NISSAN TIIDA 2008 Service Repair Manual
Manufacturer: NISSAN, Model Year: 2008, Model line: TIIDA, Model: NISSAN TIIDA 2008Pages: 2771, PDF Size: 60.61 MB
Page 1721 of 2771
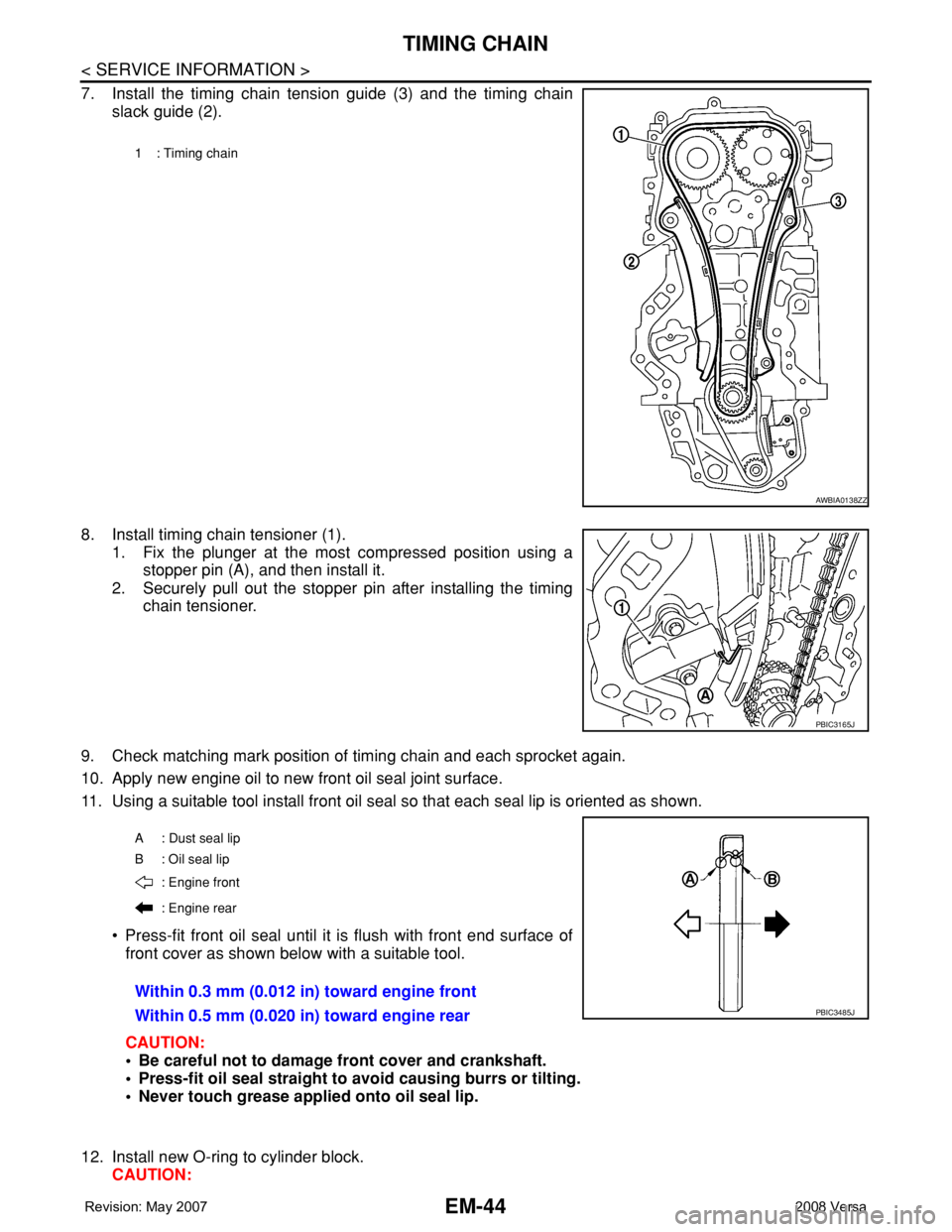
EM-44
< SERVICE INFORMATION >
TIMING CHAIN
7. Install the timing chain tension guide (3) and the timing chain
slack guide (2).
8. Install timing chain tensioner (1).
1. Fix the plunger at the most compressed position using a
stopper pin (A), and then install it.
2. Securely pull out the stopper pin after installing the timing
chain tensioner.
9. Check matching mark position of timing chain and each sprocket again.
10. Apply new engine oil to new front oil seal joint surface.
11. Using a suitable tool install front oil seal so that each seal lip is oriented as shown.
• Press-fit front oil seal until it is flush with front end surface of
front cover as shown below with a suitable tool.
CAUTION:
• Be careful not to damage front cover and crankshaft.
• Press-fit oil seal straight to avoid causing burrs or tilting.
• Never touch grease applied onto oil seal lip.
12. Install new O-ring to cylinder block.
CAUTION:
1 : Timing chain
AWBIA0138ZZ
PBIC3165J
A : Dust seal lip
B: Oil seal lip
: Engine front
: Engine rear
Within 0.3 mm (0.012 in) toward engine front
Within 0.5 mm (0.020 in) toward engine rear
PBIC3485J
Page 1722 of 2771
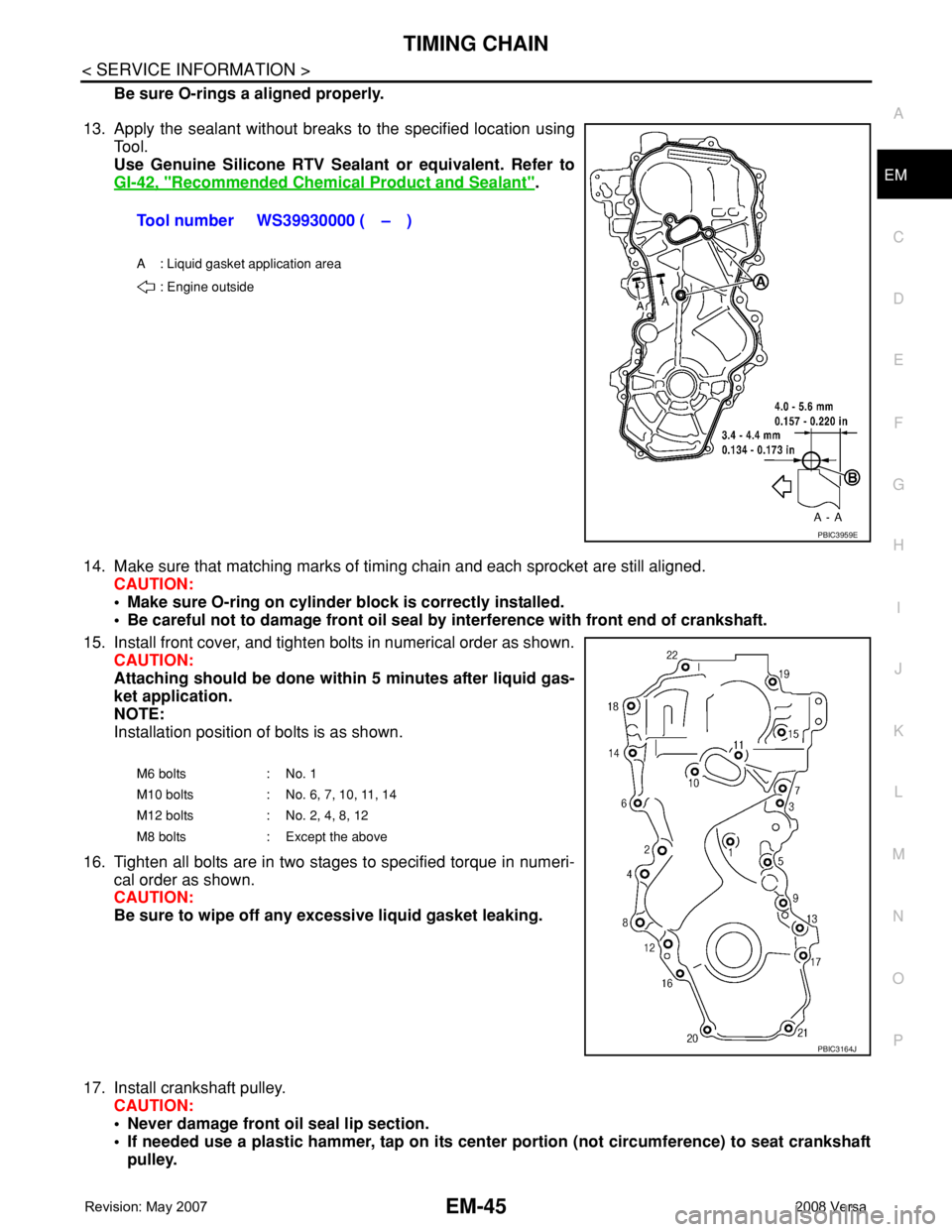
TIMING CHAIN
EM-45
< SERVICE INFORMATION >
C
D
E
F
G
H
I
J
K
L
MA
EM
N
P O
Be sure O-rings a aligned properly.
13. Apply the sealant without breaks to the specified location using
Tool.
Use Genuine Silicone RTV Sealant or equivalent. Refer to
GI-42, "
Recommended Chemical Product and Sealant".
14. Make sure that matching marks of timing chain and each sprocket are still aligned.
CAUTION:
• Make sure O-ring on cylinder block is correctly installed.
• Be careful not to damage front oil seal by interference with front end of crankshaft.
15. Install front cover, and tighten bolts in numerical order as shown.
CAUTION:
Attaching should be done within 5 minutes after liquid gas-
ket application.
NOTE:
Installation position of bolts is as shown.
16. Tighten all bolts are in two stages to specified torque in numeri-
cal order as shown.
CAUTION:
Be sure to wipe off any excessive liquid gasket leaking.
17. Install crankshaft pulley.
CAUTION:
• Never damage front oil seal lip section.
• If needed use a plastic hammer, tap on its center portion (not circumference) to seat crankshaft
pulley.Tool number WS39930000 ( – )
A : Liquid gasket application area
: Engine outside
PBIC3959E
M6 bolts : No. 1
M10 bolts : No. 6, 7, 10, 11, 14
M12 bolts : No. 2, 4, 8, 12
M8 bolts : Except the above
PBIC3164J
Page 1723 of 2771
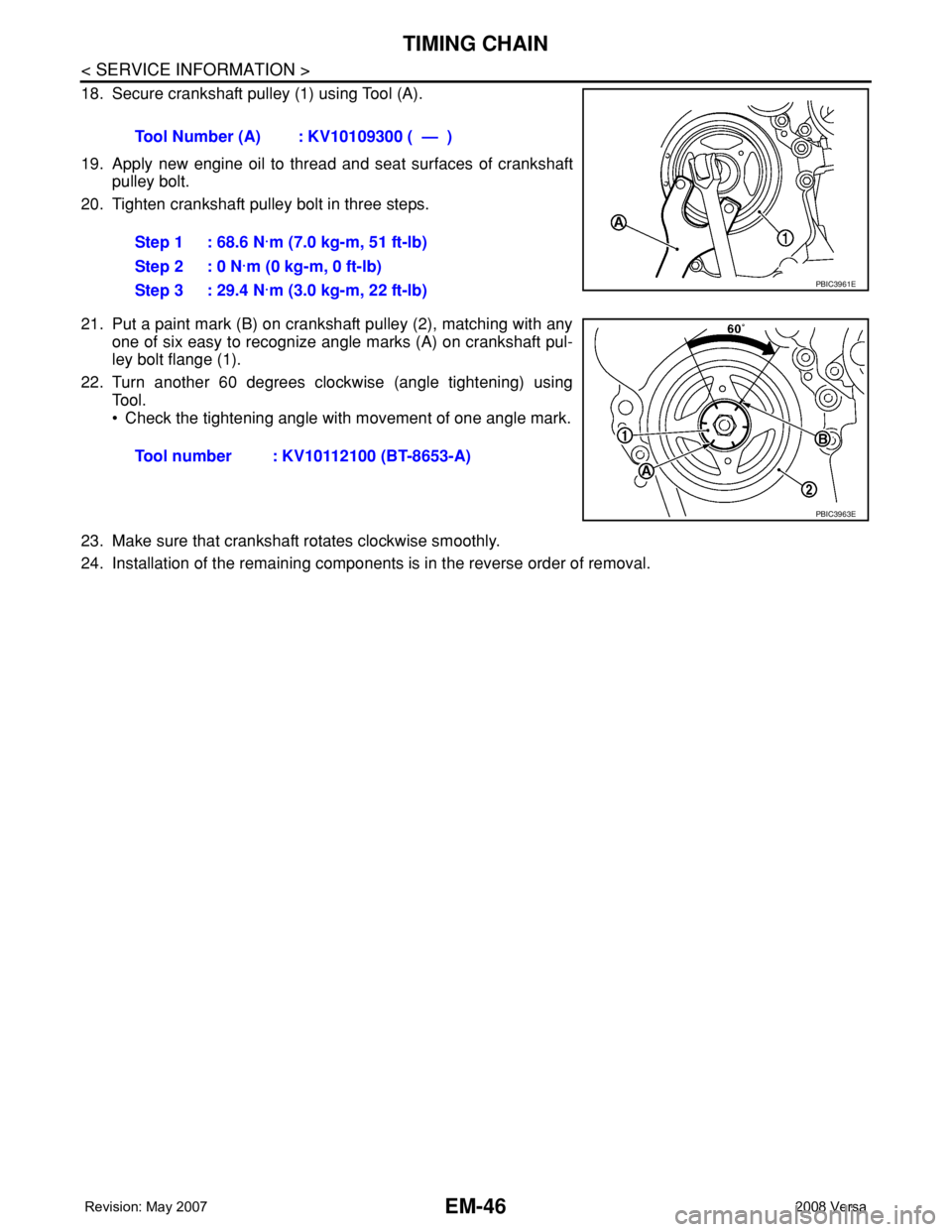
EM-46
< SERVICE INFORMATION >
TIMING CHAIN
18. Secure crankshaft pulley (1) using Tool (A).
19. Apply new engine oil to thread and seat surfaces of crankshaft
pulley bolt.
20. Tighten crankshaft pulley bolt in three steps.
21. Put a paint mark (B) on crankshaft pulley (2), matching with any
one of six easy to recognize angle marks (A) on crankshaft pul-
ley bolt flange (1).
22. Turn another 60 degrees clockwise (angle tightening) using
Tool.
• Check the tightening angle with movement of one angle mark.
23. Make sure that crankshaft rotates clockwise smoothly.
24. Installation of the remaining components is in the reverse order of removal.Tool Number (A) : KV10109300 ( — )
Step 1 : 68.6 N·m (7.0 kg-m, 51 ft-lb)
Step 2 : 0 N·m (0 kg-m, 0 ft-lb)
Step 3 : 29.4 N·m (3.0 kg-m, 22 ft-lb)
PBIC3961E
Tool number : KV10112100 (BT-8653-A)
PBIC3963E
Page 1724 of 2771
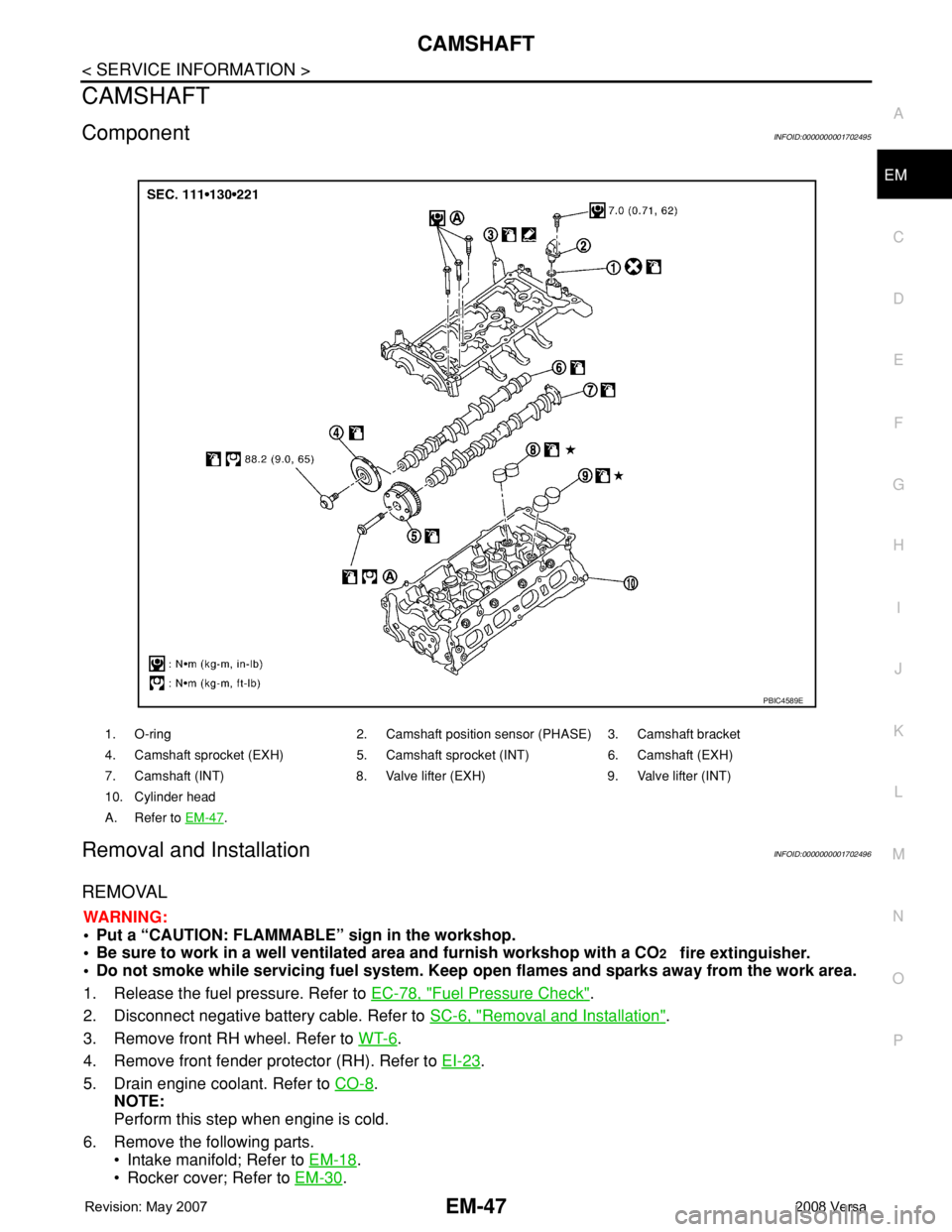
CAMSHAFT
EM-47
< SERVICE INFORMATION >
C
D
E
F
G
H
I
J
K
L
MA
EM
N
P O
CAMSHAFT
ComponentINFOID:0000000001702495
Removal and InstallationINFOID:0000000001702496
REMOVAL
WARNING:
• Put a “CAUTION: FLAMMABLE” sign in the workshop.
• Be sure to work in a well ventilated area and furnish workshop with a CO
2 fire extinguisher.
• Do not smoke while servicing fuel system. Keep open flames and sparks away from the work area.
1. Release the fuel pressure. Refer to EC-78, "
Fuel Pressure Check".
2. Disconnect negative battery cable. Refer to SC-6, "
Removal and Installation".
3. Remove front RH wheel. Refer to WT-6
.
4. Remove front fender protector (RH). Refer to EI-23
.
5. Drain engine coolant. Refer to CO-8
.
NOTE:
Perform this step when engine is cold.
6. Remove the following parts.
• Intake manifold; Refer to EM-18
.
• Rocker cover; Refer to EM-30
.
1. O-ring 2. Camshaft position sensor (PHASE) 3. Camshaft bracket
4. Camshaft sprocket (EXH) 5. Camshaft sprocket (INT) 6. Camshaft (EXH)
7. Camshaft (INT) 8. Valve lifter (EXH) 9. Valve lifter (INT)
10. Cylinder head
A. Refer to EM-47
.
PBIC4589E
Page 1725 of 2771
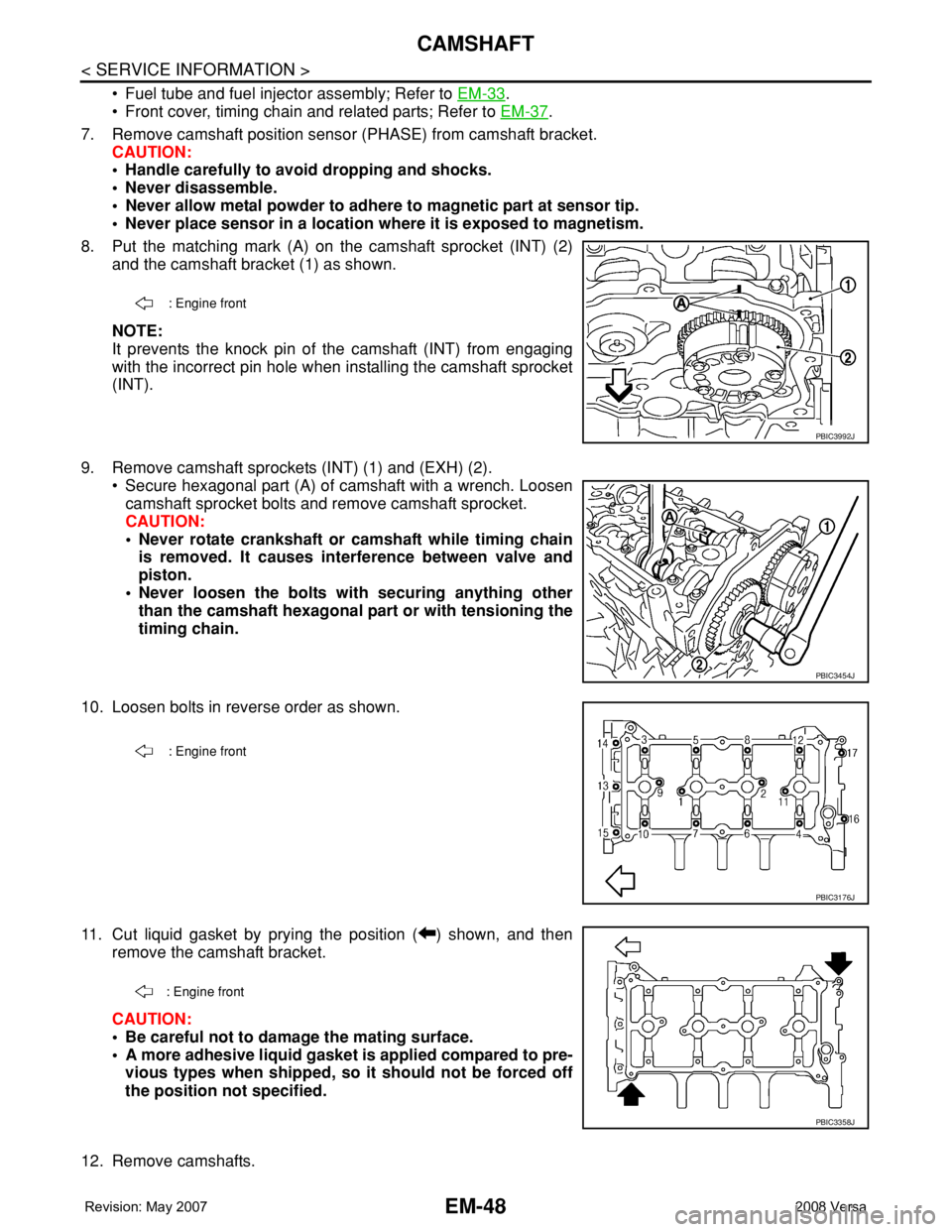
EM-48
< SERVICE INFORMATION >
CAMSHAFT
• Fuel tube and fuel injector assembly; Refer to EM-33.
• Front cover, timing chain and related parts; Refer to EM-37
.
7. Remove camshaft position sensor (PHASE) from camshaft bracket.
CAUTION:
• Handle carefully to avoid dropping and shocks.
• Never disassemble.
• Never allow metal powder to adhere to magnetic part at sensor tip.
• Never place sensor in a location where it is exposed to magnetism.
8. Put the matching mark (A) on the camshaft sprocket (INT) (2)
and the camshaft bracket (1) as shown.
NOTE:
It prevents the knock pin of the camshaft (INT) from engaging
with the incorrect pin hole when installing the camshaft sprocket
(INT).
9. Remove camshaft sprockets (INT) (1) and (EXH) (2).
• Secure hexagonal part (A) of camshaft with a wrench. Loosen
camshaft sprocket bolts and remove camshaft sprocket.
CAUTION:
• Never rotate crankshaft or camshaft while timing chain
is removed. It causes interference between valve and
piston.
• Never loosen the bolts with securing anything other
than the camshaft hexagonal part or with tensioning the
timing chain.
10. Loosen bolts in reverse order as shown.
11. Cut liquid gasket by prying the position ( ) shown, and then
remove the camshaft bracket.
CAUTION:
• Be careful not to damage the mating surface.
• A more adhesive liquid gasket is applied compared to pre-
vious types when shipped, so it should not be forced off
the position not specified.
12. Remove camshafts.
: Engine front
PBIC3992J
PBIC3454J
: Engine front
PBIC3176J
: Engine front
PBIC3358J
Page 1726 of 2771
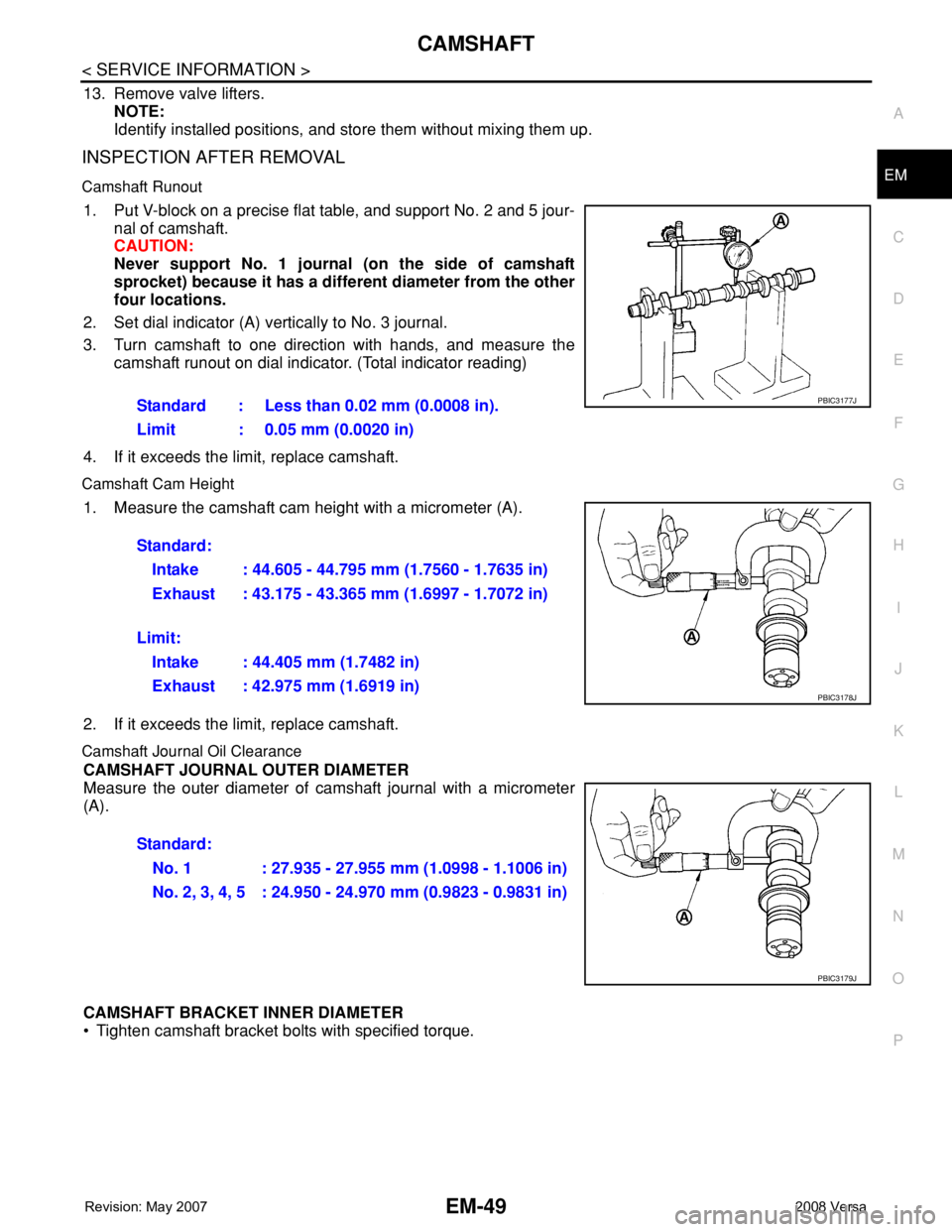
CAMSHAFT
EM-49
< SERVICE INFORMATION >
C
D
E
F
G
H
I
J
K
L
MA
EM
N
P O
13. Remove valve lifters.
NOTE:
Identify installed positions, and store them without mixing them up.
INSPECTION AFTER REMOVAL
Camshaft Runout
1. Put V-block on a precise flat table, and support No. 2 and 5 jour-
nal of camshaft.
CAUTION:
Never support No. 1 journal (on the side of camshaft
sprocket) because it has a different diameter from the other
four locations.
2. Set dial indicator (A) vertically to No. 3 journal.
3. Turn camshaft to one direction with hands, and measure the
camshaft runout on dial indicator. (Total indicator reading)
4. If it exceeds the limit, replace camshaft.
Camshaft Cam Height
1. Measure the camshaft cam height with a micrometer (A).
2. If it exceeds the limit, replace camshaft.
Camshaft Journal Oil Clearance
CAMSHAFT JOURNAL OUTER DIAMETER
Measure the outer diameter of camshaft journal with a micrometer
(A).
CAMSHAFT BRACKET INNER DIAMETER
• Tighten camshaft bracket bolts with specified torque. Standard : Less than 0.02 mm (0.0008 in).
Limit : 0.05 mm (0.0020 in)
PBIC3177J
Standard:
Intake : 44.605 - 44.795 mm (1.7560 - 1.7635 in)
Exhaust : 43.175 - 43.365 mm (1.6997 - 1.7072 in)
Limit:
Intake : 44.405 mm (1.7482 in)
Exhaust : 42.975 mm (1.6919 in)
PBIC3178J
Standard:
No. 1 : 27.935 - 27.955 mm (1.0998 - 1.1006 in)
No. 2, 3, 4, 5 : 24.950 - 24.970 mm (0.9823 - 0.9831 in)
PBIC3179J
Page 1727 of 2771
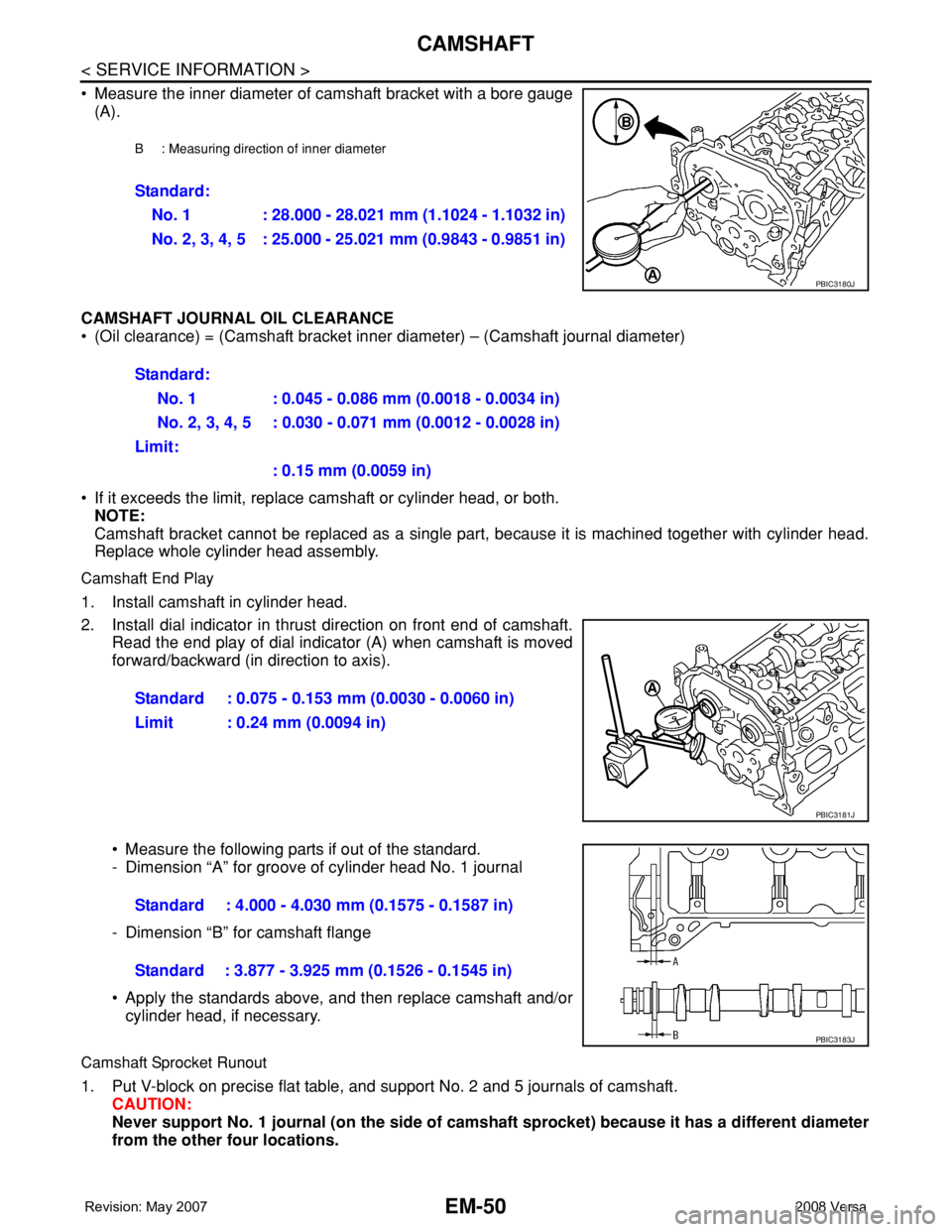
EM-50
< SERVICE INFORMATION >
CAMSHAFT
• Measure the inner diameter of camshaft bracket with a bore gauge
(A).
CAMSHAFT JOURNAL OIL CLEARANCE
• (Oil clearance) = (Camshaft bracket inner diameter) – (Camshaft journal diameter)
• If it exceeds the limit, replace camshaft or cylinder head, or both.
NOTE:
Camshaft bracket cannot be replaced as a single part, because it is machined together with cylinder head.
Replace whole cylinder head assembly.
Camshaft End Play
1. Install camshaft in cylinder head.
2. Install dial indicator in thrust direction on front end of camshaft.
Read the end play of dial indicator (A) when camshaft is moved
forward/backward (in direction to axis).
• Measure the following parts if out of the standard.
- Dimension “A” for groove of cylinder head No. 1 journal
- Dimension “B” for camshaft flange
• Apply the standards above, and then replace camshaft and/or
cylinder head, if necessary.
Camshaft Sprocket Runout
1. Put V-block on precise flat table, and support No. 2 and 5 journals of camshaft.
CAUTION:
Never support No. 1 journal (on the side of camshaft sprocket) because it has a different diameter
from the other four locations.
B : Measuring direction of inner diameter
Standard:
No. 1 : 28.000 - 28.021 mm (1.1024 - 1.1032 in)
No. 2, 3, 4, 5 : 25.000 - 25.021 mm (0.9843 - 0.9851 in)
PBIC3180J
Standard:
No. 1 : 0.045 - 0.086 mm (0.0018 - 0.0034 in)
No. 2, 3, 4, 5 : 0.030 - 0.071 mm (0.0012 - 0.0028 in)
Limit:
: 0.15 mm (0.0059 in)
Standard : 0.075 - 0.153 mm (0.0030 - 0.0060 in)
Limit : 0.24 mm (0.0094 in)
PBIC3181J
Standard : 4.000 - 4.030 mm (0.1575 - 0.1587 in)
Standard : 3.877 - 3.925 mm (0.1526 - 0.1545 in)
PBIC3183J
Page 1728 of 2771
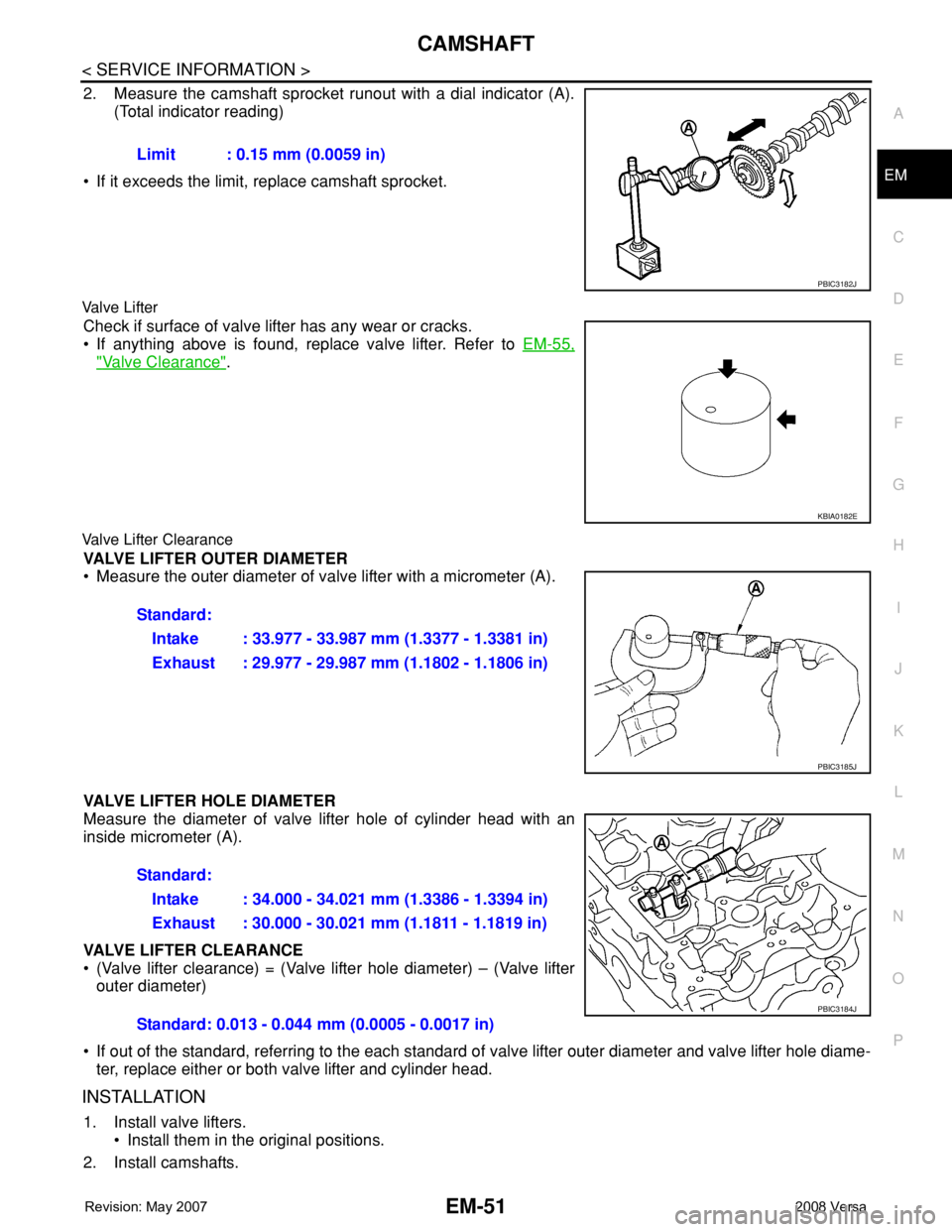
CAMSHAFT
EM-51
< SERVICE INFORMATION >
C
D
E
F
G
H
I
J
K
L
MA
EM
N
P O
2. Measure the camshaft sprocket runout with a dial indicator (A).
(Total indicator reading)
• If it exceeds the limit, replace camshaft sprocket.
Valve Lifter
Check if surface of valve lifter has any wear or cracks.
• If anything above is found, replace valve lifter. Refer to EM-55,
"Valve Clearance".
Valve Lifter Clearance
VALVE LIFTER OUTER DIAMETER
• Measure the outer diameter of valve lifter with a micrometer (A).
VALVE LIFTER HOLE DIAMETER
Measure the diameter of valve lifter hole of cylinder head with an
inside micrometer (A).
VALVE LIFTER CLEARANCE
• (Valve lifter clearance) = (Valve lifter hole diameter) – (Valve lifter
outer diameter)
• If out of the standard, referring to the each standard of valve lifter outer diameter and valve lifter hole diame-
ter, replace either or both valve lifter and cylinder head.
INSTALLATION
1. Install valve lifters.
• Install them in the original positions.
2. Install camshafts.Limit : 0.15 mm (0.0059 in)
PBIC3182J
KBIA0182E
Standard:
Intake : 33.977 - 33.987 mm (1.3377 - 1.3381 in)
Exhaust : 29.977 - 29.987 mm (1.1802 - 1.1806 in)
PBIC3185J
Standard:
Intake : 34.000 - 34.021 mm (1.3386 - 1.3394 in)
Exhaust : 30.000 - 30.021 mm (1.1811 - 1.1819 in)
Standard: 0.013 - 0.044 mm (0.0005 - 0.0017 in)
PBIC3184J
Page 1729 of 2771
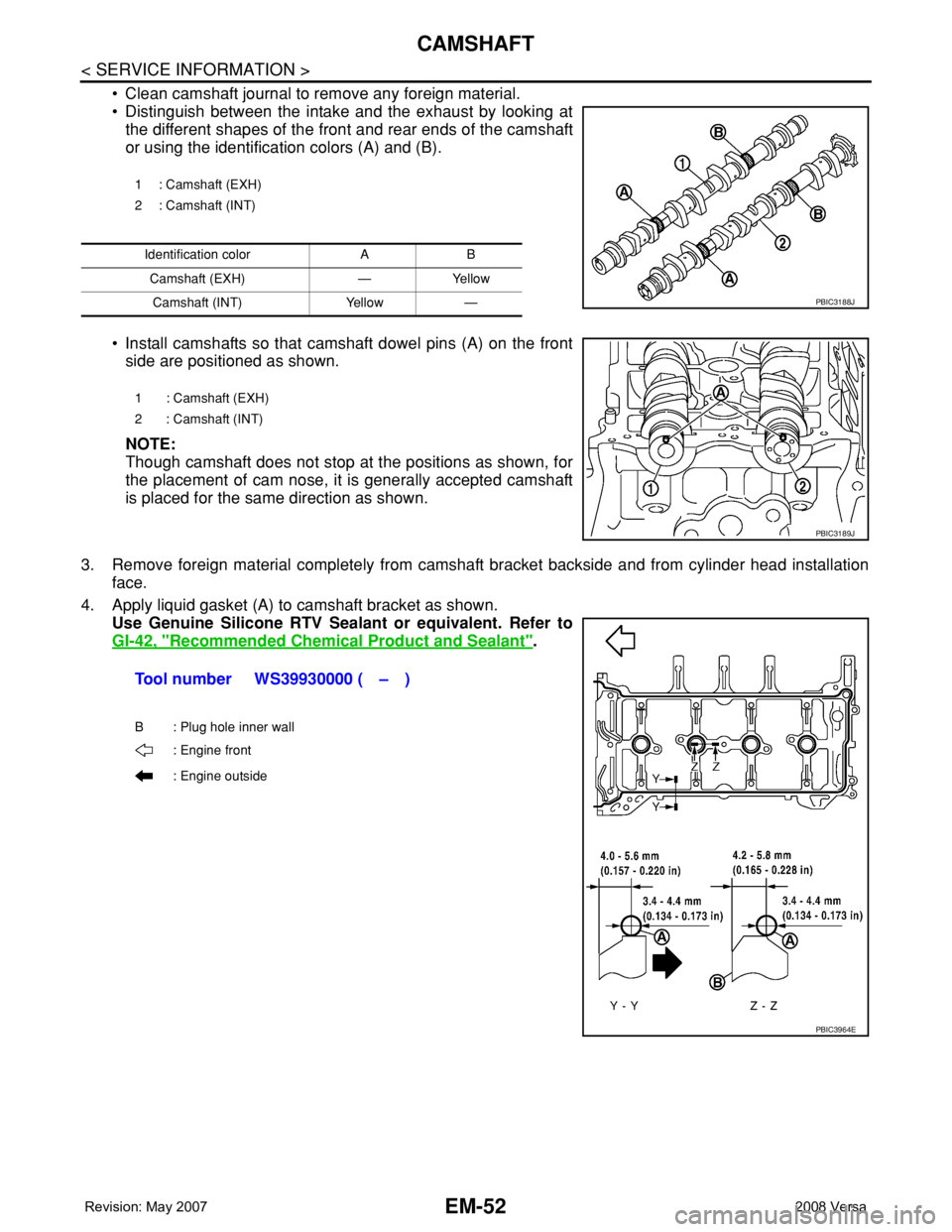
EM-52
< SERVICE INFORMATION >
CAMSHAFT
• Clean camshaft journal to remove any foreign material.
• Distinguish between the intake and the exhaust by looking at
the different shapes of the front and rear ends of the camshaft
or using the identification colors (A) and (B).
• Install camshafts so that camshaft dowel pins (A) on the front
side are positioned as shown.
NOTE:
Though camshaft does not stop at the positions as shown, for
the placement of cam nose, it is generally accepted camshaft
is placed for the same direction as shown.
3. Remove foreign material completely from camshaft bracket backside and from cylinder head installation
face.
4. Apply liquid gasket (A) to camshaft bracket as shown.
Use Genuine Silicone RTV Sealant or equivalent. Refer to
GI-42, "
Recommended Chemical Product and Sealant".
1 : Camshaft (EXH)
2 : Camshaft (INT)
Identification color A B
Camshaft (EXH) — Yellow
Camshaft (INT) Yellow —
PBIC3188J
1 : Camshaft (EXH)
2 : Camshaft (INT)
PBIC3189J
Tool number WS39930000 ( – )
B : Plug hole inner wall
: Engine front
: Engine outside
PBIC3964E
Page 1730 of 2771
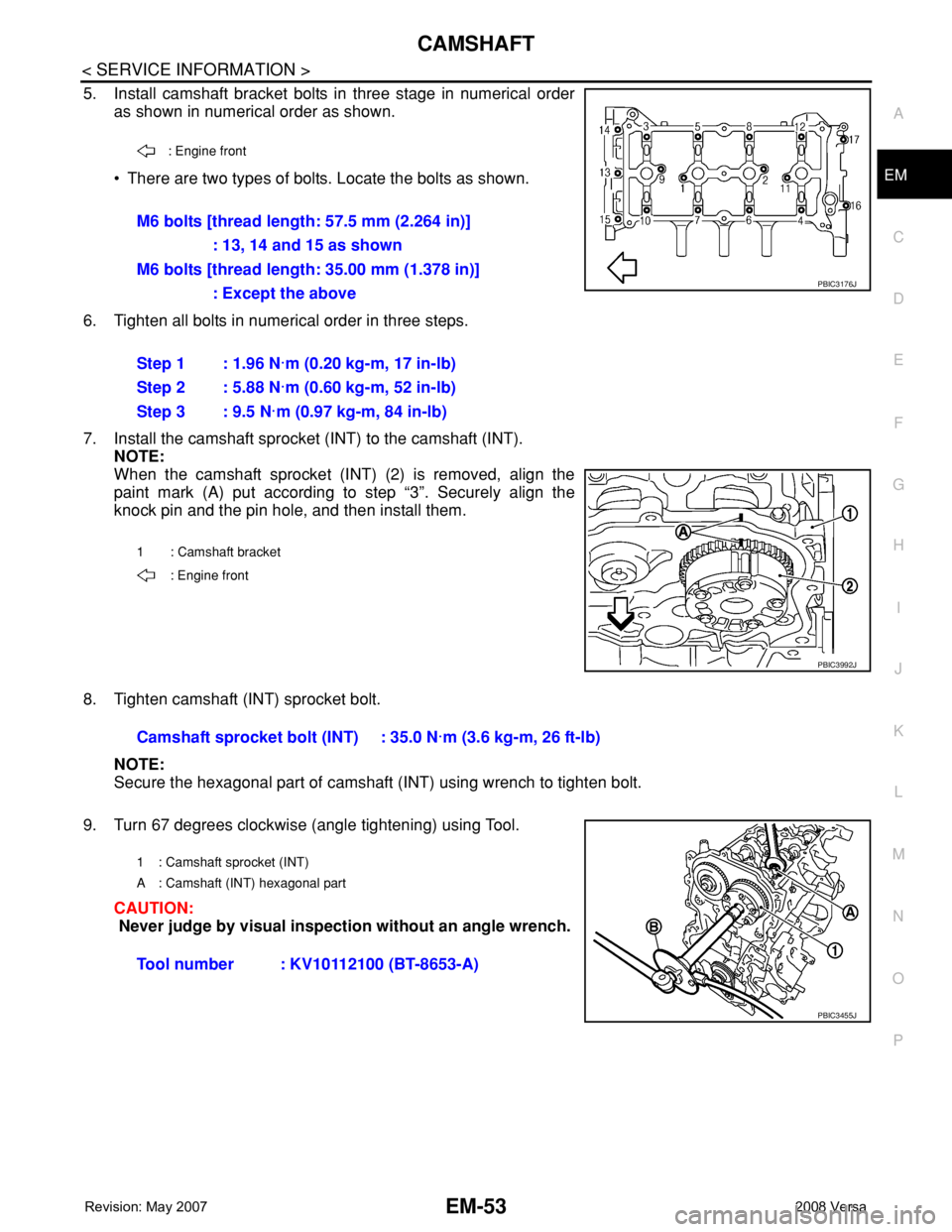
CAMSHAFT
EM-53
< SERVICE INFORMATION >
C
D
E
F
G
H
I
J
K
L
MA
EM
N
P O
5. Install camshaft bracket bolts in three stage in numerical order
as shown in numerical order as shown.
• There are two types of bolts. Locate the bolts as shown.
6. Tighten all bolts in numerical order in three steps.
7. Install the camshaft sprocket (INT) to the camshaft (INT).
NOTE:
When the camshaft sprocket (INT) (2) is removed, align the
paint mark (A) put according to step “3”. Securely align the
knock pin and the pin hole, and then install them.
8. Tighten camshaft (INT) sprocket bolt.
NOTE:
Secure the hexagonal part of camshaft (INT) using wrench to tighten bolt.
9. Turn 67 degrees clockwise (angle tightening) using Tool.
CAUTION:
Never judge by visual inspection without an angle wrench.
: Engine front
M6 bolts [thread length: 57.5 mm (2.264 in)]
: 13, 14 and 15 as shown
M6 bolts [thread length: 35.00 mm (1.378 in)]
: Except the above
Step 1 : 1.96 N·m (0.20 kg-m, 17 in-lb)
Step 2 : 5.88 N·m (0.60 kg-m, 52 in-lb)
Step 3 : 9.5 N·m (0.97 kg-m, 84 in-lb)
1 : Camshaft bracket
: Engine front
PBIC3176J
PBIC3992J
Camshaft sprocket bolt (INT) : 35.0 N·m (3.6 kg-m, 26 ft-lb)
1 : Camshaft sprocket (INT)
A : Camshaft (INT) hexagonal part
Tool number : KV10112100 (BT-8653-A)
PBIC3455J