NISSAN ALMERA TINO 2001 Service Repair Manual
Manufacturer: NISSAN, Model Year: 2001, Model line: ALMERA TINO, Model: NISSAN ALMERA TINO 2001Pages: 3051, PDF Size: 46.38 MB
Page 3021 of 3051
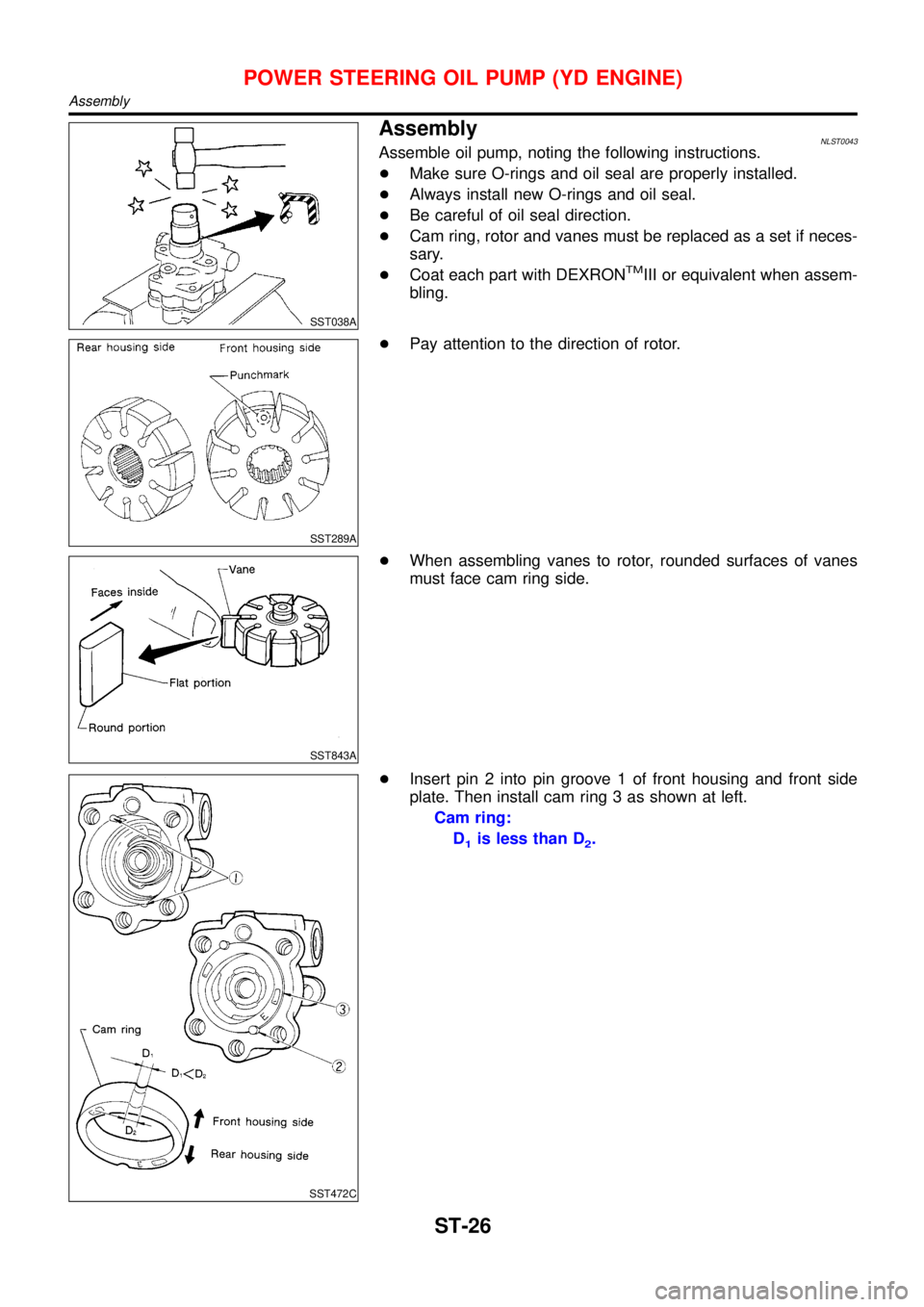
SST038A
AssemblyNLST0043Assemble oil pump, noting the following instructions.
+Make sure O-rings and oil seal are properly installed.
+Always install new O-rings and oil seal.
+Be careful of oil seal direction.
+Cam ring, rotor and vanes must be replaced as a set if neces-
sary.
+Coat each part with DEXRON
TMIII or equivalent when assem-
bling.
SST289A
+Pay attention to the direction of rotor.
SST843A
+When assembling vanes to rotor, rounded surfaces of vanes
must face cam ring side.
SST472C
+Insert pin 2 into pin groove 1 of front housing and front side
plate. Then install cam ring 3 as shown at left.
Cam ring:
D
1is less than D2.
POWER STEERING OIL PUMP (YD ENGINE)
Assembly
ST-26
Page 3022 of 3051
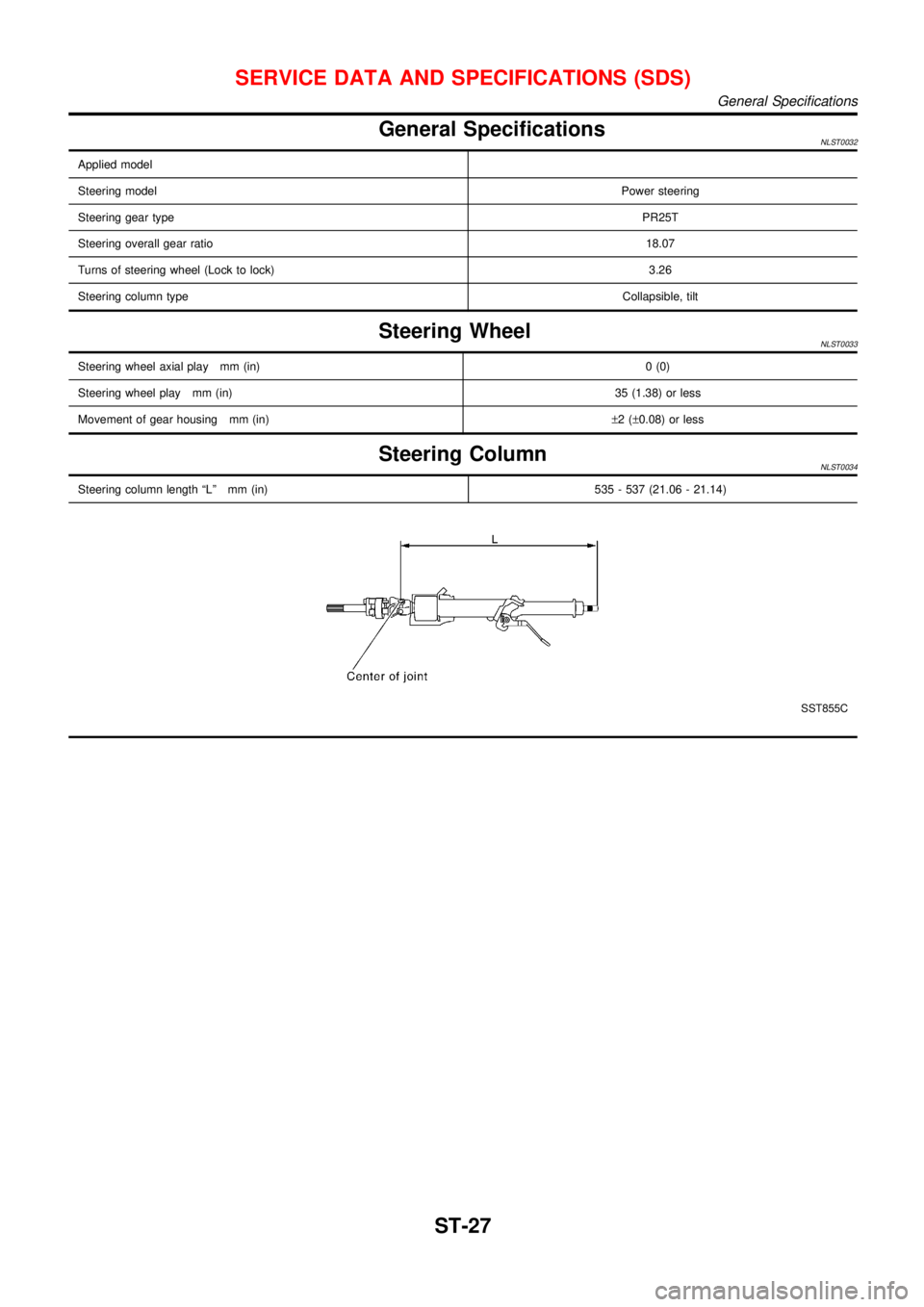
General SpecificationsNLST0032
Applied model
Steering modelPower steering
Steering gear typePR25T
Steering overall gear ratio18.07
Turns of steering wheel (Lock to lock)3.26
Steering column typeCollapsible, tilt
Steering WheelNLST0033
Steering wheel axial play mm (in)0 (0)
Steering wheel play mm (in)35 (1.38) or less
Movement of gear housing mm (in)±2(±0.08) or less
Steering ColumnNLST0034
Steering column length“L”mm (in) 535 - 537 (21.06 - 21.14)
SST855C
SERVICE DATA AND SPECIFICATIONS (SDS)
General Specifications
ST-27
Page 3023 of 3051
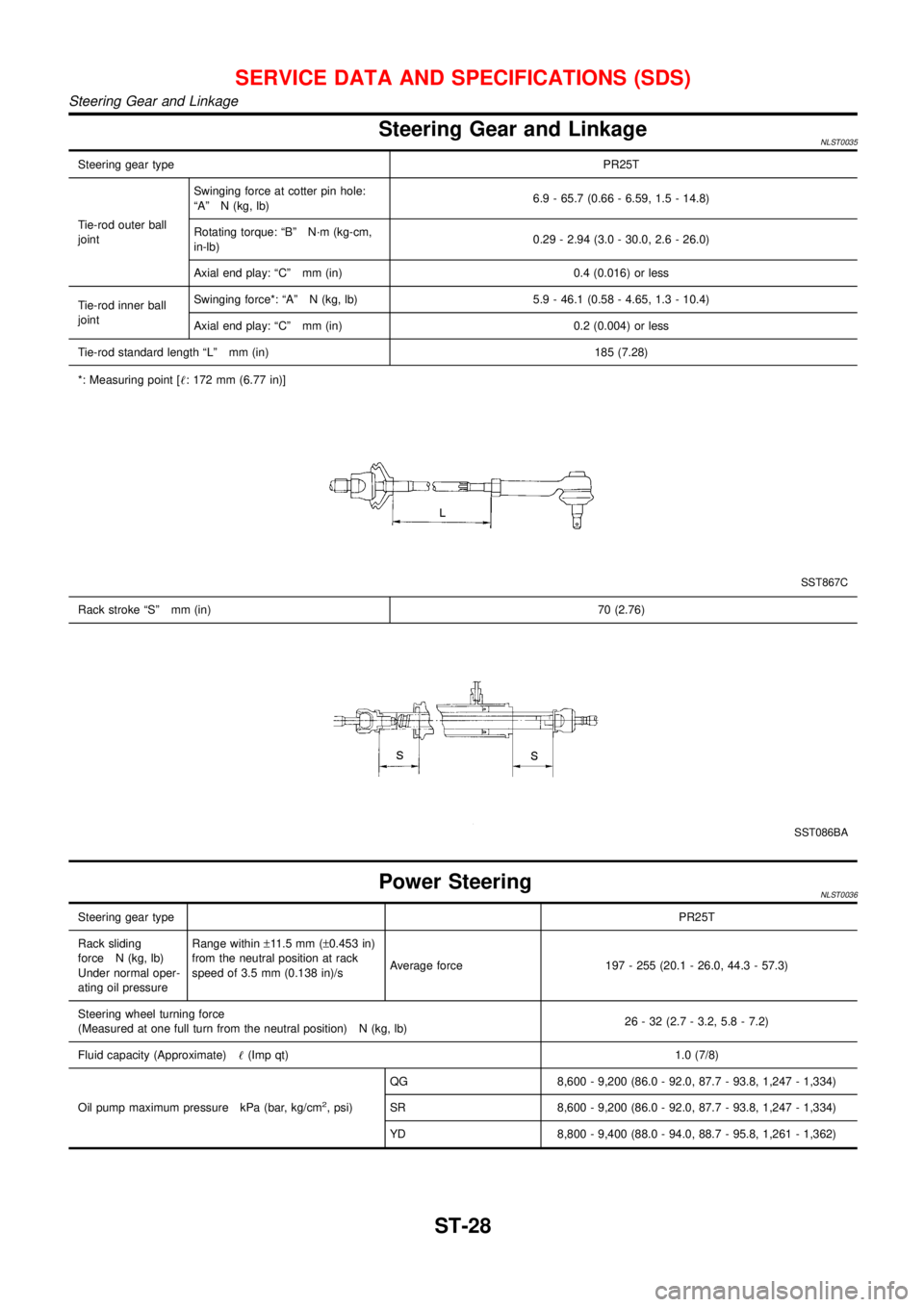
Steering Gear and LinkageNLST0035
Steering gear typePR25T
Tie-rod outer ball
jointSwinging force at cotter pin hole:
“A”N (kg, lb)6.9 - 65.7 (0.66 - 6.59, 1.5 - 14.8)
Rotating torque:“B”N·m (kg-cm,
in-lb)0.29 - 2.94 (3.0 - 30.0, 2.6 - 26.0)
Axial end play:“C”mm (in) 0.4 (0.016) or less
Tie-rod inner ball
jointSwinging force*:“A”N (kg, lb) 5.9 - 46.1 (0.58 - 4.65, 1.3 - 10.4)
Axial end play:“C”mm (in) 0.2 (0.004) or less
Tie-rod standard length“L”mm (in) 185 (7.28)
*: Measuring point [!: 172 mm (6.77 in)]
SST867C
Rack stroke“S”mm (in)70 (2.76)
SST086BA
Power SteeringNLST0036
Steering gear typePR25T
Rack sliding
force N (kg, lb)
Under normal oper-
ating oil pressureRange within±11.5 mm (±0.453 in)
from the neutral position at rack
speed of 3.5 mm (0.138 in)/sAverage force 197 - 255 (20.1 - 26.0, 44.3 - 57.3)
Steering wheel turning force
(Measured at one full turn from the neutral position) N (kg, lb)26 - 32 (2.7 - 3.2, 5.8 - 7.2)
Fluid capacity (Approximate)!(Imp qt)1.0 (7/8)
Oil pump maximum pressure kPa (bar, kg/cm
2, psi)QG 8,600 - 9,200 (86.0 - 92.0, 87.7 - 93.8, 1,247 - 1,334)
SR 8,600 - 9,200 (86.0 - 92.0, 87.7 - 93.8, 1,247 - 1,334)
YD 8,800 - 9,400 (88.0 - 94.0, 88.7 - 95.8, 1,261 - 1,362)
SERVICE DATA AND SPECIFICATIONS (SDS)
Steering Gear and Linkage
ST-28
Page 3024 of 3051
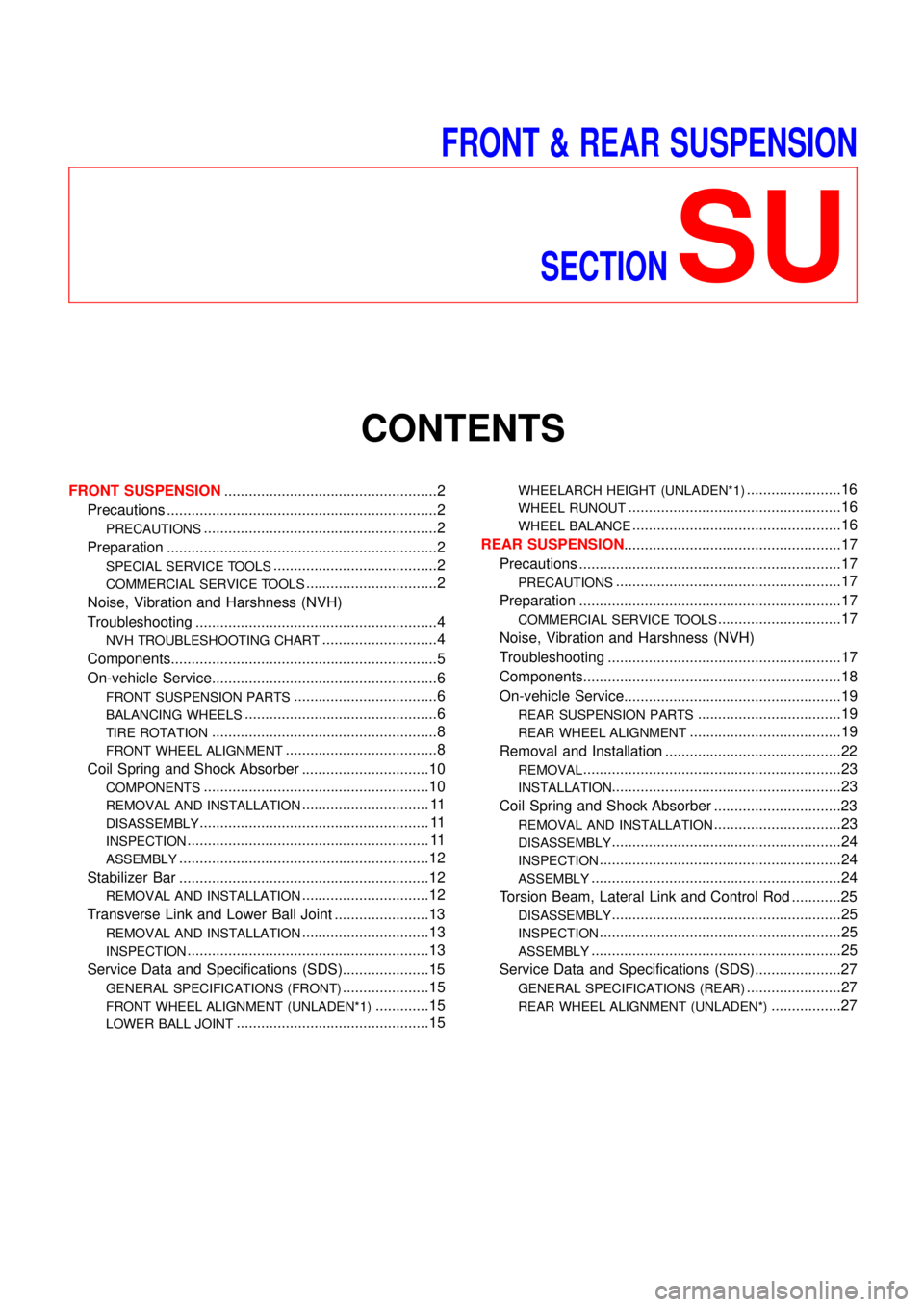
FRONT & REAR SUSPENSION
SECTION
SU
CONTENTS
FRONT SUSPENSION....................................................2
Precautions ..................................................................2
PRECAUTIONS.........................................................2
Preparation ..................................................................2
SPECIAL SERVICE TOOLS........................................2
COMMERCIAL SERVICE TOOLS................................2
Noise, Vibration and Harshness (NVH)
Troubleshooting ...........................................................4
NVH TROUBLESHOOTING CHART............................4
Components.................................................................5
On-vehicle Service.......................................................6
FRONT SUSPENSION PARTS...................................6
BALANCING WHEELS...............................................6
TIRE ROTATION.......................................................8
FRONT WHEEL ALIGNMENT.....................................8
Coil Spring and Shock Absorber ...............................10
COMPONENTS.......................................................10
REMOVAL AND INSTALLATION............................... 11
DISASSEMBLY........................................................ 11
INSPECTION........................................................... 11
ASSEMBLY.............................................................12
Stabilizer Bar .............................................................12
REMOVAL AND INSTALLATION...............................12
Transverse Link and Lower Ball Joint .......................13
REMOVAL AND INSTALLATION...............................13
INSPECTION...........................................................13
Service Data and Specifications (SDS).....................15
GENERAL SPECIFICATIONS (FRONT).....................15
FRONT WHEEL ALIGNMENT (UNLADEN*1).............15
LOWER BALL JOINT...............................................15
WHEELARCH HEIGHT (UNLADEN*1).......................16
WHEEL RUNOUT....................................................16
WHEEL BALANCE...................................................16
REAR SUSPENSION.....................................................17
Precautions ................................................................17
PRECAUTIONS.......................................................17
Preparation ................................................................17
COMMERCIAL SERVICE TOOLS..............................17
Noise, Vibration and Harshness (NVH)
Troubleshooting .........................................................17
Components...............................................................18
On-vehicle Service.....................................................19
REAR SUSPENSION PARTS...................................19
REAR WHEEL ALIGNMENT.....................................19
Removal and Installation ...........................................22
REMOVAL...............................................................23
INSTALLATION........................................................23
Coil Spring and Shock Absorber ...............................23
REMOVAL AND INSTALLATION...............................23
DISASSEMBLY........................................................24
INSPECTION...........................................................24
ASSEMBLY.............................................................24
Torsion Beam, Lateral Link and Control Rod ............25
DISASSEMBLY........................................................25
INSPECTION...........................................................25
ASSEMBLY.............................................................25
Service Data and Specifications (SDS).....................27
GENERAL SPECIFICATIONS (REAR).......................27
REAR WHEEL ALIGNMENT (UNLADEN*).................27
Page 3025 of 3051
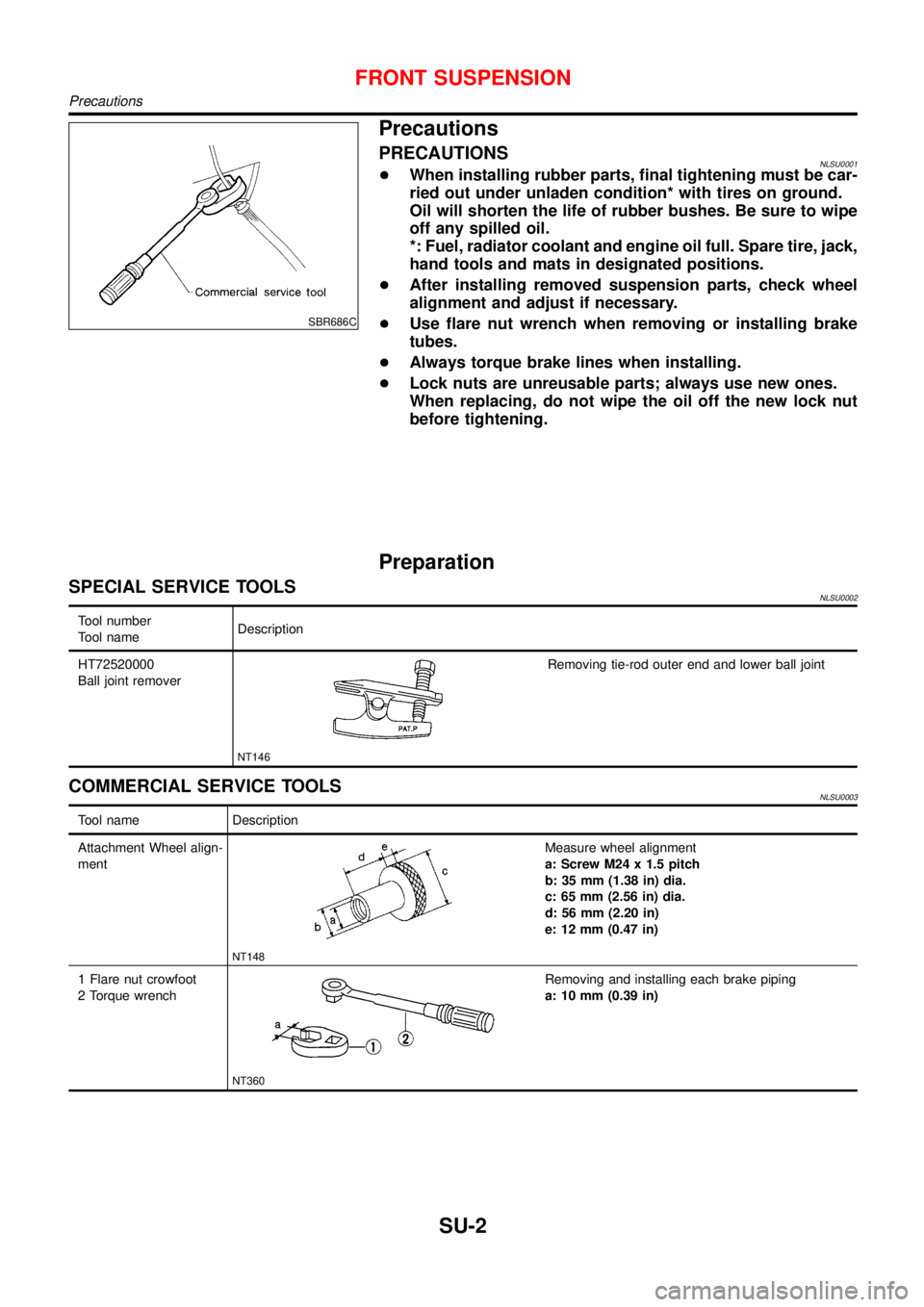
SBR686C
Precautions
PRECAUTIONSNLSU0001+When installing rubber parts, final tightening must be car-
ried out under unladen condition* with tires on ground.
Oil will shorten the life of rubber bushes. Be sure to wipe
off any spilled oil.
*: Fuel, radiator coolant and engine oil full. Spare tire, jack,
hand tools and mats in designated positions.
+After installing removed suspension parts, check wheel
alignment and adjust if necessary.
+Use flare nut wrench when removing or installing brake
tubes.
+Always torque brake lines when installing.
+Lock nuts are unreusable parts; always use new ones.
When replacing, do not wipe the oil off the new lock nut
before tightening.
Preparation
SPECIAL SERVICE TOOLSNLSU0002
Tool number
Tool nameDescription
HT72520000
Ball joint remover
NT146
Removing tie-rod outer end and lower ball joint
COMMERCIAL SERVICE TOOLSNLSU0003
Tool name Description
Attachment Wheel align-
ment
NT148
Measure wheel alignment
a: Screw M24 x 1.5 pitch
b: 35 mm (1.38 in) dia.
c: 65 mm (2.56 in) dia.
d: 56 mm (2.20 in)
e: 12 mm (0.47 in)
1 Flare nut crowfoot
2 Torque wrench
NT360
Removing and installing each brake piping
a: 10 mm (0.39 in)
FRONT SUSPENSION
Precautions
SU-2
Page 3026 of 3051
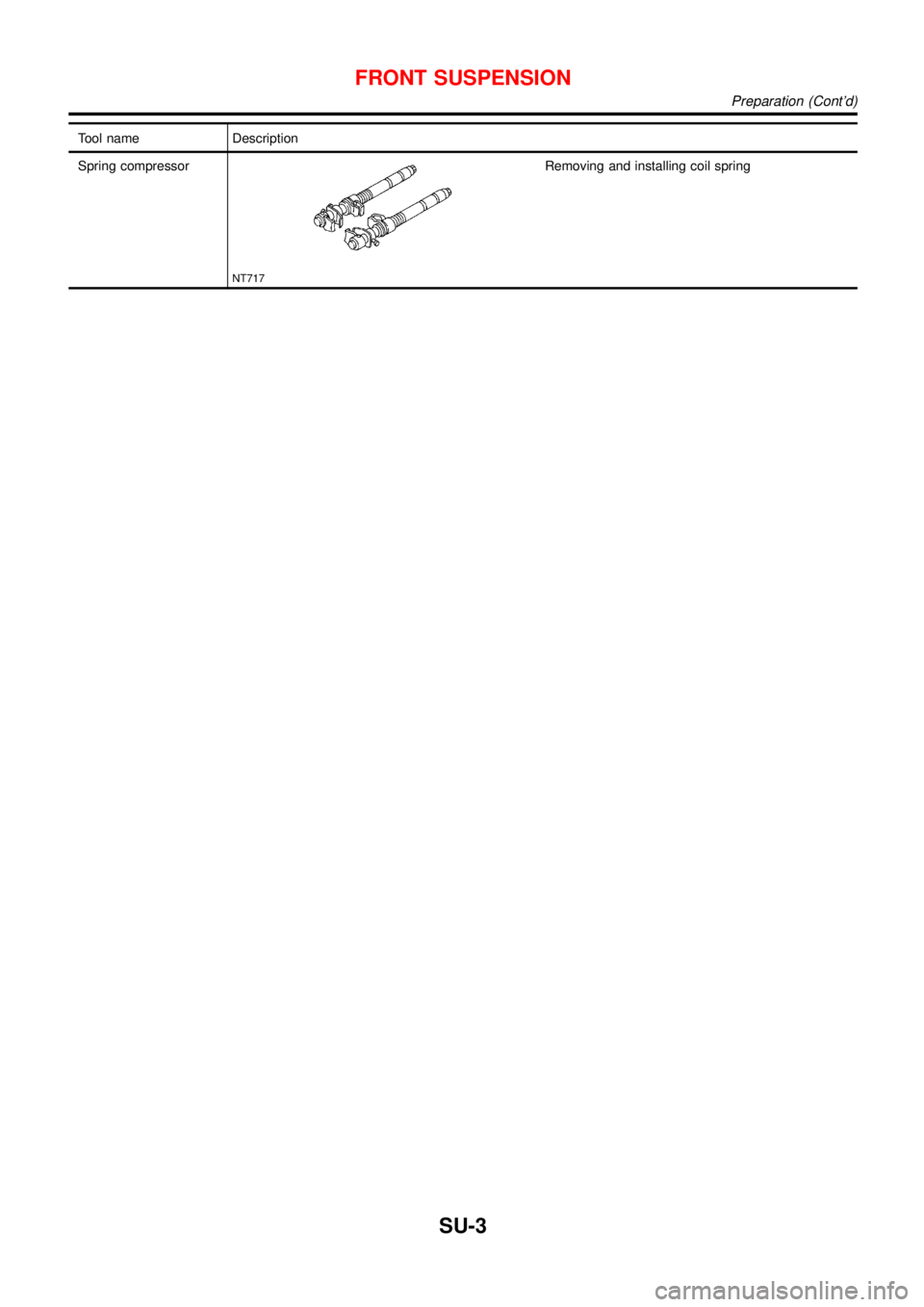
Tool name Description
Spring compressor
NT717
Removing and installing coil spring
FRONT SUSPENSION
Preparation (Cont’d)
SU-3
Page 3027 of 3051
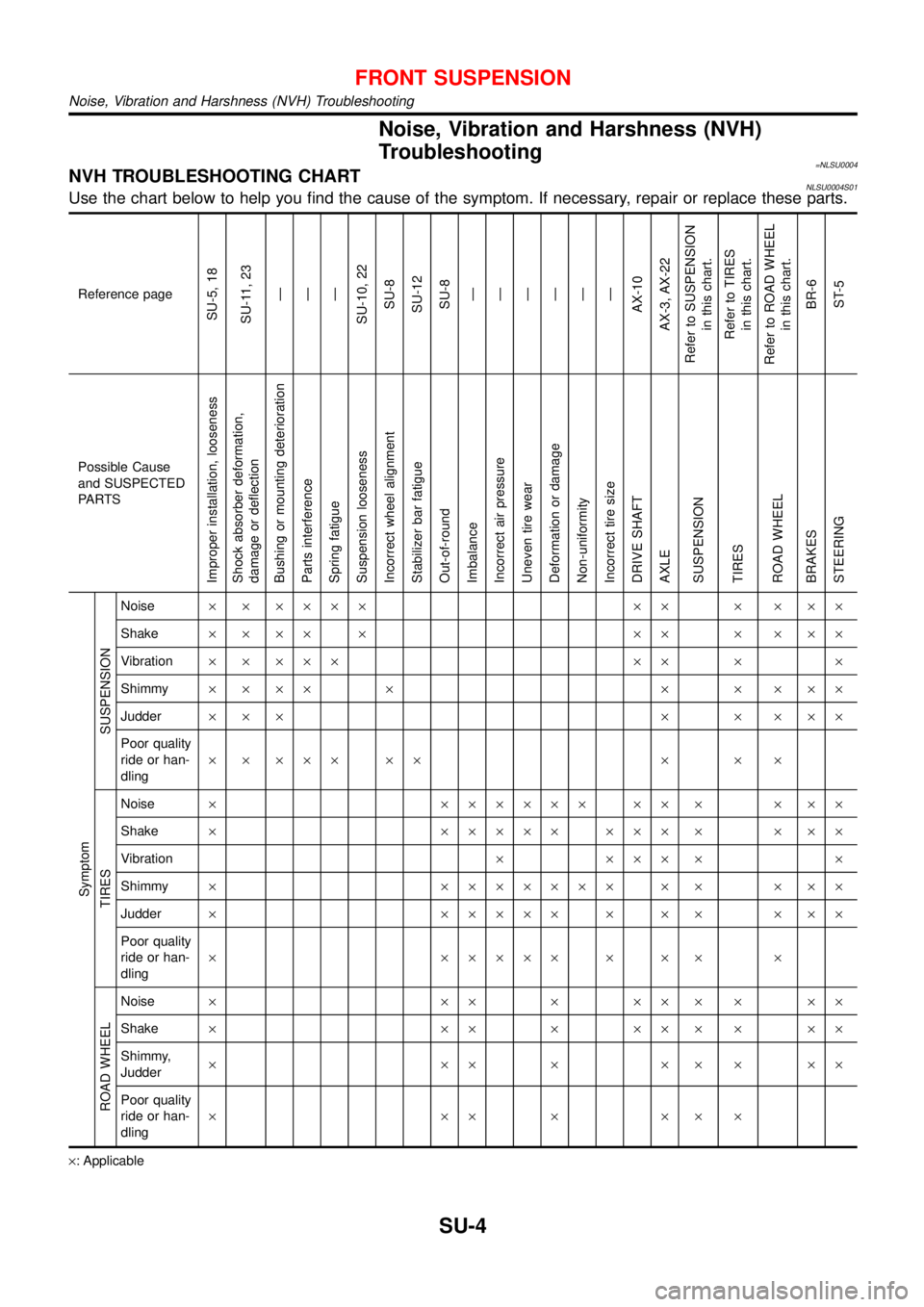
Noise, Vibration and Harshness (NVH)
Troubleshooting
=NLSU0004NVH TROUBLESHOOTING CHARTNLSU0004S01Use the chart below to help you find the cause of the symptom. If necessary, repair or replace these parts.
Reference page
SU-5, 18
SU-11, 23
—
—
—
SU-10, 22
SU-8
SU-12
SU-8
—
—
—
—
—
—
AX-10
AX-3, AX-22
Refer to SUSPENSION
in this chart.
Refer to TIRES
in this chart.
Refer to ROAD WHEEL
in this chart.
BR-6
ST-5
Possible Cause
and SUSPECTED
PA R T S
Improper installation, looseness
Shock absorber deformation,
damage or deflection
Bushing or mounting deterioration
Parts interference
Spring fatigue
Suspension looseness
Incorrect wheel alignment
Stabilizer bar fatigue
Out-of-round
Imbalance
Incorrect air pressure
Uneven tire wear
Deformation or damage
Non-uniformity
Incorrect tire size
DRIVE SHAFT
AXLE
SUSPENSION
TIRES
ROAD WHEEL
BRAKES
STEERING Symptom
SUSPENSION
Noise× × ×××× ×× × × ××
Shake× × ×× × ×× × × ××
Vibration× × ××× ×× × ×
Shimmy×××× × × × ×××
Judder××× × × ×××
Poor quality
ride or han-
dling× × ××× ×× × × ×
TIRES
Noise× ×××××× ×× × × ××
Shake× ××××× ××× × × ××
Vibration× ××× × ×
Shimmy× ××××××× × × × ××
Judder× ××××× × × × × ××
Poor quality
ride or han-
dling× ××××× × × × ×
ROAD WHEEL
Noise× ×××××××××
Shake× ×××××××××
Shimmy,
Judder×××××××××
Poor quality
ride or han-
dling×××××××
×: Applicable
FRONT SUSPENSION
Noise, Vibration and Harshness (NVH) Troubleshooting
SU-4
Page 3028 of 3051
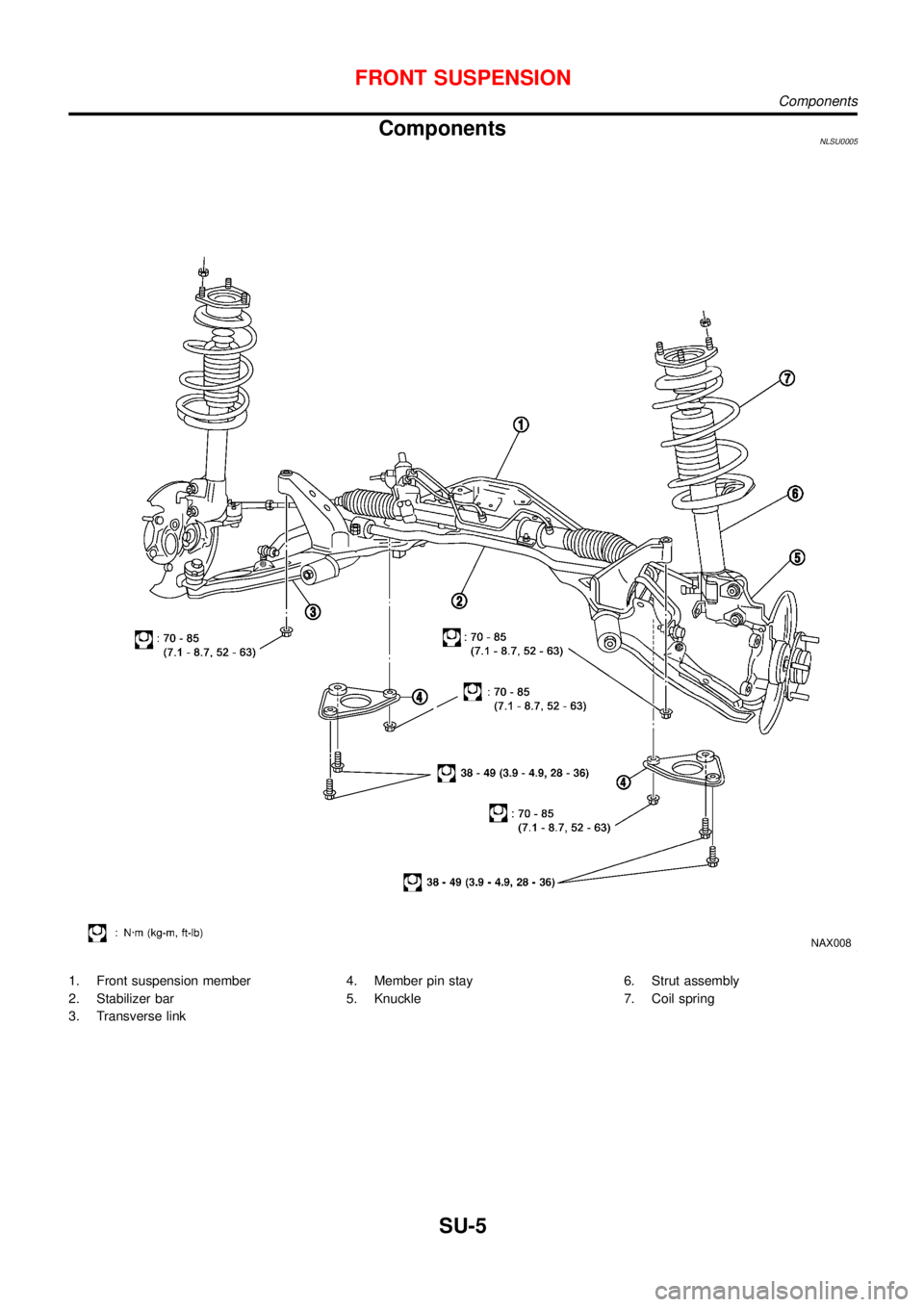
ComponentsNLSU0005
NAX008
1. Front suspension member
2. Stabilizer bar
3. Transverse link4. Member pin stay
5. Knuckle6. Strut assembly
7. Coil spring
FRONT SUSPENSION
Components
SU-5
Page 3029 of 3051
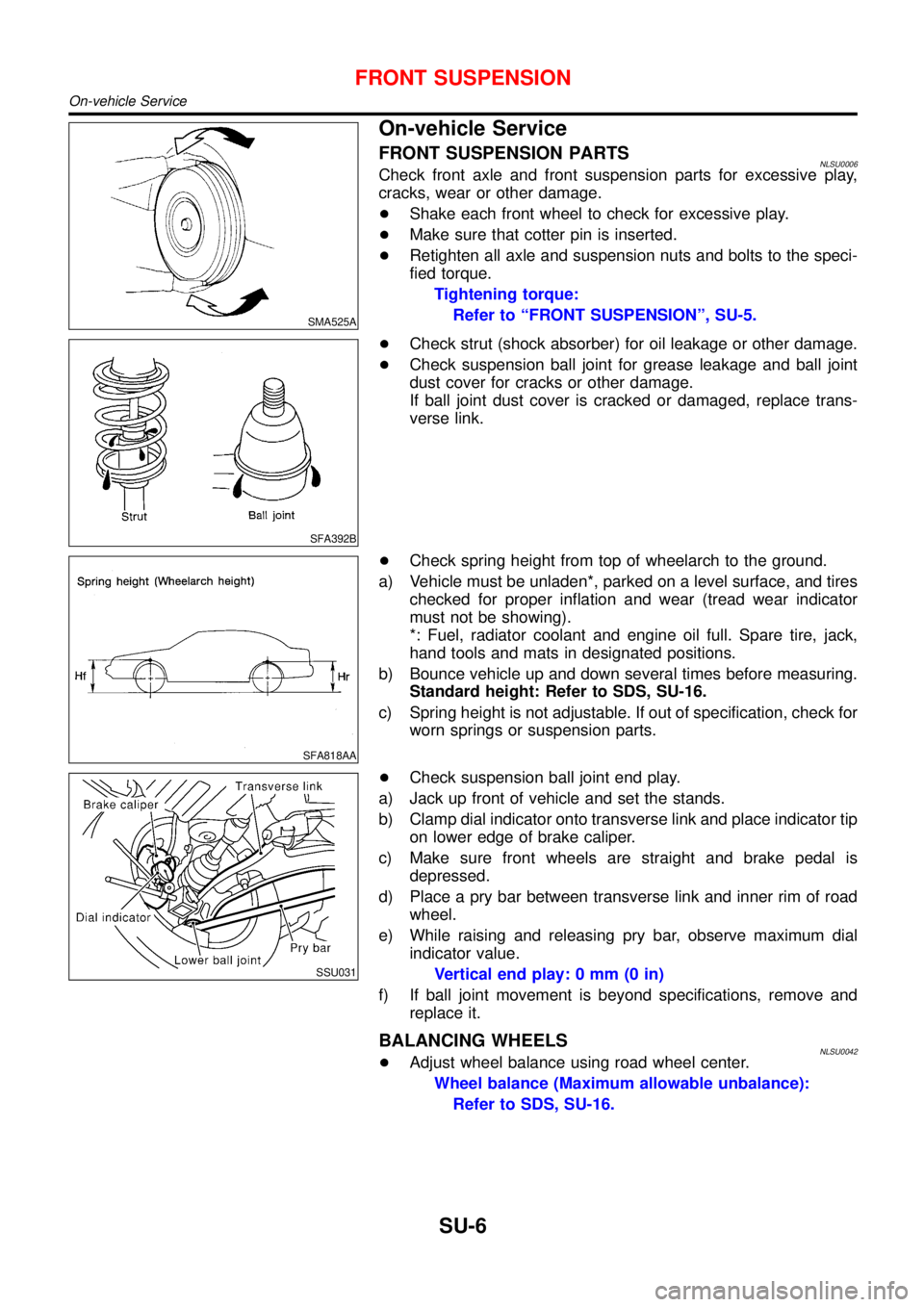
SMA525A
On-vehicle Service
FRONT SUSPENSION PARTSNLSU0006Check front axle and front suspension parts for excessive play,
cracks, wear or other damage.
+Shake each front wheel to check for excessive play.
+Make sure that cotter pin is inserted.
+Retighten all axle and suspension nuts and bolts to the speci-
fied torque.
Tightening torque:
Refer to “FRONT SUSPENSION”, SU-5.
SFA392B
+Check strut (shock absorber) for oil leakage or other damage.
+Check suspension ball joint for grease leakage and ball joint
dust cover for cracks or other damage.
If ball joint dust cover is cracked or damaged, replace trans-
verse link.
SFA818AA
+Check spring height from top of wheelarch to the ground.
a) Vehicle must be unladen*, parked on a level surface, and tires
checked for proper inflation and wear (tread wear indicator
must not be showing).
*: Fuel, radiator coolant and engine oil full. Spare tire, jack,
hand tools and mats in designated positions.
b) Bounce vehicle up and down several times before measuring.
Standard height: Refer to SDS, SU-16.
c) Spring height is not adjustable. If out of specification, check for
worn springs or suspension parts.
SSU031
+Check suspension ball joint end play.
a) Jack up front of vehicle and set the stands.
b) Clamp dial indicator onto transverse link and place indicator tip
on lower edge of brake caliper.
c) Make sure front wheels are straight and brake pedal is
depressed.
d) Place a pry bar between transverse link and inner rim of road
wheel.
e) While raising and releasing pry bar, observe maximum dial
indicator value.
Vertical end play: 0 mm (0 in)
f) If ball joint movement is beyond specifications, remove and
replace it.
BALANCING WHEELSNLSU0042+Adjust wheel balance using road wheel center.
Wheel balance (Maximum allowable unbalance):
Refer to SDS, SU-16.
FRONT SUSPENSION
On-vehicle Service
SU-6
Page 3030 of 3051
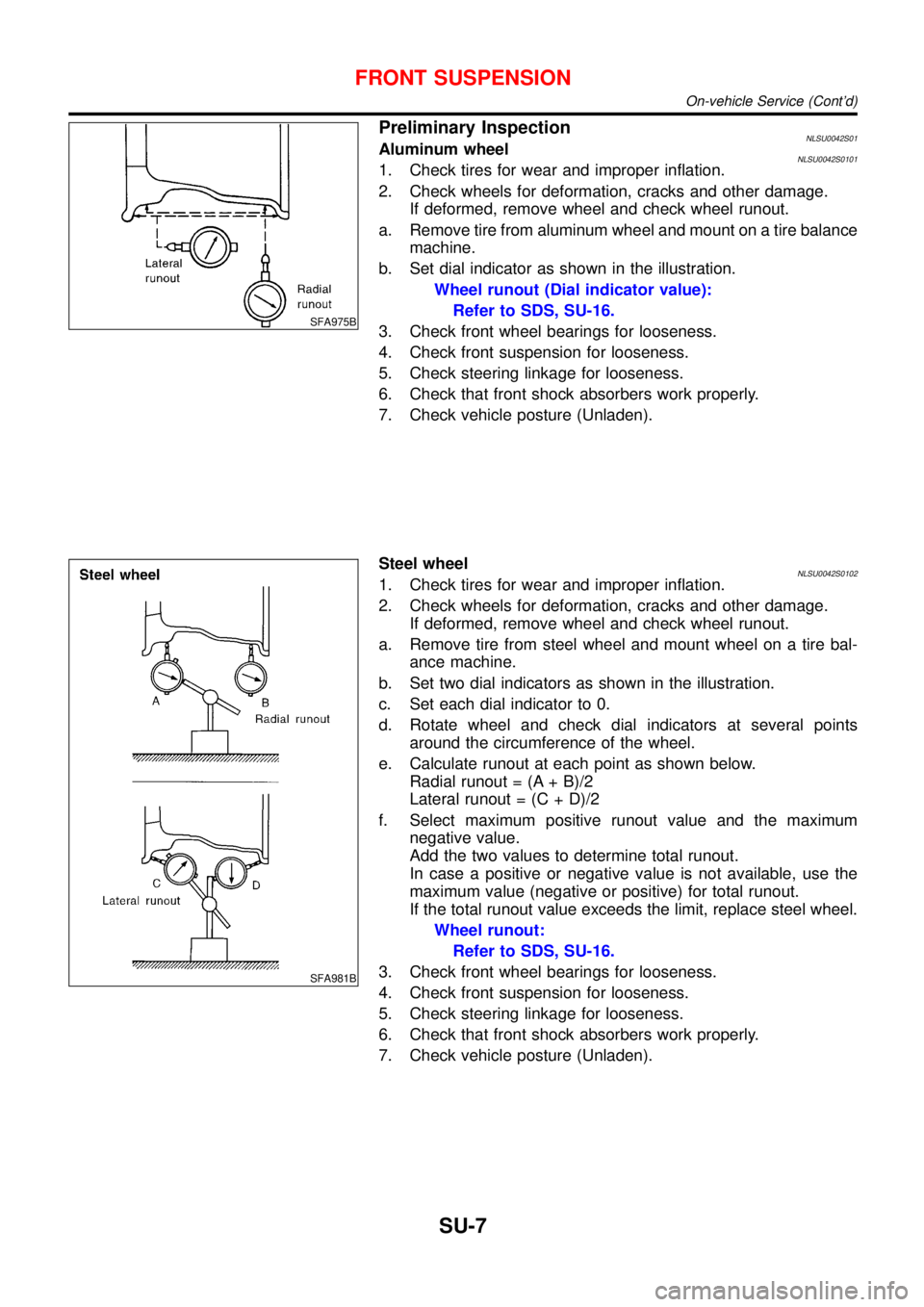
SFA975B
Preliminary InspectionNLSU0042S01Aluminum wheelNLSU0042S01011. Check tires for wear and improper inflation.
2. Check wheels for deformation, cracks and other damage.
If deformed, remove wheel and check wheel runout.
a. Remove tire from aluminum wheel and mount on a tire balance
machine.
b. Set dial indicator as shown in the illustration.
Wheel runout (Dial indicator value):
Refer to SDS, SU-16.
3. Check front wheel bearings for looseness.
4. Check front suspension for looseness.
5. Check steering linkage for looseness.
6. Check that front shock absorbers work properly.
7. Check vehicle posture (Unladen).
SFA981B
Steel wheelNLSU0042S01021. Check tires for wear and improper inflation.
2. Check wheels for deformation, cracks and other damage.
If deformed, remove wheel and check wheel runout.
a. Remove tire from steel wheel and mount wheel on a tire bal-
ance machine.
b. Set two dial indicators as shown in the illustration.
c. Set each dial indicator to 0.
d. Rotate wheel and check dial indicators at several points
around the circumference of the wheel.
e. Calculate runout at each point as shown below.
Radial runout = (A + B)/2
Lateral runout = (C + D)/2
f. Select maximum positive runout value and the maximum
negative value.
Add the two values to determine total runout.
In case a positive or negative value is not available, use the
maximum value (negative or positive) for total runout.
If the total runout value exceeds the limit, replace steel wheel.
Wheel runout:
Refer to SDS, SU-16.
3. Check front wheel bearings for looseness.
4. Check front suspension for looseness.
5. Check steering linkage for looseness.
6. Check that front shock absorbers work properly.
7. Check vehicle posture (Unladen).
FRONT SUSPENSION
On-vehicle Service (Cont’d)
SU-7