RENAULT KANGOO 1998 KC / 1.G Heating And Ventilation Repair Manual
KANGOO 1998 KC / 1.G
RENAULT
RENAULT
https://www.carmanualsonline.info/img/7/1738/w960_1738-0.png
RENAULT KANGOO 1998 KC / 1.G Heating And Ventilation Repair Manual
Trending: seats, engine oil, oil capacity, steering wheel, air conditioning, air bleeding, coolant
Page 51 of 73
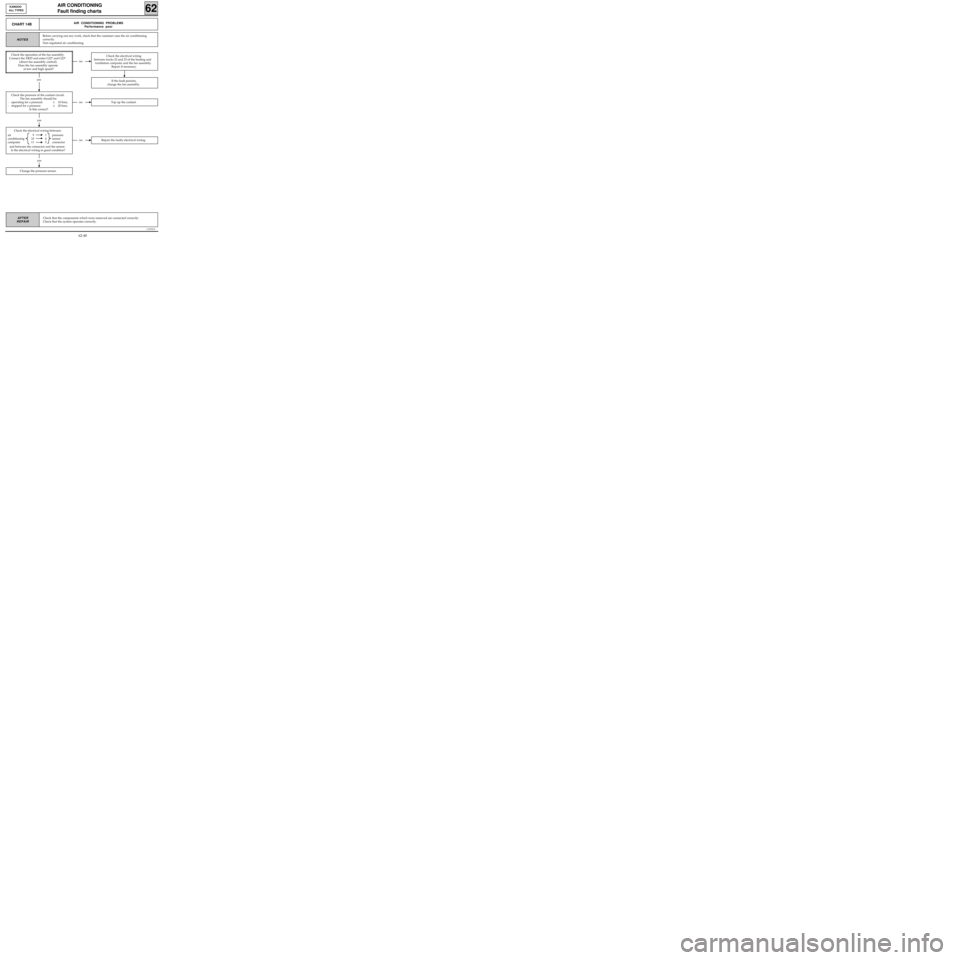
Check the electrical wiring between:
air 9 1 pressure
conditioning 10 4 sensor
computer 11 5 connector
and between the connector and the sensor.
Is the electrical wiring in good condition?
c11010.0
AIR CONDITIONING
Fault finding charts
62
KANGOO
ALL TYPES
AFTER
REPAIR
yes
CHART 14BAIR CONDITIONING PROBLEMS
Performance poor
NOTES
no
yes
noRepair the faulty electrical wiring.
yes
noTop up the coolant.
Change the pressure sensor.
Before carrying out any work, check that the customer uses the air conditioning
correctly.
Non regulated air conditioning.
Check the operation of the fan assembly.
Connect the XR25 and enter G22* and G23*
(direct fan assembly control).
Does the fan assembly operate
at low and high speed?
Check the pressure of the coolant circuit.
The fan assembly should be:
- operating for a pressure≥ 10 bars,
- stopped for a pressure≥ 20 bars.
Is this correct?
Check the electrical wiring
between tracks 22 and 23 of the heating and
ventilation computer and the fan assembly.
Repair if necessary.
If the fault persists,
change the fan assembly.
Check that the components which were removed are connected correctly.
Check that the system operates correctly.
62-40
Page 52 of 73
Check the continuity and insulation from 12
volts of the electrical wiring
between:
air 22 F2 low speed
conditioning relay
computer 23 M2 high speed
relay
Is the wiring in good condition?
c11010.0
AIR CONDITIONING
Fault finding charts
62
KANGOO
ALL TYPES
AFTER
REPAIR
CHART 15COOLING FAN DOES NOT OPERATE
NOTES
yes
noRepair the faulty
electrical wiring.
noChange the faulty relay(s).
yes
noRepair.
yes
A
Non regulated air conditioning.
The compressor operates.
Check the condition of the fuses.
Change them if necessary.
Check that 12 volts is present on track 5 of the
low speed and high speed relays.
Is this correct?
Check that the fan assembly is correctly
supplied with 12 volts and 0 volt.
Is this correct?
Check that the components which were removed are connected correctly.
Check that the system operates correctly.
62-41
Page 53 of 73
yes
Check the electrical wiring between:
heating and 9 1 inter-
ventilation 10 4 mediate
computer 11 3 connector
and between:
inter- 1 A pressure
mediate 4 C sensor
connector 3 B
Is the wiring in good condition?
c11010.0
AIR CONDITIONING
Fault finding charts
62
KANGOO
ALL TYPES
AFTER
REPAIR
CHART 15
CONT
A
noTop up the coolant circuit.
yes
noRepair the faulty
electrical wiring.
With the air conditioning selected and
ventilation on maximum, check the pressure
of the coolant circuit using the XR25 by
entering #16.
- The fan cuts in at low speed for a pressure
≥ 10 bars,
- The fan cuts in at high speed for a pressure
≥ 20 bars.
Are the pressure values correct?
Change the pressure sensor.
If the fault persists,
change the fan.
Check that the components which were removed are connected correctly.
Check that the system operates correctly.
62-42
Page 54 of 73
c11010.0
AIR CONDITIONING
Fault finding - Associated checks
62
KANGOO
ALL TYPES
COMMAND MODE G--*
To use this function, enter G on the XR25 keypad, then the number of the command selected followed by
an asterisk.
G21* : compressor clutch control
G22* : fan low speed control
G23* : fan high speed control
G24* : recirculation motor control
G13* : end of fault finding
COMMAND MODE #
# 08 : fan assembly speed
# 15 : engine speed
# 16 : pressure of coolant in the circuit
62-43
Page 55 of 73
AIR CONDITIONING
Wiring diagram
62D7F ENGINE
PRO13781
62-44
Page 56 of 73
AIR CONDITIONING
Wiring diagram
62F8Q ENGINE
PRO13948
62-45
Page 57 of 73
AIR CONDITIONING
Wiring diagram
62E7J ENGINE
PRO14441
62-46
Page 58 of 73
AIR CONDITIONING
Wiring diagram
62
D7F/F8Q and E7J
ENGINES
120 Injection computer
171 Air conditioning clutch
206 Air control pressure switch
225 Diagnostic socket
234 Fan assembly relay
236 Fuel pump relay
248 Fan assembly thermal switch
260 Fuse box
319 Air conditioning control panel
320 Base fan assembly/Air conditioning
419 Air conditioning control unit
466 Shunt box
597 Engine fuse box
700 Cooling fan relay (low speed)
R67 Front of engine/Engine
NB : Evaporator sensor (depending on assembly)
62-47
Page 59 of 73
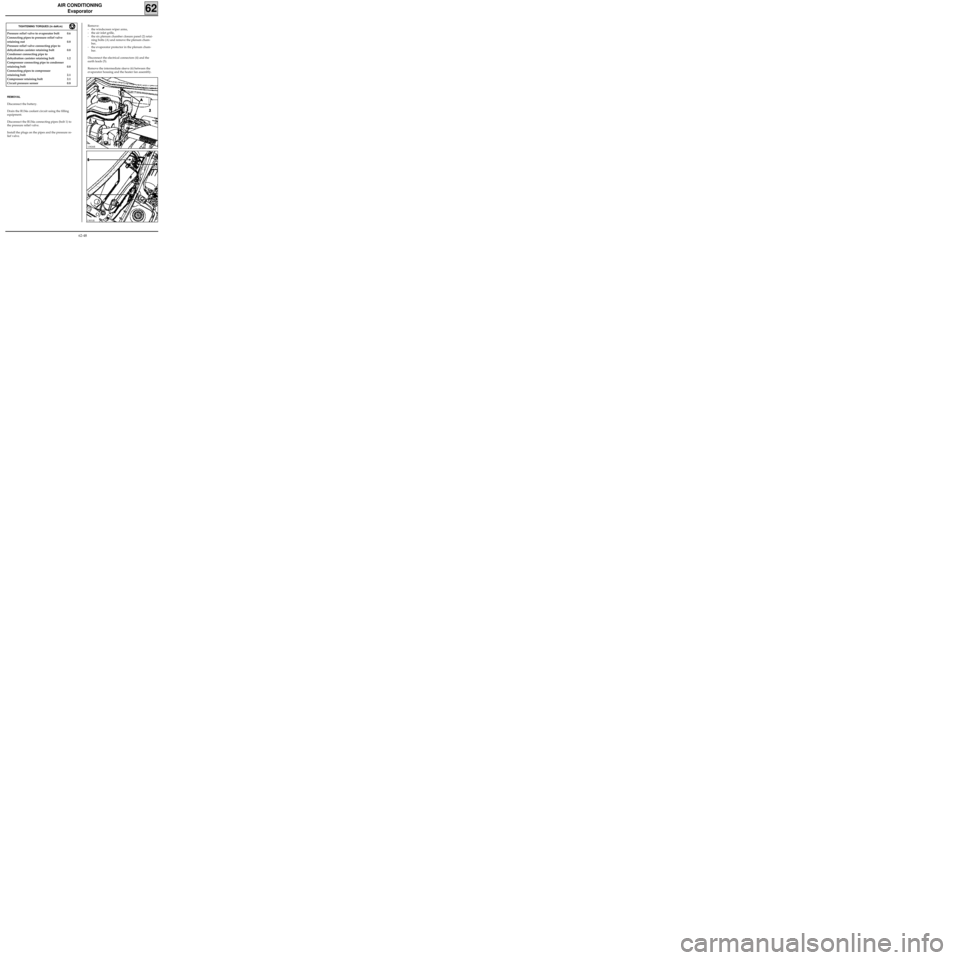
TIGHTENING TORQUES (in daN.m)
AIR CONDITIONING
Evaporator
62
13831R
Pressure relief valve to evaporator bolt 0.6
Connecting pipes to pressure relief valve
retaining nut 0.8
Pressure relief valve connecting pipe to
dehydration canister retaining bolt 0.8
Condenser connecting pipe to
dehydration canister retaining bolt 1.2
Compressor connecting pipe to condenser
retaining bolt 0.8
Connecting pipes to compressor
retaining bolt 2.1
Compressor retaining bolt 2.1
Circuit pressure sensor 0.8
REMOVAL
Disconnect the battery.
Drain the R134a coolant circuit using the filling
equipment.
Disconnect the R134a connecting pipes (bolt 1) to
the pressure relief valve.
Install the plugs on the pipes and the pressure re-
lief valve.Remove:
- the windscreen wiper arms,
- the air inlet grille,
- the six plenum chamber closure panel (2) retai-
ning bolts (A) and remove the plenum cham-
ber,
- the evaporator protector in the plenum cham-
ber.
Disconnect the electrical connectors (4) and the
earth leads (5).
Remove the intermediate sleeve (6) between the
evaporator housing and the heater fan assembly.
13826R
62-48
Page 60 of 73
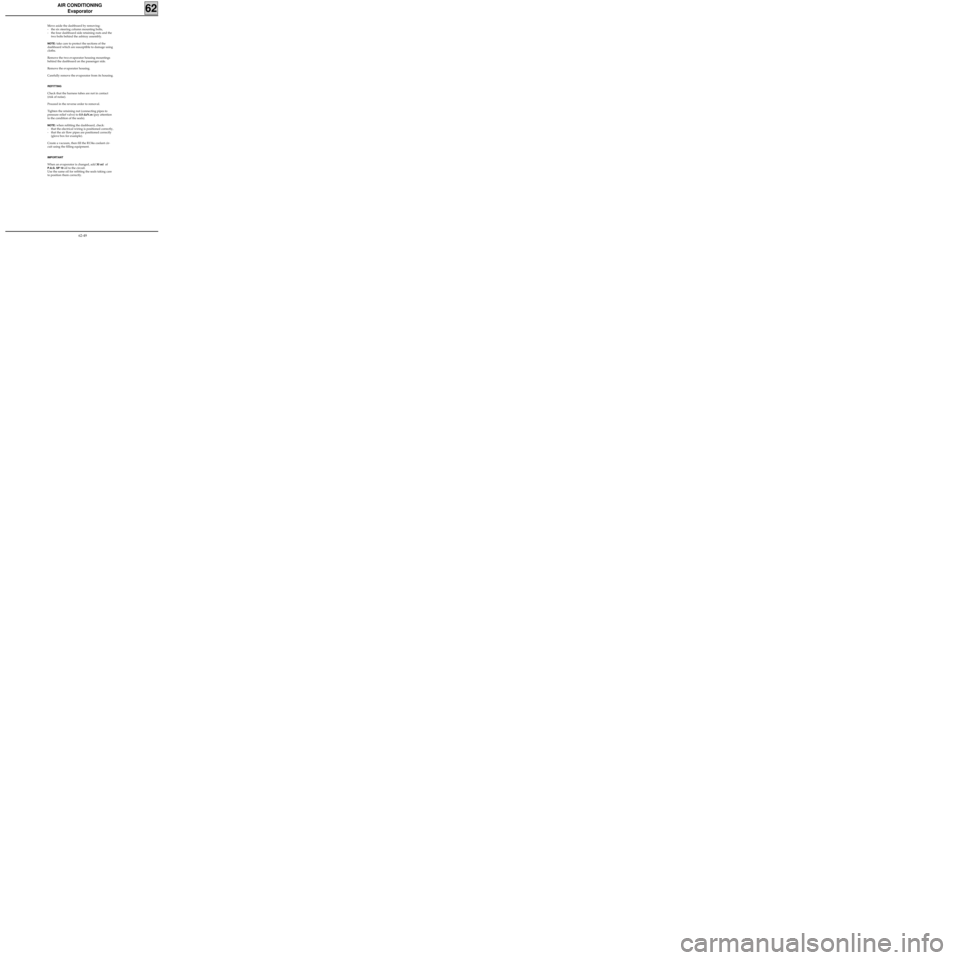
AIR CONDITIONING
Evaporator
62
Move aside the dashboard by removing:
- the six steering column mounting bolts,
- the four dashboard side retaining nuts and the
two bolts behind the ashtray assembly.
NOTE: take care to protect the sections of the
dashboard which are susceptible to damage using
cloths.
Remove the two evaporator housing mountings
behind the dashboard on the passenger side.
Remove the evaporator housing.
Carefully remove the evaporator from its housing.
REFITTING
Check that the harness tubes are not in contact
(risk of noise).
Proceed in the reverse order to removal.
Tighten the retaining nut (connecting pipes to
pressure relief valve) to 0.8 daN.m (pay attention
to the condition of the seals).
NOTE: when refitting the dashboard, check:
- that the electrical wiring is positioned correctly,
- that the air flow pipes are positioned correctly
(glove box for example).
Create a vacuum, then fill the R134a coolant cir-
cuit using the filling equipment.
IMPORTANT
When an evaporator is changed, add 30 ml of
P.A.G. SP 10 oil to the circuit.
Use the same oil for refitting the seals taking care
to position them correctly.
62-49
Trending: oil capacity, service, display, fuse chart, open bonnet, ABS, belt