check engine light NISSAN PULSAR 1987 User Guide
[x] Cancel search | Manufacturer: NISSAN, Model Year: 1987, Model line: PULSAR, Model: NISSAN PULSAR 1987Pages: 238, PDF Size: 28.91 MB
Page 56 of 238
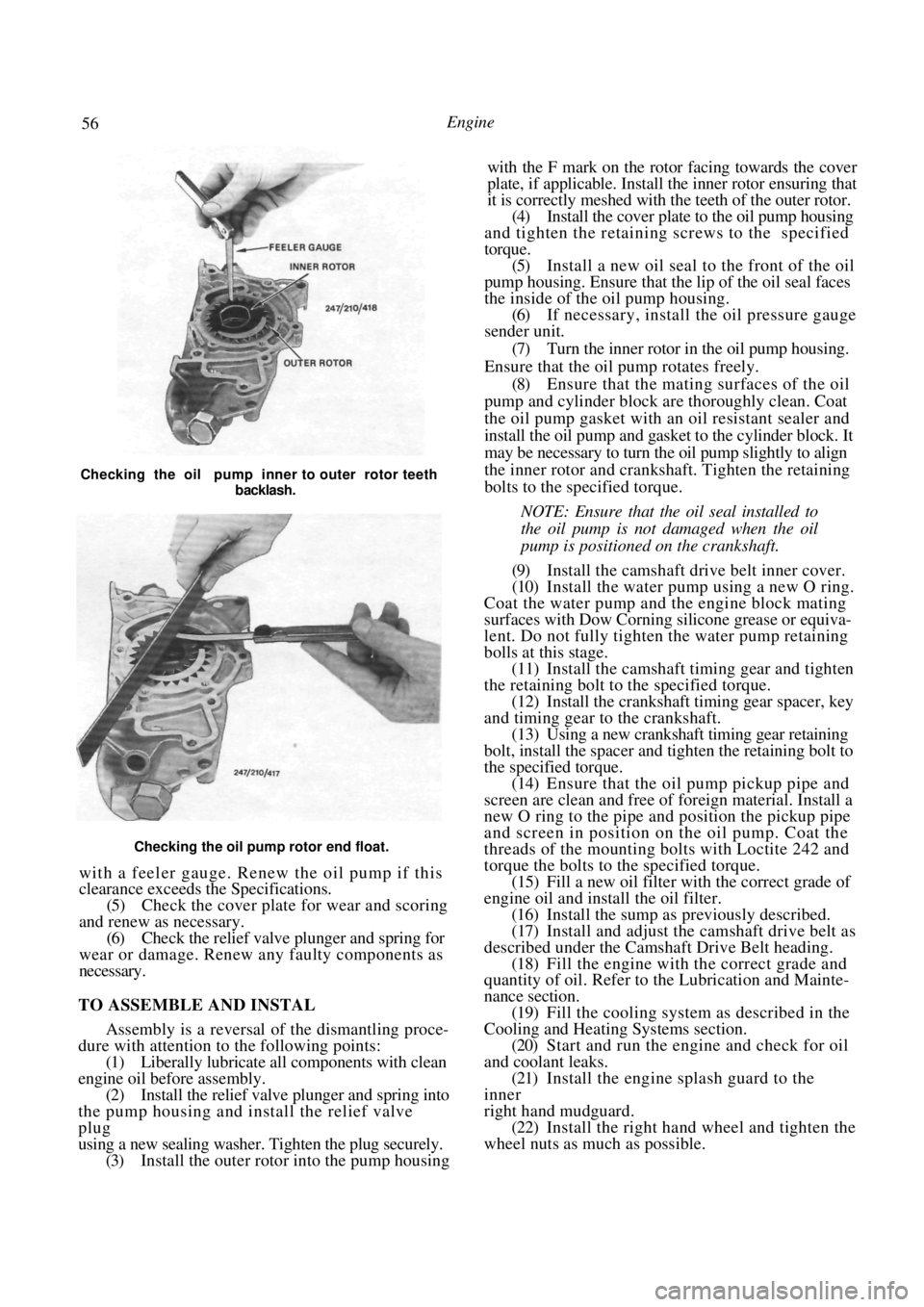
56 Engine
Checking the oil pump rotor end float.
with a feeler gauge. Renew the oil pump if this
clearance exceeds the Specifications.
(5) Check the cover plate for wear and scoring
and renew as necessary. (6) Check the relief valve plunger and spring for
wear or damage. Renew any faulty components as
necessary.
TO ASSEMBLE AND INSTAL
Assembly is a reversal of the dismantling proce-
dure with attention to the following points:
(1) Liberally lubricate all components with clean
engine oil before assembly. (2) Install the relief valve plunger and spring into
the pump housing and install the relief valve
plug
using a new sealing washer. Tighten the plug securely. (3) Install the outer rotor into the pump housing with the F mark on the rotor facing towards the cover
plate, if applicable. Install the inner rotor ensuring that
it is correctly meshed with the teeth of the outer rotor.
(4)
Install the cover plate to the oil pump housing
and tighten the retaining screws to the specified
torque. (5) Install a new oil seal to the front of the oil
pump housing. Ensure that the lip of the oil seal faces
the inside of the oil pump housing. (6) If necessary, install the oil pressure gauge
sender unit.
(7) Turn the inner rotor in the oil pump housing.
Ensure that the oil pump rotates freely. (8) Ensure that the mating surfaces of the oil
pump and cylinder block are thoroughly clean. Coat
the oil pump gasket with an oil resistant sealer and
install the oil pump and gasket to the cylinder block. It
may be necessary to turn the oil pump slightly to align
the inner rotor and crankshaft. Tighten the retaining
bolts to the specified torque.
NOTE: Ensure that the oil seal installed to
the oil pump is not damaged when the oil
pump is positioned on the crankshaft.
(9) Install the camshaft drive belt inner cover.
(10) Install the water pump using a new O ring.
Coat the water pump and the engine block mating
surfaces with Dow Corning silicone grease or equiva-
lent. Do not fully tighten the water pump retaining
bolls at this stage. (11) Install the camshaft timing gear and tighten
the retaining bolt to the specified torque.
(12) Install the crankshaft timing gear spacer, key
and timing gear to the crankshaft. (13) Using a new crankshaft timing gear retaining
bolt, install the spacer and tighten the retaining bolt to
the specified torque. (14) Ensure that the oil pump pickup pipe and
screen are clean and free of foreign material. Install a
new O ring to the pipe and position the pickup pipe
and screen in position on the oil pump. Coat the
threads of the mounting bolts with Loctite 242 and
torque the bolts to the specified torque. (15) Fill a new oil filter with the correct grade of
engine oil and install the oil filter. (16) Install the sump as previously described.
(17) Install and adjust the camshaft drive belt as
described under the Camshaft Drive Belt heading. (18) Fill the engine with the correct grade and
quantity of oil. Refer to the Lubrication and Mainte-
nance section.
(19) Fill the cooling system as described in the
Cooling and Heating Systems section. (20) Start and run the engine and check for oil
and coolant leaks. (21) Install the engine splash guard to the
inner
right hand mudguard. (22) Install the right hand wheel and tighten the
wheel nuts as much as possible.
Checking the oil pump inner to outer rotor teeth
backlash.
Page 61 of 238
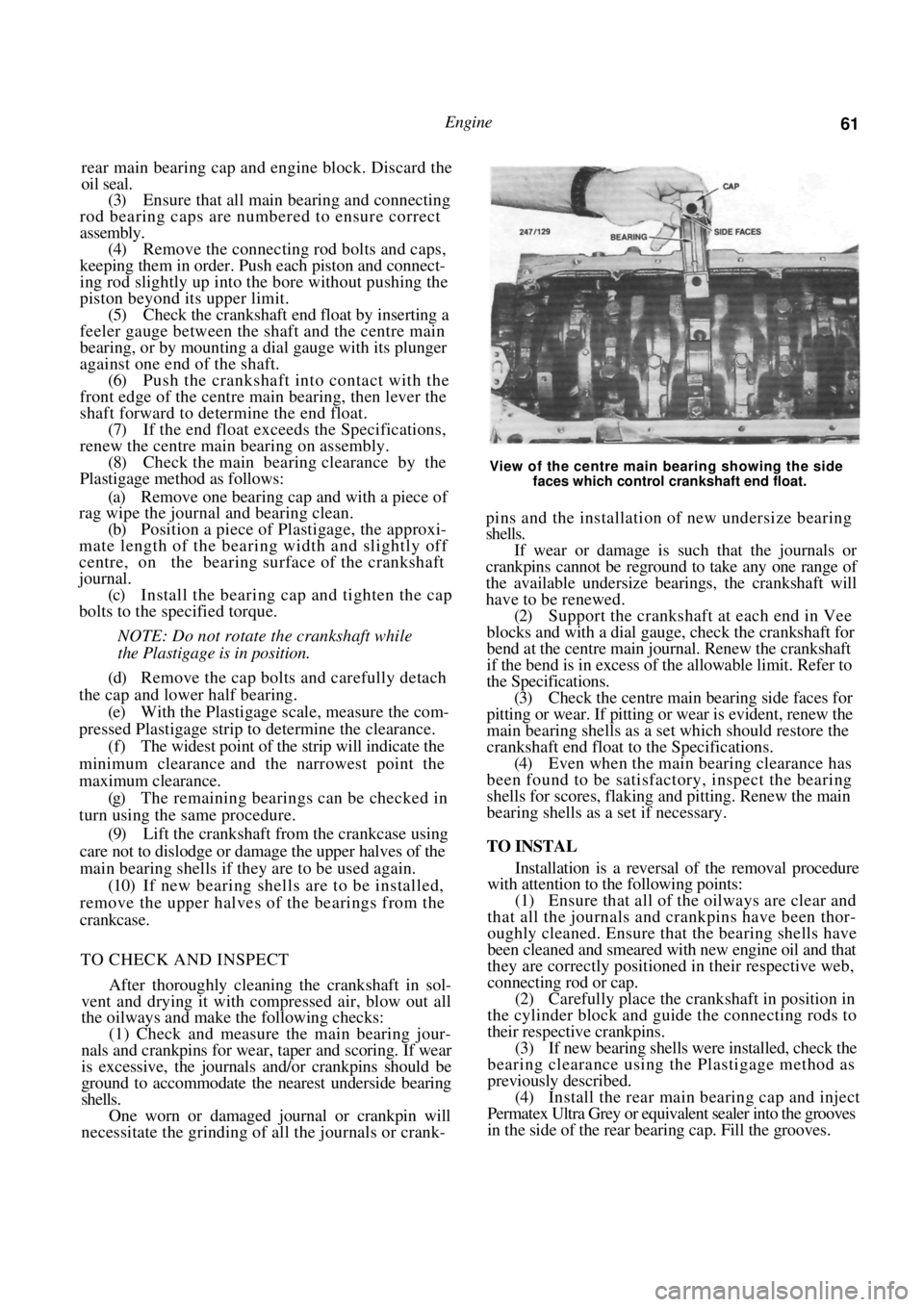
Engine 61
rear main bearing cap and engine block. Discard the
oil seal.
(3) Ensure that all main bearing and connecting
rod bearing caps are numbered to ensure correct
assembly. (4) Remove the connecting rod bolts and caps,
keeping them in order. Push each piston and connect-
ing rod slightly up into the bore without pushing the
piston beyond its upper limit. (5) Check the crankshaft end float by inserting a
feeler gauge between the shaft and the centre main
bearing, or by mounting a dial gauge with its plunger
against one end of the shaft. (6) Push the crankshaft into contact with the
front edge of the centre main bearing, then lever the
shaft forward to determine the end float.
(7) If the end float exceeds the Specifications,
renew the centre main bearing on assembly. (8) Check the main bearing clearance by the
Plastigage method as follows:
(a) Remove one bearing cap and with a piece of
rag wipe the journal and bearing clean.
(b) Position a piece of Plastigage, the approxi-
mate length of the bearing width and slightly off
centre, on the bearing surface of the crankshaft
journal. (c) Install the bearing ca p and tighten the cap
bolts to the specified torque.
NOTE: Do not rotate the crankshaft while
the Plastigage is in position.
(d) Remove the cap bolts and carefully detach
the cap and lower half bearing. (e) With the Plastigage scal e, measure the com-
pressed Plastigage strip to determine the clearance. (f) The widest point of the strip will indicate the
minimum clearance and th e narrowest point the
maximum clearance. (g) The remaining bearings can be checked in
turn using the same procedure.
(9) Lift the crankshaft from the crankcase using
care not to dislodge or damage the upper halves of the
main bearing shells if they are to be used again. (10) If new bearing shells are to be installed,
remove the upper halves of the bearings from the
crankcase.
TO CHECK AND INSPECT
After thoroughly cleaning the crankshaft in sol-
vent and drying it with co mpressed air, blow out all
the oilways and make the following checks:
(1) Check and measure the main bearing jour-
nals and crankpins for wear, taper and scoring. If wear
is excessive, the journals and/or crankpins should be
ground to accommodate the nearest underside bearing
shells.
One worn or damaged journal or crankpin will
necessitate the grinding of all the journals or crank-
View of the centre main bearing showing the side
faces which control crankshaft end float.
pins and the installation of new undersize bearing
shells.
If wear or damage is such that the journals or
crankpins cannot be reground to take any one range of
the available undersize bearings, the crankshaft will
have to be renewed.
(2) Support the crankshaft at each end in Vee
blocks and with a dial gauge, check the crankshaft for
bend at the centre main jour nal. Renew the crankshaft
if the bend is in excess of the allowable limit. Refer to
the Specifications.
(3) Check the centre main bearing side faces for
pitting or wear. If pitting or wear is evident, renew the
main bearing shells as a set which should restore the
crankshaft end float to the Specifications. (4) Even when the main bearing clearance has
been found to be satisfact ory, inspect the bearing
shells for scores, flaking and pitting. Renew the main
bearing shells as a set if necessary.
TO INSTAL
Installation is a reversal of the removal procedure
with attention to the following points:
(1) Ensure that all of the oilways are clear and
that all the journals and crankpins have been thor-
oughly cleaned. Ensure that the bearing shells have
been cleaned and smeared with new engine oil and that
they are correctly positioned in their respective web,
connecting rod or cap. (2) Carefully place the crankshaft in position in
the cylinder block and guide the connecting rods to
their respective crankpins.
(3) If new bearing shells were installed, check the
bearing clearance using the Plastigage method as
previously described. (4) Install the rear main bearing cap and inject
Permatex Ultra Grey or equivalent sealer into the grooves
in the side of the rear bearing cap. Fill the grooves.
Page 62 of 238
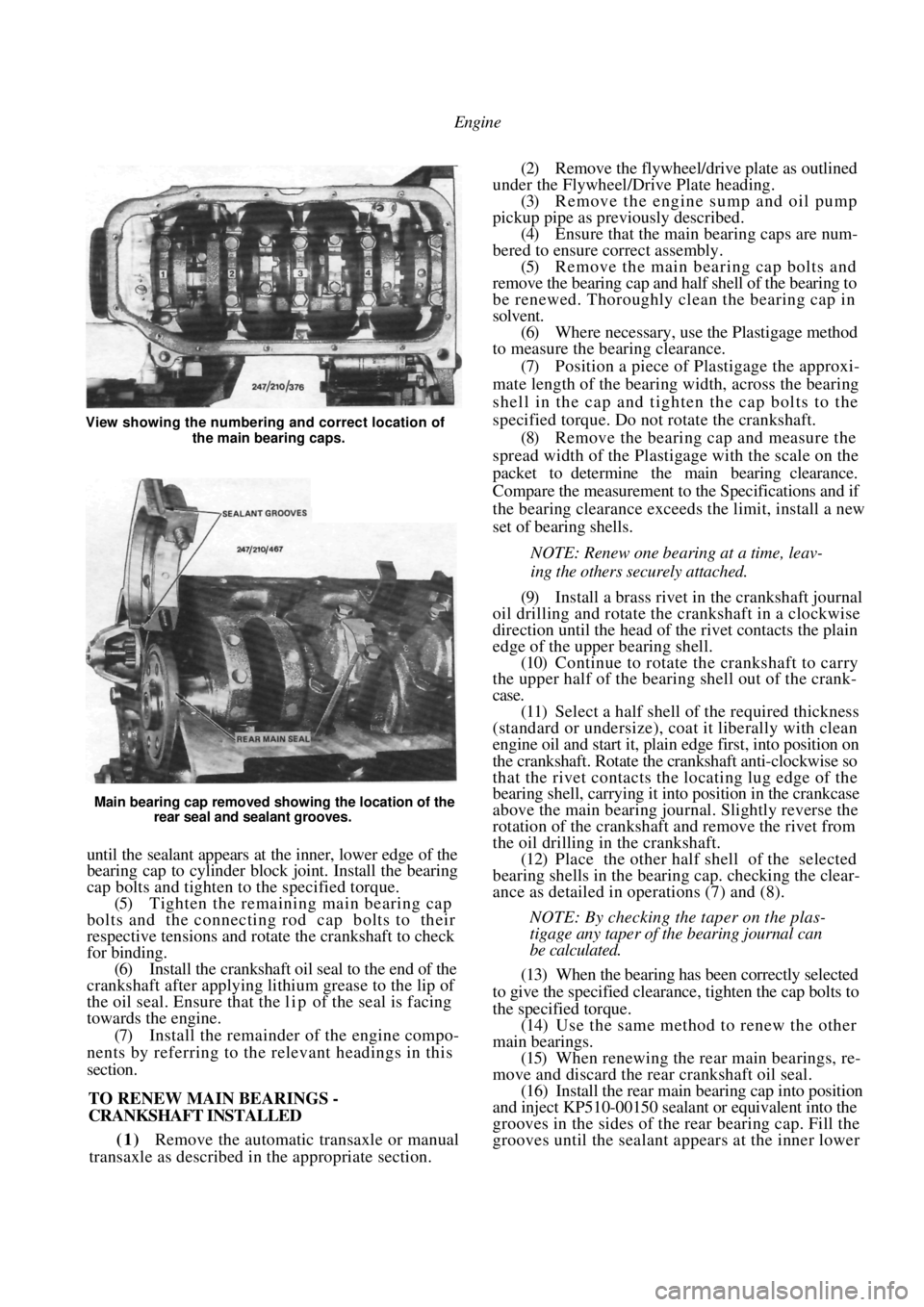
Engine
Main bearing cap removed showing the location of the rear seal and sealant grooves.
until the sealant appears at the inner, lower edge of the
bearing cap to cylinder block joint. Install the bearing
cap bolts and tighten to the specified torque.
(5) Tighten the remaining main bearing cap
bolts and the connecting rod cap bolts to their
respective tensions and rotate the crankshaft to check
for binding. (6) Install the crankshaft oil seal to the end of the
crankshaft after applying lithium grease to the lip of
the oil seal. Ensure that the l i p of the seal is facing
towards the engine.
(7) Install the remainder of the engine compo-
nents by referring to the relevant headings in this
section.
TO RENEW MAIN BEARINGS -
CRANKSHAFT INSTALLED
(1) Remove the automatic transaxle or manual
transaxle as described in the appropriate section.
(2) Remove the flywheel/drive plate as outlined
under the Flywheel/Drive Plate heading. (3) Remove the engine sump and oil pump
pickup pipe as previously described. (4) Ensure that the main bearing caps are num-
bered to ensure correct assembly. (5) Remove the main bearing cap bolts and
remove the bearing cap and half shell of the bearing to
be renewed. Thoroughly clean the bearing cap in
solvent. (6) Where necessary, use the Plastigage method
to measure the bearing clearance.
(7) Position a piece of Plastigage the approxi-
mate length of the bearing width, across the bearing
shell in the cap and tigh ten the cap bolts to the
specified torque. Do not rotate the crankshaft. (8) Remove the bearing cap and measure the
spread width of the Plastigage with the scale on the
packet to determine the main bearing clearance.
Compare the measurement to the Specifications and if
the bearing clearance exceeds the limit, install a new
set of bearing shells.
NOTE: Renew one bearing at a time, leav-
ing the others securely attached.
(9) Install a brass rivet in the crankshaft journal
oil drilling and rotate the crankshaft in a clockwise
direction until the head of the rivet contacts the plain
edge of the upper bearing shell. (10) Continue to rotate the crankshaft to carry
the upper half of the bearing shell out of the crank-
case.
(11) Select a half shell of the required thickness
(standard or undersize), coat it liberally with clean
engine oil and start it, plai n edge first, into position on
the crankshaft. Rotate the crankshaft anti-clockwise so
that the rivet contacts the locating lug edge of the
bearing shell, carrying it into position in the crankcase
above the main bearing journal. Slightly reverse the
rotation of the crankshaft and remove the rivet from
the oil drilling in the crankshaft. (12) Place the other half shell of the selected
bearing shells in the bear ing cap. checking the clear-
ance as detailed in operations (7) and (8).
NOTE: By checking the taper on the plas-
tigage any taper of the bearing journal can
be calculated.
(13) When the bearing has been correctly selected
to give the specified clearance, tighten the cap bolts to
the specified torque. (14) Use the same method to renew the other
main bearings. (15) When renewing the rear main bearings, re-
move and discard the rear crankshaft oil seal. (16) Install the rear main bearing cap into position
and inject KP510-00150 sealant or equivalent into the
grooves in the sides of the rear bearing cap. Fill the
grooves until the sealant a ppears at the inner lower
View showing the numbering and correct location of
the main bearing caps.
Page 72 of 238
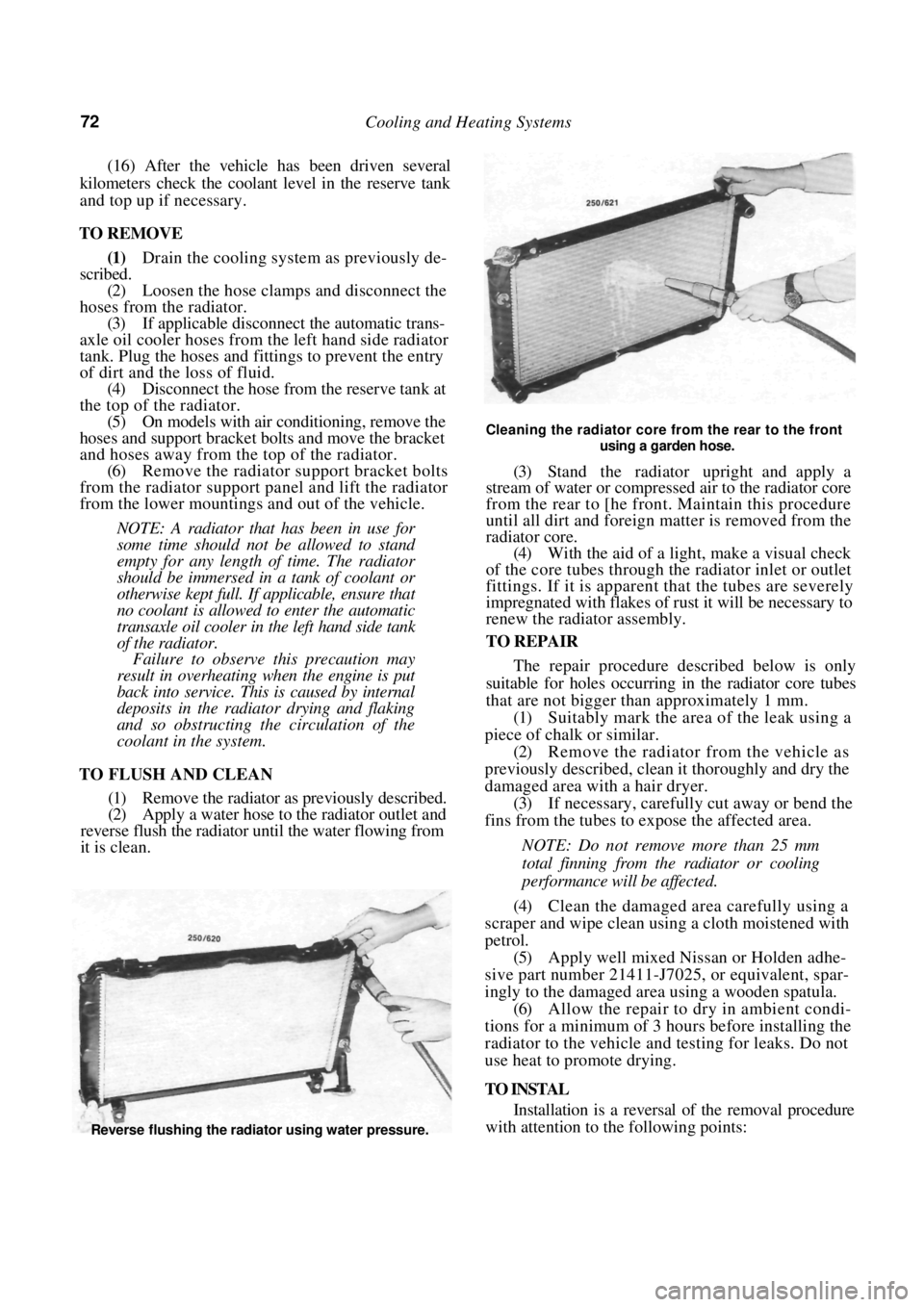
72 Cooling and Heating Systems
(16) After the vehicle has been driven several
kilometers check the coolant level in the reserve tank
and top up if necessary.
TO REMOVE
(1) Drain the cooling system as previously de-
scribed.
(2) Loosen the hose clamps and disconnect the
hoses from the radiator. (3) If applicable disconnect the automatic trans-
axle oil cooler hoses from the left hand side radiator
tank. Plug the hoses and fitt ings to prevent the entry
of dirt and the loss of fluid.
(4) Disconnect the hose from the reserve tank at
the top of the radiator. (5) On models with air conditioning, remove the
hoses and support bracket bolts and move the bracket
and hoses away from the top of the radiator. (6) Remove the radiator support bracket bolts
from the radiator support pa nel and lift the radiator
from the lower mountings and out of the vehicle.
NOTE: A radiator that has been in use for
some time should not be allowed to stand
empty for any length of time. The radiator
should be immersed in a tank of coolant or
otherwise kept full. If applicable, ensure that
no coolant is allowed to enter the automatic
transaxle oil cooler in the left hand side tank
of the radiator.
Failure to observe this precaution may
result in overheating when the engine is put
back into service. This is caused by internal
deposits in the radiator drying and flaking
and so obstructing the circulation of the
coolant in the system.
TO FLUSH AND CLEAN
(1) Remove the radiator as previously described.
(2) Apply a water hose to the radiator outlet and
reverse flush the radiator until the water flowing from
it is clean.
Cleaning the radiator core from the rear to the front
using a garden hose.
(3) Stand the radiator upright and apply a
stream of water or compressed air to the radiator core
from the rear to [he front. Maintain this procedure
until all dirt and foreign matter is removed from the
radiator core.
(4) With the aid of a light, make a visual check
of the core tubes through the radiator inlet or outlet
fittings. If it is apparent that the tubes are severely
impregnated with flakes of rust it will be necessary to
renew the radiator assembly.
TO REPAIR
The repair procedure described below is only
suitable for holes occurring in the radiator core tubes
that are not bigger than approximately 1 mm.
(1) Suitably mark the area of the leak using a
piece of chalk or similar. (2) Remove the radiator from the vehicle as
previously described, clean it thoroughly and dry the
damaged area with a hair dryer. (3) If necessary, carefully cut away or bend the
fins from the tubes to expose the affected area.
NOTE: Do not remove more than 25 mm
total finning from the radiator or cooling
performance will be affected.
(4) Clean the damaged area carefully using a
scraper and wipe clean using a cloth moistened with
petrol.
(5) Apply well mixed Nissan or Holden adhe-
sive part number 21411-J7025, or equivalent, spar-
ingly to the damaged area using a wooden spatula.
(6) Allow the repair to dry in ambient condi-
tions for a minimum of 3 hours before installing the
radiator to the vehicle and testing for leaks. Do not
use heat to promote drying.
TO INSTAL
Installation is a reversal of the removal procedure
with attention to the following points:
Reverse flushing the radiator using water pressure.
Page 77 of 238
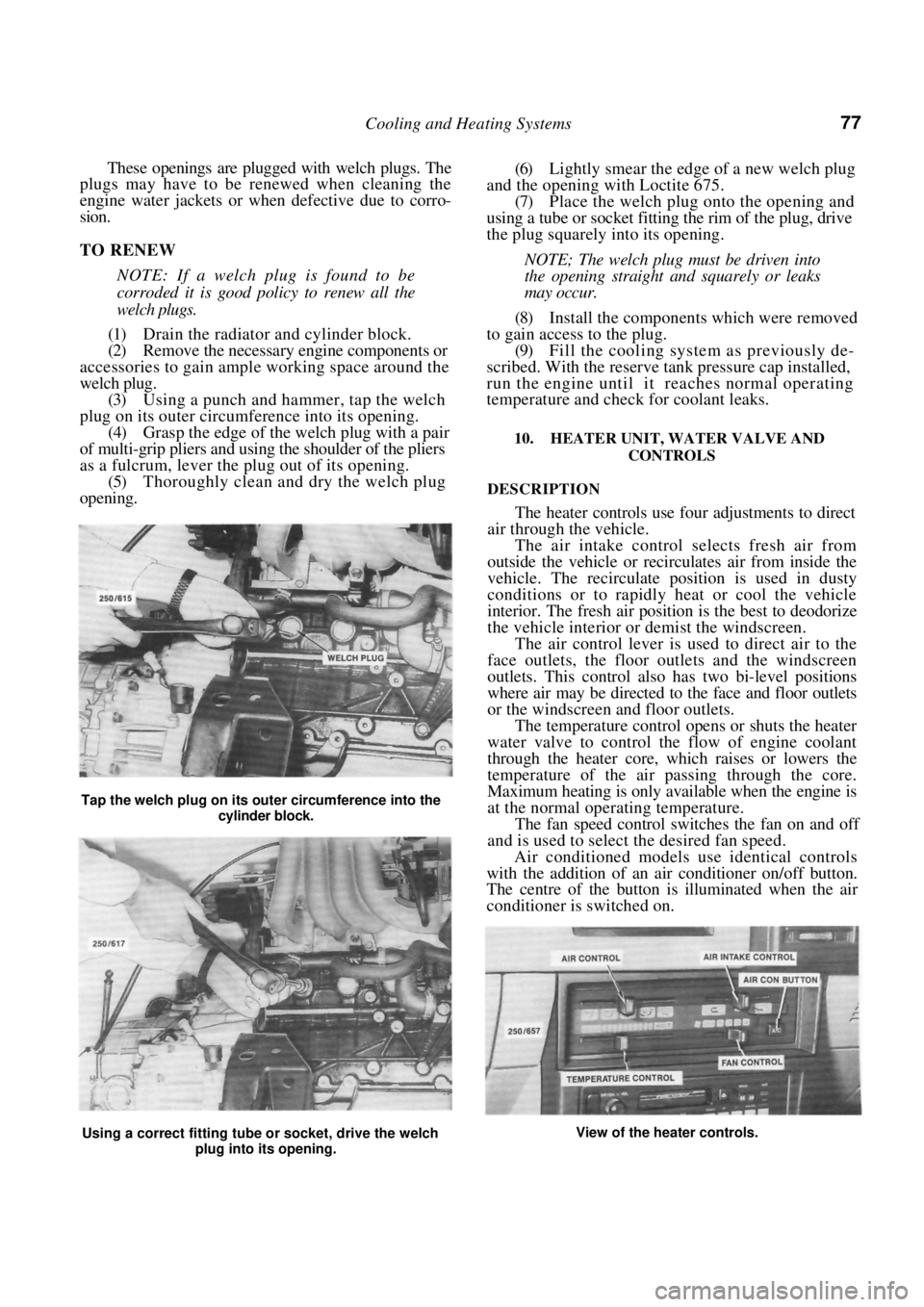
Cooling and Heating Systems 77
These openings are plugged with welch plugs. The
plugs may have to be renewed when cleaning the
engine water jackets or when defective due to corro-
sion.
TO RENEW
NOTE: If a welch plug is found to be
corroded it is good policy to renew all the
welch plugs.
(1) Drain the radiator and cylinder block.
(2) Remove the necessary engine components or
accessories to gain ampl e working space around the
welch plug. (3) Using a punch and hammer, tap the welch
plug on its outer circumference into its opening. (4) Grasp the edge of the welch plug with a pair
of multi-grip pliers and using the shoulder of the pliers
as a fulcrum, lever the plug out of its opening. (5) Thoroughly clean and dry the welch plug
opening.
(6) Lightly smear the edge of a new welch plug
and the opening with Loctite 675. (7) Place the welch plug onto the opening and
using a tube or socket fitting the rim of the plug, drive
the plug squarely into its opening.
NOTE; The welch plug must be driven into
the opening straight and squarely or leaks
may occur.
(8) Install the components which were removed
to gain access to the plug. (9) Fill the cooling system as previously de-
scribed. With the reserve tank pressure cap installed,
run the engine until it reaches normal operating
temperature and check for coolant leaks.
10. HEATER UNIT, WATER VALVE AND
CONTROLS
DESCRIPTION
The heater controls use four adjustments to direct
air through the vehicle.
The air intake control selects fresh air from
outside the vehicle or recirculates air from inside the
vehicle. The recirculate position is used in dusty
conditions or to rapidly heat or cool the vehicle
interior. The fresh air positi on is the best to deodorize
the vehicle interior or demist the windscreen.
The air control lever is used to direct air to the
face outlets, the floor outle ts and the windscreen
outlets. This control also has two bi-level positions
where air may be directed to the face and floor outlets
or the windscreen and floor outlets.
The temperature control opens or shuts the heater
water valve to control the flow of engine coolant
through the heater core, which raises or lowers the
temperature of the air passing through the core.
Maximum heating is only available when the engine is
at the normal operating temperature.
The fan speed control switches the fan on and off
and is used to select the desired fan speed.
Air conditioned models use identical controls
with the addition of an air conditioner on/off button.
The centre of the button is illuminated when the air
conditioner is switched on.
Tap the welch plug on its ou ter circumference into the
cylinder block.
Using a correct fitting tube or socket, drive the welch
plug into its opening. View of the heater controls.
Page 79 of 238
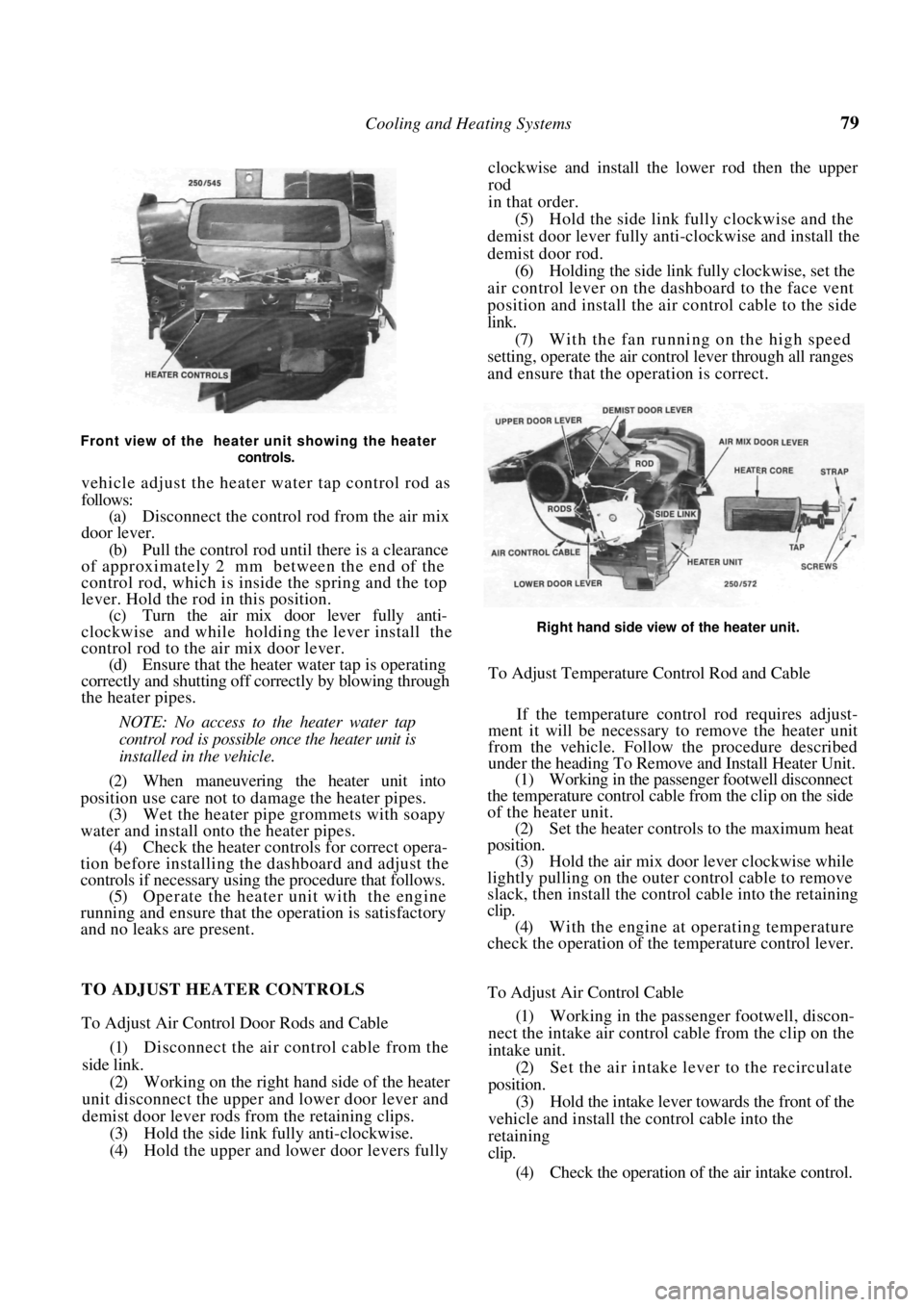
Cooling and Heating Systems 79
Front view of the heater unit showing the heater controls.
vehicle adjust the heater water tap control rod as
follows:
(a) Disconnect the control rod from the air mix
door lever.
(b) Pull the control rod un til there is a clearance
of approximately 2 mm between the end of the
control rod, which is inside the spring and the top
lever. Hold the rod in this position.
(c) Turn the air mix door lever fully anti-
clockwise and while holding the lever install the
control rod to the air mix door lever. (d) Ensure that the heater water tap is operating
correctly and shutting off correctly by blowing through
the heater pipes.
NOTE: No access to the heater water tap
control rod is possible once the heater unit is
installed in the vehicle.
(2) When maneuvering the heater unit into
position use care not to damage the heater pipes. (3) Wet the heater pipe grommets with soapy
water and install onto the heater pipes. (4) Check the heater controls for correct opera-
tion before installing the dashboard and adjust the
controls if necessary using the procedure that follows. (5) Operate the heater unit with the engine
running and ensure that the operation is satisfactory
and no leaks are present. clockwise and install the lower rod then the upper
rod
in that order.
(5)
Hold the side link fully clockwise and the
demist door lever fully anti-clockwise and install the
demist door rod. (6) Holding the side link fully clockwise, set the
air control lever on the dashboard to the face vent
position and install the air control cable to the side
link. (7) With the fan running on the high speed
setting, operate the air cont rol lever through all ranges
and ensure that the operation is correct.
Right hand side view of the heater unit.
To Adjust Temperature Control Rod and Cable
If the temperature control rod requires adjust-
ment it will be necessary to remove the heater unit
from the vehicle. Follow the procedure described
under the heading To Remove and Install Heater Unit.
(1) Working in the passenger footwell disconnect
the temperature control cable from the clip on the side
of the heater unit. (2) Set the heater controls to the maximum heat
position. (3) Hold the air mix door lever clockwise while
lightly pulling on the outer control cable to remove
slack, then install the control cable into the retaining
clip.
(4) With the engine at operating temperature
check the operation of the temperature control lever.
TO ADJUST HEATER CONTROLS
To Adjust Air Control Door Rods and Cable
(1) Disconnect the air control cable from the
side link. (2) Working on the right hand side of the heater
unit disconnect the upper and lower door lever and
demist door lever rods from the retaining clips.
(3) Hold the side link fully anti-clockwise.
(4) Hold the upper and lower door levers fully To Adjust Air Control Cable
(1)
Working in the passeng er footwell, discon-
nect the intake air control cable from the clip on the
intake unit. (2) Set the air intake lever to the recirculate
position. (3) Hold the intake lever to wards the front of the
vehicle and install the control cable into the
retaining
clip.
(4) Check the operation of the air intake control.
Page 89 of 238
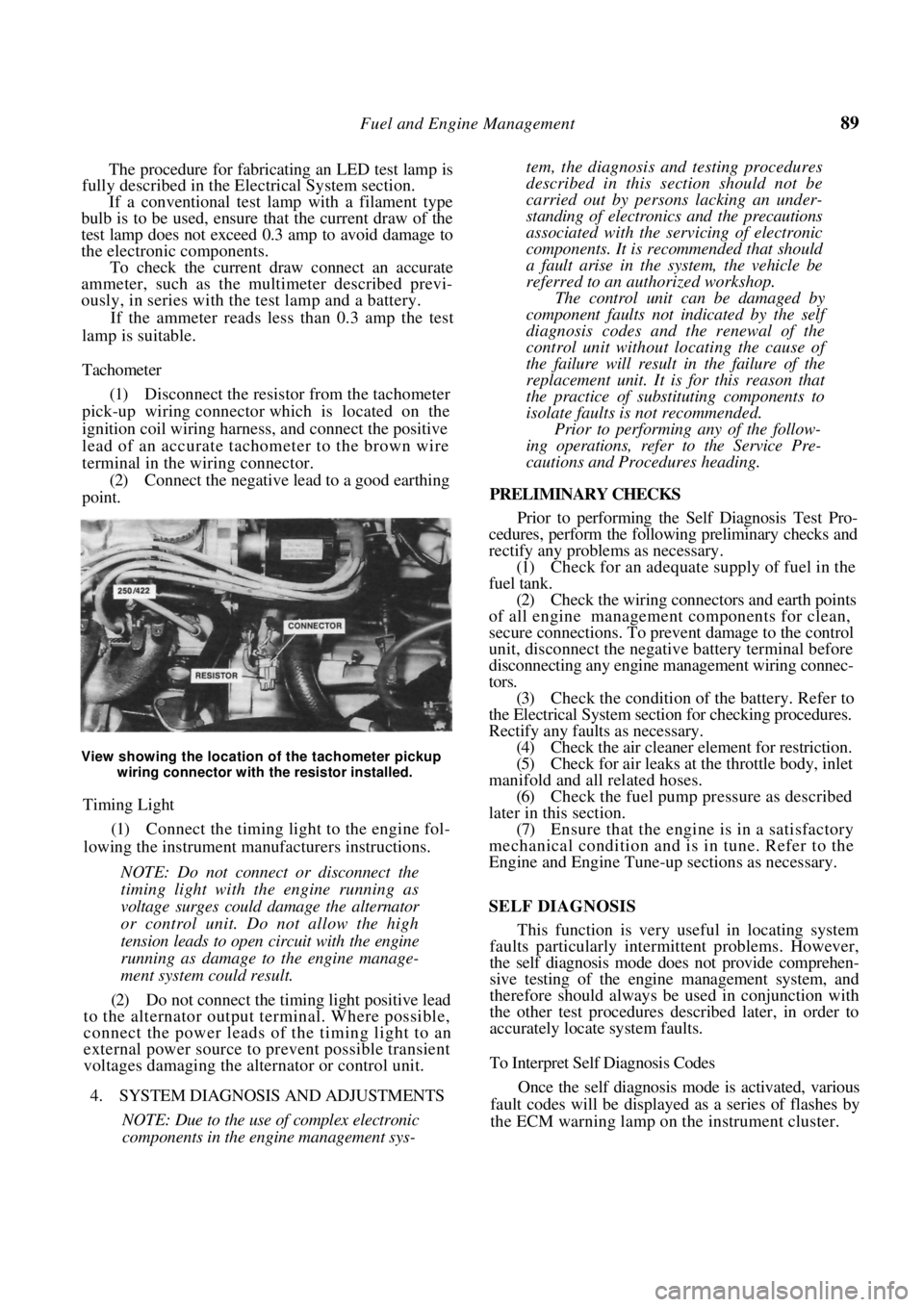
Fuel and Engine Management 89
The procedure for fabricating an LED test lamp is
fully described in the El ectrical System section.
If a conventional test lamp with a filament type
bulb is to be used, ensure that the current draw of the
test lamp does not exceed 0.3 amp to avoid damage to
the electronic components.
To check the current draw connect an accurate
ammeter, such as the multimeter described previ-
ously, in series with the test lamp and a battery.
If the ammeter reads less than 0.3 amp the test
lamp is suitable.
Tachometer
(1) Disconnect the resistor from the tachometer
pick-up wiring connector which is located on the
ignition coil wiring harness, and connect the positive
lead of an accurate tachometer to the brown wire
terminal in the wiring connector. (2) Connect the negative lead to a good earthing
point.
View showing the location of the tachometer pickup
wiring connector with the resistor installed.
Timing Light
(1) Connect the timing light to the engine fol-
lowing the instrument manufacturers instructions.
NOTE: Do not connect or disconnect the
timing light with the engine running as
voltage surges could damage the alternator
or control unit. Do not allow the high
tension leads to open circuit with the engine
running as damage to the engine manage-
ment system could result.
(2) Do not connect the timing light positive lead
to the alternator output terminal. Where possible,
connect the power leads of the timing light to an
external power source to prevent possible transient
voltages damaging the alternator or control unit.
4. SYSTEM DIAGNOSIS AND ADJUSTMENTS
NOTE: Due to the use of complex electronic
components in the engine management sys-
tem, the diagnosis and testing procedures
described in this section should not be
carried out by persons lacking an under-
standing of electronics and the precautions
associated with the servicing of electronic
components. It is rec ommended that should
a fault arise in the system, the vehicle be
referred to an authorized workshop.
The control unit can be damaged by
component faults not indicated by the self
diagnosis codes and the renewal of the
control unit without lo cating the cause of
the failure will result in the failure of the
replacement unit. It is for this reason that
the practice of substituting components to
isolate faults is not recommended.
Prior to performing any of the follow-
ing operations, refer to the Service Pre-
cautions and Procedures heading.
PRELIMINARY CHECKS
Prior to performing the Self Diagnosis Test Pro-
cedures, perform the following preliminary checks and
rectify any problems as necessary.
(1) Check for an adequate supply of fuel in the
fuel tank. (2) Check the wiring connectors and earth points
of all engine management components for clean,
secure connections. To prevent damage to the control
unit, disconnect the negative battery terminal before
disconnecting any engine ma nagement wiring connec-
tors. (3) Check the condition of the battery. Refer to
the Electrical System sectio n for checking procedures.
Rectify any faults as necessary. (4) Check the air cleaner element for restriction.
(5) Check for air leaks at the throttle body, inlet
manifold and all related hoses. (6) Check the fuel pump pr essure as described
later in this section. (7) Ensure that the engine is in a satisfactory
mechanical condition and is in tune. Refer to the
Engine and Engine Tune-up sections as necessary.
SELF DIAGNOSIS
This function is very useful in locating system
faults particularly intermittent problems. However,
the self diagnosis mode does not provide comprehen-
sive testing of the engine management system, and
therefore should always be used in conjunction with
the other test procedures described later, in order to
accurately locate system faults.
To Interpret Self Diagnosis Codes
Once the self diagnosis mode is activated, various
fault codes will be displayed as a series of flashes by
the ECM warning lamp on the instrument cluster.
Page 91 of 238
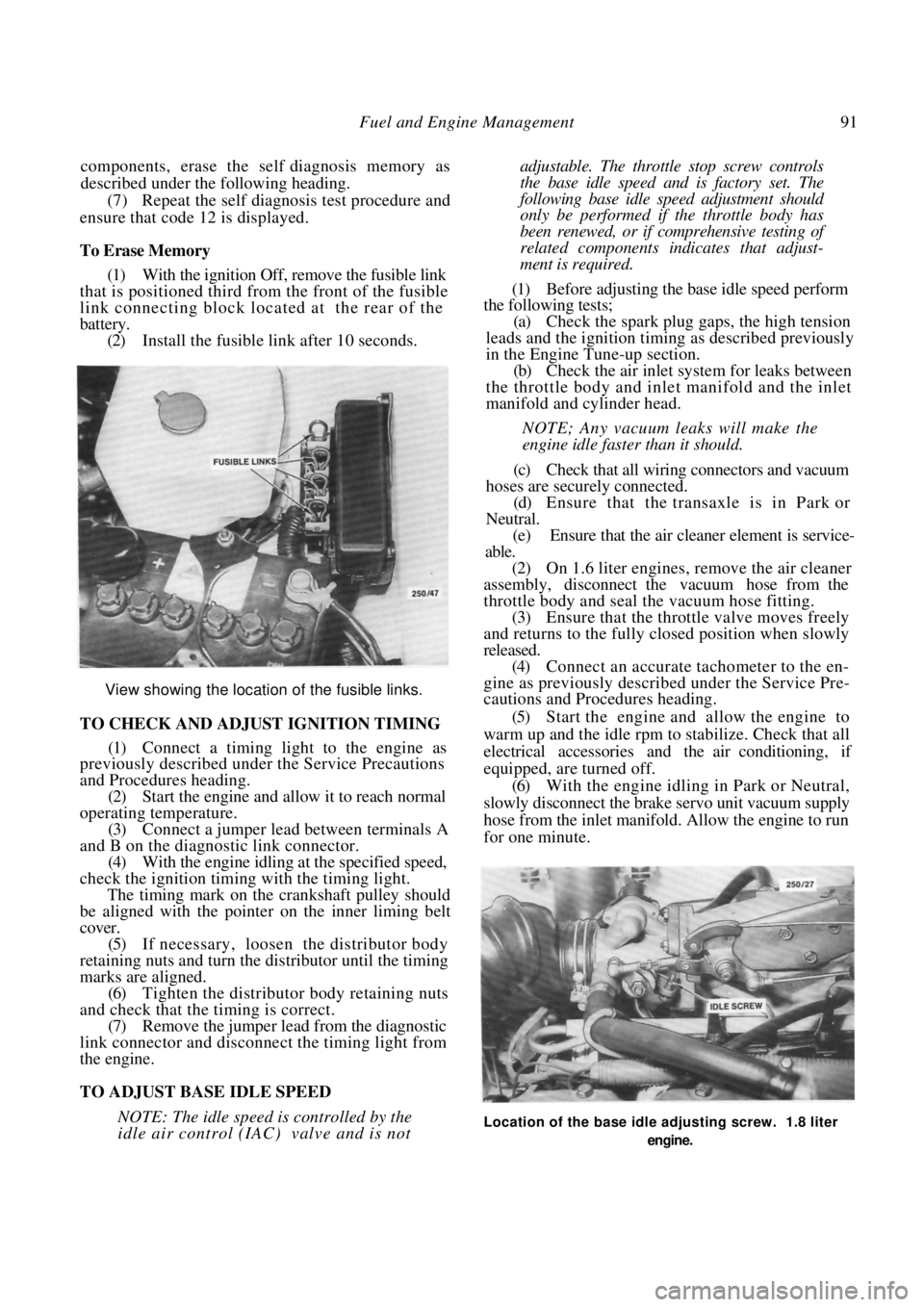
Fuel and Engine Management 91
components, erase the self diagnosis memory as
described under the following heading.
(7) Repeat the self diagnosis test procedure and
ensure that code 12 is displayed.
To Erase Memory
(1) With the ignition Off, remove the fusible link
that is positioned third from the front of the fusible
link connecting block located at the rear of the
battery. (2) Install the fusible link after 10 seconds.
View showing the location of the fusible links.
TO CHECK AND ADJUST IGNITION TIMING
(1) Connect a timing light to the engine as
previously described under the Service Precautions
and Procedures heading.
(2) Start the engine and allow it to reach normal
operating temperature. (3) Connect a jumper lead between terminals A
and B on the diagnostic link connector. (4) With the engine idling at the specified speed,
check the ignition timing with the timing light.
The timing mark on the crankshaft pulley should
be aligned with the pointer on the inner liming belt
cover.
(5) If necessary, loosen the distributor body
retaining nuts and turn the distributor until the timing
marks are aligned. (6) Tighten the distributor body retaining nuts
and check that the timing is correct. (7) Remove the jumper lead from the diagnostic
link connector and disconnect the timing light from
the engine.
TO ADJUST BASE IDLE SPEED
NOTE: The idle speed is controlled by the
idle air control (IAC) valve and is not
adjustable. The throttle stop screw controls
the base idle speed a nd is factory set. The
following base idle speed adjustment should
only be performed if the throttle body has
been renewed, or if comprehensive testing of
related components indicates that adjust-
ment is required.
(1) Before adjusting the base idle speed perform
the following tests;
(a) Check the spark plug gaps, the high tension
leads and the ignition timin g as described previously
in the Engine Tune-up section.
(b) Check the air inlet syst em for leaks between
the throttle body and inlet manifold and the inlet
manifold and cylinder head.
NOTE; Any vacuum leaks will make the
engine idle faster than it should.
(c) Check that all wiring connectors and vacuum
hoses are securely connected. (d) Ensure that the transaxle is in Park or
Neutral. (e) Ensure that the air cleaner element is service-
able.
(2) On 1.6 liter engines, remove the air cleaner
assembly, disconnect the vacuum hose from the
throttle body and seal the vacuum hose fitting.
(3) Ensure that the throttle valve moves freely
and returns to the fully closed position when slowly
released. (4) Connect an accurate tachometer to the en-
gine as previously descri bed under the Service Pre-
cautions and Procedures heading.
(5) Start the engine and allow the engine to
warm up and the idle rpm to stabilize. Check that all
electrical accessories and the air conditioning, if
equipped, are turned off. (6) With the engine idling in Park or Neutral,
slowly disconnect the brake servo unit vacuum supply
hose from the inlet manifold. Allow the engine to run
for one minute.
Location of the base idle adjusting screw. 1.8 liter
engine.
Page 95 of 238
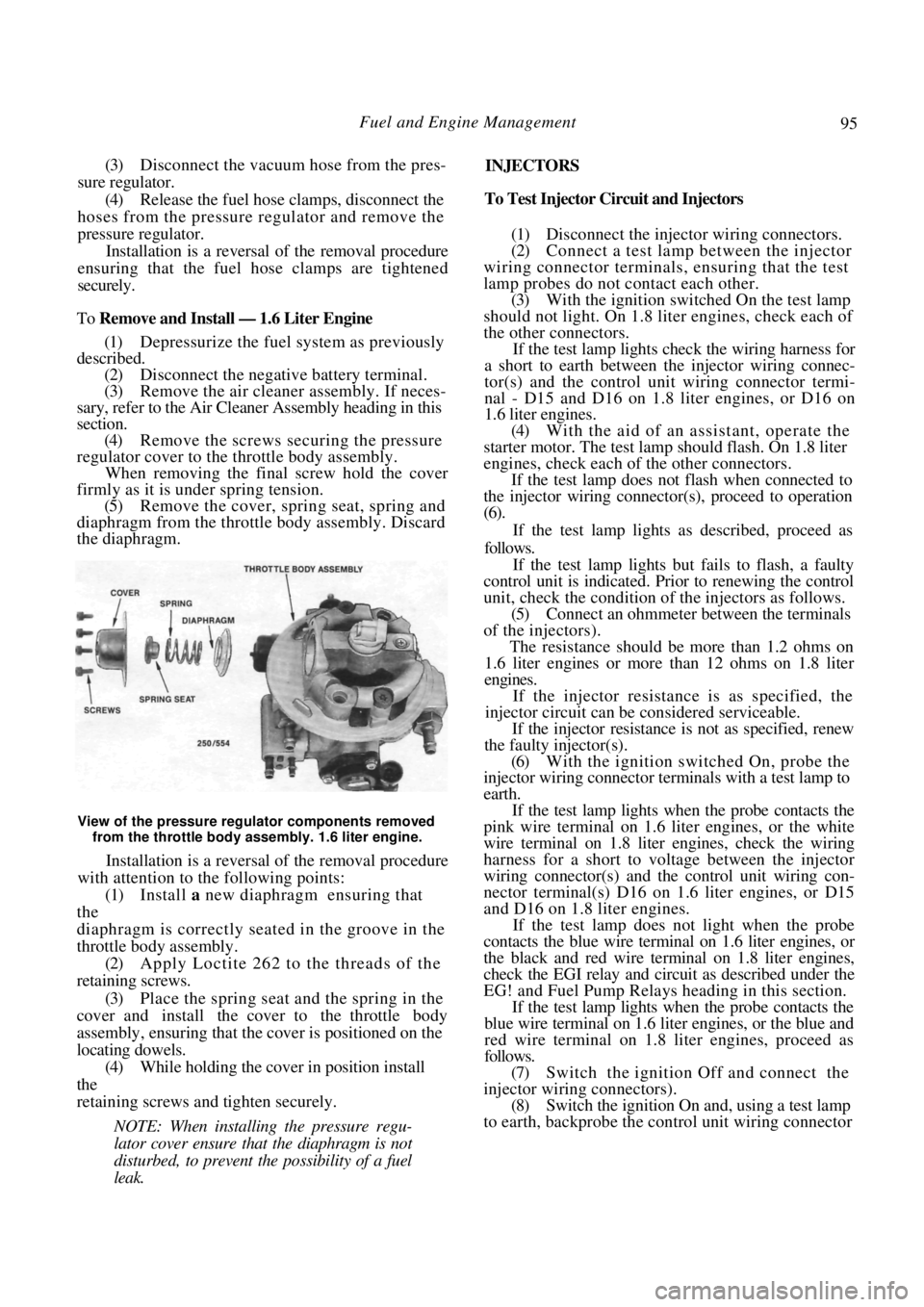
Fuel and Engine Management 95
(3) Disconnect the vacuum hose from the pres-
sure regulator.
(4) Release the fuel hose clamps, disconnect the
hoses from the pressure regulator and remove the
pressure regulator. Installation is a reversal of the removal procedure
ensuring that the fuel hose clamps are tightened
securely.
To Remove and Install — 1.6 Liter Engine
(1) Depressurize the fuel system as previously
described. (2) Disconnect the negative battery terminal.
(3) Remove the air cleaner assembly. If neces-
sary, refer to the Air Cleane r Assembly heading in this
section. (4) Remove the screws securing the pressure
regulator cover to the throttle body assembly. When removing the final screw hold the cover
firmly as it is under spring tension.
(5) Remove the cover, spring seat, spring and
diaphragm from the thrott le body assembly. Discard
the diaphragm.
View of the pressure regulator components removed
from the throttle body assembly. 1.6 liter engine.
Installation is a reversal of the removal procedure
with attention to the following points:
(1) Install a new diaphragm ensuring that
the
diaphragm is correctly seat ed in the groove in the
throttle body assembly. (2) Apply Loctite 262 to the threads of the
retaining screws.
(3) Place the spring seat and the spring in the
cover and install the cover to the throttle body
assembly, ensuring that the cover is positioned on the
locating dowels. (4) While holding the cover in position install
the
retaining screws and tighten securely.
NOTE: When installing the pressure regu-
lator cover ensure that the diaphragm is not
disturbed, to prevent the possibility of a fuel
leak.
INJECTORS
To Test Injector Circuit and Injectors
(1) Disconnect the injector wiring connectors.
(2) Connect a test lamp between the injector
wiring connector terminals, ensuring that the test
lamp probes do not contact each other. (3) With the ignition switched On the test lamp
should not light. On 1.8 liter engines, check each of
the other connectors.
If the test lamp lights check the wiring harness for
a short to earth between the injector wiring connec-
tor(s) and the control unit wiring connector termi-
nal - D15 and D16 on 1.8 liter engines, or D16 on
1.6 liter engines.
(4) With the aid of an assistant, operate the
starter motor. The test lamp should flash. On 1.8 liter
engines, check each of the other connectors.
If the test lamp does not flash when connected to
the injector wiring connecto r(s), proceed to operation
(6).
If the test lamp lights as described, proceed as
follows.
If the test lamp lights but fails to flash, a faulty
control unit is indicated. Pr ior to renewing the control
unit, check the condition of the injectors as follows.
(5) Connect an ohmmeter between the terminals
of the injectors).
The resistance should be more than 1.2 ohms on
1.6 liter engines or more than 12 ohms on 1.8 liter
engines.
If the injector resistance is as specified, the
injector circuit can be considered serviceable.
If the injector resistance is not as specified, renew
the faulty injector(s).
(6) With the ignition switched On, probe the
injector wiring connector terminals with a test lamp to
earth.
If the test lamp lights when the probe contacts the
pink wire terminal on 1.6 liter engines, or the white
wire terminal on 1.8 liter engines, check the wiring
harness for a short to volt age between the injector
wiring connector(s) and the control unit wiring con-
nector terminal(s) D16 on 1.6 liter engines, or D15
and D16 on 1.8 liter engines.
If the test lamp does not light when the probe
contacts the blue wire termin al on 1.6 liter engines, or
the black and red wire term inal on 1.8 liter engines,
check the EGI relay and circ uit as described under the
EG! and Fuel Pump Relays heading in this section.
If the test lamp lights when the probe contacts the
blue wire terminal on 1.6 lite r engines, or the blue and
red wire terminal on 1.8 liter engines, proceed as
follows.
(7) Switch the ignition Off and connect the
injector wiring connectors). (8) Switch the ignition On and, using a test lamp
to earth, backprobe the cont rol unit wiring connector
Page 96 of 238
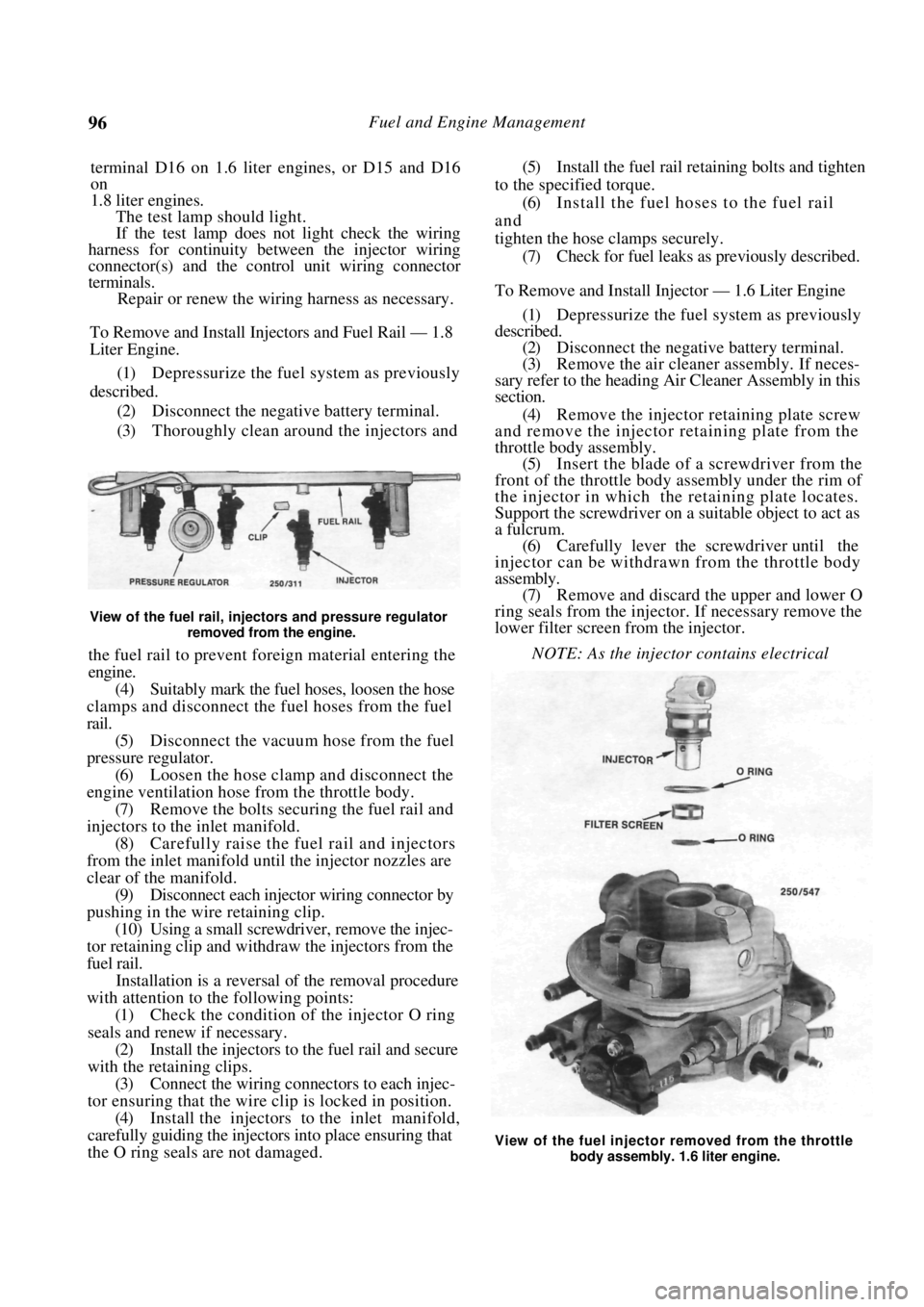
96 Fuel and Engine Management
terminal D16 on 1.6 liter engines, or D15 and D16
on
1.8 liter engines.
The test lamp should light.
If the test lamp does not light check the wiring
harness for continuity between the injector wiring
connector(s) and the control unit wiring connector
terminals.
Repair or renew the wiring harness as necessary.
To Remove and Install Injectors and Fuel Rail — 1.8
Liter Engine.
(1) Depressurize the fuel system as previously
described.
(2) Disconnect the negative battery terminal.
(3) Thoroughly clean around the injectors and
View of the fuel rail, injectors and pressure regulator
removed from the engine.
the fuel rail to prevent foreign material entering the
engine.
(4) Suitably mark the fuel hoses, loosen the hose
clamps and disconnect the fuel hoses from the fuel
rail. (5) Disconnect the vacuum hose from the fuel
pressure regulator. (6) Loosen the hose clamp and disconnect the
engine ventilation hose from the throttle body. (7) Remove the bolts securing the fuel rail and
injectors to the inlet manifold. (8) Carefully raise the fuel rail and injectors
from the inlet manifold until the injector nozzles are
clear of the manifold. (9) Disconnect each injector wiring connector by
pushing in the wire retaining clip.
(10) Using a small screwdriver, remove the injec-
tor retaining clip and withdraw the injectors from the
fuel rail.
Installation is a reversal of the removal procedure
with attention to the following points:
(1) Check the condition of the injector O ring
seals and renew if necessary. (2) Install the injectors to the fuel rail and secure
with the retaining clips. (3) Connect the wiring connectors to each injec-
tor ensuring that the wire clip is locked in position. (4) Install the injectors to the inlet manifold,
carefully guiding the injectors into place ensuring that
the O ring seals are not damaged.
(5) Install the fuel rail retaining bolts and tighten
to the specified torque. (6) Install the fuel hoses to the fuel rail
and
tighten the hose clamps securely.
(7) Check for fuel leaks as previously described.
To Remove and Install Injector — 1.6 Liter Engine
(1) Depressurize the fuel system as previously
described. (2) Disconnect the negative battery terminal.
(3) Remove the air cleaner assembly. If neces-
sary refer to the heading Air Cleaner Assembly in this
section.
(4) Remove the injector retaining plate screw
and remove the injector retaining plate from the
throttle body assembly. (5) Insert the blade of a screwdriver from the
front of the throttle body assembly under the rim of
the injector in which the retaining plate locates.
Support the screwdriver on a suitable object to act as
a fulcrum. (6) Carefully lever the screwdriver until the
injector can be withdrawn from the throttle body
assembly.
(7) Remove and discard the upper and lower O
ring seals from the injector . If necessary remove the
lower filter screen from the injector.
NOTE: As the injector contains electrical
View of the fuel injector removed from the throttle body assembly. 1.6 liter engine.