set clock OPEL GT-R 1973 Service Manual
[x] Cancel search | Manufacturer: OPEL, Model Year: 1973, Model line: GT-R, Model: OPEL GT-R 1973Pages: 625, PDF Size: 17.22 MB
Page 27 of 625
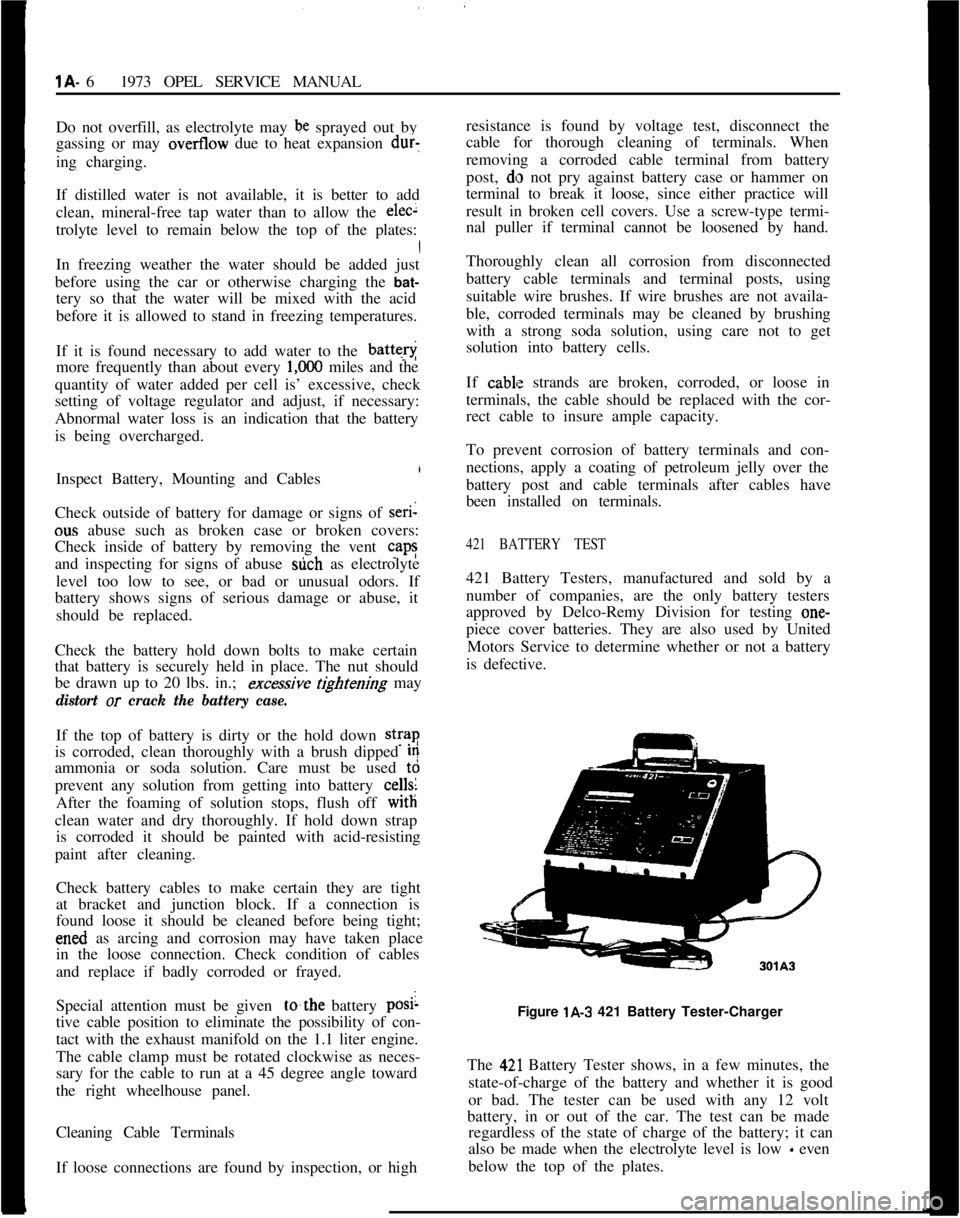
j
/lA- 61973 OPEL SERVICE MANUAL
Do not overfill, as electrolyte may
be sprayed out by
gassing or may overtlow due to heat expansion dur:
ing charging.
If distilled water is not available, it is better to add
clean, mineral-free tap water than to allow the
elec2trolyte level to remain below the top of the plates:
In freezing weather the water should be added just
before using the car or otherwise charging the bat-
tery so that the water will be mixed with the acid
before it is allowed to stand in freezing temperatures.
If it is found necessary to add water to the
batterimore frequently than about every
1,ooO miles and the
quantity of water added per cell is’ excessive, check
setting of voltage regulator and adjust, if necessary:
Abnormal water loss is an indication that the battery
is being overcharged.
Inspect Battery, Mounting and Cables
Check outside of battery for damage or signs of se&ous abuse such as broken case or broken covers:
Check inside of battery by removing the vent caps
and inspecting for signs of abuse
stich as electrolyte
level too low to see, or bad or unusual odors. If
battery shows signs of serious damage or abuse, it
should be replaced.
Check the battery hold down bolts to make certain
that battery is securely held in place. The nut should
be drawn up to 20 lbs. in.;excessjve tightening may
distort or crack the battery case.If the top of battery is dirty or the hold down str?e
is corroded, clean thoroughly with a brush dipped
IFammonia or soda solution. Care must be used td
prevent any solution from getting into battery
cellslAfter the foaming of solution stops, flush off witli
clean water and dry thoroughly. If hold down strap
is corroded it should be painted with acid-resisting
paint after cleaning.
Check battery cables to make certain they are tight
at bracket and junction block. If a connection is
found loose it should be cleaned before being tight;ened as arcing and corrosion may have taken place
in the loose connection. Check condition of cables
and replace if badly corroded or frayed.
Special attention must be given to,the battery posi-
tive cable position to eliminate the possibility of con-
tact with the exhaust manifold on the 1.1 liter engine.
The cable clamp must be rotated clockwise as neces-
sary for the cable to run at a 45 degree angle toward
the right wheelhouse panel.
Cleaning Cable Terminals
If loose connections are found by inspection, or highresistance is found by voltage test, disconnect the
cable for thorough cleaning of terminals. When
removing a corroded cable terminal from battery
post, do not pry against battery case or hammer on
terminal to break it loose, since either practice will
result in broken cell covers. Use a screw-type termi-
nal puller if terminal cannot be loosened by hand.
Thoroughly clean all corrosion from disconnected
battery cable terminals and terminal posts, using
suitable wire brushes. If wire brushes are not availa-
ble, corroded terminals may be cleaned by brushing
with a strong soda solution, using care not to get
solution into battery cells.
If
cabbz strands are broken, corroded, or loose in
terminals, the cable should be replaced with the cor-
rect cable to insure ample capacity.
To prevent corrosion of battery terminals and con-
nections, apply a coating of petroleum jelly over the
battery post and cable terminals after cables have
been installed on terminals.
421 BATTERY TEST421 Battery Testers, manufactured and sold by a
number of companies, are the only battery testers
approved by Delco-Remy Division for testing one-
piece cover batteries. They are also used by United
Motors Service to determine whether or not a battery
is defective.
Figure lA-3 421 Battery Tester-Charger
The
42,l Battery Tester shows, in a few minutes, the
state-of-charge of the battery and whether it is good
or bad. The tester can be used with any 12 volt
battery, in or out of the car. The test can be made
regardless of the state of charge of the battery; it can
also be made when the electrolyte level is low
- even
below the top of the plates.
Page 41 of 625
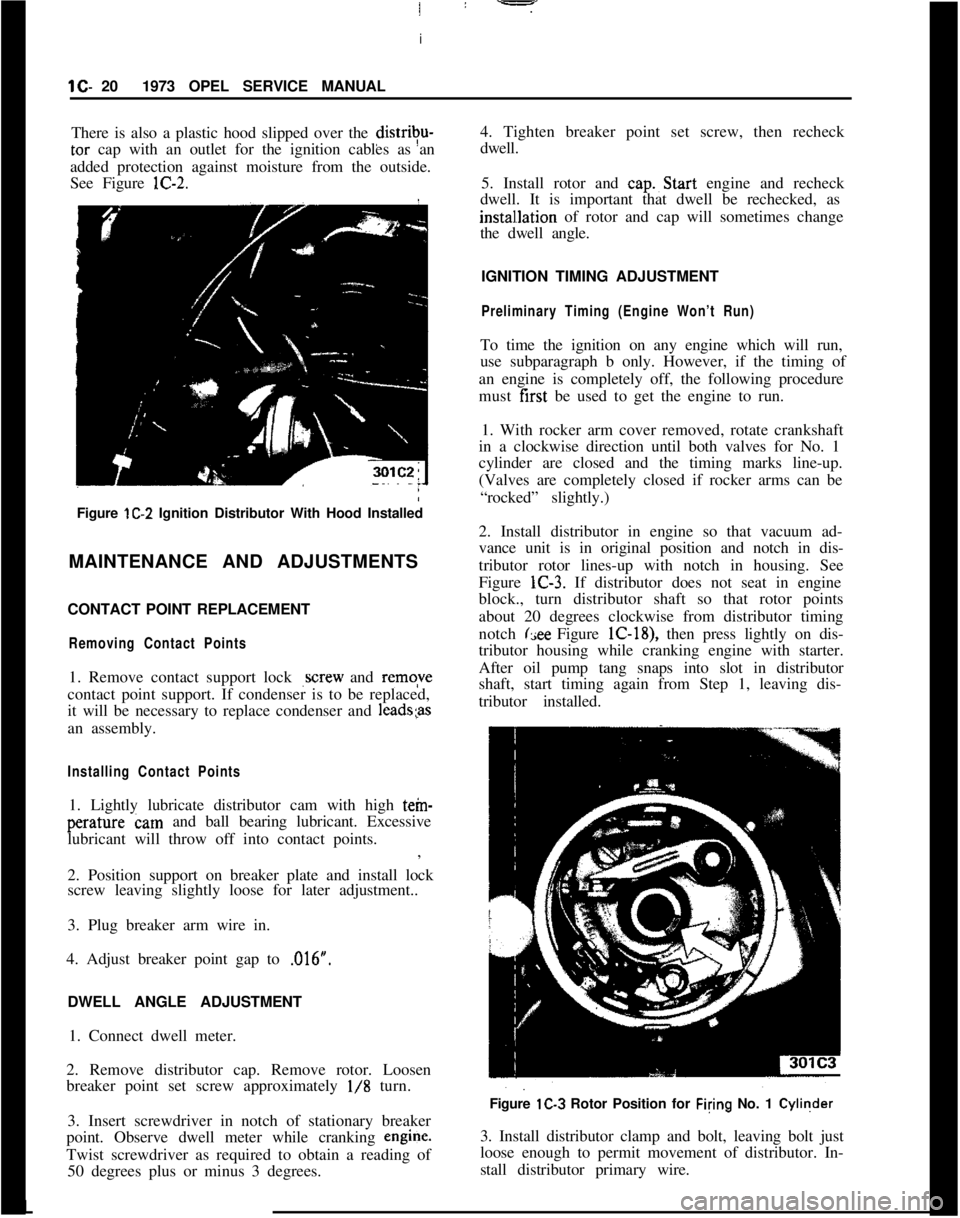
I
ilC- 201973 OPEL SERVICE MANUAL
There is also a plastic hood slipped over the distrivu-tar cap with an outlet for the ignition cables as an
added protection against moisture from the outside.
See Figure lC-2.
Figure lC-2 Ignition Distributor With Hood Installed
MAINTENANCE AND ADJUSTMENTS
CONTACT POINT REPLACEMENT
Removing Contact Points1. Remove contact support lock
,screw and remqve
contact point support. If condenser is to be replaced,
it will be necessary to replace condenser and
1eads;asan assembly.
Installing Contact Points1. Lightly lubricate distributor cam with high tein-perature cam and ball bearing lubricant. Excessive
lubricant will throw off into contact points.
:
,
2. Position support on breaker plate and install lock
screw leaving slightly loose for later adjustment..
3. Plug breaker arm wire in.
4. Adjust breaker point gap to ,016”.
/
DWELL ANGLE ADJUSTMENT
1. Connect dwell meter.
2. Remove distributor cap. Remove rotor. Loosen
breaker point set screw approximately
l/8 turn.
3. Insert screwdriver in notch of stationary breaker
point. Observe dwell meter while cranking engine.
Twist screwdriver as required to obtain a reading of
50 degrees plus or minus 3 degrees.4. Tighten breaker point set screw, then recheck
dwell.
5. Install rotor and cap.~Start engine and recheck
dwell. It is important that dwell be rechecked, as
instal~lation of rotor and cap will sometimes change
the dwell angle.
IGNITION TIMING ADJUSTMENT
Preliminary Timing (Engine Won’t Run)To time the ignition on any engine which will run,
use subparagraph b only. However, if the timing of
an engine is completely off, the following procedure
must first be used to get the engine to run.
1. With rocker arm cover removed, rotate crankshaft
in a clockwise direction until both valves for No. 1
cylinder are closed and the timing marks line-up.
(Valves are completely closed if rocker arms can be
“rocked” slightly.)
2. Install distributor in engine so that vacuum ad-
vance unit is in original position and notch in dis-
tributor rotor lines-up with notch in housing. See
Figure lC-3. If distributor does not seat in engine
block., turn distributor shaft so that rotor points
about 20 degrees clockwise from distributor timing
notch
(see Figure lC-18), then press lightly on dis-
tributor housing while cranking engine with starter.
After oil pump tang snaps into slot in distributor
shaft, start timing again from Step 1, leaving dis-
tributor installed.
Figure lC-3 Rotor Position for Filing No. 1 Cyliqder
3. Install distributor clamp and bolt, leaving bolt just
loose enough to permit movement of distributor. In-
stall distributor primary wire.L
Page 42 of 625
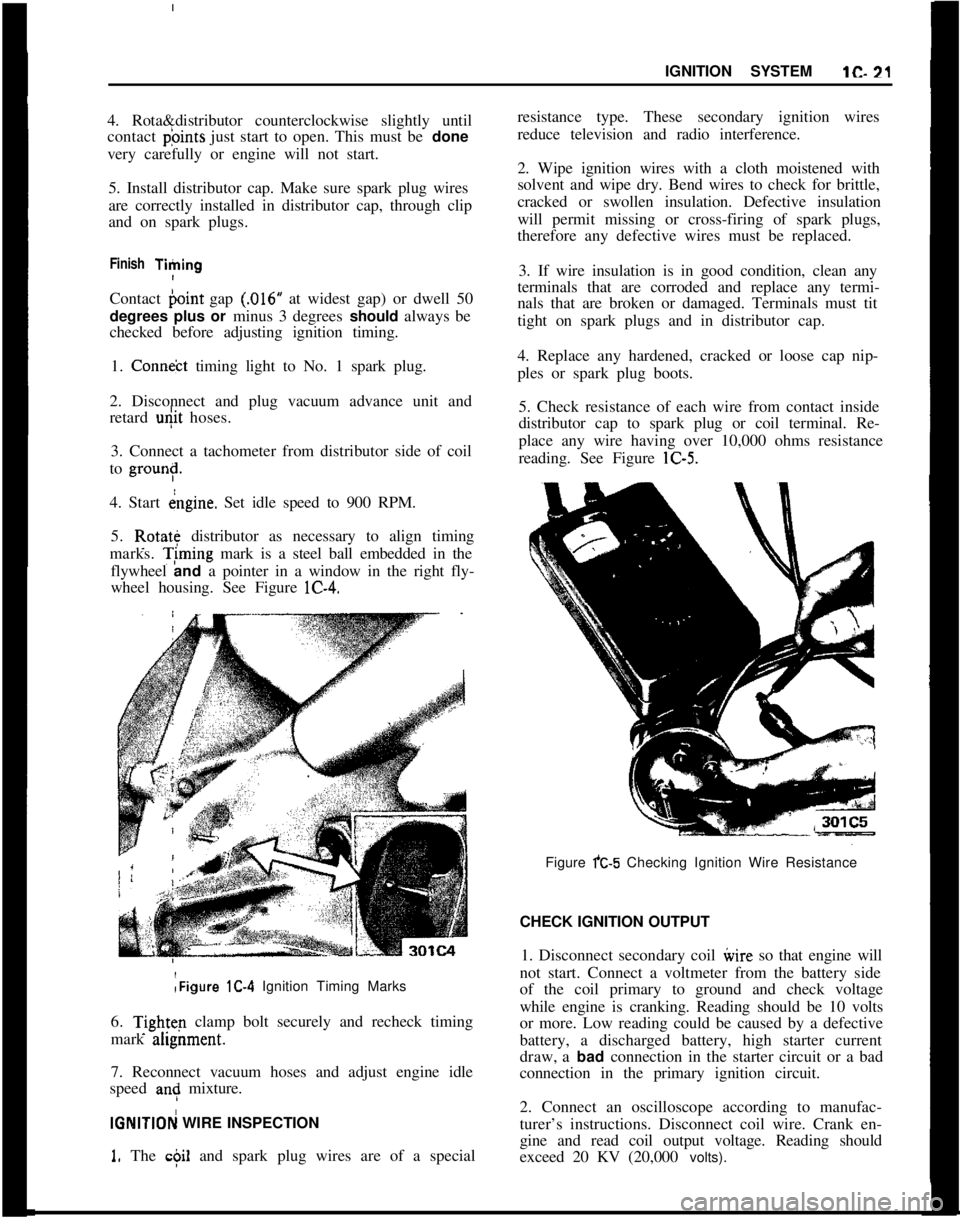
IGNITION SYSTEMlC-214. Rota&distributor counterclockwise slightly until
contact pbints just start to open. This must be done
very carefully or engine will not start.
5. Install distributor cap. Make sure spark plug wires
are correctly installed in distributor cap, through clip
and on spark plugs.
Finish TimingIContact boint gap
(.016” at widest gap) or dwell 50
degrees plus or minus 3 degrees should always be
checked before adjusting ignition timing.
1. Connekt timing light to No. 1 spark plug.
2. Disconnect and plug vacuum advance unit and
retard u$it hoses.
3. Connect a tachometer from distributor side of coil
to
groun$l.4. Start dngine. Set idle speed to 900 RPM.
5. Rotate distributor as necessary to align timing
marks. T;ming mark is a steel ball embedded in the
flywheel and a pointer in a window in the right fly-
wheel housing. See Figure lC-4.:Figure lC-4 Ignition Timing Marks
6.
Tightq clamp bolt securely and recheck timing
mark ahgnment.
7. Reconnect vacuum hoses and adjust engine idle
speed
an: mixture.
IGNlTlOFj WIRE INSPECTION
1. The c$il and spark plug wires are of a specialresistance type. These secondary ignition wires
reduce television and radio interference.
2. Wipe ignition wires with a cloth moistened with
solvent and wipe dry. Bend wires to check for brittle,
cracked or swollen insulation. Defective insulation
will permit missing or cross-firing of spark plugs,
therefore any defective wires must be replaced.
3. If wire insulation is in good condition, clean any
terminals that are corroded and replace any termi-
nals that are broken or damaged. Terminals must tit
tight on spark plugs and in distributor cap.
4. Replace any hardened, cracked or loose cap nip-
ples or spark plug boots.
5. Check resistance of each wire from contact inside
distributor cap to spark plug or coil terminal. Re-
place any wire having over 10,000 ohms resistance
reading. See Figure lC-5.
Figure fC-5 Checking Ignition Wire Resistance
CHECK IGNITION OUTPUT
1. Disconnect secondary coil ivire so that engine will
not start. Connect a voltmeter from the battery side
of the coil primary to ground and check voltage
while engine is cranking. Reading should be 10 volts
or more. Low reading could be caused by a defective
battery, a discharged battery, high starter current
draw, a bad connection in the starter circuit or a bad
connection in the primary ignition circuit.
2. Connect an oscilloscope according to manufac-
turer’s instructions. Disconnect coil wire. Crank en-
gine and read coil output voltage. Reading should
exceed 20 KV (20,000 volts).
Page 341 of 625
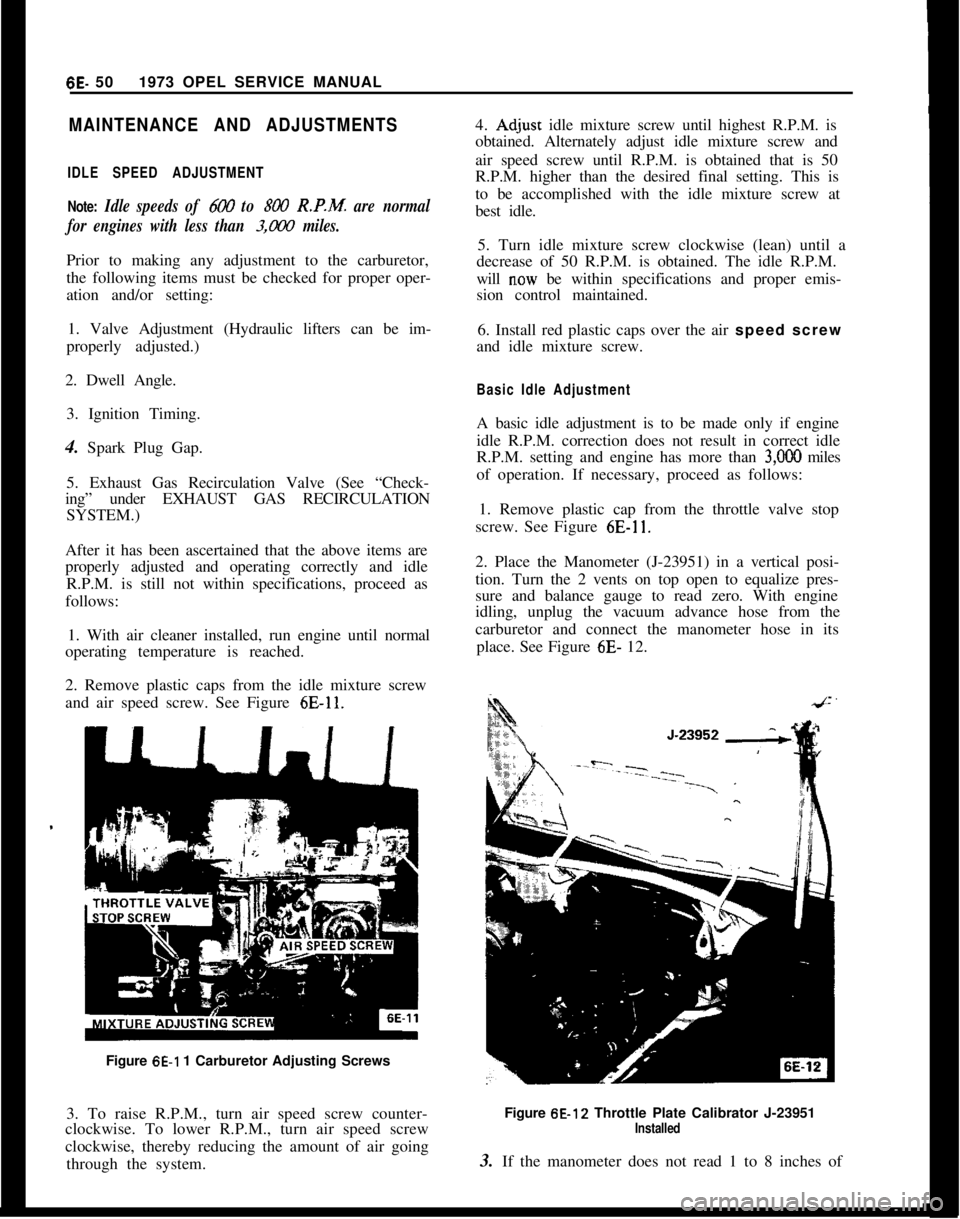
6E- 501973 OPEL SERVICE MANUALMAINTENANCE AND ADJUSTMENTS
IDLE SPEED ADJUSTMENT
Note:
Idle speeds of 600 to 800 R.P.M. are normal
for engines with less than
3,ooO miles.Prior to making any adjustment to the carburetor,
the following items must be checked for proper oper-
ation and/or setting:
1. Valve Adjustment (Hydraulic lifters can be im-
properly adjusted.)
2. Dwell Angle.
3. Ignition Timing.
4. Spark Plug Gap.
5. Exhaust Gas Recirculation Valve (See “Check-
ing” under EXHAUST GAS RECIRCULATION
SYSTEM.)
After it has been ascertained that the above items are
properly adjusted and operating correctly and idle
R.P.M. is still not within specifications, proceed as
follows:
1. With air cleaner installed, run engine until normal
operating temperature is reached.
2. Remove plastic caps from the idle mixture screw
and air speed screw. See Figure
6E-11.Figure
6E-1 1 Carburetor Adjusting Screws
3. To raise R.P.M., turn air speed screw counter-
clockwise. To lower R.P.M., turn air speed screw
clockwise, thereby reducing the amount of air going
through the system.4.
Ad,just idle mixture screw until highest R.P.M. is
obtained. Alternately adjust idle mixture screw and
air speed screw until R.P.M. is obtained that is 50
R.P.M. higher than the desired final setting. This is
to be accomplished with the idle mixture screw at
best idle.
5. Turn idle mixture screw clockwise (lean) until a
decrease of 50 R.P.M. is obtained. The idle R.P.M.
will
n.ow be within specifications and proper emis-
sion control maintained.
6. Install red plastic caps over the air speed screw
and idle mixture screw.
Basic Idle AdjustmentA basic idle adjustment is to be made only if engine
idle R.P.M. correction does not result in correct idle
R.P.M. setting and engine has more than
3,OOO miles
of operation. If necessary, proceed as follows:
1. Remove plastic cap from the throttle valve stop
screw. See Figure
6E-11.2. Place the Manometer (J-23951) in a vertical posi-
tion. Turn the 2 vents on top open to equalize pres-
sure and balance gauge to read zero. With engine
idling, unplug the vacuum advance hose from the
carburetor and connect the manometer hose in its
place. See Figure 6E- 12.
Figure 6E-12 Throttle Plate Calibrator J-23951
Installed3. If the manometer does not read 1 to 8 inches of
Page 359 of 625
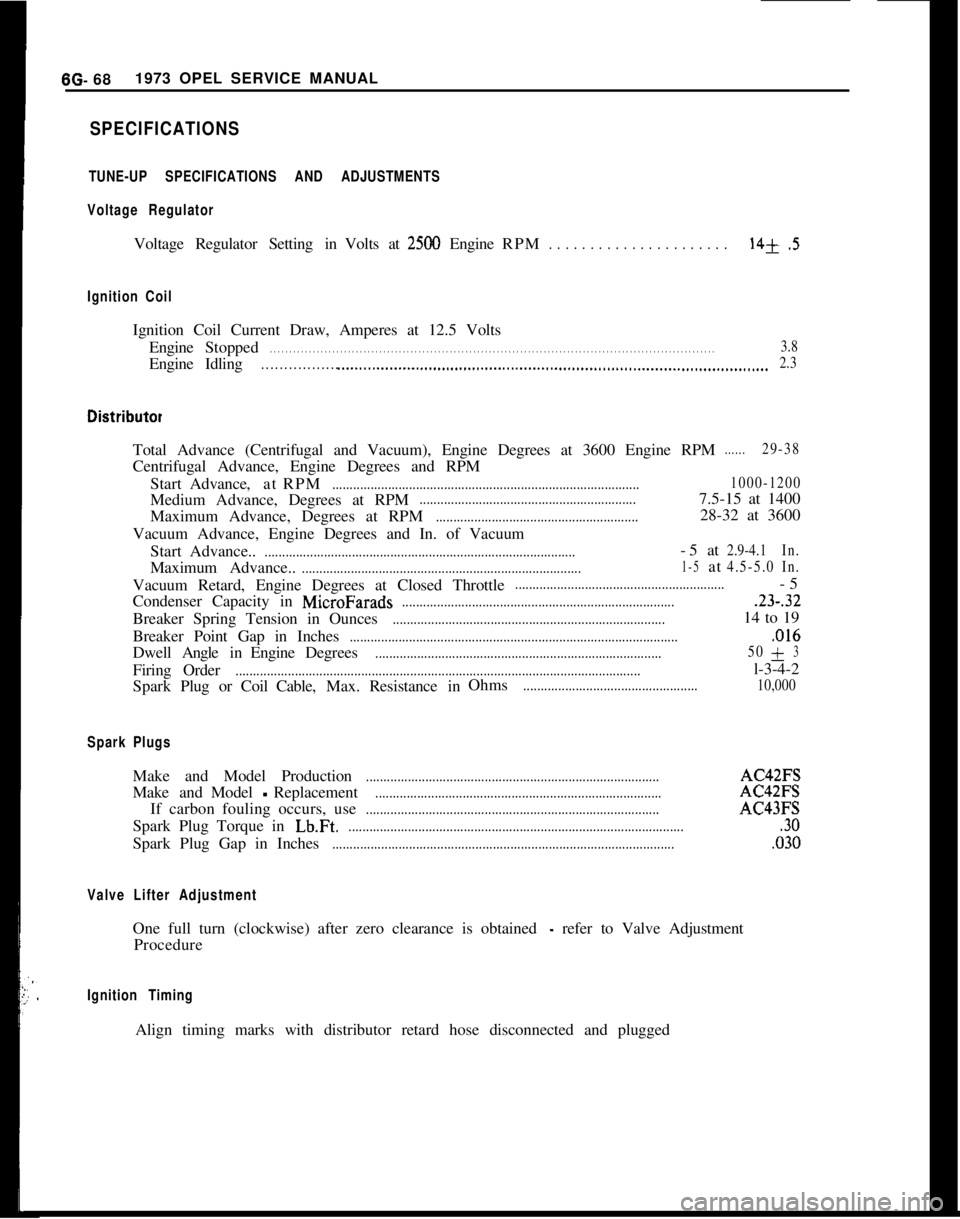
6G- 68 1973 OPEL SERVICE MANUAL
SPECIFICATIONS
TUNE-UP SPECIFICATIONS AND ADJUSTMENTS
Voltage Regulator
Voltage Regulator Setting in Volts at2500 Engine RPM. . . . . . . . . . . . . . . . . . . . . .14+.5
Ignition Coil
Ignition Coil Current Draw, Amperes at 12.5 Volts
Engine Stopped
. . . . . . . . . . . . . . . . . . . . . . . . . . . . . . . . . . . . \
. . . . . . . . . . . . . . . . . . . . . . . . . . . . . . . . . . . . \
. . . . . . . . . . . . . . . . . . . . . . . . . . . . . . . . . . . . \
. . . . . .3.8
EngineIdling. . . . . . . . . . . . . . . . . .._.....................................................................\
........................... 2.3
Total Advance (Centrifugal and Vacuum), Engine Degrees at 3600 Engine \
RPM......29-38
Centrifugal Advance, Engine Degrees and RPM
Start Advance, atRPM
........................................................................\
................ 1000-1200
Medium Advance, Degrees at RPM..............................................................7.5-15 at 1400
Maximum Advance, Degrees at RPM
..........................................................28-32 at 3600
Vacuum Advance, Engine Degrees and In. of Vacuum Start Advance..
........................................................................\
.................-5at2.9-4.1 In.
Maximum Advance..........................................................................\
........1-5at4.5-5.0In.
Vacuum Retard, Engine Degrees at Closed Throttle............................................................-5
Condenser Capacity in
MicroFarads........................................................................\
.......23-.32
Breaker Spring Tension in Ounces........................................................................\
......14 to 19
Breaker Point Gap in Inches
........................................................................\
......................,016
Dwell AngleinEngine Degrees........................................................................\
.......... 50+3
Firing
Order........................................................................\
............................................l-3-4-2
Spark Plug or Coil Cable,Max.Resistance in Ohms
..................................................
10,000
Spark Plugs
Make and Model Production........................................................................\
............AC42FS
Make andModel
-Replacement........................................................................\
..........AC42FS
If carbon fouling occurs, use
........................................................................\
............AC43FS
Spark Plug Torque in
Lb.Ft.........................................................................\
.........................30
Spark Plug Gap in Inches........................................................................\
..........................,030
Valve Lifter Adjustment
One full turn (clockwise) after zero clearance is obtained - refer to Valve Adjustment
Procedure
Ignition Timing
Align timing marks with distributor retard hose disconnected and plugged\
Page 401 of 625
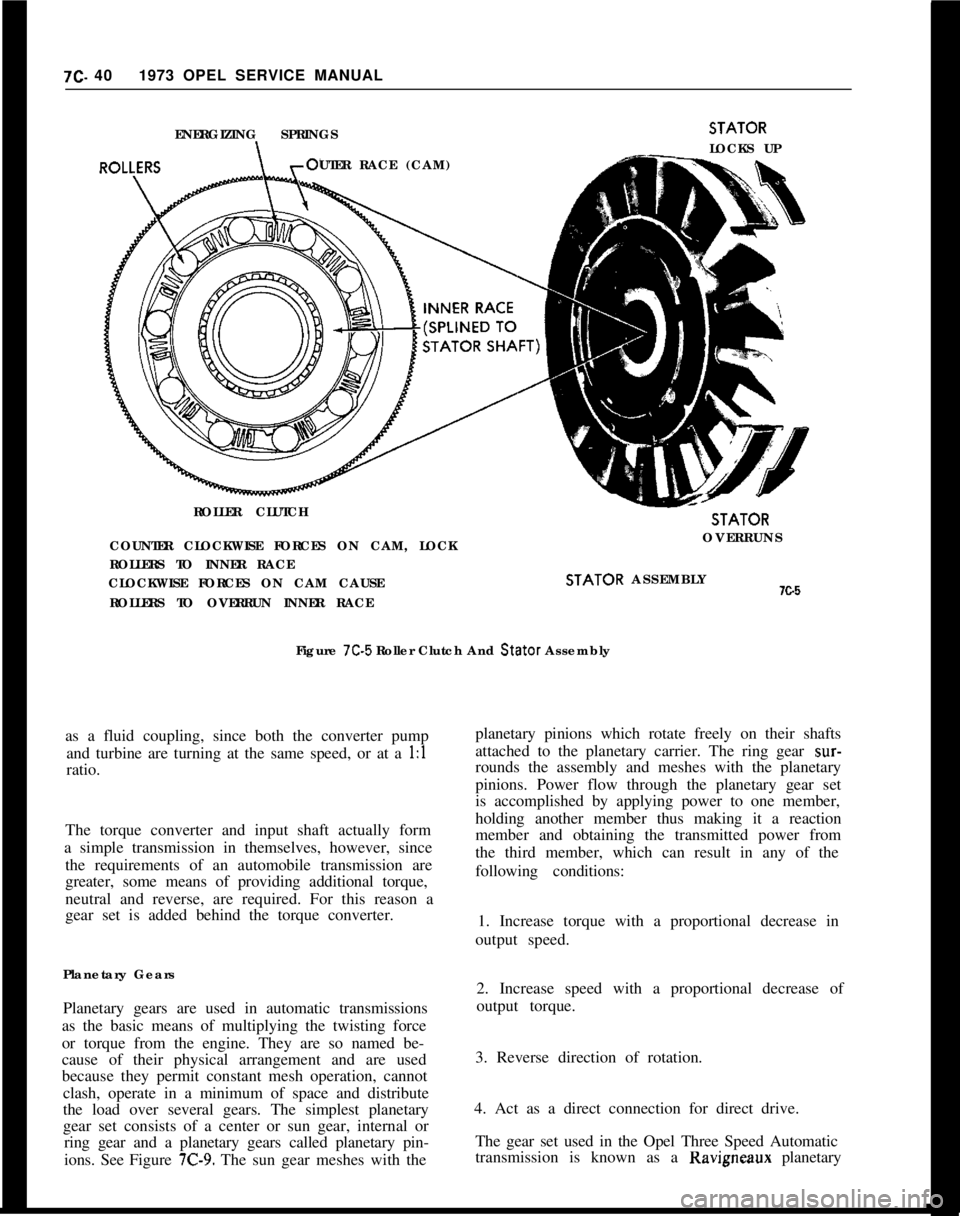
7C- 401973 OPEL SERVICE MANUAL
ENERGIZING SPRINGS
UTER RACE (CAM)
ROLLER CLUTCHSTATOR
LOCKS UPSTATOR
COUNTER CLOCKWISE FORCES ON CAM, LOCKOVERRUNS
ROLLERS TO INNER RACE
CLOCKWISE FORCES ON CAM CAUSESTATOR ASSEMBLYx.5
ROLLERS TO OVERRUN INNER RACE
Figure 7C-5 Roller Clutch And Stator Assembly
as a fluid coupling, since both the converter pump
and turbine are turning at the same speed, or at a 1:l
ratio.
The torque converter and input shaft actually form
a simple transmission in themselves, however, since
the requirements of an automobile transmission are
greater, some means of providing additional torque,
neutral and reverse, are required. For this reason a
gear set is added behind the torque converter.
Planetary Gears
Planetary gears are used in automatic transmissions
as the basic means of multiplying the twisting force
or torque from the engine. They are so named be-
cause of their physical arrangement and are used
because they permit constant mesh operation, cannot
clash, operate in a minimum of space and distribute
the load over several gears. The simplest planetary
gear set consists of a center or sun gear, internal or
ring gear and a planetary gears called planetary pin-
ions. See Figure
7C-9. The sun gear meshes with theplanetary pinions which rotate freely on their shafts
attached to the planetary carrier. The ring gear
sur-rounds the assembly and meshes with the planetary
pinions. Power flow through the planetary gear set
is accomplished by applying power to one member,
holding another member thus making it a reaction
member and obtaining the transmitted power from
the third member, which can result in any of the
following conditions:
1. Increase torque with a proportional decrease in
output speed.
2. Increase speed with a proportional decrease of
output torque.
3. Reverse direction of rotation.
4. Act as a direct connection for direct drive.
The gear set used in the Opel Three Speed Automatic
transmission is known as a Ravigneaux planetary
Page 402 of 625
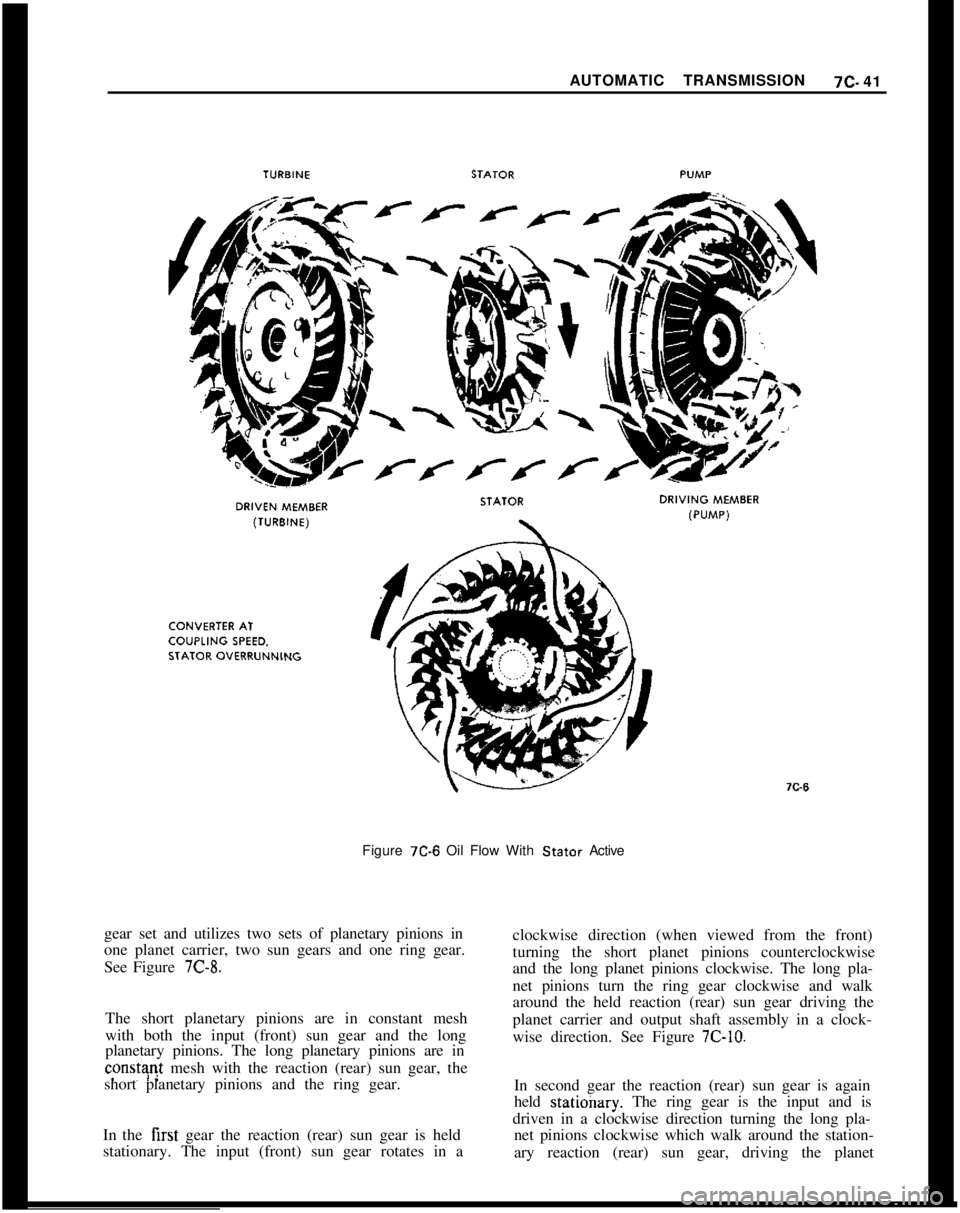
AUTOMATIC TRANSMISSION7c- 41
Figure
7C-6 Oil Flow With Stator Active
gear set and utilizes two sets of planetary pinions in
one planet carrier, two sun gears and one ring gear.
See Figure
7C-8.The short planetary pinions are in constant mesh
with both the input (front) sun gear and the long
planetary pinions. The long planetary pinions are inconstr$ mesh with the reaction (rear) sun gear, the
short planetary pinions and the ring gear.
In the first gear the reaction (rear) sun gear is held
stationary. The input (front) sun gear rotates in aclockwise direction (when viewed from the front)
turning the short planet pinions counterclockwise
and the long planet pinions clockwise. The long pla-
net pinions turn the ring gear clockwise and walk
around the held reaction (rear) sun gear driving the
planet carrier and output shaft assembly in a clock-
wise direction. See Figure
7C-10.In second gear the reaction (rear) sun gear is again
held statioinry. The ring gear is the input and is
driven in a clockwise direction turning the long pla-
net pinions clockwise which walk around the station-
ary reaction (rear) sun gear, driving the planet
Page 420 of 625
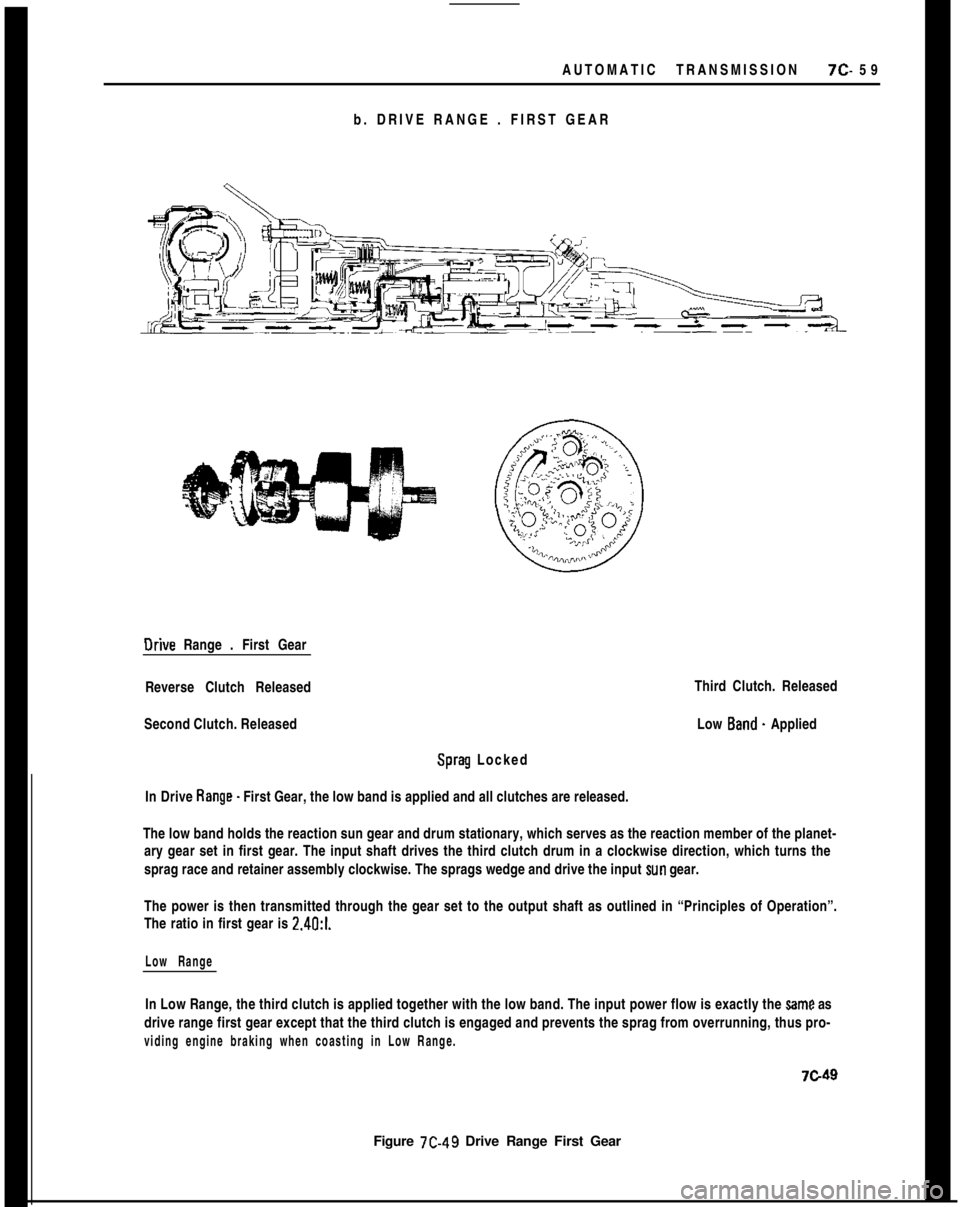
AUTOMATIC TRANSMISSION7c- 59
b. DRIVE RANGE . FIRST GEAROrive Range . First Gear
Reverse Clutch Released
Second Clutch. Released
Sprag Locked
In Drive Range. First Gear, the low band is applied and all clutches are released.
Figure 7C-49 Drive Range First GearThird Clutch. Released
Low Band. Applied
The low band holds the reaction sun gear and drum stationary, which serves as the reaction member of the planet-
ary gear set in first gear. The input shaft drives the third clutch drum in a clockwise direction, which turns the
sprag race and retainer assembly clockwise. The sprags wedge and drive the input
sun gear.
The power is then transmitted through the gear set to the output shaft as outlined in “Principles of Operation”.
The ratio in first gear is 2.4O:l.
Low RangeIn Low Range, the third clutch is applied together with the low band. The input power flow is exactly the
Same as
drive range first gear except that the third clutch is engaged and prevents the sprag from overrunning, thus pro-
viding engine braking when coasting in Low Range.
7c49
Page 550 of 625
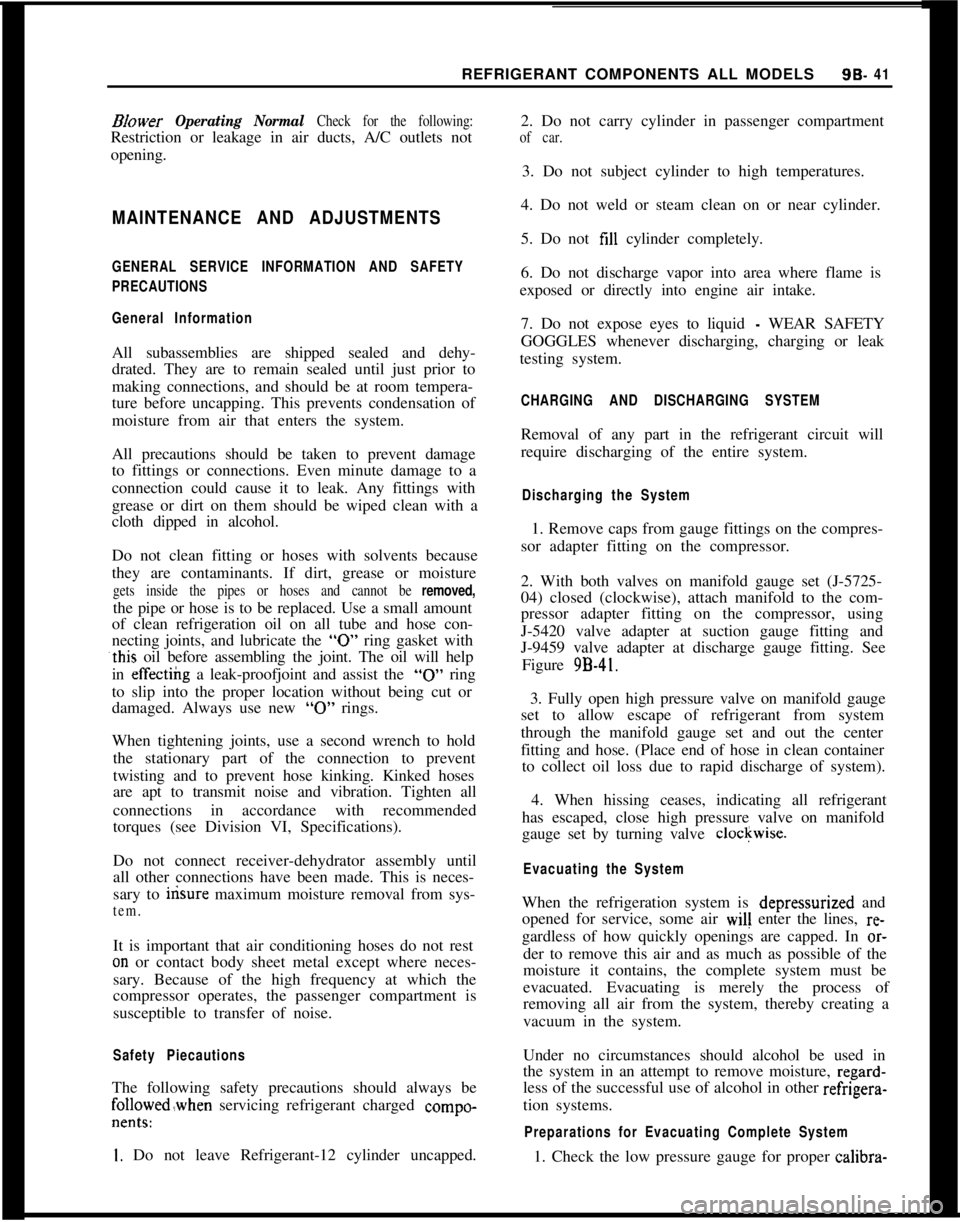
REFRIGERANT COMPONENTS ALL MODELS9s. 41
BIower Operating Normal Check for the following:Restriction or leakage in air ducts, A/C outlets not
opening.2. Do not carry cylinder in passenger compartment
of car.3. Do not subject cylinder to high temperatures.
MAINTENANCE AND ADJUSTMENTS4. Do not weld or steam clean on or near cylinder.
5. Do not fill cylinder completely.
GENERAL SERVICE INFORMATION AND SAFETY
PRECAUTIONS6. Do not discharge vapor into area where flame is
exposed or directly into engine air intake.
General InformationAll subassemblies are shipped sealed and dehy-
drated. They are to remain sealed until just prior to
making connections, and should be at room tempera-
ture before uncapping. This prevents condensation of
moisture from air that enters the system.
All precautions should be taken to prevent damage
to fittings or connections. Even minute damage to a
connection could cause it to leak. Any fittings with
grease or dirt on them should be wiped clean with a
cloth dipped in alcohol.
Do not clean fitting or hoses with solvents because
they are contaminants. If dirt, grease or moisture
gets inside the pipes or hoses and cannot be removed,the pipe or hose is to be replaced. Use a small amount
of clean refrigeration oil on all tube and hose con-
necting joints, and lubricate the
“0” ring gasket with
this oil before assembling the joint. The oil will help
in effectitig a leak-proofjoint and assist the
“0” ring
to slip into the proper location without being cut or
damaged. Always use new
“0” rings.
When tightening joints, use a second wrench to hold
the stationary part of the connection to prevent
twisting and to prevent hose kinking. Kinked hoses
are apt to transmit noise and vibration. Tighten all
connections in accordance with recommended
torques (see Division VI, Specifications).7. Do not expose eyes to liquid
- WEAR SAFETY
GOGGLES whenever discharging, charging or leak
testing system.
CHARGING AND DISCHARGING SYSTEMRemoval of any part in the refrigerant circuit will
require discharging of the entire system.
Discharging the System1. Remove caps from gauge fittings on the compres-
sor adapter fitting on the compressor.
2. With both valves on manifold gauge set (J-5725-
04) closed (clockwise), attach manifold to the com-
pressor adapter fitting on the compressor, using
J-5420 valve adapter at suction gauge fitting and
J-9459 valve adapter at discharge gauge fitting. See
Figure
9B-41.3. Fully open high pressure valve on manifold gauge
set to allow escape of refrigerant from system
through the manifold gauge set and out the center
fitting and hose. (Place end of hose in clean container
to collect oil loss due to rapid discharge of system).
4. When hissing ceases, indicating all refrigerant
has escaped, close high pressure valve on manifold
gauge set by turning valve clockwise.
Do not connect receiver-dehydrator assembly until
all other connections have been made. This is neces-
sary to itisure maximum moisture removal from sys-
tem.It is important that air conditioning hoses do not rest
on or contact body sheet metal except where neces-
sary. Because of the high frequency at which the
compressor operates, the passenger compartment is
susceptible to transfer of noise.
Evacuating the SystemWhen the refrigeration system is depressurized and
opened for service, some air will enter the lines, re-
gardless of how quickly openings are capped. In
or-der to remove this air and as much as possible of the
moisture it contains, the complete system must be
evacuated. Evacuating is merely the process of
removing all air from the system, thereby creating a
vacuum in the system.
Safety PiecautionsThe following safety precautions should always be
followed~,when servicing refrigerant charged compo-nents:Under no circumstances should alcohol be used in
the system in an attempt to remove moisture,
regard-less of the successful use of alcohol in other refrigera-
tion systems.
Preparations for Evacuating Complete System
1. Do not leave Refrigerant-12 cylinder uncapped.
1. Check the low pressure gauge for proper calibra-
Page 551 of 625
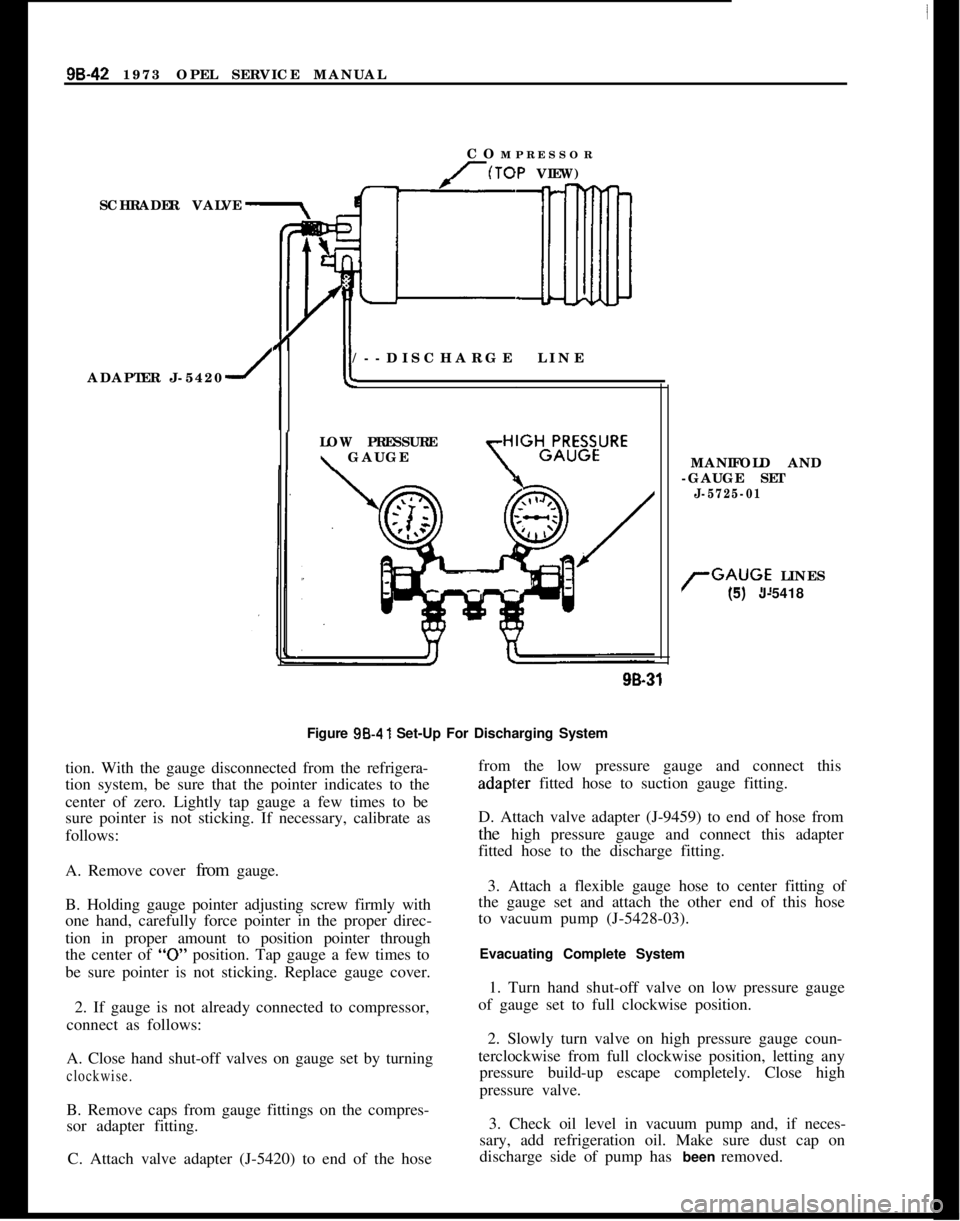
98-42 1973 OPEL SERVICE MANUAL
SCHRADER VALVE
ADAPTER J-54201COMPRESSOR(TOP VIEW)[/--DISCHARGE LINE
ILOW PRESSURE\ GAUGE
MANIFOLD AND
-GAUGE SET
J-5725-01
rGAUGE LINES
(5) J-541899-31
Figure 98.41 Set-Up For Discharging System
tion. With the gauge disconnected from the refrigera-
tion system, be sure that the pointer indicates to the
center of zero. Lightly tap gauge a few times to be
sure pointer is not sticking. If necessary, calibrate as
follows:
A. Remove cover from gauge.
B. Holding gauge pointer adjusting screw firmly with
one hand, carefully force pointer in the proper direc-
tion in proper amount to position pointer through
the center of
“0” position. Tap gauge a few times to
be sure pointer is not sticking. Replace gauge cover.
2. If gauge is not already connected to compressor,
connect as follows:
A. Close hand shut-off valves on gauge set by turning
clockwise.B. Remove caps from gauge fittings on the compres-
sor adapter fitting.
C. Attach valve adapter (J-5420) to end of the hosefrom the low pressure gauge and connect thisadapl:er fitted hose to suction gauge fitting.
D. Attach valve adapter (J-9459) to end of hose from
the high pressure gauge and connect this adapter
fitted hose to the discharge fitting.
3. Attach a flexible gauge hose to center fitting of
the gauge set and attach the other end of this hose
to vacuum pump (J-5428-03).
Evacuating Complete System
1. Turn hand shut-off valve on low pressure gauge
of gauge set to full clockwise position.
2. Slowly turn valve on high pressure gauge coun-
terclockwise from full clockwise position, letting any
pressure build-up escape completely. Close high
pressure valve.
3. Check oil level in vacuum pump and, if neces-
sary, add refrigeration oil. Make sure dust cap on
discharge side of pump has been removed.