check engine RENAULT SCENIC 2000 J64 / 1.G Technical Note 3426A User Guide
[x] Cancel search | Manufacturer: RENAULT, Model Year: 2000, Model line: SCENIC, Model: RENAULT SCENIC 2000 J64 / 1.GPages: 118, PDF Size: 1.5 MB
Page 28 of 118
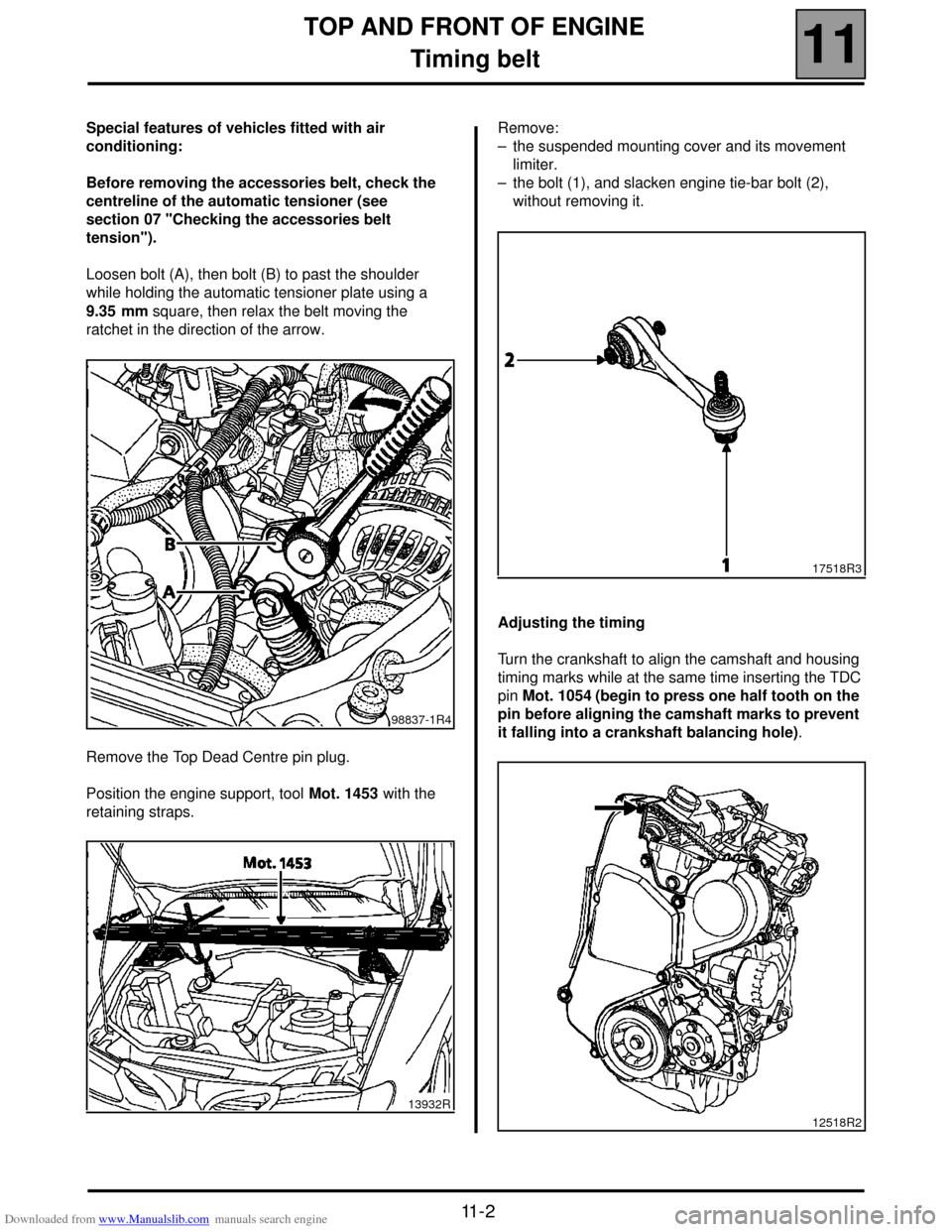
Downloaded from www.Manualslib.com manuals search engine TOP AND FRONT OF ENGINE
Timing belt
11
11 - 2
Special features of vehicles fitted with air
conditioning:
Before removing the accessories belt, check the
centreline of the automatic tensioner (see
section 07 "Checking the accessories belt
tension").
Loosen bolt (A), then bolt (B) to past the shoulder
while holding the automatic tensioner plate using a
9.35 mm square, then relax the belt moving the
ratchet in the direction of the arrow.
Remove the Top Dead Centre pin plug.
Position the engine support, tool Mot. 1453 with the
retaining straps.Remove:
– the suspended mounting cover and its movement
limiter.
– the bolt (1), and slacken engine tie-bar bolt (2),
without removing it.
Adjusting the timing
Turn the crankshaft to align the camshaft and housing
timing marks while at the same time inserting the TDC
pin Mot. 1054 (begin to press one half tooth on the
pin before aligning the camshaft marks to prevent
it falling into a crankshaft balancing hole).
98837-1R4
13932R
17518R3
12518R2
Page 29 of 118
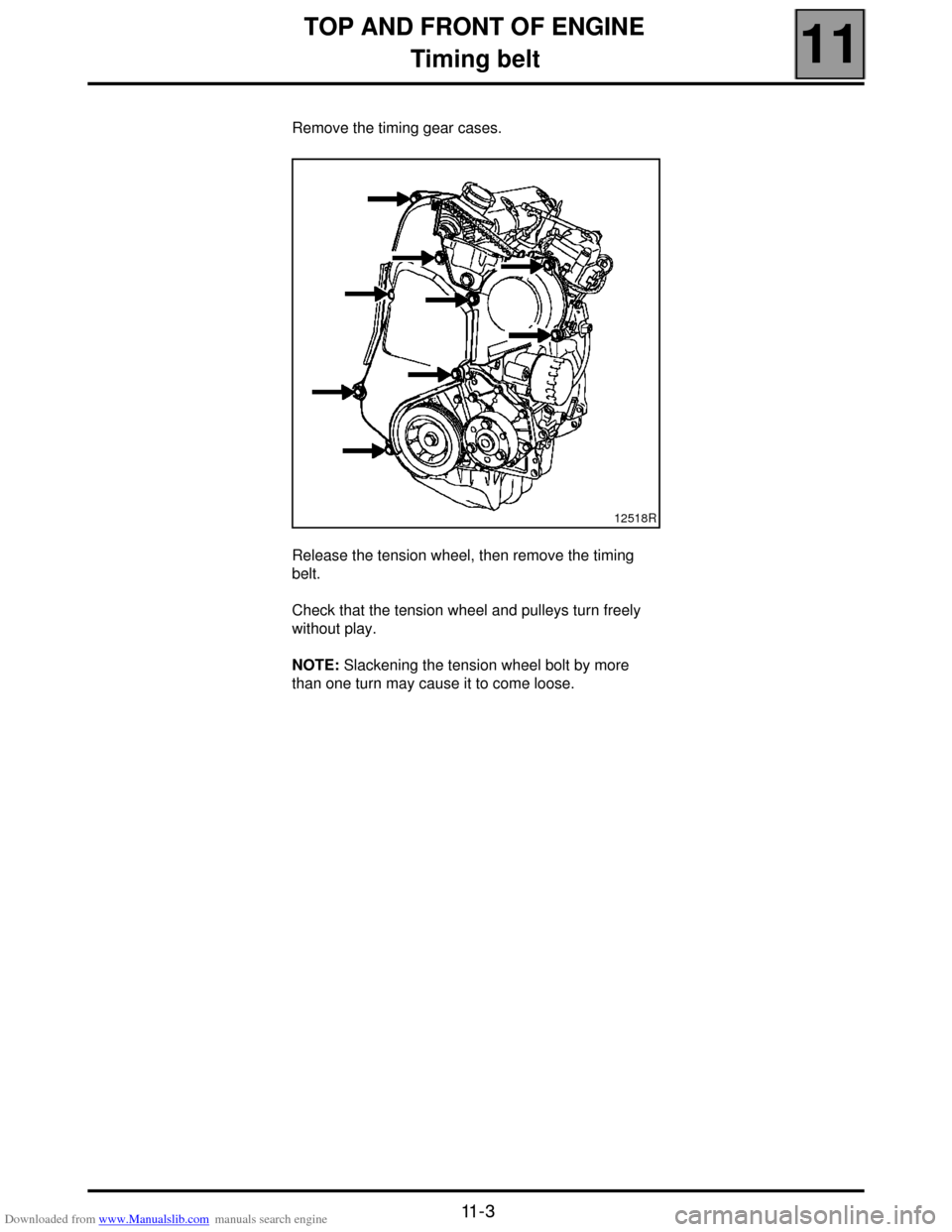
Downloaded from www.Manualslib.com manuals search engine TOP AND FRONT OF ENGINE
Timing belt
11
11 - 3
Remove the timing gear cases.
Release the tension wheel, then remove the timing
belt.
Check that the tension wheel and pulleys turn freely
without play.
NOTE: Slackening the tension wheel bolt by more
than one turn may cause it to come loose.
12518R
Page 30 of 118
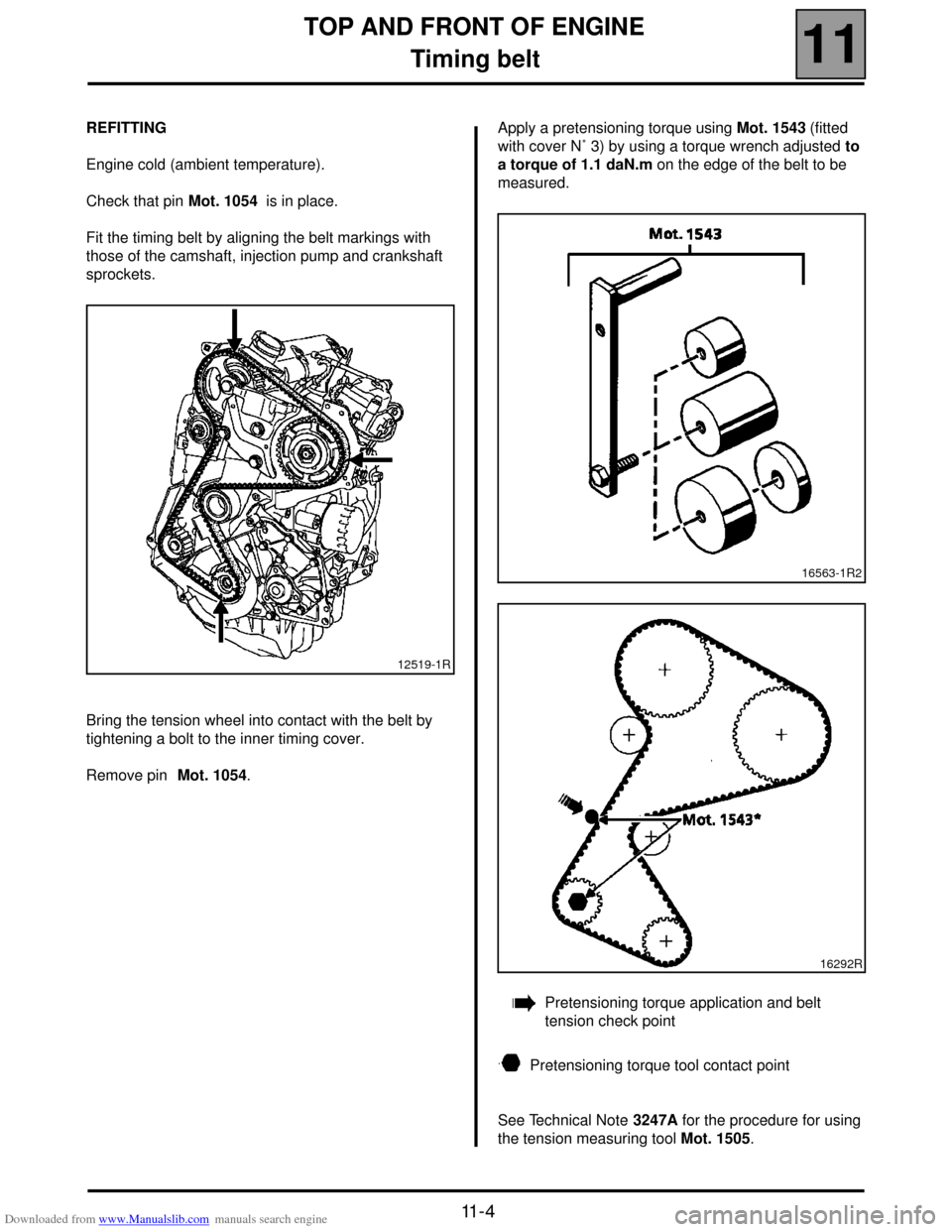
Downloaded from www.Manualslib.com manuals search engine TOP AND FRONT OF ENGINE
Timing belt
11
11 - 4
REFITTING
Engine cold (ambient temperature).
Check that pin Mot. 1054 is in place.
Fit the timing belt by aligning the belt markings with
those of the camshaft, injection pump and crankshaft
sprockets.
Bring the tension wheel into contact with the belt by
tightening a bolt to the inner timing cover.
Remove pin Mot. 1054.Apply a pretensioning torque using Mot. 1543 (fitted
with cover N˚ 3) by using a torque wrench adjusted to
a torque of 1.1 daN.m on the edge of the belt to be
measured.
Pretensioning torque application and belt
tension check point
Pretensioning torque tool contact point
See Technical Note 3247A for the procedure for using
the tension measuring tool Mot. 1505.
12519-1R
16563-1R2
16292R
Page 32 of 118
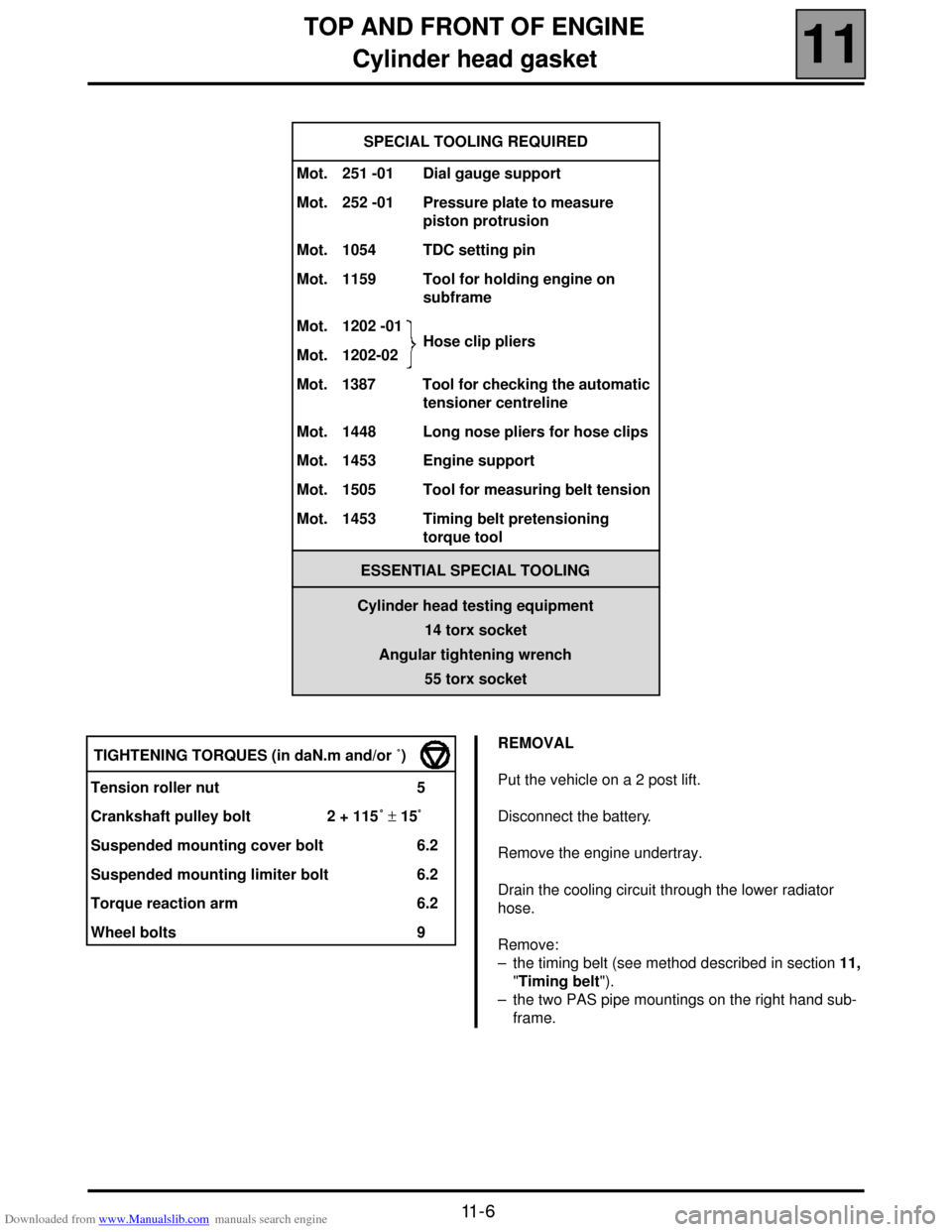
Downloaded from www.Manualslib.com manuals search engine TOP AND FRONT OF ENGINE
Cylinder head gasket
11
11 - 6
Cylinder head gasket
SPECIAL TOOLING REQUIRED
Mot. 251 -01 Dial gauge support
Mot. 252 -01 Pressure plate to measure
piston protrusion
Mot. 1054 TDC setting pin
Mot. 1159 Tool for holding engine on
subframe
Mot. 1202 -01
Hose clip pliers
Mot. 1202-02
Mot. 1387 Tool for checking the automatic
tensioner centreline
Mot. 1448 Long nose pliers for hose clips
Mot. 1453 Engine support
Mot. 1505 Tool for measuring belt tension
Mot. 1453 Timing belt pretensioning
torque tool
ESSENTIAL SPECIAL TOOLING
Cylinder head testing equipment
14 torx socket
Angular tightening wrench
55 torx socket
REMOVAL
Put the vehicle on a 2 post lift.
Disconnect the battery.
Remove the engine undertray.
Drain the cooling circuit through the lower radiator
hose.
Remove:
– the timing belt (see method described in section 11,
"Timing belt").
– the two PAS pipe mountings on the right hand sub-
frame. TIGHTENING TORQUES (in daN.m and/or ˚)
Tension roller nut 5
Crankshaft pulley bolt 2 + 115˚ ± 15˚
Suspended mounting cover bolt 6.2
Suspended mounting limiter bolt 6.2
Torque reaction arm 6.2
Wheel bolts 9
Page 37 of 118
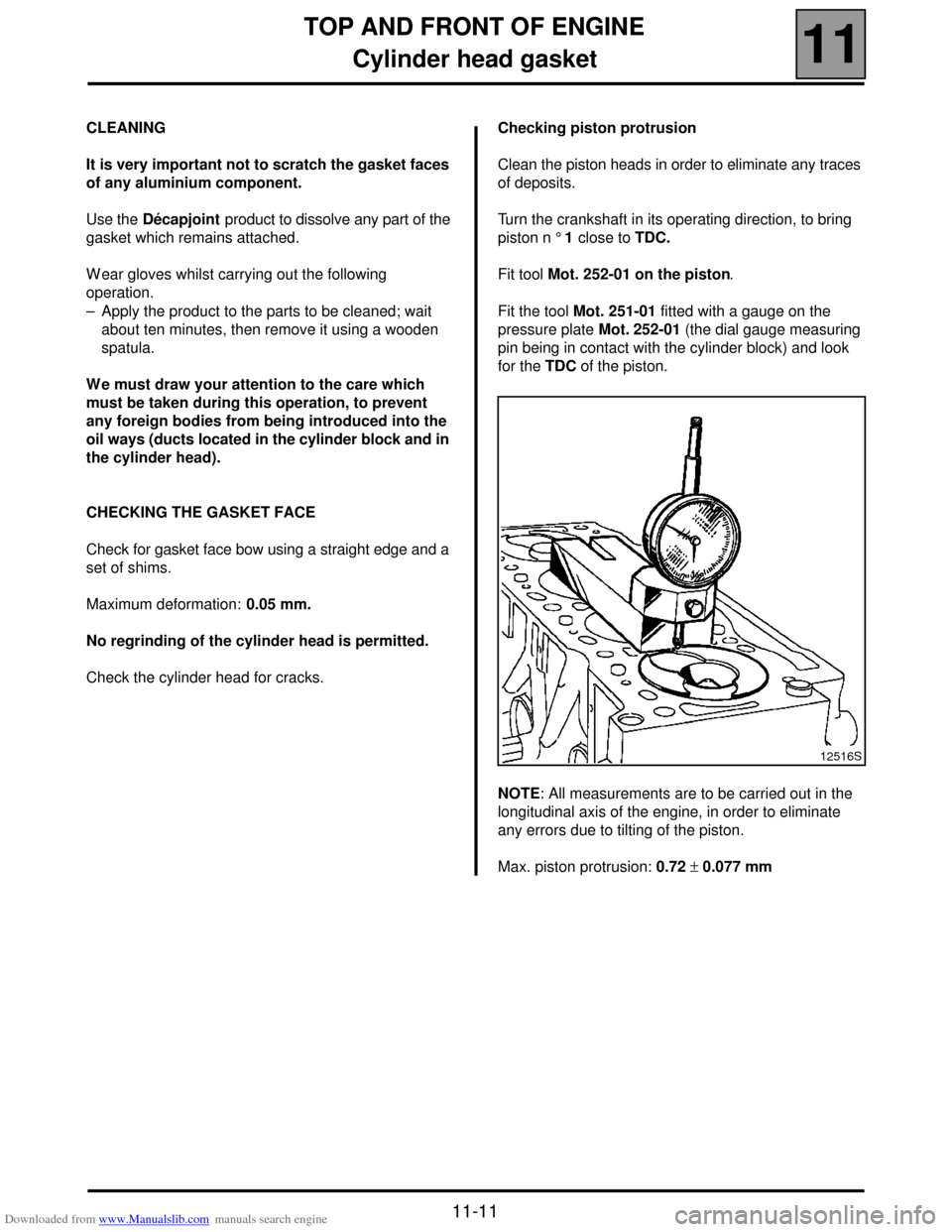
Downloaded from www.Manualslib.com manuals search engine TOP AND FRONT OF ENGINE
Cylinder head gasket
11
11-11
CLEANING
It is very important not to scratch the gasket faces
of any aluminium component.
Use the Décapjoint product to dissolve any part of the
gasket which remains attached.
W ear gloves whilst carrying out the following
operation.
– Apply the product to the parts to be cleaned; wait
about ten minutes, then remove it using a wooden
spatula.
W e must draw your attention to the care which
must be taken during this operation, to prevent
any foreign bodies from being introduced into the
oil ways (ducts located in the cylinder block and in
the cylinder head).
CHECKING THE GASKET FACE
Check for gasket face bow using a straight edge and a
set of shims.
Maximum deformation: 0.05 mm.
No regrinding of the cylinder head is permitted.
Check the cylinder head for cracks.Checking piston protrusion
Clean the piston heads in order to eliminate any traces
of deposits.
Turn the crankshaft in its operating direction, to bring
piston n ° 1 close to TDC.
Fit tool Mot. 252-01 on the piston.
Fit the tool Mot. 251-01 fitted with a gauge on the
pressure plate Mot. 252-01 (the dial gauge measuring
pin being in contact with the cylinder block) and look
for the TDC of the piston.
NOTE: All measurements are to be carried out in the
longitudinal axis of the engine, in order to eliminate
any errors due to tilting of the piston.
Max. piston protrusion: 0.72 ± 0.077 mm
12516S
Page 41 of 118
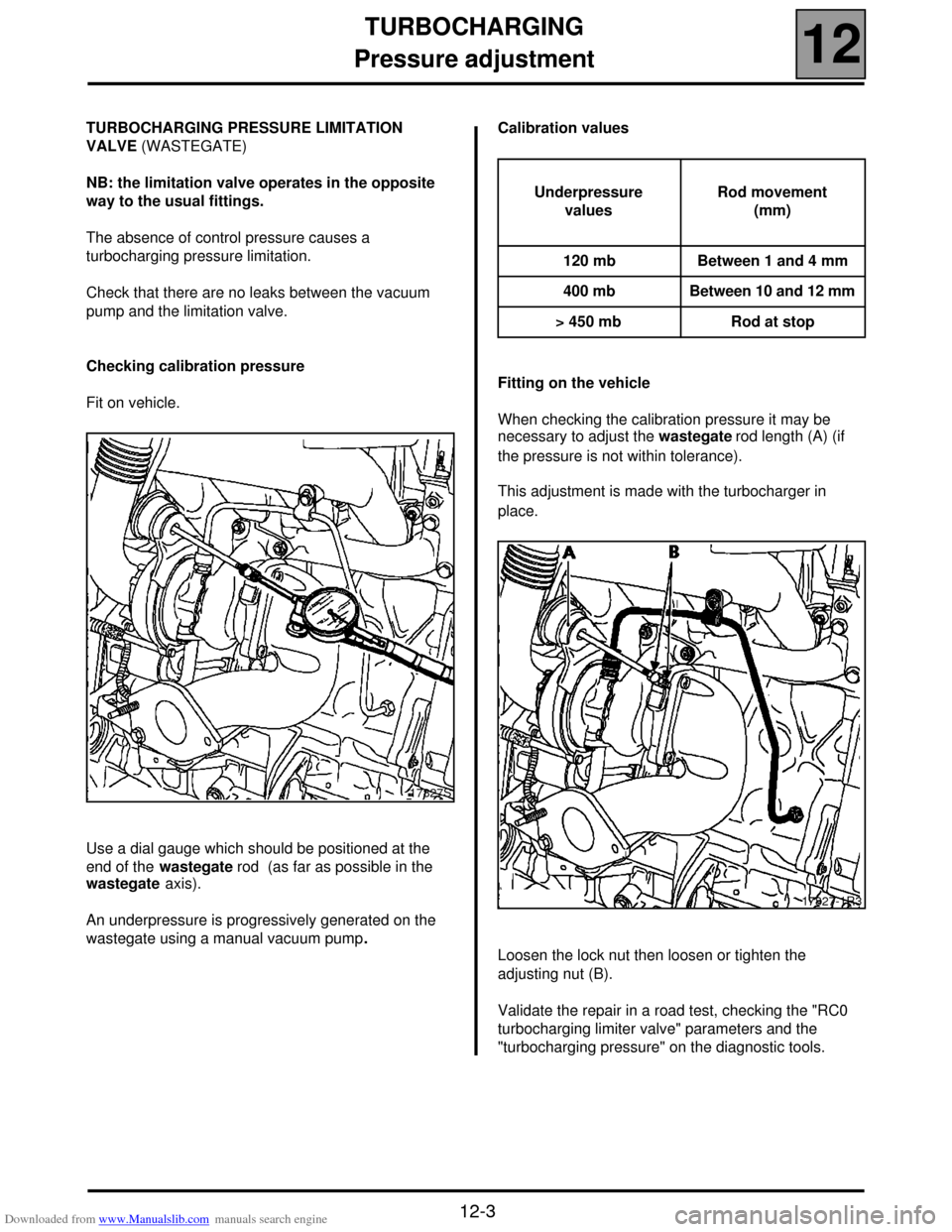
Downloaded from www.Manualslib.com manuals search engine TURBOCHARGING
Pressure adjustment
12
12-3
Pressure adjustment
TURBOCHARGING PRESSURE LIMITATION
VALVE (WASTEGATE)
NB: the limitation valve operates in the opposite
way to the usual fittings.
The absence of control pressure causes a
turbocharging pressure limitation.
Check that there are no leaks between the vacuum
pump and the limitation valve.
Checking calibration pressure
Fit on vehicle.
Use a dial gauge which should be positioned at the
end of the wastegate rod (as far as possible in the
wastegate axis).
An underpressure is progressively generated on the
wastegate using a manual vacuum pump.Calibration values
Fitting on the vehicle
When checking the calibration pressure it may be
necessary to adjust the wastegate rod length (A) (if
the pressure is not within tolerance).
This adjustment is made with the turbocharger in
place.
Loosen the lock nut then loosen or tighten the
adjusting nut (B).
Validate the repair in a road test, checking the "RC0
turbocharging limiter valve" parameters and the
"turbocharging pressure" on the diagnostic tools.
17827S
Underpressure
valuesRod movement
(mm)
120 mb Between 1 and 4 mm
400 mb Between 10 and 12 mm
> 450 mb Rod at stop
17827-1R3
Page 44 of 118
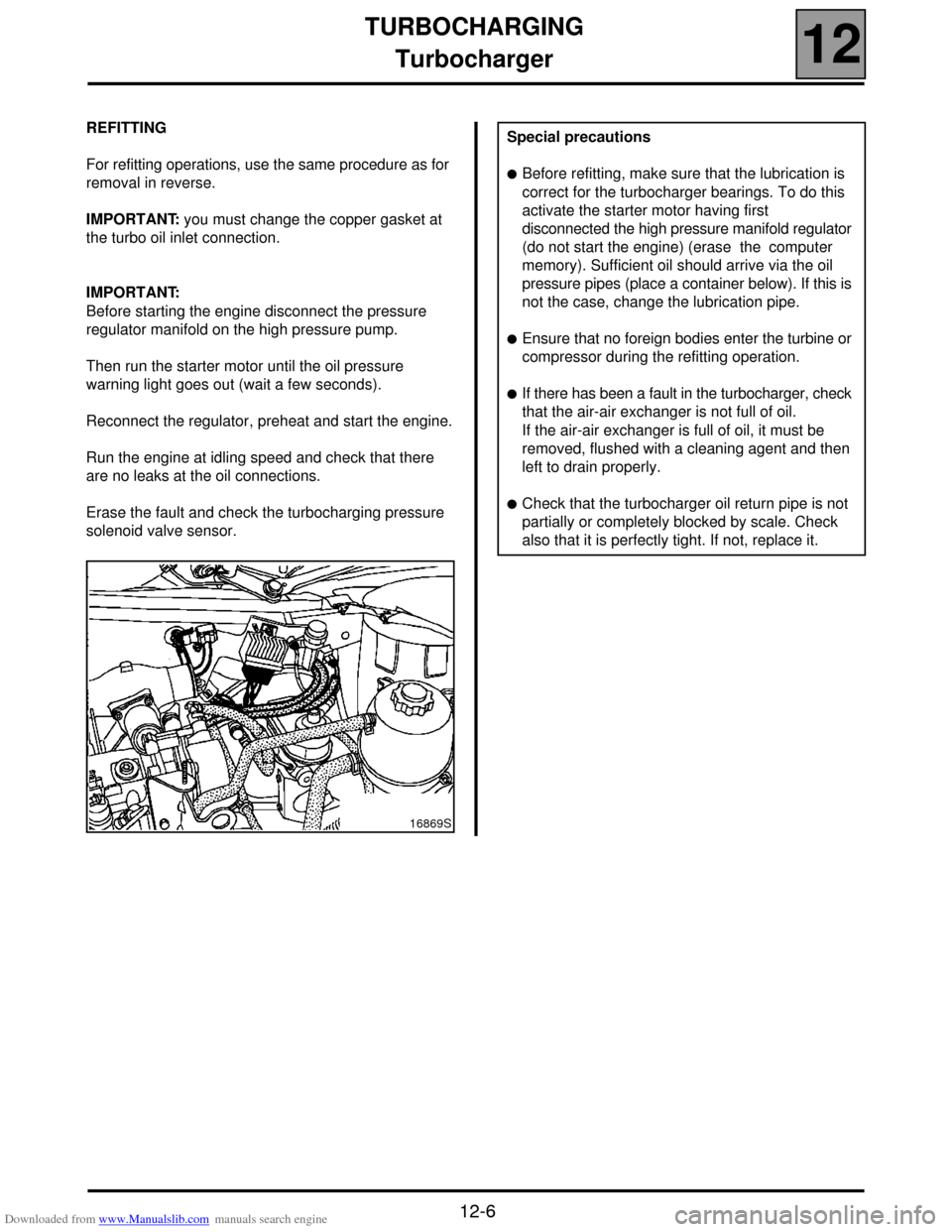
Downloaded from www.Manualslib.com manuals search engine TURBOCHARGING
Turbocharger
12
12-6
REFITTING
For refitting operations, use the same procedure as for
removal in reverse.
IMPORTANT: you must change the copper gasket at
the turbo oil inlet connection.
IMPORTANT:
Before starting the engine disconnect the pressure
regulator manifold on the high pressure pump.
Then run the starter motor until the oil pressure
warning light goes out (wait a few seconds).
Reconnect the regulator, preheat and start the engine.
Run the engine at idling speed and check that there
are no leaks at the oil connections.
Erase the fault and check the turbocharging pressure
solenoid valve sensor.
16869S
Special precautions
!Before refitting, make sure that the lubrication is
correct for the turbocharger bearings. To do this
activate the starter motor having first
disconnected the high pressure manifold regulator
(do not start the engine) (erase the computer
memory). Sufficient oil should arrive via the oil
pressure pipes (place a container below). If this is
not the case, change the lubrication pipe.
!Ensure that no foreign bodies enter the turbine or
compressor during the refitting operation.
!If there has been a fault in the turbocharger, check
that the air-air exchanger is not full of oil.
If the air-air exchanger is full of oil, it must be
removed, flushed with a cleaning agent and then
left to drain properly.
!Check that the turbocharger oil return pipe is not
partially or completely blocked by scale. Check
also that it is perfectly tight. If not, replace it.
Page 55 of 118
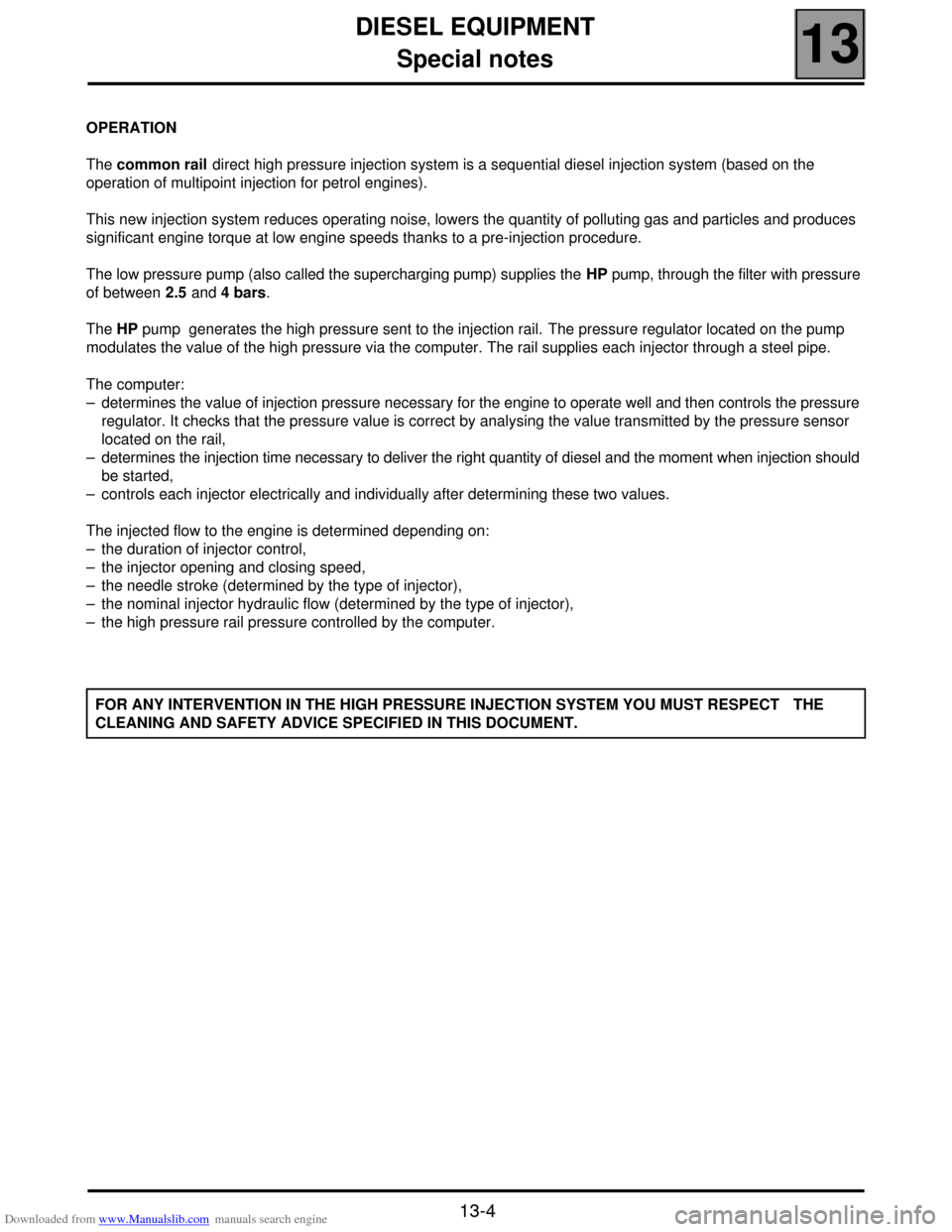
Downloaded from www.Manualslib.com manuals search engine DIESEL EQUIPMENT
Special notes
13
13-4
OPERATION
The common rail direct high pressure injection system is a sequential diesel injection system (based on the
operation of multipoint injection for petrol engines).
This new injection system reduces operating noise, lowers the quantity of polluting gas and particles and produces
significant engine torque at low engine speeds thanks to a pre-injection procedure.
The low pressure pump (also called the supercharging pump) supplies the HP pump, through the filter with pressure
of between 2.5 and 4 bars.
The HP pump generates the high pressure sent to the injection rail. The pressure regulator located on the pump
modulates the value of the high pressure via the computer. The rail supplies each injector through a steel pipe.
The computer:
– determines the value of injection pressure necessary for the engine to operate well and then controls the pressure
regulator. It checks that the pressure value is correct by analysing the value transmitted by the pressure sensor
located on the rail,
– determines the injection time necessary to deliver the right quantity of diesel and the moment when injection should
be started,
– controls each injector electrically and individually after determining these two values.
The injected flow to the engine is determined depending on:
– the duration of injector control,
– the injector opening and closing speed,
– the needle stroke (determined by the type of injector),
– the nominal injector hydraulic flow (determined by the type of injector),
– the high pressure rail pressure controlled by the computer.
FOR ANY INTERVENTION IN THE HIGH PRESSURE INJECTION SYSTEM YOU MUST RESPECT THE
CLEANING AND SAFETY ADVICE SPECIFIED IN THIS DOCUMENT.
Page 56 of 118
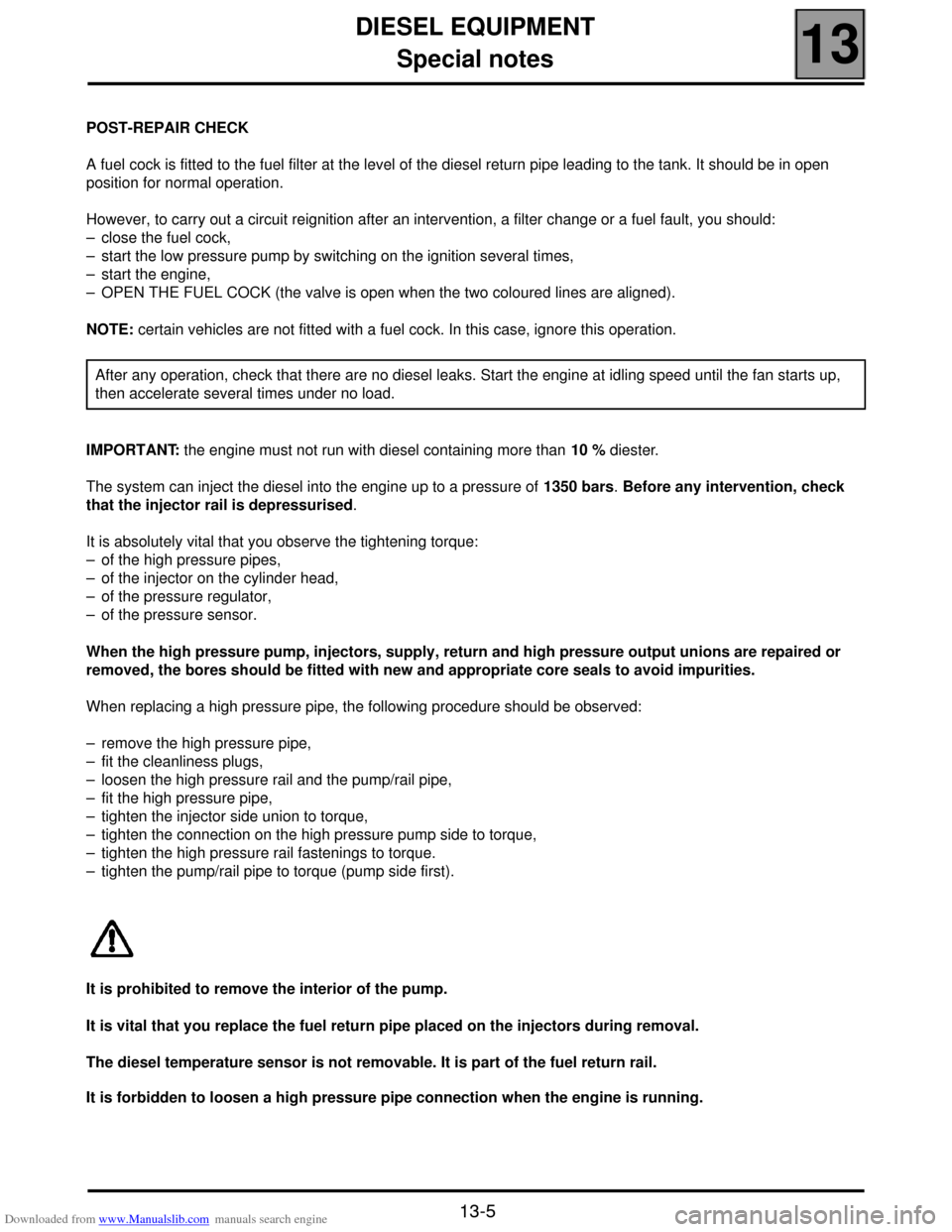
Downloaded from www.Manualslib.com manuals search engine DIESEL EQUIPMENT
Special notes
13
13-5
POST-REPAIR CHECK
A fuel cock is fitted to the fuel filter at the level of the diesel return pipe leading to the tank. It should be in open
position for normal operation.
However, to carry out a circuit reignition after an intervention, a filter change or a fuel fault, you should:
– close the fuel cock,
– start the low pressure pump by switching on the ignition several times,
– start the engine,
– OPEN THE FUEL COCK (the valve is open when the two coloured lines are aligned).
NOTE: certain vehicles are not fitted with a fuel cock. In this case, ignore this operation.
IMPORTANT: the engine must not run with diesel containing more than 10 % diester.
The system can inject the diesel into the engine up to a pressure of 1350 bars. Before any intervention, check
that the injector rail is depressurised.
It is absolutely vital that you observe the tightening torque:
– of the high pressure pipes,
– of the injector on the cylinder head,
– of the pressure regulator,
– of the pressure sensor.
When the high pressure pump, injectors, supply, return and high pressure output unions are repaired or
removed, the bores should be fitted with new and appropriate core seals to avoid impurities.
When replacing a high pressure pipe, the following procedure should be observed:
– remove the high pressure pipe,
– fit the cleanliness plugs,
– loosen the high pressure rail and the pump/rail pipe,
– fit the high pressure pipe,
– tighten the injector side union to torque,
– tighten the connection on the high pressure pump side to torque,
– tighten the high pressure rail fastenings to torque.
– tighten the pump/rail pipe to torque (pump side first).
It is prohibited to remove the interior of the pump.
It is vital that you replace the fuel return pipe placed on the injectors during removal.
The diesel temperature sensor is not removable. It is part of the fuel return rail.
It is forbidden to loosen a high pressure pipe connection when the engine is running.After any operation, check that there are no diesel leaks. Start the engine at idling speed until the fan starts up,
then accelerate several times under no load.
Page 58 of 118
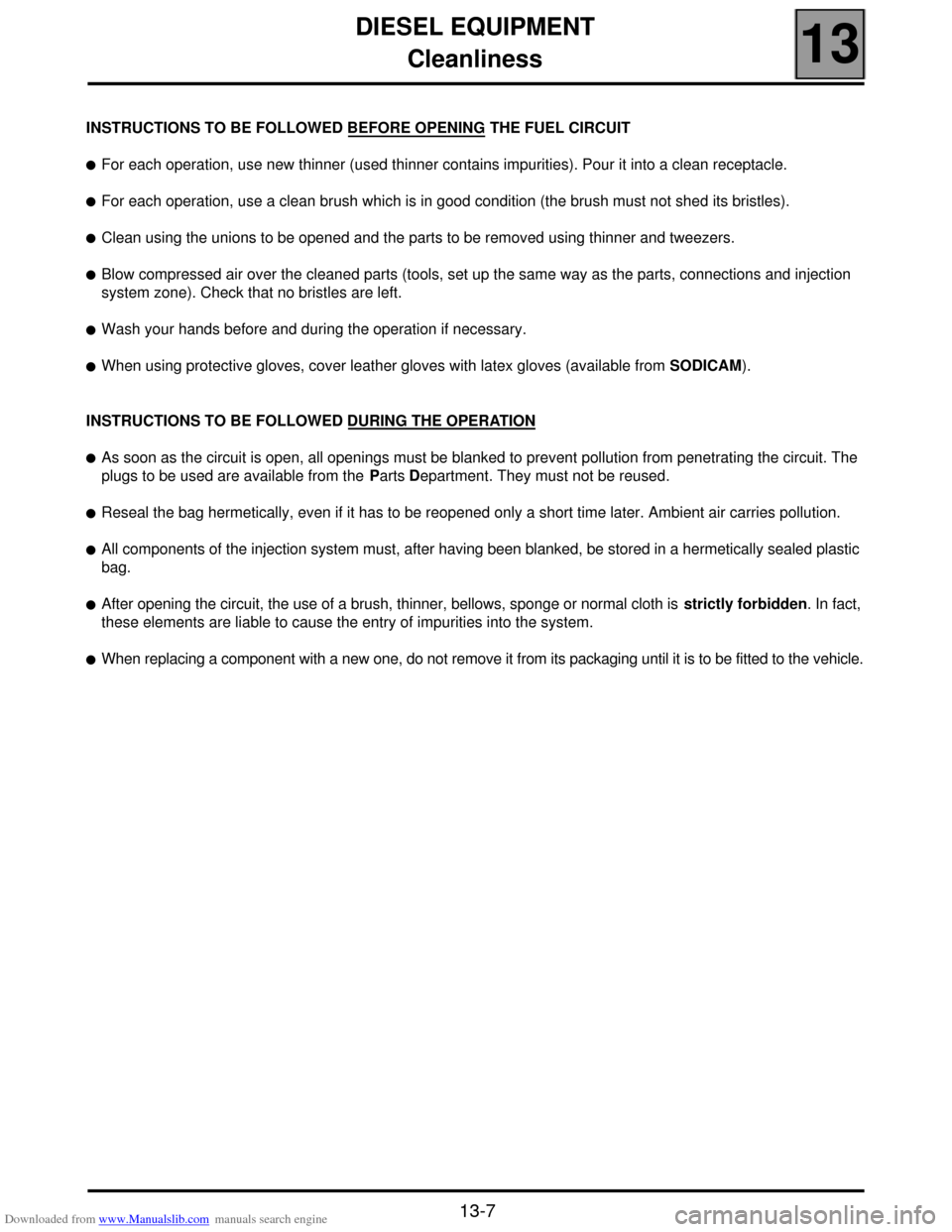
Downloaded from www.Manualslib.com manuals search engine DIESEL EQUIPMENT
Cleanliness
13
13-7
INSTRUCTIONS TO BE FOLLOWED BEFORE OPENING THE FUEL CIRCUIT
!For each operation, use new thinner (used thinner contains impurities). Pour it into a clean receptacle.
!For each operation, use a clean brush which is in good condition (the brush must not shed its bristles).
!Clean using the unions to be opened and the parts to be removed using thinner and tweezers.
!Blow compressed air over the cleaned parts (tools, set up the same way as the parts, connections and injection
system zone). Check that no bristles are left.
!Wash your hands before and during the operation if necessary.
!When using protective gloves, cover leather gloves with latex gloves (available from SODICAM).
INSTRUCTIONS TO BE FOLLOWED DURING THE OPERA
TION
!As soon as the circuit is open, all openings must be blanked to prevent pollution from penetrating the circuit. The
plugs to be used are available from the Parts Department. They must not be reused.
!Reseal the bag hermetically, even if it has to be reopened only a short time later. Ambient air carries pollution.
!All components of the injection system must, after having been blanked, be stored in a hermetically sealed plastic
bag.
!After opening the circuit, the use of a brush, thinner, bellows, sponge or normal cloth is strictly forbidden. In fact,
these elements are liable to cause the entry of impurities into the system.
!When replacing a component with a new one, do not remove it from its packaging until it is to be fitted to the vehicle.