NISSAN VERSA 2006 Workshop Service Repair Manual
Manufacturer: NISSAN, Model Year: 2006, Model line: VERSA, Model: NISSAN VERSA 2006Pages: 2896, PDF Size: 64.73 MB
Page 2701 of 2896
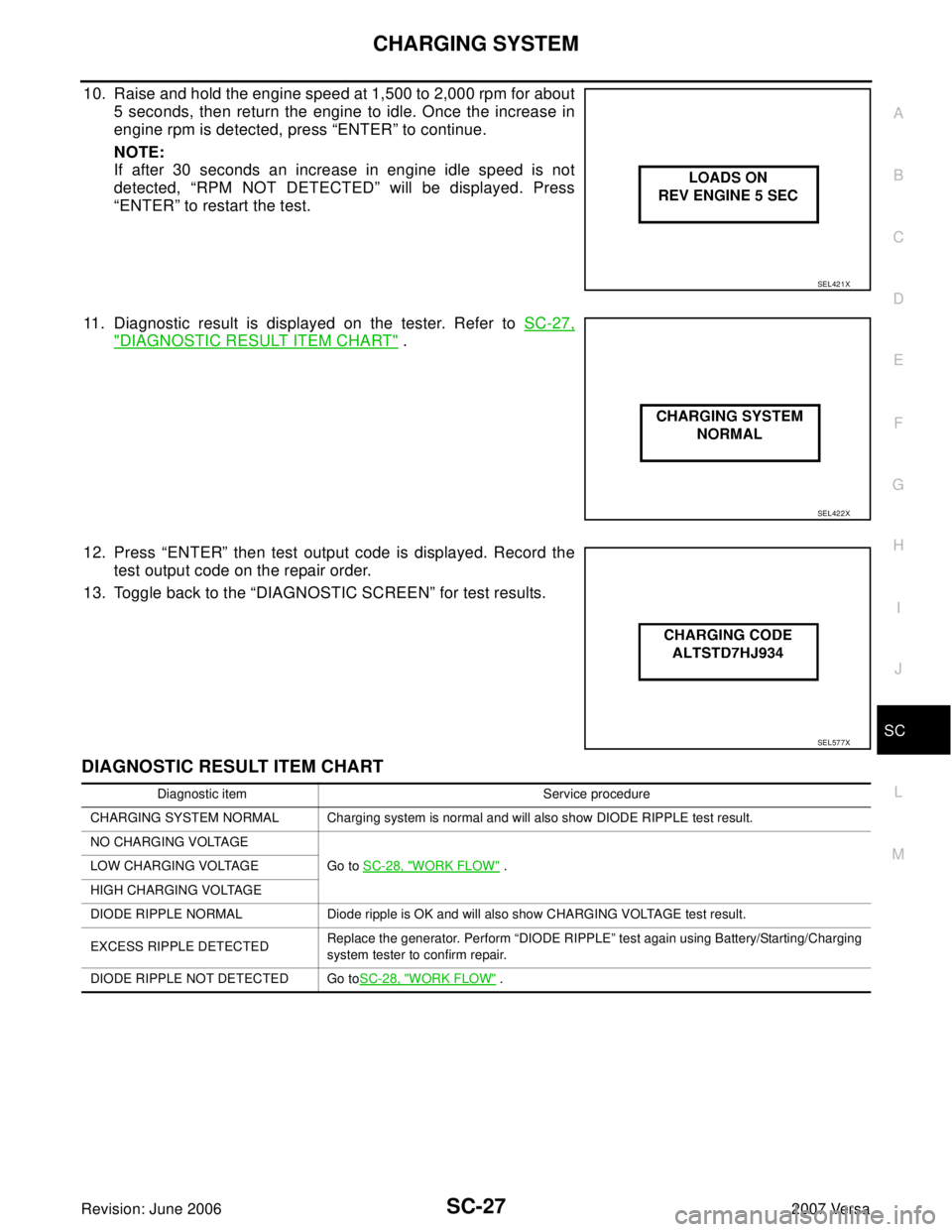
CHARGING SYSTEM
SC-27
C
D
E
F
G
H
I
J
L
MA
B
SC
Revision: June 20062007 Versa
10. Raise and hold the engine speed at 1,500 to 2,000 rpm for about
5 seconds, then return the engine to idle. Once the increase in
engine rpm is detected, press “ENTER” to continue.
NOTE:
If after 30 seconds an increase in engine idle speed is not
detected, “RPM NOT DETECTED” will be displayed. Press
“ENTER” to restart the test.
11. Diagnostic result is displayed on the tester. Refer to SC-27,
"DIAGNOSTIC RESULT ITEM CHART" .
12. Press “ENTER” then test output code is displayed. Record the
test output code on the repair order.
13. Toggle back to the “DIAGNOSTIC SCREEN” for test results.
DIAGNOSTIC RESULT ITEM CHART
SEL421X
SEL422X
SEL577X
Diagnostic item Service procedure
CHARGING SYSTEM NORMAL Charging system is normal and will also show DIODE RIPPLE test result.
NO CHARGING VOLTAGE
Go to SC-28, "
WORK FLOW" . LOW CHARGING VOLTAGE
HIGH CHARGING VOLTAGE
DIODE RIPPLE NORMAL Diode ripple is OK and will also show CHARGING VOLTAGE test result.
EXCESS RIPPLE DETECTEDReplace the generator. Perform “DIODE RIPPLE” test again using Battery/Starting/Charging
system tester to confirm repair.
DIODE RIPPLE NOT DETECTED Go toSC-28, "
WORK FLOW" .
Page 2702 of 2896
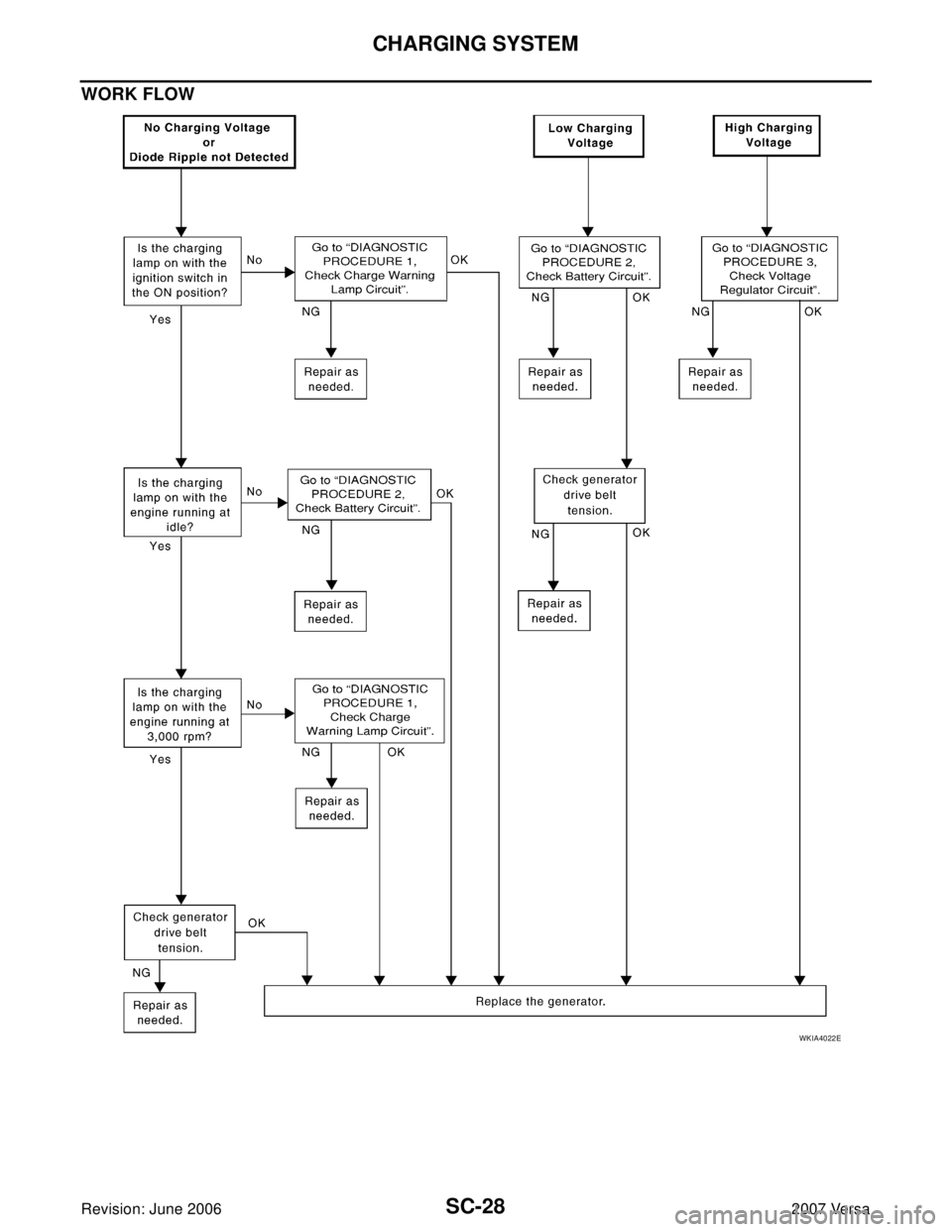
SC-28
CHARGING SYSTEM
Revision: June 20062007 Versa
WORK FLOW
WKIA4022E
Page 2703 of 2896
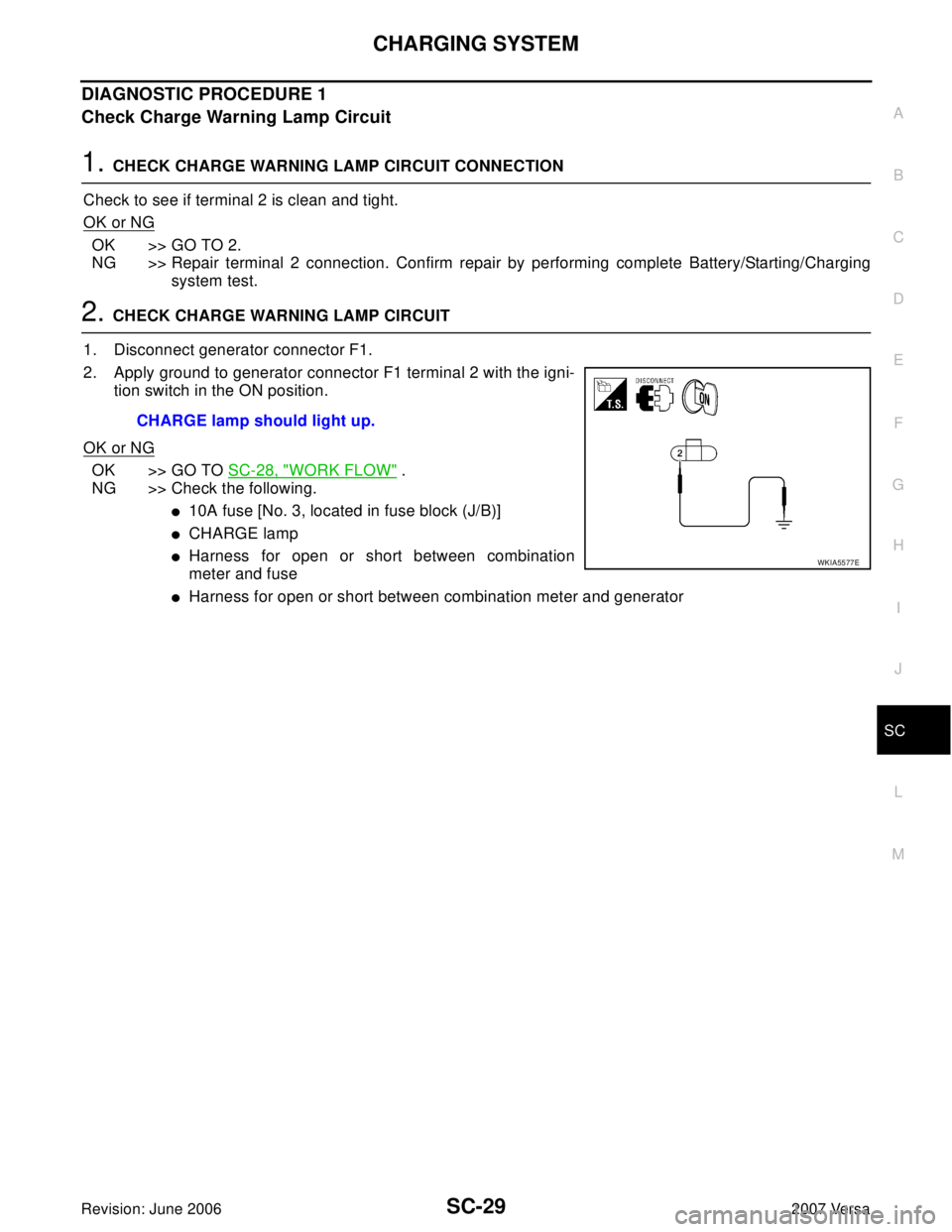
CHARGING SYSTEM
SC-29
C
D
E
F
G
H
I
J
L
MA
B
SC
Revision: June 20062007 Versa
DIAGNOSTIC PROCEDURE 1
Check Charge Warning Lamp Circuit
1. CHECK CHARGE WARNING LAMP CIRCUIT CONNECTION
Check to see if terminal 2 is clean and tight.
OK or NG
OK >> GO TO 2.
NG >> Repair terminal 2 connection. Confirm repair by performing complete Battery/Starting/Charging
system test.
2. CHECK CHARGE WARNING LAMP CIRCUIT
1. Disconnect generator connector F1.
2. Apply ground to generator connector F1 terminal 2 with the igni-
tion switch in the ON position.
OK or NG
OK >> GO TO SC-28, "WORK FLOW" .
NG >> Check the following.
10A fuse [No. 3, located in fuse block (J/B)]
CHARGE lamp
Harness for open or short between combination
meter and fuse
Harness for open or short between combination meter and generator CHARGE lamp should light up.
WKIA5577E
Page 2704 of 2896
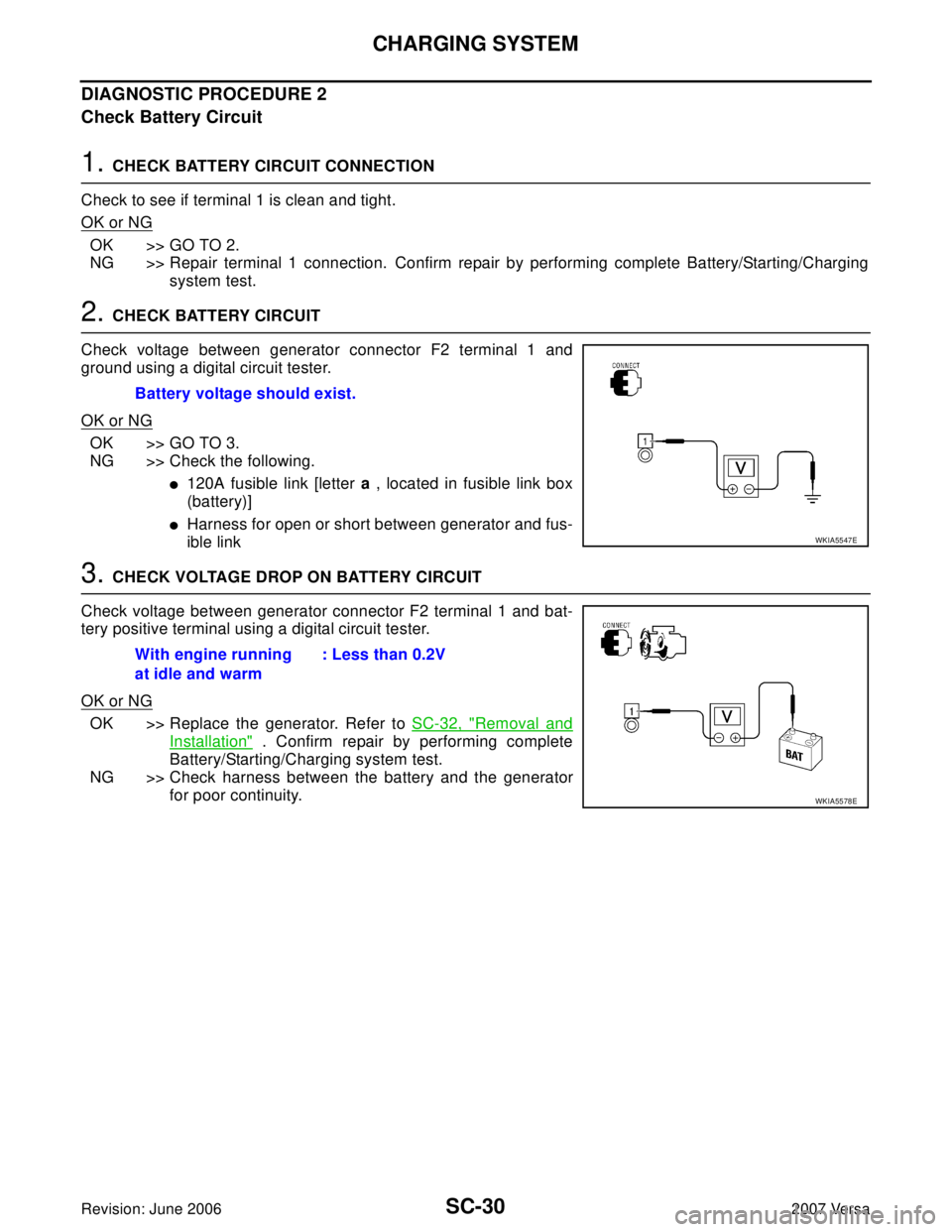
SC-30
CHARGING SYSTEM
Revision: June 20062007 Versa
DIAGNOSTIC PROCEDURE 2
Check Battery Circuit
1. CHECK BATTERY CIRCUIT CONNECTION
Check to see if terminal 1 is clean and tight.
OK or NG
OK >> GO TO 2.
NG >> Repair terminal 1 connection. Confirm repair by performing complete Battery/Starting/Charging
system test.
2. CHECK BATTERY CIRCUIT
Check voltage between generator connector F2 terminal 1 and
ground using a digital circuit tester.
OK or NG
OK >> GO TO 3.
NG >> Check the following.
120A fusible link [letter a , located in fusible link box
(battery)]
Harness for open or short between generator and fus-
ible link
3. CHECK VOLTAGE DROP ON BATTERY CIRCUIT
Check voltage between generator connector F2 terminal 1 and bat-
tery positive terminal using a digital circuit tester.
OK or NG
OK >> Replace the generator. Refer to SC-32, "Removal and
Installation" . Confirm repair by performing complete
Battery/Starting/Charging system test.
NG >> Check harness between the battery and the generator
for poor continuity. Battery voltage should exist.
WKIA5547E
With engine running
at idle and warm: Less than 0.2V
WKIA5578E
Page 2705 of 2896
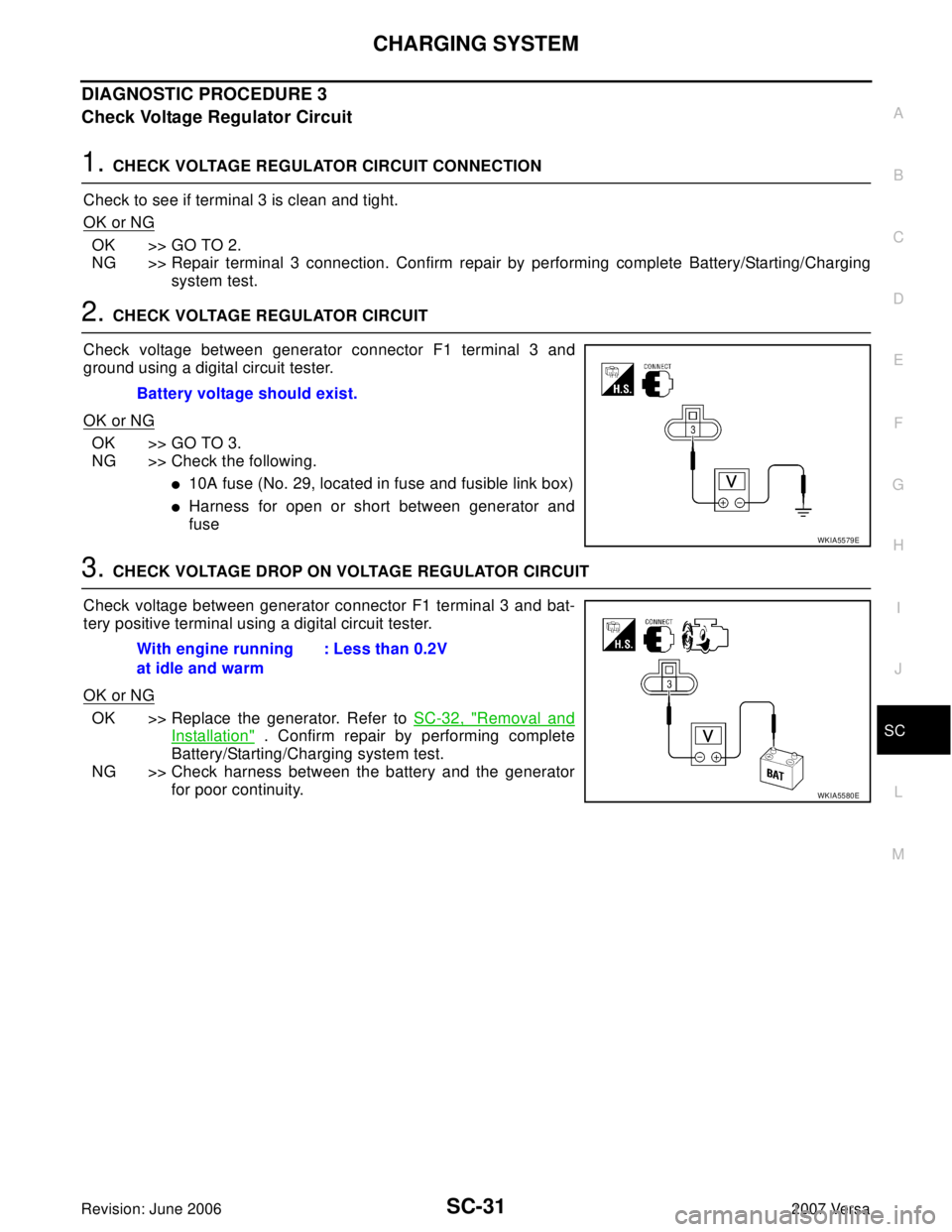
CHARGING SYSTEM
SC-31
C
D
E
F
G
H
I
J
L
MA
B
SC
Revision: June 20062007 Versa
DIAGNOSTIC PROCEDURE 3
Check Voltage Regulator Circuit
1. CHECK VOLTAGE REGULATOR CIRCUIT CONNECTION
Check to see if terminal 3 is clean and tight.
OK or NG
OK >> GO TO 2.
NG >> Repair terminal 3 connection. Confirm repair by performing complete Battery/Starting/Charging
system test.
2. CHECK VOLTAGE REGULATOR CIRCUIT
Check voltage between generator connector F1 terminal 3 and
ground using a digital circuit tester.
OK or NG
OK >> GO TO 3.
NG >> Check the following.
10A fuse (No. 29, located in fuse and fusible link box)
Harness for open or short between generator and
fuse
3. CHECK VOLTAGE DROP ON VOLTAGE REGULATOR CIRCUIT
Check voltage between generator connector F1 terminal 3 and bat-
tery positive terminal using a digital circuit tester.
OK or NG
OK >> Replace the generator. Refer to SC-32, "Removal and
Installation" . Confirm repair by performing complete
Battery/Starting/Charging system test.
NG >> Check harness between the battery and the generator
for poor continuity. Battery voltage should exist.
WKIA5579E
With engine running
at idle and warm: Less than 0.2V
WKIA5580E
Page 2706 of 2896
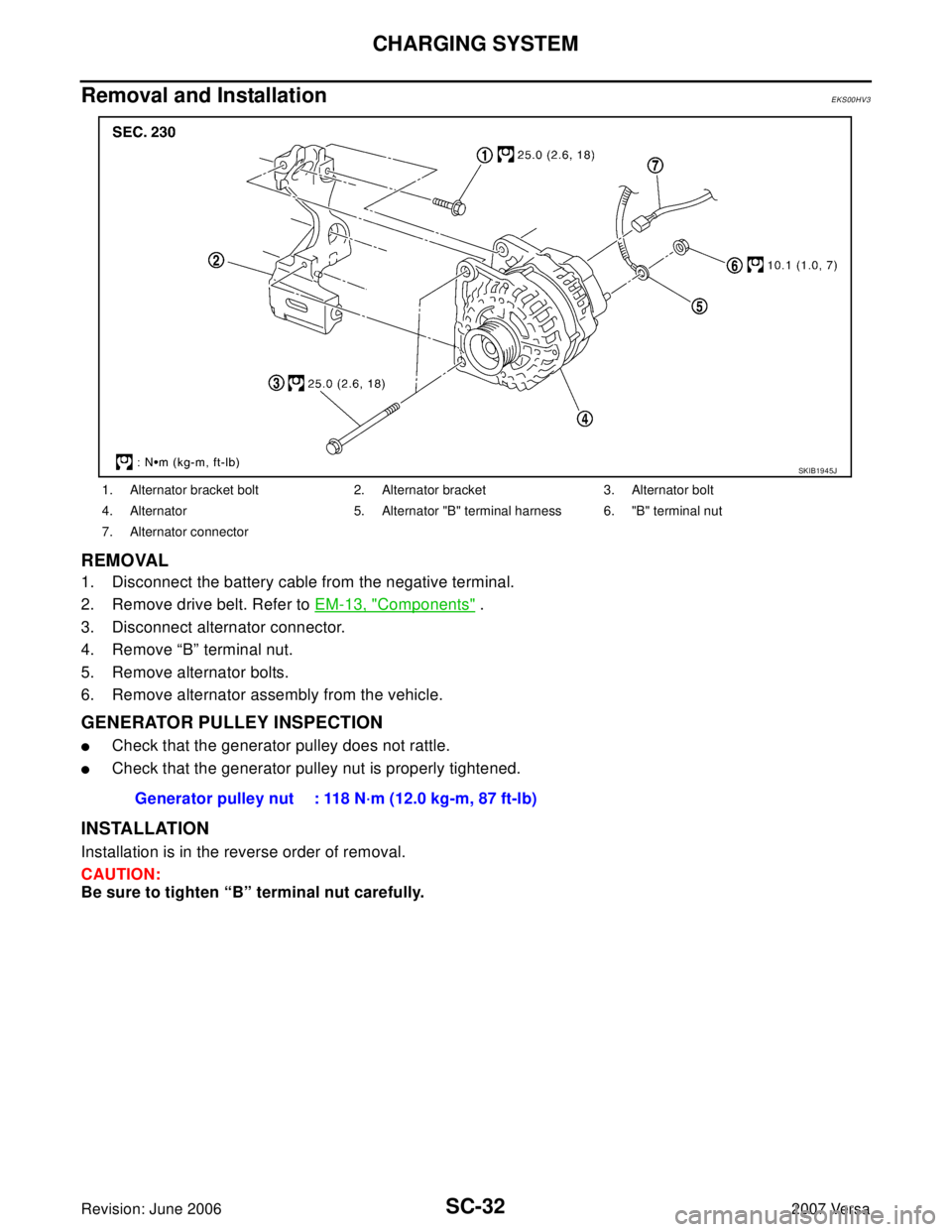
SC-32
CHARGING SYSTEM
Revision: June 20062007 Versa
Removal and Installation EKS00HV3
REMOVAL
1. Disconnect the battery cable from the negative terminal.
2. Remove drive belt. Refer to EM-13, "
Components" .
3. Disconnect alternator connector.
4. Remove “B” terminal nut.
5. Remove alternator bolts.
6. Remove alternator assembly from the vehicle.
GENERATOR PULLEY INSPECTION
Check that the generator pulley does not rattle.
Check that the generator pulley nut is properly tightened.
INSTALLATION
Installation is in the reverse order of removal.
CAUTION:
Be sure to tighten “B” terminal nut carefully.
1. Alternator bracket bolt 2. Alternator bracket 3. Alternator bolt
4. Alternator 5. Alternator "B" terminal harness 6. "B" terminal nut
7. Alternator connector
SKIB1945J
Generator pulley nut : 118 N·m (12.0 kg-m, 87 ft-lb)
Page 2707 of 2896
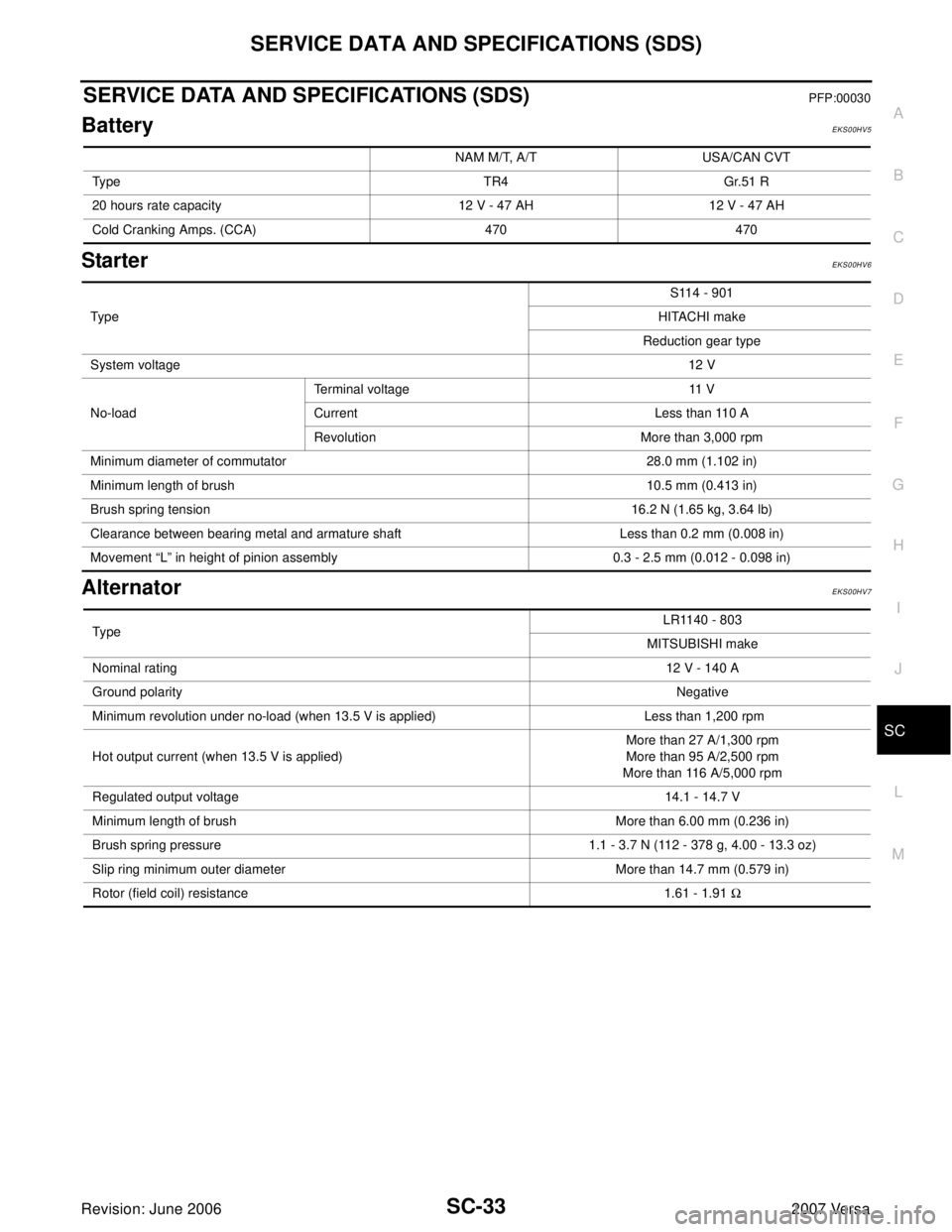
SERVICE DATA AND SPECIFICATIONS (SDS)
SC-33
C
D
E
F
G
H
I
J
L
MA
B
SC
Revision: June 20062007 Versa
SERVICE DATA AND SPECIFICATIONS (SDS)PFP:00030
BatteryEKS00HV5
StarterEKS00HV6
AlternatorEKS00HV7
NAM M/T, A/T USA/CAN CVT
Type TR4 Gr.51 R
20 hours rate capacity 12 V - 47 AH 12 V - 47 AH
Cold Cranking Amps. (CCA) 470 470
Typ eS114 - 901
HITACHI make
Reduction gear type
System voltage12 V
No-loadTerminal voltage 11 V
Current Less than 110 A
Revolution More than 3,000 rpm
Minimum diameter of commutator 28.0 mm (1.102 in)
Minimum length of brush 10.5 mm (0.413 in)
Brush spring tension16.2 N (1.65 kg, 3.64 lb)
Clearance between bearing metal and armature shaft Less than 0.2 mm (0.008 in)
Movement “L” in height of pinion assembly 0.3 - 2.5 mm (0.012 - 0.098 in)
Ty peLR1140 - 803
MITSUBISHI make
Nominal rating12 V - 140 A
Ground polarityNegative
Minimum revolution under no-load (when 13.5 V is applied) Less than 1,200 rpm
Hot output current (when 13.5 V is applied)More than 27 A/1,300 rpm
More than 95 A/2,500 rpm
More than 116 A/5,000 rpm
Regulated output voltage14.1 - 14.7 V
Minimum length of brush More than 6.00 mm (0.236 in)
Brush spring pressure 1.1 - 3.7 N (112 - 378 g, 4.00 - 13.3 oz)
Slip ring minimum outer diameter More than 14.7 mm (0.579 in)
Rotor (field coil) resistance 1.61 - 1.91 Ω
Page 2708 of 2896
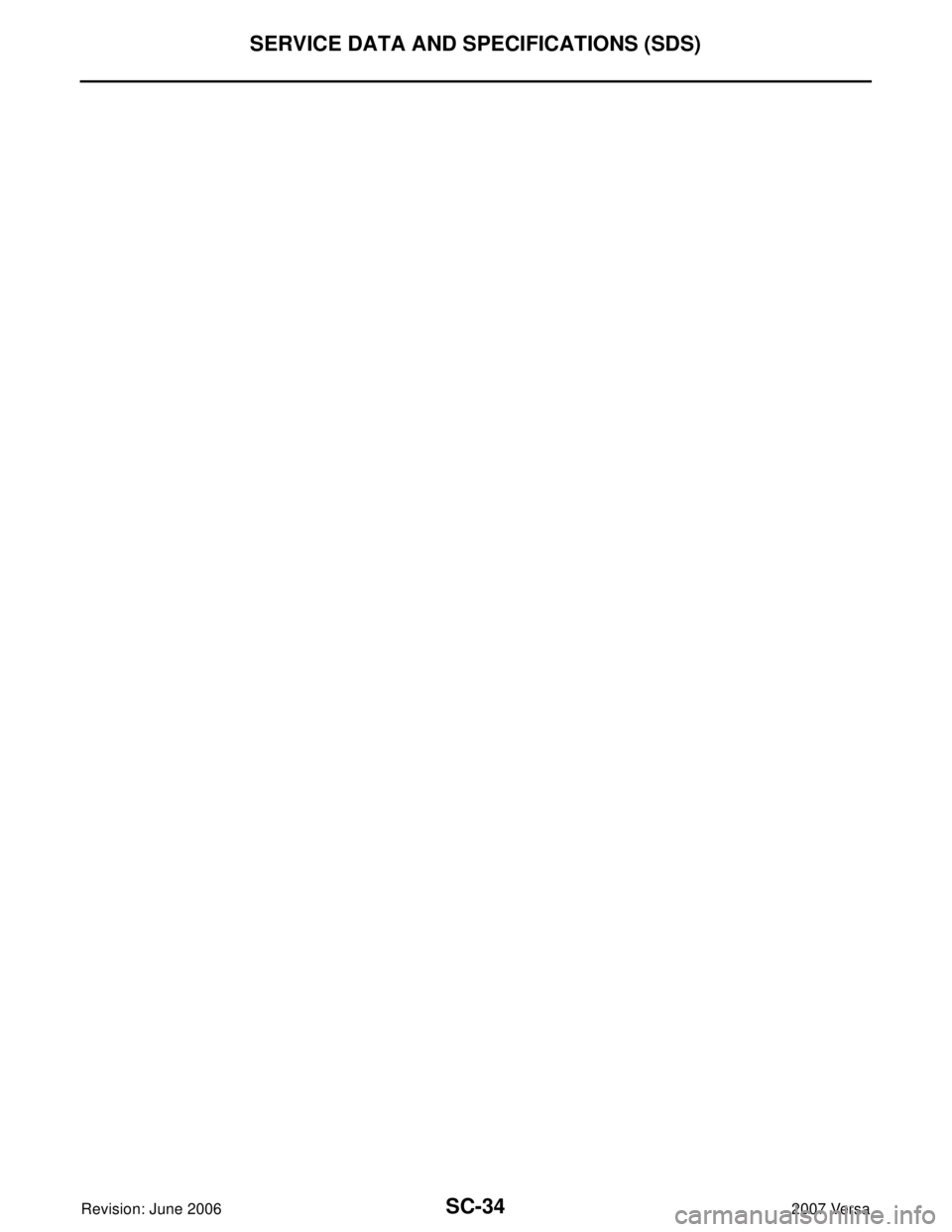
SC-34
SERVICE DATA AND SPECIFICATIONS (SDS)
Revision: June 20062007 Versa
Page 2709 of 2896
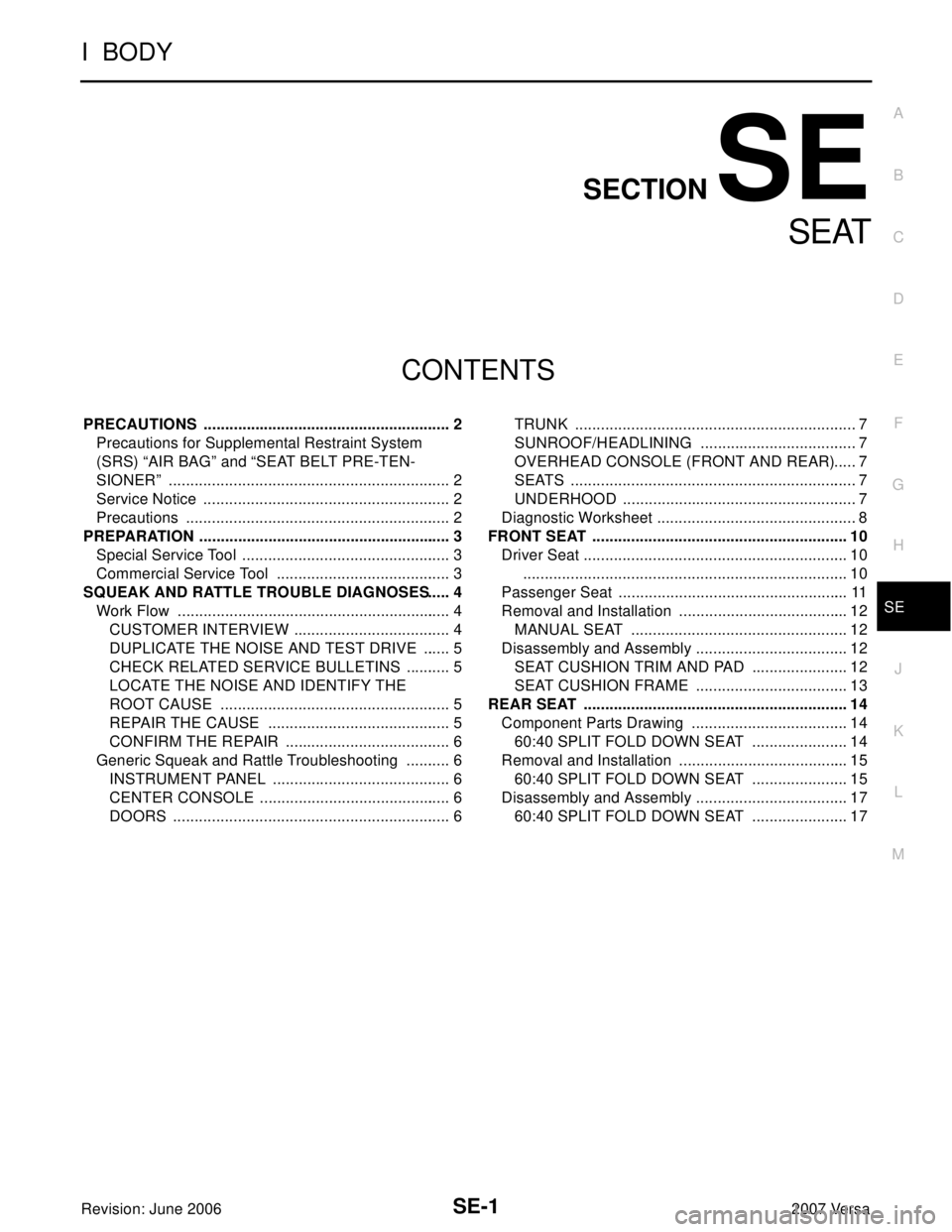
SE-1
SEAT
I BODY
CONTENTS
C
D
E
F
G
H
J
K
L
M
SECTION SE
A
B
SE
Revision: June 20062007 Versa PRECAUTIONS .......................................................... 2
Precautions for Supplemental Restraint System
(SRS) “AIR BAG” and “SEAT BELT PRE-TEN-
SIONER” .................................................................. 2
Service Notice .......................................................... 2
Precautions .............................................................. 2
PREPARATION ........................................................... 3
Special Service Tool ................................................. 3
Commercial Service Tool ......................................... 3
SQUEAK AND RATTLE TROUBLE DIAGNOSES ..... 4
Work Flow ................................................................ 4
CUSTOMER INTERVIEW ..................................... 4
DUPLICATE THE NOISE AND TEST DRIVE ....... 5
CHECK RELATED SERVICE BULLETINS ........... 5
LOCATE THE NOISE AND IDENTIFY THE
ROOT CAUSE ...................................................... 5
REPAIR THE CAUSE ........................................... 5
CONFIRM THE REPAIR ....................................... 6
Generic Squeak and Rattle Troubleshooting ........... 6
INSTRUMENT PANEL .......................................... 6
CENTER CONSOLE ............................................. 6
DOORS ................................................................. 6TRUNK .................................................................. 7
SUNROOF/HEADLINING ..................................... 7
OVERHEAD CONSOLE (FRONT AND REAR) ..... 7
SEATS ................................................................... 7
UNDERHOOD ....................................................... 7
Diagnostic Worksheet ............................................... 8
FRONT SEAT ............................................................ 10
Driver Seat .............................................................. 10
............................................................................ 10
Passenger Seat ...................................................... 11
Removal and Installation ........................................ 12
MANUAL SEAT ................................................... 12
Disassembly and Assembly .................................... 12
SEAT CUSHION TRIM AND PAD ....................... 12
SEAT CUSHION FRAME .................................... 13
REAR SEAT .............................................................. 14
Component Parts Drawing ..................................... 14
60:40 SPLIT FOLD DOWN SEAT ....................... 14
Removal and Installation ........................................ 15
60:40 SPLIT FOLD DOWN SEAT ....................... 15
Disassembly and Assembly .................................... 17
60:40 SPLIT FOLD DOWN SEAT ....................... 17
Page 2710 of 2896
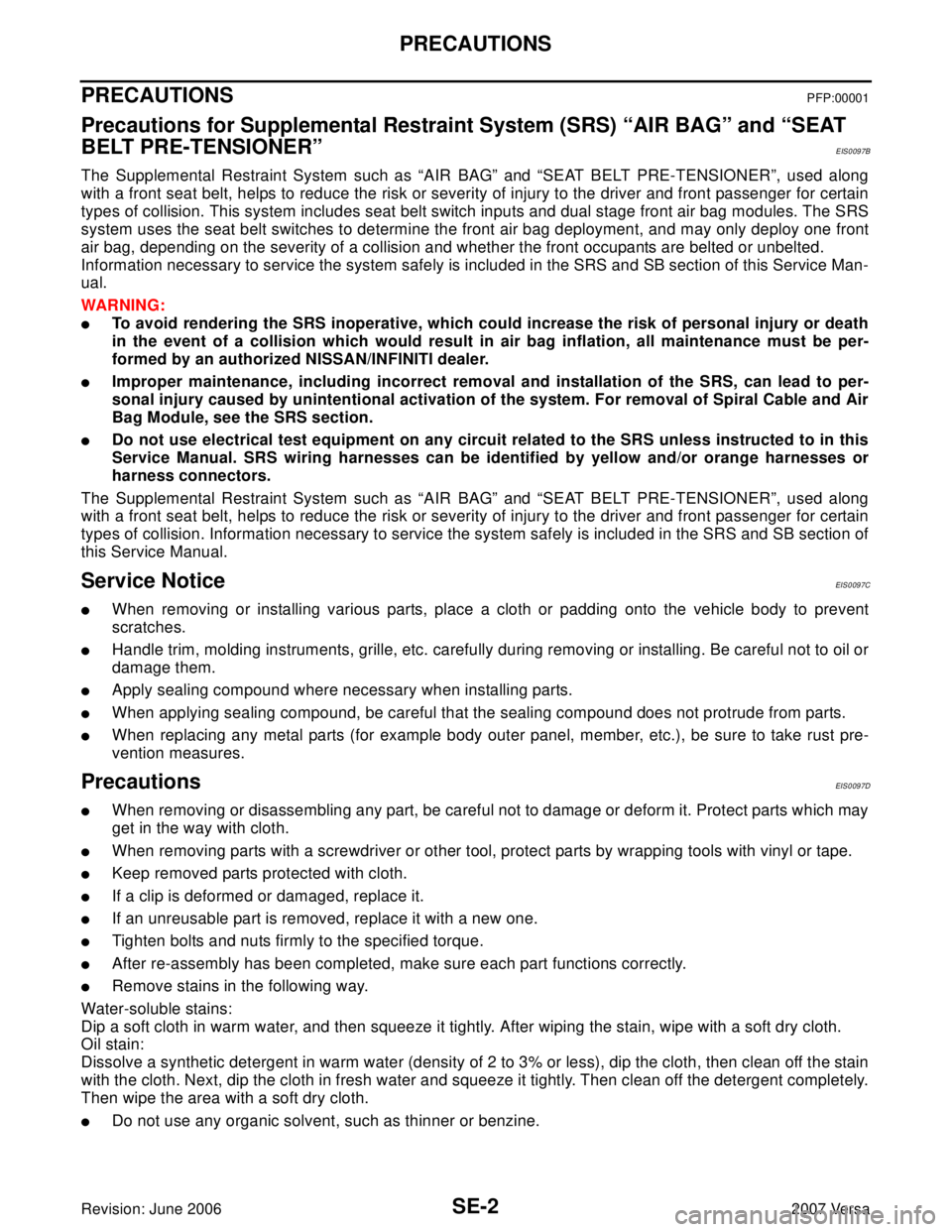
SE-2
PRECAUTIONS
Revision: June 20062007 Versa
PRECAUTIONSPFP:00001
Precautions for Supplemental Restraint System (SRS) “AIR BAG” and “SEAT
BELT PRE-TENSIONER”
EIS0097B
The Supplemental Restraint System such as “AIR BAG” and “SEAT BELT PRE-TENSIONER”, used along
with a front seat belt, helps to reduce the risk or severity of injury to the driver and front passenger for certain
types of collision. This system includes seat belt switch inputs and dual stage front air bag modules. The SRS
system uses the seat belt switches to determine the front air bag deployment, and may only deploy one front
air bag, depending on the severity of a collision and whether the front occupants are belted or unbelted.
Information necessary to service the system safely is included in the SRS and SB section of this Service Man-
ual.
WAR NIN G:
To avoid rendering the SRS inoperative, which could increase the risk of personal injury or death
in the event of a collision which would result in air bag inflation, all maintenance must be per-
formed by an authorized NISSAN/INFINITI dealer.
Improper maintenance, including incorrect removal and installation of the SRS, can lead to per-
sonal injury caused by unintentional activation of the system. For removal of Spiral Cable and Air
Bag Module, see the SRS section.
Do not use electrical test equipment on any circuit related to the SRS unless instructed to in this
Service Manual. SRS wiring harnesses can be identified by yellow and/or orange harnesses or
harness connectors.
The Supplemental Restraint System such as “AIR BAG” and “SEAT BELT PRE-TENSIONER”, used along
with a front seat belt, helps to reduce the risk or severity of injury to the driver and front passenger for certain
types of collision. Information necessary to service the system safely is included in the SRS and SB section of
this Service Manual.
Service NoticeEIS0097C
When removing or installing various parts, place a cloth or padding onto the vehicle body to prevent
scratches.
Handle trim, molding instruments, grille, etc. carefully during removing or installing. Be careful not to oil or
damage them.
Apply sealing compound where necessary when installing parts.
When applying sealing compound, be careful that the sealing compound does not protrude from parts.
When replacing any metal parts (for example body outer panel, member, etc.), be sure to take rust pre-
vention measures.
Precautions EIS0097D
When removing or disassembling any part, be careful not to damage or deform it. Protect parts which may
get in the way with cloth.
When removing parts with a screwdriver or other tool, protect parts by wrapping tools with vinyl or tape.
Keep removed parts protected with cloth.
If a clip is deformed or damaged, replace it.
If an unreusable part is removed, replace it with a new one.
Tighten bolts and nuts firmly to the specified torque.
After re-assembly has been completed, make sure each part functions correctly.
Remove stains in the following way.
Water-soluble stains:
Dip a soft cloth in warm water, and then squeeze it tightly. After wiping the stain, wipe with a soft dry cloth.
Oil stain:
Dissolve a synthetic detergent in warm water (density of 2 to 3% or less), dip the cloth, then clean off the stain
with the cloth. Next, dip the cloth in fresh water and squeeze it tightly. Then clean off the detergent completely.
Then wipe the area with a soft dry cloth.
Do not use any organic solvent, such as thinner or benzine.