ESP RENAULT SCENIC 2007 J84 / 2.G Power Assisted Steering User Guide
[x] Cancel search | Manufacturer: RENAULT, Model Year: 2007, Model line: SCENIC, Model: RENAULT SCENIC 2007 J84 / 2.GPages: 59, PDF Size: 0.19 MB
Page 31 of 59
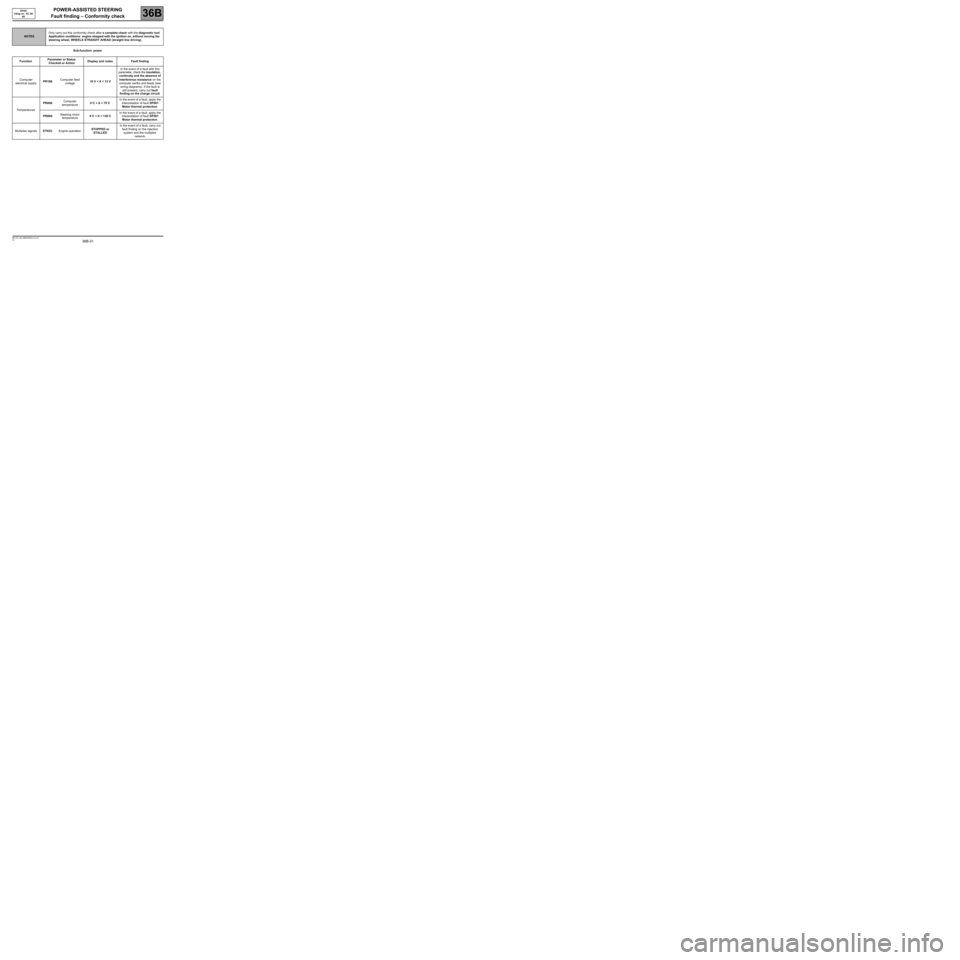
POWER-ASSISTED STEERING
Fault finding – Conformity check
36B
36B-31V5 MR-372-J84-36B000$528_fra.mif
EPAS
Vdiag no.: 05, 09,
0D
Sub-function: power
NOTESOnly carry out this conformity check after a complete check with the diagnostic tool.
Application conditions: engine stopped with the ignition on, without moving the
steering wheel, WHEELS STRAIGHT AHEAD (straight line driving).
FunctionParameter or Status
Checked or ActionDisplay and notes Fault finding
Computer
electrical supplyPR108:Computer feed
voltage10 V < X < 13 VIn the event of a fault with this
parameter, check the insulation,
continuity and the absence of
interference resistance on the
computer earths and feeds (see
wiring diagrams). If the fault is
still present, carry out fault
finding on the charge circuit.
TemperaturesPR008:Computer
temperature0˚C < X < 75˚CIn the event of a fault, apply the
interpretation of fault DF001
Motor thermal protection.
PR009:Steering motor
temperature0˚C < X < 130˚CIn the event of a fault, apply the
interpretation of fault DF001
Motor thermal protection.
Multiplex signalsET023:Engine operationSTOPPED or
STALLEDIn the event of a fault, carry out
fault finding on the injection
system and the multiplex
network.
Page 35 of 59
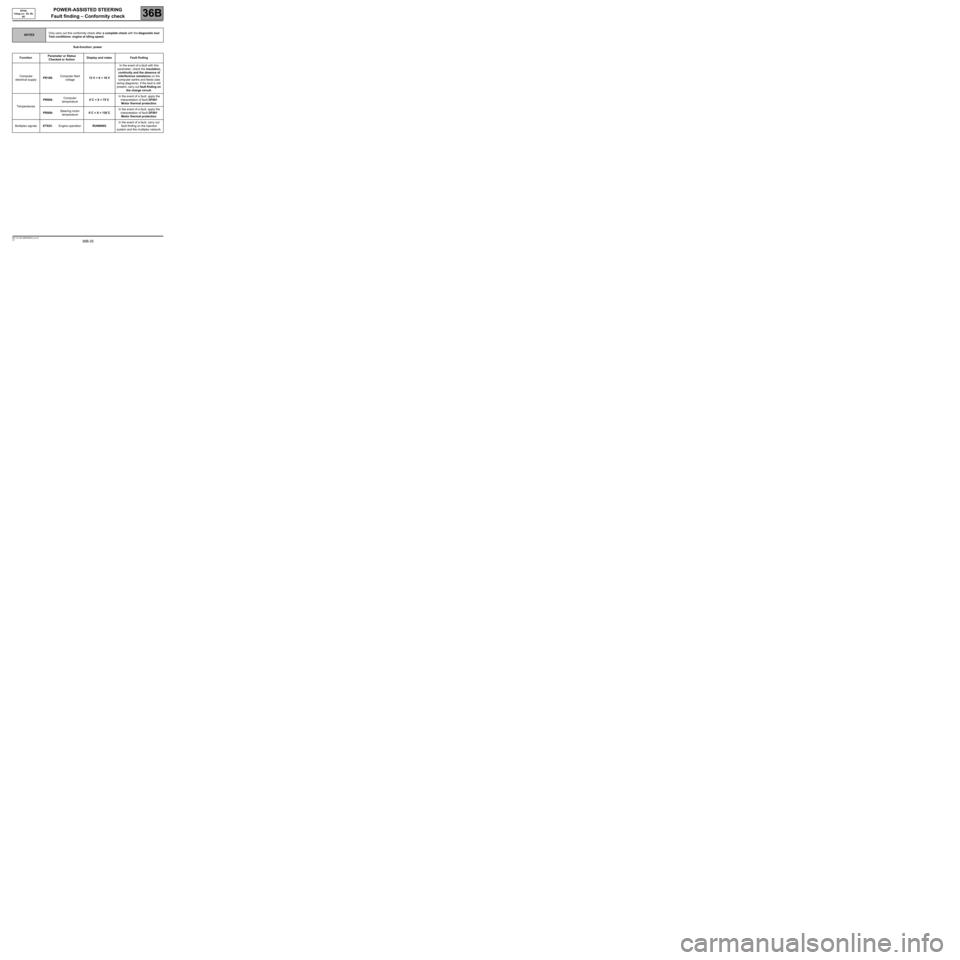
POWER-ASSISTED STEERING
Fault finding – Conformity check
36B
36B-35V5 MR-372-J84-36B000$528_fra.mif
EPAS
Vdiag no.: 05, 09,
0D
Sub-function: power
NOTESOnly carry out this conformity check after a complete check with the diagnostic tool.
Test conditions: engine at idling speed.
FunctionParameter or Status
Checked or ActionDisplay and notes Fault finding
Computer
electrical supplyPR108:Computer feed
voltage12 V < X < 16 VIn the event of a fault with this
parameter, check the insulation,
continuity and the absence of
interference resistance on the
computer earths and feeds (see
wiring diagrams). If the fault is still
present, carry out fault finding on
the charge circuit.
TemperaturesPR008:Computer
temperature0˚C < X < 75˚CIn the event of a fault, apply the
interpretation of fault DF001
Motor thermal protection.
PR009:Steering motor
temperature0˚C < X < 130˚CIn the event of a fault, apply the
interpretation of fault DF001
Motor thermal protection.
Multiplex signalsET023:Engine operationRUNNINGIn the event of a fault, carry out
fault finding on the injection
system and the multiplex network.
Page 38 of 59
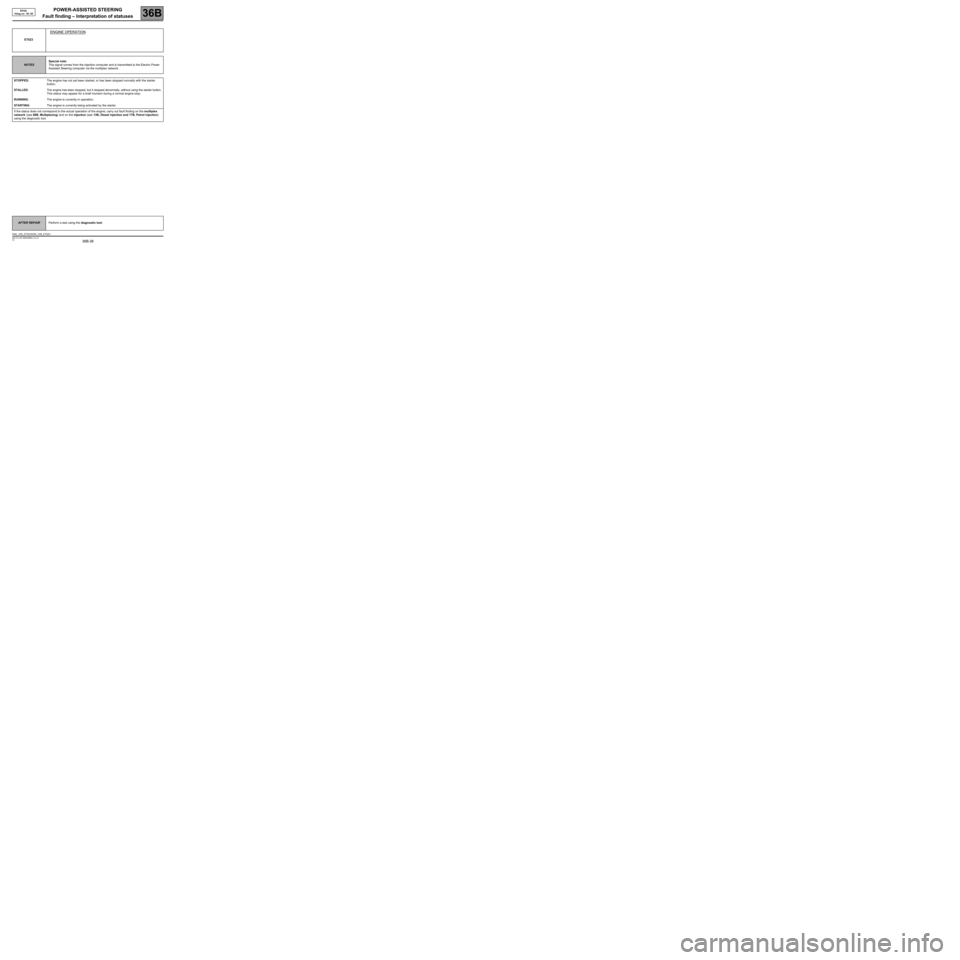
POWER-ASSISTED STEERING
Fault finding – Interpretation of statuses
36B
36B-38V5 MR-372-J84-36B000$660_fra.mif
EPAS
Vdiag no.: 05, 09
ET023
ENGINE OPERATION
NOTESSpecial note:
This signal comes from the injection computer and is transmitted to the Electric Power
Assisted Steering computer via the multiplex network.
STOPPED:The engine has not yet been started, or has been stopped normally with the starter
button.
STALLED:The engine has been stopped, but it stopped abnormally, without using the starter button.
This status may appear for a brief moment during a normal engine stop.
RUNNING:The engine is currently in operation.
STARTING:The engine is currently being activated by the starter.
If the status does not correspond to the actual operation of the engine, carry out fault finding on the multiplex
network (see 88B, Multiplexing) and on the injection (see 13B, Diesel injection and 17B, Petrol injection)
using the diagnostic tool.
AFTER REPAIRPerform a test using the diagnostic tool.
DAE_V05_ET023/DAE_V09_ET023
Page 39 of 59
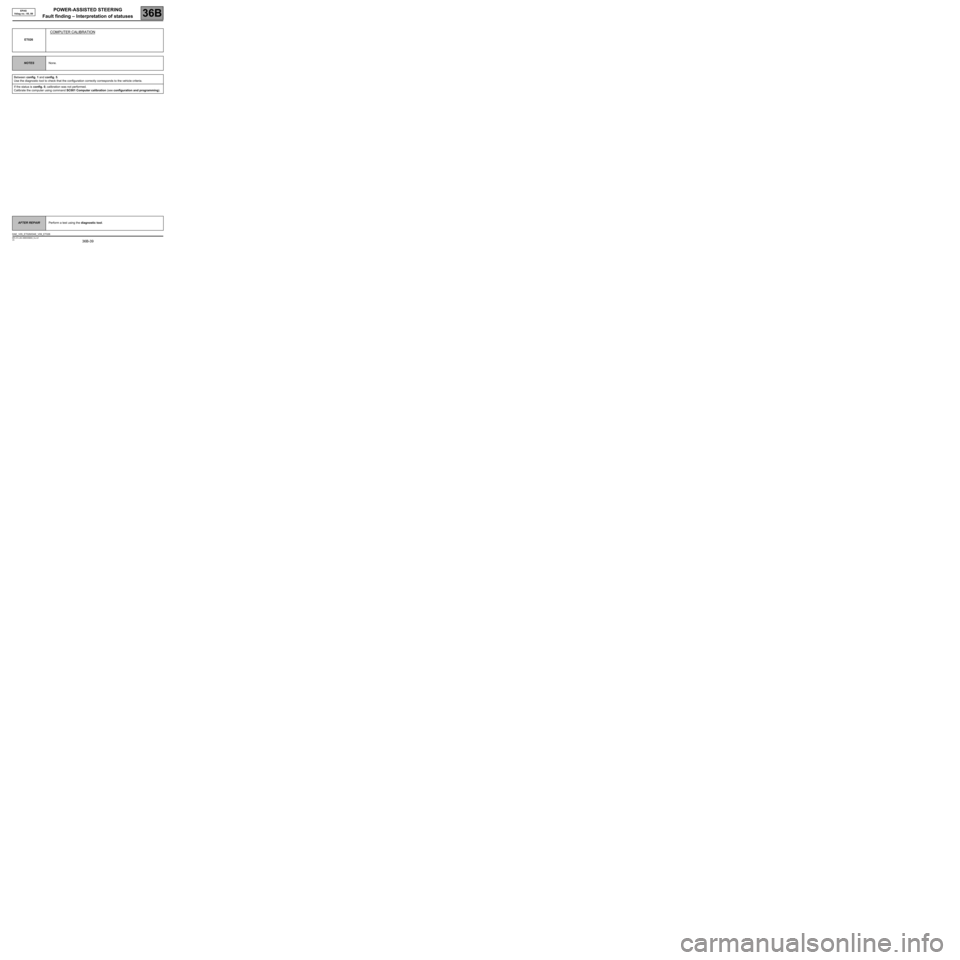
POWER-ASSISTED STEERING
Fault finding – Interpretation of statuses
36B
36B-39V5 MR-372-J84-36B000$660_fra.mif
EPAS
Vdiag no.: 05, 09
ET026
COMPUTER CALIBRATION
NOTESNone.
Between config. 1 and config. 5.
Use the diagnostic tool to check that the configuration correctly corresponds to the vehicle criteria.
If the status is config. 0, calibration was not performed.
Calibrate the computer using command SC001 Computer calibration (see configuration and programming).
AFTER REPAIRPerform a test using the diagnostic tool.
DAE_V05_ET026/DAE_V09_ET026
Page 43 of 59
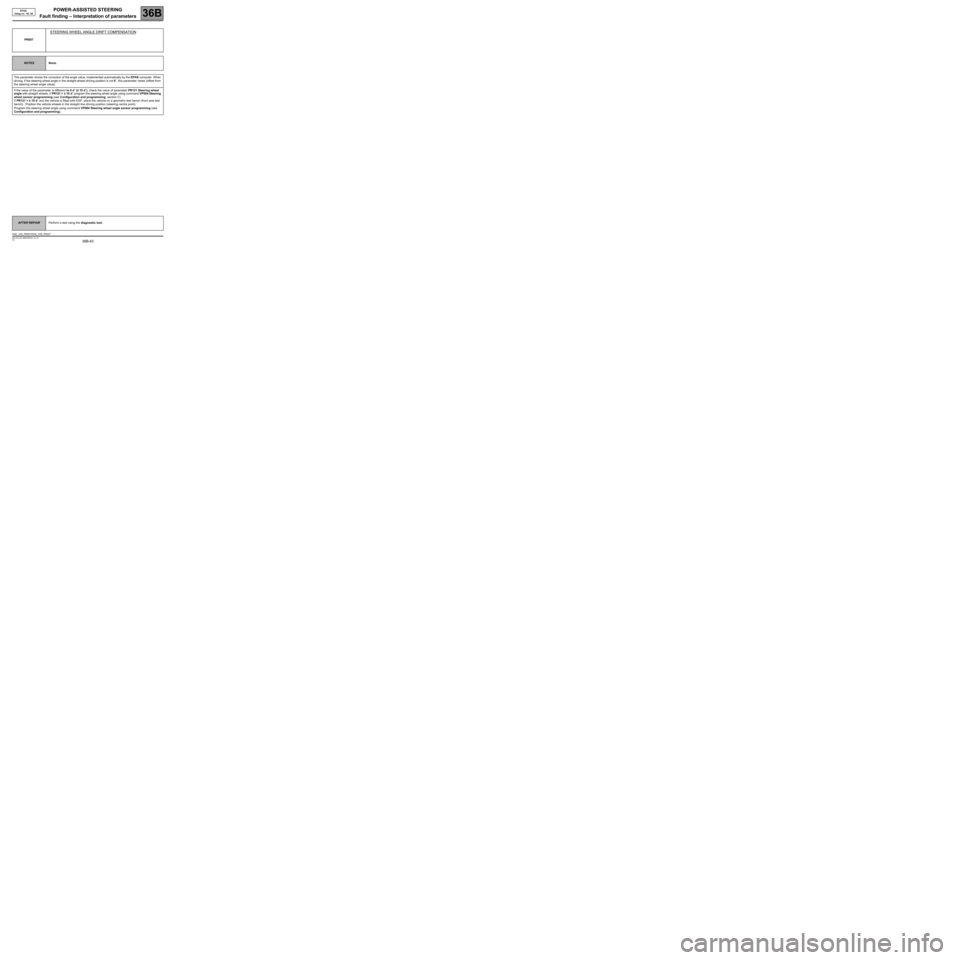
POWER-ASSISTED STEERING
Fault finding – Interpretation of parameters
36B
36B-43V5 MR-372-J84-36B000$792_fra.mif
EPAS
Vdiag no.: 05, 09
PR007
STEERING WHEEL ANGLE DRIFT COMPENSATION
NOTESNone.
This parameter shows the correction of the angle value, implemented automatically by the EPAS computer. When
driving, if the steering wheel angle in the straight-ahead driving position is not 0˚, this parameter varies (offset from
the steering wheel angle value).
If the value of the parameter is different to 0 d˚ (± 10 d˚), check the value of parameter PR121 Steering wheel
angle with straight wheels, if PR121 > ± 10 d˚ program the steering wheel angle using command VP004 Steering
wheel sensor programming (see Configuration and programming, section C).
If PR121 < ± 10 d˚ and the vehicle is fitted with ESP, place the vehicle on a geometry test bench (front axle test
bench).. Position the vehicle wheels in the straight line driving position (steering centre point).
Program the steering wheel angle using command VP004 Steering wheel angle sensor programming (see
Configuration and programming).
AFTER REPAIRPerform a test using the diagnostic tool.
DAE_V05_PR007/DAE_V09_PR007
Page 46 of 59
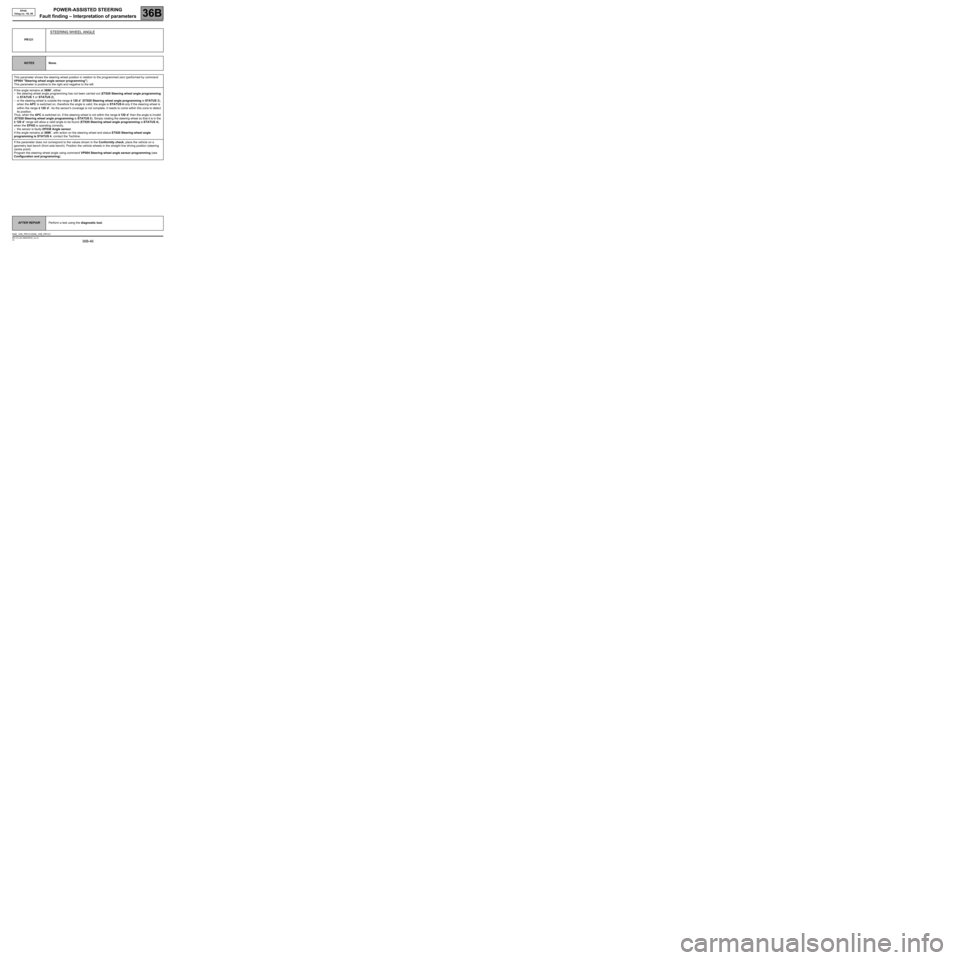
POWER-ASSISTED STEERING
Fault finding – Interpretation of parameters
36B
36B-46V5 MR-372-J84-36B000$792_fra.mif
EPAS
Vdiag no.: 05, 09
PR121
STEERING WHEEL ANGLE
NOTESNone.
This parameter shows the steering wheel position in relation to the programmed zero (performed by command
VP004 "Steering wheel angle sensor programming").
This parameter is positive to the right and negative to the left.
If the angle remains at 3696˚, either:
–the steering wheel angle programming has not been carried out (ET020 Steering wheel angle programming
is STATUS 1 or STATUS 2),
–or the steering wheel is outside the range ± 120 d˚ (ET020 Steering wheel angle programming is STATUS 3),
when the APC is switched on, therefore the angle is valid; the angle is STATUS 4 only if the steering wheel is
within the range ± 120 d˚. As the sensor's coverage is not complete, it needs to come within this zone to detect
its position.
Thus, when the APC is switched on, if the steering wheel is not within the range ± 120 d˚ then the angle is invalid
(ET020 Steering wheel angle programming is STATUS 3). Simply rotating the steering wheel so that it is in the
± 120 d˚ range will allow a valid angle to be found (ET020 Steering wheel angle programming is STATUS 4),
when the EPAS is operating correctly,
–the sensor is faulty DF038 Angle sensor.
If the angle remains at 3696˚, with action on the steering wheel and status ET020 Steering wheel angle
programming is STATUS 4, contact the Techline.
If the parameter does not correspond to the values shown in the Conformity check, place the vehicle on a
geometry test bench (front axle bench). Position the vehicle wheels in the straight line driving position (steering
centre point).
Program the steering wheel angle using command VP004 Steering wheel angle sensor programming (see
Configuration and programming).
AFTER REPAIRPerform a test using the diagnostic tool.
DAE_V05_PR121/DAE_V09_PR121
Page 50 of 59
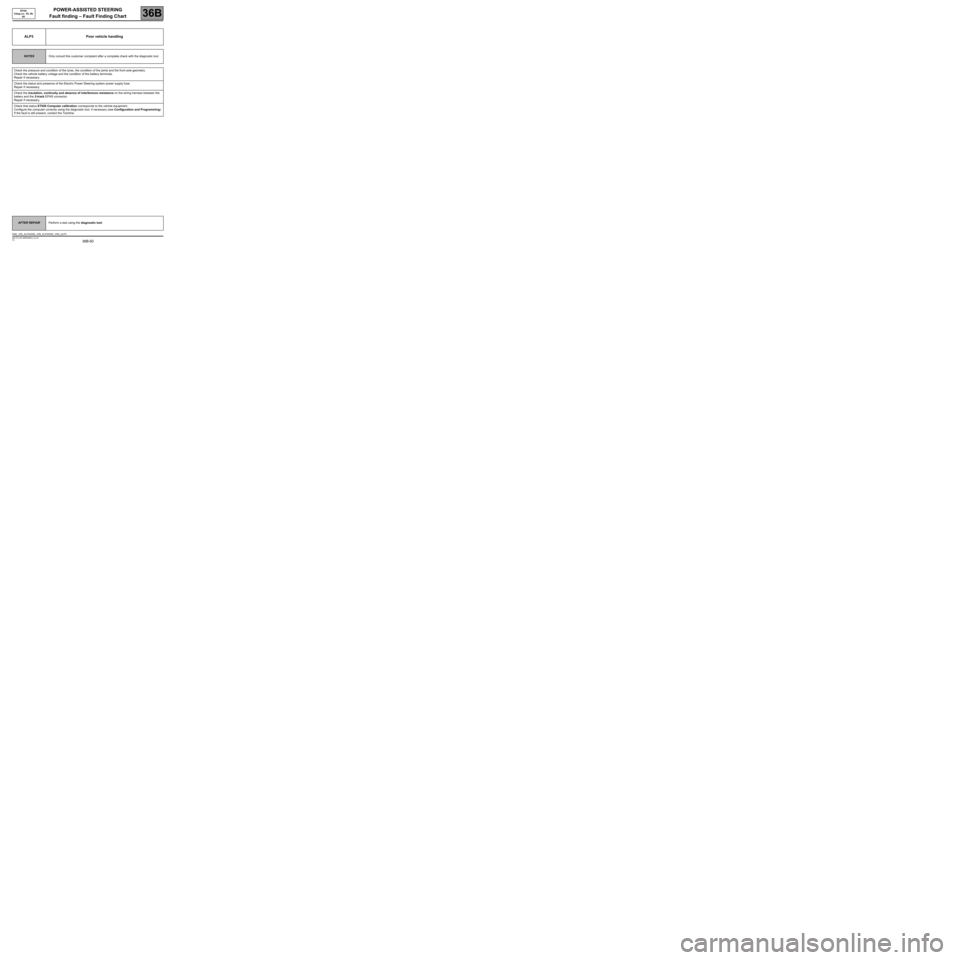
POWER-ASSISTED STEERING
Fault finding – Fault Finding Chart
36B
36B-50V5 MR-372-J84-36B000$924_fra.mif
EPAS
Vdiag no.: 05, 09,
0D
ALP3 Poor vehicle handling
NOTESOnly consult this customer complaint after a complete check with the diagnostic tool.
Check the pressure and condition of the tyres, the condition of the joints and the front axle geometry.
Check the vehicle battery voltage and the condition of the battery terminals.
Repair if necessary.
Check the status and presence of the Electric Power Steering system power supply fuse.
Repair if necessary.
Check the insulation, continuity and absence of interference resistance on the wiring harness between the
battery and the 2-track EPAS connector.
Repair if necessary.
Check that status ET026 Computer calibration corresponds to the vehicle equipment.
Configure the computer correctly using the diagnostic tool, if necessary (see Configuration and Programming).
If the fault is still present, contact the Techline.
AFTER REPAIRPerform a test using the diagnostic tool.
DAE_V05_ALP3/DAE_V09_ALP3/DAE_V0D_ALP3