check engine NISSAN GT-R 1998 User Guide
[x] Cancel search | Manufacturer: NISSAN, Model Year: 1998, Model line: GT-R, Model: NISSAN GT-R 1998Pages: 230, PDF Size: 12.66 MB
Page 40 of 230
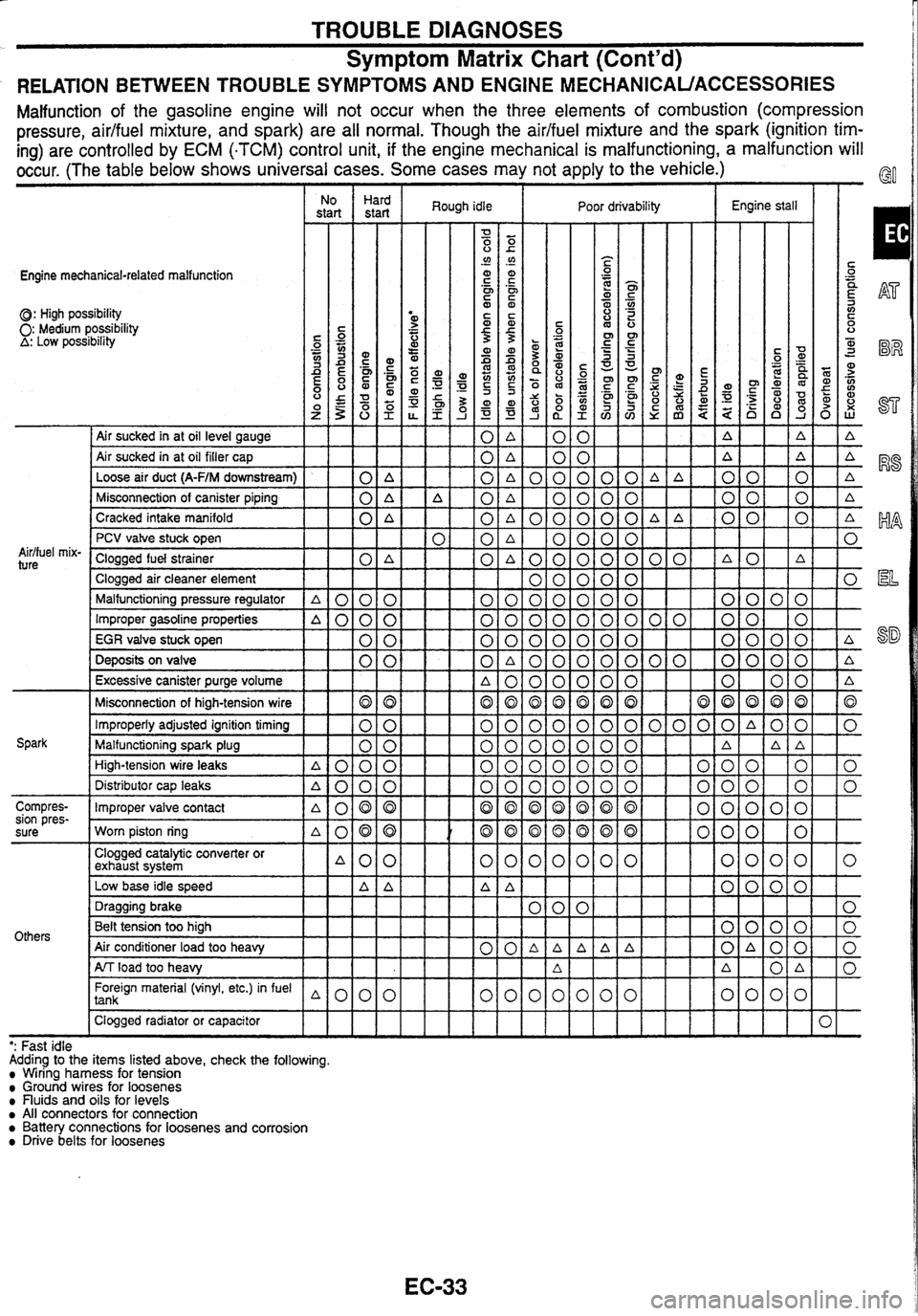
TROUBLE DIAGNOSES
Symptom Matrix Chart (Cont'd)
RELATION BETWEEN TROUBLE SYMPTOMS AND ENGINE MECHANICAUACCESSORIES
Malfunction of the gasoline engine will not occur when the three elements of combustion (compression
pressure, aidfuel mixture, and spark) are all normal. Though the
aidfuel mixture and the spark (ignition tim-
ing) are controlled by ECM
(.TCM) control unit, if the engine mechanical is malfunctioning,
a malfunction will
occur. (The table below shows universal cases. Some cases may not apply to the vehicle.)
Engine mechanical-related malfunction
0: High possibility 0: Medium possibility A: Low posstbility
I No I Hard
start start
I Air sucked in at oil level gauge
Air sucked in at oil filler cap
Loose air duct
(A-F/M downstream) 0 A
Misconnection of canister piping
0 A
Cracked intake manifold
0 A
Aidfuel
mix-
ture
PCV valve stuck open
Clogged fuel strainer
0 A
Clogged air cleaner element
Malfunctioning pressure regulator
A 0 0 0
Improper gasoline properties A000
EGR valve stuck open 0 0
Deposits on valve 0 0
Excessive canister purge volume
Misconnection of high-tension wire
Improperly adjusted ignition timing
Malfunctioning spark plug
High-tension wire leaks
A000
Spark Distributor cap leaks
A000
Compres-
Improper valve contact
sion pres-
. a080
sure Worn piston ring ~080
Others
Clogged catalytic converter or
exhaust system A00
Low base idle speed A
A
Foreign material (vinyl, etc.) in fuel 1 tank
Clogged radiator or capacitor
IIII
Rough idle I Poor drivability Engine stall
- - - - - - -- ': Fast
idle
Adding to the items listed above, check the following.
Wiring harness for tension Ground wires for loosenes nuids and oils for levels All connectors for connection Battery connections for loosenes and corrosion Drive belts for loosenes
Page 41 of 230
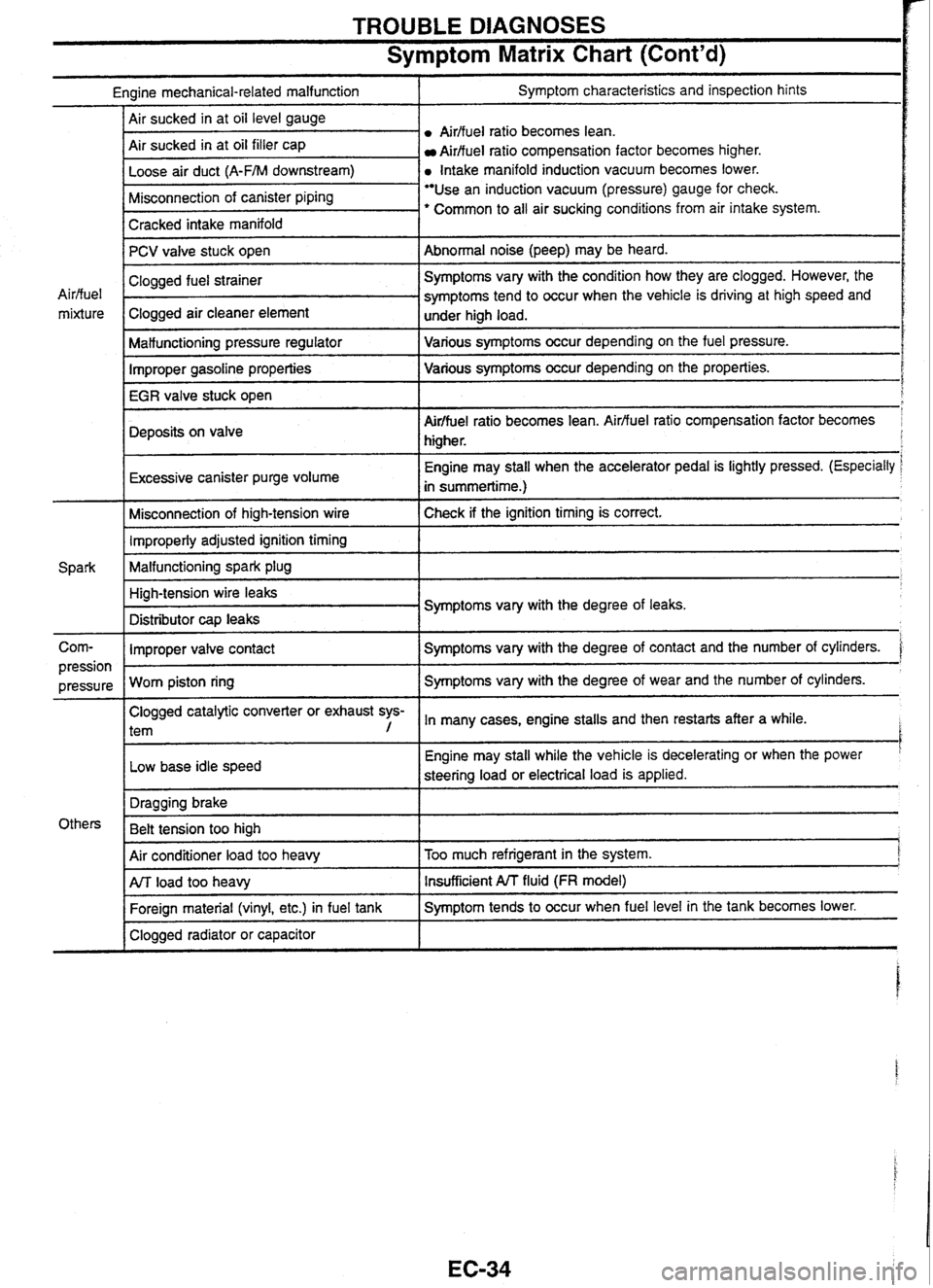
TROUBLE DIAGNOSES
Symptom Matrix Chart (Cont'd)
Engine mechanical-related malfunction I Symptom characteristics and inspection hints
Airffuel
ratio becomes lean.
Air sucked in at oil filler cap
Aidfuel ratio compensation factor becomes higher.
a Intake manifold induction vacuum becomes lower.
I Cracked intake manifold I
Misconnection of canister piping Use an induction vacuum (pressure) gauge for check.
' Common to all air sucking conditions from air intake system.
-
PCV valve stuck open
I Malfunctioning pressure regulator I Various symptoms occur depending on the fuel pressure.
Abnormal noise (peep) may
be heard.
Air/fuel
mixture
Improper gasoline properties Various
symptoms occur depending on the properties.
IEGRiale
stuck open
I
Clogged fuel strainer .
Clogged air cleaner element
Deposits on valve
r
Symptoms vary with the condition how they are clogged. However, the
symptoms tend to occur when the vehicle is driving at high speed and
under high load.
I
Air/fuel ratio becomes lean. Airfluel ratio compensation factor becomes
higher.
Excessive canister purge volume
I
Engine may stall when the accelerator pedal is lightly pressed. (Especially
in summertime.)
Misconnection of high-tension wire Check if the ignition timing
is correct. 1 Improperly adjusted ignition timing 1
Malfunctioning spark plug 1
Corn- I Improper valve contact I Symptoms vary with the degree of contact and the number of cylinders. '
High-tension wire leaks
Distributor
cap leaks Symptoms
vary with the degree of leaks.
Clogged catalytic converter or exhaust sys-
l tem , In many cases, engine stalls and then restarts after a while. I
pression I
Low base idle speed
pressure
Worn piston ring I
Engine may
stall while the vehicle is decelerating or when the power '
steering load or electrical load is applied.
Symptoms vary
with the degree of wear and the number of cylinders.
I
Air conditioner load too heavy I Too much refrigerant in the system. j
Others Dragging
brake
Belt tension too high
1
I Clogged radiator or capacitor I
ArJ load too heavy
Foreign material (vinyl, etc.) in fuel tank Insufficient A/T fluid (FR model)
Symptom tends to occur when fuel level in the tank becomes lower.
Page 42 of 230
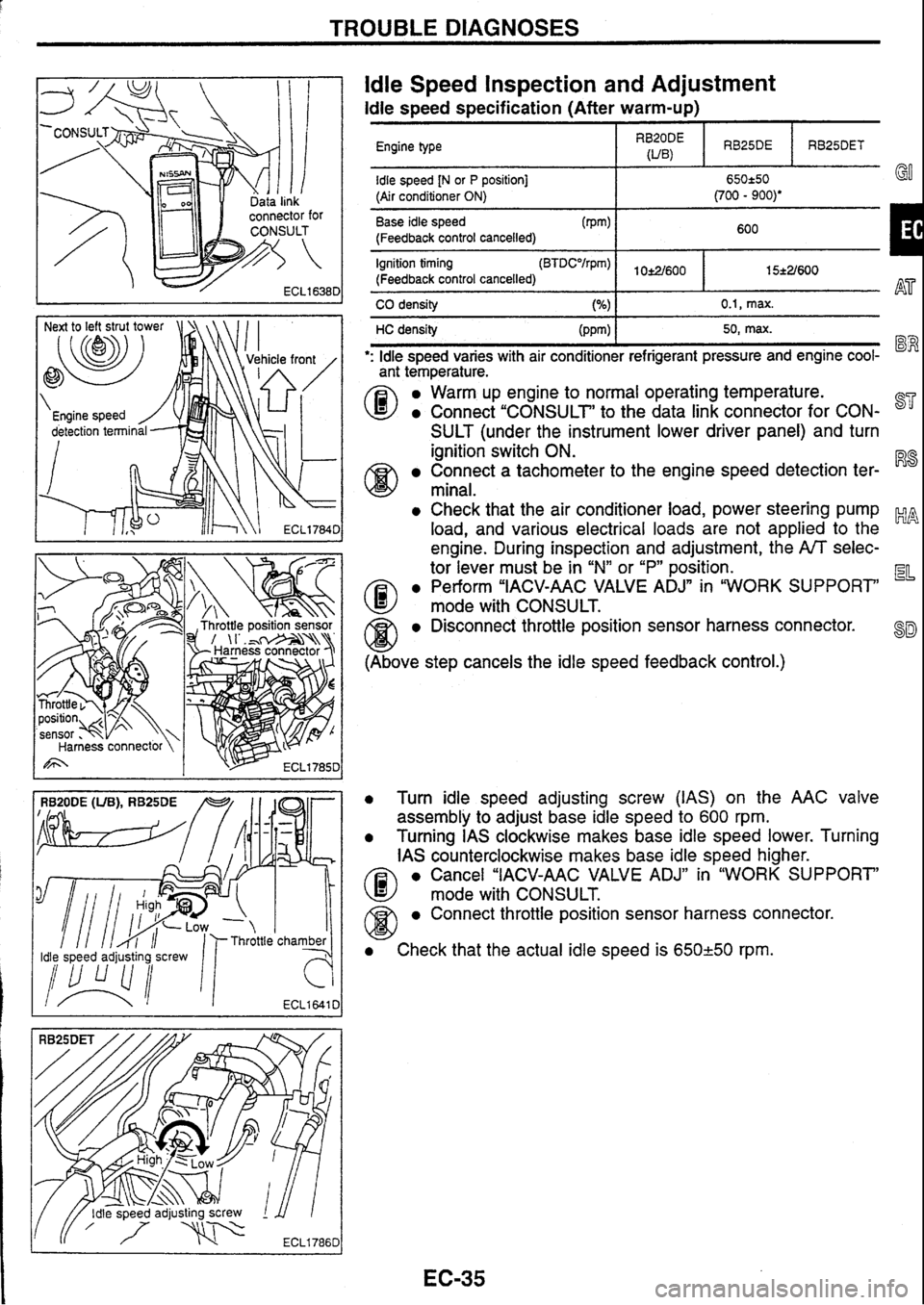
TROUBLE DIAGNOSES
ldle speed adjusting screw
ECL1641 C
ldle Speed Inspection and Adjustment
ldle speed specification (After warm-up)
Engine type I RygE I RB25DE I RB25DET
Base idle speed (Pm)
(Feedback control cancelled) 600
I 1
idle speed [N or P position] (Air conditioner ON)
Ignition timing
(Feedback control cancelled) I 15*2/600
. . I I
650250 Go (700 - 900)'
CO density 0.1, max.
HC density 50, max.
': ldle speed varies with air conditioner refrigerant pressure and engine cool- "" "
ant temperature.
0
a Warm up engine to normal operating temperature.
a Connect "CONSULT' to the data link connector for CON- 87'
SULT (under the instrument lower driver panel) and turn
ignition switch ON.
Connect a tachometer to the engine speed detection ter- R8
minal.
a Check that the air conditioner load, power steering pump ~p, -4 load, and various electrical loads are not applied to the
engine. During inspection and adjustment, the
A/T selec-
tor lever must be in
"N"
or
"P"
position.
a Perform "IACV-AAC VALVE ADJn in "WORK SUPPORT EL
@ mode with CONSULS.
@ a Disconnect throttle position sensor harness connector. 8~
(Above step cancels the idle speed feedback control.)
0 Turn idle speed adjusting screw (IAS) on the AAC valve
assembly to adjust base idle speed to
600 rpm.
a Turning IAS clockwise makes base idle speed lower. Turning
IAS counterclockwise makes base idle speed higher.
a Cancel "IACV-AAC VALVE ADJ" in "WORK SUPPORT'
@ mode with CONSULT.
a Connect throttle position sensor harness connector.
a Check that the actual idle speed is 650-1-50 rpm.
Page 43 of 230
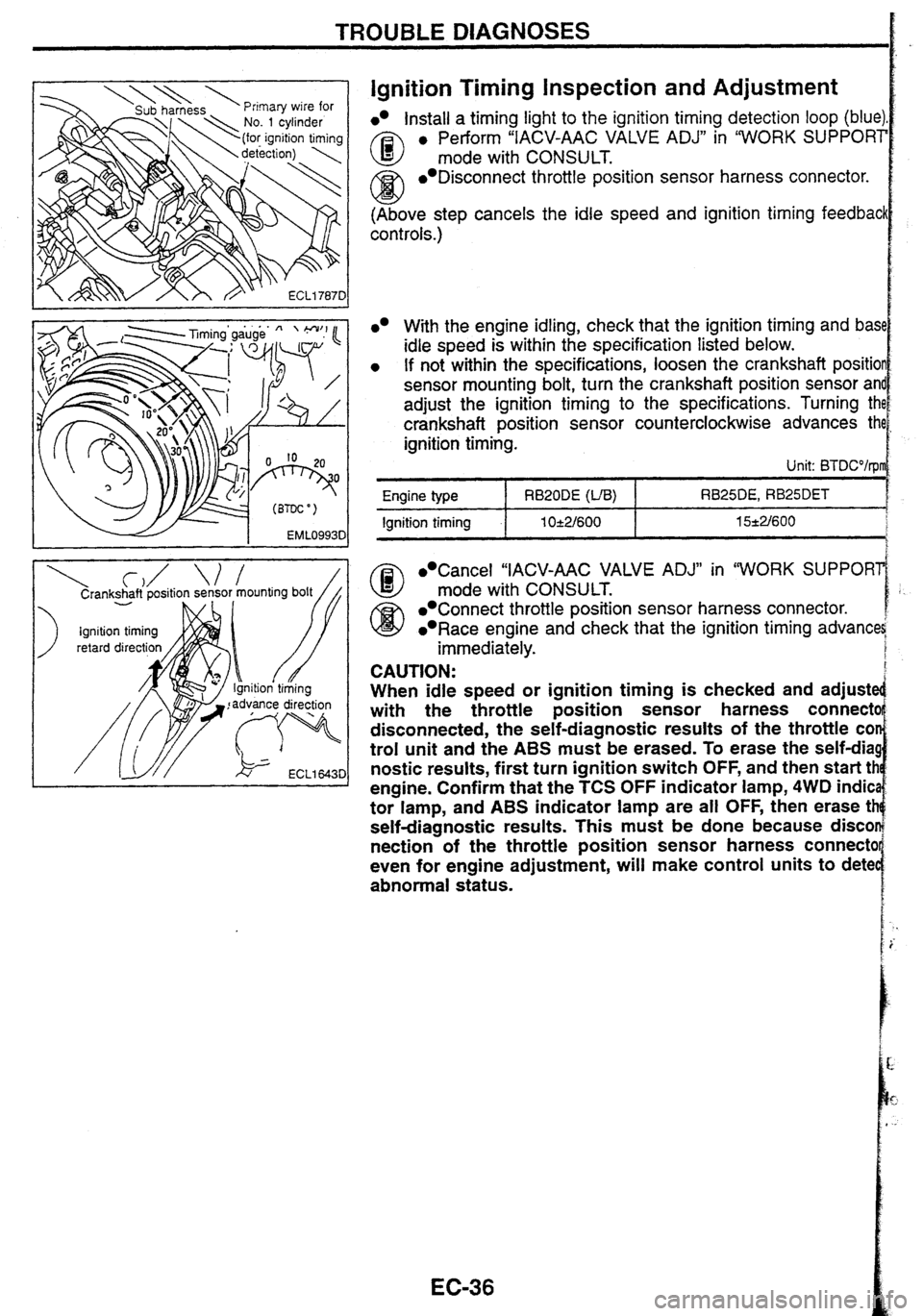
TROUBLE DlAGNOSES
Ignition Timing inspection and Adjustment
lnstall a timing light to the ignition timing detection loop (blue)
A3 e Perform "IACV-AAC VALVE ADJ" in "WORK SUPPORT
mode with CONSULT.
/Ci3 Disconnect throttle position sensor harness connector.
w (Above step cancels the idle speed and ignition timing feedbacl
cont rots.)
Cancel "IACV-AAC VALVE ADJ" in "WORK SUPPORl
@ mode with CONSULT.
Connect throttle position sensor harness connector.
Race engine and check that the ignition timing advana
immediately.
With the engine idling, check that the ignition timing and bas1
idle speed is within the specification listed below.
If not within the specifications, loosen the crankshaft positio
sensor mounting bolt, turn the crankshaft position sensor
an
adjust the ignition timing to the specifications. Turning th
crankshaft position sensor counterclockwise advances th
ignition timing.
Unit: BTDCO/rpl
CAUTION:
When idle speed or ignition timing is checked and adjuste
with the throttle position sensor harness
connectc
disconnected, the self-diagnostic results of the throttle
COI
trol unit and the ABS must be erased. To erase the self-dia!
nostic
results, first turn ignition switch OFF, and then start tt
engine. Confirm that the
TCS OFF indicator lamp, 4WD indic
tor lamp, and
ABS indicator lamp are all OFF, then erase tt
self-diagnostic results. This must be done because disco
nection
of the throttle position sensor harness connectc
even for engine adjustment,
will make control units to dete
abnormal status.
RB25DE, RB25DET
15*2/600 Engine type
Ignition timing
RB20DE (VB)
1 O-e2/600
Page 44 of 230
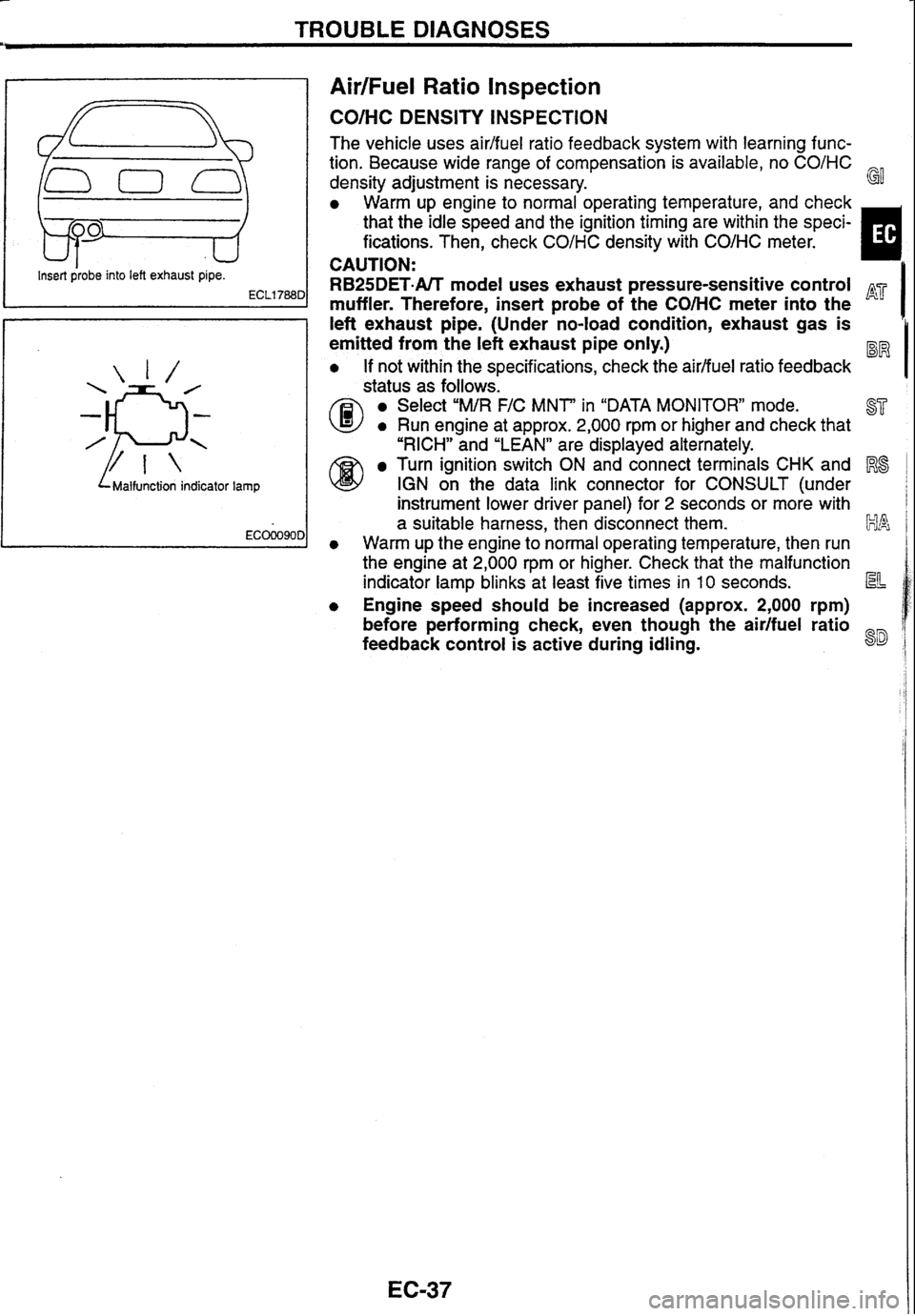
TROUBLE DIAGNOSES
AirIFuel Ratio Inspection
Insert probe into left exhaust pipe.
ECLl788D
L Malfunction indicator lamp
CO/HC DENSITY INSPECTION
The vehicle uses aidfuel ratio feedback system with learning func-
tion. Because wide range of compensation is available, no
CO/HC
density adjustment is necessary. G!
Warm up engine to normal operating temperature, and check
that the idle speed and the ignition timing are within the speci-
fications. Then, check
CO/HC density with COIHC meter.
CAUTION:
muffler. Therefore, insert probe of the COMC meter into the
I
RB25DET-NT model uses exhaust pressure-sensitive control
I left exhaust pipe. (under -no-load condition, exhaust gas is
emitted from the left exhaust pipe only.)
a If not within the specifications, check the airlfuel ratio feedback
@status as follows.
Select "MIR FIC MNT" in "DATA MONITOR" mode.
a Run engine at approx. 2,000 rpm or higher and check that ST
I "RICH" and "LEAN" are displayed alternately.
Turn ignition switch ON and connect terminals CHK and Rs
@ IGN on the data link connector for CONSULT (under
instrument lower driver panel) for
2 seconds or more with
a suitable harness, then disconnect them. klk~
a Warm up the engine to normal operating temperature, then run
the engine at 2,000
rpm or higher. Check that the malfunction
indicator lamp blinks at least five times in
10 seconds. La=
0 Engine speed should be increased (approx. 2,000 rpm)
before performing check, even though the
air/fuel ratio
feedback control is active during idling.
8D
Page 45 of 230
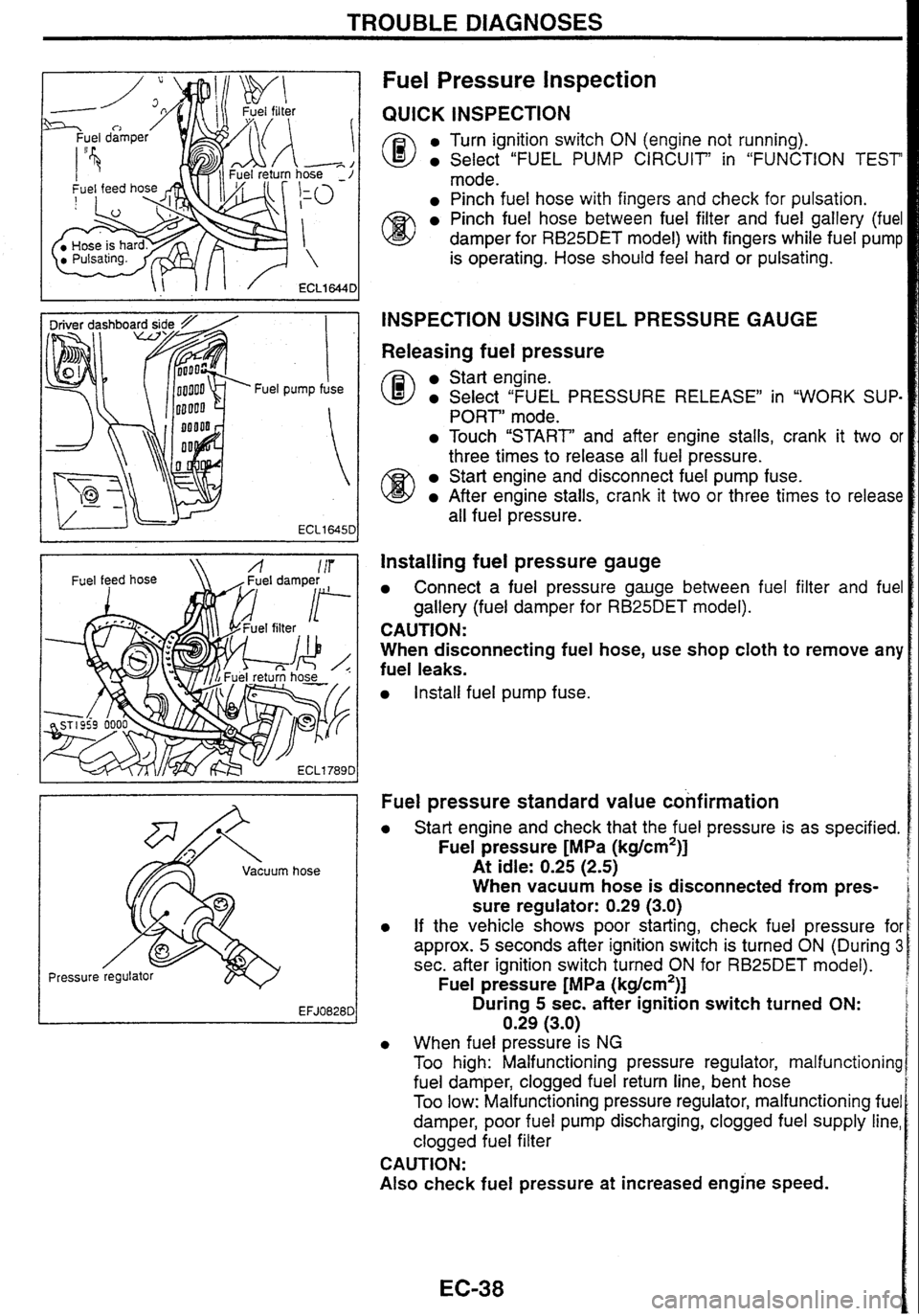
TROUBLE DIAGNOSES
Fuel Pressure Inspection
Fuel pump fuse
Pressure hose
QUICK
INSPECTION
0 Turn ignition switch ON (engine not running).
Select "FUEL PUMP CIRCUIT' in "FUNCTION TEST
mode.
Pinch fuel hose with fingers and check for pulsation.
Pinch fuel hose between fuel filter and fuel gallery (fue
@ damper for RB2SDET model) with fingers while fuel puml
is operating. Hose should feel hard or pulsating.
INSPECTION USING FUEL PRESSURE GAUGE
Releasing fuel pressure
Start engine.
Select "FUEL PRESSURE RELEASE" in "WORK SUP
PORT' mode.
Touch "START' and after engine stalls, crank it two o
three times to release all fuel pressure.
Start engine and disconnect fuel pump fuse.
After engine stalls, crank it two or three times to releas
all fuel pressure.
Installing fuel pressure gauge
Connect a fuel pressure gauge between fuel filter and fue
gallery (fuel damper for
RB25DET model).
CAUTION:
When disconnecting fuel hose, use shop cloth to remove an!
fuel leaks.
Install fuel pump fuse.
Fuel pressure standard value confirmation
Start engine and check that the fuel pressure is as specified.
Fuel pressure [MPa (kg/cm2)]
At idle: 0.25 (2.5)
When vacuum hose is disconnected from pres-
sure regulator:
0.29 (3.0)
If the vehicle shows poor starting, check fuel pressure fo
approx.
5 seconds after ignition switch is turned ON (During :
sec. after ignition switch turned ON for RB25DET model).
Fuel pressure [MPa (kg/cm2)]
During 5 sec. after ignition switch turned ON:
0.29 (3.0)
When fuel pressure is NG
Too high: Malfunctioning pressure regulator, malfunction in^
fuel damper, clogged fuel return line, bent hose
Too low: Malfunctioning pressure regulator, malfunctioning fue
damper, poor fuel pump discharging, clogged fuel supply line
clogged fuel filter
CAUTION:
Also check fuel pressure at increased engine speed.
Page 47 of 230
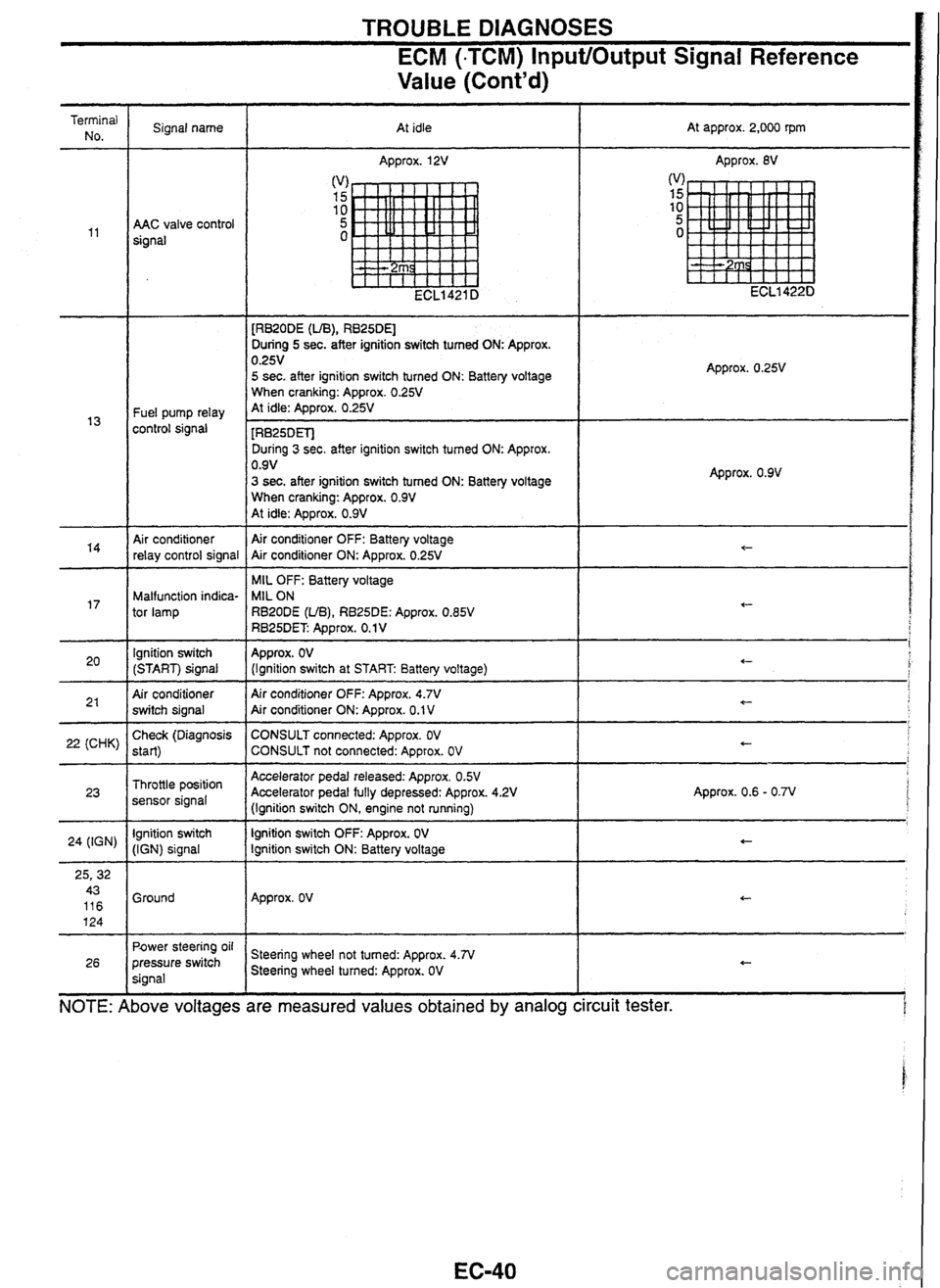
TROUBLE DIAGNOSES
ECM (-TCM) InputlOutput Signal Reference
Value (Cont'd)
d
voltages are
Terminal No. Signal name
At idle At
approx. 2,000 rpm
Approx.
12V Approx. 8V
AAC valve control
signal
[RB20DE
(UB), RB25DEl
During 5 sec. after ignition switch tumed ON: Approx. 0.25V 5 sec. after ignition switch turned ON: Battery voltage
When cranking: Approx. 0.25V At idle: Approx. 0.25V Fuel pump relay
control signal - - [RB25DETJ
During 3 sec. after ignition switch tumed ON: Approx.
0.9V
3 sec. after ignition switch tumed ON: Battery voltage
When cranking: Approx. 0.9V At idle: Approx. 0.9V
Approx. 0.9V
Air conditioner
relay control signal Air conditioner
OFF: Battery voltage
Air conditioner ON: Approx. 0.25V
MIL OFF: Battery voltage
MIL ON
RBZODE
(UB), RB25DE: Approx. 0.85V RB25DET Approx. 0.1 V
Malfunction indica-
tor lamp
lgnition switch
(START) signal
Air conditioner
switch signal Approx.
OV (Ignition
switch at START Battery voltage)
Air conditioner OFF: Approx.
4.7V Air conditioner ON: Approx. 0.1 V -
22 (CHK) Check
(Diagnosis
start)
Throttle position
sensor signal
lgnition switch
(IGN) signal CONSULT
connected: Approx. OV CONSULT not connected: Approx. OV
Accelerator pedal released: Approx. OSV Accelerator pedal fully depressed: Approx. 4.2V
(Ignition switch ON, engine not running)
lgnition switch
OFF: Approx. OV lgnition switch ON: Battery voltage Approx.
0.6 - 0.7V
24
(IGN)
Ground Approx.
OV
Power
steering oil
pressure switch
signal Steering
wheel not tumed: Approx. 4.N Steering wheel turned: Approx. OV
26
NOTE: I bove measured values obtained by analog ircuit
tester.
Page 68 of 230
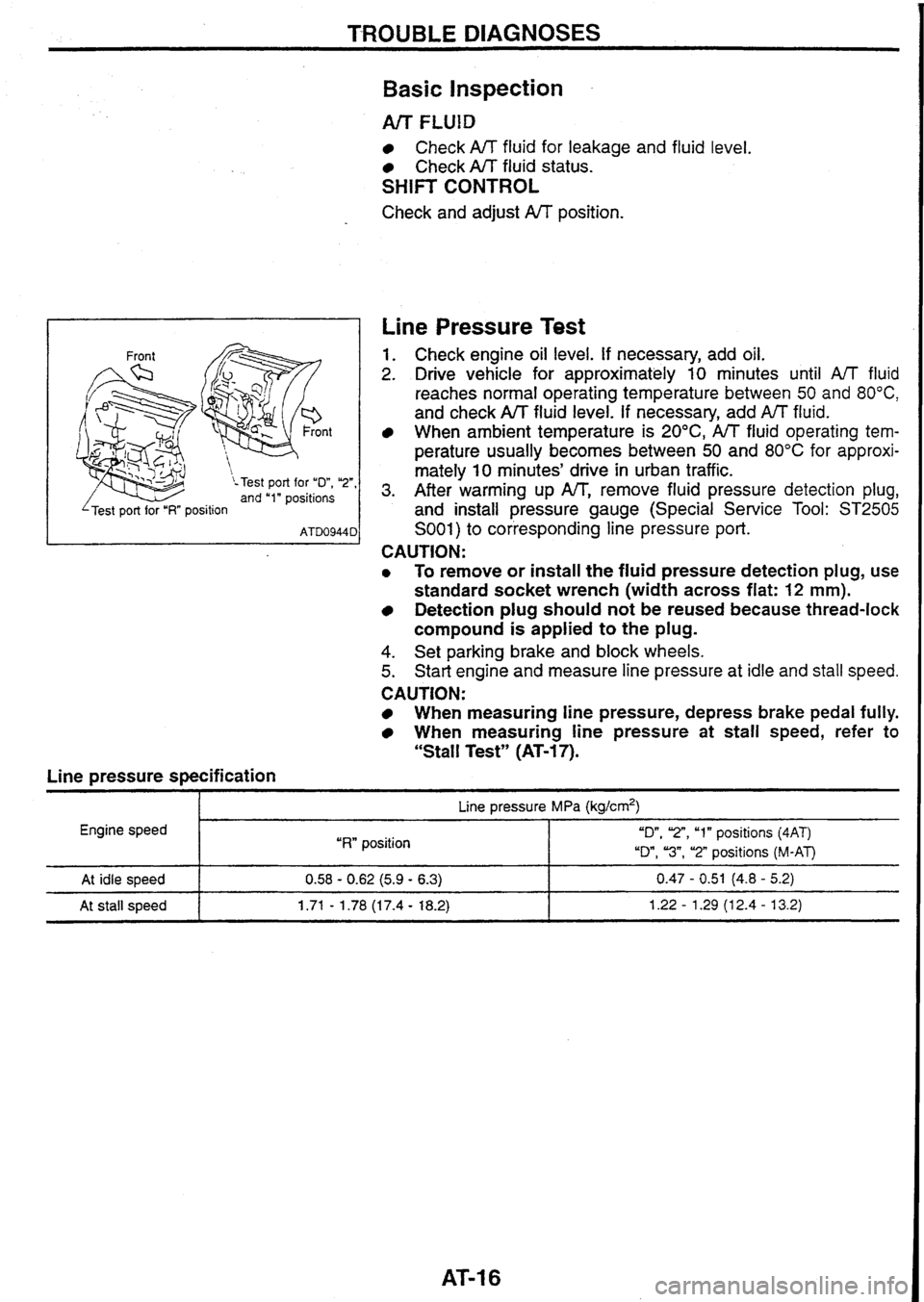
TROUBLE DIAGNOSES
n t
\-Test port for "D", "2", and "1" positions
I 'Test port for "I?" position I
Line pressure specification
Basic Inspection
Arr FLUlD
Check A/T fluid for leakage and fluid level.
Check A/T fluid status.
SHIFT CONTROL
Check and adjust A/T position.
Line Pressure Test
1. Check engine oil level. If necessary, add oil.
2. Drive vehicle for approximately 10 minutes until A/T fluid
reaches normal operating temperature between
50 and 80°C,
and check A/T fluid level. If necessary, add fluid.
When
ambient temperature is 20°C, A/T fluid operating tem-
perature
usually becomes between 50 and 80°C for approxi-
mately
10 minutes' drive in urban traffic.
3. After warming up IW', remove fluid pressure detection plug,
and install pressure gauge (Special Service Tool:
ST2505
S001) to corresponding line pressure port.
CAUTION:
0 To remove or install the fluid pressure detection plug, use
standard socket wrench (width across flat:
12 mm).
Detection plug should not be reused because thread-lock
compound is applied
to the plug.
4. Set parking brake and block wheels.
5. Start engine and measure line pressure at idle and stall speed.
CAUTION:
When measuring line pressure, depress brake pedal fully.
When measuring line pressure at stall speed, refer to
"Stall Test" (AT-17).
I p- Line pressure MPa (kg/crn2)
Engine speed
I "RW position "On, 'Z", "1" positions (4AT)
"Dm,
"3", "2" positions (M-AT)
At idle speed
At stall speed 0.58 - 0.62 (5.9 - 6.3) 0.47 - 0.51 (4.8 - 5.2)
1.71
- 1.78 (1 7.4 - 18.2) 1.22 - 1.29 (1 2.4 - 13.2)
Page 69 of 230
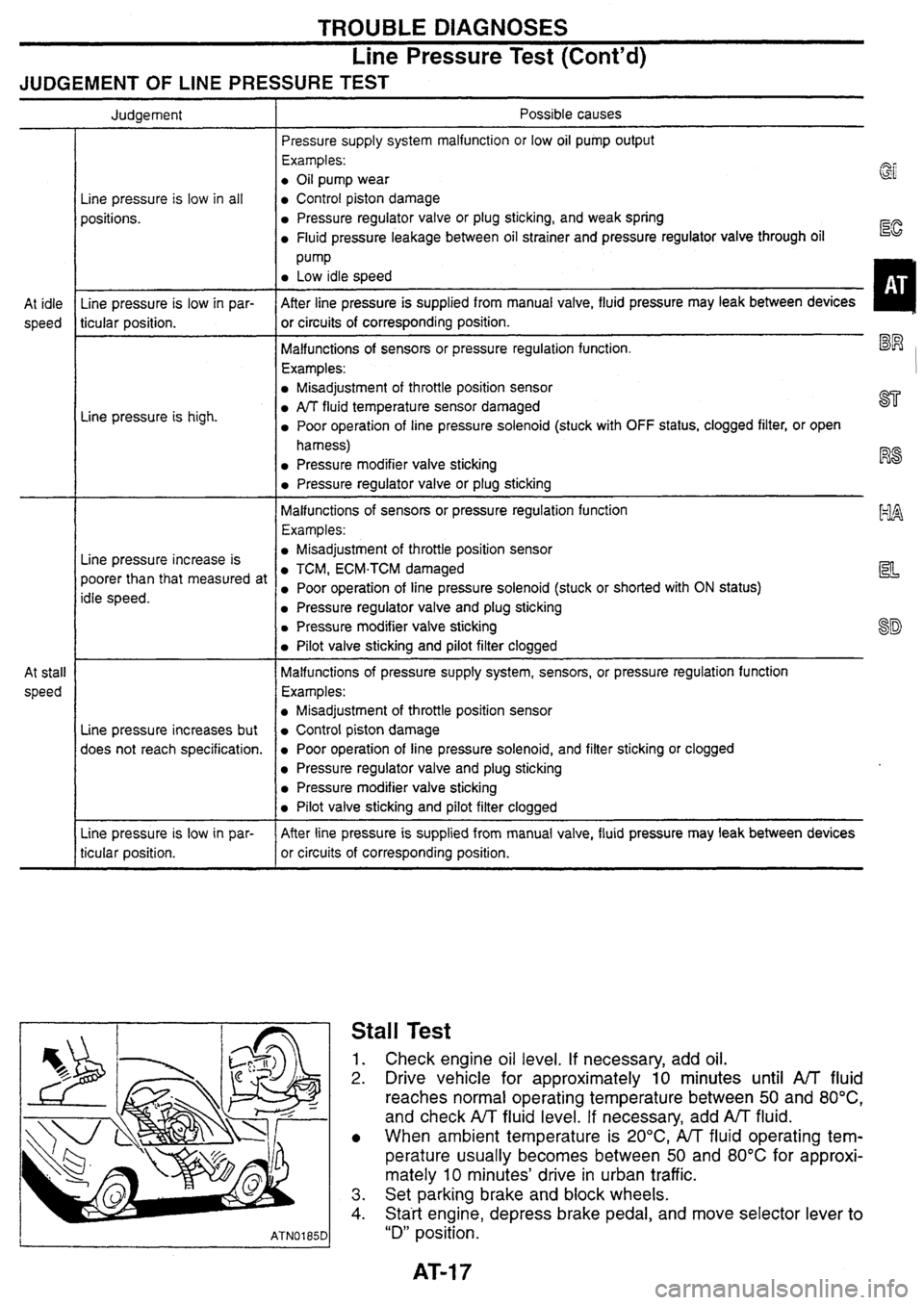
TROUBLE DIAGNOSES
Line Pressure Test (Cont'd)
JUDGEMENT OF LINE PRESSURE TEST
At idle
speed
At stall
speed Judgement
Line pressure is low in all
positions.
Line pressure is low in par-
ticular position.
Line pressure is
high.
Line pressure increase is
poorer than that measured at
idle speed.
Line pressure increases but
does not reach specification.
Line pressure is low in par-
ticular position. Possible
causes
Pressure supply system malfunction or low oil pump output
Examples:
0 Oil pump wear
Control piston damage
Pressure regulator valve or plug sticking, and weak spring
Fluid pressure leakage between oil strainer and pressure regulator valve through oil Eg
Pump
Low idle speed
After line pressure is supplied from manual valve, fluid pressure may leak between devices
or circuits of corresponding position.
1
Malfunctions of sensors or pressure regulation function. El
Examples:
Misadjustment of throttle position sensor
PJT fluid temperature sensor damaged ST
Poor operation of line pressure solenoid (stuck with OFF status, clogged filter, or open
harness)
Pressure modifier valve sticking F%
Pressure regulator valve or plug sticking
Malfunctions of sensors or pressure regulation function
Examples:
EILA
Misadjustment of throttle position sensor
TCM, ECM.TCM damaged la
Poor operation of line pressure solenoid (stuck or shorted with ON status)
Pressure regulator valve and plug sticking
Pressure modifier valve sticking
sf$
Pilot valve sticking and pilot filter clogged
Malfunctions of pressure supply system, sensors, or pressure regulation function
Examples:
Misadjustment of throttle position sensor
Control piston damage
Poor operation of line pressure solenoid, and filter sticking or clogged
Pressure regulator valve and plug sticking
Pressure modifier valve sticking
Pilot valve sticking and pilot filter clogged
After line pressure is supplied from manual valve, fluid pressure
may leak between devices
or circuits of corresponding position.
Stall Test
1. Check engine oil level. If necessary, add oil.
2. Drive vehicle for approximately 10 minutes until A/T fluid
reaches normal operating temperature between
50 and 80°C,
and check A/T fluid level. If necessary, add AfT fluid.
When ambient temperature is
20°C,
A/T fluid operating tem-
perature usually becomes between 50 and
80°C for approxi-
mately
10 minutes' drive in urban traffic.
3. Set parking brake and block wheels.
4. Statt engine, depress brake pedal, and move selector lever to
"D" position.
Page 71 of 230
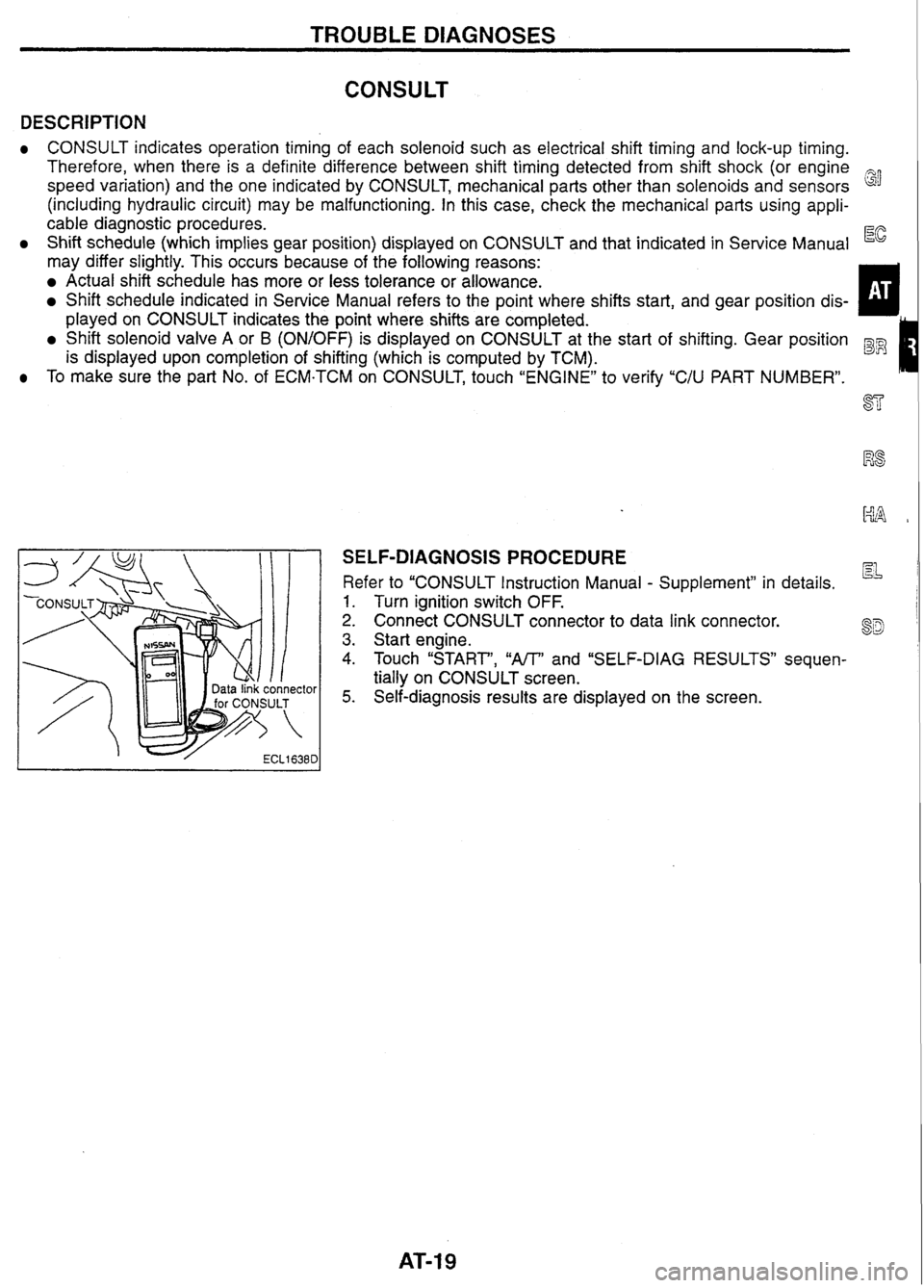
TROUBLE DIAGNOSES
DESCRIPTION
CONSULT indicates operation timing of each solenoid such as electrical shift timing and lock-up timing.
Therefore, when there is a definite difference between shift timing detected from shift shock (or engine
speed variation) and the one indicated by CONSULT, mechanical parts other than solenoids and sensors
(including hydraulic circuit) may be malfunctioning. In this case, check the mechanical parts using appli-
cable diagnostic procedures.
Shift schedule (which implies gear position) displayed on CONSULT and that indicated in Service Manual
may differ slightly. This occurs because of the following reasons:
Actual shift schedule has more or less tolerance or allowance.
Shift schedule indicated in Service Manual refers to the point where shifts start, and gear position dis-
played on CONSULT indicates the point where shifts are completed.
Shift solenoid valve A or B (ON/OFF) is displayed on CONSULT at the start of shifting. Gear position
is displayed upon completion of shifting (which is computed by TCM).
To make sure the part No. of ECM-TCM on CONSULT, touch "ENGINE" to verify "C/U PART NUMBER".
SELF-DIAGNOSIS PROCEDURE
Refer to "CONSULT Instruction Manual - Supplement" in details.
1. Turn ignition switch OFF.
2. Connect CONSULT connector to data link connector.
3. Start engine.
4. Touch "START', "NT and "SELF-DIAG RESULTS" sequen-
tially on CONSULT screen.
5. Self-diagnosis results are displayed on the screen.