check engine OPEL FRONTERA 1998 Workshop Manual
[x] Cancel search | Manufacturer: OPEL, Model Year: 1998, Model line: FRONTERA, Model: OPEL FRONTERA 1998Pages: 6000, PDF Size: 97 MB
Page 5348 of 6000
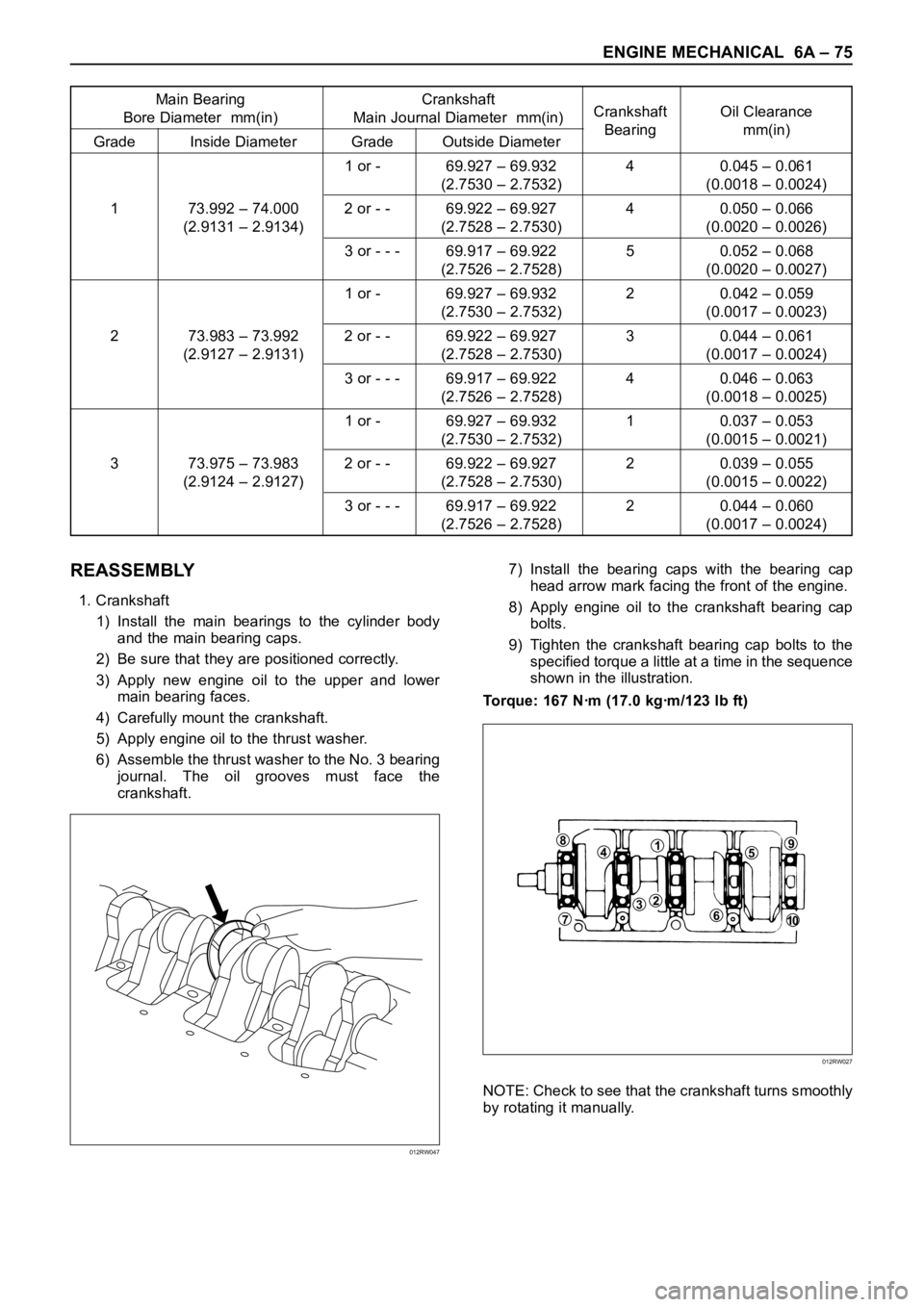
ENGINE MECHANICAL 6A – 75
Main Bearing Crankshaft
Bore Diameter mm(in) Main Journal Diameter mm(in)Crankshaft Oil Clearance
Grade Inside Diameter Grade Outside DiameterBearing mm(in)
1 or - 69.927 – 69.932 4 0.045 – 0.061
(2.7530 – 2.7532) (0.0018 – 0.0024)
1 73.992 – 74.000 2 or - - 69.922 – 69.927 4 0.050 – 0.066
(2.9131 – 2.9134) (2.7528 – 2.7530) (0.0020 – 0.0026)
3 or - - - 69.917 – 69.922 5 0.052 – 0.068
(2.7526 – 2.7528) (0.0020 – 0.0027)
1 or - 69.927 – 69.932 2 0.042 – 0.059
(2.7530 – 2.7532) (0.0017 – 0.0023)
2 73.983 – 73.992 2 or - - 69.922 – 69.927 3 0.044 – 0.061
(2.9127 – 2.9131) (2.7528 – 2.7530) (0.0017 – 0.0024)
3 or - - - 69.917 – 69.922 4 0.046 – 0.063
(2.7526 – 2.7528) (0.0018 – 0.0025)
1 or - 69.927 – 69.932 1 0.037 – 0.053
(2.7530 – 2.7532) (0.0015 – 0.0021)
3 73.975 – 73.983 2 or - - 69.922 – 69.927 2 0.039 – 0.055
(2.9124 – 2.9127) (2.7528 – 2.7530) (0.0015 – 0.0022)
3 or - - - 69.917 – 69.922 2 0.044 – 0.060
(2.7526 – 2.7528) (0.0017 – 0.0024)
REASSEMBLY
1. Crankshaft
1) Install the main bearings to the cylinder body
and the main bearing caps.
2) Be sure that they are positioned correctly.
3) Apply new engine oil to the upper and lower
main bearing faces.
4) Carefully mount the crankshaft.
5) Apply engine oil to the thrust washer.
6) Assemble the thrust washer to the No. 3 bearing
journal. The oil grooves must face the
crankshaft.7) Install the bearing caps with the bearing cap
head arrow mark facing the front of the engine.
8) Apply engine oil to the crankshaft bearing cap
bolts.
9) Tighten the crankshaft bearing cap bolts to the
specified torque a little at a time in the sequence
shown in the illustration.
Torque: 167 Nꞏm (17.0 kgꞏm/123 lb ft)
NOTE: Check to see that the crankshaft turns smoothly
by rotating it manually.
012RW047
84159
610
237
012RW027
Page 5349 of 6000
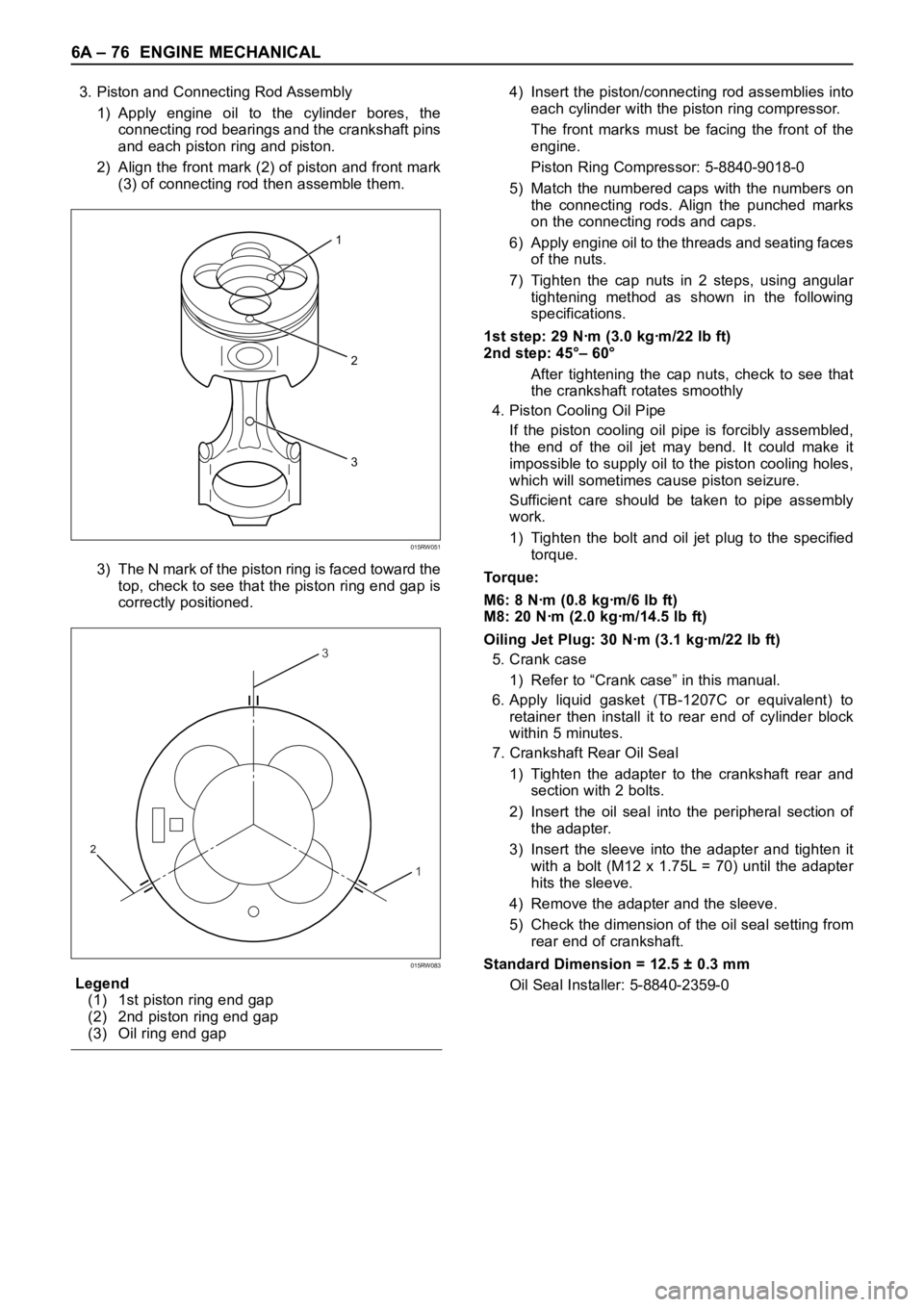
6A – 76 ENGINE MECHANICAL
3. Piston and Connecting Rod Assembly
1) Apply engine oil to the cylinder bores, the
connecting rod bearings and the crankshaft pins
and each piston ring and piston.
2) Align the front mark (2) of piston and front mark
(3) of connecting rod then assemble them.
3) The N mark of the piston ring is faced toward the
top, check to see that the piston ring end gap is
correctly positioned.
Legend
(1) 1st piston ring end gap
(2) 2nd piston ring end gap
(3) Oil ring end gap4) Insert the piston/connecting rod assemblies into
each cylinder with the piston ring compressor.
The front marks must be facing the front of the
engine.
Piston Ring Compressor: 5-8840-9018-0
5) Match the numbered caps with the numbers on
the connecting rods. Align the punched marks
on the connecting rods and caps.
6) Apply engine oil to the threads and seating faces
of the nuts.
7) Tighten the cap nuts in 2 steps, using angular
tightening method as shown in the following
specifications.
1st step: 29 Nꞏm (3.0 kgꞏm/22 lb ft)
2nd step: 45°– 60°
After tightening the cap nuts, check to see that
the crankshaft rotates smoothly
4. Piston Cooling Oil Pipe
If the piston cooling oil pipe is forcibly assembled,
the end of the oil jet may bend. It could make it
impossible to supply oil to the piston cooling holes,
which will sometimes cause piston seizure.
Sufficient care should be taken to pipe assembly
work.
1) Tighten the bolt and oil jet plug to the specified
torque.
To r q u e :
M6: 8 Nꞏm (0.8 kgꞏm/6 lb ft)
M8: 20 Nꞏm (2.0 kgꞏm/14.5 lb ft)
Oiling Jet Plug: 30 Nꞏm (3.1 kgꞏm/22 lb ft)
5. Crank case
1) Refer to “Crank case” in this manual.
6. Apply liquid gasket (TB-1207C or equivalent) to
retainer then install it to rear end of cylinder block
within 5 minutes.
7. Crankshaft Rear Oil Seal
1) Tighten the adapter to the crankshaft rear and
section with 2 bolts.
2) Insert the oil seal into the peripheral section of
the adapter.
3) Insert the sleeve into the adapter and tighten it
with a bolt (M12 x 1.75L = 70) until the adapter
hits the sleeve.
4) Remove the adapter and the sleeve.
5) Check the dimension of the oil seal setting from
rear end of crankshaft.
Standard Dimension = 12.5 ± 0.3 mm
Oil Seal Installer: 5-8840-2359-0
2
3
1
015RW051
3
1
2
015RW083
Page 5352 of 6000
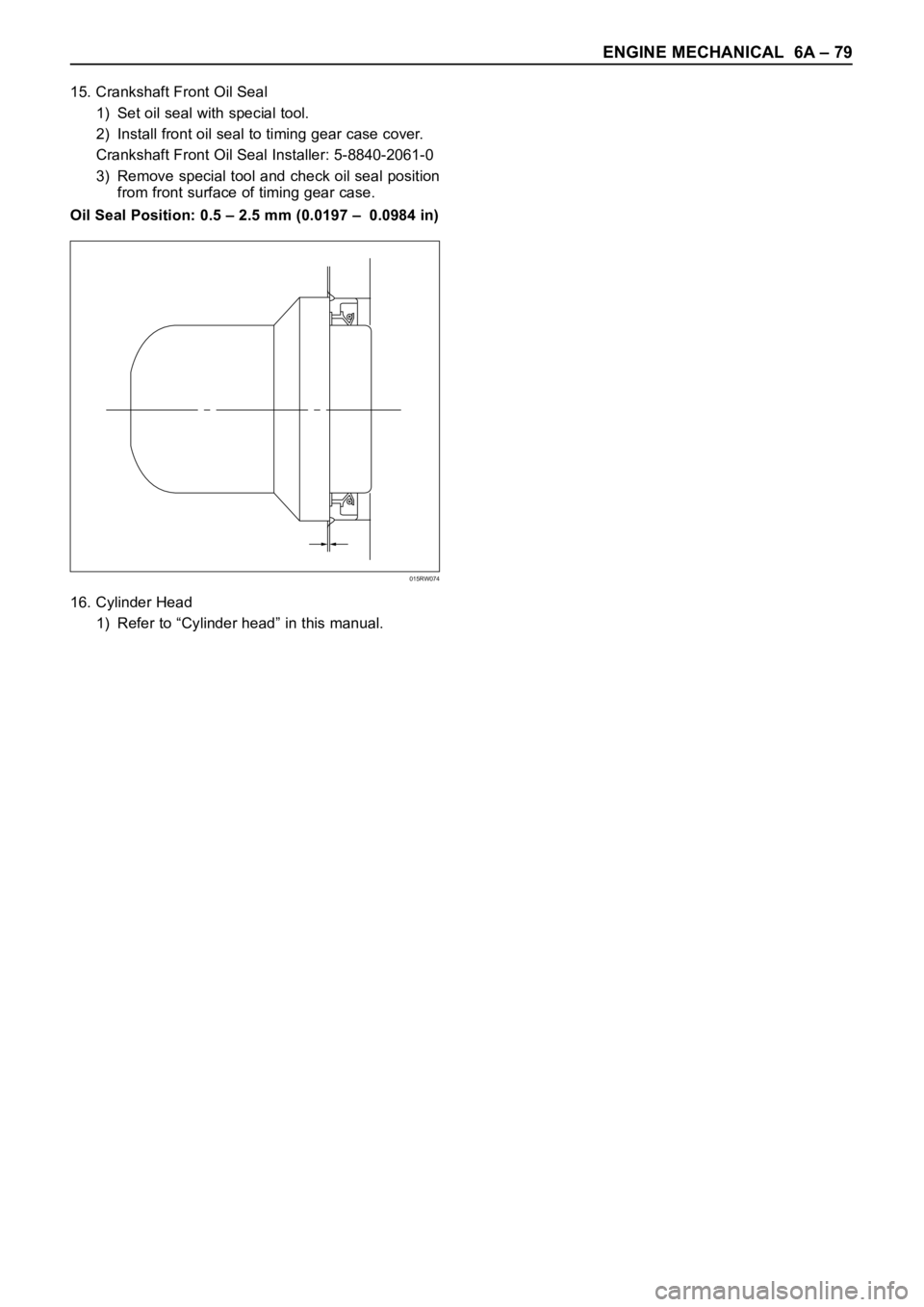
15. Crankshaft Front Oil Seal
1) Set oil seal with special tool.
2) Install front oil seal to timing gear case cover.
Crankshaft Front Oil Seal Installer: 5-8840-2061-0
3) Remove special tool and check oil seal position
from front surface of timing gear case.
Oil Seal Position: 0.5 – 2.5 mm (0.0197 – 0.0984 in)
16. Cylinder Head
1) Refer to “Cylinder head” in this manual.
ENGINE MECHANICAL 6A – 79
015RW074
Page 5354 of 6000
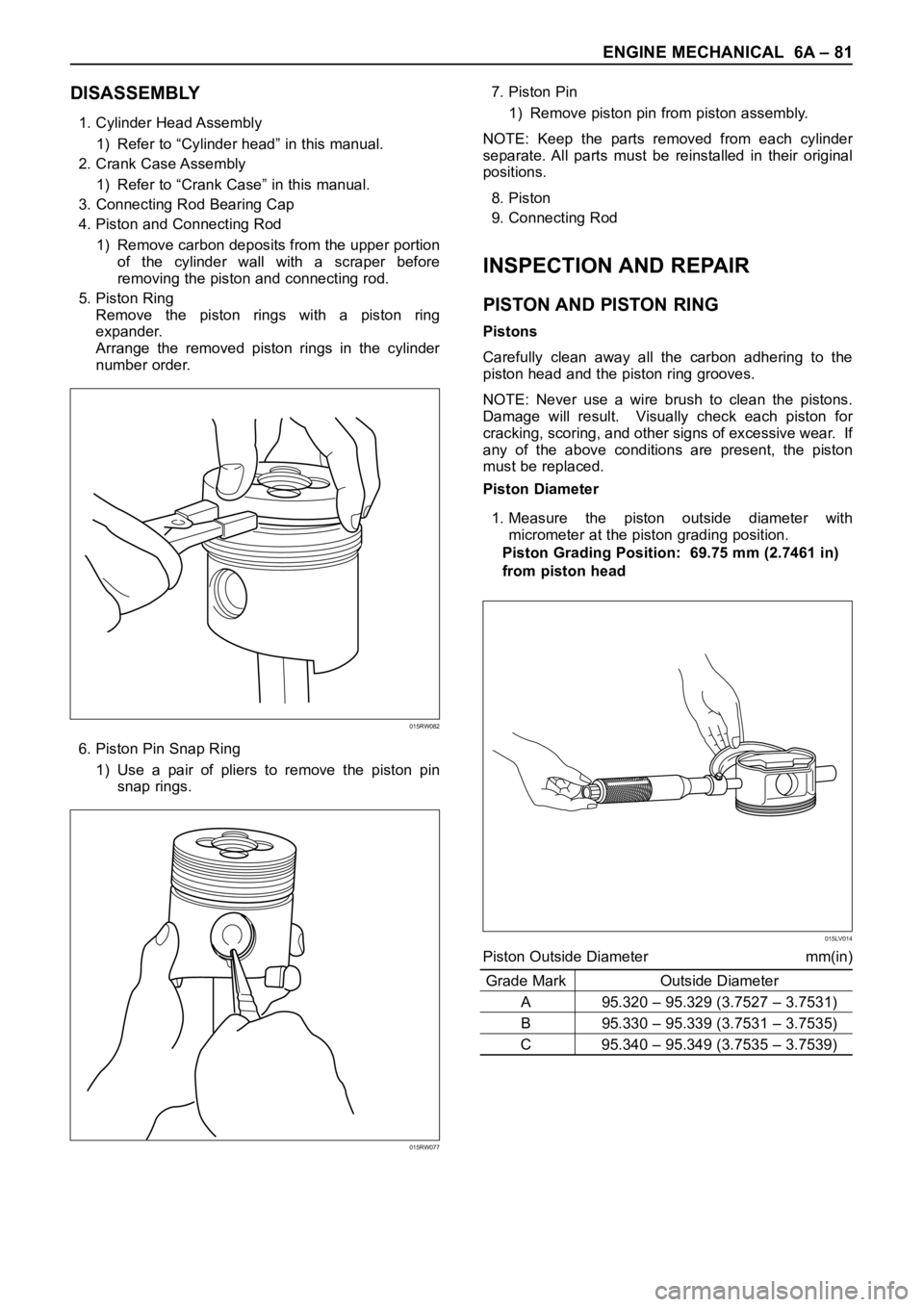
ENGINE MECHANICAL 6A – 81
DISASSEMBLY
1. Cylinder Head Assembly
1) Refer to “Cylinder head” in this manual.
2. Crank Case Assembly
1) Refer to “Crank Case” in this manual.
3. Connecting Rod Bearing Cap
4. Piston and Connecting Rod
1) Remove carbon deposits from the upper portion
of the cylinder wall with a scraper before
removing the piston and connecting rod.
5. Piston Ring
Remove the piston rings with a piston ring
expander.
Arrange the removed piston rings in the cylinder
number order.
6. Piston Pin Snap Ring
1) Use a pair of pliers to remove the piston pin
snap rings.7. Piston Pin
1) Remove piston pin from piston assembly.
NOTE: Keep the parts removed from each cylinder
separate. All parts must be reinstalled in their original
positions.
8. Piston
9. Connecting Rod
INSPECTION AND REPAIR
PISTON AND PISTON RING
Pistons
Carefully clean away all the carbon adhering to the
piston head and the piston ring grooves.
NOTE: Never use a wire brush to clean the pistons.
Damage will result. Visually check each piston for
cracking, scoring, and other signs of excessive wear. If
any of the above conditions are present, the piston
must be replaced.
Piston Diameter
1. Measure the piston outside diameter with
micrometer at the piston grading position.
Piston Grading Position: 69.75 mm (2.7461 in)
from piston head
Piston Outside Diameter mm(in)
Grade Mark Outside Diameter
A 95.320 – 95.329 (3.7527 – 3.7531)
B 95.330 – 95.339 (3.7531 – 3.7535)
C 95.340 – 95.349 (3.7535 – 3.7539)
015RW082
015RW077
015LV014
Page 5357 of 6000
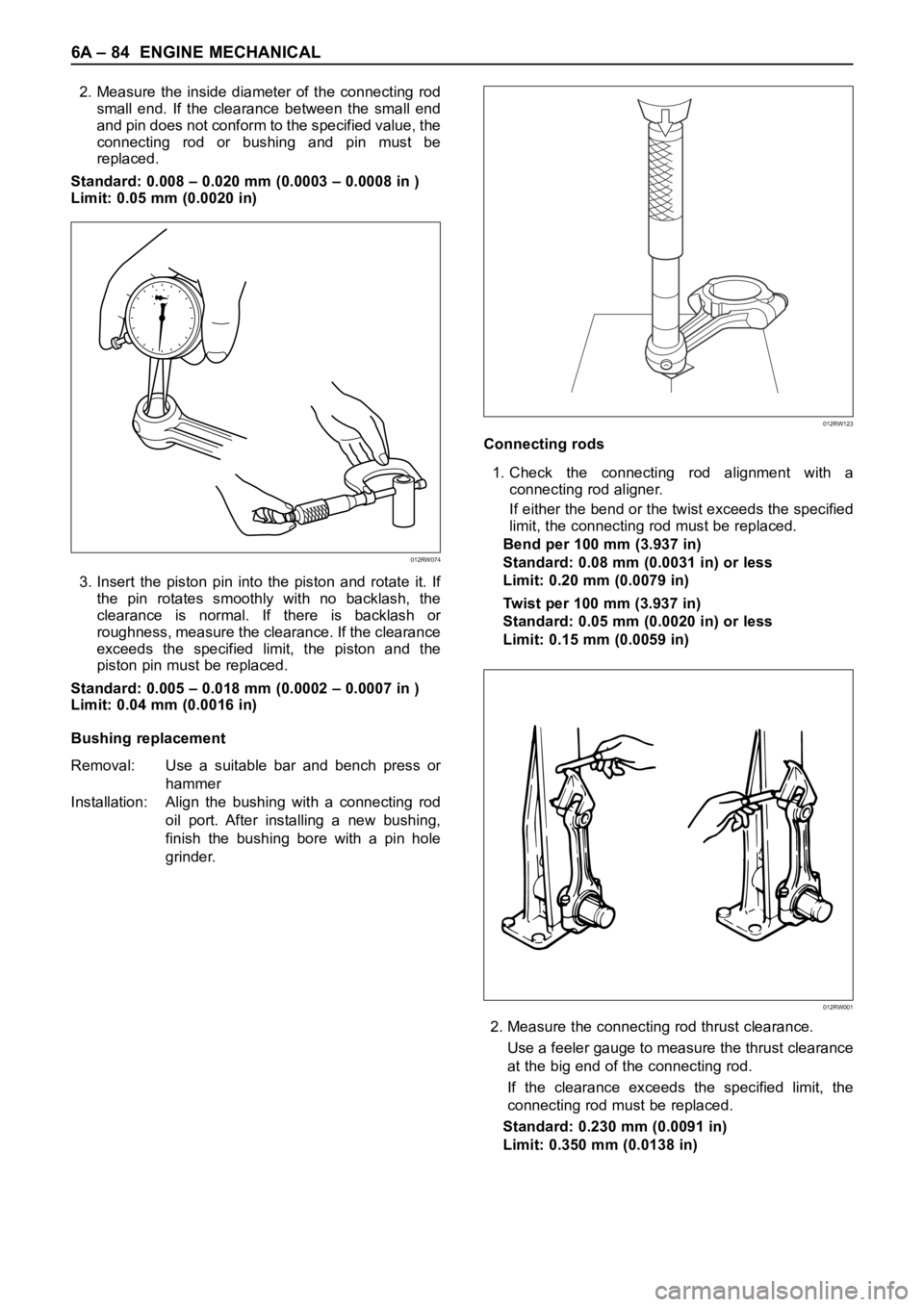
6A – 84 ENGINE MECHANICAL
2. Measure the inside diameter of the connecting rod
small end. If the clearance between the small end
and pin does not conform to the specified value, the
connecting rod or bushing and pin must be
replaced.
Standard: 0.008 – 0.020 mm (0.0003 – 0.0008 in )
Limit: 0.05 mm (0.0020 in)
3. Insert the piston pin into the piston and rotate it. If
the pin rotates smoothly with no backlash, the
clearance is normal. If there is backlash or
roughness, measure the clearance. If the clearance
exceeds the specified limit, the piston and the
piston pin must be replaced.
Standard: 0.005 – 0.018 mm (0.0002 – 0.0007 in )
Limit: 0.04 mm (0.0016 in)
Bushing replacement
Removal: Use a suitable bar and bench press or
hammer
Installation: Align the bushing with a connecting rod
oil port. After installing a new bushing,
finish the bushing bore with a pin hole
grinder.Connecting rods
1. Check the connecting rod alignment with a
connecting rod aligner.
If either the bend or the twist exceeds the specified
limit, the connecting rod must be replaced.
Bend per 100 mm (3.937 in)
Standard: 0.08 mm (0.0031 in) or less
Limit: 0.20 mm (0.0079 in)
Twist per 100 mm (3.937 in)
Standard: 0.05 mm (0.0020 in) or less
Limit: 0.15 mm (0.0059 in)
2. Measure the connecting rod thrust clearance.
Use a feeler gauge to measure the thrust clearance
at the big end of the connecting rod.
If the clearance exceeds the specified limit, the
connecting rod must be replaced.
Standard: 0.230 mm (0.0091 in)
Limit: 0.350 mm (0.0138 in)
012RW074
012RW123
012RW001
Page 5358 of 6000
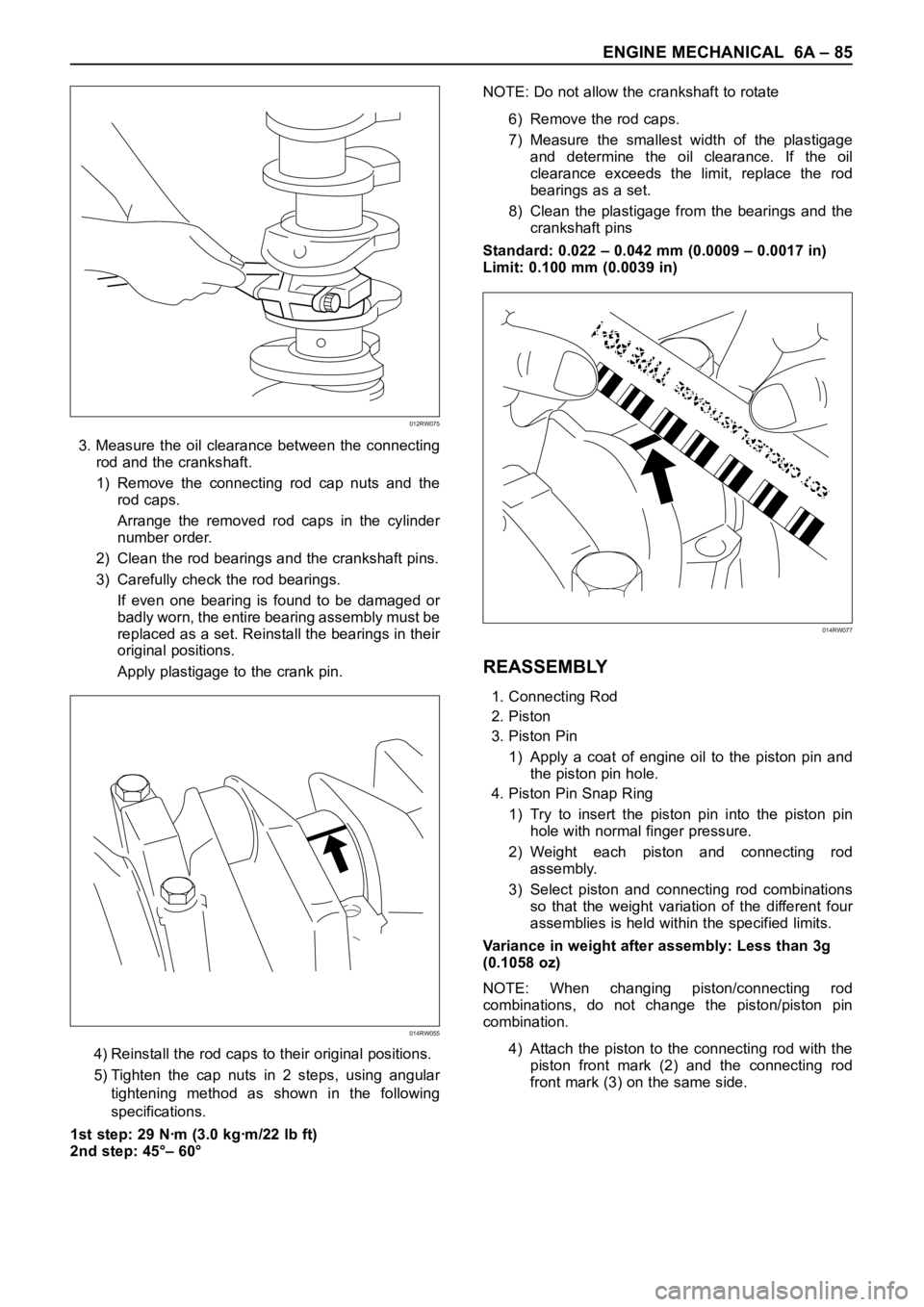
ENGINE MECHANICAL 6A – 85
3. Measure the oil clearance between the connecting
rod and the crankshaft.
1) Remove the connecting rod cap nuts and the
rod caps.
Arrange the removed rod caps in the cylinder
number order.
2) Clean the rod bearings and the crankshaft pins.
3) Carefully check the rod bearings.
If even one bearing is found to be damaged or
badly worn, the entire bearing assembly must be
replaced as a set. Reinstall the bearings in their
original positions.
Apply plastigage to the crank pin.
4) Reinstall the rod caps to their original positions.
5) Tighten the cap nuts in 2 steps, using angular
tightening method as shown in the following
specifications.
1st step: 29 Nꞏm (3.0 kgꞏm/22 lb ft)
2nd step: 45°– 60°NOTE: Do not allow the crankshaft to rotate
6) Remove the rod caps.
7) Measure the smallest width of the plastigage
and determine the oil clearance. If the oil
clearance exceeds the limit, replace the rod
bearings as a set.
8) Clean the plastigage from the bearings and the
crankshaft pins
Standard: 0.022 – 0.042 mm (0.0009 – 0.0017 in)
Limit: 0.100 mm (0.0039 in)
REASSEMBLY
1. Connecting Rod
2. Piston
3. Piston Pin
1) Apply a coat of engine oil to the piston pin and
the piston pin hole.
4. Piston Pin Snap Ring
1) Try to insert the piston pin into the piston pin
hole with normal finger pressure.
2) Weight each piston and connecting rod
assembly.
3) Select piston and connecting rod combinations
so that the weight variation of the different four
assemblies is held within the specified limits.
Variance in weight after assembly: Less than 3g
(0.1058 oz)
NOTE: When changing piston/connecting rod
combinations, do not change the piston/piston pin
combination.
4) Attach the piston to the connecting rod with the
piston front mark (2) and the connecting rod
front mark (3) on the same side.
014RW055
012RW075
014RW077
Page 5359 of 6000
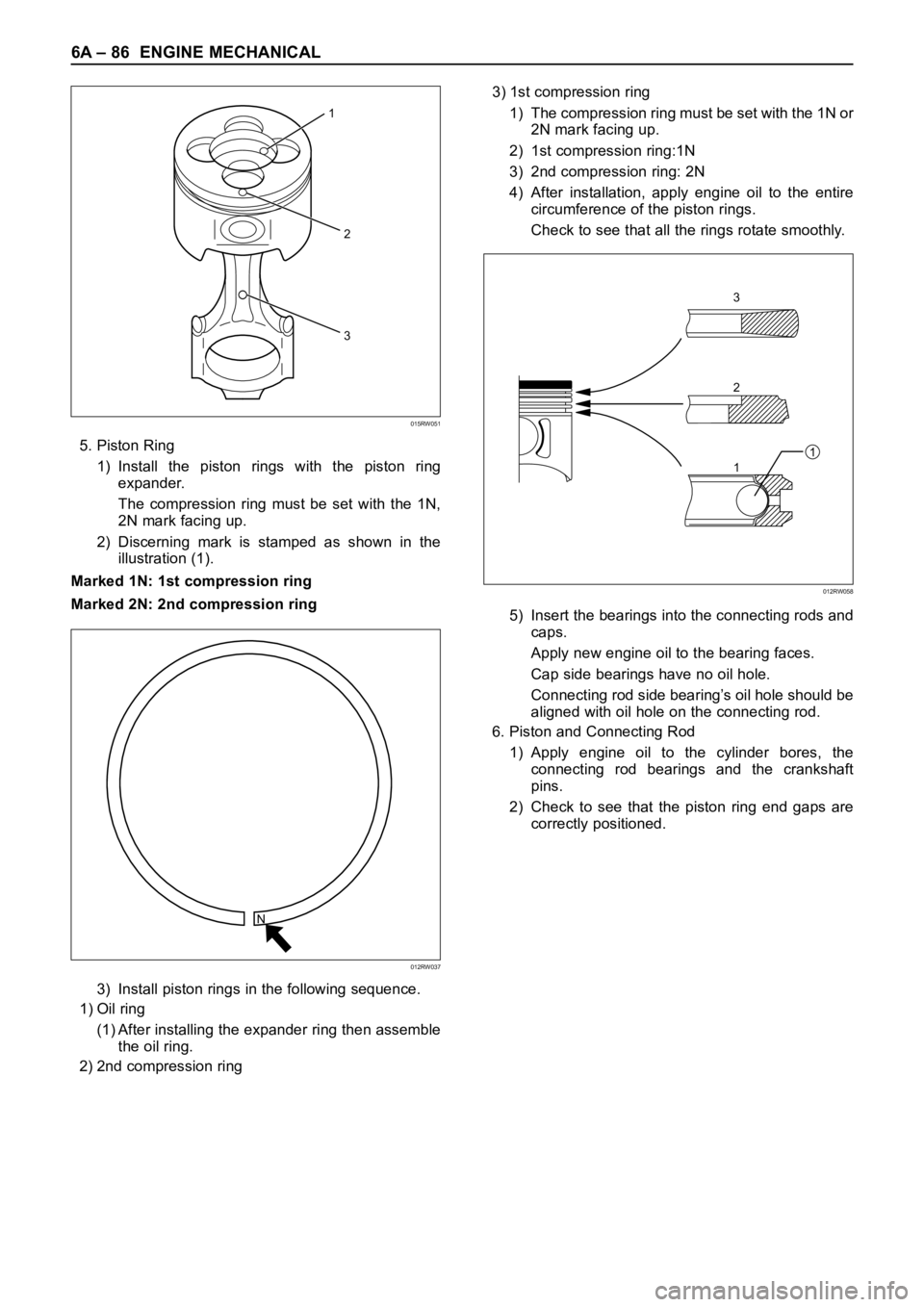
6A – 86 ENGINE MECHANICAL
5. Piston Ring
1) Install the piston rings with the piston ring
expander.
The compression ring must be set with the 1N,
2N mark facing up.
2) Discerning mark is stamped as shown in the
illustration (1).
Marked 1N: 1st compression ring
Marked 2N: 2nd compression ring
3) Install piston rings in the following sequence.
1) Oil ring
(1) After installing the expander ring then assemble
the oil ring.
2) 2nd compression ring3) 1st compression ring
1) The compression ring must be set with the 1N or
2N mark facing up.
2) 1st compression ring:1N
3) 2nd compression ring: 2N
4) After installation, apply engine oil to the entire
circumference of the piston rings.
Check to see that all the rings rotate smoothly.
5) Insert the bearings into the connecting rods and
caps.
Apply new engine oil to the bearing faces.
Cap side bearings have no oil hole.
Connecting rod side bearing’s oil hole should be
aligned with oil hole on the connecting rod.
6. Piston and Connecting Rod
1) Apply engine oil to the cylinder bores, the
connecting rod bearings and the crankshaft
pins.
2) Check to see that the piston ring end gaps are
correctly positioned.
N
012RW037
2
3
1
015RW051
3
2
11
012RW058
Page 5360 of 6000
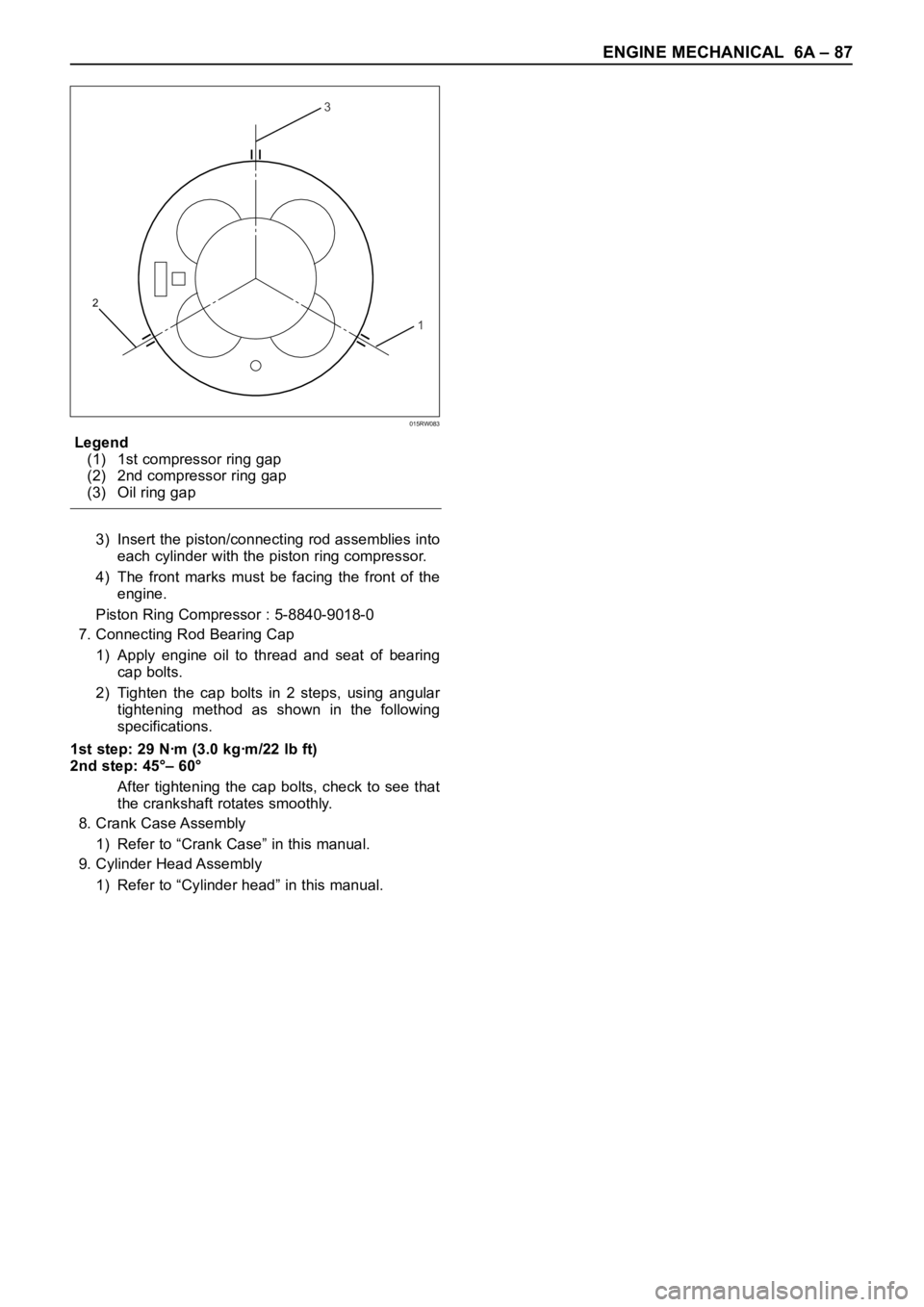
ENGINE MECHANICAL 6A – 87
Legend
(1) 1st compressor ring gap
(2) 2nd compressor ring gap
(3) Oil ring gap
3) Insert the piston/connecting rod assemblies into
each cylinder with the piston ring compressor.
4) The front marks must be facing the front of the
engine.
Piston Ring Compressor : 5-8840-9018-0
7. Connecting Rod Bearing Cap
1) Apply engine oil to thread and seat of bearing
cap bolts.
2) Tighten the cap bolts in 2 steps, using angular
tightening method as shown in the following
specifications.
1st step: 29 Nꞏm (3.0 kgꞏm/22 lb ft)
2nd step: 45°– 60°
After tightening the cap bolts, check to see that
the crankshaft rotates smoothly.
8. Crank Case Assembly
1) Refer to “Crank Case” in this manual.
9. Cylinder Head Assembly
1) Refer to “Cylinder head” in this manual.
3
1
2
015RW083
Page 5362 of 6000
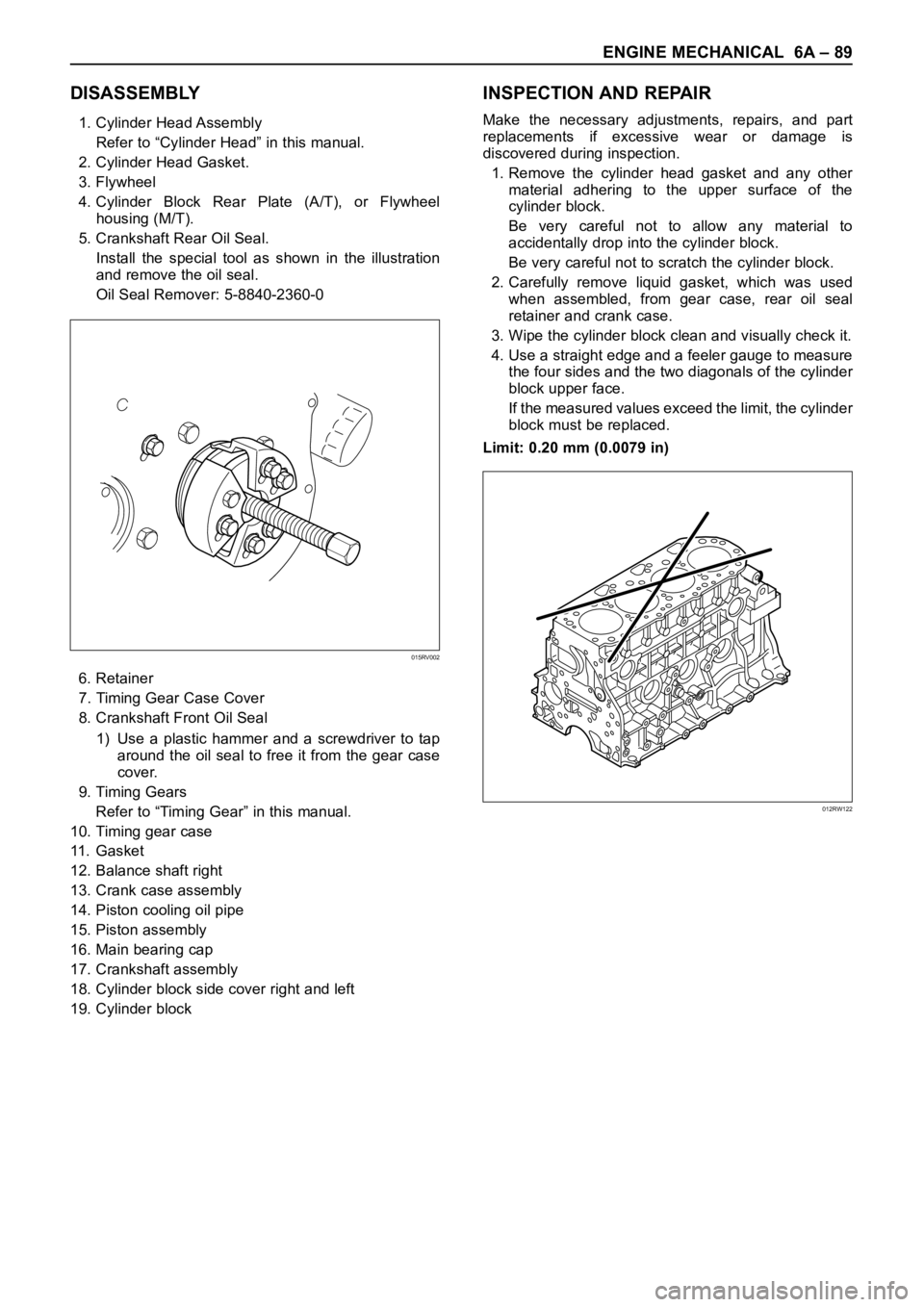
ENGINE MECHANICAL 6A – 89
DISASSEMBLY
1. Cylinder Head Assembly
Refer to “Cylinder Head” in this manual.
2. Cylinder Head Gasket.
3. Flywheel
4. Cylinder Block Rear Plate (A/T), or Flywheel
housing (M/T).
5. Crankshaft Rear Oil Seal.
Install the special tool as shown in the illustration
and remove the oil seal.
Oil Seal Remover: 5-8840-2360-0
6. Retainer
7. Timing Gear Case Cover
8. Crankshaft Front Oil Seal
1) Use a plastic hammer and a screwdriver to tap
around the oil seal to free it from the gear case
cover.
9. Timing Gears
Refer to “Timing Gear” in this manual.
10. Timing gear case
11 . G a s k e t
12. Balance shaft right
13. Crank case assembly
14. Piston cooling oil pipe
15. Piston assembly
16. Main bearing cap
17. Crankshaft assembly
18. Cylinder block side cover right and left
19. Cylinder block
INSPECTION AND REPAIR
Make the necessary adjustments, repairs, and part
replacements if excessive wear or damage is
discovered during inspection.
1. Remove the cylinder head gasket and any other
material adhering to the upper surface of the
cylinder block.
Be very careful not to allow any material to
accidentally drop into the cylinder block.
Be very careful not to scratch the cylinder block.
2. Carefully remove liquid gasket, which was used
when assembled, from gear case, rear oil seal
retainer and crank case.
3. Wipe the cylinder block clean and visually check it.
4. Use a straight edge and a feeler gauge to measure
the four sides and the two diagonals of the cylinder
block upper face.
If the measured values exceed the limit, the cylinder
block must be replaced.
Limit: 0.20 mm (0.0079 in)
015RV002
012RW122
Page 5364 of 6000
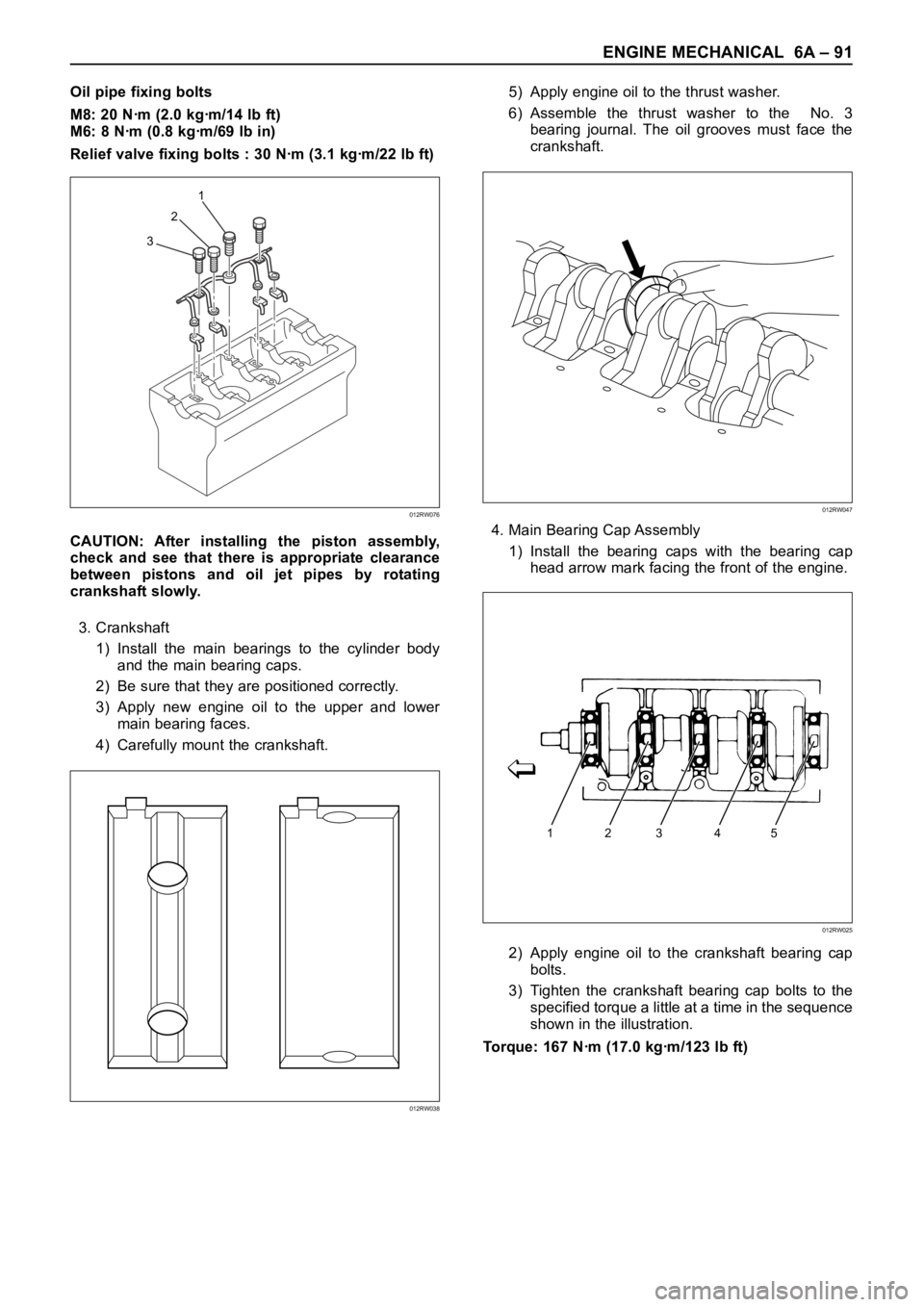
ENGINE MECHANICAL 6A – 91
Oil pipe fixing bolts
M8: 20 Nꞏm (2.0 kgꞏm/14 lb ft)
M6: 8 Nꞏm (0.8 kgꞏm/69 lb in)
Relief valve fixing bolts : 30 Nꞏm (3.1 kgꞏm/22 lb ft)
CAUTION: After installing the piston assembly,
check and see that there is appropriate clearance
between pistons and oil jet pipes by rotating
crankshaft slowly.
3. Crankshaft
1) Install the main bearings to the cylinder body
and the main bearing caps.
2) Be sure that they are positioned correctly.
3) Apply new engine oil to the upper and lower
main bearing faces.
4) Carefully mount the crankshaft.5) Apply engine oil to the thrust washer.
6) Assemble the thrust washer to the No. 3
bearing journal. The oil grooves must face the
crankshaft.
4. Main Bearing Cap Assembly
1) Install the bearing caps with the bearing cap
head arrow mark facing the front of the engine.
2) Apply engine oil to the crankshaft bearing cap
bolts.
3) Tighten the crankshaft bearing cap bolts to the
specified torque a little at a time in the sequence
shown in the illustration.
Torque: 167 Nꞏm (17.0 kgꞏm/123 lb ft)
321
012RW076
012RW038
012RW047
12345
012RW025