mm(0in)
+Check dust cover for damage. Replace it and cover clamp if
necessary.
FRONT SUSPENSION
Transverse Link and Lower Ball Joint (Cont’d)
SU-14
Page 3038 of 3051
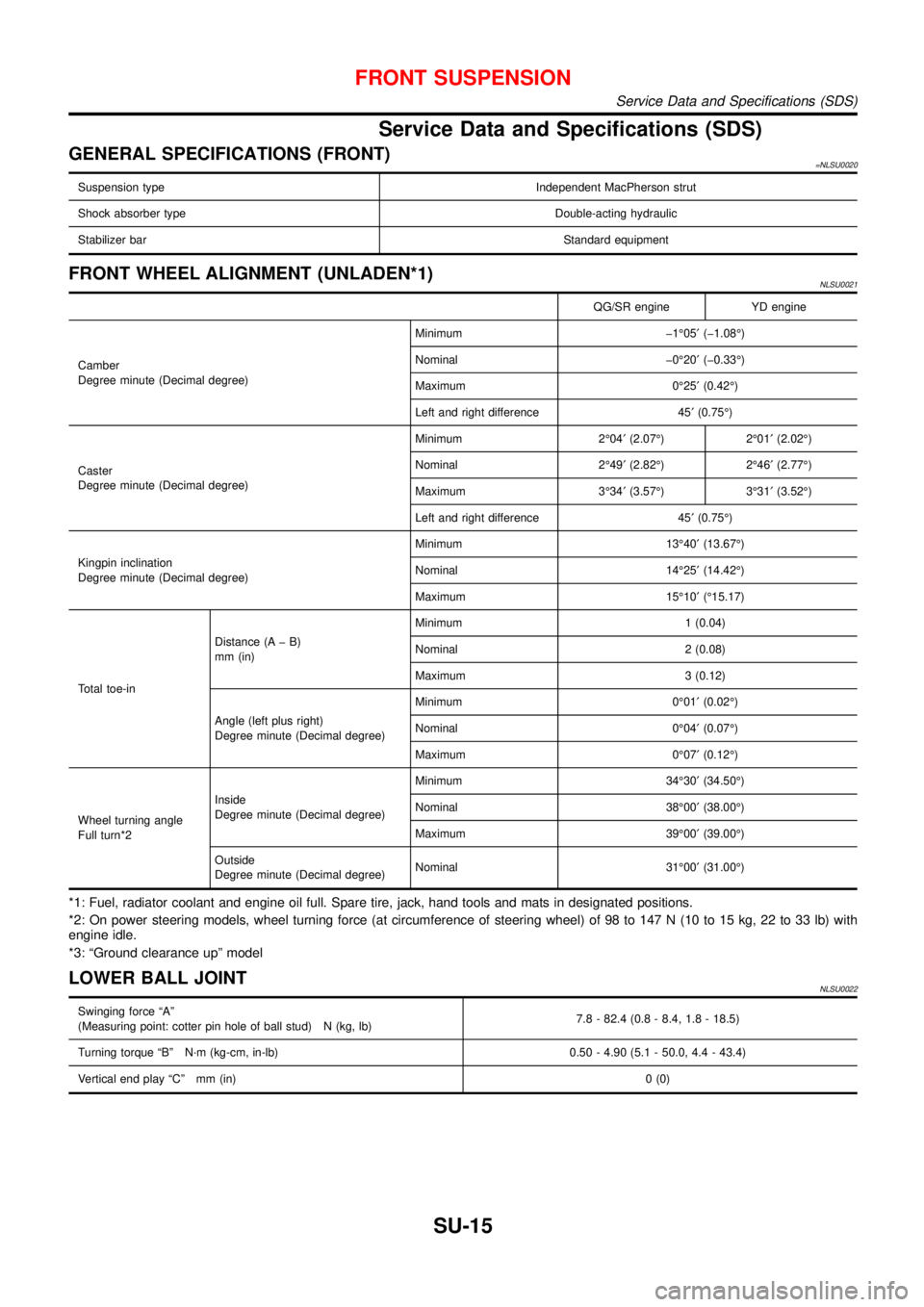
Service Data and Specifications (SDS)
GENERAL SPECIFICATIONS (FRONT)=NLSU0020
Suspension type Independent MacPherson strut
Shock absorber type Double-acting hydraulic
Stabilizer barStandard equipment
FRONT WHEEL ALIGNMENT (UNLADEN*1)NLSU0021
QG/SR engine YD engine
Camber
Degree minute (Decimal degree)Minimum 1°05′( 1.08°)
Nominal 0°20′( 0.33°)
Maximum 0°25′(0.42°)
Left and right difference 45′(0.75°)
Caster
Degree minute (Decimal degree)Minimum 2°04′(2.07°) 2°01′(2.02°)
Nominal 2°49′(2.82°) 2°46′(2.77°)
Maximum 3°34′(3.57°) 3°31′(3.52°)
Left and right difference 45′(0.75°)
Kingpin inclination
Degree minute (Decimal degree)Minimum 13°40′(13.67°)
Nominal 14°25′(14.42°)
Maximum 15°10′(°15.17)
Total toe-inDistance (A B)
mm (in)Minimum 1 (0.04)
Nominal 2 (0.08)
Maximum 3 (0.12)
Angle (left plus right)
Degree minute (Decimal degree)Minimum 0°01′(0.02°)
Nominal 0°04′(0.07°)
Maximum 0°07′(0.12°)
Wheel turning angle
Full turn*2Inside
Degree minute (Decimal degree)Minimum 34°30′(34.50°)
Nominal 38°00′(38.00°)
Maximum 39°00′(39.00°)
Outside
Degree minute (Decimal degree)Nominal 31°00′(31.00°)
*1: Fuel, radiator coolant and engine oil full. Spare tire, jack, hand tools and mats in designated positions.
*2: On power steering models, wheel turning force (at circumference of steering wheel) of 98 to 147 N (10 to 15 kg, 22 to 33 lb) with
engine idle.
*3: “Ground clearance up” model
LOWER BALL JOINTNLSU0022
Swinging force “A”
(Measuring point: cotter pin hole of ball stud) N (kg, lb)7.8 - 82.4 (0.8 - 8.4, 1.8 - 18.5)
Turning torque “B” N·m (kg-cm, in-lb) 0.50 - 4.90 (5.1 - 50.0, 4.4 - 43.4)
Vertical end play “C” mm (in)0 (0)
FRONT SUSPENSION
Service Data and Specifications (SDS)
SU-15
Page 3039 of 3051
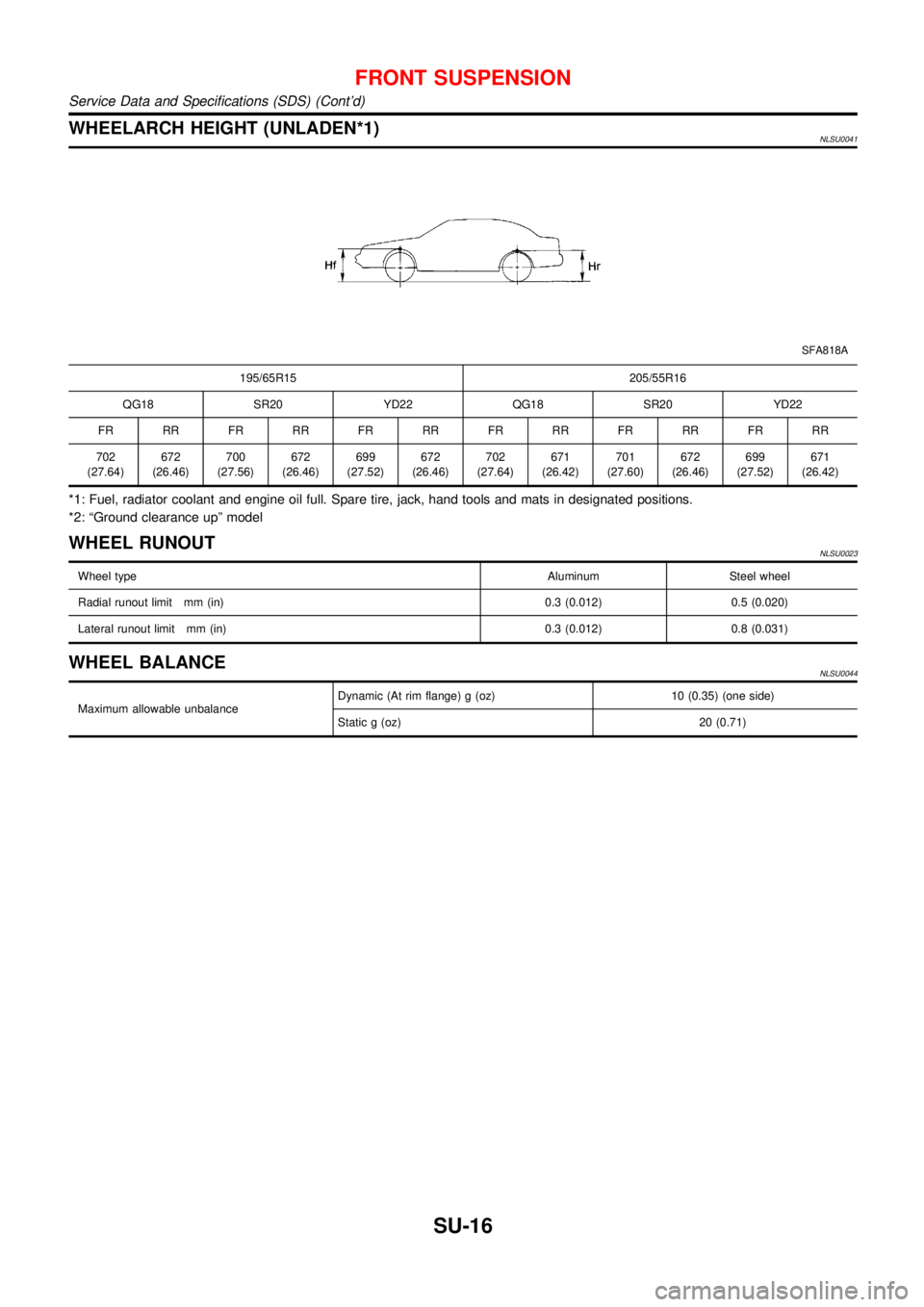
WHEELARCH HEIGHT (UNLADEN*1)NLSU0041
SFA818A
195/65R15 205/55R16
QG18 SR20 YD22 QG18 SR20 YD22
FR RR FR RR FR RR FR RR FR RR FR RR
702
(27.64)672
(26.46)700
(27.56)672
(26.46)699
(27.52)672
(26.46)702
(27.64)671
(26.42)701
(27.60)672
(26.46)699
(27.52)671
(26.42)
*1: Fuel, radiator coolant and engine oil full. Spare tire, jack, hand tools and mats in designated positions.
*2:“Ground clearance up”model
WHEEL RUNOUTNLSU0023
Wheel typeAluminum Steel wheel
Radial runout limit mm (in) 0.3 (0.012) 0.5 (0.020)
Lateral runout limit mm (in) 0.3 (0.012) 0.8 (0.031)
WHEEL BALANCENLSU0044
Maximum allowable unbalanceDynamic (At rim flange) g (oz) 10 (0.35) (one side)
Static g (oz) 20 (0.71)
FRONT SUSPENSION
Service Data and Specifications (SDS) (Cont’d)
SU-16
Page 3040 of 3051
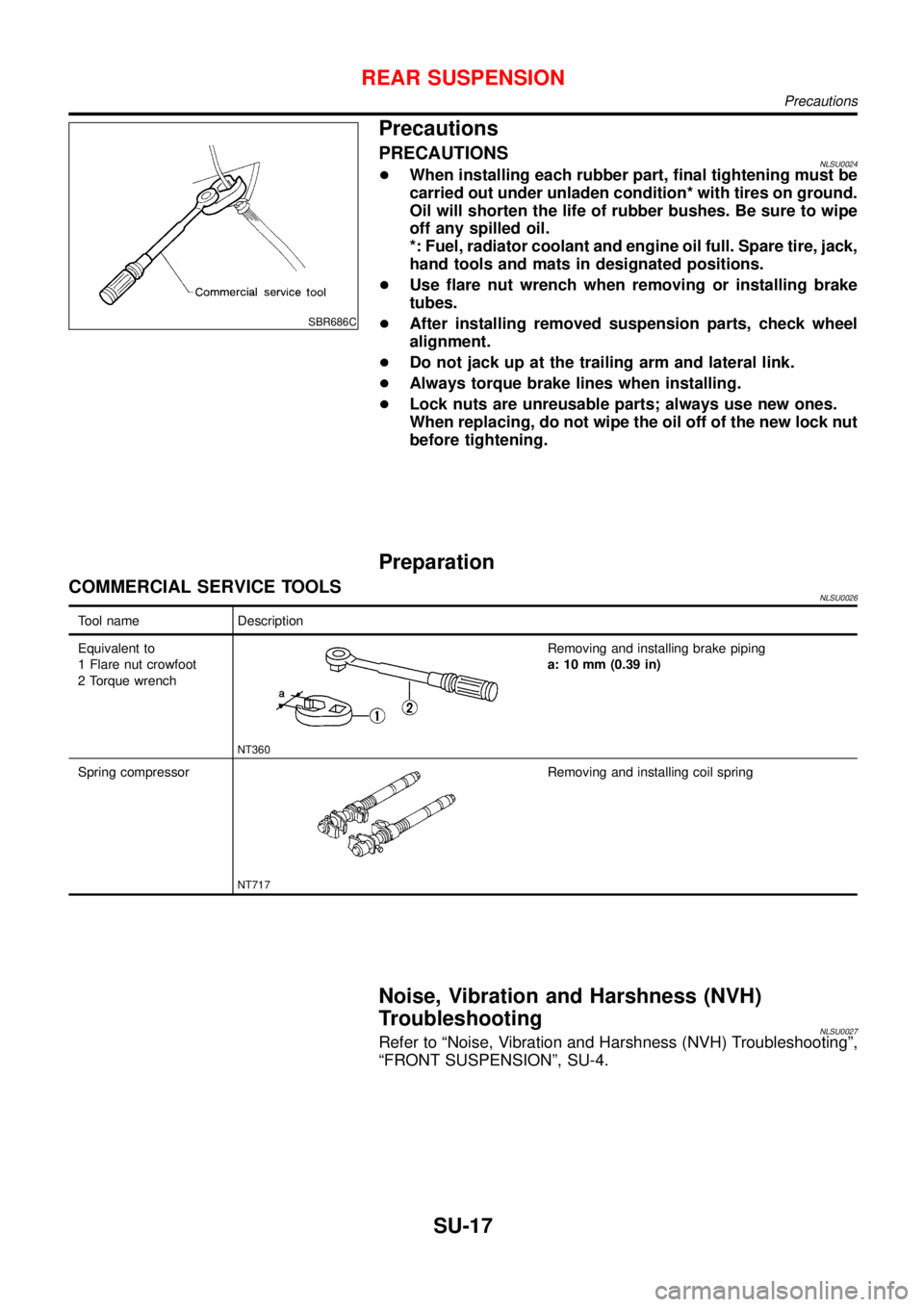
SBR686C
Precautions
PRECAUTIONSNLSU0024+When installing each rubber part, final tightening must be
carried out under unladen condition* with tires on ground.
Oil will shorten the life of rubber bushes. Be sure to wipe
off any spilled oil.
*: Fuel, radiator coolant and engine oil full. Spare tire, jack,
hand tools and mats in designated positions.
+Use flare nut wrench when removing or installing brake
tubes.
+After installing removed suspension parts, check wheel
alignment.
+Do not jack up at the trailing arm and lateral link.
+Always torque brake lines when installing.
+Lock nuts are unreusable parts; always use new ones.
When replacing, do not wipe the oil off of the new lock nut
before tightening.
Preparation
COMMERCIAL SERVICE TOOLSNLSU0026
Tool name Description
Equivalent to
1 Flare nut crowfoot
2 Torque wrench
NT360
Removing and installing brake piping
a: 10 mm (0.39 in)
Spring compressor
NT717
Removing and installing coil spring
Noise, Vibration and Harshness (NVH)
Troubleshooting
NLSU0027Refer to“Noise, Vibration and Harshness (NVH) Troubleshooting”,
“FRONT SUSPENSION”, SU-4.
REAR SUSPENSION
Precautions
SU-17