ignition OPEL FRONTERA 1998 Workshop Manual
[x] Cancel search | Manufacturer: OPEL, Model Year: 1998, Model line: FRONTERA, Model: OPEL FRONTERA 1998Pages: 6000, PDF Size: 97 MB
Page 3460 of 6000
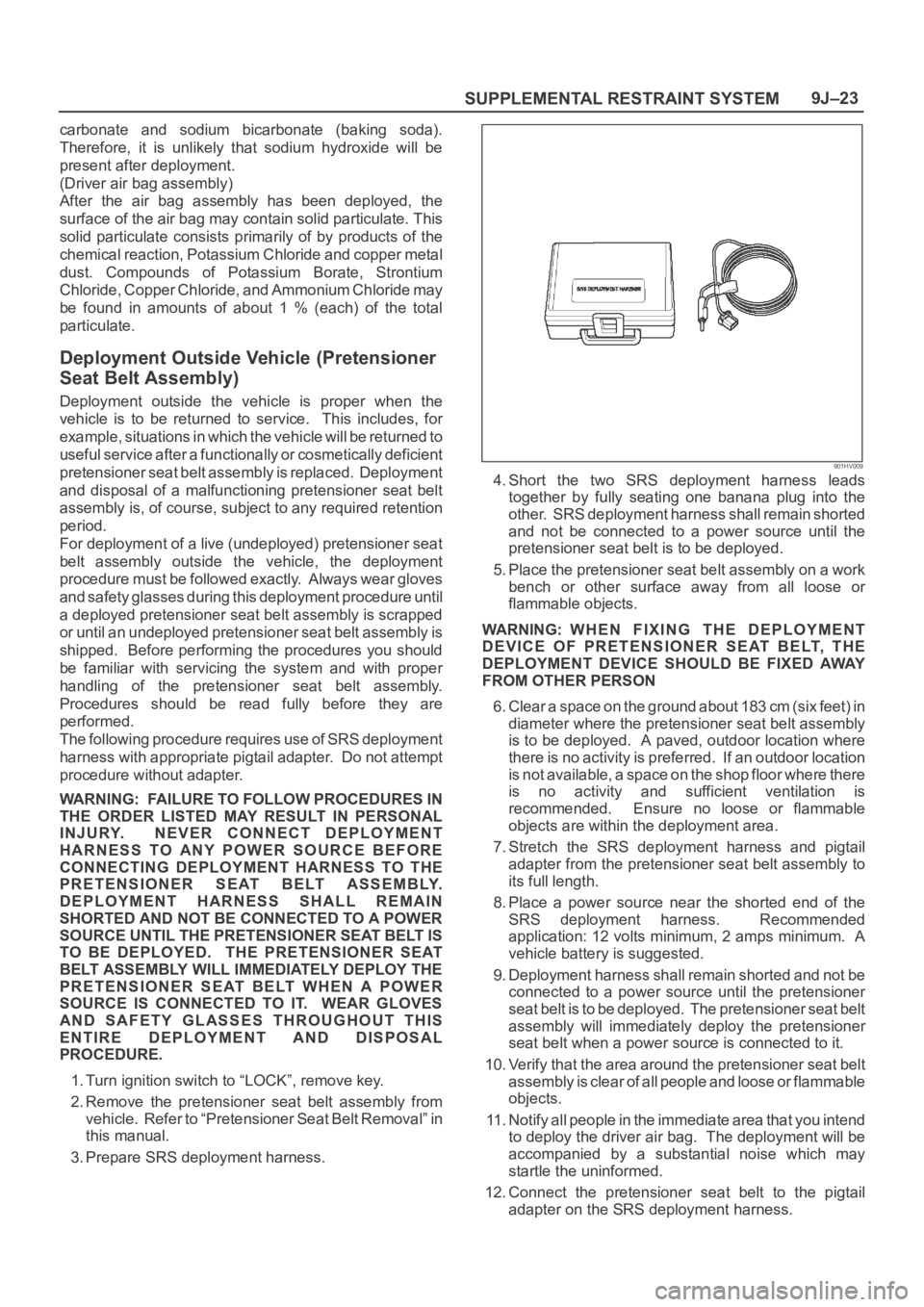
SUPPLEMENTAL RESTRAINT SYSTEM9J–23
carbonate and sodium bicarbonate (baking soda).
Therefore, it is unlikely that sodium hydroxide will be
present after deployment.
(Driver air bag assembly)
After the air bag assembly has been deployed, the
surface of the air bag may contain solid particulate. This
solid particulate consists primarily of by products of the
chemical reaction, Potassium Chloride and copper metal
dust. Compounds of Potassium Borate, Strontium
Chloride, Copper Chloride, and Ammonium Chloride may
be found in amounts of about 1 % (each) of the total
particulate.
Deployment Outside Vehicle (Pretensioner
Seat Belt Assembly)
Deployment outside the vehicle is proper when the
vehicle is to be returned to service. This includes, for
example, situations in which the vehicle will be returned to
useful service after a functionally or cosmetically deficient
pretensioner seat belt assembly is replaced. Deployment
and disposal of a malfunctioning pretensioner seat belt
assembly is, of course, subject to any required retention
period.
For deployment of a live (undeployed) pretensioner seat
belt assembly outside the vehicle, the deployment
procedure must be followed exactly. Always wear gloves
and safety glasses during this deployment procedure until
a deployed pretensioner seat belt assembly is scrapped
or until an undeployed pretensioner seat belt assembly is
shipped. Before performing the procedures you should
be familiar with servicing the system and with proper
handling of the pretensioner seat belt assembly.
Procedures should be read fully before they are
performed.
The following procedure requires use of SRS deployment
harness with appropriate pigtail adapter. Do not attempt
procedure without adapter.
WARNING: FAILURE TO FOLLOW PROCEDURES IN
THE ORDER LISTED MAY RESULT IN PERSONAL
INJURY. NEVER CONNECT DEPLOYMENT
HARNESS TO ANY POWER SOURCE BEFORE
CONNECTING DEPLOYMENT HARNESS TO THE
PRETENSIONER SEAT BELT ASSEMBLY.
DEPLOYMENT HARNESS SHALL REMAIN
SHORTED AND NOT BE CONNECTED TO A POWER
SOURCE UNTIL THE PRETENSIONER SEAT BELT IS
TO BE DEPLOYED. THE PRETENSIONER SEAT
BELT ASSEMBLY WILL IMMEDIATELY DEPLOY THE
PRETENSIONER SEAT BELT WHEN A POWER
SOURCE IS CONNECTED TO IT. WEAR GLOVES
AND SAFETY GLASSES THROUGHOUT THIS
ENTIRE DEPLOYMENT AND DISPOSAL
PROCEDURE.
1. Turn ignition switch to “LOCK”, remove key.
2. Remove the pretensioner seat belt assembly from
vehicle. Refer to “Pretensioner Seat Belt Removal” in
this manual.
3. Prepare SRS deployment harness.
901HV009
4. Short the two SRS deployment harness leads
together by fully seating one banana plug into the
other. SRS deployment harness shall remain shorted
and not be connected to a power source until the
pretensioner seat belt is to be deployed.
5. Place the pretensioner seat belt assembly on a work
bench or other surface away from all loose or
flammable objects.
WARNING: WHEN FIXING THE DEPLOYMENT
DEVICE OF PRETENSIONER SEAT BELT, THE
DEPLOYMENT DEVICE SHOULD BE FIXED AWAY
FROM OTHER PERSON
6. Clear a space on the ground about 183 cm (six feet) in
diameter where the pretensioner seat belt assembly
is to be deployed. A paved, outdoor location where
there is no activity is preferred. If an outdoor location
is not available, a space on the shop floor where there
is no activity and sufficient ventilation is
recommended. Ensure no loose or flammable
objects are within the deployment area.
7. Stretch the SRS deployment harness and pigtail
adapter from the pretensioner seat belt assembly to
its full length.
8. Place a power source near the shorted end of the
SRS deployment harness. Recommended
application: 12 volts minimum, 2 amps minimum. A
vehicle battery is suggested.
9. Deployment harness shall remain shorted and not be
connected to a power source until the pretensioner
seat belt is to be deployed. The pretensioner seat belt
assembly will immediately deploy the pretensioner
seat belt when a power source is connected to it.
10. Verify that the area around the pretensioner seat belt
assembly is clear of all people and loose or flammable
objects.
11. Notify all people in the immediate area that you intend
to deploy the driver air bag. The deployment will be
accompanied by a substantial noise which may
startle the uninformed.
12. Connect the pretensioner seat belt to the pigtail
adapter on the SRS deployment harness.
Page 3462 of 6000
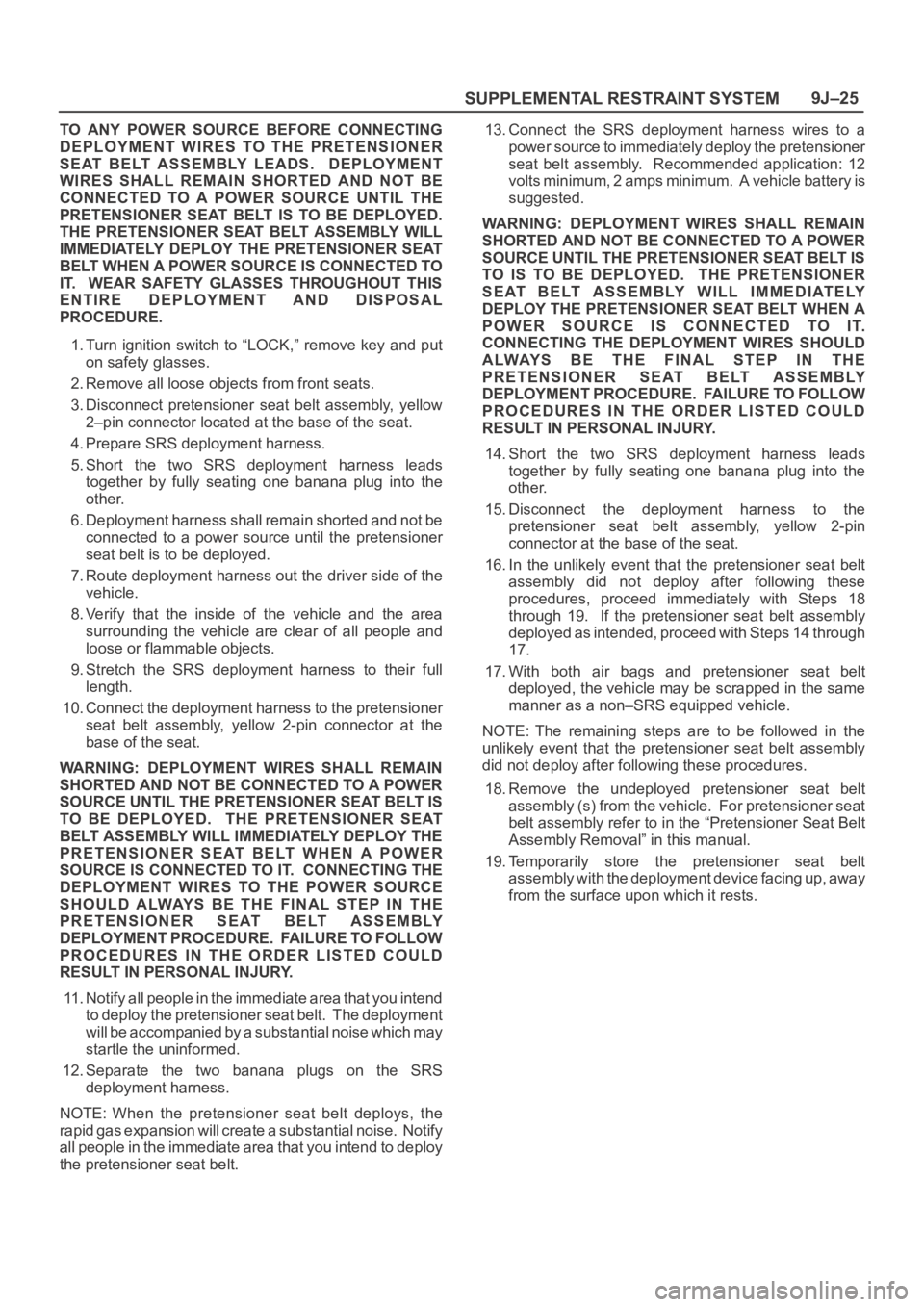
SUPPLEMENTAL RESTRAINT SYSTEM9J–25
TO ANY POWER SOURCE BEFORE CONNECTING
DEPLOYMENT WIRES TO THE PRETENSIONER
SEAT BELT ASSEMBLY LEADS. DEPLOYMENT
WIRES SHALL REMAIN SHORTED AND NOT BE
CONNECTED TO A POWER SOURCE UNTIL THE
PRETENSIONER SEAT BELT IS TO BE DEPLOYED.
THE PRETENSIONER SEAT BELT ASSEMBLY WILL
IMMEDIATELY DEPLOY THE PRETENSIONER SEAT
BELT WHEN A POWER SOURCE IS CONNECTED TO
IT. WEAR SAFETY GLASSES THROUGHOUT THIS
ENTIRE DEPLOYMENT AND DISPOSAL
PROCEDURE.
1. Turn ignition switch to “LOCK,” remove key and put
on safety glasses.
2. Remove all loose objects from front seats.
3. Disconnect pretensioner seat belt assembly, yellow
2–pin connector located at the base of the seat.
4. Prepare SRS deployment harness.
5. Short the two SRS deployment harness leads
together by fully seating one banana plug into the
other.
6. Deployment harness shall remain shorted and not be
connected to a power source until the pretensioner
seat belt is to be deployed.
7. Route deployment harness out the driver side of the
vehicle.
8. Verify that the inside of the vehicle and the area
surrounding the vehicle are clear of all people and
loose or flammable objects.
9. Stretch the SRS deployment harness to their full
length.
10. Connect the deployment harness to the pretensioner
seat belt assembly, yellow 2-pin connector at the
base of the seat.
WARNING: DEPLOYMENT WIRES SHALL REMAIN
SHORTED AND NOT BE CONNECTED TO A POWER
SOURCE UNTIL THE PRETENSIONER SEAT BELT IS
TO BE DEPLOYED. THE PRETENSIONER SEAT
BELT ASSEMBLY WILL IMMEDIATELY DEPLOY THE
PRETENSIONER SEAT BELT WHEN A POWER
SOURCE IS CONNECTED TO IT. CONNECTING THE
DEPLOYMENT WIRES TO THE POWER SOURCE
SHOULD ALWAYS BE THE FINAL STEP IN THE
PRETENSIONER SEAT BELT ASSEMBLY
DEPLOYMENT PROCEDURE. FAILURE TO FOLLOW
PROCEDURES IN THE ORDER LISTED COULD
RESULT IN PERSONAL INJURY.
11. Notify all people in the immediate area that you intend
to deploy the pretensioner seat belt. The deployment
will be accompanied by a substantial noise which may
startle the uninformed.
12. Separate the two banana plugs on the SRS
deployment harness.
NOTE: When the pretensioner seat belt deploys, the
rapid gas expansion will create a substantial noise. Notify
all people in the immediate area that you intend to deploy
the pretensioner seat belt.13. Connect the SRS deployment harness wires to a
power source to immediately deploy the pretensioner
seat belt assembly. Recommended application: 12
volts minimum, 2 amps minimum. A vehicle battery is
suggested.
WARNING: DEPLOYMENT WIRES SHALL REMAIN
SHORTED AND NOT BE CONNECTED TO A POWER
SOURCE UNTIL THE PRETENSIONER SEAT BELT IS
TO IS TO BE DEPLOYED. THE PRETENSIONER
SEAT BELT ASSEMBLY WILL IMMEDIATELY
DEPLOY THE PRETENSIONER SEAT BELT WHEN A
POWER SOURCE IS CONNECTED TO IT.
CONNECTING THE DEPLOYMENT WIRES SHOULD
ALWAYS BE THE FINAL STEP IN THE
PRETENSIONER SEAT BELT ASSEMBLY
DEPLOYMENT PROCEDURE. FAILURE TO FOLLOW
PROCEDURES IN THE ORDER LISTED COULD
RESULT IN PERSONAL INJURY.
14. Short the two SRS deployment harness leads
together by fully seating one banana plug into the
other.
15. Disconnect the deployment harness to the
pretensioner seat belt assembly, yellow 2-pin
connector at the base of the seat.
16. In the unlikely event that the pretensioner seat belt
assembly did not deploy after following these
procedures, proceed immediately with Steps 18
through 19. If the pretensioner seat belt assembly
deployed as intended, proceed with Steps 14 through
17.
17. With both air bags and pretensioner seat belt
deployed, the vehicle may be scrapped in the same
manner as a non–SRS equipped vehicle.
NOTE: The remaining steps are to be followed in the
unlikely event that the pretensioner seat belt assembly
did not deploy after following these procedures.
18. Remove the undeployed pretensioner seat belt
assembly (s) from the vehicle. For pretensioner seat
belt assembly refer to in the “Pretensioner Seat Belt
Assembly Removal” in this manual.
19.Temporarily store the pretensioner seat belt
assembly with the deployment device facing up, away
from the surface upon which it rests.
Page 3465 of 6000
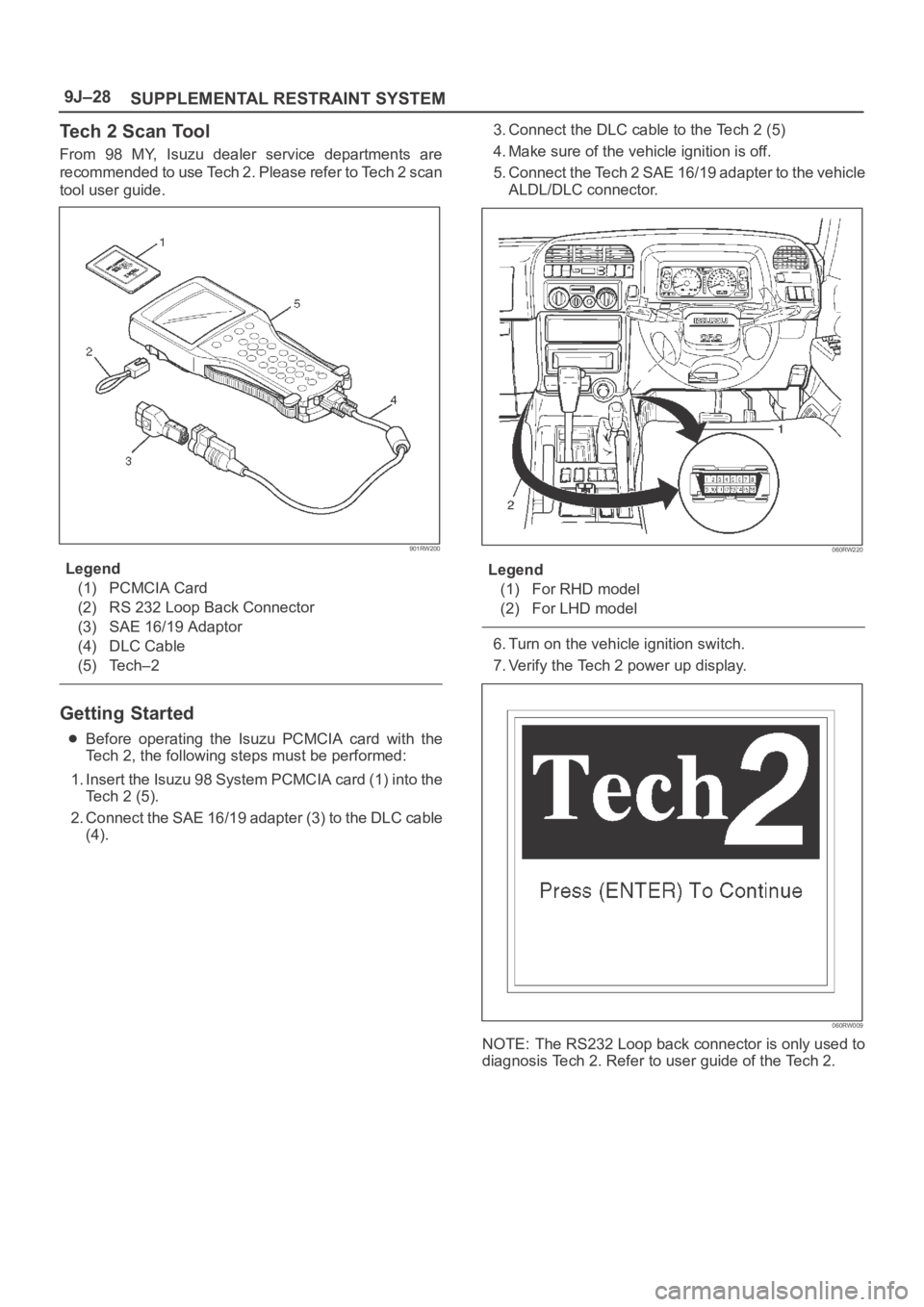
SUPPLEMENTAL RESTRAINT SYSTEM 9J–28
Tech 2 Scan Tool
From 98 MY, Isuzu dealer service departments are
recommended to use Tech 2. Please refer to Tech 2 scan
tool user guide.
901RW200
Legend
(1) PCMCIA Card
(2) RS 232 Loop Back Connector
(3) SAE 16/19 Adaptor
(4) DLC Cable
(5) Tech–2
Getting Started
Before operating the Isuzu PCMCIA card with the
Tech 2, the following steps must be performed:
1. Insert the Isuzu 98 System PCMCIA card (1) into the
Tech 2 (5).
2. Connect the SAE 16/19 adapter (3) to the DLC cable
(4).3. Connect the DLC cable to the Tech 2 (5)
4. Make sure of the vehicle ignition is off.
5. Connect the Tech 2 SAE 16/19 adapter to the vehicle
ALDL/DLC connector.
060RW220
Legend
(1) For RHD model
(2) For LHD model
6. Turn on the vehicle ignition switch.
7. Verify the Tech 2 power up display.
060RW009
NOTE: The RS232 Loop back connector is only used to
diagnosis Tech 2. Refer to user guide of the Tech 2.
Page 3467 of 6000
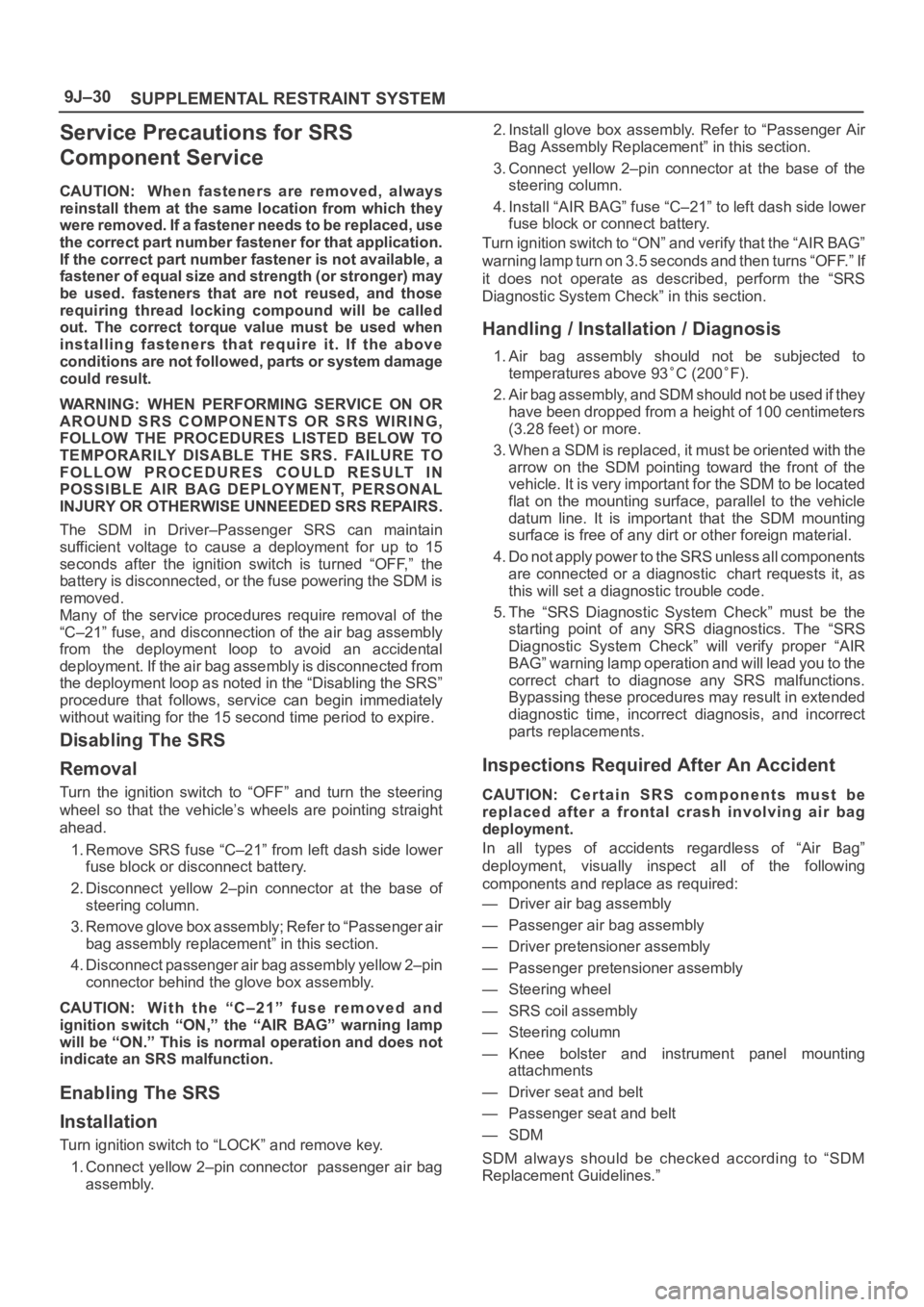
SUPPLEMENTAL RESTRAINT SYSTEM 9J–30
Service Precautions for SRS
Component Service
CAUTION: When fasteners are removed, always
reinstall them at the same location from which they
were removed. If a fastener needs to be replaced, use
the correct part number fastener for that application.
If the correct part number fastener is not available, a
fastener of equal size and strength (or stronger) may
be used. fasteners that are not reused, and those
requiring thread locking compound will be called
out. The correct torque value must be used when
installing fasteners that require it. If the above
conditions are not followed, parts or system damage
could result.
WARNING: WHEN PERFORMING SERVICE ON OR
AROUND SRS COMPONENTS OR SRS WIRING,
FOLLOW THE PROCEDURES LISTED BELOW TO
TEMPORARILY DISABLE THE SRS. FAILURE TO
FOLLOW PROCEDURES COULD RESULT IN
POSSIBLE AIR BAG DEPLOYMENT, PERSONAL
INJURY OR OTHERWISE UNNEEDED SRS REPAIRS.
The SDM in Driver–Passenger SRS can maintain
sufficient voltage to cause a deployment for up to 15
seconds after the ignition switch is turned “OFF,” the
battery is disconnected, or the fuse powering the SDM is
removed.
Many of the service procedures require removal of the
“C–21” fuse, and disconnection of the air bag assembly
from the deployment loop to avoid an accidental
deployment. If the air bag assembly is disconnected from
the deployment loop as noted in the “Disabling the SRS”
procedure that follows, service can begin immediately
without waiting for the 15 second time period to expire.
Disabling The SRS
Removal
Turn the ignition switch to “OFF” and turn the steering
wheel so that the vehicle’s wheels are pointing straight
ahead.
1. Remove SRS fuse “C–21” from left dash side lower
fuse block or disconnect battery.
2. Disconnect yellow 2–pin connector at the base of
steering column.
3 . R e m o v e g l o v e b o x a s s e m b l y ; R e f e r t o “ P a s s e n g e r a i r
bag assembly replacement” in this section.
4. Disconnect passenger air bag assembly yellow 2–pin
connector behind the glove box assembly.
CAUTION: W i t h t h e “ C – 2 1 ” f u s e r e m o v e d a n d
ignition switch “ON,” the “AIR BAG” warning lamp
will be “ON.” This is normal operation and does not
indicate an SRS malfunction.
Enabling The SRS
Installation
Turn ignition switch to “LOCK” and remove key.
1. Connect yellow 2–pin connector passenger air bag
assembly.2. Install glove box assembly. Refer to “Passenger Air
Bag Assembly Replacement” in this section.
3. Connect yellow 2–pin connector at the base of the
steering column.
4. Install “AIR BAG” fuse “C–21” to left dash side lower
fuse block or connect battery.
Turn ignition switch to “ON” and verify that the “AIR BAG”
warning lamp turn on 3.5 seconds and then turns “OFF.” If
it does not operate as described, perform the “SRS
Diagnostic System Check” in this section.
Handling / Installation / Diagnosis
1. Air bag assembly should not be subjected to
temperatures above 93
C (200F).
2. Air bag assembly, and SDM should not be used if they
have been dropped from a height of 100 centimeters
(3.28 feet) or more.
3. When a SDM is replaced, it must be oriented with the
arrow on the SDM pointing toward the front of the
vehicle. It is very important for the SDM to be located
flat on the mounting surface, parallel to the vehicle
datum line. It is important that the SDM mounting
surface is free of any dirt or other foreign material.
4. Do not apply power to the SRS unless all components
are connected or a diagnostic chart requests it, as
this will set a diagnostic trouble code.
5. The “SRS Diagnostic System Check” must be the
starting point of any SRS diagnostics. The “SRS
Diagnostic System Check” will verify proper “AIR
BAG” warning lamp operation and will lead you to the
correct chart to diagnose any SRS malfunctions.
Bypassing these procedures may result in extended
diagnostic time, incorrect diagnosis, and incorrect
parts replacements.
Inspections Required After An Accident
CAUTION: C e r t a i n S R S c o m p o n e n t s m u s t b e
replaced after a frontal crash involving air bag
deployment.
In all types of accidents regardless of “Air Bag”
deployment, visually inspect all of the following
components and replace as required:
— Driver air bag assembly
— Passenger air bag assembly
— Driver pretensioner assembly
— Passenger pretensioner assembly
— Steering wheel
— SRS coil assembly
— Steering column
— Knee bolster and instrument panel mounting
attachments
— Driver seat and belt
— Passenger seat and belt
—SDM
SDM always should be checked according to “SDM
Replacement Guidelines.”
Page 3486 of 6000
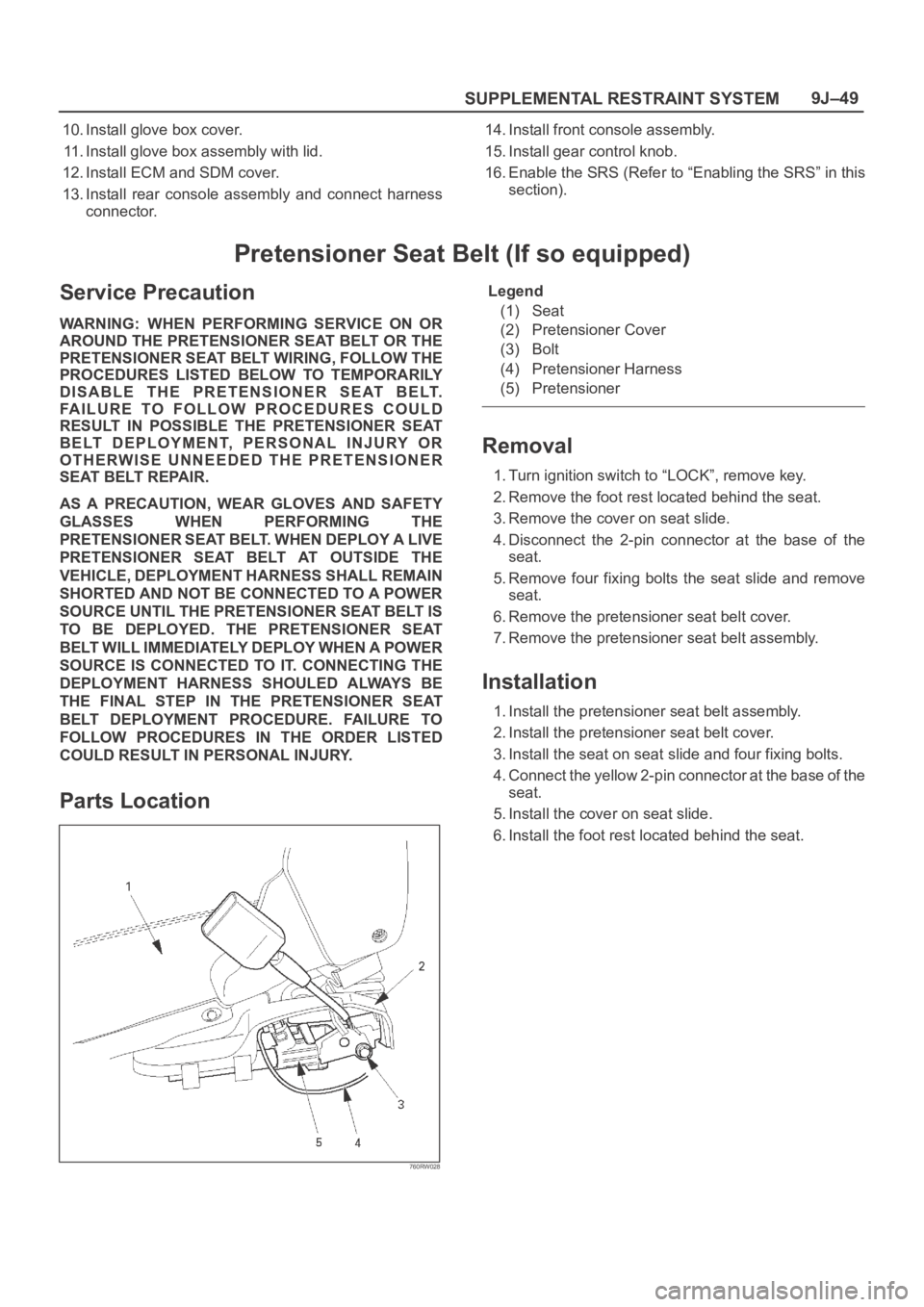
SUPPLEMENTAL RESTRAINT SYSTEM9J–49
10. Install glove box cover.
11. Install glove box assembly with lid.
12. Install ECM and SDM cover.
13. Install rear console assembly and connect harness
connector.14. Install front console assembly.
15. Install gear control knob.
16. Enable the SRS (Refer to “Enabling the SRS” in this
section).
Pretensioner Seat Belt (If so equipped)
Service Precaution
WARNING: WHEN PERFORMING SERVICE ON OR
AROUND THE PRETENSIONER SEAT BELT OR THE
PRETENSIONER SEAT BELT WIRING, FOLLOW THE
PROCEDURES LISTED BELOW TO TEMPORARILY
DISABLE THE PRETENSIONER SEAT BELT.
FAILURE TO FOLLOW PROCEDURES COULD
RESULT IN POSSIBLE THE PRETENSIONER SEAT
BELT DEPLOYMENT, PERSONAL INJURY OR
OTHERWISE UNNEEDED THE PRETENSIONER
SEAT BELT REPAIR.
AS A PRECAUTION, WEAR GLOVES AND SAFETY
GLASSES WHEN PERFORMING THE
PRETENSIONER SEAT BELT. WHEN DEPLOY A LIVE
PRETENSIONER SEAT BELT AT OUTSIDE THE
VEHICLE, DEPLOYMENT HARNESS SHALL REMAIN
SHORTED AND NOT BE CONNECTED TO A POWER
SOURCE UNTIL THE PRETENSIONER SEAT BELT IS
TO BE DEPLOYED. THE PRETENSIONER SEAT
BELT WILL IMMEDIATELY DEPLOY WHEN A POWER
SOURCE IS CONNECTED TO IT. CONNECTING THE
DEPLOYMENT HARNESS SHOULED ALWAYS BE
THE FINAL STEP IN THE PRETENSIONER SEAT
BELT DEPLOYMENT PROCEDURE. FAILURE TO
FOLLOW PROCEDURES IN THE ORDER LISTED
COULD RESULT IN PERSONAL INJURY.
Parts Location
760RW028
Legend
(1) Seat
(2) Pretensioner Cover
(3) Bolt
(4) Pretensioner Harness
(5) Pretensioner
Removal
1. Turn ignition switch to “LOCK”, remove key.
2. Remove the foot rest located behind the seat.
3. Remove the cover on seat slide.
4. Disconnect the 2-pin connector at the base of the
seat.
5. Remove four fixing bolts the seat slide and remove
seat.
6. Remove the pretensioner seat belt cover.
7. Remove the pretensioner seat belt assembly.
Installation
1. Install the pretensioner seat belt assembly.
2. Install the pretensioner seat belt cover.
3. Install the seat on seat slide and four fixing bolts.
4. Connect the yellow 2-pin connector at the base of the
seat.
5. Install the cover on seat slide.
6. Install the foot rest located behind the seat.
Page 3489 of 6000
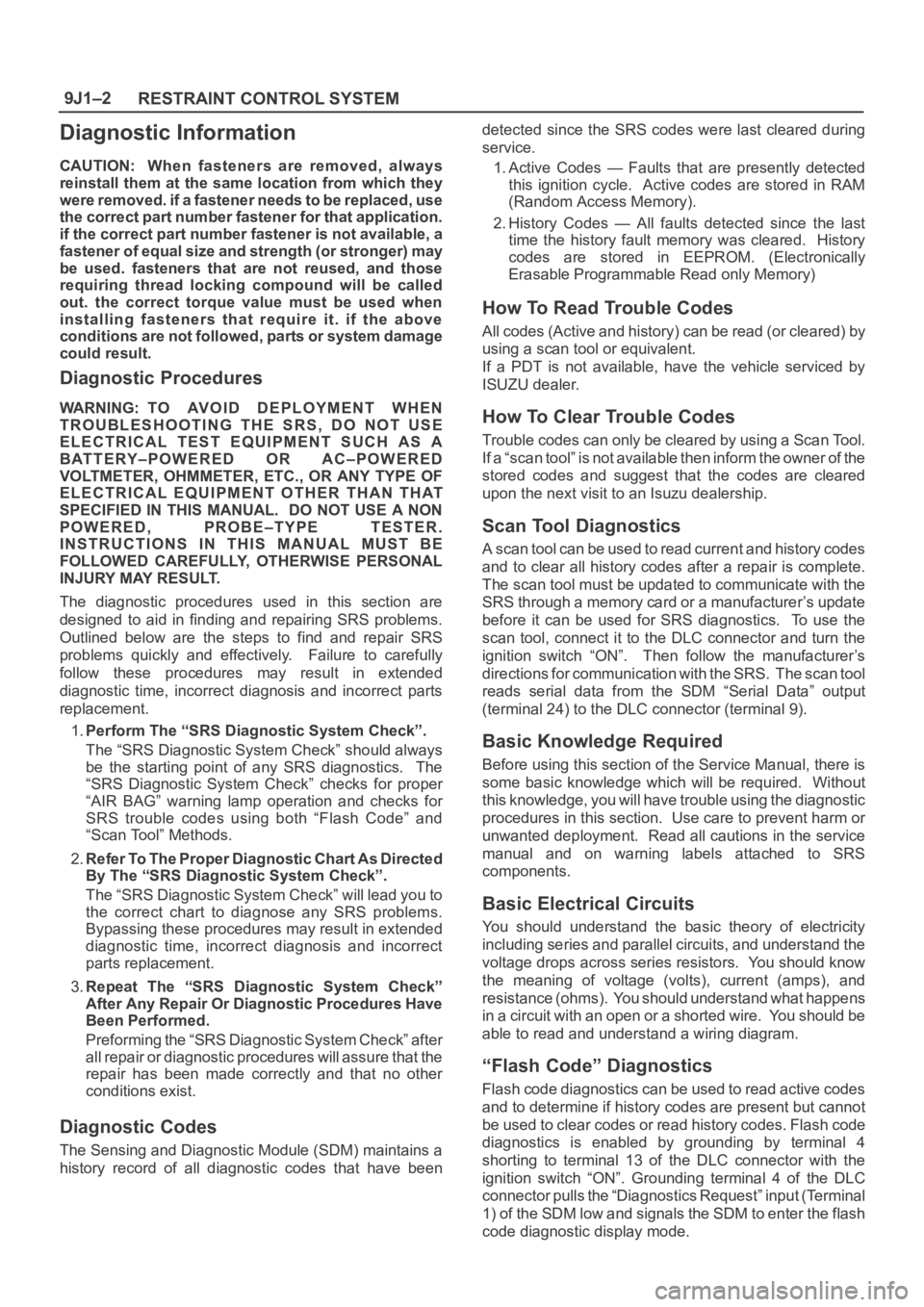
RESTRAINT CONTROL SYSTEM 9J1–2
Diagnostic Information
CAUTION: When fasteners are removed, always
reinstall them at the same location from which they
were removed. if a fastener needs to be replaced, use
the correct part number fastener for that application.
if the correct part number fastener is not available, a
fastener of equal size and strength (or stronger) may
be used. fasteners that are not reused, and those
requiring thread locking compound will be called
out. the correct torque value must be used when
installing fasteners that require it. if the above
conditions are not followed, parts or system damage
could result.
Diagnostic Procedures
WARNING: TO AVOID DEPLOYMENT WHEN
TROUBLESHOOTING THE SRS, DO NOT USE
ELECTRICAL TEST EQUIPMENT SUCH AS A
BATTERY–POWERED OR AC–POWERED
VOLTMETER, OHMMETER, ETC., OR ANY TYPE OF
ELECTRICAL EQUIPMENT OTHER THAN THAT
SPECIFIED IN THIS MANUAL. DO NOT USE A NON
POWERED, PROBE–TYPE TESTER.
INSTRUCTIONS IN THIS MANUAL MUST BE
FOLLOWED CAREFULLY, OTHERWISE PERSONAL
INJURY MAY RESULT.
The diagnostic procedures used in this section are
designed to aid in finding and repairing SRS problems.
Outlined below are the steps to find and repair SRS
problems quickly and effectively. Failure to carefully
follow these procedures may result in extended
diagnostic time, incorrect diagnosis and incorrect parts
replacement.
1.Perform The “SRS Diagnostic System Check”.
The “SRS Diagnostic System Check” should always
be the starting point of any SRS diagnostics. The
“SRS Diagnostic System Check” checks for proper
“AIR BAG” warning lamp operation and checks for
SRS trouble codes using both “Flash Code” and
“Scan Tool” Methods.
2.Refer To The Proper Diagnostic Chart As Directed
By The “SRS Diagnostic System Check”.
The “SRS Diagnostic System Check” will lead you to
the correct chart to diagnose any SRS problems.
Bypassing these procedures may result in extended
diagnostic time, incorrect diagnosis and incorrect
parts replacement.
3.Repeat The “SRS Diagnostic System Check”
After Any Repair Or Diagnostic Procedures Have
Been Performed.
Preforming the “SRS Diagnostic System Check” after
all repair or diagnostic procedures will assure that the
repair has been made correctly and that no other
conditions exist.
Diagnostic Codes
The Sensing and Diagnostic Module (SDM) maintains a
history record of all diagnostic codes that have beendetected since the SRS codes were last cleared during
service.
1. Active Codes — Faults that are presently detected
this ignition cycle. Active codes are stored in RAM
(Random Access Memory).
2. History Codes — All faults detected since the last
time the history fault memory was cleared. History
codes are stored in EEPROM. (Electronically
Erasable Programmable Read only Memory)
How To Read Trouble Codes
All codes (Active and history) can be read (or cleared) by
using a scan tool or equivalent.
If a PDT is not available, have the vehicle serviced by
ISUZU dealer.
How To Clear Trouble Codes
Trouble codes can only be cleared by using a Scan Tool.
If a “scan tool” is not available then inform the owner of the
stored codes and suggest that the codes are cleared
upon the next visit to an Isuzu dealership.
Scan Tool Diagnostics
A scan tool can be used to read current and history codes
and to clear all history codes after a repair is complete.
The scan tool must be updated to communicate with the
SRS through a memory card or a manufacturer’s update
before it can be used for SRS diagnostics. To use the
scan tool, connect it to the DLC connector and turn the
ignition switch “ON”. Then follow the manufacturer’s
directions for communication with the SRS. The scan tool
reads serial data from the SDM “Serial Data” output
(terminal 24) to the DLC connector (terminal 9).
Basic Knowledge Required
Before using this section of the Service Manual, there is
some basic knowledge which will be required. Without
this knowledge, you will have trouble using the diagnostic
procedures in this section. Use care to prevent harm or
unwanted deployment. Read all cautions in the service
manual and on warning labels attached to SRS
components.
Basic Electrical Circuits
You should understand the basic theory of electricity
including series and parallel circuits, and understand the
voltage drops across series resistors. You should know
the meaning of voltage (volts), current (amps), and
resistance (ohms). You should understand what happens
in a circuit with an open or a shorted wire. You should be
able to read and understand a wiring diagram.
“Flash Code” Diagnostics
Flash code diagnostics can be used to read active codes
and to determine if history codes are present but cannot
be used to clear codes or read history codes. Flash code
diagnostics is enabled by grounding by terminal 4
shorting to terminal 13 of the DLC connector with the
ignition switch “ON”. Grounding terminal 4 of the DLC
connector pulls the “Diagnostics Request” input (Terminal
1) of the SDM low and signals the SDM to enter the flash
code diagnostic display mode.
Page 3491 of 6000
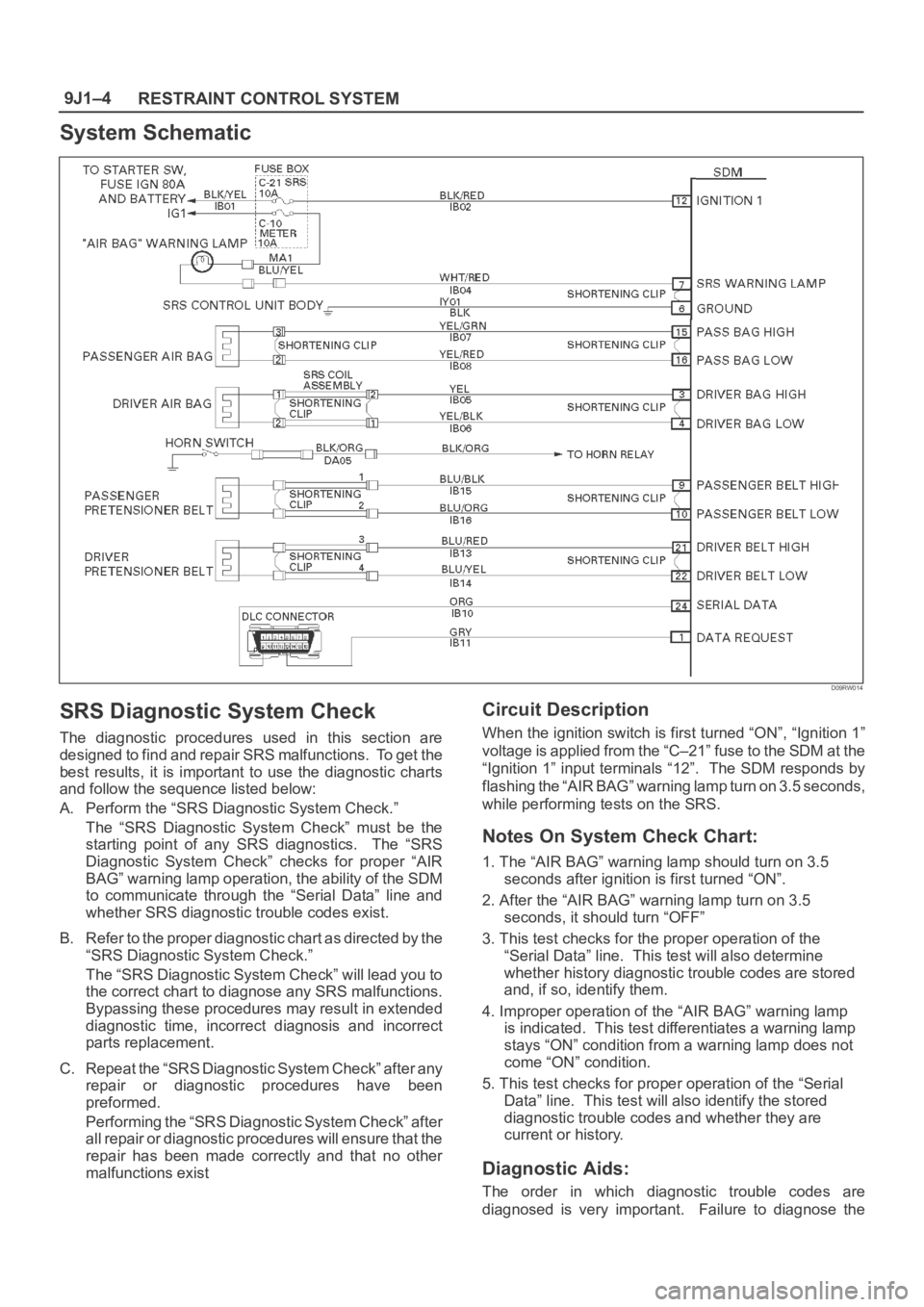
RESTRAINT CONTROL SYSTEM 9J1–4
System Schematic
D09RW014
SRS Diagnostic System Check
The diagnostic procedures used in this section are
designed to find and repair SRS malfunctions. To get the
best results, it is important to use the diagnostic charts
and follow the sequence listed below:
A. Perform the “SRS Diagnostic System Check.”
The “SRS Diagnostic System Check” must be the
starting point of any SRS diagnostics. The “SRS
Diagnostic System Check” checks for proper “AIR
BAG” warning lamp operation, the ability of the SDM
to communicate through the “Serial Data” line and
whether SRS diagnostic trouble codes exist.
B. Refer to the proper diagnostic chart as directed by the
“SRS Diagnostic System Check.”
The “SRS Diagnostic System Check” will lead you to
the correct chart to diagnose any SRS malfunctions.
Bypassing these procedures may result in extended
diagnostic time, incorrect diagnosis and incorrect
parts replacement.
C. Repeat the “SRS Diagnostic System Check” after any
repair or diagnostic procedures have been
preformed.
Performing the “SRS Diagnostic System Check” after
all repair or diagnostic procedures will ensure that the
repair has been made correctly and that no other
malfunctions exist
Circuit Description
When the ignition switch is first turned “ON”, “Ignition 1”
voltage is applied from the “C–21” fuse to the SDM at the
“Ignition 1” input terminals “12”. The SDM responds by
flashing the “AIR BAG” warning lamp turn on 3.5 seconds,
while performing tests on the SRS.
Notes On System Check Chart:
1. The “AIR BAG” warning lamp should turn on 3.5
seconds after ignition is first turned “ON”.
2. After the “AIR BAG” warning lamp turn on 3.5
seconds, it should turn “OFF”
3. This test checks for the proper operation of the
“Serial Data” line. This test will also determine
whether history diagnostic trouble codes are stored
and, if so, identify them.
4. Improper operation of the “AIR BAG” warning lamp
is indicated. This test differentiates a warning lamp
stays “ON” condition from a warning lamp does not
come “ON” condition.
5. This test checks for proper operation of the “Serial
Data” line. This test will also identify the stored
diagnostic trouble codes and whether they are
current or history.
Diagnostic Aids:
The order in which diagnostic trouble codes are
diagnosed is very important. Failure to diagnose the
Page 3492 of 6000
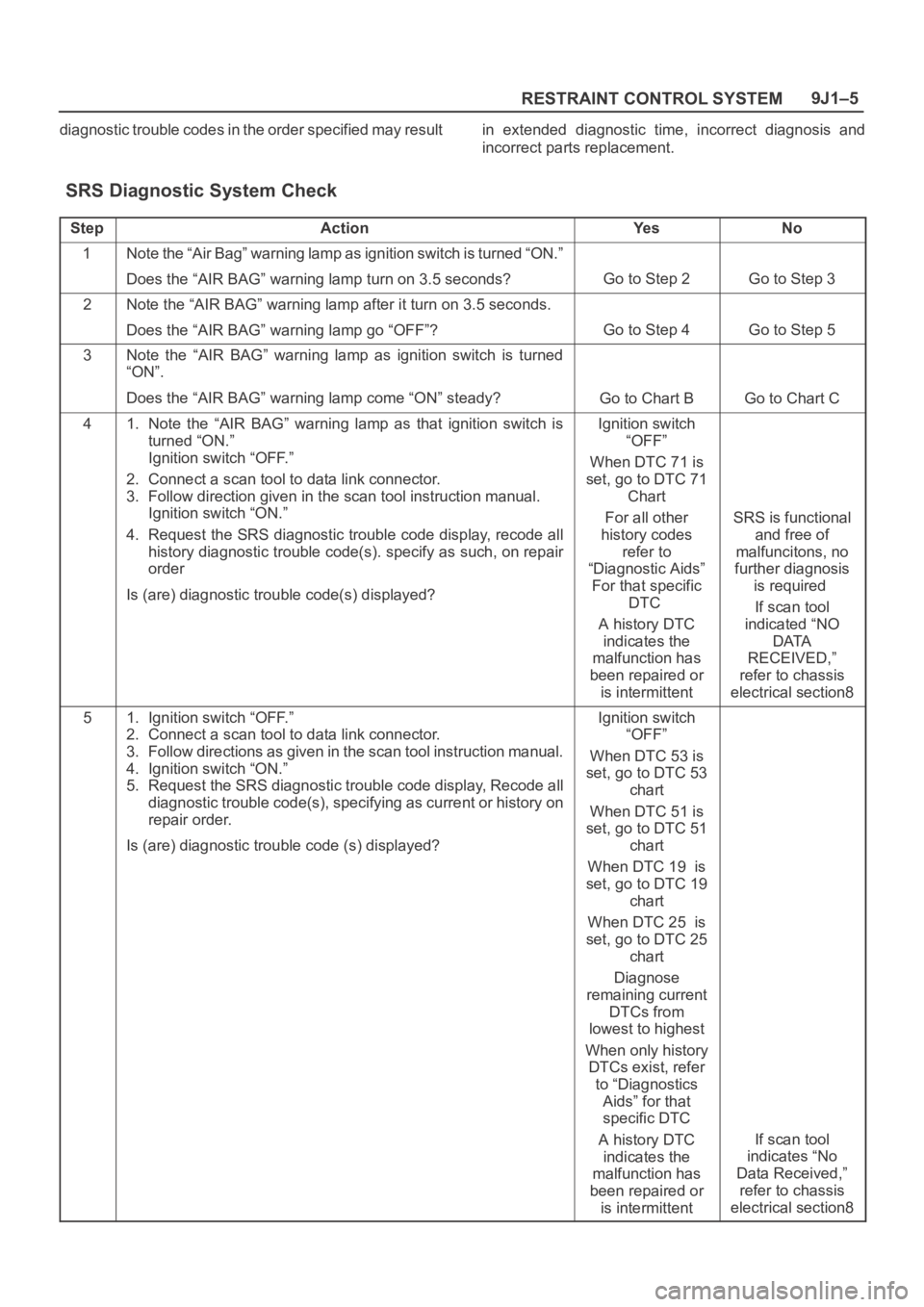
9J1–5
RESTRAINT CONTROL SYSTEM
diagnostic trouble codes in the order specified may result in extended diagnostic time, incorrect diagnosis and
incorrect parts replacement.
SRS Diagnostic System Check
StepActionYe sNo
1Note the “Air Bag” warning lamp as ignition switch is turned “ON.”
Does the “AIR BAG” warning lamp turn on 3.5 seconds?
Go to Step 2Go to Step 3
2Note the “AIR BAG” warning lamp after it turn on 3.5 seconds.
Does the “AIR BAG” warning lamp go “OFF”?
Go to Step 4Go to Step 5
3Note the “AIR BAG” warning lamp as ignition switch is turned
“ON”.
Does the “AIR BAG” warning lamp come “ON” steady?
Go to Chart BGo to Chart C
41. Note the “AIR BAG” warning lamp as that ignition switch is
turned “ON.”
Ignition switch “OFF.”
2. Connect a scan tool to data link connector.
3. Follow direction given in the scan tool instruction manual.
Ignition switch “ON.”
4. Request the SRS diagnostic trouble code display, recode all
history diagnostic trouble code(s). specify as such, on repair
order
Is (are) diagnostic trouble code(s) displayed?Ignition switch
“OFF”
When DTC 71 is
set, go to DTC 71
Chart
For all other
history codes
refer to
“Diagnostic Aids”
For that specific
DTC
A history DTC
indicates the
malfunction has
been repaired or
is intermittent
SRS is functional
and free of
malfuncitons, no
further diagnosis
is required
If scan tool
indicated “NO
DATA
RECEIVED,”
refer to chassis
electrical section8
51. Ignition switch “OFF.”
2. Connect a scan tool to data link connector.
3. Follow directions as given in the scan tool instruction manual.
4. Ignition switch “ON.”
5. Request the SRS diagnostic trouble code display, Recode all
diagnostic trouble code(s), specifying as current or history on
repair order.
Is (are) diagnostic trouble code (s) displayed?Ignition switch
“OFF”
When DTC 53 is
set, go to DTC 53
chart
When DTC 51 is
set, go to DTC 51
chart
When DTC 19 is
set, go to DTC 19
chart
When DTC 25 is
set, go to DTC 25
chart
Diagnose
remaining current
DTCs from
lowest to highest
When only history
DTCs exist, refer
to “Diagnostics
Aids” for that
specific DTC
A history DTC
indicates the
malfunction has
been repaired or
is intermittent
If scan tool
indicates “No
Data Received,”
refer to chassis
electrical section8
Page 3493 of 6000
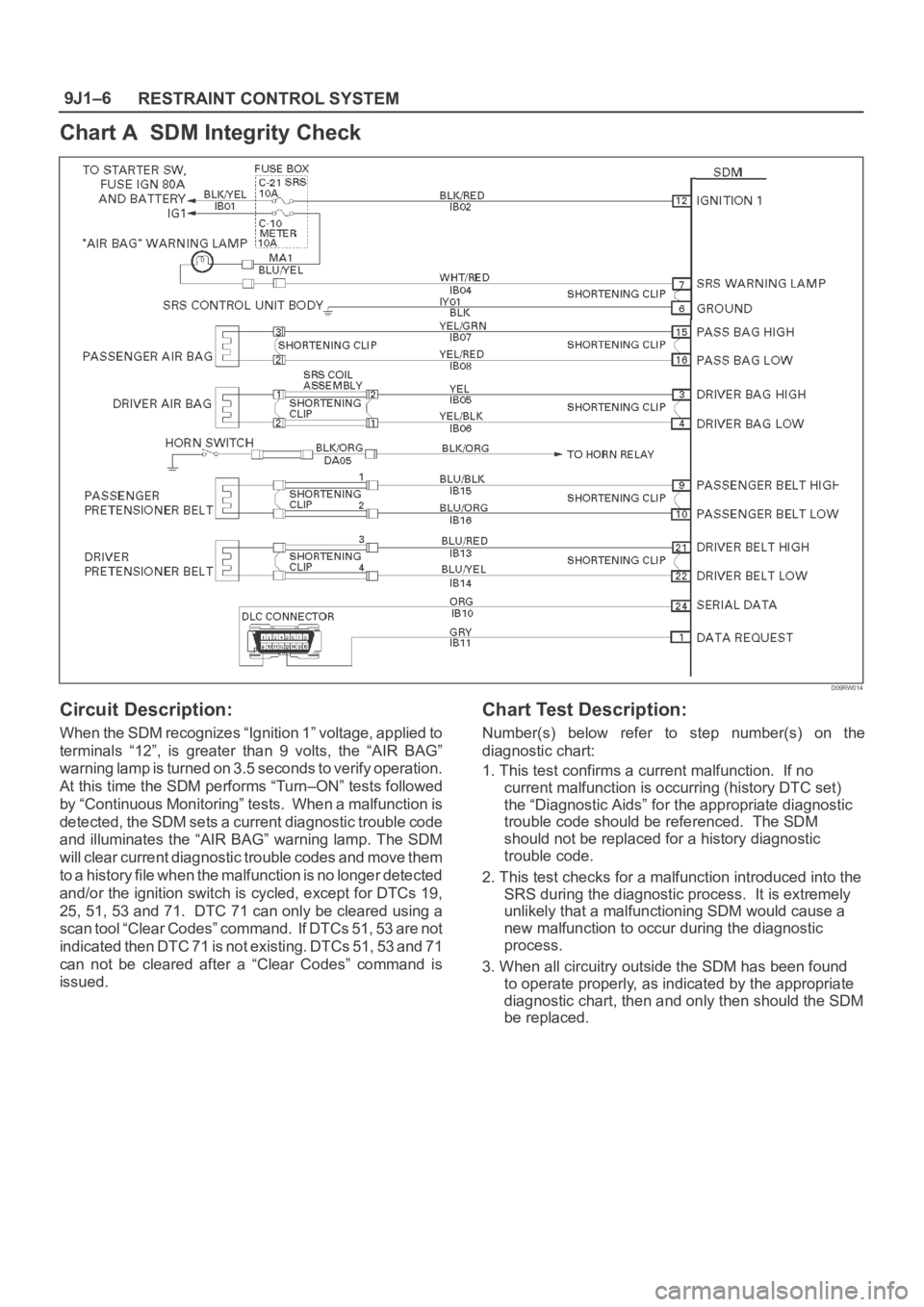
RESTRAINT CONTROL SYSTEM 9J1–6
Chart A SDM Integrity Check
D09RW014
Circuit Description:
When the SDM recognizes “Ignition 1” voltage, applied to
terminals “12”, is greater than 9 volts, the “AIR BAG”
warning lamp is turned on 3.5 seconds to verify operation.
At this time the SDM performs “Turn–ON” tests followed
by “Continuous Monitoring” tests. When a malfunction is
detected, the SDM sets a current diagnostic trouble code
and illuminates the “AIR BAG” warning lamp. The SDM
will clear current diagnostic trouble codes and move them
to a history file when the malfunction is no longer detected
and/or the ignition switch is cycled, except for DTCs 19,
25, 51, 53 and 71. DTC 71 can only be cleared using a
scan tool “Clear Codes” command. If DTCs 51, 53 are not
indicated then DTC 71 is not existing. DTCs 51, 53 and 71
can not be cleared after a “Clear Codes” command is
issued.
Chart Test Description:
Number(s) below refer to step number(s) on the
diagnostic chart:
1. This test confirms a current malfunction. If no
current malfunction is occurring (history DTC set)
the “Diagnostic Aids” for the appropriate diagnostic
trouble code should be referenced. The SDM
should not be replaced for a history diagnostic
trouble code.
2. This test checks for a malfunction introduced into the
SRS during the diagnostic process. It is extremely
unlikely that a malfunctioning SDM would cause a
new malfunction to occur during the diagnostic
process.
3. When all circuitry outside the SDM has been found
to operate properly, as indicated by the appropriate
diagnostic chart, then and only then should the SDM
be replaced.
Page 3494 of 6000
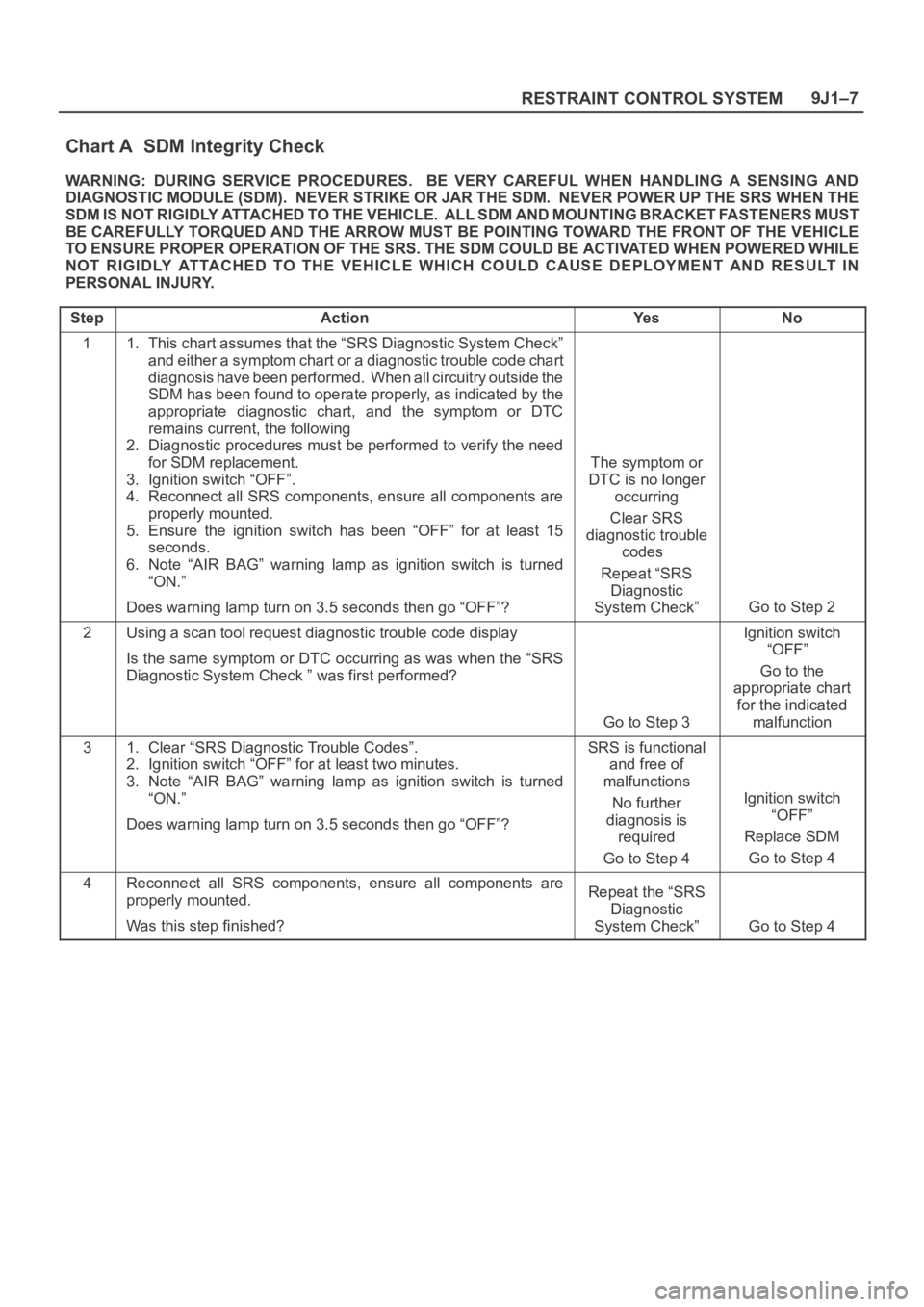
9J1–7
RESTRAINT CONTROL SYSTEM
Chart A SDM Integrity Check
WARNING: DURING SERVICE PROCEDURES. BE VERY CAREFUL WHEN HANDLING A SENSING AND
DIAGNOSTIC MODULE (SDM). NEVER STRIKE OR JAR THE SDM. NEVER POWER UP THE SRS WHEN THE
S D M I S N O T R I G I D LY AT TA C H E D T O T H E V E H I C L E . A L L S D M A N D M O U N T ING BRACKET FASTENERS MUST
BE CAREFULLY TORQUED AND THE ARROW MUST BE POINTING TOWARD THE FRONT OF THE VEHICLE
TO ENSURE PROPER OPERATION OF THE SRS. THE SDM COULD BE ACTIVATED WHEN POWERED WHILE
NOT RIGIDLY ATTACHED TO THE VEHICLE WHICH COULD CAUSE DEPLOYMENT AND RESULT IN
PERSONAL INJURY.
Step
ActionYe sNo
11. This chart assumes that the “SRS Diagnostic System Check”
and either a symptom chart or a diagnostic trouble code chart
diagnosis have been performed. When all circuitry outside the
SDM has been found to operate properly, as indicated by the
appropriate diagnostic chart, and the symptom or DTC
remains current, the following
2. Diagnostic procedures must be performed to verify the need
for SDM replacement.
3. Ignition switch “OFF”.
4. Reconnect all SRS components, ensure all components are
properly mounted.
5. Ensure the ignition switch has been “OFF” for at least 15
seconds.
6. Note “AIR BAG” warning lamp as ignition switch is turned
“ON.”
Does warning lamp turn on 3.5 seconds then go “OFF”?
The symptom or
DTC is no longer
occurring
Clear SRS
diagnostic trouble
codes
Repeat “SRS
Diagnostic
System Check”
Go to Step 2
2Using a scan tool request diagnostic trouble code display
Is the same symptom or DTC occurring as was when the “SRS
Diagnostic System Check ” was first performed?
Go to Step 3
Ignition switch
“OFF”
Go to the
appropriate chart
for the indicated
malfunction
31. Clear “SRS Diagnostic Trouble Codes”.
2. Ignition switch “OFF” for at least two minutes.
3. Note “AIR BAG” warning lamp as ignition switch is turned
“ON.”
Does warning lamp turn on 3.5 seconds then go “OFF”?SRS is functional
and free of
malfunctions
No further
diagnosis is
required
Go to Step 4
Ignition switch
“OFF”
Replace SDM
Go to Step 4
4Reconnect all SRS components, ensure all components are
properly mounted.
Was this step finished?Repeat the “SRS
Diagnostic
System Check”
Go to Step 4