ignition RENAULT SCENIC 2007 J84 / 2.G Automatic Transmission Siemens TA2005 Workshop Manual
[x] Cancel search | Manufacturer: RENAULT, Model Year: 2007, Model line: SCENIC, Model: RENAULT SCENIC 2007 J84 / 2.GPages: 139, PDF Size: 0.43 MB
Page 2 of 139
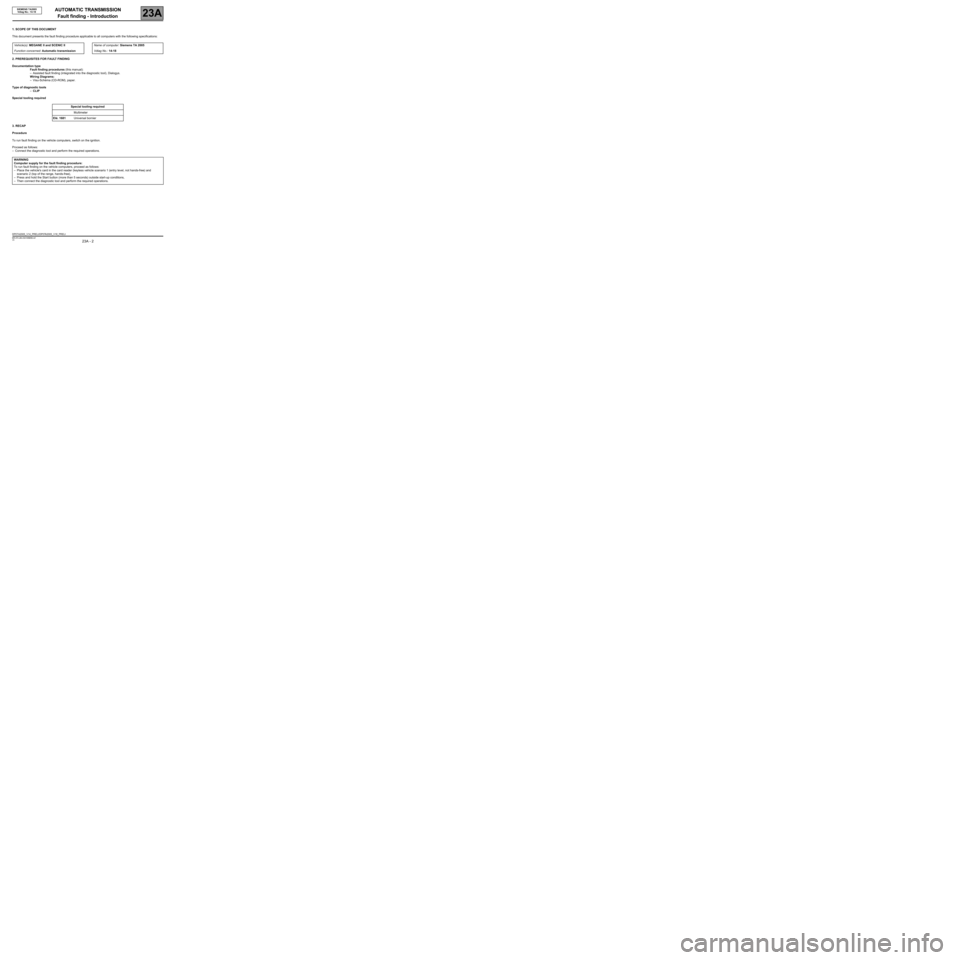
AUTOMATIC TRANSMISSION
Fault finding - Introduction
23A
23A - 2V5 MR-372-J84-23A100$058.mif
123A
SIEMENS TA2005
Vdiag No.: 14-18AUTOMATIC TRANSMISSION
Fault finding - Introduction
1. SCOPE OF THIS DOCUMENT
This document presents the fault finding procedure applicable to all computers with the following specifications:
2. PREREQUISITES FOR FAULT FINDING
Documentation type
Fault finding procedures (this manual):
–Assisted fault finding (integrated into the diagnostic tool), Dialogys.
Wiring Diagrams:
–Visu-Schéma (CD-ROM), paper.
Type of diagnostic tools
–CLIP
Special tooling required
3. RECAP
Procedure
To run fault finding on the vehicle computers, switch on the ignition.
Proceed as follows:
–Connect the diagnostic tool and perform the required operations. Vehicle(s): MEGANE II and SCENIC II
Function concerned: Automatic transmissionName of computer: Siemens TA 2005
Vdiag No.: 14-18
Special tooling required
Multimeter
Elé. 1681Universal bornier
WARNING
Computer supply for the fault finding procedure:
To run fault finding on the vehicle computers, proceed as follows:
–Place the vehicle's card in the card reader (keyless vehicle scenario 1 (entry level, not hands-free) and
scenario 2 (top of the range, hands-free),
–Press and hold the Start button (more than 5 seconds) outside start-up conditions,
–Then connect the diagnostic tool and perform the required operations.
DP0TA2005_V14_PRELI/DP0TA2005_V18_PRELI
MR-372-J84-23A100$058.mif
Page 3 of 139
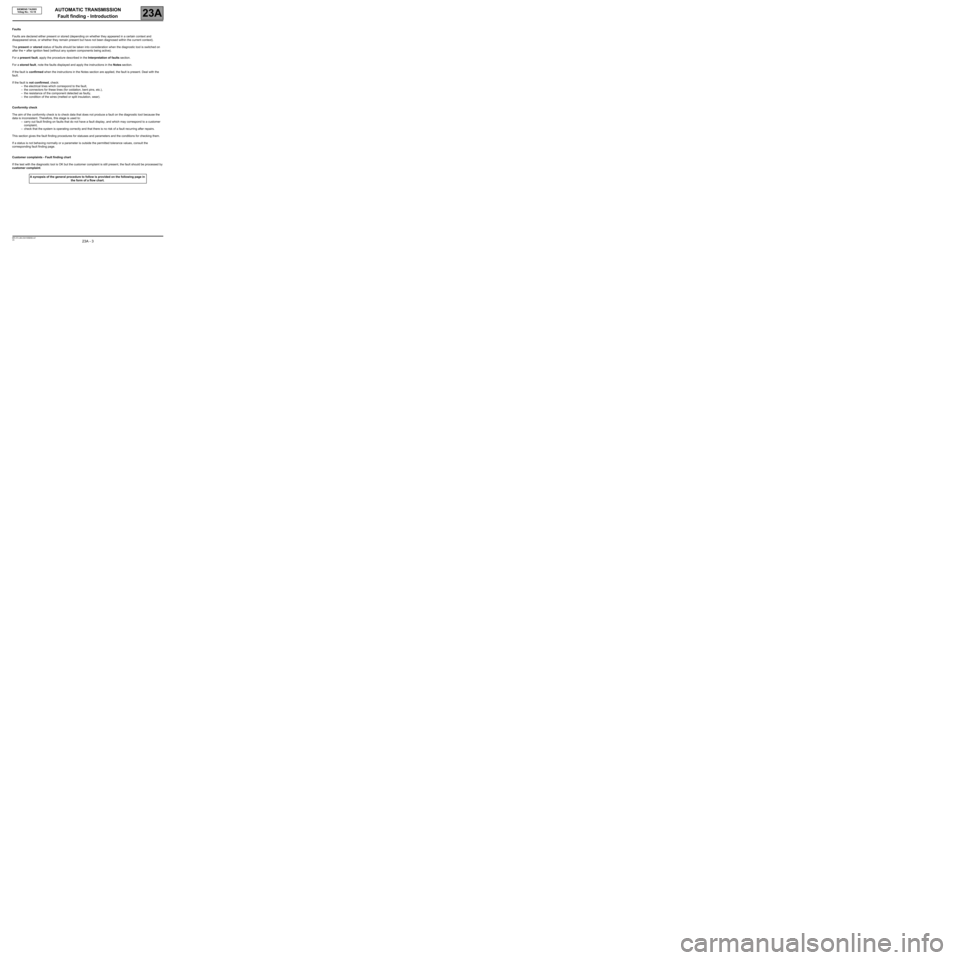
AUTOMATIC TRANSMISSION
Fault finding - Introduction
23A
23A - 3V5 MR-372-J84-23A100$058.mif
SIEMENS TA2005
Vdiag No.: 14-18
Faults
Faults are declared either present or stored (depending on whether they appeared in a certain context and
disappeared since, or whether they remain present but have not been diagnosed within the current context).
The present or stored status of faults should be taken into consideration when the diagnostic tool is switched on
after the + after ignition feed (without any system components being active).
For a present fault, apply the procedure described in the Interpretation of faults section.
For a stored fault, note the faults displayed and apply the instructions in the Notes section.
If the fault is confirmed when the instructions in the Notes section are applied, the fault is present. Deal with the
fault.
If the fault is not confirmed, check:
–the electrical lines which correspond to the fault,
–the connectors for these lines (for oxidation, bent pins, etc.),
–the resistance of the component detected as faulty,
–the condition of the wires (melted or split insulation, wear).
Conformity check
The aim of the conformity check is to check data that does not produce a fault on the diagnostic tool because the
data is inconsistent. Therefore, this stage is used to:
–carry out fault finding on faults that do not have a fault display, and which may correspond to a customer
complaint,
–check that the system is operating correctly and that there is no risk of a fault recurring after repairs.
This section gives the fault finding procedures for statuses and parameters and the conditions for checking them.
If a status is not behaving normally or a parameter is outside the permitted tolerance values, consult the
corresponding fault finding page.
Customer complaints - Fault finding chart
If the test with the diagnostic tool is OK but the customer complaint is still present, the fault should be processed by
customer complaint.
A synopsis of the general procedure to follow is provided on the following page in
the form of a flow chart.
Page 11 of 139
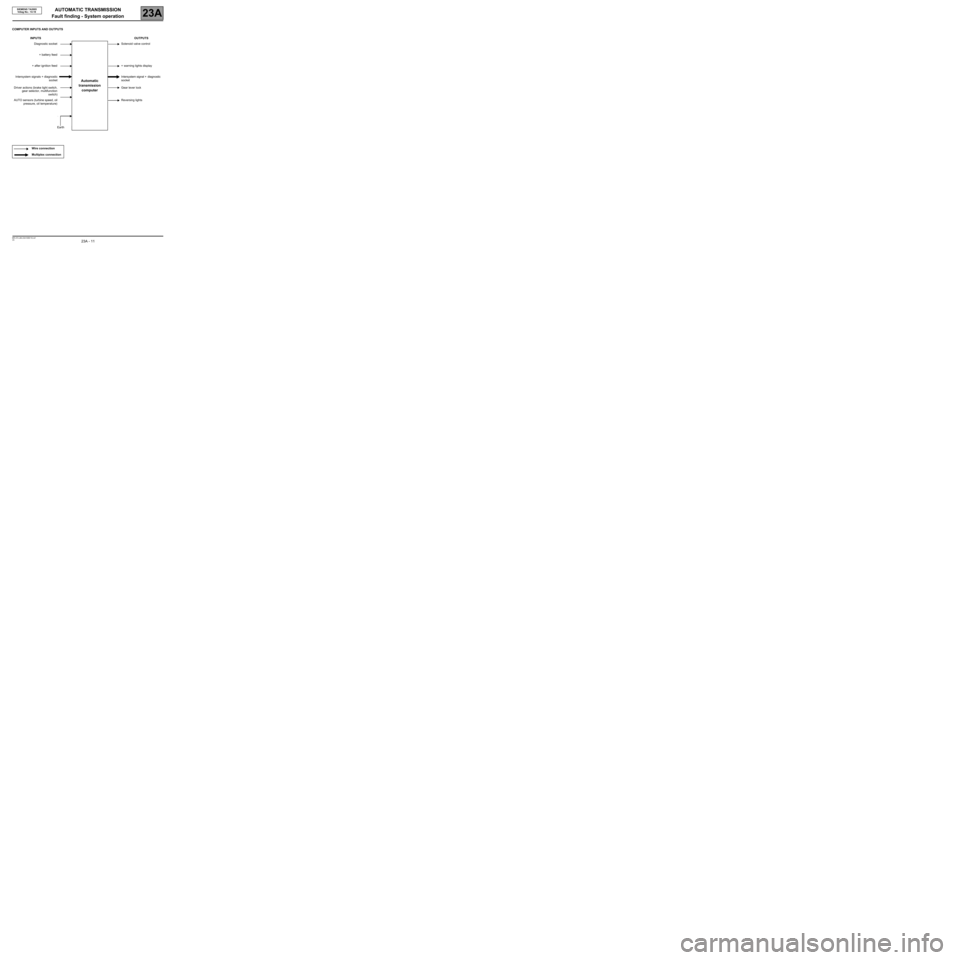
AUTOMATIC TRANSMISSION
Fault finding - System operation
23A
23A - 11V5 MR-372-J84-23A100$116.mif
SIEMENS TA2005
Vdiag No.: 14-18
COMPUTER INPUTS AND OUTPUTS
INPUTS OUTPUTS
Diagnostic socket
Automatic
transmission
computer
Solenoid valve control
+ battery feed
+ after ignition feed + warning lights display
Intersystem signals + diagnostic
socketIntersystem signal + diagnostic
socket
Driver actions (brake light switch,
gear selector, multifunction
switch)Gear lever lock
AUTO sensors (turbine speed, oil
pressure, oil temperature)Reversing lights
Earth
Wire connection
Multiplex connection
Page 12 of 139
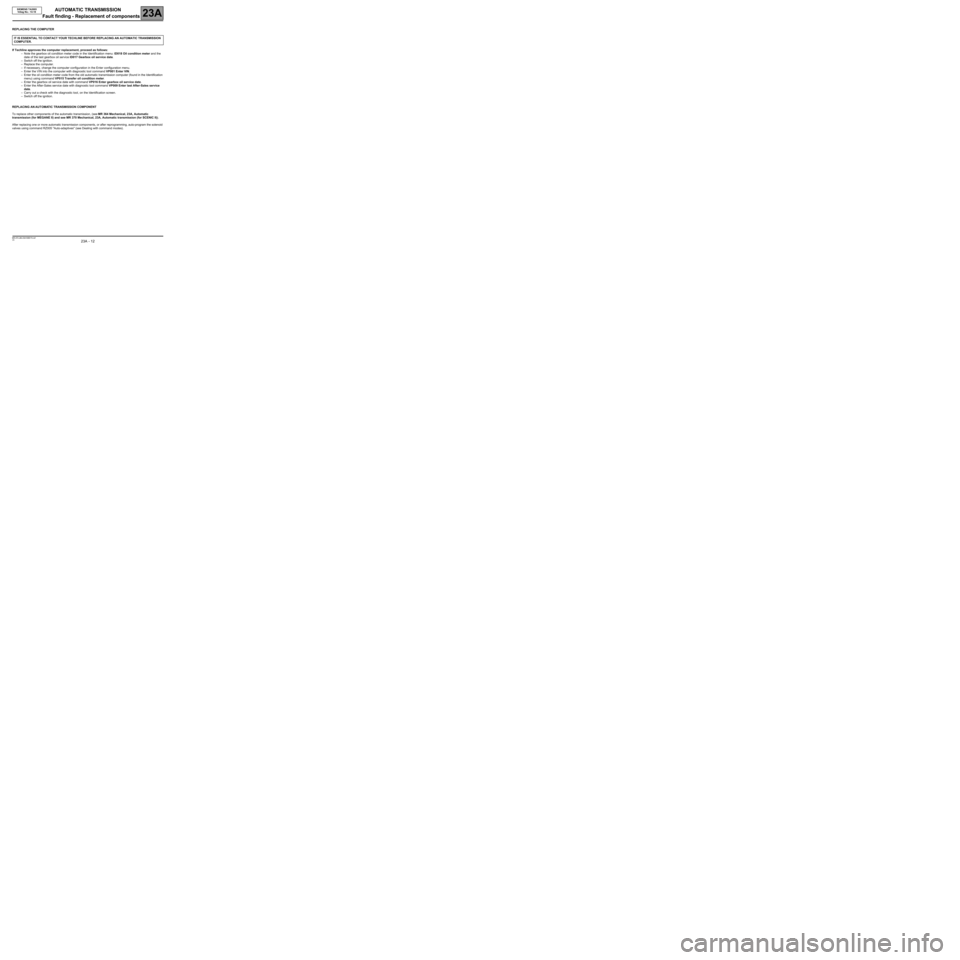
Fault finding - Replacement of components23A
23A - 12V5 MR-372-J84-23A100$174.mif
SIEMENS TA2005
Vdiag No.: 14-18AUTOMATIC TRANSMISSION
Fault finding - Replacement of components
REPLACING THE COMPUTER
If Techline approves the computer replacement, proceed as follows:
–Note the gearbox oil condition meter code in the Identification menu: ID018 Oil condition meter and the
date of the last gearbox oil service ID017 Gearbox oil service date.
–Switch off the ignition.
–Replace the computer.
–If necessary, change the computer configuration in the Enter configuration menu.
–Enter the VIN into the computer with diagnostic tool command VP001 Enter VIN.
–Enter the oil condition meter code from the old automatic transmission computer (found in the Identification
menu) using command VP015 Transfer oil condition meter.
–Enter the gearbox oil service date with command VP016 Enter gearbox oil service date.
–Enter the After-Sales service date with diagnostic tool command VP009 Enter last After-Sales service
date.
–Carry out a check with the diagnostic tool, on the Identification screen.
–Switch off the ignition.
REPLACING AN AUTOMATIC TRANSMISSION COMPONENT
To replace other components of the automatic transmission, (see MR 364 Mechanical, 23A, Automatic
transmission (for MEGANE II) and see MR 370 Mechanical, 23A, Automatic transmission (for SCENIC II)).
After replacing one or more automatic transmission components, or after reprogramming, auto-program the solenoid
valves using command RZ005 "Auto-adaptives" (see Dealing with command modes).IT IS ESSENTIAL TO CONTACT YOUR TECHLINE BEFORE REPLACING AN AUTOMATIC TRANSMISSION
COMPUTER.
MR-372-J84-23A100$174.mif
Page 13 of 139
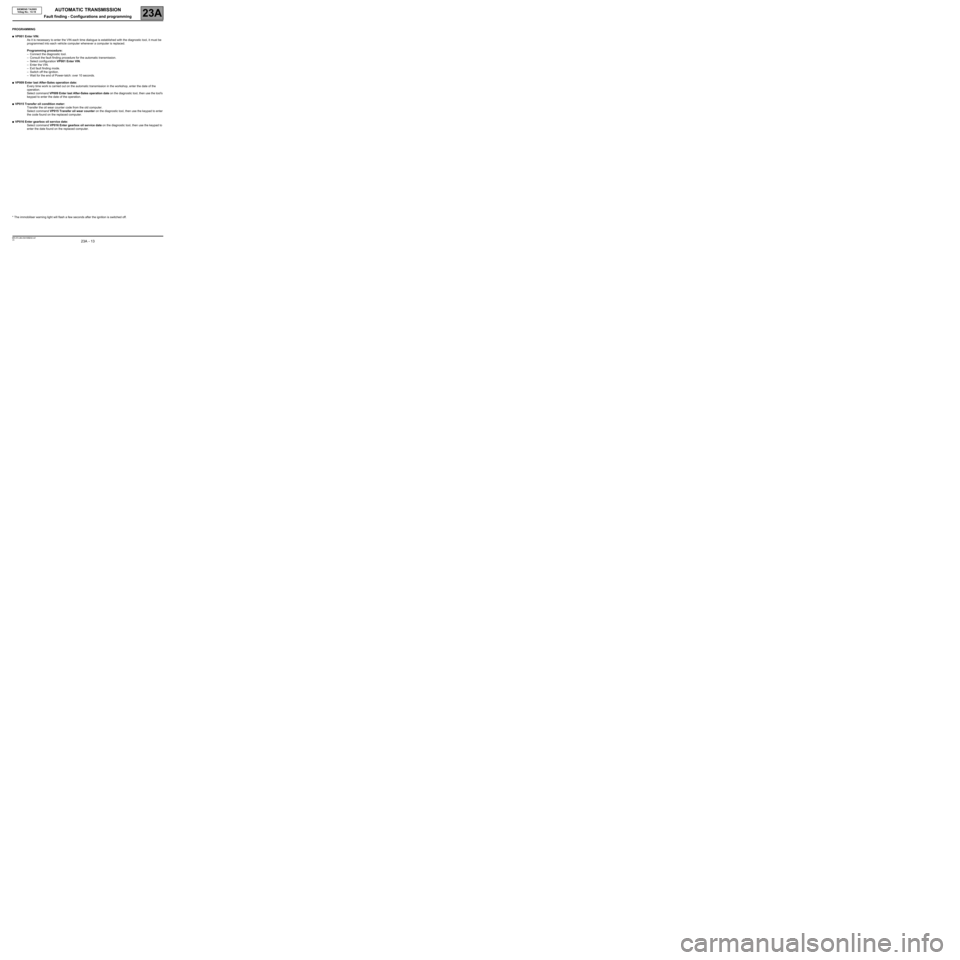
Fault finding - Configurations and programming23A
23A - 13V5 MR-372-J84-23A100$232.mif
SIEMENS TA2005
Vdiag No.: 14-18AUTOMATIC TRANSMISSION
Fault finding - Configurations and programming
PROGRAMMING
●VP001 Enter VIN:
As it is necessary to enter the VIN each time dialogue is established with the diagnostic tool, it must be
programmed into each vehicle computer whenever a computer is replaced.
Programming procedure:
–Connect the diagnostic tool.
–Consult the fault finding procedure for the automatic transmission.
–Select configuration VP001 Enter VIN.
–Enter the VIN.
–Exit fault finding mode.
–Switch off the ignition.
–Wait for the end of Power-latch: over 10 seconds.
●VP009 Enter last After-Sales operation date:
Every time work is carried out on the automatic transmission in the workshop, enter the date of the
operation.
Select command VP009 Enter last After-Sales operation date on the diagnostic tool, then use the tool's
keypad to enter the date of the operation.
●VP015 Transfer oil condition meter:
Transfer the oil wear counter code from the old computer.
Select command VP015 Transfer oil wear counter on the diagnostic tool, then use the keypad to enter
the code found on the replaced computer.
●VP016 Enter gearbox oil service date:
Select command VP016 Enter gearbox oil service date on the diagnostic tool, then use the keypad to
enter the date found on the replaced computer.
* The immobiliser warning light will flash a few seconds after the ignition is switched off.
MR-372-J84-23A100$232.mif
Page 16 of 139
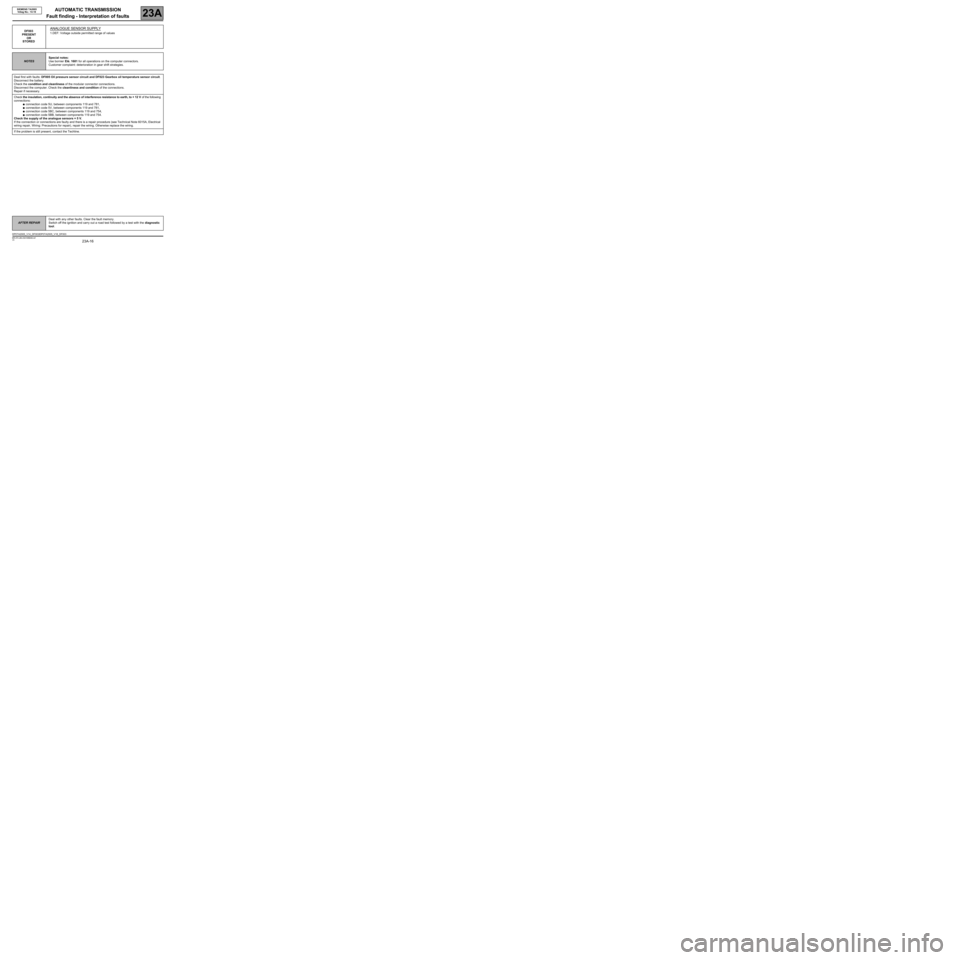
Fault finding - Interpretation of faults23A
23A-16V5 MR-372-J84-23A100$348.mif
SIEMENS TA2005
Vdiag No.: 14-18AUTOMATIC TRANSMISSION
Fault finding - Interpretation of faults
DF003
PRESENT
OR
STOREDANALOGUE SENSOR SUPPLY
1.DEF: Voltage outside permitted range of values
NOTESSpecial notes:
Use bornier Elé. 1681 for all operations on the computer connectors.
Customer complaint: deterioration in gear shift strategies.
Deal first with faults: DF005 Oil pressure sensor circuit and DF023 Gearbox oil temperature sensor circuit.
Disconnect the battery.
Check the condition and cleanliness of the modular connector connections.
Disconnect the computer. Check the cleanliness and condition of the connections.
Repair if necessary.
Check the insulation, continuity and the absence of interference resistance to earth, to + 12 V of the following
connections:
●connection code 5U, between components 119 and 781,
●connection code 5V, between components 119 and 781,
●connection code 5BC, between components 119 and 754,
●connection code 5BB, between components 119 and 754.
Check the supply of the analogue sensors = 5 V.
If the connection or connections are faulty and there is a repair procedure (see Technical Note 6015A, Electrical
wiring repair, Wiring: Precautions for repair), repair the wiring. Otherwise replace the wiring.
If the problem is still present, contact the Techline.
AFTER REPAIRDeal with any other faults. Clear the fault memory.
Switch off the ignition and carry out a road test followed by a test with the diagnostic
tool.
DP0TA2005_V14_DF003/DP0TA2005_V18_DF003
MR-372-J84-23A100$348.mif
Page 17 of 139
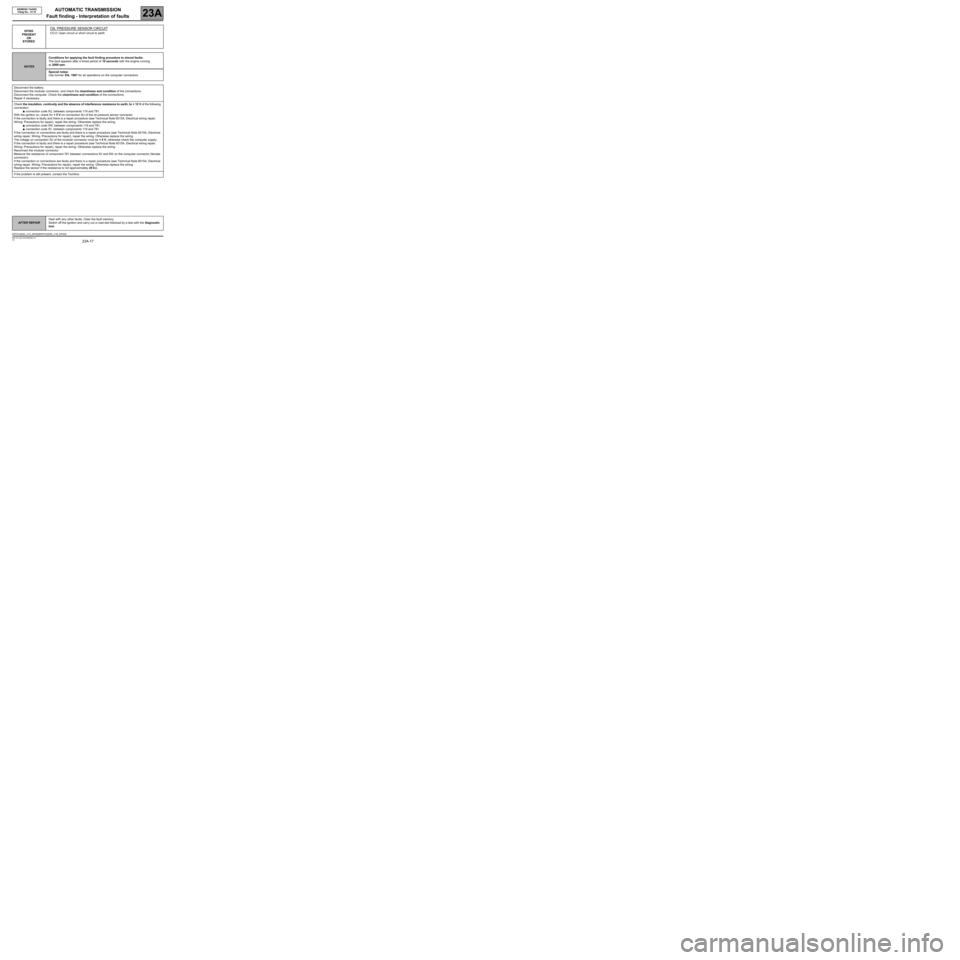
AUTOMATIC TRANSMISSION
Fault finding - Interpretation of faults
23A
23A-17V5 MR-372-J84-23A100$348.mif
SIEMENS TA2005
Vdiag No.: 14-18
DF005
PRESENT
OR
STOREDOIL PRESSURE SENSOR CIRCUIT
CO.0: Open circuit or short circuit to earth
NOTESConditions for applying the fault finding procedure to stored faults:
The fault appears after a timed period of 10 seconds with the engine running
at 2000 rpm.
Special notes:
Use bornier Elé. 1681 for all operations on the computer connectors.
Disconnect the battery.
Disconnect the modular connector, and check the cleanliness and condition of the connections.
Disconnect the computer. Check the cleanliness and condition of the connections.
Repair if necessary.
Check the insulation, continuity and the absence of interference resistance to earth, to + 12 V of the following
connection:
●connection code 5U, between components 119 and 781.
With the ignition on, check for + 5 V on connection 5U of the oil pressure sensor connector.
If the connection is faulty and there is a repair procedure (see Technical Note 6015A, Electrical wiring repair,
Wiring: Precautions for repair), repair the wiring. Otherwise replace the wiring.
●connection code 5W, between components 119 and 781,
●connection code 5V, between components 119 and 781.
If the connection or connections are faulty and there is a repair procedure (see Technical Note 6015A, Electrical
wiring repair, Wiring: Precautions for repair), repair the wiring. Otherwise replace the wiring.
The voltage on connection 5U of the modular connector must be + 5 V, otherwise check the computer supply.
If the connection is faulty and there is a repair procedure (see Technical Note 6015A, Electrical wiring repair,
Wiring: Precautions for repair), repair the wiring. Otherwise replace the wiring.
Reconnect the modular connector.
Measure the resistance of component 781 between connections 5V and 5W on the computer connector (female
connector).
If the connection or connections are faulty and there is a repair procedure (see Technical Note 6015A, Electrical
wiring repair, Wiring: Precautions for repair), repair the wiring. Otherwise replace the wiring.
Replace the sensor if the resistance is not approximately 20 kΩ.
If the problem is still present, contact the Techline.
AFTER REPAIRDeal with any other faults. Clear the fault memory.
Switch off the ignition and carry out a road test followed by a test with the diagnostic
tool.
DP0TA2005_V14_DF005/DP0TA2005_V18_DF005
Page 18 of 139
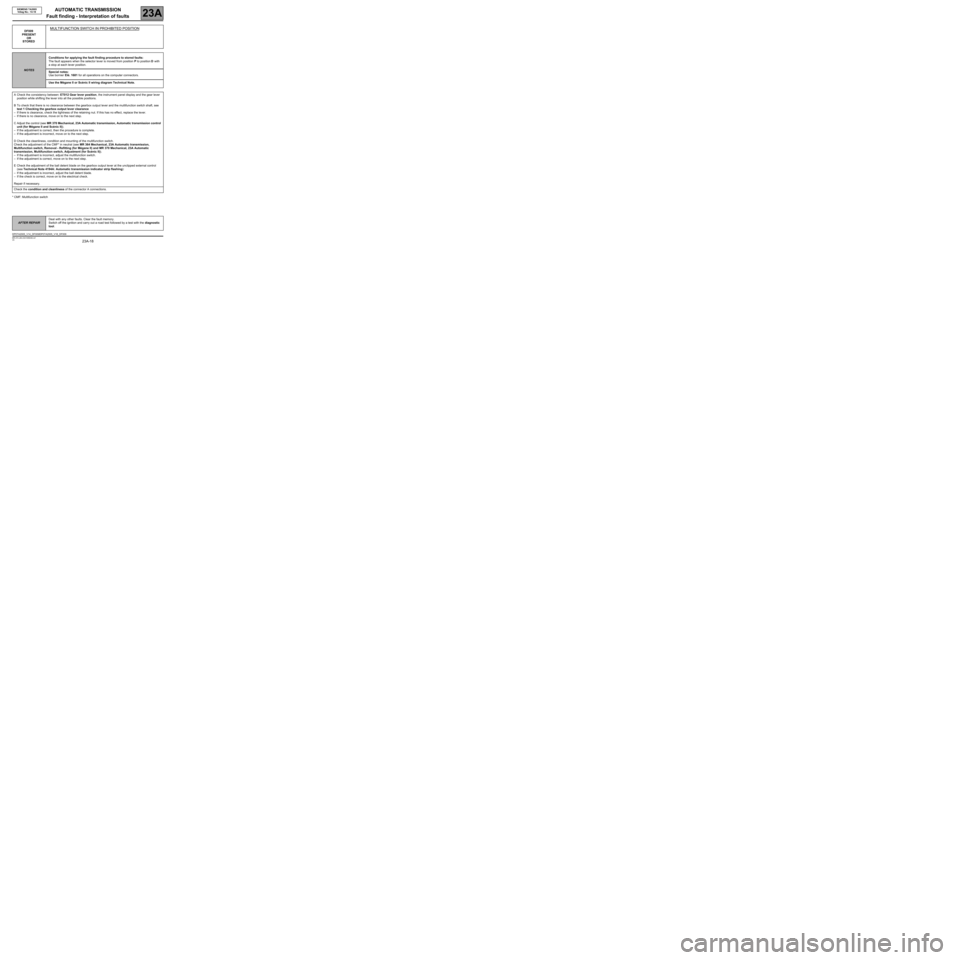
AUTOMATIC TRANSMISSION
Fault finding - Interpretation of faults
23A
23A-18V5 MR-372-J84-23A100$348.mif
SIEMENS TA2005
Vdiag No.: 14-18
* CMF: Multifunction switch DF009
PRESENT
OR
STORED
MULTIFUNCTION SWITCH IN PROHIBITED POSITION
NOTESConditions for applying the fault finding procedure to stored faults:
The fault appears when the selector lever is moved from position P to position D with
a stop at each lever position.
Special notes:
Use bornier Elé. 1681 for all operations on the computer connectors.
Use the Mégane II or Scénic II wiring diagram Technical Note.
ACheck the consistency between: ET012 Gear lever position, the instrument panel display and the gear lever
position while shifting the lever into all the possible positions.
BTo check that there is no clearance between the gearbox output lever and the multifunction switch shaft, see
test 1 Checking the gearbox output lever clearance
–If there is clearance, check the tightness of the retaining nut. If this has no effect, replace the lever.
–If there is no clearance, move on to the next step.
CAdjust the control (see MR 370 Mechanical, 23A Automatic transmission, Automatic transmission control
unit (for Mégane II and Scénic II)).
–If the adjustment is correct, then the procedure is complete.
–If the adjustment is incorrect, move on to the next step.
DCheck the cleanliness, condition and mounting of the multifunction switch.
Check the adjustment of the CMF* in neutral (see MR 364 Mechanical, 23A Automatic transmission,
Multifunction switch, Removal - Refitting (for Mégane II) and MR 370 Mechanical, 23A Automatic
transmission, Multifunction switch, Adjustment (for Scénic II)).
–If the adjustment is incorrect, adjust the multifunction switch.
–If the adjustment is correct, move on to the next step.
ECheck the adjustment of the ball detent blade on the gearbox output lever at the unclipped external control
(see Technical Note 4194A: Automatic transmission indicator strip flashing):
–If the adjustment is incorrect, adjust the ball detent blade.
–If the check is correct, move on to the electrical check.
Repair if necessary.
Check the condition and cleanliness of the connector A connections.
AFTER REPAIRDeal with any other faults. Clear the fault memory.
Switch off the ignition and carry out a road test followed by a test with the diagnostic
tool.
DP0TA2005_V14_DF009/DP0TA2005_V18_DF009
Page 19 of 139
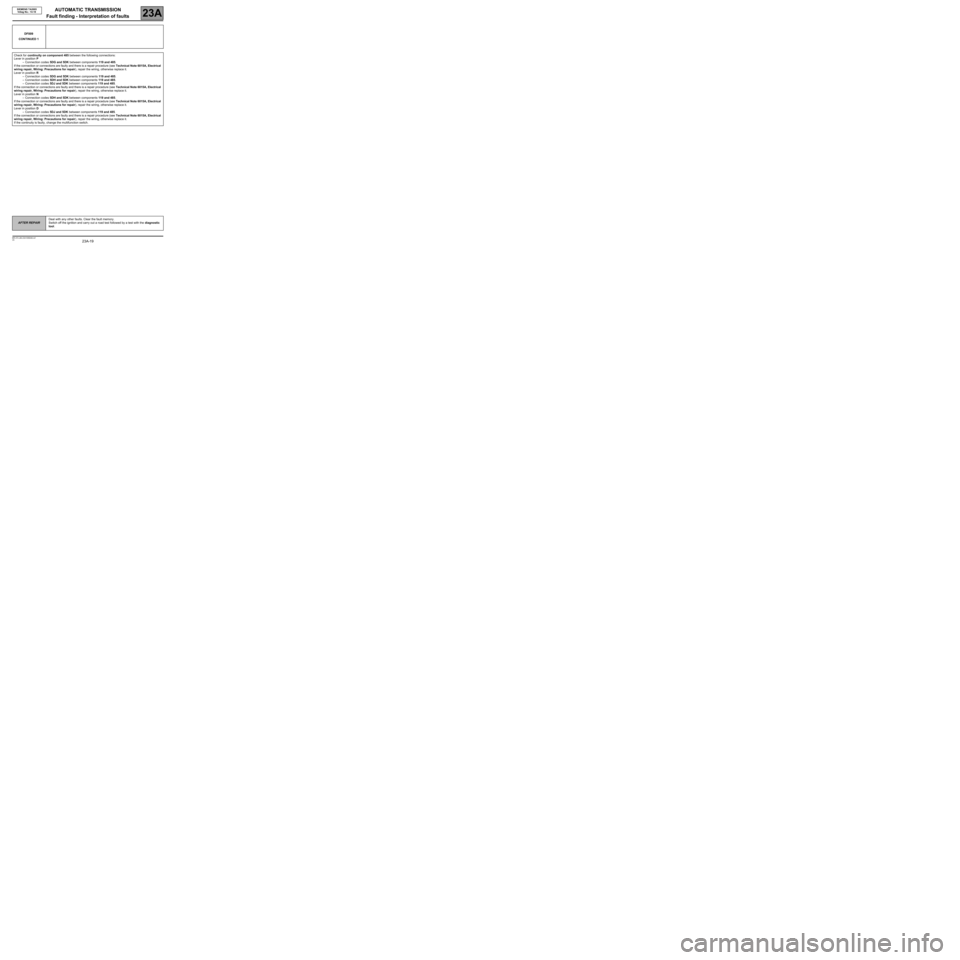
AUTOMATIC TRANSMISSION
Fault finding - Interpretation of faults
23A
23A-19V5 MR-372-J84-23A100$348.mif
SIEMENS TA2005
Vdiag No.: 14-18
DF009
CONTINUED 1
Check for continuity on component 485 between the following connections:
Lever in position P
–Connection codes 5DG and 5DK between components 119 and 485.
If the connection or connections are faulty and there is a repair procedure (see Technical Note 6015A, Electrical
wiring repair, Wiring: Precautions for repair), repair the wiring, otherwise replace it.
Lever in position R
–Connection codes 5DG and 5DK between components 119 and 485.
–Connection codes 5DH and 5DK between components 119 and 485.
–Connection codes 5DJ and 5DK between components 119 and 485.
If the connection or connections are faulty and there is a repair procedure (see Technical Note 6015A, Electrical
wiring repair, Wiring: Precautions for repair), repair the wiring, otherwise replace it.
Lever in position N
–Connection codes 5DH and 5DK between components 119 and 485.
If the connection or connections are faulty and there is a repair procedure (see Technical Note 6015A, Electrical
wiring repair, Wiring: Precautions for repair), repair the wiring, otherwise replace it.
Lever in position D
–Connection codes 5DJ and 5DK between components 119 and 485.
If the connection or connections are faulty and there is a repair procedure (see Technical Note 6015A, Electrical
wiring repair, Wiring: Precautions for repair), repair the wiring, otherwise replace it.
If the continuity is faulty, change the multifunction switch.
AFTER REPAIRDeal with any other faults. Clear the fault memory.
Switch off the ignition and carry out a road test followed by a test with the diagnostic
tool.
Page 20 of 139
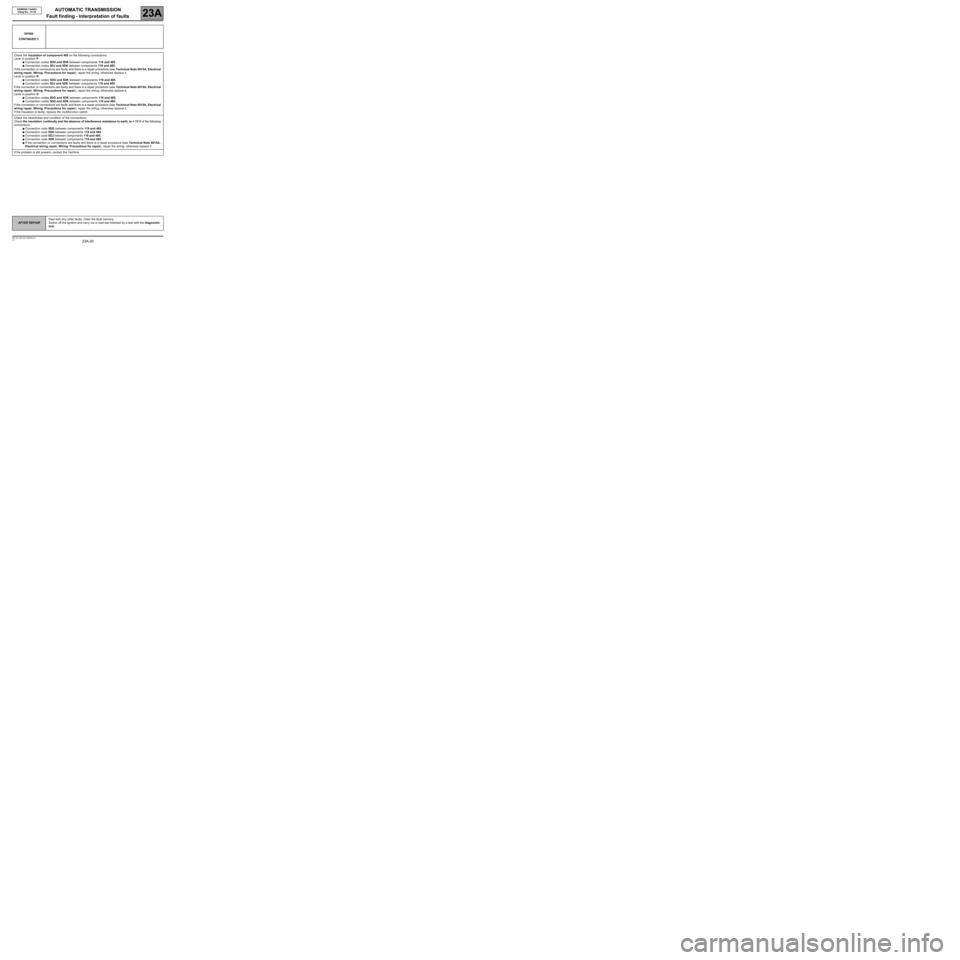
AUTOMATIC TRANSMISSION
Fault finding - Interpretation of faults
23A
23A-20V5 MR-372-J84-23A100$348.mif
SIEMENS TA2005
Vdiag No.: 14-18
DF009
CONTINUED 2
Check the insulation of component 485 on the following connections:
Lever in position P
●Connection codes 5DH and 5DK between components 119 and 485.
●Connection codes 5DJ and 5DK between components 119 and 485.
If the connection or connections are faulty and there is a repair procedure (see Technical Note 6015A, Electrical
wiring repair, Wiring: Precautions for repair), repair the wiring, otherwise replace it.
Lever in position N
●Connection codes 5DG and 5DK between components 119 and 485.
●Connection codes 5DJ and 5DK between components 119 and 485.
If the connection or connections are faulty and there is a repair procedure (see Technical Note 6015A, Electrical
wiring repair, Wiring: Precautions for repair), repair the wiring, otherwise replace it.
Lever in position D
●Connection codes 5DG and 5DK between components 119 and 485.
●Connection codes 5DH and 5DK between components 119 and 485.
If the connection or connections are faulty and there is a repair procedure (see Technical Note 6015A, Electrical
wiring repair, Wiring: Precautions for repair), repair the wiring, otherwise replace it.
If the insulation is faulty, replace the multifunction switch.
Check the cleanliness and condition of the connections.
Check the insulation, continuity and the absence of interference resistance to earth, to + 12 V of the following
connections:
●Connection code 5DG between components 119 and 485.
●Connection code 5DH between components 119 and 485.
●Connection code 5DJ between components 119 and 485.
●Connection code 5DK between components 119 and 485.
●If the connection or connections are faulty and there is a repair procedure (see Technical Note 6015A,
Electrical wiring repair, Wiring: Precautions for repair), repair the wiring, otherwise replace it.
If the problem is still present, contact the Techline.
AFTER REPAIRDeal with any other faults. Clear the fault memory.
Switch off the ignition and carry out a road test followed by a test with the diagnostic
tool.